Introduction to Additive Manufacturing PDF
Document Details
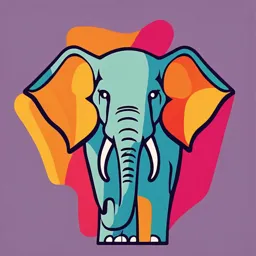
Uploaded by ConfidentDogwood8420
Mukesh Patel School of Technology Management & Engineering, Mumbai
Dr. Samadhan P. Deshmukh
Tags
Summary
This document provides an introduction to additive manufacturing (AM), also known as 3D printing. It covers the history, definitions, and classification of AM processes. This document also touches on important topics like design for additive manufacturing (DfAM), industry trends, and related file formats.
Full Transcript
Unit 1 Introduction to Additive Manufacturing Things to be learned… Dr. Samadhan P. Deshmukh, MPSTME, Mumbai 2 Introduction to AM Dr. Samadhan P. Deshmukh, MPSTME, Mumbai 3 McKinsey Report 2013 Dr. Samadhan P. Deshmukh, MPSTME, Mumbai 4 (M...
Unit 1 Introduction to Additive Manufacturing Things to be learned… Dr. Samadhan P. Deshmukh, MPSTME, Mumbai 2 Introduction to AM Dr. Samadhan P. Deshmukh, MPSTME, Mumbai 3 McKinsey Report 2013 Dr. Samadhan P. Deshmukh, MPSTME, Mumbai 4 (Management Consulting Firm) McKinsey Report 2013 Dr. Samadhan P. Deshmukh, MPSTME, Mumbai 5 (Management Consulting Firm) Dr. Samadhan P. Deshmukh, MPSTME, Mumbai 6 Dr. Samadhan P. Deshmukh, MPSTME, Mumbai 7 History of AM Dr. Samadhan P. Deshmukh, MPSTME, Mumbai 8 Additive Manufacturing History of AM 1980-2000 The earliest 3D printing technologies first became visible in the late 2000- 1980’s, at which time they were called Rapid Prototyping (RP) technologies. This is because the processes were originally conceived as a fast and more cost-effective method for creating prototypes for product development within industry. 1983 Charles Hull invents Stereolithography (SLA). Charles ‘Chuck’ Hull was the first to develop a technology for creating solid objects from a CAD/CAM file, inventing the process he termed ‘stereolithography’ in 1983. SLA works by curing and solidifying successive layers of liquid photopolymer resin using an ultraviolet laser. The field that came to be known variously as 'additive manufacturing', 'rapid prototyping' and '3D printing' was born. https://www.asme.org/topics- resources/content/infographic-the-history-of-3d-printing Dr. Samadhan P. Deshmukh, MPSTME, Mumbai 10 Dr. Samadhan P. Deshmukh, MPSTME, Mumbai 11 Dr. Samadhan P. Deshmukh, MPSTME, Mumbai 12 AM applications timeline Source: Royal Academy of Engineering, UKDr. Samadhan P. Deshmukh, MPSTME, Mumbai 13 Distinction between AM, CNC and Other techniques Dr. Samadhan P. Deshmukh, MPSTME, Mumbai 14 Traditional manufacturing-Machining Dr. Samadhan P. Deshmukh, MPSTME, Mumbai 15 Traditional manufacturing-Injection Moulding Dr. Samadhan P. Deshmukh, MPSTME, Mumbai 16 Subtractive v/s Additive Dr. Samadhan P. Deshmukh, MPSTME, Mumbai 17 Subtractive v/s Additive Dr. Samadhan P. Deshmukh, MPSTME, Mumbai 18 Additive v/s Subtractive Subtractive Injection molding Additive Dr. Samadhan P. Deshmukh, MPSTME, Mumbai 19 Challenges in CNC machining The cavity may be too deep to machine The undercut here cannot be performed without more than 3 axes machine The base cannot be machined Sharp internal features without holding it in a fixture cannot be machined without a tool radius Dr. Samadhan P. Deshmukh, MPSTME, Mumbai Source: Gibson, Additive Manufacturing 20 Distinction between AM and CNC Machining Material Speed Complexity Accuracy Geometry Programming Dr. Samadhan P. Deshmukh, MPSTME, Mumbai 21 Dr. Samadhan P. Deshmukh, MPSTME, Mumbai 22 Dr. Samadhan P. Deshmukh, MPSTME, Mumbai 23 Additive Manufacturing Defined Dr. Samadhan P. Deshmukh, MPSTME, Mumbai 24 Additive Manufacturing defined Additive Manufacturing(AM) is a process by which digital 3D design data is used to build up a component in layers by depositing material. From the International committee for Additive Manufacturing Technologies of ASTM Dr. Samadhan P. Deshmukh, MPSTME, Mumbai 28 Dr. Samadhan P. Deshmukh, MPSTME, Mumbai 30 Reasons to use AM Dr. Samadhan P. Deshmukh, MPSTME, Mumbai 31 Why is Additive Manufacturing such a big deal NOW? Improved automation Wide availability of A growing library of and component CAD/CAM software. ‘printable’ materials. technologies. Major industry and Freedom to operate Momentum, government enabled by patent confidence, and investment. expirations. creative vision. Dr. Samadhan P. Deshmukh, MPSTME, Mumbai 32 Reasons to use AM Dr. Samadhan P. Deshmukh, MPSTME, Mumbai 33 Dr. Samadhan P. Deshmukh, MPSTME, Mumbai 34 Reasons to use AM Dr. Samadhan P. Deshmukh, MPSTME, Mumbai 35 Complexity Dr. Samadhan P. Deshmukh, MPSTME, Mumbai 36 Part a. fuselage for an unmanned aerial vehicle. Part b. Multiple materials Simultaneously Part c. Section of chain Part d. Facial implant Part e. Multiple colour Part f. Ratchet mechanism Part h. Brain gear model Part i. Conformal lattice structure Dr. Samadhan P. Deshmukh, MPSTME, Mumbai 37 Dr. Samadhan P. Deshmukh, MPSTME, Mumbai 38 Dr. Samadhan P. Deshmukh, MPSTME, Mumbai 39 Mapal, http://additivemanufacturing.com Reasons to use AM Dr. Samadhan P. Deshmukh, MPSTME, Mumbai 40 Internal channels and cavities Geometry optimization Dr. Samadhan P. Deshmukh, MPSTME, Mumbai 41 Dr. Samadhan P. Deshmukh, MPSTME, Mumbai 42 Reasons to use AM Dr. Samadhan P. Deshmukh, MPSTME, Mumbai 43 Dr. Samadhan P. Deshmukh, MPSTME, Mumbai 44 Dr. Samadhan P. Deshmukh, MPSTME, Mumbai 45 Dr. Samadhan P. Deshmukh, MPSTME, Mumbai 46 Reasons to use AM Dr. Samadhan P. Deshmukh, MPSTME, Mumbai 47 Dr. Samadhan P. Deshmukh, MPSTME, Mumbai 48 Reasons to use AM - Mass Customization Dr. Samadhan P. Deshmukh, MPSTME, Mumbai 49 Classifications of AM processes Dr. Samadhan P. Deshmukh, MPSTME, Mumbai 50 Major AM processes based on Hopkinson and Dickens’ classification Stereolithography Liquid Based Jetting Systems Direct Light Processing Selective Laser Sintering Three-Dimensional Printing Fused Metal Deposite Systems Electron Beam Melting AM Processes Powder Based Selective Laser Melting Selective Masking Sintering Selective Inhibition Sintering Electro photographic Layered Manufacturing High Speed Sintering Solid Based Fused Deposition Modelling Sheet Stacking Technologies FDM: Fused Deposition Modeling SLS: Selective Laser Sintering DMLS : Direct metal laser sintering SLA: Stereo lithography DOD: Drop on Demand SLM: Selective Laser Melting DLP : Digital light processing EBM: Electron beam melting Dr. Samadhan P. Deshmukh, MPSTME, Mumbai 53 Major Technologies of AM Vat photo polymerization – Stereolithography (SLA) and Digital light processing (DLP) Powder Bed Fusion – Electron Beam Melting (EBM), Selective Laser Sintering (SLS), Selective Heat Sintering (SHS) Material Extrusion – Fusible Deposition Modelling (FDM) Material Jetting – Multi jet Modelling (MJM) Sheet Laminations – Laminated Object Manufacturing (LOM) Directed Energy Deposition – Laser Engineered Net Shaping (LENS) Dr. Samadhan P. Deshmukh, MPSTME, Mumbai 54 1. Vat photo polymerization: processes that utilize a liquid photopolymer contained in a vat and processed by selectively delivering energy to cure specific regions of a part cross-section. 2. Powder bed fusion: processes that utilize a container filled with powder processed selectively using an energy source, most commonly a scanning laser or electron beam. 3. Material extrusion: processes that deposit a material by extruding it through a nozzle, typically while scanning the nozzle in a pattern that produces a part cross-section. 4. Material jetting: ink-jet printing processes. 5. Binder jetting: processes where a binder printed into a powder bed in order to form part cross-sections. 6. Sheet lamination: processes that deposit a layer of material at a time, where the material is in sheet form. 7. Directed energy deposition: processes that simultaneously deposit a material (usually powder or wire) and provide energy to process that material through a single deposition device. Dr. Samadhan P. Deshmukh, MPSTME, Mumbai 55 Dr. Samadhan P. Deshmukh, MPSTME, Mumbai 56 Dr. Samadhan P. Deshmukh, MPSTME, Mumbai 57 Dr. Samadhan P. Deshmukh, MPSTME, Mumbai 58 Dr. Samadhan P. Deshmukh, MPSTME, Mumbai 59 AM Technologies Material is selectively dispensed through a nozzle and solidifies Fused Deposition Modeling (FDM) Dr. Samadhan P. Deshmukh, MPSTME, Mumbai 60 AM Technologies Fused Deposition Modeling (FDM) Dr. Samadhan P. Deshmukh, MPSTME, Mumbai 61 AM Technologies Material is cured by light activated polymerization Stereolithography (SLA) Dr. Samadhan P. Deshmukh, MPSTME, Mumbai 62 AM Technologies Energy (typically a Laser or electron Beam) used to selectively fuse a region of powder bed) Selective Laser Sintering (SLS) Dr. Samadhan P. Deshmukh, MPSTME, Mumbai 63 AM Technologies Sheets are bonded to form the object Laminated Object Manufacturing (LOM) Dr. Samadhan P. Deshmukh, MPSTME, Mumbai 64 Technology and Material Matrix Technology Polymers Metals Ceramics Composites Stereo lithography l l Digital light processing l Multi-jet modeling (MJM) l l Fused deposition modeling (FDM) l Electron beam melting l Selective laser sintering l l l l Selective heat sintering l Direct metal laser sintering l Powder bed and inkjet head printing l l l l Plaster-based 3D printing l l Laminated object manufacturing l l l l Ultrasonic consolidation l Laser metal deposition l l Dr. Samadhan P. Deshmukh, MPSTME, Mumbai 65 AM Industry - Present and future Dr. Samadhan P. Deshmukh, MPSTME, Mumbai 66 Additive manufacturing has been around for more than 30 years, the majority of growth has occurred since 2010. This lead to a large number of 3D printers entering the industry, making it significantly easier for designers to access additive manufacturing technology. Number of printers under $5000 sold globally per year - Wohlers report 2015 Dr. Samadhan P. Deshmukh, MPSTME, Mumbai 67 Additive Manufacturing AM applications As of today, AM applications have been developed in various industries AM Revenues per industry segment (2012) CONSUMER PROD./ AUTOMOTIVE MEDICAL/DENTAL ELECTRONICS 370 [EUR m] 320 [EUR m] 380 [EUR m] TOOLS/MOLDS OTHER AEROSPACE 180 [EUR m] 230 [EUR m] 330 [EUR m] Source: Wohlers Associates; Expert interviews; Roland Berger AM applications sector wise Dr. Samadhan P. Deshmukh, MPSTME, Mumbai 69 AM applications Decorative Automobile Spare Parts Archaeological Dr. Samadhan P. Deshmukh, MPSTME, Mumbai 70 Complete life cycle applications Dr. Samadhan P. Deshmukh, MPSTME, Mumbai 71 AM applications by select end markets Potential Future Industries Current Applications Applications Concept modelling and Embedding AM electronics prototyping directly on parts Structural and non structural Complex engine parts Commercial Aerospace product parts and Defense Low volume replacement parts Aircraft wing parts Other structural aircraft components Specialized parts for space On demand parts/spares in exploration space Space Structures using light-weight, Large structures directly high Strength materials created in space Dr. Samadhan P. Deshmukh, MPSTME, Mumbai 72 AM applications by select end markets Potential Future Industries Current Applications Applications PR and manufacturing of Sophisticated auto end user auto parts components Automotive Parts and assemblies for Auto components designed antique cars and race cars through crowd sourcing Quick prodcution of cars Developing organs for Prostheses and implants implants Healthcare Medical Instruments and Large scale Pharmaceutical models production Hearing aids and dental Developing human tissues implants for regenerative therapies Dr. Samadhan P. Deshmukh, MPSTME, Mumbai 73 AM applications by select end markets Potential Future Industries Current Applications Applications Co-designing and creating Rapid Prototyping with customers Creating designs and Customized living spaces testing iterations Consumer Products Growing mass Customized jewellery and customization of watches consumer products Limited product customization Dr. Samadhan P. Deshmukh, MPSTME, Mumbai 74 Prototypes for Medical Applications Dr. Samadhan P. Deshmukh, MPSTME, Mumbai 75 Medical Implants Dr. Samadhan P. Deshmukh, MPSTME, Mumbai 76 Applications of AM in Bio-printing Dr. Samadhan P. Deshmukh, MPSTME, Mumbai 77 Potential application for AM in the biomedical space. Orthopaedics Implants Dental Implants Tissue And Organ Implants: 80% of the total candidates on the organ donation waiting list are waiting for a kidney. Huge opportunity to save lives Prosthetics Skin tissue printing machine based on 3D printing technology, which enables printing of human skin tissues to be directly implanted on a human limb. Feasible to print living tissue structures to replace injured or diseased tissue in patients. Dr. Samadhan P. Deshmukh, MPSTME, Mumbai 78 Scaffolds in Tissue Engineering The developing field of tissue engineering (TE) aims to regenerate damaged tissues by combining cells from the body with highly porous scaffold biomaterials, which act as templates for tissue regeneration, to guide the growth of new tissue. Biodegradable scaffolds are preferred The engineered bladder scaffold seeded with cells Dr. Samadhan P. Deshmukh, MPSTME, Mumbai 80 3D bio-plotters A 3D-Bioplotter® machine (courtesy of EnvisionTEC GmbH). A completed mesh (left) and the sectioned view (right) (courtesy of EnvisionTEC GmbH). Dr. Samadhan P. Deshmukh, MPSTME, Mumbai 84 Example of 3D printed organs Cross section of 3D bioprinted human liver tissue using 3 cell types (courtesy of Organovo Inc.). Dr. Samadhan P. Deshmukh, MPSTME, Mumbai 87 Proven research in 3D printing in biomedical applications Winston-Salem, NC - Using a sophisticated, custom-designed 3D printer, regenerative medicine scientists at Wake Forest Baptist Medical Center, have proved that it’s feasible to print living tissue structures to replace injured or diseased tissue in patients. Reporting in Nature Biotechnology, the scientists said they printed ear, bone and muscle structures. When implanted in animals, the structures matured into functional tissue and developed a system of blood vessels. Most importantly, these early results indicate that the structures have the right size, strength and function for use in humans. Dr. Samadhan P. Deshmukh, MPSTME, Mumbai 89 Drug Delivery Whole new research opportunities in pharmaceutical research and bio-technology applications. Drug dosage forms - Personalised drug dosages Supporting delivery - Unique dosage forms Helping to research cures – Complex drug release profiles Dr. Samadhan P. Deshmukh, MPSTME, Mumbai 91 Other Applications FabCafe in the Shibuya, Tokyo offers custom-printed chocolate, that resemble a customer’s face. It’s done with 3D printing technology Alumina dental implants Dr. Samadhan P. Deshmukh, MPSTME, Mumbai 92 Food Manufacturing Dr. Samadhan P. Deshmukh, MPSTME, Mumbai 93 Home Manufacturing Customization: Bristle hardness Colour Old toothbrush Handle Style and shape etc. New toothbrush Laser scanner to input personalized data Home 3D Printer Dr. Samadhan P. Deshmukh, MPSTME, Mumbai 94 Additive Manufacturing Materials used Short introduction in AM to the technology Additive Manufacturing There are way too many Short proprietary introduction to materials the technology from the many different 3D printer vendors. Liquid Based Powder Based Solid Based Dr. Samadhan P. Deshmukh, MPSTME, Mumbai 97 Nylon, or Polyamide, is commonly used in Manufacturing Additive powder form with the sintering process or in filament form with the FDM process. It is a strong, flexible and durable plastic material Short introduction to the technology that has proved reliable for 3D printing. It is naturally white in colour but it can be coloured — pre- or post printing. This material can also be combined (in powder format) with powdered aluminium to produce another common 3D printing material for sintering Alumide. ABS is another common plastic used for 3D printing, and is widely used on the entry- level FDM 3D printers in filament form. It is a particularly strong plastic and comes in a wide range of colours. ABS can be bought in filament form from a number of non- proprietary sources, which is another reason why it is so popular. PLA is a bio-degradable plastic material that has gained traction with 3D printing for this very reason. It can be utilized in resin format for DLP/SL processes as well as in filament form for the FDM process. It is offered in a variety of colours, including transparent, which has proven to be a useful option for some applications of 3D printing. However it is not as durable or as flexible as ABS. LayWood is a specially developed Additive 3D printing material for entry- level extrusion 3D Manufacturing printers. It comes in filament form and is a wood/polymer composite (also referred to as Short introduction to the technology WPC). A growing number of metals and metal composites are used for industrial grade 3D printing. Two of the most common are aluminium and cobalt derivatives. One of the strongest and therefore most commonly used metals for 3D printing is Stainless Steel in powder form for the sintering/ melting/EBM processes. It is naturally silver, but can be plated with other materials to give a gold or bronze effect. In the last couple of years Gold and Silver have been added to the range of metal materials that can be 3D printed directly, with obvious applications across the jewellery sector. These are both very strong materials and are processed in powder form. Titanium is one of the strongest possible metal materials and has been used for 3D printing industrial applications for some time. Supplied in powder form, it can be used for the sintering/melting/ EBM processes. Bio Materials - There is a huge amount of research Additive Manufacturingbeing conducted into the potential of 3D printing bio materials for a host of medical (and other) applications. Living tissue is Short introduction to the technology being investigated at a number of leading institutions with a view to developing applications that include printing human organs for transplant, as well as external tissues for replacement body parts. Food - Experiments with extruders for 3D printing food substances has increased dramatically over the last couple of years. Chocolate is the most common (and desirable). There are also printers that work with sugar and some experiments with pasta and meat. Looking to the future, research is being undertaken, to utilize 3D printing technology to produce finely balanced whole meals. Other - Standard Objet 3D printing materials can be combined during the printing process — in various and specified concentrations to form new materials with the required properties. Up to 140 different Digital Materials can be realized from combining the existing primary materials in different ways. Concrete A test bracket printedDr. in range of different 3D printed materials Samadhan P. Deshmukh, MPSTME, Mumbai 101 10 9 8 7 6 5 4 3 2 1 Mumbai Dr. Samadhan P. Deshmukh, MPSTME, 102 AM Process Chain Dr. Samadhan P. Deshmukh, MPSTME, Mumbai 103 3D Printing Process Source: How 3D Printing Works in 4 steps, my3dconcepts, acc 6.6.20 Dr. Samadhan P. Deshmukh, MPSTME, Mumbai 104 Generic AM process Step 1: CAD Step 2: Conversion to STL Step 3: Transfer to AM Machine and STL File Manipulation Step 4: Machine Setup Step 5: Build Step 6: Removal Step 7: Post-processing Step 8: Application Dr. Samadhan P. Deshmukh, MPSTME, Mumbai 105 Dr. Samadhan P. Deshmukh, MPSTME, Mumbai 106 Dr. Samadhan P. Deshmukh, MPSTME, Mumbai 107 A CAD model on the left converted into STL format on the right Dr. Samadhan P. Deshmukh, MPSTME, Mumbai 108 AM file formats Dr. Samadhan P. Deshmukh, MPSTME, Mumbai 109 CAD and file formats for AM STL (Standard Triangle Language) - the industry standard file type for 3D Printing. Uses a series of triangles to represent the surfaces of a solid model. Modern CAD (Computer Aided Design) software allow you to export their native file format into STL. 3D model then converted into machine language (G-code) through a process called “slicing” and is ready to print. Dr. Samadhan P. Deshmukh, MPSTME, Mumbai 110 All CAD software have their own way to export STL files. Dr. Samadhan P. Deshmukh, MPSTME, Mumbai 111 Dr. Samadhan P. Deshmukh, MPSTME, Mumbai 112 Dr. Samadhan P. Deshmukh, MPSTME, Mumbai 113 Various File Formats STL (Standard Tessellation Language) 3MF (3D Manufacturing Format) AMF (Additive Manufacturing File Format) PLY (Polygon File Format) VRML (Virtual Reality Modelling Language) SLC (StereoLithography Contour) file format CLI (Common Layer Interface) file format RPI (Rapid Prototyping Interface) file format LEAF or Layer Exchange ASCII Format Dr. Samadhan P. Deshmukh, MPSTME, Mumbai 114 STL (file format) STL (STereoLithography) Standard Triangle Language Standard Tessellation Language Dr. Samadhan P. Deshmukh, MPSTME, Mumbai 115 STL STL (STereoLithography) file, as the de facto standard, has been used in many, if not all, rapid prototyping systems. STL file, conceived by the 3D Systems, USA, created from the CAD database via an interface on the CAD system. File consists of an unordered list of triangular facets representing the outside skin of an object. Two formats to the STL file - ASCII format and binary format. Size of the ASCII STL file larger than that of the binary format but is human readable. Dr. Samadhan P. Deshmukh, MPSTME, Mumbai 116 Dr. Samadhan P. Deshmukh, MPSTME, Mumbai 117 Convention for storing each triangle The triangulation to be made such that there are no vertices in the middle of an edge or a face. Consistent with the vertex-to-vertex rule WRONG triangulation for STL Dr. Samadhan P. Deshmukh, MPSTME, Mumbai 118 STL Triangular facets described by a set of X, Y and Z coordinates for each of the three vertices and a unit normal vector with X, Y and Z to indicate which side of facet is an object. Several advantages of the STL file - Provides a simple method of representing 3D CAD data. Already a de facto standard and has been used by most CAD systems and rapid prototyping systems. Provide small & accurate files for data transfer for certain shapes. Dr. Samadhan P. Deshmukh, MPSTME, Mumbai 119 Disadvantages of the STL File Format STL files limited to describing only the surface geometry of a three- dimensional object. No representation of color, texture, material, substructure, or other attributes typically found in other CAD model formats. Dr. Samadhan P. Deshmukh, MPSTME, Mumbai 120 3MF The 3D Manufacturing Format (3MF) - Allows design applications to send 3D models to a mix of other applications, platforms, services Contains a 3D model, material, and property information compressed with Zip compression. 3MF files may also store a print ticket, thumbnail image, and one or more digital signatures. 3MF specification allows companies to focus on innovation, rather than on basic interoperability issues, and it is engineered to avoid the problems associated with other 3D file formats Dr. Samadhan P. Deshmukh, MPSTME, Mumbai 121 3MF File format created by Microsoft, an XML-based data format. Launched in 2015 to make 3D printing easier with a Windows 10 operating system. With.3MF, all model information contained in a single archive and it is extensible. Unlike.STL,.3MF carries complete model information including mesh, textures, materials and colours. Because it's open-source and powerful, 3MF gets a lot of love in the 3D printing world. It's most widely used in the commercial and industrial sectors. Dr. Samadhan P. Deshmukh, MPSTME, Mumbai 122 3MF Complete: Containing all of the necessary model, material and property information in a single archive Human Readable: Using common structures such as OPC, ZIP, and XML to ease development Simple: A short, clear specification, making development easy and validation fast Extensible: Leveraging XML namespaces allow for both public and private extensions while maintaining compatibility Unambiguous: Clear language and conformance tests ensure a file is always consistent from digital to physical Free: Access to and implementation of the 3MF specification is and will always be free of royalties, patents and licensing Dr. Samadhan P. Deshmukh, MPSTME, Mumbai 123 AMF AMF (Additive Manufacturing File Format) - A 3D file format used for storing and describing objects to be processed through Additive Manufacturing. Introduced as the ASTM standard file format for 3D printing in 2011 An XML-based format designed to contain native support for file specifications such as geometry, scale, color, material, lattices, duplicates, and orientation. Introduced as an alternative to the STL file format to address many of the pitfalls of the current popular file format. STL files introduce errors such as leaks and inconsistences, and also does not support color, material choice, or orientation Dr. Samadhan P. Deshmukh, MPSTME, Mumbai 124 Dr. Samadhan P. Deshmukh, MPSTME, Mumbai 125 VRML VRML (“vermal”,.WRL file extension), or Virtual Reality Modelling Language, is a newer file type than.STL. Can hold a single UV colour map. Ideal for 3D printers with two extruders and for models that consist of more than one colour. Not as widely used as.STL, contains colour data means it definitely has its place. Used for interactive 3D objects and vector graphics. Slicing software like Cura can use VRML files but not all programs support it. Dr. Samadhan P. Deshmukh, MPSTME, Mumbai 126 PLY PLY (Polygon File Format) files are generated by 3D scanners. Include a description of one object as a collection of vertices, faces and other elements. Information can include colour, transparency, surface and texture details and much more. When 3D printing, you convert a PLY file into the format accepted by the 3D printer. PLY was first developed for 3D surface scanners and it is still used by some scanners today. It allows surface detail and RGB colour instructions. Dr. Samadhan P. Deshmukh, MPSTME, Mumbai 127 Part orientation Dr. Samadhan P. Deshmukh, MPSTME, Mumbai 128 Dr. Samadhan P. Deshmukh, MPSTME, Mumbai 129 Importance of part orientation Part accuracy - By orientating the part in different directions, there is a significant difference in the print quality. Build time - Orientation can also have a significant impact on print time Part strength - Some 3D printing build parts that have inherently anisotropic properties, meaning they are much stronger in the XY direction than the Z direction. Support Structures - Support material adds extra time and cost to a 3D print. Surface finish - the top or upward facing surfaces of a 3D printed part will have the best surface finish Dr. Samadhan P. Deshmukh, MPSTME, Mumbai 130 Dr. Samadhan P. Deshmukh, MPSTME, Mumbai 131 Dr. Samadhan P. Deshmukh, MPSTME, Mumbai 132 Two identical cylinders printed at the same layer height in different orientations (left: vertically, right: horizontally) Dr. Samadhan P. Deshmukh, MPSTME, Mumbai 133 Why is layer height important? Layer height - Important design parameter that impacts the printing time, cost, visual appearance and physical properties of a printed part. Often the visual difference between parts printed at 100 μm and 200 μm is very small. The part at 100 μm will take twice as long to print (the 3D printer will have to trace twice as many cross sections) and this will have an impact on the cost. Dr. Samadhan P. Deshmukh, MPSTME, Mumbai 134 3 FDM parts printed at 50, 200 and 300 microns (left to right). Dr. Samadhan P. Deshmukh, MPSTME, Mumbai 135 A macro view of the FDM prints (50, 200 and 300 microns from left to right) shown at P.the Dr. Samadhan same Deshmukh, scale MPSTME, for comparison. Mumbai 136 Dr. Samadhan P. Deshmukh, MPSTME, Mumbai 137 Rules of Thumb Orientate cylindrical features vertically for a smoother surface finish. Consider the direction of the loading when choosing part orientation of a functional part. Part orientation is most important for FDM and SLA/DLP 3D printing processes. Dr. Samadhan P. Deshmukh, MPSTME, Mumbai 138 Support generation Dr. Samadhan P. Deshmukh, MPSTME, Mumbai 139 FDM printers can’t deposit molten thermoplastic on thin air. Certain part geometries require support structures, usually printed in the same material as the parts themselves. Removing support structure materials can be difficult, often far easier to design parts in such a way that minimizes the need for support structures. Support materials that dissolve in liquid available, but generally used them in tandem with higher-end FDM 3D printers. Using dissolvable supports increase the overall cost of a print. Dr. Samadhan P. Deshmukh, MPSTME, Mumbai 140 Apart from external support structures for overhanging features, internal support structures also play significant roles in building parts by means of filling internal space with support structures, thus reducing the material and build time remarkably. In order to avoid difficulties in handling three-dimensional processing of STL model, a support generation approach based on sliced layers is proposed to generate both internal and external supports for AM. In the external support structures generation, the general methodology is improved by identifying external support areas correctly and reasonably. Dr. Samadhan P. Deshmukh, MPSTME, Mumbai 141 The support structure (in blue) generated by Cura software Dr. Samadhan P. Deshmukh, MPSTME, Mumbai 142 Depending on the degree of overhang, FDM print might need support Dr. Samadhan P. Deshmukh, MPSTME, Mumbai 143 A visual illustration of support structures needed for printing a Y, H & T with FDM Y, H, and T printed with FDM with support Dr. Samadhan P. Deshmukh, MPSTME, Mumbai 144 SLA printed part showing some marks An SLA print with support structure where support was located Dr. Samadhan P. Deshmukh, MPSTME, Mumbai 145 FFF bracket printed in PLA (Grey) showcasing dissolved PVA support (White) Dr. Samadhan P. Deshmukh, MPSTME, Mumbai 146 Model slicing Dr. Samadhan P. Deshmukh, MPSTME, Mumbai 147 What is Slicing? Act of converting a 3D model into a set of instructions for the 3D printers is called Slicing. ‘Slices’ the 3D model into thin layers, and further determine how each layer should be printed (the tool path) to get minimum time, best strength, etc. A slicer software takes a 3D CAD model which is generally an STL format file and converts it into a g-code that gives commands to the printer. Dr. Samadhan P. Deshmukh, MPSTME, Mumbai 148 Slicing - foundational operation of 3D printing. Requires computing the intersection curves of models and slicing planes. Operation is time-consuming, and is a key factor that affects printing quality. Most slicing algorithms work on standard tessellation language (STL) models. The data in the STL file format is a discretized form of the 3D models, which contain discretization errors. Many studies considered a slicing algorithm on the original data of the 3D models. Dr. Samadhan P. Deshmukh, MPSTME, Mumbai 149 Following are the three major types of settings that can be controlled in a slicer software - Print Settings: layer heights, shells, infill per cent, and speed Filament Settings: filament diameter, extrusion multiplier, the temperature of the extruder, and print bed. Printer settings: nozzle diameter, print bed shape (L x W), and Z offset. Dr. Samadhan P. Deshmukh, MPSTME, Mumbai 150 Contour generation Dr. Samadhan P. Deshmukh, MPSTME, Mumbai 151 Sample Algorithm to read and analyze Gcode (Source: ScienceDirect) Dr. Samadhan P. Deshmukh, MPSTME, Mumbai 152 Machine set up Dr. Samadhan P. Deshmukh, MPSTME, Mumbai 153 Orientation Layer Height (Object resolution) Infill density Dr. Samadhan P. Deshmukh, MPSTME, Mumbai 154 Dr. Samadhan P. Deshmukh, MPSTME, Mumbai 155 Skirt (as shown in fig ‘a’): It is a single outline surrounding the part without touching the actual 3D object. Brim (as shown in fig ‘b’): It is a layer printed along the print bed that touches the actual 3D object. Raft (as shown in fig ‘c’): A series of layers are printed before the model is printed. It serves as a detachable base for the 3D object. Dr. Samadhan P. Deshmukh, MPSTME, Mumbai 156 Dr. Samadhan P. Deshmukh, MPSTME, Mumbai 157 Build file preparation Dr. Samadhan P. Deshmukh, MPSTME, Mumbai 158 Parts of a slicer software Dr. Samadhan P. Deshmukh, MPSTME, Mumbai 159 Printing Materials and their recommended temperatures Dr. Samadhan P. Deshmukh, MPSTME, Mumbai 160 Dr. Samadhan P. Deshmukh, MPSTME, Mumbai 161 AM Advantages Dr. Samadhan P. Deshmukh, MPSTME, Mumbai 162 AM Advantages Elimination of design constraints Allow parts to be produced with complex geometry with no additional costs related to complexity Build speed; reduction of lead time Flexibility in design No expensive tooling requirements Dimensional accuracy Wide range of materials (polymers, metals, ceramics) Well suited to the manufacture of high value replacement, repair parts Green manufacturing, clean, minimal waste Dr. Samadhan P. Deshmukh, MPSTME, Mumbai 163 Additive Manufacturing Design complexity and freedom: Short introduction to the technology The advent of 3D printing has seen a proliferation of products (designed in digital environments), which involve levels of complexity that simply could not be produced physically in any other way. While this advantage has been taken up by designers and artists to impressive visual effect, it has also made a significant impact on industrial applications, whereby applications are being developed to materialize complex components that are proving to be both lighter and stronger than their predecessors. Speed: You can create complex parts within hours , with limited human resources. Only machine operator is needed for loading the data and the powder material, start the process and finally for the finishing. During the manufacturing process no operator is needed. Customisation 3D printing processes allow for mass customisation — the ability to personalize products according to individual needs and requirements. Even within the same build chamber, the nature of 3D printing means that numerous products can be manufactured at the same time according to the end-users requirements at no additional process cost. Additive Manufacturing Tool-less Short introduction to the technology For industrial manufacturing, one of the most cost-, time- and labour-intensive stages of the product development process is the production of the tools. For low to medium volume applications, industrial 3D printing — or additive manufacturing — can eliminate the need for tool production and, therefore, the costs, lead times and labour associated with it. This is an extremely attractive proposition, that an increasing number or manufacturers are taking advantage of. Furthermore, because of the complexity advantages stated above, products and components can be designed specifically to avoid assembly requirements with intricate geometry and complex features further eliminating the labour and costs associated with assembly processes. Extreme Lightweight design AM enable weight reduction via topological optimization No storage cost Since 3D printers can “print” products as and when needed, and does not cost more than mass manufacturing, no expense on storage of goods is required. Increased employment opportunities Widespread use of 3D printing technology will increase the demand for designers and technicians to operate 3D printers and create blueprints for products. Additive Manufacturing Sustainable / Environmentally Friendly Short introduction to the technology 3D printing is also emerging as an energy-efficient technology that can provide environmental efficiencies in terms of both the manufacturing process itself, utilising up to 90% of standard materials, and, therefore, creating less waste, but also throughout an additively manufactured product’s operating life, by way of lighter and stronger design that imposes a reduced carbon footprint compared with traditionally manufactured products. Fairphone 3D printed accessories made on demand from recycled wood fiber material A custom functional bracket 3D printed with SLS nylon. Dr. Samadhan P. Deshmukh, MPSTME, Mumbai 167 Single step manufacture The 3D printing process (red) compared to the traditional manufacturing process (black). Dr. Samadhan P. Deshmukh, MPSTME, Mumbai 168 Complex and intricate designs can easily be produced by some 3D printing technologies Dr. Samadhan P. Deshmukh, MPSTME, Mumbai 169 Customizable 3D printed headphones designed by Print+ Dr. Samadhan P. Deshmukh, MPSTME, Mumbai 170 AM Limitations Part size Production series: Generally suitable for unitary or small series and is not relevant for mass production. For small sized parts, series up to 25000 parts/year are already possible. Dr. Samadhan P. Deshmukh, MPSTME, Mumbai 171 Additive Manufacturing Questionable Accuracy Short introduction to the technology 3D printing is primarily a prototyping technology, meaning that parts created via the technology are mainly test parts. As with any viable test part, the dimensions have to be precise in order for engineers to get an accurate read on whether or not a part is feasible. While 3D printers have made advances in accuracy in recent years, many of the plastic materials still come with an accuracy disclaimer. For instance, many materials print to either +/- 0.1 mm in accuracy, meaning there is room for error. Support material removal When production volumes are small, the removal of support material is usually not a big issue. When the volumes are much higher, it becomes an important consideration. Support material that is physically attached is of most concern. Limitations of raw material At present, 3D printers can work with approximately 100 different raw materials. This is insignificant when compared with the enormous range of raw materials used in traditional manufacturing. More research is required to devise methods to enable 3D printed products to be more durable and robust. Material cost: Today, the cost of most materials for additive systems ( Powder ) is slightly greater than that of those used for traditional manufacturing. Additive Manufacturing Considerable effort required for application design and for setting process parameters Short introduction to the technology Complex set of around 180 material, process and other parameters and specific design required to fully profit from the technology Material properties: A limited choice of materials is available. Actually, materials and there properties (e.g., tensile property, tensile strength, yield strength, and fatigue) have not been fully characterized. Also, in terms of surface quality, even the best RM processes need perhaps secondary machining and polishing to reach acceptable tolerance and surface finish. Intellectual property issues The ease with which replicas can be created using 3D technology raises issues over intellectual property rights. The availability of blueprints online free of cost may change with for-profit organizations wanting to generate profits from this new technology. Limitations of size 3D printing technology is currently limited by size constraints. Very large objects are still not feasible when built using 3D printers. Additive Manufacturing Cost of printers Short introduction to the technology The cost of buying a 3D printer still does not make its purchase by the average householder feasible. Also, different 3D printers are required in order to print different types of objects. Also, printers that can manufacture in colour are costlier than those that print monochrome objects. Unchecked production of dangerous items Liberator, the world’s first 3D printed functional gun, showed how easy it was to produce one’s own weapons, provided one had access to the design and a 3D printer. Governments will need to devise ways and means to check this dangerous tendency. Things learnt… Dr. Samadhan P. Deshmukh, MPSTME, Mumbai 175 References Dr. Samadhan P. Deshmukh, MPSTME, Mumbai 176 References Videos - 1. https://www.youtube.com/watch?v=EHvO-MlzAIM 2. https://www.youtube.com/watch?v=t4S0mKjXtT4&t=81s 3. https://www.youtube.com/watch?v=lcj5xhTux9M&t=56s Redwood, B., Schffer, F., & Garret, B. (2017). The 3D printing handbook: technologies, design and applications. 3D Hubs. Mueller, B. (2012). Additive manufacturing technologies–Rapid prototyping to direct digital manufacturing. Assembly Automation. Dr. Samadhan P. Deshmukh, MPSTME, Mumbai 177 Any Questions? Dr. Samadhan P. Deshmukh, MPSTME, Mumbai 178 Thank You Dr. Samadhan P. Deshmukh, MPSTME, Mumbai 179