DM308 Production Techniques 2 Lecture 7 PDF
Document Details
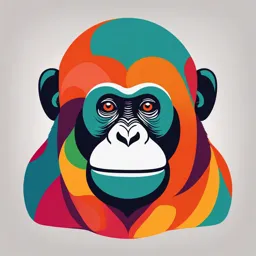
Uploaded by SafeDiscernment
University of Strathclyde
Dr. Vassili Vorontsov
Tags
Summary
This document is a lecture on the metallurgical processing of high-temperature superalloys, including jet engine operation and related topics. It covers various aspects of materials, components, microstructure, and coatings used in these applications. The lecture was given by Dr. Vassili Vorontsov of the University of Strathclyde.
Full Transcript
DM308 Production Techniques 2 Lecture 7 – Metallurgical processing of high-temperature superalloys Dr. Vassili Vorontsov Department of Design, Manufacture and Engineering management, Faculty of Engineering, University of Strathclyde [email protected] High-temperature superalloys Jet eng...
DM308 Production Techniques 2 Lecture 7 – Metallurgical processing of high-temperature superalloys Dr. Vassili Vorontsov Department of Design, Manufacture and Engineering management, Faculty of Engineering, University of Strathclyde [email protected] High-temperature superalloys Jet engine operation Suck→ Squeeze→ Bang→ Blow Combustion Chamber Exhaust Nozzle Compressor mVaircraft mVjet Shaft Turbine Faster, hotter, cheaper A 200°C rise in turbine entry temperature (TET) gives a 5% saving in fuel burn. A 1% decrease in fuel burn for a Boeing 777 reduces operating costs by about £1,000,000 over a 15 year period. If the weight of an aero engine can be reduced by 50kg this gives a 0.5% saving in fuel burn. Weight ↓ Temperature ↑ Fuel Efficiency ↑ Cost ↓ Life ↑ Evolution of turbine entry temperature 1728K (1455°C) – Melting point of Ni There is a persisting drive to increase the turbine entry temperature (TET) of aero engines. This is the temperature of the gas entering the first stage of the high-pressure (HP) turbine as it leaves the combustion chamber. The Carnot cycle dictates that increasing in the TET would increase the thermal efficiency of the engine, which is the ratio of the useful work to the work of combustion. The TET of any engine is always going to be limited by the hightemperature capability of the materials used to manufacture the turbine components. While work is always ongoing to develop new materials that can withstand greater operating temperatures, other technologies have allowed the TET to exceed the melting points of the superalloys that are presently used. Intricate networks of cooling channels are machined into the interior of HP turbine blades, ensuring that their temperature is within the limits of the material. The HP turbine components are also protected by ceramic thermal barrier coatings (TBCs). Materials in a jet engine Below we see the typical distribution of materials in a modern engine: Nickel base superalloys Superalloy components The major superalloy components and key material requirements: Turbine Blades Turbine Discs Creep resistance Oxidation resistance Castability Coatability Guide Vanes High strength @ temp. Creep resistance Fatigue resistance Oxidation resistance Corrosion resistance Processability Combustors Thermal stress resistance Oxidation resistance Castability Coatability LCF fatigue resistance Oxidation resistance Weldability Ni-Al binary system The Ni-Al binary system is the basis of nickel base superalloys: ’ Microstructure of superalloys A typical superalloy microstructure comprises a g phase matrix populated by numerous g’ precipitates, which provide strengthening (precipitation hardening). ’ ’ Crystal structure of g and g’ phases The g and g’ phases both have a face-centred cubic crystal structure, but g’ has an ordered structure. This gives rise to order strengthening due to the formation of antiphase boundary defects when dislocations glide though the g’ precipitates during plastic deformation. g Al Al Ni Al Al Ni Ni Ni Ni Al Al Ni Al ≈ 8-22 at.% Al in Ni chemically disordered Al Ni3Al chemically ordered Properties of the g’ phase The special properties of the g’ phase constitute a major contribution to the high-temperature strength of superalloys: 1. Ductile compared to most intermetallics. 2. Strength increases with temperature (Yield Stress Anomaly). 3. Precipitates from the phase via short-range ordering. 4. Has a low lattice parameter mismatch with the parent phase and forms coherent interfaces with it. ’ Strengthening in superalloys Superalloys exhibit a combination of beneficial strengthening mechanisms that result in outstanding high-temperature strength: Solution strengthening Order strengthening Strength of Superalloys Precipitate strengthening Coherency strengthening PX vs SX superalloys Superalloy components generally fall into two categories singlecrystals (SX) and polycrystalline (PX): Turbine Blades and Guide Vanes Small Cast to near net shape Single crystals High volume fraction of ’ Expensive (due to element choice) Turbine Discs and Combustors Large Wrought into shape Polycrystalline (PX) Smaller volume fraction of ’ Less expensive Structure of a turbine blade Single crystal turbine blades have complex geometries with elaborate networks of internal cooling channels and holes. On the outside, thermal barrier coatings act as heat shields protecting the base metal from the extreme temperatures. Production of such sophisticated components requires a combination of state-of-the-art manufacturing techniques. Cooling air Cooling air Single pass Multi-pass Thermal Barrier Coating Investment casting Investment casting using the “lost wax” process is used to manufacture the turbine blades with their intricate inner structure. It allows complex geometries to be cast and can produce a fine surface finish. Investment casting of turbine blades A wax model of the blade known as a template is first prepared. Inside the template is a ceramic core that has the shape of the cooling channels. Multiple templates are joined using wax runners and dipped into ceramic slurry. The wax is burned out in a furnace to leave behind a fired ceramic mould. Molten alloy is then poured into the mould and allowed to solidify. The ceramic ores are removed using chemical or vibrational methods. Wax template/model Finished investment mould ceramic core Finished castings Investment casting of turbine blades Cutaway of investment mould showing intricate ceramic core that will form the cooling channels. Automated coating of wax template assembly in ceramic slurry. Why cast single crystal blades? Lost wax investment casting is only part of blade manufacture. Conventional casting only produces polycrystalline blades with fine and uniform grains. At high-temperatures the grains can slide during creep. The creep life can be improved significantly using directional solidification which produces oblong columnar grains and reducing overall grain boundary area. Eliminating grain boundaries altogether in single crystal castings gives the longest creep life. Why cast single crystal blades? Below we see a grain structure comparison between conventionally cast, directionally solidified and single crystal turbine blade castings. The directional solidification process used to produce the latter two is shown on the following slide. conventionally cast directionally solidified single crystal Directional solidification Water Melt chamber separator valve Crucible and charge Melting chamber Water cooled induction melting coil Vacuum Graphite heating element Furnace chamber Mould Mould withdrawal chamber Water cooled chill and ram Mould chamber separator valve Water Growing single crystals The high thermal gradient created by the directional solidification process forces the liquid to solidify as tree-like structures called dendrites. Dendrites aligned parallel to the solidification direction grow faster than the rest. As they grow, they branch out to form secondary and tertiary arms/branches which block the growth of slower misaligned dendrites. Single crystal A spiral grain selector helps accelerate the elimination process by continually changing the growth direction. Eventually only the dendrites of a single crystal orientation should remain. Grain selector Poly crystal Possible casting defects Though directional solidification is a state-of-the-art process, it is still not perfect and a number of casting defects may be possible that would result in a blade being scrapped: Secondary Grains Freckles Low-angle Grain Boundaries Recrystallised Grains Ceramic Core ”Kissout” Slivers Bicrystal (from starter) Scrap rates Below we see that up to a third of all blade castings have to be scrapped and recycled due to the presence of casting defects: Second generation alloys (up to 3wt.% Re) Third generation alloys (up to 6wt.% Re) Heat treatment of turbine blades The blades are then subjected to a series of heat treatments to obtain the optimum microstructure. Solution treatment dissolves all g’ precipitates and homogenises the composition. Ageing heat treatments are used to grow the desired distribution of g’ precipitates to obtain optimum creep srength. Superalloy CMSX-4 Temperature Solution heat treatment ≈ 1320°C / 16 hours Primary ageing treatment 1080°C / 4 hours Secondary ageing treatment 870°C / 16 hours Time Post-casting operations The heat-treated blades still have to undergo a number of further finishing and quality control procedures: 1 Machine blade to shape and perform NDT 2 Apply bond coat 3 Deposit TBC 4 Laser drill effusion (cooling) holes 5 Heat treat to optimise microstructure 6 Re-Perform NDT Neutron radiograph of turbine blade showing retained fragment of ceramic core. Superalloys in harsh environments Some superalloys operate in very harsh environments that may accelerate high-temperature oxidation and corrosion. Therefore, they must be adequately protected to prevent premature failure. Component failure Below are examples of turbine blades that failed due to hightemperature oxidation and/or corrosion. Coatings can be used to help protect the blades from these undesirable degradation phenomena. Forming protective oxides Oxide-metal volume ratio is one way of judging whether an oxide will be protective. Alumina and chromia are good candidates because oxygen diffusivity in these oxides is low. Chromia volatilises at higher temperatures, but provides good corrosion resistance. Types of turbine blade coatings Thermal barrier coatings Overlay coatings Diffusion coatings Diffusion coatings Al-rich b phase Interdiffusion zone Al-rich d phase Overlay coatings Type I MCrAlX Ni or Co Reactive rare earth metal Y, Zr, Hf Type II NiCrAl Type III Plasma spraying Powder Cathode Plasma gas Anode Plasma spraying of TBC Splat morphology Electron beam PVD Vacuum Electron gun Vapour stream Part manipulator Ion sources Ingot feeders Thermal barrier coatings “Herring bone” Produced by EB-PVD Produced by plasma spraying Diffusioncoated or EBPVD bond coat Plasma-sprayed bond coat Role of coatings Coating failures Diffusion coatings – microstructutal degradation (e.g. voids+brittle TCPs) Overlay coatings – fatigue cracking TBCs – delamination Superalloys for disc applications This failure was not a fault in the disc material, but an oil mist fire resulting from a defective oil pipe. The disc was operating at a higher temperature than what it was intended for. Turbine discs are ~20% of engine weight. Want to make them light, but very strong. Very high kinetic energy when spinning. Failure very undesirable. It is important to make correct operational lifetime predictions. Importance of making strong discs Processing routes for disc manufacture There are two processing routes that are used for the manufacture of turbine discs: Cast and wrought Cheaper method Only suitable for alloys with lower g’ content Only the core of the billet has desired microstructure. Outer material has to be machined away. (wasteful) Powder metallurgy More expensive Suitable for alloys with higher g’ content Precise grain size control Uniform microstructure Cast-and-wrought processing route Producing high-purity alloys Given the critical nature of discs as engine components, it is paramount that the alloys used to manufacture them are of the highest purity. The VIM→ESR→VAR method is widely used to produce high quality metal ingots of superalloys, titanium alloys and high grade steels intended for high performance applications. Vacuum induction melting Vaccum induction melting (VIM) is used to produce the primary alloy ingots from raw element stock. In VIM the alloy feedstock is melted inside a crucible surrounded by an induction coil. The high-power alternating current in the coil induces eddy currents in the metals, which cause resistive heating that eventually melts them. Double-chamber VIM Large-scale industrial VIM VIM crucible VIM refining In addition to melting, VIM can also be used to help refine allows. Addition of carbon to the melt allows the removal of oxygen and other dissolved gases by the formation of carbon monoxide CO bubbles. Eddy currents help transport the bubbles through the melt and towards the surface where they are degassed. Due to the low pressure environment of a vacuum, some undesirable trace elements are also removed by evaporation and degassing. Summary of post VIM operations VIM is a staple method for producing high-purity primary ingots and is a starting point for a number of subsequent industrial processes. Electro slag refining Electro slag refining (ESR) is a process for further purifying alloy ingots produced by VIM. The as-cast VIM ingot is used as a consumable electrode connected to a high-power AC supply. It is fed into a molten engineering slag/flux which is heated by the current and floats on top of the molten alloy below. The solid VIM ingot melts and the alloy droplets sink through the slag to the melt pool below. The alloy is cleansed of impurities which either react with the slag as the droplets sink through it, or float to the top of the melt pool to join the slag pool. ESR Industrial ESR furnace Multiple ingots undergoing ESR Post ESR ingot Note the dark slag “hat” at the very top. Vacuum arc remelting Vacuum arc remelting (VAR) is another secondary melting process that is used to further purify high-value alloy ingots. The ingot is connected to a high power DC supply as a sacrificial electrode. Lowering the ingot creates a spark gap and the resulting electric arc melts it and molten alloy droplets fall into the melt pool below. VAR is a slow and expensive process. Many high-performance alloys may be VARed two to three times over to achieve highest purity for mission-critical applications. Advantages of VAR Tight control of solidification rate High degree of miucrostructural control Greater homogeneity Vacuum helps remove dissolved gases Industrial VAR furnaces Vacuum helps remove more volatile impurities like carbon and sulphur No centreline porosity Processing of metals that cannot be melted in open air furnaces such as titanium Finished VAR ingot Ingot to billet conversion After the VIM+ESR+VAR stages the ingots are annealed in a furnace at high temperature to ensure that they are chemically homogeneous. After annealing, the ingots must be converted into forged billets to reduce their diameter and to reduce the overall grain size so as to improve the strength. The ingots are subjected to cogging/upsetting whereby they are incrementally rotated in an open die forge to reduce their diameter. Open die upsetting and simulation The process is repeated several times until the desired reduction and microstructure are achieved. Quad-die cogging Powder metallurgy route Gas atomisation VIM Remelt and atomise Hot isostatic press Sieve Can Degas and seal OR HIP Extrude Forge (Isothermally) Isothermal forging Advantages: Better control of recrystallisation and grain growth than hotforging using cold dies. Near net shape manufacture (Lower material use, better die filling.) Problems: Requires a vacuum and molybdenum dies Low output rate Expensive Dual microstructure treatment Dual microstructure treatment Fatigue in turbine discs Slip Bands 12ppm Boron 29ppm Boron Lifing turbine discs Spin testing of discs is very expensive and destroys the disc. Mechanical testing of coupons does not reproduce the real stress state with sufficient accuracy and a great number of test specimens is required. This determines the failure probability distribution used to life discs. Life predictions have to be made theoretically based on the disc geometry, material properties, and existing knowledge of failures. NDT is also performed so that existing cracks are taken into account. Summary Superalloys are the premier high-temperature material for structural applications such as manufacture of aero engines. Superalloys are based on the nickel-aluminium system and make use of a range of strengthening mechanisms to achieve their outstanding strength and creep resistance at high temperatures. The alloys are used only in the hottest sections of the gas turbines due to the high density of nickel. Lighter materials are favoured elsewhere. Components that see the highest temperatures - blades and vanes are investment cast as single crystals using directional solidification. Larger components like discs and combustors are polycrystalline because they need high strength and fatigue resistance. Discs are either cast-and-wrought or produced by powder metallurgy. VIM+ESR+VAR are very important for purifying high-performance alloys. Coatings are of paramount importance for turbine blades and vanes to protect from oxidation, corrosion and extreme temperatures – diffusion coating, spray coatings and TBCs.