COSH 413 - Construction Occupational Safety and Health Module 1 - Introduction to OSH Standards, 2023 PDF
Document Details
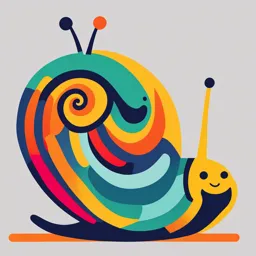
Uploaded by BrandNewChrysocolla
Don Honorio Ventura State University
Tags
Related
- COSH 413 - Construction Occupational Safety and Health - Module 1 PDF
- Chapter 1: Introduction to OSH Standard, Legislation, and D.O. No. 13 PDF
- Module 1 - Introduction to COSH PDF
- Occupational Safety and Health (OSH) in the Philippines PDF
- OHS Standards Module 4 PDF
- Basic Occupational Safety and Health PDF
Summary
This document is a module from Don Honorio Ventura State University, Philippines, on Construction Occupational Safety and Health. It introduces OSH standards, legislation, and department order 13 of the Department of Labor and Employment (DOLE).
Full Transcript
Republic of the Philippines DON HONORIO VENTURA STATE UNIVERSITY Cabambangan, Villa de Bacolor, Pampanga COLLEGE OF ENGINEERING AND ARCHITECTURE Department of Civil Engineering A. Course Code / Title : COSH 413 – Construction Occupational Safety and Health B. Module Number : Module 1 – Introdu...
Republic of the Philippines DON HONORIO VENTURA STATE UNIVERSITY Cabambangan, Villa de Bacolor, Pampanga COLLEGE OF ENGINEERING AND ARCHITECTURE Department of Civil Engineering A. Course Code / Title : COSH 413 – Construction Occupational Safety and Health B. Module Number : Module 1 – Introduction to OSH Standard, Legislation, and DO no. 13 C. Time Frame : Last Week of August to First Week of September 2023 (3 hours) D. Description : This module describes the OSH Standard, Legislation and the Department Order 13 of DOLE E. Objectives : At the end of this module, the learner should be able to: 1. Basic knowledge about the legislation, agencies related to OSH 2. Appreciation of the importance of OSH standards in construction industry 3. Knowledge in the guidelines governing OSH in construction industry F. Contents: OSH Legislation, Administration and Enforcement VISION & MISSION ⚫ Attainment of full, decent, and productive employment for every Filipino worker. ⚫ Promote gainful employment opportunities, develop human resources, protect workers and promote their welfare and maintain industrial peace. There are eleven (11) agencies and six (6) bureaus that are attached to the DOLE, and they are: ⚫ Employees Compensation Commission ⚫ Institute for Labor Studies ⚫ Maritime Training Council ⚫ National Conciliation and Mediation Board ⚫ National Labor Relations Commission ⚫ National Maritime Polytechnic ⚫ National Wages and Productivity Commission ⚫ Occupational Safety and Health Center ⚫ Overseas Workers Welfare Administration ⚫ Philippine Overseas Employment Administration ⚫ Technical Education and Skills Development Authority 6 BUREAUS 1. Labor and Employment Statistics 2. Labor Relations 3. Local Employment 4. Rural Workers 5. Women and Young Workers 6. Labor Working Conditions What are the Occupational Safety and Health Standards? OSH Standards are mandatory rules and standards set and enforced to eliminate or reduce occupational safety and health hazards in the workplace. Occupational health and safety is a cross-disciplinary area concerned with protecting the safety, health and welfare of people engaged in work or employment. The goal of all occupational health and safety programs is to foster a safe work environment. As a secondary effect, it may also protect co-workers, family members, employers, customers, suppliers, nearby communities, and other members of the public who are impacted by the workplace environment. It may involve interactions among many subject areas, including occupational medicine, occupational (or industrial) hygiene, public health, safety engineering, chemistry, health physics, ergonomics, toxicology, epidemiology, environmental health, industrial relations, public policy, industrial sociology, medical sociology, social law, labor law and occupational health psychology. The OSH Standards are mandatory rules on occupational safety and health promulgated pursuant to Article 162, Book IV of the Labor Code of the Philippines, P.D. 442. BOOK FOUR HEALTH, SAFETY AND SOCIAL WELFARE BENEFITS Title I MEDICAL, DENTAL AND OCCUPATIONAL SAFETY Chapter II OCCUPATIONAL HEALTH AND SAFETY Art. 162. Safety and health standards. The Secretary of Labor and Employment shall, by appropriate orders, set and enforce mandatory occupational safety and health standards to eliminate or reduce occupational safety and health hazards in all workplaces and institute new, and update existing, programs to ensure safe and healthful working conditions in all places of employment. Art. 163. Research. It shall be the responsibility of the Department of Labor and Employment to conduct continuing studies and research to develop innovative methods, techniques and approaches for dealing with occupational safety and health problems; to discover latent diseases by establishing causal connections between diseases and work in environmental conditions; and to develop medical criteria which will assure insofar as practicable that no employee will suffer impairment or diminution in health, functional capacity, or life expectancy as a result of his work and working conditions. • What does safety and health in the workplace mean? Safety refers to the physical or environmental conditions of work which comply with prescribed Occupational Safety and Health (OSH) Standards and which allow the workers to perform the job without or within acceptable exposure limit to hazards. Occupational safety also refers to practices related to production and work process. Health means a sound state of the body and mind of the workers that enables the worker or employee to perform the job normally. • What is the purpose of OSH Standards? OSH Standards aim to provide at least the minimum acceptable degree of protection that must be afforded to every worker in relation to the working conditions and dangers of injury, sickness or death that may arise by reason of the worker's occupation. The provision of OSH Standards by the State is an exercise of police power, with the intention of promoting the welfare and well-being of the workers. • What are covered by the General OSH Standards? All establishments, workplaces and other undertakings are covered, including agricultural enterprises whether operating for profit or not, except: • Residential places exclusively devoted to dwelling purposes. • Mines which is under the Department lf Environment and Natural Resources (DENR). • What does right to safe and healthful conditions of work mean? It means that the worker shall be assured of effective protection against the danger of injury, sickness or death through safe and healthful working conditions. • What is the minimum standard on safety and health in the workplace? The OSH Standards provide that every company shall keep and maintain its workplace free from work hazards that are likely to cause physical harm to the workers or damage to property. Thus, the worker is entitled to be provided by the employer with: • Appropriate seats, lighting and ventilation; • Adequate passageways, exits and firefighting equipment; • Separate facilities for men and women; • Appropriate safety devices like protective gears, masks, helmets, safety boots, coats or firstaid kits; • Medicines, medical supplies or first-aid kits; • Free medical and dental services and facilities. • What other safety requirements should employers provide their employees? Employers must provide their employees with the following instruments and/or working stations: • Appropriate protective equipment and clothing such as overall head coverings, goggles, gloves aprons and respirators; • A properly designed exhaust system and waste disposal, local exhaust or general ventilation to keep toxic fumes or gases, away from workers' breathing zone; • Adequate number of fire extinguishers in the workplace; • Designated safe smoking and welding areas far from combustible, flammable or explosive materials, containers filled with explosives or flammable substances, and containers that have held explosives or flammable materials; • What safety measures must be observed within the premises of establishments? Establishments must observe the following safety measures: • Building premises shall have adequate fire, emergency or danger signs and safety instructions of standard colors and sizes visible at all times; • Other visible signs that may be needed to direct the driver of motorized vehicle such as STOP, YIELD, and DO NOT ENTER, properly positioned within the compound of the establishment shall be used to increase safety especially during the night; • Handicapped employees shall be restricted only to designated workplaces. As far as practicable and feasible they shall be provided with facilities for safe and convenient movement within the establishment; • Good housekeeping shall be maintained at all times through cleanliness of building, yards, machines, equipment, regular waste disposal, and orderly arrangement of process operations, storage and filing materials; • Adequate dressing rooms, locker rooms, comfort rooms and lavatories separate for male and female workers shall be provided. •Who enforces OSH Standards? The Secretary of Labor and Employment, through the Regional Director or his other authorized representative, enforces the OSH Standards in the exercise of visitorial and enforcement powers. •What is visitorial power? Visitorial power refers to the authority to conduct inspections or investigations in the premises of an employer at any time of the day or night whenever work is being undertaken. This is necessary to determine violations or to enforce the rights of workers under the Labor Code. Under this power, the employer may be required to submit reports and other documents to determine any violation. • What is enforcement power? Enforcement power refers to the authority of the Secretary or the Regional Director to order an erring employer, after due notice and hearing, to comply with labor standards and issue a writ of execution in case of non-compliance. If the violation poses grave and imminent danger to the health and safety of workers, suspension or cessation of the operations may be effected within 24 hours from the issuance of the order. •How are these Standards enforced? These standards are enforced through the inspectorate system. Thus, every employer shall provide to the Secretary or to his/her duly authorized representative access to its premises or records at any time of the day or night whenever there is work to determine and effect compliance. Every establishment or workplace shall be inspected at least once a year. However, special inspection visits may be authorized by the Regional Office to investigate work-related accidents, occupational illness or dangerous occurrences, conduct surveys, follow-up inspection recommendations, or to conduct investigations or inspections upon request of an employer, worker or labor union in the establishment. •If a worker or representative of workers or any concerned person believes that such a violation of the OSH Standards exists which threatens with physical harm or poses imminent danger to life, what shall he do to correct the danger? The said worker or workers’ representative shall request the RO for an inspection of their area by giving full particulars or details regarding such violation or danger. • What does the Regional Office do in such a case? The Regional Office evaluates the report and conducts a special inspection or investigation immediately in the subject establishment. The complainant is notified in writing of the outcome of such investigation. • Fines and Penalties 6|P a g e What are the duties and responsibilities of the employers and the employees in relation to enforcement and compliance with OSH Standards in the workplace? Rules of the Occupational Safety and Health Standards 1000 General Provisions 1160 Boiler 1010 Other Safety Rules 1170 Unfired Pressure Vessels 1020 Registration 1180 Internal Combustion Engine* 1030 Training and & Accreditation 1200 Machine Guarding 6 1040 Health & Safety Committee 1210 Electrical Safety 1050 Notification & Keeping of Occ. Illness &Injuries 1220 Elevators & Related Equipment 1230 Identification of Piping System 1060 Premises of Establishments 1240 Power Piping Lines* 1070 Environmental Control 1410 Construction Safety 1080 Personal Protective Equipment 1420 Logging 1090 Hazardous Materials 1940 Fire Protection & Control 1100 Gas & Electric Welding & Operations 1950 Pesticides & Fertilizers Cutting 1960 OH Services 1120 Hazardous Work Processes 1970 Fees 1040 Explosives 1980 Authority of LGUs 1050 Materials Handling &Storage 1990 Final Provisions Rule 1005: DUTIES OF EMPLOYER • • • • Furnish his workers a place of employment free from hazardous conditions. Comply with the requirements of the Standards. Give complete job safety instruction to all his workers Use only approved devices and equipment in his workplace. DUTIES OF THE EMPLOYERS • • • • • Adopt administrative policies on safety in accordance with the provisions of the Standards; Report to the Regional Director or his/her duly authorized representative the policies adopted and the safety organization established; Submit reports to the Regional Director or his/her duly authorized representative once in every three months on the safety performance, safety committee meetings and its recommendations and measures taken to implement the recommendation; Act on recommended safety measures; Provide access to appropriate authorities. Rule 1005: DUTIES OF EMPLOYEES • • • • Cooperate with the employer in carrying out the provisions of the Standards. Report any work hazard to his/her supervisor Follow all instructions by the employer in compliance with the OSHS provisions Make proper use of all safeguards and safety devices. DUTIES OF THE EMPLOYEES • Follow safety policies; • • • • Report unsafe conditions and practices to the Supervisor; Serve as member of the Health and Safety Committee; Cooperate with Health and Safety Committee; Assist government agencies in the conduct of safety and health inspection. 7 General Provisions (Rule 1010) DUTIES OF OTHER PERSONS • Any person including builders or contractors, who visits, builds, innovates or installs devices in establishments or workplaces shall comply with the provision of OSHS rules and all regulations issued by the employer in compliance with the Standards and other issuances of the Secretary. Rule 1020 - Registration • • • Every employer shall register his/her business with the Regional Labor Office or authorized representative to provide the DOLE with information as guide in its enforcement activities. Free of charge Valid for lifetime, except when there is change in name, location, ownership; opening after previous closing Rule 1030 - Training and Accreditation of Personnel in OSH The BWC either directly or through accredited organizations, shall conduct continuing training programs to increase the supply and competence of personnel qualified to carry out the provision of this Standards. Employer to appoint a safety officer on a full-time or part-time basis depending on the type of workplace (whether hazardous or non-hazardous) and number of workers in the workplace. Rule 1033: Training and Personal Complement: The Minimum qualifications; duties and number of required safety and health officer shall be as follows: 1. All safety officers must complete the Bureau-prescribed training course prior to their appointment as in their respective places of employment. 2. All full-time safety officers must meet the requirement of duly accredited Safety Practitioners or Safety Consultants by the Bureau. 3. Not less than the following number of supervisors or technical personnel shall tahe the required trainings and shall be appointed as a safety officer on a fulltime or part time basis, depending on the number of workers employed and the hazardous or nonhazardous pursuant to Rule 1013 of these Standards. Rule 1030 - Training and Accreditation of Personnel in OSH All Safety Officers must complete the Bureau prescribed Training Course A full-time safety officer must be duly accredited by the OSHC. ACCREDITATION PROGRAM OF DOLE Note: The employment of a full-time safety officer may not be required if the employer enters into a written contract with a qualified consultant or consulting organization whose duties and responsibilities shall be the duties of a safety practitioner as stated in this Rule. The employment of a consultant, however, will not excuse the employer from the required training of his supervisors or technical personnel. 8 RULE 1040 - Health and Safety Committee •What is a Safety and Health Committee? A Safety and Health Committee is a group of employees or workers and management that plans and makes policies in all matters pertaining to safety and health in the workplace. All establishments are required to have a Safety and Health Committee. •When shall an establishment organize a Safety and Health Committee? In every workplace, a Safety and Health Committee shall be organized within sixty days after the Standards take effect, and for new establishments, within one month from the date business starts operating. In both cases the Safety and Health Committee shall reorganize every January of the following year. •What are the types and composition of a Safety and Health Committee? The types and composition of the Safety and Health Committee shall be organized according to the number of employees or workers in a workplace. •What are the duties of the Safety and Health Committee? Safety and Health Committee shall: • • • • • • • • Plan and develop accident prevention programs in the workplace; Inspect workplace to detect unsafe conditions; Review reports of inspection, results of accident investigations and implementation of accident prevention program; Conduct safety meetings at least once a month; Submit reports to the manager/owner on its meetings and activities; Provide necessary assistance to government inspecting authorities in the proper conduct of activities relating to enforcement of the provisions of the Standards; Train workers in safe work habits and procedures; Develop and maintain a disaster contingency plan and organize such emergency service units as may be necessary to handle disaster situations pursuant to the Emergency Preparedness Manual for Establishments of the Office of Civil Defense. Duties of Employer 1. Establishes and adopts in writing administrative policies on safety and health 2. Reports to the enforcing authority the policies adopted and required report requirements. 3. Acts on recommended measures of health and safety committee and in case of nonadoption, informs the committee of the reason 9 What are the duties of the Safety Officer? As per Rule 1047 of OSHS: ➢ ➢ ➢ ➢ ➢ ➢ ➢ Advises employers, supervisors and workers on matters of safety for their guidance Investigates accidents as part of the Safety Committee Coordinates safety training programs for employees and employers Make safety inspections of the plant as part of the Safety Committee Maintains or helps maintain an accident record system Acts as Secretary of the Safety Committee Provides assistance to government inspectors in the conduct of safety and health inspection Qualifications of a Safety Consultant (OSHS Rule 1034.01) o One who has been a Safety and Health Practitioner for at least five (5) years and has taken the necessary training prescribed by the Bureau o Safety Practitioners with at least ten (10) years of experience in all levels of occupational safety and health may not be required to undergo the required training provided they secure from the |Bureau a certification attesting to their competence to qualify as consultants. o All Safety Consultants or consulting organizations shall be accredited by the Bureau and registered with the Regional Office Concerned. No person or organization may be allowed, hired or otherwise employed in the practice of Occupational Safety and Health unless the requirements of the Rule are complied with. Department Order no 13 Series of 1998 This Department Order sets the guidelines, rules and procedures, to be followed by all concerned in the implementation of Department of Labor and Employment D.O. No. 13 (DOLE D.O. No. 13), Series of 1998 otherwise known as the "Guidelines Governing Occupational Safety and Health in the Construction Industry", with emphasis given on the methodology to be used in estimating the cost of construction safety and health program. In compliance with Section 17 of DOLE D. O. No. 13, the implementation of construction safety shall be considered in all stages of project procurement (design, estimate, and construction) and its cost shall be integrated to the overall project cost under Pay Item "SPLConstruction Safety and Health" as a lump sum amount, to be quantified in the detailed estimate. Likewise, all requirements, provisions, and instructions pertaining to the implementation of Construction Safety and Health in every project shall be included in the project bidding documents specifically under the Instructions to Bidders. 10 Republic of the Philippines DON HONORIO VENTURA STATE UNIVERSITY Cabambangan, Villa de Bacolor, Pampanga COLLEGE OF ENGINEERING AND ARCHITECTURE Department of Civil Engineering A. Course Code / Title : COSH 413 – Construction Occupational Safety and Health B. Module Number : Module 2 – Construction Site Premises and Demolition Safety C. Time Frame : 4th - 5th Week of September 2023 (4.5 hours) D. Description : This module describes the 5S of Good Housekeeping, Construction Site Premises and Demolition Safety E. Objectives : At the end of this module, the learner should be able to: 1. Know the 5S of good housekeeping 2. Know the importance of safety signages, fire safety, electrical safety, lifting operations safety, the safety inspections, demolition safety, and noise and vibrations in a construction site F. Contents: HOUSEKEEPING SIGNS OF POOR HOUSEKEEPING 1. 2. 3. 4. 5. 6. 7. cluttered and poorly arranged areas untidy or dangerous storage of materials presence of items no longer needed or in excess dusty, dirty floors and work surfaces tools and equipment left in work areas no waste bins and containers presence of spills and leaks Disadvantages of Poor Housekeeping ⚫ Low Morale ⚫ Low Productivity ⚫ Fire WHAT IS GOOD HOUSEKEEPING? Good housekeeping means there is a clean and orderly place for everything and everything is in place. The 5S of Good Housekeeping ▪ Seiri (Sort/eliminate) ▪ Seiton (Systematize/organize) ▪ Seiso (Sweep/clean/polish) ▪ ▪ Seiketsu (Sanitize/standardize) Shitsuke (Selfdiscipline/training Controls ⚫ ⚫ ⚫ ⚫ Clean work area Provide waste bins Keep floors, aisles and stairs free from obstructions Properly stack & store materials, tools and equipment Rule 1060 OSHS – Premises of establishments – Good housekeeping shall be always maintained thru cleanliness of building, yards, machines and equipment, regular waste disposal and orderly processes, operations, storage and filling of materials. Deteriorating housekeeping may be the first evidence of a deteriorating safety and health program. SAFETY SIGNAGES A Safety Sign provides information about health and safety at work by means of a signboard, a safety color and a safety message to a specific object, activity or situation. D.O. 13 Section 9 Construction Safety Signage Construction Safety Signage must be provided to warn the workers and the public of hazards existing in the workplace. Signage shall be posted in prominent positions at strategic locations and, as far as practicable, be in the language understandable to most of the workers employed. Section 9.1 The signage should include but are not limited to: a) Mandatory requirement on the usage of personal protective equipment prior to entry to the b) c) d) e) f) project site. Areas where there are potential risks of falling objects. Areas where there are potential risks of falling. Areas where explosives and flammable substances are used and stored. Areas where there are tripping or slipping hazards. Approaches to working areas where danger from toxic or irritant airborne contaminants/substances may exist which should indicate the name of the contaminant/ substance involve and the type of respiratory equipment to be worn. g) All places where contact with or proximity to electrical/ facility equipment can cause danger. h) All places where workers may encounter dangerous moving parts of machineries or equipment. Location of fire alarms and firefighting equipment. Instruction on the usage of specific construction equipment. k) Periodic updating of man-hours lost. i) j) Safety Bulletin Board Mandatory provision of safety and warning signs are reiterated not only for the protection of workers, but also the public in general. Signs should conform with the standard requirements of the OSHS. Where Signages are needed . . . ⚫ ⚫ ⚫ ⚫ ⚫ ⚫ ⚫ ⚫ ⚫ Usage of PPE Falling/falling objects Explosives and flammable substances Tripping and Slipping Hazards Toxic or irritant airborne contaminants/ substances Proximity to electrical facilities/equipment Moving parts of machines Location of Fire Fighting Equipment Instructional signs/Update of man-hours lost PPE Safety Scoreboard Effective Visuals 1. Change Periodically 2. Employees Involvement 3. LARGE Enough 4.Locate Properly 5. Use COLOR 6. K I S S FIRE SAFETY Fire is the result of the chemical combination of a combustible material (fuel) with oxygen in the presence of enough heat. If any one of the three is missing, a fire will not start. The relationship is called fire triangle. It is important that every worker, not only supervisor, knows the main causes of fire, how fire spreads, how to fight fire, and how to prevent fire. Basic Chemistry of Fire ➢ Fuel. Or combustible materials. This includes many substances such as natural gas (methane), plastics, wood, natural and artificial fibers, paper, coal and other living matter. Inorganic substances are also combustible, substances like hydrogen, ammonium nitrate magnesium, phosphorus, sodium, and sulfur. ➢ Oxygen. Fire normally draws its fire through the air, which is a mixture of 21 percent oxygen and 78 percent nitrogen. 16% of oxygen is needed to sustain fire. ➢ Heat. Sufficient heat to raise the temperature of the fuel surface to a point where chemical union of the fuel and oxygen occurs. The temperature at which the substance gives off these vapors or gases in sufficient quantity to be ignited is called the “flash point” of the substance. ➢ Chemical Reaction. Vapors of gases, which are distilled during burning process of a material, are carried into the flame Three methods of Heat Transfer ➢ Conduction. Is the transfer of thermal energy between neighboring molecules in a substance due to a temperature gradient. It takes place in solids, such as metals, timber, concrete, and glass. Some solids, such as metals, are better conductor of heat than woods, for example. ➢ Convection. Is one of the major modes of heat transfer and mass transfer. It takes place in fluids and gases cause by the convection currents. ➢ Radiation. Is electromagnetic radiation emitted from a material which is due to the heat of the material, the characteristics of which depend on its temperature. It is the process of heat transmission through air and gases. If you are sitting close to a bonfire, he will feel the heat of the fire, even though the surrounding is cold, this is an example of heat radiation. Sources of Ignition ➢ ➢ ➢ ➢ ➢ ➢ ➢ ➢ Electrical equipment. Hot surfaces produced by defective electrical equipment are a common source of ignition. Spontaneous Ignition. If some liquids are heated or sprayed to a very hot surface, it may ignite spontaneously without a present ignition source. Spontaneous Combustion. Is a type of combustion which occurs without an external ignition source. Combustion begins if a sufficiently strong oxidizer, such as oxygen, is present. Smoking. In many workplaces, employees smoking, or other persons smoking in a certain area, can be a source of fire. Friction. Sparks can be created by friction, for instance where the moving part of a machine comes to contact with a fixed part, or two moving surfaces rub each other or slide together during machine operation. Engines, Vehicle Emissions and Hot Surfaces. In vehicle maintenance, and parking areas, diesel-petrol engine, vehicle emissions and hot surfaces like exhaust systems can be a source of ignition. Open Flame Sources. Open flame in the workplaces such as boilers, furnaces, portable heating appliances, etc can be also a source of ignition. Lighting. In limited cases, lighting can be a source of ignition. Products of Combustion ➢ Fire Gases. Are the vaporized products of combustion? ➢ Flame. Is the visible luminous body of a burning gas, which becomes hotter and less luminous when it is mixed with increased amounts of oxygen? ➢ Heat. Is the process of energy transfer from one body or system due to thermal contact? ➢ Smoke. The Visible product of incomplete combustion. Phases of Burning ➢ ➢ ➢ Incipient Phase or Beginning Phase Flame Producing or Free-Burning Phase Smoldering phase INCIPIENT PHASE – or beginning of fire • • • • • • oxygen is plentiful Temp has not built to high peak Breathing not difficult Direct water application Ventilation: not a problem Little steam production FREE BURNING PHASE – fire begins to deplete the room’s oxygen supply and temperature greatly increased. • • • • • • Fire has involved more fuels Oxygen supply is being depleted Heat accumulates at ceiling SCBA is a must Ventilation: not a definite need Good steam production SMOLDERING PHASE – after oxygen content of the air falls below 15%, the fire enters a smoldering phase where flame may cease but dense smoke and heat completely fill the room. • • • • • • Oxygen supply is below 15% Temp is very high Normal breathing not possible Backdraft hazard Fire extinguishment: indirect method Ventilation is a must ****************************************************************************************** ********** Fire Spread Control ➢ Starvation or Fuel Removal. There are three ways to achieve starvation: ▪ Take the fuel away from the fire ▪ Take the fire away from the fuel ▪ Reduce the quantity or bulk of the fuel. ➢ Smothering or oxygen removal. Smothering can be achieved by: ▪ Allowing the fire to consume the oxygen while preventing the inward flow of more oxygen ▪ Adding an inert gas to the burning mixture. Oxygen levels can be reduced below the minimum (16%) percentage needed for combustion by purging and rendering the atmosphere inert in closed containers or processing systems. ➢ Cooling or heat source control. The most common means of fire. Water is the most effective and cheapest medium for fighting a fire. Classifications of Fire and Extinguishing Methods ➢ ➢ ➢ ➢ ➢ Class A or combustible materials such as solid materials, wood, cloth, paper, and natural fibers. Water is used in cooling to reduce the temperature of the burning material below its ignition temperature. It is the most effective way of extinguishing the Class A fire. Class B fires involve Flammable liquids, greases, and gases. Foam, vaporizing liquids, carbon dioxide and dry powder can be used on Class B fires. There may be some restrictions on the type of foam which can be used because some foam breaks down on contact with alcohols. Class C fires involve energized electrical equipment. This class of fire can be controlled using non-conducting extinguishing agents. The safest procedure is to always de- energize high voltage circuits and treat as Class A or Class B fire depending on the fuel. Class D fires involve combustible metals such as magnesium, titanium, zirconium, sodium, and potassium. Water and other common extinguishing agents are ineffective on this kind of fire because of its extremely high temperature. There is no agent available that will effectively control fires in all combustible metals. Special extinguishing agents are available for control of fire in each of the metals and are marked specifically for that metal. Class K fire or kitchen fire. Fires that involve cooking oils or fats are designated "Class K" under the US system, and "Class F" under the European/Australasian systems. Though such fires are technically a subclass of the flammable liquid/gas class, the special characteristics of these types of fires are considered important enough to recognize separately. Fire Extinguishers - Is an active fire protection device used to extinguish or control small fires, often in emergency situations. This is the first line of defense. Fire extinguishers are further divided into handheld and cart-mounted, also called wheeled extinguishers. Handheld extinguishers weigh from 0.5 to 14 kilograms (1 to 30 pounds), and are hence, easily portable by hand. Cart-mounted units typically weigh 23+ kilograms (50+ pounds). These wheeled models are most commonly found at construction sites, airport runways, heliports, as well as docks and marinas. Portable Firefighting These are appliances designed to be carried and operated by hand. These contains extinguishing medium which can be expelled by action of internal pressure and directed on to a fire. The maximum mass of a portable extinguisher in working order is 23kg. ➢ Water. These operate on the basis of cooling and reducing the temperature within a fire, slowing down the rate of combustion and preventing reignition from taking place. Water is the most efficient form of extinguisher for use on Class A fires. ➢ Foam. Foam applied to a fire has a smothering effect, preventing further air from reaching the combustion area or seat of the fire. ➢ Carbon dioxide. It produces a snow that is converted to gas in the fire. This has the effect of slowing down the rate of combustion, reducing the available oxygen through the smothering effect created. ➢ Dry Chemical. These incorporate a specific powder mixture that interferes with the combustion process, reducing the combustion rate until no further ignition and reignition of the fuel can take place. They are designed for Class A and B fires. Proper Use of Fire Extinguishers The Parts of the Fire Extinguisher FIRE PROTECTION FIRE is a chemical reaction between a flammable or combustible material and oxygen. Classification of Fire PREVENTION Control of Heat Source –Welding –Cutting –Friction from Grinding –Electricity –Friction Methods of Extinguishing Fire • Removal of Fuel • Blanketing or Smothering • Cooling or Quenching Using the Fire Extinguisher Always remember the.. PASS-word ELECTRICAL SAFETY Like any other forms of energy, it can be completely safe provided it is treated and handled with care and people know the basic principles in its use. Electrical abuse and misuse, however, can result to serious injuries, fire, damage to plant and equipment, even death. Every piece of equipment is a potential source of electrical shock. Even an electrical shock small enough not to cause an injury can trigger an involuntary reaction that may result in physical harm. Electric accidents are classified into electric shock caused by contact with charged or leaked parts of electric facilities; a burn cause by discharge arc, eye injury caused by strong light from arc welding work; and fire or explosion ignited by overheat, sparks, leakage current, static charges, and the like. An effective electrical safety policy coupled with an employee training and hazard awareness program can further prevent electrical shock. It is also recommended that an effective electrical inspection program be implemented and conducted periodically as conditions warrant. Myths and Misconceptions about electricity: ➢ Electricity takes the path of least resistance. This myth implies that current only takes low ➢ ➢ ➢ ➢ ➢ resistance paths. Current will take any path, high or low resistance in order to return to the source that provides power. A person is led to believe that electricity wants to go to ground and simply disappear. Current uses the ground to get back to its grounded power source. When an electrical tool or appliance is into water, it does not short out. If the switch is ON, the item will continue to operate. If it is switched OFF, it will do no harm. AC reverse polarity is not hazardous. The switch is supposed to be on the “hot” conductor supplying power to the item. It takes high voltage to kill; 120 volts AC is not dangerous. Current is. However, AC voltage as low as 60 volts can kill. At higher voltage, the body can be severely burned and yet the victim could live. Double- insulated power tools are doubly safe and can be used in wet and damp locations. Basic Electrical Terms Voltage- the difference in potentials between points (measured in volts) Current- The movement or flow of electric charges (measured in amperes) Resistance- The property of material that opposes the flow of electric current (measured in ohms) Ohm’s law- the current flowing in a circuit is directly proportional to the voltage and inversely proportional to the resistance. Conductor- permits electrons or electric current to flow through it Conductors have low resistance to electricity and are used for wires, switches and electrical connections. Insulator- Used to provide barrier around a conductor (to prevent accidental contact). Insulators have a very high resistance to the flow of electricity and are used to cover wiring and other electrical components Semiconductors - can change their resistance to act as either a conductor or an insulator. They are used to make computer microchips. Electrical Circuit - Any combination of a conductor and a source of electricity connected to permit electrons to travel in a continuous stream. Electricity may take multiple paths, flowing through all possible circuits. The greatest amount of current will flow through the path of least resistance, or lowest resistance, or lowest impedance. Any part of your body that accidentally bridges the gap between two different voltage levels creates a new electrical circuit, and your body may provide the path of least resistance to the ground. Equipment grounding connects all conductive materials that enclose electrical lines. Bypassing grounds or careless handling of grounding connections can result in electrical fires and fatal accidents Circuit-Protection Devices (CPDs) ➢ Fuses ➢ Circuit breakers ➢ Ground fault circuit- interrupters (GFCIs)- A GFCI is a supersensitive appliance, rapid action power switch which breaks a circuit when there is more than 5 milliamps difference between the hot wire and the neutral or grounded conductors. Rules for Circuit Protection ➢ Do not create an octopus connection ➢ Never bypass, bridge nor disable any circuit protection device in an energized or live ➢ ➢ ➢ ➢ circuit Always make sure the power is safely off. Replace a fuse with the exact duplicate. Use fuse pliers for added protection Be sure the markings on the old and new fuses match. Electrical Shock – is the most serious electrical hazard. This happens when you touch a live wire, a tool or machine with poor insulation. You then become a conductor. The danger of an electric shock is not directly related to the voltage, but mainly determined by the following conditions: current value, type of power supply, duration of electric shock, passage of current and human condition. The minimum current at which a man feels an electric shock is about 1 mA at 60Hz; the limit current at which man can endure the pain of an electric shock is about 7 to 8 mA and the maximum current at which man can still move is about 10 to 15 mA. The heart is particularly the susceptible to electric shock. The flow of the current disturbs the hearts rhythm, upsetting the blood flow and affecting its vital functions. When the current increases, the heart shivers and death results in few minutes. Measures for Preventing Electric Shock Accidents Accidents or deaths by an electric shock are mostly caused by contact with power transmission lines, followed by movable or portable electric machines and equipment, switches, wiring, capacitors, and other power facilities. To prevent such accidents, even death, it is necessary to check the electric facilities and put them in order, and to conduct training for handling electric equipment and working method around electric facilities. 1. Maintenance and Inspection of electric facilities ➢ Check the wiring, movable wires, switches and all electric machines and equipment if provided with complete insulation cover and enclosures. If you found out that it is faulty, they must be repaired immediately. ➢ Before using the electric equipment, check the earth conductor is connected and not damaged and see to it that the earth pole is not floating. ➢ Before using the welding machines, check if the electrode holders, safety devices and tools such as automatic voltage reducing device for AC welding machines and leakage circuit breaking equipment for preventing electric shocks are complete. 2. Electric shock prevention when handling live lines and working near live lines When handling hot lines, it is necessary to install an insulation protector, and have workers wear safety garments such as insulation gloves and electric safety helmet. For high- voltage live lines, it is preferable to use live line working tools such as live sticks, live line working carts, and insulation bench. If working near a high- voltage live lines, workers must approach within 30cm from overhead live lines or within 60 cm from sideway or underneath live lines. The workers must wear insulation protective garments, or the live lines must be provided with a safety device. Low- voltage live lines must be protected in the same way. ➢ Electric safety Helmet. Or electric safety helmet is useful to prevent an electric shock and protect the head from flying and falling objects. The helmet consists of high- insulating synthetic resin, such as polyethylene. Polyester and hard polyvinylchloride. ➢ Electric Rubber gloves o For high voltage. When handling high voltage live lines, the gloves protect the hands and forearms. o For low voltage Raw and synthetic rubbers are used, of which the latter has better wear resistance. The withstand voltage is 2,000 V/min for raw rubber gloves and 1, 000 V/min for synthetic gloves. ➢ Electric Insulation garments. Is used to protect both shoulders and back from an electric shock. ➢ ➢ ➢ ➢ Electric sleeve cover. Protects arms from electric shock Electric insulation tube. Electric insulation sheet Protective tube for construction field. 3. Electric shock prevention when handling power failure It is caused by misrecognition of hot lines, touching residual electric charges, and error of power transmission and this accident is greater at power failure than at normal operation. First Aid Procedures Mild Shock ➢ ➢ ➢ ➢ ➢ Have the worker sit down Be sure muscle movement is normal Check for loss of feeling in any part of the body Check the pulse rate and breathing If there is no severe pain, the worker can return to work. Continuous Shock ➢ Remove the contact of the worker from energized source using wooden chair, broom handle, plastic pipe or rope. ➢ When you have freed the victim from the power source, assess if the victim’s condition. Check the airway, breathing and pulse. Always bring the victim to the doctor for medical attention after first aid. Lockout - is blocking the flow of energy from the power source to the equipment- and keeping it blocked out. Lockout/ tag out protects you from the unexpected start-up of machines or release of stored energy during service or maintenance. Lockout- tag out procedure ➢ ➢ ➢ ➢ ➢ Place a lock on a disconnection switch, circuit breaker, valve handle to make sure it cannot be moved from the OFF or closed position. Attach a written tag at the place where the equipment would be energized, such as the ON switch or on a valve that opens a supply line. NEVER use you LOTO for blocking personal or unauthorized items NEVER lend or borrow a lock or tag NEVER remove someone else’s lock or tag 6 steps to lockout/ tag out 1. Preparation- know the equipment, its energy source before working on it 2. Shutdown- turn off the equipment 3. Isolation- find and isolate every form of energy that the machine uses. This includes pulling fuses, throwing disconnects and capping any secondary sources of energy. 4. Application- anything that might restore the flow of energy to the work area must be locked out. In situations where multiple pieces of equipment are being locked, an authorized employee places all keys in a lock box to which each employee attaches his or her personal lock. 5. Control- even after the equipment is locked out, you must control the stored energy. a. Relieve, disconnect or restrain any residual hazardous energy that could be present b. Check that all moving parts have been stopped. c. Relieve trapped pressure d. Install ground wires to discharge electrical capacitors. e. Block or support elevated equipment f. Check continuously if energy build- up is possible 6. Verify a. Energy source is shut down. Blocked off, controlled, and locked out b. Warn everyone in the lockout area and be sure they are moved to a safe place c. Activate controls that might restore power to the machine you are working on d. If equipment does not start, restore all controls to the OFF position and begin to work 3 steps to removal and Re- Energizing a System 1. Restore Work Area a. Remove all tools b. Double check all equipment components c. Replace all safety features, such as machine guards d. Close access panels that were opened to perform service on equipment 2. Notify Personnel. Notify all employees that LOTO devices are being removed. Remove employees from the area or make sure they are at a safe distance from the equipment. 3. Remove LOTO Devices. The person who placed each device must be the one to remove it. Someone who placed a LOTO device is not present, notify your supervisor who will follow specific procedures. Never remove it yourself. After all devices are removed, tell involved employees that LOTO is ended, and that the equipment is being re-energized. SAFETY IN LIFTING OPERATIONS CLASSIFICATION OF MATERIAL HANDLING OPERATIONS Refers to any methods for moving materials: • by people • by people using equipment MANUAL MATERIAL HANDLING Manual Material Handling means moving or handling things by lifting, carrying, placing, pushing, or storing using own physical strength. CORRECT MANUAL LIFT BAD MANUAL LIFT Proper Lifting Method Stand close to the load Keep feet apart Keep back straight Bend your knees and not your back Grip the object with the whole hand Lift load gradually Keep body weight directly over your feet and use muscle power of legs What makes manual material handling hazardous? •Load too heavy •May have a shape that makes it hard to handle •Wet, slippery, or have sharp edges •Unstable or can shift its center of gravity •Too big or high to block your frontal vision •Located too high or low for a safe lift Mechanical Handling Classification • • Manually Powered • Pushcart • Hand Pallet Motor/Pneumatic/Hydraulic driven • Lifting Equipment • Hoist • Cranes • Transport Equipment • forklift • tractor • dump truck How Do Accidents Occur? Instability – unsecured load, load capacity exceeded, or ground not level or too soft Lack of communication - the point of operation is a distance from the crane operator or not in full view of the operator Lack of training Inadequate maintenance or inspection Hazards in Crane Operations • • • • • Structural failure Overloading Instability Falling or slipping load Electrical Hazards Safety Precautions in Crane Operation • • • • • • • • • • Do not carry or use crane beyond the rated load Never move load over people. Never allow personnel to ride on a load. Center the crane over the load before starting to hoist. Lift, move & lower loads smoothly. Do not leave suspended load unattended. Keep hook block more than 2m above the floor when not in use. Use tagline to stabilize and control loads. Respond to signals from designated signalman only. Maintain safe distance from electrical transmission lines. Rigging Is the process where a load is prepared for lifting using a lifting machine. The main part of this process is the tying up of the load with sling and/or other connecting devices so that the load could be hooked onto a crane. Sling Inspection • • • • • Broken Wires Abrasion Crushed Strands Corrosion Kinks Safety Inspection Is a systematic way of identifying potential workplace hazards before they cause a health and safety problem. Purposes of Safety Inspection • Eliminate Hazards • Assess Effectiveness of OSH Program • Display Visible Management Commitment to Safety • Establish Accountability • Identify Training Needs • Fulfill Legal Obligations Types of Inspection Continuous Inspection a process conducted as part of their job responsibilities in noting and correcting potential danger Periodic/Interval Inspection a systematic process with specific intervals and widely regarded as “real” safety and health inspection Intermittent/Emergency Inspection an unscheduled inspection may be After Inspection •Writing of inspection report •Correction of hazards •Monitoring and evaluation Corrective Actions •Immediately correct everything possible. •Report at once conditions beyond one’s authority and suggest solutions. Take intermediate action as needed. Our main goal in the premises..... DEMOLITION It is the complete or partial dismantling of a building or structure by pre-planned and controlled methods or procedures. “SAFE DEMOLITION REQUIRES ADEQUATE PLANNING” Why Plan? • • • • • • Identify the Hazards Meet Legislative Requirements Ensure Appropriate Equipment Ensure Safe Disposal of Materials Determine Appropriate Methods of Demolition Determine Cost of Demolition Demolition Technique Sequential -gradual reduction of height in reverse order to its construction Induced -key structural members are weakened or removed, causing the whole part of the structure to collapse Method of Demolition Manual – use of handheld tools Mechanical – use of heavy equipment, wires and chain, power shear, etc. Explosives – by the use of explosives Workplan • • • • • • • • • • Sequence of Work Operation Estimate of Time and Completion Equipment to be used Proposed Access and Egress Public Protection Bracing and Shoring Disconnection of Services Methods of Handling/ Disposal of Scraps PPE Requirements Demolition Personnel and Supervisor Hazards Associated with Demolition • Falls • Being Hit/Trapped/Crushed by Objects • Manual Handling • Hazardous Substances and Dangerous Goods • Noise and Vibration • Electric Shock • Fires and Explosions • Equipment Falls • • • • • Falling through fragile roofing material Falling through openings Falling from open edges Falling out of elevating work platforms Failure of equipment Being Hit/Trapped/Crushed by Objects • • • • Falling debris (from service ducts and lift shafts) Accidental/uncontrolled collapse of a structure Use of equipment (crane lifting loads) Failure of structural members (load bearing steelwork) Manual Handling • Using equipment • Operating equipment • Manual demolition • Lifting material • Clearing up • Loading trucks/bins Hazardous Substances Lead lead based paint, tanks containing lead-based petrol Asbestos sprayed coatings, insulation materials, fire resistant walls/partitions, cement sheets, flooring materials PCBs stones, bricks, and concrete aggregates Dangerous Goods Flammable liquids/ vapors and sludge from industrial process and confined space Noise and Vibration • Equipment • Falling debris • Explosives Electric Shocks Live wires from structures Fires and Explosions • Flammable Materials • Welding or cutting • Leaks of Explosives gases from accidental damage of pipes • Arson, especially when the is site unattended. Equipment • • • • • • • • • • • Electrocution Plant failure Dropping materials Equipment striking a person Noise and Vibration Flying particles Dust and other airborne hazards Falling objects onto operators Structural collapse of floors Welding and cutting hazards Falls Isolation • • • Install screens on equipment to protect from dust and noise Install barriers and fences Mark off hazardous areas Personal Protective Equipment (PPE) • • • • • • Safety Helmets Harnesses and Lanyards Boots Gloves Respirators Hearing Protectors Republic of the Philippines DON HONORIO VENTURA STATE UNIVERSITY Cabambangan, Villa de Bacolor, Pampanga COLLEGE OF ENGINEERING AND ARCHITECTURE Department of Civil Engineering A. Course Code / Title : COSH 413 – Construction Occupational Safety and Health B. Module Number : Module 3 – Excavation Safety and Heavy Equipment Safety C. Time Frame : 4th - 5th Week of September 2023 (3 hours) D. Description : This module describes the Excavation Safety and Heavy Equipment Safety E. Objectives : At the end of this module, the learner should be able to: 1. Understand the importance determination of hazards in excavation works 2. Know the typical accidents that occur in using heavy equipment and safe operation guidelines F. Contents: EXCAVATION • Is any man-made cut, cavity or depression in an earth surface that is formed by earth removal Trench • is a narrow excavation where the depth is greater than its width, and the width measured at the bottom is not greater than 15 ft. Hazards of Excavation Works • • • • • • Soil Collapse Falls Vehicular Traffic Underground Utilities Working Surface Confined Space Conditions Principal Causes of Soil Collapse • • • • • Steep cutting angle Super imposed load Shock & Vibration Water Pressure Drying Prevention of Soil Collapse Type A – Most stable: clay Type B – Medium stability: silt and unstable rock (disturbed soil as type B) Type C – Least stable: gravel, loamy sand, submerged soil, soil from which water is freely seeping. Prevention of Soil Collapse ▪ Cut the slope at a safe angle (H:V) • Type A - 3/4:1 or 53° • Type B - 1:1 or 45° • Type C - 1½ :1 or 34° • Provision of shoring and timbering Plate Lining System The walls of every excavation over 1 meter deep shall be supported by adequate shoring… Falls • Minimum Berm - not less than one third of the depth of the excavation - may be reduced to not less than 1 meter provided that materials are stable, shoring and barriers are present (Per Rule 1413 of the OSHS) • • Barricades of at least 1 meter high should be provided. Signs should be posted to prevent the public from going near the excavation Surface Crossing of Trenches • • • • Walkways or bridges must be provided Minimum clear width of 20 in. With standard rails Extended a minimum of 24 in. past the surface edge Vehicular Traffic • • • Provide workers with warning vests or other suitable garments marked with reflectorized materials Designate a trained flag person along with signs and barricades when necessary Use horn or give signals to ensure safety. Underground Utilities • • Determine location of underground facilities and take necessary steps to prevent damage to these facilities. In an open excavation, support, protect or remove underground installation. Working Surface • • Excavation shall be kept free of water at all times And in muddy area, workers should be provided with boots to reduce the hazard of slipping. Groundwater Control Sump Pumping Single-sided Well Point Well Pointing Double-sided Well Point CONFINED SPACE CONDITIONS Hazardous Atmosphere: • • • Oxygen, O2 : < 19.5% or > 23.5% Flammable gas concentration > 10% of Lower Flammability Limit (LFL) Hazardous toxic chemicals Excavation in confined space Check the condition of the atmosphere before entry Do not work alone in a confined space Provide lifeline Provide ventilation or blower before entering Provide emergency rescue equipment such as breathing apparatus, safety harness and line and basket stretcher Working in Excavation • Prior to opening Check excavation permit Identify all underground installations Remove trees, boulders, stumps, other surface encumbrances and hazards before starting excavation • During operations Wear appropriate PPE Give special attention to side slopes that are adversely affected by weather, moisture content or vibration Safe working distance between workers Maintain guardrails, fences, or other barricades and warning lights • • • During break time, workmen should never stand or take rest on high banks of soft material Do not leave tools, materials, or debris in walkways, ramps, or near the edge of excavations Do not use guardrails as resting place Inspection • • • • Daily before start of each shift After heavy rain When fissures, tension cracks, undercutting, water seepage, bulging at the bottom or other conditions occur When there is any indication of change or movement in adjacent structures or spoil pile Rule 1413 of the OSHS states that excavation shall be inspected at least once everyday. Summary Key Points: ➢ An excavation may not be safe to enter without a proper support structure being provided. ➢ Back-filled grounds are especially dangerous. ➢ Water increases the possibility of a cave in. ➢ Excavation should be considered as a confined space. ➢ A worker does not have to be completely buried in soil to be seriously injured or killed. HEAVY EQUIPMENT SAFETY Many types of mobile construction heavy equipment are being used in a construction site doing a wide variety of work. Most of these machines operate within close proximity to persons on foot. With this, many people are exposed to hazards associated with this equipment. In short, you have a congested construction site with personnel on foot, and mobile machines working in the same area at the same time TOTAL EQUIPMENT SAFETY MANAGEMENT 1. Management Commitment • Restrict entry onto site of non-essential personnel. • Establish Controlled Entry Points to site. • Coordinate Operations of Various Trades Working in the Same Areas. • Provide Fundamental Site Rules and Training to all Persons at Risk. • Adequate Lay-Down Areas Established. 2. Employee Involvement • All must receive basic orientation. • Attend operator’s Tool Box Meetings • Must learn, follow, and obey established Safety rules. • Realize that they must see and be seen. DO#13 Sec. 12S & H Information 12.6 Specialized instruction and training should be given to: a. drivers/operators of lifting appliances, transport, earth-moving and materials-handling equipment and machinery or any equipment of specialized or dangerous nature. b. Workers as signalers 3. Pre-Construction Job Hazard Analysis • • • Identify Potential Known Hazards. Job Conditions: Haul Roads, Access Points. Lay down/Storage Areas. 4. Hazard Prevention and Controls • • • • Perimeter Fencing, Enclosures, signs. Spotters provided for in-the-blind, backing machines and/or equipment. Be Alert; Stay Clear; Hear Warnings. Temporary Barricades around Hazards 5. Equipment maintenance • Duly certified mechanics and operators shall conduct daily routine inspection • Inspect before operation • Check instrumentation • Check safety devices; horns, lights • Warm up and make trial run • Keep machine clean • Be aware of abnormalities SAFE OPERATION GUIDELINES 1. AUTHORIZED OPERATOR • • • Qualified with license Well trained Good physical condition EQUIPMENT OPERATOR RESPONSIBILITIES • • • • • Keep control of the Machine at all Times. Take Machine “Out of Service”, if it is unsafe to operate. Familiarity with the operating characteristics of your machine. Be on The Look-Out For Other Trades Working in the Same Area. Frequently check for the Location of