Chapter 5.4 - Quality Management PDF
Document Details
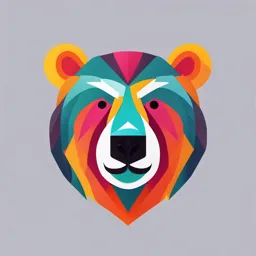
Uploaded by AdroitPerception3329
null
2021
RAIC
Tags
Summary
This document from the RAIC discusses quality management in architectural practice. It covers quality planning, control, and assurance, and discusses the relationship between architectural services and products. It introduces concepts such as "instruments of service" and how those relate to the construction process.
Full Transcript
10/24/21, 4:21 PM Chapter 5.4 - RAIC Chapter 5.4...
10/24/21, 4:21 PM Chapter 5.4 - RAIC Chapter 5.4 Quality Management Print this page Introduction Quality management in architectural practice encompasses all of the processes that ensure architectural service delivery meets the standards set by the client, the firm, professional associations of architects, and agencies responsible for building codes and derivative trades standards. These processes include establishing the standards for service delivered (quality planning), evaluating the firm’s work against those standards (quality control), establishing and evaluating quality management processes (quality assurance), and making management and strategic changes to firm processes, practices and culture to bring the results of work into alignment with those standards. Quality can only be achieved when services are delivered in a consistent, professional manner. Because of the diversity and complexity of architectural practice, the achievement of quality is an ongoing challenge. This chapter briefly discusses quality management within an architectural practice. During the design and procurement phases, quality management in architectural practice is typically focused on the coordination of the “instruments of service” with attention paid to the construction drawings and specifications, the key deliverables of the document production phase. However, quality management goes beyond that single deliverable created in the document production phase. All deliverables of the service, from a pre-design report to a supplemental instruction to a returned telephone call, are a demonstration of a firm’s approach and attitude towards the quality standard that it sets. During the construction phase, attention is shifted to the means and methods of delivering construction administration services. These services vary depending upon the particulars of a project’s design, the method of construction project delivery, and the type of construction agreement, as well as the regulatory requirements of each jurisdiction. Product vs. Service In understanding how quality management relates to architectural services delivery, it is important to distinguish between a “product” and a “service.” Architectural practice is a knowledge-creating endeavour that is delivered through a service. Although architectural services usually contribute to the construction of a building (a product), the output of an architectural practice is not the building itself, but rather knowledge expressed in the form of drawings, renderings, reports and other “instruments of service.” These “instruments of service” are the deliverables generated to communicate design knowledge to constructors who will then translate that knowledge into build form. Within the context of the design project itself, the deliverables, drawings, specifications or renderings are a “product.” The “service” includes consultation, managing stakeholder engagement, coordination of the design, conducting field reviews, and the other activities involved in delivering architectural services. During construction, instruments of service expand to include the various deliverables that review the contractor’s proposals for constructing the design (e.g., submittals and their review) as well as those needed to evaluate the subsequent execution of that design (e.g., field review reports) and value, and to pay the contractor for that execution (e.g., payment certificates). Definitions of Quality There is currently no single universally accepted, clear or rigorous definition of quality; however, certain elements help to define quality as it relates to architectural services. A common thread in these definitions is the establishment of requirements and putting systems in place to assure that requirements are delivered. Quality: provides value to clients; facilitates doing the right things — right the first time, on time, all the time and to the client’s satisfaction; satisfies fitness for purpose (offering solutions that fit the purpose); provides service which consistently meets or exceeds performance levels required by the client. Long before the service sector of the economy took a strong interest in quality, manufacturing industries recognized the following principles, which are applicable to the service industry: quality is determined to a much greater degree by management than it is by staff or workers; https://chop.raic.ca/chapter-5.4 1/6 10/24/21, 4:21 PM Chapter 5.4 - RAIC quality applies to both the product and the process of creating that product; quality is planned in, not simply inspected in; as quality goes up, some costs go down; the cost of avoiding mistakes is usually less than the cost of correcting them. As an example of the importance of “the cost of avoiding mistakes is usually less than the cost of correcting them,” consider this case: During the final stages of document production, the coordination of an architectural element and the mechanical element needed to be detailed. The deadline for tender was rapidly approaching. “We’ll get to it during tender with an addendum. Leave it for now.” It may have taken two hours to resolve the coordination issue, but other items that would affect the bid took priority. But when the documents went to tender, the team was immediately re-assigned to another high priority project and the detail did not get fixed. The issue re-emerged during construction. It then took fifteen hours of discussion, e-mails, negotiation, claim for an extra, drawing of the detail by someone who must re-orient to the project, and change processing. Terminology Over the years, consultants and standards writing organizations have developed terms which relate to quality. Understanding this terminology is important. Quality Management Quality management refers to what an architectural practice does to manage its processes and activities (the architectural services it delivers). Quality management is a systematic way of achieving quality at every stage of a process to ensure that the client’s requirements are met on time and all the time. Quality Planning Quality planning refers to determining the quality standards that are relevant for a project and how to put those standards in place so that requirements will be met. Quality standards have four main contributors, which can be individually and collectively integrated: 1. The core services required by regulators and which govern professional practice, including: provincial and territorial architect acts and regulations; building codes; special codes and standards referenced by building codes, such as product standards. 2. The collaborators in defining and providing services on a project, including: clients and client-consultant agreements; contractors and client-contractor agreements; communities where a project is located, including local zoning and building by-laws. 3. The contexts of each project, including: building type and functional program; climate in the location of the project; complexity of a project; schedule, e.g., traditional design-bid-build, fast-track, etc. 4. The concepts that underlie a particular architectural practice, such as: traditional project delivery tools and methods; integrated design process (IDP); integrated project delivery (IPD); building information modeling (BIM) usage. Until recently, the development and implementation of quality planning was viewed as a scale-driven challenge – larger practices could devote the time and effort to developing and implementing paper- or server-based systems at considerable expense, while smaller practices could not. In today’s environment of inexpensive cloud-based databases accessible to tablet and hand-held devices, size no longer matters. Quality Assurance https://chop.raic.ca/chapter-5.4 2/6 10/24/21, 4:21 PM Chapter 5.4 - RAIC Quality assurance can be defined as the planned and systematic activities arising from quality planning, implemented to fulfil requirements for quality. The term is sometimes used incorrectly as, and interchangeably with, “quality control.” For example, an architect’s audit of how well the firm’s coordination activities are completed through reviewing the causes of construction phase change orders is “quality assurance.” The coordination of a complete set of tender documents is “quality control.” The first is both random and planned, based on sampling. The second is continuous and comprehensive, involving all design activities. The adoption of a quality management system provides assurance to clients and others that the service will be consistent, and requirements will be met. Quality Control In architecture, quality control is the process of reviewing the work of any phase of services to verify it is consistent with established design and construction standards. It also involves identifying the reasons for variations in quality and associated risks, and resolving problems. In the delivery of architectural services, this can be as simple as reviewing correspondence to be sent to clients, or as complex as the task of reviewing a set of contract documents to identify errors or omissions prior to tender. Quality Management Systems in Architectural Practice Quality management for architects focuses on a process to ensure that professional services are consistently provided and continuously improved. This process will vary from practice to practice and from project to project. A good quality management system has the following objectives: identify a common understanding of the services required and expected; confirm that the client receives the expected service and remains satisfied; prevent errors in architectural practice; prevent delays to the delivery of the architect’s contracted services; as a consequence, reduce the costs to the architectural practice; improve productivity; continuously improve services; meet quality assurance requirements agreed to by the client and the architect. Implementing a quality management system encourages the architect or managing principals to: seek work that falls within the expertise of the practice and its consultants; recruit, train and retain staff who contribute to both their own individual success and the success of the practice; realize the potential of every staff member by providing consistent and creative work methods as well as opportunities for greater involvement; facilitate the staff’s professional development; support staff to participate in and influence the quality of service provided to clients; support staff so that tasks to be performed and objectives to be achieved are understood, including how they affect quality; encourage contributions that enhance quality by giving due recognition and reward for achievement; assess periodically the factors that motivate personnel to provide quality service; use appropriate information technology and management methods; provide a work environment that fosters excellence. Quality Management Systems for the Practice No matter how the practice is organized, ensuring the provision of quality architectural services requires that several strategic and administrative functions must be in place, including: a committed leadership; a mission statement and possibly also a “quality” statement; a clear organizational structure (see also Chapter 3.1 – Starting and Organizing an Architectural Practice); a staffing plan and opportunities for professional development and empowerment (see also Chapter 3.6 – Human Resources); office policies and procedures, and document and data filing and retrieval systems (see also Chapter 3.5 – Office Administration). Quality Management Systems for the Project An effective quality management system should be used for every project and for every phase of the project. This includes thorough project planning to ensure that services are delivered on time, accurately and within budget. The current state and decreasing costs of technology available to architectural practices enable the efficient creation of project quality management systems. https://chop.raic.ca/chapter-5.4 3/6 10/24/21, 4:21 PM Chapter 5.4 - RAIC Quality management systems may use the following tools and techniques: Work Plan A work plan is a comprehensive list of the steps required to plan and execute a project. In today’s cloud-based work environment, a work plan ideally has these characteristics: Master/specific – Rather than developing a work plan for each and every project, a practice develops and maintains a master work plan that includes those steps required by regulation and best practice as well as those elements of work that a specific practice has developed, which mark its uniqueness among peers. The master work plan should be able to be copied and easily edited for each specific project. Instructional – Each step in the work plan should include the practice’s work instructions for the execution of the task. A newer practice may use standard instructions derived from standard professional recommendations (such as this document). As a project evolves, it will probably refine various instructions to reflect “the way we do it here.” In the absence of practice-wide systems, younger staff are already collaborating around “how do I do this?” using various apps. Diarized – In our increasingly “real time” work environment, it becomes important for staff to record progress on sometimes complex tasks. In the absence of practice-wide systems, younger staff are already doing this using various apps. Diarized steps should also be able to be concluded, e.g., time-dated note made when the step has been completed. Actionable – Many project steps, e.g., respond to RFI, issue proposed change, etc., require the issuance of related “instruments of service,” traditionally forms and checklists, as further described below. Actions As noted above, certain steps in design and construction often involve the use of pre-formatted “standard” documents or forms, which may be required only once or many times during a project. Because they are formulaic and often repetitive on a project, they are useful in systems design and management. Examples include: meeting notes, minutes, etc.; design reports; design reviews; coordination review templates; risk identification and management; value engineering exercises; RFIs and their responses; payment certification; changes to the work; supplemental instructions; submittal review; mock-up review; general review, including: observations; deficiencies; non-conformances; closeout documentation; warranty items and documentation. These and other actions have many common elements that make them easier to systematize, including: “tags” or links to one or more work plan steps; a unique action name; a location within the building (during design as well as construction); an assignee and assignor (which can change as an action evolves); a due date (preferably with reminders), which may change as the action evolves. In addition to changed assignees, assignors and due dates, actions may include fields or content that may evolve as an action is pursued. Some examples include: the text (writing) associated with an action’s evolution and resolution; in the case of changes to the work, payment certification and other financial elements, changing monetary values. Checklists https://chop.raic.ca/chapter-5.4 4/6 10/24/21, 4:21 PM Chapter 5.4 - RAIC As differentiated from work plans and actions, checklists are logically formulated lists that describe the ordered execution requirements for an element of service, or for the contractor, an element of construction. Work plan work instructions are often best presented as checklists describing the “first this, then that” nature of work plan activities. The accurate and truthful execution of a checklist is often taken as prima facie evidence of a quality-managed process. Although checklists may appear daunting, when properly organized they simply delineate items to be considered: before design (or later, construction) services proceed in detail; during the execution of a service; before a service is deemed completed. This three-part ordering of a checklist gives it logic and follows recommendations of checklist creation experts such as Atul Gawande. A well-designed checklist will reduce errors. The CHOP features many checklists in Chapter 5.1 – Management of the Design Project. Building Information Modeling (BIM) and Quality Management “BIM is not a thing or a software but a human activity that ultimately involves broad process changes in construction.” – BIM Handbook: A Guide to Building Information Modeling for Owners, Designers, Engineers, Contractors and Facility Managers (285) Building information modeling (BIM) is beginning to radically change quality management processes across the design-construction- operation supply chain. Through the use of the same or a federated building model by all members of the design and construction teams, fabricators and manufacturers, the building, its systems, components, and elements can be coordinated on an ongoing basis. Rather than each project entity producing its own drawings – from the architect’s plans, sections and elevations, to the steel stair fabricant’s shop drawings – the model provides a consistent vehicle for communicating design, fabrication, erection, and operational information. See Chapter 5.6 – Building Information Modeling. For a discussion of quality assurance and quality control in the context of BIM, refer to the Canadian Practice Manual for BIM, Volume 2 – Company Context, Chapter 8 – Challenges, pp. 141-147. Quality Management Benefits Effective quality management systems generally pay off in the following ways: improved service and client satisfaction; improved efficiency and effectiveness and ultimately higher profit margins; improved “marketability;” greater “peace of mind” for principals and staff; improved processes and procedures which result in successful building projects; greater job satisfaction. Perhaps the greatest potential bene t of widespread implementation of quality management systems is an improved public perceptionof the architecturalprofession.Quality managementcan help to ensurethat the servicesand the work of architectsare respectedand successfullytransformedinto buildingsthat improvethe humancondition.Smallerarchitecturalpracticesmay chooseto develop a simple quality managementsystemusing the many checklistsfound in this CanadianHandbookof Practicefor https://chop.raic.ca/chapter-5.4 5/6