Chapter 41: Management Systems PDF
Document Details
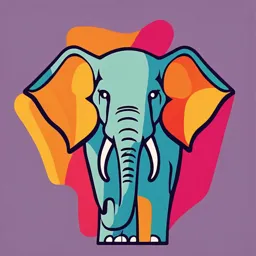
Uploaded by DependableBlankVerse7073
Embry-Riddle Aeronautical University
Tags
Summary
This document provides an overview of management systems, focusing on OSHA safety and healthy practices. It discusses workplace injuries, various safety and health program elements, and provides examples of hazards, controls, and PPE. The document also covers the importance of employee involvement and management leadership in creating a positive and safe work environment.
Full Transcript
Chapter 41: Management Systems General Duty Clause ◼ Where a specific written OSHA standard does not address a particular hazard, the General Duty Clause applies. ◼ All four of the following conditions must be met: ◼ A hazard exists in the workplace ◼ The hazard is recognize...
Chapter 41: Management Systems General Duty Clause ◼ Where a specific written OSHA standard does not address a particular hazard, the General Duty Clause applies. ◼ All four of the following conditions must be met: ◼ A hazard exists in the workplace ◼ The hazard is recognized ◼ The hazard is causing, or is likely to cause, serious physical harm to employees ◼ A feasible means exists to reduce the hazard ◼ Ergonomics, heat/cold stress, combustible dust, lasers, workplace violence Workplace Injuries ◼ Ergonomics 21-33% ◼ Heat/cold stress - 789 heat-related hospitalizations and 54 heat-related deaths from 2018 to 2021 ◼ Combustible dust – 2021:163 fires, 53 explosions, 215 injuries and 69 deaths ◼ Lasers - only 26 incidents since 1999 ◼ Workplace violence – 2020: 705 deaths and 27,000 lost-time injuries Two Approaches ◼ Comprehensive Safety and Health Program ◼ Occupational Safety and Health Management Systems OSHA Recommended Practices for Safety and Health Programs ◼ “Although compliance with the law, including specific OSHA standards, is an important objective, an effective program looks beyond specific requirements of law to address all hazards. It will seek to prevent injuries and illnesses, whether or not compliance is at issue.” (https://www.osha.gov/laws-regs/federalregister/1989-01-26) ◼ In addition, OSHA acknowledges that comprehensive safety and health programs help reduce injuries, lost workdays, and employers’ costs for workers’ compensation insurance. OSHA Recommended Practices for Safety and Health Programs ◼ OSHA’s recommended practices for an overall safety and health program emphasize a proactive approach to managing workplace safety and health rather than individual compliance programs ◼ An overall safety and health program goes beyond specific requirements of the law to address all hazards and includes provisions for systematic identification, evaluation, and prevention or control of hazards before they cause injury or illness ◼ This ultimately promotes a positive work environment and avoids the direct and indirect costs of worker injuries and illnesses OSHA’s Safety and Health System Model MANAGEMENT LEADERSHIP & WORKSITE EMPLOYEE ANALYSIS INVOLVEMENT HAZARD TRAINING PREVENTION & CONTROL OSHA’s Model OSHA’s Model Element 1 – Management Leadership ◼ Management Leadership ◼ Safety and health must be a part of the company’s mission, not just a written program on the shelf ◼ Management should set a good example (always wear PPE, obey all safety rules) ◼ Management should enforce safety rules and require a prompt response time when hazard is identified Element 2 –Employee Involvement ◼ Employee Involvement ◼ Workers know potential hazards and have a vested interest in effective protection ◼ Group input provides a wider range of experience ◼ Employees are more likely to support and use programs in which they have input Element 3- Hazard Analysis ◼ Managers and employees analyze all worksite conditions to identify and eliminate existing or potential hazards Hazard Analysis ◼ Includes all departments ◼ Reviews current tasks and proposed changes ◼ Reviews equipment condition ◼ Reviews work practices ◼ Reviews personal protective equipment ◼ Reviews injury and illness reports Element 4 – Hazard Prevention and Control When you find a hazard, controls should be selected according to this priority: Examples of Eliminating the Hazard ◼ Non-needle IV systems ◼ Placement of valves and controls at ground level ◼ Prevention through design ◼ Mechanical mechanisms rather than manual Examples of Engineering Controls ◼ Retracting and self- shielding needles ◼ GFCI on electrical outlets near water ◼ Machine guards ◼ Local exhaust ventilation ◼ Chemical fume hoods Examples of Administrative ◼ Lock-out/tag-out energy sources before equipment maintenance ◼ Prohibit recapping used needles ◼ Job rotation ◼ Housekeeping Examples of PPE ◼ Gloves ◼ Aprons ◼ Goggles ◼ Respirators ◼ Safety Glasses Element 5 – Education and Training ◼ Is appropriate training being conducted? ◼ Are employees learning what they should? ◼ Are any unsafe work practices being used? Element 6 - Program Evaluation & Review Performance can be monitored through: ◼ Safety Committee ◼ Employee feedback ◼ Self-Inspection Program ◼ Injury Investigation and Evaluation ◼ Leading and Lagging Indicators Element 7 – Host Employer/Contract Employees Host employers are responsible for the safety of some contract/temporary employees: ◼ https://www.osha.gov/sites/default/files/public ations/OSHA3735.pdf ◼ https://www.osha.gov/memos/2014-07- 15/policy-background-temporary-worker- initiative ◼ https://www.osha.gov/safety- management/communication OSHA Safety and Health Programs ◼ Recommended Practices for Safety and Health Programs https://www.osha.gov/safety- management ◼ Construction https://www.osha.gov/sites/default/files /publications/OSHA3886.pdf OUHSC Comprehensive Safety and Health Policy and Program ◼ OUHSC Comprehensive Safety and Health Policy and Program https://compliance.ouhsc.edu/Portals/1 061a/Assets/EHSO/Policies%20and%20 Programs/COMPPOLICY.pdf?ver=2019- 09-11-035137-370 Management Systems ◼ A system to establish policy and objectives and to achieve those objectives. ◼ Six common elements – ◼ Policy ◼ Planning ◼ Implementation and Operation ◼ Performance Assessment ◼ Improvement ◼ Management Review Occupational Health and Safety Management Systems (OHSMS) ◼ A system that an organization puts into place that supports an occupational health and safety policy, and provides for both achieving objectives and continual improvement ◼ Several OHSMS formats, platforms, and standards are available - the most common in the US are: ◼ ANSI/ASSP Z10.0 - 2019 Occupational Health and Safety Management Systems ◼ ISO 45001 Occupational Health and Safety OHSMS ◼ Both management systems have expectations that the organization have in place processes to assure: Management is providing direction and leadership Workers are extensively involved Resources are adequate Hazards are identified and evaluated Risks are assessed and prioritized Risk elimination, reduction, or control measures are taken Injuries and illnesses are reduced Management system deficiencies and opportunities for improvement are identified Continuing communication about the status of compliance or noncompliance so that continual improvement can be made Management constantly reviews for effectiveness ANSI/ASSP Z10.0-2019 Occupational Safety and Health Management Systems ◼ Voluntary consensus standard ◼ ASSP video https://www.youtube.com/watch?v=Fu5jrd3s -YU&t=28s ◼ ASSP free resource: https://store.assp.org/PersonifyEbusiness/Sto re/Product-Details/productId/201243100 (In Canvas) ANSI/ASSP Z10.0-2019 Occupational Safety and Health Management Systems 1. Scope, Purpose and Application 2. References 3. Definitions 4. Context of the Organization – Strategic Considerations 5. Management Leadership and Worker Participation 6. Planning 7. Support 8. Implementation and Operation 9. Evaluation and Corrective Action 10. Management Review What’s Different ◼ Setting SMART (Specific, Measurable, Achievable, Realistic/Relevant, Timebound) Goals ◼ Continual Improvement ◼ Plan-Do-Check-Act model Environmental Management Systems ◼ Purpose: ◼ Establish comprehensive environmental compliance/protection program ◼ Identify all regulations and requirements that apply to the company ◼ Establish organizational commitment ◼ Establish responsibility and accountability within the company Environmental Management Systems ◼ Not required by law ◼ Benefits: ◼ Competitive advantage in global marketplace ◼ Public image ◼ Minimize legal liabilities Basic Process in an EMS ◼ Reviewing the organization's environmental goals ◼ Analyzing its environmental impacts and compliance obligations (or legal and other requirements) ◼ Setting environmental objectives and targets to reduce environmental impacts and ensure compliance ◼ Establishing programs to meet these objectives and targets ◼ Monitoring and measuring progress in achieving the objectives ◼ Ensuring employees' environmental awareness and competence ◼ Reviewing progress of the EMS and achieving improvements EMS ◼ ISO 14001 - the World's EMS Standard (International Organization for Standardization) https://www.youtube.com/watch?v=J7Fak8Q I6Ww&t=31s ◼ What is Environmental Management System? https://www.youtube.com/watch?v=teco- gm9qF0&t=13s ISO 14000/14001 ◼ “ISO 14000 is a global series of environmental management systems (EMS) standards, providing a framework for organizations to demonstrate their commitment to environmental responsibility. ◼ An EMS enables an organization to control the environmental aspects and impacts of its activities, products and services by establishing targets and objectives related to identified environmental management goals. Once implemented, an EMS will improve compliance with legislative and regulatory requirements, reduce exposure to liability, prevent pollution, reduce waste and create a more positive public image. ◼ Organizations that register to ISO 14001, the most important of the ISO 14000 standards, demonstrate sound environmental management practices, are able to prevent environmental disasters and government sanctions, and experience fewer regulatory audits by correcting environmental problems. ISO 14000 supporting documents include environmental labeling, life-cycle assessment, environmental aspects in product standards, and environmental performance evaluation.” ISO 14001 ◼ Environmental Management System ◼ Audit process to verify that the organization is doing what it says it will do ◼ Continual improvement ◼ Plan-do-check-adjust (or act) model ◼ Is not a checklist for compliance 4.2 Policy Environmental Policy 4.3 Planning Environmental Aspects Legal & Other Objectives & Targets Requirements and Programs 4.4 Implementation & Competence, Training Documentation Operation and Awareness Resources, Roles, Operational Control Communication Responsibility and Authority Emergency Preparedness Control of Documents & Response Monitoring & 4.5 Checking Evaluation of Compliance Measurement Nonconformity, Corrective Action & Preventive Action Control of Records Internal Audit ISO 14001 Standard 4.6 Management Management Review Review Environmental Policy Declares your organization’s commitment to the environment. Provides the framework for planning and action. Environmental Aspects Identify environmental attributes of your activities, products and services Determine which aspects that could have significant impacts on the environment “Significant Environmental Aspects and Associated Impacts” ◼ ISO 14001 requires that companies identify the environmental aspects of the activities, products, and services that have, or may have, a significant environmental impact ◼ Aspect: “an element of an organization's activities or products or services that interacts or can interact with the environment” ◼ Impact: “A change to the environment, whether adverse or beneficial, wholly or partially resulting from an organization's environmental aspects.” ◼ Overall “risk footprint” and is to consider the full lifecycle of the product ISO 14001 ◼ ”Consistent with a life cycle perspective, the organization shall: ◼ establish controls as appropriate to ensure that its environmental requirement(s) are addressed in the design and development process for the product or service, considering each stage of its life cycle; ◼ determine its environmental requirement(s) for the procurement of products and services as appropriate; ◼ communicate its relevant environmental requirement(s) to external providers, including contractors; ◼ consider the need to provide information about potential significant environmental impacts associated with the transportation or delivery, use, end-of-life treatment and final disposal of its products and services.” Product Stewardship ◼ The concept of product stewardship, according to AIHA is "responsibly managing the health, safety, and environmental aspects of raw materials, intermediate, and consumer products throughout their life cycle and across the value chain in order to prevent or minimize negative impacts and maximize value" Product Stewardship ◼ The principles of product stewardship and sustainability include an evaluation of product life-cycle analysis and sustainable product development, which consider the potential hazards during development, production, use and disposal and address appropriate practices such as substitution, waste minimization and recycle/reuse/repurpose up front rather than at the end of the life cycle Procurement ◼ Supply chain accountability ◼ Environmental polluters ◼ Child labor (Nike) ◼ Examples: ◼ Nike Shoe Plant in Vietnam Is Called Unsafe for Workers: a front page article in the New York Times 1997 ◼ “toluene…was in the air at different sites in the factory studied at 6 to 177 times the amount allowed by Vietnamese regulations, which itself is about four times as strict as American toluene standards” ◼ Apple criticized for China supply chain pollution (2011) ◼ Ikea’s main supplier in Brazil accused of environmental damage (2024) ◼ Shipping emissions Walmart, Target and Home Depot 2021 Legal and Other Requirements Identify and ensure access to relevant laws and regulations (and other requirements to which your organization adheres) Objectives, Targets and Programs Establish environmental goals for your organization, in line with your policy, your environmental aspects, impacts, views of management, and other factors Action plans to achieve objectives and targets Resources, Roles, Responsibility and Authority Establish roles and responsibilities and provide resources, with clear designation of authority Competence, Training and Awareness Ensure that your employees are trained and capable of carrying out environmental responsibilities Communication Establish processes for internal and external communication of the environmental management issues. Virginia EMS Conference 48 Operational Control Identify, plan and manage your operations and activities in line with your policy, objectives and targets Emergency Preparedness and Response Identify potential emergencies and develop procedures for preventing emergencies and responding to them Evaluation of Compliance Periodically evaluate the legal and other requirements Keep records of the results Nonconformity, Corrective Action & Preventive Action Identify and correct problems; prevent recurrences. 52 Documentation Keep adequate records of EMS performance. Internal Audit Periodically, review your commitments, verify that your EMS is operating as intended Report the audit results to senior management Management Review Review the EMS with an eye to continual improvement EMS Supporting Documents (objective evidence) Elements of the ISO 14001:2004 Standard Procedure Work Product on Paper 1. Environmental Policy 4.2 Policy 2. Environmental Aspects 4.3.1 Matrix 3. Legal & Other Requirements 4.3.2 Matrix 4. Objectives, Targets and Programs 4.3.3 Template or matrix of programs 5. Resources, Roles, Responsibility and Authority 4.4.1 Organization chart 6. Competence, Training and Awareness 4.4.2 Needs matrix, schedule & records 7. Communication 4.4.3 Memos, log sheets, news letters 8. Documentation 4.4.4 Flow chart (document structure) 9. Control of Documents 4.4.5 Flow chart (approval & revisions) 10. Operational Control 4.4.6 SOP’s, contractor packet 11. Emergency Preparedness & Response 4.4.7 Plans, inspections 12. Monitoring & Measurement 4.5.1 2 types of tracking matrix 13. Evaluation of Compliance 4.5.2 Compliance audit results 14. Nonconformity, Corrective & Preventive Action 4.5.3 Competed corrective action form 15. Control of Records 4.5.4 Retention time matrix 16. Internal Audit 4.5.5 Audit schedule & results October 2008 Virginia EMS Conference 56 17. Management Review 4.6 Reports, meeting minutes Return on Investment The Tip of the Iceberg Direct Costs: ◼ Medical treatment (physician, hospital, ambulance) ◼ Compensation to worker for time off Indirect Costs: ◼ Overtime costs or temporary worker cost to DIRECT cover for injured employee ◼ Decreased morale and productivity ◼ Increased employee turnover ◼ Retraining INDIRECT ◼ Spoiled product ◼ Unhappy customers ◼ Cleanup time ◼ Schedule delays ◼ Expenditures for return-to-work programs and job accommodations for injured workers ◼ Increased workers’ compensation and other insurance costs ◼ Accident investigation/reports/paperwork ◼ Production time lost by the injured employee, fellow workers and supervisors ◼ Legal fees OUHSC Example ◼ In 1989, OUHSC established the Environmental Health and Safety Office (EHSO) with a preliminary goal of providing required annual safety and health training to the large and varied employee pool, that primarily consists of healthcare, laboratory and office personal ◼ The OUHSC Site Support department performs construction and building maintenance activities on campus, and includes the Carpentry, Electric, Landscape, Paint, Air Conditioning, Plumbing, Biomedical Equipment and Utility Control Shops. In 1995, it was determined that Site Support employees were not attending/receiving safety training being offered. Reasons given included: ◼ lack of appropriateness of the training sessions (the general sessions were geared towards healthcare, laboratory, or office personnel and not geared towards the hazards encountered in the Site Support shops); ◼ length of time required to be in training and away from the job at hand; and ◼ accounting concerns that require billing for every hour of each Site Support employee's time against some account, resulting in time in training being billed against a building maintenance account. OUHSC Example ◼ Through a cooperative effort on both parts, the EHSO and Site Support agreed to a trial arrangement which included employee safety training sessions which were: ◼ held approximately weekly in each of eight individual shops; ◼ tailored to that shop's hazards and procedures; ◼ 15-30 minutes in length; and ◼ held at the beginning of the day or immediately after a break (while all employees were at the shop already). ◼ Note, this was long before the advent of online training, which we subsequently developed and implemented ◼ The following slides showed the return on investment that was presented to administration following the first two years of implementation The first year shown is prior to implementing training. The first year of training was 95-96, and the reason the medical costs went up is because the employees were never told how to report on the job injuries prior to this. However, you can see that the OTJ injuries went down subsequent years after initiating training. This slide shows that yes, the lost billable time in training increased. However, after the first couple of years, we were able to do more refresher training rather than initial training, so the time was reduced. The argument that the department lost billable income when employees weren’t out working and were in training was offset by the fact that when they were off injured, they also didn’t bring in income for the department. The lost billable time was clearly recovered when training was implemented. So yes, the first year there were increased costs associated with implementing the training program, and educating workers on how to report OTJ injuries, but after the process was able to continue, the overall savings to the department could easily be seen Ways to Show Return on Investment ◼ OSHA’s Safety Pays ◼ https://www.osha.gov/safetypays ◼ https://www.osha.gov/safetypays/tool ◼ ASSE ◼ http://www.asse.org/professionalaffairs/roi/ ◼ https://web.archive.org/web/20170809112713/http://www.asse.org/ass ets/1/7/How_to_Promote_the_Business_Value_of_EHS.pdf ◼ https://web.archive.org/web/20150305074825/http://www.asse.org/bos c-article-6/ or https://elcosh.org/document/1082/d000047/asse-white- paper-addressing-the-return-on-investment-for-safety,-health-and- environmental-(sh&e)-management-programs.html ◼ AIHA ◼ The Business Case for EHS ◼ AIHA Strategy to Demonstrate the Value of Industrial Hygiene ◼ AIHA-IH Value-Case Study 1 Other Resources ◼ The ROI of safety https://www.safetyandhealthmagazine. com/articles/17819-the-roi-of-safety Bottom Line – SAFETY PAYS! Having an effective safety and health program will: ◼ Reduce injury, illness, and absenteeism ◼ Reduce workers’ comp costs ◼ Increase productivity and morale ◼ Decrease potential for regulatory fines ◼ Decrease potential for fire hazards, insurance costs, and other risk management issues ◼ Homework 6