CH4-BF-gpoe_2024.pdf
Document Details
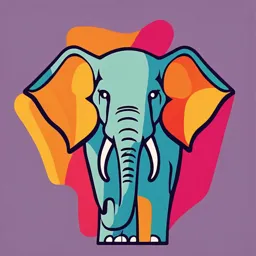
Uploaded by PraisingCerium
2024
Tags
Full Transcript
Chapter – 4 BLAST FURNACES 4.1 Introduction BF is a counter current heat and mass exchanger, in which solid raw materials are charged from the top of the furnace and hot blast, is sent through the bottom via tuyeres. The heat is transferred from the gas to the burden and oxygen from the burden to th...
Chapter – 4 BLAST FURNACES 4.1 Introduction BF is a counter current heat and mass exchanger, in which solid raw materials are charged from the top of the furnace and hot blast, is sent through the bottom via tuyeres. The heat is transferred from the gas to the burden and oxygen from the burden to the gas. Gas ascends up the furnace while burden and coke descend down through the furnace. The counter current nature of the reactions makes the overall process an extremely efficient one in reducing atmosphere. The real growth of blast furnace technology came with the production of high strength coke which enabled the construction of large size blast furnaces. 4.2 Raw materials and their quality In India steel is being produced largely through the blast furnace. Iron ore, sinter and coke are the major raw materials for blast furnace smelting. Raw materials: The following raw materials usedfor the production of pig iron: (i) Iron ore (ii) Limestone / L D Slag (iii)Dolomite (iv) Quartzite (v) Manganese ore (vi) Sinter (vii) Coke (viii) Pellets (ix) Scrap (Steel / Iron) (x) Coal Dust / Coal Tar Iron ore: Iron bearing materials; provides iron to the hot metal. Iron ores is available in the form of oxides, sulphides, and carbonate, the oxide form known as hematite (red in colour) is mostly used in SAIL plants. It is the principal mineral in blast furnace for extraction of pig iron, generally rich in iron content varying from 62 % to 66 % associated often with naturally occurring fines (-10 MM) to the extent of 20 %. Although relatively free from impurities like phosphorous, sulphur and copper, they have high aluminaand silica contentas gangue. The high alumina content makes the slag highly viscous and creates problems for stable furnace operation. Limestone / LD Slag: Acts as flux. Helps in reducing the melting point of gangue present in the iron bearing material and combines effectively with acidic impurities to form slag in iron making. LD slag is a substitute for limestone which is easily available in a steel plant. Its usage helps in waste utilization and thus reduces production cost. 43 Quartzite: It acts as an additive.Quartzite is a mineral of SiO2 (silica) and under normal circumstances contains about 96 – 97 % of SiO2 rest being impurities. Quartzite plays its role in counteracting the bad effects of high alumina in slag through maintaining optimum slag basicity. Manganese ore: It acts as additive for the supply of Manganese in the hot metal. Manganese ore is available in the form of combined oxides of Mn and Fe and usual content of Mn is about 28 – 32 % for steel plant use, However Manganese ore available with SAIL is having high alkali contents so it should be used judicially. Coke: Itacts as a reductant and fuel, supports the burden and helps in maintaining permeable bed. Coke (metallurgical) used in blast furnace both as fuel & reducing agent. The Indian coal is characterized by high ash (25 – 30 %) and still worse, a wide fluctuation in ash content, poor coke strength leading to excessive generation of fines, rapid fluctuation in moisture content etc. The problem of poor quality coke has been tackled by adding imported coal (75-95%) in the indigenous coal blend to get a coke ash of 13 – 16 %. Sinter: It is iron bearing material. Fines that are generated in the plant/mines are effectively utilized by converting them to sinter. It provides the extra lime required for the iron ore and coke ash that is charged in the blast furnace. Sintering is the process of agglomeration of fines (steel plant waste and iron ore fines) by incipient fusion caused by heat available from the coke contained in the charge. The lumpy porous mass thus obtained is known as “sinter”. Scrap (Steel / Iron): Scrap is generrated in the process of product making in a steel plant which is gainfully utilized by back charging in the Blast Furnaces. It increases the furnaces productivity and reduces the production cost. Pellets: It is also an iron bearing materials. The micro-fines which cannot be used for sinter making can be used for pellet manufacturing and the pellets formed will be charged in the BF. Coal dust Injection: It acts as an auxiliary fuel, reduces coke consumption in the blast furnaces. The coal is injected through the tuyeres. 44 Different sources of raw materials Sl. No. Raw material 1. Iron ore 2. Limestone 3. Dolomite 3 BSP RSP DSP ISP Dalli Rajhara Raoghat Meghahatubur u Kiriburu Barsua Bolani Kalta GuaMeghaha Meghahatuburu tuburu Kiriburu Gua Bolani Meghahatubu ru Nandini Kuteswar Jaisalmer Imported Hirri Imported Kuteswar Jaisalmer Imported Kuteswar Jaisalmer Imported Jaisalmer Imported Baraduar Belha Baraduar Imported Belha Baraduar Imported BSL Kiriburu Meghahatubur u Bolani Barsua Gua Manoharpur Nandini Kuteswar Jaisalmer Imported Birmitrapur Belha Imported Quality of raw materials Material Iron Ore(Lumps) Sinter Coke Chemical Analysis Specification Fe 61.0% min. SiO2 P Al2O3/SiO2 2.5 ± 0.5 % 0.10% max. 0.70 max. Fe 50-58% FeO 7-10% SiO2 4-6% Al2O3 2-3% CaO MgO 9 – 13% 2 – 3% Ash 13 – 15% VM(VOLATILE MATTER) 70 Softening Melting range: 1200 – 1450oC CRI(Coke Reactivity Index): 21 -23 CSR(Coke Strength after Reduction) > 64 Limestone LD slag Mn ore CDI coal Quartzite Moisture S FIXED C CaO SiO2 MgO CaO MgO SiO2 Mn SiO2 Al2O3 P FIXED C VM(VOLATILE MATTER) Ash SiO2 Al2O3 5 ± 0.5% 0.5 - 0.6% 82- 85% 38 % min. 6.5 ± 1% 8.5 ± 0.5% 40.8 ± 1% 10.5 ± 0.5% 15.50% 30% min. 30% max. 5% max. 0.30% max. 60-70% 20-25% 9 – 11% 96% min 1.5% max M40 >80% M10