Aircraft Fabric Covering PDF
Document Details
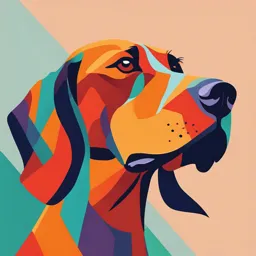
Uploaded by DaringDream
Tags
Summary
This document provides a comprehensive overview of aircraft fabric covering, from the historical use of organic fabrics to modern polyester options. It details the different materials and processes used in fabric covering, including types of dope coatings and other supplemental materials. The document also touches upon legal aspects of fabric covering and various testing methods.
Full Transcript
Chapter 3 Aircraft Fabric Covering General History Fabric-covered aircraft play an important role in the history of aviation. The famous Wright Flyer utilized a fabric-covered wood frame in its design, and fabric covering continued to be used by many aircraft designers and builders during the early...
Chapter 3 Aircraft Fabric Covering General History Fabric-covered aircraft play an important role in the history of aviation. The famous Wright Flyer utilized a fabric-covered wood frame in its design, and fabric covering continued to be used by many aircraft designers and builders during the early decades of production aircraft. The use of fabric covering on an aircraft offers one primary advantage: light weight. In contrast, fabric coverings have two disadvantages: flammability and lack of durability. Finely woven organic fabrics, such as Irish linen and cotton, were the original fabrics used for covering airframes, but their tendency to sag left the aircraft structure exposed to the elements. To counter this problem, builders began coating the fabrics with oils and varnishes. In 1916, a mixture of cellulose dissolved in nitric acid, called nitrate dope, came into use as an aircraft fabric coating. Nitrate dope protected the fabric, adhered to it well, and tautened it over the airframe. It also gave the fabric a smooth, durable finish when dried. The major drawback to nitrate dope was its extreme flammability. To address the flammability issue, aircraft designers tried a preparation of cellulose dissolved in butyric acid called butyrate dope. This mixture protected the fabric from dirt and moisture, but it did not adhere as well to the fabric as nitrate dope. Eventually, a system combining the two dope coatings was developed. First, the fabric was coated with nitrate dope for its adhesion and protective qualities. Then, subsequent coats of butyrate dope were added. Since the butyrate dope coatings reduced the overall flammability of the fabric covering, this system became the standard fabric treatment system. The second problem, lack of durability, stems from the eventual deterioration of fabric from exposure to the elements that results in a limited service life. Although the mixture of nitrate dope and butyrate dope kept out dirt and water, solving some of the degradation issue, it did not address deterioration caused by ultraviolet (UV) radiation from the sun. Ultraviolet radiation passed through the dope and degraded not only the fabric, but also the aircraft structure underneath. Attempts to paint the coated fabric proved unsuccessful, because paint does not adhere well to nitrate dope. Eventually, aluminum solids were added to the butyrate coatings. This mixture reflected the sun’s rays, prevented harmful UV rays from penetrating the dope, and protected the fabric, as well as the aircraft structure. Regardless of treatments, organic fabrics have a limited lifespan; cotton or linen covering on an actively flown aircraft lasts only about 5–10 years. Furthermore, aircraft cotton has not been available for over 25 years. As the aviation industry developed more powerful engines and more aerodynamic aircraft structures, aluminum became the material of choice. Its use in engines, aircraft frames, and coverings revolutionized aviation. As a covering, aluminum protected the aircraft structure from the elements, was durable, and was not flammable. Although aluminum and composite aircraft dominate modern aviation, advances in fabric coverings continue to be made because gliders, home-built, and light sport aircraft, as well as some standard and utility certificated aircraft, are still produced with fabric coverings. [Figure 3-1] The nitrate/ butyrate dope process works well, but does not mitigate the short lifespan of organic fabrics. It was not until the introduction of polyester fabric as an aircraft covering in the 1950s that the problem of the limited lifespan of fabric covering was solved. The transition to polyester fabric had some problems because the nitrate and butyrate dope coating Figure 3-1. Examples of aircraft produced using fabric skin. 3-1 process is not as suitable for polyester as it is for organic fabrics. Upon initial application of the dopes to polyester, good adhesion and protection occurred; as the dopes dried, they would eventually separate from the fabric. In other words, the fabric outlasted the coating. Re-covering existing fabric aircraft is an accepted maintenance procedure. Not all aircraft covering systems include the use of dope coating processes. Modern aircraft covering systems that include the use of nondope fabric treatments show no signs of deterioration even after decades of service. In this chapter, various fabrics and treatment systems are discussed, as well as basic covering techniques. Warp as Bi Selvage edge Fill Selvage edge Eventually, dope additives were developed that minimized the separation problem. For example, plasticizers keep the dried dope flexible and nontautening dope formulas eliminate separation of the coatings from the fabric. Properly protected and coated, polyester lasts indefinitely and is stronger than cotton or linen. Today, polyester fabric coverings are the standard and use of cotton and linen on United States certificated aircraft has ceased. In fact, the long staple cotton from which grade-A cotton aircraft fabric is made is no longer produced in this country. Pinked edge Figure 3-2. Aircraft fabric nomenclature. Fabric Terms To facilitate the discussion of fabric coverings for aircraft, the following definitions are presented. Figure 3-2 illustrates some of these items. Warp—the direction along the length of fabric. Fill or weave—the direction across the width of the fabric. Count—the number of threads per inch in warp or filling. Ply—the number of yarns making up a thread. Bias—a cut, fold, or seam made diagonally to the warp or fill threads. Pinked edge—an edge which has been cut by machine or special pinking shears in a continuous series of Vs to prevent raveling. Selvage edge—the edge of cloth, tape, or webbing woven to prevent raveling. Greige—condition of polyester fabric upon completion of the production process before being heat shrunk. Cross-coat—brushing or spraying where the second coat is applied 90° to the direction the first coat was applied. The two coats together make a single cross coat. [Figure 3-3] Legal Aspects of Fabric Covering When a fabric-covered aircraft is certificated, the aircraft manufacturer uses materials and techniques to cover the aircraft that are approved under the type certificate issued for that aircraft. The same materials and techniques must be used by maintenance personnel when replacing the aircraft fabric. Descriptions of these materials and techniques are in the manufacturer’s service manual. For example, aircraft originally manufactured with cotton fabric can only be re-covered with cotton fabric unless the Federal Aviation Administration (FAA) approves an exception. Approved exceptions for alternate fabric-covering materials and procedures are common. Since polyester fabric coverings deliver performance advantages, such as lighter weight, longer life, additional strength, and lower cost, many older aircraft originally manufactured with cotton fabric have received approved alteration authority and have been recovered with polyester fabric. There are three ways to gain FAA approval to re-cover an aircraft with materials and processes other than those with which it was originally certificated. One is to do the work in accordance with an approved supplemental type certificate (STC). The STC must specify that it is for the particular aircraft model in question. It states in detail exactly what alternate materials must be used and what procedure(s) must be followed. Deviation from the STC data in any way renders 3-2 First application Second application (applied when first coat is tacky) Figure 3-3. A single cross coat is made up of two coats of paint applied 90° to each other. the aircraft unairworthy. The holder of the STC typically sells the materials and the use of the STC to the person wishing to re-cover the aircraft. The second way to gain approval to re-cover an aircraft with different materials and processes is with a field approval. A field approval is a one-time approval issued by the FAA Flight Standards District Office (FSDO) permitting the materials and procedures requested to replace those of the original manufacturer. A field approval request is made on FAA Form 337. A thorough description of the materials and processes must be submitted with proof that, when the alteration is completed, the aircraft meets or exceeds the performance parameters set forth by the original type certificate. The third way is for a manufacturer to secure approval through the Type Certificate Data Sheet (TCDS) for a new process. For example, Piper Aircraft Co. originally covered their PA-18s in cotton. Later, they secured approval to recover their aircraft with Dacron fabric. Recovering an older PA-18 with Dacron in accordance with the TCDS would be a major repair, but not an alteration as the TCDS holder has current approval for the fabric. Advisory Circular (AC) 43.13-1, Acceptable Methods, Techniques, and Practices—Aircraft Inspection and Repair, contains acceptable practices for covering aircraft with fabric. It is a valuable source of general and specific information on fabric and fabric repair that can be used on Form 337 to justify procedures requested for a field approval. Submitting an FAA Form 337 does not guarantee a requested field approval. The FSDO inspector considers all aspects of the procedures and their effect(s) on the aircraft for which the request is being filed. Additional data may be required for approval. Title 14 of the Code of Federal Regulations (14 CFR) part 43, Appendix A, states which maintenance actions are considered major repairs and which actions are considered major alterations. Fabric re-covering is considered a major repair and FAA Form 337 is executed whenever an aircraft is re-covered with fabric. Appendix A also states that changing parts of an aircraft wing, tail surface, or fuselage when not listed in the aircraft specifications issued by the FAA is a major alteration. This means that replacing cotton fabric with polyester fabric is a major alteration. A properly executed FAA Form 337 also needs to be approved in order for this alteration to be legal. FAA Form 337, which satisfies the documentation requirements for major fabric repairs and alterations, requires participation of an FAA-certificated Airframe and Powerplant (A&P) mechanic with an Inspection Authorization (IA) in the re-covering process. Often the work involved in re-covering a fabric aircraft is performed by someone else, but under the supervision of the IA (IA certification requires A&P certification). This typically means the IA inspects the aircraft structure and the re-cover job at various stages to be sure STC or field approval specifications are being followed. The signatures of the IA and the FSDO inspector are required on the approved FAA Form 337. The aircraft logbook also must be signed by the FAA-certificated A&P mechanic. It is important to contact the local FSDO before making any major repair or alteration. Approved Materials There are a variety of approved materials used in aircraft fabric covering and repair processes. In order for the items to legally be used, the FAA must approve the fabric, tapes, threads, cords, glues, dopes, sealants, coatings, thinners, additives, fungicides, rejuvenators, and paints for the manufacturer, the holder of an STC, or a field approval. Fabric A Technical Standard Order (TSO) is a minimum performance standard issued by the FAA for specified materials, parts, 3-3 processes, and appliances used on civil aircraft. For example, TSO-C15d, Aircraft Fabric, Grade A, prescribes the minimum performance standards that approved aircraft fabric must meet. Fabric that meets or exceeds the TSO can be used as a covering. Fabric approved to replace Grade-A cotton, such as polyester, must meet the same criteria. TSO-C15d also refers to another document, Society of Automotive Engineers (SAE) Aerospace Material Specification (AMS) 3806D, which details properties a fabric must contain to be an approved fabric for airplane cloth. Lighter weight fabrics typically adhere to the specifications in TSO-C14b, which refers to SAEAMS 3804C. When a company is approved to manufacture or sell an approved aviation fabric, it applies for and receives a Parts Manufacturer Approval (PMA). Currently, only a few approved fabrics are used for aircraft coverings, such as the polyester fabrics Ceconite™, Stits/Polyfiber™, and Superflite™. These fabrics and some of their characteristics are shown in Figure 3-4. The holders of the PMA for these fabrics have also developed and gained approval for the various tapes, chords, threads, and liquids that are used in the covering process. These approved materials, along with the procedures for using them, constitute the STCs for each particular fabric covering process. Only the approved materials can be used. Substitution of other materials is forbidden and results in the aircraft being unairworthy. Other Fabric Covering Materials The following is an introduction to the supplemental materials used to complete a fabric covering job per manufacturer’s instruction or a STC. Anti-Chafe Tape Anti-chafe tape is used on sharp protrusions, rib caps, metal seams, and other areas to provide a smoother surface to keep the fabric from being torn. It is usually self-adhesive cloth tape and is applied after the aircraft is cleaned, inspected, and primed, but before the fabric is installed. Reinforcing Tape Reinforcing tape is most commonly used on rib caps after the fabric covering is installed to protect and strengthen the area for attaching the fabric to the ribs. Rib Bracing Rib bracing tape is used on wing ribs before the fabric is installed. It is applied spanwise and alternately wrapped around a top rib cap and then a bottom rib cap progressing from rib to rib until all are braced. [Figure 3-5] Lacing the ribs in this manner holds them in the proper place and alignment during the covering process. Surface Tape Surface tape, made of polyester material and often preshrunk, is obtained from the STC holder. This tape, also known as finishing tape, is applied after the fabric is installed. It is used over seams, ribs, patches, and edges. Surface tape can have straight or pinked edges and comes in various widths. For curved surfaces, bias cut tape is available, which allows the tape to be shaped around a radius. Approved Aircraft Fabrics Fabric Name or Type Weight (oz/sq yd) Count (warp x fill) New Breaking Strength (lb) (warp, fill) Minimum Deteriorated Breaking Strength TSO Ceconite™ 101 3.5 69 x 63 125,116 70% of original specified fabric C-15d Ceconite™ 102 3.16 60 x 60 106,113 70% of original specified fabric C-15d Polyfiber™ Heavy Duty-3 3.5 69 x 63 125,116 70% of original specified fabric C-15d Polyfiber™ Medium-3 3.16 60 x 60 106,113 70% of original specified fabric C-15d Polyfiber™ Uncertified Light 1.87 90 x 76 66,72 uncertified Superflight™ SF 101 3.7 70 x 51 80,130 70% of original specified fabric C-15d Superflight™ SF 102 2.7 72 x 64 90,90 70% of original specified fabric C-15d Superflight™ SF 104 1.8 94 x 91 75,55 uncertified Grade A Cotton 4.5 80 x 84 80,80 56 lb/in (70% of New) C-15d Figure 3-4. Approved fabrics for covering aircraft. 3-4 Clips Martin clip Trailing edge Rib cap Section of rib Screws Figure 3-5. Inter-rib bracing holds the ribs in place during the covering process. PK screw Rib Lacing Cord Washer Rib lacing cord is used to lace the fabric to the wing ribs. It must be strong and applied as directed to safely transfer in-flight loads from the fabric to the ribs. Rib lacing cord is available in a round or flat cross-section. The round cord is easier to use than the flat lacing, but if installed properly, the flat lacing results in a smoother finish over the ribs. Reinforcing tape Sewing Thread Fabric Rib Rivets Sewing of polyester fabric is rare and mostly limited to the creation of prefitted envelopes used in the envelope method covering process. When a fabric seam must be made with no structure underneath it, a sewn seam could be used. Polyester threads of various specifications are used on polyester fabric. Different thread is specified for hand sewing versus machine sewing. For hand sewing, the thread is typically a three-ply, uncoated polyester thread with a 15-pound tensile strength. Machine thread is typically four-ply polyester with a 10pound tensile strength. Special Fabric Fasteners Each fabric covering job involves a method of attaching the fabric to wing and empennage ribs. The original manufacturer’s method of fastening should be used. In addition to lacing the fabric to the ribs with approved rib lacing cord, special clips, screws, and rivets are employed on some aircraft. [Figure 3-6] The first step in using any of these fasteners is to inspect the holes into which they fit. Worn holes may have to be enlarged or re-drilled according to the manufacturer’s instructions. Use of approved fasteners is mandatory. Use of unapproved fasteners can render the covering job unairworthy if substituted. Screws and rivets often incorporate the use of a plastic or aluminum washer. All fasteners and rib lacing are covered with finishing tape once installed to provide a smooth finish and airflow. Lace Figure 3-6. Clips, screws, rivets, or lace are used to attach the fabric to wing and empennage ribs. 3-5 Primer Figure 3-7. Plastic, aluminum, and seaplane grommets are used to reinforce drain holes in the fabric covering. Grommets Grommets are used to create reinforced drain holes in the aircraft fabric. Usually made of aluminum or plastic, they are glued or doped into place on the fabric surface. Once secured, a hole is created in the fabric through the center of the grommet. Often, this is done with a hot soldering pencil that also heat seals the fabric edge to prevent raveling. Seaplane grommets have a shield over the drain hole to prevent splashed water from entering the interior of the covered structure and to assist in siphoning out any water from within. [Figure 3-7] Drain holes using these grommets must be made before the grommets are put in place. Note that some drain holes do not require grommets if they are made through two layers of fabric. Inspection Rings The structure underneath an aircraft covering must be inspected periodically. To facilitate this in fabric-covered aircraft, inspection rings are glued or doped to the fabric. They provide a stable rim around an area of fabric that can be cut to allow viewing of the structure underneath. The fabric remains uncut until an inspection is desired. The rings are typically plastic or aluminum with an approximately threeinch inside diameter. Spring clip metal panel covers can be fitted to close the area once the fabric inside the inspection ring has been cut for access. [Figure 3-8] The location of the inspection rings are specified by the manufacturer. Additional rings are sometimes added to permit access to important areas that may not have been fitted originally with inspection access. The airframe structure of a fabric covered aircraft must be cleaned, inspected, and prepared before the fabric covering process begins. The final preparation procedure involves priming the structure with a treatment that works with the adhesive and first coats of fabric sealant that are to be utilized. Each STC specifies which primers, or if a wood structure, which varnishes are suitable. Most often, two-part epoxy primers are used on metal structure and two-part epoxy varnishes are used on wood structure. Utilize the primer specified by the manufacturer’s or STC’s instructions. Fabric Cement Modern fabric covering systems utilize special fabric cement to attach the fabric to the airframe. There are various types of cement. [Figure 3-9] In addition to good adhesion qualities, flexibility, and long life, fabric cements must be compatible with the primer and the fabric sealer that are applied before and after the cement. Fabric Sealer Fabric sealer surrounds the fibers in the fabric with a protective coating to provide adhesion and keep out dirt and moisture. The sealer is the first coat applied to the polyester fabric after it is attached to the airframe and heat shrunk to fit snugly. Dope-based fabric coating systems utilize nontautening nitrate dope as the primary fabric sealant. The application of tautening dope may cause the fabric to become too taut resulting in excess stress on the airframe that could damage it. Nondope coating systems use proprietary sealers that are also nontautening. [Figure 3-9] Fillers After the fabric sealer is applied, a filler is used. It is sprayed on in a number of cross coats as required by the manufacturer or the fabric covering process STC. The filler contains solids or chemicals that are included to block UV light from reaching the fabric. Proper fill coating is critical because UV light is the single most destructive element that causes polyester fabric to deteriorate. Dope-based processes use butyrate dope fillers while other processes have their own proprietary formulas. When fillers and sealers are combined, they are known as fabric primers. Aluminum pastes and powders, formerly added to butyrate dope to provide the UV protection, have been replaced by premixed formulas. Topcoats Figure 3-8. Inspection rings and an inspection cover. Once the aircraft fabric has been installed, sealed, and fillcoat protected, finishing or topcoats are applied to give the aircraft its final appearance. Colored butyrate dope is common in dope-based processes, but various polyurethane topcoats are also available. It is important to use the topcoat 3-6 Aircraft Covering Systems APPROVED PROPRIETARY PRODUCT NAME Covering System Air-Tech STC # SA7965SW Allowable Fabrics Ceconite™ Poly-Fiber™ Superflite™ Base Urethane Cement UA-55 Water Filler UV Block PFU 1020 PFU 1030 PFU 1020 PFU 1030 PFUW 1050 PFUW 1050 Topcoats CHSM Color Coat Ceconite™/ Randolph System SA4503NM Ceconite™ Dope New Super Seam Nitrate Dope Rand-O-Fill Colored Butyrate Dope Ranthane Polyurethane Stits/Poly-Fiber™ SA1008WE Poly-Fiber™ Vinyl Poly-tak Poly-brush Poly-spray Vinyl Poly-tone, Aero-Thane, or Ranthane Polyurethane Stewart System SA01734SE Ceconite™ Poly-Fiber™ Water-borne EkoBond EkoFill EkoFIll EkoPoly Superflite™ System1 System VI SA00478CH and others Superflite™ 101,102 Superflite™ 101,102 Dope U-500 Dacproofer SrayFil Urethane U-500 SF6500 SF6500 Tinted Butyrate Dope Superflite™ CAB Figure 3-9. Examples of FAA-approved fabric covering processes. above the ideal temperature for a product. It also can be used to prevent blushing of a dope finish when high humidity conditions exist. products and procedures specified in the applicable STC to complete an airworthy fabric re-covering job. The use of various additives is common at different stages when utilizing the above products. The following is a short list of additional products that facilitate the proper application of the fabric coatings. Note again that only products approved under a particular STC can be used. Substitution of similar products, even though they perform the same basic function, is not allowed. A catalyst accelerates a chemical reaction. Catalysts are specifically designed for each product with which they are mixed. They are commonly used with epoxies and polyurethanes. A thinner is a solvent or mixture of solvents added to a product to give it the proper consistency for application, such as when spraying or brushing. A retarder is added to a product to slow drying time. Used mostly in dope processes and topcoats, a retarder allow more time for a sprayed coating to flow and level, resulting in a deeper, glossier finish. It is used when the working temperature is elevated slightly An accelerators contains solvents that speed up the drying time of the product with which it is mixed. It is typically used when the application working temperature is below that of the ideal working temperature. It can also be used for faster drying when airborne contaminants threaten a coating finish. Rejuvenator, used on dope finishes only, contains solvents that soften coatings and allow them to flow slightly. Rejuvenator also contains fresh plasticizers that mix into the original coatings. This increases the overall flexibility and life of the coatings. Fungicide and mildewicide additives are important for organic fabric covered aircraft because fabrics, such as cotton and linen, are hosts for fungus and mildew. Since fungus and mildew are not concerns when using polyester fabric, these additives are not required. Modern coating formulas contain premixed anti-fungal agents, providing sufficient insurance against the problem of fungus or mildew. 3-7 Available Covering Processes The covering processes that utilize polyester fabric are the primary focus of this chapter. Examples of FAA-approved aircraft covering processes are listed in Figure 3-9. The processes can be distinguished by the chemical nature of the glue and coatings that are used. A dope-based covering process has been refined out of the cotton fabric era, with excellent results on polyester fabric. In particular, plasticizers added to the nitrate and butyrate dopes minimize the shrinking and tautening effects of the dope, establish flexibility, and allow esthetically pleasing tinted butyrate dope finishes that last indefinitely. Durable polyurethane-based processes integrate well with durable polyurethane topcoat finishes. Vinyl is the key ingredient in the popular Poly-Fiber covering system. Air Tech uses an acetone thinned polyurethane compatible system. The most recent entry into the covering systems market is the Stewart Finishing System that uses waterborne technology to apply polyurethane coatings to the fabric. The glue used in the system is water-based and nonvolatile. The Stewart Finishing System is Environmental Protection Agency (EPA) compliant and STC approved. Both the Stewart and Air Tech systems operate with any of the approved polyester fabrics as stated in their covering system STCs. All the modern fabric covering systems listed in Figure 3-9 result in a polyester fabric covered aircraft with an indefinite service life. Individual preferences exist for working with the different approved processes. A description of basic covering procedures and techniques common to most of these systems follows later in this chapter. Ceconite™, Polyfiber™, and Superflight™ are STC-approved fabrics with processes used to install polyester fabric coverings. Two companies that do not manufacturer their own fabric have gained STC approval for covering accessories and procedures to be used with these approved fabrics. The STCs specify the fabrics and the proprietary materials that are required to legally complete the re-covering job. The aircraft fabric covering process is a three-step process. First, select an approved fabric. Second, follow the applicable STC steps to attach the fabric to the airframe and to protect it from the elements. Third, apply the approved topcoat to give the aircraft its color scheme and final appearance. Although Grade-A cotton can be used on all aircraft originally certificated to be covered with this material, approved aircraft cotton fabric is no longer available. Additionally, due to the shortcomings of cotton fabric coverings, most of these aircraft have been re-covered with polyester fabric. In the rare instance the technician encounters a cotton fabric covered aircraft that is still airworthy, inspection and repair procedures specified in AC 43.13-1, Chapter 2, Fabric Covering, should be followed. Determining Fabric Condition—Repair or Recover? Re-covering an aircraft with fabric is a major repair and should only be undertaken when necessary. Often a repair to the present fabric is sufficient to keep the aircraft airworthy. The original manufacturer’s recommendations or the covering process STC should be consulted for the type of repair required for the damage incurred by the fabric covering. AC 43.13-1 also gives guidelines and acceptable practices for repairing cotton fabric, specifically when stitching is concerned. Often a large area that needs repair is judged in reference to the overall remaining lifespan of the fabric on the aircraft. For example, if the fabric has reached the limit of its durability, it is better to re-cover the entire aircraft than to replace a large damaged area when the remainder of the aircraft would soon need to be re-covered. On aircraft with dope-based covering systems, continued shrinkage of the dope can cause the fabric to become too tight. Overly tight fabric may require the aircraft to be re-covered rather than repaired because excess tension on fabric can cause airframe structural damage. Loose fabric flaps in the wind during flight, affecting weight distribution and unduly stressing the airframe. It may also need to be replaced because of damage to the airframe. Another reason to re-cover rather than repair occurs when dope coatings on fabric develop cracks. These cracks could expose the fabric beneath to the elements that can weaken it. Close observation and field testing must be used to determine if the fabrics are airworthy. If not, the aircraft must be re-covered. If the fabric is airworthy and no other problems exist, a rejuvenator can be used per manufacturer’s instructions. This product is usually sprayed on and softens the coatings with very powerful solvents. Plasticizers in the rejuvenator become part of the film that fills in the cracks. After the rejuvenator dries, additional coats of aluminumpigmented dope must be added and then final topcoats applied to finish the job. While laborious, rejuvenating a dope finish over strong fabric can save a great deal of time and money. Polyurethane-based finishes cannot be rejuvenated. Fabric Strength Deterioration of the strength of the present fabric covering is the most common reason to re-cover an aircraft. The strength of fabric coverings must be determined at every 100-hour and annual inspection. Minimum fabric breaking strength is used to determine if an aircraft requires re-covering. 3-8 Fabric strength is a major factor in the airworthiness of an aircraft. Fabric is considered to be airworthy until it deteriorates to a breaking strength less than 70 percent of the strength of the new fabric required for the aircraft. For example, if an aircraft was certificated with Grade-A cotton fabric that has a new breaking strength of 80 pounds, it becomes unairworthy when the fabric strength falls to 56 pounds, which is 70 percent of 80 pounds. If polyester fabric, which has a higher new breaking strength, is used to re-cover this same aircraft, it would also need to exceed 56 pounds breaking strength to remain airworthy. In general, an aircraft is certified with a certain fabric based on its wing loading and its never exceed speed (VNE). The higher the wing loading and VNE, the stronger the fabric must be. On aircraft with wing loading of 9 pounds per square foot and over, or a VNE of 160 miles per hour (mph) or higher, fabric equaling or exceeding the strength of Grade A cotton is required. This means the new fabric breaking strength must be at least 80 pounds and the minimum fabric breaking strength at which the aircraft becomes unairworthy is 56 pounds. On aircraft with wing loading of 9 pounds per square foot or less, or a VNE of 160 mph or less, fabric equaling or exceeding the strength of intermediate grade cotton is required. This means the new fabric breaking strength must be at least 65 pounds and the minimum fabric breaking strength at which the aircraft becomes unairworthy is 46 pounds. Lighter weight fabric may be found to have been certified on gliders or sailplanes and may be used on many uncertificated aircraft or aircraft in the Light Sport Aircraft (LSA) category. For aircraft with wing loading less than 8 pounds per square foot or less, or VNE of 135 mph or less, the fabric is considered unairworthy when the breaking strength has deteriorated to below 35 pounds (new minimum strength of 50 pounds). Figure 3-10 summarizes these parameters. How Fabric Breaking Strength is Determined Manufacturer’s instructions should always be consulted first for fabric strength inspection methodology. These instructions are approved data and may not require removal of a test strip to determine airworthiness of the fabric. In some cases, the manufacturer’s information does not include any fabric inspection methods. It may refer the IA to AC 43.131, Chapter 2, Fabric Covering, which contains the approved FAA test strip method for breaking strength. The test strip method for the breaking strength of aircraft covering fabrics uses standards published by the American Society for Testing and Materials (ASTM) for the testing of various materials. Breaking strength is determined by cutting a 1¼ inch by 4–6 inch strip of fabric from the aircraft covering. This sample should be taken from an area that is exposed to the elements—usually an upper surface. It is also wise to take the sample from an area that has a dark colored finish since this has absorbed more of the sun’s UV rays and degraded faster. All coatings are then removed and the edges raveled to leave a 1-inch width. One end of the strip is clamped into a secured clamp and the other end is clamped such that a suitable container may be suspended from it. Weight is added to the container until the fabric breaks. The breaking strength of the fabric is equal to the weight of the lower clamp, the container, and the weight added to it. If the breaking strength is still in question, a sample should be sent to a qualified testing laboratory and breaking strength tests made in accordance with ASTM publication D5035. Note that the fabric test strip must have all coatings removed from it for the test. Soaking and cleaning the test strip in methyl ethyl ketone (MEK) usually removes all the coatings. Properly installed and maintained polyester fabric should give years of service before appreciable fabric strength degradation occurs. Aircraft owners often prefer not to have test strips cut out of the fabric, especially when the aircraft or the fabric covering is relatively new, because removal of a test strip damages the integrity of an airworthy Fabric Performance Criteria IF YOUR PERFORMANCE IS... FABRIC STRENGTH MUST BE... New Breaking Strength Minimum Breaking Strength Ů)TCFG# > 80 lb > 56 < 160 mph Ů+PVGTOGFKCVG > 65 lb > 46 < 135 mph Ů.KIJVYGKIJV > 50 lb > 35 Loading VNE Speed > 9 lb/sq ft > 160 mph < 9 lb/sq ft < 8 lb/sq ft Type Figure 3-10. Aircraft performance affects fabric selection. 3-9 component if the fabric passes. The test strip area then must be repaired, costing time and money. To avoid cutting a strip out of airworthy fabric, the IA makes a decision based on knowledge, experience, and available nondestructive techniques as to whether removal of a test strip is warranted to ensure that the aircraft can be returned to service. An aircraft made airworthy under an STC is subject to the instructions for continued airworthiness in that STC. Most STCs refer to AC 43.13-1 for inspection methodology. PolyFiber™ and Ceconite™ re-covering process STCs contain their own instructions and techniques for determining fabric strength and airworthiness. Therefore, an aircraft covered under those STCs may be inspected in accordance with this information. In most cases, the aircraft can be approved for return to service without cutting a strip from the fabric covering. The procedures in the Poly-Fiber™ and Ceconite™ STCs outlined in the following paragraphs are useful when inspecting any fabric covered aircraft as they add to the information gathered by the IA to determine the condition of the fabric. However, following these procedures alone on aircraft not re-covered under these STCs does not make the aircraft airworthy. The IA must add their own knowledge, experience, and judgment to make a final determination of the strength of the fabric and whether it is airworthy. Exposure to UV radiation appreciably reduces the strength of polyester fabric and forms the basis of the Poly-Fiber™ and Ceconite™ fabric evaluation process. All approved covering systems utilize fill coats applied to the fabric to protect it from UV. If installed according to the STC, these coatings should be sufficient to protect the fabric from the sun and should last indefinitely. Therefore, most of the evaluation of the strength of the fabric is actually an evaluation of the condition of its protective coating(s). Upon a close visual inspection, the fabric coating(s) should be consistent, contain no cracks, and be flexible, not brittle. Pushing hard against the fabric with a knuckle should not damage the coating(s). It is recommended the inspector check in several areas, especially those most exposed to the sun. Coatings that pass this test can move to a simple test that determines whether or not UV light is passing through the coatings. This test is based on the assumption that if visible light passes through the fabric coatings, then UV light can also. To verify whether or not visible light passes through the fabric coating, remove an inspection panel from the wing, fuselage, or empennage. Have someone hold an illuminated 60-watt lamp one foot away from the exterior of the fabric. No light should be visible through the fabric. If no light is visible, the fabric has not been weakened by UV rays and can be assumed to be airworthy. There is no need to perform the fabric strip strength test. If light is visible through the coatings, further investigation is required. Fabric Testing Devices Mechanical devices used to test fabric by pressing against or piercing the finished fabric are not FAA approved and are used at the discretion of the FAA-certificated mechanic to form an opinion on the general fabric condition. Punch test accuracy depends on the individual device calibration, total coating thickness, brittleness, and types of coatings and fabric. If the fabric tests in the lower breaking strength range with the mechanical punch tester or if the overall fabric cover conditions are poor, then more accurate field tests may be made. The test should be performed on exposed fabric where there is a crack or chip in the coatings. If there is no crack or chip, coatings should be removed to expose the fabric wherever the test is to be done. The Maule punch tester, a spring-loaded device with its scale calibrated in breaking strength, tests fabric strength by pressing against it while the fabric is still on the aircraft. It roughly equates strength in pounds per square inch (psi) of resistance to breaking strength. The tester is pushed squarely against the fabric until the scale reads the amount of maximum allowable degradation. If the tester does not puncture the fabric, it may be considered airworthy. Punctures near the breaking strength should be followed with further testing, specifically the strip breaking strength test described above. Usually, a puncture indicates the fabric is in need of replacement. A second type of punch tester, the Seyboth, is not as popular as the Maule because it punctures a small hole in the fabric when the mechanic pushes the shoulder of the testing unit against the fabric. A pin with a color-coded calibrated scale protrudes from the top of the tester and the mechanic reads this scale to determine fabric strength. Since this device requires a repair regardless of the strength of the fabric indicated, it is not widely used. Seyboth and Maule fabric strength testers designed for cotton- and linen-covered aircraft, not to be used on modern Dacron fabrics. Mechanical devices, combined with other information and experience, help the FAA-certificated mechanic judge the strength of the fabric. [Figure 3-11] General Fabric Covering Process It is required to have an IA involved in the process of recovering a fabric aircraft because re-covering is a major repair 3-10 Maule tester 25 30 35 40 45 55 60 Calibrated scale 50 65 70 75 80 Seyboth or punch tester Red Yellow Green M A U L E Fabric Fabric Figure 3-11. Seyboth and Maule fabric strength testers. or major alteration. Signatures are required on FAA Form 337 and in the aircraft logbook. To ensure work progresses as required, the IA should be involved from the beginning, as well as at various stages throughout the process. This section describes steps common to various STC and manufacturer covering processes, as well as the differences of some processes. To aid in proper performance of fabric covering and repair procedures, STC holders produce illustrated, step-by-step instructional manuals and videos that demonstrate the correct covering procedures. These training aids are invaluable to the inexperienced technician. Since modern fabric coverings last indefinitely, a rare opportunity to inspect the aircraft exists during the recovering process. Inspectors and owner-operators should use this opportunity to perform a thorough inspection of the aircraft before new fabric is installed. The method of fabric attachment should be identical, as far as strength and reliability are concerned, to the method used by the manufacturer of the aircraft being recovered or repaired. Carefully remove the old fabric from the airframe, noting the location of inspection covers, drain grommets, and method of attachment. Either the envelope method or blanket method of fabric covering is acceptable, but a choice must be made prior to beginning the re-covering process. Blanket Method vs. Envelope Method In the blanket method of re-covering, multiple flat sections of fabric are trimmed and attached to the airframe. Certified greige polyester fabric for covering an aircraft can be up to 70 inches in width and used as it comes off the bolt. Each aircraft must be considered individually to determine the Figure 3-12. Laying out fabric during a blanket method re-covering job. size and layout of blankets needed to cover it. A single blanket cut for each small surface (i.e., stabilizers and control surfaces) is common. Wings may require two blankets that overlap. Fuselages are covered with multiple blankets that span between major structural members, often with a single blanket for the bottom. Very large wings may require more than two blankets of fabric to cover the entire top and bottom surfaces. In all cases, the fabric is adhered to the airframe using the approved adhesives, following specific rules for the covering process being employed. [Figure 3-12] An alternative method of re-covering, the envelope method, saves time by using precut and pre-sewn envelopes of fabric to cover the aircraft. The envelopes must be sewn with approved machine sewing thread, edge distance, fabric fold, etc., such as those specified in AC 43.13-1 or an STC. Patterns are made and fabric is cut and stitched so that each major surface, including the fuselage and wings, can be covered with a single, close-fitting envelope. Since envelopes are cut to fit, they are slid into position, oriented with the seams in the proper place, and attached with adhesive to the airframe. Envelope seams are usually located over airframe structure in inconspicuous places, such as the trailing edge structures and the very top and bottom of the fuselage, depending on airframe construction. Follow the manufacturer’s or STC’s instructions for proper location of the sewn seams of the envelope when using this method. [Figure 3-13] Preparation for Fabric Covering Work Proper preparation for re-covering a fabric aircraft is essential. First, assemble the materials and tools required to complete the job. The holder of the STC usually supplies a materials and tools list either separately or in the STC manual. Control of temperature, humidity, and ventilation is needed in the work environment. If ideal environmental conditions cannot be met, additives are available that compensate for this for most re-covering products. Rotating work stands for the fuselage and wings provide 3-11 prevent static electricity build-up may be required. All fabric re-covering processes also involve multiple coats of various products that are sprayed onto the fabric surface. Use of a high-volume, low-pressure (HVLP) sprayer is recommended. Good ventilation is needed for all of the processes. Figure 3-13. A custom-fit presewn fabric envelope is slid into position over a fuselage for the envelope method of fabric covering. Other than fitting, most steps in the covering process are the same as with the blanket covering method. easy, alternating access to the upper and lower surfaces while the job is in progress. [Figure 3-14] They can be used with sawhorses or sawhorses can be used alone to support the aircraft structure while working. A workbench or table, as well as a rolling cart and storage cabinet, are also recommended. Figure 3-15 shows a well conceived fabric covering workshop. A paint spray booth for sprayed-on coatings and space to store components awaiting work is also recommended. Many of the substances used in most re-covering processes are highly toxic. Proper protection must be used to avoid serious short- and long-term adverse health effects. Eye protection, a proper respirator, and skin protection are vital. As mentioned in the beginning of this chapter, nitrate dope is very flammable. Proper ventilation and a rated fire extinguisher should be on hand when working with this and other covering process materials. Grounding of work to Rotatable wood stand and sawhorse Removal of Old Fabric Coverings Removal of the old covering is the first step in replacing an aircraft fabric covering. Cut away the old fabric from the airframe with razor blades or utility knife. Care should be taken to ensure that no damage is done to the airframe. [Figure 3-16] To use the old covering for templates in transferring the location of inspection panels, cable guides, and other features to the new covering, the old covering should be removed in large sections. NOTE: any rib stitching fasteners, if used to attach the fabric to the structure, should be removed before the fabric is pulled free of the airframe. If fasteners are left in place, damage to the structure may occur during fabric removal. Preparation of the Airframe Before Covering Once the old fabric has been removed, the exposed airframe structure must be thoroughly cleaned and inspected. The IA collaborating on the job should be involved in this step of the process. Details of the inspection should follow the manufacturer’s guidelines, the STC, or AC 43.13-1. All of the old adhesive must be completely removed from the airframe with solvent, such as MEK. A thorough inspection must be done and various components may be selected to be removed for cleaning, inspection, and testing. Any repairs that are required, including the removal and treatment of all corrosion, must be done at this time. If the airframe is steel tubing, many technicians take the opportunity to grit blast the entire airframe at this stage. The leading edge of a wing is a critical area where airflow Rotating stand and sawhorse Figure 3-14. Rotating stands and sawhorses facilitate easy access to top and bottom surfaces during the fabric covering process. 3-12