Catalysis And Catalytic Cracking Process PDF
Document Details
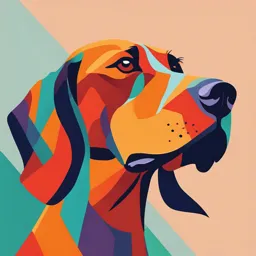
Uploaded by WelcomeEpic
Tags
Summary
This document provides an overview of catalysis and catalytic cracking. It explains the concept of catalysis as a method to increase the rate of chemical reactions, and discusses the properties of catalysts. It also details catalytic cracking, a process in petroleum refining used to convert heavy hydrocarbons into lighter ones, like gasoline.
Full Transcript
**CATALYSIS AND CATALYTIC CRACKING PROCESS** **INTRODUCTION** In the industry, time means money, and the speed with which reactions take place is of great importance. Catalysis is the most efficient means for accelerating majority of chemical reactions. The sphere of catalytic process application...
**CATALYSIS AND CATALYTIC CRACKING PROCESS** **INTRODUCTION** In the industry, time means money, and the speed with which reactions take place is of great importance. Catalysis is the most efficient means for accelerating majority of chemical reactions. The sphere of catalytic process application is continuously expanding. The use of catalysts enables the rate of chemical reactions to be increased thousand and sometimes millions times. Many industrial processes could be realized only because catalysts were used. Almost 90% of the new manufacturing processes mastered during recent years by the chemical industry are based on catalytic process. **Catalysis** Catalysis is the most effective means for accelerating the majority of chemical reactions. The use of catalyst enables the rate of chemical to be increased thousands or even million times faster than uncatalysed reactions. Almost 90% of the new manufacturing process it is paramount to industrial survival to understand catalysis and the catalytic processes. Catalysis is the process in which the rate of chemical reaction is either increased or decreased by means of a chemical substance known as catalyst. Unlike other reagents that participate in the chemical reaction, a catalyst is not affected by the reaction itself. It simply participate in the chemical reaction with the reactants but restore its chemical composition when the catalysis terminate catalysis is not only a way of increasing the productive capacity of equipment, but also a way of improving the quality of the products. It eliminates the need of additional purification and concentration of the products. The general features of catalysis is that the catalytic reaction has a lower rate -- limiting free energy change to the transition state than the corresponding uncatalysed reaction resulting in a large reaction rate at the same temperature. The economical efficiency of catalysis is that the process generally occurs at a lower temperature which reduces the expenditure of energy. Catalysis is used in the manufacture of the most important chemical products namely hydrogen, ammonia, acids of sulphur and nitrogen. It is widely use in the manufacture of alcohols, acids, aldehydes, phenol, synthetic resins and plastics, artificial rubber and motor fuels, dyes, medicine. etc most of the element of periodic table and many of their compounds are used as catalyst in modern catalytic processes. A catalyst is a chemical substance that takes part in a chemical reaction it either promotes the rate or inhibits of the rate of the chemical reaction and it does not get consumed in the process. Catalysis that speed up the reaction rate are called positive catalyst while those that slow down the reaction rate are called negative catalyst or inhibitors. Also substances that enhance the activity of catalysts are called promoters and substances that deactivate catalyst are called catalytic poisons. **PROPERTIES OF CATALYSTS** Catalysts are generally porous solids with a highly developed internal surface area and many elements of the periodic table and also a variety of their compounds can be as solid catalysts. The basic properties of catalysts are 1\. They must be active in a given reaction. 2\. They must be stable to the action of contact poison. 3\. They must have a high mechanical strength. 4\. They must be relatively cheap. 5\. They must be hat resistance and have a definite thermal conductivity. Generally, catalysts used are rarely individual masses. They are a complicated mixtures called contact mass. This consists of three main parts namely the catalyst proper, activators and carriers. Activators or promoters are substances that increase the activity of a catalyst. They increase the surface area of catalytically active substance or improves the thermal stability of a catalyst, they sometime lower the poisoning of a catalyst. Carrier or supports are thermally stable porous substance into which a catalyst is applied in some way or other. First the porous contact mass is created with a greatly developed internal active surface its mechanical strength and thermal stability are improved typical carriers are silicate, alumino-silicate, asbestors, pumice, carbon, kaolin, diatomaceous earth and some salt. Wife typical catalyst include platinum, mixed vanadium (v) oxide. The activity of a catalyst depends not only on it chemical composition but also on its physical characteristics such as the size of the grains, porosity, pore size and the nature of their surface. **CATALYTIC CRACKING** Catalytic cracking has, without a doubt, become the major process in the petroleum refining industry for producing gasoline from heavy oils and today is the most important means for increasing the ratio of light to heavy products from crude oil. Catalytic cracking is a refining process to convert high boiling non gasoline hydrocarbons into lowers boiling gasoline components. The catalyst may be in a fixed bed, moving bed or fluid bed. Large scale construction of catalytic crackers began in the 1940s and this process very quickly superseded thermal cracking for gasoline production due to its higher yields and improved product qualities. **BRIEF HISTORY** The catalytic cracking process was developed from a discovery by Houndry in 1979 that certain naturally occurring silica aluminum clays catalyzed the cracking of high molecular weight hydrocarbons to give a good yield of gasoline. The catalyst, however quickly become coated with a layer of coke which blocked the catalytic sites and reduced its cracking activity. This was restored by carefully burning off the coke in a stream of air and the regenerated catalyst could then be used for a further processing cycle. The first catalytic cracking plants were built in the USA in the period from 1930 to 1940. The process was first used around 1942 and employs a powdered catalyst. These plants used multiple fixed bed reactors which had to be periodically switched from cracking to regenerate duty to maintain catalyst activity. Eventually two systems evolved namely the moving bed and fluidized bed process. In the moving bed process, the catalyst is allowed to fall slowly by gravity through the reactor and the regenerator vessels before being returned mechanically to the top of the reactor. The fluidized process on the other hand is based on the fluidization properties of the fine powders which enable the catalyst to be transported continuously between the reactor and regenerator at extremely high flow rates of 2 systems developed the fluidized bed process has been the most widely used and today, represents over 95% of all cracking plants. **MECHANISMS OF CATALYTIC CRACKING** Initial process implementations were based on a low activity alumina catalyst and a reactor where the catalyst particles were suspended in a rising flow of feed hydrocarbons in a fluidized bed. In news designs, cracking takes place using a very active zeolite based catalyst in a short contact time vertical or upward sloped pipe called the riser. Pre-heated feed is sprayed into the base of the riser via feed nozzles where if contacts extremely hot fluidized catalyst at 1230 to 1400 of (665 to 760^o^C). The list catalyst vapourises the feed and catalyses the cracking reactions that breakdown the high molecular weight oil into lighter components including LPG, diesel and gasoline. The catalyst hydrocarbon mixture flows upward through the riser for first few seconds and that the mixture is separated via cyclones. The catalyst free hydrocarbon are noted to main fractionators for separation into LPG, gasoline, naphtha, light crude oils used in diesel and jet fuel and heavy fuel oil. During the trip up the riser, the cracking catalyst is spent by reactions which deposit coke on the catalyst and greatly reduce activity and selectivity. The used catalyst is disengaged from the cracking hydrocarbon vapours and sent to a stripper where it is contacted with steam to remove hydrocarbons remaining in the catalyst pores. The spent catalyst then flow into a fluidized bed regenerator where air (or in some cases air plus oxygen) is used to burn off the coke to restore catalyst activity and also provide the necessary heat for the next reaction cycle since cracking is an endothermic reaction. The regenerated catalyst then flows to the base of the riser repeating the cycle. Catalytic cracking is similar to thermal cracking except that catalyst facilitate the conversion of the heavier molecules into light products typical temperature are from 850-900^o^F at much lower pressures of 10-20psi. The catalysts use in refining cracking units are typically solid materials such as zeolite, aluminum hydro silicate treated bentonite clay, fullers earth, auxite and silica-alumina, they could come in the forms of powers, beads, pellet or shaped materials called extradites. There are three basic functions in the catalytic cracking process and there are; - Reaction: feed stock reacts with catalyst and cracks into different hydrocarbons. - Regeneration: catalyst is activated by burning off coke. - Fractionation: cracking hydrocarbon steam is separated into various products. **THE STOCK, PARAMETERS AND PRODUCT OF CATALYTIC CRACKING** The feed stocks may range from naphtha cuts (included in normal heavier feed for upgrading) to reducing crude. Usually feedstock preparation to remove stock and heavy asphalts -- is carried out through any one of the following ways coking propane desasphalting, furfural extraction, vacuum distillation, viscosity breaking, thermal cracking and hydrodesulphurization. The major cracking reaction takes place on the carbon-carbon bond of heavy cuts and crude to form lighter paraffins and olefins. Olefins are the most reactive class of hydrocarbons in catalytic cracking they tend to crack rapidly between 1000 and 10,000 times greater than are found in thermal cracking olefins also undergo rapid isomerization to produce a mixture of isomers in which the distribution of double bond and degree of chain branding approach thermodynamic equilibrium. Naphthenes are also stocked for the catalytic cracking process due to their greater number of secondary and tertiary carbon atoms, crack move readily than the corresponding straight chain paraffin but less readily than olefins. Major parameters in catalytic cracking are - Temperature - Pressure - Catalyst -- oil ratio (Ratio of the weight of catalyst entering the reactor per hour. - Space velocity (weight or volume of charged oil hour per weight). **EFFECT OF TEMPERATURE ON THE CATALYTIC PROCESS** For endothermic catalytic cracking to be achieve the maximum yield of product at a faster rate, the temperature of the reaction into be raised. However, for reversible exothermic catalytic reaction the temperature must be kept at an optimal level for maximum product yield but this is dependent on factors such as catalyst activity, the reactant concentration and the contact. **EFFECT OF CATALYST OIL RATIO** The catalyst oil ratio is a term used to describe the concentration of the reactant to the concentration of the catalyst. An increase in concentration will increase the reaction rate. However, a great increase in the concentration of the reactant is impermissible for number of reasons. For example when a process is highly exothermic and efficient to remove the heat thermal spoiling of the catalyst may occur (the oxidation of SO~2~). **PRODUCTS OF CATALYTIC CRACKING** Products of catalytic cracking includes paraffins with a high degree isomerization. It crack large straight chain hydrocarbon into shorter and in case branched isomer of the shorter hydrocarbons. Under severe cracking conditions with low acidity catalyst, the higher boiling points olefins are almost completely converted to lower carbon number olefins (C~3~-C~5~) in the LGP and light gasoline boiling ranges. Hydrogen transfer is catalytic cracking stabilize or preserve gasoline boiling range olefins formed by primary cracking of gas oil the gasoline product has an elevated octane rating. The LPG got is an important source of C3-C4 olefins and isooctane that are essential feeds for alkylations process and the production of polymers such as polypropylene. The catalytic cracking breaks complex hydrogen into simpler molecules in order to increase the quality and quantity of tiger, more desirable products and decrease the amount of residuals. This process rearranges the molecular of hydrocarbon compounds to convert heavy hydrocarbon feedstock into lighter fractions such as kerosene, gasoline, liquefied petroleum gas, eating oil and petrochemical feed stock. **TYPES OF CATALYTIC CRACKING** There are types of catalytic cracking - Fluid catalytic cracking - Moving bed catalytic cracking - Fixed bed catalytic cracking **FIXED BED CATALYTIC CRACKING** This is fixed bed cyclic regenerable catalytic cracking process for converting distillate charge stocks - cover gas oils - into yields of gasoline light and heavy distillate, coke, butanes and fuel gas. These used multiple fixed bed reactors which had to be periodically switched from cracking to regeneration duty to maintain catalyst activity. Synthetic and natural bead catalysts have been employed and have wasted more than 1 ½ a years. Feedstock having initial boiling points between 400 and 450ºf and end points of 750vi have yielded 35 to 40& debutanizer gasoline of 85.0 to 87.0 octane number. operating conditions in the reactor for a typical feed have been in the range of 840 to 8759f, in the 30 psig and 1.0 to 2.0 (v.hr /v) space velocity. Because of elaborate instrumentation required and of the economic attractiveness to the large and small refiner! operation of the modern moving and fluid bed catalytic cracking processes, the fixed bed unit have been replaced. **Fluid Catalytic Cracking (FCC)** Fluid catalytic cracking of \"cat cracking\" is basic gasoline-making process. Using intense heat (about 1,000 degrees Fahrenheit). low pressure and a powdered catalysis la substance that accelerates chemical reactions), the cat cracker can convert most relatively heavy fractions into smaller gasoline molecules. The fluid cracker consists of a catalysis section and a fractionating section that operate together as an Integrated processing unit. The catalyst section contains the reactor and regenerator, which, with the standpipe and riser, forms the catalyst circulation unit. The fluid catalysis is continuously circulated between the reactor and the regenerator using air, oil vapors, and steam as the conveying media. A typical FCC process involves mixing a preheated hydrocarbon charge with hot, regenerated catalyst as it enters the riser leading to the reactor. The charge is combined with a recycle stream within the riser. vapourized. and raised to reactor temperature (900°-1,0000 F) by the hot catalyze. As the mixture travels up the riser, the charge is cracked at 10-30 F) by the hot catalyst. As the mixture travels up the riser, the charge is cracked at 10-30 psi. In the more modern FCC units, all cracking takes place in the riser. The \"reactor\" no longer functions as a reactor, it merely serves as a holding vessel for the cybiome. This cracking continues until the oil vapours are separated from the catalyst in the reactor cyclones. The resultant product stream (cracked product) is then charged to a fractionating column where it is separated into fractions and some of the heavy oil is recycled to the riser. Spent catalyst is regenerated to get ria of coke that collects on the catalyst during the process. Spent flows through the catalysis stripper to the regenerator. where most of the coke deposits burn off at the bottom where preheated air and spend catalysis are mixed. Fresh catalysis is added and worm-out catalyst removed to optimize the cracking process. **Moving Bed Catalytic Cracking** The moving-bed catalytic cracking process is similar to the FCC Process. The catalyst is in the form of pellets that are moved continuously to the top of the unit by conveyor or pneumatic lift tubes io a storage hopper, then flow downward by sarin through the reactor, and finally to a regenerator. The regenerator and hopper are isolated from the reactor steam seal. The cracked products is separated into recycle gas. oil. clarified oil. distillate. naphtha. and wet gas. **\ ** **THERMAL PROCESSES OF HYDROCARBON** **Thermal cracking** Thermal cracking can be described as the decomposition or cracking of a hydrocarbon at elevated temperature to form material of lower molecular weight. Without doubt, thermal, cracking is the oldest hydrocarbon conversion process with its origins dating back as far as 1860, and it provided early refining industry with a means of producing desirable, low boiling point hydrocarbons form relatively low-value, heavier stocks. Over the years, the thermal cracking process has found a wide range of uses, and its versatility can be illustrated by mentioning some of the feedstock\'s it can receive. These may include butane, naphtha, and gas oils, as well as atmospheric and vacuum residues. **FORMS OF THERMAL CRACKING** The widely used form of thermal cracking today is the steam cracking process in which straight-run naphtha boiling between 30 and 160° is converted to a range of low molecular weight olefins, including ethylene, propane, butanes and butadiene. This process, which is carried out at low hydrocarbon partial pressures obtained by steam dilution and produces some of the building blocks used in petrochemical manufacture. Other thermal cracking processes still in common used include 'vispreaking' and 'coking' both are used to convert residual materials, but whereas visbreaking is carried out under relatively mild conditions as a means of reducing fuel oil viscosities, coking is conducted at high severities to produce distillates products and petroleum coke. **THERMAL CRACKING REACTION** Depending on the feedstock type and product requirement thermal cracking can be carried our over a wide range of temperature from 450 to 750°C and at pressures varying from atmospheric to 70 bars. Thermal cracking reactions are believed to proceed through the formation of hydrocarbon free radicals. Free radicals are formed by carbon-carbon bond scission, generally towards the centre of e hydrocarbon molecule. For example, a paraffin containing 16 carbon atoms, when subjected too high temperature, may fragment into two free radicals each containing eight carbon atoms. C~16~H~24~ 2CH~3~(CH~2~)~6~CH~2~ Free radical This is often referred to as the initiation reaction paraffin side chains of cycle hydrocarbons may also form free radicals by a similar reaction, although breakage of carbon-carbon bond in an aromatic nucleus is very unlikely to occur. **THERMAL CRACKING PROCESS** **1) VISBREAKING** Visbreaking or viscosity breaking is a low severity thermal cracking operation, often used for reducing the viscosity of straight-run residual oils. Normally, such residual oils are very viscous and if required for sale as heavy fuel oil must be blended with a relatively high-value distillate to meet the finished product viscosity specification. Visbreaking reduces the quantity of distillate required as diluents or \"alter-stock\" and this material can then be diverted to a more profitable outlet, such as diesel oil. Visbreak temperature at the heating coil outlet range from 450 to 500 depending on the design of the unit and the nature of the feesstock. The pressure may vary between 4 and 20 bars, but higher pressure is often preferred since this gives greater control over residence time by minimizing evaporation. 2\. COKING Coking processes are relatively severe cracking operations designed to convert residual oil products, such as straight-run atmospheric and vacuum residues, tars and pitches, into more valuable lighter products, such as naphtha and diesel oil. In addition, gas and coke are produced. The yield of each is dependent on the coking conditions and the quantity of the feedstock fed to the process. The main purpose oi this process is to produce ion-carbon gas oil for catalytic feedstock. Generally, gasoline. gas and coke are secondary products. There are two main types of coking processes available, namely, delayed and fluid coking, The latter process has further been developed into a process known as flexi-coking, whereby the fluid coke produced is gasified to produce low thermal: valve gas. **3. MIXED -- PHASE CRACKING** Mixed-phase cracking is a continuous thermal decomposition process for conversion of heavy products to gasoline-boiling components. In general, mixed-phase cracking processes employ rapid heating of the charging stock. A high ratio of liquid vapor is maintained, and increasing temperature necessitates increase in pressure to prevent excessive evaporation. **4) VAPOUR - PHASE CRACKING** Vapour-phase cracking processes were installed for gasoline production, but even in the early days of thermal cracking relative process economics favored use of mixed-phase units hard carbon (coke) was often deposited in vapor-phase unit heater tubes, causing failures. Vapour-phase cracking is a high temperature, low-pressure thermal conversion process. **PYROLYSIS** Pyrolysis is the chemical decomposition of condensed organic substances by heating. The word is coined from the Greek-derived elements pyro \"fire\" and lysis \"decomposition\" Pyrolysis is a special case of thermolysis related to the chemical process of charring, and is most commonly used for organic materials. It occurs spontaneously at high temperature (e.g. above 300° for wood, it varies for other material), for example in fires or when vegetation comes into contact with lava in volcanic eruptions. In general, it produces gas and liquid products and leaves a solid residue richer in carbon content. Extremely pyrolysis which leaves mostly carbon as the residue, is called carbonization. It does not involve reactions with oxygen or any other regents but can take place in their presence. Pyrolysis is heavily used in the chemical industry, for example, to produce charcoal, activated carbon, methanol and other chemicals from wood, to convert ethylene dichloride into vinyl chloride to make PVC, to produce coke from coal, to convert biomass into syngas. It is an important chemical process in several cooking procedure such as baking, frying, grilling and caramelizing. Pyrolysis is also a too o chemical analysis to example by pyrolysis gas chromatography mass spectrometry and in carbon-it dating pyrolysis has also be applied to the decomposition di organic material in the presence of super-heated water or stream (hydrous pyrolysis, for example steam cracking of Oil.