CASA B-06a Aircraft Materials and Corrosion PDF 2022
Document Details
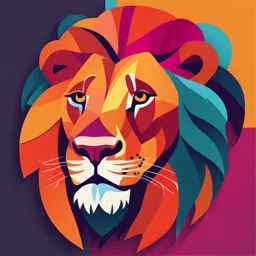
Uploaded by FaultlessMarsh8570
null
2022
CASA
Tags
Summary
This document is a study guide on aircraft materials and corrosion, specifically for CASA B-06a Aircraft Maintenance licenses. It covers various topics such as ferrous and non-ferrous metals, composite materials, and corrosion. The guide includes learning objectives and detailed explanations.
Full Transcript
MODULE 06 Category B1 and B2 Licences CASA B-06a Aircraft Materials and Corrosion Copyright © 2020 Aviation Australia All rights reserved. No part of this document may be reproduced, transferred, sold or otherwise disposed of, without the written permission of Aviation Australia. CONTROLLED DOCUMENT...
MODULE 06 Category B1 and B2 Licences CASA B-06a Aircraft Materials and Corrosion Copyright © 2020 Aviation Australia All rights reserved. No part of this document may be reproduced, transferred, sold or otherwise disposed of, without the written permission of Aviation Australia. CONTROLLED DOCUMENT 2022-05-18 B-06a Materials and Hardware CASA Part 66 - Training Materials Only Page 2 of 229 Knowledge Levels Category A, B1, B2 and C Aircraft Maintenance Licence Basic knowledge for categories A, B1 and B2 are indicated by the allocation of knowledge levels indicators (1, 2 or 3) against each applicable subject. Category C applicants must meet either the category B1 or the category B2 basic knowledge levels. The knowledge level indicators are defined as follows: LEVEL 1 Objectives: The applicant should be familiar with the basic elements of the subject. The applicant should be able to give a simple description of the whole subject, using common words and examples. The applicant should be able to use typical terms. LEVEL 2 A general knowledge of the theoretical and practical aspects of the subject. An ability to apply that knowledge. Objectives: The applicant should be able to understand the theoretical fundamentals of the subject. The applicant should be able to give a general description of the subject using, as appropriate, typical examples. The applicant should be able to use mathematical formulae in conjunction with physical laws describing the subject. The applicant should be able to read and understand sketches, drawings and schematics describing the subject. The applicant should be able to apply his knowledge in a practical manner using detailed procedures. LEVEL 3 A detailed knowledge of the theoretical and practical aspects of the subject. A capacity to combine and apply the separate elements of knowledge in a logical and comprehensive manner. Objectives: The applicant should know the theory of the subject and interrelationships with other subjects. The applicant should be able to give a detailed description of the subject using theoretical fundamentals and specific examples. The applicant should understand and be able to use mathematical formulae related to the subject. The applicant should be able to read, understand and prepare sketches, simple drawings and schematics describing the subject. The applicant should be able to apply his knowledge in a practical manner using manufacturer's instructions. The applicant should be able to interpret results from various sources and measurements and apply corrective action where appropriate. 2022-05-18 B-06a Materials and Hardware CASA Part 66 - Training Materials Only Page 3 of 229 Table of Contents Aircraft Materials - Ferrous (6.1.1) Learning Objectives Metal Alloy Steels 10 10 11 Ferrous Metal Characteristics and Properties 11 Strength 11 Metal Loading Forces 12 Hardness 15 Malleability 15 Ductility 16 Brittleness 17 Elasticity 18 Toughness 19 Conductivity 20 Thermal Expansion 21 Fusibility 22 Ferrous Metals 23 Iron (Ferrite) 23 Steel Composition 23 Identification of Steels 25 Society of Automotive Engineers Steel Numbering 25 SAE Steel Numbering System 25 Alloying Agents in Steel 27 Purpose of Ferrous Metal Alloys 27 Carbon 27 Other Alloying Agents 28 Stainless Steel 31 Heat Treatment of Steel 32 Purpose of Steel Heat Treatment 32 Annealing 32 Normalising 33 Hardening 34 Tempering 35 Case Hardening Aircraft Materials - Non-Ferrous (6.2.1) 2022-05-18 B-06a Materials and Hardware CASA Part 66 - Training Materials Only 36 38 Page 4 of 229 Learning Objectives 38 Properties of Non-Ferrous Metals 39 Non-Ferrous Metals 39 Identifying Aluminium 39 Wrought Aluminium Alloys Designation System 40 Aluminium and Alloys Series 42 Clad Aluminium Alloy (Alclad) 48 Heat Treatment of Aluminium Alloys 49 Heat Treatment 49 Solution Heat Treatment 49 Precipitation Heat Treatment 50 Annealing 52 Aluminium Alloy Temper Designations 53 Reheat Treatment 54 Non-Heat-Treatable Aluminium 55 Strain-Hardening 56 Hardness Designations 57 Other Alloy Types 58 Magnesium and Its Alloys 58 Titanium and Its Alloys 59 Nickel and its Alloys 60 Monel 60 Copper and its Alloys Aircraft Materials - Metallic Testing (6.1.2 and 6.2.2) Learning Objectives Testing of Metallic Materials 64 64 65 Metal Testing 65 Hardness Testing 65 Brinell Hardness Tester 66 Rockwell Hardness Tester 67 Tensile Strength Testing 69 Fatigue Strength Testing 70 Airframe Fatigue Testing 71 Impact Resistance Testing Aircraft Materials - Composite and Non-Metallic (6.3.1.1) Learning Objectives 2022-05-18 62 B-06a Materials and Hardware CASA Part 66 - Training Materials Only 72 76 76 Page 5 of 229 Non-Metallic Structural Materials Use of Composite Materials in Aircraft Construction What Is a Composite Structure? 77 77 78 Composite Structure 78 Composites in Aircraft Structures 79 Composite Elements 81 Composite Fibres 83 Reinforcing Fibres 83 Fibreglass (Glass Cloth) 83 Aramid 84 Carbon 86 Ceramic Fibre 87 Fibre Science 89 Composite Fabrics 91 Fabric Orientation 91 Fabric Styles 93 Fabric Weaves 95 Plain Weave 95 Satin Weave 96 Composite Bonding 98 Matrix Systems 98 Resin Matrix Systems 98 Adhesives (Bonding Agents) 104 Pre-impregnated Materials 106 Fillers 109 Working With Resins and Catalysts Resin and Catalyst Terminology Disposing of Resins Aircraft Materials - Composite Maintenance, Inspection and Repairs (6.3.1.2) 111 111 113 115 Learning Objectives 115 Composite Inspection 116 2022-05-18 Composite Inspection Methods 116 Visual Inspection 116 Tap Testing 117 Ultrasonic Inspection 118 Radiographic Inspection 119 B-06a Materials and Hardware CASA Part 66 - Training Materials Only Page 6 of 229 Thermography 120 Composites Defects and Damage 122 Damage Classifications 122 Cosmetic Defects 122 Impact Damage 123 Delamination 124 Disbonds 125 Cracks 125 Resin Matrix Damage 127 Water and Aircraft Fluid Intrusion 127 Hole Damage 129 Composite Repairs 131 Composite Repairs 131 Composites Damage Assessment and Repair Process 131 Potted Repairs 132 Injection Repairs 133 Laminate Damage to One Surface 135 Laminate Damage Through the Part 135 Sandwich Structure Repairs 136 Honeycomb Core Repairs 137 Transparent Plastic Repair 138 Sealants Corrosion (6.4) Learning Objectives 140 143 143 Chemical Fundamentals of Corrosion Corrosion 144 Dry Corrosion 145 Wet Corrosion 146 Direct Chemical Attack 147 Mercury 148 Types of Corrosion 2022-05-18 144 150 Electrochemical Series 150 Galvanic Corrosion 150 Stress Corrosion 152 Surface Corrosion 153 Pitting Corrosion 154 Intergranular Corrosion 156 B-06a Materials and Hardware CASA Part 66 - Training Materials Only Page 7 of 229 Filiform Corrosion 158 Fretting Corrosion 159 Exfoliation Corrosion 160 Microbiological Corrosion 162 Material Types and Susceptibility to Corrosion 165 Metal Corrosion Susceptibility 165 Aluminium 165 Anodised Aluminium 165 Magnesium 166 Titanium 167 Cadmium 168 Chromium 169 Nickel 170 Copper and Copper Alloys 171 Silver 172 Gold 173 Tin 174 Effects of Corrosion on Metals 174 Aircraft Rivets (6.5.4) Learning Objectives 176 176 Rivet Specifications and Standards 177 Rivets 177 Solid-Shank Rivets 178 Rivet Codes 179 Rivet Head Design 182 Rivet Alloys 183 1100 Aluminium (A) 184 2117 Aluminium Alloy (AD) 185 5056 Aluminium Alloy (B) 186 2017 Aluminium Alloy (D) 187 2024 Aluminium Alloy (DD) 189 7050-T73 Aluminium Alloy (E) 189 Corrosion-Resistant Steel (F) 190 Monel (M) 191 Rivet Heat Treatment 191 Special Rivets and Fasteners 193 Special (Blind) Rivet Applications 2022-05-18 B-06a Materials and Hardware CASA Part 66 - Training Materials Only 193 Page 8 of 229 Friction-Lock Rivets 193 Types of Mechanical-Lock Rivets 194 Huck-Loks 195 Olympic-LOKs 196 CherryMAX™ 197 Hi-Shear Rivets 198 Special Fastener Applications 199 Hi-Loks 199 Jo-Bolt Fastener 200 Removal of Special Fasteners Pipes, Hoses and Unions (6.6) Learning Objectives Rigid Lines 203 203 204 Rigid Lines Applications 204 Size Designations 206 Rigid Line Fittings and Unions 208 Tube Flaring 208 Flared-Tube Fittings 209 Flareless Tube Fittings 210 Identification of Flareless Fittings 211 Flareless Fittings 212 Universal Bulkhead Fittings 214 Tapered Pipe Thread Fittings 214 Banjo Fittings 215 Quick-Disconnect Couplings 216 Beading 217 Flexible Fluid Lines 220 Flexible Fluid Lines Application 220 Outer Cover 222 Flexible Line Identification 222 Types of Flexible Hose 223 Flexible Pipe Fittings 2022-05-18 201 227 Introduction 227 Swaged-End Fittings 227 Reusable Fittings 227 Blanks 228 B-06a Materials and Hardware CASA Part 66 - Training Materials Only Page 9 of 229 Aircraft Materials - Ferrous (6.1.1) Learning Objectives 6.1.1.1.1 Describe the characteristics and properties of common alloy steels used in aircraft (Level 2). 6.1.1.1.2 Identify common alloy steels used in aircraft (Level 1). 6.1.1.2.1 Describe heat treatment of alloy steels (Level 2). 6.1.1.2.2 Describe the application of alloy steels (Level 2). 2022-05-18 B-06a Materials and Hardware CASA Part 66 - Training Materials Only Page 10 of 229 Metal Alloy Steels Ferrous Metal Characteristics and Properties In this resource the term 'Metal characteristics' is used to identify a feature or quality of the material. When using metal in manufacturing and construction, a given metal is known to possess several characteristics which determine where and how it can be used. These characteristics includes strength, hardness, malleability, ductility, brittleness, conductivity, expansion, elasticity, toughness, fusibility and density. In this resource the term Metal property is used to identify an attribute, quality, or characteristic of a metal. By adding (alloying) small amounts of other materials, the properties of the material characteristics are changed dramatically. As an example, in a basic form adding carbon to steel increases the hardness property of the core material. Aircraft in assembly line at Boeing 2022-05-18 B-06a Materials and Hardware CASA Part 66 - Training Materials Only Page 11 of 229 Strength One way to classify metals is according to the amount of strength they possess. A metal’s strength is determined by the percentages of the parent metal and other elements used to make an alloy. There are many different types of strength, including: Tensile strength Compressive strength Shear strength Torsional strength Bending strength Fatigue strength Impact strength (also known as toughness). 2022-05-18 B-06a Materials and Hardware CASA Part 66 - Training Materials Only Page 12 of 229 Metal Loading Forces Each type of strength listed is a measure of how a metal reacts to a specific type of loading. Tensile strength is the ability of a piece of sheet metal to withstand stress in tension. There are three definitions of tensile strength: Yield strength – the stress at which material strain changes from elastic deformation to plastic deformation, causing it to deform permanently. Ultimate strength – the maximum stress a material can withstand when subjected to tension, compression or shearing; the maximum stress on the stress-strain curve. Breaking strength – the stress coordinate on the stress-strain curve at the point of rupture. Reference numbers on the stress vs strain curve for structural steel include: Ultimate strength Yield strength (elastic limit) Rupture (or fracture) Strain-hardening region Necking region. Stress, σ Strain hardening Necking Ultimate strength Fracture Yield strength Strain, ε Image by under the Creative Commons Licence Stress vs strain curve for structural steel (tensile strength) 2022-05-18 B-06a Materials and Hardware CASA Part 66 - Training Materials Only Page 13 of 229 The remaining four fundamental loading forces (excluding tension which is described above) are listed below: Compressive strength is a metal’s ability to withstand being pressed or squeezed. Shear strength is a metal’s ability to withstand shear stress. Torsional strength is a metal’s ability to resist rotational shear. Bending strength is a metal’s bending strength. Fundamental loading forces The remaining types of strength include: Fatigue strength, or endurance strength, which is a metal’s ability to resist repeated loading. Impact strength (toughness), which is a metal’s ability to resist shock. This will be elaborated on in the following section. 2022-05-18 B-06a Materials and Hardware CASA Part 66 - Training Materials Only Page 14 of 229 Fractured metal due to fatigue The following sections will describe the specific properties of metals, each of which typically relate to a type or several types of metallic strengths outlined above. Hardness A metal’s hardness is its ability to resist cutting, penetration or abrasion. The tensile strength of steel relates directly to its hardness, but for most metals this relationship is not absolute. Some metals are hardened through heat-treating or work hardening, while others are softened by a process called annealing. Metal hardness testing 2022-05-18 B-06a Materials and Hardware CASA Part 66 - Training Materials Only Page 15 of 229 Malleability A material’s ability to be bent, formed or shaped without cracking or breaking is called malleability. Hardness and malleability are generally considered opposite properties. To help increase malleability, several metals are annealed, or softened. Under this condition, complex shapes can be formed. After forming is complete, the metal is then heat-treated to increase its strength. A metal may be fully annealed when the forming is started, but hammering and shaping can harden it to such an extent that it must be re-annealed before forming is completed. A malleable metal is able to be hammered, pressed, or rolled into thin sheets without breaking. Metal pressed to form structures in aircraft panels A malleable metal is highly ductile and a non-malleable metal is brittle. 2022-05-18 B-06a Materials and Hardware CASA Part 66 - Training Materials Only Page 16 of 229 Ductility The ability of metal to be drawn into wire stock, extrusions or rods is called ductility. Ductile metal is used for control cables which must be regularly inspected. Ductile metals are preferred for aircraft use because of their ease of forming and resistance to failure under shock loads. 2022-05-18 B-06a Materials and Hardware CASA Part 66 - Training Materials Only Page 17 of 229 Brittleness Brittleness is a material’s tendency to break or shatter when exposed to stress, and is the opposite of ductility and malleability. A brittle metal is more apt to break or crack before it changes shape. Because structural metals are often subjected to shock loads, brittleness is not a desirable property. Cast iron and very hard steel are examples of brittle ferous metals. Ductile fracture vs brittle fracture 2022-05-18 B-06a Materials and Hardware CASA Part 66 - Training Materials Only Page 18 of 229 Elasticity Elasticity is a metal’s tendency to return to its original shape after normal stretching and bending. The flexibility of spring steel used to construct landing gear is a good example of elasticity. Another form of elasticity is demonstrated when aircraft skins expand and contract when an aircraft is pressurised. A metal’s elastic limit is the point beyond which the metal does not return to its original shape after a deforming force is removed. Some non-ferous metals have very low elastic limits, while the elastic limit of hard spring steel is very high. Elasticity is a metal’s tendency to return to its original shape after normal stretching and bending 2022-05-18 B-06a Materials and Hardware CASA Part 66 - Training Materials Only Page 19 of 229 Toughness Toughness is a material’s ability to resist tearing or breaking when it is bent or stretched. Hammer faces and wrenches are examples of metal that must be tough as well as hard to be useful. Toughness of metals 2022-05-18 B-06a Materials and Hardware CASA Part 66 - Training Materials Only Page 20 of 229 Conductivity Conductivity is the property which enables a metal to carry heat or electricity. If a metal is able to transmit heat, it is said to be thermally conductive. However, before a metal can carry heat away from its source, it must first absorb it. This ability to conduct heat away is called heat exchange. The fins on the cylinder heads of an air-cooled piston engine remove heat in this fashion. Metals that can carry heat also carry electrons, making them good electrical conductors. Electrical conductivity is the measure of a material’s ability to allow electron flow. A metal conductor can be a wire, an aircraft frame or an engine. Conductivity of metals 2022-05-18 B-06a Materials and Hardware CASA Part 66 - Training Materials Only Page 21 of 229 Thermal Expansion The ability of a metal to expand when heated and shrink when cooled is called thermal expansion. The amount of expansion or contraction is predictable at specific temperatures and is called its coefficient of expansion. All aircraft experience thermal expansion and contraction as the ambient temperature changes. Thermal expansion Fusibility The ability of metal to be joined by heating and melting is called fusibility. To fuse metal means to melt two or more compatible pieces of metal into one continuous part. The correct term is fusion joining or welding. Photo by Rob Lambert on Unsplash Welding is a form of fusing 2022-05-18 B-06a Materials and Hardware CASA Part 66 - Training Materials Only Page 22 of 229 Ferrous Metals Iron (Ferrite) Any alloy containing iron as its chief constituent is called a ferrous metal. Ferrous metals include steel, cast iron, and titanium, as well as alloys of iron with other metals (such as with stainless steel). The most common ferrous metal in aircraft structures is steel, an alloy of iron with a controlled amount of carbon added. Iron is a chemical element which is fairly soft, malleable and ductile in its pure form. It is silvery white in colour and quite heavy. Iron combines readily with oxygen to form iron oxide, which is more commonly known as rust. This is one reason iron is usually mixed with various forms of carbon and other alloying agents or impurities. Iron ore Iron poured from a furnace into moulds is known as cast iron and normally contains more than 2% carbon and some silicon. Cast iron has few aircraft applications because of its low strength-to-weight ratio. However, it is used in engines for items such as valve guides, where its porosity and wear characteristics allow it to hold a lubricant film. It is also used in piston rings. 2022-05-18 B-06a Materials and Hardware CASA Part 66 - Training Materials Only Page 23 of 229 Steel Composition Steel is a material composed primarily of iron. All types of steel contain a second element: carbon. Many other alloying elements are used in most steel, but iron and carbon are the only elements found in all steel. Composition of Steel The difference between steel, cast iron and wrought iron is primarily based on the carbon content. 2022-05-18 B-06a Materials and Hardware CASA Part 66 - Training Materials Only Page 24 of 229 Identification of Steels Society of Automotive Engineers Steel Numbering In general, the Society of Automotive Engineers (SAE) uses a four-digit numerical index system to represent chemical composition standards for steel specifications: The first digit identifies the principal alloying element. The second digit indicates the percentage of the principal alloying element. The last two digits indicate the average carbon content in hundredths of a percent. Steel Numbering System 2022-05-18 B-06a Materials and Hardware CASA Part 66 - Training Materials Only Page 25 of 229 SAE Steel Numbering System SAE designations for major classifications of steel: 1xxx – Carbon steels 2xxx – Nickel steels 3xxx – Nickel-chromium steels 4xxx – Molybdenum steels 5xxx – Chromium steels 6xxx – Chromium-vanadium steels 7xxx – Tungsten steels 8xxx – Nickel-chromium-molybdenum steels 9xxx – Silicon-manganese steels. Aviation Australia SAE Numbering System 2022-05-18 B-06a Materials and Hardware CASA Part 66 - Training Materials Only Page 26 of 229 Alloying Agents in Steel Purpose of Ferrous Metal Alloys Iron has few practical uses in its pure state. However, adding small amounts of other materials to molten iron dramatically changes its properties. Some of the more common alloying agents include carbon, sulphur, silicon, phosphorous, nickel and chromium. Carbon Carbon is the most common alloying element found in steel. When carbon is mixed with iron, compounds of iron carbides called cementite form. The carbon in steel allows the steel to be heattreated to obtain varying degrees of hardness, strength and toughness. The greater the carbon content, the more receptive steel is to heat treatment and therefore the higher its tensile strength and hardness. However, higher carbon content decreases the malleability and weldability of steel. A metal’s hardness, or temper, is indicated by a letter designation that is separated from the alloy designation by a dash. Ferrous materials are generally classified according to their carbon content. Low-carbon or mild steel: Is primarily used in non-structural areas, but has (in the past) been used in steel-tube construction. Easily welded. Machines readily. Does not accept heat treatment. Medium-carbon steels: Will accept heat treatment. Is especially adaptable for machining or forging. Used where surface hardness is desirable. High-carbon steels: Very hard. Primarily used in springs, files and some cutting tools. The following graph shows the relationship between the percentage of carbon in steel and its properties including tensile strength, ductility and hardness. 2022-05-18 B-06a Materials and Hardware CASA Part 66 - Training Materials Only Page 27 of 229 Carbon steel characteristics Other Alloying Agents Silicon When silicon is alloyed with steel, it acts as a hardener. Used in small quantities, it also improves ductility. Manganese Mangalloy (manganese steel) is a unique non-magnetic steel with extreme anti-wear properties. The material is very resistant to abrasion and will achieve up to three times its surface hardness during conditions of impact, without any increase in brittleness which is usually associated with hardness. 2022-05-18 B-06a Materials and Hardware CASA Part 66 - Training Materials Only Page 28 of 229 Sulphur Sulphur is usually an undesirable impurity in steel rather than an alloying element. Sulphur causes steel to be brittle when rolled or forged, and therefore it must be removed in the refining process. If all the sulphur cannot be removed, its effects can be countered by adding manganese. The manganese combines with the sulphur to form manganese sulphide, which does not harm the finished steel. In addition to eliminating sulphur and other oxides from steel, manganese improves a metal’s forging characteristics by making it less brittle at rolling and forging temperatures. Alloying additions of sulphur in small amounts will tend to improve the machinability of a steel. Machinability is the ease with which a metal can be cut (machined). Phosphorous Phosphorous raises the yield strength of steel and improves low-carbon steel’s resistance to atmospheric corrosion. Nickel Nickel adds strength and hardness to steel and increases its yield strength. It also slows the rate of hardening when steel is heat-treated, which increases the depth of hardening and produces a finer grain structure. The finer grain structure reduces steel’s tendency to warp and scale when heattreated. Chromium Chromium is alloyed with steel to increase strength and hardness as well as improve its wear and corrosion resistance. Because of its characteristics, chromium steel is used in balls and rollers of antifriction bearings. In addition to its use as an alloying element in steel, chromium is electrolytically deposited on cylinder walls and bearing journals to provide a hard, wear-resistant surface. Nickel-Chromium Steel Nickel toughens steel, and chromium hardens it. Therefore, when both elements are alloyed, they give steel desirable characteristics for use in high-strength structural applications. 2022-05-18 B-06a Materials and Hardware CASA Part 66 - Training Materials Only Page 29 of 229 Molybdenum One of the most widely used alloying elements for aircraft structural steel is molybdenum. It reduces the grain size of steel and increases both its impact strength and elastic limit. Molybdenum steels are extremely wear resistant and possess a great deal of fatigue strength. Chrome-molybdenum (chrome-moly) steel machines readily, is easily welded by either gas or electric arc, and responds well to heat treatment. Chrome-moly steel is an ideal choice for landing gear structures and engine mounts. Furthermore, chrome-moly’s toughness and wear resistance make it a good material for engine cylinders and other highly stressed engine parts. Vanadium When combined with chromium, vanadium produces a strong, tough, ductile steel alloy. Ball bearings are made of chrome-vanadium steel. Tungsten Tungsten has an extremely high melting point and adds this characteristic to steel it is alloyed with. Because tungsten steels have high density (high mass) and retain their hardness at elevated operating temperatures, they are typically used for control surface balance weights and breaker contacts in magnetos. Tungsten balance weights 2022-05-18 B-06a Materials and Hardware CASA Part 66 - Training Materials Only Page 30 of 229 Titanium Titanium steel alloys have very high tensile strength and toughness (and at higher temperatures). Titanium steel is also lightweight and has high corrosion resistance whilst the ability to withstand extreme temperatures. Stainless Steel Stainless steel is a classification of corrosion-resistant steels that contain large amounts of chromium and nickel. Their strength and resistance to corrosion make them well suited for high-temperature applications such as firewalls and exhaust system components. Stainless steel engine shroud segments 2022-05-18 B-06a Materials and Hardware CASA Part 66 - Training Materials Only Page 31 of 229 Heat Treatment of Steel Purpose of Steel Heat Treatment As mentioned before, pure iron is not suitable for use as a structural material. It is weak, soft, very ductile and unresponsive to heat treatment. Steel, which is typically iron alloyed with carbon and a few percent to a few tens of percent of other alloying elements, can be heat-treated to a wide range of strengths, toughnesses and ductilities. Carbon is the most important of these alloying elements in terms of the mechanical properties of steel, and most heat treatments of steel are based primarily on controlling the distribution of carbon. Heat treatment of steel is the process of heating and cooling carbon steel to change its physical and mechanical properties without changing its original shape and size. Heat treatment is often associated with increasing the strength of the steel, but it can also be used to alter certain manufacturability objectives, such as to improve machinability or formability, restore ductility, etc. Thus, heat treatment is a useful process to bolster other manufacturing processes and to improve product performance by increasing strength or other desirable characteristics. Highcarbon steels are particularly suitable for heat treatment since carbon steel responds well to the treatment and the commercial use of steels exceeds that of any other material. Steel being heat treated There are many different types of heat treatment processes, and each process provides different desirable characteristics to the product. 2022-05-18 B-06a Materials and Hardware CASA Part 66 - Training Materials Only Page 32 of 229 Annealing Annealing softens steel and relieves internal stress. Annealing steel involves heating it, soaking it for a specified time and then cooling it. The steel can be cooled by leaving it in the furnace and allowing both the furnace and steel to cool together or by packing the steel in hot sand or ash so the heat is conducted away slowly. Annealing oven 2022-05-18 B-06a Materials and Hardware CASA Part 66 - Training Materials Only Page 33 of 229 Normalising The processes of forging, welding and machining usually leave stresses within steel that could lead to failure. These stresses are relieved in ferrous metals by a process known as normalising. This process involves heating the steel and maintaining the temperature until the metal is uniformly heat-soaked. The steel is then removed from the oven and allowed to cool in still air. Although this process does allow particles of carbon to precipitate out, the particles are not as large as those formed when steel is annealed. One of the most important uses of normalising in aircraft work is on welded parts. When a part is welded, internal stresses and strains set up in the adjacent material. Allowing the heated steel to cool in still air 2022-05-18 B-06a Materials and Hardware CASA Part 66 - Training Materials Only Page 34 of 229 Hardening Carbon steel can be hardened readily. The maximum hardness attained by carbon steel depends almost entirely on its carbon content. Hardening steel involves heating it so carbon can disperse uniformly. Once this occurs, the alloy is cooled rapidly by quenching it in water, oil or brine (water with a high salt content). The speed of the quench is determined by the quenching medium. Oil provides the slowest quench, and brine is the most rapid. Quenching steel 2022-05-18 B-06a Materials and Hardware CASA Part 66 - Training Materials Only Page 35 of 229 Tempering Tempering reduces the undesirable qualities of the steel's brittleness. Tempering an alloy is done by heating it to a certain temperature and holding it there until it becomes heat-soaked. It is then allowed to cool to room temperature in still air. Tempering not only reduces hardness and brittleness, but also relieves stress and improves steel’s ductility and toughness. Tempering also involves allowing the metal to cool in room temperature air 2022-05-18 B-06a Materials and Hardware CASA Part 66 - Training Materials Only Page 36 of 229 Case Hardening Aircraft components like bearings and gears that require metal with hard, durable surfaces and core material that remains tough. This is accomplished through a process called case-hardening. Lowcarbon and low-alloy steels are best suited for case-hardening. If high-carbon steel is case-hardened, the hardness penetrates the core and causes brittleness. Aviation Australia Case hardening 2022-05-18 B-06a Materials and Hardware CASA Part 66 - Training Materials Only Page 37 of 229 Aircraft Materials - Non-Ferrous (6.2.1) Learning Objectives 6.2.1.1.1 Describe the characteristics and properties of common non-ferrous materials used in aircraft (Level 2). 6.2.1.1.2 Describe the identification of common non-ferrous materials used in aircraft (Level 2). 6.2.1.2.1 Describe heat treatment of non-ferrous materials (Level 2). 6.2.1.2.2 Describe the application of non-ferrous materials (Level 2). 2022-05-18 B-06a Materials and Hardware CASA Part 66 - Training Materials Only Page 38 of 229 Properties of Non-Ferrous Metals Non-Ferrous Metals Much of the metal used on aircraft contains no iron. The term that describes metals which have elements other than iron as their base is non-ferrous. Aluminium, copper, titanium and magnesium are some of the more common non-ferrous metals used in aircraft construction and repair. Examples of non-ferrous metals Identifying Aluminium Aluminium is a silver-white metallic element obtained by electrolysing bauxite. Aluminium sheets 2022-05-18 B-06a Materials and Hardware CASA Part 66 - Training Materials Only Page 39 of 229 Pure aluminium lacks sufficient strength to be used for aircraft construction. However, its strength increases considerably when it is alloyed, or mixed with other compatible metals. For example, when aluminium is mixed with copper or zinc, the resultant alloy is as strong as steel with only one third the weight. Furthermore, the corrosion resistance possessed by the aluminium carries over to the newly formed alloy. Aluminium alloys are classified by their major alloying ingredient. The elements most commonly used for aluminium alloying are: copper magnesium manganese zinc. There are two main classes of aluminium alloys: Wrought alloys, rolled from an ingot or extruded from customer-specified shapes Cast alloys, poured as a liquid into a mould and cooled into a solid shape. Most aircraft parts are wrought aluminium alloys. Wrought aluminium alloy 2022-05-18 B-06a Materials and Hardware CASA Part 66 - Training Materials Only Page 40 of 229 Wrought Aluminium Alloys Designation System Wrought aluminium alloys are identified by a four-digit index system. Aluminium alloy four-digit number system 1xxx Series The 1xxx Series is the only exception to the wrought alloy designation system. The first digit indicates the minimum aluminium content is 99% and there is no major alloying element. The second digit indicates modifications to impurity limits. If the second digit is zero, there is no special control on individual impurities, eg: 1000. The third and fourth digits provide the minimum aluminium percentage above 99%. Thus, 1100 indicates minimum aluminium content of 99.00% with individual impurity control. Likewise, 1030 indicates 99.30% minimum aluminium without special control of individual impurities. The designations 1130, 1230, 1330, etc. indicate the same purity with special control of one or more impurities. 2022-05-18 B-06a Materials and Hardware CASA Part 66 - Training Materials Only Page 41 of 229 2xxx Through 9xxx Series The major alloying elements are indicated by the first digit, as follows: 2xxx – Copper 3xxx – Manganese 4xxx – Silicon 5xxx – Magnesium 6xxx – Magnesium and silicon 7xxx – Zinc 8xxx – Other element 9xxx – Unused series. The second digit indicates alloy modification. If the second digit is zero, it indicates the original alloy. Digits 1 through 9, which are assigned consecutively, indicate alloy modifications. The last two digits have no special significance, serving only to identify the different alloys in the group (number has no significance but is unique). Aviation Australia Percentage of alloying element table 2022-05-18 B-06a Materials and Hardware CASA Part 66 - Training Materials Only Page 42 of 229 Aluminium and Alloys Series Alloys within the 1xxx Series are made of pure aluminium with the following features: Strain-hardenable High formability, corrosion resistance and electrical conductivity Electrical, chemical applications Aluminium 1xxx alloy - pure aluminium ingot Alloys within the 2xxx Series utilise copper as the principle alloying agent. When aluminium is mixed with copper, certain metallic changes take place in the resultant alloy’s grain structure. For the most part, these changes are beneficial and produce greater strength. However, a major drawback to aluminium-copper alloys is their susceptibility to intergranular corrosion when improperly heattreated. Most aluminium alloy used in aircraft structures is aluminium-copper. Two of the most commonly used in the construction of skins and rivets are 2017 and 2024. 2022-05-18 B-06a Materials and Hardware CASA Part 66 - Training Materials Only Page 43 of 229 Aluminium 2xxx alloy The 3xxx Series alloys have manganese as the principle alloying element and are generally considered non-heat-treatable. The most common variation is 3003, which offers moderate strength and has good working characteristics. Aluminium 3xxx alloy The 4xxx Series aluminium is alloyed with silicon, which lowers a metal’s melting temperature. This results in an alloy that works well for welding and brazing. 2022-05-18 B-06a Materials and Hardware CASA Part 66 - Training Materials Only Page 44 of 229 Aluminium 4xxx alloy Magnesium is used to produce the 5xxx Series alloys. These alloys possess good welding and corrosion-resistance characteristics. However, if the metal is exposed to high temperatures or excessive cold-working, its susceptibility to corrosion increases. Aluminium 5xxx alloy - Aluminium magnesium alloy wire If silicon and magnesium are added to aluminium, the resultant alloy carries a 6xxx Series designation that have medium strength with good forming and corrosion-resistance properties. 2022-05-18 B-06a Materials and Hardware CASA Part 66 - Training Materials Only Page 45 of 229 Aluminium 6xxx alloy When parts require more strength and little forming, harder aluminium alloys are employed. The 7xxx Series aluminium alloys are made harder and stronger by the addition of zinc. Some widely used forms of aluminium-zinc alloys are 7075 and 7178. For example, on a medium-sized passenger aircraft: Frames, stringers, keel and floor beams, and wing ribs made of aluminium alloy 7075 (aluminium and zinc) – High mechanical properties and improved stress corrosion cracking resistance Bulkheads, window frames and landing gear beam made of aluminium alloy 7079 (aluminium and zinc) – Tempered to minimise residual heat treatment stresses Wing upper skin, spars and beams made of aluminium alloy 7178 (aluminium, zinc, magnesium and copper) – High compressive-strength-to-weight ratio Landing gear beam made of aluminium alloy 7175 (aluminium, zinc, magnesium and copper) – A very tough, very high-tensile-strength alloy Wing lower skin made of aluminium alloy 7055 (aluminium, zinc, magnesium and copper) – Superior stress corrosion. 2022-05-18 B-06a Materials and Hardware CASA Part 66 - Training Materials Only Page 46 of 229 Aluminium alloys are extensively used in major airframe structures The 8xxx Series provides exceptionally high strength and elasticity, so this alloy is used for aerospace applications where an increases in stiffness combined with high strength reduces component weight. Aluminium 8xxx alloys - the fractured surfaces of the 8090 Al-Li alloy 2022-05-18 B-06a Materials and Hardware CASA Part 66 - Training Materials Only Page 47 of 229 The 9xxx Series alloys are unassigned at this time. Clad Aluminium Alloy (Alclad) Most external aircraft surfaces are made of Alclad aluminium. Alclad is a pure aluminium coating that is rolled onto both surfaces of a heat-treated aluminium alloy sheets used for aircraft construction. The clad surface greatly increases the corrosion resistance of an aluminium alloy. However, if it is penetrated, corrosive agents can attack the alloy within. For this reason, sheet metal should be protected from scratches and abrasions. In addition to providing a starting point for corrosion, abrasions create potential stress points. Clad aluminium alloy on wing in construction 2022-05-18 B-06a Materials and Hardware CASA Part 66 - Training Materials Only Page 48 of 229 Heat Treatment of Aluminium Alloys Heat Treatment Heat treatment is a series of operations involving the heating and cooling of metals in their solid state. Its aim is to make the metal more useful, serviceable and safe for a definite purpose. Heattreating a metal can make it harder, stronger and more resistant to impact. It can also make a metal softer and more ductile. However, one heat-treating operation cannot produce all these characteristics. In fact, some properties are often improved at the expense of others. In being hardened, for example, a metal may become brittle. All heat-treating processes are similar in that they involve the heating and cooling of metals. They differ, however, in the temperature to which the metal is heated and the rate at which it is cooled. Precipitation heat-treatment oven Two types of heat treatments are used on aluminium alloys: solution heat treatment and precipitation heat treatment. 2022-05-18 B-06a Materials and Hardware CASA Part 66 - Training Materials Only Page 49 of 229 Solution Heat Treatment The process of heating certain aluminium alloys to allow the alloying element to mix with the base metal is called solution heat-treating. In this procedure, metal is heated in either a molten sodium or potassium nitrate bath or in a hot-air furnace to a temperature just below its melting point. As an example the temperature is then held to within a small tolerance of this temperature and the base metal is soaked until the alloying element is uniform throughout. Once the metal has sufficiently soaked, it is removed from the furnace and cooled or quenched. It is extremely important that the removal of an alloy from the furnace to the quench is performed within a specified time (approx.10 seconds). The reason for this is that when metal leaves the furnace and starts to cool, its alloying metals begin to precipitate out of the base metal. If this process is not stopped, large grains of alloy become suspended in the aluminium and weaken the alloy. Excessive precipitation also increases the likelihood of intergranular corrosion. To help minimise the amount of alloying element that precipitates out of a base metal, a quenching medium is selected to ensure the proper cooling rate. For example, a water bath provides the appropriate cooling rate for aluminium alloys. Thin sheet metal normally warps and distorts when it is quenched, so it must be straightened immediately after it is removed from the quench. After the quench, all metals must be rinsed thoroughly since the salt residue from the sodium or potassium nitrate bath can lead to corrosion if left on the alloy. Solution heat treatment - allows Solution heat treatment 2022-05-18 B-06a Materials and Hardware CASA Part 66 - Training Materials Only Page 50 of 229 Precipitation Heat Treatment Heat-treatable aluminium alloys are comparatively soft when first removed from a quench. With time, however, the metal becomes hard and gains strength. When an alloy is allowed to cool at room temperature, it is referred to as natural aging and can take several hours or several weeks. For example, aluminium alloyed with copper gains about 90% of its strength in the first half-hour after it is removed from the quench and becomes fully hard in about 4 or 5 days. Precipitation heat treatment An alloy’s aging process time can be lengthened or shortened. For example, the aging process can be slowed by storing a metal at a sub-freezing temperature immediately after it is removed from the quench. On the other hand, the aging process can be accelerated by reheating a metal and allowing it to soak for a specified period of time. This type of aging is called artificial age-hardening, precipitation-hardening or precipitation heat treatment. This process develops hardness, strength and corrosion resistance by locking a metal’s grain structure together. Naturally aged alloys, such as copper-zinc-magnesium alloys, derive their full strength at room temperature in a relatively short period and require no further heat treatment. However, other alloys, particularly those with high zinc content, need thermal treatment to develop full strength. These alloys are called artificially aged alloys. 2022-05-18 B-06a Materials and Hardware CASA Part 66 - Training Materials Only Page 51 of 229 Naturally aged alloy 2022-05-18 B-06a Materials and Hardware CASA Part 66 - Training Materials Only Page 52 of 229 Annealing Annealing is a process that softens a metal and decreases internal stress. In general, annealing is the opposite of hardening. To anneal an aluminium alloy, the metal’s temperature is raised to an annealing temperature and held there until the metal becomes thoroughly heat-soaked. When annealing clad aluminium metals, they should be heated as quickly and as carefully as possible. The reason for this is that if clad aluminium is exposed to excessive heat, some of the core material tends to mix with the cladding. This reduces the metal’s corrosion resistance. Aviation Australia Thermal treatment table 2022-05-18 B-06a Materials and Hardware CASA Part 66 - Training Materials Only Page 53 of 229 Aluminium Alloy Temper Designations Heat-treatable alloys have their hardness condition designated by the letter T followed by one or more numbers. Commonly used designations includes: T – Solution heat-treated. T3 – Solution heat-treated, followed by strain-hardening. Different amounts of strainhardening of the heat-treated alloy are indicated by a second digit. For example, T36 indicates that the material has been solution heat-treated and has had its thickness reduced 5% by coldrolling. T4 – Solution heat-treated, followed by natural aging at room temperature to a stable condition. T5 – Artificially aged after being rapidly cooled during a fabrication process such as extrusion or casting. T6 – Solution heat-treated, followed by artificial aging (precipitation heat-treated). 2022-05-18 B-06a Materials and Hardware CASA Part 66 - Training Materials Only Page 54 of 229 Reheat Treatment A material which has been previously heat-treated can generally be heat-treated several times. As an example, rivets made of 2017 or 2024 are extremely hard and typically receive several heat treatments to make them soft enough to drive. The number of solution heat treatments allowed for clad materials is limited due to the increased diffusion of core material into the cladding. This diffusion results in decreased corrosion resistance. As a result, clad material is generally limited to no more than three heat treatments. Reheat treatment facility 2022-05-18 B-06a Materials and Hardware CASA Part 66 - Training Materials Only Page 55 of 229 Non-Heat-Treatable Aluminium The non-heat-treatable aluminium alloys are usually designated, therefore, in the 1000, 3000, 4000, 5000 Series. Their properties can be adjusted by cold work, usually by cold-rolling. Commercially pure aluminium does not benefit from heat treatment since there are no alloying materials in its structure. Non-heat treatable alloys Strain-Hardening Both heat-treatable and non-heat-treatable aluminium alloys can be strengthened and hardened through strain-hardening, also referred to as cold-working or work-hardening. This process requires mechanically working a metal at a temperature below its critical range. Strainhardening alters the grain structure and hardens the metal. The mechanical working can consist of rolling, drawing or pressing. Strain hardening 2022-05-18 B-06a Materials and Hardware CASA Part 66 - Training Materials Only Page 56 of 229 Heat-treatable alloys have their strength increased by rolling after they have been solution heattreated. On the other hand, non-heat-treatable alloys are hardened in the manufacturing process when they are rolled to their desired dimensions. However, at times these alloys are hardened too much and must be partially annealed. Hardness Designations Where appropriate, a metal’s hardness, or temper, is indicated by a letter designation that is separated from the alloy designation by a dash. When the basic temper designation must be more specifically defined, one or more numbers follow the letter designation. The digit following the designations H1, H2 and H3 indicates the degree of strain-hardening. For example, the number 8 represents the maximum tensile strength, while O indicates an annealed state. Therefore, for example, an H38 material has been strain- hardened and stabilised, and is fully hard. 2022-05-18 B-06a Materials and Hardware CASA Part 66 - Training Materials Only Page 57 of 229 Other Alloy Types Magnesium and Its Alloys Magnesium alloys are used for castings and in their wrought form are available in sheets, bars, tubing and extrusions. Magnesium is one of the lightest metals with sufficient strength and suitable working characteristics for use in aircraft structures. It has a lower density than aluminium and weighs only about two thirds as much as aluminium. Wheel assemblies commonly use magnesium alloys The drawbacks to using magnesium are: High susceptibility to corrosion – This is overcome by treating the surface with chemicals that form an oxide film and exclude oxygen. Tendency to crack when formed – This is overcome by heating the parts when forming, such as hot-dimpling thin material. Readiness to burn in a dust or small particle form. For this reason, caution must be exercised when grinding and machining magnesium. If a fire occurs, extinguish it by smothering it with dry sand or some other dry material that excludes air from the metal and cools its surface. If water is used, it will only intensify the fire. 2022-05-18 B-06a Materials and Hardware CASA Part 66 - Training Materials Only Page 58 of 229 Grinding magnesium alloy Solution heat treatment of magnesium alloys increases tensile strength, ductility and resistance to shock. If it is artificially aged (precipitation heat-treated) after solution heat treatment, the hardness and yield strength are increased. Solution heat treatment increases hardness of magnesium alloys as used in gearbox and generator housings 2022-05-18 B-06a Materials and Hardware CASA Part 66 - Training Materials Only Page 59 of 229 Titanium and Its Alloys Titanium and its alloys are lightweight metals with very high strength. In addition to its light weight and high strength, titanium and its alloys have excellent corrosion resistance characteristics, particularly to the corrosive effects of salt water. However, since the metal is sensitive to both nitrogen and oxygen, it must be converted to titanium dioxide with chlorine gas and a reducing agent before it can be used. Because of its high strength-to-weight ratio, titanium is now used extensively in the civilian aerospace industry. Although titanium was once rare on commercial aircraft, modern jet transports now utilise alloys containing 10% to 15% titanium in structural areas. Titanium and its alloys - aircraft engine CFM56, fan blades, TA6V titanium alloy Nickel and its Alloys Nickel is a silver-white metallic element and its two most commonly used alloys are: Monel Inconel. 2022-05-18 B-06a Materials and Hardware CASA Part 66 - Training Materials Only Page 60 of 229 Monel Monel contains nickel and copper with small amounts of iron and manganese. Monel can be welded and has very good machining characteristics. Certain types of Monel, especially those containing small percentages of aluminium, are heat-treatable to tensile strengths equivalent to steel. Monel works well in gears and parts that require high strength and toughness, as well as for parts in exhaust systems that require high strength and corrosion resistance at elevated temperatures. Monel rivets are also available for aircraft structural applications. Nickel and its alloys - Monel 2022-05-18 B-06a Materials and Hardware CASA Part 66 - Training Materials Only Page 61 of 229 Inconel Inconel contains nickel and chromium with small amounts of iron and other elements. These alloys find frequent use in turbine engines because of their ability to maintain their strength and corrosion resistance under extremely high temperatures. For example, Inconel can be found in nozzle supports, fan casings and blades. Inconel found in Pratt and Whitney gas turbine engine Inconel and stainless steel are similar in appearance and are frequently used in the same areas. Differentiating between the two must be done through a chemical test. 2022-05-18 B-06a Materials and Hardware CASA Part 66 - Training Materials Only Page 62 of 229 Copper and its Alloys Copper is a bright reddish metallic element often occurring in thin sheets or plates filling narrow cracks or fissures. Neither copper nor its alloys find much use as structural materials in aircraft construction. However, due to its excellent electrical and thermal conductivity, copper is the primary metal used for electrical wiring. Of the several alloys that use copper as a base, the following are the primary alloys found on aircraft: Brass – commonly used in electrical components due to is high conductivity. Bronze – used in bushings, bearings, fuel metering valves and valve seats. Beryllium – one of the most used copper alloys. Beryllium is used for diaphragms, precision bearings and bushings, ball cages and spring washers. Safety Data Sheets (SDS) identifies beryllium copper as a hazardous material because grinding, dust or fumes produce airborne contaminants. Copper used in electrical wire and components 2022-05-18 B-06a Materials and Hardware CASA Part 66 - Training Materials Only Page 63 of 229 Aircraft Materials - Metallic Testing (6.1.2 and 6.2.2) Learning Objectives 6.1.2. Recall testing of ferrous materials for hardness, tensile strength, fatigue strength and impact resistance (Level 1). 6.2.2 Recall testing of non-ferrous materials for hardness, tensile strength, fatigue strength and impact resistance (Level 1). 2022-05-18 B-06a Materials and Hardware CASA Part 66 - Training Materials Only Page 64 of 229 Testing of Metallic Materials Metal Testing Once a heat-treatment process has been carried out, the material must be tested to ensure that the desired qualities have been achieved. Some of the properties tested for are: Hardness Tensile strength Fatigue strength Impact resistance. Note: Testing is carried out with a test piece consisting of the same material and thickness of the component which was heat-treated along with the component. Image by IABG Dresden via Wikipedia Commons Licence IABG Fatigue test of the Airbus A380 Wing 2022-05-18 B-06a Materials and Hardware CASA Part 66 - Training Materials Only Page 65 of 229 Hardness Testing Since the strength of most metals varies with hardness, it is often required to measure the hardness of a metal. The two most widely used methods of hardness measurement are the Brinell and Rockwell methods. Brinell Hardness Tester The Brinell hardness tester uses a hydraulic force to impress a spherical penetrator into the surface of a sample. This force is hydraulically applied by a hand pump and read on a pressure gauge. When the sample is removed from the tester, the diameter of the impression is measured with a special calibrated microscope. The diameter of the impression is then converted into a Brinell number by using a chart furnished with the tester. Aviation Australia Brinell hardness tester 2022-05-18 B-06a Materials and Hardware CASA Part 66 - Training Materials Only Page 66 of 229 Brinell hardness tester Relevant Youtube link: Brinell hardness testing 2022-05-18 B-06a Materials and Hardware CASA Part 66 - Training Materials Only Page 67 of 229 Rockwell Hardness Tester The Rockwell hardness tester gives the same information as the Brinell tester, except that it measures the depth to which the penetrator sinks into the material rather than the diameter of the impression. A minor load is applied and the machine is zeroed. A major load is then applied and the dial on the tester indicates the depth the penetrator sinks into the metal. Instead of indicating the depth of penetration in thousandths of an inch, it indicates it in Rockwell numbers on either a red or a black scale. Rockwell testers use three types of penetrators and three major loads that may be applied during the test. Benchtop Rockwell hardness tester Relevant Youtube link: Rockwell testing 2022-05-18 B-06a Materials and Hardware CASA Part 66 - Training Materials Only Page 68 of 229 Rockwell hardness tester Tensile Strength Testing Tensile strength of a ferrous metal is tested by applying a longitudinal load to a sample of material and plotting the load against the resulting elongations on a graph. Tensile testing Relevant Youtube link: Tensile test 2022-05-18 B-06a Materials and Hardware CASA Part 66 - Training Materials Only Page 69 of 229 Tensile testing 2022-05-18 B-06a Materials and Hardware CASA Part 66 - Training Materials Only Page 70 of 229 Fatigue Strength Testing Fatigue strength testing establishes the stress level at which structural failure will occur. A specially shaped test piece is gripped at one end, while at the other end a ball race is fitted. A load is suspended from the ball race and the test piece is then rotated from the end at which it is held by an electric motor. Under the action of the overhung load, it is stressed in tension and compression once every revolution. The number of cycles completed is measured to determine fatigue failure. This number of cycles is then classified as fatigue life. Fatigue strength testing - The Wohler Cantilever bending fatigue machine 2022-05-18 B-06a Materials and Hardware CASA Part 66 - Training Materials Only Page 71 of 229 Airframe Fatigue Testing Aircraft are subjected to fatigue tests. The purpose of an airframe fatigue test is to provide key data that help design engineers identify the likelihood and causes of premature fatigue damage or wear on the airplane's structure and structural components. Aircraft are subjected to fatigue strength tests to determine fatigue life of components, which helps with the development of maintenance programs. An F35 Lighting II multirole combat aircraft fatigue test is shown. Airframe fatigue testing - F35 at British Aerospace Relevant Youtube link: Boeing 787 fatigue testing 2022-05-18 B-06a Materials and Hardware CASA Part 66 - Training Materials Only Page 72 of 229 Impact Resistance Testing Two tests, the Charpy and Izod impact tests, are used to measure the impact resistance (or impact strength) of a metal. Both are mechanical tests in which a pendulum hammer (swinging through a fixed distance) fractures a standard-size notched piece of material with one blow. The main difference between the Izod impact test and the Charpy impact test is that each one uses a different beam configuration (cantilevered configuration vs a three-point beam configuration). Impact resistance testing 2022-05-18 B-06a Materials and Hardware CASA Part 66 - Training Materials Only Page 73 of 229 Izod and Charpy testing Relevant Youtube link: Izod impact testing 2022-05-18 B-06a Materials and Hardware CASA Part 66 - Training Materials Only Page 74 of 229 Charpy V-notch (CVN) Technique By far the most common impact testing method used today for metals is the Charpy V-notch impact test. In this technique, the specimen is in the shape of a bar of square cross section with a V-notch. The load is applied as an impact below from a weighted pendulum hammer that is released from an initial height. The pendulum with a knife edge strikes and fractures the specimen at the notch. The pendulum continues its swing, rising to a maximum final height, which is lower than the initial height. The energy necessary to fracture the test piece is directly calculated from the difference in initial and final heights of the swinging pendulum. Charpy V-Notch test Relevant Youtube link: Charpy impact test 2022-05-18 B-06a Materials and Hardware CASA Part 66 - Training Materials Only Page 75 of 229 Aircraft Materials - Composite and NonMetallic (6.3.1.1) Learning Objectives 6.3.1.1 Identify how the use of composite materials in aircraft construction has evolved (S). 6.3.1.1.1.1 Describe the characteristics and properties of common composite materials, other than wood, used in aircraft (Level 2). 6.3.1.1.1.2 Describe the characteristics and properties of non-metallic materials, other than wood, used in aircraft (Level 2). 6.3.1.1.1.3 Identify common composite and non-metallic materials, other than wood, used in aircraft (Level 1). 6.3.1.1.2 Describe the use of sealant and bonding agents suitable for aircraft use with common composite and non-metallic materials, other than wood (Level 2). 2022-05-18 B-06a Materials and Hardware CASA Part 66 - Training Materials Only Page 76 of 229 Non-Metallic Structural Materials Use of Composite Materials in Aircraft Construction Non-metallic structural materials played a key role in the early days of aviation. However, after the introduction of aluminium, non-metallic materials saw considerably less use. Today, aluminium is still the most widely used material in the construction and repair of aircraft. However, since its introduction, several new materials have come into use, many of which are spin-offs from the space program. These materials once again have the aviation industry taking a close look at non-metallic materials for use on aircraft, and they are becoming more common in construction of more aircraft components, even fuselages and wings. Non-Metallic materials used in aircraft construction 2022-05-18 B-06a Materials and Hardware CASA Part 66 - Training Materials Only Page 77 of 229 What Is a Composite Structure? Composite Structure The term composite is used to describe two or more materials that are combined to form a structure that is much stronger than the individual components. Composite structures differ from metallic structures in several ways: excellent elastic properties, customisability in strength and stiffness, damage tolerance characteristics and sensitivity to environmental factors. Consequently, composites require a vastly different approach compared to metals with regard to their design, fabrication and assembly, quality control and maintenance. Difference in design, fabrication, assembly, quality control and maintenance of composites One main advantage to using a composite over a metal structure is its high strength-to-weight ratio. Weight reduction is a primary objective when designing structures using composite materials. 2022-05-18 B-06a Materials and Hardware CASA Part 66 - Training Materials Only Page 78 of 229 Types of fibres and bonding material determine composite strength In addition, the use of composites allows the formation of complex, aerodynamically contoured shapes, reducing drag and significantly extending the range of the aircraft. Composite strength depends on the types of fibres and bonding materials used and how the part is engineered to distribute and withstand specific stresses. 2022-05-18 B-06a Materials and Hardware CASA Part 66 - Training Materials Only Page 79 of 229 Composites in Aircraft Structures Composite materials are found in the manufacture of primary flight controls and high-integrity structural repairs in aircraft. Amount of composite materials used in A320 Composite materials used in primary flight controls 2022-05-18 B-06a Materials and Hardware CASA Part 66 - Training Materials Only Page 80 of 229 Composite materials used in high integrity structural repairs Composite Elements In aircraft construction, most currently produced composites consist of a reinforcing material to provide structural strength, joined with a matrix material to serve as the bonding substance. In addition, adding core material saves overall weight and gives shape to the structure. Composites with reinforcing material 2022-05-18 B-06a Materials and Hardware CASA Part 66 - Training Materials Only Page 81 of 229 The three main parts of a fibre-reinforced composite are the fibre, the matrix and the interface or boundary between the individual elements of the composite. 2022-05-18 B-06a Materials and Hardware CASA Part 66 - Training Materials Only Page 82 of 229 Composite Fibres Reinforcing Fibres Reinforcing fibres provide the primary structural strength to the composite structure when combined with a matrix. Reinforcing fibres can be used in conjunction with one another (hybrids), woven into specific patterns (fibre science), combined with other materials such as rigid foams (sandwich structures) or simply used in combination with various matrix materials. Each type of composite combination provides specific advantages. Following are the four most common types of reinforcing fibres used in commercial aircraft composites: Fibreglass (glass cloth) Aramid Carbon/graphite Ceramic. Reinforcing fibres 2022-05-18 B-06a Materials and Hardware CASA Part 66 - Training Materials Only Page 83 of 229 Fibreglass (Glass Cloth) Fibreglass is made from small strands of molten silica glass (about 1260 °C) that are spun together and woven into cloth. Many different weaves of fibreglass are available, depending on the particular application. Its widespread availability and its low cost make fibreglass one of the most popular reinforcing fibres. Fibreglass weighs more than most other composite fibres, but has less strength. In the past, it was used for non-structural applications; the weave was heavy and added polyester resins made the part brittle. Recently, however, newly developed matrix formulas have increased the benefits of using fibreglass. Fibreglass E and S glass is high tensile strength fibreglass 2022-05-18 B-06a Materials and Hardware CASA Part 66 - Training Materials Only Page 84 of 229 Aramid In the early 1970s, DuPont introduced Aramid, an organic aromatic-polyamide polymer commercially known as Kevlar®. Aramid exhibits high tensile strength, exceptional flexibility, high tensile stiffness, low compressive properties and excellent toughness. The tensile strength of Kevlar® composite material is approximately 4 times greater than alloyed aluminium. Aramid fibres are non-conductive and produce no galvanic reaction with metals. Another important advantage is its outstanding strengthto-weight ratio; it is very light compared to other composite materials. Aramid-reinforced composites also demonstrate excellent vibration-damping characteristics in addition to a high degree of shatter and fatigue resistance. Kevlar 2022-05-18 B-06a Materials and Hardware CASA Part 66 - Training Materials Only Page 85 of 229 Aramid (Kevlar) A disadvantage of Aramid is that it stretches, which can cause problems when it is cut. Drilling Aramid can also be a problem if the drill bit grabs a fibre and pulls until it stretches to its breaking point. 2022-05-18 B-06a Materials and Hardware CASA Part 66 - Training Materials Only Page 86 of 229 Carbon Carbon fibre Advantages of carbon materials are their high compressive strength and degree of stiffness. However, carbon fibre is cathodic, while aluminium and steel are anodic. Thus, carbon promotes galvanic corrosion when bonded to aluminium or steel, and special corrosion-control techniques are needed to prevent this occurrence. Carbon materials are kept separate from aluminium components when sealants and corrosion barriers, such as fibreglass, are placed at the interfaces between composites and metals. To further resist galvanic corrosion, anodise, prime and paint any aluminium surfaces prior to assembly with carbon material. Carbon-fibre composites are used to fabricate primary structural components such as ribs and wing skins. Even very large aircraft can be designed with a reduced number of reinforcing bulkheads, ribs and stringers thanks to the high strength and high rigidity of carbon-fibre composites. Carbon fibre is stronger in compressive strength than Kevlar®, but it is more brittle. 2022-05-18 B-06a Materials and Hardware CASA Part 66 - Training Materials Only Page 87 of 229 Ceramic Fibre Ceramic fibres are used in high-temperature applications. This form of composite will retain most of its strength and flexibility at temperatures up to 1200 °C. For example, tiles on the space shuttle are made of a special ceramic composite that dissipates heat quickly. Some firewalls are also made of ceramic-fibre composites. The most common use of ceramic fibres in civilian aviation is in combination with a metal matrix for high-temperature applications. Ceramic fibre sheets 2022-05-18 B-06a Materials and Hardware CASA Part 66 - Training Materials Only Page 88 of 229 Gas turbine engine - ceramic fibre inlet guide vanes 2022-05-18 B-06a Materials and Hardware CASA Part 66 - Training Materials Only Page 89 of 229 Fibre Science The selective placement of fibres needed to obtain the greatest amount of strength in various applications is known as fibre science. The strength and stiffness of a composite depends on the orientation of the plies to the load direction. A sheet-metal component will have the same strength no matter which direction it is loaded. For example, if a wing in flight bends upwards as well as twists, the part can be manufactured so one layer of fibres runs the length of the wing, reducing the bending tendency, and another layer runs at 45° and at 90° to limit the twisting. Each layer may have the major fibres running in a different direction. The strength of the fibres is parallel to the direction the threads run. This is how designers can customise fibre direction for the type of stress the part might encounter. In flight, the structure tends to bend and twist. The fibre layers are laid in a way that limits these forces, thereby customising a part to the type of stresses encountered. Fibres direction can be customised to reduce stress 2022-05-18 B-06a Materials and Hardware CASA Part 66 - Training Materials Only Page 90 of 229 Composite Fabrics Fabric Orientation When working with composite fibres, it is important to understand the construction and orientation of the fabric because all design, manufacturing and repair work begins with the orientation of the fabric. Unlike in metallic structures, the strength of a composite structure relies on the proper placement and use of the reinforcing fibres. Some of the terms used to describe fibre orientation are warp, weft, selvage edge and bias. Fabric orientation Warp The warp of threads in a section of fabric run the length of the fabric as it comes off the roll or bolt. Warp direction is designated as 0°. There are typically more threads woven into the warp direction than the fill direction, making the fibre stronger in the warp direction. Because warp is critical in fabricating or repairing composites, insertion of another colour or type of thread at periodic intervals identifies the warp direction. Weft/Fill Weft, or fill, threads of the fabric are those that run perpendicular (90°) to the warp fibres. The weft threads interweave with the warp threads to create the reinforcing cloth. 2022-05-18 B-06a Materials and Hardware CASA Part 66 - Training Materials Only Page 91 of 229 Selvage Edge The selvage edge of the fabric is the tightly woven edge parallel to the warp direction, which prevents edges from unravelling. The selvage edge is removed before the fabric is utilised. The weave of the selvage edge is different from that of the body of the fabric and does not have the same strength characteristics as the rest of the fabric. Bias The bias is the fibre orientation that runs at a 45° angle (diagonal) to the warp threads. The bias allows for manipulation of the fabric to form contoured shapes. Fabrics can often be stretched along the bias but seldom along the warp or fill. Warp and selvage edge 2022-05-18 B-06a Materials and Hardware CASA Part 66 - Training Materials Only Page 92 of 229 Weft and bias 2022-05-18 B-06a Materials and Hardware CASA Part 66 - Training Materials Only Page 93 of 229 Fabric Styles Fabrics used in composite construction are manufactured in several different styles: unidirectional bidirectional multidirectional. Component designers can use any or all of these fabric styles, depending on the strength and flexibility requirements of the component part. Unidirectional A unidirectional fibre orientation is one in which all of the major fibres run in one direction, giving the fabric the majority of its strength in a single direction. This type of fabric is not woven together, meaning there are no fill fibres. Occasionally, small cross threads are used to hold the major fibre bundles in place. However, the cross threads are not considered woven fibres. Unidirectional fibres held by cross threads 2022-05-18 B-06a Materials and Hardware CASA Part 66 - Training Materials Only Page 94 of 229 Bidirectional/Multi-directional Bidirectional or multi-directional fabric orientation calls for the fibres to run in two or more directions. Bidirectional fabrics are woven with the warp threads usually outnumbering the weft, so there is usually more strength in the warp direction than in the weft. Multidirectional fabric orientation Fabric Weaves Fabrics are woven together in a number of weaves and weights. Woven fabrics are more resistant to fibre breakout, delamination and damage than unidirectional materials. Because of the wide variety of uses and strength requirements, composite fabrics are available in many weaves. Some of them are: Plain weave Satin weave Twill weave. 2022-05-18 B-06a Materials and Hardware CASA Part 66 - Training Materials Only Page 95 of 229 Plain Weave In this most simple weave pattern, warp and fill yarns are interlaced over and under each other in alternating fashion. The plain weave provides good stability, porosity and the least yarn slippage for a given yarn count. Plain weave Satin Weave In the satin weave, the warp floats or skips over as many as 12 fill yarns before being woven in. A satin weave is notable for its smooth surface created by the relatively long warp yarn floats. Satin weave 2022-05-18 B-06a Materials and Hardware CASA Part 66 - Training Materials Only Page 96 of 229 Twill Weave Twill weaves repeat on three or more warp and fill yarns. Twill weaves have a distinctive diagonal line on the surface of the fabric and come in many variations. A two by two Twill weave The most common weaves used in advanced composite aircraft construction are the plain and satin weaves. Common weave patterns 2022-05-18 B-06a Materials and Hardware CASA Part 66 - Training Materials Only Page 97 of 229 Composite Bonding Matrix Systems The matrix is a bonding material that completely surrounds the fibre, giving it extra strength. The strength of a composite lies in the ability of the matrix to transfer stress to the reinforcing fibres. An advanced composite uses various manufacturing techniques and newer matrix formulas with newer reinforcing fabrics. Matrix system Polyester resin is an example of an early matrix formula used with fibreglass for many non-structural applications such as fairings, spinners and trim. The old polyester/fibreglass formulas did not offer sufficient strength for fabricating primary structural members; it can be somewhat brittle. The newer matrix materials display remarkably improved stress-distributing characteristics, heat resistance, chemical resistance and durability. Most of the newer matrix formulas for aircraft are epoxy resins. Resin matrices are two-part systems consisting of a resin and a catalyst or hardener, which acts as a curing agent. The term resin often means both parts together, not just the resin. 2022-05-18 B-06a Materials and Hardware CASA Part 66 - Training Materials Only Page 98 of 229 Resin Matrix Systems Resin matrix systems are a type of plastic. Some companies refer to composites as fibre-reinforced plastics. There are two general categories of plastics: thermoplastic thermosetting. By themselves, these resins do not have sufficient strength for use in structural applications, however, when used as a matrix and reinforced with other materials, they form the high strength, lightweight structural composites used today. 2022-05-18 B-06a Materials and Hardware CASA Part 66 - Training Materials Only Page 99 of 229 Thermoplastic Resins Thermoplastic resins use heat to form the part into the desired shape, one that is not necessarily permanent. If a thermoplastic is heated a second time, it will flow to form another shape. Two types of transparent thermoplastic materials are used for aircraft windshields and side windows: cellulose acetate and acrylic. Early aircraft used cellulose acetate plastic because of its transparency and light weight. However, it tends to shrink and turn yellow and therefore has almost completely been replaced. Acrylic plastics are identified by such trade names as Lucite or Plexiglas, or in Britain by the name Perspex. Acrylic is stiffer than cellulose acetate, is more transparent and, for all practical purposes, is colourless. Thermoplastic resin windshield 2022-05-18 B-06a Materials and Hardware CASA Part 66 - Training Materials Only Page 100 of 229 Thermosetting Resins Thermosetting resins are usually liquids or low-melting-point solids in their initial form. When used to produce finished goods, they are cured by the use of a catalyst, heat or a combination of the two. Once cured, solid thermosetting resins cannot be converted back to their original liquid form. Unlike thermoplastic resins, cured thermosets will not melt and flow, but will soften when heated (and lose hardness). Once formed, they cannot be reshaped. At this time, two common structural airframe applications are: Polyester resin Epoxy resin. Thermosetting resins use in airframe 2022-05-18 B-06a Materials and Hardware CASA Part 66 - Training Materials Only Page 101 of 229 Polyester Resin Polyester resin, an early thermosetting matrix formula, is mainly used with fibreglass composites to create non-structural applications such as fairings, spinners and aircraft trim. While fibreglass possesses many virtues, its greatest limitation lies in its lack of structural rigidity. Polyester resins give fibreglass cohesiveness and rigidity. Polyester resin wheel fairing The actual cure of polyester resin occurs when a chemical reaction between the catalyst and accelerator generates heat within the resin. The less surface area there is for heat to escape, the more heat remains in the resin and the faster it cures. Therefore, when submitted to identical conditions, a thick layer of resin cures more rapidly than a thin layer. 2022-05-18 B-06a Materials and Hardware CASA Part 66 - Training Materials Only Page 102 of 229 Polyester laminating resin Warning: Never mix accelerators directly with catalysts as they will violently react with each other, and catch on fire or explode, if not diluted by the resin first. 2022-05-18 B-06a Materials and Hardware CASA Part 66 - Training Materials Only Page 103 of 229 Epoxy Resins Most of the newer aircraft composite matrix formulas utilise epoxy resins, which are thermosetting plastic resins. Epoxy resin systems are well known for their outstanding adhesion, strength, and resistance to moisture and chemicals. Not all types of epoxy resin is suitable for every type of structure or repair. Make sure to use the resin called for in the manufacturer’s repair manual. Epoxy resins are two-part systems consisting of a base resin and a hardener – not a catalyst – for curing. Hardener is mixed in larger amounts than the catalyst used in the previously described polyester resin, which was an early thermosetting matrix formula. Epoxy resins 2022-05-18 B-06a Materials and Hardware CASA Part 66 - Training Materials Only Page 104 of 229 Adhesives (Bonding Agents) Resins come in different forms. Resins used for laminating are generally thinner to allow proper saturation of the reinforcing fibres. Others are used for bonding and are typically known as adhesives or bonding agents because they glue parts together. Adhesive resins and catalysts are available either in premixed quantities or in separate containers. One of the most unique forms of adhesive is the film adhesive. This type of adhesive pre-blends the resin and catalyst on a thin film of plastic. Refrigeration of the film is required to slow the cure rate (the rate of change to its permanent form) of the resin. If left out at room temperature, the resin and catalyst will start to cure. In the freezer, the curing process slows, lengthening the shelf life of the film. Adhesive films are often used to help bond patches to a repair area. Adhesive films for patching Another form of adhesive is available in foam, which is primarily used to splice replacement honeycomb core segments to existing cores. When heat is applied to the adhesive, it foams up and expands into crevices. These types of foaming adhesives can also be used to permanently install fasteners. 2022-05-18 B-06a Materials and Hardware CASA Part 66 - Training Materials Only Page 105 of 229 Film adhesive 2022-05-18 B-06a Materials and Hardware CASA Part 66 - Training Materials Only Page 106 of 229 Pre-impregnated Materials Pre-impregnated fabrics, commonly known as ‘pre-pregs’, are fabrics that have the resin system already saturated into the fabric. Because many epoxy resins have high viscosity, it is often difficult to mix and work epoxy resins into the fabric to completely encapsulate the fibres. Fabrics are preimpregnated with the proper amount and weight of a resin matrix to eliminate the mixing and application details, such as proper mix ratios and application procedures. Pre-impregnating materials 2022-05-18 B-06a Materials and Hardware CASA Part 66 - Training Materials Only Page 107 of 229 Pre-impregnating unidirectional fabrics Pre-preg materials offer convenience over raw fabrics in many ways: The pre-preg contains the proper amount of matrix. The reinforcing fibres are completely encapsulated with the matrix. During hand lay-up, if a resin system has a high viscosity or is very thick, it is sometimes difficult to get the resin into and around each individual fibre to produce the strongest cure. This is not a problem with pre-preg fabrics. Pre-preg fabrics eliminate the need to manually weigh and mix components. In hand lay-up, the resin and curing agent must be properly weighed. In many cases, pre-preg materials produce a stronger component or repair. Pre-pregs were invented for use by aircraft manufacturers to reduce the problems associated with completely wetting the fabric with resin. They also save time and reduce the problems associated with weighing and mixing the resins. 2022-05-18 B-06a Materials and Hardware CASA Part 66 - Training Materials Only Page 108 of 229 Pre-preg fabrics also have disadvantages when working in a maintenance facility. Some of the disadvantages of working with pre-pregs are: Many pre-pregs must be stored in a freezer. This requirement must be met. If some pre-pregs are allowed to remain at room temperature for even a few hours, the resins/catalysts start their chemical reaction and begin to cure. Pre-preg fabrics usually have a limited shelf life even if kept in the freezer. Pre-preg material is much more expensive than raw fabric that can be impregnated with the same type of resin system. This is especially true if the material exceeds its shelf life and must be discarded. Moisture, dust or other contaminants will compromise bond durability. Pre-impregnated composite materials kept in cold storage Warning: Bags containing pre-preg material should be opened only in a controlled environment and not opened until the material has thawed to room temperature. 2022-05-18 B-06a Materials and Hardware CASA Part 66 - Training Materials Only Page 109 of 229 Fillers Fillers, also known as thixotropic agents, are materials added to resins to control viscosity and weight, to reduce pot life and cured strength, and to make application of the resin easier. Fillers increase the volume of the resin, making it less dense and less susceptible to cracking as well as lowering its weight. Most fillers are inert and will not react chemically with the resin. Microballoons, chopped fibres and flox are common types of fillers used in composite construction. Microballoons are small spheres manufactured from plastic or glass. Plastic microballoons must be mixed with a compatible resin system that will not dissolve the plastic. The advantages to using microballoons are that they provide greater concentrations of resin in the edges and corners of the structure; they are less dense, which reduces the overall weight; and they provide lower stress concentrations throughout the structure. However, microballoons do not add strength to the composite structure. Flox is the fuzzy fibre taken from the fabric strands. Both chopped fibres and flox may be used when added strength is desired. If a hole in a composite structure needs to be filled, a mixture of resin and flox will provide more strength than pure resin. Using pure epoxy resin produces brittle and heavy plugs. Composite fillers 2022-05-18 B-06a Materials and Hardware CASA Part 66 - Training Materials Only Page 110 of 229 Working With Resins and Catalysts Resin and Catalyst Terminology Shelf Life This is the time span that a product will remain useful. It should be listed on the label. Temperature during storage will affect the shelf life. Pot Life and Gel Time Pot life and gel time are strictly related to the activity of the catalyst. They are governed by both the proportion of the catalyst and the ambient temperature. For a given proportion of catalyst, the higher the air temperature, the shorter the pot life and gel time of the resin. Hardening Time Hardening time can vary greatly depending on the size and thickness of the moulding and the proportion of resin present. It will also again be affected by the air temperature. Maturing Time The further period of time over which the moulding will continue to gain hardness and, eventually, complete stability is called the maturing time. When fully matured, the moulding will achieve its maximum strength, hardness, chemical resistance and stability. 2022-05-18 B-06a Materials and Hardware CASA Part 66 - Training Materials Only Page 111 of 229 Mix Ratio A slightly improper mix ratio can make a tremendous amount of difference in the strength of the final composite. Because the mixing procedures are so important, they are always included with the resin containers. The resin manufacturer outlines the correct mixing procedures and this may be displayed on the container. Proper mixing procedures Manufacturers often produce pre-measured matrix packages. The advantage of using pre-packaged resin systems is that they eliminate the weighing process and therefore remove the possibility of a mixing ratio error. Pre-packaged and pre-measured resin 2022-05-18 B-06a Materials and Hardware CASA Part 66 - Training Materials Only Page 112 of 229 The resin and catalyst are divided into separate containers that are attached at one end. When they are ready for use, the partition which separates the resin from the catalyst is broken to allow the two to mix. Still within the package, the resin/catalyst combination is mixed together by squeezing and kneading the package to thoroughly blend the mixture. When completely mixed, the package is cut with scissors and the resin dispensed. Disposable cartridges that store, mix and apply two-component materials are also available and convenient to use. They are available in many sizes and can be tailored to specific uses. Like the premeasured packages, cartridges also eliminate mixing-ratio errors. To use epoxy cartridges, the seal that separates the two components must be broken with a plunger. The materials are then mixed together by moving the plunger in a twisting and up-and-down motion to thoroughly mix the resin and catalyst. The label describes how many strokes are required to give a thorough mix. A needle or syringe may then be installed onto the end of the cartridge, and the resin dispensed. Be sure to check the cartridge part number, shelf-life expiration date and any special instructions. Epoxy disposable cartridges 2022-05-18 B-06a Materials and Hardware CASA Part 66 - Training Materials Only Page 113 of 229 Disposing of Resins Dispose of cured polyester resin/epoxy products in accordance with local regulations. Time-expired polyester resin systems are disposed by mixing them with the appropriate catalyst and then disposing of the cured product in accordance with local regulations. Dispose of time-expired two-part epoxy resin systems by mixing the two components together and disposing of the cured product in accordance with local regulations. Do not dispose of unmixed, uncured polyester resin/epoxy in general waste bins. Do not dispose of catalyst-soaked rags in general waste bins as rags could spontaneously combust. Contact local hazardous-material-collection agencies for collection and disposal of large quantities of uncured product, accelerators and catalysts. 2022-05-18 B-06a Materials and Hardware CASA Part 66 - Training Materials Only Page 114 of 229 Aircraft Materials - Composite Maintenance, Inspection and Repairs (6.3.1.2) Learning Objectives 6.3.1.1.2.1 Describe the use of sealants suitable for aircraft use with common composite and non-metallic materials, other than wood (Level 2). 6.3.1.2.1.1 Describe the detection of defects in composite and non-metallic material other than wood and fabric (Level 2). 6.3.1.2.1.2 Describe the detection of deterioration in composite and non-metallic material other than wood and fabric (Level 2). 6.3.1.2.2 Describe the repair of composite and non-metallic material other than wood and fabric (Level 2). 2022-05-18 B-06a Materials and Hardware CASA Part 66 - Training Materials Only Page 115 of 229 Composite Inspection Composite Inspection Methods Today’s composite inspection techniques and non-destructive testing (NDT) methods typically involve the use of multiple methods to accurately determine the airworthiness of the structure. Fortunately, many metal inspection and NDT methods transfer to composite applications. Composite structures require ongoing inspection intervals along with non-scheduled damage inspection and testing. When a composite structure is damaged, it must first be thoroughly inspected to determine the extent of the damage, which often extends beyond the immediately apparent defect. Proper inspection and testing methods help determine the classification of damage, which is whether the damage is repairable or the part must be replaced. In addition, classifying the damage helps to determine the proper method of repair. The manufacturer’s structural repair manual outlines inspection procedures, damage classification factors, and recommended repair methods. Inspection of composite blades on a gas turbine engine 2022-05-18 B-06a Materials and Hardware CASA Part 66 - Training Materials Only Page 116 of 229 Visual Inspection Visual inspection is the most frequently used inspection method in aviation. Ideally, pilots, ground crew and maintenance technicians visually inspect the aircraft on a daily basis. This method of inspection is generally used to detect resin-rich areas, resin starvation, edge delamination, fibre break-out, cracks, blistering and other types of surface irregularities. A strong light and magnifying glass are useful tools for visual inspection. In extremely critical cases, a small microscope is helpful for determining whether the fibres in a cracked surface are broken or if the crack affects the resin only. Visual inspection 2022-05-18 B-06a Materials and Hardware CASA Part 66 - Training Materials Only Page 117 of 229 Tap Testing A tap testing inspection is an effective way to discover if a finished job/repair has a good bond line or has air pockets or other inclusions that may have caused a disbond. Tap testing inspection Tap testing using a small tap testing tool 2022-05-18 B-06a Materials and Hardware CASA Part 66 - Training Materials Only Page 118 of 229 Ultrasonic Inspection Ultrasonic inspection is the most common instrumental NDT method used on composites today. An ultrasonic tester is useful for detecting internal damage such as delaminations, core crush and other subsurface defects. Two common methods of ultrasonic testing include the pulse echo and through-transmission methods. Ultrasonic inspection In the pulse echo method, the tester generates ultrasonic pulses, sends them through the part and receives the return echo. The echo patterns are displayed on an oscilloscope. An advantage to the pulse echo method is that it requires access to only one side of the structure. The through-transmission method uses two transducers. One emits ultrasonic waves through the part and the other receives them. Defects located at multiple levels throughout the structure are more easily detected because the receiver, located on the backside of the part, receives the reduced number of sound waves that pass through the defects. 2022-05-18 B-06a Materials and Hardware CASA Part 66 - Training Materials Only Page 119 of 229 Radiographic Inspection Radiography or x-ray inspection is used to detect differences in the thickness or physical density when compared to the surrounding material of a composite. Unlike ultrasonic or tap testing, it can be used to detect surface or internal cracks, entrapped water inside honeycomb core cells, foreign objects in the composite structure, and the extent and size of the damage. Radiographic inspection Thermography Thermography locates flaws by detecting temperature variations at the surface of a damaged part. Heat is applied to the part and the temperature gradients are measured using an infrared camera. Thermography requires knowledge of the thermal conductivity of the test specimen and a reference standard for comparison purposes. https://www.infratec.eu/thermography/industries-applications/aerospace-industry/ Thermography image of an aircraft after landing 2022-05-18 B-06a Materials and Hardware CASA Part 66 - Training Materials Only Page 120 of 229 Thermography is also used to identify water ingress into aircraft structures, by imaging the aircraft in flight or post flight. 2022-05-18 B-06a Materials and Hardware CASA Part 66 - Training Materials Only Page 121 of 229 Composites Defects and Damage Damage Classifications Depending on the manufacturer of the aircraft, damage is usually classified according to three categories: Negligible – damage that may be corrected by a simple repair procedure with no restrictions on flight operations Repairable – damage to the skin, bond or core that cannot exist without placing restrictions on flight operations, but can be repaired Non-repairable – damage to the structure or component that cannot be repaired (component must be replaced). Areas of condensation remaining on a structure after the aircraft has warmed up following coldsoaking at altitude might indicate water ingress and should be investigated. Damage to composite fibres 2022-05-18 B-06a Materials and Hardware CASA Part 66 - Training Materials Only Page 122 of 229 Cosmetic Defects A cosmetic defect is a defect on the outer surface skin that does not involve damage to the structural reinforcing fibres. Cosmetic defects 2022-05-18 B-06a Materials and Hardware CASA Part 66 - Training Materials Only Page 123 of 229 Impact Damage Impact damage occurs when a foreign object strikes the part. The degree of damage may range from slight to severe. The most common cause of impact damage is careless handling during transportation or storage, or standing parts on their edge without adequate protection. The thin face sheets on a sandwich panel are very susceptible to impact damage. An area that has been subjected to impact damage should also be inspected for delamination around the impacted area. Nicking, chipping, cracking or breaking away pieces of the edge or corner can also be caused by improper handling. Impact damage 2022-05-18 B-06a Materials and Hardware CASA Part 66 - Training Materials Only Page 124 of 229 Delamination Delamination is the separation of fabric layers of material in a laminate. Delamination can occur with no visible indications from the outer skin. To compound the problem, delamination often accompanies other types of damage, particularly impact damage. This damage occurs as the result of several causes, including impact, moisture ingress in the fabric or lightning strikes. Delamination Disbonds Disbonding is a separation of the composite material from another material to which it has been adhesively bonded. This is different to a delamination, which refers to a similar separation between any plies or layers of the composite. Separation between the skin and core of a composite sandwich structure is separately referred to as a core disbond. A disbond may be the consequence of poor adhesion, service loading or impact damage. The disbond may not be visible externally and, if tight or weakly bonded, may be difficult to detect using NDT methods. This type of defect is known as a kissing bond. Disbonding is particularly important to avoid in joins such as end connections. Disbonds 2022-05-18 B-06a Materials and Hardware CASA Part 66 - Training Materials Only Page 125 of 229 Cracks Cracks can occur in composite structures just as in metallic ones. Cracking is a common form of damage in composites arising in manufacture or under service conditions. It has a significant effect on the integrity of the composite, allowing environmental ingress and damage to extend under service loading. Cracking is often associated with the final stages of in-service failure. Sometimes cracks can be detected visually, but other times they may require more advanced methods of non-destructive inspection (NDI). A thorough inspection should be made to determine the extent of each crack. ATSB Transport Safety Report, Occurrence Investigation AO-2014-032 Composite material damage on the vertical stabiliser of an ATR 72 2022-05-18 B-06a Materials and Hardware CASA Part 66 - Training Materials Only Page 126 of 229 Cracking Resin Matrix Damage Damage to the resin matrix can be caused by many things, such as fire or excessive heat, UV rays, paint stripper, impacts, etc. Resin matrix damage 2022-05-18 B-06a Materials and Hardware CASA Part 66 - Training Materials Only Page 127 of 229 Water and Aircraft Fluid Intrusion Intrusion of water and other fluids is especially a problem with honeycomb cores. It causes weight gain, contamination of bond joints, corrosion in aluminium honeycomb and disbonds if the water freezes and expands. Thermographic image showing moisture ingress Water intrusion is a very common problem with high-temperature repairs. The heat of curing causes the trapped water to turn to steam, disbonding face sheets around the repair. It is a progressive way to inadvertently convert a small area of damage into a large one. 2022-05-18 B-06a Materials and Hardware CASA Part 66 - Training Materials Only Page 128 of 229 Water and aircraft fluid intrusion 2022-05-18 B-06a Materials and Hardware CASA Part 66 - Training Materials Only Page 129 of 229 Hole Damage Holes may occur from impact damage, from over-torqued fasteners or as a result of fastener pullthrough. Holes drilled in the wrong location, wrong size or wrong number can also be classified as hole damage. Holes caused by a lightning strike may burn off resins, leaving bare cloth. Tiny holes, known as pinholes, in the skin surface are not easily detected; however, they could lead to more extensive damage. If moisture is allowed to get into the core structure, along with the airflow over the part, it could cause a small delamination, which could grow into a very large delamination. Pin holes on skin surface could expand to cause large holes 2022-05-18 B-06a Materials and Hardware CASA Part 66 - Training Materials Only Page 130 of 229 Composite Repairs Composite Repairs The exact procedures for repair of various laminated composite structures depend partly on the type of damage incurred. The damage can range from a relatively simple surface scratch to damage extending completely through all internal plies and the core honeycomb material. There are four basic types of composite repairs: Bolted metal or cured composite patches Bonded metal or cured composite patches Resin injections New repair plies laminated to the damage. Bolted and bonded surface patches are not usually recommended due to the fact that these types of patches do not restore the strength characteristics of the original structure. A bolted or bonded patch that is attached to the surface also causes undesirable aerodynamic changes. Resin injection repairs fill holes or voids by injecting resin into the hole of a damaged area using a needle and syringe. This type of repair is usually done on non-structural parts. The injected resin does not restore the original strength and in some cases expands t