Block 8 Coating Removal PDF
Document Details
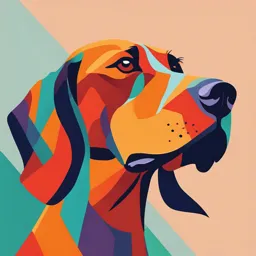
Uploaded by RewardingKazoo8831
Tags
Related
- TU Project Work: Simulation of Anti-reflective Coating on Crystalline Silicon Solar Cell using PC1D PDF
- Tablet Coating Processes (PDF)
- Tablet Coating: Chapter 3-2 (PDF)
- On-Off Thermoresponsive Coating Agent for Maize Seeds (PDF)
- Advances in Controlled Release Fertilizers: Cost-Effective Coating Techniques and Smart Stimuli-Responsive Hydrogels PDF
- Efficiency Improvement Coating to HSC Pump Case Study PDF
Summary
This document provides detailed instructions on coating removal procedures, including different types of paint removal methods. It also covers topics such as using different types of abrasive tools, plastic media blasting methods, and spray equipment.
Full Transcript
Block 8 801A: COATING REMOVAL: TO 1-1-8 is for removal of applications of organic coatings, and PPE TO 1-1-690: General Advanced composites repairs. Mechanical Compatibility is defined as using the right tool for the right job. Material Compatibility is defined as using compatible materials for...
Block 8 801A: COATING REMOVAL: TO 1-1-8 is for removal of applications of organic coatings, and PPE TO 1-1-690: General Advanced composites repairs. Mechanical Compatibility is defined as using the right tool for the right job. Material Compatibility is defined as using compatible materials for a job. Compatible materials include the idea of using tools that would cause additional damage. Examples being using similar metals in repairs. Removal Prep: Removal prep includes cleaning and inspecting the area. Allowing the area to dry. Protect/mask off any special area and position aircraft in a sheltered area. Types of paint removal: There are two types of ways to remove paint. Chemical and mechanical paint removal. Chemical paint removal is the fastest and easiest method. However, it is also hazardous and it is important to consult the TO before use. It is important to remember that Chemical Paint removal is not authorized on ADVANCED COMPOSITES. The second type of paint removal is mechanical. Mechanical paint removal includes abrasive cloths/paper and abrasive mats. It is important to note that topcoat removal and primer removal include different grades of abrasive. The top coat requires a courser grit or a grade c abrasive. A grade C abrasive is also known as a medium grade typically around 120 grit. Primer removal requires a finer grade or a grade b abrasive. A grade B abrasive is typically around 240 grit. When using motor-driven abrasives ALL ATTACHMENTS must HAVE A HIGHER RPM RATING THAN THE TOOL BEING USED. I.e.: drill/grinder. PLASTIC MEDIA BLASTING (PBM): Plastic media blasting is a form of paint removal. PMB is the PREFERRED METHOD OF PAINT REMOVAL FOR ADVANCED COMPOSITES. PMB is used for the removal of topcoat. The preferred Clean up for pmb is a HEPA vacuum but when unavailable you can use compressed air with no more than 30psi. Dry abrasive blasting: Provides excellent and rapid paint removal. Only down to primer on advanced composite surfaces. Plastic Media blasting uses TYPE V: Acrylic plastic. Blasting Cabinet: The blasting cabinet is where media plastic is done. It’s THREE MAJOR COMPONENTS ARE THE 1. CABINET/GLOVE BOX, 2. BLAST/RECLAIMER ASSEMBLY, AND THE 3. DUST COLLECTOR. The reclaimer separates debris and good media recycling the good media back into the cabinet. The dust collector collects all debris. The collector drum must be replaced at 90% capacity. Blasting Booth: This is similar to the blastic cabinet but has two notable differences. The booth is much larger and has a difference in the volume of media output. Its major components are the same but instead of a cabinet, it is a booth. Theory of operation: You must have clean and dry compressed air mixed with clean and dry media. Blasting Parameters: - Substrate (Metallic or non-metallic) - Type of media (Acrylic Plastic) - Nozzle pressure (25-40 psi) (TO 1-1-8) - Standoff distance (12-24in) - Angle of impingement (30-90) - Dwell Time (How fast or slow the nozzle should be kept moving. Pre-blast prep: Prevents clumping and damage. - Clean and dry - Control leaks - Maskuing and aircraft position are important in pre-blast prep. After prep and before and after your work always remember to do PRE/POST INSPECTION of all equipment/gear/and assembly parts. PPE for cabinet: White painting suit. PPE for BOOTH: Tyvek racing suit w/ blasting helmet. (Kepp 50ft from sources of ignition. 803a: HVLP SPRAY EQUIPMENT: HIGH VOLUME LOW-PRESSURE SPRAY GUN: Use 1-10 psi. (Benefits include less overspray/waste/dafer/and atomizing) When using a high-volume low-pressure spray gun there are three classes of guns otherwise known as delivery methods. 1. Suction feed: Suction feed uses a pressurized paint cup of 20 psi or lower. This is also an attached delivery method. 2. Pressure feed: Pressure feed is used for large-volume painting such as pressure pot/tank painting. This is a separate or connected-through hoses style. 3. Gravity feed: Gravity feed Is the most common and is done for painting small to medium parts. Also, the feed sits atop the spray gun. HLVP BREAKDOWN/PARTS: - Fluid Cup: -Typically holds one quart -Small area -Spray time is limited to capacity -Supplies fluid - NOSE ASSEMBLY: AIR CAP and FLUID TIP: -Air cap: Pushes air out (wing ports face direction of travel, horizontal movement = wings are also horizontal) -Fluid tip: Pushes coating material out and mixes are with atomized fluid -Fluid needle: Fluid needle must be same diameter as fluid tip. When the trigger is pulled the needle moves back and releases fluid. -Spray pattern adjustment screw: (clockwise adjustment to decrease the width of pattern and counter-clockwise to increase width) -Fluid needle adjustment screw: (Clockwise to decrease flow and counter-clockwise to increase flow) Spray Gun cleaning units: two types - Filtration: Reutilizes the solvent requires you to replace solvent and change filter. (Most common in the field (50psi for 1-5 min). - Distilled: Recycles solvent and separates waste, does not require solvent disposal. 803C: Pressure pots: LARGE VOLUME PAINTING Pressure pots are pressurized and have a size from two quarts to 120 gallons. - Parts include a Pressure regulator (air pressure) and Material regulator (Flow rate). - Safety valve (Release pressure) Agitators: Mix paint and can be either electrically or pneumatically powered. Keeps paint suspended and must be explosion proof. 802a: Passivation Coating: TREATING/COATING METAL TO REDUCE THE CHEMICAL REACTIVITY OF ITS SURFACE Surface prep/prior coating Cleaning surface: 1-1-691 Solvent wipe: 1-1-8 Water break test: Pass = ready for passivation (coalesce = continuous film) -Chromate conversion coating (alodine) USED ON Aluminum and Alloys -Three forms: Form 1(liquid concentrate), Form 2(powder), Form 3(pre-mixed) -Remember to miz in accordance with TO 1-1-8 Application of passivation coating: Apply immediately after corrosion removal Immersion/Submersion/dunking is the best method of application. Apply cross coat between 1-5 minutes. When using alodine the surface will turn green if dirty or corroded. - Proper color is a brassy yellow - - Don’t agitate before dry - -You can force dry at 140 degrees for a max 1 hr. Don’t allow the solution to come in contact with thinners, acetones, or combustibles. 803B: Coating defects: Paint Terms: - Adhesion: Adhesion is when the surface is roughened or cleaned to promote adherence/stick - Coating: Coating generally consists of a primer and topcoat. - Primer: Primer is a way to promote corrosion protection for metal and is also an adherent for the top coat (primer is not suitable for a top coat) - Top coat: A top coat is for the toughness, outdoor durability, and good chemical resistance - Vehicle: A vehicle is the liquid portion of the coating consisting of volatiles and non volatiles. - Volatile: Volatiles include solvents and dilutants that are lost through evaporation in curing - Non-volatile: Nonvolatile includes pigments and resins that form and leave an actual film on the surface. - Viscosity: Viscosity refers to a liquid’s resistance to flow which is measured with a viscometer. - Viscosity is measured with either a Zahn cup or Ford cup or drip of 17-23 seconds. IMPROPER SURFACE TREATMENT DEFECTS: 1. Pinhole Cavities: “Solvent pop” is due to an insufficient primer dry time and painting over volatile gases. 2. Peeling: Peeling is due to improper roughing or moisture removal 3. Blistering: Due to moisture resembling water blisters 4. Fish eyes: This is due to silicon left on the surface 5. Pitting/cupping: This is due to corrosion left on the surface 6. Crazing/mudcracking/checking: This is due to painting over a hard glossy coat 7. Sandpaper Finish: This can be due to insufficient scuffing, unsatisfactory primer, improper cleaning, and a stroking gun too far away. Surface Defects due to IMPROPER USE OF TECHNIQUE APPLICATIONS: 1. Runs and Sags: Runs and sags are due ot too heavy of a paint application due to spraying too close at uneven angles. 2. Streaks: Streaks are due to improper overlapping and air pressure being too high 3. Orange Peel: Orange peel-like application is due to insufficient thinning due to the coating being too thick. Defects due to equipment and need for adjustment: 1. Heavy Center: Low atomizing pressure, fluid pressure too high (air low) 2. Split Spray: Atomizing pressure high, Air pressure high, and fluid low 3. Heavy Top/Bottom & Heavy Left/Right: Air cap clogged (check for dirt/burr) 4. Wrinkling: (Prune Like) Coats applied fast, humidity, rising temps 5. Blushing: Cloudening/ whitening (Moisture condensation from the atmosphere) Faulty Finishing Material: If your dinish is faulty this is because your coating/ paint being used was either stored improperly or the material was expired. Spray Gun troubleshooting: - Paint dont spray: Check for paint, blockage - Paint dont transfer: Check for dirty tool or a clogged air vent/cup cover - Excessive fog: Check for the pressure being too high - If paint leaks: Check the fluid tip, the tip may be damaged or the needle and tip may be different. - If paint gun sputters the fluid tip may be loose, so make sure to tighten all assemblies. 803D: Basic Facts about spray booth Purpose: A fireproof compartment built to confine and remove fumes & overspray during the painting process. Design: There are two types of designs for a spray booth. Type 1 being a partially enclosed booth whihc utilizes a cross flow system. And type 2 which is fully enclosed and can utilize a cross flow system or a down draft. Filters: Aka Baffles: These are dry filters that collectc/ pull overspray into filters and then exhausted. (Most Common) Air velocity: Term used to describe the speed of air moving thru the empty spray booth. (Most booths operate with an air velocity of 100 feet per min). Major Components of the spray booth: 1. Exhaust Fans: Pulls overspray from booth 2. Air replacement Unit: Replaces air that was vented by exhaust fans 3. Manometer: A draft gauge that monitors the air velocity and indicator of filters being filled to capacity Surface Prep: Preparing Unpainted surfaces: Solvent Wipe, passivate, and tack rag Preparing Painted surfaces: Scuff, Solvent wipe, Re-passivate, Tack Rag Preparing a primed surface: Solvent wipe, scuff, solvent wipe, tack rag TIME PASSED: - 5-8 hrs: Tack rag and then apply top coat - 8-24 hrs: Solvent wipe, Tack rag, and then top coat - 24+ hrs: Scuff sand, solvent wipe, tack rag, then top coat Epoxy Primer prep: 2 part system -3-5 min prep Coating prep and application is found in TO 1-1-8 -Dwell time (Induction Time): Allows resin & catalyst to chemically combine w/ each other (30 min) -Then check viscosity - Epoxy primer must be applied within 48 hrs of passivation. -Apply single coat: 1-1.5 mils wet film thickness(wft) which should cure to around.6 to.9 dry film thickness (1 mil=.001) -Dry until no fingerprints can be left Polyurethane Top Coat: -Select proper ocating in accordance with TO-23 -Polyurethane typically doesnt need a dwell time -Apply 1 wet cross coat When curing either wait 12 hrs @ 60 degrees and below or seven days if temp is below 75 degrees. Major Paint touch up: 72 hr cure time after painting for major parts - Major skin panels 9ft and over - Minor paint touch ups = 30 hr cure time Cleaning and Maintaining HVLP gun: - Clean after every use - Dont submerge in thinner/solution - Dont dismantle gun after every job AFOSH 48-137=respiratory afi 91-203 = occupational safety