Benchwork Lecture Notes PDF
Document Details
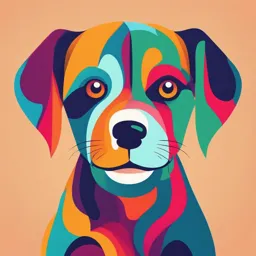
Uploaded by ProdigiousDaisy408
Batangas State University
Tags
Summary
These lecture notes provide a comprehensive overview of benchwork, covering various aspects of the topic, including safety in the workshop, tools and equipment, and general procedures.
Full Transcript
BENCHWORK It is a term used to describe any type of work that is managed using a workbench rather than with the use of heavy machinery in a plant setting or in a larger area. It refers to the work or job that is completed at a stationary setting rather than relying on machinery to do...
BENCHWORK It is a term used to describe any type of work that is managed using a workbench rather than with the use of heavy machinery in a plant setting or in a larger area. It refers to the work or job that is completed at a stationary setting rather than relying on machinery to do the job. It involves the use of different hand tools such as hammers, hacksaws, wrenches, files, chisels, punches, screw – drivers, etc., CARPENTRY BENCHWORK It involves the crafting of different types of furniture or frames for upholstered furniture pieces. The idea behind the carpentry benchwork furniture creation is to carefully craft each component by hand. HAND TOOL It is a device use for performing work on a material or a physical system using only hands. It can be manually used by employing force or electrically powered using electrical current. GENERAL SAFETY IN BENCHWORK Recognize safe and unsafe work practices in a shop Perform your job in a manner that is safe for you and other workers and develop safe work habits Develop responsibility for personal safety and safety of fellow workers Think safely and work safely at all times Keep hands away from moving parts Get first aid immediately for any injury Be neat, tidy and safely dressed for job being performed Never wear loose clothing: – Short sleeves or rolled up – Remove or tuck in all neckties – Always tie shop apron in the back – Long hair must be protected by hair net or cap – No canvas or open-toes sandals – Remove wrist watches, rings and bracelets Always wear approved safety glasses: – Plain safety glasses with side shields – Plastic safety goggles – Face shields HOUSEKEEPING Keep machine and hand tools clean Keep floor free from oil and grease Sweep up metal chips on floor frequently Never place tools or materials on floor close to machine Do not place tools and materials on machine table Never use rag near moving parts Remove all burrs and sharp edges with file before handling any workpiece REMEMBER: Safety is everyone’s concerns and responsibility CARE OF HAND TOOLS Put those tools not in use in a safe place while you are working Put tools away while you are through with them To save time, assign each tool to a place in a tool box Do not leave sharp tools in the floor area Use the right tool for the right job LAYING OUT It is a shop term used to include the marking or scribing It is the operation of scribing center locations, straight lines, arcs, circles, or contour lines on the surface of a piece of metal to show the machinist the finished size and shape of the part to be manufactured The information regarding the size and shape of part is taken from a technical drawing The care and accuracy of the layout plays an important role in determining the accuracy of finished parts, since the machinist uses these layout lines as a guide for machining LAYOUT TOOLS AND ACCESSORIES LAYING OUT WITH TRY−SQUARE AND STEEL RULE Remove all burrs from the workpiece and clean it properly. Start the layout from a square machined (or filed) surface. Use a try−square and a steel rule. Place the point of the scriber on the workpiece against the try−Square edge. Hold the scriber 15 inclined away from the workpiece and in the direction in which it is to be drawn LAYING OUT CIRCLES WITH THE DIVIDER Lay out the center of the circle Punch the center of the circle Adjust the divider to the proper radius while using a steel rule or a vernier caliper Place one point of the divider in the center punch hole and give some force to this leg. Move around the fixed leg and scratch the surface. Laying out parallel lines Laying out circles LAYING OUT WITH SURFACE GAUGE LAYING OUT WITH PROTRACTOR HAMMER The hammer is a very simple striking tool, being just a weighted head and a handle to direct its course It is used nearly in every operation related to metal works They are made of cast steel or carbon steel Classification of hammer Hard hammer Soft hammer Soft – face hammer Several types of hammer Ball peen hammer – a common form of machinist hammer Ball peen Cheek Head Neck Poll Eye Face Straight peen hammer – use for spreading or drawing out metal and is use in swaging and riveting Straight peen Cross-peen hammer – use for swaging and riveting Cross peen Claw hammer - use for driving and pulling nails Claw Sledges – use for heavy work. They can be procured in both single-face and double- face and vary in weight from 4 to 20 pounds. The handles vary in length up to 36 inches. Hammer assembly Hammer mainly consists of a face, peen and body. The face and the peen are hardened and tempered but the rest of the body is kept soft. A wooden handle is fitted in the eyehole of the hammer with the help of a wedge. The wedge spreads the handle and fixes it inside the hole Uses of hammers For striking: a. Punches b. Cold chisels c. Steel letters d. Figures It is also used for: a. Forging hot metals b. Riveting c. Bending d. Straightening e. Peening f. Stretching and swaging Safety in using hammer: The handle of a hammer should be dry and not greasy The surface of a handle should be smooth The face of a hammer should not be spotted, if it so then make it smooth by grinding Hold the hammer handle always nearer to its tail end BENCH VISE/ VISES There are two types of vises usually found aboard. The machinist's vise is a heavy-duty holding tool with parallel jaws and either a fixed or swivel base. The utility vise is satisfactory for general work and is designed for a variety of uses. It has a small anvil and anvil horn as part of the back jaw. Parts of a vise Proper maintenance and lubrication of vise: For satisfactory operation, keep the vise clean, oiled, and in good general condition. The screw that operates the movable jaw should be lubricated frequently with light grease or heavy cylinder oil. The slide should be wiped clean every day and light machine oil should be spread over it. Never oil the swivel joint of a vise, however, as its holding power would be impaired. Always tighten and loosen a vise by holding the handle with the hands, applying the weight of the body to secure the turning pressure. Do not hit the vise handle with a hammer When the vise is not in use, the jaws should be brought lightly together, with the handle in the vertical position. Safety precautions in using vise: Be sure to keep fingers clear of the jaws when clamping work in the vise. Use care to keep them from being pinched between the end of the handle and the head of the screw, the latter accident being a very common one. When holding heavy work in a vise, it is advisable to place a block of wood or metal under the work as a prop to prevent it from sliding down and perhaps falling to the floor or on the foot. Care should also be exercised to see that the vise is not opened beyond the limit of the screw as the movable jaw may drop off and the users suffer serious injury. If it is necessary to pound against metal parts held in a vise, be sure to pound against the back jaw, as it is heavier than the front jaw and strong enough to absorb the shock of the blows. CLAMPS When the vise is not available, a clamp can be used as a gripping device. It can be used to hold pieces of material together while they are being worked on. A different kind of clamp is often used to make a temporary fastening in the engine room when it is desired to lift or take a strain on some object. To do so, the clamp is securely fastened to a convenient beam, and a line or small hoist then suspended from the clamp. SCREWDRIVERS It is a hand tool that is use to turn screw It is use in tightening or loosening screw Three main parts of screwdriver: Handle Shank Blade Several types of screwdrivers - The standard screwdriver is used for most ordinary work and comes in a variety of sizes. The blade must have sharp corners and fit the slot in the screw closely - The offset screwdriver makes work possible in tight corners where the straight type will not enter. It has one blade forged in line with the shank, and the other blade at right angles to the shank - The Phillips-type screwdriver is made with a specially shaped blade to fit Phillips-type cross-slot screws. The heads of these screws have two slots that cross in the center - The ratchet screwdriver is used to drive or remove small screws rapidly PLIERS It is a hand tool use for seizing and bending wires Types of plier Side-cutting pliers are used principally for holding and bending thin material or for cutting wire Long-nose pliers make it possible to bend or form metal into a variety of shapes, to hold objects in tight spots, and to make delicate adjustments Diagonal-cutting pliers have short jaws with blades at a slight angle. This tool is valuable when removing and replacing cotter pins, and can be used not only to cut the pins to the desired length but to spread the ends after the pins are in place WRENCHES It is a tool for exerting a twisting strain, as in turning bolts and nuts As the majority of nuts and bolt heads are hexagonal, or 6-sided, many wrenches are specially designed to fit hex-heads and hex-nuts Several types of wrench Open-end Wrenches is a solid and nonadjustable wrench with openings in one or both ends are called open-end wrenches The jaws of open-end wrenches are placed at an angle in order to make it easier to work with the wrenches in close quarters, as it is frequently necessary to tighten or loosen a nut where there is very little space in which to swing a wrench. Adjustable open-end wrench is a handy all-round wrench for light work. One jaw of this wrench is fixed and the other jaw is moved along a slide by a screw adjustment Monkey wrenches are useful in many instances, when tightening or loosening pipe unions. When using monkey wrenches, take the same precautions as with adjustable wrenches. Box-end wrench has 6 inside faces, or notches, but most of them have 12 notches, this wrench being known as a 12-point or double-hex box wrench Combination wrench is therefore helpful, using the box end for starting the nuts when loosening them, or for final tightening, and the open end for faster turning Socket wrenches are heavy-duty wrenches, made with 4 inside faces for square nuts or with 6 inside faces for hex-nuts Torque wrench is used as a socket wrench handle in order to exert the desired amount of strain when tightening nuts and bolts Hook spanner works on a round nut which has a series of notches cut in its outer surface. The hook, or lug, is placed in one of the notches and the handle turned to loosen or tighten the nut Adjustable spanner is designed to fit nuts of various diameters Pin spanners have a pin instead of a lug, the pin fitting a round hole in the edge of the nut U-shaped spanners have either lugs or pins that fit in notches or holes in the top of the nut or screw plug Allen-type wrench has a 6-sided shaft that fits into the hex-shaped recess of set screws and cap screws Bristo-type wrench has a number of splines on the shaft, the design tending to reduce spreading SHEARS AND SNIPS Hand shears, or snips, are used for cutting sheet metal of various kinds and thicknesses Several commonly used types of snips Straight snips have blades that are flat and straight on the inside surfaces Scroll-pivoter snips being more suitable for such purposes. The blades of the latter tool are approximately at right angles and provide clearance for following curves Circular snips, with their curved blades, will handle all except the smallest curves. They are available for either right-hand or left-hand use Hawksbill snips can cut inside and outside circles of small radii. Their narrow curved blades are bevelled enough to permit sharp turns without buckling the material Trojan snips are slender-bladed snips used for straight or curved cutting. The blades are small enough to permit sharp turns, and will also cut outside and inside curves. They are sometimes known as combination snips Bolt cutter is sometimes called bolt cropper is a tool used for cutting chains, padlocks, bolts and wire mesh PUNCHES/ PUNCH It is a tool use for stamping perforating It is a process of making a hole or impression with a stamping or perforating tool Several types of punches Center punch is used to make a starting mark for a drill when holes are to be drilled in metal. If the center punch mark is not made, the drill will wander or "walk away" from the desired center. Prick punches are generally used for marking centers and lines in layout work Starting punches, sometimes called drifts, have a long taper from the tip to the body. They are made that way to withstand the shock of heavy blows. They may be used for knocking out rivets after their heads have been cut off, or for freeing pins or bolts from their holes Pin punch is use and designed to follow through the hole without wiggling. Both starting punches and pin punches must have flat ends Alining or lining up punch is used to line up corresponding holes in adjacent parts, for example when working on engines that have pans and cover plates Hollow shank gasket punch is use in cutting holes in gasket materials and the cutting end is tapered to a sharp edge to produce a clean uniform hole HACKSAWS The hacksaw is a tool used to saw/ cut metal A hand hacksaw mainly serves to separate materials and also to produce grooves and slits Types of hacksaw The pistol-grip type is adjustable to take various blade lengths The straight-handled hacksaw is not adjustable, although it may be constructed with the adjustable feature Hacksaw assembly Hacksaw blades are made of high-grade tool steel or tungsten steel, and are available from 6 to 16 inches in length. Two types of hacksaw blade: all-hard blade flexible blade. In the flexible blade, only the teeth are hardened. The pitch of a blade indicates the number of teeth it has per inch, pitches of 14, 18, 24 and 32 being available. Selecting the right blade: When selecting the best blade for a job, it is necessary to consider the type of blade and the pitch. An all-hard blade is best for sawing brass, tool steel, cast iron, and heavy cross- section stock. A flexible blade is usually best for sawing hollow shapes and metals having a light cross section. A 14-pitch blade should be used on machine steel, cold-rolled steel, or structural steel, as it will cut fast and free. The 18-pitch blade, which is the blade for general purpose work, is used on solid stock of aluminum, bearing metal, tool steel, high-speed steel, cast iron, etc. A 24-pitch blade is used for cutting thick-wall tubing, pipe, brass, copper, and channel and angle iron. Use the fine tooth 32-pitch blade for thin-wall tubing and sheet metal. Forward stroke with pressure and return stroke without pressure. Use the full length of the saw blade. Saw in a straight line along the marking line Numbers of teeth of hacksaw blade Three types of hacksaw blade set The right and wrong angles for various kinds of work CHISELS One of the most valuable tools aboard ship is the flat cold chisel. These chisels are usually made of octagonal tool-steel bar stock, carefully hardened and tempered, and are used for cutting purposes where snips or a hacksaw cannot be used. They are also used to shear off rivets, to smooth castings and to split rusted nuts from bolts. The cutting edge is ground slightly convex and this causes the center portion to receive the greatest shock, and protects the weaker corners. Chipping is the term applied to the method of removing metal from a surface with a chisel, as shown in the figure which also illustrates the correct and incorrect methods of preparing the cutting edges Work Process: The workpiece must be properly clamped when chiselling. The chisel must be struck on the center of the head, in the direction of the axis of the chisel. The correct wedge angle must be maintained when grinding the chisel (measure with an angle gauge). The tool must be cooled frequently when sharpening, so that it does not lose its temper. Safety precautions in chipping: Always wear goggles when chipping with a chisel. Also be careful not to send chips flying toward other workmen or into machinery. The safest method is to have a guard (a piece of canvas of sufficient size attached to two wooden pedestals) placed so as to catch the flying chips. Keep the hammer and the head end of the chisel clean and free of grease and oil to prevent the hammer from slipping. Special cold chisels If it is necessary to cut keyways or slots, the cape chisel can be used. This chisel is like a flat chisel except that the cutting edge is very narrow. It has the same point angle, and is held and used in the same manner. Rounded or semi-circular grooves should be cut with the round-nose chisel. This chisel is also used to "draw back" a drill that has "walked away" from its intended center. The diamond-point chisel is tapered square at the cutting end, and then ground at an angle to provide the sharp diamond point. It is used for cutting V-grooves and inside sharp angles. Cutting sheet metal with cold chisel FILES Files are hardened steel tools for cutting, smoothing, or polishing metal. They vary in length, in shape, in arrangement, or cut of teeth so as to provide files for various uses. The file is a cutting tool to work materials. It has many cutting edges which are like small chisels (file teeth) and are harder than the material being worked upon. For cutting metals normally, Cross−Cut files are used. These files have an overcut, and an up cut. When using a file, several cutting wedges always act at the same time. File terminology Files have either single-cut or double-cut teeth. Single-cut files have rows of teeth cut parallel to each other, the teeth being set at an angle of about 65° with the centerline. Single-cut files are used for sharpening. Tools finish filing, and draw-filing. They are also the best tools for smoothing the edges of sheet metal. Single-cut file Double-cut files have criss-crossed rows of teeth, the double cut forming teeth that are diamond-shaped and suitable for quick removal of metal and for rough work. Double-cut file Files are also graded according to the spacing and size of their teeth, or their coarseness and fineness. These grades are known as: Rough-cut Middle-cut Bastard Second-cut Smooth Dead-smooth Grades of file teeth Types of file Selecting a file for a job: It is necessary to consider its shape, which means both the outline and the cross- sectional shape. Cross-sectional shapes of files Mill files are tapered both in width and thickness, and are available with either square or round edges, or with one safe edge, that is, an edge with no teeth. Mill files are used for lathe work, draw-filing, and other fine, precision work. They are always single-cut. Flat files are general purpose files, tapering in width and thickness, and generally used when a fast cutting tool is desired. Square files are tapered on all four sides and are used to enlarge rectangular-shaped holes and slots. Round files serve the same purpose for round openings. Small round files are often called rat-tail files. The half-round file is a general purpose tool, the rounded side being used on curved surfaces and the flat face on flat surfaces. When filing an inside curve, a round or half- round file with curve most nearly matching the curve of the work should be used. Triangular or 3-square or 3-corner files are tapered on all three sides. They are used to file cutters, acute internal angles, and to clear out square corners. Special triangular files are used to file saw teeth. A warding file is extremely thin and has sharply tapered edges. Its chief use is on work where space is limited. Knife files have one thin edge and one thick edge, and are used on keyways, slots, etc. A rasp is similar to the file except that it has coarse teeth raised by a triangular punch, and is usually used on wood. Hand files are somewhat thicker than flat files, but their edges are parallel. Correct way to hold file The correct way to hold a file is with the handle against the palm of the right hand, thumb on top. Hold the end of the file in the left hand with the fingers curled under it. When filing, lean the body forward during part of the forward stroke and straighten up at the finish. The file must be held straight or the surface of the work will not be flat. Not more than 30 or 40 strokes per minute should be taken; too much speed will cause the file to rock, and the corners of the stock will be rounded off. Too much pressure will bend the file and tend to have the effect in the figure of the file. Too much speed and too much pressure Apply pressure on the forward stroke only. Unless the file is lifted from the work on the return stroke, it will become dull much sooner than it should. (This does not apply, however, when filing very soft metals, such as lead or aluminum. On soft work, pressure on the return stroke helps to keep the cuts in the file free of removed metal.) When round surfaces are filed, best results are obtained by working, a rocking motion being used. Surfaces and edges are often draw-filed to make them smooth and true. In draw-filing, hold the file at right angles to do the work. Filing round surfaces Draw-filing DRILLS AND DRILLING Drilling is the operation of producing hole by removing metal from solid mass using twist drill. TWIST DRILL It is a tool that does the work of drilling by slicing metal away as it rotates Twist drills are also used for cutting larger holes in metal A twist drill is a cutting−tool used to produce a hole in a piece of metal or other material. The most common drill manufactured has two cutting edges (lips) and two straight or helical flutes. The flutes provide the cutting edges with cutting fluid and allow the chips to escape during the drilling operation. Twist drills are available with either 2, 3, or 4 flutes (the spiral grooves formed along the sides), but drills having 3 or 4 flutes are used for following smaller drills or for enlarging cored holes, and are not suitable for drilling into solid stock. The spiral flutes provide several advantages: They give a correct rake angle to the lips, a They cause chips formed while drilling to curl tightly so that they occupy the minimum amount of space. They form channels through which such chips can escape from the hole. They allow the lubricant, when one is used, to flow easily down to the cutting edge of the drill. RAKE ANGLE Drill bit materials: High−speed steels drills are the most commonly used drills, since they can be operated at good speeds and the cutting edges can withstand heat and wear. Cemented−carbide drills, which can be operated much faster than high−speed steel drills, are used to drill hard materials. They can be operated at high speeds and they can withstand higher heat. Twist drills are made of carbon steel or high-speed alloy steel. Carbon steel drills are satisfactory for the general run of work and are less expensive, although they may lose their hardness if heated excessively. High-speed drills are used on tough metals and at high speeds. They will keep on cutting when red hot, but should be cooled in still air; if cooled quickly they may crack or split Drill Terminology - Before a drill is used on any kind of work, it is important that it be correctly ground and sharpened. If a drill is not in proper condition for work, it will drill with difficulty, make a hole that is rough or off size, and perhaps break while in use. The dead center is the sharp chisel edge at the extreme tip end of the drill. It is formed by the intersection of the cone-shaped surfaces of the point and should always be in the exact center of the axis of the drill. The point of a drill is the entire cone-shaped surface at the cutting end. It should not be confused with the dead center. The heel of a drill is the portion of the point back of the cutting lips or edges. The lip clearance angle is the angle at which the drill point is ground off just back of the lips. The margin is the narrow strip which extends the whole length of the flutes, being part of a cylinder that is interrupted by the flutes and by what is known as body clearance. The portion of the drill back of the margin is of slightly less diameter than the margin, and the difference is known as body clearance. Body clearance reduces the friction between the drills mid and the walls of the hole, while the margin insures that the hole is of the right size. It runs the entire length of the drill between the flutes, gradually increasing in thickness toward the shank. TWIST DRILLTERMINOLOGY A twist drill may be divided into three main sections: Shank: The shank is the part of the drill that fits into a holding device. It may be either straight or tapered. Body: The body contains the flutes, margin, and body clearance of the drill. Point: Shape and condition of the point are very important to the cutting action of the drill. Recommended drill points for various materials DRILL SHANK The drill shank is the end that fits into the chuck of the hand drill, electric drill or drill press. Straight-shank drills are used to drill holes up to about 1/2 inch in diameter. Larger holes are usually drilled with the taper-shank drill. The square-shank drill is made to use in a brace. Twist drill shanks Hand drilling tools DRILL PRESS A drill press is a machine used for drilling operations available in a wide variety of types and sizes to suit different types and sizes of workpieces. The most common machine type found in a metal shop is the floor−type drill press. Parts of a drill press Base The base, usually made of cast iron, provides stability for the machine and rigid mounting for the column. The base is usually provided with holes so that it may be bolted to a table or bench to keep it rigid. The slots or ribs in the base allow the work−holding device for the workpiece to be clamped to the base. Column The column is an accurate, vertical, cylindrical post that fits into the base. The table, which is fitted on the column, may be adjusted to any point between the base and head. The head of the drill press is mounted near the top of the column. Table The table, either round or rectangular in shape, is used to support the workpiece to be machined. The table, whose surface is at 90 degree to the column, may be raised, lowered, and swiveled around the column. On some models it is possible to tilt and lock the table in either direction for drilling holes on an angle. Slots are provided in most tables to allow jigs, fixtures, or large workpieces to be clamped directly to the table. Drilling Head The head, mounted close to the top of the column, contains the mechanism to revolve the cutting tool and advance into the workpiece. The spindle, which is a round shaft that holds and drives the cutting tool, is housed in the spindle sleeve. The spindle sleeve does not resolve, but is moved up and down by the hand feed lever that is connected to the pinion on the rack of the spindle sleeve. The end of the spindle may have a tapered hole to hold taper shank tools, or it may be threaded or tapered for attaching a drill chuck. Hand feed lever The hand feed lever is used to control the vertical movement of the spindle sleeve and the cutting tool. Depth stop A depth stop, attached to the spindle sleeve, can be set to control the depth that a cutting tool enters the workpiece. Drill Chuck Drill chucks are the most common devices used on a drill press for holding straight−shank cutting tools. Most drill chucks contain three jaws that move all at the time when the outer collar is turned. The three jaws hold the straight shank of a cutting tool securely and cause it to run accurately. Drill Press Radial Drilling Machine Tool-holding devices of drill press Used to hold or drive cutting tool Drill press spindle provides means of holding and driving cutting tool. The end of it may be tapered or threaded for mounting drill chuck Most common tool holding device: Drill chucks Most common devices used for holding straight-shank cutting tools It contains three jaws that move simultaneously when outer sleeve turned Drill sleeves Used to adapt cutting tool shank to machine spindle if taper on tool is smaller than tapered hole in spindle Drill sockets Used when hole in spindle of drill press too small for taper shank of drill Work-holding devices of drill press Used to clamp or hold workpiece Most common tool holding device: Drill vise Used to hold round, square or odd-shaped rectangular pieces Clamps or straps Used to fasten work to drill table or an angle plate for drilling various sizes and usually supported at end by step block and bolted to table by T-bolt that fits into table T-slot Clamping hints Always place bolt close to workpiece Have packing block slightly higher than work surface being clamped Insert piece of paper between machine table the workpiece to prevent shifting Place metal shim between clamp and workpiece Use sub-base or liner under rough casting Shim parts that do not lie flat to prevent rocking Safety rules in using drill press Never wear loose clothing A hair net or a cap must protect long hair to prevent it from becoming caught in the revolving parts of the drill press. Never wear rings, watches, bracelets or necklaces while working in a machine shop. Always wear safety glasses when operating any machine. Never set the speed, adjust or measure the work until the machine is completely stopped. Keep the work area and floor clean and free of oil and grease. Never clamp taper shank drills, end mills, or non−standard tools in a drill chuck. Never leave a chuck key in a drill chuck at any time. Always use the brush to remove chips. Always clamp workpieces when drilling holes larger than ½ in. (12.7 mm) in diameter. When drilling sheet metal, it is necessary to clamp the sheet on a piece of wood. Reduce drilling pressure as the drill breaks through the workpiece. Always remove the burrs from a hole that has been drilled COUNTERSINKING Operation of producing tapered or cone-shaped enlargement to end of hole Process of enlarging top end of hole to shape of cone to accommodate conical- shaped heads of fasteners Procedure to Countersink a Hole for a Machine Screw Mount an 82º countersink in drill chuck Adjust spindle speed to about ½ that used for drilling Place workpiece on drill table With spindle stopped, lower countersink into hole - Clamp work if necessary Raise countersink slightly, start machine, and feed countersink by hand until proper depth is reached. - Diameter checked by placing inverted screw in countersunk hole If several holes to do, set depth stop Countersink all holes to depth set on gage REAMING Operation of sizing and producing smooth, round hole from previously drilled or bored hole Rotary cutting tool with several straight or helical cutting edges along body Used to accurately size and finish hole previously formed by drilling Two classifications reamers Hand Machine Reamer Parts Three main parts of reamer Shank Body Angle of chamfer Reamer Care Never turn reamer backward; ruin edges Always store reamers in separate containers to prevent cutting edges from being nicked Never roll or drop reamers on metal surfaces When not in use, reamer should be oiled Fine, free-cutting grinding wheel should be used for re-sharpening reamers Procedure for Hand Reaming a Straight Hole 1. Mount work on parallels in vise and clamp it securely to table 2. Drill hole to proper size, leaving allowance for hand reamer to be used 3. Do not move location of work or table; remove drill and mount stub center in drill chuck 4. Start end of reamer in drilled hole 5. Fasten tap wrench on reamer 6. Engage stub center in center hole on end of reamer 7. With down feed lever, apply slight pressure while turning reamer clockwise by hand 8. Apply cutting fluid and ream hole 9. When removing reamer, turn it clockwise, never counterclockwise Machine Reaming a Straight Hole 1. Mount work on parallels in vise and fasten securely to table 2. Select proper-size drill for reaming allowance required and drill hole 3. Mount proper reamer in drill press 4. Adjust spindle speed to suit reamer and work material 5. Start drill press and carefully lower spindle until chamfer on reamer starts to cut 6. Apply cutting fluid and feed reamer by applying enough pressure to keep reamer cutting 7. Remove reamer from hole by raising down feed handle 8. Shut off machine and remove burr from edge of hole COUNTERBORING Enlarging top of previously drilled holes to given depth to provide square shoulder for head of bolt or cap screw Operation of enlarging end of hole that has been drilled previously Depth slightly greater than head of bolt, cap screw or pin it is to accommodate Procedure to Counterbore a Hole 1. Set up and fasten work securely 2. Drill proper size of hole in workpiece to suit body of pin or screw 3. Mount correct size of counterbore in drill press 4. Set drill press speed to approximately one-quarter that used for drilling 5. Bring counterbore close to work to see that the pilot turns freely in drilled hole 6. Start machine, apply cutting fluid and counterbore TAPPING Cutting internal threads in hole with cutting tool called tap Performed by hand or under power with tapping attachment It is done immediately after drilling operation Hand taps It is a set of tapping tool containing taper, plug, bottoming tap. A tap is a cutting tool used to cut internal threads. Normally it’s made of high−speed steel (HSS). Machine taps Designed to withstand torque required to thread hole and clear chips Tap – cutting angle Tap wrenches (adjustable) Tap wrenches (fixed) Working Steps for Hand Tapping 1. Select the correct size and type of tap for the job (blind hole or through hole). 2. Select the correct tap wrench for the size being used. 3. Use a suitable cutting fluid (No cutting fluid for brass or cast iron). 4. Place the tap in the hole as near to vertical as possible. 5. Apply equal down−pressure on both handles, and turn the tap clockwise (for right−hand thread) for about two turns. 6. Remove the tap wrench and check the tap for squareness. Check at two positions 90 degree to each other. 7. If the tap has not entered squarely, remove it from the hole and restart it by applying slight pressure in the direction from which the tap leans. Be careful not to exert too much pressure in the straightening process, otherwise the tap may be broken. 8. Turn the tap clockwise one−half turn and then turn it backward about one−quarter of a turn to break the chip. This must be done with a steady motion to avoid breaking the tap Turn clockwise with light pressure Check the 90 angle Procedure to Tap a Hole by Hand in a Drill Press 1. Mount work on parallels with center-punch mark on work in line with spindle and clamp work securely to drill press table 2. Adjust drill press table height so drill may be removed after hole has been drilled without moving table or work 3. Center drill hole location 4. Drill hole to correct tap drill size for tap to be used 5. Mount stub center in drill chuck Or remove drill chuck and mount special center in drill press spindle 6. Fasten suitable tap wrench on end of tap 7. Place tap in drilled hole, lower drill press spindle until center fits into center hole in tap shank 8. Turn tap wrench clockwise to start tap 9. Continue to tap hole, applying light pressure Threading Dies A threading die is used to cut external threads on round workpieces. The most common threading dies are the adjustable and solid types. The round adjustable die is split on one side and can be adjusted to cut slightly over or under−sized threads. It is mounted in a die stock, which has two handles for turning the dies onto the work. The solid die, cannot be adjusted and generally used for re−cutting damaged or oversized threads. Solid dies are turned onto the thread with a special die−stock, or adjustable wrench Threading with a Hand Die − Working Steps The threading process requires the machinist to work carefully to produce usable parts and avoid damage. The following describes the procedure to be used. 1. Chamfer the end of the workpiece with a file or on the grinder. Consider that a 3/4” thread requires a bolt with an outside diameter of 3/4”. 2. Fasten the workpiece securely in a vise. Hold small diameter work short to prevent it from bending. 3. Select the proper die and die stock. 4. Lubricate the tapered end of the die with a suitable cutting lubricant. 5. Place the tapered end of the die squarely on the workpiece. 6. Apply down−pressure on both die−stock handles and turn clockwise several turns. 7. Check the die to see if it has started squarely with the work. 8. If it is not square, remove the die from the workpiece and restart it squarely, applying slight pressure while the die is being turned. 9. Turn the die forward one turn, and then reverse it approximately one−half of a turn to break the chip. 10. Apply cutting fluid frequently during the threading process. Other drilling operations BORING Truing and enlarging hole by means of single-point cutting tool SPOT FACING Smoothing and squaring surface around hole to provide seat for head of cap screw or nut Boring bar fitted with double-edged cutting tool and pilot section on end to fit into existing hole SHARPENING TOOLS For some tools it is very important to keep them sharp at all times. Common tools, such as scribers, center punches, chisels, drill bits, tool bits for lathe machine needs to be sharpened every time you feel that they do not cut well. Bench Grinder or Pedestal Grinder The bench grinder is used for the sharpening of cutting tools and the rough grinding of metal. Because the work is usually held in the hand, this type of grinding is sometimes called “offhand grinding”. The bench grinder is mounted on a bench while the pedestal grinder being a larger machine is fastened to the floor. Both types consist of an electric motor with a coarse abrasive grinding wheel for the fast removal of metal while the other is a fine abrasive wheel for finish grinding. The grinding wheels are normally made of Aluminum−Oxide or Silicon−Carbide. Aluminum−Carbide is used to grind High−Tensile−Strength Materials. Silicon−Carbide is used to grind Low−Tensile−Strength Materials. Parts of a grinder The wheel guards give the necessary protection while grinding The tool rest provide a rest for either the work or hands while grinding The eye shield is an additional protection for the eyes and should be used Redressing the grinding wheels When a grinding wheel is used, several things can happen to it: Grooves become worn in the face of the wheel The abrasive grains will lose its cutting action Small metal particles imbed themselves in the wheel, causing it to become loaded or clogged. Use from time to time a disc type dresser or a dressing stone to remove the grooves and the metal particles. This will also re−sharpen the abrasive grains. Safety precautions (grinder/ pedestal type) 1. Stand to one side out of line of wheel when starting it up. 2. The face of the wheel must be flat and free from grooves. 3. Work should be feed slowly and gradually. 4. Make sure that the tool rest is only 1/8in from the face of the wheel. 5. Do not set tool rest while machine is in motion. 6. Use face of wheel only, unless it is designed for grinding on the side; otherwise, side pressure may break the wheel. Use the entire face of the wheel to avoid grooving. 7. Stop wheel if it chatters or vibrates excessively. 8. All wheels should be tested for soundness. 9. Hold the job against wheel firmly so that it will not slip out of the hand and cause hands and fingers to come in contact to the wheel. 10. Use clamp or other holding devices for holding short pieces. 11. Always use face shield or goggles even of grinder is provided with protective glass shields. Sharpening Scriber and Center Punch 1. Scriber and center punch should be ground in the position as shown beside. 2. Use the tool rest to rest your hands while bringing the tool in the right position. 3. Rotate the tool while grinding. 4. Cool the tool down from time to time. 5. Do not overheat the metal. Sharpening Chisel 1. Chisels should be ground in the position as shown 2. Use the tool rest to rest your hands while bringing the tool in the right position. 3. Use the whole grinding wheel while grinding. Move with the tool regularly from the left to the right side and back. 4. Cool the tool down from time to time. 5. Do not overheat the metal. 6. Grind the chisel−point parallel and straight. PIPE FITTING It is the occupation of installing or repairing piping or tubing systems that convey liquid, gas, and occasionally solid materials. This work involves selecting and preparing pipe or tubing, joining it together by various means, and the location and repair of leaks. TOOLS FOR LAYING-OUT, FITTING AND INSTALLING PIPES Laying out tools Tools use in pipe installation -Tape measure -Teflon tape & pipe seal -Plumb−bob -Pipe wrench -Nylon cord -Chain wrench -Mechanical level -Adjustable wrench -Scriber -Vise grip -Soapstone or pencil -Hammer -Cold chisel Tools use in pipe cutting & threading -Set of screw driver -Pipe vise -Set of combination wrench -Hacksaw -Universal pliers -Pipe cutter -Electric drill machine -File half−round -Set of masonry drill bits -Deburrer -Set of wall plug (TOX) -Pipe threader manual -Set of pipe clamps, fixtures -Pipe threader machine type -Test gauge for final pressure test -Cutting Oil PIPE FITTING PROCESS FOR GALVANIZED PIPES Measurement of Galvanized Steel Pipes Like in other occupational areas measuring is one of the most important parts of pipe installation. Before you cut any pipe, exact measurements must be taken. Most likely for measuring pipes the tape rule is to be used. For marking out the use of scriber, pencil or soap stone is common. An accepted overall tolerance for pipe installations is 2 mm plus and 2 mm minus the demanded size. Below you can find some methods on how to measure properly. 1 = Center to face 2 = Engagement of thread 3 = Center of fitting to end of pipe measurement Pipe lengths are generally measured by one of the following methods: End of pipe thread to center of fitting 1 = Center of fitting to center of fitting 2 = End of pipe to end of pipe An "end of pipe to center of fitting" measurement is made by tightening the first fitting on the threaded end of a pipe. Then place the end of the rule exactly in the center of the next fitting, measure along the pipe and mark out the proper length. CLAMPING DEVICE OF PIPES To cut pipes they must be fixed to prevent them from rotating. The pictures below show you some common holding devices. Portable Tri-stand Chain Vise Portable Tri-stand Yoke Vise Bench Yoke Vise Top Screw Post Chain Vise Top Screw Stand Chain Vise Top Screw Bench Chain Vise Bottom Screw Bench Chain Vise Portable Kit Yoke Vise (Fits 4" Plank) Portable Kit Yoke Vise (Fits 4" Post) CUTTING GALVANIZED PIPES There are two common manual ways to cut galvanized steel pipes. Using a hacksaw Using a pipe cutter Hacksaw The hacksaw is the most important cutting tool for sawing metal to the required size. The following procedure is recommended: Before you start sawing, make sure you have measured and marked the correct length. Clamp the pipe as short as possible to prevent rotating during cutting and to prevent unnecessary vibration Use the edge of a file to make a notch at the marked position. This notch will make it easy to start with sawing. Saw with steady, even strokes, keeping the blade upright and square in the cut. Use the full length of the blade. Before finishing the cutting operation, the pipe must be supported with one hand. This will prevent the fall of the cut pipe and prevent the blade of the hacksaw being damaged. Pipe Cutter Actually this type of cutter does not remove any metal. The wheel squeezes the metal and forces it ahead of the cutter until the pipe is cut through. The operation is very easy. After mounting the pipe cutter to the pipe, tighten the feeding screw so that the cutting wheel is touching the pipe. Rotate the pipe cutter around the pipe. After the first or second turn, check that the cutting wheel is hitting exactly the scribed line. Keep rotating and every two or three turn’s use the feeding screw to put some more pressure on the cutting wheel. Before the cut is completed support the pipe with your left hand so that it does not fall. Since cutting the pipe in this manner leaves a large ridge on the inside of the pipe, which would obstruct the flow, the pipe must be de−burred or reamed with a file or a pipe reamer. Filing and De−burring the Pipe After cutting the pipe check the square ness of the pipe end. If it is necessary file it to the right angle. Remember, the installation of a pipe system should be done accurately. This means that the pipes should be free from any burr inside or outside. MANUAL PIPE THREADING When using galvanized pipes for installations most likely both ends of the pipe will have a thread. Since all pipefittings are tapered with the internal (female) pipe thread during manufacturing, the pipe fitter has to cut only the external thread. Characteristics of Tapered Pipe Threads according to the ANSI and ISO Standard Nominal Pipe Size Threads per Inch Appr. Length of threads Appr. Number of threads to be cut 1/8 27 3/8 10 ¼ 18 5/8 11 3/8 18 5/8 11 ½ 14 ¾ 10 ¾ 14 ¾ 10 1 11 ½ 1 11 1¼ 11 ½ 1 11 1½ 11 ½ 1 11 2 11 ½ 1 11 Galvanized steel pipe joint Thread Cutting Procedure Select the correct die head Put the die head in the ratchet socked using the knob to open and close the socket Check the correct position of die head Fix the pipe in a suitable vice (pipe extension within 150 mm to 250 mm) Apply a cutting lubricant to the part, which is to be threaded. During threading apply from time to time some new lubricant. Catch the dropping down lubricant and the chips in a box. Otherwise it will contaminate the floor and make it slippery. Bring the die−stock to the pipe and apply a little pressure to the stock. Keep the handle at right angles to the pipe axis. Rotate the handle clockwise with slight pressure towards the pipe, at right angles to the pipe axis. When the dies "bite" into the pipe, stop pushing and simply continue the rotation, by moving the handle up and down. If the die sticks there are probably some metal chips in the way. To break the metal chips reverse the knob and move the die anti−clockwise for half a round. Then proceed with cutting. After cutting the full length of thread reverse the knob and move the die anti−clockwise until you can take it off. Finally, clean off the threads with a wire brush and some cleaning rag. Test the thread with a fitting (elbow or tee). If it is too tight, adjust the dies again and repeat the threading operation. Finally clean the stock and die and store them properly. ASSEMBLING GALVANIZED STEEL PIPES A pipe fitters basic skill is to assemble, join and install pipe systems. He must know what kind of joint to use for different kind of piping materials, and must be able to make this joint absolutely watertight. Joints should not have leak. When you start to join or assemble galvanized pipes and fittings, you must know that the parallel female thread and the taper male are, without doubt, the most common type of connection. Procedure of Assembling: Fix the pipe in an applicable pipe vice If necessary clean the pipe with a steel brush or a cleaning rag Make sure that the pipe is also clean inside. Remove any burr and other materials To make a sound screw joint, threads must engage freely and it should be possible to turn the fitting for the first few turns by hand without any difficulty Wrap "Teflon" tape round the male thread in the same direction as the male thread. Do not apply sealing compound. Screw the pipe fitting onto the end of the galvanized pipe by hand as far as it will go Now use a pipe wrench. Adjust the wrench to the right size while using the adjustment wheel. Continue the screwing process, using gradual, even increase in force to tighten the threads together. Do not over−tighten the fitting. This can cause a pipe fitting to split. If you assemble two pipe joints (a fitting in between) then use two pipe wrenches. To assemble pipes with a diameter bigger than 2", the use of a chain wrench is sometimes recommended. But do not use it for diameters below 2". Otherwise the pipe might be flattened or damaged. UNION When the threaded ends of two pipes meet, the best way to assemble them, or connect them, is to use a union. This makes it easy to take the pipe system apart for repairs. A union is a device used to connect pipes. It usually consists of three pieces: There are two different types of unions available: One with a ground joint which does not acquire a sealing to make the connection watertight One, which requires a soft rubber, leather or "Teflon" washer to make the connection watertight Note: A little grease on the union joint ensures easy disconnection. Use two pipe wrenches to assemble or tighten the union. Hold one side of the union in one pipe wrench and the ring of the union in the other. Turn the two pipe wrenches gently in opposite directions until it is tighten.