BEEE-UNIT 3 PDF
Document Details
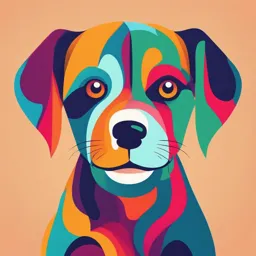
Uploaded by RejoicingDysprosium
SRM Institute of Science and Technology
Tags
Related
Summary
This document provides information on topics in electrical engineering, focusing on machines and drives, transformers, and various types of motors. The content could be used as study material or a reference guide.
Full Transcript
21EES101T-ELECTRICAL AND ELECTRONICSENGINEERING EEE-UNIT 3 Machines and Drives Construction and working principle of DC machines- Construction and Working principle of a single-phase Transformer- Construction and working of three phase Inductor motor, BLDC motor...
21EES101T-ELECTRICAL AND ELECTRONICSENGINEERING EEE-UNIT 3 Machines and Drives Construction and working principle of DC machines- Construction and Working principle of a single-phase Transformer- Construction and working of three phase Inductor motor, BLDC motor, PMSM, Stepper and Servo motor -Introduction to Electrical Drives-Block diagram explanation of chopper fed DC drives, Selection of drives for real time applications (cranes/EV/ Pumping applications) Practice on chopper applications, Demo on DC& AC machines 1 2 3 4 5 6 Single Phase Transformer Principle of operation The transformer works on the principle of electromagnetic induction. In this case, the conductors are stationary and the magnetic flux is varying with respect to time. Thus, the induced emf comes under the classification of statically induced emf. The transformer is a static piece of apparatus used to transfer electrical energy from one circuit to another. The two circuits are magnetically coupled. One of the circuits is energized by connecting it to a supply at specific voltage magnitude, frequency and waveform. Then, we have a mutually induced voltage available across the second circuit at the same frequency and waveform but with a change in voltage magnitude if desired. These aspects are indicated in Fig. 7 Construction The following are the essential requirements of a transformer: (a) A good magnetic core (b) Two windings (c) A time varying magnetic flux The transformer core is generally laminated and is made out of a good magnetic material such as transformer steel or silicon steel. Such a material has high relative permeability and low hysteresis loss. In order to reduce the eddy current loss, the core is made up of laminations of iron. ie, the core is made up of thin sheets of steel, each lamination being insulated from others 8 9 10 11 BLDC Motor 12 13 14 15 PMSM 16 17 18 19 Stepper Motor 02-09-2022 20 Why Stepper Motor? Motor that moves one step at a time A digital version of an electric motor Each step is defined by a Step Angle Relatively inexpensive Ideal for open loop positioning control − Can be implemented without feedback − Minimizes sensing devices − Just count the steps Torque − Holds its position firmly when not turning − Eliminates mechanical brakes − Produces better torque than DC motors at lower speeds Positioning applications 02-09-2022 21 Types of Stepping Motors Permanent Magnet − Magnetic rotor Variable Reluctance − Non-magnetic, geared rotor Hybrid − Combines characteristics from PM and VR − Magnetic, geared rotor 02-09-2022 22 02-09-2022 23 Variable Reluctance Stepper Motor It consists of a wound stator and a soft iron multi-tooth rotor. The stator has a stack of silicon steel laminations on which stator windings are wound. Usually, it is wound for three phases which are distributed between the pole pairs. The rotor carries no windings and is of salient pole type made entirely of slotted steel laminations. The rotor pole’s projected teeth have the same width as that of stator teeth. The number of poles on stator differs to that of rotor poles, which provides the ability to self start and bidirectional rotation of the motor. 02-09-2022 24 Cross section model of 3-ph VR stepper motor and winding arrangement 02-09-2022 25 VR Stepper motor has following modes of operation 1. 1 phase ON (or) Full step operation mode 2. 2 phase ON mode 3. Alternate 1 phase ON and 2 phase ON mode (or) Half step operation mode 4. Micro stepping operation mode 02-09-2022 26 Working of Variable Reluctance Stepper Motor The stepper motor works on the principle that the rotor aligns in a particular position with the teeth of the excitation pole in a magnetic circuit wherein minimum reluctance path exist. Whenever power is applied to the motor and by exciting a particular winding, it produces its magnetic field and develops its own magnetic poles. Due to the residual magnetism in the rotor magnet poles, it will cause the rotor to move in such a position so as to achieve minimum reluctance position and hence one set of poles of rotor aligns with the energized set of poles of the stator. At this position, the axis of the stator magnetic field matches with the axis passing through any two magnetic poles of the rotor. 02-09-2022 27 When the rotor aligns with stator poles, it has enough magnetic force to hold the shaft from moving to the next position, either in clockwise or counter clockwise direction. The stepper motor works on the principle that the rotor aligns in a particular position with the teeth of the excitation pole in a magnetic circuit wherein minimum reluctance path exist. Whenever power is applied to the motor and by exciting a particular winding, it produces its magnetic field and develops its own magnetic poles. Due to the residual magnetism in the rotor magnet poles, it will cause the rotor to move in such a position so as to achieve minimum reluctance position and hence one set of poles of rotor aligns with the energized set of poles of the stator. At this position, the axis of the stator magnetic field matches with the axis passing through any two magnetic poles of the rotor. When the rotor aligns with stator poles, it has enough magnetic force to hold the shaft from moving to the next position, either in clockwise or counter clockwise direction. 02-09-2022 28 02-09-2022 29 Servo Motor ❑ Servo is an electromagnetic device uses a negative feedback mechanism to converts an electric signal into controlled motion. Basically, servos behave like as actuators which provide precise control over velocity, acceleration, and linear or angular position. ❑ It consists of four things: DC motor, position sensor, gear train, and a control circuit. The gear mechanism connected with the motor provides the feedback to the position sensor. ❑ If the motor of the servo is operated by DC then it is called a DC servo motor and if it is operated by AC then it is called as AC servo motor. The gear of the servo motor is generally made up of plastic but in high power servos, it is made up of metal. 30 Types of Servo Motors on the Basis of Rotation Positional Rotation Servos: Positional servos can rotate the shaft in about half of the circle. Also, it has the feature to protect the rotational sensor from over-rotating. Positional servos are mainly used in limbs, robotic arms, and in many other places. Continuous Rotation Servos: Continuous servos are similar in construction to the positional servo. But, it can move in both clockwise and anticlockwise directions. These types of servos are used in radar systems and robots. Linear Servos: Again linear servos are also like a positional servo, but with additional gears to the adjust the output from circular to back-and-forth. These type of servos are used in high model airplanes and are rare to find on the stores. 31 On the Basis of Operating Signal (i) Analog Servomotors: Analog servos are operated over PWM (Pulse Width Modulation) signals. (ii) Digital Servomotors: Digital Servo receives signal and acts at high-frequency voltage pulses. Digital servo gives a smooth response and consistent torque, due to faster pulse. Digital servos consume more power than an analog servo. On the Basis of Operating Power (i) DC Servo Motor (ii) AC Servo Motor 32 Construction of Servo Motor: 33 Closed loop system - Servo Motor: 34 Stator Winding: This type of winding wound on the stationary part of the motor. It is also known as field winding of the motor. Rotor Winding: This type of winding wound on the rotating part of the motor. It is also known as an armature winding of the motor. Bearing: These are of two types, i.e, font bearing and back bearing which are used for the movement of the shaft. Shaft: The armature winding is coupled on the iron rod is known as the shaft of the motor. Encoder: It has the approximate sensor which determines the rotational speed of motor and revolution per minute of the motor. 35 Working of Servo Motors ❑ The servo has a position sensor, a DC motor, a gear system, a control circuit. The DC motor run at high speed and low torque when getting power from a battery. The position of shaft senses by position sensor from its definite position and supply information to the control circuit. ❑ The reduction gearbox is connected to a shaft which decreases the RPM of the motor. The output shaft of the reduction gearbox is the same as of motor which is connected with encoder or potentiometer. ❑ The output of the encoder is then connected to the control circuit. The wires of the servomotor are also connected to the control circuit. ❑ The motor control through microcontroller by sending signals in the form of PWM which decodes the control circuit to rotate the motor in required angle the control circuit moves the motor in a clockwise or anticlockwise direction, with this the shaft also rotates in the desired direction. 36 Applications of Servo Motors ❑ They are used to control the positioning and movement of elevators in radio controlled airplanes. ❑ They play an important role in robotics information of robot because of their smooth switching on or off and accurate positioning. ❑ They are used in hydraulic systems to maintain hydraulic fluid in the aerospace industry. ❑ In radio controlled toys these are also used. ❑ They are used to extend or replay the disc trays in electronic devices such as DVDs or Blue-ray Disc players. ❑ They are used to maintain the speed of vehicles in the automobile industries. 37 Electrical Drives Diesel/petrol/gas/stream engines, hydraulic motors, electric motors 38 Advantages of Electrical Drives 39 Block Diagram of Electric Drive System 40 Components in electric drives Motors DC motors - permanent magnet – wound field AC motors – induction, synchronous brushless DC Applications, cost, environment Natural speed-torque characteristic is not compatible with load requirements Power sources DC – batteries, fuel cell, photovoltaic - unregulated AC – Single- three- phase utility, wind generator - unregulated Power processor To provide a regulated power supply Combination of power electronic converters More efficient Flexible Compact AC-DC, DC-DC, DC-AC, AC-AC 41 Components in electric drives Control unit Complexity depends on performance requirement analog- noisy, inflexible, ideally has infinite bandwidth. DSP/microprocessor – flexible, lower bandwidth - DSPs perform faster operation than microprocessors (multiplication in single cycle), can perform complex estimations Electrical isolation between control circuit and power circuit is needed: Malfunction in power circuit may damage control circuit Safety for the operator Avoid conduction of harmonic to control circuit 42 Components in electric drives Sensors Sensors (voltage, current, speed or torque) is normally required for closed-loop operation or protection. Electrical isolation between sensors and control circuit is needed. The term ‘sensorless drives’ is normally referred to the drive system where the speed is estimated rather than measured. 43 Applications of Electric Drives Transportation Systems Rolling Mills Paper Mills Textile Mills Machine Tools Fans and Pumps Robots Washing Machines etc 44 Chopper fed dc drive 45 Factors for selection of Electrical Drives 46 Solar Powered Pump System 47 Solar Powered Pump Drives with reciprocating pump ❖ For pump ratings of 1 kW and above, three phase induction motor drive is employed. ❖ A PWM voltage source inverter with maximum-power-point- tracker is used for variable frequency control of the squirrel- cage induction motor. Solar pump drive using induction motor 48 Solar Powered Pump Drives with battery ❖ Solar Powered Pump Drives with an intermediate battery, can also be used. ❖ The drive is fed from the battery charged by solar panel. Solar pump with a battery 49 Selection of drives and control schemes for lifts and cranes 50 Selection of drives and control schemes for lifts and cranes 1) Quick Lift: To allow a lightly loaded or empty hoist to move up and down faster than the base speed of the motor 2) Reverse Plug Simulation: When reversing directions, the inverter will decelerate at a faster rate than the normal deceleration rate. 3) Load Hold (Hang Time): To hold a load aloft at zero speed without setting the brake. Permit precise positioning of the load without delays normally associated with mechanical operation of the brake. 4) Fast Stop: To Rapidly decelerate the drive when the run command is removed i.e. when back-up limit switch is tripped 51 Selection of drives and control schemes for lifts and cranes 4) Speed Control: To accommodate five-speed cabin/pendant control, infinitely variable speed control, and a bi-polar voltage or analog current input speed command 5) Micro speed Positioning Control: To Permit extremely slow movements for greater positioning accuracy 6) Dual Upper and Lower Limit Switch Inputs: To accommodate limit-switch inputs on both the upper and lower travel of the hoist displayed. Further movement in hoist direction is prevented. 7) Torque Limits: Two sets of Fwd and rev torque limits are provided. 8) Torque Limited Acceleration / Deceleration Times: For smooth starts and stops to prevent load sway 52 EV Control schemes 53 EV Control schemes 54