BCE 223L Construction Materials and Testing PDF
Document Details
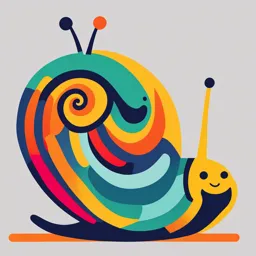
Uploaded by WarmMoscovium
University of Mindanao
Engr. Clib James I. Delos Reyes
Tags
Related
Summary
This document is a self-instructional manual (SIM) for self-directed learning (SDL) for students in a civil engineering program at the University of Mindanao. It covers construction materials and testing.
Full Transcript
College of Engineering Education 2nd Floor, B&E Building Matina Campus, Davao City...
College of Engineering Education 2nd Floor, B&E Building Matina Campus, Davao City Telefax: (082) 296-1084 Phone No.: (082)300-5456/300-0647 Local 133 UNIVERSITY OF MINDANAO College of Engineering Education Civil Engineering Program Physically Distanced but Academically Engaged Self-Instructional Manual (SIM) for Self-Directed Learning (SDL) Course/Subject: : BCE 223L – CONSTRUCTION MATERIALS AND TESTING Name of Teacher: ENGR. CLIB JAMES I. DELOS REYES THIS SIM/SDL MANUAL IS A DRAFT VERSION ONLY; NOT FOR REPRODUCTION AND DISTRIBUTION OUTSIDE OF ITS INTENDED USE. THIS IS INTENDED ONLY FOR THE USE OF THE STUDENTS WHO ARE OFFICIALLY ENROLLED IN THE COURSE/SUBJECT. EXPECT REVISIONS OF THE MANUAL. Page 1 of 208 College of Engineering Education 2nd Floor, B&E Building Matina Campus, Davao City Telefax: (082) 296-1084 Phone No.: (082)300-5456/300-0647 Local 133 TABLE OF CONTENTS PAGE Cover Page ……………………………………………………………………………………………… 1 Table of Contents……………………………………………………………………………………….. 2 Course Outline………………………………………………………………………………………… ….. 4 Course Outline Policy…………………………………………………………………………………. 4 Course Information……………………………………………………………………………………. 6 Topic/ Activity Unit Learning Outcomes- Unit 1 Big Picture in Focus: ULO-1a…………………………………………………………………..….. 7 Metalanguage…………………………………………………………………………………... 7 Essential Knowledge………………………………………………………………………… 7 INTRODUCTION: Building Stones, Structural Clay and Aggregates 1. Types and Properties of Building Stones, Structural Clay …... 8 2. Aggregates ……………………………………………………………………….. 15 3. Reducing Field Sample of Aggregates to Testing Size …………. 15 4. Determination of Surface Moisture of Coarse Aggregates …….. 18 5. Sieve Analysis of Coarse Aggregates …………………………………… 20 6. Determination of Unit Weight of Aggregates ……………………….. 25 7. Specific Gravity Determination – FA & C ……………………………… 26 8. Absorption Determination- FA & CA ……………………………………. 26 9. Unit Weight Determination- FA & CA ………………………………….. 32 10. Moisture Content Determination- FA & CA …………………………. 37 11. Determination of Fineness Modulus ……………………………………. 39 12. Soundness Test ………………………………………………………………….. 43 13. Test for Organic Impurities ………………………………………………….. 47 14. Abrasion Test …………………………………………………………………….. 50 SELF HELP ………………………………………………………………………………………. 53 Let’s Check …………………………………………………………………………………….. 53 Let’s Analyze …………………………………………………………………………………. 54. In a Nutshell ………………………………………………………………………………….. 54 Q & A Lists …………………………………………………………………………………….. 55 Keyword Index …………………………………………………………………………….. 56 Unit Learning Outcomes – Unit 2 Big Picture in Focus: ULO-2a…………………………………………………………………..….. 57 Metalanguage…………………………………………………………………………………... 57 Essential Knowledge………………………………………………………………………… 57 INTODUCTION : Cement and Concrete 1. Types of Cement Used in Construction ………………………………………. 57 2. Hydraulic Cement by Vicat Needle………………………………………………. 72 3. Common Concrete Mix Proportion and Its Application…………………. 74 4. Portland and Hydraulic Cement Concrete …………………………………… 91 5. Admixtures ……………………………………………………….…………………….. 93 6. Completed Pavement …………………………………………………………………. 106 SELF HELP ……………………………………………………………………………………… 109 Let’s Check …………………………………………………………………………………….. 109 Let’s Analyze …………………………………………………………………………………. 110 In a Nutshell ………………………………………………………………………………….. 111 Q & A Lists …………………………………………………………………………………….. 111 Page 2 of 208 College of Engineering Education 2nd Floor, B&E Building Matina Campus, Davao City Telefax: (082) 296-1084 Phone No.: (082)300-5456/300-0647 Local 133 Keyword Index …………………………………………………………………………….. 111 Unit Learning Outcomes- Unit 3 Big Picture in Focus: ULO-3a…………………………………………………………………..….. 112 Metalanguage…………………………………………………………………………………... 112 Essential Knowledge………………………………………………………………………… 112 INTRODUCTION: Metals and Woods 1. Metals: Wrought Iron, Cast Iron, Steel and Alloys ….…………… 112 2. Quality Test for Bending, Tension and Chemical Analysis …… 123 3. Reinforcing Steel………………………………………………………………. 138 4. Markings ………………………………..………………………………………… 143 5. Basic Properties ……………………………………………………………….. 144 6. Tensile Test ……………… ……………………………………………………. 146 7. Wood: Characteristics and It’s Physical Properties ……………. 155 8. Testing Requirements ………………………………………………………. 157 SELF HELP …………………………………………………………………………………….. 187 Let’s Check …………………………………………………………………………………….. 187 Let’s Analyze …………………………………………………………………………………. 188 In a Nutshell ………………………………………………………………………………….. 188 Q & A Lists …………………………………………………………………………………….. 189 Keyword Index …………………………………………………………………………….. 189 Unit Learning Outcomes- Unit 4 Big Picture in Focus: ULO-1a…………………………………………………………………..….. 190 Metalanguage…………………………………………………………………………………... 190 Essential Knowledge………………………………………………………………………… 190 INTRODUCTION: Asphalts 1. Bituminous Materials ………..……………………………………………… 190 2. Composition of Asphalts……………………………………………………. 193 3. Kinds and Uses of Asphalt ………………………………………………… 196 4. Quality of Bituminous Materials Used in Different Mixtures/Surfaces ……………………………………………………………. 198 5. Bituminous Mixing Plants …………………………………………………. 203 6. Laboratory Tests for Bituminous Materials ……………………….. 206 SELF HELP ……………………………………………………………………………………… 225 Let’s Check …………………………………………………………………………………….. 225 Let’s Analyze ……………………………………………………………………………….…. 225 In a Nutshell …………………………………………………………………………………... 226 Q & A Lists ……………………………………………………………………………………... 226 Keyword Index ……………………………………………………………………………… 227 Page 3 of 208 College of Engineering Education 2nd Floor, B&E Building Matina Campus, Davao City Telefax: (082) 296-1084 Phone No.: (082)300-5456/300-0647 Local 133 COURSE OUTLINE: BCE 223L – CONSTRUCTION MATERIALS AND TESTING Course Coordinator: Engr. Clib James I. Delos Reyes Email: [email protected] Student Consultation: - Mobile: N/A Phone: (082) 2961084 or local 131 Office Effectivity Date: August 8, 2022 Mode of Delivery: Blended (On-Line with face to face or virtual sessions) Time Frame: 36 Hours lecture and 54 Hours laboratory Student Workload: Expected Self-Directed Learning Requisites: CE 117 Co- requisite: BCE 222 Credit: 2 units lecture, 1unit laboratory Attendance Requirements: A minimum of 95% attendance is required at all scheduled Virtual or face to face sessions. COURSE OUTLINE POLICY Areas of Concern Details Contact and Non-contact This 2-unit and 1-unit laboratory course self-instructional Hours manual is designed for blended learning mode of instructional delivery with scheduled face to face or virtual sessions. The expected number of hours will be 36 hours lecture and 54 hours laboratory including the face to face or virtual sessions. The expected number of hours will be 90 including the face- to-face or virtual sessions. The face-to-face sessions shall include the summative assessment tasks (exams) since this course is crucial in the licensure examination for civil engineers. Assessment Task Submission Submission of assessment tasks shall be on 3rd, 5th, 7th and 9th week of the term. The assessment paper shall be attached with a cover page indicating the title of the assessment task (if the task is performance), the name of the course coordinator, date of submission and name of the student. The document should be emailed to the course coordinator. It is also expected that you already paid your tuition and other fees before the submission of the assessment task. If the assessment task is done in real time through the features in the Blackboard Learning Management System, the schedule shall be arranged ahead of time by the course coordinator. Since this course is included in the licensure examination for civil engineers, you will be required to take the exam inside the University. This should be scheduled ahead of time by your course coordinator. This is non-negotiable for all licensure- based programs. Turnitin Submission To ensure honesty and authenticity, all assessment tasks are (if necessary) required to be submitted through Turnitin with a maximum similarity index of 30% allowed. This means that if your paper goes beyond 30%, the students will either opt to redo her/his Page 4 of 208 College of Engineering Education 2nd Floor, B&E Building Matina Campus, Davao City Telefax: (082) 296-1084 Phone No.: (082)300-5456/300-0647 Local 133 paper or explain in writing addressed to the course coordinator the reasons for the similarity. In addition, if the paper has reached more than 30% similarity index, the student may be called for a disciplinary action in accordance with the University’s OPM on Intellectual and Academic Honesty. Please note that academic dishonesty such as cheating and commissioning other students or people to complete the task for you have severe punishments (reprimand, warning, expulsion). Penalties for Late The score for an assessment item submitted after the Assignments/Assessments designated time on the due date, without an approved extension of time, will be reduced by 5% of the possible maximum score for that assessment item for each day or part day that the assessment item is late. However, if the late submission of assessment paper has a valid reason, a letter of explanation should be submitted and approved by the course coordinator. If necessary, you will also be required to present/attach evidences. Return of Assignments/ Assessment tasks will be returned to you two (2) weeks Assessments after the submission. This will be returned by email or via Blackboard portal. For group assessment tasks, the course coordinator will require some or few of the students for online or virtual sessions to ask clarificatory questions to validate the originality of the assessment task submitted and to ensure that all the group members are involved. Assignment Resubmission You should request in writing addressed to the course coordinator his/her intention to resubmit an assessment task. The resubmission is premised on the student’s failure to comply with the similarity index and other reasonable grounds such as academic literacy standards or other reasonable circumstances e.g. illness, accidents financial constraints. Re-marking of Assessment You should request in writing addressed to the program Papers and Appeal coordinator your intention to appeal or contest the score given to an assessment task. The letter should explicitly explain the reasons/points to contest the grade. The program coordinator shall communicate with the students on the approval and disapproval of the request. If disapproved by the course coordinator, you can elevate your case to the program head or the dean with the original letter of request. The final decision will come from the dean of the college. Grading System All culled from BlackBoard sessions and traditional contact Page 5 of 208 College of Engineering Education 2nd Floor, B&E Building Matina Campus, Davao City Telefax: (082) 296-1084 Phone No.: (082)300-5456/300-0647 Local 133 Submission of the final grades shall follow the usual University system and procedures. Preferred Referencing Style Depends on the discipline; if uncertain or inadequate, use the general practice of the APA 6th Edition. Student Communication You are required to create a umindanao email account which is a requirement to access the BlackBoard portal. Then, the course coordinator shall enroll the students to have access to the materials and resources of the course. All communication formats: chat, submission of assessment tasks, requests etc. shall be through the portal and other university recognized platforms. You can also meet the course coordinator in person through the scheduled face to face sessions to raise your issues and concerns. For students who have not created their student email, please contact the course coordinator or program head. Contact Details of the Dean Dr. Charlito L. Cañesares Email: [email protected] Phone: (082) 296-1084 or 300-5456 loc. 133 Contact Details of the Engr. Showna Lee T. Sales Program Email: [email protected] Head Phone: (082) 296-1084 or 300-5456 loc. 133 Students with Special Needs Students with special needs shall communicate with the course coordinator about the nature of his or her special needs. Depending on the nature of the need, the course coordinator with the approval of the program coordinator may provide alternative assessment tasks or extension of the deadline of submission of assessment tasks. However, the alternative assessment tasks should still be in the service of achieving the desired course learning outcomes. Help Desk Contact Jessica Dagohoy CEE [email protected] Page 6 of 208 College of Engineering Education 2nd Floor, B&E Building Matina Campus, Davao City Telefax: (082) 296-1084 Phone No.: (082)300-5456/300-0647 Local 133 082-2272902 Library Contact Brigida E. Bacani [email protected] 09513766681 GSTC Contact Ronadora E. Deala, RPsy, RPm, RGC, LPT [email protected] 09212122846 Silvino P. Josol [email protected] 0906075772 Course Information – see/download course syllabus in the Blackboard LMS CC’s Voice: Hello prospective engineers! Welcome to this course BCE 223L: Construction Materials and Testing. By now, I am confident that you really wanted to become a civil engineer and that you have visualized yourself with professional expertise and ethical responsibility in the practice of the profession. Furthermore, show dedication and initiative in research and innovation or entrepreneurial ventures, and professional development. CO: Upon completion of this course, you are expected to: CO1. Recognize the physical and structural properties for most common and advanced construction materials CO 2. Conduct experiments on common construction materials according to international standards such as the American Society for Testing and Materials (ASTM) CO 3. Evaluate the results of the test of common construction material Let us begin! BIG PICTURE Week 1 to 3: Unit Learning Outcomes 1 (ULO 1): At the end of the unit, you are expected to: a. Demonstrate knowledge and understanding of the properties and behaviors of most common and advance construction material such as building stones, structural clay and aggregates. b. Conduct the methods, procedures and formulas of different experiments on common construction materials according to international standards such as ASTM & AASTHO. Big Picture inULO Focus 1a. Demonstrate knowledge and understanding of the properties and behaviors of most common and advance construction material such as building stones, structural clay and aggregates Metalanguage This section deals with the study of different types and properties of construction materials such as building stones, structural clay and aggregates. Page 7 of 208 College of Engineering Education 2nd Floor, B&E Building Matina Campus, Davao City Telefax: (082) 296-1084 Phone No.: (082)300-5456/300-0647 Local 133 Please proceed immediately to the “Essential Knowledge”. Essential Knowledge To perform the aforesaid big picture (unit learning outcomes) for the first three (3) weeks of the course, you need to fully understand the following essential knowledge that will be laid down in the succeeding pages. Please note that you are not limited to exclusively refer to these resources. Thus, you are expected to utilize other books, research articles and other resources that are available in the university’s library e.g. ebrary, search.proquest.com etc. INTRODUCTION Building material is any material which is used for construction purposes. This can be classified as natural or synthetic. Many naturally occurring substances such as rocks, clay, sand and wood , even twigs and leaves, have been used for construction. Apart from naturally occurring materials, many man-made products are in use, some more and some less synthetic. The manufacturing of building materials is an established industry in many countries and the use of these materials is typically segmented into specific specialty trades, such as carpentry, insulation, plumbing, and roofing work. TYPES AND PROPERTIES OF BUILDING STONES & STRUCTURAL CLAY I. Building Stones Stones are naturally occurring compact, solid and massive material that make the crust of the earth. Technically, the stones are called as rocks. The rocks occur in great variety. The rocks possess suitable properties often find use in building stones. It follows that all building stones are rocks in nature, all rocks may not be useful as building stones. Classification of Stones A. Geological Classification This classification is based on mode of formation of the rock from which building stones are obtained. Three main group recognized are: I) Igneous Rocks - those rocks of the earth that have been formed by the natural process of cooling and crystallization from originally hot and molten magma. Granite, Gabbro, Basalt, Diorite and Obsidian are some of the examples of Igneous Rocks. II) Sedimentary Rocks - are formed from any type of preexisting rocks by a simple process of breakdown into smaller particles under the influence of natural agencies like wind, water and ice and atmospheric gases. This type of rocks includes Conglomerate, Sandstone, Siltstone, Shale, etc. III) Metamorphic Rocks - These are originally either igneous or sedimentary rocks. The process for their change under the influence of increased temperature, pressure, and chemical environment is called metamorphism. The most well-known examples of metamorphic rocks are marble and slate. B. Physical Classification The basis for such a classification is the physical properties of rocks, the manner and arrangement of different particles and mass forming a stone. They classified as follows: Page 8 of 208 College of Engineering Education 2nd Floor, B&E Building Matina Campus, Davao City Telefax: (082) 296-1084 Phone No.: (082)300-5456/300-0647 Local 133 I) Foliated Rocks - show definite parallel arrangement of minerals showing a tendency to split in a specific direction. Examples are gneiss, and schist. II) Stratified Rocks - formed due to the splitting of parallel layers of sedimentary rocks. They exhibit distinct layers which can be separated. The plane of separation is called as a cleavage plane. Examples are limestone, slate, and sandstone. III) Unstratified Rocks - are granular or crystalline structure and become solid and cooling. They do not show any sign of strata. Examples are igneous rocks like granite, basalt, etc. C. Chemical Classification The presence of chemical constituents in the rocks is the basis for their type of classification. they are as follows: I) Argillaceous Rocks - clay and alumina is the main constituents. Examples of the argillaceous rocks are slate, laterite, etc. II) Siliceous Rocks - in this type, silica is the main constituent. The presence of the silica in the free state is called sand, and in the combined state is silicate. Examples of the silicate rocks are sandstone, quartzite, etc. III) Calcareous Rocks - calcium carbonate or lime is the main constituents in these rocks. They are readily acted upon by dilute HCL. Examples are limestone, marble, etc. II. Structural Clay Structural Clay is a widely used material in the construction Industry. It is a recyclable and sustainable product, it is fire resistant and the color ranges from light brown to burnt red. The various types of clay products used in the construction industry are: 1. Brick – is extensively used in the construction of the external and internal walls of the building where they are joined with cement plaster. 2. Terracotta – is used as a roofing material and external natural tile cladding material to create the feel of exposed brick work. 3. Hollow Block Tile – are used to create the external walls of the building and are very good insulators of sound and heat. 4. Paver Blocks – are used in driveways and landscaped gardens. They are light in weight, strong and are usually in the form of interlocking tiles. 5. Brick Glazed Tile – Glazed brick tiles are used as an external cladding material so as to give the look of exposed brick work. 6. Roofing Material – Clay is used as roofing material in many houses having sloped roofs. This prevents the entry of water into the interiors. It is mainly used in areas having heavy rainfall. III. Properties of Building Materials A. Physical Properties These are the properties required to estimate the quality and condition of the material without any external force. The physical properties of engineering materials are as follows: Bulk Density is the ratio of mass to the volume of the material in its natural state that is including voids and pores. It is expressed in kg/m3. Bulk density influences the mechanical properties of materials like strength, heat and conductivity etc. Page 9 of 208 College of Engineering Education 2nd Floor, B&E Building Matina Campus, Davao City Telefax: (082) 296-1084 Phone No.: (082)300-5456/300-0647 Local 133 Porosity gives the volume of the material occupied by pores. It is the ratio of volume of pores to the volume of material. Porosity influences many properties like thermal conductivity, strength, bulk density, durability etc. Durability is the property of a material to withstand against the combined action of atmospheric and other factors. If the material is more durable, it will be useful for longer life. Maintenance cost of material is dependent of durability. Specific Gravity is the ratio of mass of given substance to the mass of water at 4oC for the equal volumes. Fire resistance is the ability to withstand against fire without changing its shape and other properties. Fire resistance of a material is tested by the combined actions of water and fire. Fireproof materials should provide more safety in case of fire. Frost resistance is the ability of a material to resist freezing or thawing. It depends upon the density and bulk density of material. Denser materials will have more frost resistance. Moist materials have low frost resistance and they lose their strength in freezing and become brittle. Weathering Resistance is the property of a material to withstand against all atmospheric actions without losing its strength and shape. Weathering effects the durability of material. For example, corrosion occurs in iron due to weathering. To resist this paint layer is provided. Spalling Resistance is the ability of a material to undergo certain number of cycles of sharp temperature variations without failing. It is the dependent of coefficient of linear expansion. Water Absorption is the capacity of a material to absorb and retain water in it. It is expressed in % of weight of dry material. It depends up on the size, shape and number of pores of material. Water Permeability is the ability of a material to permit water through it. Hygroscopicity is the property of a material to absorb water vapor from the air. It depends on the relative humidity, porosity, air temperature etc. Refractoriness is the property of a material which cannot melts or lose its shape at prolonged high temperatures (1580oC or more). Example: fire clay is high refractory material. B. Mechanical Properties Mechanical properties of the materials are find out by applying external forces on them. The mechanical properties are, Strength is the capacity of a material to resist failure caused by loads acting on it. The load may be compressive, tensile or bending. It is determined by dividing the ultimate load taken by the material with its cross sectional area. Hardness is the property of a material to resist scratching by a herder body. MOHS scale is used to determine the hardness of a materials. Elasticity is the capacity of a material to regain its initial shape and size after removal of load is known as elasticity and the material is called as elastic material. Plasticity is when the load applied on the material will undergo permanent deformation without cracking and retain this shape after the removal of load then it is said to be plastic material. Brittleness is when the material subjected to load, fails suddenly without causing any deformation then it is called brittle material. Page 10 of 208 College of Engineering Education 2nd Floor, B&E Building Matina Campus, Davao City Telefax: (082) 296-1084 Phone No.: (082)300-5456/300-0647 Local 133 Fatigue. If a material is subjected to repeated loads, then the failure occurs at some point which is lower than the failure point caused by steady loads. Impact Strength. If a material is subjected to sudden loads and it will undergo some deformation without causing rupture. It designates the toughness of material. Abrasion Resistance. The loss of material due to rubbing of particles while working is called abrasion. The abrasion resistance for a material makes it durable and provided long life. Creep is the deformation caused by constant loads for long periods. C. Chemical Properties The properties of materials against the chemical actions or chemical combinations are termed as chemical properties. And they are, Chemical Resistance is the ability of a construction material to resist the effects of chemicals like acids, salts and alkalis. Corrosion Resistance. Formation of rust (iron oxide) in metals, when they are subjected to atmosphere is called as corrosion. D. Thermal Properties The thermal properties of a material are those that are related to the materials response to heat. When a material is subjected to a change in temperature, it may expand, contract, conduct, or reflect heat. Ceramics can withstand high temperatures, are good thermal insulators, and do not expand greatly when heated. Thermal Capacity is the property of a material to absorb heat and it is required to design proper ventilation. It influences the thermal stability of walls. It is expressed in J/NC and it is calculated by the formula: Thermal capacity, T = [H/(M(T2 – T1))] Where H = quantity of heat required to increase the temperature from T1 to T2 T1 = Initial temperature T2 = Final temperature M = Mass of material in N. Thermal Conductivity. The amount of heat transferred through unit area of specimen with unit thickness in unit time is termed as thermal conductivity. Thermal Resistivity. It is the ability to resist heat conduction. And it is the reciprocal of thermal conductivity. When it is multiplied by thickness of material it gives thermal resistance. Specific Heat is the quantity of heat required to heat 1 N of material by 1C. Specific heat is useful when we use the material in high temperature areas. IV. AGGREGATES Aggregate, in building and construction, is a material used for mixing with cement, bitumen, lime, gypsum, or other adhesive to form concrete or mortar. The aggregate gives volume, stability, resistance to wear or erosion, and other desired physical properties to the finished product. Commonly used aggregates include sand, crushed or broken stone, gravel (pebbles), broken blast-furnace slag, boiler ashes (clinkers), burned shale, and burned clay. Fine aggregate usually consists of sand, crushed stone, or crushed slag screenings; coarse aggregate consists of gravel (pebbles), fragments of broken stone, slag, and other coarse substances. Fine aggregate is used in making thin concrete slabs or other structural members and where a smooth surface is desired; coarse aggregate is used for more massive members. Page 11 of 208 College of Engineering Education 2nd Floor, B&E Building Matina Campus, Davao City Telefax: (082) 296-1084 Phone No.: (082)300-5456/300-0647 Local 133 V. PROPERTIES OF AGGREATES 1. Composition. Aggregates consisting of materials that can react with alkalis in cement and cause excessive expansion, cracking and deterioration of concrete mix should never be used. Therefore, it is required to test aggregates to know whether there is presence of any such constituents in aggregate or not. 2. Size & Shape. The size and shape of the aggregate particles greatly influence the quantity of cement required in concrete mix and hence ultimately economy of concrete. 3. Surface Texture. The development of hard bond strength between aggregate particles and cement paste depends upon the surface texture, surface roughness and surface porosity of the aggregate particles. If the surface is rough but porous, maximum bond strength develops. 4. Specific Gravity. The ratio of weight of oven dried aggregates maintained for 24 hours at a temperature of 100 to 110 C, to the weight of equal volume of water displaced by saturated dry surface aggregate is known as specific gravity of aggregates. 5. Bulk Density. It is defined as the weight of the aggregate required to fill a container of unit volume. It is generally expressed in kg/litre. 6. Voids. The empty spaces between the aggregate particles are known as voids. The volume of void equals the difference between the gross volume of the aggregate mass and the volume occupied by the particles alone. 7. Porosity & Absorption. The minute holes formed in rocks during solidification of the molten magma, due to air bubbles, are known as pores. Rocks containing pores are called porous rocks. Water absorption may be defined as the difference between the weight of very dry aggregates and the weight of the saturated aggregates with surface dry conditions. 8. Fineness Modulus. Fineness modulus is generally used to get an idea of how coarse or fine the aggregate is. More fineness modulus value indicates that the aggregate is coarser and small value of fineness modulus indicates that the aggregate is finer. 9. Deleterious Materials. Aggregates should not contain any harmful material in such a quantity so as to affect the strength and durability of the concrete. 10. Crushing Value. The aggregates crushing value gives a relative measure of resistance of an aggregate to crushing under gradually applied compressive load. 11. Impact Value. The aggregate impact value gives a relative measure of the resistance of an aggregate to sudden shock or impact. 12. Abrasion value of aggregates. The abrasion value gives a relative measure of resistance of an aggregate to wear when it is rotated in a cylinder along with some abrasive charge. What is ASTM? ASTM was originally known as the American Society of the International Association for Testing and Materials when it was created in 1898 by Pennsylvania Railroad engineers and scientists. Its purpose was to address and prevent the frequent rail breaks that were plaguing the industry by developing standards that would ensure higher quality rail products. Today, the American Society for Testing and Materials is known as ASTM International. It consists of over 30,000 members that include product users, producers, consumers, academics, and consultants. ASTM is still headquartered in Pennsylvania, but it also has offices throughout the world that are located in Belgium, Canada, China, and Mexico, as well as one other domestic office in Washington DC. Page 12 of 208 College of Engineering Education 2nd Floor, B&E Building Matina Campus, Davao City Telefax: (082) 296-1084 Phone No.: (082)300-5456/300-0647 Local 133 ASTM has come a long way from creating standards for steel in the railroad industry. Today, ASTM develops and publishes technical standards for many different industries with the goal of enhancing performance and safety over a wide range of products, materials, systems, and services. Thousands of ASTM standards are upheld all over the world, each with their own unique number. Each standard falls into a variety of categories which include: Standard Specification Standard Test Method Standard Practice Guide Standard Classification Terminology Standard Not only does ASTM create dependable standards, the society also offers technical training programs, proficiency testing, and inter-laboratory crosscheck programs. Continuing education and online training programs are available for industries and government employees. Courses can include plastics, coal, statistics, glass, and more. Self- guided training courses are available for QA/QC technicians who work with cement, concrete strength training, and who conduct aggregate testing. On-site training is also available, as are certification programs that cover a wide variety of products, materials, systems, and services in keeping with third party compliance standards. This is a list of ASTM International standards. Standard designations usually consist of a letter prefix and a sequentially assigned number. This may optionally be followed by a dash and the last two digits of the year in which the standard was adopted. Prefix letters correspond to the following subjects: A = Iron and Steel Materials B = Nonferrous Metal Materials C = Ceramic, Concrete, and Masonry Materials D = Miscellaneous Materials E = Miscellaneous Subjects F = Materials for Specific Applications G = Corrosion, Deterioration, and Degradation of Materials This list may include either current or withdrawn standards. A withdrawn standard has been discontinued by its sponsoring committee. A standard may be withdrawn with or without replacement. What is AASHTO? The American Association of State Highway and Transportation Officials (AASHTO) is a nonprofit, nonpartisan association representing highway and transportation departments in the 50 states, the District of Columbia, and Puerto Rico. It represents all transportation modes including: air, highways, public transportation, active transportation, rail, and water. Its primary goal is to foster the development, operation, and maintenance of an integrated national transportation system. AASHTO works to educate the public and key decision makers about the critical role that transportation plays in securing a good quality of life and sound economy for our nation. AASHTO serves as a liaison between state departments of transportation and the Federal government. AASHTO is an international leader in setting technical standards for all phases of highway system development. Standards are issued for design, construction of highways and bridges, materials, and many other technical areas. AASHTO serves as a catalyst for excellence in transportation by offering: Page 13 of 208 College of Engineering Education 2nd Floor, B&E Building Matina Campus, Davao City Telefax: (082) 296-1084 Phone No.: (082)300-5456/300-0647 Local 133 1. Smart solutions and promising practices; 2. Critical information, training and data; 3. Direct technical assistance to states; and 4. Unchallenged expertise. AASHTO is guided by a Board of Directors made up of the chief transportation officers from the 50 states, the District of Columbia, and Puerto Rico. The 12-member Executive Committee is led by AASHTO’s elected officers, and is assisted by its executive director. AASHTO’s policy development, standards setting, and technical activities are the product of volunteer state department of transportation personnel who work through the AASHTO committee structure. The committees collaborate throughout the year and typically meet annually. These committees, which represent the highest standard of transportation expertise in the country, address virtually every element of planning, designing, constructing, and maintaining transportation services. STANDARD PRACTICE FOR REDUCING SAMPLES OF AGGREGATE TO TESTING SIZE REFERENCED STANDARD: ASTM C702-87 / AASHTO T248-89 The field samples of aggregate must generally be reduced to an appropriate size for testing to determine physical characteristics, such as, sieve analysis, soundness, hardness, etc. The methods described in this test method are intended to minimize variations in the aggregate characteristics between the smaller test sample and the larger field sample. Several methods of sample reduction will be described. The technician must be sure to use the appropriate technique dependent on such factors as aggregate size and moisture content. The reduction methods include: Method A - Mechanical Splitter Method B - Miniature Stockpile Method C - Quartering In some circumstances, reducing the field sample prior to testing is not recommended. Substantial differences may unavoidably occur during sample reduction, i.e., in the case of an aggregate having relatively few large size particles in the sample. These few particles may be unequally distributed among the reduced size test samples. If the test sample is being examined for certain contaminants occurring as a few discreet particles in a small percentage, the reduced test sample may not be truly representative of the total aggregate as produced. In these cases, the entire original field sample should be tested. Failure to carefully follow the procedures in these methods of sample reduction may result in providing a nonrepresentative sample for subsequent testing, resulting in inaccurate test results, and ultimately, failure of the aggregate to perform as intended. SUMMARY OF PROCEDURE Aggregate and other materials sampled in the field need to be reduced to appropriate sizes for testing. It is, therefore, necessary to reduce field samples while minimizing the chance of variability during handling. In some instances, a few particles on a given sieve might affect a gradation significantly enough to alter an interpretation of the field sample and subsequently the entire material's compliance with specifications. Page 14 of 208 College of Engineering Education 2nd Floor, B&E Building Matina Campus, Davao City Telefax: (082) 296-1084 Phone No.: (082)300-5456/300-0647 Local 133 The appropriate field sample reduction method is dependent chiefly on the nominal maximum size of the aggregate, the amount of free moisture in the sample, and the equipment available. The following chart should be used in selecting the appropriate reduction method for the aggregate to be tested. METHOD A -- MECHANICAL SPLITTER Apparatus Mechanical Splitter - The mechanical sample splitter shall have an even number of equal width chutes, not less than eight for coarse or combined aggregate, or twelve for fine aggregate. The chutes shall discharge alternately to each side of the splitter. For coarse and combined aggregates, the width of the individual chutes shall be approximately twice the largest size particle in the sample to be reduced. For dry fine aggregate in which the entire sample will pass the 3/8 in. (9.5 mm) sieve, the minimum width of the chutes shall be at least fifty percent larger than the largest particles in the sample with a maximum width of 3/4 in. (20 mm). The splitter shall be equipped with at least two receptacles (catch pans) to hold the two halves of the sample during splitting. It shall also be equipped with a hopper or straight-edge pan with a width equal to or slightly less than the overall width of the assembly of chutes, by which the sample may be fed at a controlled rate into the chutes. The splitter and accessories shall be designed to allow the sample to flow smoothly without restriction or loss of material. Mechanical splitters are commonly available in sizes adequate for aggregate having the largest particle size not over 1 1/2 in. (37.5 mm). Procedure 1. Place the original sample, or portion thereof, in the hopper or pan and uniformly distribute it from edge to edge being sure the sample appears homogenous (well- blended). Carefully introduce the sample into the chutes in a manner to allow the aggregate to flow freely through the openings and into the catch pans. Continue this procedure until the entire sample has been halved, being careful that catch pans do not overflow. 2. Remove the catch pans and set aside. Continue splitting one half of the material. Follow this procedure, being sure to split entire increments, until the desired test sample size is obtained. Retain the unused material until all desired tests are performed in case a retest is needed. Page 15 of 208 College of Engineering Education 2nd Floor, B&E Building Matina Campus, Davao City Telefax: (082) 296-1084 Phone No.: (082)300-5456/300-0647 Local 133 Note: Sometimes a significant amount of fines may be lost in the splitting process if the sample is extremely dry and the action of pouring the sample through the splitter chutes creates a large dust cloud, suspending the fines in the air above the splitter. If this is a serious concern, then add a small amount of water to the original sample and mix thoroughly before splitting the sample. The extra moisture will prevent many of the fines from becoming suspended in the air and drifting off. Remember to not add so much water that the moisture content ends up being at or greater than the SSD condition, in which case the mechanical splitting method would no longer be valid. In any case, be sure to perform the splitting procedure in a well-ventilated area while wearing a suitable dust mask. METHOD B -- MINIATURE STOCKPILE Apparatus Straight-edge scoop Shovel or trowel (for mixing the aggregate) Small sampling thief, small scoop, or spoon Procedure This method is for damp, fine aggregate only. 1. Place the field sample on a hard, clean, level surface where there will be no loss of material or contamination. Mix the sample by turning the entire sample over three times with a shovel. With the last turning, shovel the entire sample into a conical pile by depositing each shovelful on top of the preceding one. 2. Obtain a sample for each test to be performed by selecting at least five increments of material at random locations from the miniature stockpile using a sample thief, small scoop, or spoon. METHOD C -- QUARTERING Apparatus Straight-edged scoop Flat-edged shovel or trowel Broom or brush Alternate method only - canvas blanket measuring approximately 6 ft. x 8 ft (2 m by 2.5 m). Procedure 1. Place the original sample on a hard, clean, level surface. Mix the material thoroughly by turning the entire sample over with the shovel at least three times. With the last turning, shovel the entire sample into a conical pile by depositing each shovelful on top of the preceding one. Carefully flatten the conical pile to a uniform thickness and diameter by pressing down the apex with the shovel so that each quarter section of the resulting pile will contain the material originally in the pile. The pile diameter should be approximately four to eight times the thickness. 2. Divide the flattened pile into four equal quarters with the shovel or trowel. Remove two diagonally opposite quarters, including all fine material. Brush the cleared spaces clean. Successively mix and quarter the remaining material in the same fashion as the original sample. Continue this process until the desired quantity is obtained. Save the unused portion of the original field sample until all testing is completed in case a retest is needed. Page 16 of 208 College of Engineering Education 2nd Floor, B&E Building Matina Campus, Davao City Telefax: (082) 296-1084 Phone No.: (082)300-5456/300-0647 Local 133 METHOD C -- ALTERNATIVE As an alternative to Method B, when the floor surface is uneven, the field sample may be placed on a canvas blanket and mixed with a shovel, or by alternatively lifting each corner of the blanket and pulling the blanket over the sample toward the diagonally opposite corner causing the material to be rolled. Flatten and divide the pile as described in Method B, or if the surface beneath the blanket is too uneven, insert a stick or pipe dividing the pile into two equal parts. Remove the stick leaving a fold in the canvas between the sample halves. Slide the stick under the canvas blanket again at a right angle to the first division and dissecting the two halves of the sample through their centers. Lift the stick evenly from both ends dividing the sample into equal quarters. Remove two diagonal parts including the fine material and clean the area. Successively mix and quarter the remaining material until the desired sample size is obtained. Note: The quartering method is fairly time intensive and thus is generally used in situations where an adequate mechanical splitter is unavailable. Diligence and care is required to ensure that the samples obtained by quartering remain representative of the entire field sample. STANDARD TEST METHOD FOR TOTAL EVAPORABLE MOISTURE CONTENT OF AGGREGATE BY DRYING REFERENCED STANDARD: ASTM C566-96 / AASHTO T255-92 The moisture content in aggregate is used to determine the binder content for HMA during production of the mixture in a plant. The procedure requires that a known amount of aggregate be obtained, the aggregate heated to remove the moisture, and the percentage of moisture determined. Ovens, hot plates, heat lamps or microwave ovens are used for heating the sample. Apparatus Balance sensitive to 1.0 gram Source of Heat (oven, electric or gas hot plate, electric heat lamps, or microwave oven) Sample Container, suitable for method of heating Procedure 1. Weigh the sample and record the weight 2. Dry the sample until there is less than 0.1% change in weight over subsequent weighings. 3. Record the weight of the sample after the sample has cooled sufficiently not to damage the balance. Sample Problem: Given the following information, determine the percent of moisture content in the Sand and No. 57. Given: Page 17 of 208 College of Engineering Education 2nd Floor, B&E Building Matina Campus, Davao City Telefax: (082) 296-1084 Phone No.: (082)300-5456/300-0647 Local 133 Sand Weight of wet sample = 585 grams Weight of dry sample = 540 grams No. 57 Weight of wet sample = 1205 grams Weight of dry sample = 1190 grams Absorption Sand = 0.5% No. 57 = 0.9% 𝑊𝑡. 𝑜𝑓 𝑊𝑒𝑡 − 𝑊𝑡. 𝑜𝑓 𝐷𝑟𝑦 𝑀𝑜𝑖𝑠𝑡𝑢𝑟𝑒 𝐶𝑜𝑛𝑡𝑒𝑛𝑡 = × 100 − %𝐴𝑏𝑠. 𝑊𝑡. 𝑜𝑓 𝑑𝑟𝑦 Solution: Sand 585−540 𝑀𝑜𝑖𝑠𝑡𝑢𝑟𝑒 𝐶𝑜𝑛𝑡𝑒𝑛𝑡 = [( 540 )× 100] − 0.5% = 7.8% No. 57 1205 − 1190 𝑀𝑜𝑖𝑠𝑡𝑢𝑟𝑒 𝐶𝑜𝑛𝑡𝑒𝑛𝑡 = [( ) × 100] − 0.9 = 0.4% 1190 SIEVE ANALYSIS OF AGGREGATES REFERENCED STANDARD: ASTM C 136-84a, AASHTO T27-93, ASTM C33 / C33M-18, AASHTO T-27 Sieve analysis which is also known as gradation test is a laboratory test procedure that is an effective way of analyzing or determining the particle size distribution of coarse aggregates within a given sample. The process separates fine particles from coarser particles by passing the material through a number of sieves of different mesh sizes. Particle size distribution is defined using the mass and volume. Particle size determinations on large samples of aggregate are necessary to ensure that aggregates perform as intended for their specified use. Particle size distribution can affect a wide range of properties such as the strength of concrete, solubility of a mixture, surface area properties, and even their taste. This information can then be used to determine compliance with design and production requirements. Data can also be used to better understand the relationship between aggregates or blends and to predict trends during production. In this method, the soil is sieved through a set of sieves. A known mass of material is placed on top of a group of nested sieves (arranged in order of decreasing size from top to bottom) and mechanically shaken for a designated period of time. Particles move horizontally or vertically through sieve mesh. Sieves are wire screen having square openings. Size of these openings gives the sieves their name which is called sieve number. A sieve with a mesh opening of 4.75 mm is designated as 4.75 mm Sieve (Sieve number written on sieve). Similarly, a 600-micron sieve refers to a sieve which has a mesh opening of 0.600 mm. The two Page 18 of 208 College of Engineering Education 2nd Floor, B&E Building Matina Campus, Davao City Telefax: (082) 296-1084 Phone No.: (082)300-5456/300-0647 Local 133 major standards governing test sieves and appropriate sizes are ASTM E11 and ISO 565/3310-1, both of which specify parameters for aperture dimensions, mesh size, and statistical variations. Opening sizes and mesh diameters for test sieves are often duplicated between these two standards, making it easier to select the proper sieve size for your material. Sieve mesh opening sizes range from 5in (125mm) down to #635 (20µm). There are two methods in sieving analysis, the Manual Sieving Method and the Mechanical Sieving Method. Manual sieving method is carried out in places where there is no electricity and mainly used in, onsite differentiation among large and small particles. Mechanical sieving method is used in laboratories to assure the quality and this is the widely used method in present days. In mechanical sieving the method can be classified into two further groups depending on their sieving movement as horizontal movement sieving method and vertical movement sieving method. The vertical movement sieving method is also known as throw-action sieving and vibratory sieving methods. There are two ways or methods in weighing the material retained on each of the sieves, the Dry Sieve Analysis and Wet Sieve Analysis. Dry sieve analysis is considered mostly and here the testing particles (specimen) are in dry state. Wet sieve analysis is carried out after the dry sieve analysis. The purpose of the wet sieve analysis is to remove all the particles which are finer than 75 microns (of the last sieve) particles from the sample so that we arrive at the correct sieve analysis results. In performing sieve test one must consider and know the two categories of coarse grains soils. The portion of soil, which contains particle size bigger than 4.75 mm is retained on the sieve. This portion is called gravel fraction. Gravels, having grain size greater than 4.75 mm. The portion of soil, which contains particle size less than 4.75 mm passed through the sieve. This portion is called sand fraction. Sand, having grain size smaller than 4.75 mm. For gravel fractions we require sieves of sizes 80 mm, 40 mm, 20 mm, 10 mm and 4.75 mm. This set is called set of coarse sieves as it sieves coarser part of the coarse soils. Second set of sieves for sand fractions consists sieves of sizes 2 mm, 1 mm, 600 µ, 425 µ, 212 µ, 150 µ and 75 µ. If we didn’t mention, then 1 mm that is millimeter is equal to 1000 micrometer which we denote as letter micron. So 1 mm is equal to 1000 micron. So here 600 microns is actually 0.6 mm. This set of sieves is called set of fine sieves as it sieves finer part of the coarse soils. A test procedure for an effective determination of the particle size distribution of coarse aggregates. First, find a sample that ensure that aggregates perform as intended for their specified used. Make sure that sample is clean and no foreign materials, such as, feces etc. Then, collect the chosen sample. After that, transport it to the testing laboratory. When it arrived in the testing center, prepare it for testing. Lastly, test and record the result. Part of testing is weighing the material. There are two methods of weighing the sample. First is the Cumulative Method where each sieve fraction, beginning with the coarsest, is placed in a previously tared pan and weighed. This process is repeated until all fractions and the bottom pan have been added and weighed. This is a good time saving option since you don’t have to empty out or tare the pan on the scale. Second one is the Fractional Method where operator weighs the contents of each sieve fraction separately, waiting to discard material until the entire test is complete. The technician then calculates the amount retained and passing the sieve to the nearest 0.1% by total mass. In Cumulative Method, as each retained fraction is added, divide the cumulative mass by the total mass of the sample and multiply by 100 to calculate percent retained. Subtract the cumulative percent retained on a given sieve from 100 to calculate percent passing. (Cumulative Mass / Total Mass) × 100 = Cumulative % Retained 100 – (Cummulative % Retained) = Cumulative Retained Passing Page 19 of 208 College of Engineering Education 2nd Floor, B&E Building Matina Campus, Davao City Telefax: (082) 296-1084 Phone No.: (082)300-5456/300-0647 Local 133 On the other hand, Fractional Method, divide the mass retained on each sieve by the total and multiply by 100 to calculate percent retained. Calculate percent passing by subtracting the percent retained on the sieve nested beneath. [Fractional Mass (on each sieves) ÷ Total Mass] × 100 = (% Fractional Retained) (% Fractional Retained) – (% Retained on the sieve below) = (% Fractional Passing) In calculating the percentage of amount of soil retained on each sieve as weight of retained soil on the sieve divided by total weight of soil sample multiplied by 100. This way we know what percentage of the total weight is retained on a particular sieve. Percentage weight retained on the 1st sieves is w1 divided by W multiply by 100. For calculation purposes and to determine some important characteristics, we also calculate two values. First one is cumulative percentage retained. Now cumulative percentage retained of any sieve is percentage weight retained on that sieve plus all percentage weight retained on all the sieves above it. Cumulative percentage retained is the total percentage amount of soil which could not pass the particular sieve. In other words, this percent amount of soil has grain size greater than the sieve number. Second value we calculate is percentage finer, using which we plot a graph called particle size distribution curve. Percentage finer, as name suggests, is the percentage amount of soil which is finer, than a particular sieve. Testing tips: ❖ Avoid overloading sieves. ❖ Allow enough time on a sieve shaker or testing screen for complete separation. ❖ Watch for degradation. ❖ Consider reducing shaker time intervals or using a different method. ❖ Check sieves for wear, torn mesh or distorted openings regularly. ❖ Do not use tools or probes to dislodge trapped particles. ❖ Take care when transferring material to the tare weighing pan. ❖ Don’t forget to pre-dry the sample. Sample Problem: From the results of a sieve analysis, shown below, determine: a. The percent finer than each sieve and plot a grain size distribution curve. b. D10, D30, D60 from the grain-size distribution curve. c. The uniformity coefficient, Cu. and d. The coefficient of gradation, Cc. Table 1 Sieve Number Mass of soil retained on each sieve (g) 4 0 10 40 20 60 40 89 Page 20 of 208 College of Engineering Education 2nd Floor, B&E Building Matina Campus, Davao City Telefax: (082) 296-1084 Phone No.: (082)300-5456/300-0647 Local 133 60 140 80 122 100 210 200 56 Pan 12 Solution: a. Mass of Soil Cumulative percent Sieve Percent retained of Percent finer retained on retained on each sieve Number each sieve (%) (%) each sieve (g) (%) 4 0 0 0 100 10 40 5.49 5.49 94.51 20 60 8.23 13.72 86.28 40 89 12.21 25.93 74.07 60 140 19.20 45.13 54.87 80 122 16.74 61.87 38.13 100 210 28.81 90.68 9.32 200 56 7.68 98.36 1.64 Pan 12 1.64 100 0 729 Percent Retained = (Mass of Soil Retained/Total Mass of Soil) No. 4 Sieve No. 80 Sieve 0 122 % 𝑅𝑒𝑡𝑎𝑖𝑛𝑒𝑑 = 729 × 100% % 𝑅𝑒𝑡𝑎𝑖𝑛𝑒𝑑 = 729 × 100% % 𝑅𝑒𝑡𝑎𝑖𝑛𝑒𝑑 = 0% % 𝑅𝑒𝑡𝑎𝑖𝑛𝑒𝑑 = 16.74% No. 10 Sieve No. 100 Sieve 40 210 % 𝑅𝑒𝑡𝑎𝑖𝑛𝑒𝑑 = 729 × 100% % 𝑅𝑒𝑡𝑎𝑖𝑛𝑒𝑑 = 729 × 100% % 𝑅𝑒𝑡𝑎𝑖𝑛𝑒𝑑 = 5.49% % 𝑅𝑒𝑡𝑎𝑖𝑛𝑒𝑑 = 28.81% No. 20 Sieve No. 200 Sieve 60 210 % 𝑅𝑒𝑡𝑎𝑖𝑛𝑒𝑑 = 729 × 100% % 𝑅𝑒𝑡𝑎𝑖𝑛𝑒𝑑 = 729 × 100% % 𝑅𝑒𝑡𝑎𝑖𝑛𝑒𝑑 = 8.23% % 𝑅𝑒𝑡𝑎𝑖𝑛𝑒𝑑 = 7.67% No. 40 Sieve Pan 89 12 % 𝑅𝑒𝑡𝑎𝑖𝑛𝑒𝑑 = 729 × 100% % 𝑅𝑒𝑡𝑎𝑖𝑛𝑒𝑑 = 729 × 100% % 𝑅𝑒𝑡𝑎𝑖𝑛𝑒𝑑 = 12.21% % 𝑅𝑒𝑡𝑎𝑖𝑛𝑒𝑑 = 1.65% No. 60 Sieve 140 % 𝑅𝑒𝑡𝑎𝑖𝑛𝑒𝑑 = 729 × 100% % 𝑅𝑒𝑡𝑎𝑖𝑛𝑒𝑑 = 19.20% Page 21 of 208 College of Engineering Education 2nd Floor, B&E Building Matina Campus, Davao City Telefax: (082) 296-1084 Phone No.: (082)300-5456/300-0647 Local 133 Distribution Curve b. D10, D30, D60 from the grain-size distribution curve. c. The uniformity coefficient, Cu D10 = 0.15mm D30 = 0.17mm D60 = 0.28mm 𝐷60 0.28𝑚𝑚 𝐶𝑢 = = = 1.9 𝐷10 0.15𝑚𝑚 d. The coefficient of gradation, Cc 𝐷30 2 (0.17𝑚𝑚)2 𝐶𝑐 = = = 0.69 𝐷10 𝑥 𝐷60 0.28𝑚𝑚 𝑥 0.15𝑚𝑚 Page 22 of 208 College of Engineering Education 2nd Floor, B&E Building Matina Campus, Davao City Telefax: (082) 296-1084 Phone No.: (082)300-5456/300-0647 Local 133 Determination of Unit Weight of Aggregates There are two standard test methods in the determination for unit mass (weight) of an aggregate, the Loose Method and the Rodded Method, using ASTM C29. Procedure using Loose Method: Determine the weight of the empty bucket. Fill the bucket to overflowing by means of shovel or scoop. Exercise care to prevent segregation of the particle size of the sample. Level the surface of the aggregate using straightedge. Clean the outside of the bucket and remove excess dust and particles. Determine the mass of the bucket with aggregates, and record the data. Procedure using Rodded Method: Fill the bucket one-third full. Rod the layer of aggregate with 25 strokes of the tamping rod evenly distributed over the surface. Fill the bucket two-thirds full again and rod 25 times. Fill the bucket to over flowing and rod again for 25 times. After rodding, level the surface with a straightedge. Clean the surface of the bucket and remove excess materials. Determine the weight of the bucket with aggregates and record data. After using either of the two methods, unit weights are then calculated with the formula as follows: SPECIFIC GRAVITY & ABSORPTION DETERMINATION OF FINE AND COARSE AGGREGATES REFERENCED STANDARD: ASTM C127-88, AASHTO T85-91 Specific Gravity is the ratio of the weight of a given volume of aggregate to the weight of an equal volume of water. Absorption is a measure of the amount of water that an aggregate can absorb into its pore structure and is determined by the same test procedure. Aggregate is a granular material, such as sand, gravel, crushed stone, crushed hydraulic-cement concrete, or iron blast-furnace slag, used with a hydraulic cementing medium to produce either concrete or mortar. There are two types of aggregates: Fine Aggregates – are particles entirely passing the 4.75 mm (No. 4) sieve, and predominantly retained on the 75 µm sieves. Coarse Aggregates– are aggregates that will not pass through a sieve with 4.75 mm openings. Page 23 of 208 College of Engineering Education 2nd Floor, B&E Building Matina Campus, Davao City Telefax: (082) 296-1084 Phone No.: (082)300-5456/300-0647 Local 133 I. Specific Gravity Determination of Aggregates For fine aggregates, the specific gravity may be expressed as bulk oven dry (OD), bulk saturated surface dry (SSD), or apparent specific gravity (A). Let us first define the terms: A. Bulk Dry Specific Gravity – It is used to determine the specific gravity of a compacted aggregate by determining the ratio of its weight to the weight of an equal volume of water. In this test, the aggregates have to be: Dry (no water in sample). Saturated surface dry (SSD, water fills the HMA air voids). Submerged in water (underwater). B. Bulk Saturated Surface Dry Specific Gravity (SSD) – The ratio of the weight in air of a unit volume of aggregate, including the weight of water within the voids filled to the extent achieved by submerging in water for approximately 15-19 hours, to the weight in air of an equal volume of gas-free distilled water at a stated temperature. SSD (Saturated, Surface Dry) – This is a condition in which the aggregate has been soaked in water and has absorbed water into its pore spaces. The excess, free surface moisture removed so that the particles are still saturated, but the surface of the particle is essentially dry. C. Apparent Specific Gravity (Gsa) – It is the ratio of the weight in air of a unit volume of the impermeable portion of aggregate (does not include the permeable pores in aggregate) to the weight in air of an equal volume of gas-free distilled water at the stated temperature. D. Absorption (% Abs) – The increase in weight of aggregate due to water in the pores of the material, but not including water adhering to the outside surface of the particles. Specific Gravity Determination of Coarse Aggregates Perform calculations and determine values using the appropriate formula below. In these formulas, A = oven dry mass, B = SSD mass, and C = weight of SSD in water. A. Bulk Oven Dry Specific Gravity (OD) Page 24 of 208 College of Engineering Education 2nd Floor, B&E Building Matina Campus, Davao City Telefax: (082) 296-1084 Phone No.: (082)300-5456/300-0647 Local 133 B. Bulk Saturated Surface Dry Specific Gravity (SSD) C. Apparent Specific Gravity D. Absorption (% A) Materials needed (Coarse Aggregates) Water Tank Cloth Coarse Aggregates Tray Wire Basket Balance scale Procedures for Coarse Aggregates: 1. Dry the test sample to constant mass at a temperature of 110 ±5°C (230 ±9°F) and cool in air at room temperature for 1 to 3 hours. 2. Immerse the aggregate in water at room temperature for a period of 15 to 19 hours. 3. Place the empty basket into the water bath and attach to the balance. Inspect the immersion tank to ensure the water level is at the overflow outlet height. Tare the balance (set to 0) with the empty basket attached in the water bath. 4. Remove the test sample from the water and roll it in a large absorbent cloth until all visible films of water are removed. Wipe the larger particles individually. 5. Determine the SSD mass of the sample, and record this and all subsequent masses to the nearest 0.1 g or 0.1 percent of the sample mass, whichever is greater. Designate this mass as “B”. Page 25 of 208 College of Engineering Education 2nd Floor, B&E Building Matina Campus, Davao City Telefax: (082) 296-1084 Phone No.: (082)300-5456/300-0647 Local 133 6. Re-inspect the immersion tank to insure the water level is at the overflow outlet height. Immediately place the SSD test sample in the sample container and weigh it in water maintained at 23.0 ±1.7°C (73.4 ±3°F). Shake the container to release entrapped air before recording the weight. Designate this submerged weight as “C”. 7. Remove the sample from the basket. Ensure all material have been removed. Place in a container of known mass. 8. Dry the test sample to constant mass and cool in air at room temperature for 1 to 3 hours. Designate this mass as “A”. II. Specific Gravity and Absorption of Fine Aggregates Perform calculations and determine values using the appropriate formula below. In these formulas, where: A = Oven dry weight, B = SSD weight, C = Weight of SSD in water. A. Bulk Dry Specific Gravity B. Bulk Saturated Surface Dry Specific Gravity (SSD) C. Apparent Specific Gravity D. Absorption (% A) Materials needed (Fine Aggregates): Pycnometer Oven (Soil Testing) Distilled Water Tray Balance scale Fine aggregates Page 26 of 208 College of Engineering Education 2nd Floor, B&E Building Matina Campus, Davao City Telefax: (082) 296-1084 Phone No.: (082)300-5456/300-0647 Local 133 Procedure for Fine Aggregates: 1. Thoroughly mix the sample and reduce the sample if required. The sample size for this procedure is approximately 1000g of material passing the 4.75 mm sieve (mesh strainer). 2. Dry test samples to constant weight in an oven set at 230 ± 9°F (110 ± 5°C). Cool the sample at room temperature for 1 to 3 hours. After the cooling period, immerse the sand in water at room temperature for a period of 15 to 19 hours. This is the recommended procedure to eliminate the need to pour excess water from the sand prior to testing. The decantation process is time consuming and difficult, since great care must be taken to avoid pouring some of the sample along with the water. 3. Pour water from sample, avoiding loss of fines. Spread the sample on a flat, non-absorbent surface or tray. Stir the sample occasionally to assist in homogeneous drying. A current of warm air may be used to assist drying procedures; however, fine particles may be lost with this procedure if not careful. 4. Determine the SSD condition of the sand using the Cone Test. Throughout the process of drying in Step 3, test the sand for SSD condition using the cone method. Place the cone with the large diameter down on a glass plate. Fill cone to overflowing with drying sand. Lightly tamp the fine aggregate into the mold with 25 light drops of the tamper. Each drop should start about 1/5 in. above the top surface of the fine aggregate. Remove loose sand from base and carefully lift the mold vertically. If surface moisture is still present, the fine aggregate will retain the molded shape. When the sand achieves an SSD condition, the sand will slump. 5. Calibrate a specific gravity flask pycnometer by filling with water at 73.4 ± 3°F (23 ± 1.7°C) to the calibration line. Record this weight as the weight of the pycnometer filled with water to the nearest 0.1g. 6. Place the SSD sand into the pycnometer and fill with water (set at 73.4 ± 3°F (23 ± 1.7°C)) to 90% of pycnometer capacity. 7. Bring the pycnometer to the pycnometer-calibrated capacity with additional water. If bubbles prevent the proper filling of the pycnometer, adding a few drops of isopropyl alcohol is recommended to disperse the foam. Place the pycnometer in a water bath at the regulated temperature and allow the sample to equalize. 8. Determine the total weight of pycnometer, specimen, and water. Record the weight to the nearest 0.1g as weight of pycnometer with sample and water. Additional: The common errors during testing: Getting the aggregate SSD - neither wetter nor drier. Balance calibration errors. Ensuring that the change in height of the water when the sample is submerged is compensated for. Not allowing the sample to become fully saturated before testing for SSD and Immersed mass. Full drying to constant mass. Over-drying sensitive materials (driving off water that is actually part of the sample) either by poor temperature control, or the characteristics of the aggregate. Water temperature effects (its density). Purity of the water. Not allowing sufficient time for the balance to stabilize its reading. Removal of air bubbles when weighing under water. Loss of particles, due to poor technique (carelessness), insufficient washing at the beginning, friable particles. Having a sample where particles are less dense than water. Some or all thereof. Page 27 of 208 College of Engineering Education 2nd Floor, B&E Building Matina Campus, Davao City Telefax: (082) 296-1084 Phone No.: (082)300-5456/300-0647 Local 133 Problem : Determine calculations based on appropriate formula. A = Weight of oven dry sample B = Weight of Pycnometer with water only S = Weight of Saturated Surface Dry of sample C = Weight of Pycnometer with sample and water Bulk Specific Gravity (Gsb) Gsb = A / (B + S – C) Bulk SSD Specific Gravity (Gsb SSD) Gsb SSD = S / (B + A – C) Apparent Specific Gravity (Gsa) Gsa = A / (A + B – C) Absorption (% Abs) % Abs = [(S – A) / A] x 100 Trial A B S C B+S-C B+A-C S-A 1 497.1 670.7 500.05 938.2 232.55 229.6 2.95 2 496.7 679.6 499.77 938.2 241.17 238.1 3.07 3 496.5 671.6 499.61 938.2 233.01 229.9 3.11 Gsb SSD, S / Gsb, A / (B + Gsa, A / (B + % Abs., [(S – A) Trial (B + S – C) S – C) A – C)