BBA-OM201-Chapter 6 Managing Quality (2020) PDF
Document Details
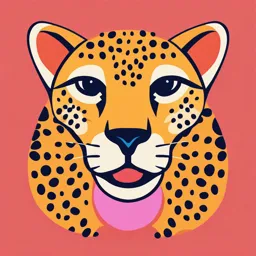
Uploaded by RapidAwe5466
2020
Jeff Heyl
Tags
Summary
These lecture notes cover the topic of managing quality in operations management. The document discusses quality as a strategy, and also explores how managing quality can improve profitability. It includes insights from various authors and experts like Heizer, Render, and Munson.
Full Transcript
Managing Quality 6 PowerPoint presentation to accompany Heizer, Render, Munson Operations Management, Thirteenth Edition, Global Edition Principles of Operations Management, Eleventh Edition PowerPoint slides by Jeff Heyl...
Managing Quality 6 PowerPoint presentation to accompany Heizer, Render, Munson Operations Management, Thirteenth Edition, Global Edition Principles of Operations Management, Eleventh Edition PowerPoint slides by Jeff Heyl Copyright © 2020 Pearson Education Ltd. All Rights Reserved. 6-1 Managemen Managin EX: What's the year the recent edition released? =2015 NO CHEAT SHEET ! Outline ► Global Company Profile: Arnold Palmer Hospital ► Quality and Strategy ► Defining Quality ► Determinants of Product & Service Quality ► Cost of Quality ► Total Quality Management ► Tools of TQM ► The Role of Inspection Copyright © 2020 Pearson Education Ltd. All Rights Reserved. 6-2 Managing Quality Provides a Competitive Advantage Arnold Palmer Hospital ► Delivers over 14,000 babies annually ► Virtually every type of quality tool is employed ► Continuous improvement ► Employee empowerment ► Benchmarking ► Just-in-time (JIT) ► Quality tools Copyright © 2020 Pearson Education Ltd. All Rights Reserved. 6-3 Learning Objectives When you complete this chapter you should be able to: 6.1 Define quality and TQM 6.2 Describe the ISO international quality management system standards 6.3 Explain Six Sigma 6.4 Explain how benchmarking is used in TQM 6.5 Use the seven tools of TQM Copyright © 2020 Pearson Education Ltd. All Rights Reserved. 6-4 Strategies for Competitive Advantage 1. Differentiation – better, or at least different 2. Cost leadership – cheaper 3. Response – more responsive Copyright © 2020 Pearson Education Ltd. All Rights Reserved. 6-5 Quality and Strategy ► Managing quality supports differentiation, low cost, and response strategies ► Quality helps firms increase sales and reduce costs ► Building a quality organization is a demanding task Copyright © 2020 Pearson Education Ltd. All Rights Reserved. 6-6 Two Ways Quality Improves Profitability Figure 6.1 Sales Gains via Improved response Flexible pricing Improved reputation Improved Increased Quality Profits Reduced Costs via Increased productivity Lower rework and scrap costs Lower warranty costs Copyright © 2020 Pearson Education Ltd. All Rights Reserved. 6-7 The Flow of Activities win the customer's minds Organizational Practices Leadership, Mission statement, Effective operating procedures, Staff support, Training Yields: What is important and what is to be accomplished Quality Principles Customer focus, Continuous improvement, Benchmarking, Just-in-time, Tools of TQM Yields: How to do what is important and to be accomplished Employee Fulfillment employee motivation Empowerment, Organizational commitment Yields: Employee attitudes that can accomplish what is important Customer Satisfaction Winning orders, Repeat customers Figure 6.2 Yields: An effective organization with a competitive advantage Copyright © 2020 Pearson Education Ltd. All Rights Reserved. 6-8 Defining Quality W. G An operations manager’s objective is to build a total quality management system that identifies and satisfies customer needs Copyright © 2020 Pearson Education Ltd. All Rights Reserved. 6-9 meet the strategical need of the customer Defining Quality The totality of features and characteristics of a product or service that bears on its ability to satisfy stated or implied needs American Society for Quality Understanding customer needs is fundamental for effective management. However, not all needs are explicitly communicated by customers. Implied needs are those that are not directly stated but can be inferred from the customer's behavior, context, or underlying motivations. Copyright © 2020 Pearson Education Ltd. All Rights Reserved. 6 - 10 Different Views of Quality user view : how to compare with the standard ► User based: better performance, more features design process > - ► Manufacturing based: conformance to standards, making it right the first time ► Product based: specific and measurable attributes of the product Copyright © 2020 Pearson Education Ltd. All Rights Reserved. 6 - 11 - compare with competitor products Determinants of Product Quality & HBR quality o tangible products Performance refers to a product’s primary operating characteristics Features refers to secondary aspect of performance and those characteristics that supplement the basic functioning Reliability reflects probability of a product malfunctioning or failing within a specified time period (mean time to first failure, mean time between failures) Conformance refers to the degree to which a product’s design and operating characteristics meet established standards or specifications (defect rates, service calls) Durability refers to the amount of use one gets from a product before it deteriorates or breaks down (a measure of product life) product life how many years Serviceability includes speed, courtesy, competence, service standard, and the ease of repair and installation (mean time to repair, timeliness, complaint-handling procedures) Aesthetics involves how a product looks, feels, sounds, tastes, or smells (a subjective dimension based on individual preference) Perceived quality is inferred about quality rather than reality itself from various tangible and intangible aspects of a product i.e. reputation, images, advertising and brand names Source: David A. Garvin (1987). Competing on the Eight Dimensions of Quality. Harvard Business Review. The November 1987 Issue. Copyright © 2020 Pearson Education Ltd. All Rights Reserved. 6 - 12 Determinants of Service Quality consistency of performance Table 6.6 - Reliability involves consistency of performance and dependability Responsiveness concerns the willingness or readiness of employees to provide service Competence means possession of the required skills and knowledge to perform the service Access involves approachability and ease of contact service and sign to # Courtesy involves politeness, respect, consideration, and friendliness emphasize on Communication means keeping customers informed and listening to them listening to customers Credibility involves trustworthiness, believability, and honesty Security is the freedom from danger, risk, or doubt Understanding/knowing the customer involves making the effort to understand the customer's needs Tangibles include the physical evidence of the service Copyright © 2020 Pearson Education Ltd. All Rights Reserved. 6 - 13 Outline ► Global Company Profile: Bechtel Group ► The Importance of Project Management ► Project Planning ► Project Scheduling ► Project Controlling ► Project Management Techniques: CPM ► Determining the Project Schedule Copyright © 2017 Pearson Education Ltd 3-2 Critical Path and Slack Times for Milwaukee Paper Figure 3.16 A C F 0 2 2 4 4 7 0 2 2 4 10 13 2 2 3 Start Slack = 0 Slack = 0 E Slack = 6 H 0 0 4 8 13 15 0 0 4 8 13 15 0 4 2 B D Slack = 0 G Slack = 0 0 3 3 7 8 13 1 4 4 8 8 13 3 4 5 Slack = 1 Slack = 1 Slack = 0 There are 4 paths (1) A-C-F-H (2) A-C-E-G-H (3) A-D-G-H (4) B-D-G-H Copyright © 2017 Pearson Education Ltd There is 1 critical path: A-C-E-G-H 3 - 66 Implications of Quality 1. Company reputation ► Perception of new products ► Employment practices ► Supplier relations 2. Product liability ► Reduce risk 3. Global implications ► Improved ability to compete Copyright © 2020 Pearson Education Ltd. All Rights Reserved. 6 - 14 Malcolm Baldrige National Quality Award ► Established in 1988 by the U.S. government ► Designed to promote TQM practices ► Any types of organization can apply for assessment. Copyright © 2020 Pearson Education Ltd. All Rights Reserved. 6 - 15 Baldrige Criteria Applicants are evaluated on: The US government use 7 factors CATEGORIES POINTS ① Leadership 120 ② Strategic Planning 85 ③ Customer Focus 85 ⑪ Measurement, Analysis, and Knowledge 90 Management ⑤ Workforce Focus 85 ⑥ Operations Focus 3 how you take care of your employee 85 ⑦ Results 450 1000 Copyright © 2020 Pearson Education Ltd. All Rights Reserved. 6 - 16 International relation quality management ISO 9000 International Quality Management System Standards ► International recognition ► Encourages quality management procedures, detailed documentation, work instructions, and recordkeeping ► 2015 revision gives greater emphasis to risk-based thinking ► Over 1.6 million certifications in 201 countries ► Critical for global business Copyright © 2020 Pearson Education Ltd. All Rights Reserved. 6 - 17 ISO 9000: Quality Management System ► Quality Management Principles (QMP) QMP1 – Customer Focus QMP2 – Leadership QMP3 – Engagement of People QMP4 – Process Approach QMP5 – Improvement QMP6 – Evidence-based Decision Making QMP7 – Relationship Management ↳ use the data when making decision about quality Copyright © 2020 Pearson Education Ltd. All Rights Reserved. 6 - 18 A Comparison between Baldrige Award and ISO 9000 Criteria of Malcolm Baldrige Award Quality Management Principles of ISO 9001 Leadership QMP2 – Leadership Strategic Planning - Customer Focus QMP1 – Customer Focus Measurement, Analysis, and Knowledge QMP6 – Evidence-based Decision Management Making Workforce Focus QMP3 – Engagement of People Operations Focus QMP4 – Process Approach Results - QMP5 – Improvement QMP7 – Relationship Management Copyright © 2020 Pearson Education Ltd. All Rights Reserved. 6 - 19 ISO 9000: Family of Standards ► ISO 9000:2015 QUALITY MANAGEMENT SYSTEMS — FUNDAMENTALS AND VOCABULARY ► ISO 9001:2015 QUALITY MANAGEMENT SYSTEMS — REQUIREMENTS ► ISO 9004:2018 QUALITY MANAGEMENT — QUALITY OF AN ORGANIZATION — GUIDANCE TO ACHIEVE SUSTAINED SUCCESS ► ISO 19011:2018 GUIDELINES FOR AUDITING MANAGEMENT SYSTEMS Remark: ISO 9000, ISO 9001 and related ISO quality management standards are based on the seven Quality Management Principles (7QMP) Copyright © 2020 Pearson Education Ltd. All Rights Reserved. 6 - 20 * Grow Om ISO 9001: Quality Management Systems - Requirements ISO 9001: 1987 (first edition) train the people to work the same way to reduce variety Focus on conforming to procedures rather than the management process as a whole. ISO 9001: 1994 follow their heart & do it accordingly , a lot of variety in product Place a greater concentration on quality assurance through preventive actions. ISO 9001: 2000 quality management system quality is the management : system Demand to have management system effectiveness via process performance measures. ISO 9001: 2008 use the same standard & structure and Design the document to work in congruence with ISO’s other management standards such as ISO 14001. ISO 9001: 2015 (current edition) risk-based thinking and detect opportunities Focus on risk-based thinking and risk management. An emphasis on leadership and increased flexibility. Regarding documentation are notable. Copyright © 2020 Pearson Education Ltd. All Rights Reserved. 6 - 21 shall must comply with ISO 9001: Quality Management Systems - Requirements * gree on ISO 9001: consisting of 11 clauses Clause 0: Introduction Clause 1: Scope Clause 2: References Clause 3: Terms and Definitions Clause 4: Context of the organization Clause 5: Leadership and commitment Planning Clause 6: Planning for the QMS & resource Clause 7: Support & resource management manage Clause 8: Operational planning and control ment Clause 9: Performance evaluation Clause 10: Improvement Copyright © 2020 Pearson Education Ltd. All Rights Reserved. 6 - 22 1 Question in this slide Costs of Quality ► Prevention costs - reducing the potential for defects such as training cost, design cost, maintenance cost price pay for appraisal ► Appraisal costs - evaluating products, parts, and services such as testing cost, inspecting cost, calibrating cost pay for repair costs ► Internal failure costs - producing defective parts or service before delivery such as repair cost, rework cost, downgrade product ► External failure costs - O defects discovered after delivery such as replacement cost, warranty, lawsuit > cannot detect by themselves - Copyright © 2020 Pearson Education Ltd. All Rights Reserved. ↳ customer detect defect 6 - 23 Costs of Quality Total Total Cost Cost External Failure Internal Failure Prevention Appraisal Quality Improvement Copyright © 2020 Pearson Education Ltd. All Rights Reserved. 6 - 24 Strategic Quality Planning Quality as a Strategy Costs of Quality Prevention Costs Appraisal Costs Failure Costs Internal External Lundvall–Juran Model Copyright © 2020 Pearson Education Ltd. All Rights Reserved. 4- 25 6 - 25 2 question in the Exam who is initiator of this thought Leaders in Quality be able to classify if you want to improve the quality you need to improve the management related to ↑ TABLE 6.1 LEADER W. Edwards Deming Leaders in the Field of Quality Management PHILOSOPHY/CONTRIBUTION Deming insisted management accept responsibility for quality father of quality building good systems. The employee cannot produce management products that on average exceed the quality of what the process is capable of producing. His 14 points for implementing quality improvement are presented in this chapter. Joseph M. Juran A pioneer in teaching the Japanese how to improve quality, ↳ define the Juran believed strongly in top-management commitment, word quality support, and involvement in the quality effort. He was also a if its fit for use believer in teams that continually seek to raise quality standards. its Juran varies from Deming somewhat in focusing on the a quality = product customer and defining quality as fitness for use, not necessarily the written specifications. Copyright © 2020 Pearson Education Ltd. All Rights Reserved. 6 - 26 Leaders in Quality TABLE 6.1 Leaders in the Field of Quality Management LEADER PHILOSOPHY/CONTRIBUTION Armand Feigenbaum His 1961 book Total Quality Control laid out 40 steps to ↳ proposed TQC quality improvement processes. He viewed quality not as a ↳ introduce cross- set of tools but as a total field that integrated the processes of a functional teamwork company. His work in how people learn from each other’s to improve system successes led to the field of cross-functional teamwork. Philip B. Crosby Quality Is Free was Crosby’s attention-getting book published in 1979. Crosby believed that in the traditional trade-off between ↳ most successful promote the the cost of improving quality and the cost of poor quality, the cost - concept of poor quality is understated. The cost of poor quality should of design > - include all of the things that are involved in not doing the job believe in zero defect right the first time. Crosby coined the term zero defects and - if you design well and stated, “There is absolutely no reason for having errors or put all effort on the first defects in any product or service.” trial there is no reason to do it many times Copyright © 2020 Pearson Education Ltd. All Rights Reserved. 6 - 27 2-3 questions Deming's Fourteen Points ↳ believe that the of is variation he enemy quality TABLE 6.2 Deming's 14 Points for Implementing Quality Improvement 1. Create consistency of purpose 2. Lead to promote change 3. Build quality into the product; stop depending on inspections to catch problems 4. Build long-term relationships based on performance instead of awarding business on price foresee relationship between supplier & buyer 5. Continuously improve product, quality, and service 6. Start training 7. Emphasize leadership Copyright © 2020 Pearson Education Ltd. All Rights Reserved. 6 - 28 Deming's Fourteen Points TABLE 6.2 Deming's 14 Points for Implementing Quality Improvement 8. Drive out fear 9. Break down barriers between departments 10. Stop haranguing workers (forceful and lengthy lecture or criticism) 11. Support, help, and improve 12. Remove barriers to pride in work (Allow everyone to take pride in their work without being rated or compared) 13. Institute a vigorous program of education and self-improvement 14. Put everyone in the company to work on the transformation Copyright © 2020 Pearson Education Ltd. All Rights Reserved. 6 - 29 Ethics and Quality Management ► Operations managers must deliver healthy, safe, quality products and services product must be tested first before launching. ► Poor quality risks: injuries, lawsuits, recalls, and regulation violations ► Ethical conduct must dictate response to problems ► All stakeholders must be considered Copyright © 2020 Pearson Education Ltd. All Rights Reserved. 6 - 30 Total Quality Management ► Encompasses entire organization from supplier to customer ► Stresses a commitment by management to have a continuing companywide drive toward excellence in all aspects of products and services that are important to the customer Copyright © 2020 Pearson Education Ltd. All Rights Reserved. 6 - 31 Related Concepts of TQM 1) Continuous improvement 2) Six Sigma 3) Employee empowerment 4) Benchmarking 5) Just-in-time (JIT) 6) Knowledge of TQM tools Copyright © 2020 Pearson Education Ltd. All Rights Reserved. 6 - 32 Continuous Improvement e ► Never-ending process of continuous improvement ► Covers people, equipment, suppliers, materials, procedures ► Every operation can be improved Copyright © 2020 Pearson Education Ltd. All Rights Reserved. 6 - 33 called "Deming" cycle-a japanese cycle Shewhart's PDCA Model Figure 6.3 4. Act 1. Plan Implement Identify the the plan, pattern and document make a plan 3. Check 2. Do Is the plan Test the working? plan Copyright © 2020 Pearson Education Ltd. All Rights Reserved. 6 - 34 Continuous Improvement > injapanese also called "Kaizen" - ► Kaizen describes the ongoing process of unending improvement (incremental quality improvement) ► TQM and zero defects also used to describe continuous improvement ↳ in order to achieve zero defect points Copyright © 2020 Pearson Education Ltd. All Rights Reserved. 6 - 35 anwansves * kaizen kaikaku , Quality Improvement ↳ japanese method Performance/ Impact/ Quality level address the new example when demand & make - Steve job introduced ↑ adjustmeas Iphone , he use to breakthrough Pongoing arment Time Copyright © 2020 Pearson Education Ltd. All Rights Reserved. 6 - 36 1 question in final exam what are the differences between Kaizen , Kaikaku and Kakushin Quality Improvement KAIZEN KAIKAKU KAKUSHIN Change + Good = Change for Better, Change + Revolutionary = Radical New + Revolutionary = Continuous Improvement Change, Breakthrough Improvement Transformational Innovation, Reform, Renewal Identify waste in the processes Applied when a significant impact is Applied when radical, disruptive and remove it. Repeat it needed. innovation is needed. continuously until it nears Involves a radical change such as Substantially changes the product perfection. new production technology, a new or working processes, rupturing the Focus the work on where value is piece of equipment or new existing principles. created (shop floor). materials. Impacts the current established Improvements take days or weeks A specialized team, such as market. to be delivered. engineering, makes the Improvement actions demand Delivers high quality at a low cost. improvement. intellectual effort, high curiosity, and Requires real-time, good-quality Improvements take months or years intensive research in research, data for identification and resolution to be delivered. development and innovation (RD&I) of problems. Delivers high quality at a higher areas. cost. Improvements take months or years Requires access to recent historical to be delivered. data and analytics tools. Delivers innovative or disruptive products or services. Requires good historical data and careful agile planning to minimize uncertainty and risk. (1) People’s mindsets, behaviors, and discipline. (2) Strong work processes for capturing, valuing and tracking initiatives. Copyright(3) ToolsPearson © 2020 which help accurate Education Ltd.data-driven decision-making. All Rights Reserved. 6 - 37 reduce the process of variation - as much as possible Six Sigma concept six sigma !!! ↳ must have less than 3 4 Two meanings. ► defect per million or will not be qualified as six sigma ► Statistical definition of a process that is 99.9997% capable,> 3.4 defects per You can - control your - million opportunities (DPMO) quality to be ↳ number of rejects gg 99/ ► A program designed to reduce defects,. lower costs, save time, and improve customer satisfaction ► A comprehensive system for achieving and sustaining business success Copyright © 2020 Pearson Education Ltd. All Rights Reserved. 6 - 38 Definitions ▶s – Standard Deviation, a measure of variability ▶Six Sigma – A quality improvement philosophy that focuses on eliminating defects through reduction of variation in a new muuuuuu process ▶Defect – A measurable outcome that is not within acceptable (specification) limits Copyright © 2020 Pearson Education Ltd. All Rights Reserved. 6 - 39 - very close to Six Sigma Program use "DMAIC" ► Originally developed by Motorola, adopted and enhanced by Honeywell and GE ► Highly structured approach to process improvement 6s ► A strategy ► A discipline – DMAIC ► A set of 7 tools Copyright © 2020 Pearson Education Ltd. All Rights Reserved. 6 - 40 Six Sigma Model 1. Defines the project’s purpose, scope, and outputs, then identifies the required process information keeping in mind the customer’s definition of quality 2. Measures the process and collects data 3. Analyzes the data, ensuring repeatability and reproducibility DMAIC Approach 4. Improves by modifying or redesigning existing processes and procedures 5. Controls the new process to make sure performance levels are maintained Copyright © 2020 Pearson Education Ltd. All Rights Reserved. 6 - 41 Implementing Six Sigma ► Emphasize defects per million opportunities as a standard metric ► Provide extensive training ► Focus on top management leadership (Champion) ► Create qualified process improvement experts (Black Belts, Green Belts, etc.) - cannot be 100 % complete ► Set stretch objectives: ambitious and challenging objectives that individuals or teams set, usually exceeding their current abilities and resources. It's a type of objectives that aren't meant to be 100% completed. Copyright © 2020 Pearson Education Ltd. All Rights Reserved. 6 - 42 Implementing Six Sigma ► Emphasize defects per million opportunities as a standard metric ► Provide extensive training ► Focus on top management leadership (Champion) ► Create qualified process improvement experts (Black Belts, Green Belts, etc.) This cannot be accomplished without a ► Set stretch objectives major commitment from top level management Copyright © 2020 Pearson Education Ltd. All Rights Reserved. 6 - 43 Employee Empowerment ► Getting employees involved in product and process improvements ► 85% of quality problems are due to materials and process ► Techniques 1) Build communication networks that include employees 2) Develop open, supportive supervisors 3) Move responsibility to employees 4) Build a high-morale organization 5) Create formal team structures: Quality circles Copyright © 2020 Pearson Education Ltd. All Rights Reserved. 6 - 44 Employee Empowerment : Quality Circles ► Group of employees who meet regularly to solve problems ► Trained in planning, problem solving, and statistical methods ► Often led by a facilitator, not a leader or a manager ► Very effective when done properly Copyright © 2020 Pearson Education Ltd. All Rights Reserved. 6 - 45 Benchmarking Selecting best practices in the same industry to use as a standard for performance 1. Determine what to benchmark 2. Form a benchmark team 3. Identify benchmarking partners 4. Collect and analyze benchmarking information 5. Take action to match or exceed the benchmark Copyright © 2020 Pearson Education Ltd. All Rights Reserved. 6 - 46 Benchmarking : Best Practices for Resolving Customer Complaints Table 6.3 BEST PRACTICE JUSTIFICATION Make it easy for clients to complain It is free market research Respond quickly to complaints It adds customers and loyalty Resolve complaints on first contact It reduces cost Use computers to manage complaints Discover trends, share them, and align your services Recruit the best for customer service It should be part of formal training and jobs career advancement Copyright © 2020 Pearson Education Ltd. All Rights Reserved. 6 - 47 Internal Benchmarking ▶When the organization is large enough ▶Data more accessible ▶Can and should be established in a variety of areas Copyright © 2020 Pearson Education Ltd. All Rights Reserved. 6 - 48 Just-in-Time (JIT) ► 'Pull' system of production scheduling including supply management ► Production only when signaled ► Allows reduced inventory levels ► Inventory costs money and hides process and material problems ► Encourages improved process and product quality Copyright © 2020 Pearson Education Ltd. All Rights Reserved. 6 - 49 You have no intention to hide it no production stop Just-in-Time (JIT) Lean inventory is the inventory at the minimum level necessary to keep operations running TABLE 16.2 LEAN INVENTORY TACTICS Use a pull system to move inventory Reduce lot sizes Develop just-in-time delivery systems with suppliers Deliver directly to point of use Perform to schedule Reduce setup time Use group technology Copyright © 2020 Pearson Education Ltd. All Rights Reserved. 6 - 50 Just-in-Time (JIT) Reduce Inventory ▶Reducing inventory uncovers the "rocks" ▶Problems are exposed ▶Ultimately there will Inventory be virtually no inventory and no problems ▶Shingo says "Inventory is evil" Copyright © 2020 Pearson Education Ltd. All Rights Reserved. 6 - 51 Just-in-Time (JIT) Reduce Variability take action > solve - quality problem Inventory level Process Scrap downtime Setup Quality time problems Late deliveries Figure 16.3 Copyright © 2020 Pearson Education Ltd. All Rights Reserved. 6 - 52 Just-in-Time (JIT) Reduce Variability Inventory level Process Scrap downtime Setup Quality time problems Late deliveries Figure 16.3 Copyright © 2020 Pearson Education Ltd. All Rights Reserved. 6 - 53 Just-in-Time (JIT) Reduce Variability Inventory level No scrap Quality problems Setup removed time reduced Process No late downtime deliveries removed Figure 16.3 Copyright © 2020 Pearson Education Ltd. All Rights Reserved. 6 - 54 Just-in-Time (JIT) Relationship to quality: ► JIT cuts the cost of quality ► JIT improves quality ► Better quality means less inventory and better, easier-to- employ JIT system Copyright © 2020 Pearson Education Ltd. All Rights Reserved. 6 - 55 Knowledge of TQM Tools (Logical Order) Big Picture Data Data Analysis Problem Prioritization Collection Identification Flowchart Check Histograms Cause- Pareto (Process Sheets and-Effect Chart Diagram) Diagram Scatter Diagram Control Charts Copyright © 2020 Pearson Education Ltd. All Rights Reserved. 6 - 56 Seven Tools of TQM (a) Flowchart (Process Diagram): A chart that describes the steps in a process Figure 6.6 Copyright © 2020 Pearson Education Ltd. All Rights Reserved. 6 - 57 MRI Flowchart 1. Physician schedules MRI 7. If unsatisfactory, repeat 2. Patient taken to MRI 8. Patient taken back to room 3. Patient signs in 9. MRI read by radiologist 4. Patient is prepped 10. MRI report transferred to 5. Technician carries out MRI physician 6. Technician inspects film 11. Patient and physician discuss 8 80% 1 2 3 4 5 6 7 11 9 10 20% Copyright © 2020 Pearson Education Ltd. All Rights Reserved. 6 - 58 10 work stations from 1st to last Harley-Davidson’s Assembly Flowchart Frame tube Frame-building Frame Hot-paint bending work cells machining frame painting THE ASSEMBLY LINE TESTING Engines and Incoming parts transmissions 28 tests Arrive on a JIT schedule from a Air cleaners Oil tank work cell 10-station work cell in Milwaukee Fluids and mufflers Shocks and forks In less than 3 Fuel tank work cell Handlebars hours, 450 parts and subassemblies Wheel work cell Fender work cell go into a Harley Roller testing motorcycle Crating Copyright © 2020 Pearson Education Ltd. All Rights Reserved. 6 - 59 Seven Tools of TQM (b) Check Sheet: An organized method of recording data collect data about defects// classify defect types Hour Defect 1 2 3 4 5 6 7 8 A /// / / / / /// / B // / / / // /// C / // // //// Figure 6.6 Copyright © 2020 Pearson Education Ltd. All Rights Reserved. 6 - 60 histogram show frequency Seven Tools of TQM use basic mathematics to classify data set (c) Histogram: A distribution showing the frequency of occurrences of a variable Distribution The "normal distribution" is Frequency the most commonly used distribution in statistics. A variable that is normally distributed has a histogram that is bell-shaped, with only one peak, and is symmetric around the mean. Repair time (minutes) Figure 6.6 Copyright © 2020 Pearson Education Ltd. All Rights Reserved. 6 - 61 Seven Tools of TQM > - tool to identify relationship between 2 (d) Scatter Diagram: A graph of the variables. value of one variable vs. another variable Productivity Absenteeism Figure 6.6 Copyright © 2020 Pearson Education Ltd. All Rights Reserved. 6 - 62 Seven Tools of TQM (d) Scatter Diagram: Four patterns 2 relationships strong relationship moderate relationship no relationship strong non-linear Copyright © 2020 Pearson Education Ltd. All Rights Reserved. 6 - 63 Seven Tools of TQM (e) Statistical Process Control Chart: A chart with time on the horizontal axis to plot values of a statistic if measurement between upper and lower then its ok , but if it goes beyond the limit then there must be issue in variation Upper control limit Target value Lower control limit Time Figure 6.6 Copyright © 2020 Pearson Education Ltd. All Rights Reserved. 6 - 64 Statistical Process Control The objective of a process control system is to provide a statistical signal when assignable causes of variation are present Copyright © 2020 Pearson Education Ltd. All Rights Reserved. 6 - 65 Statistical Process Control (SPC) ► Uses statistics and control charts to tell when to take corrective action => find the root cause ► Drives process improvement ► Four key steps ► Measure the process ► When a change is indicated, find the assignable cause ► Eliminate or incorporate the cause ► Restart the revised process Copyright © 2020 Pearson Education Ltd. All Rights Reserved. 6 - 66 Statistical Process Control (SPC) ► Variability is inherent in every process ► Natural or common causes ► Special or assignable causes ► Provides a statistical signal when assignable causes are present we don't try to eliminate common causes of variation ► Quickens appropriate actions to eliminate assignable causes Copyright © 2020 Pearson Education Ltd. All Rights Reserved. 6 - 67 Natural Variations ► Also called common causes ► Affect virtually all production processes ► Expected amount of variation ► Output measures follow a probability distribution ► For any distribution there is a measure of central tendency and dispersion ► If the distribution of outputs falls within acceptable limits, the process is said to be "in control" Copyright © 2020 Pearson Education Ltd. All Rights Reserved. 6 - 68 Assignable Variations ► Also called special causes of variation ► Generally this is some change in the process ► Variations that can be traced to a specific reason ► The objective is to discover when assignable causes are present ► Eliminate the bad causes ► Incorporate the good causes Copyright © 2020 Pearson Education Ltd. All Rights Reserved. 6 - 69 Patterns in Control Charts Upper control limit Target no trend no point go beyond the limit Lower control limit Normal behavior. Process is "in control." Figure S6.7 Copyright © 2020 Pearson Education Ltd. All Rights Reserved. 6 - 70 Patterns in Control Charts Upper control limit Target Lower control limit One plot out above (or below). Investigate for cause. Process is "out of control." Figure S6.7 Copyright © 2020 Pearson Education Ltd. All Rights Reserved. 6 - 71 Patterns in Control Charts Upper control limit Target Lower control limit Trends in either direction, 5 points. Investigate for cause of progressive change. Figure S6.7 Copyright © 2020 Pearson Education Ltd. All Rights Reserved. 6 - 72 Patterns in Control Charts Upper control limit Target Lower control limit Two plots very near lower (or upper) control. Investigate for cause. Figure S6.7 Copyright © 2020 Pearson Education Ltd. All Rights Reserved. 6 - 73 Patterns in Control Charts Upper control limit Target Lower control limit Run of 5 above (or below) central line. Investigate for cause. Figure S6.7 Copyright © 2020 Pearson Education Ltd. All Rights Reserved. 6 - 74 Patterns in Control Charts Upper control limit Target Lower control limit Erratic behavior. Investigate. Figure S6.7 Copyright © 2020 Pearson Education Ltd. All Rights Reserved. 6 - 75 Control Charts Plot the percentage of free throws missed 40% Upper control limit Coach’s 20% target value Lower 0% | | | | | | | | | control 1 2 3 4 5 6 7 8 9 limit Game number Figure 6.8 Copyright © 2020 Pearson Education Ltd. All Rights Reserved. 6 - 76 Seven Tools of TQM (f) Cause-and-Effect Diagram (Fishbone Diagram): A tool that identifies process elements (causes) that may effect an outcome Cause Materials Methods Effect Manpower Machinery Figure 6.6 Copyright © 2020 Pearson Education Ltd. All Rights Reserved. 6 - 77 Cause-and-Effect Diagrams Material Method (ball) (shooting process) Grain/Feel Aiming point (grip) Size of ball Air pressure Bend knees Hand position Balance Lopsidedness Follow-through Missed Training free-throws Rim size Conditioning Motivation Rim height Consistency Rim alignment Backboard stability Concentration Machine Manpower (hoop & (shooter) Figure 6.7 backboard) Copyright © 2020 Pearson Education Ltd. All Rights Reserved. 6 - 78 Seven Tools of TQM (g) Pareto Chart: A graph to identify and plot problems or defects in descending order of frequency Frequency Percent A B C D E Figure 6.6 Copyright © 2020 Pearson Education Ltd. All Rights Reserved. 6 - 79 5 question in the exam Pareto Charts Copyright © 2020 Pearson Education Ltd. All Rights Reserved. 6 - 80 Pareto Charts Rule of Thumb : Data for October cutoff at 80 % – 100 70 – – 93 – 88 60 – 54 Cumulative percentage Frequency (number) 50 – – 72 40 – Number of 30 – occurrences 20 – 12 10 – 4 3 2 0 – Room svc Check-in Pool hours Minibar Misc. 72% 16% 5% 4% 3% Causes and percentage of the total Copyright © 2020 Pearson Education Ltd. All Rights Reserved. 6 - 81 Inspection ► Involves examining items to see if an item is good or defective ► Detect a defective product ► Does not correct deficiencies in process or product ► It is expensive ► Issues ► When to inspect ► Where in process to inspect Copyright © 2020 Pearson Education Ltd. All Rights Reserved. 6 - 82 Remember this slide for final exam When and Where to Inspect 1. At the supplier’s plant while the supplier is producing 2. At your facility upon receipt of goods from your supplier 3. Before costly or irreversible processes 4. During the step-by-step production process 5. When production or service is complete 6. Before delivery to your customer 7. At the point of customer contact ↳ when you buy Copyright © 2020 Pearson Education Ltd. All Rights Reserved. 6 - 83 When and Where to Inspect Table 6.4 How Samsung Tests Its Smartphones Stress testing with nail punctures, extreme temperatures Durability and overcharging Visual inspection Comparing the battery with standardized models X-ray Looking for internal abnormalities Charge and discharge Power up and down the completed phone Organic pollution (TVOC) Looking for battery leakage Opening the battery cell to inspect tab welding and Disassembling insulation tape conditions Accelerated usage Simulated 2 weeks of real-life use in 5 days Checking for change in voltage throughout the Volatility (OVC) manufacturing process Copyright © 2020 Pearson Education Ltd. All Rights Reserved. 6 - 84 Inspection ► Many problems select the proper devices ► Worker fatigue ► Measurement error ► Process variability ► Cannot inspect quality into a product ► Robust design, empowered employees, and sound processes are better solutions Copyright © 2020 Pearson Education Ltd. All Rights Reserved. 6 - 85 Source Inspection techniques to reduce inspection : control the source ► Also known as source control ► The next step in the process is your customer ► Ensure perfect product to your customer Copyright © 2020 Pearson Education Ltd. All Rights Reserved. 6 - 86 Source Inspection ► Poka-yoke is the concept of foolproof devices or techniques designed to pass only acceptable products ↳ use tool to detect human error Copyright © 2020 Pearson Education Ltd. All Rights Reserved. 6 - 87 Poka Yoke in Process Design ► Poka-yoke is a concept in total quality management which is related to restricting errors at cradle itself (help operator to avoid (yokeru) mistakes (poka). ► It deals with "error proofing", fail-safe" or "mistake-proofing". ► What are the three types of mistake proofing? I. Elimination: eliminating the step that causes the error. II. Replacement: replacing the step with an error-proof one. III. Facilitation: making the correct action far easier than the error. Copyright © 2020 Pearson Education Ltd. All Rights Reserved. 6 - 88 Poka Yoke in Process Design Source: https://www.nikunjbhoraniya.com/2019/03/poka-yoke-error-proofing.html Copyright © 2020 Pearson Education Ltd. All Rights Reserved. 6 - 89 Source Inspection ► Checklists ensure consistency and completeness Copyright © 2020 Pearson Education Ltd. All Rights Reserved. 6 - 90 used by service firm Service Industry Inspection TABLE 6.5 Examples of Inspection in Services ORGANIZATION WHAT IS INSPECTED STANDARD Alaska Airlines Last bag on carousel Less than 20 minutes after arrival at the gate Airplane door opened Less than 2 minutes after arrival at the gate Jones Law Office Receptionist performance Phone answered by the second ring Billing Accurate, timely, and correct format Attorney Promptness in returning calls Hard Rock Hotel Reception desk Use customer’s name Doorman Greet guest in less than 30 seconds Room All lights working, spotless bathroom Minibar Restocked and charges accurately posted to bill Copyright © 2020 Pearson Education Ltd. All Rights Reserved. 6 - 91 Service Industry Inspection TABLE 6.5 Examples of Inspection in Services ORGANIZATION WHAT IS INSPECTED STANDARD Arnold Palmer Hospital Billing Accurate, timely, and correct format Pharmacy Prescription accuracy, inventory accuracy Lab Audit for lab-test accuracy Nurses Charts immediately updated Data entered correctly and Admissions completely Olive Garden Busboy Serves water and bread within Restaurant 1 minute Busboy Clears all entrée items and crumbs prior to dessert Waiter Knows and suggest specials, desserts Copyright © 2020 Pearson Education Ltd. All Rights Reserved. 6 - 92 Service Industry Inspection TABLE 6.5 Examples of Inspection in Services ORGANIZATION WHAT IS INSPECTED STANDARD Nordstrom Department Display areas Attractive, well-organized, Store stocked, good lighting Stockrooms Rotation of goods, organized, clean Salesclerks Neat, courteous, very knowledgeable Copyright © 2020 Pearson Education Ltd. All Rights Reserved. 6 - 93 TQM In Services ► Service quality is more difficult to measure than the quality of goods ► Service quality perceptions depend on 1) Intangible differences between products 2) Intangible expectations customers have of those products Copyright © 2020 Pearson Education Ltd. All Rights Reserved. 6 - 94 Service Quality The operations manager must recognize: ► The tangible component of services is important ► The service process is important ► The service is judged against the customer’s expectations ► Exceptions will occur Copyright © 2020 Pearson Education Ltd. All Rights Reserved. 6 - 95 20 question Service Specifications Copyright © 2020 Pearson Education Ltd. All Rights Reserved. 6 - 96 Service Recovery Strategy ► Managers should have a plan for when services fail ► Marriott's LEARN routine ► Listen ► Empathize ► Apologize ► React ► Notify Copyright © 2020 Pearson Education Ltd. All Rights Reserved. 6 - 97 cause & Effect analysis with why-why analysis 5 Why analysis