Bandsaw PDF
Document Details
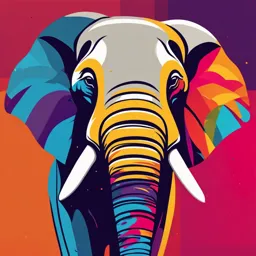
Uploaded by AttractiveJaguar
Tags
Summary
This document provides a detailed description of bandsaw operation, maintenance and safety. It explains various aspects of bandsaw functionality including blade changes, guide adjustments and other technical details.
Full Transcript
Bandsaw Re-saw/bandsaw mill is the most efficient for processing logs o Narrow blade, less waste o 4-6” wide o Can book-match grain Bandsaws have been around a long time and the only real improvements are the amount of guards now on them o Also very quiet, make sure it is off befor...
Bandsaw Re-saw/bandsaw mill is the most efficient for processing logs o Narrow blade, less waste o 4-6” wide o Can book-match grain Bandsaws have been around a long time and the only real improvements are the amount of guards now on them o Also very quiet, make sure it is off before cleaning or maintenance Size of bandsaw is measured by wheel diameter o The larger the wheel the greater capacity o Larger wheels also mean taller machines Blade is a continuous loop around 2, but sometimes 3 wheels o 3 wheeled machines have greater throat capacity but suffer from more blade breakages due to the added flex Blade runs between 2 sets of blade guides o One under the table – is fixed o One above the table – is adjustable depending on thickness of part Guides should be set about ¼” above part being cut The max height of upper blade guide determines the re-saw capacity of the bandsaw o Guide assemblies are made up of Thrust blocks/bearings These prevent the blade from being pushed off the wheel Guide blocks/bearings Blocks are usually ceramic and wear-out faster These prevent the blade from twisting and keep it straight in the cut, help prevent drift Must be positioned behind the teeth of the blade All elements in both guide sets need to be properly adjusted during each blade change Cutting force is straight down towards table o No real line of fire, though small parts can still get thrown if caught between blade and throat plate Machine is belt driven o Motor on bottom Lower wheel is fixed o Has stepped pulleys – can lower the speed and increase torque Tension and tracking happens on the top wheel o Tension must be properly done before tracking can be attempted Proper dust collection is important o Sawdust falls into lower wheel house Can get packed onto wheel if too much builds up Wheel brush reduces build-up If not careful blade can be pulled off the wheel when backing out of a cut o Especially rip cuts where the kerf closes up o Not dangerous but will most likely damage blade Most have tilting tables and rip fences o Dimensions, if any, are not accurate Steps in blade changing: o Isolate tool o Remove table key o Open wheel houses and remove guards o Back-off upper and lower guide assemblies o Remove blade tension o Carefully remove blade and fold up o Blow out dust build-up from guide assemblies and wheel houses o Unfold new blade and make sure teeth are pointing the right way o Carefully feed blade through table and onto wheels o Tension blade o Track blade o Move thrust blocks/bearings into place o Move guide block/bearings into place o Rotate wheel and check set-up o Replace guards and close wheel-houses o Replace table key o Plug tool back in o Burp-test tool to ensure everything is running smoothly Different blades for different applications o The narrower the blade the tighter the radius o Wide blades good for re-sawing boards o Can have regular tooth blades or skipped tooth (has less teeth) Regular tooth blades will give a finer cut o Most bandsaws will take blades from 1/8” wide to 1” wide The wider the blade the more tension it needs o 3/8” blade is a good general purpose blade, can get most jobs done o Skip tooth better for re-sawing o Blades are welded together Bad welds can cause improper tracking Tooth spacing around the weld needs to be consistent with the rest of the blade or it will create a rigid spot that will break faster o Folding wider blades can be dangerous Wear gloves Make sure when folding that you unfold with the teeth facing down Bandsaw safety o Cuts straight down o Passive/quiet machine – can cause lax safety o Never stand on the right side of the machine – if blade breaks it can be ejected that way o Be mindful of where your fingers and thumbs are, especially as you finish a cut o Isolate when making any adjustments to the blade Avoiding drift o Clean, sharp blade o Properly tensioned o Proper blade selection o Proper guide assembly adjustments o Slow, consistent feed rate Let the saw do the cutting