Fiber Optic Thermometers MSENSE®-FO ECU-I, -S and Test Unit Installation and Operating Instructions PDF
Document Details
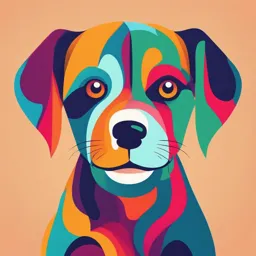
Uploaded by FunnyTriumph
2021
Tags
Summary
This document provides installation and operating instructions for fiber optic thermometers, specifically the MSENSE®-FO ECU-I, -S and Test Unit. It details safety information, personnel qualifications, and product descriptions, targeting professional users.
Full Transcript
Fiber Optic Thermometers MSENSE®-FO ECU-I, -S and Test Unit Installation and Operating Instructions 7323150/19 EN Rev. 19 – 02.2021 1 Document no. MAN0008-EN-R19-LE © Copyright Rugged Monitoring Inc. Your contact for all inquiries about this MSENSE® FO system and acce...
Fiber Optic Thermometers MSENSE®-FO ECU-I, -S and Test Unit Installation and Operating Instructions 7323150/19 EN Rev. 19 – 02.2021 1 Document no. MAN0008-EN-R19-LE © Copyright Rugged Monitoring Inc. Your contact for all inquiries about this MSENSE® FO system and accessories: MR Service & Complaint Maschinenfabrik Reinhausen GmbH Falkensteinstraße 8 93059 Regensburg Germany https://www.reinhausen.com/ [email protected] [email protected] If required, you will receive at this address more information about the product and issues this technical document. The MSENSE®-FO is made available for the Maschinenfabrik Reinhausen GmbH Company and is manufactured by: Rugged Monitoring Québec Inc. 1415 rue Frank-Carrel, Suite 230 Québec City, QC, G1N 4N7 Canada Copyright Rugged Monitoring Québec Inc. All rights reserved The contents of this publication can be modified without prior notice. The greatest care has been taken with the preparation of texts, illustrations, and software programs. Nevertheless, Rugged Monitoring Québec Inc. cannot be held legally responsible for any remaining faulty specifications nor accept any liability for these. 2 Document no. MAN0008-EN-R19-LE © Copyright Rugged Monitoring Inc. TABLE OF CONTENTS 1 PRODUCT CERTIFICATIONS................................................................................................................................7 1.1 CERTIFICATIONS.........................................................................................................................................................7 2 SAFETY INFORMATION.........................................................................................................................................8 2.1 APPROPRIATE USE.......................................................................................................................................................8 2.2 FUNDAMENTAL SAFETY INSTRUCTIONS......................................................................................................................8 2.2.1 Grounding and earthing....................................................................................................................................8 2.2.2 Personal protective equipment..........................................................................................................................8 2.2.3 Work area...........................................................................................................................................................8 2.2.4 Explosion protection..........................................................................................................................................9 2.2.5 Safety markings..................................................................................................................................................9 2.2.6 Ambient conditions.............................................................................................................................................9 2.2.7 Modifications and conversions..........................................................................................................................9 2.2.8 Spare parts.........................................................................................................................................................9 2.2.9 Working during operation.................................................................................................................................9 2.3 PERSONNEL QUALIFICATION.......................................................................................................................................9 2.3.1 Electrically skilled person..................................................................................................................................9 2.3.2 Electrically trained persons............................................................................................................................ 10 2.3.3 Operator.......................................................................................................................................................... 10 2.3.4 Technical Service............................................................................................................................................ 10 2.3.5 Service & Complaint....................................................................................................................................... 10 2.4 PERSONAL PROTECTIVE EQUIPMENT........................................................................................................................ 10 2.4.1 Personal protective equipment to be worn always......................................................................................... 10 2.4.2 Special personal protective equipment........................................................................................................... 10 2.5 IT SECURITY............................................................................................................................................................. 11 3 GETTING STARTED.............................................................................................................................................. 12 3.1 MSENSE FO PRODUCT DESCRIPTIONS.................................................................................................................... 13 3.2 MSENSE FO PRODUCT SPECIFICATIONS................................................................................................................. 13 3.2.1 MSENSE FO ECU-S specifications ( )............................................................................................. 14 3.2.2 MSENSE FO Test Unit specifications ( )............................................................................................. 15 3.2.3 MSENSE FO ECU-I specifications ( ).............................................................................................. 16 3.3 PROBE OPTIONS AND RELATED ACCESSORIES.......................................................................................................... 16 3.4 CALIBRATION........................................................................................................................................................... 18 3.5 TRANSFORMER APPLICATIONS................................................................................................................................. 18 4 UNPACKING............................................................................................................................................................ 19 4.1 INCOMING QUALITY TEST ON PROBES...................................................................................................................... 19 5 BEST PRACTICES FOR POWER TRANSFORMERS..................................................................................... 20 5.1 INTRODUCTION........................................................................................................................................................ 20 5.2 PROBE INSTALLATION.............................................................................................................................................. 20 5.2.1 Best practices related to probe installation.................................................................................................... 21 5.2.2 Probe connector cleaning............................................................................................................................... 21 5.2.3 Radial spacer preparation.............................................................................................................................. 22 5.2.4 Spacer installation in the winding.................................................................................................................. 22 5.2.5 Probe installation in other places................................................................................................................... 23 5.2.6 Fiber cable routing best practices.................................................................................................................. 23 5.2.7 Probe testing................................................................................................................................................... 23 5.2.8 Conclusion (probe installation)...................................................................................................................... 23 5.3 FEEDTHROUGH INSTALLATION BEST PRACTICES..................................................................................................... 23 5.3.1 Feedthrough testing........................................................................................................................................ 24 5.3.2 Feedthrough connector cleaning.................................................................................................................... 24 5.4 TANK WALL PLATE (MOUNTING FLANGE) INSTALLATION BEST PRACTICES............................................................. 24 5.4.1 Bolted wall plate installation best practices (with O-ring)............................................................................ 25 3 Document no. MAN0008-EN-R19-LE © Copyright Rugged Monitoring Inc. 5.4.2 Bolted wall plate installation best practices (without O-ring)....................................................................... 25 5.4.3 Welded wall plate installation best practices................................................................................................. 25 5.5 EXTENSION CABLE INSTALLATION BEST PRACTICES................................................................................................ 25 5.5.1 Extension cable testing................................................................................................................................... 25 5.6 INTERFACE BOX INSTALLATION BEST PRACTICES.................................................................................................... 25 6 MSENSE FO MONITOR INSTALLATION........................................................................................................ 26 6.1 MSENSE FO ECU-S INSTALLATION ( ).................................................................................................... 26 6.1.1 MSENSE FO ECU-S mechanical installation................................................................................................ 26 6.1.2 MSENSE FO ECU-S electrical installation................................................................................................... 27 6.1.3 MSENSE FO ECU-S analog outputs.............................................................................................................. 28 6.1.4 MSENSE FO ECU-S ethernet ports (option)................................................................................................. 28 6.2 MSENSE FO TEST UNIT INSTALLATION ( )................................................................................................. 29 6.3 MSENSE FO ECU-I INSTALLATION ( )..................................................................................................... 29 6.3.1 MSENSE FO ECU-I mechanical installation................................................................................................. 29 6.3.2 MSENSE FO ECU-I electrical installation.................................................................................................... 30 6.3.3 RS-485 serial port........................................................................................................................................... 32 6.4 TESTING YOUR RS-485 SERIAL CONNECTION.......................................................................................................... 33 6.4.1 Testing your Modbus connection.................................................................................................................... 33 6.4.2 Testing your IEC 60870-5-101 serial connection ( )........................................................................ 34 6.4.3 Testing your DNP 3.0 serial connection ( )...................................................................................... 34 6.5 USING THE MSENSE FO INSTRUMENT FOR THE FIRST TIME................................................................................... 35 7 MAINTENANCE AND TROUBLESHOOTING................................................................................................. 36 7.1 MSENSE FO ECU-S INSTRUMENT ( )....................................................................................................... 36 7.2 MSENSE FO TEST UNIT INSTRUMENT ( ).................................................................................................... 36 7.3 MSENSE FO ECU-I INSTRUMENT ( )........................................................................................................ 37 8 MSENSE FO THERMOMETER HARDWARE REFERENCE....................................................................... 38 8.1 MSENSE FO ECU-S REFERENCE ( )......................................................................................................... 38 8.1.1 Display and keypad description...................................................................................................................... 38 8.1.2 System error.................................................................................................................................................... 39 8.2 MSENSE FO TEST UNIT REFERENCE ( )...................................................................................................... 39 8.2.1 Display description......................................................................................................................................... 39 8.3 MSENSE FO ECU-I REFERENCE ( ).......................................................................................................... 40 8.3.1 MSENSE FO ECU-I display description........................................................................................................ 40 8.4 HOW TO ACCESS THE LOGGED DATA........................................................................................................................ 41 8.5 INTERPRETATION OF “%” RESULTS.......................................................................................................................... 41 9 MSET-FO SOFTWARE DESCRIPTION............................................................................................................. 43 9.1 INSTALLATION AND INITIAL OPERATION.................................................................................................................. 43 9.1.1 MSET-FO software installation...................................................................................................................... 43 9.2 DATA MODE (TEMPERATURE ACQUISITION)............................................................................................................. 45 9.2.1 Logging data to a PC file................................................................................................................................ 46 9.3 DEVICE CONFIGURATION MODE............................................................................................................................... 46 9.3.1 SETUP tab...................................................................................................................................................... 47 9.3.2 CHANNELS tab.............................................................................................................................................. 48 9.3.3 COMMUNICATION tab................................................................................................................................. 48 9.3.4 ANALOG OUTPUTS tab ( ).............................................................................................................. 49 4 Document no. MAN0008-EN-R19-LE © Copyright Rugged Monitoring Inc. 9.3.5 CONDITIONS tab ( )....................................................................................................................... 50 9.3.6 RELAYS tab ( ).................................................................................................................................. 51 9.3.7 AGING tab ( ).................................................................................................................................... 52 9.3.8 Importing / Exporting instrument configurations........................................................................................... 54 9.4 DOWNLOADING DATA FILES.................................................................................................................................... 55 9.5 ALARM MANAGEMENT............................................................................................................................................ 55 9.6 VIRTUAL CONFIGURATIONS..................................................................................................................................... 56 9.7 FIRMWARE UPGRADE............................................................................................................................................... 56 10 ETHERNET COMMUNICATION PROTOCOLS ( )....................................................................... 59 10.1 CONNECTING TO THE ETHERNET PORT.................................................................................................................... 59 10.1.1 Fixed IP address............................................................................................................................................. 59 10.1.2 Dynamic IP address (with DHCP server)...................................................................................................... 60 10.2 UPGRADING ETHERNET OPTION FIRMWARE............................................................................................................. 61 10.3 HOW TO USE MODSCAN TO EXERCISE YOUR MODBUS CONNECTION...................................................................... 62 10.4 USING THE IED EXPLORER TOOL (FREEWARE)........................................................................................................ 63 11 MODBUS REGISTER TABLE.......................................................................................................................... 65 12 DNP 3.0 DATA POINT MAP ( )............................................................................................................ 73 13 IEC 60870-5 DATA MAP ( ).................................................................................................................. 79 13.1 IEC 60870-5-101 INTEROPERABILITY LIST (SERIAL PORT)...................................................................................... 79 13.2 IEC 60870-5-104 INTEROPERABILITY LIST (ETHERNET PORT)................................................................................. 82 13.3 IEC 60870-5 DATA MAP........................................................................................................................................... 85 14 IEC 61850 CID FILE DESCRIPTION ( )............................................................................................ 92 15 APPENDIX – MECHANICAL DRAWINGS................................................................................................... 94 15.1 TEMPERATURE PROBE.............................................................................................................................................. 94 15.2 FEEDTHROUGH......................................................................................................................................................... 94 15.3 EXTENSION CABLE AND EXTENSION CABLE BUNDLE............................................................................................... 95 15.3.1 Single extension cable..................................................................................................................................... 95 15.3.2 Bundle extension cable................................................................................................................................... 95 15.4 MOUNTING FLANGE (TANK WALL PLATE)................................................................................................................ 95 15.5 INTERFACE BOX....................................................................................................................................................... 96 15.6 INSTRUMENT – MSENSE FO ECU-S ( ).................................................................................................... 97 15.7 INSTRUMENT – MSENSE FO TEST UNIT ( )................................................................................................. 97 15.8 INSTRUMENT – MSENSE FO ECU-I ( )..................................................................................................... 98 16 INDEX.................................................................................................................................................................... 99 5 Document no. MAN0008-EN-R19-LE © Copyright Rugged Monitoring Inc. Notice Permanent damage may be done to the thermometer if the power supply connections are not done correctly. Only approved power supply modules (24 / 48 VDC ± 10%) should be used to operate the MSENSE FO ECU-I and MSENSE FO ECU-S thermometers. DO NOT CONNECT TO AC 100-240 POWER SOURCES!!!!!! These products do not contain any user-serviceable parts. Opening these precision instruments will void their warranty and may disturb its factory calibration. Always seek servicing from an authorized Maschinenfabrik Reinhausen service depot. To assure cleanliness of the optical connector, keep the protection cap on unused connectors at all time. Fiber optic probes and extension cables are fragile and will break if the bending radius becomes less than ~1 cm, even temporarily. Probe and extension cable breakages are not covered under the standard Maschinenfabrik Reinhausen warranty. MSENSE-FO instruments are available to support different types of temperature probes; currently, 62.5- and 200-micron (µ) probes are supported. It is imperative to realize that an instrument configured to read a given probe type will interface only for that specific type, 62.5 or 200 µ. This guide assumes that the standard probe size is 200 µ, unless specified otherwise. The sizes 62.5 and 200 µ refer to the diameter of the core of the fiber that is used to build probes, feedthroughs, and extension cables; this guide will simply refer to 62.5 µ or 200 µ to distinguish between the two types. Furthermore, two types of 62.5 µ probes are supported; these are referred as “LumaSense” or Fiso” probes1; there is a software selection that must be made in the MSET-FO app to select the probe type that you are using, see section 9.3.1 for more information. It should be noted that the MSENSE-FO standard probe, extension cable and feedthrough fiber size is 200 µ. Most drawings and screenshots presented in this manual are given only for illustration purposes and are not necessarily presented to be easily readable (to save space). For more details, please refer to the applicable marketing materials (e.g., brochures, etc.) and software (e.g., MSET-FO). 1 “LumaSense” is a trademark owned by LumaSense Technologies Inc. “Fiso” is a trademark owned by Fiso Technologies Inc. 6 Document no. MAN0008-EN-R19-LE © Copyright Rugged Monitoring Inc. 1 PRODUCT CERTIFICATIONS Due to the unique nature of the fiber optic probes that are used with these Maschinenfabrik Reinhausen transducer systems, probes and extension cables are not guaranteed. When using any electrical appliance, basic safety precautions should be followed, including the following: Do not operate in wet / damp environments Do not operate in explosive atmospheres Keep product surface dry and clean. Always make sure all electrical installations are made in accordance with local authorities’ regulations and laws. 1.1 Certifications The following certifications and conformity tests have been done successfully on the MSENSE FO instruments. Emission Radiated Emission FCC part 15 subpart B (2018); CISPR 11 (2015 + A1 2016) Conducted Emission FCC part 15 subpart B (2018); CISPR 11 (2015 + A1 2016) Immunity Conducted Immunity IEC 61000-4-6 (2013) 10 Vrms Radiated Electromagnetic Field IEC 61000-4-3 (2006 + A1 2007 + A2 2010); IEEE C37.90.2 Immunity (2004) Up to 20 V/m ESD Immunity IEC 61000-4-2 (2008); IEEE C37.90.3 (2001) Up to ±8 kV contact, ±15 kV air Fast Transients Immunity IEC 61000-4-4 (2012); IEEE C37.90.1 (2012) Up to ±4 kV Surge Immunity IEC 61000-4-5 (2014) Up to ±2 kV L-L; ±1 kV L-G Magnetic field Immunity IEC 61000-4-8 (2009) 100 A/m continuous, 1 kA/m for 3 s Damped Oscillatory Magnetic Field IEC 61000-4-10 (2016) 100 A/m Conducted Disturbances Immunity IEC 61000-4-16 (2015) 30V 1 min, 300 V 1 s Damped Oscillatory Wave Immunity IEC 61000-4-18 (2006); IEEE C37.90.1 (2012) Up to ±2.5 kV, 1 MHz Voltage Dips and Interruptions IEC 61000-4-29 (2000) 0%: < 10 msec IEC 60870-2-1 (1995); IEC 61000-4-17 (1999 + A1 2001 + A2 DC Voltage Ripple 2009) 15% Safety Low Voltage Directive IEC 61010-1 (2010) Environmental Enviromental protection IEC 60529 IP20 RoHS Directive 2011/65EU WEEE Directive 2012/19/EU REACH Directive CE No 1907/2006 These products are CE marking certified. This device complies with Part 15 of the FCC Rules. Operation is subject to the following two conditions: (1) this device may not cause harmful interference, and (2) this device must accept any interference received, including interference that may cause undesired operation. 7 Document no. MAN0008-EN-R19-LE © Copyright Rugged Monitoring Inc. 2 SAFETY INFORMATION This technical document contains detailed descriptions regarding the safe and proper installation, connection, commissioning and use of the MSENSE FO products. Carefully read this technical document to familiarize yourself with the product. This technical document is an integral part of the product. This instrument is designed and manufactured based on state-of-the-art technologies. Nevertheless, risks of accidents are always possible, as a result of any misuses of this instrument. 2.1 Appropriate use The MSENSE FO is designed mainly for use in electrical energy systems and facilities. It is designed mainly to detect and report emerging, potentially harmful trends in the monitored equipment in real-time by measuring the temperatures at various locations inside a power transformer. The device is not designed and is not suitable for detecting rapidly developing faults and therefore is not intended to protect the equipment from such faults (e.g. through shutdown). For this, please use safety devices that have been designed for this purpose. If used as intended, in compliance with the requirements and conditions specified in this technical document and the warning notices in this technical document and attached to the product, the product does not pose risk of injury or damage to property or the environment. This applies throughout the entire service life of the product, from delivery to installation and operation and including removal and disposal. The following is considered appropriate use: Operate the product in accordance with this technical document, the agreed-upon delivery conditions, and the technical data. Ensure that all necessary work is performed by qualified personnel only. Only use the equipment included in the delivery for the intended purpose and in accordance with the specifications of this technical document. Observe the notices in this technical document regarding electromagnetic compatibility and the technical data. 2.2 Fundamental safety instructions To prevent accidents, disruptions, and damages as well as unacceptable adverse effects on the environment, those responsible for transport, installation, operation, maintenance and disposal of the product or parts of the product must be guided by the following recommendations. 2.2.1 Grounding and earthing The models MSENSE FO ECU-I and ECU-S have provision for an enclosure ground connection ( ). Make sure an appropriate connection is made to the system ground where the instrument is installed. 2.2.2 Personal protective equipment Loosely worn or unsuitable clothing increases the danger of becoming trapped or caught up in rotating parts and the danger of getting caught on protruding parts. This could result in danger to life. All necessary devices and personal protective equipment required for a given task, such as a hard hat, safety footwear, etc. must be worn. Observe the "Personal protective equipment" (see section 2.4). Never wear damaged personal protective equipment. Never wear rings, necklaces, or other jewelry. If you have long hair, wear a hairnet. 2.2.3 Work area Untidy and poorly lit work areas can lead to accidents. 8 Document no. MAN0008-EN-R19-LE © Copyright Rugged Monitoring Inc. Keep the work area clean and tidy. Make sure that the work area is well lit. Observe the applicable laws for accident prevention in the relevant country. 2.2.4 Explosion protection Highly flammable or explosive gases, vapors and dusts can cause serious explosions and fire. Do not install or operate these products in areas where a risk of explosion is present. 2.2.5 Safety markings Warning signs and safety information plates are safety markings on the product. They are an important aspect of the safety concept. Observe all safety markings on the product. Make sure all safety markings on the product remain intact and legible. Replace safety markings that are damaged or missing. 2.2.6 Ambient conditions To ensure reliable and safe operation, the product must only be operated under the ambient conditions specified in the technical data. Observe the specified operating conditions and requirements for the installation location. 2.2.7 Modifications and conversions Unauthorized or inappropriate changes to the product may lead to personal injury, material damage and operational faults. Only modify the product after consultation with Maschinenfabrik Reinhausen. 2.2.8 Spare parts Spare parts not approved by Maschinenfabrik Reinhausen may cause physical injury and damage the product. Only use spare parts approved by the manufacturer. Contact Maschinenfabrik Reinhausen. 2.2.9 Working during operation You must only operate the product when it is in a sound operational condition. Otherwise it could pose a danger to human life. Regularly check the operational reliability of safety equipment. Perform the inspection tasks described in this technical document regularly. 2.3 Personnel qualification The person responsible for assembly, commissioning, operation, maintenance and inspection must ensure that personnel are sufficiently qualified. 2.3.1 Electrically skilled person The electrically skilled person has a technical qualification and therefore has the required knowledge and experience and is also conversant with the applicable standards and regulations. The electrically skilled person is also proficient in the following: Can identify potential dangers independently and is able to avoid them. Can perform work on electrical systems. Is specially trained for the working environment in which (s)he works. 9 Document no. MAN0008-EN-R19-LE © Copyright Rugged Monitoring Inc. Must satisfy the requirements of the applicable statutory regulations for accident prevention. Always make sure all electrical installations are made in accordance with local authorities’ regulations and laws. 2.3.2 Electrically trained persons An electrically trained person receives instructions and guidance from an electrically skilled person in relation to the tasks undertaken and the potential dangers in the event of inappropriate handling as well as the protective devices and safety measures. The electrically trained person works exclusively under the guidance and supervision of an electrically skilled person. 2.3.3 Operator The operator uses and operates the product in line with this technical document. The operating company provides the operator with instruction and training on the specific tasks and the associated potential dangers arising from improper handling. 2.3.4 Technical Service We strongly recommend having maintenance, repairs and retrofitting carried out by our Technical Service department. This ensures that all work is performed correctly. If maintenance is not carried out by our Technical Service department, please ensure that the personnel who carry out the maintenance are trained and authorized to do so by Maschinenfabrik Reinhausen. 2.3.5 Service & Complaint Contact information for all inquiries regarding the MSENSE®-FO: Maschinenfabrik Reinhausen GmbH Falkensteinstrasse 8 93059 Regensburg Germany [email protected] [email protected] If required, you will receive at these email addresses more information about this product and issues related to this technical document. 2.4 Personal protective equipment Personal protective equipment must be worn during work to minimize risks to health.. Always wear the personal protective equipment required for the job at hand. Never wear damaged personal protective equipment. Observe information about personal protective equipment provided in the work area. 2.4.1 Personal protective equipment to be worn always Protective clothing Close-fitting work clothing with a low tearing strength, with tight sleeves and with no protruding parts. It mainly serves to protect the wearer against being caught by moving machine parts. Safety shoes To protect against falling heavy objects and slipping on slippery surfaces. 2.4.2 Special personal protective equipment Safety glasses To protect the eyes from flying parts and splashing liquids. Visor To protect the face from flying parts and splashing liquids or other dangerous substances. 10 Document no. MAN0008-EN-R19-LE © Copyright Rugged Monitoring Inc. Hard hat To protect from falling and flying parts and materials. Hearing protection To protect from hearing damage. Protective gloves To protect from mechanical, thermal, and electrical hazards. 2.5 IT security Observe the following recommendations for the secure operation of the product. Ensure that only authorized personnel have access to this device. Only use the device within an ESP (electronic security perimeter). Ensure that the device is only operated by trained personnel who are familiar with IT security. All protocol interfaces (Modbus RTU, DNP3, IEC 61850, etc.) only have read access to the MSENSE FO. Changing parameters or data through them is not possible. Observe the information of access rights, user levels and password settings in the MSET-FO parameterization software operating instructions. 11 Document no. MAN0008-EN-R19-LE © Copyright Rugged Monitoring Inc. 3 GETTING STARTED Your MSENSE®-FO temperature-sensing instruments allows you to take full advantage of the benefits inherent to fiber optic sensing technology. It offers accurate and reliable temperature measurements, combined with extraordinary insensitivity to EMI/RFI, high voltage insulation and disturbance free sensing due to the non-electrical nature of the sensor element used. Not only does the MSENSE FO Maschinenfabrik Reinhausen family of products gives access to reliable measurements, it also offers a simple user interface that makes the technology easy to use. Moreover, no special calibration is required when changing the fiber optic sensor probes. It offers up to 24 (model dependent) optical channels in a single compact and rugged enclosure. The MSENSE FO instruments are uniquely fitted with an optical integrity feature that ensures that the internal optical modules are within accuracy specifications. The thermometers are packaged in rugged enclosures which makes it ideally suited for OEM transformer and other industrial applications. Each unit is fitted with a micro-USB connector ( ). This interface allows for all data transfer, to or from a Windows computer. The transfer protocol is a fast serial scheme, a standard in the industry. The portable Test Unit is powered via this micro-USB connector while models MSENSE FO ECU-I and ECU-S are powered via a different connector (terminal block). These thermometers include the latest developments in fiber optic temperature measurement technologies. Most types of GaAs-based probes now available on the market are supported, even probes manufactured by our competitors. It will also interface with and read marginal probes, or probes with dirty connectors, and so forth. It will give you years of excellent service. The MSET-FO software package would be a good complement to your thermometer. This Windows software allows the user to configure any MSENSE FO instrument; it should be noted that most functions are programmable only from MSET- FO. Temperature logging can be performed in two ways: 1- Directly in the instrument, using a user supplied microSD memory card (in theory, up to 2 TB ) 2- With MSET-FO. In this case, logging can be done concurrently from 6 instruments (up to 64 channels) 3- Logging rate from one sample per second 4- Both logging methods can be used simultaneously. A serial RS-485 communication port is a standard feature; this could be useful for Modbus communication (industrial applications). Up to 32 instruments can be linked together when using the Modbus communication protocol. Furthermore, DNP 3.0 and IEC 60870-5-101 serial protocols are also standard features for the MSENSE FO ECU-S instrument ( ). The MSENSE FO ECU-I and ECU-S are fitted with a system fault relay (C-form, 5 A max). This relay is not user programmable. 12 Document no. MAN0008-EN-R19-LE © Copyright Rugged Monitoring Inc. 3.1 MSENSE FO product descriptions This manual effectively covers three distinct products, each one being dedicated to a task and role. Each of these product versions can support either 62.5 or 200 µ probes; make sure you are using the proper version to interface to your actual probes2. These three products are: MSENSE FO ECU-S ( ): This is a complete instrument that is normally installed in a transformer marshalling cabinet, as a permanent installation. It features up to 24 optical channels, and it is offered with several options, such as relays, analog outputs, Ethernet interface with smart communication protocols. MSENSE FO Test Unit ( ): This is a portable battery-operated instrument that is recommended for testing probes while they are being installed in a transformer. MSENSE FO ECU-I ( ): This is sub-system intended to be integrated into a high-end monitoring system, such as the Maschinenfabrik Reinhausen ETOS system. It features a minimal number of features, as higher-end features would normally be provided by the ETOS system. In this user guide the name “MSENSE FO” is used to refer to features to all three models of instruments. 3.2 MSENSE FO product specifications This is only a summary of the most important specifications for the three MSENSE FO monitor instruments; for complete product specifications, please refer to the marketing product brochures. 2 It is important to remember that 62.5 and 200 µ systems are not interchangeable! For example, if you have a 200 µ instrument, it will interface only to 200 µ probes, feedthroughs, and extension cables. For instruments configured to interface with 62.5 µ probes, a sticker like this will be found on the instrument (no sticker for 200 µ compatible instrument): Additionally, when using 62.5 µ probes, do not forget to select the appropriate probe manufacturer (LumaSense or Fiso) in the MSET-FO software tool; see section 9.3.1 for information on how this selection can be made. 13 Document no. MAN0008-EN-R19-LE © Copyright Rugged Monitoring Inc. 3.2.1 MSENSE FO ECU-S specifications ( ) Resolution 0.1 C Accuracy ± 1 C Calibrated Temperature -45 to 200 C Range (Extended calibration available on special order) Usable Temperature Range -80 to 200 C Number of channels 8, 12 or 16 Probe length 1 to 500 meters (and more) Sensor GaAs dielectric epoxy tipped optical fiber probes Typically, 0.2 to 0.5 second, per channel Response time (Probe and setting configuration dependent) Maximum sampling rate is ~ 5 Hz (per channel) All Maschinenfabrik Reinhausen probes (200 µ probes only) Probe compatibility Most competitive 200 µ GaAs probes Unit C only (oF selectable in MSET-FO software) On a user-removable microSD memory card (4 or 8 GB, ) Data logging option With the Ethernet and logging options, a non-removable memory card is supplied in addition to the removable card (mirrored logging) Operating temperature -40 to 72 C, non-condensing Storage temperature -40 to 85 C Display of temperature readings as well as various user information Local display Display of 6 values; will scroll to display additional temperature values, and error messages Analog output option Internal module (4-20 mA and 0-10 V), with 8 programmable outputs Relays option 8 form-C relays, rated at 5 A (VAC) RS-485 port (Modbus, DNP 3.0, and IEC 60870-5-101) – Ground Serial port insulated RJ45 – With advance communication protocols (IEC 61850, Modbus Ethernet option over Ethernet, and IEC 60870-5-104) Fiber optic communication SFP module can be added to the Ethernet option Power 24 / 48 VDC ±10%, ~20 watts Through USB port ( ) (and Ethernet port, if available). Both Firmware upgradability processors need to be upgraded independently from each other Size 267L x 187W x 72H mm Weight 0.8 kg Standard interface Micro-USB connector ( ) All technical specifications are subject to change without notice. 14 Document no. MAN0008-EN-R19-LE © Copyright Rugged Monitoring Inc. 3.2.2 MSENSE FO Test Unit specifications ( ) Resolution 0.1 C Accuracy ± 1 C Calibrated Temperature -45 to 200 C Range (Extended calibration available on special order) Usable Temperature Range -80 to 200 C Number of channels 4 Probe length 1 to 500 meters (and more) Sensor GaAs dielectric epoxy tipped optical fiber probes Typically, 0.2 to 0.5 second, per channel (Probe and setting configuration dependent) Response time Sampling rate is ~ 5 Hz (per channel) Note: to guarantee the 0.2 sec acquisition time, acquisition mode must be in fixed-time acquisition mode (non-AGC). GaAs probes with either 62.5 µ or 200 µ probes (must be selected at time of order) Probe compatibility Most competitive GaAs probes (must match same probe fiber diameter) Unit C only (oF selectable in MSET-FO software) Data logging On user supplied micro-SD card, from 1 sec ( ) Operating temperature -30 to 55 C, non-condensing Storage temperature -30 to 65 C Local display Display of temperature readings as well as various user information Standard interface Micro-USB connector ( ) 5 VDC (USB port, ), ~150 mA (up to 500 mA when the Power MSENSE FO TEST UNIT battery is charging) Capacity of 2,500 mA-h (enough for about 10 hours of continuous Internal battery use, when battery is fully charged) Firmware upgradability Through USB port ( ) Size 182L x 125W x 69H mm Weight MSENSE FO TEST UNIT: 0.6 kg. All technical specifications are subject to change without notice. 15 Document no. MAN0008-EN-R19-LE © Copyright Rugged Monitoring Inc. 3.2.3 MSENSE FO ECU-I specifications ( ) Resolution 0.1 C Accuracy ± 1 C Calibrated Temperature Range -45 to 200 C Usable Temperature Range -80 to 200 C Number of channels 8 or 12 (200 µ probes) or 8 (62.5 µ probes) Probe length 1 to 500 meters (and more) Sensor GaAs dielectric epoxy tipped optical fiber probes Typically, 0.2 to 0.5 second, per channel Response time (Probe and setting configuration dependent) Sampling rate is ~ 5 Hz (per channel) GaAs probes with either 62.5 µ or 200 µ probes (must be selected at time of order) Probe compatibility Most competitive GaAs probes (must match same probe fiber diameter) Unit C only (oF selectable in MSET-FO software) Data logging On a user-removable microSD memory card ( ) Operating temperature -40 to 72 C, non-condensing Storage temperature -40 to 85 C One status LED per optical channel (12 in total) Local display Information LEDs: Power on/off, logging status, TX/RX communication, alarm (also called sometime system fault) Relays option 1 form-C relays, rated at 5 A – System fault Serial port RS-485 port (for Modbus connection) – Ground insulated Power 24 / 48 VDC ±10%, ~10 watts Firmware upgradability Through USB port ( ) Size 198L x 130W x 56H mm Weight 0.7 kg Standard interface Micro-USB connector ( ) All technical specifications are subject to change without notice. 3.3 Probe options and related accessories The following figures give short descriptions of the various probe configurations and related accessories that are optionally available from Maschinenfabrik Reinhausen. For more information about dimensions and other specifications, please refer to appendix 15. 16 Document no. MAN0008-EN-R19-LE © Copyright Rugged Monitoring Inc. Probe for hot spot transformer (with and without disc): Feedthrough: Tank Wall Plate: Interface Box (I-Box): 17 Document no. MAN0008-EN-R19-LE © Copyright Rugged Monitoring Inc. ST-ST Extension Cable Extension cable bundles are also available. 3.4 Calibration Your MSENSE FO thermometer comes factory calibrated. Experience has shown that re-calibration is not required over the whole product life; however, if your ISO company rules state that an annual re-calibration is required, then it is your responsibility to comply with those rules. For laboratory applications, a new calibration is standard every 12 months or whenever performance verification indicates that calibration is necessary; NIST traceable calibration certificates are available. All calibrations are performed at the factory. Contact your Maschinenfabrik Reinhausen Representative for further information. 3.5 Transformer applications Transformer winding monitoring is one of the most important applications for the MSENSE FO instrument. The next chapter is dedicated to power transformer applications. It gives information related to the installation of probes, feedthroughs, extension cables, etc., as they should be applied when dealing with oil-filled power transformers. It should be noted that these best practices are based on my years of experience in installing such systems in power transformers, but it must be mentioned that specific transformer manufacturers can have their own installation procedures that may differ from the information presented here. Notice: The ultimate responsibility regarding the installation of probes remains with the transformer manufacturer. Maschinenfabrik Reinhausen cannot be held responsible for any issues related to probe, feedthrough and extension cable installation. 18 Document no. MAN0008-EN-R19-LE © Copyright Rugged Monitoring Inc. 4 UNPACKING Before using your MSENSE FO thermometer, check the box content to be sure all items have been included. Your package should normally contain: MSENSE FO instrument User manual (this manual) (paper copy not included, supplied as a PDF document downloadable from the Internet). Contact Maschinenfabrik Reinhausen for a copy ([email protected] or https://www.reinhausen.com/. Calibration Certificate. Options: Power supply module (universal input: 100-240 VAC, 50/60 Hz). Fiber optic temperature sensor probes Fiber optic extension cables and extension bundles Fiber optic couplings and feedthroughs Interface box MSET-FO software package™ (downloadable from the Internet). Make sure all listed items have been received and are in good condition. Note any evidence of rough handling in transit; immediately report any damage to the shipping agent. Should a part be missing or damaged, please contact your distributor immediately. Returns must be made with the original packaging, accompanied by an authorization number (RMA). Your distributor will provide you with information concerning the return of merchandise. The carrier will not honour damage claims unless all shipping material is saved for inspection. After examining and removing contents, save packing material and carton in the event reshipment becomes necessary. 4.1 Incoming quality test on probes When new probes are received, we strongly recommend testing them. Section 5.2.7 gives a detailed procedure on how to perform probe testing. 19 Document no. MAN0008-EN-R19-LE © Copyright Rugged Monitoring Inc. 5 BEST PRACTICES FOR POWER TRANSFORMERS 5.1 Introduction As the main application forecasted for the MSENSE FO monitor is monitoring temperatures in oil-filled power transformers, this chapter presents information and experience gained over the years by Maschinenfabrik Reinhausen regarding the use and application related to this monitor. The content of this chapter is based on hands-on experience in installing probes in power transformers, and on theory and information provided by IEEE and IEC. Notice: The information presented in this chapter is provided to help engineers that are new to the use of fiber optic sensors in power transformers. Each manufacturer has their own best practices, which are most of the time confidential to their manufacturing organization; this is fine. For these experienced users, the information given here could be used to consider improvements to their internal procedures. Notice: The ultimate responsibility regarding probe installation procedures and locations remains with the transformer manufacturers. Typically, sensor locations will be based on calculations made by the manufacturer engineers. Maschinenfabrik Reinhausen cannot take responsibility for the installation and the use of the MSENSE FO instrument and related accessories. 5.2 Probe installation Although windings found in transformers can take several forms, this chapter addresses the installation in the most common type of windings; these windings can be characterized as follows: Core type transformers (shell type transformers are also made but are much rarer) Disc type windings. These have radial spacers. There exists also 3 other type of windings, for core type transformers: o Helical windings, which are quite like disc type windings, and have radial spacers o Layer windings; these are quite common for low voltage windings and have vertical spacers. Probe installation must be done on the winding machine, and probes must be inserted between layers, near the top of the winding (exact positions to be confirmed by design engineers). The probe should be embedded in pressboard material (to avoid cooling of the sensor by flowing oil) which will then be squeezed in cooling ducts o Sheet (or foil) windings, for low voltage only. Probe installation would be similar to layer windings. The rest of this guide will concentrate on disc type windings, in core type transformers. Furthermore, it is good to know that the Maschinenfabrik Reinhausen FO-Sensor probes are available in two configurations: 1- With disc. The disc version offers the following benefits: a. If offers an excellent protection against compression of the GaAs sensing crystal b. It is easier to install (less installation skill required) and offers a more secure probe installation in spacers c. It offers a well-defined sensor position (sensor is located at center of the disc) d. It offers an excellent pulling force (above 80 N) without compromising the sensor position e. No need to squeeze the probe cable in the radial spacer, as the disc will retain positively the probe tip into the spacer f. It is recommended for all probe installations, even in locations other than windings 2- Without disc. Some manufacturers still prefer this version, as this version has been marketed for a long time (disc probes have a more recent history). Maschinenfabrik Reinhausen recommend disc probe for ALL applications. This drawing presents all variations for which FO-Sensor probes are available. 20 Document no. MAN0008-EN-R19-LE © Copyright Rugged Monitoring Inc. 5.2.1 Best practices related to probe installation When installing probes, please keep in mind these points: Always respect bending radius o Minimum radius of 8 mm, and make sure the number of bends are kept to a minimum o If you coil unused fiber cable, make sure coil diameter is at least 250 mm Avoid squeezing the fiber cable anywhere o One exception: if you are using probes without disc, the probe cable will need to be squeezed in the radial spacer, near the probe tip ▪ Warning: NEVER squeeze the tip itself!!!, this could damage the probe ▪ To avoid these problems, probes with discs are recommended! Make sure the tip of the probe is covered with pressboard material or crepe paper, to ensure that no oil is flowing in the immediate vicinity of the sensing element (flowing could unduly cool the sensor) Always test your probe with a suitable instrument (all Maschinenfabrik Reinhausen instruments can display % performance of probes); the MSENSE FO Test Unit is recommended for testing. Recommended values are 100% for probe alone and 65% for probe, feedthrough and extension cable. Testing should be done according to each manufacturer practices; however, it is recommended to test them at least 5 times during transformer manufacturing: o Incoming inspection o Probe installation in spacer o After spacer installation in winding o Before and after drying cycle o After tanking (from outside of tank, through the feedthrough and using an extension cable). 5.2.2 Probe connector cleaning When working with fiber optic, it is always very important to keep your connectors clean. This is the reason why all probes are supplied with “Isopropyl Alcohol Pre-Moistened Wipes”, that can be used to clean connectors in the field. With a moistened wipe, wipe the ST connector end in circle for a few seconds. Probes are always supplied with silicone caps, to insure their protection against dirt and other foreign material, such as grease, etc. You should train your workers, so they keep these caps on the probe connectors at all time, except with testing probes with an appropriate instrument (MSENSE FO Test Unit), or when you are ready to connect them to feedthroughs. The cleaning is illustrated here: 21 Document no. MAN0008-EN-R19-LE © Copyright Rugged Monitoring Inc. 5.2.3 Radial spacer preparation The following picture gives an example of a probe (with disc) installed in a radial spacer. The procedure given here will work well for spacers that have a minimum thickness of 3 mm. If you intend to install probes in thinner spacers, contact Maschinenfabrik Reinhausen for further information. The spacer should be machined as follows: Machine (or drill) a 9 mm diameter hole where calculated by your design engineers o Although not optimal, it would be acceptable in most cases to make the hole in the center of the spacer, as shown above o This hole should not be done if you are going to install a non-disc probe Machine or saw (with a band saw) a ~3 mm wide slot, as shown above o It is recommended to make the exit slot at an angle, as shown (20 to 30 o), as this causes fewer bending stresses as the fiber exits the spacer Optionally, you can wrap the spacer in crepe paper to ensure no oil flow is present near the sensor o This wrapping would be mandatory if you use the non-disc version of the probe Suggestion: for the non-disc version of the probe, you must be careful with: o Apply no pressure on the tip of the probe o Make sure the probe cable is well squeezed in the slot, to prevent it from getting out of the slot if the fiber cable is pull on by installers. Remember also that the Teflon sheathing of the cable will become softer at higher temperatures, so a good squeeze is recommended. To avoid these situations, the disc version of the probe is always recommended. If you need to use a spacer thicker than 3 mm, it is recommended to “construct” a spacer using multiple layers of pressboard material, with the middle pressboard being 3 mm thick (with a slot and hole where the probe would be installed). For example, for a 5 mm thick spacer, use 2 pieces of 1 mm thick material and 1 piece of 3 mm thick (with the probe in it). All pieces should be glued together, like a sandwich. Crepe paper wrapping is optional. Do not drill or saw a slot in the outer layers of the pressboard material (to insure no oil flow around the sensor). 5.2.4 Spacer installation in the winding As late as possible during your manufacturing process, a modified spacer (with pre-installed probe) should be installed to replace an existing spacer. Normally (subject to your design engineer calculations), this new spacer would be installed near 22 Document no. MAN0008-EN-R19-LE © Copyright Rugged Monitoring Inc. the top of the winding, where the winding hottest temperature is expected to occur. This would normally be between the first and second winding disk or second and third winding disk. You can use a wedge to help opening the winding to remove a spacer and to insert the new modified one. 5.2.5 Probe installation in other places Maschinenfabrik Reinhausen FO-Sensor probes are completely dielectric and are immune to electrical and magnetic fields. As such they are ideal for sensing temperatures in windings, so the resulting temperature data could be used to evaluate the degradation of the transformer insulation material over time. However, users may be interested sometime to install probes in other locations, such as: Core (yoke) temperature. In this case, one can pre-mount a probe in a pressboard sandwich, as described above. For installation in a cooling duct. Top oil. In this case, the probe should be mounted also in some sort of pressboard sandwich and held above a winding. Any other places, such as the steel internal structure, etc. 5.2.6 Fiber cable routing best practices When routing the fiber cables out of windings, one should pay attention to these 2 points: There must be some slack in the probe cable between any 2 anchoring points. Where the probe cable is anchored, they should make sure the cable is tightened up a bit loosely especially if crepe paper is used for doing this. 5.2.7 Probe testing The best way to test a probe is to measure its optical power performance. The MSENSE FO Test Unit is recommended for this purpose. When connected directly to a probe, the power reading should be 100%; if the reading is less than 100%, you should investigate immediately the probe installation in the winding and the fiber cable routing. For more information on probe and extension cable testing, refer to section 8.5 below. 5.2.8 Conclusion (probe installation). As we have demonstrated in this chapter, Maschinenfabrik Reinhausen probes can be mounted anywhere in a transformer, although their prime purpose would be to monitor hot-spot temperatures in windings. These probes, especially the version with disc, are very easy to use and are very robust; this should simplify their installation by the transformer manufacturer and ensure consistent and reliable temperature information for the transformer operator. 5.3 Feedthrough installation best practices This section presents the best practices involved in the installation of feedthroughs. A common problem regarding the installation of feedthroughs is leaking, normally due to insufficient tightening. Thread sealant is recommended Loctite 567 or 3M Rite-Lok PS67 or PS92 23 Document no. MAN0008-EN-R19-LE © Copyright Rugged Monitoring Inc. Apply a small quantity on the feedthrough tread before screwing it to the tank wall plate, as shown here: Before tightening: After tightening: Torque by “feeling” and by number of turns With NPT threads, it is not possible to specify a recommended torque value, so we need to proceed by “feeling” (just like all plumbers are doing) The suggested procedure is to hand tight the feedthrough and then add ~2 turns with a wrench fitted with a 14 mm socket You will need to apply substantial torque, especially if you are not using any sealant. A 30+ cm wrench is recommended. To avoid any problems regarding leaking, Maschinenfabrik Reinhausen offers a service whereby feedthroughs are pre- installed on the tank wall plate and are tested for leaks under pressure. 5.3.1 Feedthrough testing The best way to test the feedthroughs is to have them connected inside the transformer tank to their respective probes (a feedthrough cannot be tested by itself). Using the same technique as outlined in section 5.2.7 above, one can confirm that all probe-feedthrough combination work well if the power percentage reading is at least 65%. 5.3.2 Feedthrough connector cleaning Due to their bulkhead construction, feedthroughs are vulnerable to getting dirty. It is recommended to keep the supplied caps on both ends of the feedthrough at all time. As compare to probe connector cleaning (see section 5.2.7), feedthrough cleaning is a bit more complicated, but the idea is similar. You will need “Isopropyl Alcohol Pre-Moistened Wipes” (same as for connector cleaning) and cleaning swabs (normally supplied with the feedthroughs). The following 2 pictures show the procedure. 5.4 Tank wall plate (mounting flange) installation best practices This section presents the best practices involved in the installation of a tank wall plate (also called Mounting Flange). The plates are offered with various mounting options, either bolted or welded. Furthermore, the bolted version can be supplied with an O-ring or not; if the plate has no provision for an O-ring, then a user supplied gasket must be used. 24 Document no. MAN0008-EN-R19-LE © Copyright Rugged Monitoring Inc. The plate can be installed either on the wall of the transformer tank, or on the transformer top; the decision on its location depends on the transformer active part design; for designs where the active part is attached to the transformer top cover the tank wall plate would normally be located on the top of the transformer. However, for ease of access to the plate, it is better to have the plate located on the transformer wall, as in this case, it would not be necessary to shut down the transformer to access the feedthroughs inside de Interface Box. 5.4.1 Bolted wall plate installation best practices (with O-ring) These plates are supplied with a Viton O-ring. Make sure the O-ring groove is clean, and that the O-ring is well inserted in the O-ring groove. Make sure also that the mating surface on the transformer tank is clean and does not have scratches that could lead to eventual oil leaks. 8 bolts should be welded at the appropriate places, and mating nuts should be available. Prior to bolting the plate, make sure the O-ring is in its groove, to avoid pinching it when bolting the plate.. 5.4.2 Bolted wall plate installation best practices (without O-ring) To install this type of plate, the user must provide a gasket; normally, this gasket will be made of the same material as other gaskets on the same transformer.. 5.4.3 Welded wall plate installation best practices Here, to install the plate, the user will have to weld it to the transformer tank. Take note that the installation of the feedthroughs must on the plate must be done after the welding process, to avoid heat damages to the feedthroughs. 5.5 Extension cable installation best practices The purpose of the extension cables is to carry the optical signal available at the output of each feedthrough to the MSENSE FO instrument normally located inside the transformer marshaling cabinet. Extension cables must be protected to the environmental elements; the best way to do this is to run a metallic conduit (rigid or flexible) between the Interface Box and the Marshaling Cabinet; one tube should normally enough to accommodate at least 24 extension cable (minimum of ~5 cm diameter). The best way to pull the extensions through this tubing is to use a fish tape line. If you are using rigid tubing, it is recommended to use 90o elbows with an opening; this would allow you to pull the extension cables piecewise, pulling the extensions one section at a time. When pulling the cables, be careful to avoid any kinks along the way, as if the bending radius becomes smaller than about 3 mm at any given time it could snap the fiber inside and making this extension unusable. 5.5.1 Extension cable testing The testing of the extension should be done in the same way as one would test a probe. Its testing is only possible when a probe-feedthrough-extension-cable assembly is tested together (an extension cable cannot be tested by itself). Refer to the sections 5.2.7 and 5.3.1 for more information. 5.6 Interface Box installation best practices The purpose of the Interface Box is to protect the feedthroughs and extension cables from the environmental elements. The box is to be pierced on the bottom face so a gland can be installed and provide a way to interface to a metallic tube through which the extension cables will be routed; see section 5.5 for more information on extension cables. The box is intended to be bolted over a compatible tank wall plate (with threaded mounting holes); bolts are included with box package. The suggested torque for these mounting bolts is 5 lb-ft (~ 8 Nm). 25 Document no. MAN0008-EN-R19-LE © Copyright Rugged Monitoring Inc. 6 MSENSE FO MONITOR INSTALLATION This chapter contains an overview of: Mechanical installation Electrical wiring Fiber optic sensor connection Installation of USB driver (required to use the MSET-FO software) Making your first measurements. As each MSENSE FO instrument model is different, the information given below is presented in three different sections. Make sure you pick up the correct section as it is applicable to your instrument. 6.1 MSENSE FO ECU-S installation ( ) 6.1.1 MSENSE FO ECU-S mechanical installation The following drawings give all mechanical information that would be necessary to install the MSENSE FO ECU-S either in a transformer cabinet swing panel, or to bolt it on a recessed mounting plate. The MSENSE FO ECU-S instrument has the same enclosure irrespective of the total number of optical channels, up to 24. The details are shown here: When the MSENSE FO ECU-S has more than 6 optical channels, the display will scroll automatically, displaying 6 channels at a time. There is a LED on top of each display field which indicates which channel is currently being displayed. For the 24- channel version, all 24 channels will be shown after a total of 4 display cycles. In case of a system error, an additional cycle will display the error message. See section 8.1 for more information. 26 Document no. MAN0008-EN-R19-LE © Copyright Rugged Monitoring Inc. 6.1.2 MSENSE FO ECU-S electrical installation This drawing shows all electrical connections that are possible on a fully populated MSENSE FO ECU-S instrument. The following connectors are to be used by features that offered as options on the MSENSE FO ECU-S. These are: Relays 1-8 (connectors # 3 and 4); current must be limited to 5 Amp AC Analog outputs 1-8 (connectors 6 and 7) Ethernet, Copper RJ45 (connector 10) Ethernet, SFP module, fiber (connector 9). The small opening found on the right side of the instrument (as seen in the drawing above) reveals 2 features: A micro-USB connector, that can be used to connect to MSET-FO software A microSD memory card slot, where a SD card ( ) can be inserted to allow for in-instrument temperature logging3. Reading the SD card content can be done by removing the card from the instrument and reading it with a USB adapter on a PC computer. Data files can also be transferred to a PC using the MSET-FO software; however, this could be a long process for large files. When removing the card, it is suggested to stop the logging process by powering down the instrument (this is not mandatory but would be safer). If you have the Ethernet option AND have ordered from Maschinenfabrik Reinhausen a microSD memory card option, mirrored data logging will also be performed on the non-removable memory card present on the Ethernet board option. Removing and inserting the microSD card ( ) can be difficult as the card is a bit deep inside the MSENSE FO ECU-S enclosure. You can use small pliers to help extracting the card; be gentle with your pliers as not to damage the card. Mating connectors are supplied with the unit, when the corresponding options are present. 3 It is highly recommended to get your microSD memory cards ( ) from Maschinenfabrik Reinhausen, even if they are relatively expensive. The Maschinenfabrik Reinhausen cards feature a wide temperature range and are ruggedized, for demanding industrial applications. 27 Document no. MAN0008-EN-R19-LE © Copyright Rugged Monitoring Inc. The following guidelines should be followed when wiring the terminal blocks: Current and voltage should be limited to 5 A4 and 240 VAC (limited by relay specifications) Wire gauge range is 12-30 AWG (0.2 to 2.5 mm) Torque on screws should be 0.5 to 0.6 Nm (4.4 to 5.3 Lb-In) Recommended insulation stripping length: 7 mm When using stranded wires, crimped wire ferrules should be used to prevent loose strands from creating short circuits (recommended pin length: 8 mm). The relays 1-8 are completely general-purpose relays and are fully programmable by the user (with MSET-FO). They are Form-C relays, with a common terminal, a no (no = normally open) terminal and a nc (nc = normally closed) terminal. Take note that these relays are forced to stay in their non-energized state for a few seconds after the MSENSE FO ECU-S is powered up, during the processor boot-up time. The System Fault relay is a Form-A relay (2 contacts) that is “hard-wired” and not programmable by the user. It is energized or activated when the MSENSE FO ECU-S is running normally. This relay should be energized in less than one second after the MSENSE FO ECU-S is powered up. Grounding provision ( ) is included on the MSENSE FO ECU-S instrument; make sure it is connected to your system ground. 6.1.3 MSENSE FO ECU-S analog outputs The optional internal analog output option is easy to use; it is also very flexible. To configure them, you will need to run the MSET-FO software; see section 9.3.4 below. Here are some features, with some comments: Voltage outputs. You can select 0-5 V or 0-10 V. Please note that this requires a ground connection, so be careful with ground loops, which can easily affect the voltage readings. Current outputs. 4-20 mA is the industry norm. This is a better choice for industrial applications, as it is ground insulated (no ground loops). All outputs are completely programmable: o They are not “hard” assigned to any specific optical channel o One output can reflect the temperature values of many optical channels (e.g., minimum or maximum temperature read from many channels) o For each output, you can define the low and high temperatures (the difference between these two is called “span”) o With “Error Style”, you can define the behavior of the output if no temperature is read for that output. The most common setting is “Max Val” as this will simulate a high temperature in case of error. The following figure shows the Analog Outputs tab, from MSET-FO. You are referred to chapter 9 (MSET-FO) for clarifications on how to set the various parameters. 6.1.4 MSENSE FO ECU-S ethernet ports (option) The Ethernet option is normally offered with a copper standard RJ45 connector. This option adds the following functionalities to the MSENSE FO ECU-S: Support for IEC 61850 communication protocol 4 Current limitation for DC situations is much lower, in the order of 0.2 A at 240 VDC. 28 Document no. MAN0008-EN-R19-LE © Copyright Rugged Monitoring Inc. Support for Modbus over Ethernet communication protocol The IEC 60870-5-104 communication protocol (on Ethernet). Ethernet fiber communication is supported by adding an SFP module. More information on SFP module can be found on Wikipedia: https://en.wikipedia.org/wiki/Small_form-factor_pluggable_transceiver. Both Ethernet connections (RJ45 and fiber) can be used concurrently. This offers an unprecedented level of communication reliability. 6.2 MSENSE FO Test Unit installation ( ) The MSENSE FO Test Unit comes calibrated and ready to use. The figure, below, shows the main view of the MSENSE FO Test Unit, along with the top and side (where the electrical connections are available) views. You may need to connect it to a power source for a few hours to make sure the internal battery has enough charge to use it without power connection. Battery charging status ST connectors Micro-SD memory slot USB port ( 6.3 MSENSE FO ECU-I installation ( ) 6.3.1 MSENSE FO ECU-I mechanical installation The following drawings give all mechanical information that would be necessary to install the MSENSE FO ECU-I in your enclosure. The MSENSE FO ECU-I instrument has the same enclosure irrespective of the total number of optical channels, 8 or 12 for 200 µ probes, or 8 for 62.5 µ probes. The details are shown here: 29 Document no. MAN0008-EN-R19-LE © Copyright Rugged Monitoring Inc. There is one LED for each optical channel. These LEDs can take 4 states, as follows: OFF, channel is disabled Green, temperature is read normally, with a good optical signal Red, a temperature can be read but its power level is lower than 65%. See section 8.5 for more information on how to interpret this percentage value Flashing red, if no temperature can be read from this enabled channel (e.g., no probe or broken probe) To stop the flashing, use a good probe or disable this channel. 6.3.2 MSENSE FO ECU-I electrical installation This drawing shows all electrical connections that are possible on a fully populated MSENSE FO ECU-I instrument. 30 Document no. MAN0008-EN-R19-LE © Copyright Rugged Monitoring Inc. A microSD memory card slot, where a SD card ( ) can be inserted to allow for in-instrument temperature logging5. Reading the SD card content can be done by removing the card from the instrument and reading it with a USB adapter on a PC computer. Files can also be transferred to a PC using MSET-FO; however, this could be a long process for large files. When removing the card, it is suggested to stop the logging process by powering down the instrument (this is not mandatory but would be safer). Mating connectors (terminal blocks) are supplied with the unit, when the options are present. The following guidelines should be followed when wiring the terminal blocks: Current and voltage should be limited to 5 A6 and 240 VAC (limited by relay specifications) Wire gauge range is 12-30 AWG (0.2 to 2.5 mm) Torque on screws should be 0.5 to 0.6 Nm (4.4 to 5.3 Lb-In) Recommended insulation stripping length: 7 mm When using stranded wires, crimped wire ferrules should be used to prevent loose strands from creating short circuits (recommended pin length: 8 mm). 5 It is highly recommended to get your microSD memory cards ( ) from Maschinenfabrik Reinhausen, even if they are relatively expensive. The Maschinenfabrik Reinhausen cards feature a wide temperature range and are ruggedized, for demanding industrial applications. 6 Current limitation for DC situations is much lower, in the order of 0.2 A at 240 VDC. 31 Document no. MAN0008-EN-R19-LE © Copyright Rugged Monitoring Inc. The System Fault relay is a Form-C relay (3 contacts) that is “hard-wired” and not programmable by the user. It is energized or activated when the MSENSE FO ECU-I is running normally. In normal operating conditions, this relay should be energized in less than one second after the MSENSE FO ECU-I is powered up. Grounding provision ( ) is included on the MSENSE FO ECU-S instrument; make sure it is connected to your system ground. 6.3.3 RS-485 serial port A serial RS-485 port found on some of the MSENSE FO instruments ( and ) is intended to be used as a slave port (Modbus, and IEC 60870-5-101 or DNP 3.0 for the MSENSE FO ECU-S instrument, ). You can configure its parameters (baud rate, parity, etc.) with the MSET-FO. This port is ground insulated, except for the Test Unit instrument. The port can be configured either as a 2W configuration (half-duplex, 2 wires) or as a 4W configuration (full-duplex, 4 wires). The mating connector (included with the instrument) is Phoenix part # 1827622, or Digikey part # 277-8837-ND. Contact Maschinenfabrik Reinhausen for more information. Recommendation: It is strongly suggested to use an insulated interface to connect the Modbus communication to a PC computer. Maschinenfabrik Reinhausen recommends the use of Model USOPTL4, available from B&B Electronics (web site: http://www.bb-elec.com/USOPTL4), or equivalent. Recommendation: It is strongly suggested to install two termination resistors (120 Ω), one at each end of the communication cable; this is especially important when working with a long cable and at high baud rate. The following drawings show examples of typical wirings for a Modbus communication scheme (4W and 2W). 32 Document no. MAN0008-EN-R19-LE © Copyright Rugged Monitoring Inc. 6.4 Testing your RS-485 serial connection 6.4.1 Testing your Modbus connection ModScan can be a very useful tool to exercise your RS-485 serial Modbus connection. Please note that using ModScan is only a suggestion; there exists other solutions in the market and you are free to use them as you wish. You can download it from here: https://www.win-tech.com/html/demos.htm; it can be used free of charge for up to 30 days, after which you will need to buy it from WinTech. You will need to know the COMx port number for your serial port. The easiest way to do this is to invoke Device Manager on your PC, as shown here (which is COM4 for this example): Please note that the Ports entry in the list (as shown above) will appear only if a serial port is detected by your Windows operating system. The above example confirms that the serial port is COM4; take note of this information as you will need it to connect to ModScan. Take note that you will probably have to load a serial driven which is different that the one described in section 9.1.1.1 below. This means that your MSENSE FO will need 2 different serial COM port for communication: One for USB communication ( ) One for Modbus communication. Select Connection from the top tool bar of ModScan and then Connect, to get this setup window: 33 Document no. MAN0008-EN-R19-LE © Copyright Rugged Monitoring Inc. The following window appears. In this example, we are displaying 8 temperature values (see figure below); to do this, make sure these parameters are set correctly: Address. The address for temperature Channel # 1 is hex 0181 (see Chapter 10 for a complete Modbus register description), or dec 385. As ModScan counts register starting at 1 (not 0), then you need to add 1 to 385. Thus, the starting address is 386, in this example here. Length. As we want to read 8 channels, this should be 8. Device Id. This is the instrument identification (node address); it should be a number between 1 and 247. It must match the id that you have given to an instrument; use MSET-FO to set this id. Modbus register type. The temperature values are “Input Register” type registers. Note that displayed temperature values are multiplied by 100, as shown in the figure. A value of -302 means that this channel is disabled and -303 means that no probe was detected for that channel. Note also that only 2 probes (channels 2 & 3) were connected here. 6.4.2 Testing your IEC 60870-5-101 serial connection ( ) As an alternative to Modbus, you can use IEC 60870-5 protocol for data exchange over the RS-485 port. Refer to the table in chapter 12 for IEC 60870-5 data structure. 6.4.3 Testing your DNP 3.0 serial connection ( ) As an alternative to Modbus, you can use DNP 3.0 protocol for data exchange over the RS-485 port. Refer to the table in chapter 12 for DNP 3.0 data structure. 34 Document no. MAN0008-EN-R19-LE © Copyright Rugged Monitoring Inc. 6.5 Using the MSENSE FO instrument for the first time To make your first temperature measurements, do as follows: Remove the dust cap on the optical connectors of the MSENSE FO instrument. Remove the dust cap on the probe connectors. Insert each probe connector into a sensor connector on the MSENSE FO. Make sure the two mating parts are properly aligned and twist the connector clockwise to fasten it securely. Notice: Do not apply force on this connector! Apply power to the MSENSE FO (24 to 48 VDC for the ECU-I and ECU-S instruments, or 5V USB power for the Test Unit, ) Within a few seconds, your instrument will display temperatures values, or for the MSENSE FO ECU-I model, the LEDs corresponding to the optical channels where there is a probe will turn green. With model MSENSE FO ECU-I, you will need the MSET-FO software to get temperature values; refer to chapter 9. 35 Document no. MAN0008-EN-R19-LE © Copyright Rugged Monitoring Inc. 7 MAINTENANCE AND TROUBLESHOOTING The MSENSE FO instruments are designed so no periodic maintenance is required. Once installed in a marshalling cabinet, it is highly recommended not to disconnect or connect the extension cables connected to the MSENSE FO instrument. After installation, this instrument will not require any maintenance. All MSENSE FO instruments do not contain any user replaceable or serviceable by the end-user. In case of problems, you are urged to contact our service department; see section 2.3.5. The following tables give answers to most common problems. 7.1 MSENSE FO ECU-S instrument ( ) Power LED off External 24-48 VDC power is absent 3-pin power connector is plugged in the wrong socket Alarm LED is on (fault relay) The instrument does not start Try to power it off and on again (after a few seconds) No temperature data is displayed No probe is detected Make sure your instrument is designed to support the diameter of probes being tested (62.5 or 200 µ) Verify the whole probe connection link (probe, feedthrough, and extension cable) Try to clean all optical connectors Make sure this channel is not disabled Optical power percentage is Probe optical signal is weak below 65% Try to clean all optical connectors Modbus communication does not Make sure instrument Modbus communication parameters are work correctly set (baud rate, parity and node address) Make sure cabling is correct USB communication does not FTDI serial driver is not install or not install correctly. work Try to reinstall the driver. See section 9.1.1.1 Logging does not work Micro-SD card may be corrupted. Try reading the card on a PC, and Windows will suggest repairing the file system in case of corruption. 7.2 MSENSE FO Test Unit instrument ( ) Power LED off External 5 VDC power is absent and battery is discharged No temperature data is displayed No probe is detected Make sure your instrument is designed to support the diameter of probes being tested (62.5 or 200 µ) Verify the whole probe connection link (probe, feedthrough, and extension cable) Try to clean all optical connectors Make sure this channel is not disabled 36 Document no. MAN0008-EN-R19-LE © Copyright Rugged Monitoring Inc. Optical power percentage is Probe optical signal is weak below 65% Try to clean all optical connectors Modbus communication does not Make sure instrument Modbus communication parameters are work correctly set (baud rate, parity and node address) Make sure cabling is correct USB communication does not FTDI serial driver is not install or not install correctly. work Try to reinstall the driver. See section 9.1.1.1 Logging does not work Micro-SD card may be corrupted. Try reading the card on a PC, and Windows will suggest repairing the file system in case of corruption. 7.3 MSENSE FO ECU-I instrument ( ) Power LED off External 24-48 VDC power is absent 3-pin power connector is plugged in the wrong socket Alarm LED is on The instrument does not start Try to power it off and on again (after a few seconds) Channel LED is off for a given No probe is detected channel Make sure your instrument is designed to support the diameter of probes being tested (62.5 or 200 µ) Verify the whole probe connection link (probe, feedthrough, and extension cable) Try to clean all optical connectors Make sure this channel is not disabled Channel LED is red for a given Probe optical signal is weak channel Try to clean all optical connectors Modbus communication does not Make sure instrument Modbus communication parameters are work correctly set (baud rate, parity and node address) Make sure cabling is correct USB communication does not FTDI serial driver is not install or not install correctly. work Try to reinstall the driver. See section 9.1.1.1 Logging does not work Micro-SD card may be corrupted. Try reading the card on a PC, and Windows will suggest repairing the file system in case of corruption. 37 Document no. MAN0008-EN-R19-LE © Copyright Rugged Monitoring Inc. 8 MSENSE FO THERMOMETER HARDWARE REFERENCE 8.1 MSENSE FO ECU-S reference ( ) 8.1.1 Display and keypad description The display can show 7 different menu screens. You can navigate from one to the next by pressing the “Menu” key. 4 keys are available to navigate through the various menu screens, as follows: MENU key. This allows for cycling through the menus or to return from sub-menu back to its parent menu. UP / DOWN arrow keys. Use these to change the value of configuration parameters, when that