MSENSE® DGA 9 Installation and Operating Instructions PDF
Document Details
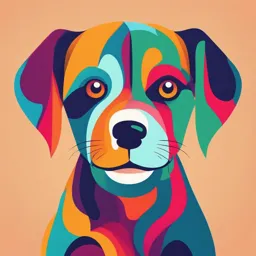
Uploaded by FunnyTriumph
2022
Tags
Summary
This document provides installation and operating instructions for the MSENSE® DGA 9 oil analysis device. It covers safety, installation procedures, and device operation details. The document is aimed at professional users.
Full Transcript
Online – Oil analysis MSENSE® DGA 9 Installation and Operating Instructions 7045899/03 EN – 06.2022 Your contact for all inquiries about the MSENSE® DGA 9: MR Service & Complaint Maschinenfabrik Reinhausen GmbH Falkensteinstraße 8 93059 Regensburg Germany service@reinhausen.com complaint@reinhause...
Online – Oil analysis MSENSE® DGA 9 Installation and Operating Instructions 7045899/03 EN – 06.2022 Your contact for all inquiries about the MSENSE® DGA 9: MR Service & Complaint Maschinenfabrik Reinhausen GmbH Falkensteinstraße 8 93059 Regensburg Germany service@reinhausen.com complaint@reinhausen.com If required, you will receive at this address more information about the product and issues this technical document. The MSENSE® DGA 9 will be available for the Maschinenfabrik Reinhausen GmbH manufactured by: EMH Energie-Messtechnik GmbH Vor dem Hassel 2 D-21438 Brackel Germany MTE Meter Test Equipment AG Landis + Gyr-Strasse 1 CH-6300 Zug Switzerland Copyright MTE Meter Test Equipment AG All rights reserved The contents of this publication can be modified without prior notice. The greatest care has been taken with the preparation of texts, illustrations and programs. Nevertheless, MTE Meter Test Equipment AG cannot be held legally responsible for any remaining faulty specifications nor accept any liability for these. List of contents 1. Introduction................................................................................................................................ 4 Contact................................................................................................................................. 4 Revision Rights..................................................................................................................... 4 Completeness....................................................................................................................... 4 Legal provisions.................................................................................................................... 5 Safety Guidelines................................................................................................................. 5 2. Safety.......................................................................................................................................... 6 Intended Use........................................................................................................................ 6 Basic safety instructions....................................................................................................... 6 Qualification of the staff........................................................................................................ 8 Personal protective equipment............................................................................................. 9 IT security........................................................................................................................... 10 3. General information................................................................................................................. 11 4. Mountinginstructions.............................................................................................................. 12 Installation position............................................................................................................. 12 Safety notes on installation................................................................................................. 13 Heating.................................................................................................................................. 13 Preparing installation.......................................................................................................... 17 4.3.1 Mechanical connection................................................................................................ 17 4.3.1.1 Flange connection................................................................................................ 17 4.3.1.2 Threaded joint...................................................................................................... 17 4.3.2 Supply voltage connection........................................................................................... 18 4.3.3 Tools required............................................................................................................. 18 4.3.4 Sealing of the connecting thread................................................................................. 18 4.3.4.1 Thread sealing tape.............................................................................................. 18 4.3.4.2 Thread adhesive................................................................................................... 19 4.3.4.3 Flat gasket............................................................................................................ 19 Installation.......................................................................................................................... 20 4.4.1 Mechanical installation................................................................................................. 20 4.4.1.1 Direct mounting.................................................................................................... 20 4.4.1.2 Indirect mounting.................................................................................................. 37 4.4.2 Electrical connection.................................................................................................... 43 4.4.3 Initial start-up............................................................................................................... 46 4.4.4 Turn off the device....................................................................................................... 48 4.4.5 Automatic activation following the interruption of the supply voltage............................ 49 5. Hardware components............................................................................................................ 50 Internal front view with controls........................................................................................... 50 View of rear........................................................................................................................ 51 Connections for the measuring and controller card............................................................. 53 5.3.1 Configuration of relay output 1 with coding bridge 1 (J1)............................................. 57 Extraction menu...................................................................................................... 64 5.4.1 Hardware components................................................................................................. 65 6. Device firmware....................................................................................................................... 68 General information............................................................................................................ 68 MSENSE® DGA 9 7045899/03 EN – 06.2022 Page 1 6.1.1 Main screen................................................................................................................. 68 Process flow....................................................................................................................... 69 6.2.1 Zero measurement...................................................................................................... 70 6.2.2 Vacuum generation..................................................................................................... 71 6.2.3 Leak testing................................................................................................................. 72 6.2.4 Filling level L1.............................................................................................................. 73 6.2.5 Degasing..................................................................................................................... 74 6.2.6 Filling level L2.............................................................................................................. 75 6.2.7 Gas measurement....................................................................................................... 76 6.2.8 Ventilation.................................................................................................................... 77 6.2.9 Draining....................................................................................................................... 78 6.2.10 Ventilation.................................................................................................................... 78 6.2.11 Waiting (only when switching from measurement cell # 2 to measurement cell # 1).... 79 Operation by means of device keyboard............................................................................. 80 6.3.1 Cursor keys................................................................................................................. 80 6.3.2 “Home” key.................................................................................................................. 80 6.3.3 Alphanumeric keypad.................................................................................................. 80 6.3.4 Contrast settings.......................................................................................................... 81 Main menu.......................................................................................................................... 82 Extraction status...................................................................................................... 83 6.5.1 Acknowledge fault............................................................................................ 86 6.5.2 Deactivate device (“unmount”).......................................................................... 86 6.5.3 Activating the device (“mount”)......................................................................... 86 Gas-in-oil measurements......................................................................................... 87 6.6.1 Graph view....................................................................................................... 88 6.6.2 Table view........................................................................................................ 89 Duval triangle.......................................................................................................... 90 Alarm / Alarm history............................................................................................... 90 6.8.1 Alarm acknowledegement................................................................................ 92 6.8.2 Alarm settings of the selected alarm................................................................. 92 Device settings........................................................................................................ 93 6.10.1 Transformer-related settings............................................................................. 94 6.10.1.1 DGA adjustment........................................................................................ 94 6.10.2 Settings – analogue outputs.............................................................................. 95 6.10.3 Alarm limits and alarm sources......................................................................... 97 6.10.3.1 Create new alarm...................................................................................... 98 MSENSE® DGA 9 7045899/03 EN – 06.2022 Page 2 6.10.3.2 Alarm settings............................................................................................ 99 6.10.4 MSENSE® DGA Settings................................................................................ 102 6.10.4.1 DGA measurement cycle interval............................................................ 103 6.10.4.2 Test digital outputs.................................................................................. 104 6.10.4.3 Device options......................................................................................... 105 6.10.4.4 Date, time, clock settings......................................................................... 107 6.10.4.5 Communication / Interfaces..................................................................... 109 7. Modbus Function, register and address mapping.............................................................. 122 MODBUS TCP.................................................................................................................. 125 MODBUS Serial Communication Adapter Example.......................................................... 125 7.9.1 MODBUS RS232 ASCII with Modpoll (RS232 for service purposes only).................. 125 7.9.2 MODBUS / RTU on RS485 bus (with Modpoll).......................................................... 126 8. RS 485 Wiring........................................................................................................................ 128 RS485.............................................................................................................................. 128 Termination, working point setting, earthing and protection of the RS485 bus.................. 128 9. Troubleshooting.................................................................................................................... 129 Extraction chamber fault................................................................................................... 129 9.1.1 Brief instructions on site............................................................................................. 129 9.1.2 Brief instructions by way of remote diagnosis............................................................ 129 9.1.3 Gas extraction principle............................................................................................. 130 9.1.3.1 Extraction cycle.................................................................................................. 130 9.1.3.2 Device activation................................................................................................ 130 9.1.4 Fault.......................................................................................................................... 130 9.1.5 Fault – Signalling....................................................................................................... 131 9.1.6 Faults – Analysis and acknowledgement options....................................................... 131 9.1.6.1 Reading out service data.................................................................................... 131 9.1.6.2 Brief instruction on reading out service data....................................................... 132 9.1.6.3 On-site fault analysis.......................................................................................... 132 9.1.6.4 Fault - Extraction status menu............................................................................ 132 9.1.6.5 Fault – Acknowledgement by hand..................................................................... 133 9.1.6.6 Fault – Acknowledgement via command file....................................................... 133 9.1.7 MSET DGA Service Tool........................................................................................... 134 9.1.7.1 Distribution / Installation...................................................................................... 134 9.1.7.2 System requirements.......................................................................................... 134 9.1.7.3 Sequence diagnostics – Data read..................................................................... 134 9.1.7.4 Connection and start.......................................................................................... 134 9.1.7.5 Interface selection.............................................................................................. 135 10. Technical specifications....................................................................................................... 139 11. Dimensions MSENSE® DGA 9............................................................................................... 141 Dimensions gate valve / ball valve connection.................................................................. 142 11.1.1 Pipe thread G 1½” DIN ISO 228-1............................................................................. 142 11.1.2 Pipe thread 1½” NPT ANSI B 1.20.1.......................................................................... 142 MSENSE® DGA 9 7045899/03 EN – 06.2022 Page 3 1. Introduction This technical file contains detailed descriptions to safely and properly install, connect, commission, and monitor the product. The target group of this technical document is exclusively specially trained and authorized specialist personnel. Contact Your contact for all inquiries about the MSENSE® DGA 9: MR Service & Complaint Maschinenfabrik Reinhausen GmbH Falkensteinstraße 8 93059 Regensburg Germany service@reinhausen.com complaint@reinhausen.com If required, you will receive further information on the product and issues of this technical document at this address. The MSENSE® DGA 9 is manufactured for Maschinenfabrik Reinhausen GmbH by: EMH Energie-Messtechnik GmbH Vor dem Hassel 2 D-21438 Brackel Germany MTE Meter Test Equipment AG Landis + Gyr-Strasse 1 CH-6300 Zug Switzerland Revision Rights The information contained in this technical document is the technical specifications released at the time of printing. Significant changes will be reflected in a new edition of the technical file. Document name and version number of this technical document can be found in the footer. Completeness This technical document is only complete together with the other applicable documents. The following documents apply to this product: Installation and Operating Instructions MSENSE® DGA 9 (this document) Operating Instructions MSET DGA Software Test report MSENSE® DGA 9 7045899/03 EN – 06.2022 Page 4 Legal provisions Trademark Microsoft, Microsoft Windows are either registered trademarks or trademarks of Microsoft Corporation in the United States and / or other countries. All other trademarks, registered trademarks, service marks and trade names are the property of their respective owners. Disclaimer After the editorial deadline of this documentation, the product may have changed. The information in this document is subject to change without notice and does not constitute an obligation of Maschi- nenfabrik Reinhausen GmbH. Changes to the technical data or design changes and changes to the scope of delivery are expressly reserved. The data and illustrations contained in this document, which expressly refer to third-party devices and equipment, are not binding. In principle, the information and agreements reached when processing the respective offers and orders are binding. The original operating instructions were cre- ated in German. Maschinenfabrik Reinhausen GmbH assumes no responsibility for any errors that may occur in this operating manual prepared by the manufacturer. If you have suggestions for improvement or changes or have found errors in this manual, please inform us. No part of this document may be reproduced in any form or by any means, electronic or mechanical, including photocopying, without the express writ- ten permission of Maschinenfabrik Reinhausen GmbH and the manufacturer. All rights reserved. Safety Guidelines This manual contains notices that you must observe in the interests of your own personal safety and to avoid damage to property. The instructions for your personal safety are marked by a warning triangle. Those who only refer to the prevention of property damage have no warning triangle. The warnings are displayed in decreasing order of severity according to the respective hazard level. Death or serious injury will result if proper precautions are not taken. Property damage can occur if the appropriate precautionary measure is not taken. An undesirable result or condition may occur if the corresponding note is ignored. In cases where two or more levels of danger apply, only the most severe level warning is used on its own. A warning with a warning triangle refers primarily to possible personal injury. But it can also mean property damage at the same time. For the personal safety of the installation and operating personnel, please observe and follow the safety instructions in the chapter of this manual! MSENSE® DGA 9 7045899/03 EN – 06.2022 Page 5 2. Safety This technical file contains detailed descriptions to safely and properly install, connect, commission, and monitor the product. Read this technical document carefully to familiarize yourself with the product. This technical document is part of the product. Read and pay special attention to the safety instructions in this chapter. Observe the warnings in this technical file in order to avoid dangers arising from the operation. The product is manufactured according to the state of the art. Nonetheless, dangers to the life and limb of the user or impairments of the product and other material assets may occur due to functional use. Intended Use The MSENSE® DGA is intended exclusively for use in systems and facilities of electrical power engi- neering. It is used for the early detection and reporting of evolving, potentially harmful trends in the monitored equipment (e.g., transformer) by measuring the concentration of gases and moisture in the equipment's insulating oil. The device is not designed and is not capable of detecting very fast developing faults and thus not intended to protect the device from such faults (e.g., by shutting down). For this purpose, please use safety devices designed for this purpose. Proper use and compliance with the conditions and conditions specified in this technical file as well as the warnings contained in this technical documentation and on the product do not pose a risk to per- sons, property and equipment Environment. This applies over the entire service life, from delivery to assembly and operation to dis- assembly and disposal. The intended use is as follows: Operate the product according to this technical document, the agreed terms of delivery and the technical data. Make sure that all necessary work is done by qualified personnel only. Use the devices supplied only for the intended purpose and in accordance with the specifica- tions of this technical document. Observe the notes in this technical document for electromagnetic compatibility and the technical data.Safety Basic safety instructions In order to prevent accidents, breakdowns, accidents and environmental damage, the person respon- sible for the transport, installation, operation, maintenance and disposal of the product or parts of the product must ensure that: MSENSE® DGA 9 7045899/03 EN – 06.2022 Page 6 Personal protective equipment Loosely worn or unsuitable clothing increases the risk of being caught or wound on rotating parts and the danger of getting caught on protruding parts. This poses a danger to life and limb. All necessary equipment as well as the personal protective equipment required for the respec- tive activity such. As a helmet, protective work shoes, etc. wear. Observe the section "Personal protective equipment". Never wear damaged personal protective equipment. Never wear rings, necklaces and other jewellery. For long hair wear hairnet. Workspace Disarray and unlit work areas can lead to accidents. Keep the work area clean and tidy. Make sure the work area is well lit. Comply with applicable accident prevention legislation in the country. Explosion protection Highly flammable or explosive gases, vapours and dusts can lead to severe explosions and fire. Do not mount and operate the product in potentially explosive atmospheres. safety information Warning labels and safety labels are safety labels on the product. They are an important part of the security concept. Safety markings are shown and described in the chapter "Product description". Observe all safety labels on the product. Keep all safety labels on the product complete and legible. Replace damaged or obsolete safety markings. Environmental conditions To ensure reliable and safe operation, the product must only be operated under the ambient conditions specified in the technical data. Observe specified operating conditions and site installation requirements. Changes and conversions Unauthorized or improper modifications of the product may result in personal injury, property damage or malfunction. Change product only after consultation with Maschinenfabrik Reinhausen. Spare Parts Spare parts not approved by Maschinenfabrik Reinhausen can lead to personal injury and property damage to the product. Use only replacement parts approved by the manufacturer. Contact Maschinenfabrik Reinhausen. Working in the company The product may only be operated in perfect working order. Otherwise there is danger to life and limb. Check safety devices regularly for their functionality. MSENSE® DGA 9 7045899/03 EN – 06.2022 Page 7 The inspection work described in this technical file perform regularly. Qualification of the staff The person responsible for installation, commissioning, operation, maintenance and inspection must ensure adequate qualification of the personnel. Electrician The qualified electrician has knowledge and experience as well as knowledge of the relevant standards and regulations due to their professional training. In addition, the electrician has the following skills: The electrician independently identifies possible dangers and is able to avoid them. The electrician is able to carry out work on electrical installations. The electrician is specially trained for the working environment in which she works. The electrician must comply with the provisions of the applicable accident prevention legisla- tion. Electrically trained persons A person trained in electrical engineering is instructed and instructed by a qualified electrician about the tasks assigned to him and possible dangers of improper behaviour, as well as protective devices and protective measures. The person trained in electrical engineering works exclusively under the di- rection and supervision of a qualified electrician. Operator The operator uses and operates the product within the scope of this technical document. He is informed and trained by the operator about the special tasks and the possible dangers of improper behaviour. Technical service It is strongly recommended that installations, maintenance, repairs and retrofits be carried out by our technical service. This ensures the professional execution of all work. If work is not carried out by the Maschinenfabrik Reinhausen technical service, it must be ensured that the personnel are trained and authorized by Maschinenfabrik Reinhausen. MR Service & Complaint Maschinenfabrik Reinhausen GmbH Falkensteinstraße 8 93059 Regensburg Germany service@reinhausen.com complaint@reinhausen.com MSENSE® DGA 9 7045899/03 EN – 06.2022 Page 8 Personal protective equipment At work, personal protective equipment is required to minimize health hazards. Always wear the necessary protective equipment during work. Never wear damaged protective equipment. Follow instructions in the work area for personal protective equipment. Basically to be worn protective equipment Protective clothing Close-fitting work wear with low tear resistance, with tight sleeves and no protruding parts. It is mainly used to protect against being caught by moving machine parts. Safety shoes To protect against heavy falling parts and slipping on slippery surfaces. Special protective equipment in special ambient conditions Safety goggles To protect the eyes from flying parts and liquid splashes. Face Shield To protect the face from flying parts and liquid splashes or other dangerous sub- stances. Helmet To protect against falling and flying parts and materials. Ear protection To protect against hearing damage. Protective gloves For protection against mechanical, thermal and electrical hazards. MSENSE® DGA 9 7045899/03 EN – 06.2022 Page 9 IT security Observe the following recommendations for the safe operation of the product. Make sure that only authorized persons have access to the device. Use the device only within an electronic security perimeter (ESP). Make sure that the device is operated only by trained personnel who are sensitized to IT secu- rity. All protocol interfaces (Modbus, DNP3 and IEC 61850) have read-only access to the MSENSE® DGA 9. A change of parameters or data is not possible. Access to the parameterisation via the MSET parameterisation software can be protected by passwords. Change the passwords on a regular basis. Observe the notes on access authorisations, user levels and password settings in the operating in- structions for the MSET parameterisation software. MSENSE® DGA 9 7045899/03 EN – 06.2022 Page 10 3. General information The MSESNE DGA 9 device is a permanently installed multiple “gas-in-oil” analysis system. It enables the individual measurement of oil moisture (H2O) and the key gases dissolved in the oil: hydrogen (H2), carbon monoxide (CO), carbon dioxide (CO2), methane (CH4), acetylene (C2H2), ethylene (C2H4), ethane (C2H6) and oxygen (O2). While hydrogen (H2) occurs in almost every fault in the insulation system of power transformers and carbon monoxide (CO) is a sign of problems with cellulose / paper insulation, the presence of or in- crease in acetylene (C2H2) and ethylene (C2H4) serves to classify faults such as overheating, partial discharge or high energy arcing. Oxygen (O2) is an indicator of damage to the sealing of hermetically sealed transformers. The key advantages Individual measurements of hydrogen (H2), carbon monoxide (CO), carbon dioxide (CO2), me- thane (CH4), acetylene (C2H2), ethylene (C2H4), ethane (C2H6) and oxygen (O2). Measurement of oil moisture (H2O) Communication interfaces ETHERNET 10/100 Mbit / s (copper / RJ45 or fibre optic / SC du- plex) and RS485 to support the transmission protocols MODBUS® RTU / ASCII, MODBUS® TCP as well as the proprietary protocol. Optional on-board DNP3 serial modem for connection to a process control system (SCADA) using communication protocol DNP3. Optional on-board IEC 61850 modem for communication with substations by means of com- munication protocol IEC 61850. This device may only be used in accordance with the instructions in this man- ual. If this device is used in a way not specified by the manufacturer, the guaran- tee can expire and impair the protection to be determined by the measuring device. The device manufacturer does not accept any liability for property damage or personal injury resulting from improper use or non-observance of the safety in- structions. MSENSE® DGA 9 7045899/03 EN – 06.2022 Page 11 4. Mountinginstructions Installation position The installation location is very important for the correct function of the MSENSE ® DGA 9. There are three possible installation locations in the case of a typical transformer: Pos. 1 Cooler return line: Install the MSENSE® DGA 9 on a straight pipe section at the connection between the un- derside of the cooler and the transformer tank. To avoid vacuum the device must always be mounted on the discharge side (beyond the elbow) of the circulation pump. Remark: Only choose this location if constant oil flow through the cooling system is guaranteed. Pos. 2 Drain valve transformer tank: The flange of the drain valve must be fitted at a minimum height of 40 cm for the MSENSE® DGA 9 to be installed. Pos. 3 Upper filling valve: This position may only be used if the oil level is at least 100 cm higher than the centre of the device flange. However, it is not recommended since it is difficult to operate or read the device in this position. Pos. 4 Never install the MSENSE® DGA 9 above the cooler or on the intake side of the pump! Remark: There must be good and constant oil circulation available at the installation location. MSENSE® DGA 9 7045899/03 EN – 06.2022 Page 12 Safety notes on installation The following safety notes must be strictly followed during installation. Otherwise no warranty claims can be made. Never remove the protective cap of the connecting thread before you are ready to install the device at the transformer valve. This cap protects the connection unit from damage by dust and other foreign matter. In addition, it protects the connecting thread and/or the adapter. Remark: Use the protective cap provided after you have dismantled the device as well. Device cap Only trained personnel may remove the device protective cover; the power supply must be switched off before the device protective cover is removed! Danger due to hazardous voltage. Heating Do not lay external cables above the heating units, as in this case, temperatures of up to approx. 80°C can occur in the event of a fault! Danger through heat. Never close the ventilation opening for the oxygen supply. These are lo- cated on the underside of the device's protective hood and on the device's back plate. Never use and / or store hydro-carbonaceous compounds in the vicinity of the measurement cell. Never clean the MSENSE® DGA 9 with solvent, as the gases severely affect the measurement accuracy and sensitivity of the sensors. Use only a dry cloth to clean this device! MSENSE® DGA 9 7045899/03 EN – 06.2022 Page 13 Never expose the connecting unit to vacuum. A vacuum can cause problems during the filling process. Before every gas release or filling of the transformer, remove the MSENSE® DGA 9 from the transformer valve. Alternatively, you can close the transformer valve. Never operate the MSENSE® DGA 9 on a close transformer valve for longer periods. Please remove the device if this can not be prevented. Always heed the removal instructions. Never install the MSENSE® DGA 9 on the intake side of the cooling system pump! The MSENSE® DGA 9 may only be installed at a position that is at least 100 cm below the oil filling level. Never install the MSENSE® DGA 9 on a knee pipe or pipe bend! Turbulence in pipe bends can result in a vacuum that can cause problems on the device. Never install or remove the MSENSE® DGA 9 without opening the aera- tion screw first! Never mount the MSENSE® DGA 9 on galvanised connections or valves! Galvanised connections or valves can react with the oil, which can lead to erro- neous readings. Never use a high-pressure cleaner to clean the MSENSE® DGA 9! High pressure cleaners used to clean the transformer could cause serious damage to the MSENSE® DGA 9. MSENSE® DGA 9 7045899/03 EN – 06.2022 Page 14 Never use multiple slip-joint pliers. The use of such tools can damage the surfaces of the connection unit and those of the connecting thread. Use an M55 open-ended spanner or a 1½" ad- justable spanner. Note!!! Incorrect or improper handling of the connection unit, such as vacuum, paint or solvent, will lead to expiry of the warranty claim. The device may only be mounted and operated in restricted working ar- eas which are not freely accessible! Safety gloves must be worn during mounting of the device. If the unit is to be installed over 1 m, the use of personal protective equipment to prevent falling and specially trained personnel are neces- sary. The high weight means two people are required for mounting the unit. Use lifting equipment. This avoids undesired movement during installa- tion The device may only be mounted by a specialist MSENSE® DGA 9 7045899/03 EN – 06.2022 Page 15 During mounting and removal leakage of any hazardous substances to the environment must be avoided. Collect pollutants directly at the outlet points. MSENSE® DGA 9 7045899/03 EN – 06.2022 Page 16 Preparing installation A visual inspection must be carried out on the device before installation. For this purpose, unscrew the two knurled screws and then remove the device protective cover. All the connector plugs, cables and hoses must be connected. 4.3.1 Mechanical connection The connection device of the MSENSE® DGA 9 has an external thread of the type G 1½"’ ISO DIN 228-1 or 1½" NPT ANSI B 1.20.1 (must be specified on the order). The MSENSE® DGA 9 should be installed on a gate valve with full passage or on a ball valve on the transformer. These stop valves usually have a blind flange fitted. For this reason, they must be retrofitted before installation with a suitable threaded flange, connecting adapter or threaded joint. This results in 2 different types of installation. 4.3.1.1 Flange connection The MSENSE® DGA 9 is screwed directly to the threaded flange, i.e. the device is turned around its own axis in order to be fixed in place. This type of installation requires free space measuring 430 mm in diameter around the centre of the connecting flange. Remark: The thread depth of the threaded flange or the connecting adapter should be at least 25 mm. 4.3.1.2 Threaded joint We recommend connecting the MSENSE® DGA 9 by a threaded joint (flat sealing) on the gate valve/ball valve. This threaded joint, also known as a fitting, is made up of a threaded flange, a flat- sealing insert and a union nut. In this case, the device is not turned during installation, rather the union nut is turned to fix the device in place. A flat gasket is used for this. Additional sealing of the thread using thread sealing tape or thread adhesive is not necessary in this case, or only rarely. Remark: Some ball valves also have union nuts (pump ball valve). MSENSE® DGA 9 7045899/03 EN – 06.2022 Page 17 4.3.2 Supply voltage connection The MSENSE® DGA 9 is available in 4 different voltage versions (please ensure to specify when or- dering). Depending on which nominal voltage version is being used, the following alternating or direct current connection (in the form of a 3-pin mains connection cable) must be present near to the de- vice: Nominal voltage version MSENSE® DGA 9 Supply voltage 120 V -20% +15% AC 50…60Hz 96 Vmin... 138 Vmax AC 50…60Hz 230 V -20% +15% AC 50…60Hz 184 Vmin... 264 Vmax AC 50…60Hz 120 V -20% +15% DC 96 Vmin... 138 Vmax DC 230 V -20% +15% DC 184 Vmin... 264 Vmax DC The power consumption of MSENSE® DGA 9 is max. 600 VA. Fuse: 120V:T6,3A 230V: T3, 15A 4.3.3 Tools required The mechanical and electrical installation of the MSENSE® DGA 9 device can be carried out using the following tools/aids: Tool / aids Use Long hexagon key size 4 Vent screw Digital multimeter Check supply voltage Screwdriver no. 2 Supply voltage Brass brush Connecting unit M55 open-ended spanner and/or 1½" adjustable spanner Connecting unit Bucket, oil absorbent, cloth, paper towels Absorbing leaking oil Plastic sheet Catching parts which fall or are dropped 4.3.4 Sealing of the connecting thread The connecting thread can be secured and sealed in different ways. Either a thread sealing tape or a thread adhesive should be used: 4.3.4.1 Thread sealing tape The thread sealing tape, also known as Teflon tape or PTFE tape (polytetrafluoroethylene) is wound tightly around the external thread of the MSENSE® DGA 9 connecting unit. We recommend the use of a Teflon tape for coarse threads (100g/m2). Note !!! If you use Teflon for sealing the connecting thread, no connections are possible later. !!!! Leak hazard !!!! MSENSE® DGA 9 7045899/03 EN – 06.2022 Page 18 4.3.4.2 Thread adhesive We recommend the two Henkel products LOCTITE® 7471 (activator) and LOCTITE® 577 (seal and securing) in combination. The activator LOCTITE® 7471 increases curing speed and is used before the actual thread adhesive LOCTITE® 577 is applied to 3 or 4 turns of the external thread on the MSENSE® DGA 9 connecting unit. Note!!! Please note the specifications and safety instructions provided by the manufacturer!!! 4.3.4.3 Flat gasket When a threaded joint is used, there is no need to seal and secure the connection using thread sealing tape or thread adhesive. In this case, the flat gasket seals and the union nut secures the connection. MSENSE® DGA 9 7045899/03 EN – 06.2022 Page 19 Installation Once installation preparations have been completed, the MSENSE® DGA 9 can be installed. Installa- tion is divided into 3 steps: Mechanical installation [4.4.1] Electrical connection [4.4.2] Initial start-up (4.4.3) 4.4.1 Mechanical installation The sequence for mechanical installation depends on the connection on the transformer side. There are 2 basic types of mechanical installation: Direct mounting [4.4.1.1] Indirect mounting [4.4.1.2] Remark: In the event of heavy vibrations at the installation valve/gate valve, strain should be relieved using a support. 4.4.1.1 Direct mounting In the case of direct mounting, the MSENSE® DGA 9 is screwed directly to the threaded flange, i.e. the device is turned around its own axis in order to be fixed in place. This type of installation requires free space measuring 430 mm in diameter around the centre of the connecting flange. The threaded joint can be sealed and fixed in place using thread sealing tape or thread adhesive. Direct mounting with thread sealing tape Direct mounting with thread adhesive [4.4.1.1.2] Note !!! Do not remove the protective cap (by turning it slowly) until you are ready to install the MSENSE® DGA 9 at the connecting valve/gate valve! MSENSE® DGA 9 7045899/03 EN – 06.2022 Page 20 4.4.1.1.1 Direct mounting with thread sealing tape Use a dry cloth / paper towel to clean the inside of the threaded flange. Use a dry cloth / paper towel to clean the external thread of the connecting unit. Remove any residual thread sealing tape completely from the external thread. A brass brush or spirit can be used for stubborn soiling. The spirit must be completely dry before work can continue. MSENSE® DGA 9 7045899/03 EN – 06.2022 Page 21 Wind 3 to 15 layers of thread sealing tape (depending on the thread's characteristics) tightly in the clockwise direction (seen from the back) around the connecting thread of the MSENSE® DGA 9. The first thread groove should remain free. Place the MSENSE® DGA 9 horizontally onto the threaded flange. Make sure the device does not twist. MSENSE® DGA 9 7045899/03 EN – 06.2022 Page 22 Screw the MSENSE® DGA 9 2 or 3 times clockwise by hand into the threaded flange. Now use an M55 open-ended spanner or a 1 ½" adjustable spanner to screw the MSENSE® DGA 9 by a further 5 or 6 turns clockwise into the threaded flange and stop when the vent screw is in the 9 o'clock position. Remark: If the unit can be screwed in without a great deal of effort being necessary, too little thread sealing tape has been used. The device has to be screwed off again, the thread sealing tape removed completely and the mounting procedure then repeated. MSENSE® DGA 9 7045899/03 EN – 06.2022 Page 23 Remove the two knurled screws and the device protective cover. Now align the MSENSE® DGA 9 by turning it clockwise until the vent screw is at the 12 o'clock position at the top. Make sure the device is fitted firmly in this final position. Remark: The device may only be aligned by turning clockwise. As soon as the device is turned anti-clockwise for alignment, mounting must be carried out again! Note!!! When thread sealing tape is used, screwing the device beyond the 12 o'clock position results in the device having to be screwed back off again, the thread sealing tape being removed completely and mounting being carried out again MSENSE® DGA 9 7045899/03 EN – 06.2022 Page 24 Note!!! The following steps must be carried out in accordance with company procedures. Work carefully and prevent air getting into the transformer. Use a bucket to collect any leaking oil. Unscrew the vent screw by 3 or 4 turns anti-clockwise using the long size 4 hexagon key (vent- ing is active). Open the transformer gate valve very carefully until oil runs out of the sample hose. Allow the escaping oil to run into a container. MSENSE® DGA 9 7045899/03 EN – 06.2022 Page 25 Close the vent screw as soon as there are no more air bubbles escaping from the sample hose. Now open the gate valve/ball valve completely. MSENSE® DGA 9 7045899/03 EN – 06.2022 Page 26 Secure the end of the sample hose using a hose clip Use a dry cloth / paper towel to remove oil residues thoroughly from the device. Note!!! Do not use solvents for cleaning! MSENSE® DGA 9 7045899/03 EN – 06.2022 Page 27 Check every 30 minutes whether the thread connection is leak-proof. MSENSE® DGA 9 7045899/03 EN – 06.2022 Page 28 4.4.1.1.2 Direct mounting with thread adhesive Use a dry cloth / paper towel to clean the inside of the threaded flange. Use a dry cloth / paper towel to clean the external thread of the connecting unit. Remove any residual thread sealing tape completely from the external thread. A brass brush or spirit can be used for stubborn soiling. The spirit must be completely dry before work can continue. MSENSE® DGA 9 7045899/03 EN – 06.2022 Page 29 Apply LOCTITE® 7471 (activator) by spraying or brushing it onto both sealing faces. During spraying, the openings (transformer gate valve and MSENSE® DGA 9) must be covered/sealed by a clean cloth / paper towel. Allow the activator to flash off completely in a well ventilated room until the surface is completely dry. Remark: After activation, the thread connection should be glued within 7 days at the latest. Soiling should be avoided before gluing. Apply LOCTITE® 577 (adhesive) 360° in a ring shape on 3 to 4 thread grooves of the external thread, leaving the first thread groove clear. Use suitable gloves so that you can apply the adhesive to the bottom of the thread groove, filling the intermediate spaces well. Remark: Adapt the adhesive quantity accordingly in the case of larger intermediate spaces. MSENSE® DGA 9 7045899/03 EN – 06.2022 Page 30 Place the MSENSE® DGA 9 horizontally onto the threaded flange. Make sure the device does not twist. Screw the MSENSE® DGA 9 2 or 3 times clockwise by hand into the threaded flange. MSENSE® DGA 9 7045899/03 EN – 06.2022 Page 31 Now use an M55 open-ended spanner or a 1½" adjustable spanner to screw the MSENSE® DGA 9 by a further 5 or 6 turns clockwise into the threaded flange and stop when the vent screw is in the 9 o'clock position. Remark: If the unit can be screwed in without a great deal of effort being necessary, too little thread sealing adhesive has been used. The device has to be unscrewed again, the thread sealant has to be completely removed with a brass brush and the mounting has to be carried out again. Remove the two knurled screws and the device protective cover. Now align the device by turning it clockwise until the vent screw is at the 12 o'clock position at the top. Make sure the device is fitted firmly in this final position. MSENSE® DGA 9 7045899/03 EN – 06.2022 Page 32 We recommend that you wait for 30 minutes before you continue with the further installation steps. The thread adhesive only cures under pressure i.e. in the thread grooves of the pipe connection. For this reason, any excessive thread adhesive should be removed using a clean cloth. Remark: The adhesive has completely cured and achieved resistance against environmental in- fluences after one week. Note!!! The following steps must be carried out in accordance with company procedures. Work carefully and prevent air getting into the transformer. Use a container to collect any leaking oil. Unscrew the vent screw by 3 or 4 turns anti-clockwise using the long size 4 hexagon key (vent- ing is active). MSENSE® DGA 9 7045899/03 EN – 06.2022 Page 33 Open the transformer gate valve very carefully until oil runs out of the sample hose. Allow the escaping oil to run into a container. Close the vent screw as soon as there are no more air bubbles escaping from the sample hose.. MSENSE® DGA 9 7045899/03 EN – 06.2022 Page 34 Now open the gate valve/ball valve completely. Secure the end of the sample hose using a hose clip MSENSE® DGA 9 7045899/03 EN – 06.2022 Page 35 Use a dry cloth / paper towel to remove oil residues thoroughly from the device. Note!!! Do not use solvents for cleaning! Check every 30 minutes whether the thread connection is leak-proof. MSENSE® DGA 9 7045899/03 EN – 06.2022 Page 36 4.4.1.2 Indirect mounting In the case of indirect mounting, the MSENSE® DGA 9 is fixed in place by screwing the union nut on the threaded joint. A flat gasket is used as a thread seal here. Note!!! Do not remove the protective cap (by turning it slowly) until you are ready to install the MSENSE® DGA 9 at the connecting valve/gate valve! Use a dry cloth / paper towel to clean the inside of the union nut. Use a dry cloth / paper towel to clean the external thread of the connecting unit. Completely remove any soiling from the external thread with a brass brush. MSENSE® DGA 9 7045899/03 EN – 06.2022 Page 37 Place the MSENSE® DGA 9 horizontally onto the threaded joint. Make sure the device does not twist. Note!!! Make sure that the gasket has been inserted between MSENSE® DGA 9 and the screw connection. Turn the union nut by hand onto the external thread of the connection unit until it stops. MSENSE® DGA 9 7045899/03 EN – 06.2022 Page 38 Remove the two knurled screws and the device protective cover. Now align the device by turning it clockwise until the vent screw is at the 12 o'clock position at the top. Use a M55 open-ended spanner or 1½" adjustable spanner to tighten the union nut until the connection is a firm fit. Make sure that the 12 o'clock alignment is not displaced. Use an addi- tional M55 open-ended spanner or a 1½" to lock the device during tightening and hold it in position. Note!!! The following steps must be carried out in accordance with company procedures. Work carefully and prevent air getting into the transformer. Use a container to collect any leaking oil. Unscrew the vent screw by 3 or 4 turns anti-clockwise using the long size 4 hexagon key (vent- ing is active). MSENSE® DGA 9 7045899/03 EN – 06.2022 Page 39 Open the transformer gate valve very carefully until oil runs out of the sample hose. Allow the escaping oil to run into a container. Close the vent screw as soon as there are no more air bubbles escaping from the sample hose. MSENSE® DGA 9 7045899/03 EN – 06.2022 Page 40 Now open the gate valve/ball valve completely. Secure the end of the sample hose using a hose clip Use a dry cloth / paper towel to remove oil residues thoroughly from the device. Note!!! Do not use solvents for cleaning! MSENSE® DGA 9 7045899/03 EN – 06.2022 Page 41 Check every 30 minutes whether the thread connection is leak-proof. MSENSE® DGA 9 7045899/03 EN – 06.2022 Page 42 4.4.2 Electrical connection Note! There must be a 10A overcurrent protective device available in the installation Note! A disconnecting device must be available for the device, easy to reach for the user and identifiable as a disconnecting device for this device. Use reinforced pipes as protection for all cables and connect these to the respective connections in the device. All the cables must be provided by the customer. The following versions are available for the electrical connections: 1 x M16 SKINTOP® threaded joint (clamping range 4.5... 10.0 mm 2 x M20 SKINTOP® threaded joint (clamping range 7.0... 13.0 mm 1 x M25 SKINTOP® threaded joint (clamping range 9.0... 17.0 mm) Note!!! Where smaller cable diameters are involved, appropriate reducing seal inserts must be used to guarantee clamping and tightness of the cable gland! Remark: The MSENSE® DGA 9 is delivered with 2 SKINTOP® threaded joints M16 and M20 from the factory! The four remaining ducts are sealed with blind plugs M20 and M25. MSENSE® DGA 9 7045899/03 EN – 06.2022 Page 43 Mains connection: Recommendation for the mains connection cable: Cable type: PUR-PUR CEE JB 3x1.50 (or similar) Cable diameter : 8.1 mm Cable cross-section : 1.5 mm2 (of the 3 individual wires) Minimum cross-section: 0.75 mm² (maximum cable length at 120V: 25m, at 230V: 50m Modem communication: (Exclusively for service purposes) Ethernet communication: Ethernet communication can be connected by copper cable (RJ45) or fibre optic cable (SC-Du- plex) (please state when placing your order). For the copper variant, the connection socket (RJF 544) is located directly on the back of the device. The connection for the fibre optic version must be routed through the cable gland and connected directly on the inside of the device. Copper cable: Recommendation for the Ethernet communication cable (copper): Cable type: Ethernet cable Cat. 5e with RJ45 connector (RJF 544 6) Cable diameter : 6.3 mm Fibre optic cable: Recommendation for the Ethernet communication cable (light waves): Cable type: HITRONIC® HQN 1000 multi-mode G4 62.5/125 with SC-Duplex connector Cable diameter : 6.5 mm Bending radius: min. 15 x Ø Alarm outputs: Recommendation for the analogue line cable: Cable type: ÖLFLEX® FD855CP (or similar) Cable diameter : 13.3 mm Cable cross-section : 0.5 mm2 (of the 16 individual wires) MSENSE® DGA 9 7045899/03 EN – 06.2022 Page 44 Do not route external wiring over the heaters. Danger through heat. When connecting external cables, please note the following: The red-rimmed area can reach tem- peratures of up to 80 ° C in the event of a fault. Do not lay cables over this area! MSENSE® DGA 9 7045899/03 EN – 06.2022 Page 45 4.4.3 Initial start-up As soon as the device is connected to a power source, a short beep will sound and the LCD screen will show the main menu after a brief moment. To begin with, the time and date have to be set and then the device must be activated / initialized by the operator. Setting the time and date under “Device Settings” The user can navigate through the individual menus by using the arrow keys. The active field / menu is highlighted in black and can be selected by pressing the Enter key. To enter the sub-menu “Date, time, clock settings”, please select the following sub-menu symbols. Main menu Device settings 123456 Device settings MSENSE® DGA 9 Settings Date, time, clock settings The time and date are entered us- ing the device keyboard. It con- sists of an alphanumeric keypad, the arrow and the enter key. The numbers must be entered com- pletely with separators (e.g. 15:12:30). The colon is en- tered using the key and the minus sign is entered using the key. The entry is then completed with the Enter key (6.10.4.4). Finish making the entries by pressing the “Save and exit menu” MSENSE® DGA 9 key Settings Device settings Main menu MSENSE® DGA 9 7045899/03 EN – 06.2022 Page 46 Activate / initialise device under extraction status To enter the sub-menu “Extraction status”, please select the following sub-menu symbols. Main menu Extraction status The MSENSE® DGA 9 does not automatically start the measure- ment cycle after installation and the application of the supply volt- age (exception: after a power fail- ure while the device is running). A warning symbol in the picture indi- cates this status. The activation must be done explicitly by the op- erator! Device activation The initialisation cycle detects the device’s current state and estab- lishes a defined state of the sys- tem. Following successful initialisation, the device’s state changes to the “Wait” process step until the next measuring cycle is started. Exit menu Main menu If the function is correct, you can reinstall the protective hood and fix it with the two knurled screws. Every 20 minutes, a measurement is started. A measuring cycle lasts at least 15.... 18 minutes. Note: Activation / initialisation of the MSENSE® DGA 9 device typically uses the term “mount”. MSENSE® DGA 9 7045899/03 EN – 06.2022 Page 47 4.4.4 Turn off the device Note!!! The device must always be taken out of operation using the “de- activation” key, before it becomes de-energised and can then be disas- sembled!!!! Deactivate device under extraction status Main menu Extraction status The device’s deactivation has to be done explicitly by the user and can be done at any time. Device deactivation By deactivating the device, the current process step is stopped and a controlled draining is trig- gered. Following its successful deactiva- tion, the device is inactive. A warning symbol indicates this sta- tus. Exit menu Main menu The device can now be de-energised and disassembled. Note: In order to deactivate the MSENSE® DGA 9, the term “unmount” is typically used. MSENSE® DGA 9 7045899/03 EN – 06.2022 Page 48 4.4.5 Automatic activation following the interruption of the supply voltage If a device has already been activated, the automatic activation will be started after the supply voltage is interrupted. You will hear a short beep sound and, after a brief moment, the screen will show the special menu item “Extraction chamber (Pollution warning! - Indication of pollution!)”. The waiting time until automatic activation is then started. This is shown with a second-by-second countdown timer. Furthermore, short beeps are audible (the first 25 seconds is a short beep tone every 5 seconds and a short beep tone is then heard every second for the last 5 seconds). There is the option to cancel the automatic activation with the key within 30 seconds and to manually activate the device at a later point in time (4.4.3). Once the waiting time has elapsed, the automatic activation will start and the LCD will show the main menu. Cancel the device’s automatic activation Initial position of the cursor (the key has no stored function) Exit menu Remark: After leaving the initial position, this can no longer be reached. MSENSE® DGA 9 7045899/03 EN – 06.2022 Page 49 5. Hardware components Internal front view with controls After removing the housing's protective hood, the inner front section and its operating elements become visible. This comprises the following components: LCD-Display with 320 x 240 pixels Threaded bolt for the attachment of the device protective cap Alphanumeric keypad for entering numbers and text Arrow keys for navigation in menus and data entry Enter key to activate and confirm functions and data entry MSENSE® DGA 9 7045899/03 EN – 06.2022 Page 50 View of rear Connecting unit with external thread G 1½” DIN ISO 228-1 or 1½” NPT ANSI B 1.20.1 MSENSE® DGA 9 7045899/03 EN – 06.2022 Page 51 Mains connection with SKINTOP® threaded joint M16 Nominal voltages: 120 V -20% +15% AC 50/60Hz 1) or 230 V -20% +15% AC 50/60Hz 1) or 120 V -20% +15% DC 1) or 230 V -20% +15% DC 1) Other nominal voltages upon request Power consumption: max. 600 VA Fuse for 120V: T6, 3 A Fuse for 230V: T3, 15 A Connect the power cable as follows: AC version DC version Phase: L Plus conductor: + Neutral conductor: N Minus conductor: – Protective earth: PE Protective earth: PE Remark 1): 120 V 120 V -20% = 96 Vmin 120 V +15% = 138 Vmax 230 V 230 V -20% = 184 Vmin 230 V +15% = 264 Vmax System connection with SKINTOP® threaded joint M20 Communication / alarms and additional sensors: Implementation with SKINTOP® blind threaded joint M20 Implementation with SKINTOP® blind threaded joint M25 ETHERNET communication port with RJ45 socket (RJF TV Type: 2) Communication interface ETHERNET 10/100 Mbit for copper cable Vent opening Used as an output for the vacuum compressor (gas/air mixture of the measurement cell) MSENSE® DGA 9 7045899/03 EN – 06.2022 Page 52 Connections for the measuring and controller card MSENSE® DGA 9 7045899/03 EN – 06.2022 Page 53 Connector plug X12: Valve control V4... V9 [Valve Control V4-V9] Connection for ventilation, bypass, measurement cell switching, vacuum and inlet / outlet valve. X12:12 V9 Inlet / outlet valve X12:11 V9 Inlet / outlet valve X12:10 V8 Vent valve for measurement cell 2 X12:9 V8 Vent valve for measurement cell 2 X12:8 V7 Vacuum valve for measurement cell 2 X12:7 V7 Vacuum valve for measurement cell 2 X12:6 V6 Measurement cell switching valve X12:5 V6 Measurement cell switching valve X12:4 V5 Bypass valve oil pump X12:3 V5 Bypass valve oil pump X12:2 V4 Vent valve for measurement cell 1 X12:1 V4 Vent valve for measurement cell 1 Connector plug X11: Filling level / Flow [Oil-Level Oil-Flow] Connection for filling levels and flow MSENSE® DGA 9 7045899/03 EN – 06.2022 Page 54 X11:10 (not connected) X11:9 F1 Flow meter X11:8 F1 Impulse Flow meter X11:7 F1 Flow meter X11:6 L0 out Filling level sensor zero acknowledgement X11:5 L0 Filling level sensor zero acknowledgement X11:4 L1 out Filling level sensor low X11:3 L1 Filling level sensor low X11:2 L2 out Filling level sensor high X11:1 L2 Filling level sensor high Connector plug X16: Heating Bridge Connection of the heating resistors with a supply voltage of 230 V X16:6 ┌ Heating measurement cell 2 X16:5 └ Heating measurement cell 2 X16:4 ┌ Heating measurement cell 1 X16:3 └ Heating measurement cell 1 X16:2 ┌ Heating extraction chamber X16:1 └ Heating extraction chamber Connection of the heating resistors with a supply voltage of 120 V X16:6 ┌ (not connected) X16:5 └ (not connected) X16:4 ┌ (not connected) X16:3 └ (not connected) X16:2 ┌ (not connected) X16:1 └ (not connected) MSENSE® DGA 9 7045899/03 EN – 06.2022 Page 55 Connector plug X15: Heating Neutral Connection of the heating resistors with a supply voltage of 230 V X15:6 N (not connected) X15:5 N Heating measurement cell 2 X15:4 N (not connected) X15:3 N Heating measurement cell 1 X15:2 N (not connected) X15:1 N Heating extraction chamber Connection of the heating resistors with a supply voltage of 120 V X15:6 N Heating measurement cell 2 X15:5 N Heating measurement cell 2 X15:4 N Heating measurement cell 1 X15:3 N Heating measurement cell 1 X15:2 N Heating extraction chamber X15:1 N Heating extraction chamber MSENSE® DGA 9 7045899/03 EN – 06.2022 Page 56 Connection terminals X401: Relay outputs 1... 4 [4 x Relay-out X401] Connection for relay outputs 1... 4 (220 VDC/VAC / 2 A / 60 W) Relays Output 4 Relays Output 3 Relays Output 2 Relays Output 1 Relay contacts X401:8 DOR4 Relay output 4 X401:7 DOR4 Relay output 4 X401:6 DOR3 Relay output 3 X401:5 DOR3 Relay output 3 X401:4 DOR2 Relay output 2 X401:3 DOR2 Relay output 2 X401:2 DOR1 Relay output 1 or (J1: see also 5.3.1) X401:1 DOR1 Relay output 1 5.3.1 Configuration of relay output 1 with coding bridge 1 (J1) If coding bridge 1 is inserted as shown in the following figure, relay output 1 is configured so that the contact is closed during the device’s operation. In the event of a fault, the contact opens. Coding bridge 1 for configuring relay contact 1 (X401 / KL401) MSENSE® DGA 9 7045899/03 EN – 06.2022 Page 57 Connection terminals X402: Relay outputs 5... 8 [4 x Relay-out X402] Connection for relay outputs 5... 8 (220 VDC/VAC / 2 A / 60 W) Relay contact X402:8 DOR8 Relay output 8 X402:7 DOR8 Relay output 8 X402:6 DOR7 Relay output 7 X402:5 DOR7 Relay output 7 X402:4 DOR6 Relay output 6 X402:3 DOR6 Relay output 6 X402:2 DOR5 Relay output 5 X402:1 DOR5 Relay output 5 Connection terminals X403: Relay outputs 9... 10 [2 x Relay-out X403] Connection for relay outputs 9... 10 (220 VDC/VAC / 2 A / 60 W) Relay contact X403:4 DOR10 Relay output 10 X403:3 DOR10 Relay output 10 X403:2 DOR9 Relay output 9 X403:1 DOR9 Relay output 9 Connection terminals X301: Relay outputs 1... 4 [Analogue output 1-4] Connection for analogue outputs 1... 4 (0 / 4…. 20 mA DC) Analogue Output 4 Analogue Output 3 Analogue Output 2 Analogue Output 1 X301:8 AO4 Analogue output 4 X301:7 AO4 Analogue output 4 X301:6 AO3 Analogue output 3 X301:5 AO3 Analogue output 3 X301:4 AO2 Analogue output 2 X301:3 AO2 Analogue output 2 X301:2 AO1 Analogue output 1 X301:1 AO1 Analogue output 1 MSENSE® DGA 9 7045899/03 EN – 06.2022 Page 58 Connection terminals X302: Relay outputs 5... 8 [Analogue output 5-8] Connection for analogue outputs 5... 8 (0 / 4…. 20 mA DC) Analogue Output 8 Analogue Output 7 Analogue Output 6 Analogue Output 5 X302:8 AO8 Analogue output 8 X302:7 AO8 Analogue output 8 X302:6 AO7 Analogue output 7 X302:5 AO7 Analogue output 7 X302:4 AO6 Analogue output 6 X302:3 AO6 Analogue output 6 X302:2 AO5 Analogue output 5 X302:1 AO5 Analogue output 5 Connection terminals X303: Relay outputs 9... 10 [Analogue output 9-10] Connection for analogue outputs 9... 10 (0 / 4…. 20 mA DC) Analogue Output 10 Analogue Output 9 X303:4 AO10 Analogue output 10 X303:3 AO10 Analogue output 10 X303:2 AO9 Analogue output 9 X303:1 AO9 Analogue output 9 Connection terminals X304: RS485 interface Connection for RS485 interface Analogue Modem RS 485 Interface X304:5 Phone A Analogue modem (exclusively for service purposes) X304:4 Phone B Analogue modem (exclusively for service purposes) X304:3 GND IO RS-485 interface X304:2 OUT A RS-485 interface X304:1 OUT B RS-485 interface MSENSE® DGA 9 7045899/03 EN – 06.2022 Page 59 MSENSE® DGA 9 7045899/03 EN – 06.2022 Page 60 Connector plug X13: Valve control V1... V3 [Valve Control V1-V3] Connection for degassing, measurement cell separation and vacuum MZ1 - valve X13:6 V3 Vacuum value for measurement cell 1 X13:5 V3 Vacuum value for measurement cell 1 X13:4 V2 Measurement cell isolation valve X13:3 V2 Measurement cell isolation valve X13:2 V1 Degassing valve X13:1 V1 Degassing valve Connector plug X14: Voltage 12VDC / Pump / Compressor [UC / P-Oil / P-Air] Connection for voltage 12VDC, oil pump and compressor X14:6 K1 Compressor X14:5 K1 Compressor X14:4 P1 Pump X14:3 P1 Pump X14:2 UC Voltage 12 VDC X14:1 UC Voltage 12 VDC Connector plug X8: Temperature heating [Temp. HeatX] Connection for temperature sensors – heating MSENSE® DGA 9 7045899/03 EN – 06.2022 Page 61 X8:6 TX-Chmbr Temperature sensor extraction chamber X8:5 TX-Chmbr Temperature sensor extraction chamber X8:4 TMC2 Temperature sensor measurement cell 2 X8:3 TMC2 Temperature sensor measurement cell 2 X8:2 TMC1 Temperature sensor measurement cell 1 X8:1 TMC1 Temperature sensor measurement cell 1 Connector plug X3: Moisture in oil / oil temperature Oil] Connection for the moisture in oil sensor and oil temperature sensor X3:7 T2 Oil temperature sensor extraction chamber X3:6 T2 Oil temperature sensor extraction chamber X3:5 M1GND Moisture in oil sensor extraction chamber X3:4 M1 Moisture in oil sensor extraction chamber X3:3 M1 Moisture in oil sensor extraction chamber X3:2 M1out Moisture in oil sensor extraction chamber X3:1 M1in Moisture in oil sensor extraction chamber Connector plug X17: Heating Phase Connection of the heating resistors with a supply voltage of 230 V X17:6 N (not connected) X17:5 N Heating measurement cell 2 X17:4 N (not connected) X17:3 N Heating measurement cell 1 X17:2 N (not connected) X17:1 N Heating extraction chamber MSENSE® DGA 9 7045899/03 EN – 06.2022 Page 62 Connection of the heating resistors with a supply voltage of 120 V X17:6 N Heating measurement cell 2 X17:5 N Heating measurement cell 2 X17:4 N Heating measurement cell 1 X17:3 N Heating measurement cell 1 X17:2 N Heating extraction chamber X17:1 N Heating extraction chamber Connection terminals X1: Power supply Connection power supply Connector X1: 1 is connected to the fuse carrier supplied by the main connector. X1:1 L Phase AC / Plus conductor DC X1:2 - X1:3 N Neutral AC / Minus conductor DC X1:4 - X1:5 PE Protective earth / Protective earth Connection ETHERNET communication [Ethernet] Communication port via Ethernet Copper cable or fibre optic cable (RJ45) (SC-Duplex) Connection socket X5: Measurement cell 1 [Measurement cell 1 1005 / X5] Connection for the measurement cell 1 via REDEL panel jack 4-pole 0° coded X5:4 TxSENS Measurement cell 1 transmission signal X5:3 RxSENS Measurement cell 1 reception signal X5:2 GND 8 Volt supply X5:1 8V 8 Volt supply MSENSE® DGA 9 7045899/03 EN – 06.2022 Page 63 Connection socket X6: Measurement cell 2 [Measurement cell 2 1009 / X6] Connection for the measurement cell 2 via REDEL panel jack 4-pole 0° coded X6:4 TxSENS Measurement cell 2 transmission signal X6:3 RxSENS Measurement cell 2 reception signal X6:2 GND 8 Volt supply X6:1 8V 8 Volt supply Extraction menu MSENSE® DGA 9 7045899/03 EN – 06.2022 Page 64 5.4.1 Hardware components Filling level sensor L0 (L0 zero acknowledgement) Filling level sensor L1 (L1 extraction chamber) Filling level sensor L2 (L2 extraction chamber) Valve V9 (safety) Flow measurement (fill / drain flow) Valve V1 (filling / draining, circulation) Valve V3 (vacuum MZ1) Valve V7 (vacuum MZ2) Compressor K1 Valve V4 (ventilation MZ1) Valve V8 (ventilation MZ2) Valve V2 (measurement cell separation, oil from gas) Valve V6 (switching between MZ1 and MZ2) Oil pump P1 Valve V5 (bypass filling) Oil separator Oil-moisture extraction chamber Oil temperature extraction chamber MSENSE® DGA 9 7045899/03 EN – 06.2022 Page 65 MSENSE® DGA 9 7045899/03 EN – 06.2022 Page 66 MSENSE® DGA 9 7045899/03 EN – 06.2022 Page 67 6. Device firmware General information The “gas-in-oil” analysis system MSENSE® DGA 9 is based on microprocessor control. A 32-bit “Cold- fire” processor with a processor cycle frequency of 240 MHz is used. The device software was devel- oped in programming language “C”. The system has a flash memory of 128 Mbyte capacity for saving the measured data. This corresponds to a memory capacity for measured data for about 10 years. After that, the oldest data are overwritten by the current measured values. When using analogue sen- sors, memory capacity is reduced. When using additional sensors, the storage capacity depends on the number of sensors and the chosen storage interval. The following calculation formula can be used to determine the storage capacity: 128 220Byte SpeichertiefeTage 12 23000 Byte / Tag + 288 Byte / Tag Sensorspeichern 1 Std n =1 With an additional sensor and a storage interval of 5 minutes, the result is as follows: 128 220Byte 128 220Byte Speichertiefedays 2500 Tage 2300 Tag + 3456 Byte / Tag 26456 Byte / Tag The defined alarms also affect the storage capacity. Each alarm status change requires 12 bytes of space. Note!!! To avoid data loss, the measured values should be read out regularly us- ing the Windows-based MR MSET DGA software. 6.1.1 Main screen 3 seconds The relative moisture of the oil is displayed on the main screen in alternating fashion between the absolute and relative oil moisture. The bar for the oil moisture changes between its absolute and rela- tive moisture (3s change interval). MSENSE® DGA 9 7045899/03 EN – 06.2022 Page 68 Process flow This chapter contains a description of the individual process steps and the information regarding safety and the associated functions. In the event of a fault, the process is interrupted and the system is set to a defined state (pump and compressor standstill, all valves closed). Colour Aggregate State White Pump: Standstill compressor: Standstill Level: not reached Flow: not available Green Pump: Operation Compressor: Operation Level: reached Flow: available 2/2-way valve: A-P open 3/2-way valve: A-R closed / A-P open Yellow 2/2-way valve: A-P closed 3/2-way valve: A-R open / A-P closed Remarks: The valve V6 for switching between the measurement cells is not listed in the graphs. The fact is that it switches through to measurement cell 1 when de-energised. MSENSE® DGA 9 7045899/03 EN – 06.2022 Page 69 6.2.1 Zero measurement In this process step, the zero measurement is executed. Legend Condition of components Filling level L0 “not reached” Filling level L1 “not reached” Filling level L2 “not reached” Valve V9 “closed” Flow F1 “not available” Valve V1 “degassing” Valve V3/V7 “closed” Compressor K1 "standstill” Valve V4/V8 “closed” Valve V2/V6 “closed” Pump P1 "standstill” Valve V5 “open” Safety functions and fault detection Zero measurement Monitored components Detectable errors Filling sensors zero acknowledgement, low and high Filling level L0, L1 or L2 reached Measurement cell Measurement cell offline Pressure sensor in measurement cell Pressure unstable MSENSE® DGA 9 7045899/03 EN – 06.2022 Page 70 6.2.2 Vacuum generation In this process step, a vacuum is generated in the measurement cell. Legend Condition of components Filling level L0 “not reached” Filling level L1 “not reached” Filling level L2 “not reached” Valve V9 “closed” Flow F1 “not available” Valve V1 “degassing” Valve V3/V7 “open” Compressor K1 “operation” Valve V4/V8 “closed” Valve V2/V6 “closed” Pump P1 "standstill” Valve V5 “open” Safety functions and fault detection Vacuum generation Monitored components Detectable errors Filling sensors zero acknowledgement, low and high Filling level L0, L1 or L2 reached Measurement cell Measurement cell offline Pressure sensor in measurement cell No pressure drop MSENSE® DGA 9 7045899/03 EN – 06.2022 Page 71 6.2.3 Leak testing This process step checks the pressure stability of the whole system. Legend Condition of components Filling level L0 “not reached” Filling level L1 “not reached” Filling level L2 “not reached” Valve V9 “closed” Flow F1 “not available” Valve V1 “filling - draining” Valve V3/V7 “closed” Compressor K1 "standstill” Valve V4/V8 “closed” Valve V2/V6 “open” Pump P1 "standstill” Valve V5 “open” Safety functions and fault detection Leakage test Monitored components Detectable errors Filling sensors zero acknowledgement, low and high Filling level L0, L1 or L2 reached Measurement cell Measurement cell offline Pressure sensor in measurement cell Pressure drop Flow measurement Valve V9 does not close properly MSENSE® DGA 9 7045899/03 EN – 06.2022 Page 72 6.2.4 Filling level L1 In this process step, the extraction chamber is filled with oil up filling level L1. Legend Condition of components Filling level L0 “reached” Filling level L1 “reached” Filling level L2 “not reached” Valve V9 “open” Flow F1 “present - filling” Valve V1 “filling - draining” Valve V3/V7 “closed” Compressor K1 "standstill” Valve V4/V8 “closed” Valve V2/V6 “open” Pump P1 "standstill” Valve V5 “open” Safety functions and fault detection Filling level L1 Monitored components Detectable errors Filling sensors zero acknowledgement, low and high Filling level L0 or L1 not reached Filling level L2 reached Filling sensors zero acknowledgement, low and high Filling level drops Flow measurement Filling stagnates Time monitoring Filling time exceeded Measurement cell Measurement cell offline Pressure sensor in measurement cell Pressure drop Flow stops MSENSE® DGA 9 7045899/03 EN – 06.2022 Page 73 6.2.5 Degasing In this process step, the gases dissolved in oil are released by way of circulation into the air in the extraction chamber (headspace principle). This results in a balance being achieved in the proportionate quantities of gas between oil and air. Legend Condition of components Filling level L0 “reached” Filling level L1 “reached” Filling level L2 “not reached” Valve V9 “closed” Flow F1 “not available” Valve V1 “degassing” Valve V3/V7 “closed” Compressor K1 "standstill” Valve V4/V8 “closed” Valve V2/V6 “closed” Pump P1 “Operation” Valve V5 “closed” Safety functions and fault detection Degassing Monitored components Detectable errors Filling sensors zero acknowledgement, low and high Filling level L1 or L1 not reached Filling level L2 reached Filling sensors zero acknowledgement, low and high Filling level drops Measurement cell Measurement cell offline Pressure sensor in measurement cell Pressure drop Valve V4 does not close properly Flow measurement Valve V6 does not close properly MSENSE® DGA 9 7045899/03 EN – 06.2022 Page 74 6.2.6 Filling level L2 In this process step, the extraction chamber is filled with oil up to filling level L2 and the gaseous air is forced from the extraction chamber into the measurement cell. Legend Condition of components Filling level L0 “reached” Filling level L1 “reached” Filling level L2 “reached” Valve V9 “open” Flow F1 “present - filling” Valve V1 “filling - draining” Valve V3/V7 “closed” Compressor K1 "standstill” Valve V4/V8 “closed” Valve V2/V6 “open” Pump P1 "standstill” Valve V5 “open” Safety functions and fault detection Filling level L2 Monitored components Detectable errors Filling sensors zero acknowledgement, low and high Filling level L0, L1 or L2 reac