On-Load Tap Changer Type T Operating Instructions PDF
Document Details
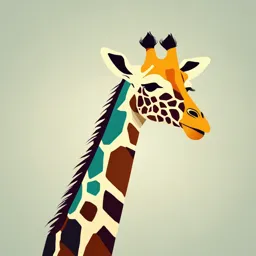
Uploaded by BestSellingBeige
null
Tags
Related
- On-load tap-changer OILTAP® M Technical Data TD 050/03 PDF
- On-Load Tap Changer Type T Inspection Instructions PDF
- Technical Data On-Load Tap Changer Type H PDF
- VACUTAP® VM®, VM 300, VMS® On-load tap-changer Technical Data PDF
- Transformer Tap Changer PDF
- EENG 105: Distribution System & Substation Design PDF
Summary
This document provides detailed operating instructions for the On-Load Tap Changer Type T. It covers installation steps, connecting leads, transformer ratio tests, and other operational procedures.
Full Transcript
MASCHINENFABRIK MR* REINHAUSEN ON-LOAD TAP CHANGER TYPE T Operatin g Instruct ions MASCHINENFABRIK...
MASCHINENFABRIK MR* REINHAUSEN ON-LOAD TAP CHANGER TYPE T Operatin g Instruct ions MASCHINENFABRIK M R REINHAUSEN B A 79/86 e n — 0392/500 Maschinenfabrik Reinhausen GmbH Printed in Germany Postfach 1 2 03 60 D-93025 Regensburg Phone: +49-941-4090-0 Fax: +49-941-4090-111 Telex: 6 5 881 ON-LOAD TAP CHANGER TYPE T Operating Instructions No. 79/86 Contents Page 1.General........ciiiiiiiiiiiiee cana Cetaseracesareaneanes 2 2. Shipment.........coiiiiiiint tiiinrerrnannnnncen eenranes 3 3. Installation of the on-load tap changer into the standard-typetransformertank...............ciceiiiiinnas. 4 4. Installation of the onload tap changer into the bell-type cover........ 6 5. Connecting the step winding and the tap changer take-offleads....... 9 6. Transformerratiotest.............ccciiiiiiiiniiiiinnnnens. 15 7. Drying procedure andflllingintheoil..............cccvvvinans... 15 8. Pipe connections E T I | 9. Mounting the motor drive unit, the bevel gear and the drive shaft...... 17 10. Putting the tap changer into operation in the transformer factory...... 18 11. Transporting the transformer to the operatingsite.................. 19 12. Putting into operation at the operatingsite..............c.ccveune. 19 13. S u p e r v i s i o n i n s e r v i c e............ coi iii ii ric ries 19 14. Inspections.........ocivvnunans ess esvranaisarassasaenernns 20 15. APPENAIX.....oiiiiiiiiiiiiit treet asia 20 1. GENERAL The tap changer (fig. 1 , 2) consists of the diverter switch installed into an oil compartment pressure-proof sepa- rated from the transformer oil and of the tap selector mounted below it. The tap changer is attached to the transformer cover by means of the tap changer head, which also serves for coupling the drive shaft and for con- necting a pipe to the oil conservator. If required, the tap selector may be equipped with a change-over selector. For the standard version, models without change-over selector are available for up to 18 and with change-over selector for up to 35 operating positions. The design of the tap changer and the designation of its main parts are shown in the installation drawings 894 242 and 894 240 in the appendix. These Operating Instructions contain all information regarding installation and operation of the different standard models of tap changer type T. Note: these Operating Instructions apply accordingly t o the special design with eccentric arrangement (fig. 3) of the upper gear unit o n the tap changer head. The following models of this tap chan- ger type are available (without and with change-over selector): Tap changers T 600 Tap changers T 1000 T 11600 (see fig. 1), T1601, T1 1001 T Ill 1000 (see fig. 2), T | 1001 (tap selector size C & D), T 11502. (tap selector size DE & E only), The tap selectors of tap changer T12002, T 13000. T 600 are almost identical with those of tap changer type M. All single-pole tap changers are avail- ableasa group 3x TI... witha com- mon motor drive. 2, SHIPMENT TTT hn CABRLEH RANT SL Tap changer and motor drive are shipped in the adjustment position. The tap changer is packed in two parts, diverter switch and tap selector and are well protected against mois- ture. Both the diverter switch and the tap selector are blocked in the adjust- ment position. The tap changer equipment is shipped as follows: Diverter switch oil compartment with tap changer head and diverter switch unit assembled (max. weight approx. 210 kg), fig. 4. Tap selector (max. weight approx. 230 kg), fig. 5. Motor drive unit MA 7 (approx. 90 kg), fig. 6 or MA 7/8 (approx. 130 kg). Drive shaft with coupling parts and bevel gear (max. weight approx. 20 kg), fig. 7. Protective relay RS 2001 (weight 3.5 kg), fig. 8. Check shipment against documents. Store all parts in a dry place. The tap changer parts must be left wrapped in their plastic cover, unwrap just before installation. In general, drive shaft parts, bevel gear and protective relay are packed with the tap changer. 3. INSTALLATION OF THE 3.3 Attaching the tap selector to the ON-LOAD TAP CHANGER diverter switch oil compartment INTO THE STANDARD-TYPE TRANSFORMER TANK The tap selector is to be elevated to the oil compartment from below and then _ attached to it. At the same time the 3.1 Mounting flange mechanical coupling for the tap selector drive has to be performed. For mounting the tap changer head to Finally, the tap selector connecting the transformer cover a mounting leads have t o be connected to the flange is necessary. This mounting diverter switch oil compartment. flange should meet the requirements of the tap changer head gasket surface Proceed a s follows: (see fig. 9 and dwgs. 894 242 and 894 240 in the appendix). Put down the tap selector to a level surface. For positioning the thread studs we recommend the use of the respective Get ready all screws and nuts of tap drilling template (see fig. 10 and dwg. selector suspension. 890 183 in the appendix). The drilling template will be supplied with the first Put the tap selector to an appropriate tap changer type T, free of charge. elevating mechanism. Be sure not to touch the tap selector connecting leads on the bottom (with tap changers 3.2 Attachment of the tap changer T 1000 only). head to the transformer cover Diverter switch oil compartment and tap selector remain separated for the time being. The diverter switch oil compartment is to be lowered through the cover aperture ( = mounting flange) and fastened by bolts to the mounting flange by means of the tap changer head. Later on, the tap selector will be fastened to the diverter switch oil compartment (see section 3.3). Proceed as follows: Put the diverter switch oll compartment on a level surface. Clean sealing surfaces of mounting flange and tap changer head. Take care of screening rings Remove the blocking pin from the Put an oil-proof gasket on the mount- (with 150 kV and 220 kV only). tap selector coupling (fig. 12). ing flange of the transformer cover. The coupling must not be displaced Check position of tap changer head. afterwards. Lift the diverter switch oil compartment by hooking up the tap changer head. Attach the tap changer head to the Elevate the tap selector to the diverter Lower the oil compartment cautiously mounting flange by bolting. switch oil compartment. Be sure that into the mounting flange. tap selector connecting leads clear the Having done this remove the diverter switch oil compartment and wooden beams and blocking remain undamaged. plate from coupling (fig. 11) of o i l compartment bottom. Position coupling parts and attach- ment points of tap selector and oil compartment to match properly. Elevate the tap selector to the final height. Bolt the tap selector suspen- sion to the oil compartment bottom: Tap changer T 600 (fig. 13) 2 hexagonal head bolts M10 x 110 with self-locking nuts (w.s.17), max. torque 44 Nm. 2 hexagonal head bolts M10 x 80 (w.s.17), with lock washers, max. torque 44 Nm. Tap changer T 1000 (fig. 14) 2 hexagonal recess head screws M12 x 45 (w.s. 8) with self-locking nuts (w.s. 19), max. torque 60 Nm. 4 hexagonal recess head screws M10 x 45 (w.s. 8) with self-locking nuts (w.s. 17), max. torque 44 Nm. The nuts should be put to the inner side of oil compartment bottom posts. Connection of tap selector connecting leads on the diverter switch oil com- partment: All connections should be carried out carefully. The tightening torques indicated should b e applied. B e sure that all screw connections are locked safely and screened b y the screening caps supplied with the equipment. T i l l 600, T1601 6 connecting leads t o 6 oil compart- ment terminals according to fig. 15. Attachment by nuts M16 (w.s. 24), recommended torque (50 + 5) Nm, lock tabs. T l 1000, T 1 1001 12 connecting leads t o 2 x 6 oil compartment terminals according to fig. 16. Attachment by nuts M16 (w.s. 24), recommended torque (50 + 5) Nm, lock tabs. T11502, T12002 All diverter switch sectors are connec- ted in parallel by 2 rings outside the oil compartment which the tap selector connecting leads are to be attached to. T11502: 6 leads T12002: 8 leads Attachment of leads by heaxagonal head screws M10 x 45 with self- locking nuts, recommended torque (40 + 5) Nm, (fig. 17a, 17b). 4, INSTALLATION OF THE ON- LOAD TAP CHANGER INTO THE BELL-TYPE COVER (fig. 18) JHB i) AB i For mounting and connecting the tap hy, : changer a supporting structure is ne- I cessary which allows for a provisional il attachment of the tap changer by : means of the oll compartment sup- | porting flange (see dwg. 830 753 in appendix). RU For mounting the tap changer head onto the transformer cover a mounting flange as described under section 3.1 is recommended. ~ First of all, the tap changer head is to dL be dismounted from the diverter switch oil compartment, then the oil compart- For this purpose, open the tap changer ment and the tap selector are to be head cover (24 hexagonal head screws bolted together and lifted into the ‘M10, w.s.17, with lock washers). supporting structure. Take care of the cover gasket (round rubber gasket, fig. 19). 4.1 Dismountingthe tap changer head Before installation, the tap changer head (special design) has to be re- moved from the diverter switch oil compartment flange. 6 Remove the position indicator dial (remove the clip from the shaft end, (fig. 20)). Keep washers for reas- sembly. Take note of red-marked area not covered by the suspension plate of the diverter switch unit (fig. 21). Remove the fixing nuts of the diverter switch unit (4 nuts M8, w.s. 13, lock washers, fig. 22). Withdraw the diverter switch unit care- fully from the oll compartment (fig. 23). Keep the diverter switch unit in a vertical position. Remove the suction pipe. Withdraw the pipe connection from the tap changer head (fig. 24). Take care of O-rings. Unscrew the remaining bolts (17 nuts M8, w. s.13, lock washers). Lift the tap changer head off the oil compartment supporting flange. Take care of the gasket. 4.2 Assembly of diverter switch oil compartment and tap selector, Mounting the on-load tap For connecting the tap winding and the attachment of tap selector con- changer to the transformer tap changer take-off terminal, follow necting leads active part (core and coils) the instructions according to section 5. The assembly of diverter switch oil Lift the assembled tap changer into the Please note: The connected tap compartment and tap selector as well supporting structure according to sec- leads must not cause any tension o n as connection of tap selector con- tion 4.2 by means of the level traverse the tap changer. The tap leads necting leads should be carried out (see dwg. 890 180 in appendix). Make should be assembled i n such a way according to section 3.3. In this case, sure that the tap changer is in proper as to allow the tap changer to be however, the oll compartment is to be mounting position and fasten it there moved into its ultimate position after lowered by means of the level traverse safely. the bell-type transformer cover set (see appendix, dwg. 890 180) onto the “up. tap selector instead of the tap selector being elevated to the oil compartment. 44 Mounting the bell-type transformer cover Before mounting the bell-type trans- former cover clean the sealing surface of the oil compartment supporting flange. Put the gasket on the flange (fig. 25). Lift the bell-type cover over the trans- former active part and lower it into its final position. Before mounting the tap changer head clean the sealing surfaces (head bot- tom, mounting flange). Put an oil-re- sistant gasket on the mounting flange. Place the tap changer head on the mounting flange. Please note: To allow for final levelling leave a clearance of 5 to 20 mm bet- ween tap changer head and support- ing flange. Check the mounting posi- tion of the tap changer head by means of 2 adjusting bolts in the supporting flange of the diverter switch oil com- partment (fig. 25) and marks of supporting flange and tap changer head (fig. 26) which allow for assembly Inthe correct position. Attach the tap changer head to the mounting flange. Slightly lift the tap changer by means of the level traverse (see fig. 27 and appendix, drawing 890 180). Make sure that all supporting flange studs slide easily through the fixing holes of the tap changer head. Screw the nuts to all studs which are not covered by the diverter switch supporting plate (fig. 28, see also section 4.1). Use 17 nuts M8 (wrench size 13, max. torque 14 Nm, lock Mount the cover on the tap changer Attach the position indication dial. washers). Put the clip on the shaft end. head. Make sure that rubber gasket in The dial can be mounted in correct the cover is in its proper position. Remount the suction pipe. Make sure Equally fasten the 24 screws M10 position only by means of its coupling that the O-rings are properly placed. pin (fig. 29). (wrench size 17), max. torque 34 Nm The O-rings should be greased slightly (fig. 30). before mounting. Remount the diverter switch unit. Make sure that the diverter switch supporting plate is in the proper position in the tap changer head. Attach the supporting plate by means of 14 nuts M8 (wrench size 13, max. torque 14 Nm, lock washers). 5. CONNECTION OF TAP WINDING TAP CHANGER TAKE-OFF LEADS The tap winding has to be connected to the tap changer according to the wiring diagram supplied with the particular tap changer equipment. Please note: All connections to the tap changer should be made carefully and locked safely. The tap leads should be assembled in such a way to allow for Coarse tap selector Reversing switch connecting all leads to the tap changer without tension. If necessary, lead ends should be shaped in form of expansion loops. Tap leads in the vicinity of the change-over selector (see fig. 31... 33, reversing switch, coarse tap selector) must be placed properly to allow for sufficient clearance to change-over selector moving parts otherwise causing blocking of the tap changer. Tap selectorT 600 31 Tap selector T 1000, tap selector size C , D and DE 32 HII Tap selector T 1000 tap selector size E 33 In case of single-pole tap changers T11001-CD, T11502 a n dT | 2002 parallel operating tap selector termi- nals should distinctly be connected in parallel to avoid a possible commuta- tion surge during tap change operation. 5.1 Tap selector T 600 (fig. 34) Fine tap selector terminals are flat shaped and provided with a through-hole for M10-screws or equi- valent to enable tap leads being con- nected by means of cable shoes (fig. 35). Flat side of terminal is horizontal or vertical alternatively. Screening caps will be supplied on request, for attach- ment see fig. 36. Change-over selector terminals Reversing switch (fig. 37, 38): Terminals ( + , =) are with one flat side, provided with a through-hole for M10- screws or equivalent. Flat side of terminal is vertical only. Terminals (K) and terminals (n-1) of fine tap selector as extended fine tap selector terminals with through-hole for M10-screws or equivalent. Flat side of terminal is horizontal only. Coarse tap selector (fig. 39): Terminals (0, + , - ) are same as fine tap selector terminals, flat side of terminal is horizontal only. 10 5.2 Tap selector T 1000, tap selector size C/D (fig. 40) Fine tap selector terminals are flat shaped and provided with a through-hole for M12-screws or equi- valent to enable tap leads being con- nected by means of cable shoes to one or two sides of contact. Flat side of ter- minal is horizontal or vertical alterna- tively (fig. 41). Screening caps (MR-No. 061 606) will be supplied on request, for attachment see (fig. 42). Change-over selector terminals Reversing switch: Terminals ( + , - ) are same as fine tap selector terminals. Terminals (K) are flat shaped with through-hole for M12-screws or equivalent. Flat side of terminal is only vertical (fig. 43). Screening caps for terminals (K) will be supplied on request (MR-No. 085 915), for attachment see fig. 44. Coarse tap selector: Terminals (-) are same as fine tap selector terminals. Terminals (+) are flat shaped with through-hole for M12-screws or equivalent (fig. 45), flat side of terminals is horizontal only. Screening caps will be supplied on request (MR-No. 085 915), for attachment see fig. 46). Terminals (0) are same as terminals (K) of reversing switch (fig. 43, 44). 11 5.3 Tap selectorT 1000, tap selector size E (fig. 47) With tap selector size E tap leads can only be connected b y means of solder- ing connectors to their respective terminals. The soldering connectors (see dwg. 893 898), screws and nuts are part of our delivery. Fine tap selector terminals The soldering connectors (fig. 48) will be supplied screwed on the tap selector terminals (fig. 49). For disassembly please proceed as follows: Withdraw screening electrodes by using handles (fig. 50) supplied with the equipment. Unscrew two recess head screws M10 x 30 per contact, remove self- locking nuts and soldering connectors. Perform soldered connection between tap leads and connector. Adjust mount- 50 51 ing position of connector for later at- tachment to the terminal. Slide screening electrode over lead end (fig. 51). Attach lead end to terminal by means of two screws M10 x 30 with self- locking nuts (fig. 52). Use the ratched handle supplied with the first tap selector of size E without charge. Push screening electrode over lead end onto the terminal by applying a considerable pressure (snap-in-attach- ment (fig. 53)). 53 12 Fine tap selector terminals of tap selector bar ”K”’ (with change-over selector only, fig. 54), contact designation (standard) as follows: Designation of terminal 5 No. of contacts per plane 10 12 14 16 18 Unscrew two nuts M10 (w.s. 17) and remove the soldering connector. Perform soldered connection between lead end and connector. Attach solder- ing connector by two screws M10 with self-locking nuts, recommended torque (40 + 5) Nm. Change-over selector terminals Reversing switch: Terminals ( + , -) are same as fine tap selector terminals (see above). Terminal K: Unscrew two nuts M10 (w.s. 17) and remove soldering con- nector. Perform soldered connection between lead end and connector. Attach soldering connector by two screws M10 with self-locking nuts, recommended torque (40 + 5) Nm (fig. 55). Coarse tap selector: Terminals (-) are same as fine tap selector terminals (see above). Terminals (0) are same as terminals (K) of reversing switch (fig. 55), see above. Terminals (+) are flat shaped with through-hole for screw M12 (part of de- livery), flat sides are horizontal only. The tap lead can only be connected t o the terminal by using appropriate cable shoes. The entire connection is to be screened by using screening caps (MR-No. 085 915) according to fig. 56 55 and insulated after assembly by a soft- paper insulation thickness of 5 mm at least. Screening caps, screws M12 x 50 and self-locking nuts are part of our delivery. 56 13 5.4 Terminals of the potential switch Terminals are thread studs M12 with selfdocking nuts (w.s. 19) and screening caps (see fig. 57) to enable leads being connected by means of cable shoes, self-locking nuts should be tightened by max. torque of 50 Nm. Please note: Tap leads in the vicinity of the potential switch should be placed properly t o allow for sufficient clearance to the movable switching rod (fig. 58) otherwise causing block- ing of the change-over selector drive mechanism. I 55 Connecting the tap changer take-off lead The tap changer take-off lead should be connected to the connecting ring of the diverter swich oil compartment and locked safely. Connecting screws are not part of our delivery but screening caps. Tap changerT 111600, T i l 1000, T1601, T11001-C/D One through-hole of the connecting ring (staggered through 120°) with 13 mm dia. for M12-screws or equi- valent (fig. 59). Tap changer T | 1001-DE/E, T11502, T12002, T13000 Three through-holes of the connecting ring (staggered through 120°) with 11 mm dia. for M10-screws or equi- valent (fig. 60). 14 6. TRANSFORMER RATIO TEST 7.1.1.2 Drying in the transformer tank If the transformer is to be dried in its We recommend to ratio-meter the tank the interior of the tap changer transformer with a low AC voltage must be connected to vacuum, as the before drying. For operating the drive tap changer head cover remains shaft in the tap changer head a short closed during the entire drying pro- tube of nominal width 25 mm with an cess. The tap changer head cover is insert coupling bolt of 12 mm dia. to- vacuum-proof. gether with a hand wheel or a hand crank may be used. To ensure sufficient drying of the in- terior of the oil compartment and tap In case of tap changer set 3x TI... changer insert, connect a by-pass tube three tap changer heads have to be of at least 25 mm nominal width bet- connected by the horizontal part of the ween the transformer tank and the drive shaft (see section 9.2 and 9.8). 7. DRYING PROCEDURE AND connecting flange to the oil compart- FILLING IN THE OIL ment. When using an MA 7, 16.5 drive shaft revolutions are required for one tap For ease of handling connect the by- change operation, when using an 7.1 Drying procedure pass tube either between flanges E2 MA 9, one drive shaft revolution is and Q or flanges E2 and R of the tap required. The diverter switch action The dielectric properties of the tap changer head (position of connecting can be heard distinctly. changer can only be guaranteedif the flanges see section 8 and drawing tap changer is subjected to a drying 893 899 of appendix). For operating the change-over selector. treatment according to the following a higher torque is necessary. The tap instructions (7.1.1 or 7.1.2). Procedure, temperature, pressure and changer end positions shown on the duration of the drying process are circuit diagram supplied with the described initem 7.111. delivery must never be overrun. It is 7.1.1 Vacuum-drying process therefore necessary to check the operating position through the inspec- 7.1.2 Vapor-phase drying process tion glass in the tap changer head 7.1.1.1 Drying in the autoclave cover (fig. 61). Keep the number of tap Before starting the drying procedure, change operations t o a minimum as When drying in autoclave remove the open the kerosene drain plug (fig. 62) long as the tap changer has not been tap changer head cover first. and drain the condensate from the oil immersed in oil. After the transformer compartment. ratio test the tap changer has t o be set Heating up back to the adjustment position in the tap changer in air of atmospheric The kerosene drain plug is easily which it was delivered by MR. pressure with a temperature rise of accessible between oil compartment The position is indicated in the wiring 10°C/hour to a maximum final tem- bottom and tap selector gear. diagram delivered with the equipment. perature of 110°C. Unscrew from outside. The kerosene drain plug is loss-proof Note: If the transformer is to be vapor- Preparatory drying and must b e closed safely after the phase dried in its own tank, open the in circulating air with a temperature of drying process. kerosene drain screw (see section 110°C max. applied to the tap changer 7.1.2). for a duration of 20 hours. Vacuum-drying with a temperature of 110°C max. applied to the tap changer and a residual pressure of 10-3 bar for a duration of 60 hours. 24mm 62 15 When drying the transformer in its own - 7.1.3 PLEASE NOTE: D o not 8. PIPE CONNECTIONS tank (see section 7.1.2.2) the drain operate the tap changer plug, in general, i s not accessible without oil after drying from outside and can only be The tap changer head is provided with opened from inside the oil compart- If, however, it is unavoidable to sub- three pipe connections. After loosen- ment. sequently operate the tap changer fill ing the thrust collar (4 boits M10, the diverter switch oil compartment w. s. 17) these pipe connections can Before unscrewing the plug from inside with oll and totally immerse the tap be swivelled according to by socket wrench (see appendix, dwg. selector in oll. requirements. 890 182) withdraw the diverter switch and re-insert again afterwards. 7.2 Filling in the oll 8.1 Pipe connectionR for Please note: The kerosene drain plug protective relay RS 2001 must be closed again after the drying Put the cover on the tap changer head. process (withdraw the diverter switch Tighten all 24 cover bolts M10 (wrench For mounting the protective relay unit, close the drain plug, re-insert the size 17, max. torque 34 Nm). RS 2001 follow our Operating diverter switch unit). Instructions No. 59. Tap changer and transformer are filled u p with new oll under vacuum. Please note: 7.1.2.1 Drying i n the autoclave For this purpose use pipe connection S or R. For applying vacuum t o the tap The relay serial number Is the same as When drying in autoclave remove the changer a by-pass tube between con- that of the tap changer. tap changer head cover first. nections E2 and Q is to be installed in order to evacuate both oil compart- The relay is to be mounted as near to Heating up: ment and the transformer simultane- the tap changer head as possible and by admitting the kerosene vapor at a ously. in horizontal position. temperature of about 90°C. Keep this rate of temperature constant for 3 to 4 The arrow on the relay should point hours. towards the oil conservator when mounted. Drying: by increasing the vapor temperature The pipe t o the oil conservator should by about 10°C per hour to the desired be installed with an inclination of at final temperature with not more than least 2%. 125°C applied to the tap changer. The drying time is normally the same as the transformer drying time. 8.2 Pipe connections S for suction pipe 7.1.2.2 Drying in the transformer tank This is the connection for the feeding pipe of a stationary oll filter. If there is If the transformer is to be dried in its no filter, the pipe connection should be tank, the tap changer head cover re- provided with a pipe with drain cock mains closed during the entire drying easily accessible on one side of the process. To ensure sufficient drying of transformer tank. the interior of the diverter switch oil compartment and of the diverter switch unit connect a common tube of at least 8.3 Pipe connection Q 50 mm width between the vapor lead (special design, required for and two connecting flanges of the tap stationary oil filter only) changer head open to the oil compart- ment. This Is the pipe connection for the return pipe of a stationary oil filter. Use flanges Q and R for tap changers type T. (For position of connecting Otherwise there is a dummy plug flanges see section 8 and dwg. 893 899 instead of the pipe connection. of appendix.) 16 8.4 Connection flange E2 In general, this flange is covered by a dummy plug. The flange hole is open to the transformer tank directly be- neath the tap changer head. Optionally, it may be connected to the gas accumulating tube for the Buchholz relay. 9. MOUNTING THE MOTOR 9.2 Mounting the bevel gear 9.3 Mounting the drive shaft DRIVE UNIT, THE BEVEL. GEAR AND THE DRIVE The bevel gear is to be attached to a The drive shaft shall be assembled SHAFT support on the transformer cover by according t o our Operating Instruc- means of 2 bolts (through-holes tions No. 42. The drive shaft is the 18 mm dia., see appendix, dwg. mechanical connection between the 9.1 Mounting the motor drive unit CDm 6400). motor drive and tap changer head. (see appendix, dwg. 895 660 The bevel gear diverts the driving force and 895 661 respectively) Please note: from the vertical to the horizontal direc- tion. Accordingly, the vertical part of For comprehensive information see Make sure that bevel gear serial the drive shaft is to be mounted bet- our Operating Instructions No. 40 for number and tap changer serial number ween motor drive unit and bevel gear, motor drive unit MA 7 or No. 80 for correspond. whereas the horizontal part of the drive motor drive unit MA 9 respectively. shaft is t o be mounted between bevel The horizontal part of the drive shaft gear and tap changer head. The drive Please note: shaft itself consists of a square tube must be in proper alignment with the trunnion in the tap changer head. and is t o be connected on both ends Serial no. of motor drive unit and tap After loosening the thrust collar to the respective implement by two changer must be the same (name- (6 bolts M8, w.s. 13) the upper gear coupling brackets and one coupling plate). unit can be swivelled (fig. 64). bolt. After adjusting the upper gear unit, When mounting the drive shaft make Motor drive unit and tap changer must the thrust collar must be re-tightened sure that the trunnions to be connec- bein the same operating position (this (max. torque 15 Nm). Tablock the ted are propertly aligned. position is indicated inthe connection Screws. diagram supplied with the equipment). Square shaft, coupling brackets, bolts, For special bevel gears and for inter- nuts and lock tabs are made of corro- The adjustment position is marked on sion-proof steel. We recommend, mediate bearings of the vertical or the position indicator of the motor horizontal part of the drive shaft these however, to apply the same outside drive by means of an arrow. instructions apply analogously. varnish here as to the transformer tank. The motor drive unit shall be mounted at the provided place on the transfor- mer tank in a vertical position and pro- tected against excessive transformer vibrations. The square shaft and plate for the foot (4) Mount the horizontal drive 10.2 Final oil filling step protection on the transformer shaft between the tap changer cover are supplied in oversize (various heads by turning the trunnions. Fill up the tap changer completely with standard lengths). These parts must be transformer oil via the oil conservator. cut to the required size before 5) Return the tap changer set, that mounting. Is all tap changer poles to- Bleed the tap changer head via the gether, into the adjustment bleeder screw in the head cover (E¢): Finally equalize the rotation lag bet- position.The adjustment posi- Remove screw cap M30/w.s. 36 ween tap changer and motor drive unit tion is reached by turning the (fig. 65), lift valve tappet by means of according to Operating Instructions, drive shaft in clockwise a screw driver. for MA 7: No. 40, for MA 9: No. 80. direction. Bleed the suction pipe (S) via the Check simultaneous operation ~~ bleeder screw of the elbow: cap nut Tap changers 3xT1... of all diverter switches. M16 (w.s. 22, max. torque 9 Nm), Check coincidence of position slotted bleeder screw M6 (max. torque This procedure is also recommended of all tap changer heads and the 2 Nm, fig. 65). for all other type T designs. motor drive unit. Mount the vertical drive shaft. Due to the special arrangement of the 10.3 Ground connections tap changer poles in three columns, the horizontal drive shaft must be Connect the ground screws (2 screws mounted between the three tap chan- M12 with nut, w.s. 19, max. torque ger heads above the tank cover. Since 60 Nm, of the tap changer head to th a swivelling of the upper gear unit will transformer cover. : initiate a switching action make sure that the adjustment position of the di- Connect the ground screw (M12, verter switch is regained after align- w.s. 19, max. torque 60 Nm) of the ment of the gear units. motor drive housing to the transformer tank. For this purpose proceed as follows: (1) Check that the operating positions of all columns are 10. PUTTING THE TAP identical (tap changer head, CHANGER INTO OPERATION inspection window). The tap IN THE TRANSFORMER changer poles must be i n the FACTORY adjustment position. (2) Turn the upper gear unit of the 10.1 Operational tests tap changer heads into the coupling position and fix there Before applying voltage to the trans- (tighten thrust collars). former check the mechanical opera- Observe the arrow on the drive tion of tap changer and motor drive. shaft flange below the punched serial number. The direction of For these test operations the tap. the arrow indicates the rotation changer has to be run through the 10.4 Electrical transformer tests sense when cranking the motor complete operating cycle... drive clockwise and must be After the preceding operations perform identical on all gear units. Make sure that i n each operating the transformer acceptance tests. position the indicators of motor drive (38) Operate the tap changer poles and tap changer (tap changer head) separately by one step by ro- read the same position. tating the trunnions counter- clockwise until the diverter Make sure that in both end positions switch operates once. the electrical and mechanical limit stops function automatically (see Check coincidence of operating Operating Instructions No. 40 for positions of all tap changer motor drive unit MA 7 or No. 80 for heads. motor drive unit MA 9 respectively). 18 11. TRANSPORTING THE 12. PUTTING INTO SERVICE AT 13. SUPERVISION IN SERVICE, TRANSFORMER TO THE THE OPERATING SITE FAILURES OPERATING SITE Before putting the transformer into It is only necessary to inspect the tap If the transformer is to be transported service, operational tests of tap chan- changer head, the protective relay and without the motor drive unit, set the ger and motor drive have to be per- the motor drive unit occasionally. motor drive to the adjustment position, formed according to section 10.1. uncouple and dismount. At the same time check the function of Pay special attention to: the protective relay. For remounting the motor drive unit oil tightness of sealings of the tap follow the instructions according to The protective relay has to be inserted changer head, the protective relay and section 9.1. into the tripping circuit of the circuit the pipe connections, breakers so that energization of the If the transformer is stored or trans- protective relay switches off the trans- tightness of the motor drive housing, ported without oil conservator, a by- former immediately (see Operating pass tube must be installed between Instructions No. 59 for protective relay proper function of the electrical space the interior of the tap changer and RS 2001). heater in the motor drive unit, the transformer tank t o compensate the static pressure caused b y expan- Make sure the circuit breakers switch- the condition of the control apparatus sion of oil. ing off the transformer operate when in the motor drive unit. the test push button »OFF« is pressed. Install this by-pass tube between pipe Be sure that they energize the trans- In case of a response of the protective connections E , and Q of the tap chan- former only after push button relay it is absolutely necessary to ger head. »IN SERVICE« of the protective relay check the tap changer and trans- has been pressed. former. For short time conditions of 2 t o 4 For this purpose withdraw also the weeks without oil conservator, lower Check whether all stop valves diverter unit. the oil level by approx. 5 litres. between oil conservator and tap In addition see Operating Instructions changer head are open. No. 59 for the protective relay RS 2001. if the transformer is to be transported or stored without oll filling, drain the oil After reconnecting the transformer, tap Before returning t o service, make of the tap changer completely. change operations under load can be sure that the tap changer and trans- performed. Gas accumulating under former are undamaged. Never recon- The interior of the tap changer should the cover of the tap changer head will nect the transformer without prior be conserved and protected in the cause minor oil displacement. checking. same way as the transformer itself (nitrogen-sealing). In case of serious trouble with tap changer or motor drive - provided that When a prolonged stand-by period is the repair cannot easily be done on site expected, connect the heater of the - and in case of a response of the pro- motor drive unit to power. tective relay please contact the autho- rized MR representative, the trans- former manufacturer or Maschinenfabrik Reinhausen GmbH Technischer Service Falkensteinstrasse 8 Postfach 12 03 60 W-8400 Regensburg12 Telefon (09 41) 40 90-0 Telefax (09 41) 4 4203 Telex 6 5 881 Telegramme: oltc reinhausen 19 14. INSPECTIONS Standard values for oil testing according to CIGRE report 12-13 (1982) applying * to transformer oil at service temperature: We recommend inspection of the tap Water content”) Dielectric strength”) changing equipment at regular inter- vals to maintain a high level of Neutral-end tap changers 40 ppm 30kv/2.5 mm operating reliability. Single-pole tap changers 30 ppm 40 kv/2.5 mm *) measured according to Karl-Fischer method based on IEC Publication 814 In general, the inspection can be carried out by qualified and trained personnel within one day provided it is of measured accordingto DIN 57 370 Teil1/VDE 0370 Teil 1/12.78 1985) well prepared and organized. On-load Transformer Number of tap change operations The number of tap change operations tap changer rated-current without oil filter with oil filter determining the inspection intervals indicated in table | are figures based T 111600 upto 600A 80000 100 000 on experience with oil qualities T I 1000 upto 600A 8 0 000 100 000 normally used. u p t o 1000 A 6 0 000 100 000 Regardless of the number of opera- T1601/600 upto 600A 8 0 000 100 000 tions we recommendinspection after 6 T11001/1000 upto 600A 80000 100 000 to 7 years of service or after 4 years of u p t o 1000 A 6 0 000 100 000 service respectively if the tap changer T11502/1500 u p t o 1 0 0 0A 6 0 000 100 000 operating voltage is equal or higher u p t o 1500 A 5 0 000 100 000 than 220 kV. T12002/2000 u p t o 2000 A 4 0 000 8 0 000 If the number of operations per year is T 13000 u p t o 3000 A 40.000 80000 20 000 or higher, the use of our oil filter plant type 51 (see Operating Instruc- Table!l Inspection intervals tions No. 18) is recommended. Filtering of switching oil allows to extend the inspection and oil change intervals. Continuous filtering also increases the mechanical life of the diverter switch by immediately 15. APPENDIX removing all abrasive particles. Installation drawings The user should regularly test the T I 600, T1601, T I 1 0 0 1 - C / D , T 1 1 5 0 2........ 894 242 baseaaarees FE. transformer insulating oil. The dielec- T I 1000, TI11001-DE/E, T12002, T 1 3 0 0 0...... c c 0 v n e r s n n n s n n a n 894 240 tric strength and the water content of the oil (record oil temperature during Tap selector terminals sample-taking) must comply with the THI600, TI601, TI1001-C/D, T I 1 5 0 2...... c c v v v i i r i r n n n n n n a n n 893 913 respective standards such as IEC Publication 422 (1973), DIN 57 370 Teil 2/VDE 0370 Teil 2/12.78. T I I 1000-C/D/DE, T11001-DE, T 2 0 0 2 C/D/DE, TI3000......co0vvnnns frets aaa rrerae eae 893 829, 893 830 If inspection has not been performed TUI1000-E, TI1001-E, TI12002-E.........cccivvunnnn, 893 832, 893 833 by MR-personnel, please give us your Assembly instruction for tap selector terminals, report for data collecting purposes. tapselectorsizeE....... iii i iii eae 893 826 This will enable us to give you useful Soldering connectors for tap selector terminals, recommendations for your next tapselelctorsize E.... coin e e i ri iiraeeas 893 898 inspection. Tapchangerhead...........c.ciiiiiiiriiinninracnsrnnnnes 893 899 Drilling template fortap changerhead.............cccciivvniint, 890 183 Supporting flange for bell-type transformercover.................. 890 753 Leveltraverse... vue iii ir triste sata 890 180 Socket wrench for kerosene drainscrew inne.........coviiiiie 890 182 Protective relay RS 2001, dimensiondrawing............ccvvaunnn 892 608 Motor drive unit MA 7, dimensiondrawing........ccevveineinninn 895 660 Motor drive unit MA 7/8, dimensiondrawing................ooan, 895 661 Bevel gear CD 6400, dimension drawing........ooeevivniianenes 892916 20 " FLAT = £4 SURFACE 91 12 wf Ee] 25a ¥ WITHDRAWAL. HEIGHT 1500 MM ———————————ef ¥ : AV fase TAKE-OFF TERMINAL 76 THICKNESS T1001C/D T1502 TAKE-OFF TERMINAL MOUNTING FLANGE ON TRANSFORMER COVER FONG BOLT M12 GASKET FOR TAP CHANGER HEAD POSITION INDICATOR INSPECTION WINDOW DRIVE SHAFT FOR POSITION INDICATOR THROUGH- HOLE 15mm TAP CHANGER HEAD 24 COVER OF TAP CHANGER HEAD 25 CENTRIC GEAR UNIT WITH DRIVE SHAFT 25a 26 PPE CONNECTION R FOR PROTECTIVE RELAY 27 PIPE CONNECTION S FOR SUCTION PIPE 28 PIPE CONNECTION Q FOR RETURN PIPE[WITH OIL FILTER UNIT ONLY) 29a BLEEDER SCREW OF TAP CHANGER HEAD COVER 290 PIPE CONNECTION FOR TRANSFORMER OIL 29¢cBLEEDER SCREW FOR SUCTION PIPE 31 DIVERTER SWITCH OIL COMPARTMENT 32 BOTTOM OF OIL COMPARTMENT WITH SPACER 32a AND 80LT 32b 33 GRADING R I N G I W150 ITHKV AND 2 2 0KV ONLY ) 34 TERMINAL OF DIVERTER SWITCH OL COMPARTMENT 35 TAP CHANGER TAKE-OFF TERMINAL (WITH TIX 600 NEUTRAL) 36 SUCTION PIPE 41 SUSPENSION OF TAP SELECTOR 42 TAP SELECTOR GEAR 43 FINE TAP SELECTOR PROVIDE SUFFICIENT 44 CHANGE- OVER SELECTOR CLE. 4S TAP SELECTOR TERMINAL TRANSFORMER TANK BOTTOM ARANCE 46 CHANGE-OVER SELECTOR TERMINAL "X“/"0" RESP 47 CHANGE-OVER SELECTOR TERMINAL “+“/“~"RESP. 48 CONNECTING LEAD TAP SELECTOR/DIVERTER S777 SWITCH 51 DIVERTER SWITCH UNIT 52 SUPPORTING CYLINDER OEAR PLATE S4 FIXING BOLT $5 LIFTING LUG 56 TRANSITION RESISTORS MASCHINENFABRIK O n load tap changer type T N 2664.1 e n M R REINHAUSEN Model T 11 600, T1601, T11001-C/D, T 11502 894 242:1E Installation drawing 290 5 22 — % 25a 2% —0 a] —T— 8 — b | [7A 7 3 & 53 7 52 | z 8 2 I : HH x T U1 1000 ake-oFF TERMINAL oi 2 2 § THD 1 3B i = 10 THICKNESS Ss = A {Jp — tT 17 i Ia% e| So] —16 T11001-DE/E 14 2 CJD TAKE-OFF TERMNAL ur 1 ) 35 32 48 J NF 11 MOUNTING FLANGE ON TRANSFORMER COVER 12 FIXING BOLT M12 po 13 GASKET FOR TAP CHANGER HEAD 1% POSITION INDICATOR 15 INSPECTION WINDOW ] 16 ORIVE SHAFT FOR POSITION INDICATOR 7 THROUGH- HOLE tSmm DIA. —] 42 21 TAP CHANGER HEAD 43 — 4h 22 COVER BOLT — 23 GASKET FOR TAP CHANGER HEAD COVER 24 CQVER OF TAP CHANGER HEAD 25 CENTRIC GEAR UNIT WITH DRIVE SHAFT 25a 26 PIPE CONNECTION R FOR PROTECTIVE RELAY 27 PIPE CONNECTION S FOR SUCTION PIPE 28 PIPE CONNECTION Q FOR RETURN PIPE (WITH OIL FILTER ONLY) 29a BLEEDER SCREW OF TAP CHANGER HEAD COVER 29b PIPE CONNECTION FOR TRANSFORMER OIL 29c BLEEDER SCREW FOR SUCTION PIPE 31 DIVERTER SWITCH Oil. COMPARTMENT 32 BOTTOM OF OIL COMPARTMENT 33 GRADING RING (WITR S O K V AND 220KV ONLY) 34 OF SWITCH OIL MENT 35 TAP CHANGER TAKE -OFF TERMINAL (WITH T IH 1000: NEUTRAL} 36 SUCTION PIPE 41 SUSPENSION OF TAP SELECTOR 42 TAP SELECTOR GEAR 43 FINE YAP SELECTOR T T TT 44 CHANGE-OVER SELECTOR 45 TAP SELECTOR TERMINAL FOR TAP SELECTOR SIZE C/0,SEEN26331593629.1N2634)893830, 4 TAP SELECTOR TERMINAL FOR TAP SELECTOR SIZE E, SEEI N 2 5 0 8 0 (N2535839812 0 6 8 2 6N2636893633 48 CONNECTING LEAD TAP SELECTOR/DIVERTER SWITCH roves s e c u CLEARANCE 5, Sym 53 GEAR PLATE vo TRANSFORMER TANK BOTTOM 54 FIXING BOLT TT 7 7 b t TRANSITION RESISTORS MASCHINENFABRIK On load tap changer type T N 2663.4 en M R REINHAUSEN Model T 1111000, T 1 1001-DE/E, T 12002, T | 3000 894 240:4E EE PE Installation drawing WITH SCREENING CAP WITHOUT SCREENING CAP {SPECIAL DESIGN) (STANDARD — | TN YN gs i. ‘ TERMINAL OF FINE TAP SELECTOR (EXCEPT CONTACT — “M=-1" WITH REVERSING SWITCH) ja-2() N- AND OF COARSE TAP SELECTOR Ebi] 056 919 J65_.oc. REVERSING SWITCH TERMINAL “ N - 1" OF FINE =R TAP SELECTOR AND TERMINAI —— Li "OF REVERSING SWITCH REVERSINGSWITCH NY Bb y TERMINALS (+) AND{~} / RL © x 4 MASCHINENFABRIK On load tap changer type T N 2641 en M R REINHAUSEN Tap selector terminals: T lll 600, T1601, 893 913:0E I E— T11001-C/D, T 1 5 0 2 VARIANT (D VARIANT © WITHOUT SCREENING CAPS WITH SCREENING CAPS {STANDARD} TERMINALS OF FINE TAP SELECTOR AND CHANGE- OVER SELECTOR (EXCEPT TERMINAL *K") 7 77 - ~=P13 [= | J 4 | ZL 4 _a Ne —— \_/ p 2 5 —=}46 \.~ ~ J 1] 061606: prd— OF FINE TAP SELECTOR AND CHANGE- OVER SELECTOR SEE DIM.DWG. TAP SELECTOR TERMINAL " K " " $556 — ———— CT / \| 7) VEE TAP SELECTOR ( CENTER LINE { i = ; [1 | [ } EE Ne] i « | § A 085915: MASCHINENFABRIK O n load tap changertype T N 2633.4 e n M R REINHAUSEN Tap selector terminals, tap selector size C/D (DE): 893 829:4E I SERA T I 1000, T1001, T12002, T | 3000, with reversing switch VARIANT VARIANT @ WITHOUT SCREENING CAPS WITH SCREENING CAPS TERMINALS OF FINE TAP SELECTOR AND CHANGE-OVER SELECTOR [EXCEPT TERMINAL"+, K* AND 0%) FOR DIMENSIONS OFFINE TAP SELECTOR ANDCHANGE-| OVER SELECTOR. SEE DIM.OWG. Gr 650 TO TAP SELECTOR CAGE RING CENTER CENTER LINE « TAP SELECTOR 15%] TAP SELECTOR TERMINAL "+,K” 300 TO TAP SELECTOR CAGE RING CENTER——— —_—— es —— Never LINE OF en =A TAP SELECTOR MASCHINENFABRIK On load tap changer type T N 2634.4 en M R REINHAUSEN Tap selector terminals, tap selector size C/D (DE): 893 830:4E EE EE T I 1000, T 11001, T 12002, T | 3000, with coarse tap selector g TAP SELECTOR TERMINAL WITH mm SOLDERING CONNECTOR I (LOO 069:) 1 BY FOR ASSEMBLY SEE = OWG.(N 2608)893826: l T ] HEXAGONAL RECESS HEAD SCREW M10 WITH HEX NUT lL — SELF -LOCKING ARE PART OF OUR DELIVERY | Lal) FOR DIMENSIONS OF TAP SELECTOR | AND CHANGE -OVER SELECTOR SEE DIM. DWG. ODD-NUMBERED TAP SELECTOR TERMINAL ON K - B A R WITH $552 ————= SOLDERING CONNECTORII( LOOO70:) HEX HEAD SCREW M10X30AND HEX NUT SELF-LOCKING ARE PART OF OUR DELIVERY TORQUE H M R -~ suPPLY 552 — = K -TAP SELECTOR TERMINAL" K "WITH SOLDERING CONNECTOR II {LOO 0 7 0 : ) HEX HEAD SCREW M 1 0 x 4 0 AND HEX NUT SELF-LOCKING ARE PART OF OUR DELIVERY [ \ [ U K MR- SUPPLY SOLDERING H O L E D I A. ALTERNATIVELY: 3% WITH 1 HOLE # 1 4 2 , 152...26,2 2 HOLES 1 2 2 , 132...21,2 MASCHINENFABRIK On load tap changertype T N 2635.4 e n M R REINHAUSEN Tap selector terminals, tap selector size E, T lll 1000, 893 832:4E T11001, T12002, with reversing switch F M R ~ SUPPLY TAP SELECTOR TERMINALS OFTAP SELECTOR AND CHANGE-OVER SELECTOR WITH SOLDERING CONNECTOR 1{LOO0S9:) (EXCEPT TAP SELECTOR TERMINALS OF K-BAR " 0L* ) AND-TAP SELECTOR T E R M I N A FOR ASSEMBLY SEE DWG.IN 2608) 853826: | HEXAGONAL RECESS HEAD SCREW M10 HEX NUT SELF-LOCKING ARE PART OF OUR DELIVERY FOR DIMENSIONS OF TAP SELECTOR AND CHANGE -OVER SELECTOR SEE DIM. DwWe. O Re r ] OFRTAP S E L E C T— 655 TO C E N T E TAP SELECTOR TERMINAL “ 0 * CAGERING WITH SOLDERING CONNECTOR 1 (LOO 0702) X / CENTER LINE OF TAP VIEW X ho & ODD-NUMBERED TAP SELECTOR TERMINAL ON K-BAR WITH SOLDERING CONNECTOR | (Loo 071) HEX HEAD SCREW M1Dx30AND HEX NUT SELF-LOCKING ARE PART OF OUR i "w DELIVERY 3 MR- SUPPLY~ ~ SOLDERING HOLE DIA. ALTERNATIVELY Fe WITH | HOLE # 142 ,52...262 2 HOLES $ 1 2 2 , B 2... 2 1 , 2 $552 — 56 E RTAP 300 TO C E N T OF O R RING S E L E C TCAGE -== TAP SELECTOR TERMINAL " + " AND "K"~ d ~] CENTER LINE OF TAP SELECTOR F- PAPER INSULATION RECOMMENDED SOT I N GHEX HEAD SCREW M12x50 S C R E E NCAF, AND HEX NUT ARE P A ROFT OUR DELIVERY MASCHINENFABRIK O n load tap changertype T N.2636.5 e n M R REINHAUSEN Tap selector terminals, tap selector size E, T l i l1000, 893 833:5E T 11001, T 2 0 0 2 , with coarse tap selector Z= p N 2608.1 e n 893 826 1E a3dino3y ( © HOLI3NNOJ ONI¥IAT10S 40 LNIWHOVLLY Ji AINJWHIVLLY ¥314V NIVOV NMVHAHLIM 3 9 AVW | 3004103713 *310N (IVNINYAL ¥OLO313S dvi OL(1)3A0YLIT TI ONINIIHIS 40 INIWHOVLLY NI-dVNS {X1VNTIANGNI a33qH0 38 NV) SL4vd) Tap selector size E, connection of tap lead L43SN13AINA NOOVX3H:915 £80— 3131dW00 | O n load tap changertype T L3HOLV:615£80 [1:1 38NL ONINIHLON3T Vv LINNOW LON 0 d {ANZATIAA 1SHId FHL Hod) HIN AG O3[TddNS L3HOLIVY 9) @avn (© STTANVH 40 SNVIW AG ()SIA0YLIT TI ONINIZHIS MVHAHLIM — WAV, DATS MASCHINENFABRIK AVA y aV a V A V REINHAUSEN AY3AIT30 HNO H0 Ly4vd S1391A30 (© MR SOLDERING CONNECTOR 1 (L00089:) APPLICATION: FINE TAP SELECTOR TERMINALS, TERMINAL(+) S & [-]) OF REVERSING SWITCH. TERMINALS (~) OF COARSE TAP SE