B11 LMSS Module 4 Rev 03 Secure PDF
Document Details
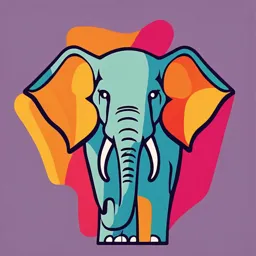
Uploaded by BravePoisson
null
Tags
Summary
This is a presentation about B11 LMSS Module 4. The document details safety services, technical safety, and various aspects within the module.
Full Transcript
DO NOT COPY – DO NOT SHARE We’ll be with you shortly B11 LMSS™ Welcome to B11 LMSS Module 4 DO NOT COPY – DO NOT SHARE Safety Services UK and EU Lead– Matt Chandy...
DO NOT COPY – DO NOT SHARE We’ll be with you shortly B11 LMSS™ Welcome to B11 LMSS Module 4 DO NOT COPY – DO NOT SHARE Safety Services UK and EU Lead– Matt Chandy 3 years experience supporting Safety Interlocks Customer Application Support Manager VP Technical Safety – Jenny Tuertscher Expert member of ISO TC199 WG3, WG5, WG6, WG7, WG8 & ISO TC313 WG1 Member of ANSI B11 committees FS Engineer (TÜV Rheinland) #14247 / 17 – Machinery B11 LMSSTM Certification #AA311265118 B11 LMSS™ Welcome to B11 LMSS Module 4 DO NOT COPY – DO NOT SHARE Join in! Time Session Ask questions at any time 15 Mins B11.20 Setting the Scene Breaks We will aim for a break every hour or so 150 Mins Requirements with one longer break in the middle 15 Mins R15.06 Setting the Scene Mute 90 Mins Requirements When you’re not talking please use the mute button Reactions Please make use of the “reaction” buttons Lower your hand by pressing it again B11 LMSS™ Overview B11 LMSS DO NOT COPY – DO NOT SHARE Module 1 Module 2 Module 3 Module 4 Module 5 Examination Introduction to B11.19 Risk B11.26 Integrating LOTO and 50 Multiple Standards and Reduction Functional Machines and electrical safety choice questions Regulations Measures Safety Robotics ANSI Z244.1 and 90 Mins B11.0 Safety of Inherently Safe Performance B11.20 and RIA NFPA 79 Machinery By Design Levels R15.06 Risk Engineering Categories Assessment Controls Control General Administrative Reliability Requirements Controls Fault considerations B11 LMSS™ B11 LMSS Scope DO NOT COPY – DO NOT SHARE This course will instruct you on: Standards and Regulations What are machinery safety standards Why are they useful How do you use them Overview of the key standards This course does not: Cover specific machinery/industry details Cover every single requirement laid out in the standards and regulations (But it will show you how to find them!) B11 LMSS™ DO NOT COPY – DO NOT SHARE ANSI B11.20 (2017) Safety Requirements for the Integration of Machinery into a System The primary objective of this standard is to eliminate or control hazards to personnel associated with integrated machinery systems by establishing requirements for the construction, operation and maintenance of these machine systems. To accomplish this objective, responsibilities have been assigned to the supplier (e.g., manufacturer, rebuilder, reconstructor, installer, integrator), the user, the modifier, and personnel in the working environment. B11 LMSS™ Learning Objectives DO NOT COPY – DO NOT SHARE Introduction to B11.20 Responsibilities Design, Construction, Re-construction and Modification Layout, Installation, Testing and Start-up Risk Reduction Measures Set-up, Operation & Maintenance Training Decommissioning B11 LMSS™ B11.20 History DO NOT COPY – DO NOT SHARE Approved 1991 Machine Tools - Manufacturing Systems/Cells - Safety 1st edition Requirements For Construction, Care, And Use; Approved 2004 Safety Requirements For Integrated Manufacturing 2nd edition Systems Approved 2017 Safety Requirements for the Integration of Machinery Current into a System edition B11 LMSS™ B11 SDC Members DO NOT COPY – DO NOT SHARE Alan Metelsky, FS Eng., Chair / Anne Matthias, PE,Vice-Chair / David Felinski, Secretary Organizations Represented Names of Representatives Organizations Represented Names of Representatives (Delegates and Alternates) (Delegates and Alternates) A3 – Association for Advancing Automation Carole Franklin Jeff Fryman LM - Liberty Mutual Craig Karasack, CSP Julie Thompson, CSP AEC - Aluminum Extruders Council Mel Mitchell, CSP Bradley Wyatt, CSP, CMSE MAG - MAG Automotive LLC Erik Carrier Doug Watts Amazon Robotics Jeread Sines, FS Eng, B11 LMSS Pat Barry MPIF - Metal Powder Industries Federation Bill Edwards James P. Adams ASSP - American Society of Safety Professionals Ted Sberna, Sr. Anne Matthias, PE NIOSH - National Institute for Occupational Safety & Health Richard Current, PE AMT - Association for Manufacturing Technology Russ Bensman Alan Metelsky, FS Eng. Omron Tina Hull, FS Exp. Frank Webster BOEING - The Boeing Company Rhiannon McPherson Mark Ellington & Stephen Thomas OSHA - Occupational Safety and Health Administration Ken Stevanus Mary Bauer, CSP, CIH, B11 LMSS Bridgestone Kenji Furukawa, FS Eng. Joey Hinson, FS Eng. PILZ - Pilz Automation Safety, LP Mike Beerman Dino Mariuz CSA - Canadian Standards Association Andrea Holbeche, P. Eng. Walter Veugen PLASTICS - Plastics Industry Association Jeff Linder Dale Bartholomew Deere & Co. Tony Beeth Scott Winter PMA - Precision Metalforming Association James G. Barrett, Jr. PhD David Klotz Euchner Ron Yemmens Jilani Bouchane PMMI, Assoc. of Packaging and Processing Technology Bruce Main, PE, CSP Tom Egan Exponent, Inc. Stephen Andrew, PE, CSM Alex Zelhofer, PhD, PE PSDMA - Presence Sensing Device Manufacturers Association Jim Kirton Mike Carlson FDR – FDR Safety, LLC Mike Taubitz Joe Wolfsberger, CIH & Luke Contos Rockford Systems Brian Boes Matt Brenner Fortress Safety Jenny Tuertscher, FS Eng., B11 LMSS Joshua Hill Rockwell Automation Darin Magnuson, FS Eng Jonathan Barrett, FS Eng GM - General Motors Corporation Mike Douglas Tony Ross Safe-T-Sense Mike Poynter, FS Eng Federico Badillo Honda Development & Manufacturing of America Todd Dickey Doug Titus SMACHA - Sheet Metal & Air Conditioning Justin Crandol, CSP Rick Di Ioli Contractors National Association IDEM Safety Mark Witherspoon Amir Mohtasham SICK, Inc. Chris Soranno, FS Exp. Nate Gose, FS Exp. Komatsu America Industries, LLC George Schreck James Landowski TMMNA - Toyota Motor Manufacturing North America Chip Boertlein Michael Collier, B11 LMSS B11 LMSS™ B11.20 Subcommittee members DO NOT COPY – DO NOT SHARE B11 LMSS™ Why Participate in B11 Standards? DO NOT COPY – DO NOT SHARE Help your organization or clients achieve acceptable risk with feasible risk mitigation Reflect your company’s voice into future standards Gain a deeper understanding of future standards Great networking opportunity with leading safety specialists in a variety of sectors Exceptional cross educational opportunities B11 LMSS™ B11.20 Scope DO NOT COPY – DO NOT SHARE This American National Standard specifies the safety requirements for the design, construction, installation, set-up, operation, maintenance, modification and decommissioning of integrated machinery systems. An Integrated machinery system (IMS) a) incorporates two or more industrial machines which: can operate independently of each other; and are intended for the purposes of manufacturing, treatment, movement or packaging of discrete parts or assemblies; b) is linked by a material handling system; and c) is interconnected by a control system(s) for coordinated operation. An IMS shall meet the requirements of this standard. Proper application of this standard requires compliance with ANSI B11.0 and ANSI B11.19. B11 LMSS™ DO NOT COPY – DO NOT SHARE Setting The Scene Definitions, Responsibilities and Risk Assessment B11 LMSS™ Setting The Scene DO NOT COPY – DO NOT SHARE Physical Supervisory Op. Station Environment & Control Power Sources Awareness Local Area Network/ Devices Data Link Safeguards & Stop Interlocks Devices Safeguarded Space Hazard Hazard Area Area Hazard Area Hazard Area Raw Material Scrap & Finished & Tooling Expendables Goods Figure A.1 Simple block diagram of an example IMS Figure A.2 IMS example using a robot as a material handling system B11 LMSS™ Example Control Zones DO NOT COPY – DO NOT SHARE B11 LMSS™ Learning Objectives DO NOT COPY – DO NOT SHARE Key Definitions Responsibilities Risk Assessment Process B11 LMSS™ Risk Reduction Definitions DO NOT COPY – DO NOT SHARE Clause 3 Span of Control Predetermined portion of the IMS under control of a specific device. Zone A segmented space within the integrated machinery system. Control Zone An identified portion of an IMS coordinated by the control system. Hazard Zone Any space within or around a machine in which an individual can be exposed to a hazard. Task Zone Any predetermined space within or around a machine in which personnel can perform work. B11 LMSS™ Responsibilities Who & What DO NOT COPY – DO NOT SHARE Clause 4 Supplier the design, construction, installation and risk reduction measures User identifying and mitigating sources of hazards, including hazards associated with the point(s) of operation, layout, installation, set-up, operation and maintenance of the machine and IMS Personnel following the training and safety procedures provided by the user in the operation and maintenance of the machine or IMS B11 LMSS™ Responsibilities Who & What DO NOT COPY – DO NOT SHARE Clause 4 Integrator/Modifier/Rebuilder identify and mitigate sources of hazards, including hazards associated with the point(s) of operation, layout, installation, set-up, operation and maintenance of the machine and IMS use the risk assessment process to reduce risks to an acceptable level where non-standard use or modifications can create additional hazards solicit the original supplier’s recommendations regarding any proposed modification to an IMS where practicable, that may affect the safe operation prior to making any such changes Carry out a risk assessment for the parts of a machine being modified or affected B11 LMSS™ Risk Assessment Process DO NOT COPY – DO NOT SHARE Clause 5 1. Prepare for and Set Limits of the Assessment 2. Identify Tasks and Hazards 3. Assess Initial Risk 4. Reduce Risk 5. Assess Residual Risk 6. Residual No Risk Acceptable? New/Next Hazard Yes 7. Validate Solutions 8. Results/Documentation Assessment Complete B11 LMSS™ Responsibilities & Risk Assessment Pop Quiz DO NOT COPY – DO NOT SHARE Span of control is the predetermined portion True of the IMS under control of a specific device. 1 The safeguarded space is a segmented space False A zone is a segmented within the integrated machinery system 2 space within the IMS The Modifier/Integrator/Rebuilder carries out a risk assessment for the parts of a machine True 3 being modified or affected B11 LMSS™ What did you Learn? DO NOT COPY – DO NOT SHARE Who is responsible for what Supplier, User, Integrator/Modifier/Rebuilder and Personnel The Risk Assessment Process Supplier, User, and Integrator/Modifier/Rebuilder all have responsibilities for their own parts of the process B11 LMSS™ DO NOT COPY – DO NOT SHARE Design, Construction, Re-construction, and Modification B11 LMSS™ Learning Objectives DO NOT COPY – DO NOT SHARE General Design Requirements B11 LMSS™ General Requirements DO NOT COPY – DO NOT SHARE Clause 6.1 The Risk Assessment Process applies:- to the interaction between a complete zone control system and individual separated control systems within the zone to individual control systems in relation to each other within the zone where a system consists of a combination of sections or single units B11 LMSS™ Layout Design Requirements DO NOT COPY – DO NOT SHARE Clause 6.2 Design Considerations a) access and egress; b) work tasks and associated hazards; c) work flow; e) adequate lighting; f) selection and application of engineering controls; g) span of control of the safety-related devices; h) zones; i) physical space for air quality systems; j) physical space for pedestrian movement; k) physical space for other traffic; l) physical space for stock movement; m) solid or liquid waste management. B11 LMSS™ Electrical Equipment Requirements DO NOT COPY – DO NOT SHARE Clause 6.3 NFPA 70 specifies the requirements for the interconnecting equipment (i.e., the wire, cable, conduit, fittings and methods) NFPA 79 specifies the requirements for the system or components, which are provided to operate the integrated system. Fluctuation or interruption in any of the power sources shall not cause any hazardous situations or shall initiate an immediate stopping action. Restoration of power by itself shall not cause any hazardous situations or restart the system. B11 LMSS™ Modes of Operation DO NOT COPY – DO NOT SHARE Clause 6.4 Automatic Mode Allows for access to and performance of tasks with acceptable risk Shall be manually initiated Manual & Special Mode Allows for access to and performance of manual or other specific, identified, tasks with acceptable risk Includes alternate risk reduction measures when existing ones are suspended Shall be manually selected and initiated Shall prevent remote initiation of a hazardous situation Shall prevent an external hazard entering the task zone(s) unless under local control B11 LMSS™ Modes of Operation DO NOT COPY – DO NOT SHARE Clause 6.4 Mode Design designed/constructed based upon the risk assessment; risk assessment determines how a mode is selected and whether supervision is required Mode Selection shall by itself, not generate hazardous situations; require a separate deliberate action to initiate operation; automatically group operational capabilities with risk reduction measures; be accomplished outside the hazard zone; clearly indicate its function. B11 LMSS™ Local Control DO NOT COPY – DO NOT SHARE Clause 6.5 Local Control shall… meet the following requirements…. means for selecting local control shall be located outside the hazard zone; switching between local control and remote control shall not create a hazardous situation; an IMS including multiple control stations, for a single control zone, must ensure that only one station can initiate a hazardous situation at any given time. prevent an external hazard not under local control from entering the zone(s) under local control. B11 LMSS™ Design, Construction, Re-construction, and Modification Pop Quiz DO NOT COPY – DO NOT SHARE NFPA 79 specifies the requirements for the interconnecting equipment (i.e., the wire, False 1 cable, conduit, fittings and methods) It is NFPA 70 Automatic mode shall be initiated False It shall be manually automatically 2 initiated Mode selection shall be accomplished True outside the hazard zone 3 B11 LMSS™ Isolation of Power Sources / Stored Energy DO NOT COPY – DO NOT SHARE Clause 6.6-6.7 Means for isolating all hazardous energy sources shall be provided Energy-isolating devices shall be marked or labelled to identify the power source(s) and span of control Lockout is the primary method of hazardous energy control Loss of power shall not result in a hazardous situation due to the release of stored energy. Means shall be provided for the isolation, containment or controlled release of stored hazardous energy. Where multiple sources of energy are present, each hazardous energy source shall meet this requirement. B11 LMSS™ General Requirements DO NOT COPY – DO NOT SHARE Clause 6.8, 6.9, 6.10 Emergency Movement Where required by the risk assessment a means to enable movement of the system elements in an emergency shall be provided Safety Related Parts of the Control System (SRP/CS) SRP/CS reliability shall be in line with with the level of risk reduction – per the risk assessment Zone Starting/Restarting Start/restart requires an intentional action from outside the safeguarded space Start/restart shall only be possible if all engineering devices associated with that zone are in place and functional and all safety related functions have been reset B11 LMSS™ Emergency Stop DO NOT COPY – DO NOT SHARE Clause 6.11 Emergency Stop Need based on Risk Assessment for entire system or zones Conform to B11.19 and NFPA 79 Function Only one Emergency Stop function for each span of control Hazards existing after e-stop execution shall be controlled Recovery Zone(s) associated with the span of control designed to enable recovery without creating a hazard. B11 LMSS™ Mechanical Equipment Requirements 6.13 DO NOT COPY – DO NOT SHARE Power Transmission Requirements Conform to B11.0 and B11.19 Powered moving parts Shall be safeguarded if constituting a hazard Broken or falling machine components or equipment Designed, secured or guarded to minimize probability of breakage, falling, or uncontrolled energy release Mounting In line with supplier instructions Ladders, work platforms, and walkways In accordance with ANSI A14.3 Sharp edges, corners and projections Supplier shall design and construct without exposed exterior sharp edges, corners and projections B11 LMSS™ Design, Construction, Reconstruction & Modification DO NOT COPY – DO NOT SHARE Clause 6 Fluid impact on operating environment and equipment Interaction between fluids within the IMS and outside shall not create a hazard Risk reduction design requirements Risk reduction measures shall prevent access to the hazard or reduce the risk to an acceptable level when interaction with the IMS is required. Ejected parts or fluids Guards or shields shall protect where practicable Noise Supplier shall document measured levels Noise levels and risks should be considered Location of Awareness Means Clear, unambiguous and located so the intent is readily recognizable B11 LMSS™ Documentation Requirements DO NOT COPY – DO NOT SHARE Clause 6.22 Documentation Minimum Requirements Clear comprehensive description of the system and its installation Consistency of device markings System performance specifications Physical environment specifications Description of potentially hazardous situations and how to avoid them Hazardous energy control (isolation) diagram Information on programming, operation, frequency and method of monitoring maintenance, functional testing, lubrication and inspection, maintenance of the system and risk reduction measures. Risk reduction measures and the hazards they control Alternate risk reduction measures (when primary ones suspended) Manuals covering individual machines and auxiliary equipment B11 LMSS™ Requirement for Rebuild or Modifications DO NOT COPY – DO NOT SHARE Clause 6.23 An IMS that is modified or remanufactured for a new configuration, function, capability or location shall be based on a documented risk assessment and shall comply with the requirements of this standard in effect at the time of modification. Operation and maintenance instructions and procedures shall be updated following modifications to a machine or IMS. Operation and maintenance personnel shall be trained on the modifications whenever modifications are made B11 LMSS™ Design, Construction, Reconstruction & Modification Pop Quiz DO NOT COPY – DO NOT SHARE Loss of power shall not result in a hazardous True situation due to the release of stored energy 1 The Emergency Stop must conform to B11.19 True and NFPA 79 2 Description of potentially hazardous situations and how to avoid them is a True 3 minimum requirement for documentation B11 LMSS™ What did you Learn? DO NOT COPY – DO NOT SHARE General Design Requirements Layout Electrical Modes of Operation Local Control Power sources Start and Reset Emergency Stop Fluids, Powered moving parts, Mounting Visual Awareness Ladders and Noise Documentation Rebuild and Modification B11 LMSS™ DO NOT COPY – DO NOT SHARE Layout, Installation, Testing and Start-up The requirements for the layout, installation, testing and start-up of the IMS and its associated equipment. B11 LMSS™ Layout DO NOT COPY – DO NOT SHARE Clause 7.2 Compatible with the expected operating and maintenance conditions Allow sufficient access to and egress from the IMS for operation, material handling and maintenance Clearance required between machine and associated equipment so that normal movement of personnel does not interfere with other assigned personnel Clearance between machines and associated equipment/building structures required to allow set-up, maintenance or repair tasks Sufficient space shall be provided to properly access machines for maintenance. B11 LMSS™ Installation DO NOT COPY – DO NOT SHARE Clause 7.3 Floor Loading Floor shall be capable of bearing static and dynamic loads from the machine and associated equipment Anchoring All machines within the IMS shall be anchored to prevent movement during operation Electrical Requirements NFPA 70 and NFPA 79 Hazardous Energy Control Means provided to disconnect and isolate all sources of hazardous energy dissipate stored energy allow for partial de-energization clearly identify span of control for hazardous energy-isolating devices Procedure, Training and Supervision Formal hazard energy control procedure implemented and enforced by authorized personnel Lighting Lighting required to allow personnel to perform tasks safety B11 LMSS™ Testing and Start-up DO NOT COPY – DO NOT SHARE Clause 7.4 Testing & Start-up Testing and Start-up procedure to be provided and used Only trained personnel to operate during start-up Other risk reduction measures required if engineering controls not in place If temporary processes / procedures / configurations are implemented, a separate risk assessment and interim risk reduction measures shall be applied B11 LMSS™ Layout, Installation, Testing and Start-up Pop Quiz DO NOT COPY – DO NOT SHARE The Layout must be compatible with the expected operating and maintenance True 1 conditions During installation a means to dissipate True stored energy is required 2 There is no requirement for a Testing and False Procedures based on Start-up procedure 3 Risk Assessment B11 LMSS™ What did you Learn? DO NOT COPY – DO NOT SHARE Layout, Installation, Testing and Start-up Layout Installation Testing and Start-up B11 LMSS™ DO NOT COPY – DO NOT SHARE Risk Reduction Measures When risks cannot be eliminated or reduced to an acceptable level by design and individuals are exposed to hazards associated with an industrial machine or other equipment within the IMS, risk reduction measures shall be provided in accordance with the relevant machine-specific “base” safety standard. B11 LMSS™ Learning Objectives DO NOT COPY – DO NOT SHARE Requirements Guards Engineering Control Devices Awareness Means Specific Hazards Safe Work Procedures Span of Control B11 LMSS™ Risk Reduction Measures DO NOT COPY – DO NOT SHARE Clause 8 Requirements prevent initiation of hazardous situations; cause hazardous situations within the hazard zone to achieve a safe condition; or prevent individuals from entering the hazard zone. Meet requirements of ANSI B11.19 Guards Engineering Control Devices Awareness Means Muting, Safety-Related Sensing Field Switching Safety-Related System Stop Safe work procedures B11 LMSS™ Risk Reduction Measures DO NOT COPY – DO NOT SHARE Clause 8 Perimeter Must be clearly marked Engineering controls required to prevent or detect individuals reaching into or entering Entry detection prevents initiation or stops the hazard before it can be reached Hazards between individual machines Guards required to prevent access to the hazard zone or Engineering controls required to detect individuals reaching into or entering hazard zone B11 LMSS™ Risk Reduction Measures DO NOT COPY – DO NOT SHARE Clause 8 In Production Mode IMS operation only possible when interlocked guards are closed or engineering control devices are active for the zone(s) Manual & Special Mode Alternate risk reduction measures required if an engineering control has been suspended During Process Observation If possible, perform observation from outside the safeguarded space If not possible, mode required that: uses alternative risk reduction measures; and provides access to a specific location B11 LMSS™ Risk Reduction Measures DO NOT COPY – DO NOT SHARE Clause 8 Power operated workholding hazard Engineering control(s) shall be provided Chip or coolant hazard Control using a shield Chip removal – shall not be handled by hand Slip hazard Gaging Procedures Shall not expose operator to hazards Workpiece loading device Shall be safeguarded if they expose individuals to hazards B11 LMSS™ Risk Reduction Measures – Span of Control DO NOT COPY – DO NOT SHARE Clause 8.8 The zones identify two spans of control for two individual Layout Analysis emergency stop (ES) pushbutton operators: Zone 1 Encompasses the Butt Saw and the Die Carrier specification of Limits Zone 2 Encompasses the Hydraulic Extrusion Press and Die Carrier The Die carrier responds to the e-stop of either machine task/hazard pairs as identified from a risk assessment task zone and/or control zone identification selecting risk reduction measures Safety Performance Level Meet or exceed the highest level for the risks identified within its span of control Identification Span of Control shall be clearly identifiable B11 LMSS™ Risk Reduction Measures – Span of Control DO NOT COPY – DO NOT SHARE Clause 8.8 B11 LMSS™ Risk Reduction Measures – Span of Control DO NOT COPY – DO NOT SHARE Clause 8.8 B11 LMSS™ Risk Reduction Measures – Span of Control DO NOT COPY – DO NOT SHARE Clause 8.8 PLr=c PLr=c PLr=b PLr=b PLr=d PLr=c PLr=d PLr=d PLr=d PLr=c Door 4 PLr=d Door Door Door 1 2 3 PLr=d PLr=d PLr=c PLr=d PLr=d PLr=c PLr=d PLr=d PLr=c B11 LMSS™ Risk Reduction Measures Pop Quiz DO NOT COPY – DO NOT SHARE Risk reduction measures shall prevent initiation True of hazardous situations 1 False Chips being formed should be removed by hand Consider a tool to 2 remove chips In the Span of Control, the safety performance level shall meet or exceed the highest level for True 3 the risks identified within its span of control B11 LMSS™ What did you Learn? DO NOT COPY – DO NOT SHARE Risk Reduction Requirements Perimeter and between machines Modes Guards and engineering controls Specific Hazards Span of Control B11 LMSS™ DO NOT COPY – DO NOT SHARE Set-up, Operation and Maintenance B11 LMSS™ Learning Objectives DO NOT COPY – DO NOT SHARE Machine set-up procedures Operation Maintenance Supervision Hazardous Energy Control Initiation of normal operation Safety Signs PPE B11 LMSS™ Set-up, Operation and Maintenance DO NOT COPY – DO NOT SHARE Clause 9 General Written procedures required for Control of hazardous energy Loading and unloading of materials Setup Operation Inspection and maintenance During set-up and maintenance hazardous situations shall be under local control Suppliers recommendations referenced when setting developing procedures User shall establish procedures for set-up, operation and maintenance B11 LMSS™ Machine Set-up Procedures DO NOT COPY – DO NOT SHARE Clause 9.2 Risk Reduction and awareness means In place and functioning during set-up; or Alternate risk reduction measures implemented Bypassing engineering controls requires alternate risk reduction measures Set-up personnel shall not remove risk reduction measures Unless authorized as established in the set-up procedure Before returning to normal operation Any engineering controls that were removed/bypassed/defeated shall be reestablished B11 LMSS™ Operation Procedures DO NOT COPY – DO NOT SHARE Clause 9.3 Operating procedures Shall be established, documented, and implemented so that safe operating practices are followed Risk reduction measures Administrative controls, or other risk reduction measures required where engineering control not practicable Initiation of normal production allowed when: Operating personnel properly trained on the use of the IMS Engineering controls or other risk reduction measures in place Individuals not exposed to hazards associated with the selected mode of control Proper safe work procedures are established, documented and followed B11 LMSS™ Maintenance Procedures DO NOT COPY – DO NOT SHARE Clause 9.4 Maintenance procedures Shall be established, documented and used Shall be available at all times to maintenance personnel Methods shall be established for component and part handling Shall include confirmation of safe operation of risk reduction measures after repair, replacement or adjustment Maintenance and production Maintenance and production operations shall not be performed concurrently within the same zone Risk reduction measures Shall only remove if authorized in the maintenance procedure Before return to operation All necessary repairs to be completed All risk reduction measures back in service and tested After modifications to machines Update maintenance procedures Verify maintenance personnel are trained on modifications B11 LMSS™ Maintenance Procedures DO NOT COPY – DO NOT SHARE Clause 9.4 Maintenance Inspections Inspection Program required to verify all components, auxiliary equipment and engineering controls are working properly Repair work identified during an inspection is required to performed Inspection testing and maintenance performed or supervised by a trained or experienced individual Inspections shall be documented B11 LMSS™ Supervision DO NOT COPY – DO NOT SHARE Clause 9.5 Supervision Designated supervisor required to verify: control limits access and prevents unauthorized modifications the operating and maintenance procedures are within the guidelines of the supplier's manual means to limit access, such as passwords, are used only by authorized personnel User required to ensure personnel are adequately trained to perform operational and supervisory tasks B11 LMSS™ Energy control & Initiation DO NOT COPY – DO NOT SHARE Clause 9.6, 9.7 Hazardous Energy Control User to establish a lockout / tagout procedure or apply alternative methods of hazardous energy control (LOTO or AMEC) LOTO procedure or AMEC application to consider unexpected machine motion or release of hazardous energy during entire lifecycle and from adjacent or interconnected machines/equipment Initiation of normal operation Initiation only allowed when operating personnel have been properly trained on the use of the machine; the associated risk reduction measures are in place and functioning; no persons are present within the hazard zone(s); proper safe working procedures are followed. B11 LMSS™ Safety signs & PPE DO NOT COPY – DO NOT SHARE Clause 9.8, 9.9 Safety Signs User verifies that signs and symbols are affixed, maintained and legible Warning and data labels required to be maintained and replaced as required Personal Protective Equipment Need based upon risk assessment and if required the user shall select appropriate PPE; train personnel in its proper use; enforce the use of the selected PPE. B11 LMSS™ Machine Set-up, Operation & Maintenance Pop Quiz DO NOT COPY – DO NOT SHARE Written procedures are not required False 1 for the control of hazardous energy Written procedures are required Safety signs need to be maintained True 2 Initiation of the IMS is allowed with False No one is allowed in the 3 personnel inside the hazard zone(s) hazard zone(s) B11 LMSS™ What did you Learn? DO NOT COPY – DO NOT SHARE Machine Set-up, Operation & Maintenance Procedures Supervision Hazardous Energy Control IMS Initiation Signs & PPE B11 LMSS™ DO NOT COPY – DO NOT SHARE Training All personnel shall be trained to perform the functions for which they are responsible B11 LMSS™ Learning Objectives DO NOT COPY – DO NOT SHARE Training Operator Maintenance Personnel Supervisor Retraining B11 LMSS™ Training DO NOT COPY – DO NOT SHARE Clause 10 Training required (as appropriate) to include: a) the functions and locations of manually operated controls; b)the proper use and operation of local controls; c) safe methods for installing, removing, and adjusting tooling; d)the location, span of control and method for testing all emergency stop devices; e) the location, span of control and method for installation, adjustment and testing of all engineering controls; f) the use of safety procedures (e.g., fire prevention equipment); g) procedures for maintaining a safe work area; h)procedures for inspecting and maintaining the IMS; i) location and function of all energy-isolating devices including passive isolation such as blocks; j) the proper method of operation for production set–up before the machine is placed into production; k) require that all operators demonstrate their knowledge of the proper operation of the machine. B11 LMSS™ Training DO NOT COPY – DO NOT SHARE Clause 10 Operator Include verification – through written testing, oral questioning, demonstration Maintenance Personnel Receive sufficient training to be aware of hazards that apply with routine and non-routine maintenance Supervisor Trained in safe working procedures for inspecting and maintaining the IMS Retraining Provided for the continued competence of personnel B11 LMSS™ What did you Learn? DO NOT COPY – DO NOT SHARE Training Requirements Operators Maintenance Personnel Supervisors Retraining B11 LMSS™ DO NOT COPY – DO NOT SHARE Decommissioning Process B11 LMSS™ Decommissioning Process - Responsibilities DO NOT COPY – DO NOT SHARE Clause 11 Supplier Transfer information to the user regarding the decommissioning process including disposal and recycling recommendations User Identify and mitigate sources of hazards associated with the decommissioning phase Conduct a risk assessment Conduct pre-task planning Modifier assist the user in identifying and mitigating sources of hazards associated with the decommissioning phase of the machine and IMS. be responsible for transferring information to the user relative to the decommissioning process regarding disposal and/or any recycling recommendations. B11 LMSS™ Decommissioning Process DO NOT COPY – DO NOT SHARE Clause 11 Decommissioning Task conforms to applicable local, state and federal regulations, or the authorities having jurisdiction; applicable portions of normative standards listed in B11.20 requirements or specifications from the supplier; Control of Hazardous Energy means to disconnect hazardous energy sources to be identified as part of the pre task plan method for implementation of risk reduction measures to control hazardous energy to be documented user to establish and follow procedure to limit the exposure to unexpected start-up procedures to include identification of hazardous energy sources – which may be supplied from adjacent machinery B11 LMSS™ Decommissioning Process DO NOT COPY – DO NOT SHARE Clause 11 Layout for decommissioning space includes staging areas; material handling equipment; employee walkways; other elements associated with the decommissioning of the machine. Transfer of information and risk For disposal, sale, transfer, recycling or trade, relevant information shall be disclosed to assist in the identification of potential harm or uncontrolled risk of injury. B11 LMSS™ Decommissioning Pop Quiz DO NOT COPY – DO NOT SHARE Appropriate training is required for the True proper use and operation of local controls 1 There is no need for the user to conduct a False risk assessment for the decommissioning A decommissioning risk 2 process assessment is required Layout for decommissioning space includes True employee walkways 3 B11 LMSS™ What did you Learn? DO NOT COPY – DO NOT SHARE Decommissioning Responsibilities The task Control of Hazardous energy Layout Transfer of information and risk B11 LMSS™ What did you Learn? DO NOT COPY – DO NOT SHARE B11.20 Introduction to B11.20 Responsibilities Design, Construction, Re-construction and Modification Layout, Installation, Testing and Start-up Risk Reduction Measures Set-up Operation & Maintenance Training Decommissioning B11 LMSS™ DO NOT COPY – DO NOT SHARE ANSI/R15.06-2012 for Industrial Robots and Robot Systems — Safety Requirements B11 LMSS™ Learning Objectives DO NOT COPY – DO NOT SHARE Introduction to R15.06 Hazard Identification/Risk Assessment Design & General Requirements Integration into IMS (Integrated Manufacturing Systems) Safeguarding Collaborative Robot Operation Verification and Validation B11 LMSS™ DO NOT COPY – DO NOT SHARE Setting The Scene B11 LMSS™ Learning Objectives DO NOT COPY – DO NOT SHARE Introduction to RIA R15.06 Robot Manufacturer Integrator & Installer Associated Technical Reports B11 LMSS™ R15.06 History DO NOT COPY – DO NOT SHARE American National Standard for Industrial Robots and 1st Edition Robot Systems – Safety requirements 1986 Introduced the term Control Reliable 2nd Edition 1992 Major reorganization of text, requirement to retrofit some existing installations with enabling devices and use of the 3rd Edition term space in place of envelope 1999 Risk Assessment becomes a requirement - not an option 4th Edition (Direct text adoption of ISO 10218) 2012 B11 LMSS™ ANSI R15.06 Part 1: [Industrial] Robots DO NOT COPY – DO NOT SHARE Scope Specifies requirements and guidelines for the inherent safe design, protective measures and information for use of industrial robots. Describes basic hazards associated with systems and provides requirements to eliminate, or adequately reduce, the risks associated with these hazards Does not address the robot as a complete machine and does not consider noise B11 LMSS™ ANSI R15.06 Part 2: [Industrial] Robot systems and Integration DO NOT COPY – DO NOT SHARE Specifies safety requirements for the integration of industrial robots and industrial robot systems as defined in [Part 1], and industrial robot cell(s) Integration includes a) the design, manufacturing, installation, operation, maintenance and decommissioning of the industrial robot system or cell; b) necessary information for the design, manufacturing, installation, operation, maintenance and decommissioning of the industrial robot system or cell; c) component devices of the industrial robot system or cell. Covers basic hazards and hazardous situations, providing requirements to eliminate or adequately reduce the risks Specifies requirements for the industrial robot system as part of an integrated manufacturing system Does not address noise, or deal with hazards associated with processes (e.g., laser radiation, ejected chips, welding smoke) Image courtesy of RM Group UK Ltd B11 LMSS™ RIA Standards and Technical Reports DO NOT COPY – DO NOT SHARE ANSI/RIA R15.08-1-2020 Industrial Mobile Robots – Safety Requirements - Part 1: Requirements for the Industrial Mobile Robot Provides safety requirements for the design and integration of industrial mobile robots (IMRs). RIA TR R15.306-2016 Task-based Risk Assessment Methodology Describes one method of risk assessment that complies with requirements of the 2012 R15.06 Standard RIA TR R15.406-2014: Safeguarding Explains how to design a system of safeguards to protect human workers in an industrial environment that also contains robot system(s). Supplements Standard ANSI/RIA R15.06-2012: Industrial Robot Safety RIA TR R15.506-2014: Applicability of ANSI/RIA R15.06-2012 for Existing Industrial Robot Applications Explains how to apply the ANSI/RIA R15.06-2012: Industrial Robot Safety Standard to existing robot systems RIA TR15.606-2016 Collaborative Robots Explains safety requirements specific to collaborative robots and robot systems and is supplemental to the guidance in ANSI/RIA R15.06. A U.S. National Adoption of ISO/TS 15066 RIA TR R15.706–2019: User Responsibilities Directed to the user, providing guidance and expanding on the responsibilities that are implied, but not stated specifically, in the R15.06-2012 Standard B11 LMSS™ What did you Learn? DO NOT COPY – DO NOT SHARE Setting the Scene How R15.06 is laid out Part 1 – Manufacturer Part 2 – Integrator and Installer Technical Reports supporting R15.06 B11 LMSS™ DO NOT COPY – DO NOT SHARE Part 2 Industrial Robot systems and integration B11 LMSS™ Learning Objectives DO NOT COPY – DO NOT SHARE Definitions Design Requirements and Protective Measures Verification and Validation Information for Use B11 LMSS™ ANSI R15.06 Part 2: [Industrial] Robot systems and Integration DO NOT COPY – DO NOT SHARE Scope Integration and documentation Basic hazards and hazardous situations and risk reduction requirements Requirements for industrial robot system as part of an integrated manufacturing system Does not address: noise hazards associated with processes (e.g., laser radiation, welding smoke) local, state or national OHS regulations Definition of Industrial Robot Automatically controlled, reprogrammable multipurpose manipulator, programmable in three or more axes, which can be either fixed in place or mobile for use in industrial automation applications. Includes the manipulator, controller, additional axes Image courtesy of Rees Machinery Group Ltd B11 LMSS™ Definitions DO NOT COPY – DO NOT SHARE Clause 3 Space…………. 3.13.1 operating space operational space portion of the restricted space (3.13.2) that is actually used while performing all motions commanded by the task program 3.13.2 restricted space portion of the maximum space restricted by limiting devices that establish limits which will not be exceeded NOTE – Adapted from ISO 8373:1994, definition 4.8.2. 3.13.3 safeguarded space space defined by the perimeter safeguarding 3.13.3 (Part One) maximum space space which can be swept by the moving parts of the robot as defined by the manufacturer plus the space which can be swept by the end-effector and the workpiece B11 LMSS™ Hazard Identification & Risk Assessment DO NOT COPY – DO NOT SHARE Part 1 Clause 4 Pay Particular Attention to: the intended operations at the robot, including teaching, maintenance, setting and cleaning; unexpected start-up; access by personnel from all directions; reasonably foreseeable misuse of the robot; the effect of failure in the control system; and where necessary, the hazards associated with the specific robot application. Annex A contains a list of hazards that can be present with robots B11 LMSS™ Hazard Identification & Risk Assessment DO NOT COPY – DO NOT SHARE Clause 4 Operational characteristics different to other machines Robots are capable of high energy movements through large spaces Initiation and path of movement difficult to predict Operating space of one robot may overlap that of another robot Operators may be required to work near a robot system with power to the actuators available B11 LMSS™ Hazard Identification & Risk Assessment DO NOT COPY – DO NOT SHARE Clause 4 Identify Hazards/Assess Risks Eliminate by design Prevent operators encountering hazards by bringing hazards to a safe state reduce risk during interventions (e.g., teach) Realization of this involves Design to have task outside of the safeguarded space Creation of safeguarded and restricted spaces Provision of other safeguards when interventions cannot be avoided B11 LMSS™ Hazard Identification & Risk Assessment DO NOT COPY – DO NOT SHARE Clause 4 Layout Design Establish the physical (3D) limits of the cell/system Workspaces, access and clearance Manual Intervention – ideally from outside the safeguarded space but where not practicable enabling devices required Ergonomics and Human Interface Environmental Conditions Loading and unloading Perimeter safeguarding Location of emergency stop devices - including zoning of the cell Location of enabling devices Attention to the intended use of all components B11 LMSS™ Hazard Identification & Risk Assessment DO NOT COPY – DO NOT SHARE Clause 4 Set the Limits of the system Use Limits Space Limits Time Limits Other Limits B11 LMSS™ Hazard Identification & Risk Assessment DO NOT COPY – DO NOT SHARE Clause 4 Task Identification Process control and monitoring Workpiece loading programming and verification; brief operator intervention not requiring disassembly; set-up (e.g., fixture changes, tool change); troubleshooting; correction of malfunction(s) (e.g., equipment jams, dropped parts, event recovery and abnormal conditions); control of hazardous energy (including fixtures, clamps, turntables, and other equipment); maintenance and repair; equipment cleaning. B11 LMSS™ Hazard Identification & Risk Assessment DO NOT COPY – DO NOT SHARE Clause 4 Hazard elimination & risk reduction Eliminate hazards by design or the reduction of risk by substitution Safeguard to prevent operators encountering hazards or by ensuring hazards are brought to a safe state Provide supplementary protective measures such as PPE/Signs, etc. B11 LMSS™ Design Requirements & Protective Measures DO NOT COPY – DO NOT SHARE Clause 5 Safety–related control system performance (hardware/software) Clearly stated in the information for use In R15.06 SRP/CS performance is stated as: Performance levels and categories as per ISO 13849(2006) 4.5.1 Safety Integrity Levels (SIL) as per IEC 62061 (2005) 5.2.4 Control Reliability or other requirements can be used B11 LMSS™ Design Requirements & Protective Measures DO NOT COPY – DO NOT SHARE Clause 5 Safety-related control system performance (hardware/software) 5.4 SRP/CS Performance Requirement PL=d/structure category 3 (ISO 13849-1:2006) or SIL2 (hardware fault tolerance of 1 with a proof test interval of not less than 20 years) (IEC 62061:2005) This means: a single fault in any of these parts does not lead to the loss of the safety function; whenever reasonably practicable, the single fault shall be detected at or before the next demand upon the safety function; when the single fault occurs, the safety function is always performed, and a safe state shall be maintained until the detected fault is corrected; and all reasonably foreseeable faults shall be detected A comprehensive risk assessment may determine a different performance or safety integrity level B11 LMSS™ Safety Requirements & Protective Measures DO NOT COPY – DO NOT SHARE Clause 5 Environmental Conditions Temperature, humidity, electro-magnetic disturbances, lighting, etc. Location of Controls Operational controls requiring access during automatic operation to be located outside of the safeguarded space and placed to provide a clear view of the robot restricted space Actuating Controls Designed to meet IEC 60204-1 and consistent with part one. Power Requirements Electrical - IEC 60204-1, Hydraulic - ISO 4413, Pneumatic - ISO 4414 Isolating Sources of energy Single supply disconnecting device for each type of energy source Control of Stored Energy Provide means for the control of and/or controlled release of stored hazardous energy B11 LMSS™ Design Requirements & Protective Measures DO NOT COPY – DO NOT SHARE Part 1, Clause 5.3 Actuating Controls Constructed/Located to prevent unintended operation Clear indication of the status of actuating controls required Clear labelling to indicate function Under local pendant control the initiation of robot motion or change of local control selection from any other source is prevented B11 LMSS™ Design Requirements & Protective Measures DO NOT COPY – DO NOT SHARE Part 1 For the Robot Manufacturer Clause 5 Parameter Emergency Stop Protective Stop Location of initiation Operator has quick, unobstructed access For protective devices, the location is means determined by the minimum (safe) distance formulas described in ISO 13855 Initiation Manual Manual, automatic or may be automatically initiated by a safety-related function SRP/CS Performance Shall meet the required performance Shall meet the required performance level level Reset Manual Only Manual or automatic Use Frequency Infrequent Variable; from every operation to infrequent Purpose Emergency Safeguarding or risk reduction Effect Remove energy sources to all hazards Safely control the safeguarded hazard(s) B11 LMSS™ Safety Requirements & Protective Measures DO NOT COPY – DO NOT SHARE Clause 5 Robot system stopping functions Emergency Stop At every control station Actuation stops all robot motion and hazardous functions Robot systems required to have a single emergency stop function Where 2 or more robots overlap in the same restricted space it is the same workspace Required to remain functional even if the control station is not B11 LMSS™ Design Requirements & Protective Measures DO NOT COPY – DO NOT SHARE Part1, Robot system stopping functions Clause 5.5 Protective Stop One or more protective stop functions designed for the connection of external devices Compliant with safety performance requirements Required to stop all robot motion, remove or control power to the robot drive actuators (may be manual or Automatic) One or more stop functions with stop category 0 or 1 required Additional stop category 2 functions require monitoring of the standstill condition Manufacturer required to include the stop category of every protective stop circuit in the information for uses B11 LMSS™ Safety Requirements & Protective Measures DO NOT COPY – DO NOT SHARE Clause 5 End-effector Requirements Loss of energy supply does not cause release of load Static and dynamic forces created by load and end-effector within load capacity Flange plates and accessories align correctly Detachable tools held securely whilst in use End effector withstands expected forces for its lifetime B11 LMSS™ Safety Requirements & Protective Measures DO NOT COPY – DO NOT SHARE Clause 5 Enabling Devices Comply with part one of RIA R15.06 Provided to each person entering the safeguarded space Control ALL hazards that personnel could be exposed to while performing a task inside the safeguarded space Interlocked hazardous machine functions require a separate act to restart after being stopped by the enabling device B11 LMSS™ Safety Requirements & Protective Measures DO NOT COPY – DO NOT SHARE Clause 5 Limiting Robot Motion Limiting motion establishes a restricted space and reduces the safeguarded space The safeguarded space established by perimeter guarding Restricted space established by means to limit robot, end-effector, fixture and workpiece motion Perimeter safeguards not to be installed closer to the hazard than the restricted space Additional safeguarding may be required for operator workstations B11 LMSS™ Safety Requirements & Protective Measures DO NOT COPY – DO NOT SHARE Clause 5 Mechanical Limiting Devices Primary axis needs mechanical stops (Part 1) Physically restrain motion Meet Part 1 requirements for limiting devices Non-Mechanical Limiting Devices Initiate a stop through the control system Must meet SRP/CS performance requirements Stopping distance needs to be considered Restricted space determined based on the robot with actual load Dynamic Limiting Automatic controlled change of the robot's restricted space – occurring during a portion of the robot system’s cycle Using light curtains, cam operated switches or control activated hard stops B11 LMSS™ Safety Requirements & Protective Measures DO NOT COPY – DO NOT SHARE Clause 5 Layout 5.5 Perimeter Safeguarding Guards, or sensitive Access for Interventions protective equipment Consider trapping and pinch points within the restricted space Material Handling Process Observation Prevent operators entering the Should be performed from outside of safeguarding space undetected with the safeguarded space materials B11 LMSS™ Safety Requirements Pop Quiz DO NOT COPY – DO NOT SHARE The Maximum space is the space defined False by the perimeter safeguarding 1 Safeguarded Space Emergency Stops are required at every True control station 2 PLd is the only permissible performance False level for the SRP/CS in a robot application 3 B11 LMSS™ Design Requirements & Protective Measures DO NOT COPY – DO NOT SHARE Part 1, Operational Modes Clause 5.7 Selection Mode selector lockable in each position Each position clearly identified and provide exclusive control Selector can be other means that restricts the use of certain robot functions – these means shall Indicate the selected operating mode and Not initiate robot motion or other hazards by themselves Automatic Robot executes the task function and safeguarding measures are functioning If any stop detected automatic operation prevented Switching from automatic results in a stop B11 LMSS™ Safety Requirements & Protective Measures 5 DO NOT COPY – DO NOT SHARE Clause 5.6.3 Automatic Mode Selection and Initiation Protective stop occurs if an operator enters the safeguarded space Selection done outside of the safeguarded space Switching from automatic mode creates a protective stop Initiation of automatic operation only possible with safeguards active Manual Reset, Start/Restart Start and Restart – simple and obvious Relevant safety functions have to be active to start/restart Start Interlock required to prevent auto start after either actuation of a safeguard a change in operating mode of the cell Protect operators inside the safeguarded space from start/restart Start/restart function located outside of the safeguarded space B11 LMSS™ Safety Requirements & Protective Measures DO NOT COPY – DO NOT SHARE Clause 5.6.3 Automatic Mode Unexpected start-up From each control position the operator shall be able to ensure there is nobody in the safeguarded space If this is not possible presence sensing required If presence sensing not practicable: Multiple means for isolation and lockout provided A means to lock the guard open Time limited reset devices inside the safeguarded space Failing this Audio/visual warning Pre-start delay B11 LMSS™ Safety Requirements & Protective Measures DO NOT COPY – DO NOT SHARE Clause 5.6.4 Manual Mode Reduced Speed Used for jogging/teaching/programming/program verification/maintenance Maximum speed of Tool Center Point (TCP) 250mm/s (10in/s) Risk assessment dictates whether lower speeds required Manual control from within the safeguarded space only permitted with an enabling device High-speed Restricted to program verification in exceptional circumstances All manual jogging at reduced speed Mode and pendant conforms to Part 1 Initial speed limit of 250mm/s Provide, on the pendant, a means to incrementally adjust the speed from the initial value to the full programmed speed B11 LMSS™ Safety Requirements & Protective Measures DO NOT COPY – DO NOT SHARE Clause 5.6.4 Manual Mode Remote Access for Manual Intervention a) Manual remote control only possible with the robot system in manual mode b) Only one source of control to be active c) Control, as per b) can’t override local selection d) Manual control only to be operated from the local control e)