B11 LMSS Module 5 Rev 03 PDF
Document Details
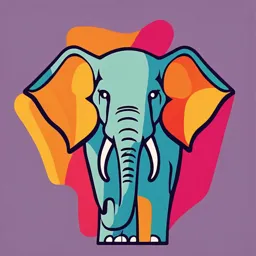
Uploaded by BravePoisson
Tags
Summary
This document is a presentation about B11 LMSS Module 5, covering topics such as NFPA 79 Electrical Safety of Machinery, intro to OSHA Regulations & Standards, and ANSI ASSP Z244.1.
Full Transcript
DO NOT COPY – DO NOT SHARE We’ll be with you shortly B11 LMSS™ Welcome to B11 LMSS Module 5 DO NOT COPY – DO NOT SHARE Safety Services UK and EU Lead– Matt...
DO NOT COPY – DO NOT SHARE We’ll be with you shortly B11 LMSS™ Welcome to B11 LMSS Module 5 DO NOT COPY – DO NOT SHARE Safety Services UK and EU Lead– Matt Chandy 3 years experience supporting Safety Interlocks Customer Application Support Manager VP Technical Safety – Jenny Tuertscher Expert member of ISO TC199 WG3, WG5, WG6, WG7, WG8 & ISO TC313 WG1 Member of ANSI B11 committees FS Engineer (TÜV Rheinland) #14247 / 17 – Machinery B11 LMSSTM Certification #AA311265118 B11 LMSS™ Welcome to B11 LMSS Module 5 DO NOT COPY – DO NOT SHARE Join in! Ask questions at any time Time Session Breaks 90 Mins NFPA 79 Electrical Safety of We will aim for a break every hour or Machinery so with one longer break in the middle 30 Mins Intro to OSHA Regulations & Standards Mute 180 Mins ANSI ASSP Z244.1 When you’re not talking please use the mute button Reactions Please make use of the “reaction” buttons Lower your hand by pressing it again B11 LMSS™ Overview B11 LMSS DO NOT COPY – DO NOT SHARE Module 1 Module 2 Module 3 Module 4 Module 5 Examination Introduction to B11.19 Risk B11.26 Integrating LOTO and 50 Multiple Standards and Reduction Functional Machines and electrical safety choice questions Regulations Measures Safety Robotics ANSI Z244.1 and 90 Mins B11.0 Safety of Inherently Safe Performance B11.20 and NFPA 79 Machinery By Design Levels RIA15.06 Risk Engineering Categories Assessment Controls Control General Administrative Reliability Requirements Controls Fault considerations B11 LMSS™ B11 LMSS Scope DO NOT COPY – DO NOT SHARE This course will instruct you on: Standards and Regulations What are machinery safety standards Why are they useful How do you use them Overview of the key standards This course does not: Cover specific machinery/industry details Cover every single requirement laid out in the standards and regulations (But it will show you how to find them!) B11 LMSS™ DO NOT COPY – DO NOT SHARE NFPA 79 (2021) Electrical Standard for Industrial Machinery B11 LMSS™ Learning Objectives DO NOT COPY – DO NOT SHARE NFPA 79 Scope, Purpose & Application Definitions General Requirements & Operating Conditions Disconnecting Means B11 LMSS™ NFPA 79 Scope, Purpose & Application DO NOT COPY – DO NOT SHARE Scope Applies to the electrical/electronic equipment, apparatus, or systems of industrial machines supplied from a nominal voltage of 1000 volts or less, and commencing at the point of connection of the supply circuit conductors to the electrical equipment of the machine Does not include the additional requirements for machines intended for use in hazardous (classified) locations Purpose Provides detailed information for the application of electrical/electronic equipment, apparatus, or systems supplied as part of industrial machines that will promote safety to life and property. Applications Not applied retroactively Changes to existing machinery must comply B11 LMSS™ NFPA 79 Key Definitions DO NOT COPY – DO NOT SHARE Clause 3 Shall Indicates mandatory requirements Should Indicates a recommendation or that which is advised but not required Equipment, materials, or services included in a list published by an organization that is acceptable to the authority having Listed jurisdiction and concerned with evaluation of products or services, that maintains periodic inspection of production of listed equipment or materials or periodic evaluation of services, and whose listing states that either the equipment, material, or service meets appropriate designated standards or has been tested and found suitable for a specified purpose. Direct Opening Operation Achievement of contact separation as the direct result of a specified movement of the switch actuator through nonresilient members (e.g., not dependent upon springs) Hazardous Condition A circumstance in which a person is exposed to a hazard(s) that has the potential to result in harm immediately or over a long period of time Safety Circuit The part of a control system containing one or more devices that perform a safety-related function. Safety-Related Function A function which is intended to maintain the safe condition of the machine, or prevent or reduce hazardous situations Controlled Stop The stopping of machine motion, while retaining power to the machine actuators during the stopping process Uncontrolled Stop The stopping of machine motion by removing power to the machine actuators, all brakes and/or other mechanical stopping devices being activated. B11 LMSS™ NFPA 79 General Requirements DO NOT COPY – DO NOT SHARE Electrical Components and Devices Installed and used in accordance with the ambient Clause 4 temperature, altitude, humidity and supply requirements below Physical Environment/Operating Conditions Electromagnetic interference must be suppressed/isolated to ensure the safety-related control functions are not lost Ambient operating air temperatures 5◦C & 40◦C (41◦F & 104◦F) Correct operation up to 1000m (3300ft) above mean sea level Protected against ingress of solid bodies and liquids and suitable for the environment where contaminants are present Avoid the effects of vibration/shock/bump by using anti vibration mountings or mount equipment away from the machine B11 LMSS™ NFPA 79 General Requirements DO NOT COPY – DO NOT SHARE Clause 4 Electrical Supply Alternating Current Supplies Electrical equipment designed to operate correctly: At 90-110% of the nominal voltage At 99-101% percent of the nominal frequency Where harmonic distortion does not exceed 10% of total voltage Where voltage of negative/zero sequence component in 3 phase supplies exceeds 2% of the positive sequence component Where supply voltage impulses do not exceed 1.5 ms Where supply voltage is interrupted at zero voltage for not more than 3 ms Where supply voltage dips do not exceed 20% B11 LMSS™ NFPA 79 General Requirements DO NOT COPY – DO NOT SHARE Clause 4 Electrical Supply Direct Current Supplies - Battery Electrical equipment designed to operate correctly: At 85-115% of the nominal voltage Where supply voltage is interrupted for not more than 5 ms Direct Current Supplies – Converting Equipment Electrical equipment designed to operate correctly: At 90-110% of the nominal voltage Where supply voltage is interrupted for not more than 20 ms Where the dc supply voltage ripple of converting equipment does not exceed 0.05 of the nominal voltage B11 LMSS™ NFPA 79 Disconnecting Means DO NOT COPY – DO NOT SHARE Clause 5 Machine Supply Circuit Disconnecting must be provided for the following: Each machine supply circuit Each machine supply circuit to a machine or a number of machines connecting to a feeder system using collector wires, collector bars, slip-ring assemblies, or flexible cable systems Each on-board power source (generators, etc.) Machine Supply Circuit Disconnecting means must disconnect the electrical equipment of the machine from the machine supply circuit B11 LMSS™ NFPA 79 Disconnecting Means DO NOT COPY – DO NOT SHARE Clause 5 Types of Machine Supply Circuit Disconnecting Means A Listed motor circuit switch rated in horsepower A listed molded case circuit breaker A listed molded case switch An instantaneous trip circuit breaker that is part of a listed combination motor controller limited to single motor applications A listed self-protected combination controller limited to single motor applications An attachment plug and receptacle for cord connection B11 LMSS™ NFPA 79 Disconnecting Means DO NOT COPY – DO NOT SHARE Clause 5 Excepted Circuits The following circuits are not required to be disconnected by the machine circuit disconnecting means: Lighting circuits for lighting required for maintenance or repair Attachment plugs and receptacles for the exclusive connection of repair or maintenance tools and equipment Undervoltage protection circuits that are only used for automatic tripping in the event of supply circuit failure Circuits supplying equipment that need to remain energized for satisfactory operation B11 LMSS™ NFPA 79 Disconnecting Means DO NOT COPY – DO NOT SHARE Clause 5 Means for Removal of Power for Prevention of Unexpected Start-Up Must be provided and must be as follows Appropriate for the intended use Conveniently located Readily identifiable as to function and purpose Provided with permanent means for locking in the off position only Removal of Power achieved by one of: Machine supply circuit disconnecting means Additional devices confirming to the types recognized in NFPA 79 Other means (e.g., contactor switched off by a control circuit) Where other means of removal of power are used, a single failure of any of its components shall not result in an inadvertent or unexpected start-up. B11 LMSS™ NFPA 79 Pop Quiz DO NOT COPY – DO NOT SHARE The stopping of machine motion, while retaining False power to the machine actuators during the stopping Controlled Stop retains 1 process is an uncontrolled stop power on actuators Machine Supply Circuit Disconnecting must be provided for each machine supply circuit True 2 Where other means of removal of power are used, a single failure of any of its components shall not True 3 result in an inadvertent or unexpected start-up. B11 LMSS™ What did you Learn DO NOT COPY – DO NOT SHARE NFPA 79 Scope, Purpose & Application Definitions General Requirements & Operating Conditions Disconnecting Means B11 LMSS™ Learning Objectives DO NOT COPY – DO NOT SHARE NFPA 79 Protection from Electrical Hazards Protection of Equipment Grounding & Bonding B11 LMSS™ NFPA 79 Protection from Electrical Hazards DO NOT COPY – DO NOT SHARE Clause 6 Live parts operating at or above 50 volts rms ac or 60 volts dc must be guarded against contact Insulation Only removable by destruction Capable of withstanding mechanical, chemical, thermal and electrical stresses it is subjected to under normal operation Enclosures Enclosure openings, and observation windows shall meet the requirements of UL 508, UL 508A, UL 50, or NEMA 250 B11 LMSS™ NFPA 79 Protection from Electrical Hazards DO NOT COPY – DO NOT SHARE Clause 6 Enclosures Access Opening an enclosure containing parts operating at or above 50 volts rms ac or 60 volts dc allowed under one or more of the following Use of a key or tool - all parts on the inside of the door protected from unintentional direct contact Disconnecting means interlocked with the enclosure door(s) Opening without a key or tool permitted only when all live parts inside are separately enclosed or guarded Interlocking Used to ensure the power is disconnected when the door(s) is opened. Access permitted without removing power only when: At all times it is possible to lock the disconnecting means off Closing the disconnecting means prevented while the door is open Live parts protected from unintentional direct contact by inherent design of components or the application of barriers Relevant information for defeating the interlock is provided B11 LMSS™ NFPA 79 Protection from Electrical Hazards DO NOT COPY – DO NOT SHARE Clause 6 Fault Protection Double Insulation Equipment to be distinctively marked and be listed to be protected by a system of double insulation Automatic Supply Disconnection Protective bonding of exposed conductive parts Overcurrent protection devices for automatic disconnection B11 LMSS™ NFPA 79 Protection from Electrical Hazards DO NOT COPY – DO NOT SHARE Clause 6 Fault Protection Protective Extra Low Voltage (PELV) Nominal voltage not greater than 30V AC or 60V DC when equipment used in normally dry locations or when large area contact of live parts with the human body is not expected 6V AC or 15V DC in all other cases One side of the circuit or point of the supply source must be grounded Live parts of the PELV to be electrically separated from other live circuits Conductors of each PELV circuit to be physically separated from those of other circuits Attachment plugs/receptacles for a PELV circuit must conform as follows: Plugs must not be able to fit receptacles in other voltage systems Receptacles must not accept plugs from other voltage systems B11 LMSS™ NFPA 79 Protection from Electrical Hazards DO NOT COPY – DO NOT SHARE Clause 6 Protection against residual voltages Live parts with a residual voltage greater than 60 volts after the supply has been disconnected to be reduced to 60 volts or less with 5 seconds of disconnection Withdrawal of plugs (and similar) resulting in the exposure of conductors to have a 1 second discharge time Capacitors to be provided with a means of discharging stored energy and the residual voltage to be reduced to 50 volts or less within a minute of capacitor disconnection Discharge circuit permanently connected to the capacitor or capacitor bank terminals or automatic means of connecting it to the capacitor bank when voltage is removed. (Manual means must not be used) A Safety Sign must be provided for Arc Flash Hazard Warning B11 LMSS™ NFPA 79 Protection of Equipment DO NOT COPY – DO NOT SHARE Clause 7 Protect equipment against the effects of the following: 1 Overcurrent from a short circuit 2 Overload or loss of cooling motors 3 Ground faults 4 Overvoltages due to lightning and switching surges 5 Abnormal temperatures 6 Loss of or reduction in the supply voltage 7 Overspeed of machines/machine elements 8 Incorrect phase sequence B11 LMSS™ NFPA 79 Grounding & Bonding DO NOT COPY – DO NOT SHARE Clause 8 The equipment frame and conductive non-current carrying parts/material must be bonded together and connected to a grounding conductor or bonding jumper Effective Ground-Fault Current Path Must be capable of safely carrying the maximum ground-fault current Equipment Grounding and Bonding Machine and all exposed non-current carrying conductive parts shall be connected to provide effective grounding Metal mounting panels with electrical devices, within non metallic enclosures, must be connected to a grounding conductor or bonding jumper Equipment Grounding Conductor Terminal Each machine supply circuit requires an equipment grounding conductor terminal in the vicinity of the phase conductor terminals Equipment grounding conductor terminal identified with the word “GROUND”, or “GND”, “GRD”, “G”, the color GREEN and the ground symbol. (PE can also be used) B11 LMSS™ NFPA 79 Grounding & Bonding DO NOT COPY – DO NOT SHARE Clause 8 Equipment Grounding Conductors and Bonding Jumpers Green, with or without a yellow stripe Copper Insulated, covered or bare and protected against damage As per table 8.2.2.4 Continuity ensured by effective connections Bolts acceptable for bonding if clean of paint, etc. Bonding jumpers to connect to a conductive door Portable, pendant and resilient-mounted equipment bonded by separate conductors B11 LMSS™ NFPA 79 Grounding & Bonding DO NOT COPY – DO NOT SHARE Clause 8 Control Circuits Control Circuits are permitted to be grounded or ungrounded When grounded the output must be grounded near the control power source Switching devices not permitted in a grounded conductor – unless the conductor(s) opened simultaneously Ungrounded control circuits to be provided with an insulation-monitoring device that indicates a ground fault or automatically interrupts the circuit B11 LMSS™ NFPA 79 Pop Quiz DO NOT COPY – DO NOT SHARE Plugs in a PELV circuit must not be able to True fit receptacles in other voltage systems 1 Insulation can be removed by applying False gentle heat and gently sliding it off Destruction required to 2 remove insulation Control Circuits are permitted to be True grounded or ungrounded 3 B11 LMSS™ What did you Learn DO NOT COPY – DO NOT SHARE NFPA 79 Protection from Electrical Hazards Protection of Equipment Grounding & Bonding B11 LMSS™ Learning Objectives DO NOT COPY – DO NOT SHARE NFPA 79 Control Circuits and Control Functions Operator Interface & Control Devices Control Equipment: Location, Mounting & Enclosures B11 LMSS™ NFPA 79 Control Circuits & Control Functions DO NOT COPY – DO NOT SHARE Clause 9 Not greater than 120V AC, single phase or 250V DC - Fault current less than 1000 amperes ms Source supply taken from load side of supply disconnecting means Provided with overcurrent protection All operating coils of electromechanical magnetic devices and indicator lamps shall be directly connected to the same side of the control circuit All contacts to be connected between the coil and the other side of the control circuit B11 LMSS™ NFPA 79 Control Circuits & Control Functions DO NOT COPY – DO NOT SHARE Clause 9 0 Uncontrolled stop by immediately removing power to machine actuators 1 Controlled stop with power to machine actuators available then power removed when stop is achieved 2 Controlled stop with power left available to the machine actuators B11 LMSS™ NFPA 79 Control Circuits & Control Functions DO NOT COPY – DO NOT SHARE Clause 9 Operating Modes One of more operating modes – e.g., automatic, manual, bypass and normal Where a hazardous condition results from mode selection, inadvertent selection must be prevented – e.g., key operated switch, access codes Mode selection alone must not initiate machine operation Safeguarding measures remain effective in all modes Selected operating mode to be indicated B11 LMSS™ NFPA 79 Control Circuits & Control Functions DO NOT COPY – DO NOT SHARE Clause 9 Start Only possible when all safeguards are in place and functioning On those machines where safeguards cannot be applied for certain operations, manual control of such operations shall be by hold-to-run controls together with enabling control, where appropriate On machines requiring the use of more than one control station to initiate a start, the following criteria shall be met Each control station to have a manually activated start All required conditions for machine operation shall be met All start devices must be in the off position before start is permitted All start devices to be actuated concurrently B11 LMSS™ NFPA 79 Control Circuits & Control Functions DO NOT COPY – DO NOT SHARE Clause 9 Stop Category 0, 1, and/or 2 stops to be provided with the minimum of at least one stop Category 0 and 1 stops to be operational at all times and category 0 to take priority Emergency Stop Shall override all other functions and operations in all modes Power to machine actuators removed as soon as possible without creating hazards Category 0 or 1 (determined by the risk assessment) Reset command must not restart machinery but may only permit restart Emergency Switching Off Where protection against direct contact is achieved only by placing out of reach or by obstacles Where other hazards or damage caused by electricity are possible Accomplished by disconnecting the machine supply circuit, effecting a Category 0 stop B11 LMSS™ NFPA 79 Control Circuits & Control Functions DO NOT COPY – DO NOT SHARE Clause 9 Hold-to-Run Controls Require the continuous actuation of the control device(s) to achieve operation Jog or inch in manual mode only Prevention of run/automatic during inch mode to be achieved by an operator interface and separate jog/inch selection method Two-Hand Controls Two control devices requiring concurrent actuation using both hands Control devices actuated within 500ms or each other If 500ms is exceeded both control devices to be released before operation is initiated Control devices require continuous actuation during the hazardous conditions Machine operation ceases upon release of either control device when hazardous conditions still present The release of both control devices is required before Machine operation is re- initiated B11 LMSS™ NFPA 79 Control Circuits & Control Functions DO NOT COPY – DO NOT SHARE Clause 9 Enabling Control Allow machine operation to be initiated by a separate start control Connect to a Category 0 or 1 stop Follow ergonomic principles For two position:- Position 1 is the off function (actuator not operated) Position 2 is the enabling function (actuator operated) For three-position:- Position 1 is the off function (actuator not operated) Stop Enable command Position 2 is the enabling function (actuator operated and in the mid position) Released Position 3 is the off function (actuator operated and past Pic/diagram its mid position) showing 3 Central Three position switch requires manual operation to positions reach position 3. Returning from 3 to 2 must not enable Compressed the function B11 LMSS™ NFPA 79 Control Circuits & Control Functions DO NOT COPY – DO NOT SHARE Clause 9 Control Functions in the Event of Failure – Risk Reduction Measures Protective devices on the machine (e.g., interlocks 1 guards, trip devices) Protective interlocking of the electrical circuit 2 Use of proven circuit techniques and components 3 Provisions of partial or complete redundancy or diversity 4 Provision for functional tests 5 B11 LMSS™ NFPA 79 Operator Interface & Control Devices DO NOT COPY – DO NOT SHARE Clause 10 Location & Mounting Mounted rigidly in reasonably dry and clean location Mounted to minimize damage Hand control not less than 0.6m (2ft) above the servicing level Operator not to be placed in a hazardous situation Inadvertent operation minimized Accidental machine overtravel will not damage limit switches or sensors Suitable for the environment Start pushbuttons mounted above or to the left of their associated stop pushbuttons Stop or emergency stop buttons at each control station and continuously operable B11 LMSS™ NFPA 79 Operator Interface & Control Devices DO NOT COPY – DO NOT SHARE Clause 10 B11 LMSS™ NFPA 79 Operator Interface & Control Devices DO NOT COPY – DO NOT SHARE Clause 10 B11 LMSS™ NFPA 79 Control Equipment: Location, Mounting & Enclosures DO NOT COPY – DO NOT SHARE Clause 11 Location & Mounting To facilitate Accessibility & Maintenance Protection against external influences/conditions Operation and maintenance of the machine Enclosure construction and door fasteners to comply with UL 508, UL 508A, UL 50, or NEMA 250 Minimum enclosure protection – Type 1 Width of working space in front of control cabinets shall be the width of the opening or 762mm (30 in) whichever greater B11 LMSS™ NFPA 79 Pop Quiz DO NOT COPY – DO NOT SHARE The enabling control connects to a True 1 Category 0 or 1 stop Source supply is taken from load True 2 side of supply disconnecting means An emergency stop actuator can be False red or black E-stop must be red on a 3 yellow background B11 LMSS™ What did you Learn DO NOT COPY – DO NOT SHARE NFPA 79 Control Circuits and Control Functions Operator Interface & Control Devices Control Equipment: Location, Mounting & Enclosures B11 LMSS™ Learning Objectives DO NOT COPY – DO NOT SHARE NFPA 79 Conductors, Cables & Flexible Cords Wiring Practices Electric Motors & Associated Equipment Accessories & Lighting Marking & Safety Signs Technical documentation Testing & Verification Servo Drives & Motors B11 LMSS™ NFPA 79 Conductors, Cables and Flexible Cords DO NOT COPY – DO NOT SHARE Clause 12 Conductors required to be insulated 1 Conductors must be copper 2 Stranded conductors in accordance with Table 12.2.2 3 Insulation – flame retardant 4 Conductors labelled accordingly 5 B11 LMSS™ NFPA 79 Wiring Practices DO NOT COPY – DO NOT SHARE Clause 13 All connections secured against accidental loosening 1 Connection means identified for the cross-sectional areas and the type of 2 conductors being terminated Terminals for more than one conductor to be identified 3 Soldered connections permitted only where terminals are identified for soldering 3 Shielded conductors terminated to prevent fraying of strands and to allow easy 4 disconnection Identification tags to be readable, permanent, and identified for use in the 5 physical environment Terminal blocks to be mounted and wired so that internal and external wiring 6 does not cross over the terminals B11 LMSS™ NFPA 79 Wiring Practices DO NOT COPY – DO NOT SHARE Clause 13 Identification of the Conductors GREEN with or without one or more YELLOW stripe to identify the equipment grounding conductor Where an AC circuit includes a grounded conductor, this conductor shall be WHITE, GRAY, or three continuous WHITE stripes on other than GREEN, BLUE, or ORANGE insulation along its entire length BLACK for ungrounded AC and DC power conductors WHITE with BLUE stripe for grounded (current- carrying) DC circuit conductor RED for ungrounded AC WHITE with ORANGE stripe for grounded (current- control conductors carrying) conductor, remains energized when the main supply circuit disconnecting means is in the off position BLUE for ungrounded DC control conductors ORANGE shall be used to identify ungrounded conductors that remain energized when the main supply circuit disconnecting means is in the off position. This color identification shall be strictly reserved for this application only B11 LMSS™ NFPA 79 Wiring Practices DO NOT COPY – DO NOT SHARE Clause 13 Attachment Plug & Receptacle Combinations No shock or hazard present on the exposed metal pins Locking type where rated to greater than 20 Amps On circuits of 300V to ground or 300V phase to phase must be skirted and contain any arc generated Equipment grounding circuit connection made before current carrying connections made Equipment grounding circuit connection is not disconnected until current carrying connections in the plug are disconnected Where more than one plug and receptacle in use in close proximity coding must be used B11 LMSS™ NFPA 79 Electric Motors & Associated Equipment DO NOT COPY – DO NOT SHARE Criteria for Selection Clause 14 Type of motor 1 Type of duty cycle 2 Fixed speed or variable speed operation 3 Mechanical vibration 4 Type of converter for motor speed control 5 Influence of the harmonic spectrum of the voltage/current feeding the motor on the temperature rise 6 Method of starting and possible influence of the inrush current on the operation of other users 7 Variation of counter torque load with time and speed 8 Influence of loads with large inertia 9 Influence of constant torque or constant power operations 10 11 Possible need of inductive reactors between motor and converter B11 LMSS™ NFPA 79 Accessories & Lighting DO NOT COPY – DO NOT SHARE Clause 15 Receptacles for Accessory Equipment Receptacles mounted externally or internally to the enclosure to be ground-fault circuit-interrupter (GFCI)-protected Receptacles to be supplied from a grounded 120-volt AC source Receptacles shall be of the parallel blade grounding type, 125-volt, single-phase, 15- or 20-ampere configuration and listed for the applied voltage All ungrounded conductors connected to the receptacle outlet to be protected against overcurrent Equipment grounding circuit connection is not disconnected until current carrying connections in the plug are disconnected Receptacles shall be suitable for the environment, and those mounted external to the enclosure and subject to dirt, dust, oil, or other contaminants shall be provided with a means to cover the receptacle when the plug is removed Lighting Circuit voltage shall not exceed 150 volts between conductors B11 LMSS™ NFPA 79 Marking & Safety Signs DO NOT COPY – DO NOT SHARE Clause 16 Requirements The electrical equipment to be marked with the supplier's name, trademark, or other identifying symbol Machine Nameplate Data Safety signs/nameplates/marking/identification to Name or trademark of supplier withstand the physical environment Model, serial number, or other designation Enclosures not clearly showing they contain electrical Rated voltage, number of phases and frequency (if ac), devices to have a safety sign in accordance with ANSI Z535 and full-load current for each supply series Ampere rating of the largest motor or load Safety signs visible on the enclosure door or cover Equipment for industrial machines to have safety signage Maximum ampere rating of the short-circuit and ground- in accordance with Z535.4 to warn of electric shock/arc fault protective device, where provided flash Short-circuit current rating of the industrial control panel Remote disconnection means and disconnection via an Electrical diagram number(s) or the number of the index attachment plug to be identified on the enclosure door to the electrical drawings Safety sign, adjacent to a disconnecting operating handle interlocked with the enclosure door required if opening the door does not de-energize all parts. B11 LMSS™ NFPA 79 Technical Documentation DO NOT COPY – DO NOT SHARE Clause 17 Information to be Provided Clear, comprehensive description of the equipment, the installation and mounting, and the connection to the electrical supply(ies) Electrical supply circuit(s) requirements Overview (block) diagram(s) where appropriate Schematic diagram(s) Information (where appropriate) on the following: Programming Sequence of operation(s) Frequency of inspection Frequency & method of functional testing Adjustment, maintenance & repair Interconnection diagram Panel layouts Instruction and service manuals Physical environment B11 LMSS™ NFPA 79 Technical Documentation DO NOT COPY – DO NOT SHARE Clause 17 Information to be Provided A description (including interconnection diagrams) of the safeguards, interacting functions, and interlocking of guards with potentially hazardous motions A description of the safeguarding means and methods provided where the primary safeguards are overridden (e.g., manual programming, program verification) Means provided for the control of hazardous energies Explanation of unique terms Parts list and recommended spare parts list Maintenance instructions and adjustment procedures Reference information (where appropriate) on the following: Lubrication diagram Pneumatic diagram Hydraulic diagram Miscellaneous system diagrams (e.g., coolant, refrigerant) B11 LMSS™ NFPA 79 Testing & Verification DO NOT COPY – DO NOT SHARE Clause 18 The verification of the continuity of the effective ground-fault current path shall be conducted and documented Verification that the electrical equipment is in compliance with the technical documentation Insulation resistance test Voltage test Protection against residual voltages test Functional test B11 LMSS™ NFPA 79 Servo Drives & Motors DO NOT COPY – DO NOT SHARE Clause 19 Requirements Branch-circuit overcurrent protection to be provided – in line with manufacturer's guidance Servo drive systems to provide protection against motor overtemperature conditions Circuit conductors supplying servo drive systems sized to have an ampacity not less than 115 percent of the rated input of the equipment Where a contactor is installed ahead of the supply conductors to the servo drive, the contactor current rating to be not less than 115 percent of the maximum servo drive nameplate rating or sized in accordance with the manufacturer's specifications B11 LMSS™ NFPA 79 Pop Quiz DO NOT COPY – DO NOT SHARE GREEN with or without one or more YELLOW stripe(s) used to identify the equipment True 1 grounding conductor The receptacle (socket) for an accessory (e.g., False drill) must be supplied from an ungrounded Grounded 120-volt AC 2 120-volt AC source source An insulation and resistance test is required True as part of the testing and verification process 3 B11 LMSS™ What did you Learn DO NOT COPY – DO NOT SHARE NFPA 79 Conductors, Cables & Flexible Cords Wiring Practices Electric Motors & Associated Equipment Accessories & Lighting Marking & Safety Signs Technical documentation Testing & Verification Servo Drives & Motors B11 LMSS™ DO NOT COPY – DO NOT SHARE Recap - Standards and Regulations B11 LMSS™ Learning Objectives DO NOT COPY – DO NOT SHARE What is OSHA OSHA Citations and Regulations Machinery Safety and US Law Responsibilities B11 LMSS™ What is OSHA? DO NOT COPY – DO NOT SHARE OSH Act – Occupational Safety and Health Act Occupational Safety and Health Act of 1970 was passed to prevent workers from being killed or seriously harmed at work OSHA – Occupational Safety and Health Administration Created by the OSH Act to set and enforce protective workplace safety and health standards Part of the US Department of Labor Promulgate regulatory standards, Enforcement (inspections and citations), Advice and Education 29 CFR 1910 – OSHA Regulations for General Industry Codifies OSHA standards directly written into law Either adopted (or adapted) from consensus standards or federal standards developed by the agency B11 LMSS™ Machinery Safety and US Law DO NOT COPY – DO NOT SHARE OSH Act of 1970 – General Duty Clause (5a 1) https://www.osha.gov/laws- regs/regulations/standardnumber/1910 Each employer shall furnish each of his employees, employment and a place of employment, which is free from recognized hazards that are causing or are likely to cause death or serious physical harm The following elements are necessary to prove a violation of the General Duty Clause: 1.The employer failed to keep the workplace free of a hazard to which employees of that employer were exposed; 2.The hazard was recognized; 3.The hazard was causing or was likely to cause death or serious physical harm; and 4.There was a feasible and useful method to correct the hazard. B11 LMSS™ Who Is Responsible Under OSHA? DO NOT COPY – DO NOT SHARE Employer Sole responsibility for the safety of his employees Employer must either acquire machinery which meet the OSHA safety requirements or must upgrade deficient machinery/installations until they do Employee Each employee shall comply with occupational safety and health standards and all rules, regulations and orders issued pursuant to this Act which are applicable to his own actions and conduct OSH Act of 1970 Public Law 91-596 Clause 5(b) Manufacturers and Integrators Machinery manufacturers and integrators may not be subject to OSHA citation if they build an unsafe machine or installations Machine manufacturers and integrators are subject to wrongful injury or death (Tort) laws in Civil Court due to unsafe machines or installations B11 LMSS™ OSHA Citations DO NOT COPY – DO NOT SHARE Penalty Minimum Penalty Maximum Type of Violation (per violation) (per violation) Top 10 Fall protection, General requirements Serious $0 $15,625 OSHA Other-than-serious $0 $15,625 citations Respiratory Protection FY 2021 Willful or Repeated $11,162 $156, 259 Ladders Posting $0 $15,625 Hazard communication Requirements Failure to Abate N/A $15,625 per day Scaffolding Fall protection, Training Control of Hazardous Energy (LOTO) Eye and Face Protection Powered Industrial Trucks Machinery and Machine Guarding B11 LMSS™ OSHA 29 CFR 1910 DO NOT COPY – DO NOT SHARE 1910.147 The Control of Hazardous Energy This standard covers the servicing and maintenance of machines and equipment in which the unexpected energization or start up of the machines or equipment, or release of stored energy, could harm employees. This standard establishes minimum performance requirements for the control of such hazardous energy 1910 Subpart O Machinery and Machine Guarding One or more methods of machine guarding shall be provided to protect the operator and other employees in the machine area from hazards such as those created by point of operation, ingoing nip points, rotating parts, flying chips and sparks. 1910.06 Incorporation by Reference List of relevant standards, mostly ANSI, which are incorporated by OSHA as regulatory standards B11 LMSS™ OSHA Case Study – Secretary v Loren Cook 2005 DO NOT COPY – DO NOT SHARE On November 4, 2004, the Secretary issued Cook a one-item citation alleging a repeat violation of § 1910.212(a)(1), for failing to provide machine guarding on certain semi-automatic spinning machines. Secretary must show that (1) the cited standard applies, (2) there was noncompliance with its terms, (3) employees had access to the violative conditions and (4) the cited employer had actual or constructive knowledge of those conditions. “Cook has established it would be economically infeasible for it to retrofit the spinning machines with door guards. It would also be pointless, because the door guards would not protect employees while they performed the one activity identified as hazardous, i.e., applying mutton paste to the spinning blank.” “Cook has established its affirmative defense of infeasibility, both technological and economic. Item 1 of the citation is vacated.” https://www.oshrc.gov/assets/1/6/Loren_Cook_Company,_Docket_No._04-2179.txt B11 LMSS™ OSHA Case Study – Secretary v Walmart 2018 DO NOT COPY – DO NOT SHARE Swisslog employee hit by a trolley in an automated storage and retrieval system at a Wal-Mart facility in 2016 OSHA had sought penalties of $126,749 each from Wal-Mart Stores East, L.P., and Swisslog Logistics, Inc. for Alleged Willful Violation of § 1910.147(c)(4)(i) “The fact of the injury is not enough, however, to establish Swisslog and Wal-Mart violated the cited standard” – Judge Sharon D. Calhoun OSHA failed to establish that the startup of any of the trolleys was unexpected. The sound of the trolley motor releasing the brake also should have been adequate warning for the injured employee to get out of the way https://www.oshrc.gov/assets/1/18/17-0777__17-0784_Decision_and_Order_-DATED-_pub_WEB.html?8272 B11 LMSS™ OSHA Case Study – Secretary v Westvaco 1993 DO NOT COPY – DO NOT SHARE Osha cited Westvaco alleging serious violation of 29 CFR 1910.147 (c)(1).(1) charging a failure to lockout the slotter section of a printer/slotter machine Westvaco argued that the standard did not apply because the task came under the minor servicing exception The judge noted that "normal production operations" is defined in 29 CFR 1910.147(b) as "the utilization of a machine or equipment to perform its intended production function." Finding this definition rather vague, he focused on the definition of setting up" in 29 CFR 1910.147(b), which reads: "any work performed to prepare a machine or equipment to perform its normal production operation. The judge noted that "setting up" is listed as an activity under the definition of "servicing and/or maintenance" in section 1910.147(b), (10) and that servicing and maintenance activities are expressly covered by the lockout standard, under 29 CFR 1910.147(a)(2)(i). He stated that, based on the plain meaning of the exception and these definitions, "work performed on the machine while the machine is not being operated to actually produce its product is either servicing or maintenance." The judge further stated that work that is performed before the normal production operation in order to prepare the machine for production is a specific service activity, called setting up. Setting up does not occur during normal production operations. Therefore, setting up cannot, by definition, fall within the exception to 1910.147(a)(2)(ii). https://www.oshrc.gov/assets/1/18/90-1341.pdf?9776 B11 LMSS™ DO NOT COPY – DO NOT SHARE ANSI/ASSP Z244.1 – 2016 (R2020) The Control of Hazardous Energy Lockout, Tagout and Alternative Methods B11 LMSS™ Learning Objectives DO NOT COPY – DO NOT SHARE Introduction History OSHA and Alternative Methods Key Definitions Responsibilities B11 LMSS™ Z244.1 History DO NOT COPY – DO NOT SHARE First Z244.1 committee meeting held in New York Begun in 1973 American National Standard for Personnel Protection - 1st edition Lockout/Tagout of Energy Sources - Minimum Safety 1982 Requirements Z244.1 ANSI/ASSP Z244.1 Control of Hazardous Energy, 2nd edition Lockout/Tagout and Alternative Methods 2003 ANSI/ASSP Z244.1 – 2016 The Control of Hazardous Energy 3rd edition Lockout, Tagout and Alternative Methods 2016 B11 LMSS™ OSHA & Alternative Methods DO NOT COPY – DO NOT SHARE B11 LMSS™ OSHA Says…… DO NOT COPY – DO NOT SHARE 1910.147(a)(1)(i) This standard covers the servicing and maintenance of machines and equipment in which the unexpected energization or start up of the machines or equipment, or release of stored energy, could harm employees. This standard establishes minimum performance requirements for the control of such hazardous energy. 1910.147(a)(2)(i) This standard applies to the control of energy during servicing and/or maintenance of machines and equipment. 1910.147(a)(2)(ii) Normal production operations are not covered by this standard (See Subpart O of this Part). Servicing and/or maintenance which takes place during normal production operations is covered by this standard only if: Exception to 1910.147(a)(2)(ii) Minor tool changes and adjustments, and other minor An employee is required to remove or bypass a guard or other safety device; or servicing activities, which take place during normal An employee is required to place any part of his or her body into an area on a production operations, are not covered by this standard if machine or piece of equipment where work is actually performed upon the they are routine, repetitive, and integral to the use of the material being processed (point of operation) or where an associated danger zone equipment for production, provided that the work is exists during a machine operating cycle. performed using alternative measures which provide effective protection B11 LMSS™ ……and in 2008 OSHA Stated - DO NOT COPY – DO NOT SHARE As a general principle, the LOTO standard does not apply to CPL 02 – 00 – 147 servicing and maintenance activities when employees are not exposed to hazardous energy. Therefore, employees can be protected from these severe workplace injuries and fatality incidents by: 1.LOTO – i.e., 29 CFR §1910.147; 2.Complying with the minor servicing exception to the LOTO standard – i.e., the note contained in §1910.147(a)(2)(ii); 3.Utilizing the cord and plug connected equipment or hot tap exemptions – i.e., §§ 1910.147(a)(2)(iii)(A) and (a)(2)(iii)(B); 4.Effective machine guarding, in compliance with Subpart O, that eliminates or prevents employee exposure from the hazardous energy associated with the machines or equipment; 5.Final actions granting LOTO standard variances (e.g., energy isolating device equivalency) in accordance with the §1905 rules; or 6.Other applicable portions of Part 1910 (e.g., guarding and LOTO contained in Subpart R special industries standards; electrical lockout and tagging requirements contained in §1910.333) that prevent employee exposure to hazardous energy. https://www.osha.gov/enforcement/directives/directivenumber/CPL B11 LMSS™ Routine, Repetitive, Integral? DO NOT COPY – DO NOT SHARE The first set of criteria for determining the application of the minor CPL 02 – 00 – 147 servicing exception is whether the activity must take place during, and is inherent to, normal production operations. These servicing activities must be necessary to allow production to proceed without interruption. Additionally, the minor servicing activity must be: Routine The activity must be performed as part of a regular and prescribed course of procedure and be performed in accordance with established practices. Repetitive The activity must be repeated regularly as part of the production process or cycle. Integral The activity must be inherent to the production process. B11 LMSS™ Safeguarding Alternatives? DO NOT COPY – DO NOT SHARE B11.19 describes effective safeguarding alternatives for the protection of employees CPL 02 – 00 – 147 Some of these described safeguards include: A. Interlocked barrier guards, B. Presence sensing devices, and C. Various devices under the exclusive control of the employee. Such guards or safety devices, when properly applied, may be used in clearing minor jams and performing other minor servicing functions, which occur during normal production operations and which meet the §1910.147(a)(2)(ii) exception criteria. During minor servicing, an employer is considered to have met the requirement for providing effective alternative protection by the use of special tools or guarding (safeguarding) techniques that effectively prevent A big thank you for the work carried out by employee exposure to hazardous energy. Mike Taubitz, who has provided guidance, assistance and material for the creation of To better illustrate effective alternative protection based on recognized this module. good engineering practices, a circuit that meets the control reliability B11 LMSS™ Further Reading DO NOT COPY – DO NOT SHARE https://www.osha.gov/enforcement/directives/cpl-02-00-163 https://www.osha.gov/sites/default/files/publications/osha3170.pdf B11 LMSS™ DO NOT COPY – DO NOT SHARE Further Reading B11 LMSS™ Introduction to Z244.1 DO NOT COPY – DO NOT SHARE ANSI/ASSP Z244.1-2016 (R2020) Establishes requirements to protect personnel from the unexpected release of hazardous energy Approved 13th October 2016 Reconfirmed in 2020 Covers machines, equipment and processes where unexpected start-up or the release of stored energy may cause harm Specifies the use of lockout (primary method), tagout or alternative methods to control hazardous energy Applies to activities such as erecting, installing, constructing, repairing, adjusting, inspecting, unjamming, set up, testing, troubleshooting, cleaning, dismantling, servicing and maintaining machines, equipment or processes Does not apply to work on cord and plug connected equipment, hot tap operations or passenger vehicles/pleasure boats/private aircraft/recreational or sport vehicles B11 LMSS™ Introduction to Z244.1 DO NOT COPY – DO NOT SHARE 1 Scope & Purpose 2 References 3 Definitions 4 Responsibilities 5 Design of Machinery/Equipment for the Control of Hazardous Energy 6 Hazardous Energy Control Program 7 Control of Hazardous Energy 8 Alternative Methods of Hazardous Energy Control B11 LMSS™ Z244.1 Key Definitions DO NOT COPY – DO NOT SHARE Clause 3 An evaluation of the probability and the degree of the possible harm or damage to Risk Assessment health due to a hazardous situation in order to determine the risk reduction measures. Risk Reduction Any action or means used to eliminate hazards and/or reduce risks. Measures That risk for which the probability of an incident or exposure occurring and the severity of harm or damage that could result is as low as reasonably practicable (ALARP) in the Acceptable Risk setting being considered. For the purpose of this standard, the terms “acceptable risk” and “tolerable risk” are considered to be synonymous. Alternative A means of controlling hazardous energy (other than energy isolation) to reduce risk to Methods an acceptable level. Lockout The placing of a lock and tag or an identifiable lock on the energy-isolating device. A means to prevent the inadvertent re-energization of machinery or equipment using a Tagout tag securely fastened to an energy-isolating device. B11 LMSS™ Who has Responsibilities? DO NOT COPY – DO NOT SHARE Clause 4 Supplier Design, construction, integration, and installation of machines, equipment or processes so that the user can effectively control hazardous energy Users Comply with Z244.1 by establishing an effective program to protect personnel from hazardous energy Personnel Comply with the hazardous energy control program B11 LMSS™ Z244.1 Introduction Pop Quiz DO NOT COPY – DO NOT SHARE OSHA has issued Regulations for General True Industry 1 29 CFR 1910 Under OSHA employer has sole responsibility True for the safety of their employees 2 Lockout is the placing of a tag on the energy- False Lock and tag or an isolating device 3 identifiable lock B11 LMSS™ What did you Learn? DO NOT COPY – DO NOT SHARE OSHA and the Law What is OSHA OSHA Citations and Regulations Machinery Safety and US Law Responsibilities Introduction to Z244.1 History of Z244.1 Alternative Methods & OSHA Contents & Definitions Responsibilities B11 LMSS™ DO NOT COPY – DO NOT SHARE Design of Machinery/Equipment for the Control of Hazardous Energy B11 LMSS™ Learning Objectives DO NOT COPY – DO NOT SHARE Risk Assessment Partial energization Energy-Isolation Devices Location Identification Capability and Suitability Information for Use Stored Energy Restraint Devices Tamper Resistance B11 LMSS™ Risk Assessment & Hazard Control Methodology DO NOT COPY – DO NOT SHARE Clause 5 Risk Assessment in accordance with B11.0, during the design phase to determine the hazard control methodologies Identification of energy necessary to perform the task(s) Elimination of hazardous energy sources Control of hazardous energy Alternative methods B11 LMSS™ Design of Machinery/Equipment for the Control of Hazardous Energy DO NOT COPY – DO NOT SHARE Clause 5 Partial Energization When it is necessary for machines to remain partially energized alternative methods required for personnel safety Component Isolation Local isolation of component parts or component systems to be provided for Energy-Isolating Devices Machines required to be designed, manufactured, supplied and installed with energy-isolating devices Devices to be capable of controlling/dissipating hazardous energy and should be integral B11 LMSS™ Energy Isolating Devices DO NOT COPY – DO NOT SHARE Clause 5.4 Location Accessible and conveniently located to facilitate their use Located outside of hazardous areas at a convenient height If not possible to locate in a convenient location proper access should be provided Identification Machine, equipment or process supplied; and Energy type and magnitude Marking to be durable enough to withstand the environment Capability An energy-isolating device is capable of being locked out if it has a hasp or other attachment means that a lockout device can be affixed to a lockable mechanism built into it B11 LMSS™ OSHA Says…… DO NOT COPY – DO NOT SHARE 1910.147(c)(2)(ii) If an energy isolating device is capable of being locked out, the employer's energy control program under paragraph (c)(1) of this section shall utilize lockout, unless the employer can demonstrate that the utilization of a tagout system will provide full employee protection as set forth in paragraph (c)(3) of this section. 1910.147(c)(2)(iii) After January 2nd 1990 whenever replacement or major repair, renovation or modification of a machine or equipment is performed, and whenever new machines or equipment are installed, energy isolating devices for such machines or equipment shall be designed to accept a lockout device. B11 LMSS™ Information For Use DO NOT COPY – DO NOT SHARE Clause 5.6 Supplier Documentation Requirements Procedures for use of energy-isolating devices Specific instructions for tasks requiring partial energization Installation Instructions Energy-Isolating Devices Procedures Specific instructions for setup, changeover, malfunctions, jams, misfeeds, troubleshooting, etc. Installation instructions for the installer identifying energy-isolating devices Instructions for releasing or controlling stored energy after isolation Warning and special instructions as necessary B11 LMSS™ Stored and Residual Energy/Control Integration DO NOT COPY – DO NOT SHARE Clause 5.7, 5.8 Stored & Residual Energy Where present and assessed as an unacceptable risk a means for safe dissipation to be provided A means of verifying status of devices required Where coasting or run down is present safeguarding to protect personnel required If safeguarding not practicable safe positioning allowed See ANSI B11.19 Control Integration When alternative methods are used during setup/troubleshooting or task requiring energization or part energization risk reduction measures shall be applied to prevent the initiation of hazardous motion or release of hazardous energy. See B11.26 B11 LMSS™ OSHA Says…… DO NOT COPY – DO NOT SHARE 1910.147(d)(5)(i) Following the application of lockout or tagout devices to energy isolating devices, all potentially hazardous stored or residual energy shall be relieved, disconnected, restrained, and otherwise rendered safe. 1910.147(d)(5)(ii) If there is a possibility of reaccumulation of stored energy to a hazardous level, verification of isolation shall be continued until the servicing or maintenance is completed, or until the possibility of such accumulation no longer exists. 1910.147(d)(6) Verification of isolation. Prior to starting work on machines or equipment that have been locked out or tagged out, the authorized employee shall verify that isolation and deenergization of the machine or equipment have been accomplished. B11 LMSS™ Restraint Devices DO NOT COPY – DO NOT SHARE Clause 5.9 e.g., safety blocks, chain locks, locking pins, and limiting/blocking pins Two options for restraint mechanisms: Mechanical Designed to hold the full working force of the machine and tooling members when the machine actuation can take place while the mechanism is in place Pics of different mechanisms Interlocked Interlocked with the machine to prevent actuation of hazardous motion(s) or situation(s) of the machine when removed from its storage position and be designed and constructed to hold the maximum anticipated load B11 LMSS™ Tamper Resistance DO NOT COPY – DO NOT SHARE Clause 5.10 Hazardous energy control methods required to provide tamper resistance based upon risk Motivation to defeat the hazardous energy control method should be considered (see ISO 14119 Annex H) B11 LMSS™ Design of Machinery Pop Quiz DO NOT COPY – DO NOT SHARE Specific instructions for tasks requiring True partial energization shall be provided 1 Motivation to defeat the hazardous energy True control methods should be considered 2 False A light curtain is a restraint device A light curtain is an input 3 device B11 LMSS™ What did you Learn? DO NOT COPY – DO NOT SHARE Design of Machinery/Equipment for the Control of Hazardous Energy Risk Assessment Partial energization Energy-Isolation Devices Location Identification Capability and Suitability Information for Use Stored Energy Restraint Devices Tamper Resistance B11 LMSS™ DO NOT COPY – DO NOT SHARE Hazardous Energy Control Program B11 LMSS™ Learning Objectives DO NOT COPY – DO NOT SHARE Methods Hazardous Energy Control Program Communication & Training Program review Management of Change B11 LMSS™ Risk Assessment Process DO NOT COPY – DO NOT SHARE 1. Prepare for and Set Limits of the Assessment 2. Identify Tasks and Hazards 3. Assess Initial Risk 4. Reduce Risk 5. Assess Residual Risk 6. Residual No Risk Acceptable? New/Next Hazard Yes 7. Validate Solutions 8. Results/Documentation Assessment Complete B11 LMSS™ Hazardous Energy Control Program DO NOT COPY – DO NOT SHARE Clause 6 The hazardous energy control methodologies selected by the user shall be one or more of the following: Control of hazardous energy Alternative methods Partial energization The methods selected by the user shall be appropriate for the hazards and the risks of a given task B11 LMSS™ Methods of Hazardous Energy Control DO NOT COPY – DO NOT SHARE Clause 6.2 The method of hazardous energy control selected depends on whether the task can be performed with or without energized conditions The PRIMARY method shall be lockout unless….. It can be demonstrated that Tagout or an alternative method provides effective protection Before adopting alternative measures the user is required to ensure a risk assessment is conducted and demonstrates the adequacy of the alternative method A documented and readily available risk assessment is required