AVIA-1065 Carburetor Maintenance PDF
Document Details
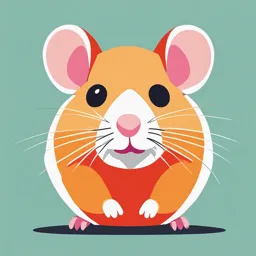
Uploaded by SnazzyDystopia5099
Fanshawe College, London, Ontario
AVIA
Tags
Summary
This document provides instruction on carburetor maintenance. It covers removal, inspection, and installation procedures, as well as troubleshooting. The document also has questions for assessment. This document is valuable for learning about aircraft engine maintenance.
Full Transcript
RECIPROCATING ENGINE AVIA 1065 Intro 1 Carburetor Maintenance AVIA-1065 2 Video Links Animated Rotary Vane Pump Continental TSIO-360 Continental Fuel Injection engine start Actual Rotary Vane Pump http://www.precisio...
RECIPROCATING ENGINE AVIA 1065 Intro 1 Carburetor Maintenance AVIA-1065 2 Video Links Animated Rotary Vane Pump Continental TSIO-360 Continental Fuel Injection engine start Actual Rotary Vane Pump http://www.precisionairmotive.com/Publication s/15-812_b.pdf 3 Review https://www.youtube.com/watch?v=d8SdqUOXuUk What are the parts of a Bendix Precision fuel injected system? – an injector – a flow divider – fuel discharge nozzles Is it a continuous-flow system? Yes Parts of the Bendix Precision Injector? an airflow section, a regulator section, a fuel metering section 4 Review What are the parts of a Continental TCM injector system? a fuel injector pump a fuel/air control unit a fuel manifold a fuel discharge nozzle It uses what type of pump? Rotary Vane type pump Aircraft using fuel injection use what type of flow for fuel injection? constant or continuous 5 6 Review 7 Review 8 Review 9 Review 10 Review 11 Carburetor Maintenance Carburetor Removal The procedures are generally much the same make sure the fuel shutoff (or selector) valve is closed disconnect the throttle and mixture control linkages lockwire the throttle valve in the closed position 12 Carburetor Maintenance disconnect: the fuel inlet line all vapor return lines all gauge lines all primer lines DO NOT alter the rigging of the throttle and mixture controls if the same carburetor is to be reinstalled remove the air scoop or air scoop adapter remove the air screens and gaskets from the carburetor remove the nuts and washers securing the carburetor to the engine remove the carburetor https://www.youtube.com/watch?v=MiO- 3vplZis 13 Carburetor Maintenance use extreme care to ensure that nothing is dropped into the engine when removing a downdraft carburetor immediately install a protective cover on the carburetor mounting flange of the engine to prevent small parts or foreign material from falling into the engine plug open fuel lines using the proper cover fittings when there is danger of foreign material entering them during removal or installation of the carburetor 14 Installation of Carburetor Check the carburetor for Carburetor Maintenance proper lockwiring before installation on an engine be sure that all shipping plugs have been removed from the carburetor openings remove the protective cover from the carburetor mounting flange on the engine place the carburetor mounting flange gasket in position 15 Carburetor Maintenance Bleed passages are incorporated in the mounting pad on some engines The gasket must be installed so that the bleed hole in the gasket is aligned with the passage in the mounting flange inspect the induction passages for the presence of any foreign material before installing the carburetor close and lockwire the throttle valves in the closed position as soon as the carburetor is placed in position on the engine until the remainder of the installation is completed 16 Place the carburetor deck screen in position to further eliminate the possibility of foreign Carburetor Maintenance objects entering the induction system when feasible connect the fuel lines and fill the carburetor with fuel When installing a carburetor that uses diaphragms for controlling fuel flow turn on the fuel boost pump then, move the mixture control from the idle 17 cutoff position to rich position continue the flow until oil-free fuel flows from the drain valve this indicates that the preservative oil has been flushed from the carburetor turn off the fuel flow plug the fuel inlet and vapor vent outlet allow the carburetor to stand for a minimum of 8 hours filled with fuel this is necessary in order to soak the diaphragms render them pliable to the same degree as when the unit was originally calibrated Carburetor Maintenance Tighten the carburetor mounting bolts to the value specified in the table of torque limits in the applicable maintenance manual Tighten and safety any other nuts and bolts incidental to the installation of the carburetor before connecting the throttle and mixture-control levers Check the throttle and mixture- control lever on the unit for freedom of movement before connecting the control cables or linkage After the carburetor has been bolted to the engine check the vapor vent lines or return lines from the carburetor to the aircraft fuel tank for restriction 18 Rigging Carburetor Controls Connect and adjust Carburetor Maintenance carburetor or fuel metering equipment throttle controls so that full movement of the throttle is obtained from corresponding full movement of the control in the cockpit Check and adjust the throttle control linkages so that springback on the throttle quadrant in the aircraft is equal in both the full-open and the full-closed position Correct any excess play or looseness of control linkage or cables Springback 19 Carburetor Maintenance Controls should be checked so that they go stop-to-stop on the carburetor Check for complete and full travel of each control Adjust the mixture control mechanism when installing carburetors or fuel metering equipment incorporating manual-type mixture controls that do not have marked positions to provide an equal amount of springback at both: the rich and the lean ends of the control quadrant in the cockpit when either the mixture control on the carburetor or the fuel metering equipment is moved through the full range 20 Where mixture controls with Carburetor Maintenance detents are used, rig that the designated positions on the control quadrant in the aircraft agree with the corresponding positions on the carburetor or fuel metering equipment Controls should move freely and smoothly without binding throughout their total travel. Check the controls for proper positioning in both: the advance position (forward) the retard position (back) correct excess play or looseness of control linkage or cables safety all controls properly to eliminate the possibility of loosening from vibration during operation 21 Adjusting Idle Mixtures Carburetor Maintenance Excessively rich or lean idle mixtures result in incomplete combustion within the engine cylinder with resultant formation of carbon deposits on the spark plugs with subsequent spark plug fouling. OR Makes it necessary to taxi at high idle speeds with: resultant fast taxi speeds excessive brake wear Each engine must have the carburetor idle mixture tailored for the particular engine installation if best operation is to be obtained 22 Carburetor Maintenance If an engine does not respond to idle mixture adjustment with the resultant stable idling characteristics previously outlined some other phase of engine operation is not correct, determine and correct the cause of the difficulty How to adjust Warm up the engine until oil and cylinder head temperatures are normal. Always make idle mixture adjustments with cylinder head temperatures at normal values Keep the propeller control in the increase rpm setting (fine/forward position) throughout the entire process of warming up the engine. The idle mixture adjustment is made on the idle mixture fuel control valve [Figure 2-46] 23 Carburetor Maintenance 24 On an engine with a conventional carburetor move the carburetor mixture control slowly and smoothly Carburetor Maintenance toward the idle cutoff position It is necessary to observe the tachometer for an indication of an rpm change on installations that do not use a manifold pressure gauge The idle mixture should be adjusted to provide an rpm rise prior to decreasing as the mixture is pulled to ICO with most installations The importance of idle mixture adjustment cannot be overstressed. Optimum engine operation at low speeds can be obtained only when proper fuel/air mixtures are delivered to every cylinder of the engine excessively rich idle mixtures and the resultant incomplete combustion cause sparkplug fouling 25 Idle Speed Adjustment Carburetor Maintenance Reset the idle stop to the idle rpm specified in the aircraft maintenance manual The engine must be warmed up thoroughly before adjusting the idle mixture Check for ignition system malfunctioning Periodically run the engine up to approximately half of normal rated speed to clear the engine throughout any carburetor adjustment procedure Some carburetors are equipped with an eccentric screw to adjust idle rpm Others use a spring-loaded screw to limit the throttle valve closing 26 Carburetor Maintenance Adjust the screw as required to increase or decrease rpm with the throttle retarded against the stop open the throttle to clear the engine; close the throttle and allow the rpm to stabilize repeat this operation until the desired idling speed is obtained 27 Carburetor Maintenance Carburetor Removal The procedures are generally much the same make sure the fuel shutoff (or selector) valve is closed disconnect the throttle and mixture control linkages lockwire the throttle valve in the closed position 28 Carburetor Maintenance disconnect: the fuel inlet line all vapor return lines all gauge lines all primer lines DO NOT alter the rigging of the throttle and mixture controls if the same carburetor is to be reinstalled remove the air scoop or air scoop adapter remove the air screens and gaskets from the carburetor remove the nuts and washers securing the carburetor to the engine remove the carburetor https://www.youtube.com/watch?v=MiO- 3vplZis 29 Carburetor Maintenance use extreme care to ensure that nothing is dropped into the engine when removing a downdraft carburetor immediately install a protective cover on the carburetor mounting flange of the engine to prevent small parts or foreign material from falling into the engine plug open fuel lines using the proper cover fittings when there is danger of foreign material entering them during removal or installation of the carburetor 30 Installation of Carburetor Carburetor Maintenance Check the carburetor for proper lockwiring before installation on an engine be sure that all shipping plugs have been removed from the carburetor openings remove the protective cover from the carburetor mounting flange on the engine place the carburetor mounting flange gasket in position 31 Carburetor Maintenance Bleed passages are incorporated in the mounting pad on some engines The gasket must be installed so that the bleed hole in the gasket is aligned with the passage in the mounting flange inspect the induction passages for the presence of any foreign material before installing the carburetor close and lockwire the throttle valves in the closed position as soon as the carburetor is placed in position on the engine until the remainder of the installation is completed 32 Place the carburetor deck screen in position to further eliminate the possibility of foreign Carburetor Maintenance objects entering the induction system when feasible connect the fuel lines and fill the carburetor with fuel When installing a carburetor that uses diaphragms for controlling fuel flow turn on the fuel boost pump then, move the mixture control from the idle 33 cutoff position to rich position continue the flow until oil-free fuel flows from the drain valve this indicates that the preservative oil has been flushed from the carburetor turn off the fuel flow plug the fuel inlet and vapor vent outlet allow the carburetor to stand for a minimum of 8 hours filled with fuel this is necessary in order to soak the diaphragms render them pliable to the same degree as when the unit was originally calibrated Carburetor Maintenance Tighten the carburetor mounting bolts to the value specified in the table of torque limits in the applicable maintenance manual Tighten and safety any other nuts and bolts incidental to the installation of the carburetor before connecting the throttle and mixture-control levers Check the throttle and mixture- control lever on the unit for freedom of movement before connecting the control cables or linkage After the carburetor has been bolted to the engine check the vapor vent lines or return lines from the carburetor to the aircraft fuel tank for restriction 34 Rigging Carburetor Controls Connect and adjust Carburetor Maintenance carburetor or fuel metering equipment throttle controls so that full movement of the throttle is obtained from corresponding full movement of the control in the cockpit Check and adjust the throttle control linkages so that springback on the throttle quadrant in the aircraft is equal in both the full-open and the full-closed position Correct any excess play or looseness of control linkage or cables Springback 35 Carburetor Maintenance Controls should be checked so that they go stop-to-stop on the carburetor Check for complete and full travel of each control Adjust the mixture control mechanism when installing carburetors or fuel metering equipment incorporating manual-type mixture controls that do not have marked positions to provide an equal amount of springback at both: the rich and the lean ends of the control quadrant in the cockpit when either the mixture control on the carburetor or the fuel metering equipment is moved through the full range 36 Carburetor Maintenance Where mixture controls with detents are used, rig that the designated positions on the control quadrant in the aircraft agree with the corresponding positions on the carburetor or fuel metering equipment Controls should move freely and smoothly without binding throughout their total travel. Check the controls for proper positioning in both: the advance position (forward) the retard position (back) correct excess play or looseness of control linkage or cables safety all controls properly to eliminate the possibility of loosening from vibration during operation 37 Adjusting Idle Mixtures Carburetor Maintenance Excessively rich or lean idle mixtures result in incomplete combustion within the engine cylinder with resultant formation of carbon deposits on the spark plugs with subsequent spark plug fouling. OR Makes it necessary to taxi at high idle speeds with: resultant fast taxi speeds excessive brake wear Each engine must have the carburetor idle mixture tailored for the particular engine installation if best operation is to be obtained 38 Carburetor Maintenance If an engine does not respond to idle mixture adjustment with the resultant stable idling characteristics previously outlined some other phase of engine operation is not correct, determine and correct the cause of the difficulty How to adjust Warm up the engine until oil and cylinder head temperatures are normal. Always make idle mixture adjustments with cylinder head temperatures at normal values Keep the propeller control in the increase rpm setting (fine/forward position) throughout the entire process of warming up the engine. The idle mixture adjustment is made on the idle mixture fuel control valve [Figure 2-46] 39 Carburetor Maintenance 40 On an engine with a conventional carburetor move the carburetor mixture control slowly and smoothly toward the idle cutoff position It is necessary to observe the tachometer for an indication of an rpm change on installations that do not use a manifold pressure gauge The idle mixture should be adjusted to provide an rpm rise prior to decreasing as the mixture is pulled to ICO with most installations Carburetor Maintenance The importance of idle mixture adjustment cannot be overstressed. Optimum engine operation at low speeds can be obtained only when proper fuel/air mixtures are delivered to every cylinder of the engine excessively rich idle mixtures and the resultant incomplete combustion cause sparkplug fouling 41 Idle Speed Adjustment Carburetor Maintenance Reset the idle stop to the idle rpm specified in the aircraft maintenance manual The engine must be warmed up thoroughly before adjusting the idle mixture Check for ignition system malfunctioning Periodically run the engine up to approximately half of normal rated speed to clear the engine throughout any carburetor adjustment procedure Some carburetors are equipped with an eccentric screw to adjust idle rpm Others use a spring-loaded screw to limit the throttle valve closing 42 Carburetor Maintenance Adjust the screw as required to increase or decrease rpm with the throttle retarded against the stop open the throttle to clear the engine; close the throttle and allow the rpm to stabilize repeat this operation until the desired idling speed is obtained 43 Fuel System Inspection and Maintenance Consists basically of an examination of the system for conformity to design requirements together with functional tests to prove correct operation Complete System: Inspect the entire system for: Wear Damage leaks Make sure that all units are securely attached and properly safetied 44 45 Fuel System Inspection and Maintenance Check for the presence of: sediment water slime In the drain plugs or valves in the fuel system or the filter and sump The filters or screens must be clean and free from corrosion Fuel Tank Inspect the tanks for: corrosion on the external surfaces security of attachment correct adjustment of straps and slings check the fittings and connections for leaks or failures Lines and Fittings Be sure that the lines are properly supported and that the nuts and clamps are securely tightened Fuel System Inspection Use a hose-clamp torque wrench to tighten hose clamps to the proper torque. and Maintenance If this wrench is not available: tighten the clamp finger-tight plus the number of turns specified for the hose and clamp Check AMM for hose/line limits i.e. braided lines 46 Fuel System Inspection and Main Line Strainers Maintenance Drain water and sediment from the main line strainer at each preflight inspection Remove and clean the screen at the periods specified in the airplane maintenance manual Examine the sediment removed from the housing Particles of rubber are often early warnings of hose deterioration Check for leaks and damaged gaskets 47 Fuel System Inspection and Maintenance aircraft engine and controls Engine operation description and oils https://youtu.be/lgtcTElNfF4 https://youtu.be/mmmcj53TNic 48 Reciprocating Engine Lubrication Systems AVIA-1065 Reciprocating Engine Lubrication Systems can be divided into two basic classifications: wet sump dry sump both systems use similar types of components the dry sump system is explained as an example system because the dry sump system contains all the components of the wet Reciprocating Engine sump system Lubrication Systems 50 Reciprocating Engine Lubrication Systems can be divided into two basic classifications: Reciprocating Engine wet sump Lubrication Systems stores oil in a reservoir inside the engine it is returned to this crankcase based reservoir after the oil is circulated through the engine 51 Reciprocating Engine Lubrication Systems can be divided into two basic classifications: dry sump pumps the oil from the engine’s crankcase to an external tank that stores the oil uses: 1. a scavenge pump 2. some external tubing 3. an external tank to Reciprocating Engine store the oil Lubrication Systems 52 Reciprocating Engine Lubrication Systems Combination Splash and Pressure Lubrication The lubricating oil is distributed to the various moving parts of a typical internal combustion engine by either: pressure splash a combination of pressure and splash 53 Reciprocating Engine Lubrication Systems Combination Splash and Pressure Lubrication pressure principal method of lubricating aircraft engines advantages: – positive introduction of oil to the bearings – cooling effect-caused by the large quantities of oil that can be pumped, or circulated, through a bearing – satisfactory lubrication in various attitudes of flight 54 Reciprocating Engine Lubrication Systems Combination Splash and Pressure Lubrication splash may be used in addition to pressure lubrication on aircraft engines never used by itself aircraft-engine lubrication systems are always either the pressure type or the combination pressure and splash type usually the latter a combination of pressure and splash 55 Reciprocating Engine 56 Lubrication Systems Lubrication System Requirements must be designed and constructed so that it functions properly within all flight attitudes and all atmospheric conditions that the aircraft is expected to operate in in wet sump engines, this requirement must be met when only half of the maximum lubricant supply is in the engine the crankcase must be vented to the atmosphere to prevent leakage of oil from excessive pressure Reciprocating Engine Lubrication Systems Dry Sump Oil Systems many reciprocating and turbine aircraft engines have pressure dry sump lubrication systems the oil supply in this type of system is carried in a tank a pressure pump circulates the oil through the engine scavenger pumps then return it to the tank as quickly as it accumulates in the engine sumps 57 Reciprocating Engine Lubrication Systems Dry Sump Oil Systems the need for a separate supply tank is apparent when considering the complications that would result if large quantities of oil were carried in the engine crankcase each engine is supplied with oil from its own complete and independent system the functions of all such systems are the same 58 Reciprocating Engine Dry Sump Oil Systems Lubrication Systems the principal units in a typical reciprocating engine dry sump oil system include [Figure 6-4]: an oil supply tank an engine-driven pressure oil pump a scavenge pump an oil cooler with an oil cooler control valve oil tank vent necessary tubing pressure and temperature indicators 59 Reciprocating Engine Lubrication Systems 60 Reciprocating Engine Lubrication Systems Oil Tanks generally associated with a dry sump lubrication system a wet sump system uses the crankcase of the engine to store the oil usually constructed of aluminum alloy must withstand any: vibration inertia fluid loads https://www.youtube.com/watch?v=cWDC XFwPLIs&t=10s 61 Reciprocating Engine Lubrication Systems Oil Tanks must have expansion space of not less than the greater of 10 percent of the tank capacity or 0.5 gallons if used with a reciprocating engine each filler cap of an oil tank that is used with an engine must provide an oil-tight seal usually placed: close to the engine high enough above the oil pump inlet to ensure gravity feed 62 Reciprocating Engine Lubrication Systems Oil Tanks oil tank capacity varies with the different types of aircraft usually sufficient to ensure an adequate supply of oil for the total fuel supply the tank filler neck is positioned to provide sufficient room for: oil expansion foam to collect the filler cap or cover: is marked with the word OIL has a drain the drain in the filler cap well disposes of any overflow caused by the filling operation 63 Reciprocating Engine Oil Tanks Lubrication Systems oil tank vent lines are provided to ensure proper tank ventilation in all attitudes of flight usually connected to the engine crankcase – to prevent the loss of oil through the vents indirectly vents the tanks to the atmosphere through the crankcase breather 64 Reciprocating Engine the return line in the top of the Lubrication Systems tank is generally positioned to discharge the returned oil against the wall of the tank in a swirling motion – this method considerably reduces foaming that occurs when oil mixes with air – baffles in the bottom of the oil tank break up this swirling action – to prevent air from being drawn into the inlet line of the oil pressure pump – foaming oil increases in volume and reduces its ability to provide proper lubrication 65 Reciprocating Engine Lubrication Systems Oil Tanks the main outlet from the tank may be in the form of a standpipe so that there’s always a reserve supply of oil for propeller feathering in case of engine failure in the case of oil-controlled propellers 66 Reciprocating Engine Lubrication Systems Oil Tanks an oil tank sump attached to the undersurface of the tank acts as a trap for moisture and sediment [Figure 6-4] the water and sludge can be drained by manually opening the drain valve in the bottom of the sump most aircraft oil systems are equipped with the dipstick-type quantity gauge often called a bayonet gauge 67 Reciprocating Engine Lubrication Systems Oil Tanks some larger aircraft systems also have an oil quantity indicating system that shows the quantity of oil during flight one type system consists essentially of an arm and float mechanism that rides the level of the oil and actuates an electric transmitter on top of the tank the transmitter is connected to a cockpit gauge that indicates the quantity of oil 68 The End 69