Automation And Control Engineering PDF
Document Details
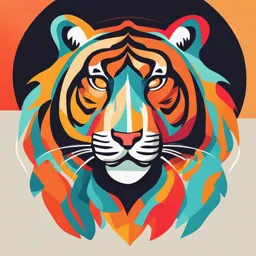
Uploaded by PremierPermutation
MICET
Tags
Summary
This document is a digital study material on automation and control engineering. It details course objectives, unit introductions, and course outlines for the subject. It also includes a course outline for the first unit.
Full Transcript
A U TO M AT I O N A N D CONTROL ENGINEERING (R17A0327) 4th Year B. Tech I- sem, Mechanical Engineering www.mrcet.ac.in COURSE OBJECTIVES UNIT - 1 CO1: To perform one or more processing operations & To understand the need of Mechatroni...
A U TO M AT I O N A N D CONTROL ENGINEERING (R17A0327) 4th Year B. Tech I- sem, Mechanical Engineering www.mrcet.ac.in COURSE OBJECTIVES UNIT - 1 CO1: To perform one or more processing operations & To understand the need of Mechatronics systems UNIT - 2 CO2: To make students familiar with the constructions and working principle of different types of sensors and transducers. UNIT - 3 CO3: Understand the fundamental concepts of electro mechanics and fluid mechanics (hydraulics and pneumatics) of Actuators and drive systems. UNIT - 4 CO4: To impart knowledge on the control elements UNIT - 5 CO5: To understand the different control schemes generally used to get best output. DEPARTMENT OF MECHANICAL ENGINEERING UNIT 1 INTRODUCTION TO A U T O M AT I O N & M E C H AT R O N I C S CO1: To perform one or more processing operations & To understand the need of Mechatronics systems www.mrcet.ac.in UNIT – I (SYLLABUS) INTRODUCTION TO AUTOMATION Types and strategies of automation Pneumatic and Hydraulic components circuits Mechanical Feeding and machine tool control to transfer the automation Introduction to Mechatronics Role of various engineering disciplines in Mechatronics Mechatronics design elements Scope of Mechatronics Applications of Mechatronics. DEPARTMENT OF MECHANICAL ENGINEERING COURSE OUTLINE UNIT -1 LECTURE LECTURE TOPIC KEY ELEMENTS LEARNING OBJECTIVES 1. INTRODUCTION TO AUTOMATION Definition of force. Understanding of basics of Automation (B2) 2 Types and strategies of automation Define types of automation Understanding of types of automation (B2) 3 Pneumatic and Hydraulic components circuits Working principle of pneumatic Understanding and Analyze the Working and hydraulic components principle of pneumatic and hydraulic circuits components circuits Parallelogram law. (B2, B4) 4 Mechanical Feeding and machine tool control Transformation of materials Remember the how material are transferred in to transfer the automation between machines (B1) 5 Introduction to Mechatronics Definition of Mechatronics Understanding of basics of Mechatronics (B2) 6 Role of various engineering disciplines in Importance of mechatronics Understanding of role of mechatronics in Mechatronics various applications (B2) 7 Mechatronics design elements Mechatronics elements Understand the what are the major elements in mechatronics 8 Scope of Mechatronics, Applications of Applications of Mechatronics Analyse the working of the washing machine , Mechatronics water level controller (B4) DEPARTMENT OF MECHANICAL ENGINEERING LECTURE 1 Introduction to Automation www.mrcet.ac.in TOPICS TO BE COVERED LECTURE 1 Introduction - Automation Definition of Automation Types of Automation Reasons for Automation Automation Strategies Pneumatic and Hydraulic components circuits DEPARTMENT OF MECHANICAL ENGINEERING AUTOMATION Definition: It is technology concerned with the application of Mechanical, electronic & computer-based systems to operate and control production in order to improves productions. DEPARTMENT OF MECHANICAL ENGINEERING If Includes: 1) Automated machine tools. 2) Automated assembly machines 3) Industrial robots. 4) Automated material handling & storages system 5) Automated inspection system for quality control 6) Feedback control & computer process control 7) Computer integrated system for planning, data collection decision making. DEPARTMENT OF MECHANICAL ENGINEERING TYPE OF AUTOMATION Automated production systems are classified into three basic types: 1) Fixed Automation 2) Programmable Automation 3) Flexible Automation DEPARTMENT OF MECHANICAL ENGINEERING FIXED AUTOMATION Fixed automation is a system in which the sequence of processing (or assembly) operations is fixed by the equipment configuration. The operations in the sequence are usually simple. It is the integration and coordination of many such operations into one piece of equipment that makes the system complex. The typical features of fixed automation are: High initial investment for custom-engineered equipment High production rates Relatively inflexible in accommodating product changes DEPARTMENT OF MECHANICAL ENGINEERING PROGRAMMABLE AUTOMATION In programmable automation, the production equipment is designed with the capability to change the sequence of operations to accommodate different product configurations. The operation sequence is controlled by a program, which is a set of instructions coded so that the system can read and interpret them. New programs can be prepared and entered into the equipment to produce new products. The typical features of programmable automation are: High investment in general-purpose equipment Low production rates relative to fixed automation Flexibility to deal with changes in product configuration Most suitable for batch production DEPARTMENT OF MECHANICAL ENGINEERING FLEXIBLE AUTOMATION The concept of flexible automation has developed only over the last 15 to 20 years, and the principles are still evolving. A flexible automated system is one that is capable of producing a variety of products (or parts) with virtually no time lost for changeovers from one product to the next. There is no production time lost while reprogramming the system and altering the physical setup (tooling, fixtures and machine settings). Consequently, the system can produce various combinations and schedules of products, instead of requiring that they be made in separate batches. The features of flexible automation can be summarized as follows: High investment for a custom-engineered system Continuous production of variable mixtures of products Medium production rates Flexibility to deal with product design variations DEPARTMENT OF MECHANICAL ENGINEERING REASONS FOR AUTOMATION Increased productivity due competition High cost of Labour Labour shortage Trend of Labour toward the sector Safety High cost of raw materials Improved Product Quality Reduced manufacturing Lead time Reduction of in process inventory High cost of not automation DEPARTMENT OF MECHANICAL ENGINEERING AUTOMATION STRATEGIES Specialization of operations Combined operations Simultaneous operations Integration of operations Increased flexibility Improved material handling and storage On- line inspection Process control & optimization Plan operations control Computer-integrated manufacturing (CIM) DEPARTMENT OF MECHANICAL ENGINEERING HYDRAULIC SYSTEM Hydraulic systems are power-transmitting assemblies employing pressurized liquid as a fluid for transmitting energy from an energy- generating source to an energy-using point to accomplish useful work DEPARTMENT OF MECHANICAL ENGINEERING BASIC COMPONENTS OF A HYDRAULIC SYSTEM Hydraulic actuator Hydraulic pump Valves External power supply (Motor) Reservoir Piping system Filters Pressure regulator regulates DEPARTMENT OF MECHANICAL ENGINEERING PNEUMATIC SYSTEM A pneumatic system carries power by employing compressed gas, generally air, as a fluid for transmitting energy from an energy-generating source to an energy-using point to accomplish useful work DEPARTMENT OF MECHANICAL ENGINEERING BASIC COMPONENTS OF A PNEUMATIC SYSTEM Pneumatic actuator Compressor Storage reservoir Valves External power supply (motor) Piping system DEPARTMENT OF MECHANICAL ENGINEERING COMPARISON BETWEEN HYDRAULIC AND PNEUMATIC SYSTEMS S. No. Hydraulic System Pneumatic System It employs a compressed gas, usually air, 1 It employs a pressurized liquid as a fluid as a fluid An oil hydraulic system operates at A pneumatic system usually operates at 2 pressures up to 700 bar 5–10 bar 3 Generally designed as closed system Usually designed as open system The system slows down when leakage 4 Leakage does not affect the system much occurs 5 Valve operations are difficult Valve operations are easy 6 Heavier in weight Lighter in weight Pumps are used to provide pressurized Compressors are used to provide 7 liquids compressed gases 8 The system is unsafe to fire hazards The system is free from fire hazards Special arrangements for lubrication are 9 Automatic lubrication is provided needed DEPARTMENT OF MECHANICAL ENGINEERING AUTOMATED FLOW LINES It consists of several machines or workstations which are linked together by work handling devices that transfer parts between the stations. The transfer of work parts occurs automatically and the workstations carry out their specialized functions automatically. The objectives of the use of flow line automation are, therefore: To reduce labor costs To increase production rates To reduce work-in-process To minimize distances moved between operations To achieve specialization of operations To achieve integration of operations DEPARTMENT OF MECHANICAL ENGINEERING TYPES OF FLOW LINES In-line type: The in-line configuration consists of a sequence of workstations in a more or less straight-line arrangement as shown in below Figure. An example of an in-line transfer machine used for metal cutting operations. DEPARTMENT OF MECHANICAL ENGINEERING Segmented in-line Type : The segmented in-line configuration consists of two or more straight line arrangement which are usually perpendicular to each other with L shaped or U shaped or rectangular shaped as shown in below Figure. The flow of work can take a few 90°turns, either for workpiece reorientation, factory layout limitations, or other reasons, and still qualify as a straight-line configuration. DEPARTMENT OF MECHANICAL ENGINEERING Rotary type: In the rotary configuration, the work parts are indexed around a circular table or dial. The workstations are stationary and usually located around the outside periphery of the dial. The parts ride on the rotating table and arc registered or positioned, in turn, at each station for its processing or assembly operation. This type of equipment is often referred to as an indexing machine or dial index machine and the configuration is shown in below DEPARTMENT OF MECHANICAL ENGINEERING METHODS OF WORK PART TRANSPORT The transfer mechanism of the automated flow line must not only move the partially completed work parts or assemblies between adjacent stations, it must also orient and locate the parts in the correct position for processing at each station. The general methods of transporting workpieces on flow lines can be classified into the following three categories: Continuous transfer Intermittent or synchronous transfer Asynchronous or power-and-free transfer DEPARTMENT OF MECHANICAL ENGINEERING TRANSFER MECHANISMS There are various types of transfer mechanisms used to move parts between stations. These mechanisms can be grouped into two types: 1) Linear transfer mechanisms 2) Rotary transfer mechanisms DEPARTMENT OF MECHANICAL ENGINEERING 1. Linear transfer mechanisms The commonly used linear transfer mechanisms are a) Walking beam transfer bar system, b) Powered roller conveyor system, and c) Chain-drive conveyor system. 2. Rotary transfer mechanisms There are several methods used to index a circular table or dial at various equal angular positions corresponding to workstation locations. a) Rack and pinion b) Ratchet and pawl c) Geneva mechanism d) CAM Mechanisms DEPARTMENT OF MECHANICAL ENGINEERING WALKING BEAM SYSTEMS Walking beam transfer mechanism, the work-parts are lifted up from their workstation locations by a transfer bar and moved one position ahead, to the next station. The transfer bar then lowers the pans into nests which position them more accurately for processing. For speed and accuracy, the motion of the beam is most often generated by a rotating camshaft powered by an electric motor or a roller movement in a profile powered by hydraulic cylinder. DEPARTMENT OF MECHANICAL ENGINEERING POWERED ROLLER CONVEYOR SYSTEM The conveyor can be used to move pans or pallets possessing flat riding surfaces. The rollers can be powered by either of two mechanisms. The first is a belt drive, in which a flat moving belt beneath the rollers provides the rotation of the rollers by friction. A chain drive is the second common mechanism used to power the rollers. Powered roller conveyors are versatile transfer systems because they can be used to divert work pallets into workstations or alternate tracks. DEPARTMENT OF MECHANICAL ENGINEERING CHAIN-DRIVE CONVEYOR SYSTEM In chain-drive conveyor system either a chain or a flexible steel belt is used to transport the work carriers. The chain is driven by pulleys in either an "over-and under" configuration, in which the pulleys turn about a horizontal axis, or an "around-the-corner" configuration, in which the pulleys rotate about a vertical axis. DEPARTMENT OF MECHANICAL ENGINEERING RACK AND PINION This mechanism is simple but is not considered especially suited to the high-speed operation often associated with indexing machines. The device is pictured in the below Figure and uses a piston to drive the rack, which causes the pinion gear and attached indexing table to rotate, A clutch or other device is used to provide rotation in the desired direction. DEPARTMENT OF MECHANICAL ENGINEERING RATCHET AND PAWL A ratchet is a device that allows linear or rotary motion in only one direction, while preventing motion in the opposite direction. Ratchets consist of a gearwheel and a pivoting spring-loaded finger called a pawl that engages the teeth. Either the teeth, or the pawl, are slanted at an angle, so that when the teeth are moving in one direction, the pawl slides up and over each tooth in turn, with the spring forcing it back with a 'click' into the depression before the next tooth. When the teeth are moving in the other direction, the angle of the pawl causes it to catch against a tooth and stop further motion in that direction. DEPARTMENT OF MECHANICAL ENGINEERING GENEVA MECHANISM The Geneva mechanism uses a continuously rotating driver to index the table, as pictured below. If the driven member has six slots for a six-station dial indexing machine, each turn of the driver will cause the table to advance one-sixth of a turn. The driver only causes movement of the table through a portion of its rotation. For a six-slotted driven member, 120° of a complete rotation of the driver is used to index the table. The other 240° is dwell. For a four slotted driven member, the ratio would be 90° for index and 270° for dwell. The usual number of indexing per revolution of the table is four, five, six, and eight. DEPARTMENT OF MECHANICAL ENGINEERING CAM MECHANISMS Various forms of cam mechanism, an example of which is illustrated in the below Figure, provide probably the most accurate and reliable method of indexing the dial. They are in widespread use in industry despite the fact that the cost is relatively high compared to alternative mechanisms. The cam can be designed to give a variety of velocity and dwell characteristics. DEPARTMENT OF MECHANICAL ENGINEERING CONTROL FUNCTIONS Controlling an automated flow line is a complex problem, owing to the sheer number of sequential steps that must be carried out. There are three main functions that are utilized to control the operation of an automatic transfer system. – The first of these is an operational requirement – The second is a safety requirement, and – The third is dedicated to improving quality. DEPARTMENT OF MECHANICAL ENGINEERING TOPICS TO BE COVERED LECTURE 2 Introduction - Mechatronics Definition of Mechatronics Role of various engineering disciplines in Mechatronics Mechatronics design elements Scope of Mechatronics Applications of Mechatronics DEPARTMENT OF MECHANICAL ENGINEERING INTRODUCTION Mechatronics is a concept of Japanese origin (1970’s). The term Mechatronics coined by “Tetsuro Mori”. Defined as the application of electronics and computer technology to control the motions of mechanical systems. DEPARTMENT OF MECHANICAL ENGINEERING INTRODUCTION It is a multidisciplinary approach to product and manufacturing system design. It involves application of electrical, mechanical, control and computer engineering to develop products, processes and systems with greater flexibility, ease in redesign and ability of reprogramming. DEPARTMENT OF MECHANICAL ENGINEERING EVALUATION OF MECHATRONICS: The technology has evolved through several stages that are termed as levels. The evolution levels of Mechatronics are: A. Primary level Mechatronics (first) B. Secondary level Mechatronics (second) C. Tertiary level Mechatronics (third) D. Quaternary level Mechatronics (fourth) DEPARTMENT OF MECHANICAL ENGINEERING DEPARTMENT OF MECHANICAL ENGINEERING ROLE OF VARIOUS ENGINEERING DISCIPLINES IN MECHATRONICS DEPARTMENT OF MECHANICAL ENGINEERING MECHATRONIC DESIGN ELEMENTS DEPARTMENT OF MECHANICAL ENGINEERING SCOPE OF MECHATRONICS Mechatronics plays a vital role in industrial sector. The scope of mechatronic in industrial sector is discussed as follows: Better design of products Better process planning Reliable and quality-oriented manufacturing.. Intelligent process control.. – Passive applications – Active applications DEPARTMENT OF MECHANICAL ENGINEERING GENERAL PARAMETERS FOR DESIGNING AN INTELLIGENT MECHATRONIC SYSTEM ARE AS FOLLOWS: Analyze product design and development specifications Select process variables, set points, processes, etc. Design proper analog and digital circuits Select mechanical components and devices Design proper mechanical system like hydraulic, pneumatic, etc. Select sensors, actuators and control components Design accurate and precise control system for various process variables Develop computer-based system (real time interfacing) Develop necessary computer software and database Integrate the above-stated parameters effectively Monitor the performance of designed system DEPARTMENT OF MECHANICAL ENGINEERING ADVANTAGES & DISADVANTAGES DEPARTMENT OF MECHANICAL ENGINEERING CHARACTERISTICS OF MECHATRONIC SYSTEM: 1. High quality product. 2. Safe. 3. Low cost. 4. Portable produced quickly 5. Serviceability, maintainability and upgradeability. DEPARTMENT OF MECHANICAL ENGINEERING REAL TIME APPLICATIONS DEPARTMENT OF MECHANICAL ENGINEERING DEPARTMENT OF MECHANICAL ENGINEERING THANK YOU www.mrcet.ac.in A U TO M AT I O N A N D CONTROL ENGINEERING (R17A0327) 4th Year B. Tech I- sem, Mechanical Engineering www.mrcet.ac.in COURSE OBJECTIVES UNIT - 1 CO1: To perform one or more processing operations & To understand the need of Mechatronics systems UNIT - 2 CO2: To make students familiar with the constructions and working principle of different types of sensors and transducers. UNIT - 3 CO3: Understand the fundamental concepts of electro mechanics and fluid mechanics (hydraulics and pneumatics) of Actuators and drive systems. UNIT - 4 CO4: To impart knowledge on the control elements UNIT - 5 CO5: To understand the different control schemes generally used to get best output. DEPARTMENT OF MECHANICAL ENGINEERING UNIT 2 SENSORS AND TRANSDUCERS CO2: To make students familiar with the constructions and working principle of different types of sensors and transducers. www.mrcet.ac.in UNIT – II (SYLLABUS) INTRODUCTION TO SENSORS AND TRANSDUCERS Performance terminology, Displacement Sensors, Position and Proximity Sensors Velocity and Motion Sensors Force and Fluid pressure Sensors Liquid flow and Liquid level Sensors Temperature and light sensors Selection of sensors. DEPARTMENT OF MECHANICAL ENGINEERING COURSE OUTLINE UNIT -2 LECTURE LECTURE TOPIC KEY ELEMENTS LEARNING OBJECTIVES 1 Introduction to Sensors and transducers, Definition of Sensors and Understanding of basics of Sensors and performance terminology transducers transducers (B2) 2 Displacement sensors Working principle of Displacement sensors 3 Position and proximity sensors Working principle of Position and proximity sensors 4 Velocity and motion sensors Working principle of Velocity and motion sensors Understand the applications of sensors 5 Force, fluid pressure sensors Working principle of Force, in various systems and to know the fluid pressure sensors functions of each element(B2) 6 Liquid flow, liquid level sensors Working principle of Liquid flow, liquid level sensors 7 Temperature, light sensors, selection of Working principle of sensors. Temperature, light sensors, selection of sensors. DEPARTMENT OF MECHANICAL ENGINEERING LECTURE 1 INTRODUCTION TO SENSORS AND TRANSDUCERS www.mrcet.ac.in TOPICS TO BE COVERED LECTURE 1 o Introduction - Sensors And Introduction - Sensors And Transducers Transducers o Performance terminology, o Displacement Sensors, o Position and Proximity Sensors o Velocity and Motion Sensors o Force and Fluid pressure Sensors o Liquid flow and Liquid level Sensors o Temperature and light sensors o Selection of sensors. DEPARTMENT OF MECHANICAL ENGINEERING SENSORS Sensor is an element which produces a signal relating to the quantity being measured. An input device which provides an output (signal) with respect to a specific physical quantity. A device that converts signals from one energy domain to electrical domain. DEPARTMENT OF MECHANICAL ENGINEERING SENSORS DEPARTMENT OF MECHANICAL ENGINEERING TRANSDUCER A device that converts variations in a physical quantity, such as pressure or brightness, into an electrical signal, or vice versa. A transducer is an electronic device that converts energy from one form to another. E.g. microphones, loudspeakers, thermometers, position and pressure sensors, and antenna DEPARTMENT OF MECHANICAL ENGINEERING SENSORS OR TRANSDUCERS ARE USED IN MECHATRONICS FOR THE FOLLOWING PURPOSES: To provide position, velocity, and acceleration information of the measuring element in a system which provides feedback information To act as protective mechanism for a system To help eliminate mechanically complex and expensive feeding and sorting devices To provide identification and indication of the presence of different components To provide real time information concerning the nature of the task being performed DEPARTMENT OF MECHANICAL ENGINEERING PERFORMANCE TERMINOLOGY Transducers or measurement systems are not perfect systems. Mechatronics design engineer must know the capability and shortcoming of a transducer or measurement system to properly assess its performance. There are a number of performance related parameters of a transducer or measurement system. These parameters are called as sensor specifications. Sensor specifications inform the user to the about deviations from the ideal behaviour of the sensors. DEPARTMENT OF MECHANICAL ENGINEERING PERFORMANCE TERMINOLOGY Static Characteristics Dynamic Characteristics – Range and Span – Response Time – Error – Time Constant – Accuracy – Rise Time – Sensitivity – Settling Time – Hysteresis error – Repeatability – Reliability – Stability – Drift – Dead band – Dead time – Resolution – Backlash DEPARTMENT OF MECHANICAL ENGINEERING CLASSIFICATION OF SENSOR /TRANSDUCER Sensors are classified in the following ways. According to the power supply – Active type – Passive type According to the mode of operation – Null type – Deflection type According to the signal characteristics (or) output – Analog – Coded type – Digital type – Frequency type DEPARTMENT OF MECHANICAL ENGINEERING CLASSIFICATION OF SENSOR /TRANSDUCER According to the measurement (or) Function – Displacement – Velocity – Acceleration According to the performance characteristics – Dimensional – Accuracy – Mass – Repeatability – Force – Linearity – Sensitivity – Proximity – Range – Pressure – Fluid Flow – Liquid level – Temperature DEPARTMENT OF MECHANICAL ENGINEERING LECTURE 2 DISPLACEMENT SENSORS www.mrcet.ac.in DISPLACEMENT SENSORS The following are examples of commonly used displacement sensors. 1. Potentiometer 2. Strain gauge 3. Capacitive sensors 4. Linear variable differential transformer DEPARTMENT OF MECHANICAL ENGINEERING POTENTIOMETER Linear or Rotary potentiometer is a variable resistance displacement transducer which uses the variable resistance transduction principle in which the displacement or rotation is converted into a potential difference due to the movement of sliding contact over a resistive element. Vout = {R2/ (R1+R2)} x V; DEPARTMENT OF MECHANICAL ENGINEERING ADVANTAGES AND DISADVANTAGES Advantages Disadvantages Less expensive Slow Dynamic Response Different sizes and shapes of potentiometers in different ranges Low Resolution are easily available Early wear of the wiper is possible High output Noisy output under high speed A.C Excitation operation or high vibrating Rugged Construction conditions Less sensitive towards vibration Noise becomes too high when the and temperature slide velocity exceeds 3 m/sec High electrical efficiency Operation is simple DEPARTMENT OF MECHANICAL ENGINEERING STRAIN GAUGE Strain gauge: it is an electrical conductor whose resistance changes as it is strained. Structure of Strain Gauges There are many types of strain gauges. Among them, a universal strain gauge has a structure such that a grid-shaped sensing element of thin metallic resistive foil (3 to 6μm thick) is put on a base of thin plastic film (15 to 16μm thick) and is laminated with a thin film. DEPARTMENT OF MECHANICAL ENGINEERING PRINCIPLE OF STRAIN GAUGES The strain gauge is tightly bonded to a measuring object so that the sensing element (metallic resistive foil) may elongate or contract according to the strain borne by the measuring object. When bearing mechanical elongation or contraction, most metals undergo a change in electric resistance. The strain gage applies this principle to strain measurement through the resistance change. Generally, the sensing element of the strain gage is made of a copper-nickel alloy foil. The alloy foil has a rate of resistance change proportional to strain with a certain constant. DEPARTMENT OF MECHANICAL ENGINEERING CAPACITIVE SENSORS Capacitive sensor is of non-contact type sensor and is primarily used to measure the linear displacements from few millimeters to hundreds of millimeters. It comprises of three plates, with the upper pair forming one capacitor and the lower pair another. The linear displacement might take in two forms: one of the plates is moved by the displacement so that the plate separation changes area of overlap changes due to the displacement. DEPARTMENT OF MECHANICAL ENGINEERING The capacitance C of a parallel plate capacitor is given by, C = (εr εo A ) / d Where εr is the relative permittivity of the dielectric between the plates, εo permittivity of free space, A area of overlap between two plates and d the plate separation. DEPARTMENT OF MECHANICAL ENGINEERING APPLICATIONS Feed hopper level monitoring Small vessel pump control Grease level monitoring Level control of liquids Metrology applications to measure shape errors in the part being produced to analyze and optimize the rotation of spindles in various machine tools such as surface grinders, lathes, milling machines, and air bearing spindles by measuring errors in the machine tools themselves Assembly line testing o to test assembled parts for uniformity, thickness or other design features to detect the presence or absence of a certain component, such as glue etc. DEPARTMENT OF MECHANICAL ENGINEERING LINEAR VARIABLE DIFFERENTIAL TRANSFORMER Definition of LVDT The term LVDT stands for the Linear Variable Differential Transformer. It is the most widely used inductive transducer that converts the linear motion into the electrical signal. The output across secondary of this transformer is the differential thus it is called so. It is very accurate inductive transducer as compared to other inductive transducers. DEPARTMENT OF MECHANICAL ENGINEERING WORKING PRINCIPLE OF LVDT Now three cases arise according to the locations of core which explains the working of LVDT are discussed below as, CASE-I: When the core is at null position (for no displacement) When the core is at null position then the flux linking with both the secondary windings is equal so the induced emf is equal in both the windings. So, for no displacement the value of output eout is zero as e1 and e2 both are equal. So, it shows that no displacement took place. DEPARTMENT OF MECHANICAL ENGINEERING CASE-II: When the core is moved to upward of null position (For displacement to the upward of reference point) In this case the flux linking with secondary winding S1 is more as compared to flux linking with S2. Due to this e1 will be more as that of e2. Due to this output voltage eout is positive. CASE-III: When the core is moved to downward of Null position (for displacement to the downward of the reference point). In this case magnitude of e2 will be more as that of e1. Due to this output eout will be negative and shows the output to downward of the reference point. DEPARTMENT OF MECHANICAL ENGINEERING OUTPUT VS CORE DISPLACEMENT A linear curve shows that output voltage varies linearly with displacement of core. DEPARTMENT OF MECHANICAL ENGINEERING ADVANTAGES OF LVDT High Range No Frictional Losses High Input and High Sensitivity Low Hysteresis Low Power Consumption. Direct Conversion to Electrical Signals DEPARTMENT OF MECHANICAL ENGINEERING DISADVANTAGES LVDT is sensitive to stray magnetic fields so it always requires a setup to protect them from stray magnetic fields. LVDT gets affected by vibrations and temperature. Applications of LVDT We use LVDT in the applications where displacements to be measured are ranging from a fraction of mm to few cms. The LVDT acting as a primary transducer converts the displacement to electrical signal directly. The LVDT can also act as a secondary transducer. E.g. the Bourbon tube which acts as a primary transducer and it converts pressure into linear displacement and then LVDT coverts this displacement into an electrical signal which after calibration gives the readings of the pressure of fluid. DEPARTMENT OF MECHANICAL ENGINEERING LECTURE 3 Position and Proximity Sensors www.mrcet.ac.in POSITION SENSORS Position sensors are basically sensors for measuring the distance travelled by the body starting from its reference position. How far the body has moved from its reference or initial position is sensed by the position sensors and often the output is given as a fed back to the control system which takes the appropriate action. Motion of the body can be rectilinear or curvilinear; accordingly, position sensors are called linear position sensors or angular position sensors. 1. Photoelectric Sensors 2. Hall effect Sensors 3. Digital Optical Encoder DEPARTMENT OF MECHANICAL ENGINEERING PHOTOELECTRIC SENSORS Photoelectric sensor is a generic name for sensors which detect an object by using light. The optical signal transmitted from the emitting part of the sensor is modified by being reflected, transmitted, absorbed, etc., by the sensing object and is then detected by the receiving part of the sensor to generate a corresponding output signal. Further, it can also be a sensor which detects light radiated from the sensing object to generate an output signal. Sensing Methods or Working Principle of Photoelectric Proximity Sensor There are three main sensing methods of the photoelectric proximity sensor and they are, 1. Through beam method 2. Retro-reflective method 3. Diffuse or Reflective method DEPARTMENT OF MECHANICAL ENGINEERING Through beam method Retro-reflective method Diffuse or Reflective method DEPARTMENT OF MECHANICAL ENGINEERING ADVANTAGES OF PHOTOELECTRIC SENSOR The sensor senses all kinds of materials. It has longer life, long sensing range and very reliability. Very fast response time and less costly. Diffuse photoelectric sensor detects small objects including color mark and label detection. mostly retro-reflective type sensor can detect transparent objects. Through beam type can detect long range and it is tolerant of dirty environment. DEPARTMENT OF MECHANICAL ENGINEERING DISADVANTAGES OF PHOTOELECTRIC SENSOR Over coarse of time lens get contaminated. Generally, the sensing range is affected due to color and reflectivity of the target. Through beam type requires transmitter (Tx) and receiver (Rx) at two separate locations Retro reflective type requires reflector in addition to Tx/Rx. This makes system installation complex DEPARTMENT OF MECHANICAL ENGINEERING HALL EFFECT SENSORS A Hall effect sensor is a device that is used to measure the magnitude of a magnetic field. Its output voltage is directly proportional to the magnetic field strength through it. Hall effect sensors are used for proximity sensing, positioning, speed detection, and current sensing applications Principle When a beam of charged particles passes through a magnetic field, forces act on the particles and the beam is deflected from its straight line path. This effect was discovered by E.R. Hall in 1879 and is called the Hall effect. DEPARTMENT OF MECHANICAL ENGINEERING WORKING Consider electrons moving in a conductive plate with a magnetic field applied at right angles to the plane of the plate. As a result of the magnetic field, the moving electrons are deflected to one side of the plate, and that side becomes negatively charged, while the opposite side becomes positively charged since the electrons are directed away from it. This charge separation produces an electric field in the material. The charge separation continues until the forces on the charged particles from the electric field just balance the forces produced by the magnetic field. DEPARTMENT OF MECHANICAL ENGINEERING HALL EFFECT SENSORS The result is a transverse potential difference V given by DEPARTMENT OF MECHANICAL ENGINEERING ADVANTAGES OF HALL EFFECT SENSORS They can be used for multiple sensor functions like position sensing, speed sensing as well as for sensing the direction of movement too. As they are solid state devices, there is absolutely no wear and tear due to absence of moving parts. They are almost maintenance free. They are robust. They are immune to vibration, dust and water. DEPARTMENT OF MECHANICAL ENGINEERING DISADVANTAGES OF HALL EFFECT SENSORS They are not capable to measure current flow at a distance more than 10 cm. The only solution to overcome this issue is to use a very strong magnet that can generate a wide magnetic field. Accuracy of the measured value is always a concern as external magnetic fields may affect the values. High Temperature affects the conductor resistance. This will in turn affect the charge carrier’s mobility and sensitivity of Hall Effect Sensors. DEPARTMENT OF MECHANICAL ENGINEERING DIGITAL OPTICAL ENCODER: A digital optical encoder is a device that converts motion into a sequence of digital pulses. By counting or decoding these bits and the pulses can be converted into relative or absolute position measurements. Encoders are in Rotary, linear configurations. The Rotary encoders are in two forms. 1. Absolute encoder 2. Incremental encoder. DEPARTMENT OF MECHANICAL ENGINEERING ABSOLUTE ENCODER The absolute encoder is designed to produce a digital word that distinguishes ‘ N’ distinct positions of the shaft. The rotating disc has four concentric circles of slots and four sensors to detect the light pulses. The slots are arranged in such a way that the output is made in the binary code. The number of bits in the binary number will be equal to the number of tracks. The most common types of numerical encoding used in the absolute encoder are gray and natural binary codes. DEPARTMENT OF MECHANICAL ENGINEERING INCREMENTAL ENCODER: A beam of light passes through the slots in a disc and it is detected by a suitable light sensor. When the disc is rotated, the output is shown in terms of pulses and these pulses being proportional to the angle of disc rotation. So the angular position of the disc is determined by the number of pulses produced. The inner track has just one hole and other two tracks have a series of equally spaced holes. The angle is determined by the number slots on the disc. DEPARTMENT OF MECHANICAL ENGINEERING PROXIMITY SENSOR A proximity sensor is a sensor able to detect the presence of nearby objects without any physical contact. Common applications for proximity sensors and limit switches include: 1. Counting moving objects; 2. Limiting the traverse of a mechanism. DEPARTMENT OF MECHANICAL ENGINEERING EDDY CURRENT PROXIMITY SENSORS When a coil is supplied with an alternating current an alternating magnetic field is produced. If there is a metal object in close proximity to this attending magnetic field, then eddy currents are induced in it. The eddy currents themselves produce a magnetic field which distorts the magnetic field responsible for their production. Consequently, the impedance of the coil changes and so the amplitude of the alternating current. This change, at some preset level, can be used to trigger a switch. DEPARTMENT OF MECHANICAL ENGINEERING CAPACITIVE PROXIMITY SENSORS DEPARTMENT OF MECHANICAL ENGINEERING PROXIMITY SWITCH’S A proximity sensor is a sensor able to detect the presence of nearby objects without any physical contact. The microswitch is a small electrical switch which requires physical contact and a small operating force to close the contacts. For example: A conveyor belt. DEPARTMENT OF MECHANICAL ENGINEERING PRINCIPLE OF WORKING OF PROXIMITY SWITCHES It consists of two magnetic switch contacts sealed in a glass tube. When a magnet is brought close to the switch, the magnetic reeds are attracted to each other and close the switch contacts. DEPARTMENT OF MECHANICAL ENGINEERING PNEUMATIC PROXIMITY SENSOR DEPARTMENT OF MECHANICAL ENGINEERING LECTURE 4 VELOCITY AND MOTION SENSORS www.mrcet.ac.in VELOCITY SENSORS Velocity sensors or tachogenerators are devices that give an output proportional to angular velocity. These sensors find wide application in motor speed control systems. Tachogenerator Pyroelectric sensors Strain Gauge as force Sensor DEPARTMENT OF MECHANICAL ENGINEERING TACHOGENERATOR If the wheel contains n teeth and rotates with an angular velocity ɷ, then the flux change with time for the coil can be considered to be of the form The induced e.m.f. e in the N turns of the pick-up coil is -N dΦ / dt and thus DEPARTMENT OF MECHANICAL ENGINEERING PYROELECTRIC SENSORS These sensors work on the principle of pyroelectricity, which states that a crystal material such as Lithium tantalite generates charge in response to heat flow. DEPARTMENT OF MECHANICAL ENGINEERING APPLICATIONS OF PYROELECTRIC SENSORS Intrusion detector Optothermal detector Pollution detector Position sensor Solar cell studies Engine analysis DEPARTMENT OF MECHANICAL ENGINEERING LECTURE 5 FORCE AND FLUID PRESSURE SENSORS www.mrcet.ac.in STRAIN GAUGE AS FORCE SENSOR DEPARTMENT OF MECHANICAL ENGINEERING PRESSURE SENSORS The devices which are used to monitor fluid pressure in industrial processes is diaphragms, bellows, capsules and tubes. The types of pressure measurements required are (1) Absolute pressure measurement, (2) Differential pressure measurements. In absolute pressure measurements the measurement is related to vacuum pressure (zero pressure) and in differential pressure measurement the difference in pressure is measured. DEPARTMENT OF MECHANICAL ENGINEERING DIAPHRAGM When the pressure, which is to be measured, is applied through the pressure inlet, the deflection of metallic diaphragm takes place. This deflection is applied to a pointer through spring or proper mechanism arrangement, due to which the pointer slides over the calibrated scale. The reading is indicated by indicating or recording instrument, which is proportional to the applied pressure. DEPARTMENT OF MECHANICAL ENGINEERING BOURDON TUBE When the pressure is applied at the open end, the tube tends to straighten out because the internal and outer radii of the bourdon tube are different. So the tube takes different areas for the pressure. The non-linear motion is converted into linear motion or displacement by means of a pointer and calibrated scale (deflection) arrangement. Necessary link, lever gear and pinion attachment is provided to the deflection system. Thus the applied pressure is measured by means of deflection over linear scale. DEPARTMENT OF MECHANICAL ENGINEERING BELLOWS As the pressure is applied to the spring-loaded metal bellows, it gets compressed and hence forces the lower end of the bellow in upward direction. This results in opposing the spring force. The pointer is connected to the spring through suitable linkage and calibration. When pressure is applied in vertical movement, the pointer moves over the calibrated scale. DEPARTMENT OF MECHANICAL ENGINEERING PIEZOELECTRIC SENSORS The electrical circuit for a piezo electric sensor is a charge generator in parallel with capacitance Cs and in parallel with Resistance Rs. The effective circuit is as shown by the Fig. when the sensor is connected via a cable of capacitance C and resistance RA. The sensor is charged subject to pressure change and the capacitor will discharge with time. The discharge time depends on the time constant of the circuit. DEPARTMENT OF MECHANICAL ENGINEERING TACTILE SENSOR There are two layers of such film is used and it is separated by a soft film which transmits vibrations. The alternating voltage is supplied in the lower PVDF film and this results in mechanical oscillations of the film. The intermediate film transmits these vibrations to the upper PVDF film. Due to the piezoelectric effect the vibrations formed are cause an alternating voltage to be produced across the upper film. So the pressure is applied to the upper PVDF film and its vibrations are affected the output voltage. DEPARTMENT OF MECHANICAL ENGINEERING LECTURE 6 LIQUID FLOW AND LIQUID LEVEL SENSORS www.mrcet.ac.in LIQUID FLOW SENSORS There are many devices used to measure the liquid flow. The basic principle in measuring flow is the fluid flowing through the pipe per second is proportional to square root of pressure difference. The following flow measuring devices are used to measure the liquid flow. 1. Orifice plate 2. Turbine meter DEPARTMENT OF MECHANICAL ENGINEERING ORIFICE PLATE The orifice plate is simply a disc, with a central hole, which is placed in the tube through which the fluid is flowing. The pressure differences is measured between a point equal to the diameter of the tube upstream and a point equal to half the diameter downstream. The orifice plate is simple, cheap, with no moving parts, and is widely used. It does not, however, work well with slurries. The accuracy is typically about ±1.5% of full range, it is non-linear, and it does produce quite an appreciable pressure loss in the system to which it is connected. DEPARTMENT OF MECHANICAL ENGINEERING TURBINE METER The turbine flowmeter consists of a multi-bladed rotor that is supported centrally in the pipe along which the flow occurs. The fluid flow results in rotation of the rotor, the angular velocity being approximately proportional to the flow rate. The rate of revolution of the rotor can be determined using a magnetic pick-up. The pulses are counted and so the number of revolutions of the rotor can be determined. The meter is expensive with an accuracy of typically about ±0.3%. DEPARTMENT OF MECHANICAL ENGINEERING LEVEL MEASUREMENT Liquid level measurement is an important and the oldest function in measurements. It is widely useful in power plants, petrochemical, paper and sugar industries. It is also useful for level measurement of exotic and hazardous process matters, fuel handling and so on. The liquid level affects pressure and rate of flow in and out of a container or vessel, due to which it is necessary to measure and control liquid levels. The service of level measurements is applicable for both solid and liquid materials or any process material. But the most important factor is to consider the nature and type of material. DEPARTMENT OF MECHANICAL ENGINEERING BUBBLER METHOD DEPARTMENT OF MECHANICAL ENGINEERING LIQUID LEVEL MEASUREMENT USING FLOAT DEPARTMENT OF MECHANICAL ENGINEERING LASER LEVEL SENSOR OR LEVEL MEASUREMENT USING LASER DEPARTMENT OF MECHANICAL ENGINEERING ULTRASONIC LIQUID LEVEL DETECTOR DEPARTMENT OF MECHANICAL ENGINEERING LECTURE 7 Temperature, light sensors, selection of sensors. www.mrcet.ac.in TEMPERATURE SENSORS The term temperature is defined as the degree of hotness or coldness of a substance or medium. Temperature may be defined as degree of heat. Due to heating or cooling, the following effects are used for measurement: i. Change in physical or chemical state of the substance or medium ii. Change in physical dimensions iii. Change in electrical properties such as resistance iv. If two dissimilar metals get joined or welded, an emf gets developed at the junction. v. Change in the intensity of total radiation emitted. DEPARTMENT OF MECHANICAL ENGINEERING THERMOCOUPLE A thermocouple works on the following principle: When two dissimilar metals A and B are welded or joined together to form a closed circuit and the junctions (J1 and J2) are kept at two different temperatures (T1 and T2), then an emf is generated resulting flow of current in the circuit or loop." One of the two junctions in the loop is reference or cold junction which is generally kept at 0°C and the other is the measuring or hot junction at which the temperature is to be measured as shown in Figure. DEPARTMENT OF MECHANICAL ENGINEERING RESISTANCE TEMPERATURE DETECTOR (RTD) DEPARTMENT OF MECHANICAL ENGINEERING BIMETALLIC THERMOMETERS DEPARTMENT OF MECHANICAL ENGINEERING LIGHT SENSORS Light Sensors are photoelectric devices / Photo sensors that convert light energy (photons) whether visible or infra-red light into an electrical signal. DEPARTMENT OF MECHANICAL ENGINEERING PHOTODIODES Are semiconductor junction, connected into a circuit in reverse bias giving a very high resistance. With no incident light, the reverse current is almost negligible and is termed the dark current. When light falls on the junction, extra hole– electron pairs are produced and there is an increase in the reverse current and the diode resistance drops. The reverse current is very nearly proportional to the intensity of the light. DEPARTMENT OF MECHANICAL ENGINEERING PHOTOTRANSISTORS The phototransistors have a light-sensitive collector–base p–n junction. When there is no incident light there is a very small collector-to-emitter current. When light is incident, a base current is produced that is directly proportional to the light intensity. This leads to the production of a collector current which is a measure of the light intensity. Phototransistor are connected in a Darlington arrangement with a conventional transistor, for higher current gain. DEPARTMENT OF MECHANICAL ENGINEERING PHOTORESISTOR A photoresistor (or light-dependent resistor, LDR, or photo-conductive cell) is a light-controlled variable resistor. The resistance of a photoresistor decreases with increasing incident light intensity (photoconductivity). DEPARTMENT OF MECHANICAL ENGINEERING SELECTION OF SENSORS The nature of output required from the sensor. The nature of measurement required. The accuracy of the sensor. The cost of the sensor. The power requirement of the sensor. The speed response of the sensor. The linearity of the sensor. The Reliability and Maintainability of the sensor. Environmental conditions under which the measurement is to be made. Signal conditioning requirements. The nominal and range of values of the sensor. Suitable output signals from the measurement. DEPARTMENT OF MECHANICAL ENGINEERING THANK YOU www.mrcet.ac.in A U TO M AT I O N A N D CONTROL ENGINEERING (R17A0327) 4th Year B. Tech I- sem, Mechanical Engineering www.mrcet.ac.in COURSE OBJECTIVES UNIT - 1 CO1: To perform one or more processing operations & To understand the need of Mechatronics systems UNIT - 2 CO2: To make students familiar with the constructions and working principle of different types of sensors and transducers. UNIT - 3 CO3: Understand the fundamental concepts of electro mechanics and fluid mechanics (hydraulics and pneumatics) of Actuators and drive systems. UNIT - 4 CO4: To impart knowledge on the control elements UNIT - 5 CO5: To understand the different control schemes generally used to get best output. DEPARTMENT OF MECHANICAL ENGINEERING UNIT 3 A C T U AT O R S A N D DRIVE SYSTEMS CO3: Understand the fundamental concepts of electro mechanics and fluid mechanics (hydraulics and pneumatics) of Actuators and drive systems. www.mrcet.ac.in UNIT – III (SYLLABUS) ACTUATORS AND DRIVE SYSTEMS Mechanical, Electrical, Hydraulic drive systems Characteristics mechanical, electrical, hydraulic and pneumatic actuators and their limitations. DEPARTMENT OF MECHANICAL ENGINEERING COURSE OUTLINE UNIT - 3 LECTURE LECTURE TOPIC KEY ELEMENTS LEARNING OBJECTIVES 1 Introduction to Actuators Define Actuator Understanding of basics of control system (B2) 2 Classification of Actuators Electric Motors like: Servomotors, Stepper motors or Direct-drive electric Types of Actuators Understanding of types of Actuators (B2) Hydraulic actuators Pneumatic actuators 3 Drive Systems Understand the applications of Drive systems and to know the working Working principle of Types of 4 Types of Drive systems principles of system(B2) Drive systems Advantages and disadvantages of Drive systems(B4) DEPARTMENT OF MECHANICAL ENGINEERING TOPICS TO BE COVERED LECTURE 1 Definition Introduction - Actuators Types of Actuators Advantages and Disadvantages Drive Systems Applications Problems Assignments DEPARTMENT OF MECHANICAL ENGINEERING LECTURE TEMPLATE – Introduction Definition Units Classification etc… – Demonstration Text Graphic/ Pictorial Video etc… – Industrial Applications – Solved Problems (1-2) Procedure – Self Learning Questions – Assignment Exercises – Summary DEPARTMENT OF MECHANICAL ENGINEERING Actuators www.mrcet.ac.in User Environment External Programming Sensors and Supervision Sensors Interns Control Unit Actuators Mechanical Structure DEPARTMENT OF MECHANICAL ENGINEERING ACTUATORS 1 – Pneumatic actuators Cylinders 2 – Hydraulic actuadors Cylinders Motors 3 – Electrical actuators Dc motors. Ac motors Steeper motors. DEPARTMENT OF MECHANICAL ENGINEERING 1 – Pneumatic actuators (cylinders) Double effect pneumatic cylinders F = P* S DEPARTMENT OF MECHANICAL ENGINEERING V v a F = P* S F - Ff = M * a P * S - k * v2 a = Ff = k * v2 M Speed is not controllable. The cylinder maximum speed is achieved when friction forces (kv2) equal those that produce DEPARTMENTthe advancing OF MECHANICAL movement (F = P.S), and a = 0. ENGINEERING V v a - The impact produced when reaching the end of the run is reduced usingDEPARTMENT a shock absorber. OF MECHANICAL ENGINEERING Electrical valve - Electrical valve: the hydraulic-electrical interface DEPARTMENT OF MECHANICAL ENGINEERING DEPARTMENT OF MECHANICAL ENGINEERING DEPARTMENT OF MECHANICAL ENGINEERING Distributor DEPARTMENT OF MECHANICAL ENGINEERING Double effect cylinders Single effect cylinders DEPARTMENT OF MECHANICAL ENGINEERING Example of commercial pneumatic cylinders (Lateral guides to prevent axial rotation ) DEPARTMENT OF MECHANICAL ENGINEERING Oval pistons to prevent the rotation of the axis avoiding the need of auxiliary guides DEPARTMENT OF MECHANICAL ENGINEERING l 2 l Classical cylinders drawbacks: a displacement of length l requires an additional length l. DEPARTMENT OF MECHANICAL ENGINEERING Dl l Solutions to reduce the occupied space DEPARTMENT OF MECHANICAL ENGINEERING Movement transmission Adjusting band Shock-absorber adjustment Cylinder’s sleeve Adjusting band Piston DEPARTMENT OF MECHANICAL ENGINEERING DEPARTMENT OF MECHANICAL ENGINEERING Pneumatic actuators (cylinders) - Economic - Reliable - High operation speed - Operation at constant force - Resistant to overloads - No speed control - Poor position speed - Noisy operation DEPARTMENT OF MECHANICAL ENGINEERING Example of pneumatic manipulator, and its mechanical states (End positions of all its cylinders) DEPARTMENT OF MECHANICAL ENGINEERING ACTUATORS 1 – Pneumatic actuators Cylinders Motors 2 – Hydraulic actuadors Cylinders Motors 3 – Electrical actuators Dc motors. Ac motors Steeper motors. DEPARTMENT OF MECHANICAL ENGINEERING 2 – Hydraulic actuators (cylinders) Dv (cm3) Q (l / min) Dl (cm) v (cm/seg.) Energy source: oil pressurized between 20 and 300 bars. F = P* S If P ^^ F ∞ - Controllable position - Controllable speed DEPARTMENT OF MECHANICAL ENGINEERING Control Electrical valve P R Pressure M regulator Pressure B Refrigeration Level Temperature Hydraulic circuit showing its essential elements DEPARTMENT OF MECHANICAL ENGINEERING At m. The regulation of the cylinder retention force P regulates the oil output producing a pressure drop. Schema of a pressure regulator DEPARTMENT OF MECHANICAL ENGINEERING QA d Control Electrical P R valve QB Ideal characteristic R A P B R d DEPARTMENT OF MECHANICAL ENGINEERING QA d Control Electrical P R valve QB R A P B R d DEPARTMENT OF MECHANICAL ENGINEERING QA d Control Electrical P R valve QB R A P B R d DEPARTMENT OF MECHANICAL ENGINEERING QA d Control P R Electrical QB valve Real characteristic R A P B R d DEPARTMENT OF MECHANICAL ENGINEERING QA QB Control Sensor Servo valve P R Set point Control A Q A QB Qo B Sensor d The use of a position sensor d makes the position servo control possible and thus hysteresis is minimized. The dead zone is minimized as well. DEPARTMENT OF MECHANICAL ENGINEERING ACTUATORS 1 – Pneumatic actuators Cylinders Motors 2 – Hydraulic actuadors Cylinders Motors 3 – Electrical actuators Dc motors. Ac motors Steeper motors. DEPARTMENT OF MECHANICAL ENGINEERING Hydraulic pumps and motors ( Kind of gears) Fix caudal DEPARTMENT OF MECHANICAL ENGINEERING Hydraulic pumps and motors ( Kind of gears) Fix caudal DEPARTMENT OF MECHANICAL ENGINEERING Hydraulic pumps ( Kind of radial pistons) Cylindrical pumps Variable caudal DEPARTMENT OF MECHANICAL ENGINEERING e e Caudal variation as a function of eccentricity e DEPARTMENT OF MECHANICAL ENGINEERING Hydraulic pumps and motors ( Kind of blades) DEPARTMENT OF MECHANICAL ENGINEERING Hydraulic pumps or motors DEPARTMENT OF MECHANICAL ENGINEERING Hydraulic actuators - Economic - Reliable - Able to support heavy loads - Resistant to overloads - Low working speed - Hydraulic group noisy in operation - Possible oil leakage DEPARTMENT OF MECHANICAL ENGINEERING INDUSTRIAL APPLICATIONS They are used in a wide range of industries where linear positioning is needed. The actuators are driven by several means including ball or lead screws, belts, or voice coils, among others. Typical applications include opening and closing dampers, locking doors, braking machine motions, etc. Link:https://www.kerryactuator.com/seven-types-of-actuators-for- industrial-applications DEPARTMENT OF MECHANICAL ENGINEERING SELF LEARNING QUESTIONS 1. Explain about types of Actuators 2. Explain about types of Drive systems 3. Explain the advantages and disadvantages of Drive systems DEPARTMENT OF MECHANICAL ENGINEERING ASSIGNMENT EXERCISES 1. Define Actuator? Explain types of Actuators? 2. Explain about Hydraulic and Pneumatic Actuators? 3. Explain about different Drive systems? 4. Explain the characteristics of different drive systems? 5. What are the Limitations of different drive systems? DEPARTMENT OF MECHANICAL ENGINEERING THANK YOU www.mrcet.ac.in A U TO M AT I O N A N D CONTROL ENGINEERING (R17A0327) 4th Year B. Tech I- sem, Mechanical Engineering www.mrcet.ac.in COURSE OBJECTIVES UNIT - 1 CO1: To perform one or more processing operations & To understand the need of Mechatronics systems UNIT - 2 CO2: To make students familiar with the constructions and working principle of different types of sensors and transducers. UNIT - 3 CO3: Understand the fundamental concepts of electro mechanics and fluid mechanics (hydraulics and pneumatics) of Actuators and drive systems. UNIT - 4 CO4: To impart knowledge on the control elements UNIT - 5 CO5: To understand the different control schemes generally used to get best output. DEPARTMENT OF MECHANICAL ENGINEERING UNIT 4 CONTROL SYSTEM COMPONENTS CO4: To impart knowledge on the control elements www.mrcet.ac.in UNIT – IV (SYLLABUS) Control system components Introduction, classification of control system- classification of control systems on the basis of control signal used, Adaptive control system, Process control systems DEPARTMENT OF MECHANICAL ENGINEERING COURSE OUTLINE UNIT - 4 LECTURE LECTURE TOPIC KEY ELEMENTS LEARNING OBJECTIVES 1 Introduction to control system Define control system Understanding of basics of control system (B2) 2 Classification of control system - Open and closed loop control system - Linear and Non-linear control system - Continuous time and discrete time Understanding of types of control systems Types of control system control system (B2) - Lumped and distributed parameter control system 3 Adaptive control system Understand the applications of control systems in various systems 4 Process control systems Working principle of Types of and to know the functions of each control systems element(B2) Analyze the control system in machines (B4) DEPARTMENT OF MECHANICAL ENGINEERING LECTURE 1 Introduction to control system www.mrcet.ac.in TOPICS TO BE COVERED LECTURE 1 Introduction to control Introduction to control system system Classification of control system Adaptive control system Process control systems DEPARTMENT OF MECHANICAL ENGINEERING INPUT The stimulus or excitation applied to a control system from an external source in order to produce the output is called input DEPARTMENT OF MECHANICAL ENGINEERING OUTPUT The actual response obtained from a system is called output. DEPARTMENT OF MECHANICAL ENGINEERING SYSTEM A system is an arrangement of or a combination of different physical components connected or related in such a manner so as to form an entire unit to attain a certain objective. DEPARTMENT OF MECHANICAL ENGINEERING CONTROL It means to regulate , direct or command a system so that the desired objective is attained DEPARTMENT OF MECHANICAL ENGINEERING CONTROL SYSTEM It is an arrangement of different physical elements connected in such a manner so as to regulate, direct or command itself to achieve a certain objective. DEPARTMENT OF MECHANICAL ENGINEERING DIFFERENCE BETWEEN SYSTEM AND CONTROL SYSTEM DEPARTMENT OF MECHANICAL ENGINEERING DIFFERENCE BETWEEN SYSTEM AND CONTROL SYSTEM DEPARTMENT OF MECHANICAL ENGINEERING A FAN: CAN'T SAY SYSTEM A Fan without blades cannot be a “SYSTEM” , Because it cannot provide a desired/proper output i.e. airflow DEPARTMENT OF MECHANICAL ENGINEERING A FAN: CAN BE A SYSTEM A Fan with blades but without regulator can be a “SYSTEM” Because it can provide a proper output i.e. airflow But it cannot be a “Control System” Because it cannot provide desired output i.e. controlled airflow DEPARTMENT OF MECHANICAL ENGINEERING CLASSIFICATION OF CONTROL SYSTEM In general control systems are classified into two categories—open loop and closed loop. Open loop control system DEPARTMENT OF MECHANICAL ENGINEERING EXAMPLES OF OPEN LOOP CONTROL SYSTEM Bread Toaster Traffic control system using lights DEPARTMENT OF MECHANICAL ENGINEERING CLOSED LOOP CONTROL SYSTEM DEPARTMENT OF MECHANICAL ENGINEERING EXAMPLES OF CLOSED LOOP CONTROL SYSTEM Automatic Electric Iron DEPARTMENT OF MECHANICAL ENGINEERING DIFFERENCE BETWEEN OPEN LOOP & CLOSED LOOP SYSTEM Comparison Open Loop System Closed Loop System The system whose control action is In closed loop, the output depends Definition free from the output on the control action of the system. Other Name Non-feedback System Feedback System Amplifier, Controller, Controlled Components Controller and Controlled Process. Process, Feedback. Construction Simple Complex Reliability Non-reliable Reliable Accuracy Depends on calibration Accurate because of feedback. Stability Stable Less Stable Optimization Not-Possible Possible Response Fast Slow Calibration Difficult Easy System Disturbance Affected Not-affected Linearity Non-linear Linear Traffic light, automatic washing Air conditioner, temperature control Examples machine, immersion rod, TV remote system, speed and pressure control etc. system, refrigerator, toaster. DEPARTMENT OF MECHANICAL ENGINEERING LINEAR AND NON-LINEAR CONTROL SYSTEMS A linear control system consists of the components having a linear relationship between the input and output signals under steady state conditions. Any system is called linear when the principle of superposition is applied. A non-linear control system consists of one or more elements, which exhibits a non-linear relationship between the input and output signals. In such system, principle of superposition is not applicable. DEPARTMENT OF MECHANICAL ENGINEERING LINEAR-TIME VARYING AND TIME-INVARIANT SYSTEMS In a control system, most physical systems are characterized by differential equations. A differential equation is linear if the coefficients are constants or functions only of an independent variable. If the coefficients of describing differential equations are functions of time, then the mathematical model is time varying. The systems which consist of linear time-variant components or elements described by linear time-variant differential equations, whose coefficients are functions of time, are called linear time-varying systems. On the other hand, dynamic systems that are composed of linear time-invariant components by linear time-invariant differential equations are called linear time-invariant systems (parameters do not vary with time). DEPARTMENT OF MECHANICAL ENGINEERING CONTINUOUS-TIME AND DISCRETE-TIME CONTROL SYSTEMS A control system in which all the system parameters are continuous functions of time t is called continuous-time control system. A control system in which all the system parameters are discrete functions of time t is called discrete-time control system. LUMPED PARAMETER AND DISTRIBUTED PARAMETER CONTROL SYSTEM The control system which can be described by ordinary differential equations is called lumped parameter control system. On the other hand, the control system which can be represented by partial differential equations, is called distributed parameter control system. DEPARTMENT OF MECHANICAL ENGINEERING DETERMINISTIC AND STOCHASTIC CONTROL SYSTEM In any control system if the response to input is predictable and repeatable, then the system is called deterministic control system. If the response to input is unpredictable and non-repeatable, then the system is called stochastic control system. CLASSIFICATION OF CONTROL SYSTEMS ON THE BASIS OF CONTROL SIGNAL USED Depending upon the nature of signals involved like electrical, mechanical, hydraulic, pneumatic or combination of these signals, the control systems may be classified as single input-single output (SISO) and multiple input-multiple output (MIMO) systems. DEPARTMENT OF MECHANICAL ENGINEERING SISO system. As the name indicates, it is a system having a single input and a single controlled variable. The output is produced by the single input solely. Only one input signal flows or passes through the system. The examples of SISO systems are voltage regulators, temperature controllers and so on. MIMO system. There are certain systems having multiple inputs and multiple outputs. The systems in which any change in one of the outputs causes a subsequent change in the other output during transient and steady state conditions are called MIMO systems. The examples are boiler in which the controlled variables are steam pressure, temperature, water level and so on. Figure shows block diagram of an MIMO system. DEPARTMENT OF MECHANICAL ENGINEERING Adaptive Control System The control systems in which the system parameters are automatically adjusted to keep the system at an optimum level are called adaptive control systems. Such type of control systems itself detects changes in the plant parameters and make essential adjustments in the controller parameters to maintain optimum level or performance. Process Control System It is an automatic regulating system (feedback control system) in which the output is a variable (physical parameters) such as temperature, pressure, pH value, flow, liquid level and so on. It is widely used in different industries like paper, sugar, petrochemical, rubber and so on. DEPARTMENT OF MECHANICAL ENGINEERING TRANSFER FUNCTION The transfer function of a linear time-invariant system is defined as the ratio of Laplace transform of the output variable to Laplace transform of the input variable under the assumption that all the initial conditions are zero. The concept of the transfer function is limited to linear, time-invariant, differential equations systems. It is widely used in designing and analysis of such systems. I. Let G(s) is the transfer function of single-input single-output system with input r(t) and controlled output c(t). II. Consider an nth order differential equation for input-output relation of linear time-invariant system. To obtain transfer function of any equation, take Laplace transforms on both sides and assume all initial conditions as zero. DEPARTMENT OF MECHANICAL ENGINEERING TRANSFER FUNCTION FOR ELECTRICAL SYSTEMS Determine the Transfer function for below circuit DEPARTMENT OF MECHANICAL ENGINEERING DEPARTMENT OF MECHANICAL ENGINEERING TRANSFER FUNCTION FOR CASCADE SYSTEMS Determine the Transfer function for below circuit DEPARTMENT OF MECHANICAL ENGINEERING DEPARTMENT OF MECHANICAL ENGINEERING TRANSFER FUNCTION OF PASSIVE AND ACTIVE ELEMENTS Passive elements. These elements do not take part in any energy transformation, e.g. resistors, capacitors and inductors. Such elements in the system store the energy but can also be used later in the system. This energy cannot exceed when delivered to the system. System elements which contain passive elements are called passive systems. Active elements. These elements take part in energy transformation. They can deliver external energy into the system. The examples of such elements are transistor, diode, op-amp. DEPARTMENT OF MECHANICAL ENGINEERING TRANSFER FUNCTION OF PASSIVE AND ACTIVE ELEMENTS Determine the Transfer function for below circuit DEPARTMENT OF MECHANICAL ENGINEERING DEPARTMENT OF MECHANICAL ENGINEERING COMMONLY USED CONTROL SYSTEM COMPONENTS DC motors which are used in servosystems are called tic servomotors. This motor provides high starting torque due to low inertia. This low inertia can be achieved by reducing armature diameter with increasing armature length so that the desired output power can be achieved. Low power rating dc servomotors are used in computer disk drives, printer, tape drives and so on. Medium and large power dc servomotors are used in machine tool industries, robots and numerically-controlled machines. In dc servomotors, field winding may be connected either in series with the armature or separate from the armature. DEPARTMENT OF MECHANICAL ENGINEERING DC servomotors may be used in two different control modes as follows: Armature control mode, in which the speed of the dc servomotor is controlled by armature current with field current constant. Field control mode, in which the armature current is maintained constant and speed of the dc servomotor is controlled by field voltage. DEPARTMENT OF MECHANICAL ENGINEERING TACHOMETERS Tachometer is used for angular speed measurement. Basically, tachometers are classified as mechanical and electrical tachometers. Electrical tachometers are further divided into ac and dc tachometers. In control system, tachometer is used as a feedback element. DEPARTMENT OF MECHANICAL ENGINEERING MECHANICAL TACHOMETERS This type of tachometer consists of mechanical assembly and movements for the measurement of speed. Revolution counter is a type of mechanical tachometer. Figure shows the construction of a revolution counter (mechanical counter). DEPARTMENT OF MECHANICAL ENGINEERING ELECTRICAL TACHOMETERS This type of tachometer converts the angular or rotational speed into electrical signal and indicates on the indicator provided. DEPARTMENT OF MECHANICAL ENGINEERING AC POSITION CONTROL SYSTEM DEPARTMENT OF MECHANICAL ENGINEERING ADVANTAGES OF AC POSITION CONTROL SYSTEMS AC amplifiers are more stable so there is no drift in operation. Because of small size of ac components, the system is compact. It has low cost. DEPARTMENT OF MECHANICAL ENGINEERING THANK YOU www.mrcet.ac.in A U TO M AT I O N A N D CONTROL ENGINEERING (R17A0327) 4th Year B. Tech I- sem, Mechanical Engineering www.mrcet.ac.in COURSE OBJECTIVES UNIT - 1 CO1: To perform one or more processing operations & To understand the need of Mechatronics systems UNIT - 2 CO2: To make students familiar with the constructions and working principle of different types of sensors and transducers. UNIT - 3 CO3: Understand the fundamental concepts of electro mechanics and fluid mechanics (hydraulics and pneumatics) of Actuators and drive systems. UNIT - 4 CO4: To impart knowledge on the control elements UNIT - 5 CO5: To understand the different control schemes generally used to get best output. DEPARTMENT OF MECHANICAL ENGINEERING UNIT 5 A C T U AT O R S A N D DRIVE SYSTEMS CO5: To understand the different control schemes generally used to get best output. www.mrcet.ac.in UNIT – V (SYLLABUS) ACTUATORS AND DRIVE SYSTEMS Introduction, concept of process control, Automatic controllers, Digital Controller, Electronic Controllers, Pneumatic Controllers, P-I Controller, PD Controller, P-I-D Controller, Hydraulic Controllers. DEPARTMENT OF MECHANICAL ENGINEERING COURSE OUTLINE UNIT - 5 LECTURE LECTURE TOPIC KEY ELEMENTS LEARNING OBJECTIVES 1 Introduction to Process control Define controller Understanding of basics of control system (B2) 2 Automatic controllers -Digital controller Understanding of types of Automatic Types of Automatic controllers -Analog controller controllers (B2) 3 Electronic controllers -Control models Understand the applications of -Composites mode electronic controllers controllers Working principle of Types of 4 Pneumatic controllers Controllers systems and to know the Pneumatic controllers -P-I controller working principles of system(B2) -PD controller Advantages and disadvantages of -P-I-D controller controllers systems(B4) 5 Hydraulic controllers Understand the applications of process -Hydraulic integral controller control systems in various systems and Hydraulic proportional controller to know the functions of each Working principle of types of element(B2) process control systems Able to analyze the which Advantages and disadvantages of Drive systems(B4) DEPARTMENT OF MECHANICAL ENGINEERING TOPICS TO BE COVERED LECTURE 1 Definition Introduction - Actuators Types of Automatic controllers Working principle of Types of controllers Applications Problems Assignments DEPARTMENT OF MECHANICAL ENGINEERING LECTURE TEMPLATE – Introduction Definition Units Classification etc… – Demonstration Text Graphic/ Pictorial Video etc… – Industrial Applications – Solved Problems (1-2) Procedure – Self Learning Questions – Assignment Exercises – Summary DEPARTMENT OF MECHANICAL ENGINEERING Process Control www.mrcet.ac.in INTRODUCTION Suppose you have a system that needs to be controlled Your software gives commands, the system responds to it – Turn x degrees to the right – Move forward 15 wheel rotations Can you always trust your commands will be executed accurately? 9 cs1567 DEPARTMENT OF MECHANICAL ENGINEERING PROBLEM EXAMPLE overshoot Ripple setpoint Increase the quantity until you get to the setpoint – Temperature, angle, speed, etc If too much, reduce the quantity, until the setpoint 10 cs1567 DEPARTMENT OF MECHANICAL ENGINEERING CLOSED LOOP CONTROLLER setpoint error signal output controller system measured quantity closed loop because it has feedback output is measured at a certain frequency signal is generated at a certain frequency which frequency is not smaller? 11 cs1567 DEPARTMENT OF MECHANICAL ENGINEERING ON-OFF CONTROL For some systems, on-off signaling is sufficient For example, a thermostat, when the heater is either on or off, and early cruise-control systems – Could do airflow or speed control also – More modern systems do it Depending on the frequency of control, overhead of on-off, etc, this could cause overshoots and undershoots (ripples) – Oscillation is a common behavior in control systems – Need to avoid it at all costs… well, almost all costs 12 cs1567 DEPARTMENT OF MECHANICAL ENGINEERING PROPORTIONAL CONTROL Good alternative to on-off control: more “control” Signal becomes proportional to the error – P ( setpoint – output ) – Example, car speed for cruise control Need to find out value of constant P – Tuning the controller is a hard job – If P is too high, what happens? – If P is too low, what happens? Typically a prop cntrl decreases response time (quickly gets to the setpoint) but increases overshoot 13 cs1567 DEPARTMENT OF MECHANICAL ENGINEERING ADDING DERIVATIVE CONTROL To avoid (or reduce) overshoot/ripple, take into account how fast are you approaching the setpoint – If very fast, overshoot may be forthcoming: reduce the signal recommended by the proportional controller – If very slow, may never get to setpoint: increase the signal – In general: D ( current measure – previous measure) PD controllers are slower than P, but less oscillation, smaller overshoot/ripple 14 cs1567 DEPARTMENT OF MECHANICAL ENGINEERING INTEGRAL CONTROL There may still be error in the PD controller – For example, the output is close to setpoint P is very small and so is the error, discretization of signal will provide no change in the P controller D controller will not change signal, unless there is change in output Take the sum of the errors over time, even if they’re small, they’ll eventually add up – I * sum_over_time (setpoint — output) Again the main problem is the value of I Can we let sum grow to infinity? 15 cs1567 DEPARTMENT OF MECHANICAL ENGINEERING SUMMARY Different types of controllers PID hardest task is tuning Controller Response Overshoot Error time On-off Smallest Highest Large Proportional Small Large Small Integral Decreases Increases Zero Derivative Increases Decreases Small change 16 cs1567 DEPARTMENT OF MECHANICAL ENGINEERING WHERE TO GET MORE INFORMATION newton.ex.ac.uk/teaching/CDHW/Feedback/ ~don/cs1567/reference/pidworksheet.xls 17 cs1567 DEPARTMENT OF MECHANICAL ENGINEERING INDUSTRIAL APPLICATIONS The Modern Industrial Workhorse: PID Controllers. Proportional- Integral-Derivative (PID) controllers are used in most automatic process control applications in industry today to regulate flow, temperature, pressure, level, and many other industrial process variables. Link: https://controlstation.com/pid-control/ DEPARTMENT OF MECHANICAL ENGINEERING ASSIGNMENT EXERCISES 1. What is meant by controller? Briefly explain about Process control? 2. Explain about Automatic controllers? 3. Explain about Electronic and Pneumatic controllers? 4. What is meant by P-I, PD and P-I-D controllers explain briefly? 5. Explain about Hydraulic controllers? DEPARTMENT OF MECHANICAL ENGINEERING THANK YOU www.mrcet.ac.in