Aircraft Material - Non Ferrous PDF
Document Details
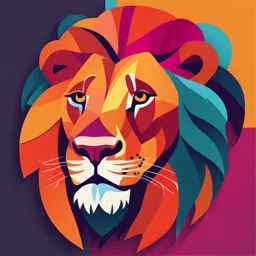
Uploaded by FaultlessMarsh8570
null
2022
null
Tags
Summary
This document provides an overview of non-ferrous metals, particularly focusing on aluminium alloys, and their properties relevant to aircraft construction. It details various types of aluminium alloys, their designation systems, and heat treatments. The document also touches upon other non-ferrous metals like magnesium and titanium, highlighting their specific characteristics and applications within the aerospace industry.
Full Transcript
Properties of Non-Ferrous Metals Non-Ferrous Metals Much of the metal used on aircraft contains no iron. The term that describes metals which have elements other than iron as their base is non-ferrous. Aluminium, copper, titanium and magnesium are some of the more common non-ferrous metals used in a...
Properties of Non-Ferrous Metals Non-Ferrous Metals Much of the metal used on aircraft contains no iron. The term that describes metals which have elements other than iron as their base is non-ferrous. Aluminium, copper, titanium and magnesium are some of the more common non-ferrous metals used in aircraft construction and repair. Examples of non-ferrous metals Identifying Aluminium Aluminium is a silver-white metallic element obtained by electrolysing bauxite. Aluminium sheets 2022-05-18 B-06a Materials and Hardware CASA Part 66 - Training Materials Only Page 39 of 229 Pure aluminium lacks sufficient strength to be used for aircraft construction. However, its strength increases considerably when it is alloyed, or mixed with other compatible metals. For example, when aluminium is mixed with copper or zinc, the resultant alloy is as strong as steel with only one third the weight. Furthermore, the corrosion resistance possessed by the aluminium carries over to the newly formed alloy. Aluminium alloys are classified by their major alloying ingredient. The elements most commonly used for aluminium alloying are: copper magnesium manganese zinc. There are two main classes of aluminium alloys: Wrought alloys, rolled from an ingot or extruded from customer-specified shapes Cast alloys, poured as a liquid into a mould and cooled into a solid shape. Most aircraft parts are wrought aluminium alloys. Wrought aluminium alloy 2022-05-18 B-06a Materials and Hardware CASA Part 66 - Training Materials Only Page 40 of 229 Wrought Aluminium Alloys Designation System Wrought aluminium alloys are identified by a four-digit index system. Aluminium alloy four-digit number system 1xxx Series The 1xxx Series is the only exception to the wrought alloy designation system. The first digit indicates the minimum aluminium content is 99% and there is no major alloying element. The second digit indicates modifications to impurity limits. If the second digit is zero, there is no special control on individual impurities, eg: 1000. The third and fourth digits provide the minimum aluminium percentage above 99%. Thus, 1100 indicates minimum aluminium content of 99.00% with individual impurity control. Likewise, 1030 indicates 99.30% minimum aluminium without special control of individual impurities. The designations 1130, 1230, 1330, etc. indicate the same purity with special control of one or more impurities. 2022-05-18 B-06a Materials and Hardware CASA Part 66 - Training Materials Only Page 41 of 229 2xxx Through 9xxx Series The major alloying elements are indicated by the first digit, as follows: 2xxx – Copper 3xxx – Manganese 4xxx – Silicon 5xxx – Magnesium 6xxx – Magnesium and silicon 7xxx – Zinc 8xxx – Other element 9xxx – Unused series. The second digit indicates alloy modification. If the second digit is zero, it indicates the original alloy. Digits 1 through 9, which are assigned consecutively, indicate alloy modifications. The last two digits have no special significance, serving only to identify the different alloys in the group (number has no significance but is unique). Aviation Australia Percentage of alloying element table 2022-05-18 B-06a Materials and Hardware CASA Part 66 - Training Materials Only Page 42 of 229 Aluminium and Alloys Series Alloys within the 1xxx Series are made of pure aluminium with the following features: Strain-hardenable High formability, corrosion resistance and electrical conductivity Electrical, chemical applications Aluminium 1xxx alloy - pure aluminium ingot Alloys within the 2xxx Series utilise copper as the principle alloying agent. When aluminium is mixed with copper, certain metallic changes take place in the resultant alloy’s grain structure. For the most part, these changes are beneficial and produce greater strength. However, a major drawback to aluminium-copper alloys is their susceptibility to intergranular corrosion when improperly heattreated. Most aluminium alloy used in aircraft structures is aluminium-copper. Two of the most commonly used in the construction of skins and rivets are 2017 and 2024. 2022-05-18 B-06a Materials and Hardware CASA Part 66 - Training Materials Only Page 43 of 229 Aluminium 2xxx alloy The 3xxx Series alloys have manganese as the principle alloying element and are generally considered non-heat-treatable. The most common variation is 3003, which offers moderate strength and has good working characteristics. Aluminium 3xxx alloy The 4xxx Series aluminium is alloyed with silicon, which lowers a metal’s melting temperature. This results in an alloy that works well for welding and brazing. 2022-05-18 B-06a Materials and Hardware CASA Part 66 - Training Materials Only Page 44 of 229 Aluminium 4xxx alloy Magnesium is used to produce the 5xxx Series alloys. These alloys possess good welding and corrosion-resistance characteristics. However, if the metal is exposed to high temperatures or excessive cold-working, its susceptibility to corrosion increases. Aluminium 5xxx alloy - Aluminium magnesium alloy wire If silicon and magnesium are added to aluminium, the resultant alloy carries a 6xxx Series designation that have medium strength with good forming and corrosion-resistance properties. 2022-05-18 B-06a Materials and Hardware CASA Part 66 - Training Materials Only Page 45 of 229 Aluminium 6xxx alloy When parts require more strength and little forming, harder aluminium alloys are employed. The 7xxx Series aluminium alloys are made harder and stronger by the addition of zinc. Some widely used forms of aluminium-zinc alloys are 7075 and 7178. For example, on a medium-sized passenger aircraft: Frames, stringers, keel and floor beams, and wing ribs made of aluminium alloy 7075 (aluminium and zinc) – High mechanical properties and improved stress corrosion cracking resistance Bulkheads, window frames and landing gear beam made of aluminium alloy 7079 (aluminium and zinc) – Tempered to minimise residual heat treatment stresses Wing upper skin, spars and beams made of aluminium alloy 7178 (aluminium, zinc, magnesium and copper) – High compressive-strength-to-weight ratio Landing gear beam made of aluminium alloy 7175 (aluminium, zinc, magnesium and copper) – A very tough, very high-tensile-strength alloy Wing lower skin made of aluminium alloy 7055 (aluminium, zinc, magnesium and copper) – Superior stress corrosion. 2022-05-18 B-06a Materials and Hardware CASA Part 66 - Training Materials Only Page 46 of 229 Aluminium alloys are extensively used in major airframe structures The 8xxx Series provides exceptionally high strength and elasticity, so this alloy is used for aerospace applications where an increases in stiffness combined with high strength reduces component weight. Aluminium 8xxx alloys - the fractured surfaces of the 8090 Al-Li alloy 2022-05-18 B-06a Materials and Hardware CASA Part 66 - Training Materials Only Page 47 of 229 The 9xxx Series alloys are unassigned at this time. Clad Aluminium Alloy (Alclad) Most external aircraft surfaces are made of Alclad aluminium. Alclad is a pure aluminium coating that is rolled onto both surfaces of a heat-treated aluminium alloy sheets used for aircraft construction. The clad surface greatly increases the corrosion resistance of an aluminium alloy. However, if it is penetrated, corrosive agents can attack the alloy within. For this reason, sheet metal should be protected from scratches and abrasions. In addition to providing a starting point for corrosion, abrasions create potential stress points. Clad aluminium alloy on wing in construction 2022-05-18 B-06a Materials and Hardware CASA Part 66 - Training Materials Only Page 48 of 229 Heat Treatment of Aluminium Alloys Heat Treatment Heat treatment is a series of operations involving the heating and cooling of metals in their solid state. Its aim is to make the metal more useful, serviceable and safe for a definite purpose. Heattreating a metal can make it harder, stronger and more resistant to impact. It can also make a metal softer and more ductile. However, one heat-treating operation cannot produce all these characteristics. In fact, some properties are often improved at the expense of others. In being hardened, for example, a metal may become brittle. All heat-treating processes are similar in that they involve the heating and cooling of metals. They differ, however, in the temperature to which the metal is heated and the rate at which it is cooled. Precipitation heat-treatment oven Two types of heat treatments are used on aluminium alloys: solution heat treatment and precipitation heat treatment. 2022-05-18 B-06a Materials and Hardware CASA Part 66 - Training Materials Only Page 49 of 229 Solution Heat Treatment The process of heating certain aluminium alloys to allow the alloying element to mix with the base metal is called solution heat-treating. In this procedure, metal is heated in either a molten sodium or potassium nitrate bath or in a hot-air furnace to a temperature just below its melting point. As an example the temperature is then held to within a small tolerance of this temperature and the base metal is soaked until the alloying element is uniform throughout. Once the metal has sufficiently soaked, it is removed from the furnace and cooled or quenched. It is extremely important that the removal of an alloy from the furnace to the quench is performed within a specified time (approx.10 seconds). The reason for this is that when metal leaves the furnace and starts to cool, its alloying metals begin to precipitate out of the base metal. If this process is not stopped, large grains of alloy become suspended in the aluminium and weaken the alloy. Excessive precipitation also increases the likelihood of intergranular corrosion. To help minimise the amount of alloying element that precipitates out of a base metal, a quenching medium is selected to ensure the proper cooling rate. For example, a water bath provides the appropriate cooling rate for aluminium alloys. Thin sheet metal normally warps and distorts when it is quenched, so it must be straightened immediately after it is removed from the quench. After the quench, all metals must be rinsed thoroughly since the salt residue from the sodium or potassium nitrate bath can lead to corrosion if left on the alloy. Solution heat treatment - allows Solution heat treatment 2022-05-18 B-06a Materials and Hardware CASA Part 66 - Training Materials Only Page 50 of 229 Precipitation Heat Treatment Heat-treatable aluminium alloys are comparatively soft when first removed from a quench. With time, however, the metal becomes hard and gains strength. When an alloy is allowed to cool at room temperature, it is referred to as natural aging and can take several hours or several weeks. For example, aluminium alloyed with copper gains about 90% of its strength in the first half-hour after it is removed from the quench and becomes fully hard in about 4 or 5 days. Precipitation heat treatment An alloy’s aging process time can be lengthened or shortened. For example, the aging process can be slowed by storing a metal at a sub-freezing temperature immediately after it is removed from the quench. On the other hand, the aging process can be accelerated by reheating a metal and allowing it to soak for a specified period of time. This type of aging is called artificial age-hardening, precipitation-hardening or precipitation heat treatment. This process develops hardness, strength and corrosion resistance by locking a metal’s grain structure together. Naturally aged alloys, such as copper-zinc-magnesium alloys, derive their full strength at room temperature in a relatively short period and require no further heat treatment. However, other alloys, particularly those with high zinc content, need thermal treatment to develop full strength. These alloys are called artificially aged alloys. 2022-05-18 B-06a Materials and Hardware CASA Part 66 - Training Materials Only Page 51 of 229 Naturally aged alloy 2022-05-18 B-06a Materials and Hardware CASA Part 66 - Training Materials Only Page 52 of 229 Annealing Annealing is a process that softens a metal and decreases internal stress. In general, annealing is the opposite of hardening. To anneal an aluminium alloy, the metal’s temperature is raised to an annealing temperature and held there until the metal becomes thoroughly heat-soaked. When annealing clad aluminium metals, they should be heated as quickly and as carefully as possible. The reason for this is that if clad aluminium is exposed to excessive heat, some of the core material tends to mix with the cladding. This reduces the metal’s corrosion resistance. Aviation Australia Thermal treatment table 2022-05-18 B-06a Materials and Hardware CASA Part 66 - Training Materials Only Page 53 of 229 Aluminium Alloy Temper Designations Heat-treatable alloys have their hardness condition designated by the letter T followed by one or more numbers. Commonly used designations includes: T – Solution heat-treated. T3 – Solution heat-treated, followed by strain-hardening. Different amounts of strainhardening of the heat-treated alloy are indicated by a second digit. For example, T36 indicates that the material has been solution heat-treated and has had its thickness reduced 5% by coldrolling. T4 – Solution heat-treated, followed by natural aging at room temperature to a stable condition. T5 – Artificially aged after being rapidly cooled during a fabrication process such as extrusion or casting. T6 – Solution heat-treated, followed by artificial aging (precipitation heat-treated). 2022-05-18 B-06a Materials and Hardware CASA Part 66 - Training Materials Only Page 54 of 229 Reheat Treatment A material which has been previously heat-treated can generally be heat-treated several times. As an example, rivets made of 2017 or 2024 are extremely hard and typically receive several heat treatments to make them soft enough to drive. The number of solution heat treatments allowed for clad materials is limited due to the increased diffusion of core material into the cladding. This diffusion results in decreased corrosion resistance. As a result, clad material is generally limited to no more than three heat treatments. Reheat treatment facility 2022-05-18 B-06a Materials and Hardware CASA Part 66 - Training Materials Only Page 55 of 229 Non-Heat-Treatable Aluminium The non-heat-treatable aluminium alloys are usually designated, therefore, in the 1000, 3000, 4000, 5000 Series. Their properties can be adjusted by cold work, usually by cold-rolling. Commercially pure aluminium does not benefit from heat treatment since there are no alloying materials in its structure. Non-heat treatable alloys Strain-Hardening Both heat-treatable and non-heat-treatable aluminium alloys can be strengthened and hardened through strain-hardening, also referred to as cold-working or work-hardening. This process requires mechanically working a metal at a temperature below its critical range. Strainhardening alters the grain structure and hardens the metal. The mechanical working can consist of rolling, drawing or pressing. Strain hardening 2022-05-18 B-06a Materials and Hardware CASA Part 66 - Training Materials Only Page 56 of 229 Heat-treatable alloys have their strength increased by rolling after they have been solution heattreated. On the other hand, non-heat-treatable alloys are hardened in the manufacturing process when they are rolled to their desired dimensions. However, at times these alloys are hardened too much and must be partially annealed. Hardness Designations Where appropriate, a metal’s hardness, or temper, is indicated by a letter designation that is separated from the alloy designation by a dash. When the basic temper designation must be more specifically defined, one or more numbers follow the letter designation. The digit following the designations H1, H2 and H3 indicates the degree of strain-hardening. For example, the number 8 represents the maximum tensile strength, while O indicates an annealed state. Therefore, for example, an H38 material has been strain- hardened and stabilised, and is fully hard. 2022-05-18 B-06a Materials and Hardware CASA Part 66 - Training Materials Only Page 57 of 229 Other Alloy Types Magnesium and Its Alloys Magnesium alloys are used for castings and in their wrought form are available in sheets, bars, tubing and extrusions. Magnesium is one of the lightest metals with sufficient strength and suitable working characteristics for use in aircraft structures. It has a lower density than aluminium and weighs only about two thirds as much as aluminium. Wheel assemblies commonly use magnesium alloys The drawbacks to using magnesium are: High susceptibility to corrosion – This is overcome by treating the surface with chemicals that form an oxide film and exclude oxygen. Tendency to crack when formed – This is overcome by heating the parts when forming, such as hot-dimpling thin material. Readiness to burn in a dust or small particle form. For this reason, caution must be exercised when grinding and machining magnesium. If a fire occurs, extinguish it by smothering it with dry sand or some other dry material that excludes air from the metal and cools its surface. If water is used, it will only intensify the fire. 2022-05-18 B-06a Materials and Hardware CASA Part 66 - Training Materials Only Page 58 of 229 Grinding magnesium alloy Solution heat treatment of magnesium alloys increases tensile strength, ductility and resistance to shock. If it is artificially aged (precipitation heat-treated) after solution heat treatment, the hardness and yield strength are increased. Solution heat treatment increases hardness of magnesium alloys as used in gearbox and generator housings 2022-05-18 B-06a Materials and Hardware CASA Part 66 - Training Materials Only Page 59 of 229 Titanium and Its Alloys Titanium and its alloys are lightweight metals with very high strength. In addition to its light weight and high strength, titanium and its alloys have excellent corrosion resistance characteristics, particularly to the corrosive effects of salt water. However, since the metal is sensitive to both nitrogen and oxygen, it must be converted to titanium dioxide with chlorine gas and a reducing agent before it can be used. Because of its high strength-to-weight ratio, titanium is now used extensively in the civilian aerospace industry. Although titanium was once rare on commercial aircraft, modern jet transports now utilise alloys containing 10% to 15% titanium in structural areas. Titanium and its alloys - aircraft engine CFM56, fan blades, TA6V titanium alloy Nickel and its Alloys Nickel is a silver-white metallic element and its two most commonly used alloys are: Monel Inconel. 2022-05-18 B-06a Materials and Hardware CASA Part 66 - Training Materials Only Page 60 of 229 Monel Monel contains nickel and copper with small amounts of iron and manganese. Monel can be welded and has very good machining characteristics. Certain types of Monel, especially those containing small percentages of aluminium, are heat-treatable to tensile strengths equivalent to steel. Monel works well in gears and parts that require high strength and toughness, as well as for parts in exhaust systems that require high strength and corrosion resistance at elevated temperatures. Monel rivets are also available for aircraft structural applications. Nickel and its alloys - Monel 2022-05-18 B-06a Materials and Hardware CASA Part 66 - Training Materials Only Page 61 of 229 Inconel Inconel contains nickel and chromium with small amounts of iron and other elements. These alloys find frequent use in turbine engines because of their ability to maintain their strength and corrosion resistance under extremely high temperatures. For example, Inconel can be found in nozzle supports, fan casings and blades. Inconel found in Pratt and Whitney gas turbine engine Inconel and stainless steel are similar in appearance and are frequently used in the same areas. Differentiating between the two must be done through a chemical test. 2022-05-18 B-06a Materials and Hardware CASA Part 66 - Training Materials Only Page 62 of 229 Copper and its Alloys Copper is a bright reddish metallic element often occurring in thin sheets or plates filling narrow cracks or fissures. Neither copper nor its alloys find much use as structural materials in aircraft construction. However, due to its excellent electrical and thermal conductivity, copper is the primary metal used for electrical wiring. Of the several alloys that use copper as a base, the following are the primary alloys found on aircraft: Brass – commonly used in electrical components due to is high conductivity. Bronze – used in bushings, bearings, fuel metering valves and valve seats. Beryllium – one of the most used copper alloys. Beryllium is used for diaphragms, precision bearings and bushings, ball cages and spring washers. Safety Data Sheets (SDS) identifies beryllium copper as a hazardous material because grinding, dust or fumes produce airborne contaminants. Copper used in electrical wire and components 2022-05-18 B-06a Materials and Hardware CASA Part 66 - Training Materials Only Page 63 of 229