Principles For Layout Plans And Sectioning Diagrams For 25kV AC Traction PDF
Document Details
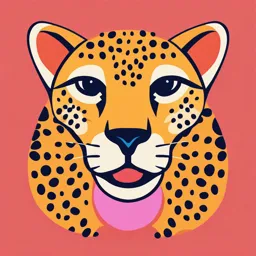
Uploaded by SolicitousOklahomaCity
null
null
null
Tags
Summary
This document provides principles for layout planning and sectioning diagrams for 25kV AC traction, covering definitions and various equipment types. It's intended for use in railway electrification projects.
Full Transcript
APPENDIX I PRINCIPLES FOR LAYOUT PLANS AND SECTIONING DIAGRAMMS FOR 25kV AC TRACTION (This is a re-production of RDSO document No. ETI/OHE/53 issued in June 1988.) 1.0 INTRODUCTION 1.1 These principles for preparation, checking and fi...
APPENDIX I PRINCIPLES FOR LAYOUT PLANS AND SECTIONING DIAGRAMMS FOR 25kV AC TRACTION (This is a re-production of RDSO document No. ETI/OHE/53 issued in June 1988.) 1.0 INTRODUCTION 1.1 These principles for preparation, checking and finalization of over head equipment lay out plans, have been framed from standardization and guidance of Railways/Railway Electrification Projects. In some cases, the principles are obligatory and should be followed. In other cases, principles have been evolved to standardize designs and to speed up the work. The principles could be relaxed in special cases, after studying individually the implications to arrive at the best solution both from economical and technical points of view. The fundamental aim of design of overhead equipment is to install all the contact wire at the requisite height and to keep it within the working range of the pantograph under all circumstances. 2.0 DEFINITIONS The technical and other terms used in this book, shall have the same meaning as defined in General and Subsidiary Rules/ac Traction Manual, unless, there is any thing repugnant to the subject or context: 2.1 BOND An electrical connection across a joint in or between adjacent lengths of rail: i) Bond, continuity – A rail bond used for maintaining continuity of the rail circuit at crossings and junctions. ii) Bond, cross – A rail bond used for connecting together two rails of a track or rails of adjacent tracks. iii) Bond impedance – A special rail bond used to bridge an insulated rail joint in ac track circuited sections in areas equipped for electric traction. iv) Bond rail – An electrical connection across a joint between two adjacent lengths of rail as part of the track return. v) Bond, Structure – An electrical connection between the steel work of track structures, bridge or station building, to which the traction overhead equipment is attached and the track return. 2.2 Cantilever assembly It is an insulated swivelling type structural member, comprising of different sizes of steel tubes, to support and to keep the overhead catenary system in position so as to facilitate current collection by the pantograph at all speed without infringing the structural members. It consists of the following structural members. i) Stay arm – It comprises of dia 28.4/33/7 mm (Small) size tube and an adjuster at the end to keep the bracket tube in position. It is insulated from mast by stay arm insulator. ii) Bracket tube – It comprises of dia 40/49 mm (Small) or dia. 30/38 mm (standard) bracket tube and insulated by bracket insulator. Catenary is supported from this member by catenary suspension bracket and catenary suspension clamp. iii) Register Arm – It comprises of dia 28.4x33.7 mm tube to register the contract wire in the desired position with the help of steady arm. INDIAN RAILWAYS- AC TRACTION MANUAL- VOLUME II PART II iv) Steady arm assembly – It is 32 x 31 mm BFB section made of aluminum- alloy to register the contact wire to the required stagger and to take the push hp of contact wire. It is always in tension. 2.3 Crossings The electrically live member/conductor passing over another electrically live member/conductor, without physical contact. i) Power line crossing – An electrical overhead transmission or distribution line or underground cable placed across railway track(s) whether electrified or not for transmission of electrical energy. ii) Crossing OHE – Crossing of two conductors of OHE crossing without physical contact. 2.4 Dropper A fitting used in overhead equipment construction for supporting the contact wire from catenary. 2.5 Electrical Clearance. The distance in air between live equipment and the nearest earthed part. 2.6 Encumbrance The axial distance on vertical plane between the catenary and the contact wire at support. 2.7 Feeder A conductor connecting (a) a substation with a feeding post, or (b) a feeding post with the OHE 2.8 Height of contact wire The distance from rail level to the under side of contact wire. 2.9 Interruptor It is a single phase Vacuum SF6/oil circuit breaker used as load switch to close the circuit on fault but does not open on fault. It is operated either by remote or manually at site. Different methods of connection of interruptors are: a) Bridging Interruptor – An interruptor which is provided at the neutral section to extend the feed from one substation to the overhead equipment normally fed by the other substation in emergencies or when the latter is out of use. This normally remains in the open position. b) Sectioning Interruptor – An interruptor which connects adjacent sub-sectors together to maintain continuity of supp This normally remains in closed position. c) Paralleling Interruptor – An interruptor which connects overhead equipments of two different tracks. This normally remains in closed position to reduce the voltage drop. 2.10 Jumper A conductor or an arrangement of conductors for electrical continuity not under tension, which forms electrical connection between two conductors or equipments. INDIAN RAILWAYS- AC TRACTION MANUAL- VOLUME II PART II 2.11 Mast A single vertical post embedded in the foundation or otherwise rigidly fixed in vertical position to support the overhead equipment with cantilever assembly. It may be rolled section or fabricated. The uprights of portals and TTCs are also called masts. Note: Pre-stressed concrete spun poles for traction overhead equipment are under development. 2.12 Neutral Section A short section of insulated dead overhead equipment which separates the sectors fed by two adjacent substations which are normally connected to different phases. 2.13 Overhead Equipment (OHE) The electrical conductors over the track together with their associated fittings, insulators and other attachments by means of which they are suspended and registered in position. All overhead electrical equipment, distribution lines, transmission lines, and feeder may be collectively referred to as overhead lines. 2.14 Overlap An arrangement of overhead equipment over a track where two sets of traction conductors are run parallel to each other for short distance over span(s) providing a smooth passage for the pantograph of an electric rolling stock. In the un-insulated overlaps two sets of conductors are separated by 200 mm and connected by a jumper. In insulated overlaps the two sets of conductors are separated by 500 mm in air. Electrical continuity is provided by an isolator. Interruptor or booster transformer. 2.15 Over line structures Any fixed structure provided over the track. The prescribed clearance is normally provided as laid down in the Schedule of Dimensions for unrestricted movement of rolling stock. 2.16 Pantograph A collapsible device mounted on an insulated from the roof of an electric engine or motor coach for collecting current from the overhead equipment. 2.17 Return Conductor A conductor which carries current from the tracks to the sub-station in the booster transformer system. 2.18 Regulating Equipment A device for maintaining the tension of OHE conductors constant under all ambient temperature conditions. Note: Such OHE is called regulated OHE. 2.19 Setting Distance (Implantation) The horizontal distance from the nearest face of traction mast to the centre line of the track. INDIAN RAILWAYS- AC TRACTION MANUAL- VOLUME II PART II 2.20 Suspension Distance The horizontal distance from the centre of the eye of catenary suspension bracket to the face of the mast for a single cantilever assembly or to the face of cross arm channel in case of multiple cantilever assembly (Ref. Fig A.1.01) 2.21 Span The distance between the centre lines of the adjacent supporting masts for overhead equipment/lines. Clear span in case of portal structure, is the distance between the inner faces of portal uprights. 2.22 Stagger Stagger of the contact wire is the horizontal distance of the contact wire from the vertical plane through the centre of pantograph plan at the contact surface. The stagger of the catenary is the horizontal distance of the eye of the catenary suspension bracket from the vertical plane through the centre of the track. 2.23 Section Insulator A device installed in the contact wire for insulating two elementary electrical sections from each other while providing a continuous path for the pantograph without break of current. 2.24 Supply Control Post It is general term which refers to an outdoor assembly of control gear, such as interruptors, isolators, potential transformers, auxiliary transformers, etc. including remote control equipment installed in a cubicle, for controlling power supply to overhead equipment. a) Feeding Post (FP) – It is a supply post where the incoming 25 kV feeder lines from the substation are terminated, and connected to the overhead equipment through interruptors. b) Sectioning and Paralleling Post (SP) – It is a supply control post situated mid-way between two feeding posts at the neutral section and provided with bridging and paralleling interruptors. c) Sub-sectioning and paralleling post (SSP) – It is a supply control post where a sectioning and paralleling interruptor is provided. d) Sub-sectioning Post (SSP)- (For single line section) it is a supply control post where a sectioning interruptor is provided. 2.25 Sector A section of overhead equipment of a track which can be energized by closing a feeder circuit breaker at the sub-station. a) Sub-sector The smallest section of overhead equipment which can be isolated remotely by opening of interruptors. b) Elementary Section – The smallest section of overhead equipment which can be isolated from the rest of the system by manual operations. INDIAN RAILWAYS- AC TRACTION MANUAL- VOLUME II PART II 2.26 Tension Length Length of conductor which is stretched between the two anchor points. 2.27 Versine The versine is the maximum offset of the rail on which spans have been measured (Para 5.1) of the curved track from the chord connecting two points, each opposite adjacent masts. 3. Electrical Clearance 3.1 Clearance The clearance between 25 kV live parts and earthed parts of fixed structures or moving loads shall be as large as possible. The electrical clearances to be maintained under the worst conditions of temperature, wind, etc. are given below: a) Minimum vertical distance between any live part of overhead equipment or pantographs and parts of any fixed structures (earthed or otherwise) or moving loads: i) long duration …320 mm ii) Short duration …270 mm b) Minimum lateral distance between any live part of overhead equipment or pantographs and parts of any fixed structure (earthed or otherwise) or moving loads. i) Long duration …320 mm ii) Short duration …220 mm Note: I) These clearances may be reduced to 250 mm (long duration) and 200 mm (short duration) with the personal approval of the Chief Electrical Engineer in very difficult locations (Rly. Board’s letter No. 76/RE/240/1 dt. 27.3.80). ii) A clearance study should be made for every over line structure/tunnel and, if required, should be referred to RDSO for advice. 3.2 Working clearance Minimum clearance between live conductor/equipments and such earthed structure/live parts of different elementary sections where men are required to work shall be 2 m. Where the clearance is not obtained the structure shall be protected by earthed metallic screens or prescribed warning boards (refer para 22.2 and 22.3) 4.0 Wind Pressure 4.1 Wind Load Wind pressures for design of all masts and determination of spans are based on IS: 875-1964 – “Code of Practice for Structural Safety of Buildings – Loading Standards” Vide an amendment issued in 1971 to this specification, wind pressures for structures of height less than 30 m were reduced by 25% Accordingly the standard wind pressures adopted are as follows for all new works for different zones as indicated in the specification: i) Green zone (light) -75 kg/m2 ii) Yellow zone (medium) -112.50 kg/m2 iii) Red zone (heavy) -150 kg/m2 INDIAN RAILWAYS- AC TRACTION MANUAL- VOLUME II PART II 4.2 Loading calculation For working out the wind loading the total projected area for the rolled sections, 150% of the projected area for fabricated structures and 2/3rd of the projected area for conductors and other circular member is taken into account. Note: The safety of masts and portals is checked for two conditions. a) At 35 degree C temperature and full wind pressure. b) At 4 degree C temperature and 20% of the governing wind pressure. 5.0 Spans 5.1 Measurement Spans shall be accurately measured by means of a steel tape. On curves, these measurement shall be taken on the outer rail of the middle track in the case of an odd number of tracks and in the case of an even number of tracks on the inner rail of the first outside track (from the centre of the formation). On single track, measurements shall be made on the outer rail. 5.2 Standard Span Standard spars shall be determined in accordance with: i) Drg. No. ETI/OHE/G/00202 for conventional OHE. ii) Drg. No. ETI/OHE/G/04201 for regulated tramway OHE and iii) Drg. No. ETI/OHE/SK/375 for composite OHE (Aluminum- alloy catenary and copper contact wire) 5.3 The spans shall be as large as practicable, but should enable the contact wire to be erected with permissible stagger. For a stipulated maximum stagger, the length of the span is governed by curvature, blow off of overhead equipment, sway of pantograph and deflection of the mast under wind condition. Standard spans shall be used to maximum extent possible. 5.4 Mid span stagger Where the two adjacent spans are located on curves of different radius or when the two versines are in opposite directions, the spans shall be determined so as to keep the mid span stagger in the two spans within the limit given in the span and stagger chart (ETI/OHE/G/00202), taking into account the stagger at the common support and the stagger at the extreme supports (see para 8) 5.5 Restrictions The following restrictions are applicable. i) On main tracks, the lengths of two consecutive spans shall not normally differ by more than 18 m. ii) The length of spans with unequal encumbrances shall be such that the axial distance between the catenary and the contact wire at the minimum dropper is not less than 150 mm. For example the length of the span with 1.4 m and 0.9 m encumbrances at the two ends shall not exceed 67.5 m. This restriction is applicable to the two spans on each side of the structure, equipping a turnout for the main OHE. INDIAN RAILWAYS- AC TRACTION MANUAL- VOLUME II PART II iii) Spans in the vicinity of over line structures with restricted head room shall be determined with reference to the electrical clearances available (See para 3) iv) The lengths of spans loaded with section insulators may require to be restricted (See para 11) v) Non-standard spans may be adopted in difficult locations, e.g. in rocky cuttings, on through girder bridges, for locations of masts on bridge piers and within station limits. vi) With crossed type equipment with actual crossings of OHEs at facing turnouts, the anchor spans shall be restricted to 54 m. vii) Where earth wire is provided, the maximum span over level crossings should be 58.5m. 5.6 Overlaps The spans at insulated and un-insulated overlaps should be designed in accordance with Drg. Nos. ETI/OHE/G/02131/Sheet 1 and RE/33/G/02121 Sh. 1 respectively. Note: If feasible, overlap shall be avoided under overhead power line crossings. 5.7. Neutral sections The spans at neutral sections should confirm to Drg. No. ETI/OHE/G/02161 sheet No. 1 and no deviations are normally permissible. 6.0 Masts, Portals, Head Spans and Foundations. 6.1 Types of masts. OHE conductors are suspended from swivelling cantilever assembly generally erected on individual masts. 6.1.1 Nine types of masts are used. These are designated as 150x150 BFB, 200x150 RSJ, K- 100, K-125, K-150, K-175, K-200 K-225 and K-250. The first two are rolled sections and remaining seven are fabricated masts. B-series (Drg. No. ETI/C/0071) masts can be used in lieu of K-series masts. Note: Sometimes 200x200 (8”x8”) BFB have been imported. These are used in lieu of 200x150 RSJ as specified in mast employment schedules, 6.1.2 Selection of masts The masts for standard applications viz. masts for single OHE, anti-creep and overlaps should be selected from the mast employment schedules. Separate mast employment schedules have been made for each wing pressure zone as under: a) Conventional OHE ( 65mm2 Cd-Cu catenary and 107 mm2 copper contact wire) Light wind pressure Drg. No. ETI/C/0702 ( 75 Kgf/m2) Sheet 1 to 5 Medium wind pressure Drg. No. ETI/OHE/G/00153 (112.5 kgf/m2) and 00154, sheet 1 to 4 INDIAN RAILWAYS- AC TRACTION MANUAL- VOLUME II PART II Heavy wind pressure Drg. No. ETI/C/0726 ( 150 Kgf/m2) Sheet 1 to 4 ETI/C/0727,0728 and 0729 b) Composite OHE (comprising of aluminum alloy catenary and 107 mm2 copper contact wire with 1000 Kgf tension in each conductor) Light wind pressure Drg. No. ETI/C/0721 sheet (75 Kgf/m2) 1 to 4 & ETI/C/0722, 0723 & 0724 Medium wind pressure Drg. No. ETI/C/0717 (112.5 Kgf/m2) Sheet 1 to 4 & ETI/C/0713,0719 & 0720 The mast employment schedules are prepared only for standard setting distance as given in Drg. No. ETI.OHE/G/00111 Sh. 1 For higher implantations and other locations like masts for turnouts, diamond crossings, umbrella type OHE etc, the load on the mast should be calculated separately for every locations and safety of the mast checked in accordance with Drg. No. ETI/OHE/G/00141 sheet 3. The permissible bending moments of the mast are given in Drg. No. ETI/SK/C/122 6.1.2.1 On long (more than 150m) bridges and within 100m from their abutments on either side and on banks where the height of the catenary above surrounding mean retarding surface is more than 30 m 25% reduction in wind pressure (para 4.1 ) should not be taken into consideration. These masts should be designed for full wind pressure i.e. Heavy ( red) wind pressure zone 200 Kgf//m2 Medium (Yellow) wind pressure zone 150 Kgf/m2 Light ( Green ) wind pressure zone 100 Kgf./m2 The maximum span should be restricted to 54 m for heavy wind pressure zone and 63 m for medium wind pressure zone. In case of curves on the banks of such bridges, the span should be 4.5 m less than the maximum span permitted by relevant span and stagger chart, but should not exceed 54 m for heavy (red) wind pressure zone and 63 M for medium (yellow) pressure zone. 6.2 Two Track Cantilever In the yards and sidings when the mast cannot be erected near the track to be equipped, it may be erected spanning one or two tracks using a two track cantilever (Drg. No. ETI/C/009, Sheet 1). This is generally used for supporting OHE near turnouts and X-overs. This arrangement should not be used for supporting OHE of two main lines. The OHE can be supported upto a distance of 10.5 m from the upright with this arrangement. 6.3 Portals On multiple track sections, where adequate track centres are not available and tracks cannot be slewed, portals are used. Each portal consists of two fabricated uprights and one fabricated boom consisting of with or without one central piece and two end pieces. 6.3.1 Three types of portals have been standardized. “N “ type portal is used for clear spans of 10 m-20m (4 track maximum), ‘O” type portal is for clear span of 20m-30m( for 6 tracks maximum) and ‘R’ type portal with span of 30m-40m (for 8 tracks maximum). 6.3.2 Where the upright of standard portals cannot be erected due to limited track centres, ‘P’ type portal may be used in place of ‘N’ type and ‘G’ type may be used in place of ‘O’ type. The width of upright of these portals INDIAN RAILWAYS- AC TRACTION MANUAL- VOLUME II PART II is 300 mm and 250 mm as against 450 mm of ‘N’ type and 550 mm of ‘O’ type respectively. In exceptional cases, BFB uprights of 152 mm width (Drg. No. ETI/C/0026 Sheet 1) may also be used with ‘N’ type portal boom. Special BFB portals with 3 legs (Drg. No. ETI/C/0027 Sheet ) may also be used in exceptional cases where N type portal can not be used. 6.3.3 The cantilevers for the extreme track are provided on the uprights of the portals in accordance with para 19. The cantilevers for the intermediate tracks are provided on the drop arms suspended from the boom (ref. Para 19.6) 6.4 Head spans In yards where un-regulated/regulated OHE is used head span may also be used to cover more than 6 tracks. Standard head span arrangement is given in Drg. No. ETI/OHE/G/03201. The head span arrangements are not used normally. 6.5 Foundations 6.5.1 Volume charts The foundation bending moment codes (FBM) for each location are obtained from the mast employment schedules or by actual calculation (Para 6.1.2) Bearing capacity of the soil is determined at the outer toe of the bottom of foundation at a representative number of locations. Where foundations are placed on the slope of banks due to increase in setting distance, the bearing capacity of the soil should be determined on the slope. Bearing capacities determined thus would be considerably less than those determined on the top of formation. Selection of the type and size of foundation is done from the volume chart. ( Drg. No. ETI/C/0058) on the basis of FBM code, type and bearing capacity of soil/shoulder width and the extent of projection above ground level. 6.5.2. Type of foundations. The following types of foundations are for OHE mast and portals. 1) For Masts i) (A) Side bearing Drg. No. ETI/C/0058 Sh. 1 (Type B) (B) Side gravity -do- (Type BG) (C) Pure gravity -do- (Type G ) (D) Pure Gravity -do- For black cotton soil (Type WBC ii) New Pure Gravity -do- Sh. 2A (Type NG) iii) NBC type foundation for dry black -do- Sh 3A cotton soil (16500 & 11000 Kgf/m2 3.0 m depth. INDIAN RAILWAYS- AC TRACTION MANUAL- VOLUME II PART II 2) For portals i) In ordinary soil Drg. No.ETI/C/0005/68 ii) In dry black cotton soil Drg. No. ETI/C/0063 6.5.2.1 In the case of OHE foundations in deep rock cutting the foundation should be below the drain. 6.5.2.2.For all future constructions of pure gravity foundation Drg. No. ETI/C/0058 sheet 2A only shall be followed. 6.5.3. Selection of foundations Side bearing foundations are used for masts where the soil bearing capacity is 11,000 or 21,500 Kgf./M2 and 300 mm wide shoulder is available on the bank. However for overlap inter masts and masts on the inside of curves, 550 mm wide shoulder is necessary ( Drg. No. ETI/C/0023). (Ref. Fig. A1.02). 6.5.4 New pure gravity foundations may be used for masts where soil bearing capacity is 5500, 8000 and 11000 Kgf./M2 or where adequate shoulder width as mentioned in para 6.5.3 is not available. In such cases, it should be ensured that foundation is not exposed. 6.5.5. Side gravity foundations may be used for masts where soil bearing capacity is 8000 and 11000 Kgf./M2, or adequate shoulder width is not available. No portion of the foundation should be exposed. 6.5.6 Pure gravity foundations (type G) are used for independent masts where soil surrounding the foundations is loose and cannot exert passive pressure on the foundations. G type foundation have been designed for soil bearing capacity of 5500 , 8000 and 11000 Kgf./M2. Pure gravity foundations (Type P) are used for portals and are designed for soil bearing capacity of 8250 and 11000 Kgf./m2. 6.5.7 Foundations in black cotton soil 6.5.7.1 The foundation of the black cotton should be done preferably in dry season i.e. from November to May. Excavations should be avoided as far as possible in case of unexpected rains in dry season also. 6.5.7.2 In black cotton soils. WBC and NBC type of foundations are used. Primarily WBC foundations are to be adopted where swelling/shrinkage is not expected to take place at the founding level and NBC foundations have to be provided where swelling/shrinkage is expected to occur. 6.5.7.3 The safe bearing capacity should be determined in accordance with IW: 6403 6.5.7.4 When in doubt regarding classification of BC soil as to dry or wet, it is preferable to make NBC type foundation. 6.5.8 Where foundations are constructed on the slope of banks, the foundations should be so located that generally no part of it is exposed. The top of foundation may then be brought to the desire level (rail level- 500 mm) by providing a super block of length and breadth equal to the top dimension of foundations. The increase in bending moment due to increased setting distance should be calculated and the designation of foundation to allow for this BM should be selected. The arrangement is shown in the Fig. No. A.1.03 6.5.9 The top of foundation should be 50-100 mm above the surrounding ground level. The length of mast below rail level should be minimum 1850 mm for regulated OHE and 1750 mm for un-regulated OHE. A 1350 mm embeddment of mast in concrete is necessary. Concrete cushion of 150 mm below the bottom of mast is also necessary. Wherever necessary, these may be achieved by providing a super block of length and width equal to the top dimension of foundation. INDIAN RAILWAYS- AC TRACTION MANUAL- VOLUME II PART II However portion of existing pure gravity foundations to Drug. No.ETI/C/0058 She. 1 corresponding to a depth of 500 mm of embankment having slope of 1:2 may be exposed. 6.5.10 Giving due consideration to the above, the most economical type of foundation should be adopted. 6.0 Contact Wire Height. 7.1 Standard height Normally the height of contact wire ( under side surface) above the track plane shall not be less than 5.50 m at any point in the span under the worst temperature conditions. To ensure this, the normal height at the suspension point shall be as under: Type of OHE Normal height of contact wire at the support point. i) Regulated a) Normal with 10 cm pre-sag 5.60 m b) Old electrification 5.55 m works with 5 cm pre-sag Note: 5 cm pre-sagged OHE was provided upto 1968. For new works 10 cm pre-sagged OHE shall normally be provided. However, OHE with 5 cm pre-sag may be provided in long tunnels and through girder bridges to achieve the minimum electrical clearance. ii) Unregulated a) Unregulated OHE designed 5.75 m for areas with a temp range of 4ºC to 65ºC. b) Unregulated OHE designed 5.65 m for areas with a temp range of 15ºC to 65ºC 7.2 The height may be reduced under over line structures after a clearance study. The minimum height shall be 4.92 m for the broad gauge and 4.02 m for the meter gauge to permit movement of “C” class ODC without physical lifting of wires. In case “C” class ODC movement is not required, the height could be reduced to 4.80 m (BG). Height may be further reduced to 4.65 m if rolling stock higher than 4.265 m are not allowed on such lines. ( Ref. Fig. A1.04) 7.2.1 At electric locomotive sheds and loco inspection pits, the minimum height shall be 5.80 m for the broad gauge and 5.50 m for the metre gauge. 7.2.2 At level crossings, the minimum height shall be 5.50 m for both broad and metre gauges. 7.3 Erection tolerance A tolerance of +/- 20 mm is permissible on the height of contact wire as measured at a point of support except on either side of an over bridge, here a tolerance of +/- 10 mm will be allowed. But the difference between the heights of contact wire at two adjacent supports shall not exceed 20 mm. In spans with gradient of contact wire, this difference of 20 mm is measured over and above the approved gradient. INDIAN RAILWAYS- AC TRACTION MANUAL- VOLUME II PART II 8.0 Stagger 8.1 Tangent track On tangent track, the contact wire is normally given a stagger of 200 mm at each support alternately on either side of the centre of the track. This is relaxed in special cases for ensuring requisite clearances in difficult locations such as in the vicinity of signals, subject to stagger at midspan not exceeding the permissible values given in Drug. No. ETI/OHE/G/00202. 8.2 On tangent track, the catenary stagger is zero for masts supporting a single equipment. The catenary is fixed vertically over the contact wire at all supports at which more than one equipment is supported, at flexible head spans and at supports with reduced encumbrance, on tangent as well as curved tracks. 8.3 Curved track On curves, the stagger of the contact wire at supports should not exceed 300 mm. The stagger of the catenary on curved track shall be determined with reference to Drug. No. ETI/OHE/G/00202. The standard values adopted are 0, +200 and – 200 Note: For maximum permissible stagger refer para 4 of Chapter V-A of Schedule I, BG Metric Schedules of Dimensions – 1973. 8.4 Turnouts and diamond crossing At turnouts, the stagger of the contact wire on the main running line shall be in accordance with Drug. No. ETI/OHE/G/00202. The stagger of contact wire of the branching line shall not exceed 300 mm at any point in the span. This is achieved by selecting a suitable location for the mast near the centre of the turnout in the case of overlap type equipment, or by suitably adjusting the point of crossing of the two contact wires in the case of crossing type equipment. 8.5 Un-insulated overlaps At un-insulated overlaps, the stagger should confirm to Drug. No. RE/33/G/02121 sheet 1. On non- uniform curves or at other locations where staggers different from those indicated in these drawings are adopted, the following points should be observed. i) The stagger of the in-running contact wire does not exceed 200 mm on tangent track and 300 mm on curved track at any support, at which only one contact wire is in-running. ii) In any span at the centre of which only one of the contact wires is in-running (as in 4-span overlap), the mid-span stagger of the in-running contact wire does not exceed the values given in Drug. No ETI/OHE/G/00202 iii) The two contact wires run parallel to each other between the intermediate supports at a distance of 200 mm from each other. 8.6 Insulated overlap At insulated overlaps, stagger should conform to Drug. No. ETI/OHE/G/02131 Sheet 1. On non- uniform curves and at other locations where stagger different from those shown in this drawing are adopted, the points mentioned against un-insulated overlap spans also apply, with the difference that between the intermediate masts the two contact wires run parallel at a distance of 500 mm from each other. INDIAN RAILWAYS- AC TRACTION MANUAL- VOLUME II PART II 8.7 Neutral Sections The stagger at overlap type neutral sections should conform to Drug. No. ETI/OHE/G/02161, Sheet No. 1. 8.7.1 The stagger at section insulator type neutral section should be so adopted that the stagger at the section insulator assembly is within the limit of +/- 100 mm (see para 11.1(iii). 8.7.2 PTFE type neutral section shall be erected on tangent track only. The stagger shall be zero at support. 9 Encumbrance 9.2 Normal The encumbrance shall normally be 1.40 m. 9.3 Reduced encumbrance The preferred values of reduced encumbrance for erection of overhead equipment under over-line structure are: ------------------------------------------------------------------------------------------------------------------------------------- Span under Recommended encum- Largest per- Over-line brances for span missible adj- Structure under over-line acent spans Structure (m) (m) (m) ------------------------------------------------------------------------------------------------------------------------------------- 1 2 3 ------------------------------------------------------------------------------------------------------------------------------------- 63.0 0.9 67.5 58.5 0.9 67.5 54.0 0.75 67.5# 49.5 0.6 63.0 45.0 0.6 63.0 40.5 0.5 58.5 36.0 0.40 54.0* 31.5 0.40 49.5 27.0 0.30 45.0 ------------------------------------------------------------------------------------------------------------------------------------- # Applicable where the encumbrance cannot be increased to 1.40 m in a single span from the value given in column 2. The normal encumbrance of 1.40 m should be provided in subsequent spans. In such cases, the encumbrance may be adjusted in such a way that the lowest point of the catenary does not fall between first dropper and the support. * See para 5.5 (1) Note I) The above values are applicable only to regulated OHE with 10 cm nominal pre-sag of contact wire. II) Special droppers may be required in spans under and adjacent to over-line structures. INDIAN RAILWAYS- AC TRACTION MANUAL- VOLUME II PART II 9.4 Minimum Encumbrance Normally, the axial distance between the catenary and the contact wire at the minimum dropper should not be less than 150 mm. Smaller droppers may be adopted in exceptional cases. If the shortest dropper is loop type and more than 150 mm, no speed restriction is called for. But it the dropper is without loop or of rigid type or less than 150 mm, the overhead equipment is deemed suitable upto 90 km/h speed. 9.5 If section insulators are to be installed in spans under over-line structures, special designs will have to be evolved. 10.0 Droppers 10.1 The standard arrangement of droppers assembly shall be as per drawing No. ETI/OHE/P/1190 10.2 The general distribution of droppers on an OHE span shall be as per drawing No. ETI/OHE/G/00161. The arrangement of OHE span should be designed in such a way that standard droppers are used. 10.3 Special droppers arrangement. The special arrangement of dropper as shown in Drug. No. ETI/OHE/P/1400 may be followed in exceptional cases wherever unavoidable. 10.3.1 The arrangement of the dropper to be adopted on the through girder bridges as shown in Drug. No. ETI/OHE/P/1410, where the OHE is supported on member of girder bridge. 10.4 Rigid dropper Adoption of rigid dropper ( made of contact wire only) should be avoided as far as practicable. It should not be adopted, at all on main running lines. 11 Section Insulators 11.1 Location Sectional insulators should be so located that the following conditions are fulfilled. i) At location of section insulator, the axial distance between the catenary and contact wire shall not be less than 450 mm in the case of single-wire section insulator and 600 mm in the case of a double wire section insulator without increasing the encumbrance at the supports beyond 1.40 m. ii) The section insulator is to be located beyond the point where the centre distance between the two tracks is equal to or more than 1.65 m. If the section insulator is erected with the free ends of the runners away from the centre of the turn out this distance may be reduced to 1.45 m. iii) The stagger of the contact wire at the location of the section insulator should normally be zero, but in no case should it exceed + 100 mm. iv) On loops, the section insulator shall, as far as possible, be located close to the first support of the overhead equipment for the loop. v) The preferred location of section insulator on main running track is 2 to 10 m from the support in the direction of traffic, though its provision on the main line should be avoided. vi) In double line section, the runners should be in the trailing direction. INDIAN RAILWAYS- AC TRACTION MANUAL- VOLUME II PART II 13.0 Tension Lengths. 13.1Regulated equipment With regulated overhead equipment every tension length is equipped with an automatic tensioning device at each end and an anticreep located approximately midway between the tensioning devices. The distance between the anticreep and the anchor mast/structures on either side should not exceed 750 m or 15 supporting masts. 13.2 Half tension lengths Half tension lengths of regulated overhead equipment, not greater than 750 m between anchorages, may be adopted where necessary. The equipment is fixed at one end and provided with an automatic tensioning device at the other, the fixed end being determined to suit convenience of erection. The half tension-length on either side of the neutral section should not exceed 600 m when the whole or a part of it is located on a curve. The distance of the axis of a 4 span insulated overlap from the anti-creeps/fixed terminations on either side shall not exceed 600 m. 13.2Bridges and tunnels Where the catenary is anchored on the face of an over line structure, the anchor shall be the anti creep point. Termination of overhead equipment or provision of an anticreep, should be avoided , as far as possible, inside the tunnels and on the mast set on bridge piers. 13.4 Masts with three brackets In the case of masts with three brackets supporting regulated equipment, anticreeps or fixed terminations of the overhead equipment should be arranged so as to keep the relative movement between brackets as low as possible so that the brackets do not foul with each other. 13.5 Unregulated equipment With unregulated equipment tension, lengths of upto 2000 m. between anchors may be adopted on tangent as well as curved track. 13.5.1 Unregulated OHE shall not take off from main running lines 13.6 Linkage of wire-runs Wire-runs linking two or more main line wire-runs shall be as short as possible. For example, the same wire run may not ordinarily be used for equipping an emergency cross –over and a loop line. 13.7 Anti-creep Anticreep arrangement: Anticreep is located approximately in the centre of a tension length. The standard arrangement should be in accordance with Drug. No. ETI/OHE/G/02111. 13.7.1 Boom type anticreep arrangement (Drug. No ETI/OHE/G/02113) may be provided on multiple track sections or in other areas where portals have been provided on account of other design considerations, Portals should not be provided specifically for provision of boom type anticreep. INDIAN RAILWAYS- AC TRACTION MANUAL- VOLUME II PART II the anchor mast and the point of crossing if there is crossing of the wires. 14.7 In case of regulated equipment, when the equipments to be anchored on a single span, anchor height shall be the standard one to get the regulation of the overhead equipment within the limit travel zone of counter weight assembly. However, single span anchoring should be avoided as far as possible. 14.8 Anchor near buildings No live anchor or equipment shall be provided near or over any hut/goomty and building, In such cases the overhead equipment should be isolated by providing cut-in-insulator and earthed by connecting it metalically to the anchor mast without providing the insulator in the anchor assembly. 14.9 Termination The anchoring arrangement of OHE are given in Drug. No. RE/33/G/03121. In polluted areas, e.g. tunnels, areas near sea-coast, neighbourhood of chemical/fertilizer/cement plants, near loco sheds, ash pits, water columns, etc long creepage path (1050 mm) insulator should be used on the anchoring arrangement. 15.0 Location of overlap 15.1Platform lines Overlaps serving platform lines should not be located opposite platform to avoid location of tensioning devices on the platforms. If it is unavoidable, half tension length may be adopted to avoid the provision of the regulating equipment on the platform 15.2 Protection by signals In the station area insulated overlaps on main running lines should be located after the stop signals. (Refer to sectioning arrangement of OHE – para 30.) 15.3 Cross over In the case of emergency cross-overs insulated overlaps in the direction of the trailing end should permit the longest train to be accommodated between the lock bar of the cross over switch and the first intermediate mast of the overlap with a minimum margin of 50m. This distance may be taken as 850 m. the overlap in the rear should be located as close as possible (Refer to sectioning arrangement of OHE – par a 30.) 15.4 Span Location of insulated and uninsulated overlaps should be decided in such way that the maximum span can be adopted to achieve parallel path of not less than 3 m for smooth change over by the pantograph. 15.5 The arrangement of overlaps should be as per standard drawings (see para 5.6 15.6 Feeders to overlaps Feeding overlaps should be sufficiently away (see para 16.2) from the stop signals to facilitate coasting of trains (with pantograph lowered in the event of extension of feed from either side. Feeders may be run, if required, from the substation which is usually located in the station areas. 16 Neutral Section 16.1Overlap type The conventional overlap type neutral section(Drug. No. ETI/OHE/G/02161, Sheet-1) shall be used except in INDIAN RAILWAYS- AC TRACTION MANUAL- VOLUME II PART II 16.2 Location of ‘OPEN DJ’ and ‘CLOSE DJ’ boards. The indication boards to indicate the approaching neutral section and ‘OPEN DJ’ , ‘CLOSE DJ’ boards shall be provided according to drawing No. ETI.OHE/G/02161 Sheet 3. 16.2.1 Separate ‘CLOSE DJ’ boards are required for EMUs and loco hauled trains. 17 Points and Crossings. 17.1General arrangement The equipment at points and crossings should preferably be of the overlap type. In unavoidable circumstances it may be of crossed type. 17.1.1The general arrangement of regulated overhead equipment at turnouts and cross overs is shown in Drug. Nos. ETI/OHE/G/02141 and 02151. For high speed running, the overlap type should be provided. 17.1.2The general arrangement of unregulated overhead equipment at turnouts and cross overs is shown in Drug. No. ETI/OHE/G/03151 and 03152, Sheet 1 & 2. 17.1.3The leading dimensions of standard turnouts and crossings are given Drug. Nos. RE/33/G/01104, sheet 1 and 01105, Sheet 1 for the broad gauge and in Drug. Nos. RE/33/G/01104, Sheet 2 and 01105, sheet 2 for the metre gauge. 17.2 Overlap type In the case of turnouts for high-speed running a mast is located near the centre of the turnout and the contact wire of the secondary track is raised in one or more spans (exclusive of the anchor span) after the centre of the turnouts, before it is anchored. A cross over is equipped in the same manner as two ordinary turnouts. Note: Overlap type overhead equipment at turn outs taking off from main line shall be provided. 17.2.1 A diamond crossing with or without slips is equipped as two turnouts, the turnout centres being coincident. The mast located near the common centre is, therefore, equipped with three bracket assemblies (See Drug. No. ETI/OHE/G/02151). 17.3 Crossed type The crossed type equipment for turnouts is normally adopted on secondary tracks but may be used on main tracks, where speeds are less than 100 km/h. The overhead equipment of the secondary track normally crosses the overhead equipment of the main track or does not have any overlapping span before anchorage. The two contact wires are clamped together to prevent relative vertical displacement. For this type of equipment, no support is necessary near the centre of turnout. 17.3.1 In case of diamond crossings with double slips, if crossed type of equipment is provided, doubling of contact wire is necessary (See Drug. No. ETI/OHE/G/03152, sheet 2). Doubling of contact wire is, however, not essential in the case of diamond crossings with single slip. In either case, no mast is necessary at the centre of the crossings. 18 Arrangement of Masts 18.,1 Location of masts. Masts should generally be arranged as far as possible in the same line parallel to the track and in the same line transverse to the track. Normally, no masts should be located between any two main running tracks. INDIAN RAILWAYS- AC TRACTION MANUAL- VOLUME II PART II 18.9 Masts shall not be located in front of station entrances. 18.10 Masts shall not be located opposite to trolley refuges, close to culverts, subways and on bridges of length less than 50 m. 18.11 No masts shall be located beyond a signal post at a distance less than 10 m. In case the OHE mast is located in the front of the signal the distance between the OHE mast and signal post should not be less than 30 m (Ref. Fig. A1.10) 18.12 Masts should be located sufficiently for away from level crossings and back of abutments of bridges. The distance between the mast and the end of the level crossing/abutment shall not normally be less than 10 m. 18.13 The sections having more than two tracks, independent masts should be provided if adequate track centres are available or if the tracks can be slewed. Where adequate track centres are not available portals will normally be adopted and they should be located in such a way as to facilitate provision of drop arm/s and bracket assembly. 18.14 In case of bad formations, if it is possible to locate the masts on either side of a track, preference should be given to the side with better stability. 18.15 Support for OHE in tunnels. In the lines tunnels, stubs for supporting OHE cantilever assembly should be provided on both sides of the tunnel, opposite each other. This would facilitate restoration of OHE in the event of damage to stubs on one side. 18.16 Masts on bridges Core holes for erecting masts on bridges should be provided as per Drug. No. RE/31/0590/63 on both sides of all the piers. Holes on piers which are not used for foundation should be filled with dry sand covered with a concrete slab. 18.17 In case of wiring a petroleum siding special precaution shall be adopted as laid down. 19 Cantilever Arrangement 19.1 Overhead equipment is supported from the masts by cantilever bracket assembly made of galvanized steel tubes. The bracket assembly shall be of the swiveling type. 19.2 Cantilever arrangement The arrangement of cantilever depends upon the height of contact wire, encumbrance, suspension distance, stagger and super elevations. Standard cantilever arrangements are given in Drug. No. ETI/OHE/G/02106, Sheet 1 & 3. 19.2.1 Platform location The arrangement of cantilever on platform shall be as per Drug. No. ETI/.OHE/G/-2104, Sheet 2. 19.3 Allowance for adjustment The bracket assembly shall be such as to permit easy adjustment of the whole equipment after erection to cater for displacement of track during maintenance to the extent of 100 mm on either side of the track centre. 19.3.1 Adjustment on bracket tube It shall be ensured at the time of selection of bracket assembly that the free length of the bracket tube beyond the INDIAN RAILWAYS- AC TRACTION MANUAL- VOLUME II PART II catenary suspension bracket fittings is atleast 150 mm to facilitate future adjustment. 19.3.2 Adjustment on stay tube The selection of stay tube at any location shall be such that its adjuster is free for adjustment of minimum 90 mm in either direction. 19.3.3. In case of curve track when the rail level is raised or the super elevation is changed due to strengthening of track structure, the pantograph axis will be shifted. If this shift is not within the possible adjustment limit of bracket assembly as specified in Clause 19.3.1 and 19.3.2 above, new cantilever may have to be provided taking care that at no stage the contact wire is beyond the specified stagger. 19.4 Size of tubes The size of stay tube and register arm tube is 28.4/33/7 mm dia. For all cantilever arrangements. The size of bracket tube is either 30/38 mm or 40/49 mm designated as standard or large respectively depending upon the location (See Drug. No. ETI/OHE/G/00158 sheet 1,2 and 3 and 00159 sheet 1,2 & 3). 19.5 Back to back arrangement More than one cantilevers (on the same side) are provided on the masts for overlap, turnouts, cross over and diamond crossings. The cantilever may be symmetrical (50 cm on either side of the mast) or asymmetrical (65 cm on one side and 35 cm on the other side of the mast). Note I) Adoption of more than three bracket assembly is not possible on a single cross arm. II) Cantilever assemblies can be provided on both sides of the masts, if the OHE of the two tracks are of the same elementary section. This is called ‘Umbrella’ construction. 19.6 Bracket assembly on drop-arm. On portals, bracket assembly for the intermediate track/s is erected on drop arms. Wherever the track centre is inadequate (i.e. suspension distance less than 1.60 m), the equipment should be supported on drop arm of reduced length so that the bracket assembly does not infringe with the swept zone of pantographs. The arrangement is shown in Drug. No. ETI/OHE/G/02108. 19.7 Bridge & Tunnels Bracket assembly of special design may be adopted on bridges and tunnels after making clearance study. 19.8 Bracket chair Bracket assembly can be designed upto suspension distance of 3.5 m only. If the suspension distance is more, bracket chair to drawing No. ETI/OHE/P/3050 and RE/33/P/3100 shall be used. 19.9 Insulator for Bracket Assembly In polluted areas e.g. tunnels, areas near sea coast, neighbourhood of chemical/fertilizer/cement plants, near steam loco sheds, ash pits, water columns etc. long creepage path (1050 mm) insulators should be used on the cantilever assemblies. INDIAN RAILWAYS- AC TRACTION MANUAL- VOLUME II PART II 20 Setting of Masts 20.1 Tangent Track The standard setting i.e. the normal distance of the nearest part of the traction mast from the centre line of tangent track shall be 2.50 m for the broad gauge and 2.35 m for the metre gauge. The setting may be reduced to a minimum of 2.36m for the broad gauge and 2.14 m for the metre gauge only in special circumstances such as yards, cuttings and bridges etc. with the approval of the Chief Electrical Engineer of railway concerned. In case of portal uprights, masts carrying more than one OHE and head span masts,a the setting should normally be less than 3.00 m for the broad gauge and 2.50 m for the metre gauge. 20.2 Curved track The minimum setting distance of masts including portals, head span masts etc. on curves is obtained by adding the curve allowance and 150 mm slewing allowance to the setting distance specified for tangent track in para 20.1. For trunk routes and main lines where the speed may be increased in near future, curve allowance should be taken as per table-III. For other routes, branch lines and yards where there is no prospect of increase in above 105 km/h in near future, the curve allowance should be taken as per table- I for Broad gauge and Table-II for metre gauge. Normally, the standard setting distance on broad gauge main lines on curves should not be less than the values given below: a) On outside curves Standard setting (m) (i) Radius of curvature 2.50 greater than or equal to 875m. (ii) Radius of curvature less 2.65 than 875m. (b) On side curves (i) Radius of curvature 2.90 greater than of equal to 3500m. (ii) Radius of curvature 3.05 greater than or equal to 2350m. but less than 3500m. (iii) Radius of curvature 3.25 greater than or equal to 1150m but less than 1150m. (iv) Radius of curvature 3.30 greater than equal to 300m. but less than 1150m. INDIAN RAILWAYS- AC TRACTION MANUAL- VOLUME II PART II 20.5 Masts near signals The visibility of signals should be kept in mind while deciding the setting up masts in their vicinity. The following principles should be observed for deciding the setting of masts near signals. 20.5.1 Colour light signals located outside all tracks. a) Colour light signals without route indicators. i) Where no approach signal is provided The minimum setting of mast before signal should be 3.25, 3.10, 3.05, 2.90 and 2.75 m for distance upto 80 m, beyond and upto 110 m ,beyond and upto 190 m, beyond and upto 270 m and beyond and upto 400 m respectively. ii) Where approach signal is provided and for signals other than distant signals. The minimum setting of masts before the signal should be 3.25, 3.10, 3.05, 2.90 and 2.75 m for distance upto 50 m. beyond and upto 70 m beyond and upto 115 m, beyond and upto 160 m and beyond and upto 240 m respectively. b) Colour light signal with route indicators. i) With horizontal route indicator The minimum setting of masts before the signal should be 3.72, 3.50, 3.25, 3.05, 2.90 and 2.75m for distances upto 60 m, beyond and upto 125 m beyond and upto 170 m, beyond and upto 215 m, beyond and upto 250 m, beyond and upto 310 m, respectively. ii) With other than horizontal route indicator The minimum setting of masts before the signal be 3.50, 3.25, 3.05, 2.90 and 2.75 m for distances upto 70 m, beyond and upto 130 m, beyond and upto 170m, beyond and upto 215 m, and beyond and upto 280 m respectively. Note : 1 See Drg. No. ETI/OHE/G/00112 also. The setting may be reduced in special cases, conforming to Figs. 6 to 9 of ibid. 2) Setting distance may be reduced for starter signals of loop lines and yard lines 20.5.2 Colour light signals located between tracks: a) Signals without route indicators: No OHE mast should, as far as possible be located in the same lane as the signal for a distance of atleast 600 m before a signal. Drop arms of portals should also not normally be located in the lane where signals are located, at least for a distance of 600 m before the signal. Where this is not possible, for any reason, the signal should be mounted on an off-set bracket, In addition, a special study should be made in each such case in respect of three drop arms before the signal, to see whether the drop arms can be off-set from the centre line of the lane in a direction opposite to the off-set of the signal or alternatively, whether it is possible to shorten the drop arms. Reduction in the signals height may also be examined. INDIAN RAILWAYS AC TRACTION MANUAL - VOL II PART I b) Signals with route indicators: The principles mentioned under para 20.5 (a) should be observed in these cases also. Note: 1 No part of a colour light signal without a route indicator should, as far as possible, be higher than 5.2 m above all level. Great care should be exercised in deciding the locations of colour light signals with route indicators so that the necessary minimum clearances are available between the signals and live out of run conductors, or pantograph sway zone. 2. On single-line sections, signals (colour light as well as semaphore) should, as far as possible, be located on the side of the track opposite to the OHE masts. 20.5.3 For semaphore signals located outside the track: The minimum setting of masts before the signal should be 3.05 , 2.90 and 2,75 m for the first second and next three masts respectively. Note : For details, See Drg. No. ETI/OHE/G/00112. 20.6 Masts on bridge piers The setting of masts on piers of bridges will be large as possible and indicated by the Railway. 20.7 Turnouts The setting of masts located near theoretical centres of turnouts and diamond crossings should be 3.0 m from the nearest track for the broad gauge and 2.75 m for the metre gauge (Ref. Fig. A1.09) 20.8 Portals Wherever portals are proposed to be used, they shall be selected with standard clear spans (distance between face of the uprights) indicated in the tables IV and V. For this purpose the clear span for any location obtained by adding the proposed setting of the two columns to the centre-to- centre distances of the tracks spanned by the portal shall be rounded off to the next higher standard span indicated in the tables. The setting of the uprights of the portal shall then be adjusted to suit the standard span selected with a minimum setting distance as specified in para 20.2. INDIAN RAILWAYS-AC TRACTION MANUAL – VOL II PART II 21.2 Where adequate clearance is available, the catenary should be erected so as to have maximum clearance from the over-line structure to reduce the possibility of birds perching on the catenary wire and coming in contact with earthed parts. 21.3 The catenary is normally passed freely under over-line structures. Where this is not possible on account of restricted clearances, the following alternatives may be adopted. i) The catenary may be suspended from the two-faces of the over-line structures. ii) Suspension from over-line structure The catenary may be suspended from the over-line structure at an intermediate point. iii) The catenary may be anchored on to the over-line structure on either side or on to special anchor structures. The anchor point should normally be the anticreep. iv) Special designs may be adopted inside covered station areas and on through girder bridges, employing even regulated tramway type equipment (contact wire only), where it is feasible. Note: At over-line structures, the span should preferably be centrally located as far possible and generally should not exceed 54.0 m. 21.4 Polluted zone Double insulation or insulator for polluted zones shall be used in the following cases: i) In tunnels (see para 19.9) For insulators located on the axis of the track in areas where steam traction would be in extensive use or where smoke is likely to accumulate. 22.0 25 kV Feeders 22.1 Suspension Where a 25 kV feeder is run longitudinally on traction masts, it shall be carried on the masts as shown in Drg. No. ETI/OHE/G/05143. The feeder may be run on either side of a mast. Two 25 kV feeders, or one return conductor and one 25 kV feeder, may be carried on a single mast, if necessary, with one feeder on each side of the mast. Note: If the 25 kV feeder and OHE are of different elementary sections, ‘Restricted clearance’ board shall be provided. 22.2 Clearances from over head equipment Where a 25 kV feeder crosses overhead equipment belonging to a different elementary electrical section, the clearance between the feeder and the overhead equipment shall not be less than two metres under any conditions. 22.3 Clearance from line side structures Normally, no feeder should be erected over huts, cabins, goomties, platforms shed or other covered structures. If unavoidable the clearance between the highest point of a covered structure and a 25 kV feeder passing over it shall be 2 m under all conditions. In the case of a 25 kV feeder passing over an over-line structures which is not covered, a suitable metallic screen shall be provided on the structure underneath the feeder. The clearance between the feeder and the highest point of the screen shall be adequate. A clearance of 2 m is desirable between INDIAN RAILWAYS – AC TRACTION MANUAL -VOL II PART II the 25 kV feeder and any part of an earthed structure for facilitating maintenance work on the structure. 23.0 Cross-Spans at Switching Stations 23.1 Cross span arrangement All the switching stations have gantry with two or more main vertical supports. Cross span wires/feeders are provided on the gantry to connect the various sections of overhead equipment by jumper connections. The general arrangement is shown in Drg. No. ETI/OHE/G/05124 23.2 Setting distance The minimum setting distance of the gantry upright which is normally aligned parallel to the track shall be 4.30 m. 23.3 Multiple track The general arrangement of connections at the switching stations on double track and multiple track section are shown in Drg. No. ETI/OHE/G/05125 and 05126 respectively. 24.0 Tramway type overhead equipment 24.1 Regulated Equipment In tramway type equipment only contact wire is provided and is auto-tensioned at the anchor by weight. The contact wire is supported by swiveling type of brackets on individual masts as indicated in DRg. No. ETI/OHE/G/04204. Generally the principles applicable to normal overhead equipment are also applicable to regulated tramway equipment except as specified below: 24.1.1. Usage The regulated tramway type equipment is to be adopted for loop lines, sidings, yards and spur lines excluding the main running line and first loop or lines taking-off from the main running line. 24.1.2 Span The maximum span is restricted to 63 m. The general arrangement is shown in Drg. No. ETI/OHE/G/04203. 24.1.3 Section Insulators Where a section insulator assembly is to be provided, the provision of a structure to support the assembly is obligatory. The arrangement is shown in Drg. No. ETI/OHE/G/04207 sheet 1 & 2. 24.1.4 The arrangement of tramway equipment at anti creep and points and crossings are shown in Drg. No. ETI/OHE/G/04205 and 04208 respectively. 24.2 Unregulated equipment The general arrangement of tramway equipment to be adopted for head span and cantilever type construction is shown in Drg. No. ETI/OHE/G/04101. The principles applicable to normal OHE are applicable to this type of unregulated equipment except as specified below. The maximum span is restricted to 30m. In station areas, where this type runs side by side with conventional equipment with contact and catenary wires, the maximum span may be increased to 31.5 m. 24.2.1 Where a section insulator is to be provided the provision of a structure becomes obligatory. INDIAN RAILWAYS – AC TRACTION MANUAL –VOL II PART II 38 25.0 Booster Transformers 25.1 100 KVA Booster Transformer wherever necessary for suppression of inductive interference of P&T communication lines running in close vicinity and parallel to 25 kV OHE may be provided separately for each running tracks. The primary winding of the booster transformer is connected in series with the OHE at insulated overlaps. The arrangement of mounting and connection is shown in RDSO Drg. No. ETI/PSI/115. 25.2 The Booster Transformers are located at an approximate spacing of 2.66 km between each other. 25.3 The location of the booster transformer should be decided considering the following aspects: a) At feeding posts and sectioning and paralleling posts the booster transformers should be located equi-distant on either side so that the mid-point falls in front of these switching stations. b) In exceptional circumstances where the booster transformers are not placed equi-distant from the feeding post or sectioning post, it must be ensured that the distance of the booster transformer from FP or SP does not exceed 1.33 km c) The booster transformer should not be located - In the vicinity of the stop signals to avoid bridging of insulated overlap by locomotives pantograph. - - Within the station limits except for very big stations. 26.0 Return Conductors. 26.1 Route In deciding the route of return conductors the obstructions en-route should be taken into consideration. Besides, adequate physical and electrical clearances should be maintained from fixed structures. The general objectives is to run the return conductor as close as possible to the associated overhead equipment so as to secure maximum compensation. Subsidiary lines such as sidings, loops etc. are not provided with return conductors. The return conductor will be normally run on the traction masts on the same side as the overhead equipment. The arrangement is shown in Drg. No. ETI/OHE?/05307. The clearance between the return conductor and the overhead equipment should not be less than 400 mm under the worst conditions. 26.2 Clearance The static and dynamic clearance to any part of the return conductor from an earthed structure should be 150 mm and 80 mm respectively. 26.3 Return conductors at over-bridges. At over-bridges return conductors may be run straight through, if possible as on normal structures. 26.4 Return conductors in complicated areas. In station areas having complicated track layout, it may not be practicable to position the return conductor sufficiently close to the associated overhead equipment to secure the required compensation. In such cases, the route of the return conductor should be decided on the merits of each case. Care being taken to avoid running of return conductor over platforms. INDIAN RAILWAYS – AC TRACTION MANUAL VOL II PART II 26.5 Tension lengths of return conductors Return conductors are normally terminated at the masts where the return conductors are connected to the rail. They may be anchored back-to-back at such masts. 26.6 Connections to booster transformers. At all booster stations, the return conductors for each track should be provided with a cut-in-insulator. The return conductor is connected in series with the secondary winding of the booster transformer and the connections of the return conductor to the booster transformer should be carried out in accordance with Drg. No. ETI/OHE/G/05413. 26.7 (I) The mid-point of return conductor shall be connected to the buried rail as per RDSO’s Drg. No. ETI/OHE/G/05306 and ETI/PSI/611. The mid-point is defined as a mid point between two consecutive booster transformers. ii) Mid-point of the return conductor before feeding posts shall be connected to the buried rail on either side of the insulated overlap and in case of sectioning posts shall be connected on either side of the neutral section. iii) Inexceptional circumstances, where mid-point does not fall in front of feeding posts and sectioning posts, the two rail links between return conductor and rail should be provided in front of feeding post and sectioning post on either side of the insulated overlap/neutral section. In these cases, mid-point should not be connected to rail. 27.0 LT Supply Transformer 27.1 Low tension power supply 230 V single phase power supply required for operation of sub-station equipment e.g. circuit breakers, interruptors, etc.lighting of the station yard, tunnels and working of colour light signals, is obtained through 25 kV 230 V , 10 KVA 50Hz. single phase LT supply transformer. It is provided at substations feeding and switching posts, stations, block-huts and at other outdoor locations e.g. level crossings with gate signals. 27.2 Capacity LT supply transformers are of 10 KVA capacity. More than one transformer are provided at large station, yard etc. 27.3 Protection LT supply transformers are protected only by a 25 kV, Amp. Dropout fuse on the primary side and 63 A fuse (rewireable d.c. type with 20 SWG tinned copper wire) on the secondary side. 27.4 Mounting Arrangement The LT supply transformer is mounted on steel platform erected on the OHE mast and connected to the 25 kV OHE through rigid aluminum bus-bar or 50 mm2 copper jumper wire. The general arrangement of mounting and connection is shown in Drg. No. ETI/PSI/036 27.5 Substation L T supply. At substation, in order to provide power to single phase transformer oil centrifuging /filtration plant, 100 KVA, 25 KV/230V 50 Hz. single phase transformers are provided. The general arrangement of mounting and connection is shown in Drg. No. ETI/PSI/0312. INDIAN RAILWAYS – AC TRACTION MANUAL -VOL II PART II 28.0 Mast and Rail Bonds 28.1Structure Bonds All traction masts shall be bonded to a non-track-circuited rail as shown in Drg. No. ETI/OHE/P/7000 (see para 29.1). In the case of portals, only one uprights of the portals, and in the case of head spans, both masts of the head spans, shall be bonded to non-track-circuited rails. 28.2 Rail Bonds The Rail bonds to connect the running rails longitudinally across a rail joint shall be in accordance with Drg. No. ETI/OHE/P/7030. 28.3 The cross bonds connecting two rails of track of rails of track or rails of adjacent track shall be in accordance with Drg No. ETI/OHE/G/05251 29.0 Earth Wires 29.1 Sectioning and earthing In sections where a non-track circuited rail is not available, as in double-rail track-circuited sections, all traction masts shall be connected together by a continuous aerial earth wire supported by the traction masts. The earth wire shall be divided into electrical sections not exceeding 1000 m in length by means of cut-in-insulators. Each section of earth wire shall be bonded to traction mast which should be connected to an earthing station (Drg. No. ETI/OHE/P/7020). With two separate earth electrodes in such a way that the interval between the earthed structures does not normally exceed 500 m as shown in Drg. No. ETI/OHE/G/05201. 29.2 In Tunnels In case of tunnels, all the traction support structures shall be connected together by a continuous earth wire, which may be supported from tunnel surface. The earth wire shall be made into discontinuous sections not exceeding 1000 m and shall be connected to earth electrodes provided not more than 500 m apart and traction rail at both ends of the tunnel. 29.3 Layout No earth wire shall cross any track. Where masts required to be connected to an earth wire are located on opposite sides of a track, separate wire-runs shall be used for connecting the masts. In complicated areas, masts may be connected to individual earthing stations. 29.4 Anchoring Earth wires need be anchored only at termination of wire-runs. 30.0 Sections Arrangement. 30.1 Necessity of sectioning OHE is divided into electrically isolated sections by provision of interruptors or isolators at overlaps and with section-insulators at turnouts. Sectioning is provided to permit isolation of OHE in small sections for maintenance or to isolate damaged OHE in case of breakdown/accident and to permit diversion of trains from up line to down line and vice-versa. However, the sectioning should be kept to the minimum consistent with operational requirement. INDIAN RAILWAYS – AC TRACTION MANUAL -VOL II PART II. 31.4 Multiple section In multiple track section, suffix ‘A’ is to be given to the multiple track mast. For instance in case of a section consisting of Up main, Down main and Up slow and Down slow track the slow track masts shall be numbered as 75/1A, 75/3A, etc. for Up slow line and 75/2A, 75/4A etc. for Down slow line. Uprights of portals, erected in multiple track sections shall be numbered with reference to main line only i.e. 75/1, 75/2 etc. 31.5 Numbering of masts of loops and sidings in station yards. 31.5.1 Individual masts. Single cantilever and double cantilever mast supporting OHEs of tracks on either side (umbrella type) for loops and sidings shall bear the station code and serial number in one thousands series (1000). The station code shall be given on above the horizontal line and the serial number below it. Masts of Up loops and siding on Up line side shall be given odd number of 1001.1003,1005 etc. in the order of progressive chainage, irrespective of the number of loops and the masts on the Down loops and sidings on the Down line side shall be given even numbers 1002, 1004, 1006 etc. In case several independent cantilever masts for different loops are located at the same chainage, loop mast nearest to the main track should bear the lowest number in the series (see Fig. 10). This system of numbering is applied from one end of a yard in the kilometerage of the starting point and progressively higher numbers is given in the direction of increase in chainage whether it is Up or Down yard. The numbering does not indicate the kilometerage. 31.5.2 (a) In case a portal is provided, the upright of the portal nearest to the main track shall be given a number in 2000 series, the other upright of the portal shall be given a number in 3000 series. In case of 3 leg portals, the farthest leg from the main track shall be given a number in 4000 serires. 31.5.2 (b) In case a portal is covering both Up and Down main lines as well as loops and siding, the numbering shall be as for the main line tracks, irrespective of the fact that it also covers loops. 31.5.2 (C) In case of a portal covering Up main line and a number of Up side secondary tracks, the upright which is located near the main track and service the main line shall be numbered with respect to the main track. Other upright shall be given the same number with suffix ‘A’. 31.5.2 (d) The upright of portals in Up yard shall have odd numbers i.e. 2001-3001, 2003-3003 etc. and the upright in Down yard shall have even numbers i.e. 2002-3002, 2004-3004 etc. 31.6 Head span mast. Procedure of numbering the mast of a head span shall be the same as that for portals detailed in 31.5.2 except that the mast of the head span shall be given numbers in 5000, 6000 and 7000 series as detailed in 31.5.2 (a). 31.7 Branch line masts All masts on branch lines taking off from the main line are to be given a prefix letter indicative of the branch line, mast e.g. Pradhankanta-Pathardih which takes off from the main line at Pradhankanta is given a prefix letter ‘P’ which is indicating of Pathardih viz. 70/14 P. 31.8 Alternative numbering Mast on loop/yard lines may also be numbered with a letter/word prefixed indicating the nomenclature of the line e.g. the mast numbers on a goods line in passenger station area may be numbered as G1, G2 etc. below the station code. The mast numbers on engine run-round line may be numbered as EL1, EL2 etc. This method may be adopted when additional lines are provided or wired subsequently. INDIAN RAILWAYS – AC TRACTION MANUAL VOL II PART II 31.9 Switching station masts Mast at the switching station are numbered with the station code of the switching station for example KGP/1 which means Kharagpur Switching Station, mast No. 1. 32.0 Numbering of Equipment 32.1 Abbreviation of equipments To identify the location of the equipments covering OHE and Switching stations a code for identifying the type of equipment followed by a S.No. is given. AT : 25 KV/230V Auxiliary Transformers BT : Booster Transformers BM: Interruptor for main lines BS: Interruptor for yard lines BX: Bus coupler interruptor BC: Bus coupler isolator CB: Circuit Breakers CT: Current Transformers DP: Double pole isolators LA: Lightening arrestor PT: Potential transformer SF: Single pole isolator at Switching Station SP: Single pole isolator at sub-station SM: Isolator for main lines SS: Isolator for secondary lines loops and yards TR: Power transformer. 32.2 Numbering circuit breakers Each power transformer, current transformer, potential transformer is given a serial number in a Railway starting from 01 except 25 kV circuit breakers which shall be according to para 32.2.2. 32.2.1 High voltage (132/110/66KV) circuit breakers are given two digit numbers progressively increasing in the direction of increasing kilometerage starting from 01. For example, the first high voltage circuit breaker will be numbered as CB/01,02,03 32.2.2. 25 kV circuit breakers are given three digit numbers - odd nos. e.g. CB/101, 103, 105 etc. for feeder breakers and even nos. CB/100,102,104 etc. for transformers circuit breakers. 32.3. The serial number of transformers and circuit breakers also follow geographical sequence within a substation/feeding post. Lower number is given for the equipment connecting at less kilometerage and higher number of for the equipment connected to higher kilometerage. 32.4 Interruptors The main line 25 kV interruptors numbered serial wise progressively increasing from a datum point on railway. e.g. BM/01, 02, 03 etc. 32.5 Yard interruptors. The yard line interruptors are numbered serial wise on a railway i.e., BS 01, 02, 03 etc. Where there are different yards for Up and Down direction, the interruptor for Up yard is given odd number and that for Down yard is given even number. INDIAN RAILWAYS – AC TRACTION MANUAL VOL II PART II INDIAN RAILWAYS – AC TRACTION MANUAL VOL II PART II 32.6 Other equipment The number of other equipments is serial wise progressively increasing irrespective of up or down line on a railway preferably according to increasing chainage. 32.7 Numbering of elementary section Elementary section for main line are given a number beginning with the number of interruptor which feeds it (see Fig. A1.21) 32.7.1 The first two/three digits of the number for an elementary section indicate the governing interruptor and last two digit indicate the progressive serial numbers. The progressive serial number for Up line are odd number starting with 01 for example 3401, 3403 etc. and even number for Down line starting with 02 such as 3502, 3504 etc. 32.7.2 Yard elementary sections The elementary section number of yard lines shall be provided with the number of the isolator which controls the feed of the line/s with a prefix ‘X’ For example, if an isolator, no. 118 controls the feed of the lines of the receiving yard the elementary section number of the lines is X 118. 32.7.3 Elementary section for two sides If the line/s are fed by an inter-locked isolator numbering of the elementary section should corresponds to the isolator number which normally feeds the line/s. 32.7.4 Type of number plates The number plates shall be in accordance with drawing No. RE/33/P/7501. INDIAN RAILWAYS – AC TRACTION MANUAL VOL II PART II