Textbook of Production Technology PDF
Document Details
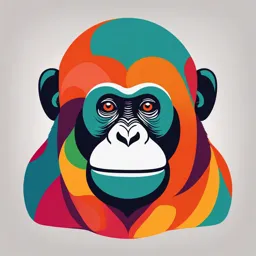
Uploaded by ImaginativePeachTree
STC/JHS
Tags
Related
Summary
This document contains questions and answers related to production technology, covering topics such as material fabrication, engineering plastics, and manufacturing processes. It includes questions on various approaches like welding and machining, along with matching questions and answers.
Full Transcript
800 A Textbook of Production Technology 13. Which of the following are fabricated using engineering plastics ? 1. Surface plate 2. Gears 3. Guideways for machine tools 4. Foundry patterns...
800 A Textbook of Production Technology 13. Which of the following are fabricated using engineering plastics ? 1. Surface plate 2. Gears 3. Guideways for machine tools 4. Foundry patterns Select the correct answer using the codes given below Codes : (a) 1, 2 and 3 (b) 1 (c) 2, 3 and 4 (d) 1, 2, 3 and 4 (Ans. c) 14. Which one of the following is the hardest cutting tool material next only to diamond ? (a) Cemented Carbides (b) Ceramics (c) Silicon (d) Cubic boron nitride (Ans. d) 15. Crater wear on tools always starts at some distance from the tool tip because at that point (a) Cutting fluid does not penerate. (b) normal stress on rake face is maximum (c) temperature is maximum (d) tool strength is minimum (Ans. c) 16. A 31.8 mm H.S.S. drill is used to drill a hole in a cast iron block 100 mmthick at a cutting speed of 20 m/min and feed 0.3 mm/rev. If the overtravel of the drill is 4 mm and approach 9 mm, the time required to drill the hole is (a) 1 min 40 s (b) 1 min 44 s (c) 1 min 49 s (d) 1 min 53 s (Ans. d) 17. A side and face cutter 125 mm diameter has 10 teeth. It operates at a cutting speed of 14 m/ min. with a table traverse 100 mm/min. The feed per tooth of the cutter is (a) 10 mm (b) 2.86 mm (c) 0.286 mm (d) 0.8 mm (Ans. c) 18. Which one is not a method of reducing cutting forces to prevent the overloading of press ? (a) providing shear on die (b) providing shear on panch (c) increasing die clearance (d) stepping punches. (Ans. c) 19. In which one of the following welding techniques is vacuum envrionment required ? (a) Ultrasonic welding (b) Laser beam welding (c) Plasma arc welding (d) Electron beam welding (Ans. d) 20. Match list I (Material) with List II (Application) and select the correct answer using the codes given below the lists : List I List II (Material) (Application) A. Ceramics 1. Construction of Chemical plants B. Refractories 2. Columns and pillars C. Stones 3. Lining of furnaces D. High silica glass 4. Tiles Codes : A B C D (a) 4 3 2 1 (b) 2 1 4 3 (c) 4 1 2 3 (d) 2 3 4 1 (Ans. a) 21. Match list I (Ingredients) with List II (Welding functions) and select the correct answer using the codes given below the lists : List I List II (Ingredients) (Welding functions) A. Silica 1. Arc stabilizer B. Potassium silicate 2. De-oxidizer C. Ferro-silicon 3. Fluxing agent D. Cellulose 4. Gas forming material Appendix III 801 Codes : A B C D (a) 3 4 2 1 (b) 2 1 3 4 (c) 3 1 2 4 (d) 2 4 3 1 (Ans. c) 22. In a CNC machine tool, encoder is used to sense and control (a) table position (b) table velocity (c) spindle speed (d) coxland flow (Ans. a) 23. In rolling a strip between two rolls, the position of the neutral point in the arc of contact does not depend on (a) amount of reduction (b) diameter of the rolls (c) co-efficient of friction (d) material of the rolls (Ans. d) 24. Match list I (NC machine tool systems) with List II (Features) and select the correct answer using the codes given below the lists : List I List II (NC machine tool systems) (Features) A. NC system 1. It has integrated automatic tool changing unit and a component indexing device. B. CNC system 2. A number of machine tools are controlled by a computer. No tape reader, the part programme is trasmitted directly to the ma- chine tool from the computer memory. C. DNC systen 3. The controller consists of soft-wired com- puter and hard-wired logic system. Graphic display of tool path is also possible. D. Machining centre 4. The instructions on tape are prepared in binary decimal form and operated by a se- ries of coded instructions. Code : A B C D (a) 4 2 3 1 (b) 1 3 2 4 (c) 4 3 2 1 (d) 1 2 3 4 (Ans. c) 25. Compare die-casting with investment casting w.r.t. production rate, melting point of work materials and ability of producing complex shaped products. 26. Name three processes of manufacturing long low carbon steel tubes. 27. What are the advantages of submerged arc welding over conventional open air manual arc welding and why ? 28. Why are the lathe-spindles made hollow ? 29. How does application of cutting fluid help in reducing cutting forces and inproving tool life and surface quality ? 30. In which machine tools, teeth of internal spur gears can be cut and which one of those machine tools work fastest ? 31. What are meant by ‘A – 60 – K – 8 – V’ when used for a grinding wheel specification ? 32. What are the major constituents of high speed steel (HSS) and uncoated single carbides which are used as cutting tool materials ? How are these carbide tool inserts manufactured ? 802 A Textbook of Production Technology IES 2003 1. During heat treatment of steel, the hardness of various structures in the increasing order is (A) martensite, fine pearlite, coarse pearlite, spheroidite (B) fine pearlite, coarse pearlite, spheroidite, martensite (C) martensite, coarse pearlite, fine pearlite, spheroidite (D) spheroidite, coarse pearlite, fine pearlite, martensite. (GATE 2003) (Ans. D) 2. Hardness of green sand mould increases with (A) increase in moisture content beyond 6 per cent (B) increase in permeability (C) decrease in permeability (D) increase in both moisture content and permeability (Ans. C) 3. In oxyacetylene gas welding, the temperature at the inner cone of the flame is around (A) 3500°C (B) 3200°C (C) 2900°C (D) 2550°C (Ans. A) 4. Cold working of steel is defined as working (A) at its recrystallisation temperature (B) above its recrystallisation temperature (C) below its recrystallisation temperature (D) at two thirds of the melting temperature of the metal (Ans. C) 5. As tool and work are not in contract in EDM process (A) no relative motion ocurs between them. (B) no wear of tool occurs (C) no power is consumed during metal cutting (D) no force between tool and work occurs (Ans. D) 6. Hardness of steel greatly improves with (A) Annealing (B) Cyaniding (C) normalising (D) tempering (Ans. B) 7. With a solidification factor of 0.97 × 66 s/m2, the solidification time (in seconds) for a spherical casting of 200 mm diameter is (A) 539 (B) 1078 (C) 4311 (D) 3233 (Ans. B) Hint : In chvorinov’s equation 2 ⎛V ⎞ t K ⎜ ⎟ , K 0.97 106 s / m2 ⎝ SA ⎠ 8. Match the following Work material Type of joining P Aluminium 1. Submerged Arc Welding Q Die Steel 2. Soldering R Copper wire 3. Thermit welding S Titanium sheet 4. Atomic Hydrogen Welding 5. Gas Tungsten Arc Welding 6. Laser Beam Weldign (A) (B) (C) (D) P–2 P–6 P–4 P–5 Q–5 Q–3 Q–1 Q–4 R–1 R–4 R–6 R–2 S–3 S–4 S–2 S–6 (Ans. D) IES – 2004 1. Write the Chemical equation for the reaction going on in the oxy-acetylene flame. Where do you get the most part of the oxygen; is it from the cylinder or the atmosphere ? 2. Clearances have to be provided on the press tools. What is the order of clearances for shear- ing operation and deep drawing operation ? On what tool will you provide the clearance in : (i) Punching operation (ii) Blanking operation 3. What is the three high rolling mill ? Indicate the movement of rolls and the workpiece. 4. What are the steps involved in making of carbide tool bits ? What do you understand by the green density of a metal powder compacted part ? What are the chief merits of a bush made by metal powder compaction. 5. An iron-carbon binary allow has 0.5% C by weight. What is this alloy called ? (a) Eutectoid alloy (b) Eutective alloy (c) Hypo-eutectioid alloy (d) Hyper-eutectoid alloy (Ans. c) 6. Match List–I (Name of alloy) with List - II (Major alloying elements) and select the correct answer using the codes given below the list : List – I List – II (Name of alloy) (Major alloying elements) A. Invar 1. Manganese B. Hadfield steel 2. Chromium C. Stellite 3. Nickel D. Stainless steel 4. Tungsten 5. Molybdenum Codes : A B C D (a) 5 1 4 2 (b) 3 2 5 1 (c) 5 2 4 1 (d) 3 1 5 2 (Ans. d) 7. Match-list – I (Name of Treatment) with List – II (media used) and select the correct answer using the codes given below the lists :- List – I List – II (Name of treatment) (Media used) A. Pack Carburising 1. Ammonia gas B. Gas Carburising 2. Sodium Cyanide C. Cyaniding 3. Carburising Compound D. Nitriding 4. Ethane 803 804 A Textbook of Production Technology Codes : A B C D (a) 3 4 2 1 (b) 2 1 3 4 (c) 3 1 2 4 (d) 2 4 3 1 (Ans. a) 8. Consider the following pairs : Heat Treatment Effects on medium Carbon steel 1. Normalising : Grain refinement 2. Full annealing : Uniform grain structure 3. Martempering : Decreased ductility 4. Spheoroidizing : Maximum softness Which of the pairs given above are correctly matched ? (a) 1 and 2 (b) 2 and 3 (c) 3 and 4 (d) 1, 2, 3 and 4 (Ans. : c) 9. Match List – I (Type of Moulding) with list – II (Mechanism involved) and select the correct answer using codes given below the lists : List – I List – II (Type of moulding) (Mechanism involved) A. Compression moulding 1. Mould cavity must be heated to cure the plastic forced into it B. Injected moulding 2. Similar to hydraulic extrusion C. Jet moulding 3. Analogous to hot pressing of powdered metals D. Extrusion moulding 4. Analogous to die casting of metals. Codes : A B C D (a) 2 4 1 3 (b) 3 1 4 2 (c) 2 1 4 3 (d) 3 4 1 2 (Ans. : d) 10. Match List – I (Steel type) with List – II (Product) and select the correct answer by using the codes given below the list : List – I (Steel type) List – II (Product) A. Mild steel 1. Screws B. Tool steel 2. Commercial beams C. Medium Carbon steel 3. Crane hooks D. High Carbon steel 4. Blanking dies Codes : A B C D (a) 2 4 1 3 (b) 3 1 4 2 (c) 2 1 4 3 (d) 3 4 1 2 (Ans. a) Question Paper 2004 805 11. Match List – I (Alloy) with List – II (Application) and select the correct answer using the codes given below the lists :– List – I (Alloy) List – II (Application) A. Silicon steel 1. Marine Bearings B. High Carbon steel 2. Cutting tools C. High speed steel 3. Springs D. Monel metal 4. Transformer laminations Codes : A B C D (a) 1 2 3 4 (b) 4 3 2 1 (c) 4 2 3 1 (d) 1 3 2 4 (Ans. : b) 12. Consider the following statements : In comparison to hot working, in cold working, 1. higher forces are required 2. no heating is required 3. less ductility is required 4. better surface finish is obtained Which of the statements given above are correct ? (a) 1, 2 and 3 (b) 2 and 4 (c) 1 and 3 (d) 2, 3 and 4 (Ans. : b) 13. Consider the following factors : 1. Size and shape that can be produced economically 2. Porosity of the parts produced. 3. Press Capacity 4. High density Which of the above are the limitations of powder metallurgy ? (a) 1, 3 and 4 (b) 2 and 3 (b) 1, 2 and 3 (d) 1 and 2 (Ans. : c) 14. Match List – I (Welding problems) with List – II (Causes) and select the correct answer using codes given below the Lists : List – I (Welding problems ) List – II (Causes) A. Cracking of weld metal 1. Excessive stresses B. Cracking of base metal 2. High joint rigidity C. Porosity 3. Failure to remove slag from previous deposit D. Inclusions 4. Oxidation 5. Excessive H2, O2, N2, in the welding atmosphere Codes : A B C D (a) 2 1 5 3 (b) 3 4 2 1 (c) 2 4 5 3 (d) 3 1 4 2 (Ans. : a) 806 A Textbook of Production Technology 15. Consider the following statements : The size of heat affected zone HAZ) will increase with 1. increased starting temperature 2. increased welding speed 3. increased thermal conductivity of the base metal 4. increase in base metal thickness Which of the statements given above are correct ? (a) 1, 2 and 3 (b) 1 and 3 (c) 1 and 4 (d) 2 and 3 (Ans. b) 16. Consider the following statements :- The magnitude of residual stresses in welding depends upon 1. Design of weldment 2. Support and clamping of components 3. Welding process used. 4. amount of metal melted/deposited. Which of the statements given above are correct ? (a) 1, 2 and 4 (b) 1, 2 and 3 (c) 1 and 3 (d) 2 and 3 (Ans. : a) 17. The cutting speed of a milling cutter while cutting brass is : (a) 45 to 60 m/min (b) 30 to 40 m/min. (c) 25 to 35 m/min (d) 15 to 20 m/min (Ans. : a) 18. Consider the following statements : The helical flute in a twist drill provides the necessary 1. Clearance anagle for the cutting edge. 2. Rake angle for the cutting edge 3. Space for the chip to come out during drilling. 4. Guidance for the drill to enter into the workpiece. Which of the statements given above are correct ? (a) 1 and 2 (b) 2 and 3 (c) 3 and 4 (d) 1 and 4 (Ans. c) 19. For improving the strength of steel at elevated temperature, which one of the following alloying elements is used : (a) Copper (b) Tungsten (c) Aluminium (d) Zinc (Ans. b) 20. Match List – I (cutting tools) with List – II (Features) and select the correct answer using the codes given below the lists : List – I (Cutting tools) List – II (Features) A. Turning tool 1. Chiesel edge B. Reamer 2. Flutes C. Milling cutter 3. Axial relief 4. Side relief Question Paper 2004 807 Codes : A B C A B C (a) 1 2 3 (c) 4 2 3 (b) 4 3 2 (d) 1 3 2 (Ans. b) 21. Match List – I (Milling Problem) with List – II (Probable Causes) and select the correct answer using the codes given below the lists : List – I (Milling problem) List – II (Probable Causes) A.Chatter 1. Too high feed B. Poor surface finish 2. Lack of rigidity in machine, fixtures, bar or workpiece C. Loss of accuracy 3. High cutting load D. Cutter burrs 4. Radial relief too great 5. Not enough lubricant Codes : A B C D A B C D (a) 2 1 5 3 (c) 4 5 2 3 (b) 2 1 3 5 (d) 4 2 3 5 (Ans. b) 22. Consider the following statements with respect to the relief angle of cutting tool : 1. This affects the direction of chip flow. 2. This reduces excessive friction between the tool and workpiece 3. This affects tool life. 4. This allows better access of coolant to the tool-workpiece interface. Which of the state- ments given above are correct ? (a) 1 and 2 (b) 2 and 3 (c) 2 and 4 (d) 3 and 4 (Ans. b) 23. One brand of milling machine has the following two index plates supplied alongwith the indexing head : Plate 1 : 15, 16, 17, 18, 19, 20 hole circles Plate 2 : 21, 23, 27, 29, 31, 33 hole circles It is proposed to mill a spur gear of 28 teeth using simple indexing method. Which one of the following combinations of index plate and number of revolutions is correct ? (a) Plate 1 : 1 revolution and 9 holes in 18 hole circles. (b) Plate 2 : 1 revolution and 9 holes in 21 pole circles. (c) Plate 2 : 1 revolution and 9 holes in 33 hole circles. (d) Plate 1 : 1 revolution and 9 holes in 15 hole circles. (Ans. b) 24. Match List – I with List – II and select the correct answer using the codes given below the lists : List – I List – II A. Plan approach angle 1. Tool face B. Rake angle 2. Tool flank 808 A Textbook of Production Technology C. Clearance angle 3. Tool face and flank D. Wedge angle 4. Cutting edge 5. Tool nose Codes : A B C D A B C D (a) 1 4 2 5 (c) 4 1 2 3 (b) 4 1 3 2 (d) 1 4 3 5 (Ans : c) 25. Match List – I (Cutting tool materials) with List – II (Manufacturing methods) and select the correct answer using the codes given below the list : List – I (Cutting tool materials) List – II (Manufacturing methods) A. HSS 1. Casting B. Stellite 2. Forging C. Cemented Carbide 3. Rolling D. UCON 4. Extrusion 5. Powder metallurgy Codes : A B C D A B C D (a) 3 1 5 2 (c) 3 5 4 2 (b) 2 5 4 3 (d) 2 1 5 3 (Ans. : d) 26. A medium carbon steel workpiece is turned on a lathe at 50 m/min. speed (cutting), 0.8 mm/ rev. feed and 1.5 mm depth of cut. What is the rate of metal removal ? (a) 1000 mm3/min. (b) 60,000 mm3/min. (c) 20,000 mm3/min (d) can not be calculated with the given data. (Ans. : b) 27. Match list – I (Machining processes) with List – II (Operating media) and select the correct answer using the codes given below the lists : List – I (Machining processes) List – II (Operating media) A. Abrasive Jet machining 1. Dielectric B. Electron – beam machining 2. Electrolyte C. Electro-chemical machining 3. Abrasive slurry D. Electro-discharge machining 4. Vacuum 5. Air Codes : A B C D A B C D (a) 5 4 2 1 (c) 4 2 3 5 (b) 4 5 2 1 (d) 2 5 3 4 (Ans. a) Question Paper 2005 809 GATE – 2005 1. Match the items of List I (Equipment) with the items of List II (Process) and select the correct answer using the given codes. List – I (Equipment) List – II (Process) P – Hot Chamber Machine 1 – Cleaning Q – Muller 2 – Core making R – Dielectric Baker 3. Die Casting S – Sand Blaster 4 – Annealing 5 – Sand mixing (A) P–2, Q–1, R–4, S–5 (B) P–4, Q–2, R–3, S–5 (C) P–4, Q–5, R–1, S–2 (D) P–3, Q–5, R–2, S–1 (Ans. D) 2. When the temperature of a solid metal increases, (A) strength of the metal decreases but ductility increases. (B) both strength and ductility of the metal decrease (C) both strength and ductility of the metal increase (D) strength of the metal increases but ductility decreases (Ans. A) 3. The strength of a brazed joint (A) decreases with increase in gap between the two joining surfaces. (B) Increases with increase in gap between the two joining surfaces. (C) decreases upto certain gap between the two joining surfaces beyond which it increases. (D) increases upto certain gap between the two joining surfaces beyond which it decreases (Ans. : D) 4. A zig zag cavity in block of high strength alloy is to be finish machined. This can be carried out by using (A) electric discharge machinery (B) electrochemical machining (C) laser beam machining (D) abrasive flow machining (Ans. :A) 5. Which among the NC operations given below are continuous path operations ? Arc Welding (AW) Milling (M) Drilling (D) Punching in sheet Metal (P) Laser cutting of sheet Metal (LC) Spot welding (SW) (A) AW, LC and M (B) AW, D, LC and M (C) D, LC, P and SW (D) D, LC, and SW (Ans. : A) 6. A 600 mm × 30 mm flat surface of a plate is to be finish machined on a shaper. The plate has been fixed with the 600 mm side along the tool travel direction. If the tool over-reach at each end of the plate is 20 mm, average cutting speed is 8m/min, feed rate is 0.3 mm/stroke and 809 810 A Test Book of Production Technology the ratio of return time to cutting time of tool is 1 : 2, the time required for machining will be (A) 8 minutes (B) 12 minutes (C) 16 minutes (D) 20 minutes (Ans. : B) 7. Spot welding of two 1 mm thick sheets of steel (density = 800 kg/m3) is carried out success- fully by passing a certain amount of current for 0.1 second through the electrodes. The resultant weld nugget formed is 5 mm in diameter and 1.5 mm thick. If the latent heat of fusion of steel is 1400 kJ/kg and the effective resistance in the welding operation is 200 , the current passing through the electrodes is approximately, (A) 1480 A (B) 3300 A (C) 4060 A (D) 9400 A Solution. :– Welding nugget volume 5 1.5 30 mm 2 3 4 Welding nugget mass = 0.008 × 30 = 0.24 gm Heat needed = 0.24 × 1400 = 336 J Now Q = I2Rt 336 = I2× 200 × 10–6 × 0.1 I2 = 16.8 × 106 I = 4100 A (Ans. : C) 8. A mould has a downsprue whose length is 20 cm and the cross-sectional area at the base of the downsprue is 1cm2. The downsprue feeds a horzontal runner leading into the mould cavity of volume 1000 cm3. The time taken to fill the mould cavity will be (A) 4.05 s (B) 5.05 s (C) 6.05 s (D) 7.25 s (Ans. B) Solution. :– Velocity at the bottom of the sprue, V 2 gh 2 981 20 = 198.1 cm/s Now area of cross-section at the base = 1 cm2 A×V×t=Q Now Q = 1000 cm3 1 × 198.1 × t = 1000 t = 5.05 s APPENDIX IV Additional Material IV.I. Sheet-Metal Formability: In sheet metal forming process, a blank (cut from a larger sheet) is formed into various shapes. All sheet metal forming operations involve a pair of tools (punch and die) to form the blank into the desired shape. During sheet metal forming operation, the material undergoes two basic modes of deformations: Mainly stretching and also drawing or bending. Before selecting a forming process, it is important to determine whether the blank can be formed into the desired shape with- out failure or not. This is decided on the basis of what is known as ‘‘Sheet-metal formability’’. It may be defined as the ability of the sheet metal to undergo the desired shape change without failure, such as by necking or tearing. The sheet metal formability depends upon certain sheet metal characteristics as discussed below:- 1. Elongation:- Since the material undergoes stretching and drawing/bending, during form- ing, large uniform elogation is desirable for good formability. At the onset of necking,. True strain, = strain – hardening exponent, n(σ = k, ε n ; k is strength coefficient). Thus, higher the value of n, larger will be the uniform elongation before it begins to neck..m Again, σ C. where is strain rate, m is strain-rate sensitivity exponent and C is the strength coefficient. The magnitude of the strain rate sensitivity exponent, m, significantly influences necking. With an increasing m, the material stretches farther before it fails. Thus, an increasing m delays necking. Elongation is nothing but a measure of the ductility of the material. Thus higher the ductility, higher will be the formability. In addition to uniform elongation and necking, the total elongation of the specimen is also a significant factor in the formability of sheet metals. The total elongation of the material increases with increasing values of n and m. Sheet metal grain size is also important. Grain size affects mechanical properties and it influ- ences the surface appearance of the formed part. The coarser the grains, the rougher is the surface appearance. Formability is also dependent upon; thickness of sheet, friction and lubrication at the punch- die-sheet metal interface, anistropy and yield point elongation. It has been proved that the thicker the sheet, the larger is its formability. However, in actual practice, a thick blank may not bend as easily around small radii without cracking. With well lubricated interface between sheet and punch/die, the strains are more uniformly distributed over the punch. Surface scratches, deep cuts and blemishes can reduce formability and cause premature tearing and failure. Again, the formability of a metal is a function of its tensile strength. The tensile strength and yield point must not be high or too much work will be required for forming the metal. Sheet Formability Tests:- During the various sheet metal forming processes, the stresses and strains developed in the material are quite complex. So, any measure of the formability of the sheet metal on the basis of material properties derived from a simple tension test( for example, % elonga- tion as an index of ductility of the material) is not very accurate. Over the years, a number of tests have been developed to evaluate the formability of a sheet metal. These tests are discussed below:- Cupping Tests:- These are the earliest developed tests. The various tests in this category are:- 1. Erichsen Test:- Here, the standard sheet metal specimen (90 mm wide) is clamped between two ring dies having 27 mm diameter openings. A steel ball or a round punch (of 20 mm diameter) is then hydraulically forced against the sheet until a crack begins to appear on the bottom 811 812 A Textbook of Production Technology face of the specimen as it is stretched into the die opening (Fig. IV. 1). The depth, d, is a measure of the formability of the sheet. 2. Olsen Test :- This test is just similar to the Erichsen test with one difference that the die opening size is 50 mm. Punch 3. Swift Test :- Swift flat bottom cup test is a standard test for deep drawing process. The sheet formability is measured in terms of Limiting Draw Ratio, LDR (See Art. Ring die 4.8.11). 4. Fukui Test :- Erichsen and Olsen d tests mainly evaluate the stretchability and the Swift test the deep drawability of the sheet Sheet specimen metal. However, the actual conditions during Ring die any forming process are quite complex (mainly a combination of stretching and drawing/bending). The Fukui test uses a hemispherical punch and produces a conical cup. Thus; this test provides a combination Fig. IV.1. Erichsen Test. of both stretching and deep drawing. The latest test methods which nearly relate to the actual conditions are discussed below:- 5. Forming Limit Diagrams, FLD:- This is a very useful technique for controlling failure in sheet metal forming and thus giving an accurate forming limit criteria. The surface of the sheet metal specimen is covered with a grid-pattern of circles (typically 2.5 mm to 5 mm is diameter), using electrochemical or photoprinting techniques. During testing, when the sheet gets deformed, the circles distort into ellipses. The major and minor axes of an ellipse give the two principal strain directions during forming. These strains are determined as the % change in the lengths of major and minor axes. These strains at any point on the surface of the sheet are then compared with the Keeler Good win diagram for the material (See Fig. IV. 2). Strain positions above the curve indi- cate failure. For enhanced accuracy, the diameter of circles in the grid can be reduced. (The failure curve for the tension-tension region was determined by Keeler and that for the tension-compression region was determined by Goodwin). The strain distribution can be altered (for example, by chang- ing the dieradius) so that the strain position moves to the safe region. 6. Stretch-Draw Shape analysis:- Here, the forming limit of the sheet metal is determined by the Olsen and Swift cupping tests. Then the specimen is broken into simple shapes and the % of stretch and draw are determined from the geometry. Then, with the help of FLD for the material, the degree of severity of the part can be determined. 7. Formability Charts:- Very useful formability charts have been developed for many pro- cesses, such as, brake forming, linear stretch forming, rubber forming, dimpling, beading and metal spinning etc. 8. Computer-analysis Program:- Just like the bulk deformation processes, computer-aided design and analysis have been applied in determining the sheet metal forming limits. The total program includes: Constitutive relations for the material, a program for analysis of FLD and an analysis program for determining the critical strains. IV. 2 Super-Plastic Forming (SPF): ‘Superplasticity’ refers to large neck-free extensions before fracture, (between 100 and 1000 %) when deforming certain metals and alloys. Extreme examples of superplastic materials are : Bubble gum and molten glass which can be drawn from melt into glass fibres without the fibres necking down. The preconditions for super plastic behaviour of a material are listed under Art. 4.3.12 on ‘‘Super-plastic forging’’. Materials with a high strain- rate sensitivity (0.3 < m > 1.0) exhibit pronounced resistance to necking (Here m is strain-rate.m. sensitivity index in the equation σ C ε ; ε is the strain-rate, for grass, m = 1). Generally, this condition is satisfied in materials with a very fine grain size (of the order of 1 μm) and at deformation Appendix IV 813 temperatures of > 0.4 Tm. Also, for superplastic materials, there is a limiting strain rate (generally below 0.0.1s–1), at which they should be formed. Major Strain, % 160 140 120 100 Failure 80 60 40 20 Safe 40 20 0 20 40 60 80 100 120 – ve Minor strain + ve, % Fig. IV.2. : Forming Limit Diagram. Advantages of SPF :- 1. High ductility and Low flow stress (of the order of 5 to 30 MPa) exist at superplastic condition. These lead to lower tooling costs and forging of difficult-to-work super-alloys (see Art. 4.2.12) or in embossing of fine details in other applications. 2. Forming of complex shapes with fine details and close tolerances. 3. Savings in materials as secondary operations are eliminated. 4. Little or no residual stresses in components. Draw backs:- (i) Very low strain-rates, resulting in large forming times. So, best suited for batch production. (ii) The component material must not be super-plastic at service temperature. Common super-plastic materials used are : - Zn–22Al and Ti – 6Al – 4V. Their bulk defor- mation can be done by – forging, coining, compression moulding (see chapter 11), extrusion and hubbing. Sheet forming of these materials can be done by : thermo-forming, vacuum forming and Blow moulding (see Chapter 11). IV. 3. Peen Forming :- Peen forming is a sheet metal working process utilizing the method of shot preening, which has been discussed in detail under Art. 4.10, along with its advantages and applications in industry. Another very useful application is to produce curvatures on thin metal sheets by striking shots on one side of the sheet. The main product application is the forming of smooth and complex curvatures on aircraft wing skins. When the sheet metal is subjected to shot peening, the surface layer expands, while the bottom layer remains rigid. The shots may be of cast steel about 2.5 mm is diameter striking the sheet surface at about 60 m/s. For thicker sections, the shots diameter can be as larger as 6 mm. IV. 4. Some Numerical Problems :- Problem 1 : Determine the choke area to fill C.I. castings neglecting directional flow and flow losses. Casting mass = 30 kg; t = 20s : = 0.007 gm / mm3, h = 160 mm ; Gate = Top gate. m 2 Solution : CA = c t 2gH ,mm Now c for taper sprue = 0.85 and H = h = 160 mm for top gate 814 A Textbook of Production Technology 30 1000 CA = 141 mm 2 0.85 0.007 20 2 9810 160 Diameter = 13.4 mm Problem 2 : Two sheets of L.C. steel with thickness = 1.50 mm each are spot welded by passing a current of 10,000 A for 5 Hz to 50 Hz supply. The maximum indentation is 10% of sheet thickness and density of spot weld nugget is 0.008 gm/mm3. If 1380 J are required to melt 1 gm of steel, find the % of heat actually utilized in making the spot weld. Assume effective resistance as 200 and diameter of nugget d = 6 t to determine nugget diameter. Also assume the nugget size to be equal to metal between the two electrodes. (GATE, 1992) Solution : Heat developed, H = I2 R t 5 = (10000)2 × 200 × 10–6 × 50 = 2000 J Diameter of nugget, dn = 6 t = 6 × 1.50 = 7.35 mm Height of nugget = 2 × t × (1 – % indentation) = 2 × 1.5 × (1 – 0.1 ) = 2.7 mm Volume of formed nugget = 7.352 × 2.7 × = 114.56 mm3 4 Mass = 114.56 × 0.008 = 0.91648 gm Heat required to melt = 0.91648 × 1380 = 1264.7424 J 1264.7424 % heat utilization = = 63.237% 2000 Problem 3 : Calculate the suitable gear train for cutting 8 TPI in a lathe with a lead screw having 4 TPI. Driver teeth P Solution : Ratio icg = Driven teeth L 1 P = Pitch of screw thread to be cut = 8 1 L = Pitch of lead screw = 4 4 45 20 icg = = = 8 85 40 Driver gear on spindle = 20 teeth Driven gear on lead screw = 40 teeth. Problem 4 : Determine the dimensions of the pattern for the casting: 300 × 200 × 150 mm cuboid with a central hole of 100 mm diameter. Material is C.I. Consider only the shrinkage allowance of 20 mm / m. Solution : Shrinkage allowance = 20 mm / m =0.02 mm / mm. Outer dimensions of the pattern = 306 × 204 × 153 mm Diameter of hole in the pattern = 100 – 2 = 98 mm. Problem 5 : Find the dimensions of the pattern by considering draft allowance also, which is 1° for external surfaces and 3° for internal surfaces. Solution : We know that the draft allowance is provided only on the vertical surfaces. Draft allowance for exterior surface = 153 tan 1° = 4 mm / side Draft allowance for interior surface = 153 tan 3° = 8 mm / side It is also clear from Fig. 3.8 that after the provision of draft allowance, the dimension of the pattern is minimum at the parting line for exterior surfaces and maximum at the parting line for interior surfaces. Top outer dimension of the pattern = 306 + 2 × 4 = 314 mm and = 204 + 2 × 4 = 212 mm and top inner dimension of the pattern hole = 98 – 2 × 8 = 82 mm Appendix IV 815 IV.5 Hydraulic Drive for Shapers: There are two systems of hydraulic drive for shapers. Constant pressure system (Fig. 8.3 Art. 8.2.1) and the constant volume system. The pump used in the constant pressure system is of the plunger type and by varying its stroke, the rate of oil flow and its pressure can be varied as per the need of the machine. In the constant volume system, Fig. IV.3, a fixed quantity of oil is delivered by a gear or vane pump to both the sides of the piston. The effective area of the piston on the head side is smaller than on the cover side (due to the presence of piston rod), the return stroke will be faster, since volume of oil /unit time = velocity × area of cross-section m / s 3 m / s m2 Or, as the pump is a constant discharge one, the same amount of oil is pumped into smaller volume. The pressure of oil is risen automatically which increases the speed during return stroke. Again, the speed of the cutting stroke can be varied by a throttle valve in the discharge pipe from the head end of the cylinder. By restricting the flow of oil, the cutting speed can be reduced without affecting the ram return speed. A relief valve is provided in the system to permit excess oil delivered by the pump to return to the reservoir. The constant pressure system is preferred for heavy and variable duty, where as, the constant volume system is favoured for machines not needing excessive power or wide variations in speed. Cutting Stroke Clapper Piston Rod Return Box Cylinder Ram Stroke Piston Reversing Tool Dog Reversing Lever Valve Chamber Relief valve Throttle valve Oil Pump Oil Reservoir Fig. IV.3 Hydraulic Shaper IV.6 Creep Feed Grinding: Conventional grinding is considered to be a finishing process (MRR being very low). To get higher MRR in grinding, a few techniques have been developed. One such method is Creep feed grinding where depth of cut is quite big at a very slow feed rate (opposite to that for conventional grinding). The method has been developed for machining Ni- alloys in Aircraft industry. Grinding wheels are of extremely hard material such as CBN or diamond held in metal matrix. These materials are prone to damage by vibrations and Chatter, but the large contact area of the process reduces this tendency, while the harder material retains it shape better than with the conventional approach to grinding. IV.7 Some Special Milling Operations:- (a) Milling of Helical Grooves (Cutting of helical teeth) : To facilitate the cutter to cut helical grooves, the workpiece must be given two simultaneous motions normal to each other : the linear motion along its axis and a rotary motion. The workpiece is held in the dividing head (mounted on the machine table) whihc is connected by means of gears to the table feed screw of the machine. 816 A Textbook of Production Technology When the table feed screw rotates, the spindle of the dividing head and hence the work will rotate through change gears, worm and worm wheel of the dividing head. Also, when the table feed screw rotates in the nut, the machine table and hence the dividing head has linear motion.The milling cutter is mounted on the arbor of the machine. To cut the helix, it is necessary to swing the machine table through an angle equal to the helix angle, on the vetical axis. Due to this, the spiral grooves are cut on a universal milling machine. Fig. (IV).4. Change Gears Spindle of the Machine Dividing Head b Gear Blank Disc Gear Cutter Tail Stock c Lead Scrow a z 1 Arbor d Machine Table Fig. IV.4. Milling of spiral grooves. The helix angle of the groove on the job is given as, d tan L where d is the diameter of the job and L is the lead of the helix. The helix angle is the angle between the tangent to the thread helix on the pitch cylinder and the axis of the job. Supposing the gear ratio between the table feed screw and the worm shaft (of the dividing head) is 1 : 1. Then, one revolution of table feed screw will rotate the worm shaft through one 1 revolution. The dividing head spindle and hence the work will rotate through of a revolution. 40 That is, for the work to complete one revolution, the worm shaft and hence the table feed screw will make 40 revolutions. If “p” is the pitch of the table feed screw, then, the distance travelled by the the table feed screw for one revolution of the work will be 40p. This is called the “Lead of the machine”. Hence, the lead of the machine is defined as the distance travelled by the machine table corresponding to one complete revolution of the dividing head spindle (and hence of the work) when the gear ratio between the table feed screw and worm shaft is 1 : 1. Thus, Lead of helix will be = Lead of machine = 40p. The diameter of the job and the lead of the helix to be cut will determine the setting of the machine and the gear ratio. The hand of the helix will determine whether an idler is needed or not in the gear train. The work must rotate left handed for left hand helix and right handed for right hand helix. Thus, for right handed helix, the table feed screw and the worm shaft should rotated in the same direction and for left handed helix, they should rotate in the opposite directions. a c Drivers Gear ratio b d Driven Lead of the machine Lead of the helix be cut