Tablet Machines PDF
Document Details
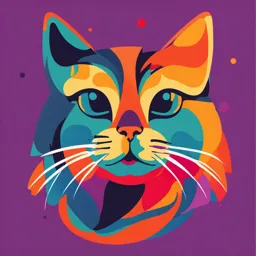
Uploaded by EncouragingIris1234
Tags
Related
- Advanced Machining Test #1 Winter Semester 2024 PDF
- Casino and Gaming PDF
- Instrumental Drawing Lecture Notes PDF
- Sharjah Maritime Academy Electrical Machines Student Workbook Fall 2024/2025 PDF
- Loi sur les mécaniciens de machines fixes (Québec) PDF
- Operating System 2024-25 BCA30110 Module IV (OS) PDF
Summary
This document provides an overview of tablet machines, including single punch and rotary types. It details common manufacturing problems like capping, picking, and mottling, along with their causes and solutions. The document discusses the importance of proper tablet manufacturing for quality and safety.
Full Transcript
# **INDUSTRIAL PHARMACY** ## **TABLET MACHINES** There are 2 types of tablet machines: 1. **Single Punch Tablet Machine:** It possesses one die and one pair of punches (upper punch and lower punch). The powder is held in a hopper which is connected to a hopper shoe located above the die. The hopp...
# **INDUSTRIAL PHARMACY** ## **TABLET MACHINES** There are 2 types of tablet machines: 1. **Single Punch Tablet Machine:** It possesses one die and one pair of punches (upper punch and lower punch). The powder is held in a hopper which is connected to a hopper shoe located above the die. The hopper shoe moves to and far over the die by rotational movement. When the hopper shoe is located over the die, the powder is fed into the die by gravity. The amount of powder filled into the die is controlled by the position of the lower punch. When the hopper shoe is located beside the die, the upper punch descends and the powder is compressed. The lower punch remains stationary during compression and the pressure is thus applied only by the upper punch and controlled by the upper punch displacement. After ejection, the tablet is pushed away by the hopper shoe as it moves back to the die for the next tablet. The output of tablets from single punch tablet machine is about 200 tablets/min. This type of machines is used mainly for small scale production and for research purposes. 2. **Rotary Tablet Machine:** This type is used for large scale production. Tablets output of over 16,000 tablet/min can be achieved by rotary machines. A rotary press operates with a number of dies and sets of punches which can vary from 3 for small rotary machines up to 60 or more for large machines. The dies are fixed in a circle in what is called die table. Both the die table and the punches rotate together during operation of the machine so that one die is always associated with one pair of punches. During tablet compression both punches operate by vertical movement. **Note:** the force that applied during tablet compression can be measured in both single punch and rotary machines by using certain device called “strain gauge”. ## **Manufacturing problems** Below are some problems that might happen during or after tablet manufacturing: ### **I. Capping:** Capping is a term used to describe the partial or complete separation of the top or bottom crowns of a tablet from the main body. Usually this problem is readily appearing immediately after compression. However, capping may occur hours or even days later. Subjecting the tablets to friability test is the quickest way of discovering such problem. Capping is caused by the entrapped air within the tablet. **Causes and solutions:** 1. High tableting rate and application of high pressure during compression. To prevent this point, the formulator should slow the tableting rate and reduce the final pressure. 2. Over drying of granules. A certain percentage of moisture is essential for good compaction while over drying causes lack of cohesion. To solve this problem, avoid over drying of granules (The water content of the granules should be between 2-4%). 3. Shape of the punch. Deep concave punches often cause capping because the curved part of the produced tablets expands easily while their bodies cannot. This problem can be solved by using flat punches. 4. Overwork of the dies. The dies develop a wear ring in the area of compression. The tablets that are compressed in this area (wear ring) have diameter that is too large to pass easily through the narrow portion of the die above the ring. Upon ejection, this constriction causes the tablet to cap. The solution of this problem is by turning the die over so that the compression occurs in unworn area above the ring. 5. Capping may be encountered in D.C. because some materials have poor compressibility. Changing these materials or using suitable binder may solve this problem. **Note:** Capping is encountered more commonly in single punch than in rotary machines because in the latter the compression is gradual that allows the entrapped air among the particles to escape. ### **II. Picking:** Is the sticking of part of the tablet on the surface of the punch. To solve this problem, the followings are useful: 1. Change the punch with one that covered with chromium because this metal is smooth and non adherent. 2. Increase the amount of the lubricant or change it to another one. 3. Increase the amount of the binder or change it to more effective one (to make the granules stronger and less adherent than before). 4. Excessive moisture may be responsible for sticking and further drying of granulation is then required. ### **III. Mottling:** It is unequal distribution of color on the tablet. **Causes and solutions:** 1. The drug or its degradation products have different color from that of the excipients. One can avoid this problem by using a coloring agent to mask the mottled appearance. 2. Migration of the dye to the surface of granules during the drying process. To overcome this problem, you have to do one of the followings: * Change the solvent. For ex., if an aqueous solution was used, change it to alcoholic one. * Reduce the drying temperature. * Reduce the particle size of the colorant (if lakes were used). ### **IV. Weight variation:** It is a case at which the weight of individual tablets differs from each other. It is an important processing problem. The weight of a tablet is normally determined by the amount of granules in the die at the moment of compression. Therefore, anything that alters the die filling can cause weight variation. **Causes and treatment:** 1. There is no uniform size distribution of the granules. To avoid this situation, ensure uniform size distribution of the granules. 2. Lower punch defect that causes difference in the fill from time to time. 3. Poor flow (very important factor). Poor flow can be treated by the use of glidant. ### **V. Hardness variation:** Tablet hardness normally depends on the weight of the granules in the die and the force of compression. Hardness variation is a problem that has the same causes as weight variation. Therefore, the solution of this problem is the same as that mentioned for weight variation. ## **Tablet evaluation and quality control** To ensure the proper quality of tablets, evaluation of tablet's chemical and physical properties must be made. The following are tests used in the quality control of tablets: 1. **General appearance:** The general appearance and overall elegance is essential for consumer acceptance. The general appearance test involves the assessment of a number of properties such as tablet shape, size, color, odor, taste, surface texture and other related properties. Tablet odor is an example. Abnormal odor usually reflects physical or chemical instability, e.g., odor of acetic acid from aspirin tablets reflects the hydrolysis of aspirin to salicylic acid and acetic acid. 2. **Hardness (Crushing strength):** Hardness is the force required to crush a tablet. Tablets require certain strength to withstand the mechanical shocks of manufacturing and shipping. The monitoring of tablet hardness is of special importance for drugs that are sensitive to change in dissolution profile as a function of the hardness. Increasing the compression force leads to comparable increase in the hardness which in turn decreases the dissolution rate. This decrease in the dissolution rate happens because increasing the compression force leads to decrease the porosity of the tablet, thus decreases the ability of the GI fluids to penetrate the tablet therefore, decrease the disintegrant efficacy. It is worth to mention that tablet hardness also affected by die filling (weight). Increasing the die filling leads to increasing tablet hardness. The accepted range of the hardness is as follows: * Conventional tablet: 4-8 kg * Chewable tablet: 3 kg * Sustained releases: 10-20 kg 3. **Friability test:** Friability is the powdering from the surface of the tablet as a result of friction that comes from handling, shipping and so on. Unlike hardness, friability test measures the mechanical strength of the tablet surface. Friability is affected by the moisture content of the tablets. Over drying of granules produce friable tablets; therefore the moisture content must be controlled. Friability can be measured by a device known as Roche Friabilator. The accepted range of friability is 1% above which the tablets patch should be rejected. The patch should also be rejected if capping is observed regardless of the percentage of friability. Chewable, orodispersible and effervescent tablets are already friable therefore, they are not subjected for this test. 4. **Disintegration test:** It is the time required for a tablet to break completely into small fragments that can pass through the certain sieve size. Tablet disintegration is an important step that precedes the dissolution process. Therefore, the disintegration test is an important test to give an idea (in vitro) about tablets ability to disintegrate (in vivo) and thus, provide adequate bioavailability. It is found that rapid dissolution of a drug associated mostly with rapid disintegration, but the reverse is not true. The disintegration test is carried out by disintegration apparatus. 5. **Dissolution test:** This test specifies the amount of the active ingredient that released in certain time. The dissolution test is done because the disintegration test alone is not enough since the disintegrated fragment of the tablet may not release the drug at appropriate rate. ## **Drug release from the tablets can be measured by two methods:** 1. **In vivo method**: It is a direct method in which a blood sample is taken from the patients and analyzed by suitable technique (bioavailability). Sometimes, this method is not preferred due to the following reasons: * Require highly skilled personnel. * Large variation and percentage of error (because it deals with humans). * High cost. 2. **In vitro method**: It is indirect method that uses instruments instead of humans to study the release of the drug. This method is easy and free from the above disadvantages. It utilizes the dissolution test apparatus for testing the drug release. **Note 1:** For each drug, there is a specific monograph in the USP or BP specifies all the required conditions to perform the dissolution test such as type of the medium to be used, its volume, speed of stirring, time intervals (sample withdrawal, method of analysis (UV, HPLC or titration), type of the apparatus (apparatus I or apparatus II) and so on. For example, the conditions to test methyl dopa tablets in USP are as follows: apparatus II, simulated gastric fluid 900 ml, 50 rpm and 20 min time interval. To pass the test successfully, the dissolved amount of methly dopa after 20 min is not less than 80% of the labeled amount assayed by UV spectroscopy. **Note 2:** When the dissolution test is done, there is no need to perform the disintegration test (but the reverse is not true) because the dissolution test gives a clearer picture about the drug release and bioavailability than the disintegration test. **Note 3:** The release profile can be plotted using the dissolution data as shown in the following figure: **[Image Description: A graph, with "Time (min)" on the x-axis and "% Released" on the y-axis, shows the percentage of drug released over time. The line on the graph starts at zero and increases to around 80% at 10 minutes and stays at that level for the rest of the time.]** ### **6. Weight variation:** The weight of the tablets is measured to ensure that the tablets contain the proper amount of the active ingredient. The USP weight variation test is run by weighing 20 tablets individually, calculating the average weight and comparing the individual tablets weights with the average. The tablets pass the test if no more than two tablets are outside the limit. The limit depends on the weight of tablets as shown in the following table (not for save): | Average tablet weight (mg) | Limit (%) | | ------------------------ | ---------- | | 130 or less | ± 10 | | 130-324 | ± 7.5 | | 324 or more | ± 5 | The above limits are plus minus. For example, if the average tablet weight of certain tablets is 500 mg then, the limit is 5%, i.e., 475-525 mg and the twenty tablets should lie within this range to pass the weight variation test. It is worth to mention that the weight variation test is valuable only if the ratio of the active ingredient in the tablet is 90% or more (e.g., aspirin or paracetamol tablets). While for moderate and low dose drugs, content uniformity test is essential. ### **7. Content uniformity:** It is performed to ensure that the tablets contain the correct amount of the active ingredient. This test is more accurate than the weight variation test therefore, when content uniformity test is done, there is no need to for weight variation test (but the reverse is not true).