Chapter 9 Phase Diagrams PDF
Document Details
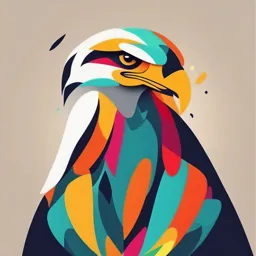
Uploaded by RationalPansy
Cuyamaca College
Tags
Summary
This chapter discusses phase diagrams and their applications in material science, particularly in understanding the properties of alloys. It details concepts such as solubility limits, solid solutions, and phase transformations. The chapter also addresses the importance of phase diagrams in various metallurgical processes.
Full Transcript
JWCL187_ch08_234-280.qxd 9/16/09 6:46 PM Page 280 280 Chapter 8 / Failure values in relation to those for the metal al- 8.D5 For an 18-8 Mo stainless steel (Figure 8.35), loys that are tabulated in Table 8.4. p...
JWCL187_ch08_234-280.qxd 9/16/09 6:46 PM Page 280 280 Chapter 8 / Failure values in relation to those for the metal al- 8.D5 For an 18-8 Mo stainless steel (Figure 8.35), loys that are tabulated in Table 8.4. predict the time to rupture for a component that is subjected to a stress of 80 MPa (11,600 Data Extrapolation Methods psi) at 700!C (973 K). 8.D3 An S-590 alloy component (Figure 8.32) 8.D6 Consider an 18-8 Mo stainless steel compo- must have a creep rupture lifetime of at least nent (Figure 8.35) that is exposed to a 100 days at 500!C (773 K). Compute the max- temperature of 500!C (773 K). What is the imum allowable stress level. maximum allowable stress level for a rupture 8.D4 Consider an S-590 alloy component (Figure lifetime of 5 years? 20 years? 8.32) that is subjected to a stress of 200 MPa (29,000 psi). At what temperature will the rupture lifetime be 500 h? Figure 8.35 Logarithm stress versus the Larson–Miller 103 T(20 + log tr)(°R–h) parameter for an 18-8 Mo stainless steel. (From F. R. Larson and J. Miller, Trans. ASME, 74, 765, 1952. 25 30 35 40 45 50 100 Reprinted by permission of ASME.) Stress (103 psi) Stress (MPa) 100 10 10 1 12 16 20 24 28 103 T(20 + log tr)(K–h) JWCL187_ch09_281-341.qxd 11/12/09 7:11 PM Page 281 Chapter 9 Phase Diagrams T he graph below is the phase diagram for pure H2O. Parameters plotted are external pressure (vertical axis, scaled logarithmically) versus temperature. In a sense this diagram is a map wherein regions for the three familiar phases—solid (ice), liquid (water), and vapor (steam)—are delineated. The three red curves represent phase boundaries that define the regions. A photograph located in each region shows an example of its phase—ice cubes, liquid water being poured into a glass, and steam that is spewing forth from a kettle. (Photographs courtesy of iStockphoto.) 1,000 100 Liquid (Water) 10 Solid Pressure (atm) (Ice) 1.0 0.1 Vapor 0.01 (Steam) 0.001 !20 0 20 40 60 80 100 120 Temperature (°C) 281 JWCL187_ch09_281-341.qxd 9/18/09 11:54 AM Page 282 WHY STUDY Phase Diagrams? One reason that a knowledge and understanding of illustrated by the phenomenon of precipitation hard- phase diagrams is important to the engineer relates to ening (Section 11.9). the design and control of heat-treating procedures; In the processing/structure/properties/perform- some properties of materials are functions of their mi- ance scheme, reasons for studying phase diagrams are crostructures, and, consequently, of their thermal his- as follows: tories. Even though most phase diagrams represent Concepts discussed in this chapter provide a foun- stable (or equilibrium) states and microstructures, they dation that is necessary for us to understand phase are nevertheless useful in understanding the develop- transformations that occur in steel alloys, as well as ment and preservation of nonequilibrium structures the consequences of these transformations—that is, and their attendant properties; it is often the case microstructural and property alterations (as present- that these properties are more desirable than those ed in Chapter 10). associated with the equilibrium state. This is aptly Learning Objectives After studying this chapter you should be able to do the following: 1. (a) Schematically sketch simple isomorphous (b) write reactions for all these transformations and eutectic phase diagrams. for either heating or cooling. (b) On these diagrams label the various phase 4. Given the composition of an iron–carbon alloy regions. containing between 0.022 wt% C and 2.14 wt% C, (c) Label liquidus, solidus, and solvus lines. be able to 2. Given a binary phase diagram, the composition (a) specify whether the alloy is hypoeutectoid of an alloy, its temperature, and assuming that or hypereutectoid, the alloy is at equilibrium, determine (b) name the proeutectoid phase, (a) what phase(s) is (are) present, (c) compute the mass fractions of proeutectoid (b) the composition(s) of the phase(s), and phase and pearlite, and (c) the mass fraction(s) of the phase(s). (d) make a schematic diagram of the microstruc- 3. For some given binary phase diagram, do the ture at a temperature just below the following: eutectoid. (a) locate the temperatures and compositions of all eutectic, eutectoid, peritectic, and con- gruent phase transformations; and 9.1 INTRODUCTION The understanding of phase diagrams for alloy systems is extremely important because there is a strong correlation between microstructure and mechanical properties, and the development of microstructure of an alloy is related to the char- acteristics of its phase diagram. In addition, phase diagrams provide valuable information about melting, casting, crystallization, and other phenomena. This chapter presents and discusses the following topics: (1) terminology asso- ciated with phase diagrams and phase transformations; (2) pressure–temperature phase diagrams for pure materials; (3) the interpretation of phase diagrams; (4) some of the common and relatively simple binary phase diagrams, including that for the iron–carbon system; and (5) the development of equilibrium microstruc- tures, upon cooling, for several situations. 282 JWCL187_ch09_281-341.qxd 9/18/09 11:54 AM Page 283 9.2 Solubility Limit 283 D e f i n i t i o n s a n d B a s i c C o n c e pt s It is necessary to establish a foundation of definitions and basic concepts relating to alloys, phases, and equilibrium before delving into the interpretation and uti- component lization of phase diagrams. The term component is frequently used in this discus- sion; components are pure metals and/or compounds of which an alloy is composed. For example, in a copper–zinc brass, the components are Cu and Zn. Solute and sol- vent, which are also common terms, were defined in Section 4.3. Another term used system in this context is system, which has two meanings. First, system may refer to a spe- cific body of material under consideration (e.g., a ladle of molten steel). Or it may relate to the series of possible alloys consisting of the same components, but with- out regard to alloy composition (e.g., the iron–carbon system). The concept of a solid solution was introduced in Section 4.3. By way of review, a solid solution consists of atoms of at least two different types; the solute atoms occupy either substitutional or interstitial positions in the solvent lattice, and the crystal structure of the solvent is maintained. 9.2 SOLUBILITY LIMIT For many alloy systems and at some specific temperature, there is a maximum con- centration of solute atoms that may dissolve in the solvent to form a solid solution; this solubility limit is called a solubility limit. The addition of solute in excess of this solubility limit results in the formation of another solid solution or compound that has a distinctly different composition. To illustrate this concept, consider the sugar–water (C12H22O11–H2O) sys- tem. Initially, as sugar is added to water, a sugar–water solution or syrup forms.As more sugar is introduced, the solution becomes more concentrated, until the solubility limit is reached or the solution becomes saturated with sugar. At this time the solution is not capable of dissolving any more sugar, and further additions simply settle to the bot- tom of the container. Thus, the system now consists of two separate substances: a sugar–water syrup liquid solution and solid crystals of undissolved sugar. This solubility limit of sugar in water depends on the temperature of the water and may be represented in graphical form on a plot of temperature along the or- dinate and composition (in weight percent sugar) along the abscissa, as shown in Figure 9.1. Along the composition axis, increasing sugar concentration is from left to right, and percentage of water is read from right to left. Because only two 100 Figure 9.1 The 200 solubility of sugar (C12H22O11) in a 80 Solubility limit sugar–water syrup. 150 Temperature (°C) Temperature (°F) 60 Liquid solution (syrup) Liquid solution + 40 solid 100 sugar 20 50 0 Sugar 0 20 40 60 80 100 Water 100 80 60 40 20 0 Composition (wt%) JWCL187_ch09_281-341.qxd 9/18/09 11:54 AM Page 284 284 Chapter 9 / Phase Diagrams components are involved (sugar and water), the sum of the concentrations at any composition will equal 100 wt%. The solubility limit is represented as the nearly vertical line in the figure. For compositions and temperatures to the left of the sol- ubility line, only the syrup liquid solution exists; to the right of the line, syrup and solid sugar coexist. The solubility limit at some temperature is the composition that corresponds to the intersection of the given temperature coordinate and the sol- ubility limit line. For example, at 20!C the maximum solubility of sugar in water is 65 wt%. As Figure 9.1 indicates, the solubility limit increases slightly with rising temperature. 9.3 PHASES phase Also critical to the understanding of phase diagrams is the concept of a phase. A phase may be defined as a homogeneous portion of a system that has uniform phys- ical and chemical characteristics. Every pure material is considered to be a phase; so also is every solid, liquid, and gaseous solution. For example, the sugar–water syrup solution just discussed is one phase, and solid sugar is another. Each has dif- ferent physical properties (one is a liquid, the other is a solid); furthermore, each is different chemically (i.e., has a different chemical composition); one is virtually pure sugar, the other is a solution of H2O and C12H22O11. If more than one phase is pres- ent in a given system, each will have its own distinct properties, and a boundary separating the phases will exist across which there will be a discontinuous and abrupt change in physical and/or chemical characteristics. When two phases are present in a system, it is not necessary that there be a difference in both physical and chemi- cal properties; a disparity in one or the other set of properties is sufficient. When water and ice are present in a container, two separate phases exist; they are physi- cally dissimilar (one is a solid, the other is a liquid) but identical in chemical makeup. Also, when a substance can exist in two or more polymorphic forms (e.g., having both FCC and BCC structures), each of these structures is a separate phase because their respective physical characteristics differ. Sometimes, a single-phase system is termed homogeneous. Systems composed of two or more phases are termed mixtures or heterogeneous systems. Most metal- lic alloys and, for that matter, ceramic, polymeric, and composite systems are heterogeneous. Ordinarily, the phases interact in such a way that the property com- bination of the multiphase system is different from, and more attractive than, either of the individual phases. 9.4 MICROSTRUCTURE Many times, the physical properties and, in particular, the mechanical behavior of a material depend on the microstructure. Microstructure is subject to direct micro- scopic observation, using optical or electron microscopes; this topic was touched on in Sections 4.9 and 4.10. In metal alloys, microstructure is characterized by the num- ber of phases present, their proportions, and the manner in which they are distrib- uted or arranged. The microstructure of an alloy depends on such variables as the alloying elements present, their concentrations, and the heat treatment of the alloy (i.e., the temperature, the heating time at temperature, and the rate of cooling to room temperature). The procedure of specimen preparation for microscopic examination was briefly outlined in Section 4.10. After appropriate polishing and etching, the different phases may be distinguished by their appearance. For example, for a two-phase JWCL187_ch09_281-341.qxd 9/18/09 11:54 AM Page 285 9.5 Phase Equilibria 285 alloy, one phase may appear light and the other phase dark. When only a single phase or solid solution is present, the texture will be uniform, except for grain boundaries that may be revealed (Figure 4.14b). 9.5 PHASE EQUILIBRIA equilibrium Equilibrium is another essential concept that is best described in terms of a ther- modynamic quantity called the free energy. In brief, free energy is a function of the free energy internal energy of a system, and also the randomness or disorder of the atoms or molecules (or entropy). A system is at equilibrium if its free energy is at a mini- mum under some specified combination of temperature, pressure, and composition. In a macroscopic sense, this means that the characteristics of the system do not change with time but persist indefinitely; that is, the system is stable. A change in temperature, pressure, and/or composition for a system in equilibrium will result in an increase in the free energy and in a possible spontaneous change to another state whereby the free energy is lowered. phase equilibrium The term phase equilibrium, often used in the context of this discussion, refers to equilibrium as it applies to systems in which more than one phase may exist. Phase equilibrium is reflected by a constancy with time in the phase characteristics of a system. Perhaps an example best illustrates this concept. Suppose that a sugar–water syrup is contained in a closed vessel and the solution is in contact with solid sugar at 20!C. If the system is at equilibrium, the composition of the syrup is 65 wt% C12H22O11–35 wt% H2O (Figure 9.1), and the amounts and compositions of the syrup and solid sugar will remain constant with time. If the temperature of the system is suddenly raised—say, to 100!C—this equilibrium or balance is tem- porarily upset in that the solubility limit has been increased to 80 wt% C12H22O11 (Figure 9.1). Thus, some of the solid sugar will go into solution in the syrup. This will continue until the new equilibrium syrup concentration is established at the higher temperature. This sugar–syrup example illustrates the principle of phase equilibrium using a liquid–solid system. In many metallurgical and materials systems of interest, phase equilibrium involves just solid phases. In this regard the state of the system is re- flected in the characteristics of the microstructure, which necessarily include not only the phases present and their compositions but, in addition, the relative phase amounts and their spatial arrangement or distribution. Free energy considerations and diagrams similar to Figure 9.1 provide infor- mation about the equilibrium characteristics of a particular system, which is im- portant, but they do not indicate the time period necessary for the attainment of a new equilibrium state. It is often the case, especially in solid systems, that a state of equilibrium is never completely achieved because the rate of approach to equilib- metastable rium is extremely slow; such a system is said to be in a nonequilibrium or metastable state. A metastable state or microstructure may persist indefinitely, experiencing only extremely slight and almost imperceptible changes as time progresses. Often, metastable structures are of more practical significance than equilibrium ones. For example, some steel and aluminum alloys rely for their strength on the develop- ment of metastable microstructures during carefully designed heat treatments (Sec- tions 10.5 and 11.9). Thus not only is an understanding of equilibrium states and structures impor- tant, but also the speed or rate at which they are established and the factors that affect the rate must be considered. This chapter is devoted almost exclusively to equilibrium structures; the treatment of reaction rates and nonequilibrium struc- tures is deferred to Chapter 10 and Section 11.9. JWCL187_ch09_281-341.qxd 9/18/09 11:54 AM Page 286 286 Chapter 9 / Phase Diagrams Concept Check 9.1 What is the difference between the states of phase equilibrium and metastability? [The answer may be found at www.wiley.com/college/callister (Student Companion Site).] 9.6 ONE-COMPONENT (OR UNARY) PHASE DIAGRAMS Much of the information about the control of the phase structure of a particular phase diagram system is conveniently and concisely displayed in what is called a phase diagram, also often termed an equilibrium diagram. Now, there are three externally control- lable parameters that will affect phase structure—temperature, pressure, and com- position—and phase diagrams are constructed when various combinations of these parameters are plotted against one another. Perhaps the simplest and easiest type of phase diagram to understand is that for a one-component system, in which composition is held constant (i.e., the phase diagram is for a pure substance); this means that pressure and temperature are the variables. This one-component phase diagram (or unary phase diagram) [sometimes also called a pressure–temperature (or P–T) diagram] is represented as a two- dimensional plot of pressure (ordinate, or vertical axis) versus temperature (ab- scissa, or horizontal axis). Most often, the pressure axis is scaled logarithmically. We illustrate this type of phase diagram and demonstrate its interpretation us- ing as an example the one for H2O, which is shown in Figure 9.2. Here it may be noted that regions for three different phases—solid, liquid, and vapor—are delin- eated on the plot. Each of the phases will exist under equilibrium conditions over the temperature–pressure ranges of its corresponding area. Furthermore, the three curves shown on the plot (labeled aO, bO, and cO) are phase boundaries; at any point on one of these curves, the two phases on either side of the curve are in equi- librium (or coexist) with one another. That is, equilibrium between solid and vapor 1,000 b 100 Liquid 10 Solid Pressure (atm) (Water) c (Ice) 2 3 1.0 0.1 Vapor 0.01 O (Steam) a 0.001 !20 0 20 40 60 80 100 120 Temperature (°C) Figure 9.2 Pressure–temperature phase diagram for H2O. Intersection of the dashed horizontal line at 1 atm pressure with the solid–liquid phase boundary (point 2) corresponds to the melting point at this pressure (T " 0#C). Similarly, point 3, the intersection with the liquid–vapor boundary, represents the boiling point (T " 100#C). JWCL187_ch09_281-341.qxd 9/18/09 11:54 AM Page 287 9.7 Binary Isomorphous Systems 287 phases is along curve aO—likewise for the solid–liquid, curve bO, and the liquid– vapor, curve cO. Also, upon crossing a boundary (as temperature and/or pressure is altered), one phase transforms to another. For example, at 1 atm pressure, during heating the solid phase transforms to the liquid phase (i.e., melting occurs) at the point labeled 2 on Figure 9.2 (i.e., the intersection of the dashed horizontal line with the solid–liquid phase boundary); this point corresponds to a temperature of 0!C. Of course, the reverse transformation (liquid-to-solid, or solidification) takes place at the same point upon cooling. Similarly, at the intersection of the dashed line with the liquid–vapor phase boundary [point 3 (Figure 9.2), at 100!C] the liquid trans- forms to the vapor phase (or vaporizes) upon heating; condensation occurs for cool- ing. And, finally, solid ice sublimes or vaporizes upon crossing the curve labeled aO. As may also be noted from Figure 9.2, all three of the phase boundary curves intersect at a common point, which is labeled O (and for this H2O system, at a tem- perature of 273.16 K and a pressure of 6.04 " 10#3 atm). This means that at this point only, all of the solid, liquid, and vapor phases are simultaneously in equilib- rium with one another. Appropriately, this, and any other point on a P–T phase di- agram where three phases are in equilibrium, is called a triple point; sometimes it is also termed an invariant point inasmuch as its position is distinct, or fixed by def- inite values of pressure and temperature. Any deviation from this point by a change of temperature and/or pressure will cause at least one of the phases to disappear. Pressure–temperature phase diagrams for a number of substances have been de- termined experimentally, which also have solid, liquid, and vapor phase regions. In those instances when multiple solid phases (i.e., allotropes, Section 3.6) exist, there will appear a region on the diagram for each solid phase, and also other triple points. Binary Phase Diagrams Another type of extremely common phase diagram is one in which temperature and composition are variable parameters, and pressure is held constant—normally 1 atm. There are several different varieties; in the present discussion, we will con- cern ourselves with binary alloys—those that contain two components. If more than two components are present, phase diagrams become extremely complicated and difficult to represent. An explanation of the principles governing and the interpre- tation of phase diagrams can be demonstrated using binary alloys even though most alloys contain more than two components. Binary phase diagrams are maps that represent the relationships between tem- perature and the compositions and quantities of phases at equilibrium, which in- fluence the microstructure of an alloy. Many microstructures develop from phase transformations, the changes that occur when the temperature is altered (ordinar- ily upon cooling). This may involve the transition from one phase to another, or the appearance or disappearance of a phase. Binary phase diagrams are helpful in pre- dicting phase transformations and the resulting microstructures, which may have equilibrium or nonequilibrium character. 9.7 BINARY ISOMORPHOUS SYSTEMS Possibly the easiest type of binary phase diagram to understand and interpret is the type that is characterized by the copper–nickel system (Figure 9.3a). Temperature is plotted along the ordinate, and the abscissa represents the composition of the al- loy, in weight percent (bottom) and atom percent (top) of nickel. The composition JWCL187_ch09_281-341.qxd 9/18/09 11:54 AM Page 288 288 Chapter 9 / Phase Diagrams Figure 9.3 (a) The Composition (at% Ni) copper–nickel phase 0 20 40 60 80 100 diagram. (b) A 1600 portion of the copper–nickel phase 2800 diagram for which compositions and 1500 phase amounts are Liquid 1453°C determined at point 2600 B. (Adapted from 1400 Phase Diagrams of Temperature (°C) Temperature (°F) Binary Nickel Alloys, Solidus line P. Nash, Editor, 1991. Liquidus line 2400 Reprinted by 1300 ! +L permission of ASM B International, Materials Park, OH.) 1200 2200 ! 1100 A 2000 1085°C 1000 0 20 40 60 80 100 (Cu) Composition (wt% Ni) (Ni) (a ) 1300 Liquid Tie line Temperature (°C) ! + Liquid B ! + Liquid ! 1200 R S ! 20 30 40 50 CL C0 C! Composition (wt% Ni) (b) ranges from 0 wt% Ni (100 wt% Cu) on the left horizontal extremity to 100 wt% Ni (0 wt% Cu) on the right. Three different phase regions, or fields, appear on the diagram, an alpha (!) field, a liquid (L) field, and a two-phase ! ! L field. Each region is defined by the phase or phases that exist over the range of temperatures and compositions delineated by the phase boundary lines. JWCL187_ch09_281-341.qxd 11/12/09 7:09 PM Page 289 9.8 Interpretation of Phase Diagrams 289 The liquid L is a homogeneous liquid solution composed of both copper and nickel. The ! phase is a substitutional solid solution consisting of both Cu and Ni atoms, and having an FCC crystal structure. At temperatures below about 1080!C, copper and nickel are mutually soluble in each other in the solid state for all com- positions. This complete solubility is explained by the fact that both Cu and Ni have the same crystal structure (FCC), nearly identical atomic radii and electronegativ- ities, and similar valences, as discussed in Section 4.3. The copper–nickel system is isomorphous termed isomorphous because of this complete liquid and solid solubility of the two components. A couple of comments are in order regarding nomenclature. First, for metallic alloys, solid solutions are commonly designated by lowercase Greek letters (!, ", #, etc.). Furthermore, with regard to phase boundaries, the line separating the L and ! " L phase fields is termed the liquidus line, as indicated in Figure 9.3a; the liquid phase is present at all temperatures and compositions above this line. The solidus line is located between the ! and ! " L regions, below which only the solid ! phase exists. For Figure 9.3a, the solidus and liquidus lines intersect at the two composition extremities; these correspond to the melting temperatures of the pure components. For example, the melting temperatures of pure copper and nickel are 1085!C and 1453!C, respectively. Heating pure copper corresponds to moving vertically up the left-hand temperature axis. Copper remains solid until its melting temperature is reached. The solid-to-liquid transformation takes place at the melting temperature, and no further heating is possible until this transformation has been completed. For any composition other than pure components, this melting phenomenon will occur over the range of temperatures between the solidus and liquidus lines; both solid ! and liquid phases will be in equilibrium within this temperature range. For example, upon heating an alloy of composition 50 wt% Ni–50 wt% Cu (Fig- ure 9.3a), melting begins at approximately 1280!C (2340!F); the amount of liquid phase continuously increases with temperature until about 1320!C (2410!F), at which the alloy is completely liquid. 9.8 INTERPRETATION OF PHASE DIAGRAMS For a binary system of known composition and temperature that is at equilibrium, at least three kinds of information are available: (1) the phases that are present, (2) the compositions of these phases, and (3) the percentages or fractions of the phases. The procedures for making these determinations will be demonstrated using the copper–nickel system. Phases Present The establishment of what phases are present is relatively simple. One just locates VMSE the temperature–composition point on the diagram and notes the phase(s) with which the corresponding phase field is labeled. For example, an alloy of composi- tion 60 wt% Ni–40 wt% Cu at 1100!C would be located at point A in Figure 9.3a; because this is within the ! region, only the single ! phase will be present. On the Isomorphous (Sb-Bi) other hand, a 35 wt% Ni–65 wt% Cu alloy at 1250!C (point B) will consist of both ! and liquid phases at equilibrium. Determination of Phase Compositions The first step in the determination of phase compositions (in terms of the concen- trations of the components) is to locate the temperature–composition point on the JWCL187_ch09_281-341.qxd 11/12/09 7:09 PM Page 290 290 Chapter 9 / Phase Diagrams VMSE phase diagram. Different methods are used for single- and two-phase regions. If only one phase is present, the procedure is trivial: the composition of this phase is simply the same as the overall composition of the alloy. For example, consider the 60 wt% Ni–40 wt% Cu alloy at 1100!C (point A, Figure 9.3a). At this composition Isomorphous (Sb-Bi) and temperature, only the ! phase is present, having a composition of 60 wt% Ni– 40 wt% Cu. For an alloy having composition and temperature located in a two-phase re- gion, the situation is more complicated. In all two-phase regions (and in two-phase regions only), one may imagine a series of horizontal lines, one at every tempera- tie line ture; each of these is known as a tie line, or sometimes as an isotherm. These tie lines extend across the two-phase region and terminate at the phase boundary lines on either side. To compute the equilibrium concentrations of the two phases, the following procedure is used: 1. A tie line is constructed across the two-phase region at the temperature of the alloy. 2. The intersections of the tie line and the phase boundaries on either side are noted. 3. Perpendiculars are dropped from these intersections to the horizontal composi- tion axis, from which the composition of each of the respective phases is read. For example, consider again the 35 wt% Ni–65 wt% Cu alloy at 1250!C, lo- cated at point B in Figure 9.3b and lying within the ! " L region. Thus, the problem is to determine the composition (in wt% Ni and Cu) for both the ! and liquid phases. The tie line has been constructed across the ! " L phase region, as shown in Figure 9.3b. The perpendicular from the intersection of the tie line with the liquidus boundary meets the composition axis at 31.5 wt% Ni–68.5 wt% Cu, which is the composition of the liquid phase, CL. Likewise, for the solidus–tie line inter- section, we find a composition for the ! solid-solution phase, C!, of 42.5 wt% Ni–57.5 wt% Cu. Determination of Phase Amounts VMSE The relative amounts (as fraction or as percentage) of the phases present at equi- librium may also be computed with the aid of phase diagrams. Again, the single- and two-phase situations must be treated separately. The solution is obvious in the single-phase region: because only one phase is present, the alloy is composed en- Isomorphous (Sb-Bi) tirely of that phase; that is, the phase fraction is 1.0 or, alternatively, the percentage is 100%. From the previous example for the 60 wt% Ni–40 wt% Cu alloy at 1100!C (point A in Figure 9.3a), only the ! phase is present; hence, the alloy is completely or 100% !. If the composition and temperature position is located within a two-phase re- gion, things are more complex. The tie line must be utilized in conjunction with a lever rule procedure that is often called the lever rule (or the inverse lever rule), which is ap- plied as follows: 1. The tie line is constructed across the two-phase region at the temperature of the alloy. 2. The overall alloy composition is located on the tie line. 3. The fraction of one phase is computed by taking the length of tie line from the overall alloy composition to the phase boundary for the other phase, and dividing by the total tie line length. JWCL187_ch09_281-341.qxd 9/18/09 11:54 AM Page 291 9.8 Interpretation of Phase Diagrams 291 4. The fraction of the other phase is determined in the same manner. 5. If phase percentages are desired, each phase fraction is multiplied by 100. When the composition axis is scaled in weight percent, the phase fractions computed using the lever rule are mass fractions—the mass (or weight) of a specific phase divided by the total alloy mass (or weight). The mass of each phase is computed from the product of each phase fraction and the total alloy mass. In the employment of the lever rule, tie line segment lengths may be deter- mined either by direct measurement from the phase diagram using a linear scale, preferably graduated in millimeters, or by subtracting compositions as taken from the composition axis. Consider again the example shown in Figure 9.3b, in which at 1250!C both ! and liquid phases are present for a 35 wt% Ni–65 wt% Cu alloy. The problem is to compute the fraction of each of the ! and liquid phases. The tie line has been con- structed that was used for the determination of ! and L phase compositions. Let the overall alloy composition be located along the tie line and denoted as C0, and mass fractions be represented by WL and W! for the respective phases. From the lever rule, WL may be computed according to S WL " (9.1a) R$S or, by subtracting compositions, Lever rule expression for computation of Ca # C0 WL " (9.1b) liquid mass fraction Ca # CL (per Figure 9.3b) Composition need be specified in terms of only one of the constituents for a binary alloy; for the preceding computation, weight percent nickel will be used (i.e., C0 " 35 wt% Ni, C! " 42.5 wt% Ni, and CL " 31.5 wt% Ni), and 42.5 # 35 WL " " 0.68 42.5 # 31.5 Similarly, for the ! phase, Lever rule R Wa " (9.2a) expression for R$S computation of !- phase mass fraction (per Figure 9.3b) C0 # CL " (9.2b) Ca # CL 35 # 31.5 " " 0.32 42.5 # 31.5 Of course, identical answers are obtained if compositions are expressed in weight percent copper instead of nickel. Thus, the lever rule may be employed to determine the relative amounts or fractions of phases in any two-phase region for a binary alloy if the temperature and composition are known and if equilibrium has been established. Its derivation is presented as an example problem. JWCL187_ch09_281-341.qxd 9/18/09 11:54 AM Page 292 292 Chapter 9 / Phase Diagrams It is easy to confuse the foregoing procedures for the determination of phase compositions and fractional phase amounts; thus, a brief summary is warranted. Compositions of phases are expressed in terms of weight percents of the compo- nents (e.g., wt% Cu, wt% Ni). For any alloy consisting of a single phase, the com- position of that phase is the same as the total alloy composition. If two phases are present, the tie line must be employed, the extremities of which determine the com- positions of the respective phases. With regard to fractional phase amounts (e.g., mass fraction of the ! or liquid phase), when a single phase exists, the alloy is com- pletely that phase. For a two-phase alloy, on the other hand, the lever rule is uti- lized, in which a ratio of tie line segment lengths is taken. Concept Check 9.2 A copper–nickel alloy of composition 70 wt% Ni–30 wt% Cu is slowly heated from a temperature of 1300!C (2370!F). (a) At what temperature does the first liquid phase form? (b) What is the composition of this liquid phase? (c) At what temperature does complete melting of the alloy occur? (d) What is the composition of the last solid remaining prior to complete melting? [The answer may be found at www.wiley.com/college/callister (Student Companion Site).] Concept Check 9.3 Is it possible to have a copper–nickel alloy that, at equilibrium, consists of an ! phase of composition 37 wt% Ni–63 wt% Cu, and also a liquid phase of composi- tion 20 wt% Ni–80 wt% Cu? If so, what will be the approximate temperature of the alloy? If this is not possible, explain why. [The answer may be found at www.wiley.com/college/callister (Student Companion Site).] EXAMPLE PROBLEM 9.1 Lever Rule Derivation Derive the lever rule. Solution Consider the phase diagram for copper and nickel (Figure 9.3b) and alloy of composition C0 at 1250!C, and let Ca, CL, Wa, and WL represent the same pa- rameters as given earlier. This derivation is accomplished through two conservation-of-mass expressions. With the first, because only two phases are present, the sum of their mass fractions must be equal to unity; that is, W! " WL # 1 (9.3) For the second, the mass of one of the components (either Cu or Ni) that is present in both of the phases must be equal to the mass of that component in the total alloy, or JWCL187_ch09_281-341.qxd 9/18/09 11:54 AM Page 293 9.8 Interpretation of Phase Diagrams 293 W!C! # WLCL ! C0 (9.4) Simultaneous solution of these two equations leads to the lever rule expres- sions for this particular situation, Equations 9.1b and 9.2b: Ca " C0 WL ! (9.1b) Ca " CL C0 " CL Wa ! (9.2b) Ca " CL For multiphase alloys, it is often more convenient to specify relative phase amount in terms of volume fraction rather than mass fraction. Phase volume frac- tions are preferred because they (rather than mass fractions) may be determined from examination of the microstructure; furthermore, the properties of a multiphase alloy may be estimated on the basis of volume fractions. For an alloy consisting of ! and " phases, the volume fraction of the ! phase, V!, is defined as ! phase volume va fraction—dependence Va ! (9.5) on volumes of ! and va # vb " phases where v! and v" denote the volumes of the respective phases in the alloy. Of course, an analogous expression exists for V", and, for an alloy consisting of just two phases, it is the case that V! # V" ! 1. On occasion conversion from mass fraction to volume fraction (or vice versa) is desired. Equations that facilitate these conversions are as follows: Wa ra Va ! (9.6a) Wa Wb # Conversion of mass ra rb fractions of ! and " phases to volume fractions Wb rb Vb ! (9.6b) Wa Wb # ra rb and Vara Wa ! (9.7a) Conversion of Vara # Vbrb volume fractions of ! and " phases to mass fractions Vbrb Wb ! (9.7b) Vara # Vbrb In these expressions, #! and #" are the densities of the respective phases; these may be determined approximately using Equations 4.10a and 4.10b. JWCL187_ch09_281-341.qxd 11/12/09 7:10 PM Page 294 294 Chapter 9 / Phase Diagrams When the densities of the phases in a two-phase alloy differ significantly, there will be quite a disparity between mass and volume fractions; conversely, if the phase densities are the same, mass and volume fractions are identical. 9.9 DEVELOPMENT OF MICROSTRUCTURE IN ISOMORPHOUS ALLOYS Equilibrium Cooling VMSE At this point it is instructive to examine the development of microstructure that occurs for isomorphous alloys during solidification. We first treat the situation in which the cooling occurs very slowly, in that phase equilibrium is continuously maintained. Isomorphous (Sb-Bi) Let us consider the copper–nickel system (Figure 9.3a), specifically an alloy of composition 35 wt% Ni–65 wt% Cu as it is cooled from 1300!C. The region of the Cu–Ni phase diagram in the vicinity of this composition is shown in Figure 9.4. Cooling of an alloy of this composition corresponds to moving down the vertical dashed line. At 1300!C, point a, the alloy is completely liquid (of composition 35 wt% Ni–65 wt% Cu) and has the microstructure represented by the circle in- set in the figure. As cooling begins, no microstructural or compositional changes will be realized until we reach the liquidus line (point b, ~1260!C). At this point, Figure 9.4 Schematic L representation of the L L development of (35 Ni) (35 Ni) microstructure during ! (46 Ni) the equilibrium 1300 a ! solidification of a 35 + L wt% Ni–65 wt% Cu alloy. L (32 Ni) b ! (46 Ni) c Temperature (°C) ! (43 Ni) ! (43 Ni) L (24 Ni) d ! ! L (32 Ni) ! ! 1200 ! e L (24 Ni) ! ! ! ! (35 Ni) ! ! ! ! ! ! ! ! ! ! ! ! ! (35 Ni) ! 1100 20 30 40 50 Composition (wt% Ni) JWCL187_ch09_281-341.qxd 9/18/09 11:54 AM Page 295 9.9 Development of Microstructure in Isomorphous Alloys 295 the first solid ! begins to form, which has a composition dictated by the tie line drawn at this temperature [i.e., 46 wt% Ni–54 wt% Cu, noted as !(46 Ni)]; the composition of liquid is still approximately 35 wt% Ni–65 wt% Cu [L(35 Ni)], which is different from that of the solid !. With continued cooling, both compo- sitions and relative amounts of each of the phases will change. The compositions of the liquid and ! phases will follow the liquidus and solidus lines, respectively. Furthermore, the fraction of the ! phase will increase with continued cooling. Note that the overall alloy composition (35 wt% Ni–65 wt% Cu) remains unchanged during cooling even though there is a redistribution of copper and nickel between the phases. At 1250!C, point c in Figure 9.4, the compositions of the liquid and ! phases are 32 wt% Ni–68 wt% Cu [L(32 Ni)] and 43 wt% Ni–57 wt% Cu [!(43 Ni)], re- spectively. The solidification process is virtually complete at about 1220!C, point d; the com- position of the solid ! is approximately 35 wt% Ni–65 wt% Cu (the overall alloy composition), whereas that of the last remaining liquid is 24 wt% Ni–76 wt% Cu. Upon crossing the solidus line, this remaining liquid solidifies; the final product then is a polycrystalline !-phase solid solution that has a uniform 35 wt% Ni–65 wt% Cu composition (point e, Figure 9.4). Subsequent cooling will produce no microstruc- tural or compositional alterations. Nonequilibrium Cooling Conditions of equilibrium solidification and the development of microstructures, as described in the previous section, are realized only for extremely slow cooling rates. The reason for this is that with changes in temperature, there must be read- justments in the compositions of the liquid and solid phases in accordance with the phase diagram (i.e., with the liquidus and solidus lines), as discussed. These readjustments are accomplished by diffusional processes—that is, diffusion in both solid and liquid phases and also across the solid–liquid interface. Inasmuch as dif- fusion is a time-dependent phenomenon (Section 5.3), to maintain equilibrium during cooling, sufficient time must be allowed at each temperature for the ap- propriate compositional readjustments. Diffusion rates (i.e., the magnitudes of the diffusion coefficients) are especially low for the solid phase and, for both phases, decrease with diminishing temperature. In virtually all practical solidification sit- uations, cooling rates are much too rapid to allow these compositional readjust- ments and maintenance of equilibrium; consequently, microstructures other than those previously described develop. Some of the consequences of nonequilibrium solidification for isomorphous al- loys will now be discussed by considering a 35 wt% Ni–65 wt% Cu alloy, the same composition that was used for equilibrium cooling in the previous section. The por- tion of the phase diagram near this composition is shown in Figure 9.5; in addition, microstructures and associated phase compositions at various temperatures upon cooling are noted in the circular insets. To simplify this discussion it will be assumed that diffusion rates in the liquid phase are sufficiently rapid such that equilibrium is maintained in the liquid. Let us begin cooling from a temperature of about 1300!C; this is indicated by point a" in the liquid region. This liquid has a composition of 35 wt% Ni–65 wt% Cu [noted as L(35 Ni) in the figure], and no changes occur while cooling through the liquid phase region (moving down vertically from point a"). At point b" (ap- proximately 1260!C), !-phase particles begin to form, which, from the tie line con- structed, have a composition of 46 wt% Ni–54 wt% Cu [!(46 Ni)]. JWCL187_ch09_281-341.qxd 9/18/09 11:54 AM Page 296 296 Chapter 9 / Phase Diagrams Figure 9.5 Schematic L representation of the L development of (35 Ni) microstructure L (35 Ni) during the a! ! +L nonequilibrium 1300 ! (46 Ni) solidification of a 35 wt% Ni–65 wt% Cu alloy. ! b! L (29 Ni) ! (40 Ni) ! (46 Ni) c! Temperature (°C) L (24 Ni) L (29 Ni) ! (42 Ni) d! ! (46 Ni) L (21 Ni) ! (40 Ni) ! (35 Ni) ! (38 Ni) e! 1200 ! (31 Ni) L (24 Ni) f! ! (46 Ni) ! (40 Ni) ! (46 Ni) ! (35 Ni) ! (40 Ni) L (21 Ni) ! (35 Ni) ! (46 Ni) ! (31 Ni) ! (40 Ni) ! (35 Ni) ! (31 Ni) 1100 20 30 40 50 60 Composition (wt% Ni) Upon further cooling to point c! (about 1240"C), the liquid composition has shifted to 29 wt% Ni–71 wt% Cu; furthermore, at this temperature the composition of the ! phase that solidified is 40 wt% Ni–60 wt% Cu [!(40 Ni)]. However, because diffusion in the solid ! phase is relatively slow, the ! phase that formed at point b! has not changed composition appreciably—that is, it is still about 46 wt% Ni—and the composition of the ! grains has continuously changed with radial position, from 46 wt% Ni at grain centers to 40 wt% Ni at the outer grain perimeters. Thus, at point c!, the average composition of the solid ! grains that have formed would be some volume weighted average composition, lying between 46 and 40 wt% Ni. For the sake of argument, let us take this average composition to be 42 wt% Ni–58 wt% Cu [!(42 Ni)]. Furthermore, we would also find that, on the basis of lever-rule computations, a greater proportion of liquid is present for these nonequilibrium conditions than for equilibrium cooling. The implication of this nonequilibrium solidification phenomenon is that the solidus line on the phase diagram has been shifted to higher Ni contents—to the average compositions of the ! phase (e.g., 42 wt% Ni at 1240"C)—and is represented by the dashed line in Figure 9.5. There is no comparable alteration of the liquidus line inasmuch as it is assumed that JWCL187_ch09_281-341.qxd 9/18/09 11:54 AM Page 297 9.10 Mechanical Properties of Isomorphous Alloys 297 equilibrium is maintained in the liquid phase during cooling because of sufficiently rapid diffusion rates. At point d! (~1220"C) and for equilibrium cooling rates, solidification should be completed. However, for this nonequilibrium situation, there is still an appre- ciable proportion of liquid remaining, and the ! phase that is forming has a com- position of 35 wt% Ni [!(35 Ni)]; also the average !-phase composition at this point is 38 wt% Ni [!(38 Ni)]. Nonequilibrium solidification finally reaches completion at point e! (~1205"C). The composition of the last ! phase to solidify at this point is about 31 wt% Ni; the average composition of the ! phase at complete solidification is 35 wt% Ni. The inset at point f ! shows the microstructure of the totally solid material. The degree of displacement of the nonequilibrium solidus curve from the equi- librium one will depend on rate of cooling. The slower the cooling rate, the smaller this displacement; that is, the difference between the equilibrium solidus and aver- age solid composition is lower. Furthermore, if the diffusion rate in the solid phase is increased, this displacement will be diminished. There are some important consequences for isomorphous alloys that have so- lidified under nonequilibrium conditions. As discussed earlier, the distribution of the two elements within the grains is nonuniform, a phenomenon termed segre- gation; that is, concentration gradients are established across the grains that are represented by the insets of Figure 9.5. The center of each grain, which is the first part to freeze, is rich in the high-melting element (e.g., nickel for this Cu–Ni sys- tem), whereas the concentration of the low-melting element increases with posi- tion from this region to the grain boundary. This is termed a cored structure, which gives rise to less than the optimal properties. As a casting having a cored structure is reheated, grain boundary regions will melt first inasmuch as they are richer in the low-melting component. This produces a sudden loss in mechanical integrity due to the thin liquid film that separates the grains. Furthermore, this melting may begin at a temperature below the equilibrium solidus temperature of the alloy. Coring may be eliminated by a homogenization heat treatment carried out at a temperature below the solidus point for the particular alloy composition. During this process, atomic diffusion occurs, which produces compositionally homogeneous grains. 9.10 MECHANICAL PROPERTIES OF ISOMORPHOUS ALLOYS We shall now briefly explore how the mechanical properties of solid isomorphous alloys are affected by composition as other structural variables (e.g., grain size) are held constant. For all temperatures and compositions below the melting tempera- ture of the lowest-melting component, only a single solid phase will exist. There- fore, each component will experience solid-solution strengthening (Section 7.9), or an increase in strength and hardness by additions of the other component. This ef- fect is demonstrated in Figure 9.6a as tensile strength versus composition for the copper–nickel system at room temperature; at some intermediate composition, the curve necessarily passes through a maximum. Plotted in Figure 9.6b is the ductil- ity (%EL)–composition behavior, which is just the opposite of tensile strength; that is, ductility decreases with additions of the second component, and the curve exhibits a minimum. JWCL187_ch09_281-341.qxd 9/18/09 11:54 AM Page 298 298 Chapter 9 / Phase Diagrams 60 Elongation (% in 50 mm [2 in.]) 60 400 Tensile strength (MPa) 50 Tensile strength (ksi) 50 40 300 40 30 200 30 20 0 20 40 60 80 100 0 20 40 60 80 100 (Cu) (Ni) (Cu) (Ni) Composition (wt% Ni) Composition (wt% Ni) (a) (b) Figure 9.6 For the copper–nickel system, (a) tensile strength versus composition, and (b) ductility (%EL) versus composition at room temperature. A solid solution exists over all compositions for this system. 9.11 BINARY EUTECTIC SYSTEMS Another type of common and relatively simple phase diagram found for binary al- loys is shown in Figure 9.7 for the copper–silver system; this is known as a binary eutectic phase diagram. A number of features of this phase diagram are important and worth noting. First, three single-phase regions are found on the diagram: !, ", and liquid. The ! phase is a solid solution rich in copper; it has silver as the solute Composition (at% Ag) 0 20 40 60 80 100 1200 2200 A 2000 Liquidus 1000 Liquid 1800 Solidus F ! +L 1600 ! "+L 779°C (TE) E Temperature (°C) Temperature (°F) 800 B G 8.0 71.9 91.2 " 1400 (C! E) (CE) (C" E) 1200 600 Solvus 1000 ! +" 800 400 C 600 H 200 400 0 20 40 60 80 100 (Cu) Composition (wt% Ag) (Ag) Figure 9.7 The copper–silver phase diagram. [Adapted from Binary Alloy Phase Diagrams, 2nd edition, Vol. 1, T. B. Massalski (Editor-in-Chief), 1990. Reprinted by permission of ASM International, Materials Park, OH.] JWCL187_ch09_281-341.qxd 9/18/09 11:54 AM Page 299 9.11 Binary Eutectic Systems 299 component and an FCC crystal structure. The !-phase solid solution also has an FCC structure, but copper is the solute. Pure copper and pure silver are also con- sidered to be " and ! phases, respectively. Thus, the solubility in each of these solid phases is limited, in that at any tem- perature below line BEG only a limited concentration of silver will dissolve in cop- per (for the " phase), and similarly for copper in silver (for the ! phase). The solubility limit for the " phase corresponds to the boundary line, labeled CBA, be- tween the "/(" ! !) and "/(" ! L) phase regions; it increases with temperature to a maximum [8.0 wt% Ag at 779"C (1434"F)] at point B, and decreases back to zero at the melting temperature of pure copper, point A [1085"C (1985"F)]. At temper- atures below 779"C (1434"F), the solid solubility limit line separating the " and " solvus line ! ! phase regions is termed a solvus line; the boundary AB between the " and " ! L fields is the