6S Lean Workplace PDF
Document Details
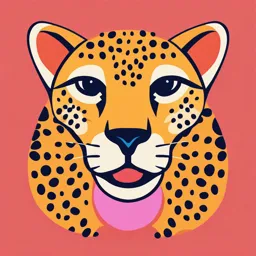
Uploaded by StupendousHibiscus
NUSRL, Ranchi
Jeanette A. David
Tags
Summary
This presentation details the 6S Lean Workplace system, a method for promoting high workplace productivity and safety through a 5S principle plus safety model. It outlines the key elements, goals, and implementation strategies related to sorting, setting in order, shining, standardizing, and sustaining.
Full Transcript
6S Lean Workplace Prepared by: Jeanette A. David 6S Lean: 5S + Safety 6S (otherwise known as 5S + Safety) is a system that aims to promote and sustain a high level of productivity and safety throughout a workspace. While adhering to the 5S principle of Sort, Set in order, Shine, Standa...
6S Lean Workplace Prepared by: Jeanette A. David 6S Lean: 5S + Safety 6S (otherwise known as 5S + Safety) is a system that aims to promote and sustain a high level of productivity and safety throughout a workspace. While adhering to the 5S principle of Sort, Set in order, Shine, Standardize, and Sustain, the 6S method adds the concept of Safety. 6 S lean not only helps organizations promote efficient working environments but also establishes a sustainable culture of safety. Seiri is sorting through all items in a location and removing all unnecessary items from the location. Goals: Reduce time loss looking for an item by reducing the number of unnecessary items. Reduce the chance of distraction by unnecessary items. Simplify inspection. Increase the amount of available, useful space. Increase safety by eliminating obstacles. Implementation: Check all items in a location and evaluate whether or not their presence at the location is useful or necessary. Remove unnecessary items as soon as possible. Place those that cannot be removed immediately in a 'red tag area' so that they are easy to remove later on. Keep the working floor clear of materials except for those that are in use for production. (Sometimes shown as Straighten) Seiton is putting all necessary items in the optimal place for fulfilling their function in the workplace. Goal: Make the workflow smooth and easy. Implementation: Arrange work stations in such a way that all tooling / equipment is in close proximity, in an easy to reach spot and in a logical order adapted to the work performed. Place components according to their uses, with the frequently used components being nearest to the workplace. Arrange all necessary items so that they can be easily selected for use. Make it easy to find and pick up necessary items. Assign fixed locations for items. Use clear labels, marks or hints so that items are easy to return to the correct location and so that it is easy to spot missing items. Seiso is sweeping or cleaning and inspecting the workplace, tools and machinery on a regular basis. Goals: Improves the production process efficiency and safety, reduces waste, prevents errors and defects. Keep the workplace safe and easy to work in. Keep the workplace clean and pleasing to work in. When in place, anyone not familiar to the environment must be able to detect any problems within 15m (50 feet) in 5 sec. Implementation: Clean the workplace and equipment on a daily basis, or at another appropriate (high frequency) cleaning interval. Inspect the workplace and equipment while cleaning. Seiketsu is to standardize the processes used to sort, order and clean the workplace. Goal: Establish procedures and schedules to ensure the repetition of the first three ‘S’ practices. Implementation: Develop a work structure that will support the new practices and make it part of the daily routine. Ensure everyone knows their responsibilities of performing the sorting, organizing and cleaning. Use photos and visual controls to help keep everything as it should be. Review the status of 5S implementation regularly using audit checklists. Shitsuke or sustain is the developed processes by self-discipline of the workers. Also translates as "do without being told". Goal: Ensure that the 5S approach is followed. Implementation: Organize training sessions. Perform regular audits to ensure that all defined standards are being implemented and followed. Implement improvements whenever possible. Worker inputs can be very valuable for identifying improvements. Accident prevention- awareness for all activities to identify and eliminate hazards for a zero accident and injury free workplace.