Aircraft Lubrication Equipment PDF
Document Details
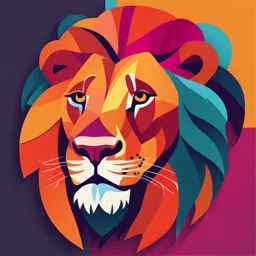
Uploaded by FaultlessMarsh8570
null
Tags
Summary
This document provides an overview of aircraft lubrication equipment, servicing, and different lubrication types. It details the various lubricant categories, their properties, and how they're applied in aircraft maintenance. It covers topics such as types of lubricants, their roles, and the specific methods associated with aircraft lubricant applications.
Full Transcript
Aircraft Lubrication Equipment Aircraft Servicing The term servicing means operations which are required to check and replenish an aircraft’s systems and to maintain an aircraft in an operational condition. In cases when an Aircraft Maintenance Manual (AMM) is produced in accordance with ATA Specifi...
Aircraft Lubrication Equipment Aircraft Servicing The term servicing means operations which are required to check and replenish an aircraft’s systems and to maintain an aircraft in an operational condition. In cases when an Aircraft Maintenance Manual (AMM) is produced in accordance with ATA Specification 100, detailed information about servicing operations will be found in Chapter 12. Many types of ground equipment may be required during aircraft servicing, and all must be compatible with the aircraft systems on which they are to be used. The ground equipment should be kept scrupulously clean and should be maintained in accordance with a schedule recommended by the manufacturer. Delivery hoses from all liquid and gas servicing trolleys should be blanked when not in use, and their cleanliness and serviceability should be checked before connection to an aircraft. Fire extinguishers suitable for fuel and electrical fires should always be readily accessible wherever an aircraft is being serviced and should be subject to regular inspection. © Aviation Australia Aircraft servicing / maintenance 2023-11-24 B-07b Maintenance Practices CASA Part 66 - Training Materials Only Page 295 of 498 Aviation Lubricants Aviation lubricants are classified into the following broad categories, depending on their application and the nature of the product. Aero Engine Oils For piston engines, engine oils are generally mineral petroleum oils, either straight mineral of the appropriate viscosity or blended with additives or part synthetic multi-grade oils. For turbojet, turboprop or turbofan engines, engine oils can be either mineral-based (mainly for earlier marks of jet engines) or synthetic. Greases Greases contain mineral or synthetic base oils with metal soaps, organic thickeners or inorganic fillers. Inhibitors Inhibitors are used for outdoor protection or internal storage. They can range from oils to solventbased compositions, pastes or even additives. Specialities Speciality lubricants include several types of miscellaneous products such as gear oils, instrument oils, damping fluids, anti-seize compounds and dry lubricants. Lubricant Properties Just as there are two basic types of aircraft engines, piston and turbine, there are two types of aviation engine lubricants, the piston-engine oils and the jet engine oils. Each oil type is blended using base stocks and additives that reflect the physical and chemical properties imposed by the corresponding engine design and operating conditions. As a result of these differences, aviation piston engine oils are blended mainly from petroleum base stocks, while modern gas turbine oils are of synthetic origin. Functions of a Lubricant Reduces friction Provides cooling Seals and cushions Protects against corrosion Cleanses. 2023-11-24 B-07b Maintenance Practices CASA Part 66 - Training Materials Only Page 296 of 498 Reduces Friction If we were to microscopically examine the surface of metal parts in an aircraft engine, we would find they are not perfectly smooth, but made up of peaks and valleys. When two such parts rub together, there is friction as metal is worn away from the surfaces. To reduce this friction, a film of oil is placed between the moving parts. The oil wets the surfaces, fills in the valleys and holds the metal surfaces apart. The movement is now between layers of the oil, which slide over each other with very little friction. The viscosity of oil is its fluid friction, and the clearance between the moving parts determines the viscosity of the oil required to prevent this film breaking away and allowing the metal-to-metal contact that causes wear. Provides Cooling The oil is in intimate contact with the moving parts of an aircraft engine, and it absorbs some of the heat from the combustion process. This heated oil then flows through the system into the oil cooler, where the heat is given up to the outside air passing through the core of the cooler. Seals and Cushions The viscous nature of oil, that is, its ability to wet the surface it contacts, makes oil a good sealing agent between the moving parts. The oil film on the cylinder walls and around the piston increases its ability to form a tight seal in the cylinder, and the thin film of oil between the rocker arm and its bushing takes up much of the hammering shock from the valve action. Protects Against Corrosion When metal is allowed to remain uncovered in the presence of moisture or chemicals that contaminate the air, rust or other surface corrosion will form. This is especially true of metal surfaces such as cylinder walls or crankshafts, which have been hardened by the process of nitriding. A film of oil covering these surfaces prevents the oxygen reacting with the metal and pitting it. Cleanses Dirt, dust, carbon and water all enter the oil, and the oil’s ability to hold these contaminants until they can be picked up and trapped in the filter helps keep the inside of the engine clean. 2023-11-24 B-07b Maintenance Practices CASA Part 66 - Training Materials Only Page 297 of 498 Types of Lubricating Oil Straight Mineral Oil MIL-L-6028B is a straight mineral oil that has been used for many years as the chief lubricant for aircraft engines. It has one main limitation: its tendency to oxidise when exposed to elevated temperatures or when aerated. Metallic-Ash Detergent Oil Certain metallic-ash-forming additives have been added to mineral oil to increase its oxidation stability. These additives were chosen to have minimise spark plug fouling and pre-ignition, and their cleaning action in the engine loosened any carbon deposits or sludge that had formed; once these were loosened, they passed through the engine, where they were prone to clog oil passages and filters. Detergent oils were given only a limited approval by some engine manufacturers and, because of their limitations, have passed off the scene as an oil suitable for aircraft use. Ashless Dispersant Oil By far the most important oil in use today is ashless dispersant (AD) oil. It does not have the carbonforming restrictions of straight mineral oil, nor does it form ash deposits as detergent oil did. Meeting the specification MIL-L-2285 1, AD oil is approved by Lycoming, Continental, Pratt and Whitney, and Franklin for use in their engines, and is the only oil used by the military services for their piston engine aircraft. Synthetic Oil The higher operating temperatures of modern reciprocating engines, and the lower temperature environment in which turbine aircraft operate, have in the past few years caused synthetic oil to be produced. Synthetic oil is proving superior to mineral oils for lubrication. At present, this oil enjoys only limited approval for piston engine aircraft use, not because of any inherent problems, but because of lack of service experience. 2023-11-24 B-07b Maintenance Practices CASA Part 66 - Training Materials Only Page 298 of 498 Turbine Engine Oil The early series of aircraft gas turbine engines could be adequately lubricated with highly refined petroleum oils because the temperatures at the turbine inlet and compressor discharge were relatively low. With successive advances in performance, petroleum-based oils began to exhibit shortcomings such as high volatility (especially at high altitudes), inadequate resistance to oxidation, too high a viscosity at low temperatures, and poor resistance to scuffing of metal surfaces. The use of mineral oils as gas turbine engine lubricants is now confined to the earlier series of Western aircraft and many Russian aircraft. Turbine engine oils 2023-11-24 B-07b Maintenance Practices CASA Part 66 - Training Materials Only Page 299 of 498 Fluid Servicing Equipment The equipment used for lubrication should be kept scrupulously clean and should only be filled with new lubricant. Each piece of equipment or container should be clearly marked with the lubricant it contains and should be kept solely for that lubricant. On modern aircraft, replenishment of engine oil, hydraulic oil and other systems containing fluids is achieved using hand-held equipment or servicing carts. These are specially designed for the task and are connected to the system by quick-release couplings. On general aviation aircraft and older aircraft, these systems may be replenished by removing the tank filler cap and pouring in the required fluid. Whichever method is used, the utmost care should be taken to ensure that only the approved fluids are used and that no foreign matter is allowed to enter the system. Servicing trolleys should be inspected regularly for cleanliness, and their delivery hoses should be capped when not in use. All utensils should be kept scrupulously clean and should be retained for use with one liquid. Quantity Level Any system containing lubricant oil must incorporate some form of quantity indication. This could be by a sight glass, a dipstick, by visibility in a filler opening. Alternatively, a contents gauge driven by a sensor in the lubricant tank may be used. Mobile oil cart When required, the system should be replenished to the 'full' level; no system should be overfilled as this could affect system operation. 2023-11-24 B-07b Maintenance Practices CASA Part 66 - Training Materials Only Page 300 of 498 Oil Cans Oil cans apply oil in smaller quantities, to parts and areas which require more exact lubrication than is possible with a general spray. Cans can apply oil in droplets, without spillage, just where the oil is wanted. Oil cans must also be clearly labelled to show the type of oil that they contain. © Aviation Australia - Image by Pierre Waldron Oil can with contents label Note: A grease gun may be used to apply oil. Aircraft Lubricating Grease Lubricant grease has a gel like (semi-solid) consistency. Grease is not simply a very viscous oil. Rather, it is an oil mixed with other ingredients to obtain a semi-solid consistency. A typical aviation grease consists of 80 to 90% base oil, 10 to 15% thickener and 5 to 10% additives. There are hundreds of grease points on a modern transport aircraft, concentrated at the landing gear and the flaps. Grease is the preferred lubricant in certain conditions, for the following reasons: In dirty, dusty, or wet conditions, grease provides a sealing medium, opposing the entry of foreign matter into moving parts Grease stays in vertical bearings, whereas oil will drain away When packed into a bearing or housing, grease lubricates for prolonged periods A grease lubrication system is cheaper and less complex than an oil system. 2023-11-24 B-07b Maintenance Practices CASA Part 66 - Training Materials Only Page 301 of 498 However, grease has limitations: Grease does not carry heat away, unlike oil. Grease must not be used where contamination is likely Grease does not wash debris and contaminants away. When lubricating a component, care should be taken to ensure that the quantity applied is adequate but not excessive. In some cases, the AMM specifies a quantity; for example 'apply 8 drops of oil'. The general rule is to apply a quantity of oil sufficient to cover the bearing surfaces, as evidenced by new lubricant exuding from the bearing. The lubricating point should be wiped clean and dry with a lintfree cloth before applying the oil or grease, and any excess exuding from the component should be wiped off to prevent the accumulation of dirt or foreign matter. The technical and performance requirements of greases arising out of these applications are not very different for various types of aircraft, excluding the products required for any specialised equipment in the system. Mineral oil thickened with calcium soap was the first type of lubricating grease produced in commercial quantities. This was followed by sodium soap greases, but as sodium salts are soluble in water, these greases tended to get washed out with the ingress of water in the system. This led to the development of water-resistant barium and lithium soap types, followed by complex thickeners of aluminium and calcium. For high-temperature applications, non-soap thickeners are used, such as modified clays and other organic compounds like substituted ureas, polymers and pigments. An example of the modified clay thickeners is Microgel™, used in many of the Aeroshell range of greases. For extremely hightemperature performance, greases were introduced with inorganic fillers, such as molybdenum disulphide and graphite. The base fluids can range from mineral oils to synthetic esters, synthesised hydrocarbons, and silicone oils, depending on the desired performance, to even vegetable oils in cases when resistance to hydrocarbons (fuels and oils) is required. Chemical- or oxygen-resistant greases are also available for special applications. For aircraft usage, several types of mineral-oil-based and synthetic greases are used, the latter offering wide temperature range applications. The number of greases required for fleet maintenance has been reduced over time due to the development of multipurpose greases and rationalisation between grease specifications of Western and Russian origin. Some of the more commonly used aircraft greases are described below. 2023-11-24 B-07b Maintenance Practices CASA Part 66 - Training Materials Only Page 302 of 498 Widely Used Airframe Lubrication Greases AeroShell Grease 7 Microgel™ (modified clay) thickened, synthetic oil base. Inhibits corrosion and resists oxidation, temperature range of -73 to +149 °C. Recommended for highly loaded gears and actuator screw mechanisms, as well as for instrument and general airframe lubrication. Conforms to MIL-PRF-22827C Type II. AeroShell Grease 7 CAUTION: It is essential to comply with the AMM when changing from one grease type (or manufacturer) to another. Some base oils are incompatible with others. Some thickening agents are incompatible with others. Do not mix MIL-PRF-22827C Type II (Aeroshell Grease 7) clay thickened grease with MIL-PRF-23827 Type I (Aeroshell Grease 33) lithium thickened grease. Mixture causes grease breakdown. If the AMM or a Service Bulletin requires a change of grease type for a specific lubrication task, it may also require disassembly of moving parts and thorough removal of the old grease. Failure to purge old grease can lead to bearing failure. 2023-11-24 B-07b Maintenance Practices CASA Part 66 - Training Materials Only Page 303 of 498 AeroShell Grease 17 AeroShell Grease 7 with 5% molybdenum disulphide. A general purpose airframe grease for heavily loaded sliding steel surfaces where protection against seizure and corrosion is desired, e.g. bogie pivot pins on jet aircraft landing assemblies; also provides outstanding anti-friction bearing lubrication. Useful temperature range is -73 to +149 °C. Conforms to MIL-G-211640. AeroShell Grease 17 2023-11-24 B-07b Maintenance Practices CASA Part 66 - Training Materials Only Page 304 of 498 AeroShell Grease 5 Microgel thickened, mineral oil base. High load-carrying ability with excellent resistance to water and high temperatures; inhibits corrosion and oxidation and has a useful temperature range of -23 to + 177 °C. Used primarily in aircraft wheel bearings and engine accessories operating at high speeds and relatively high temperatures. MIL-G-3545 (obsolete) means the MIL Spec is obsolete, not the grease. AeroShell Grease 5 Apart from the lubricants listed in this presentation, there are many more types, e.g. instrument oil, gear oils, Skydrol and compatible greases. For information about what lubricants to use and how to apply them, refer to the appropriate publications, such as: Aircraft Maintenance Manual (AMM) ATA Chapter 12 Aircraft Service Manual (ASM) non-ATA Service Bulletins Civil Aircraft Airworthiness Information and Procedures (CAAP) CAP 562 FAA Publication: AC43.13-2a/1b – Acceptable Methods of Inspection and Repair Original Equipment Manufacturer’s (OEM) Manuals. 2023-11-24 B-07b Maintenance Practices CASA Part 66 - Training Materials Only Page 305 of 498 Lubricant Methods of Application The lubricant to be used, and the method of application, are usually annotated on a diagram of the aircraft in the appropriate chapter of the AMM. A mimic diagram is a frequently used method of annotation (e.g. an oil can for oiling or a grease gun for greasing) and the type of lubricant is indicated by a symbol. Lubrication charts (on an A320) Use and maintain any tool in accordance with the manufacturer’s handbook to keep the equipment in clean condition. To ensure the correct grease is delivered to the component, always purge old grease from the nozzle before connecting to an aircraft. If grease containers are allowed to sit uncovered in a busy hangar for any length of time, there is a chance they will become contaminated. Contamination can include metal filings, abrasive dust, other fluids, etc. Keep grease containers firmly sealed and clearly identified when not in use. 2023-11-24 B-07b Maintenance Practices CASA Part 66 - Training Materials Only Page 306 of 498 Contaminated grease Using contaminated lubricants will have an adverse effect on the component they are designed to protect, causing accelerated wear and failure. Contaminated lubricants should be discarded in the proper receptacles. 2023-11-24 B-07b Maintenance Practices CASA Part 66 - Training Materials Only Page 307 of 498 Grease Lubrication Equipment Grease Nipples and Couplers All grease nipples, regardless of type, have a spring-loaded valve to prevent loss of lubricant through the nipple. It is very important to clean the nipple before attaching the grease gun coupler (adapter) since dirt can enter the component, causing wear and damage. Dirt may also become trapped under the valve, allowing grease to escape during the component’s service period and accelerating wear. The valve may also stick closed in the interval between lubrications. This prevents the nipple from accepting grease the next time a grease gun coupler is attached. Zerk Fittings Zerk grease nipples are the most common grease fitting used on aircraft. A zerk fitting imay also be termed, hydraulic fitting. The shank of the zerk fitting attaches to the component by straight or tapered threads, or by serrations. Zerk (hydraulic) fittings - serrated shank (drive) type and threaded shank type The convex top of the zerk fitting allows the concave end of the grease gun nozzle to seal against the nipple even if it is not exactly aligned. As grease pressure increases, the nozzle coupler latches on to the grease nipple. Old grease being forced from the bearing is evidence that the grease nipple is accepting grease. Stop applying grease when new grease is forced from the bearing. Clean away the excess grease. At the completion of greasing, the latched-on coupler is released by angling it over until the grease seal is broken. The drop in pressure in the nozzle releases the coupler jaws. 2023-11-24 B-07b Maintenance Practices CASA Part 66 - Training Materials Only Page 308 of 498 Flush Type Fittings The next most common grease fitting is the flush type, which are used in many locations where clearance is a problem. Flush type couplers and injector needles are normally supplied in kits that include different lengths and angles to make access easier. Flush type fittings Button Head Fittings Although button head fittings are still used on some aircraft and equipment, they are not common. A button head coupler (adaptor) must be used with care to prevent damage to the coupler-to-nipple seal. A button head coupler does not require pressure to latch on to the fitting. Button head grease fitting and coupler 2023-11-24 B-07b Maintenance Practices CASA Part 66 - Training Materials Only Page 309 of 498 Grease Guns Grease Guns are available in a wide range of designs. They all inject pressurised grease (or oil) into bearings via a range of interchangeable nozzles. Manual (lever type) grease gun The concave end of a zerk coupler is pushed onto a zerk fitting. Pressure actuated jaws latch onto the fitting as grease pressure rises. © Aviation Australia - Image by Pierre Waldron Three-jaw zerk coupler Note: If it becomes necessary to change nozzles, the new nozzle must be primed before its first use. 2023-11-24 B-07b Maintenance Practices CASA Part 66 - Training Materials Only Page 310 of 498 Each grease gun should be dedicated to a single type of grease and placarded to indicate the type. A manual or pneumatic grease gun can deliver grease to a bearing at pressures of several thousand psi. However, a manual grease gun delivers only about 1.5 grams of grease per pump stroke. The AMM frequently specifies the use of a manual grease gun for certain airframe lubrication tasks to minimise the risk of over greasing. The small quantity of grease delivered per stroke provides some protection against over pressurising bearings and forcing grease into the wrong areas, for example, adjacent electrical wiring, rubber components and mechanical systems such as brake units. Loading the gun with grease There are three methods of loading grease into a manual grease gun. 1. A loader fitting on the grease gun head can accept grease from a filler pump. 2. A grease cartridge can be inserted into the barrel from the head end after first unscrewing the head and pulling the handle down against an internal spring. 3. Alternatively, the barrel can be manually loaded from a bulk source. This method tends to cause pockets of trapped air within the grease in the barrel. This leads to air locks at the pump inlet. When this occurs, an air-release valve on the grease gun head can be operated to vent the trapped air. Note: All guns must be clearly marked with their contents and, most importantly, a check must be made to ensure that the gun is refilled with the same grease or oil as stated on its label. © Aviation Australia - Image by Pierre Waldron Grease gun (pistol-grip type) with contents label 2023-11-24 B-07b Maintenance Practices CASA Part 66 - Training Materials Only Page 311 of 498 Safe Operation of a Grease Gun A grease gun has the potential to cause serious injury due to the extreme pressures generated – several thousand psi. Both manual guns and pneumatic guns produce these pressures. CAUTION: The work area should be well illuminated, and the operator should wear eye protection against jets of high-pressure grease. CAUTION: Injector needles used with flush type fittings pose a particular risk of high-pressure injection injury. An injector needle can inject grease into the hand or finger if it slips off the grease point. There will be a momentary stab of pain but the injury may initially appear minor. However, over the following days the finger may become swollen, stiff, and is likely to become gangrenous. This may result in amputation. A zerk (hydraulic) fitting is less hazardous in this regard because its push-on coupler is more secure. Penetrants and Inhibitors Many products are approved for external and internal protection of aircraft parts, and some are available commercially. Penetrants and inhibitors are normally approved by the aircraft manufacturer and/or operator. Most are available in bulk containers; cans, such as aerosol; or plastic squeeze bottles. Penetrants and inhibitors - WD-40 can Penetrants are used to free seized parts, while inhibitors protect against corrosion; many approved products serve both functions. 2023-11-24 B-07b Maintenance Practices CASA Part 66 - Training Materials Only Page 312 of 498 Dry lubes are used in locations where wet oil or greasy parts are neither practical nor desirable, e.g. turbine engine fan blades, cabin door latches and cockpit seat tracks. Dry lubricant 2023-11-24 B-07b Maintenance Practices CASA Part 66 - Training Materials Only Page 313 of 498 Anti-Seize Compounds Use anti-seize compounds on threaded parts, bushings, igniter and spark plugs, hinges, pivots, rollers, borescope plugs, and heat exchanger or manifold bolts to prevent corrosion and allow easy disassembly. Anti-seize compound prevents galling, seizing and corrosion of metal parts exposed to high temperatures. It can also act as a low-speed lubricant and maintains a corrosion-resistant coating at high temperatures. Anti-seize compounds are often used as a lubricant for press fit assemblies. They must conform to a standard for aircraft use, such as MIL-A-907D, or be approved by the operator or by the aircraft or engine manufacturer. Application of anti-seize compound When torquing threaded parts, you need to compensate for the reduction in assembly friction, which increases torque tension by about 20% and therefore could result in the part being over-torqued. Use the correct approved anti-seize compound. In the wrong application, some silver compounds can cement parts together, making disassembly almost impossible. 2023-11-24 B-07b Maintenance Practices CASA Part 66 - Training Materials Only Page 314 of 498