Clearwater Fire & Rescue Department Vehicle and Machinery Extrication Procedures PDF 05/24/22
Document Details
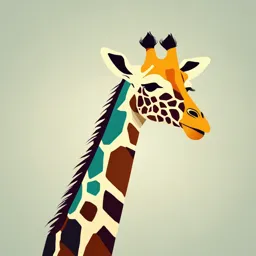
Uploaded by ThrivingIridium
Clearwater Fire and Rescue Department
2022
Scott Ehlers
Tags
Related
- Vehicle Extrication Operations PDF
- Coral Springs-Parkland Fire Department Vehicle Extrication Operations PDF
- Hoffman Estates Fire Department Vehicle Accident & Extrication Guidelines 2022 PDF
- Palm Beach County Fire Rescue Vehicle Accidents PDF
- Palm Beach County Fire Rescue Vehicle Inspection Procedure PDF
- Palm Beach County Fire Rescue Vehicle Accidents PDF SOG 310-02
Summary
This document is a standard operating procedure for vehicle and machinery extrication by the Clearwater Fire and Rescue Department, effective May 24, 2022. It outlines procedures for awareness, operations, and technician levels, covering emergency response, sizing-up incidents, and scene management, in line with NFPA 1670 standards.
Full Transcript
CLEARWATER FIRE AND RESCUE DEPARTMENT STANDARD OPERATING PROCEDURE S.O.P. 620 SUBJECT: Vehicle and Machinery Extrication PAGE 1 O...
CLEARWATER FIRE AND RESCUE DEPARTMENT STANDARD OPERATING PROCEDURE S.O.P. 620 SUBJECT: Vehicle and Machinery Extrication PAGE 1 OF 6 CATEGORY: SUBCATEGORY: Operations APPROVED BY: EFFECTIVE DATE: 03/29/01 REVISION DATE: 06/05/20 REVIEWED DATE: 05/24/22 SIGNATURE ON FILE, APPROVED TO FORM THIS DATE BY SCOTT EHLERS, FIRE CHIEF, FIRE & RESCUE DEPARTMENT FORMS REQUIRED: NOTE: Current forms are located on the Department’s SharePoint. PURPOSE: This procedure covers the emergency response phase and scene management of vehicle and machinery accidents, in accordance to NFPA 1670 “Standard on Operations and Training for Technical Rescue Incidents”. (Chapters 1,2,6) See S.O.G. Section 614.3 – Vehicle Accident Typical Expectations for additional information. This standard identifies and establishes levels of functional capabilities for safely and effectively conducting extrication operations. This procedure is intended to give personnel a basic utilization plan for handling motor vehicle and machinery accidents. Our operational functions are divided into three (3) areas: “Awareness” “ Operations” “ Technician” 620.1 Awareness A. Initial on-scene CFR personnel at vehicle and machinery rescue incidents shall conduct an awareness-level assessment to include development and implementation of the following: 1. Procedures to conduct a size-up of existing and potential conditions. 2. Identification of resources necessary to conduct safe and effective operations. 3. Procedures for implementing the emergency response system for vehicle and/or machinery rescue type incident. 4. Procedures for implementing site control and scene management. 5. Recognition of general hazards associated with vehicle and/or machinery rescue incidents. 6. Initiation of traffic control. 620.2 Operations A. On-scene emergency response personnel at vehicle and/or machinery rescue incidents shall develop and implement of the following operations-level functions: 1. Procedures to identify probable victim locations and survivability. 2. Procedures for making the rescue area safe, including the stabilization and isolation (e.g. Lock-out/ Tag-out) of all vehicles and /or machinery. 3. Procedures to identify, contain, and stop fuel release. SUBJECT: EFFECTIVE DATE: 03/29/01 S.O.P. 620 Vehicle and Machinery Extrication REVISION DATE: 06/05/20 CATEGORY: SUBCATEGORY: PAGE 2 OF 6 Operations 4. Procedures for the protection of a victim during extrication and/or disentanglement. 5. Procedures for the packaging of a victim prior to extrication and/or disentanglement. 6. Procedures for accessing victims trapped in a vehicle and/or machinery through the use of hand tools. 7. Procedures for the mitigation and management of general and specific hazards (i.e. fires and explosions) associated with vehicle and/or machinery rescue incidents. 8. Procedures for the procurement and utilization of the resources (including apparatus, equipment and trained personnel) necessary to conduct safe and effective vehicle and/or machinery rescue operations. 9. Procedures for maintaining control of traffic at the scene of vehicle and /or machinery rescue incidents. 620.3 Technician A. The extrication unit at vehicle and/or machinery rescue incidents shall develop and implement of the following technician-level functions: 1. Procedures for performing extrication and disentanglement operations involving packaging, treating, and removing victims injured and/or trapped in large/heavy vehicles and machinery. 2. Procedures for the advanced stabilization of unusual vehicle and machinery rescue situations. 3. Procedures for the use of all specialized rescue equipment immediately available and in use by the organization. 620.4 Response Requirements A. First Alarm – One (1) Rescue (ALS Unit), One (1) Engine, and One (1) Sunstar B. Extrication Up-Grade – Closest Extrication Unit and S-51 unless S-51 is the closest (T-45, T- 48, S-51) C. Air Transport Up-Grade – One (1) Engine, One (1) DC, and One (1) LR D. Second Alarm – One (1) Rescue (ALS Unit), One (1) Engine, One (1) Squad or One (1) Truck, One (1) DC, One (1) LR, and Sunstar E. Specialized Equipment – Haz-Mat, and/or Technical Rescue, and/or Dive Team, and PD. 620.5 Scene Safety Benchmark A. Scene safety is of paramount importance. This will include the safety of the civilians involved in the incident, the bystanders, and our personnel. Scene safety begins with size up of the initial arriving A.L.S. unit and engine, and safety situation status remains ongoing throughout the incident. 1. Size-Up situation. Minimal required assessment includes: a. Number of vehicles involved b. Number of victims c. Degree of damage (Minor, Moderate, Heavy) d. Lane blockage SUBJECT: EFFECTIVE DATE: 03/29/01 S.O.P. 620 Vehicle and Machinery Extrication REVISION DATE: 06/05/20 CATEGORY: SUBCATEGORY: PAGE 3 OF 6 Operations 2. Identify additional resource required. Select appropriate combination of: a. Extrication up-grade b. Additional alarms c. Haz-Mat d. Air transport e. Public Utilities (Fl. Power, CL. Gas, etc.) f. Scene safety officer 3. Apparatus placement: a. Establish a safe work area b. Block necessary traffic c. Position back enough to deploy hose lines if necessary d. Consider additional responding units (leave sufficient room for extrication units if necessary) 4. Identify location(s) of air bags, and if deployed 5. Initiation of traffic control (utilize assistance from PD) 620.6 Hazard Control and Abatement Benchmark A. Hazard Control and Abatement typically begins with the arrival of the first engine. Functions include: 1. Remove all by-standers from “HOT ZONE” 2. All Personnel in “HOT ZONE” must have full protective clothing, including eye protection 3. Identify all other hazardous conditions (power lines, trip hazards) 4. Placement of a charged foam line on the ground for fire or explosion protection during the extrication phase and/or active fuel leaks 5. Disconnect battery (after unlocking doors, rolling down electric windows, moving electric seats) NOTE: If air bags have not deployed disconnect both negative and positive cables. Remember that air bags can still deploy up to 20 minutes after the batteries have been disconnected. 6. Put vehicle in park and set parking brake – consider chocking wheels 7. Isolate any machinery by Lock-out, Tag-out procedures 8. Control any leaks and spills 620.7 Vehicle Stabilization Benchmark A. Vehicle stabilization is typically completed by the first engine. More complicated incidents will require the immediate assistance of an extrication unit (S51, T45, T48). 1. Perform stabilization techniques 2. Move vehicles that can be safely moved out of the way of an extrication in a controlled manner 3. If vehicles are entangled and cannot be separated, they must all be stabilized as a single unit – consider “marrying” the vehicles together (especially when one vehicle rests on top of the other) 4. Do NOT place cribbing in way of extrication procedures 5. Recheck cribbing frequently (especially after vehicle dynamics have been altered) 6. You may need to let air from tires to assist in stabilization 7. Keep hands from under vehicle while placing cribbing SUBJECT: EFFECTIVE DATE: 03/29/01 S.O.P. 620 Vehicle and Machinery Extrication REVISION DATE: 06/05/20 CATEGORY: SUBCATEGORY: PAGE 4 OF 6 Operations 620.8 Patient Access Benchmark A. Patient contact should be made by the designated paramedic as soon as possible after hazards have been controlled and vehicle has been stabilized or the machine has been locked out/tagged out. DO NOT ENTER A VEHICLE THAT HAS NOT BEEN STABILIZED OR WORK ON A MACHINE THAT HAS NOT BEEN DISABLED. If glass must be broken for patient access, utilize the most appropriate window that is furthest from the patient Cover patient with shield and blanket prior to breaking glass if possible When possible, approach patient head on so as to not cause patient’s head to turn Assess patient to include medical status and degree of entrapment Assist in developing extrication plan with Extrication Group and Incident Commander If possible, cut seat belts unless seat belt is suspending the patient Valuable space can be gained by moving seats back, reclining bucket seats, and tilting steering wheels REMEMBER TO MAINTAIN C-SPINE CONTROL Provide BLS/ALS supportive care Package patient as needed IF EXTRICATION OPERATIONS ARE AFFECTING PATIENT NEGATIVELY, CALL OUT ”FREEZE!!!!!!” AND ADVISE WHAT IS WRONG 620.9 Extrication Benchmark(s) (Technician Level) A. Squad 51, Truck 45, and or Truck 48 will be typically assigned as the “Extrication Group”. Typical tasks may include: “Perform advanced stabilization techniques” “Perform extrication and disentanglement operations” Utilize expertise of plant/machinery personnel when affecting machinery rescues B. Remove all glass Try to roll all windows almost all the way down, cover remaining glass, and then use center punch to break tempered glass. This will allow glass to fall inside door or car body leaving fewer hazards inside the hot zone. Announce “BREAKING GLASS” before doing so Cut windshield CAUTION: Do not breathe glass dust Cut seat belts if not already done and patient is not suspended by the belt C. Assess position of seat belt retractors, pre-tensioners, side-impact air bags, hatch back window rods D. Removing doors Assess easiest access to Nader pin or hinges (sometimes it is easier to take the door at the hinges) When preparing to use spreader, create a bite at strengthened area (at hinges or at Nader pin). If metal rips, stop and try a new bite Consider removing bolts from hinges Have wire cutters ready to cut electric wires Consider Sawsall for cutting hinges or pins SUBJECT: EFFECTIVE DATE: 03/29/01 S.O.P. 620 Vehicle and Machinery Extrication REVISION DATE: 06/05/20 CATEGORY: SUBCATEGORY: PAGE 5 OF 6 Operations DO NOT USE CUTTERS ON NADER PINS If rolling dash later, leave rear doors in place E. Removing roof Be aware of sunroofs Remove interior plastic moldings and cut seat belts Assess position of seat belt retractors and pre-tensioners BE SURE NOT TO CUT INTO SEAT BELT RETRACTORS OR PRE-TENSIONERS Removing exterior window molding will expedite Sawsall use on posts Cut “A” and “C” posts first, “B” posts last – cut posts closest to patient last Do not cut too low on posts (may be needed later for a push point) Have enough personnel on hand to remove the roof (DO NOT HIT RESCUER OR PATIENT INSIDE) Carry roof out of the “HOT ZONE” F. Rolling dash (one technique) Front doors must be open – Removed if possible a. Make cut in floor threshold (rocker panel) just in front of the seat – right at base of “A” post just behind curve on both sides (make sure cut will be ahead of sill plate) OR b. Make cut roughly at center of post as deep as possible Crib on each side of doorsill cut and at base of ram Place sill plate on threshold vertically or horizontally against “B” post Select a ram and push from sill plate to crook a bottom of “A” post Place cribbing under floor cut (or wherever floor creases) Once cribbing is in place, ram should be able to be removed if necessary G. Safety Points All personnel in “HOT ZONE” must wear full protective clothing including eye protection including interior rescuer(s) Coordinate all tasks through Extrication Group Cover sharps whenever possible Let the tool do the work MOVE AN INCH, CRIB AN INCH DO NOT GET CAUGHT BETWEEN THE TOOL AND THE VEHICLE Do not force the tool Have a “PLAN B” ready 620.10 Removal and Transfer Benchmark A. Once patient has been disentangled, treatment will continue, and he/she will be packaged and transported in accordance with Pinellas County Medical Operations Manual standard of care. B. Extrication Group should advise Incident Commander “PATIENT HAS BEEN EXTRICATED” for communication to Dispatch. SUBJECT: EFFECTIVE DATE: 03/29/01 S.O.P. 620 Vehicle and Machinery Extrication REVISION DATE: 06/05/20 CATEGORY: SUBCATEGORY: PAGE 6 OF 6 Operations 620.11 Termination Benchmark A. Upon completion of the incident, Clearwater Fire & Rescue personnel will pick up, clean, and store equipment on the apparatus in accordance with the vehicle inventory. B. Incident Commander should ensure that Dispatch is aware the incident was an “EXTRICATION OPERATION”.