WHMIS Systems Components (PDF)
Document Details
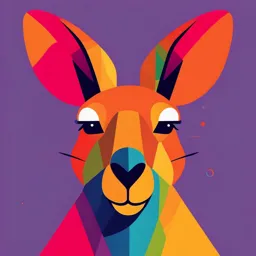
Uploaded by Reusl
Tags
Related
- Workplace Hazardous Materials Information System (WHMIS) PDF
- Industrial Safety Programs for Power Engineers PDF
- WHMIS Past Paper, 3rd Class Edition 3 - Part A2 - Safety Management Systems PDF
- WHMIS 2015 PDF
- Safe Handling of Chemicals Presentation PDF
- WHMIS Workplace Hazardous Material Information System PDF
Summary
This document discusses the components of the WHMIS systems, covering hazard identification, labeling, safety data sheets, and worker training. It outlines the responsibilities of suppliers, employers, and workers in handling hazardous materials within a workplace setting. The document emphasizes the importance of safety measures for those working with hazardous substances.
Full Transcript
Handling of Dangerous Materials • Chapter 3 ========================== OBJECTIVE ========== 2 Discuss the essential components required in the WHMIS systems. Both WHMIS 1988 and 2015 systems consist of essentially four main components. 1. Hazard identification and product classification 2. Lab...
Handling of Dangerous Materials • Chapter 3 ========================== OBJECTIVE ========== 2 Discuss the essential components required in the WHMIS systems. Both WHMIS 1988 and 2015 systems consist of essentially four main components. 1. Hazard identification and product classification 2. Labelling 3. Material Safety Data Sheets (MSDS) for WHMIS 1988 and Safety Data Sheets (SDS) for WHMIS 2015 4. Worker training and education WHMIS is enforced by the departments or agencies responsible for health and safety across all Canadian jurisdictions. The roles and responsibilities for suppliers, employers, and workers will remain the same in WHMIS2015. Note: The first component, "Hazard Identification and Product Classification" was not specifically listed as part of the WHMIS 1988 literature outline. However, it was a component of the WHMIS program. USE OF HAZARDOUS PRODUCTS IN THE WORKPLACE What must a "Supplier" do? Suppliers that manufacture or import hazardous products are required to: a) Classify products by labelling b) Provide Safety Data Sheets (SDS) or Material Safety Data Sheets (MSDS) to their customers What must an "Employer" do? When utilizing hazardous products in the workplace, the employer must: a) Ensure the products are properly labelled b) Ensure the products have an SDS sheet (or MSDS sheet) c) Ensure the products have workplace labels prepared as needed d) Use proper control measures to keep the workplace and employees safe e) Educate and train workers about these hazardous materials and how to use them safely In addition, if the employer makes or manufactures hazardous materials on the premises, they must prepare an SDS for each product. What must a Worker do? Workers must: a) Participate in their training and education b) Protect themselves and their co-workers c) Participate in identifying and controlling hazards 4th Class Edition 3 • Part A 3-5 Unit A-4 • Introduction to Plant and Fire Safety ==================== ================== LABELLING The two types of labels required are supplier labels and workplace labels. Supplier labels contain extensive information about the hazardous product, written in a specific manner, and have specific content. Supplier labels must be on every hazardous product that comes into the worksite. If not, the product cannot be used until one is supplied. Supplier labels are the first source of information any employee is likely to see about the product. It will provide all the information required in order to use it safely. The following table provides a list of required information on a supplier label. Required Information Description 1. Product Identifier The exact product name appears on the container and on the SDS. 2. Hazard Pictograms Determined by the hazard classification of the product. In some cases, no pictogram is required. 3. Signal Word (New) "Danger" or "Warning" is used to emphasize and indicate the sev erity of the hazards 4. Hazard Statement Brief standard statements of all hazards based on the hazard classification of the product. 5. Precautionary Statements Gives the recommended measures to minimize or prevent negative effects from exposure to the product, including utilizing protective equipment and emergency actions. 6. Supplier Identifier Contact information of the company responsible for this product. Workplace labels also have specific content, but are much simpler and contain only basic information. They are intended to be written by the worker or the employer, and are to be used only in the workplace. Workplace labels are required if a supplier label is damaged, or if hazardous material is poured into a different container for use within the same workplace. SAFETY DATA SHEET (SDS) AND MATERIAL SAFETY DATA SHEET (MSDS) Prepared by the manufacturer of the product, an SDS/MSDS provides a detailed description of the hazardous material. The employer is responsible for preparing the data sheet if the product is manufactured on the worksite. Of the three documents - workplace label, supplier label, and SDS - the SDS is the most comprehensive. It will be used by workers and employers, but may also be referenced by safety attendants and medical professionals. The SDS and MSDS are similar documents. Both provide comprehensive identification information for the hazardous material in question. There are minor differences between the SDS and the MSDS. The SDS, however, conforms to an international method of identification in reference to the GHS. 7----------------------s 4th Class Edition 3 • Part A 3-6 Handling of Dangerous Materials • Chapter 3 Table 1 is a comparison of the WHMIS 2015 Safety Data Sheet (SDS) (16 sections) and the 1988 Material Safety Data Sheets (MSDS) (9 sections). SDS contains additional sections to give more information regarding the material. Table 1 - 2015 SDS and 1988 MSDS I 2015 - SDS Section 1988 - MSDS 1 Identification 2 Hazard Identification 3 Composition/Information on Ingredients Hazardous Ingredients 4 First Aid Measures First Aid Measures 5 Fire-Fighting Measures Fire and Explosion Data 6 Accidental Release Measures 7 Handling and Storage 8 Exposure Controls/Personal Protection Preventive Measures 9 Physical and Chemical Properties Physical Data of Product 10 Stability and Reactivity Reactivity Data 11 Toxicological Information Toxicological Properties 12 Ecological Information 13 Disposal Considerations 14 Transport Information 15 Regulatory Information 16 Other Information Product Identification and Use MSDS Preparation and Update Information WHMIS Training for the Worksite The employer must provide WHMIS training to the workers. Employee training should cover all aspects ofWHMIS. Instruction should also include: a) Proper use of supplier labels, workplace labels, and other forms oflabelling in the plant. b) Safe use of hazardous materials on site, and the safety features and other conditions in the plant that the use of these materials requires c) Proper use of Personal Protective Equipment. d) Location of safety equipment such as eyewash fountains, emergency showers, and first aid room. e) Location of the SDS and other safety literature. The employer must be able to verify that the worker has completed the training, and has competent knowledge of the WHMIS program. This is usually a test approved by a safety officer or other Jurisdictional representative. After a test is completed, the worker will undergo hands on training. The worker must become familiar with the practices of working with hazardous materials in the workplace. Note: Additional training will be required, beyond this course material. The Employer is responsible to provide appropriate training in each employment assignment. 4th Class Edition 3 • Part A 3-7