Role of Manufacturing Towards Achieving Circular Economy: The Steel Case PDF
Document Details
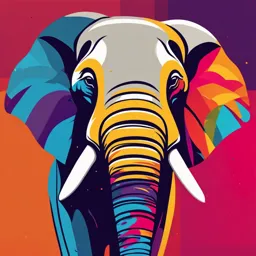
Uploaded by BestJudgment4422
Universidad de los Andes
2018
Peng Wang, Sami Kara, Michael Z. Hauschild
Tags
Summary
This journal article examines the role of manufacturing in achieving a circular economy, using the steel industry as a case study. The authors investigate how dynamic material flow analysis and stock dynamics can help understand this role. The article concludes that the circular economy will continue to be crucial to the industry for the foreseeable future and that more focus should be placed on strategies for the whole lifecycle of the process.
Full Transcript
CIRP Annals - Manufacturing Technology 67 (2018) 21–24 Contents lists available at ScienceDirect CIRP Annals - Manufacturing Technology jou rnal homep...
CIRP Annals - Manufacturing Technology 67 (2018) 21–24 Contents lists available at ScienceDirect CIRP Annals - Manufacturing Technology jou rnal homep age : ht t p: // ees.e lse vi er. com /ci r p/ def a ult. asp Role of manufacturing towards achieving circular economy: The steel case Peng Wang a, Sami Kara (1)a,*, Michael Z. Hauschild (1)b a Sustainability in Manufacturing and Life Cycle Engineering Research Group, School of Mechanical and Manufacturing Engineering, The University of New South Wales, Sydney, Australia b Division for Quantitative Sustainability Assessment, Department of Management Engineering, Technical University of Denmark, Lyngby, Denmark A R T I C L E I N F O A B S T R A C T Keywords: Circular economy (CE) has been promoted worldwide as a strategy to reduce material use and to increase the Sustainable development material use efficiency by closing material loops at the societal level. The core concept of CE is to improve the Manufacturing circularity of material use through turning materials at the end of their service life into resources for others, Circular economy however, there is very little information about the role of manufacturing in achieving CE. Using the concepts of dynamic material flow analysis and stock dynamics, this paper proposes a methodological approach to help understand the role of manufacturing in achieving CE. A number of other strategies such as material efficiency in conjunction with CE are also tested using the case of global steel use to draw conclusions. © 2018 Published by Elsevier Ltd on behalf of CIRP. 1. Introduction been well studied and appreciated. Hence, this study aims to reveal the critical role of manufacturers in achieving CE from a life-cycle based As resources become scarcer and associated impacts rise, the framework. linear pattern of ‘take, make and dispose’ in industry and society Such investigation requires a quantitative description and predic- calls for a change. In this context, circular economy (CE) has gained tion on how materials are fed, processed, stored, and recycled inside significant attention among global stakeholders including manu- the anthropogenic material cycle (AMC). Among all involved methods facturers [1–4]. The core concept of CE is to improve the circularity , the industrial ecology provides two well-established tools to of material use (i.e. recycling, remanufacturing, reuse, etc.) through serve this aim, i.e. dynamic material flow analysis (MFA), and stock turning materials at the end of their service into resources for dynamics. Herein, the dynamic MFA can systematically quantify the others [3,4]. Nevertheless, this End-of-Life (EoL)-based CE has been inflow, outflow, and loss of a given material in a process or system over criticized recently on its the feasibility of implementation , cost some period based on the mass balance principle. Stock dynamics competitiveness , rebound effect , effectiveness , etc. helps to depict the mechanism in end-of-life material flow generation Hence, a holistic investigation is highly demanded. and explore drivers in the growth of material in-use stocks, defined as Materials are essential for manufacturers to produce various the sum of material in all included in-use products. Dynamic MFA products. Meanwhile, decisions from manufacturers regarding and stock dynamics have been combined as a powerful tool to predict selection and use of materials in their corresponding activities the future global material stocks and flows in its anthropogenic cycle strongly affect the way how the material is processed in its entire life under different scenarios. cycle stages (i.e. production, manufacturing, use, and recycling). Over Iron and steel (henceforth described as steel) is selected as case the past decades, manufacturers have developed and promoted study to explore the role of manufacturing in achieving CE. Steel is various concepts (e.g. efficient manufacturing , eco-design , etc.) chosen because (a) it is the world’s most used metal for embodied in life cycle engineering (LCE) to manage the manufacturing of various products and (b) as a metal it can retain corresponding products and materials from a life cycle perspective. its utility after multiple runs of recycling and is acknowledged as the Nevertheless, only limited LCE tools have been included to assist the world most recycled metal. Hence, with abundant studies CE. Herein, the Cradle to Cradle design framework proposed by available [6,14,15], this study can provide convincing results on how Mcdonough and Mcdonough is a perfect example which aims to manufacturing contributes towards achieving CE, rendering the steel design the product in a way that enables the waste in the EoL stage to case a useful exemplary case for other materials in CE study. become a resource for manufacturing of another product at the same or higher level (upcycling). However, from a broader systematic 2. Methodology perspective, the contribution of manufacturers in achieving CE has not 2.1. Life cycle framework * Corresponding author. Implementation of circular economy can be monitored through E-mail address: [email protected] (S. Kara). the information of routes and magnitude of material in its https://doi.org/10.1016/j.cirp.2018.04.049 0007-8506/© 2018 Published by Elsevier Ltd on behalf of CIRP. 22 P. Wang et al. / CIRP Annals - Manufacturing Technology 67 (2018) 21–24 products. The well-established lifetime distribution approach [14,17] is applied: Z t Outf low ðtÞ ¼ Inf low ðxÞ f ðx; t ; vÞdx ð2Þ 1900 where f(x,t ,v) is the probability densities of the lifetime distribution function (assumed to follow Weibull distribution here), t is the lifetime of the product x, t is the current time, and v is the lifetime distribution parameter. The detailed step-by-step calculation for each stage can be found in Refs. [11,15]. 2.3. Depicting the impact of LCE tools on material flowanalysis The overall study includes the historical quantification and future projection. The indicators shown in sub-system B of Fig. 1 are quite critical for this quantification as they determine the performance of the AMC. There are 6 RE indicators that reflect the efficiency of LCE tools (metal recovery rate, recycling rate, etc.) and 3 in-use based indicators representing central aspects of the in-use stage (number of consumers, material intensity of the Fig. 1. Life cycle framework to link the LCE tools from manufacturers with material consumption and lifetime of products). For the historical use in its anthropogenic cycle. (Note: P: material production stage; M: manufacturing stage; U: in-use stage; E: end-of-life stage; A: sub-system A; B: quantification, values for those indicators are obtained directly sub-system B; C: sub-system C.) from the mass ratio of outflow to inflow or statistics. As for the future projection, those indicators are exogenously given in anthropogenic cycle. The corresponding decisions and activities scenario settings. More detailed scenarios are set based on the (e.g. LCE tools) from manufacturers can have profound impacts on change of those indicators driven by the corresponding LCE tools. the entire life cycle stages, which includes but not limited to (a) Moreover, the future projection is conducted with the well- determining the material flows and losses inside manufacturing, established stock dynamics approach. The final step is to (b) selecting ‘cleaner’ material from more efficient producers, (c) compare the results in those scenarios with the basic scenario to improving the product design with less material use for same gauge the impact of LCE tools in achieving CE. service and for durability and longevity; and (d) designing products for reusability, recyclability, and remanufacturing. 3. Steel case and scenarios settings Therefore, a novel life cycle framework to link the LCE tools and AMC is shown in Fig. 1. Within the framework, three sub-systems Case study requires various input parameters (i.e. 6 RE indicators are integrated. Sub-system A (the anthropogenic material cycle) is and 3 in-use based) as introduced in Section 2.3. For the historical located at the center of this framework which presents the quantification, the study directly adopted the results on historical material stocks and flows along its life cycle. Sub-system B material flows and stocks from previous work for the year 1900–2013 (material cycle indicators) comprises the major indicators in , in which those key indicators, and the historical demand and in- determining the material stocks and flows in the anthropogenic use stocks were obtained. For future projection, those input cycle. Sub-system C (LCE tools) is located at the outer ring of this parameters are assumed in various scenario settings in Table 1, framework, and some representative LCE tools are selected and which involves three elements: population trend estimation, per allocated to each life cycle stage. capita material in-use stock growth, and changes in other key indicators as follows: (a) the future population is based on the 2.2. Dynamic material flow modeling medium scenario in “World Population Prospects” published by United Nations Population Division. (b) The material intensity is AMC is a key concept in industrial ecology with quantitative allocated to the per capita basis using the per capita in-use stock as tools (e.g. MFA) to depict the material stocks and flows in the the proxy. The future trend of in-use growth is estimated based on anthropogenic cycle which includes four major life cycle stages: i.e. the saturation hypothesis which observed that most developed material production, manufacturing, in-use, and end-of-life. Apart countries follow a similar saturation pattern of per capita in-use from the linear flows from one stage to its following stage, four stock growth. The saturation level is around 13.4 tons steel per capita. circular routes of scraps (i.e. prompt scrap recycling, reuse, Finally, (c) the changes in key RE indicators and lifetime of products remanufacturing, and recycling of EoL scrap) have also been are determined by the scenario settings. captured in the framework. This study follows the basic dynamic Moreover, a product-specific treatment is applied to obtain MFA procedure [14,17]. For three of the life cycle stages (i.e. more detailed results in three life cycle stages (i.e. manufacturing, material production, manufacturing, and end-of-life), the mass- in-use, and end-of-life), which are quantified based on four major balance principle is applied to obtain the material inflow, outflow, categories of steel final products (i.e. construction, vehicles, and loss at the time t for stage k; machinery, and durable daily goods and others). Table 1 gives the information of the specific scenarios and the Outf low ðk; tÞ ¼ Inf low ðk; tÞ loss ðk; tÞ settings of key indicators for the steel case allocated to each life cycle ¼ Inf low ðk; tÞ RE ðk; tÞ ð1Þ stage. This study applies two main scenarios, i.e. baseline scenario (BLS) and LCE scenario (LCES): BLS represents a business-as-usual The Eq. (1) can be solved for (a) outflow using production statistics estimation of future trendswithout additional policy intervention, and (e.g. world steel yearbook) of each unit stage, (b) inflow using the LCES includes the implementation of LCE tools to improve the material mass balance with production statistics in the upstream and use along its full life cycle. To clarify the stage-specific impact of those downstream unit stage, (c) loss using the mass balance of inflow LCE tools, seven sub-scenarios were proposed to integrate the LCES (as and outflow, and (d) resource efficiency (RE) of this unit stage, shown in Table 1). Based on detailed studies in Refs. [14,15,17], the defined as the mass ratio of outflow to inflow. current value and future potential values can be obtained for the steel Meanwhile, for the in-use stage, its outflow is determined by case for most MFA indicators. With the attention and implementation using historical inflow to in-use stage and use lifetime of different of LCE tools, this study assumed that they can reach their full potentials P. Wang et al. / CIRP Annals - Manufacturing Technology 67 (2018) 21–24 23 Table 1 Parameter settings for future scenarios (based on Refs. [14,15,17]). Lifecycle stage Key indicators 2013 2050 2100 LCE tools Scenarios Abbreviation Material Metal recovery rate for ore-based 70% 70% 70% None Baseline scenario BLS production material production 70% 73% 73% Material selection Efficient material production EMP Metal recovery rate for 94% 94% 94% None Baseline scenario BLS scrap-based production 94% 97% 97% Select low-impact materials Efficient material production EMP Manufacturing Resource efficiency in 87% 87% 87% None Baseline scenario BLS manufacturing 87% 92% 92% Efficient manufacturing Efficient manufacturing EMN In-use Desired service level Follow the developed None Baseline scenario BLS countries’ pattern Saturating at 77.5% of Design for less material for Efficient material use EMU developed countries’ same service level Product lifetime Keep the lifetime same None Baseline scenario BLS for products Increase the lifetime to Design for durability Longer use lifetime LUL its potential End-of-life Recycling rate 78% 78% 78% None Baseline scenario BLS 78% 90% 90% Design for recycling Recycling scenario RYS Remanufacturing rate 0% 0% 0% None Baseline scenario BLS 0% 12% 12% Design for remanufacturing Remanufacturing scenario RMS Reuse rate 0% 0% 0% None Baseline scenario BLS 0% 12% 12% Design for reuse Reuse scenario RUS AMC All indicators Changes of indicators in all scenarios Life cycle engineering LCES above expect BLS in 2050 which is similar with Ref.. It is noted that two indicators indicative to reveal the relative impact of those strategies on future (i.e. remanufacturing rate and reuse rate) have not been modeled in efficiency in AMC, rather than giving an accurate future prediction. AMC studies for the unrecycled EoL amount. Herein, this study With regards to production trends in manufacturing, findings need to included these indicators in our AMC quantification to fit the be highlighted as follows: framework in Fig. 1, and their future trends are assumed to be increased with the same value (12%) as the recycling rate improvement (1) Despite the fact that steel has been consumed extensively in the since they are all included in the end-of-life stage. past century, the demand for this material will continue to grow strongly in the future under any scenario setting. As shown in Fig. 2A, the steel manufacturing is expected to expand its capacity 4. Results and discussion from two to four times at the end of this century compared to the level in 2000. The development of the population is one driver as it 4.1. Future steel demand remains high and will be shifted from ore- will increase from around 7 billion in 2013 to 11 billion in based to scrap-based resource 2100. Another factor, affluence, plays a more deterministic role as the in-use stock per capita increases much more significantly from This study obtained the 9 sets of results (i.e. for 9 scenarios from BLS 4 tons in 2013 to 12.3 tons (or 10 tons in EMU and LCES) in 2100. In to LCES in Table 1) regarding annual steel stocks and flows along the this context, managing the life cycle of steel use efficiently gains AMC from 1900 to 2100. Meanwhile, the results of the model have extreme importance for manufacturers and other stakeholders. been compared with historical data of in-use stocks , and a good Indeed, compared with the BLS scenario, the scenarios of EMU and conformity (i.e. less than 2% in variation) is obtained. For the LCE can help to reduce future demand in 2100 by around estimated years from 2014 to 2016, our results also give a relatively 684 million tons per year (Mt/yr) and 1323 Mt/yr, respectively, accurate result (less than 4%) compared with official data in mining compared to around 3400 Mt/yr as total demand in BLS. production. Nevertheless, the prospective results are highly (2) The scrap-based material will dominate future material sources sensitive to the scenario settings. Hence, they should be considered as for manufacturing. All scenarios are expected to have more than 50% input as scrap at the end of this century, which will trigger a reverse trend for manufacturing from handling the ore-based material to the handling of scrap-based material, as already proposed in Ref.. Hence, how to maintain and use the scrap becomes a critical future challenge for manufacturers. 4.2. The importance and inadequacy of EoL-based strategies Material circularity needs to gain importance in the future as the EoL scrap keeps increasing unprecedentedly as shown in Fig. 2B. Steel already has a good recycling performance thanks to the implemen- tation of CE and other EoL-based strategies. Nevertheless, steel still needs a better performance in recycling and reuse of scraps. As shown in Fig. 2A and B, the EoL scrap generation is enough to fully satisfy the future steel demand. However, although the recycling rate of scraps reaches its maximum in several scenarios, the scrap still fails to entirely meet the steel demand. In practice, recycling rates cannot reach 100% due to the limitations in collection, sorting, and separation in the recycling stage, and metal recovery in the production stage. As a result, the more and faster the EoL scrap flows, the more resource will be lost Fig. 2. Results for nine scenarios. (Note: (A) outflow from manufacturing (Mt/yr); and the higher impact will be caused by turning those scrap into (B) end-of-life scrap generation (Mt/yr), (C) mining production (Mt/yr), (D) resource loss from all life cycle stages (Mt/yt), and Mt: million tons; yr: year.) resource. In other word, end-of-life strategies can be viewed as end- 24 P. Wang et al. / CIRP Annals - Manufacturing Technology 67 (2018) 21–24 of-pipe solutions. This recognition reveals an inadequacy of EoL- how products are designed, produced, and managed to satisfy the based strategies which has barely been noticed before. Indeed, the market needs. As a result, the concepts related to manufacturing current CE package focuses excessively on the circularity of (i.e. design for durability and longevity and better product design materials, mainly underlining the end-of-life activities (e.g. recy- with less material use) can play a great role. And corresponding cling, reuse, and remanufacturing in Ref. ). The reduction of EoL new business models are further required. scrap generation should be prioritized since EoL-based strategies are shown to have a limited impact there. As shown in Fig. 2B, all 5. Conclusion circularity-oriented scenarios (i.e. RYS, RMS, and RUS—see Table 1) fail to reduce the end-of-life scrap generation compared with BLS. There is a great importance and urgency to expand the focus of the circular economy from the end-of-life to the entire life cycle of 4.3. The need to expand the CE package by incorporating strategies products. This can be implemented through LCE tools in the targeting the entire life cycle manufacturing stage as well as new value propositions in the business models. This recommendation builds on results obtained Resource depletion and loss are two important indicators to through the combination of two types of approaches in this work, (a) gauge the efficiency of the entire anthropogenic cycle , which a general framework to clarify the role of LCE tools in managing the can give a broader view regarding the efficiency of a given strategy anthropogenic material cycle; (b) a quantitative method (i.e. in improving anthropogenic material use. The trends of resource dynamic MFA) to gauge the corresponding leverage of each LCE depletion (using mining production as a proxy) and resource loss in tool in the anthropogenic material cycle; and (c) their application to a all scenarios are shown in Fig. 2C–D. case study to quantify the anthropogenic steel cycle annually from The material production and manufacturing stage-specific 1900 to 2100. The results indicate that steel faces an unprecedented strategies (in scenario EMP and EMU) are slightly better than need in the future and that it is essential to implement CE strategies BLS in reducing resource depletion and resource loss. It should be regardless that steel is already one of most recycled and efficiently acknowledged that the manufacturing stage has already been very used materials. Moreover, manufacturing efforts inside the factory efficient, and the potentials have nearly been fully achieved. Hence, have limited impact but manufacturing can apply strategies to the EMN scenario, which focuses on efficient manufacturing, has a promote lifecycle-based CE, especially strategies related to in-use limited impact. Meanwhile, the potential of EMP is constrained by stage. Hence, it is highly recommended to include the entire life cycle the metallurgical limits in terms of metal recovery. in the CE policy making and implementations around the world and This study also reveals the significant contributions from in-use involve manufacturers to play a core role in this effort. stage-specific strategies (i.e. efficient material use, and longer use lifetime) in promoting the performance of AMC. And this strategy is much more efficient than end-of-life stage-specific scenarios, and their potentials for improvement are also considerable. With References around 23% less material use, EMU can help to save around 250 Mt Lieder M, Rashid A (2016) Towards Circular Economy Implementation: A ore use per year. Meanwhile, about 250 Mt/yr ore can be reduced by Comprehensive Review in Context of Manufacturing Industry. Journal of prolonging the lifetime of products to their potentials (which vary Cleaner Production 115:36–51. between product categories—see details in Ref. ). Zink T, Geyer R (2017) Circular Economy Rebound. Journal of Industrial Ecology 21(3):593–602. The LCES scenario combines all studied strategies in above European Commission (2015) Closing the Loop—An EU Action Plan for the scenarios and has the best performance in reducing EoL scrap Circular Economy, European Commission, Brussels, Belgium. generation, reducing ore resource consumption, and reducing the Mcdonough W, Mcdonough W (2002) Cradle to Cradle—Remaking the Way We Make Things, North Point Press, New York, NY, USA. resource loss from the AMC as shown in Fig. 2B–D. Meanwhile, the Allwood J (2014) Squaring the Circular Economy: The Role of Recycling within a joint implementation of all those life cycle tools in the LCES Hierarchy of Material Management Strategies. Handbook of Recycling, Elsevier scenario can outperform any other scenarios by a huge advantage. Inc., Waltham, MA. Wang P, Li W, Kara S (2017) Cradle-to-Cradle Modeling of the Future Steel Flow For instance, the LCES scenario will consume around 560 Mt/yr ore in China. Resources Conservation and Recycling 117:45–57. in 2100, which is just above half of the amount (around 1073 Mt/ Pedersen G, Hauschild M (2016) Circular and Safe? The 6th International yr) in the best singular strategy—LUL scenario (in Fig. 2C). These Symposium on Food Packaging, Barcelona, Spain. 16-18 November. Duflou J, Sutherland J, Dornfeld D, Herrmann C, Jeswiet J, Kara S, Hauschild M, results demonstrate the importance of expanding the EoL-oriented Kellens K (2012) Towards Energy and Resource Efficient Manufacturing: A CE to a life-cycle based CE. Processes and Systems Approach. CIRP Annals 61:587–609. Shu L, Duflou J, Herrmann C, Sakao T, Shimomura Y, De Bock Y, Srivastava J (2017) Design for Reduced Resource Consumption During the Use Phase of 4.4. Role of manufacturing in leveraging life-cycle based CE Products. CIRP Annals 66:635–658. Hauschild M, Herrmann C, Kara S (2017) An Integrated Framework for Life The life-cycle based CE combines all strategies along the entire Cycle Engineering. Procedia CIRP 61:2–9. life cycle of products and material, and the manufacturing stage is Wang P, Li W, Kara S (2017) Dynamic Life Cycle Quantification of Metallic Elements and Their Circularity, Efficiency, and Leakages. Journal of Cleaner at the center to foster those strategies. Inside the manufacturing Production 174:1492–1502. stage, tools for efficient manufacturing can help to save raw Müller E, Hilty L, Widmer R, Schluep M, Faulstich M (2014) Modeling Metal resources and minimize resource loss as shown in EMN in Stocks and Flows: A Review of Dynamic Material Flow Analysis Methods. Environmental Science Technology 48:2102–2113. Fig. 2. Nevertheless, it should be acknowledged that strategies World Steel Association (2016) Steel—The Permanent Material in the Circular exclusively focusing on the manufacturing stage have limited Economy, World Steel Association, Brussels/Beijing. potential and impact compared with the strategies focusing on Pauliuk S, Milford R, Mu D, Allwood J (2013) The Steel Scrap Age. Environmental Science Technology 47:3448–3454. other stages. Hence, manufacturers should be urged to expand Pauliuk S, Wang T, Müller D (2013) Steel All over the World: Estimating In-use their focus to the entire life cycle of material use applying their Stocks of Iron for 200 Countries. Resources Conservation and Recycling 71:22–30. influence through the implementation of various LCE tools. Chen W, Graedel T (2012) Anthropogenic Cycles of the Elements: A Critical Review. Environmental Science Technology 46:8574–8586. It is of vital importance to have a joint use of those life cycle Milford R, Pauliuk S, Allwood J, Müller D (2013) The Roles of Energy and tools. Nevertheless, this study reveals the huge differences on the Material Efficiency in Meeting Steel Industry CO2 Targets. Environmental impact of the LCE tools corresponding to the different life cycle Science Technology 47:3455–3462. United Nations Population Division (2015) World Population Prospects (2015 Re- stages of steel products. The EoL-based strategies are indeed vision), United Nations, New York, USA. preferable to the strategies inside factories. However, the strategies Ober J (2017) Mineral Commodity Summaries 2017, US Geological Survey, related to the in-use stage can greatly outperform EoL-based Reston, VA, USA. strategies because in-use strategies can not only reduce the EoL Reck B, Graedel T (2012) Challenges in Metal Recycling. Science 337 (6095):690–695. flow generation but also support the increasing affluence with less Ellen MacArthur Foundation (2015) Delivering the Circular Economy: A Toolkit material use. Furthermore, manufacturing can greatly influence For Policymakers, Ellen MacArthur Foundation, Cowes, United Kingdom.