Répartition et Lyophilisation PDF
Document Details
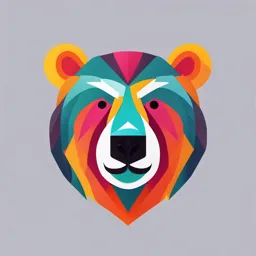
Uploaded by YouthfulCosine
IMT
Tags
Summary
Ce document présente les étapes de la répartition et de la lyophilisation des médicaments. Il détaille les différents types d'eaux utilisées, les opérations de répartition et de lyophilisation et les équipements nécessaires.
Full Transcript
2.3 LES OPERATIONS DE REPARTITION / LYOPHILISATION © Groupe IMT. Toute reproduction sans autorisation est interdite. © Groupe IMT. Toute reproduction sans autorisation est interdite. 2 LA QUALITE DES EAUX PHARMACEUTIQUES Eau = matière première la plus utilisée dans l’industrie pharmaceutique et cosm...
2.3 LES OPERATIONS DE REPARTITION / LYOPHILISATION © Groupe IMT. Toute reproduction sans autorisation est interdite. © Groupe IMT. Toute reproduction sans autorisation est interdite. 2 LA QUALITE DES EAUX PHARMACEUTIQUES Eau = matière première la plus utilisée dans l’industrie pharmaceutique et cosmétique et surtout sur les sites d’injectables En fabrication (en moyenne 98% d’un PF injectable) En tant qu’agent externe (circuits de refroidissement, nettoyage des locaux et du matériel) Elle doit être traitée comme une MP : respect de sa qualité et respect des quantités nécessaires. 3 Eaux définies à la Pharmacopée Européenne Eau purifiée : nettoyage et fabrication des formes non stériles Eau pour préparations injectables (Eau ppi) : préparations injectables 4 L’eau purifiée C’est une « eau destinée à la préparation de médicaments autres que ceux qui doivent être stériles et exempts de pyrogènes, sauf exception justifiée et autorisée ». a) L’eau purifiée en vrac est préparée => soit par distillation, => soit à l’aide d’un échangeur d’ions, => soit par tout autre procédé approprié, à partir d’une eau destinée à la consommation humaine. » b) L’eau purifiée conditionnée en récipients est de l’eau purifiée en vrac répartie en récipients et conservée dans des conditions visant à assurer la qualité microbiologique requise. Elle est exempte de tout additif. 5 L’eau pour préparations injectables (EPPI) C’est une « eau destinée à la préparation de médicaments administrés par voie parentérale dont le véhicule est aqueux ». L’eau pour préparations injectables en vrac est obtenue à partir d’eau potable ou d’eau purifiée qui est distillée. Le distillat est ensuite recueilli et conservé dans des conditions destinées à éviter toute croissance de micro-organismes et toute autre contamination. 6 © Groupe IMT. Toute reproduction sans autorisation est interdite. 7 © Groupe IMT. Toute reproduction sans autorisation est interdite. 8 FORMULATION TRAITEMENT DES AC PREPARATION STERILISATION (voire dépyrogénéisation) DES AC TRANSFERT REMPLISSAGE/FERMETURE LYOPHILISATION (si besoin) STERILISATION FINALE (si besoin) MIRAGE 9 CONDITIONNEMENT 1) Formulation On utilise comme véhicule : EPPI SOLVANTS NON AQUEUX Ils sont de nature très diverses. On trouve des hydrocarbures (paraffine additionnée ou non de vaseline), des alcools, des glycols, des huiles végétales… Ces solvants doivent avoir certaines propriétés (solubilité, viscosité, pureté, activité propre et innocuité). C’est le solvant le plus normal et le plus général pour les médicaments administrés par voie parentérale mais on peut avoir recours à d’autres solvants pour les PA peu solubles dans l’eau ou instables en milieu aqueux et aussi pour avoir un effet prolongé. 10 2) Préparation en classe C SOLUTIONS Méthodes de dissolution classiques. Au PA sont ajoutés tous les adjuvants nécessaires (pH, isotonie, bactériostatique, antioxydants, conservateurs antimicrobiens…) EMULSIONS Elles doivent être extrêmement fines donc les particules doivent être de l’ordre du micron. Elles ne doivent pratiquement pas contenir, du fait de leur mode d’administration, de particules de plus de 5µm. Leur mise au point est très délicate. SUSPENSIONS POUDRES Choisies lorsque le PA est insoluble dans l’eau ou lorsqu’on désire un effet prolongé du médicament. Taille des particules : entre 0,1µm et 10µm. Phase liquide : eau ou huile et ne doit pas du tout dissoudre le principe en suspension pour éviter phénomène de croissance des cristaux. 12 Doivent être de ténuité suffisante pour être facilement remises en solution ou suspension. Etape de filtration hors classe - Filtration Clarifiante des solutions à 0,45µm Pas de filtration pour les émulsions et suspensions mais contrôle du process de manière à assurer que la taille des globules ou particules est compatible avec la voie d’administration - Filtration Stérilisante des solutions à 0,22µm © Groupe IMT. Toute reproduction sans autorisation est interdite. 13 3) Traitement des AC a) Les AC les plus couramment utilisés AC FERMETURE Flacon verre Bouchon en caoutchouc + bague aluminium + capsule de protection Flacon plastique Technique du BFS ou bouchon plastique Ampoule verre bouteille Scellage par chalumeau Seringue pré-remplie Joint piston Poche souple Queusots ou BFS Cartouche ou carpule Capsule en caoutchouc 14 CARACTERISTIQUES La matière doit être : suffisamment transparente (vérification visuelle) inactive sur la préparation avec laquelle elle est en contact de nature à ne pas diffuser dans ou à travers la matière du récipient et éviter l’introduction de contaminants. b) Lavage des AC Objectif : Retirer les particules et l’eau résiduelle pour éliminer les contaminations par des corps étrangers. Etape de lavage par injection d’eau PPI à l’aide de buses de projection L’opérateur alimente le magasin d’ampoules et contrôle les paramètres de lavage Séchage par soufflage d’air stérile Dans le cas des carpules ou des seringues il y a une étape de siliconage Transfert vers le tunnel de stérilisation 15 b) Stérilisation/dépyrogénéisation (ampoules et flacons) Objectif : Détruire les microorganismes et les pyrogènes pouvant être présents dans les ampoules ou les flacons. Séchage L’opérateur vérifie la pression des filtres, suit la température de stérilisation (graphe) et vérifie le fonctionnement de l’enregistreur Stérilisation Dépyrogénéisation Refroidissement 4) Remplissage/fermeture des flacons en classe B ou A/B Les remplisseuses linéaires L’opérateur vérifie les paramètres machine + tests intégrité filtres et contrôle le produit 17 Elles sont munies de plusieurs tubes plongeurs alimentés chacun par une pompe doseuse. Les flacons arrivent en ligne ; le premier flacon est bloqué par un vérin, les pompes remplissent simultanément les flacons situés sous les tubes plongeurs. Comme pour la plupart des types de remplisseuses, une boucheuse y est associée. Avantage : changement de format rapide Inconvénient : cadence de remplissage limitée Les flacons sont amenés par une vis d’Archimède, introduits sur une étoile et remplis par la buse plongeante durant la rotation de l’étoile. Ce type de remplisseuse peut avoir de 12 à plus de 36 têtes de remplissage. La cadence peut atteindre, dans l’industrie pharmaceutique, 300 flacons / minute. Le remplissage peut être : - Volumétrique - Pondéral - A niveau Avantage : cadence très rapide Inconvénient : changements de format longs Les remplisseuses en continu L’opérateur vérifie les paramètres machine + tests intégrité filtres et contrôle le produit 18 Fermeture des flacons Soit par vissage, soit par enfoncement Apport des bouchons par un bol Distribution et vissage par une visseuse dont le nombre de tours est fonction du couple de serrage c’est à dire de la force de rotation à appliquer pour assurer un vissage étanche mais un dévissage manuel ou dépose sur le flacon et enfoncement Sertissage d’une bague en aluminium à l’aide de molette si nécessaire 19 5) Remplissage/scellage des ampoules bouteilles Dans le col d’une ampoule, on introduit une aiguille par laquelle est injecté un volume bien déterminé de solution. Les ampoules sont remplies une à une. L’opérateur vérifie les paramètres machine + tests intégrité filtres et contrôle le produit Les ampoules peuvent subir une étape de pré-inertage, d’inertage et de post-inertage 20 Les ampoules sont ensuite scellées par rotation dans la flamme des chalumeaux dirigée sur le col dont l’extrémité est tenue par des pinces qui assurent l’étirement pendant la fusion du verre. Les dômes sont récoltés dans un bac. Une surveillance automatique stoppe l’arrivée du gaz des chalumeaux en cas d ’extinction de flamme. 21 Contrôles réalisés en cours de répartition : - Contrôle de la masse soit statistique, soit systématique à l’aide d’une trieuse pondérale - Lisibilité du numéro de lot et de la péremption - Etanchéité après fermeture : les unités fabriquées sont plongées dans un bain coloré, dans une enceinte à vide 1er temps : mise sous vide 2ème temps : « cassage » du vide Si mauvais scellage, apparition d’une coloration dans la préparation ou diminution du volume © Groupe IMT. Toute reproduction sans autorisation est interdite. 22 © Groupe IMT. Toute reproduction sans autorisation est interdite. 23 GENERALITES Elimination de l’eau (dessiccation) par sublimation Séchage à froid (Cryodessiccation) Très grande efficacité Produit sec obtenu : lyophilisat Poreux, friable Stable meilleure conservation Facilement remis en solution (avide d’eau = lyophile) Produit en solution Produit lyophilisé SUBLIMATION PRINCIPE Changement d’état État solide Produit en solution Etat gazeux Produit lyophilisé ETATS DE LA MATIERE Le passage d’un état à l’autre est fonction : de la température de la pression Liquéfaction (condensation) Solidification Fusion Vaporisation -Ebullition -Evaporation Sublimation Condensation solide Sublimation ETATS DE LA MATIERE DESSICCATION L’EAU Eau libre En excès Imprègne le produit Eau d’adsorption Fixée à la surface du produit Eau de constitution (eau de cristallisation) Eau liée Appartient à la composition du produit PRINCIPE Elimination de l’eau libre Migration de l’eau liée vers la surface Elimination de l’eau ayant migrée à la surface LES PHASES DE LYOPHILISATION 1ère PHASE : CONGELATION Passage de l’état liquide à l’état solide A pression atmosphérique A température entre -20°c et -80°C Selon les substances dissoutes Lente Ne pas former de gros cristaux Etape critique conditionne l’aspect final du produit favorise la redissolution Garantit l’intégrité du produit 2ème PHASE : SUBLIMATION Dessiccation primaire A basse pression Autour de 5 à 500 µbars A température basse (négative) Variable au cours de la phase De - 40°C à 0°C Par fluide caloporteur circulant dans les étagères Elimination de l’eau libre Élimine environ 90 - 95% de l’eau Eau vaporisée captée par un piège à froid 3ème PHASE : DESSICCATION SECONDAIRE A très basse pression (vide très poussé) Jusqu’à 5 µbars A température moyenne La plus élevée possible (compatibles avec la stabilité produit) + 20 – + 30°C Elimination de l’eau liée Elimine environ 5 – 10% d’eau Eau vaporisée captée par un piège à froid Délicate Détérioration du produit par vide trop poussé 4ème PHASE : BOUCHAGE DES FLACONS Bouchons Crans empêchant son enfoncement complet Canalicules permettant le passage de l’eau vaporisée Fermeture par rapprochement des étagères Sous vide partiel Avec azote GRAPHIQUE EQUIPEMENTS BESOINS Produire du froid Produire du chaud Abaisser la pression Apporter de l’énergie au produit PRINCIPAUX ELEMENTS (1/3) Cuve de lyophilisation Avec ou sans double enveloppe Avec 1 ou 2* portes avec ou sans double enveloppe Cuve de condensation Ensemble d’étagères Système de bouchage interne à la chambre* Système de commande et de pilotage * Équipements optionnels PRINCIPAUX ELEMENTS (2/3) Système de circulation d’un fluide caloporteur Huile de silicone Dans les étagères, dans les doubles enveloppes* Système de chauffage du circuit caloporteur Par résistances électriques Système de réfrigération Du circuit caloporteur et du condenseur Par azote liquide ou par groupe frigorifique (compresseur) Système de pompage Par pompes à vide * Équipements optionnels PRINCIPAUX ELEMENTS (3/3) Système de nettoyage en place (NEP)* Par buses Système de stérilisation en place (SEP)* Système de filtration des gaz en amont Air ou azote Stérilisation et tests d’intégrités en place* Instruments Vannes, soupapes Sondes de température, capteurs de pression * Équipements optionnels PARAMETRES CRITERES QUALITE Aspect du gâteau Structure, couleur, uniformité, poids Taux d’humidité résiduelle Temps de dissolution Limpidité du produit reconstitué Activité du produit reconstitué Absence d’impuretés Stabilité Stérilité (pour les injectables) PARAMETRES CRITIQUES Température Des étagères À toutes les phases Régulée et mesurée par des sondes PT100 au niveau de la canalisation d’huile Durée À toutes les phases Définies par la recette de lyophilisation Pression Lors des phases de dessiccation Mesurée par des capteurs et régulée par injection de gaz AVANTAGES AVANTAGES Propriétés des produits Les températures du process évitent la dégradation du produit Conservation Plus longue À température ambiante Diminution du poids Réhydratation très facile MAITRISE DE LA CONTAMINATION RISQUES DE CONTAMINATION Particulaire Microbienne Croisée MAITRISE DE LA CONTAMINATION MAITRISE DE LA CONTAMINATION OPERATIONS A RISQUE Transferts De la répartition au lyophilisateur Du lyophilisateur au capsulage Chargement Déchargement Ces opérations sont souvent manuelles!!! MAITRISE DE LA CONTAMINATION PROCEDES A IMPACT DIRECT SUR LA CONTAMINATION Nettoyage du Lyophilisateur Stérilisation du Lyophilisateur Contrôles d’intégrité des filtres évents Contrôle d’étanchéité de l’équipement MAITRISE DE LA CONTAMINATION FACTEURS DE RISQUE (1/3) Process sous vide Risque de « fuite » vers l’intérieur important Equipement complexe Nombreux passages à travers les cuves Nombreuses vannes Étagères avec tuyauterie et flexibles Contraintes mécaniques fortes Risque d’endommager le matériel Temps de chargement Flacons partiellement bouchés présent dans la cuve pendant l’opération de chargement MAITRISE DE LA CONTAMINATION FACTEURS DE RISQUE (2/3) Risque de chûtes d’objets sur les étagères Risque de casse À la congélation Au bouchage Collage des bouchons sur les étagères Vide de ligne difficile à réaliser Manque de visibilité Manque d’accessibilité Contact opérateur –produit Lors du chargement manuel MAITRISE DE LA CONTAMINATION FACTEURS DE RISQUE (3/3) Difficulté de surveillance de l’environnement Pour les zones de chargement / déchargement Comment positionner les capteurs? Emission de particules Lors du chargement Par frottement des produits sur les étagères MAITRISE DE LA CONTAMINATION REGLEMENTATION BPF, Ligne directrice N°1 Conditions de transferts Condition de maintien au vide si scellage sous vide 34 : « Le transfert avant bouchage, de récipients partiellement clos…doit s’effectuer soit à un poste de travail de classe A dans un local de classe B soit dans des chariots de transfert scellés dans un local de classe B » 116 : « les récipients lyophilisés partiellement bouchés doivent être maintenus sous classe A jusqu’à ce que le bouchon soit entièrement inséré » 120 : si le sertissage est réalisé en dehors de la zone stérile « …les récipients doivent être protégés par un flux d’air de classe A de la sortie de la zone stérile jusqu'au sertissage » MAITRISE DE LA CONTAMINATION MAITRISE DE L’ENVIRONNEMENT MAITRISE DE LA CONTAMINATION MAITRISE DE L’EQUIPEMENT Automatisation de la préparation Des nettoyages et stérilisations de l’équipement Des stérilisations et contrôle en place des filtres gaz De l’étanchéité du système Flux Flux traversant Chargements / déchargements automatisés © Groupe IMT. Toute reproduction sans autorisation est interdite. 52 Destruction de tous les micro-organismes, effet durable tant que le matériel/produit stérilisé est protégé Selon les BPF : « la stérilité est l’absence de tout germe vivant » Méthodes qui détruisent les micro-organismes : la chaleur : air chaud ou vapeur d’eau les gaz les rayonnements ionisants Méthode qui élimine les micro-organismes : la filtration © Groupe IMT. Toute reproduction sans autorisation est interdite. 53 METHODE MOYEN Chaleur humide STERILISATION TERMINALE Chaleur sèche Gaz Rayonnements PREPARATION ASEPTIQUE FILTRATION Opérer dans des conditions et installations conçues pour empêcher la contamination microbienne Utilisation de filtres validés 54 Garantir l’innocuité en éliminant les agents infectieux éventuellement présents Garder l’intégrité du produit Eviter la contamination secondaire lors des manipulations METHODES CHALEUR SECHE CHALEUR HUMIDE UTILISATIONS Matériel Conditionnement primaire type flacons… Médicaments supportant la chaleur Matériel supportant chaleur et humidité Poudre RAYONNEMENT Pommade optalmique Matériel à usage unique type seringues, catheter GAZ FILTRATION CONDITIONS ASEPTIQUES Matériel ne supportant ni la chaleur, ni les rayonnements Solutions thermo-sensibles Suspensions 56