Fresno City Fire Department Apparatus Maintenance PDF
Document Details
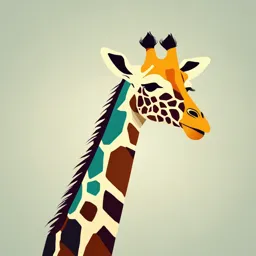
Uploaded by EfficientString
Fresno Fire Department
William Veiga, Battalion Chief
Tags
Related
- Spring Fire Department Guidelines - Self-Contained Breathing Apparatus PDF (SFD.066.REV1)
- FDNY Apparatus C-2 Training Bulletin PDF, April 29, 2008
- Fresno Fire Department Apparatus Startup and Shut Down Procedures PDF
- 7/1 Apparatus General PDF
- Spring Fire Department Self-Contained Breathing Apparatus Guidelines (SFD.066) PDF
- Los Angeles City Fire Department Training Bulletin No. 195 PDF
Summary
This document details the Fresno City Fire Department's standard operating procedures for maintaining their fire apparatus. Guidelines for repairs, operational policies, and procedures for handling disabled vehicles are included. The document also has procedures for replacing headlights.
Full Transcript
Fresno City Fire Department 200 Standard Operating Procedures Manual SECTION 207.009 APPARATUS MAINTENANCE PURPOSE The purpose of this policy is to provide members with general guidelines related to the maintenance of the Fresno Fire Department (FFD or Department) apparatus. APPLICATION This policy...
Fresno City Fire Department 200 Standard Operating Procedures Manual SECTION 207.009 APPARATUS MAINTENANCE PURPOSE The purpose of this policy is to provide members with general guidelines related to the maintenance of the Fresno Fire Department (FFD or Department) apparatus. APPLICATION This policy applies to the repair and maintenance of Department apparatus and equipment. OPERATIONAL POLICY Except as otherwise authorized by this policy, Repairs of Department vehicles, including light vehicles, are the responsibility of the Repair and Maintenance Section (Fire Shop). Members shall not disconnect, alter, or tamper with any apparatus safety or warning devices to include, but not limited to, seatbelts buzzers, back-up alarms, open door or compartment alarms, and low air and oil pressure alarms. Equipment or parts from a reserve apparatus should not be used to replace broken equipment or parts on front-line apparatus. Company officers shall place apparatus out of service for repairs when conditions, in their judgment or that of a fire mechanic, warrant such action. They shall immediately notify the Communications Center and appropriate battalion chief stating the particulars. Priority shall be given to house vehicles inside and secure when being repaired. If the vehicle is required to be stored outside, including when at fleet, the vehicles cab and compartments shall be locked. OPERATIONAL GUIDELINE 1. Report mechanical defects in apparatus or equipment to the company officer immediately upon discovery. The company officer is responsible for ensuring that a repair requisition is completed. If the condition has Effective Date: March 2019 Current Revision Date: 08/17/2023 Next Revision (1) Date: 08/17/2028 William Veiga, Battalion Chief Section 207.009 Page 1 of 2 not been corrected before the shift on duty has been relieved, inform the oncoming company officer of the issue. 2. Headlights may be changed by fire suppression members. Up to two headlamps may be stored at each station, along with the proper tools. If the headlamp is changed, make repair request so that replacement headlamps can be routed to station. 3. Engines and trucks should be serviced at 8-month intervals. 4. Maintain apparatus in a clean condition. 5. Apparatus fuel tanks should not be allowed to have less than half (½) tank of fuel. PROCESS REPAIR PROCEDURES 1. When assistance is needed for disabled apparatus the Fire Shop should be contacted. a. The crew of the disabled company or the calling party will render all possible assistance to the Repair and Maintenance Section as requested. 2. Request repairs to apparatus and equipment through FFD Shop Requests in PSTrax. 3. Small items such as extinguishers, axes, etc., should be tagged with an Administrative Manual, Section 106.048, Wired Repair Tag (FD-37) prior to dispersal to the Repair and Maintenance Section or the Supply Section. Complete an alert in PSTrax as needed. 4. The Fire Shop will help make the final determination of the operational safety of an apparatus and/or its equipment. The vehicle’s operator makes the final determination if the vehicle is safe. If there is a discrepancy in the safety of the vehicle, the company officers should defer to their battalion chief. 5. In the event a repair does not meet minimum safety standards, if improperly completed, or the interaction between Department members (Suppression and Shop) is unprofessional, any member may submit an Effective Date: March 2019 Current Revision Date: 08/17/2023 Next Revision (1) Date: 08/17/2028 William Veiga, Battalion Chief Section 207.009 Page 2 of 3 Apparatus Repair Quality Improvement Form (FD-77) directly to the chief officer responsible for the Support Services Division. REPAIR PROCEDURES WHEN OFF SITE 1. Lock apparatus and compartments when they are taken to off-site, nonFire Department locations for service. 2. Remove or lock any electronics as needed, including the MDT. a. For extended repairs, the electronics such as the MDT should be delivered to the Communications Team. HEADLIGHT REPLACEMENT PROCEDURES Figure 1 1. Turn off all vehicle exterior lighting. 2. Remove the fasteners to the headlight bezel. 3. Remove the fasteners from the headlight retaining ring as seen in Figure 1. Effective Date: March 2019 Current Revision Date: 08/17/2023 Next Revision (1) Date: 08/17/2028 William Veiga, Battalion Chief Section 207.009 Page 3 of 4 Figure 2 4. Grasp the headlight in one hand and the plastic wiring harness plug in the other. Pull the plug from the bulb until the two separate (Figure 2). 5. The installation of the new bulb is the reverse order of the removal. 6. Always check to ensure the lettering on the front of the bulb is upright; otherwise, the light beam will be out of alignment. 7. After the headlight is plugged in and secured, always recheck the lights are operating properly. INFORMATION This section intentionally left blank. DEFINITIONS This section intentionally left blank. CROSS-REFERENCES Administrative Manual Section 106.048, Wired Repair Tag (FD-37) Standard Operating Procedures Manual Section 211.001 PSTrax Effective Date: March 2019 Current Revision Date: 08/17/2023 Next Revision (1) Date: 08/17/2028 William Veiga, Battalion Chief Section 207.009 Page 4 of 4