Laboratory Safety and Regulations PDF
Document Details
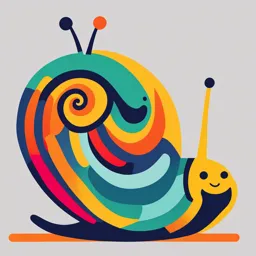
Uploaded by VigilantSaxhorn5919
Tags
Summary
This document provides an overview of laboratory safety procedures for laboratory personnel and covers various aspects of safety, from learning objectives to the disposal of materials.
Full Transcript
Laboratory Safety and Regulations Learning Objectives Be aware of the different laboratory hazards Be able to understand the different responsibilities to maintain safety Learn the different safety equipment used in the laboratory Learn how different wastes are being disposed to preve...
Laboratory Safety and Regulations Learning Objectives Be aware of the different laboratory hazards Be able to understand the different responsibilities to maintain safety Learn the different safety equipment used in the laboratory Learn how different wastes are being disposed to prevent harm What is Laboratory Safety? How do you maintain safety in the laboratory? Laboratory Safety and Regulations Clinical laboratorians, by the nature of the work they perform, are exposed daily to a variety of real or potential hazards: electric shock, toxic vapors, compressed gases, flammable liquids, radioactive material, corrosive substances, mechanical trauma, poisons, and the inherent risks of handling biologic materials In most cases, accidents can be traced directly to two primary causes: Unsafe acts (not always recognized by personnel) Unsafe environmental conditions. Laboratory Safety It is the procedure to protect the laboratory personnel, the laboratory, and the equipment. Personnel Safety These are the ways that use to protect your self and your colleagues. Laboratory Safety This ensures that the laboratory or the work place is suitable for work Equipment Safety To keep your equipment and reagent in proper storage conditions. OSHA Standards OSHA standards that regulate safety in the laboratory include: Bloodborne Pathogen Standard Formaldehyde Standard Laboratory Standard Hazard Communication Standard Respiratory Protection Standard Air Contaminants Standard Personal Protective Equipment Standard Bloodborne Pathogens This standard applies to exposure to all blood or other potentially infectious materials in any occupational setting. Development of exposure control plan Standard precaution Hazard Communication Ensures that the hazards of all chemicals used in the workplace have been evaluated and that this hazard information is successfully transmitted from employers to their employees who use the substances. Safety Data Sheets (SDSs) MSDS or SDS This contains: Section 9: Physical and chemical Section 1: Identification properties Section 2: Hazard identification Section 10: Stability and reactivity Section 3: Ingredients information Section 11: Toxicological information Section 4: First aid procedures Section 12: Ecological information Section 5: Fire-fighting procedures Section 13: Disposal considerations Section 6: Accidental-release measures Section 14: Transport information Section 7: Handling and storage Section 15: Regulatory information Section 8: Exposure controls and Section 16: Other information, personal protection including date of preparation or last revision Occupational Exposure to Hazardous Chemicals in Laboratories Development of a chemical hygiene plan to reduce or eliminate occupational exposure to hazardous chemicals. The chemical hygiene plan must detail engineering controls, PPE, safe work practices, and administrative controls, including provisions for medical surveillance and consultation Safety Responsibility The employer and the employee share safety responsibility. To ensure clarity and consistency, safety management in the laboratory should start with a written safety policy. Employer’s Responsibilities Establish laboratory work methods and safety policies. Provide supervision and guidance to employees. Provide safety information, training, PPE, and medical surveillance to employees. Provide and maintain equipment and laboratory facilities that are free of recognized hazards and adequate for the tasks required Employees’ Responsibilities Know and comply with the established laboratory safe work practices. Have a positive attitude toward supervisors, coworkers, facilities, and safety training. Be alert and give prompt notification of unsafe conditions or practices to the immediate supervisor and ensure that unsafe conditions and practices are corrected. Engage in the conduct of safe work practices and use of PPE. Signage and Labeling The National Fire Protection Association (NFPA) developed a standard hazard identification system (diamond-shaped, color-coded symbol), which has been adopted by many clinical laboratories. Signage and Labeling Manufacturers of laboratory chemicals also provide precautionary labeling information for users. Safety Equipment All laboratories are required to have safety showers, eyewash stations, and fire extinguishers and to periodically test and inspect the equipment for proper operation. It is recommended that safety showers deliver 30 to 50 gallons of water per minute at 20 to 50 pounds per square inch (psi) and be located in areas where corrosive liquids are stored or used. Eyewash stations must be accessible (i.e., within 100 ft or 10 s travel) Chemical Fume Hoods and Biosafety Cabinets Fume Hoods Fume hoods are required to contain and expel noxious and hazardous fumes from chemical reagents. The hood should never be operated with the sash fully opened Periodically, ventilation should be evaluated by measuring the face velocity with a calibrated velocity meter. Safety Equipment Biosafety Cabinets Biological safety cabinets (BSCs) remove particles that may be harmful to the employee who is working with potentially infectious biologic specimens. Biosafety cabinets are designed to offer various levels of protection, depending on the biosafety level of the specific laboratory Safety Equipment Biosafety Cabinets Chemical Storage Equipment Steel safety cabinets with self- closing doors are required for the storage of flammable liquids Only specially designed, explosion-proof refrigerators may be used to store flammable materials. PPE and Hygiene PPE: barriers that physically separate the user from a hazard. Nonlatex gloves Isolation gowns Masks, including particulate respirators Face shields Protective eyewear (goggles and safety glasses) PPE and Hygiene Emergency equipment: Chemical-resistant gloves Hearing protection (earplugs or earmuffs) Eyewash station Safety shower Fire extinguisher Laboratory spill kit First aid kit PPE and Hygiene Hand washing is a crucial component of both infection control and chemical hygiene. After removing gloves, hands should be washed thoroughly. PPE and Hygiene Handwashing procedure: 1. Wet hands with warm water. Do not allow parts of body to touch the sink. 2. Apply soap, preferably antimicrobial 3. Rub to form lather, create friction, and loosen debris. Thoroughly clean between the fingers and under the fingernails for at least 20 seconds; include thumbs and wrists in cleaning. 4. Rinse hands in a downward position to prevent recontamination of hands and wrists. 5. Obtain paper towel from the dispenser. 6. Dry hands with paper towel. 7. Turn off faucet with a clean paper towel to prevent contamination. Biologic Safety General Considerations All blood samples and other body fluids should be collected, transported, handled, and processed using standard precautions. Gloves, gowns, and face protection must be used. Centrifugation of biologic specimens produces finely dispersed aerosols that are a high-risk source of infection. Spills Any blood, body fluid, or other potentially infectious material spill must be promptly cleaned up, and the area or equipment must be disinfected immediately. Spills Safe cleanup includes the following recommendations: Alert others in area of the spill. Wear appropriate protective equipment. Use mechanical devices to pick up broken glass or other sharp objects. Absorb the spill with paper towels, gauze pads, or tissue. Clean the spill site using a common aqueous detergent. Disinfect the spill site using approved disinfectant or 10% bleach, using appropriate contact time. Rinse the spill site with water. Dispose of all materials in appropriate biohazard containers. Fire Safety Fire is basically a chemical reaction that involves the rapid oxidation of a combustible material or fuel, with the subsequent liberation of heat and light. In the clinical chemistry laboratory, all the elements essential for fire to begin are present—fuel, heat or ignition source, and oxygen (air). Classification of Fires Class A: ordinary combustible solid materials, such as paper, wood, plastic, and fabric Class B: flammable liquids/gases and combustible petroleum products Class C: energized electrical equipment Class D: combustible/reactive metals, such as magnesium, sodium, and potassium Class E: arsenal fire Classification of Fires CLASS OF FIRE TYPE OF EXTINGUISHER OPERATION A ordinary combustible: Pressurized water, dry PASS paper, wood, plastic, chemical and fabric B flammable liquids: Dry chemical, carbon PASS gasoline, paints, etc. dioxide, halon, foam C Electrical equipment: Dry chemical, carbon PASS motors, switches dioxide, halon D Flammable metals: Metal X Cover burning magnesium metal with extinguishing agent (scoop, sprinkle) E Arsenal fire Cannot be extinguished Fire Hazard When a fire is discovered, all employees are expected to take the actions in the acronym RACE RESCUE – rescue anyone in immediate danger ALARM – activate the institutional fire alarm system CONTAIN – close all doors to potentially affected areas EXTINGUISH - attempt to extinguish the fire, if possible; exit the area Fire Hazard Operation of fire extinguisher: PASS PULL pin AIM nozzle SQUEEZE trigger SWEEP nozzle Control of Other Hazards Electrical Hazards Direct hazards of electrical energy can result in death, shock, or burns. Indirect hazards can result in fire or explosion. Control of Other Hazards Electrical Hazards Precautionary procedures: Use only explosion-rated Do not work on “live” electrical equipment. (intrinsically wired) equipment in Never operate electrical equipment with hazardous atmospheres. wet hands. Be particularly careful when operating high-voltage equipment, Know the exact location of the electrical such as electrophoresis apparatus. control panel for the electricity to your work Use only properly grounded area. equipment (three-prong plug). Use only approved extension cords in Check for frayed electrical cords. temporary applications and do not Promptly report any malfunctions overload circuits. (Some local regulations or equipment producing a “tingle” prohibit the use of any extension cord.) for repair. Have ground, polarity, and leakage checks and other periodic preventive maintenance performed on outlets and equipment. Control of Other Hazards Compressed Gas Hazards Present a unique combination of hazards in the clinical laboratory: danger of fire, explosion, asphyxiation, or mechanical injuries. Control of Other Hazards Cryogenic Materials Hazards Liquid nitrogen is probably one of the most widely used cryogenic fluids (liquefied gases) in the laboratory. Can cause: fire or explosion, asphyxiation, pressure buildup, embrittlement of materials, and tissue damage similar to that of thermal burns. Control of Other Hazards Mechanical Hazards Mechanical hazards of equipment such as centrifuges, autoclaves, and homogenizers. Control of Other Hazards Ergonomic Hazards Laboratory processes often require repeated manipulation of instruments, containers, and equipment. Chronic symptoms of pain, numbness, or tingling in extremities may indicate the onset of repetitive strain disorders. Disposal of Hazardous Materials There are four basic waste disposal techniques: flushing down the drain to the sewer system Incineration landfill burial recycling Disposal of Hazardous Materials Chemical Waste Strong acids or bases should be neutralized before disposal. Foul-smelling chemicals should never be disposed of down the drain Other liquid wastes, including flammable solvents, must be collected in approved containers and segregated into compatible classes. Disposal of Hazardous Materials Radioactive Waste The manner of use and disposal of isotopes depends on the type of waste (soluble or insoluble), its level of radioactivity, and the radiotoxicity and half-life of the isotopes involved. Many clinical laboratories transfer radioactive materials to a licensed receiver for disposal. Disposal of Hazardous Materials Biohazardous Waste Medical waste (regulated waste) is defined as special waste from health care facilities and is further defined as solid waste that, if improperly treated or handled, “may transmit infectious diseases.” Disposal of Hazardous Materials Biohazardous Waste All biomedical waste should be placed in a bag marked with the biohazard symbol and then placed into a leak-proof container that is puncture resistant and equipped with a solid, tight-fitting lid. All containers must be clearly marked with the word biohazard or its symbol. Accident Documentation and Investigation Any accidents involving personal injuries, even minor ones, should be reported immediately to a supervisor. The first report of injury is used to notify the insurance company and the human resources or safety department that a workplace injury has occurred. The employee and the supervisor usually complete the report, which contains information on the employer and injured person, as well as the time and place, cause, and nature of the injury. The report is signed and dated; then, it is forwarded to the institution’s risk manager or insurance representative.