WSS Study Guide WD2.1 Intermediate Weld Discontinuities PDF
Document Details
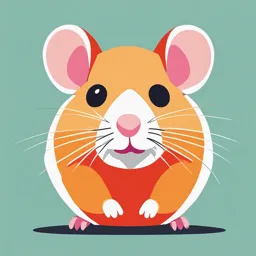
Uploaded by BestPerformingPlateau
null
Tags
Related
- Intermediate Weld Discontinuities PDF
- WSS Study Guide WD2.1 Intermediate Weld Discontinuities PDF
- WSS Study Guide WD2.1 Intermediate Weld Discontinuities PDF
- WSS Study Guide WD2.1 Intermediate Weld Discontinuities PDF
- WSS Study Guide WD2.1 Intermediate Weld Discontinuities PDF
- SLAG INCLUSIONS PDF Intermediate Weld Discontinuities
Summary
This document is a study guide for intermediate weld discontinuities. It provides a table of contents, glossary of terms, and definitions for various welding concepts.
Full Transcript
® WSS Study Guide WD2.1 Intermediate Weld Discontinuities Table of Contents Weld Discontinuities and Causes Glossary of Terms and Definitions Lesson 1 Objectives 10 1. Weld Terminology and Classes 10 2. Process or Procedure-Related Discontinuities 11 2.1 Dimensional Errors 11 2.2 Weld...
® WSS Study Guide WD2.1 Intermediate Weld Discontinuities Table of Contents Weld Discontinuities and Causes Glossary of Terms and Definitions Lesson 1 Objectives 10 1. Weld Terminology and Classes 10 2. Process or Procedure-Related Discontinuities 11 2.1 Dimensional Errors 11 2.2 Weld Profiles 13 2.3 Overlap 19 2.4 Convexity 21 2.5 Excessive Weld Reinforcement 2.6. Underfill 23 24 2.7 Insufficient Throat 24 2.8. Insufficient Leg Size 25 2.9. Undercut 26 2.10 Concavity 29 2.11 Out-of-Line Weld Beads 34 2.12 Incomplete Fusion 3% 2.13 Incomplete Joint Penetration 37 Lesson 2 Objectives 2.14 Distortion 2.15 Surface Irregularities 3. 4. Page 2 40 2.16 Slag Inclusions 43 45 Metallurgical Discontinuities 49 3.1 Porosity 49 3.2 Cracking s5 Design-Related Discontinuities Guides and Exam Exercise Copyright © 2015 CWB Group Industry Services 40 60 62 WSS Study Guide WD2.1 pP ¡ cwbgroup Intermediate Weld Discontinuities Glossary of Terms and Definitions Acceptable weld A weld meeting the applicable requirements. Arc strike A discontinuity resulting from an arc, consisting of any localized remelted metal, heat-affected metal, or change in the surface profile of any metal object. Backgouging The removal of weld metal and base metal from the weld root side of a welded joint to facilitate complete fusion and complete joint penetration upon subsequent welding from that side. Backing A material or device placed against the back side of the joint adjacent to the Jjoint root, or at both sides of a joint in electroslag and electrogas welding, to support and shield molten weld metal. The material may be partially fused or remain unfused during welding and may be either metal or nonmetal. Backing ring Backing ïn the form of a ring, generally used ïn the welding of pipe. Base metal The metal or alloy being welded, brazed, soldered, or cut. Bevel An angular edge shape. Bevel angle The angle between the bevel of a joint member and a plane perpendicular to the surface of the member. Butt joint A Joint type in whiïch the butting ends of one or more workpieces are aligned ïn approximately the same plane. Page 3 Copyright © 2015 CWB Group Industry 5ervices 4 WSS Study Guide WD2.1 . cwbgroup Intermediate Weld Discontinuities Glossary of Terms and Definitions Code A document often considered synonymous with standard or specification; however, more often it will be found to further incorporate rules of good practice by which the results required by a standard or specification may be obtained. In the United States, “code” is used as an equivalent to “standard” in Canada. Complete joint penetration (CJP) A groove weld condition in which weld metal extends through the Joint thickness. Concave fillet weld A fillet weld having a concave face. Concave root surface The configuration of a groove weld exhibiting underfill at the root surface. Concavity The maximum distance from the face of a concave fillet weld perpendicular to a line joining the weld toes. Crack A fracture-type discontinuity characterized by a sharp tip and a high ratio of length and width to opening displacement. Crater crack A crack initiated and localized within a crater. Cyclically-loaded A condition where forces acting on an object continually change significantly in magnitude and/or direction. Page 4 Copyright ® 2015 CWB Group Industrv Services WSS quá Guide WD2.1 Intermediate Weld Discontinuities Glossary of Terms and Definitions Defect A discontinuity or discontinuities that by nature or accumulated effect render a part or product unable to meet minimum applicable acceptance standards or specifications. The term designates rejectability. Depth of fusion The distance that a weld fusion extends into the base metal or previous pass from the surface melted during welding. Discontinuitv An interruption of the typical structure of a material, such as a lack of homogeneity in its mechanical, metallurgical, or physical characteristics. A discontinuity is not necessarily a defect. Ductility The physical property of a material where it is capable of sustaining large permanent changes in shape without breaking. Effective throat The minimum distance from the root of a weld to its face, less any reinforcement. Fatigue The progressive and localized structural damage that occurs when a material is subjected to cyclic loading. Fillet weld Aweld of approximately triangular cross section joining two surfaces approximately at right angles to each other in a lap joint, T-Joint, or corner Jjoint. Fillet weld size For equal leg fillet welds, the leg lengths of the largest isosceles right triangle that can be inscribed within the fillet weld cross section. For unequal leg fillet welds, the leg lengths of the largest right triangle that can be inscribed within the fillet weld cross section. Flaw An undesirable discontinuity. Groove angle The included angle between the groove faces of a groove weld. Page 5 Copyright © 2015 CWB 6roup Industr WSS Study Guide WD2.1 G Intermediate Weld Discontinuities Glossary of Terms and Definitions Groove face Any surface in a weld groove prior to welding. Groove weld size The Joint penetration of a groove weld. Hardness A measure of how resistant solid matter is to various kinds of shape change when a force is applied. Incomplete fusion (IF) A weld discontinuity in which fusion does not occur between the weld metal and the fusion faces or the adjoining weld beads. Incomplete joint penetration A Joint root condition in a groove weld in which weld metal does not extend through the joint thickness. Joint penetration The distance the weld metal extends from the weld face into the joint, exclusive of weld reinforcement. Joint root The portion of a joint to be welded where the members approach closest to each other. In cross section, the Joint root may be either a point, a line, or an area. Lamination A type of discontinuity with separation or weakness generally aligned parallel to the worked surface of a metal. Layer A stratum of weld metal consisting of one or more weld beads. Melt-through Visible root reinforcement in a joint welded from one side. Nondestructive Testing (NDT) Any of several examination methods where a component or assembly is evaluated without damaging or otherwise lessening Its intended service life. ® Copyright @© 2015 CWB Group Industry Set | | WSS Study Guide WD2.1 Intermediate Weld Discontinuities Glossary of Terms and Definitions Overlap The protrusion of weld metal beyond the weld toe or weld root. Partial joint penetration weld A groove weld in which incomplete joint penetration exists. Porosity Cavity-type discontinuities formed by gas entrapment during solidification or in a thermal spray deposit. Prod method A direct contact method of magnetic particle inspection using a prod that can locate surface and subsurface indications parallel to the alignment of the poles of the prod. Radiography (RT) A nondestructive testing method ïn which radiant energy is used in the form of eïither X-rays or Gamma rays for the volumetric examination of 0paque objects. Root edge A root face of zero width. Root face The portion of the groove face within the joint root. Root opening A separation at the joint root between the workpieces. Root surface The exposed surface of a weld opposite the side from which welding was done. Slag A nonmetallic product resulting from the mutual dissolution of flux and nonmetallic impurities in some welding or brazing processes. Slag inclusion A discontinuity consisting of slag entrapped in weld metal or at the weld interface. = L 5 2015 CWB Group Industry Service5 ® 0h WSS Study Guide WD2.1 Intermediate Weld Discontinuities Glossary of Terms and Definitions Specification A document that usually sets forth in some detail the requirements and/or acceptance criteria demanded by a buyer for a certain product. lt may be, or become, the basis of a contractual agreement between the buyer and the supplier. See also Code and Standard. Standard A document by which a product may be judged. In terms of welding, a standard generally summarizes the requirements for processes, procedures, consumables, materials, inspection, acceptance criteria, etc. See also Code and Specification. Statically-loaded A condition where forces acting on an object do not change significantly. Strain A measure of the change in dimensions of a body relative to a reference length. Stress The internal force induced in a material to counterbalance an externally applied force. Mathematically, it is the applied force divided by crosssectional area, and is represented by the Greek letter sigma, Ơ. Tension The type of force that tends to pull an object, or a surface of an object, in opposite directions. Toughness The ability of a material to resist the growth of a crack. Uliimate tensile strength The maximum stress that a material can withstand while being stretched or pulled before necking. Page 8 Copyright © 2015 CWB Group Industry Services WSS Study Guide WD2.1 Intermediate Weld Discontinuities Glossary of Terms and Definitions Undercut A groove melted into the base metal adjacent to the weld toe or weld root and left unfilled by weld metal. Weld bead Aweld resulting from a weld pass. Weld face The exposed surface of the weld on the side from which the welding was done. Weld joint mismatch Misalignment of the joïint members. Weld reinforcement Weld metal in excess of the quantity required to fill a groove weld. Weld root The points, shown ïn cross section, at which the weld metal intersects the base metal and extends furthest into the weld joint. Welding procedure The detailed methods and practices involved in the production of a weldment. Weldment An assembly joined by welding. Yield strength The stress at which a material begins to permanently deform. Page 9 | Copyright |9 2015 CWB Group Industry Services WSS Study Guide WD2.1 Intermediate Weld Discontinuities Lesson 1 Objectives AfTter completing this lesson you should be able to: $..+vo$s2s.$e$s© -¬ Categorize weld discontinuities and defects Describe the categories of weld discontinuities Explain the types of unacceptable weld profiles and their causes Describe the use of welding gauges Define incomplete fusion and incomplete joint penetration and identify their causes 1. Weld Terminology and Classes Discontinuities are interruptions in the desirable weld. A discontinuity that represents a danger to aweld or structure is a defect. Fitness for service evaluation that seeks a balance between quality, of a welding procedure. physical structure of a fitness for service of is a concept of weld reliability and economy lf a discontinulitv is assessed and determined to be a defect, it must be removed and corrected. The term defect should be used with caution, as the importance of discontinuities, both in type and quantity, is relative to the type of weldment and ïts required service conditions. The same discontinuity may be determined to be a defect in a weldment for one application and not for another application. Relevant codes and standards should be referred to in order to determine acceptance criteria for discontinuities when a discontinuity has been clearly located, identified, sized and its orientation determined. Weld discontinuities are divided into three general classes: $ Process or procedure-related $ Metallurgical $ Design-related These classes of discontinuities can be subdivided under many headings, but since ït is impossible to state rules whereby an inspector can identify all the factors likely to cause discontinuities in welds, this study guide will describe only some of them briefly. 15 CWB Group Industry Services WSS Study|Guide WD2.1 Intermediate Weld Discontinuities Inspectors will be better qualified to judge the chances of obtaining welds that are satisfactory for a particular service ïf they have a thorough knowledge of the limitations of a given welding process and an understanding of those conditions that are likely to cause the formation of discontinuities. 2. Process or Procedure-Related Discontinuities The production of satisfactory weldments depends upon, among other things, the maintenance of specified dimensions, whether it be the size and shape of welds or finished dimensions of an assembly. Requirements of this nature will be found ïn the drawings and specifications. Typically, an engineer would be consulted to determine ïf the dimensions are acceptable or unacceptable. If it is determined to be unacceptable, the discontinuity is considered a defect and must be corrected. The more common types of dimensional errors are discussed. 2.1 Dimensional Errors Dimensional errors are the direct result of poor workmanship in operations leading up to the point at which the assembly is to be welded. Errors of this nature indicate a lack of quality control and should be reported by the welding inspector so that corrective action may be initiated. Examples of dimensional errors include incorrect bevel angles, incorrect J-groove radii, incorrect root face, incorrect fit-up, incorrect root opening and irregularities in the joint preparation surfaces as shown in Figure 1. 2015 CWÊ Group Industry Services ® WSS Study Guide WD2.1 ^^. Intermediate Weld Discontinuities Incorrect Bevel Angles Incorrect Root Face Incorrect Fit.Up Incorrect Root Opening Irregularities in Joint Preparation Surfaces e1] Dimensional errors during preparogtion and fit-up An inigative of the cwbgroup. Si WSS Study Guide WD2.1 ® Analgdttve 0! i6 cwbgroup Intermediate Weld Discontinuities Insufficient root opening may cause inadequate joint penetration, incomplete fusion and slag entrapment. Km root opening Excessive root opening may cause melt-through, porositv, slag entrapment and additional distortion. KÊm --- root opening Misalignment of parts can cause insufficient effective throat and a stress concentration at the root of the weld. = Misalignment đi: 13. opyright © 2( Stress concentration An Inidalive of the WSS Study Guide WD2.1 cwbgroup „ . Intermediate Weld Discontinuities An excessive bevel angle can have two consequences; a large angle means a larger joint must be filled with weld metal and excessive distortion. ~¬ Required edge preparation _~ Actual edge preparation Bi .~¬ Additional weld metal required due to incorrect edge preparation Kê Excessive bevel or groove angle Asillustrated in Table 1, codes and specifications provide workmanship tolerances for bevel angle, root face thickness and root openings and should be followed accordingly. For example, working to CSA Standard = W59 or AWS D1.1, a groove angle specified on a drawing as 60° is required to be between 55°-70°. Alternate groove angles would only be accepted ïf a modification to the original drawing or a new detail drawing was approved by the engineer. Root Not Gouged Root Face of Joint #2 mm (1/16 in) Root Gouged Not Limited Root Opening of Joint -Without Steel Backing #+2mm(+1/18in) -With Steel Backing =¬ +6 mm (+1/4 in) (-1/8 in) NotApplicable -2mm.(-1/16in) ¬ — +2 mm (+1/16 in) -3mm - Groove Angle of Joint mm + 10 degrees - 5 degrees Workmanship tolerances (extract ƒrom CSA W59) + 10 degrees -5 degrees WSS Study Guide WD2.1 L sms ch An Iniianve gƒ the G Intermediate Weld Discontinuities Table 2 summarizes the dimensional errors and the resulting weld discontinuities or defects that may result. Dimensional Discontinuity Primary Resulting Discontinuity Insufficient root opening xe. Excessive root opening s in ung - Excessive melt through and . back side weld reinforcement - Concave root surface (in pipe welds) - Excessive distortion Misalignment (high/low) eo 2 - Insufficient groove weld size - Stress concentrations ặ Vievoi! royi Góp pyêpaïgjjon LAN ôi IBSUIEIEIBEHEIPÐGF EaCS: - Excessive melt through and back side weld reinforcement : Exeoegivo tooplacg 1 tr - Incomplete joint penetration - lrregular back bead profile Ñ - Incomplete joint penetration - Incomplete sidewall fusion TẾT - Incomplete joint penetration - Incomplete sidewall fusion 1 Gv 9g - Excessive distortion Excessive bevel angle : - Reduced mechanical Properties due to Increased local heating of weld joint (more filler metal required) Incorrect J-groove radii Zemg( IEWap5: > Incomplete sidewall fusion - Slag entrapment TAbL2| Resulting weld discontinuities from incorrect joint preparation and fit-up Page 15 Copyright © 2 5roup Industrỷ Services li WSS Study Guide WD2.1 Intermediate Weld Discontinuities - 2.1.1 Surface Irregularities Irregularities in the finished surface to be welded may also lead to various weld discontinuities. The method of preparation usually determines the types of weld discontinuity that may be experienced. " Sheared Surfaces ¬ Depending on the condition of the shear blades and the lubricants used, ~ various undesirable foreign materials may be entrapped leading to porosity, slag entrapment and incomplete fusion. - Flame Cut Surfaces ~ When oxygen is used in oxyfuel cutting, there is the potential for notches and irregularities to occur. Quite often, slag may adhere to these notches and surfaces. lf ït is not removed prior to welding, discontinuities such as . porosity, incomplete fusion, slag entrapment and chemical composition defects may 0Cccur. Codes, standards and specifications often limit surface irregularities and should be followed accordingly. ~^ r.6 Page 16 Cop\ 9 2015 CWB Group Ind; | Irregularities in the joint preparation surface can trap slag | WSS Stud) Gúide WD2.1 Intermediate Weld Discontinuities Plasma and Laser Cut Surfaces When plasma cutting is used, there is a potential for notches and irregularities to occur. Dross may adhere to the cut surface, as well as an oxide film that can produce weld discontinuities, such as porosity, if it ïs not removed by grinding ñirst. When cutting high-strength quenched and tempered steel such as ballistic armour for military applications, a localized martensitic microstructure forms along the edge of the cut surface from the localized heating and fast cooling associated with the cutting process. lIt may be necessary to remove up 2 mm of material by mechanical means to remove the hard, heat-affected zone. This high-hardness hardness region promotes crack formations due to a combination of residual stresses developed from the thermal cycles generated during cutting and subsequent welding operations. Water Jet Cut Surfaces Water jet cutting is not a thermal process and there is no change in the microstructure of the material being cut along the cut surface. There is no oxide formation or slag requiring cleaning. Welding can be successfully performed on a water jet cut surface with no preparation as long as the surfaces are uniform. Machine Cut Surfaces Milling machines, lathes and saws use oil as a lubricant when making cuts. Ít is necessary to remove this lubricant before welding to avoid weld discontinuities such as porosity. 5 CWB Group Industry Services WSS Study Guide WD2.1 Intermediate Weld Discontinuities Codes and standards, along with company welding procedures, should always be referred to before any cutting and material preparation begins. Becoming familiar with code and procedure requirements ahead of time allows for educated decisions to be made regarding cutting and preparation methods. Material should always be inspected upon receipt to ensure that its condition is acceptable and that it is the proper type and grade. Mill Certificates for material ordered should always be requested to ensure that proper type and grade of material is received. Machinists that are made aware of the required tolerances will be more likely to adhere to the requirements and advise of any problems at the early stages of the —¬ s material preparation work. 2.2 Weld Profiles Weld profiles of fillet welds and possible areas where deficiencies may be lên present as illustrated in Figure 7. Convex fillet weld with =_ Leg W « xAK? Leg unequal legs kL Concave fillet weld with equal legs Convexity Convexity > - Leg Throat Leg 'Throat ¡ `ề Throat : Leg Throat Leg L ¬ - Convex fillet weld with equal legs sẽ 67] Page 18 15 CWB Group Ind Weld profiles Concave fillet weld with Leg Leg unequal legs CWBï WSS Study Guide WD2.1 Intermediate Weld Discontinuities An nhe BH cwbgroup 2.3 Overlap Dverlap is a condition where an excess of weld metal exists at the toe of a weld beyond the limits of fusion. This produces notches that can cause a stress concentration under load as shown in Figure 8. In the case of ñillet welds, ït may reduce its effective throat. Overlap can also mask Incomplete fusion. Overlap Qverlap Km Overlop Size Notch angle Proper toe angle KÊm Notch angle oƒ fillet welds WSS Study Guide WD2.1 Intermediate Weld Discontinuities Overlap is common in fillet and groove welds with various processes and produces weld metal that is not fused to the parent metal. Some of the probable causes of overlap are: $ $ $ $ Operator technique: incorrect work and travel angles, travel speed too slow, improper weave technique Electrode: incorrect electrode size for the application Welding parameters: incorrect voltage, current, contact tip-to-work distance Surface contaminants: oil, paint, rust, mill scale The use of proper welding procedures and techniques should ensure that overlap does not occur. lf ït does occur, make sure procedures and welding techniques are reviewed to eliminate further overlap. Overlap is corrected by grinding to remove the overlap and blending to achieve the desired weld profile is acceptable. Magnetic particle testing (MT) would be a good choice after the repair to ensure that all the overlap isremoved and not hidden by the grinding operations. = Poteniial initiation point for a crack .. QOverlap Corrected by grinding and blending rie.10] Correction oƒ overlap WSS Study Guide WD2.1 > cwbgroup Intermediate Weld Discontinuities 2.4 Convexity Convexity is defined as the maximum distance from the face of a convex fillet weld perpendicular to a line joining the weld toes. In single pass fillet welds, convexity results in added stress risers at the toes of the fillet weld. Sharp corners due to excessive convexity Page 21 Copyright © 2015 CW cm) WSS Study Guide WD2.1 Intermediate Weld Discontinuities Excessive convexity tends to produce notch effects in multipass welds (see Figure 12) and may lead to other weld discontinuities, such as slag inclusions, incomplete fusion and porosity when depositing subsequent Dasses. Notch angle 9 Proper toe angle G12, Notch angle oƒ multipass groove welds Convexity, like overlap, may be caused by poor weld metal fluidity. Some of the probable causes of convexity are: $$ $ Operator technique: incorrect work and travel angles, travel speed too slow, improper weave technique Electrode: incorrect electrode size for the application Welding parameters: incorrect voltage, current, contact tip-to-work distance $ Surface contaminants: oil, paint, rust, mill scale The use of proper welding procedures and techniques should ensure that excessive convexity does not occur. Grinding to achieve a flat weld profile may be performed to correct excessive convexityv on fillet welds. If the convexity is determined to have been caused by welding cold (insufficient heat input), the weld should be completely removed by grinding or gouging and a new weld deposited. For multipass welds, grooving the toes of the weld before depositing the next pass is recommended. It may not be necessary to completely grind the weld flat if there is sufficient room to deposit the next pass. CWB Group Industry WeSS Study Guide WD2.1 PL | An native sĩ th cwbgroup Intermediate Weld Discontinuities 2.5 Excessive Weld Reinforcement Excessive weld reinforcement is defined as an area of the weld that has weld metal added in excess of that permitted by the code or standard. It is associated with groove welds and is undesirable since it tends to stiffen the section at that point as well as establish notches and increase weight (see Figure 13). This condition typically results from improper welding technique, improper welding parameters, too slow a travel speed or improper weld pass sequencing. Excess Excessive face reinforcement Excessive root reinforcerient G13, Excessive weld reinforcement Codes, specifications and standards limit the amount of reinforcement on groove welds and should be followed accordingly. The maximum reinforcement permitted by CSA Standard W59is3mm (1/8 in). The use of proper welding procedures and techniques should ensure that excessive weld reinforcement does not occur. Excessive root reinforcement may be the cause of improper fit-up or joint preparation. To repair excessive reinforcement, grind the weld to an acceptable profile, blending the toes of the weld with the base metal to reduce the notch effect at the weld toes. WSS Study Guide WD2.1 Intermediate Weld Discontinuities 2.6 Underfill Underfill is snown in Figure 14. The groove weld size of the welded joint is insufficient, reducing the effective load carrying capacity of the joint. Additional passes are required to bring the weld to the required size. Care should be taken when applying additional passes to: $ Maintain proper profiles $ $ $ Notexceed reinforcement requirements Blend passes into base material Notcreate additional weld discontinuities Underfill may be caused by any one or a combination of the following: + 9 $ $ $ Travel speed too fast Insufficient passes or layers Incorrect weave techniques Excessive included groove angles 2.7 Insufficient Throat The strength of a fillet weld is determined by the throat of the weld. It is therefore critical that the weld produced has at least the throat expected by the designer. One common problem is where there is a valley between two successive weld beads. In the most critical area, the throat, there is not enough metal. To correct this defect, ït is necessary to add more weld metal. CWB Group Industry Services WSS Study Guide WD2.1 Intermediate Weld Discontinuities Insufficient throat riG.15| Insufficient throat 2.8 Insufficient Leg Size Insufficient leg size is when one or both of the legs of a fillet weld are less than the required size. In the example shown, the vertical leg is less than the required size. Correction of insufficient leg size is achieved by depositing additional passes as shown in Figure 16. Actual throat Required leg length lu Insufficient leg length G16) roúp Industry Correction oƒ insufficient leg size x k E Corrected by adding passes si WD2.1 Ï WSSStudy Guide < nu. An niunee gi _ . Intermediate Weld Discontinuities - 2.9 Undercut ^ Undercut ïs the melting away of the parent metal during the welding process and left unfilled with weld metal. lf undercutting is not corrected, ït may be detrimental to the component and is, therefore, a defect. - Undercut will produce notches and result in stress risers, which can be harmful under load. Limitations for undercut are specified in governing codes and standards and are based on the type of loading to which the weld is subjected (i.e., static, cyclic or impact). < Undercut can occur at any stage of the welding process, for example: $ rootundercut in a single-V groove welded from one side (Figure 17 (a)) $ Sidewall undercut of a welding groove at the edge of a layer or bead, thus forming a sharp recess in the sidewall at a point where the next s _ layer or bead must fuse (Figure 17 (b)) $ External undercut reducing the base metal thickness at the line where the last bead is fused to the surface (Figure 17 (c)) Root undercut - (b) Sidewall undercut _ - External undercut FiG.17 Undercut WSS Study Guide WD2.1 Ñ cwbgroup Intermediate Weld Discontinuities Surface undercut, both internal and external, should be corrected. However, some construction codes and standards allow limited amounts of undercut to remain in the weld. The direction of primary stress on the Joint determines the influence of a given amount of undercut. On the other hand, the designer or specifier may specifically state in a product specification that undercut is not permitted. +3ợw+vs2se$® Some of the probable causes of undercut are: Operator technique: incorrect work angle, travel angle or travel speed Electrode: incorrect electrode type or size Welding parameters: incorrect voltage or current Joint accessibility and position: poor accessibility to the joint may force the use of incorrect work or travel angle. Vertical up welding is more prone to undercut than welding in the flat position. $ Joint preparation: incorrect joint preparation may cause internal undercut The use of proper welding procedures, techniques, joint preparation and fitrup should ensure that excessive undercut does not occur. Check to ensure that joint accessibility is acceptable before performing welding. Undercut discontinuities, if determined to be defects by the applicable codes and standards, can usually be corrected by cleaning and adding an additional pass. Root undercut may be more difficult to fix ïf ït is on small diameter pipe, as ït needs to be repaired from the inside of the joint. Large diameter pipe may be repaired using the same method used for external undercut. Undercut on small diameter pipe, if determined to be a defect, would have to be repaired by cutting out the section of pipe and preparing a new joint. Corrected by an additional pass He. 16] Correction of undercut Corrected profile WSS Study Guide WD2.1 Intermediate Weld Discontinuities Acceptable and unacceptable groove weld profiles are shown in Figure 19. Acceptable Groove Weld Profiles R Reinforcement, R shall not exceed 3mm(1/8in) —^ k) Underfill l) Excessive weld reinforcement m) Undercut n) Overlap G19, Groove weld profiles WsSS Study Guide WD2.1 An. Intermediate Weld Discontinuities 2.10 Concavity Concavity is defined as the maximum distance from the face of a concave ñllet weld to a line joining the weld toes. Excessive concavity occurs with fillet welds as shown in Figure 20 and Figure 21. A concave profile in the root of a groove weld is called concave root surface. The permissible concavity is generally defined by the governing code and standard. It should be noted that drawings may call for concave fillet welds, in which case the condition would not be considered a weld defect. The size of a concave fillet weld is determined by its throat size, not the actual measurement of ïts leg length. The selection of a concave fillet profile would be dependent on service conditions. Concavity Size G20) Page 29 Copyright © 2015 CWB Group Industry 5 Concavity WSS Study Guide WD2.1 An inirianue øf the : cwbgroup Intermediate Weld Discontinuities Size Le g (effective) Em Concuve fillet weld size Typical causes of concavity are: $ Operator technique: incorrect work angle, travel angle or travel speed $ Welding parameters: incorrect voltage or current $ Position of welding: vertical down welding is more prone to result in concave fillet welds mm An excessively concave weld can give a deceptive appearance of the actual weld size. Excessively concave fillet welds can be corrected by the addition of more weld passes as shown in Figure 22. riG.22| Correction oƒ concavity WSS Study Guide WD2.1 mm Intermediate Weld Discontinuities Desirable, acceptable and unacceptable fillet weld profiles are shown in Figure 23. Desirable fillet weld profiles Convexity, C shall not exceed 0.07W + 1.6 mm (1/16 in) 9) Excessive undercut h) Overlap F623: Flllet weld profiles ï) Insufficient leg WSS Study Guide WD2.1 An Inidiative of the : cwbgroup Intermediate Weld Discontinuities ISSẠ There are three common “^^ Concave rG.22| profiles: concave, flat and convex. Flat Convex Concave, flat and convex fillet weld profiles Weld deficiencies due to insufficient or excessive size and poor profile may be detected by visual examination, or by the use of suitable gauges as illustrated in Figure 25. Actual fillet weld size is defined by the shortest leg dimension in combination with the actual weld throat. Throat full size Oversize leg Six-bladed pocket size fillet guage and methods of use Mulli-purpose welding gauge IrIG.25] roup Industry Services Welding gauges WSS Study Guide WD2.1 cwbgroup Intermediate Weld Discontinuities The leg and throat size of concave fillet welds can be measured with fillet weld gauges as shown in Figure 26. mm Measuring concave filiet welds Only the leg size of convex fillet welds can be measured with fillet weld gauges as shown in Figure 27. HiG.27] Mieasuring convex fillet welds WSS Study Guide WD2.1 Intermediate Weld Discontinuities 2.11 Out-of-Line Weld Beads The following can lead to misalignment of the weld (see Figure 28): insufficient care in positioning automatic welding machines $2 $gsese b4 incorrect bead placement by the welder incorrect edge preparation inaccurate backgouging FiG.28| Out-of-line-weld beqds Out-of-line weld beads can result in incomplete joint penetration when complete joint penetration is required. Correcting this requires the removal of the weld from one side by grinding or gouging and the depositing of a new weld. Caution must be taken, as this will not be detected by visual inspection unless samples are extracted for etching to reveal the penetration profile. Nondestructive testing (NDT) methods capable of detecting discontinuities below the surface are best suited to detect this type of defect. CWB Group Industry Services WSS Study Guide WD2.1 cwbgroup Intermediate Weld Discontinuities 2.12 Incomplete Fusion Incomplete fusion is used to describe the failure to fuse between weld metal and fusion faces or adjoining weld beads. It may occur at any point in the welding groove or fillet weld as illustrated in Figures 29. Incomplete root fusion Incomplete root fusion Incomplete sidewall fusion Incomplete root fusion mm Incomplete fusion WSS Study Guide WD2.1 cwbgroup Intermediate Weld Discontinuities Incomplete fusion may be caused by a number of factors, either singly or in combination. Some of these factors are listed below: $ Improper electrode selection: selection of an electrode that is too large for the joint preparation inhibits electrode manipulation Improper welding parameters: welding parameters that are too low in in current and/or voltage Improper manipulation of the electrode: improper work or travel angles and travel speed that is too fast Improper cleaning of material: rust, oxides and mill scale that are not removed from the joint prior to welding Improper joint design: an example of this would be a narrow V-groove weld ïn a thick plate, inhibiting electrode manipulation. Figure 30 illustrates how a narrow V-groove weld would inhibit electrode manipulation. Poor joint preparation and fit-up: examples of this would be uneven root faces, uneven bevel angles and general inconsistencies in the preparation and fit-up. Narrow V- groove Inhibits electrode manipulation Wider V- groove Allows for electrode manipulation riG.20| Effect oƒ bevel øngle on the qbility to manipulate the electrode WSS Study Guide WD2.1 Intermediate Weld Discontinuities 2.13 Incomplete Joint Penetration \ The term incomplete joint penetration is a condition at the root of a groove weld where the weld metal does not extend through the joint thickness (see Figure 31). z= S _ lỀ — —<— —. Incomplete joint penetration a) Incomplete penetration - Square Butt Pu —< NI mu Incomplete joint ma b) Incomplete penetration - Single”V” penetration - „—. — mi x*. iieompielejoii - penetration — =g im c) Incomplete penetration - Double”V” I HH d) Incomplete penetration -Double Fillet —=. II Incomplete Jjoint penetration FiG.21i Incomplete joint penetrotion ® WSS Study Guide WD2.1 CWBI H Em see HN Intermediate Weld Discontinuities lt must be noted that incomplete joint penetration is not necessarily a weld defect. Some welded connections are designed with partial joint penetration welds. Incomplete joint penetration becomes a weld defect only when the codes, specifications and designs require complete joint penetration or when the required depth of penetration and resulting weld size is not achieved. The causes of incomplete joint penetration are very similar to those causing incomplete fusion and are: 1. Improper electrode seleciion. The selection of an electrode that is too large for the joint preparation limits access to the root of the joint. 2. Improper welding parameters. Current values that are too low may cause incomplete joint penetration. A voltage that is too high may also lead to incomplete joint penetration due to increased arc length and width resulting in a welding arc that is less focused at the root of the joint. 3. Improper manipulation of the electrode. Travel angle, work angle, travel speed, arc length and contact tip-to-work distance all affect penetration. An increase in travel angle beyond 15° wiïll decrease penetration and may result in incomplete Jjoint penetration. Welding the root pass of a groove weld with an angle other than 90° to the work plane will decrease root penetration and may result in incomplete joint penetration. Travel speed is optimum for achieving penetration when the electrode is at the leading edge of the weld pool. A faster or slower travel speed will reduce penetration and may result in incomplete Joint penetration. Arc length for processes using constant current power supplies (SMAW and GTAW) varies as the operator moves the electrode closer or farther from the joint. An unsteady welder may hold the electrode too far from the joint resulting in an increased (less focused) arc, which will decrease root penetration and may result in incomplete Joint penetration. For processes that use constant voltage power sources (GMAW, FCAW and MCAW), the welding current decreases as the contact tip-to-work distance increases. An unsteady welder may hold the welding gun too far away, resulting in a contact-tip-to-work distance that is too long and decreased root penetration that may result in incomplete joint penetration. Page 38 Copyright © 2015 CWB Group Industry 5ervices ï s¡ cwbgroup Intermediate Weld Discontinuities 4. Improper cleaning of the material. Rust, oxides, and mill scale that is not removed from the joint prior to welding, may result in incomplete Joint penetration. 5. Improper joint design. An example of this would be an included angle on a V-groove weld for a thick plate preventing access of the welding gun below the top surface of the plate. This would result in a contact tip-to-work distance that is too great, reducing welding current and resulting in decreased penetration, which may result in incomplete Joint penetration. 6. Poor joint preparation and fit-up. An example of this would be insufficient root gap resulting in reduced root penetration, which may cause incomplete joint penetration. Incomplete joint penetration in a joint designed as a complete joint penetration groove weld is always determined to be a defect requiring repair. Repair is performed by grinding or gouging from one side to sound weld metal, and depositing a new weld pass or weld passes. Incomplete Joint penetration of a fillet weld requires the complete removal of the fillet weld and a new weld must be deposited. Incomplete joint penetration of a partial joint penetration groove weld will most likely require the weld to be removed and a new weld deposited, or a second weld pass performed from the other side of the joint. 9 2015 CWJ Group Industr WSS Study Guide WD2.1 Intermediate Weld Discontinuities @ Lesson 2 Objectives After completing this lesson you should be able to: & Identify the types and causes of distortion $+sJgsseses 9 Describe surface irregularities Explain the formation and causes of slag inclusions Describe the formation, types, location and causes of porosity Categorize and describe the formation, detection and correction of cracks 2.14 Distortion 2.14.1 Causes The welding operation involves the application of heat and fusion of metal in localized sections of the weldment. Stresses of sufficient magnitude may occur, due to thermal expansions and contractions, which will cause distortion of the structure. The most frequently seen types of welding distortions are shown in Figure 32. It should be recognized that when distortion occurs it is not always in the simple form of distortion as shown. Distortion quite often OCcurs in compounded forms, such as bending or angular, as well as any combination of the simple forms. @® Page 40 Copyright © 2015 CWB Group Industry Services WSS Study Guide WD2.1 Intermediate Weld Discontinuities Shrinkage Longitudinal shinkage and transverse shrinkage Transverse shrinkage Angular Distortion Caused by transverse shrinkage Bending Distortion Caused by longitudinal shrinkage Buckling Caused by longitudinal shrinkage (also to a minor degree, by transverse shrinkage) Most often when welding large, thin plates or sheets G22] Page 41 Copyright © 2015 CWB Group Industry Services Types oƒ distortion , Longitudinal shrinkage WSS Study Guide WD2.1 Intermediate Weld Discontinuities Distortion may have a number of contributing causes such as: 1. Improper welding parameters. Lack of control of the current, voltage and travel speed can result in an increased heat input. 2. Improper weld pass sequencing. For weldments that may be prone to distortion, a procedure for weld pass sequencing should be developed and followed. Simply spreading out the welding to even out the heat into the weldment will help in reducing distortion ïf a procedure for weld pass sequencing is not available. 3. Improper joint preparation. An example of improper joint preparation causing increased distortion is a bevel-groove weld with an included angle larger than specified on the welding procedure. A larger included angle requires more filler metal to fill the joint, adding more heat to the joint and causing distortion. Inspection of the joint preparation should be performed before fit-up of the joint. 4. Improper joint fit up. An example of improper joint fit up causing increased distortion is a root opening that is too large. Increasing the root opening of a groove weld significantly increases the amount of filler metal required to fill the joint. Care should be taken when fitting up joints for welding and inspection of the fit-ups should be performed before welding to avoid distortion. 5. Joint design. Joint preparation should be carefully considered at the design stage. For example, thick joints can benefit from the use of double-V-, J- or U grooves. m Page 42 Copyright © 2015 CWB Group Industry Services WSS Study Gụide WD2.1 cwbgroup Intermediate Weld Discontinuities 2.15 Surface Irregularities Surface irregularities include badly shaped surface ripples, excessive spatter, inadequately filled craters, overly filled craters and arc strikes or stray arcs. They are typically the result of the welder or welding operator using incorrect welding parameters or technique. Bead irregularities are discontinuities that may be considered defects Ïf they are excessive. Bead profiles with irregular ripple patterns, when excessive, show portions of crater between ripple spacing, as shown in Figure 33. This may be considered a defect due to the increased likelihood Of cracking in these regions from the exposed craters. riG.23, 8ead irregularities An ininarive of the. WSS Studv Guide WD2.1 . cwbgroup' Intermediate Weld Discontinuities Spatter, as shown ïn Figure 34, is a discontinuity that is indicative of improper welding techniques and increase the likelihood of other associated discontinuities. Final weld passes or single pass fillet welds with excessive spatter are problems when painting operations are to be performed. Spatter removal is expensive, as it is very labour intensive. ^ =4 Em Excessive spadtter Tack welds left for inclusion in the completed weld may cause cracks. lf small tacks are made on a large, cold surface, the resulting rapid cooling (quench effect) of the weld metal and heat-affected zone may result in cracks, or micro-fissures that wÏïll develop into cracks given time and stress. Stray arc strikes, as shown in Figure 35, may cause cracks or micro-fissures due to similar rapid cooling. ^ _ _ FiG.25i Arc strikes up Indusi WSS là Guide WD2.1 Intermediate Weld Discontinuities Stray arc strikes, either with the electrode or holder, are more serious than expected. They may create a quenched and embrittled condition in the weld zone of alloy steels and are inadvisable even on mild steel, where high static or normal fatigue stresses may be encountered. Repair of such damage may be difficult and costly, involving grinding and probably preheating in the case of alloys. 2.16 Slag Inclusions Slag Inclusions are oxides and other nonmetallic solids that are sometimes found as elongated or multifaceted inclusions in welds. Slag is always produced when welding with covered electrodes, tubular flux cored electrodes and submerged arc electrodes/flux, serving as scavengers of impurities in the molten metal pool. In addition, it forms a blanket over the weld to control cooling rate and exclude atmospheric oxygen and nitrogen from the hot metal surface. During the welding process, fluxes from slag are forced below the surface of the molten metal by the stirring action of the arc. While the weld metal remains molten, slag generally has time to float to the surface of the weld due to its lower density. A number of factors may affect the ability of the slag to rise to the surface of the weld resulting ïn slag that is trapped subsurface in the weld metal. Some of these factors are: $ $ High viscosity weld metal Rapid solidification of weld metal (heat input too low for the application) $ $ $ Improper manipulation of the electrode Improper interpass cleaning Weld discontinuities from a previous weld pass Rapid solidification of the weld metal sometimes does not allow enough time for slag to float to the surface of the weld metal. This is usually due to incorrect setting of welding parameters, resulting in a heat input that is too low for the application. High-speed welding applications result in low heat inputs and fast cooling, and procedures need to be developed to ensure that slag has adequate time to escape. Page 45 Copyright © 2015 CWB Group Industry Services An Iniative øf thế WSS Study Guide WD2.1 . cwbgroup Intermediate Weld Discontinuities z —- Covered electrode \ Slag rising to HN surface of slag solidifles weld pool Plus Core wire Droplets of filler metal coated with flux or slag entering molten pool through arc Base metal Previously deposited weld bead MPRenGiog an. riG.36| Formation oƒ slag m In multipass welding, insufficient cleaning between weld passes can leave portions of the slag coating in place, which is then covered by subsequent Dasses. Such slag inclusions are often characterized by their location at the edge of the underlying metal deposits, where they tend to extend ^ longitudinally along the weld. Slag lines can be either intermittent or continuous. lí the prior pass produces a bead that is too convex, or ïf the arc has undercut the joint face, ït will be difficult to remove the slag between the groove and the ^ = deposited metal. When the slag is left in place, it is covered by subsequent passes (see Figures 37). Trapped Slag Convex bead Undercui FiG.37) Trapped slag | WSS là Guide WD2.1 Intermediate Weld Discontinuities The proper choice of welding electrode is also important as some electrodes are specially formulated. For example, flux cored electrodes designed for out-of-position welding have a fast freezing slag system. The use of these electrodes for high-speed welding applications may result in slag inclusions. The proper choice of electrodes for high-speed welding are those designed for welding in the flat and horizontal positions with more fluid slag systems. Selecting the wrong size of electrode may also result in slag inclusions. In making a root pass, the electrode may be so large that the arc strikes the side of the groove instead of the root. The slag will roll down into the root opening and become trapped under the root layer. This is because the arc failed to heat the root area to a sufficiently high temperature to allow the slag to float to the surface. Slag inclusions are usually trapped below the surface and require NDT methods capable of detecting below-surface discontinuities. The majority of slag inclusions may be prevented by proper preparation of the groove before each bead is deposited (including sufficient cleaning) and using care to correct any contour that would be difficult to fuse fully with the arc. Page 4 Copyright © 2 9 WSS Study Guide WD2.1 % ® cwbgroup Intermediate Weld Discontinuities 2.16.1 Tungsten Inclusions Tungsten inclusions are characteristic of the tungsten inert gas welding process. lf the tungsten electrode comes into contact with the weld metal, tungsten particles can be trapped in the deposited metal. Applications that employ pure tungsten are prone to this because the electrode end is molten while welding and will spït droplets of tungsten across the electrode electrode and being arc if overheated. Improper sharpening of the tungsten can also result in tungsten inclusions. Sharpening the to a fine point may result in the tip of the electrode melting off deposited in the weld metal. 2.16.2 Copper Inclusions Copper inclusions occur when pieces of the copper sheath of a carbon arc-air electrode fall into the groove and are subsequently welded over. Continuous electrode processes use copper contact tips and copper-alloy nozzles. lf these parts contact the weld pool, copper inclusions can be created. Copper inclusions may also occur during magnetic particle testing of welds. The current supplied to create the magnetic field may be passed through copper conductors (prods). lf there is poor contact between the prods and the steel when the current is applied, sparking will occur and copper particles may be melted into the structure. This tựpe of problem should be carefully avoided due to the propensity for crack propagation from the embedded inclusions. 2.16.3 Oxidation In pipe and tube welding of components for critical service (e.g., nuclear plants), some specifications forbid the presence of oxides on the internal surface of the welds. In these cases, the internal surface of the pipe/tube weld joint is filled with a constant supply of inert gas during welding. This practice is commonly called purging. lf the gas flow is inadequate, oxides wÏïll form and cause the weld to be rejected. Control of the gas supply is, therefore, an essential operation to produce sound welding. Page 48 Copyright © 2015 CWB Group Industry Services WSS Studý Guide WD2.1 cwbgroup Intermediate Weld Discontinuities 3. Metallurgical Discontinuities 3.1 Porosity The term porosity is used to describe gas pockets trapped in the solidifving weld metal. At high temperatures, gases can dissolve into the liquid metal. These gases originate from impurities in the base metal, contamination on the joint surfaces, incomplete shielding of the molten pool or contaminated weld filler metal. The amount of gas that can be absorbed by the liquid is much more than can be contained in the solid metal. When the welding process is applied correctly, the amount of absorbed gas is reduced and porosity is prevented. Gas bubbles escape here Consumable electrode Gases absorbed here Base metal Weld solidifying here tìm Formation oƒ porosity An ininanve of the WSS Study Guide WD2.1 . cwbgroup Intermediate Weld Discontinuities Porosity can occur in a variety of patterns, sizes, shapes and quantities in any position in the deposited weld metal. Some porosity may appear on the surface of the weld, and therefore can be visually detected. However, when porosity is sub-surface, non-destructive testing methods, such as radiography or ultrasonic inspection, is necessary to detect it. | WSS sua Guide WD2.1 1 ặ¡ cwbgroup Intermediate Weld Discontinuities Causes of Porosity: In multipass welding, the location of porosity in relation to the depth on the cross-section of the weld may assist in determining the probable cause. ln many cases, porosity is accumulative as subsequent passes are deposited. To avoid building up the density of the porosity to a point where a completed weld would be unacceptable, it should be removed entirely prior to the addition of further passes. .v.$--2$}. The probable causes of porosity may be categorized as: Moisture Chemistry and structure of the parent material Surface impurities and contaminants Shielding gas Welder technique Air contaminants Insufficient flux coverage Slag residue (improper interpass cleaning) 3.1.1 Moisture Moisture pick-up on flux coated electrodes, or on the surface of flux-cored wire that has been exposed to humid conditions, will cause porosity. The same situation pertains to externally applied flux in welding processes such as submerged arc and electroslag. To avoid moisture, the consumables, including fluxes, should be stored under controlled conditions. Various codes and standards may dictate procedures for the proper storage of weld consumables. Storage conditions for SMAW will be governed by the type of flux, with basic fluxing systems requiring storage temperatures above 120 °C (250 °F). This ensures moisture levels are kept at an acceptable level to produce a weld deposit with a low hydrogen designation. For SMAW and SAW processes, consumable manufacturers typically give baking instructions for electrodes and fluxes that may have been exposed to the atmosphere. Page 51 Copyright © | 2015 CWB Group Industry Services WSS Study Guide WD2.1 —¬ An initiative ØI cwbgroup thế Intermediate Weld Discontinuities 3.1.2 Chemistry and Structure of the Parent Material Under normal conditions, it is important to select the proper filler metal to match the chemistrv and properties of the material to be welded. In cases of relatively high-sulphur content metals, parent material porosity is commonly encountered. Other elements, such as zinc coating on galvanized steels, may also create excessive porosity after welding. In some applications, for example in welding T-stiffeners in shipbuilding, welding over primers is common practice. Specially formulated electrodes and welding procedures developed for welding over primer have been used in this case. Porosity is commonly encountered when welding the second side of a fillet weld because gases have little room to escape. Welding procedures for these situations can be verified by performing fracture tests on the second side welded and taking porosity counts, which are evaluated against the applicable standard. 3.1.3 Surface Contaminants When fabricating metals, the surfaces may be in contact with certain contaminants that can cause porosity. Some of these contaminants are: $ oil $ grease $ paint $ oxides Page 52 Copyright © 2015 CWB Group Industry Services WSS Study Guide WD2.1 cwbgroup Intermediate Weld Discontinuities Rust and mill scale can also absorb contaminants and become a source of DOTOSity. ,v.Ÿ.S._.scs-.2e..e Methods of preparing material for welding often introduce contaminants. Some of these methods include: shears band saws abrasive grinding wheels mechanical nibblers oxy-fuel apparatus Tools, such as air grinders, aïr chipping or aïr scaling guns, may deposit films of oil, grease or moisture on the surfaces to be welded. Inline filters should be used to remove moisture from the air system before it reaches the aïr powered tool. Carbon steel wire brushes used on stainless steels may also be a cause of porosity. Contaminants that cause porosity may also be picked up when recovering unused flux during or after submerged arc welding operations. 3.1.4 Shielding Gas Porosity associated with shielding gases is often caused by poor distribpution within the arc and surrounding areas, insufficient or excessive shielding gas flow rates, or impurities collected in the gas through hoses, connections and the torch or gun assemblies. It is possible for the shielding gas to be contaminated but this occurs mainly where bulk systems have not been properly maintained. However, shielding gas mixtures dissociate over time resulting in an uneven mixture of the gases. Loose fittings and connections may allow atmospheric gases to enter the gas hoses and assemblies and cause porosity. roup Industry Services WSS Study Guide WD2.1 - ® so Intermediate Weld Discontinuities 3.1.5 Welder Technique 2soeses$ In manual welding applications, the following may cause porosity: Taulty manipulation of the electrode excessive arc voltages incorrect electrode angle incorrect weave techniques 3.1.6 Air Contaminants Welding operations located in close proximity to painting operations may result in porosity problems. 3.1.7 Insufficient Flux Coverage Insufficient flux coverage in submerged arc welding may cause scattered surface porosity. 3.1.8 Slag Residue Slag left on the surface of tack welds may cause porosity. Interpass cleaning operations should be such that all slag is removed before depositing the next pass. Surface porosity may be detected by visual examination if the indications are large enough or by a nondestructive method that is suitable for detecting surface discontinuities. Porosity below the surface may be detected by NDT methods capable of detecting subsurface discontinulities. Relevant codes and standards should be referenced to determine the acceptance limits of porosity. Usually this is determined by the size, number and spacing of the porosity, and also the service requirements of the weldment. For example, small porosity indications are common when welding aluminum, and and are acceptable as long as the porosity indications remain small and scattered throughout the weldment. Repairing a weld with porosity that is determined to be a defect requires grinding or gouging to remove the porosity and re-welding. Care must be taken when removing weld metal that a desirable groove profile is achieved for the repair weld passes. @ Page 54 (ø 2015 CWB Group Industry Services nh WSS Study Gúide WD2.1 Intermediate Weld Discontinuities 3.2 Cracking 3.2.1 Solidification Cracking solidification cracking is a phenomenon that results in longitudinal cracks ¡in the weld metal. During the solidification of weld metal, grains begin to grow from the fusion boundary towards the central region of the weld pool. Some alloying elements and impurities are rejected ahead of the growing crystals. Their presence lowers the freezing temperature substantially below that of the first liquid to solidify. As solidification takes place, the weld and surrounding material are progressively cooling, and this gives rise to contraction strains across the weld. When solidification is almost complete, and grains begin to meet, the low melting point liquid may not have much duc