On-Load Tap Changer Type A Operating Instructions PDF
Document Details
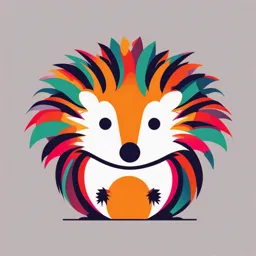
Uploaded by ValuableSugilite
Tags
Related
- On-Load Tap Changer Type M A Inspection Instructions PDF
- On-Load Tap Changer Type T Operating Instructions PDF
- On-Load Tap Changer Type T Operating Instructions PDF
- On-Load Tap Changer Type T Inspection Instructions PDF
- VACUTAP® VV® On-load Tap-changer Installation and Commissioning Instructions PDF
- VACUTAP® VV® On-load tap-changer Technical Data PDF
Summary
This document provides detailed operating instructions for an on-load tap changer (type A). It covers topics like general information, shipment details, installation procedures, connections, testing, and operational aspects. The instructions are specific to electrical engineering applications.
Full Transcript
# On-Load Tap Changer Type A Operating Instructions ## Contents - **1. General** - **2. Shipment** - **3. Installation of the tap changer** - **4. Connection of the tapped winding and of the take-off lead** - **5. Transformer ratio test** - **6. Drying process and oil filling** - **7. Mounting th...
# On-Load Tap Changer Type A Operating Instructions ## Contents - **1. General** - **2. Shipment** - **3. Installation of the tap changer** - **4. Connection of the tapped winding and of the take-off lead** - **5. Transformer ratio test** - **6. Drying process and oil filling** - **7. Mounting the protective relay** - **8. Mounting the motor drive unit, bevel gear and the drive shaft** - **9. Putting the tap changer into operation in the transformer factory** - **10. Transporting the transformer to the operating site** - **11. Putting into service at the operating site** - **12. Supervision in service** - **13. Inspections** - **15. Appendix** ## 1. General The tap changer type A is designed as a selector switch of tubular design. The switching principle combines the operational features of a diverter switch and of a tap selector. The switch oil of the tap changer is separated from the insulating transformer oil by means of the oil compartment cylinder. The tap changer is fastened to the transformer cover by its tap changer head which serves also for the mechanical connection of the tap changer to the driving shaft and for the connection of the oil compartment to the oil conservator. If required the tap changer may be equipped with a change-over selector. The design of the tap changer and the nomenclature of the main parts can be seen from the installation drawing of the appendix. The tap changer models without change-over selector are available up to a maximum of 8 and with a change-over selector up to a maximum of 15 operating positions. The operating instructions apply to the following tap changer models: - **Three-pole tap changers for star-connection (fig. 1)** - A III 100 Y without and with change-over selector - **Three-pole tap changers for any connection (fig. 2)** - A III 100 A without and with change-over selector - **Single-pole tap changers** - A I 100 without and with change-over selector ## 2. Shipment The tap changer and motor drive are shipped in the adjustment position. Check shipment against the shipping documents for completion. Until being installed the parts must be stored in a dry place. The tap changer must be remained in its plastic cover and should be unpacked immediately before its installation. Drive shaft, bevel gear and protective relay are added to the tap changer shipment. The tap changer equipment is shipped as follows (insulating parts protected against moisture): - **Tap changer type A** - (max. weight 55 kg) - **Motor drive MA 9 (about 60 kg), fig. 3** - **Motor drive MA 7 (about 90 kg)** - **Drive shaft parts with coupling parts and bevel gear (max. weight about 20 kg), fig. 4** - **Protective relay RS 2001 (3.5 kg), fig. 5** ## 3. Installation of the Tap Changer ### 3.1 Mounting Flange For mounting the tap changer head on the transformer cover the use of a mounting flange soldered to the cover is recommended. This mounting flange is to be made in accordance with the gasket surface of the tap changer head (see fig. 6 and appendix, drawing N 1051, N 1002). For positioning the studs (M12, max. length 45 mm) we recommend to use a drilling template (see fig. 7 and appendix, drawings 053 906, 053 907) which will be supplied with the first tap changer on request and without charge. ### 3.2 Attachment of the Tap Changer to the Transformer Cover Proceed as follows: - Clean the sealing surfaces (head bottom, mounting flange). - Put an oil proof gasket on the mounting flange of the transformer cover. - Lift the tap changer over the transformer cover and lower it carefully into the opening of the mounting flange. - Take care not to damage the connecting contacts of the tap changer. - Check the correct position of the tap changer head. - Fasten the tap changer head to the mounting flange. ## 4. Connection of the Tapped Winding and Take-Off Lead The tap leads have to be connected to the tap changer according to the particular tap changer connection diagram which will be supplied together with the equipment. **Please note:** All lead connections to the tap changer must be carried out carefully and locked safely. The tap leads should be assembled in such a manner to allow for connecting all leads to the tap changer without using force. If leads cross the oil compartment surface be sure to retain an adequate clearance to surface and to live parts of the tap changer. All terminals are designated according to the connection diagram. ## 5. Transformer Ratio Test We recommend to perform a ratio test at a low a. c. voltage prior to drying the transformer. In order to operate the drive shaft of the tap changer head a short tube (rated with 25 mm) with an inserted coupling bolt (12 mm diameter) together with a hand wheel or a hand crank may be used. Per step, one revolution of the drive shaft is required. The selector switch operation can distinctly be heard. The end position indicated on the applicable connection diagram (position numbering) must in no case be overrun. Therefore check always through the inspection window of the tap changer head the operating position just arrived at. Reduce the number of tap change operations to a minimum as long as the tap changer has not yet been filled with oil. After completing the test it is necessary to run again the tap changer into the adjustment position (see applicable connection diagram supplied with the tap changer). ## 6. Drying Process and Oil Filling ### 6.1 Drying Process To obtain the dielectrical values guaranteed by us the tap changer should be subjected to a minimum drying process according to the following instructions (6.11 or 6.12 alternatively). #### 6.11 Vacuum Drying in the Autoclave In case of autoclave drying remove the tap changer head cover (see fig. 11). - **Heating up:** Heat up the tap changer in air of atmospheric pressure at a temperature rise of about 10°C/h to a maximum final temperature of 110°C. - **Predrying:** Predrying in circulating air at a maximum temperature of 110°C applied to the tap changer for the duration of 20 hours. - **Drying process:** Vacuum drying at a maximum temperature of 110°C applied to the tap changer, maximum residual pressure 10-3 bar for a duration of 100 hours. #### 6.12 Vapor-phase Drying Process To allow for draining the kerosene condensate from the oil compartment, open the kerosene drain plug of the oil compartment bottom before drying. Unscrew from the outside the plug (see fig. 10). After the drying, the plug must be screwed in again. For applying the vapor-phase it is necessary to remove the tap changer head cover (see fig. 11). - **Heating up:** Apply the kerosene vapor at a temperature of about 90°C and maintain this temperature for about 3 to 4 hours. - **Drying:** Increase the kerosene vapor temperature by about 10°C/h to the required final temperature with, however, 125°C as a maximum applied to the tap changer. The duration of the drying process depends on that of the transformer. Make sure that the kerosene draining plug is tighten well after the drying process. ### 6.13 Attention: Do not operate the tap changer without oil after drying. Operate the tap changer only after filling the oil compartment with oil. ### 6.2 Oil Filling Replace the tap changer head cover. Tighten uniformly all 8 or 9 cover screws M12 (wrench size 19) (max. torque 34 Nm). ## 7. Mounting The Protective Relay (see appendix, dimension drawing RSm 2001) Basically the 2 connections R of the tap changer head can be used as required. For connection of the protective device a pipe connection with flange is provided, which must be screwed in oil tight into the bore hole R of the tap changer head. Install the protective relay RS 2001 in accordance with our Operating Instructions No. 59. Beside note the following: - The stamped serial number must coincide with that of the tap changer. - Place the protective relay as near the tap changer head as possible and in a horizontal position. - The arrow on the protective relay when fitted must point to the oil conservator. - The pipe line to the oil conservator should be inclined by at least 2%. - Provide a stop cock between the protective relay and the oil conservator to avoid draining the oil conservator in case of a tap changer inspection. ## 8. Mounting the Motor Drive Unit, The Bevel Gear and the Drive Shaft ### 8.1 Mounting the Motor Drive Unit (see appendix, dwg. N 1255 and N 1267 respectively) For comprehensive information see our Operating Instructions No. 80 for motor drive unit MA 9 or No. 40 for motor drive unit MA 7 respectively. **Please note:** Serial no. of motor drive unit and tap changer must be the same (name-plate). Motor drive unit and tap changer must be in the same operating position (this position is indicated in the connection diagram supplied with the equipment). The motor drive unit shall be mounted at the provided place on the transformer tank in a vertical position and protected against excessive transformer vibrations. ### 8.2 Mounting the Bevel Gear The bevel gear is to be attached to a support on the transformer cover by means of 2 bolts (through-holes 18 mm dia., see appendix, dwg. CDm 6400). **Please note:** Make sure that bevel gear serial number and tap changer serial number correspond. For special bevel gears and for intermediate bearings of the vertical or horizontal part of the drive shaft these instructions apply analogously. ### 8.3 Mounting the Drive Shaft The drive shaft shall be assembled according to our Operating Instructions No. 42. The drive shaft is the mechanical connection between the motor drive and tap changer head. The bevel gear diverts the driving force from the vertical to the horizontal direction. Accordingly, the vertical part of the drive shaft is to be mounted between motor drive unit and bevel gear, whereas the horizontal part of the drive shaft is to be mounted between bevel gear and tap changer head. The drive shaft itself consists of a square tube and is to be connected on both ends to the respective implement by two coupling brackets and one coupling bolt. When mounting the drive shaft make sure that the trunnions to be connected are properly aligned. Square shaft, coupling brackets, bolts, nuts and lock tabs are made of corrosion-proof steel. We recommend, however, to apply the same outside varnish here as to the transformer tank. The square shaft and plate for the foot step protection on the transformer cover are supplied in oversize (various standard lengths). These parts must be cut to the required size before mounting. Finally equalize the rotation lag between tap changer and motor drive unit according to Operating Instructions, for MA 9: No.80, for MA 7: No. 40. ## 9. Putting the Tap Changer into Operation in the Transformer Factory ### 9.1 Operational Tests Before applying voltage to the transformer, check the mechanical operation of tap changer and motor drive. For these test operations the tap changer has to be run through the complete operating cycle. - Make sure that in each operating position the indicators of motor drive and tap changer (tap changer head) read the same position. - Make sure that in both end positions the electrical and mechanical limit stops function automatically (see Operating Instructions No.80 for motor drive unit MA 9 or No. 40 for motor drive unit MA 7 respectively). ### 9.2 Final Oil Filling Fill up the tap changer completely with transformer oil via the oil conservator. - Bleed the tap changer head via the bleeder screw in the head cover: hex. head screw M8 (wrench size 13, max. torque 15 Nm). ### 9.3 Ground Connections Connect the ground screw M12 of the tap changer head and of the tap changer head cover to the transformer cover (wrench size 19, max. torque 60 Nm). Connect the ground screw of the motor drive to the transformer tank. ### 9.4 Electrical Transformer Tests After the preceding operations, the transformer acceptance test may be performed. ## 10. Transporting the Transformer to the Operating Site If the transformer is to be transported without the motor drive unit, set the motor drive to the adjustment position, uncouple and dismount. For remounting the motor drive unit, follow the instructions according to section 9.1. If the transformer is to be transported or stored without oil filling, drain the oil of the tap changer completely. The interior of the tap changer should be conserved and protected in the same way as the transformer itself (nitrogen-sealing). When a prolonged stand-by period is expected, connect the heater of the motor drive unit to power. ## 11. Putting into Operation at the Operating Site Before putting the transformer into service, operational tests of tap changer and motor drive have to be performed according to section 9.1. At the same time check the function of the protective relay. The protective relay has to be inserted into the tripping circuit of the circuit breakers in a way that energization of the protective relay switches off the transformer immediately (see Operating Instructions No. 59 for protective relay RS 2001). Make sure the circuit breakers switching off the transformer when the test push button >>OFF << is operated. Be sure that they can switch on the transformer only after the push button >>>IN SERVICE<<< of the protective relay has been pressed. Check whether all stop valves between oil conservator and tap changer head are open. ## 12. Supervision in Service, Failures It is only necessary to inspect the tap changer head, the protective relay and the motor drive unit occasionally. Pay special attention to: - oil tightness of sealings of tap changer head, the protective relay and the pipe connections, - tightness of the motor drive housing, - proper function of the electrical space heater in the motor drive unit, - the condition of the control apparatus in the motor drive unit. In case of a response of the protective relay it is absolutely necessary to check the tap changer and transformer. For this purpose withdraw also the selector switch unit. In addition see Operating Instructions No. 59 or the protective relay RS 2001. **Before returning to service, make sure that the tap changer and transformer are undamaged. Never reconnect the transformer without prior checking.** In case of serious trouble with tap changer or motor drive - provided that the repair cannot easily be done on site and in case of a response of the protective relay please contact the authorized MR representative, the transformer manufacturer or Maschinenfabrik Reinhausen GmbH Postfach 12 03 60 Technical Service D-93025 Regensburg Phone: +49-941-4090-0 Fax: +49-941-4090-501 Telex: 65881 Cables: oltc reinhausen ## 13. Inspections (see Inspection Instructions No. 88) We recommend inspection of the tap changing equipment at regular intervals to maintain a high level of operating reliability. In general, the inspection can be carried out by qualified and trained personnel within one day provided it is well prepared and organized. We recommend on principle to have the inspection carried out by our Technical Service Department. This ensures expert execution of the inspection including the retrofitting of certain components of the latest design. If the inspection is not be performed by MR personnel we suggest inquiry of the necessary spare parts (please indicate tap changer no. and number of operations). The number of operations determining the inspection intervals indicated in table I are figures based on experience with oil qualities normally used. The user should regularly test the transformer insulating oil. The dielectric strength and the water content of the oil (record oil temperature during sample-taking) must comply with the respective standards such as IEC Publication 422 (1989), DIN 57 370 Teil 2/VDE 0370 Teil 2/12.78. If inspection is not carried out by MR personnel, please send us your inspection report for our files. ## 14. Appendix - **Installation drawings** - for models without change-over selector - N 1051 - for models with change-over selector - N 1002 - **Dimension drawings of the tap changer head** - for models without change-over selector - N 1162 - for models with change-over selector - N 1161 - **Drilling template for tap changer head** - for models without change-over selector - 053 906 - for models with change-over selector - 053 907 - **Protective relay RS 2001, dimension drawing** - RSm 2001 - **Motor drive unit MA 9, dimension drawing** - N 1255 - **Motor drive unit MA 7, dimension drawing** - N 1267 - **Bevel gear CD 6400, dimension drawing** - CDm 6400 Standard values for oil testing according to CIGRE report 12-13 (1982) at service temperature: | On-load tap changer | Water content* | Dielectric strength** | |---|---|---| | A III 100 Y | < 40 ppm | > 30 kV/2.5 mm | | A III 100 Δ, A I 100 | < 30 ppm | > 40 kV/2.5 mm | * measured according to the Karl Fischer method based on IEC Publication 814 (1985) ** measured according to DIN 57 370 Teil 1 VDE 0370 Teil 1/12.78. | On-load tap changer | Rated transformer current | Number of tap change operations | |---|---|---| | A III 100 Y | up to 50 A | 100 000 | | | over 50 A | 70 000 | Regardless of the number of tap change operations, inspections must be carried out after 5-6 years. | On-load tap changer | Rated transformer current | Number of tap change operations | |---|---|---| | A III 100 A | up to 100 A | 10 000 | | A I 100 | up to 100 A | 10 000 | The first inspection must be carried out after 1 year of service or after 10,000 switching operations respectively, whichever comes first. Further inspections are required every 2 years or after 10,000 switching operations respectively, whichever comes first. ## Installation Drawings - **For models without change-over selector** - N 1051 - **For models with change-over selector** - N 1002 ## Dimension Drawings of the Tap Changer Head - **For models without change-over selector** - N 1162 - **For models with change-over selector** - N 1161 ## Drilling Template for Tap Changer Head - **For models without change-over selector** - 053 906 - **For models with change-over selector** - 053 907 ## Protective Relay RS 2001, Dimension Drawing - RSm 2001 ## Motor Drive Unit MA 9, Dimension Drawing - N 1255 ## Motor Drive Unit MA 7, Dimension Drawing - N 1267 ## Bevel Gear CD 6400, Dimension Drawing - CDm 6400 The document contains a detailed diagram of the tap changer with labels for all parts. The diagram includes the following: - SCREW - WASHER - HEAD COVER - GUIDE RING - WINDING UP DISK - POSITION INDICATION - SPRING-OPERATED ENERGY ACCUMULATOR - SWITCHING CYLINDER - OUTPUT CONTACT ROLL - TRANSITION RESISTORS - TRANSITION CONTACT ROLL - SWITCHING ELEMENT - PIVOT BEARING - HEAD - CAP NUT - WASHER - TRANSFORMER COVER - SUPPORTING FLANGE - STUD - SUPPORTING FLANGE - CURRENT OUTPUT - CONNECTING CONTACT - SELECTOR SWITCH OIL TANK - TAP CHANGER BOTTOM - COUPLING SLEEVE - PROTECTIVE RELAY - DRIVING SHAFT - GASKETS - AUXILIARY CONTACT ROLL - MAIN CONTACT ROLL - PAWL - PAWL DISK - TRANSFORMER COVER OPENING - OUTPUT CONTACT ROLL - LOCATION OF OUTPUT TERMINALS - LOCATION OF CONNECTING CONTACTS - BLEEDER SCREW (M8) - CONNECTING FACILITY FOR PROTECTIVE RELAY - TRANSFORMER COVER CUTOUT - CHANGE-OVER SELECTOR CONTACT CYLINDER - SELECTOR SWITCH CONTACT CYLINDER - CHANGE-OVER SELECTOR TERMINAL - CURRENT TAKE-OFF - SELECTOR SWITCH TERMINAL The document also contains detailed diagrams of: - Motor drive unit MA 9 - Motor drive unit MA 7 - Bevel gearing The diagrams include labels for all parts.