Introduction to Operations Management Session 1 PDF
Document Details
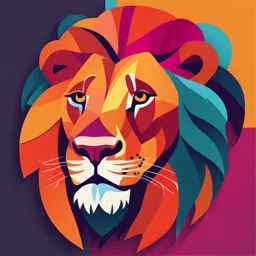
Uploaded by PopularSaxophone
The University of Waikato
Tags
Summary
This document is a presentation on Introduction to operations management, Session 1 at THE UNIVERSITY OF WAIKATO. It covers the agenda, general information, assessment, recommended textbooks, and weekly readings. The presentation is aimed at undergraduate students.
Full Transcript
Introduction to operations management Session 1 Managing manufacturing and service operations SCMGT563 Agenda General paper information About operations management Competitive priorities Goods and services Productivity measurement Agend...
Introduction to operations management Session 1 Managing manufacturing and service operations SCMGT563 Agenda General paper information About operations management Competitive priorities Goods and services Productivity measurement Agenda General paper information About operations management Competitive priorities Goods and services Productivity measurement General paper information Lectures Wednesdays, from 9am to 12pm Lecture material (slides, case studies, etc.) uploaded to Moodle International students located in New Zealand must attend the on- campus classes General paper information General paper information Assessment Class activities (60%) 1 or 2 activities during class time Service process analysis (20%) Due on 23/08 (2pm) Group video (20%) Due on 20/09 (2pm) General paper information Class activities 12 class activities will be marked The best 10 will count toward your overall grade 10@6% each = 60% Examples Short-answer question related to a reading/case study Short-answer question related to a video watched in class Reflection question on a key topic of the week Quiz Calculations etc. General paper information Group video (3 or 4 students) Groups to be formed on Moodle Only add your name to a group if you know with whom you will complete the assessment Don't add your name to a group without contacting the existing team members beforehand General paper information Extensions No request for extension will be accepted unless you are sick and provide a medical certificate A medical certificate must be emailed to me before the start of the class General paper information Recommended textbooks Jacobs & Chase 2018, Operations and supply chain management, 15th edition, McGraw-Hill/Irwin UoW Library: Hamilton and online Krajewski et al. 2021, Operations Management, 13th edition, Pearson UoW Library: online General paper information Weekly readings Textbook + additional readings/case studies available on Moodle Do the readings before coming to class Some class activities will be based on the readings Agenda General paper information About operations management Competitive priorities Goods and services Productivity measurement About operations management What is operations management? Design Purchasing Manufacturing Packing Storage Shipping About operations management Definition The design, operation, and improvement of the systems that produce and deliver an organisation’s goods and services in the manner that matches customer expectations Key points Designing, operating, and improving the processes of an organisation (what an organisation does and how it does it) Multiple functions involved (e.g. procurement, production, logistics) Both goods and services Meeting customer requirements About operations management Processes A process is a series of actions/steps that transform inputs into outputs Inputs Transformation Outputs - Materials - Physical (manufacturing) - Goods - Services - Locational (transport) - Services - Labour - Exchange (retail) - Land - Physiological (health care) - Energy - Informational (news) - Capital - Data About operations management Examples of transformation processes Transformation Organisation Inputs Outputs process Patients, doctors, Hospital nurses, equipment, Healthcare Healthy individuals medical supplies Hungry customers, Food preparation Restaurant food, chefs, Satisfied customers and service waiters/waitresses Steel, car parts, Car manufacturer tools, equipment, Car assembly Vehicles workers Students, lecturers, Transfer of University Educated individuals classrooms, library knowledge About operations management Identify the inputs, the outputs, and the core operational activities for the following organisations: Manufacturing organisation: bakery Service organisation: airline Core operational Inputs Outputs activities About operations management The importance of processes Processes create value Competition is increasingly value-based (≠ product-based) Gaining a competitive advantage requires not only product excellence, but also process excellence About operations management Operations management vs supply chain management Operations management Supply chain management Internal processes Inter-organisational that transform processes that convert resources into raw materials into goods/services consumer products About operations management Operations management vs supply chain management “n” tier suppliers 1st tier suppliers manufacturer distributor retailer consumers Operations management Supply chain management Agenda General paper information About operations management Competitive priorities Goods and services Productivity measurement Competitive priorities The critical operational dimensions to consider when developing/improving an organisation’s processes 4 areas of focus 1) Cost 2) Quality 3) Time 4) Flexibility 9 competitive priorities Competitive priorities 1. Cost Competitive Definition Process considerations Example priority Designing processes for Many supermarket Producing goods or 1.1. efficiency chains adopt a low-cost services at the lowest Low cost Negotiating aggressively strategy to offer low possible cost with suppliers prices to their customers (Adapted from Krajewski, Malhotra & Ritzman, 2021) Competitive priorities 2. Quality Competitive Definition Process considerations Examples priority Swiss-made precision Delivering an 2.1. Quality at the heart of timepieces outstanding good Top quality all processes Luxury car manufacturers (e.g. or service Rolls Royce) McDonald’s standardises work Constantly monitoring methods, staff training Producing goods or and improving 2.2. processes and the services that meet processes to prevent Consistent procurement of raw materials specifications on a defects and achieve quality to achieve the same product consistent basis similar outcomes over and process quality from one time restaurant to the next (Adapted from Krajewski, Malhotra & Ritzman, 2021) Competitive priorities 3. Time Competitive Definition Process considerations Examples priority 3.1. Quickly filling a Designing processes to Amazon offers a same-day Delivery customer order reduce lead times delivery service 7 days a week speed Courier service providers use 3.2. Introducing strict process Meeting delivery their expertise in logistics to On-time planning and developing time promises deliver shipments on-time delivery expertise in logistics around the globe Quickly Achieving cross-functional 3.3. Zara is known for its ability to introducing a integration and involving Development put new clothing designs on new good or key suppliers in the speed the market every month service development process (Adapted from Krajewski, Malhotra & Ritzman, 2021) Competitive priorities 4. Flexibility Competitive Definition Process considerations Examples priority Meeting each customer’s Ability to collect demand Dell assembles computers 4.1. individual needs by information and to and laptops exactly the way Customisation adapting the respond to real demand customers want them good/service design Designing and managing Amazon handles 1 million 4.2. Handling a wide range of robust inventory different items (‘you name Variety goods and services management processes it, we have it’) Accelerating or Postal services have flexible 4.3. Building flexibility into decelerating the rate of processes in place to handle Volume processes to adjust production to handle variations in mail/parcel flexibility production capacity demand fluctuations delivery quantities (Adapted from Krajewski, Malhotra & Ritzman, 2021) Competitive priorities Selecting competitive priorities Competitive priorities must be consistent with the overall corporate strategy Competitive priorities must address the needs of customers Trade-offs are involved Competitive priorities can vary based on market segments Agenda General paper information About operations management Competitive priorities Goods and services Productivity measurement Goods and services Definitions of services Those fruits of economic activity which you cannot drop on your toe; anything from banking to butchery, acting to accountancy (Economist, 1987) Goods are produced, services are performed (Rathwell, 1974) A good is an object, a device; a service is a deed, a performance, an effort (Berry, 1980) A service can be defined as any activity or benefit that one party can offer to another which is essentially intangible and does not result in the ownership of anything (Grönroos, 2000) Goods and services Characteristics of services Intangibility: a service is a performance and an experience, not an object Heterogeneity:variability and lack of consistency (service quality depends on time, provider, and customer) Perishability: service capacity cannot be saved, stored, or inventoried Inseparability: production and consumption occur simultaneously Goods and services Goods vs services Goods Services Tangible Intangible Homogeneous Heterogeneous Production and consumption are Production is separate from consumption simultaneous processes Can be demonstrated before the More difficult to demonstrate before purchase purchase Can be transported Cannot be transported An item A performance or an experience Produced in the interaction between Produced in a facility buyer and seller Goods and services Good-service bundling Combining goods and services Fast food restaurants: food + rapid service Fine dining experience: six-course meal + a variety of services (including sommelier, table etiquette, formal table service, relaxing atmosphere, etc.) Smart phone package: mobile phone + telecom services (data, calling, text messaging) Goods and services The goods-services continuum From the most tangible goods to the most intangible services Products are a bundle of tangible and intangible elements combined to varying degrees Pure goods: Core goods: Core services: Pure services: Goods commodities cars flights financial advice Services Agenda General paper information About operations management Competitive priorities Goods and services Productivity measurement Productivity measurement The concept of productivity Basic measure of process performance => the units of output generated by 1 unit of input Output Productivity = Input Labour productivity: the units of output per employee (or per employee hour) Machine productivity: the units of output per machine (or per machine hour) Multifactor productivity: the units of output generated by a combined set of inputs, e.g. labour + machine + energy Productivity is a relative measure (comparisons are needed) Productivity measurement Examples of productivity measures Business Productivity measure Restaurant Number of meals served per labour hour Car manufacturer Number of cars produced per shift Retail store Sales per square metre Chicken farm Kilogrammes of meat per kilogramme of feed Paper mill Tonnes of paper per cubic metre of wood Key terms/concepts Operations management Intangibility Supply chain management Heterogeneity Process Perishability Core process Inseparability Support process Productivity Product and process excellence Labour productivity Competitive priorities Machine productivity Goods vs services Multifactor productivity Goods-services continuum Questions? © Notice of copyright This screen show contains copyrighted material. Its use is restricted to study purposes at the University of Waikato. Any other use may be an infringement of copyright. Capacity management Session 2 Managing manufacturing and service operations SCMGT563 Agenda Capacity Capacity planning concepts Sizing strategies The capacity management process Planning service capacity Agenda Capacity Capacity planning concepts Sizing strategies The capacity management process Planning service capacity Capacity General definition of capacity The total amount that can be held, accommodated, received, stored or produced Frequently viewed as the maximum output of a system (e.g. a stadium, a seaport, a warehouse, a machine, etc.) over a specific period of time In operations management, capacity can also be defined as: The resources(facilities, equipment, people, etc.) needed to meet customer requirements Capacity Capacity planning Determining the capacity (resources) needed by an organisation to meet current and future demand Making adjustments to increase or decrease capacity Capacity decisions determine: The level of capital required The level of cost incurred Whether demand will be met Whether resources (facilities/equipment/people) will be used Capacity The time dimension of capacity planning Long-range: usually more than 2 years Medium-range: usually 3 months to 2 years Short-range: usually less than 3 months Capacity planning decisions Long-range: buildings, equipment, labour Medium-range: staffing adjustments, inventory, minor equipment purchases Short-range: machine allocations, production schedules, overtime Capacity Time horizons and capacity planning decisions Time horizon More/less facilities Long-range More/less equipment More/less permanent employees More/less minor equipment Personnel reassignments Medium-range More/less shifts Inventory More/less temporary/casual workers Schedules (production and people) Short-range Machine allocations Modifying capacity Using capacity Capacity Today’s focus = long-range capacity planning Determines the overall level of capital-intensive resources needed to meet demand over the long term Involves decisions that cannot be easily reversed Areas of focus Facilities Equipment Overall labour force size Capacity Measures of capacity: output vs input Output measures of capacity are usually used for standardised products (example for a car manufacturer: the number of cars produced per day) Input measures of capacity are usually used for customised products or when volumes are uncertain (example for a hospital: the number of beds available) Agenda Capacity Capacity planning concepts Sizing strategies The capacity management process Planning service capacity Capacity planning concepts Best operating level The level of capacity for which the system was designed The maximum volume of output that a system can produce Example: the maximum number of items/hour that a machine can produce At the best operating level, the average cost per unit is minimised Capacity planning concepts Capacity utilisation The degree to which a resource is used to its maximum capacity Capacity used Capacity utilisation = x 100 Best operating level Capacity used: output actually achieved The numerator (capacity used) and denominator (best operating level) must be measured in the same units and time periods Capacity planning concepts Economies of scale The cost advantage (lower cost per unit) obtained by an organisation when producing in large volumes Large volumes of production maximise the use of capacity and reduce the cost per unit The capital costs and the fixed costs are spread over more units Diseconomies of scale Economies of scales are no longer achieved because the excessive size of a facility/volume of production generates more complexity and more inefficiencies The average cost per unit increases as the size of the facility/the volume of production increases Capacity planning concepts Best operating level Average cost per unit 250 beds 500 beds 750 beds ($ per patient) Economies Diseconomies of scale of scale Hospital bed capacity Capacity planning concepts Capacity flexibility The ability to rapidly increase or decrease production levels or the ability to shift rapidly from one product to another Flexibility comes from the factory, equipment, processes, workers and the use of external capacity sources Factory: quick layout changes, quick changeovers Equipment: flexible machines Workers: multi-skilled employees able to switch easily from one task to another External sources of capacity: outsourcing, equipment leasing Processes: flexible production processes Agenda Capacity Capacity planning concepts Sizing strategies The capacity management process Planning service capacity Sizing strategies Capacity cushion Reserve capacity, i.e. capacity in excess of expected demand Capacity cushion = Design capacity – Capacity used Used to manage demand uncertainties and fluctuations The appropriate size of the capacity cushion varies from industry to industry Sizing strategies Capacity balance Matching actual customer demand and available capacity Demand exceeds capacity => lost sales Capacity exceeds demand (overcapacity beyond reserve capacity) => inefficient utilisation of the company’s resources Capacity balance (demand = capacity) is hard to achieve Dealing with imbalances Temporary measures (overtime, leasing, subcontracting, etc.) Inventory building, e.g. to manage seasonal fluctuations Longer-term capacity adjustments Sizing strategies Increasing capacity Why do you need to increase capacity? To respond to an increase in demand To minimise the risk of lost sales due to insufficient capacity Demand Small, frequent upgrades forecast vs Large, infrequent upgrades What are the advantages of Capacity each of these approaches? How do you choose between these 2 approaches? Time Sizing strategies Wait-and-see strategy Strategy that lags behind demand Small, incremental capacity adjustments that follow the increase in demand Demand Short-term options (e.g. overtime, temporary workers, subcontractors, delayed preventive equipment Capacity maintenance) are used to deal with short-term capacity shortfalls Time Sizing strategies Decreasing capacity To respond to a decrease in demand Temporary strategies: scheduling fewer hours or a factory shutdown period Permanent strategies: sale of equipment, staff reduction, or even the liquidation of an entire facility Agenda Capacity Capacity planning concepts Sizing strategies The capacity management process Planning service capacity The capacity management process 1. Estimate demand for individual products over the planning horizon Consider seasonal variations and peaks 2. Calculate equipment and labour requirements to meet demand over the planning horizon Include a level of capacity cushion 3. Identify capacity gaps/excesses over the planning horizon 4. Identify and evaluate different capacity adjustment alternatives e.g. large-scale expansion vs incremental expansion vs wait-and-see The capacity management process AlwaysRain Irrigation would like to determine its capacity requirements for the next 4 years. Currently, 2 production lines are in place to make bronze and plastic sprinklers. 3 types of sprinklers are available in both bronze and plastic: 90-degree nozzle sprinklers, 180-degree nozzle sprinklers, and 360-degree nozzle sprinklers. The capacity management process Yearly demand Year 1 (000s) Year 2 (000s) Year 3 (000s) Year 4 (000s) Plastic 90 32 44 55 56 Plastic 180 15 16 17 18 Plastic 360 50 55 64 67 Bronze 90 7 8 9 10 Bronze 180 3 4 5 6 Bronze 360 11 12 15 18 Both production lines can produce all the different types of nozzles (90/180/360). The machine needed for the bronze sprinklers requires 2 operators and can produce 12,000 sprinklers per year. The plastic injection moulding machine needed for the plastic sprinklers requires 4 operators and can produce 200,000 sprinklers per year. 3 bronze machines and 1 plastic injection moulding machine are currently available. What are the capacity requirements for the next 4 years? The capacity management process AlwaysRain Irrigation’s marketing department has undertaken an important ad campaign for the bronze sprinklers (which are more expensive but also more durable than the plastic ones). The demand forecasts for the next 4 years have been revised as follows: Yearly demand Year 1 (000s) Year 2 (000s) Year 3 (000s) Year 4 (000s) Plastic 90 32 44 55 56 Plastic 180 15 16 17 18 Plastic 360 50 55 64 67 Bronze 90 11 15 18 23 Bronze 180 6 5 6 9 Bronze 360 15 16 17 20 What are the capacity implications of the marketing campaign? Agenda Capacity Capacity planning concepts Sizing strategies The capacity management process Planning service capacity Planning service capacity Capacity planning in services vs manufacturing Manufacturing capacity Service capacity As services cannot be stored for later use, As goods can be stored for later use, inventory capacity must be available when customers can be used as a buffer need the services (no inventory) As goods are produced at one central location, As services are produced at the customer manufacturing capacity can be planned for demand and consumption point, capacity the aggregate volume of demand must be managed at each individual point As demand volatility is extremely high, service Production capacity (production schedules) capacity can be planned in increments as usually planned in 1-week increments small as 30 minutes Planning service capacity Capacity utilisation and service quality Critical relationship between service capacity utilisation and service quality Maximum capacity Zone of non-service Arrival rate Zone of service Service rate Planning service capacity Capacity utilisation and service quality Critical relationship between service capacity utilisation and service quality Maximum capacity Zone of non-service Critical zone 70% of the maximum capacity Arrival rate Zone of service Service rate Planning service capacity Balancing supply and demand in service capacity planning Demand > maximum capacity available: waiting periods and unhappy customers Demand > optimal capacity available: inferior service quality Demand < optimal capacity available: inefficient deployment of the organisation’s resources Demand = optimal capacity available: optimal scenario (but rarely happens over long periods of time because demand for services is volatile) Planning service capacity Optimal levels of utilisation are industry-specific and context- specific A low rate of utilisation is appropriate when the degree of demand uncertainty is high and/or the stakes are high (e.g. emergency rooms, fire departments) A high rate of utilisation is possible for predictable services or those without extensive customer contact (e.g. commuter trains, mail sorting) For some specific services (e.g. sport events), high utilisation is desirable and creates an atmosphere Key terms/concepts Capacity Capacity expansion strategies Capacity planning Wait-and-see strategy Output/input measures of capacity Capacity management process Best operating level (design Service capacity planning capacity) Zone of service, critical zone, zone Capacity utilisation of non-service (Dis)economies of scale Maximum capacity Capacity flexibility Optimal level of utilisation Capacity cushion Capacity utilisation and service quality Capacity balance Questions? © Notice of copyright This screen show contains copyrighted material. Its use is restricted to study purposes at the University of Waikato. Any other use may be an infringement of copyright. Process design and analysis Session 3 Managing manufacturing and service operations SCMGT563 Agenda Processes Multiple-stage processes Make-to-stock vs Make-to-order process designs Measuring processes Agenda Processes Multiple-stage processes Make-to-stock vs Make-to-order process designs Measuring processes Processes Business process A seriesof structured actions/steps performed by an organisation to transform inputs into outputs Business processes ensure that customers get what they want, when they want it, where they want it, and at a reasonable price that allows the organisation to make a profit Efficient business processes enable organisations not only to meet customer requirements, but also to reduce costs and increase competitiveness Processes Process flowcharts Drawing a process is always the first step in analysing it Flowchart: a visual representation of the basic elements of a process and the sequence of steps needed to complete it Major elements represented: tasks, flows of goods/people, decision points, storage points, etc. A flowchart is also known as a business process model Processes Flowchart symbols Storage areas or Tasks or operations queues (waiting lines) Decision points Links between the steps of the process Processes Flowchart symbols Drive to cashier booth Cash Obtain parking Cars Cash Park parked Exit from the ticket from or the car parking area entry gate card? Card Drive to automated payment machine Agenda Processes Multiple-stage processes Make-to-stock vs Make-to-order process designs Measuring processes Multiple-stage processes Multiple-stage process Seriesof independent but interconnected activities that are presented together for analysis purposes Stage 1 Stage 2 Stage 3 Multiple-stage processes Multiple-stage processes Stage 1 Stage 2 30 seconds 45 seconds Bottleneck: a step in the process that limits the capacity of the whole process Process blocking: the activities in one stage must stop because there is no place to deposit the item just completed Multiple-stage processes Multiple-stage processes WIP Stage 2 Stage 1 30 seconds 45 seconds Buffer: a storage area between stages where the output of a stage (work in process) is placed prior to being used in a downstream stage => enables the various stages of a process to work independently Multiple-stage processes Multiple-stage processes WIP Stage 2 Increased capacity to Stage 1 eliminate the Stage 2 bottleneck 30 seconds 45 seconds Multiple-stage processes Multiple-stage processes Stage 1 Stage 2 45 seconds 30 seconds Bottleneck: a step in the process that limits the capacity of the whole process Process starvation: the activities in one stage must stop because there is no work Multiple-stage processes Multiple-stage processes Starts earlier WIP Stage 1 Stage 2 45 seconds 30 seconds Multiple-stage processes Multiple-stage processes Increased Stage 1 WIP capacity to eliminate the Stage 2 bottleneck Stage 1 45 seconds 30 seconds Multiple-stage processes Buffering, blocking and starving in multiple-stage processes Bottleneck: a stage in the process that limits the capacity of the whole process Blocking: occurs when the activities in one stage must stop because there is no place to deposit the item just completed Starving: occurs when the activities in one stage must stop because there is no work Buffer: a storage area between stages where the output of a stage (work in process) is placed prior to being used in a downstream stage Agenda Processes Multiple-stage processes Make-to-stock vs Make-to-order process designs Measuring processes Make-to-stock vs Make-to-order Make-to-stock vs Make-to-order 2 different production and order fulfilment process designs Make-to-stock: goods are produced in anticipation of demand Make-to-order: goods are produced in response to demand Additional process designs will be discussed in Session 6 Make-to-stock vs Make-to-order Make-to-stock Standardised products are produced based on demand forecasts Products are stored and sold to customers from inventories Storage Forecasts Production (finished Sales goods) Make-to-order The configuration of the product is adapted to customer requirements Production is activated in response to an actual order Demand Production Delivery (order) Make-to-stock vs Make-to-order Customer places order Raw meat Cook Assemble Deliver Make-to-stock vs Make-to-order Former process Customer places order Raw Finished meat goods Cook Assemble Deliver Make-to-stock vs Make-to-order Current process Customer places order Raw meat WIP Cook Assemble Deliver Make-to-stock vs Make-to-order Assemble Deliver Custom Raw meat Custom WIP Customer Cook or places order standard? Standard Finished Assemble goods Deliver Agenda Processes Multiple-stage processes Make-to-stock vs Make-to-order process designs Measuring processes Measuring processes Process analysis and measurement allow some important questions to be answered: How many customers can the process handle per hour? How many goods can the process produce per hour? How long will it take to serve a customer? How much does the process cost? How can a company improve the flow of goods/customers? How can output be increased? How do a company’s operations compare with its competitors? Measuring processes Measuring process performance Metrics are used to measure an organisation’s performance (both current and over time) Process performance measurement enables organisations to better understand their processes and supports informed decision-making (e.g. regarding process improvement) Performance measurement supports benchmarking (the comparison of the performance of the organisation’s processes to other companies and/or to industry bests) Measuring process performance enables organisations to better schedule work and allocate capacity Measuring processes Measuring process performance Process performance metrics and how they are measured vary from industry to industry and from organisation to organisation It is essential to understand not only the context, but also how the various metrics available are used and calculated Measuring processes Productivity Basic measure of the overall performance of a process Output Productivity = Input Utilisation The most common process metric The ratio of the time that a resource (e.g. machine, labour) is actually activated relative to the time that it is available for use Time activated Utilisation = x 100 Time available Measuring processes Run time The time required to produce a batch of items Run time = Time required to produce each item x batch size Setup time The time required to prepare a machine to make a particular item Operation time The sum of the setup time and run time for a batch of items Operation time = Setup time + Run time Measuring processes Cycle time The elapsed time between starting and completing one unit of work Related concepts for products going through multiple stations: flow time or throughput time Throughput rate The output produced over a period of time (e.g. 1 hour) 1 Throughput rate = Cycle time Measuring processes Little’s Law States a mathematical relationship between throughput rate, flow time and the amount of work-in-process inventory WIP inventory: the volume of inventory tied up in the production process Work-in-process inventory = Throughput rate x Flow time Measuring processes Little’s Law Drive to On average, 100 cars arrive/leave cashier booth every hour On average, 1 car stays 2 hours in the Cash car park Cars Obtain parking parked Cash Park Exit from the ticket from (WIP) or the car parking area entry gate card? Card What is the WIP inventory of Drive to this process? automated payment machine Key terms/concepts Business process Productivity Process flowchart Utilisation Single-stage vs multiple-stage Run time, setup time, operation process time Bottleneck Cycle time Process blocking Flow time Process starvation Throughput rate Buffer Little’s Law Work in process Make-to-stock vs make-to order process design Process performance metrics Questions? © Notice of copyright This screen show contains copyrighted material. Its use is restricted to study purposes at the University of Waikato. Any other use may be an infringement of copyright. Service processes Session 4 Managing manufacturing and service operations SCMGT563 Agenda Characteristics of service operations Operational classification of services: high vs low-contact services Configuring service encounters Managing customer-introduced variability Service blueprinting Agenda Characteristics of service operations Operational classification of services: high vs low-contact services Configuring service encounters Managing customer-introduced variability Service blueprinting Characteristics of service operations 1. Intangible nature of services 2. Service/good mix 3. Management of demand fluctuations 4. Time-dependent capacity 5. Presence of customers in the service delivery system 6. People skills 7. Customer self-service 8. Proximity to customers 9. Limited protection of intellectual property Characteristics of service operations 1. Intangible nature of services Services have no physical existence The service delivery system must be designed in such a way that customers want to buy the service The process is the product 2. Service/good mix Customers purchase a mix of services and goods Characteristics of service operations 3. Management of demand fluctuations Inventory cannot be used to absorb fluctuations in demand (services are perishable => the unused service capacity is lost) A service delivery system is typically cushioned by using a mix of capacity and customer waiting time Example: a restaurant regulates demand fluctuations with capacity (e.g. waiters/waitresses/cooks, etc.) and the amount of time customers wait before being served Example: a supermarket regulates demand fluctuations with capacity (e.g. the number of check-outs open) and customer queues Characteristics of service operations 4. Time-dependent capacity Making capacity meet demand is a dominant issue in service processes Too much capacity => waste of resources Not enough capacity => customer dissatisfaction and lost sales 5. Presence of customers in the service delivery system Services are produced and consumed simultaneously (inseparability) The service environment must reflect customer expectations Customer involvement generates variability and inconsistencies (heterogeneity) 6. People skills The customer/staff interface is a critical part of the service delivery system Staff need to be able to interact positively with customers Characteristics of service operations 7. Customer self-service Customers can be actively engaged in the service delivery system 8. Proximity to customers The service delivery system is typically located close to customers Exceptions: airport, call centres, etc. A service organisation made up of small units of capacity must ensure that consistency is achieved and maintained across locations 9. Limited protection of intellectual property The most effective way to protect a service concept is by developing a robust delivery system Characteristics of service operations Service package Supporting facility: the physical resources in place Facilitating goods: the material purchased or consumed by customers Information: exchange of information between the service organisation and customers Explicit services: the intrinsic and readily observable features of the service Implicit services: the additional (sometimes psychological) benefits associated with the service Agenda Characteristics of service operations Operational classification of services: high vs low-contact services Configuring service encounters Managing customer-introduced variability Service blueprinting Operational classification of services Customer contact The physical presence of the customer in the service process High and low degree of customer contact Service systems with a high degree of customer contact are more difficult to control and to streamline In high-contact service systems, customers can affect the time of demand, the exact nature of the service, as well as the service quality Operational classification of services High-contact system Low-contact system Design decision (e.g. branch office) (e.g. check processing centre) Operations may be located Operations must be near the Facility location near supply, transport, or customer labour The facility should meet the The facility should focus on Facility layout customer’s needs and expectations production efficiency Employees are an integral part of Employees need Workforce skills the service product and must be technical/administrative skills able to interact well with customers See reading (p. 204) => 11 major differences between high-contact and low-contact service systems Agenda Characteristics of service operations Operational classification of services: high vs low-contact services Configuring service encounters Managing customer-introduced variability Service blueprinting Configuring service encounters The service design matrix Configuring service encounters Configuring service encounters 3 contrasting service encounter designs The production line approach => Service delivery treated like a manufacturing process (e.g. McDonald’s) The self-service approach => Customers take a greater role in the production of the service (e.g. ATMs, self-checkouts, salad bars) The personal attention approach => Processes designed to build a relationship with customers (e.g. luxury hotels) Agenda Characteristics of service operations Operational classification of services: high vs low-contact services Configuring service encounters Managing customer-introduced variability Service blueprinting Managing customer-introduced variability 5 types of variability introduced into the service delivery system by customers and creating operational challenges Arrival variability Request variability Capability variability Effort variability Subjective preference variability Managing customer-introduced variability 4 approaches to dealing with service variability Classic accommodation: increasing capacity (e.g. the number of employees) and/or the level of skills Classic reduction: limiting the number of service options Low-cost accommodation: automating tasks and introducing self- service options Uncompromised reduction: limiting variability by targeting specific customers and/or inducing demand Managing customer-introduced variability 4 approaches to dealing with service variability High Uncompromised reduction Classic accommodation Low-cost accommodation Quality of service/ experience Classic reduction Low Low High Cost of service (Frei, 2006) Managing customer-introduced variability 4 approaches to dealing with service variability Classic Low-cost Uncompromised Classic reduction accommodation accommodation reduction Introduce a self Offer a Make sure plenty of Limit check-in times check-in kiosk (for complementary Arrival employees are on between 2pm and customers arriving drink to customers hand (day and night) 6pm late or at night) arriving before 6pm Request Capability Effort See reading (p. 208) for more detail Subjective preference Agenda Characteristics of service operations Operational classification of services: high vs low-contact services Configuring service encounters Managing customer-introduced variability Service blueprinting Service blueprinting A service blueprint: the flowchart of a service operation Depicts the whole service process and the people involved The steps in the service delivery process The actions of customers The actions of employees The interactions between customers and employees Service blueprinting Customer actions Line of customer interaction Frontline employee actions Line of visibility Backstage employee actions Line of internal interaction Support processes Service blueprinting Blueprint of a car service operation Service blueprinting Benefits of blueprinting Visualising the process flow from different perspectives Considering service delivery as a complex and integrated process Identifying potential failures and bottlenecks in the process Analysing, redesigning and improving processes Service blueprinting Front stage Physical facilities Effective service delivery (focused on customers) Flexibility Line of visibility Backstage Efficient service delivery Tight scheduling (focused on operations) Higher processing volumes Service blueprinting Identifying service failures and fail-safing processes: poka-yokes The approach originates from the Japanese manufacturing industry Mistake-proofing technique used to eliminate errors and defects, and to ensure product quality 3 Ts Task to be performed => Has the task been performed properly? Treatment accorded to the customer => Was the interaction with the customer appropriate? Tangible experience of the customer => Do the physical elements of the service facility provide the right impression to customers? Service blueprinting Identifying service failures and fail-safing processes: poka-yokes Service blueprinting Identifying service failures and fail-safing processes: poka-yokes Service blueprinting Identifying service failures and fail-safing processes: poka-yokes Key terms/concepts Characteristics of services Classic accommodation (Intangibility, Inseparability, Classic reduction Perishability, Heterogeneity) Low-cost accommodation The 9 characteristics of service operations Uncompromised reduction Customer self-service Service blueprint Service package Line of visibility High-contact / low-contact services Front stage / backstage service operations Service design matrix Failure points in the service delivery Service variability Poka-yokes Types of customer-introduced variability Questions? © Notice of copyright This screen show contains copyrighted material. Its use is restricted to study purposes at the University of Waikato. Any other use may be an infringement of copyright.