LEEA Academy Overhead Travelling Cranes - Step Notes PDF
Document Details
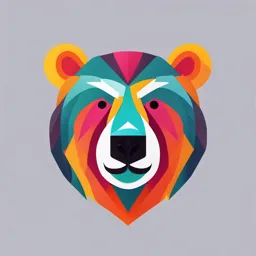
Uploaded by PromisingJadeite8923
null
2017
LEEA Academy
Tags
Related
- COSH 413 - Construction Occupational Safety & Health - Crane Safety PDF
- Overhead Travelling Cranes - Step Notes (PDF) - Apr 2017
- LEEA Academy Overhead Travelling Cranes - Step Notes (PDF) Apr 2017
- Automobile Engineering - DMX5208 PDF
- IRSOD_INCORPORATED Workshop & Station Machinery PDF
- Weaving Mechanisms PDF
Summary
This document provides step-by-step notes on overhead traveling cranes, focusing on duty classification, safety procedures, and testing considerations. It covers various aspects of crane design and operation, including factors like operating cycles, load spectrum, and testing procedures.
Full Transcript
Notes: 154 ©LEEA Academy Overhead Travelling Cranes – Step Notes – Apr 2017 – v1.3 16. Duty Classification Introduction During module 2 of this course, we looked at the various standards that are applicable to overhead travelling cran...
Notes: 154 ©LEEA Academy Overhead Travelling Cranes – Step Notes – Apr 2017 – v1.3 16. Duty Classification Introduction During module 2 of this course, we looked at the various standards that are applicable to overhead travelling cranes, whether they may be for design, gantries, thorough examination, or indeed ‘classification’. Two particular standards were listed for crane classification: 1. BS ISO 12482: Cranes – Monitoring for Crane Design Working Period (Duty Holder/Owner) Principally for the use of the crane owner/duty holder to monitor crane ‘design working period’. The standard specifies a method for monitoring, during long-term operation, the actual duty of the crane, and a means of comparing this to the original design duty which was specified through classification. 2. ISO 4301-1: Cranes and Lifting Appliances – Classification This standard establishes a general classification of cranes based on the number of operating cycles to be carried out during the expected life of the crane and a load spectrum factor which represents a nominal state of loading. Duty Classification Cranes are designed for a finite lifetime duty and this is not principally related to calendar working time. Typical operational periods are between 10 and 20 years but specific crane classification can be relative to a particular use, e.g. 5 to 10 years special use or 30+ years for a long term investment. 155 There are essentially two types (or uses) of classification: 1. The appliance as a whole (contractual and technical purposes) Classification agreed between the purchaser and the manufacturer is only provided for the overall classification of the crane as a whole and is intended for contractual and technical reference purposes, not design purposes. 2. Classification for design purposes Allows a designer to analyse the design and verify it is capable of achieving the desired life under the expected conditions of service. Notes: ©LEEA Academy Overhead Travelling Cranes – Step Notes – Apr 2017 – v1.3 Group Classification of the ‘whole crane’ Two factors are used to decide which group a crane belongs to: 1. Class of utilisation 2. State of loading Class of Utilisation Based on the users expected number of ‘operating cycles’ over the duration of the crane life. 1 x operating cycle commences when a load is ready for hoisting and ends at the moment when it is ready to hoist the next load Total operating cycles in the life of the crane is usually determined from: o Total operating hours per day And o Number of cycles per hour The overall number of operating cycles is the total of all operating cycles during the specified life of the crane ISO 4301 – Class of Utilisation of Cranes 156 We can clearly see from the previous ‘Class of Utilisation’ table from ISO 4301-1 that a class U4 crane would be undertake a maximum of 2.5 x 10⁵ operating cycles in it’s expected lifetime. i.e. 2.5 x 10⁵ = 2.5 x (10x10x10x10x10) = 2.5 x 100,000 = 250,000 operating cycles ©LEEA Academy Overhead Travelling Cranes – Step Notes – Apr 2017 – v1.3 Notes: State of Loading (Load Spectrum) This element of crane classification looks at how many times a load of a particular weight is lifted, relative to the rated capacity of the crane. E.g. 1. A 10t WLL overhead crane may lift 2.5t for 80% of its total number of operating cycles per day, and 10t for the remaining 20% 2. A 5t WLL crane may lift near to full load for 70% of its daily operating cycles and less than 1t for the 157 remaining 30% The following table provides a general view of how the state of loading (load spectrum) of a crane is established, based upon the magnitude of loads and the number of times these will be lifted over the crane’s design life: Once the class of utilisation and the state of loading have been established, the overall classification of the crane as a whole can be determined by using the following table: ©LEEA Academy Overhead Travelling Cranes – Step Notes – Apr 2017 – v1.3 Notes: Group Classification of a Mechanism as a Whole (for design purposes) We will now look at the class of utilization of a mechanism. This is characterized by the assumed total duration of use in hours. This is usually obtained from the assumed average daily utilization time in hours, 158 the number of working days per year, and the number of years of expected service: The total duration of use (hours) are theoretical values only, which only provide a basis for the design of parts of mechanisms for which the utilization time is a criteria for the choice of the part (e.g. bearings, gears and shafts). The hours stated are not considered as any guarantee of service life for a mechanism. When we now consider the state of loading for the mechanism, we are considering the extent of loading, whether that be maximum loadings or reduced loadings: ©LEEA Academy Overhead Travelling Cranes – Step Notes – Apr 2017 – v1.3 Once the class of utilisation and the state of loading have been established, the group classification to the design of specific mechanisms can be determined by using the following table: 159 Important Reminder It should also be noted that the initial section of the unit is written in a simplistic form that is intended to establish only some basic principles. The aim is to give those with little or no knowledge of the subject a basic understanding and to provide the basis for further study. This module will help examiners/inspectors whom have dealings with electrically powered lifting equipment to know the basic principles relating to duty classification and how this effects the overhead travelling crane during its service life. Notes: ©LEEA Academy Overhead Travelling Cranes – Step Notes – Apr 2017 – v1.3 17. Safety Essentials – Working on OTCs Safety Essentials: Working on Overhead Travelling Cranes There is no job so important and no service so urgent that we cannot take the time to perform our work safely and correctly! A Few Essential Rules Do not take shortcuts in the planning of safety for the work to be done Do not take risks 160 If your job cannot be done safely, your employer will not want you to do it o Always talk to your line manager if you have any concerns Report any unsafe conditions or working behaviour immediately Isolation of Energy – Basic Rules The basic rules are that there should be isolation from the power source (usually, but not exclusively, electrical energy) The isolator should be locked in position (for example by a padlock), and a sign should be used to indicate that inspection work is in progress Isolation requires use of devices that are specifically designed for this purpose; not devices such as key-lockable emergency stops or other types of switches that may be fitted to the machine Any stored energy (hydraulic or pneumatic power, for instance) should also be dissipated before the work starts If more than one examiner is involved in the work, each of them should lock off the power with their own padlock. Multi-padlock hasps can be used in such circumstances. Such isolation procedures can also be applied to locking off valves for services (such as steam) and material supplies ©LEEA Academy Overhead Travelling Cranes – Step Notes – Apr 2017 – v1.3 Before entering or working on the equipment, it is essential that the effectiveness of the isolation is verified by a suitably Competent Person Electrical Isolation Unqualified personnel should not perform any electrical examinations or testing of any kind on any electrical equipment associated with overhead travelling cranes unless they can demonstrate competency in electrical service and hazardous energy isolation, have been suitably and sufficiently trained in electrical safety, and authorised by their company management to perform such tasks. Unqualified personnel should not be allowed to perform any work on or near energised electrical equipment. 161 Accident Report “Two dock workers suffered injuries in a high voltage electric shock when they were trying to fix a crane. The maintenance worker was temporarily blinded – and is now scarred permanently - and both he and an electrician were burned. Two other men working on the job could also have suffered burns as a result and all four could easily have been killed. None of the men had received adequate training or been given sufficient information about the electricity supplies to the dockside cranes. All four workers were put at risk because their employer did not have procedures in place to ensure electrical work was carried out safely”. Source: http://www.hse.gov.uk/safemaintenance/experience.htm ©LEEA Academy Overhead Travelling Cranes – Step Notes – Apr 2017 – v1.3 Personnel Carrying Out Thorough Examinations BS7121-2-1 2012 (5) states: “It is essential that the in-service inspection and maintenance of cranes is always carried out by personnel who have been assessed by their employer as competent and have adequate training and information to carry out the work required.” LOLER also requires that thorough examinations are carried out by Competent Persons. “Competent Persons should have the necessary attributes, competencies, knowledge and experience to enable them to carry out effective thorough examinations of cranes. The nature and extent of these will depend on the purpose of the examination to be undertaken, the complexity of the cranes to be examined and the consequences of failure of those cranes. It is essential that such persons have adequate training, information and independence to carry out the work required” Note: Module 1 of this OTC Advanced Programme provides the definition of a Competent Person. Attributes of the Competent Person Competent Persons should: Be physically fit for the tasks they are to undertake Have adequate eyesight (with correction if needed) Be comfortable working at height, over water or in a confined space (if required) 162 Have a responsible attitude Be able to communicate clearly with other personnel in the location where thorough examination is taking place, including the need to take the crane out of service if it is unsafe to use Be able to demonstrate adequate literacy and numeracy; Be aware of their own limitations in knowledge and experience Source: BS7121:2-2012 5.3.2 Competencies of the Competent Person Competent Persons should be: Fully conversant with the machinery they are required to examine and its hazards, including operation necessary for thorough examination activities Properly instructed and trained Familiar with the procedures and precautions required for safe work at height, over water or in a confined space (where required) Have a responsible attitude Fully conversant with the appropriate sections of the manufacturer’s instruction manual Familiar with the use of permit to work systems where they are required by the safe system of work, and able to operate them correctly Familiar with site specific safety requirements (e.g. manufacturing, construction, process plant, nuclear, docks, airports, railways) ©LEEA Academy Overhead Travelling Cranes – Step Notes – Apr 2017 – v1.3 Trained and competent in the selection, pre-use inspection and correct use of their personal protective equipment Source: BS7121:2-2012 5.3.2 Knowledge Base of the Competent Person Competent Persons should have: An understanding of the applicable crane design standards and codes of practice for the selection and use of the relevant cranes, together with the applicable examination criteria An understanding of the safety rules and associated codes of practice that are applicable to the relevant cranes An understanding of the inspection and maintenance requirements of cranes Knowledge of appropriate test procedures which may be employed and the interpretation and limitations of those techniques An understanding of drawings and manufacturing literature relevant to the cranes to be examined Knowledge of the materials and techniques used in the manufacture and assembly of the type of cranes to be examined Source: BS7121:2-2012 5.3.4 Practical Skills of the Competent Person Competent Persons should have: 163 Be capable of detecting defects or weaknesses in cranes which could compromise the safety of the crane Have sufficient knowledge and experience to assess the importance of defects or weaknesses in the crane and identify what actions need to be taken in order to rectify them. In particular they should be able to: o Determine whether the crane is operating as intended o Specify the appropriate time-scales within which identified defects or weaknesses need to be rectified o Determine whether defects identified in the previous report of thorough examination have received attention o Determine whether all safety devices are functioning correctly o Check whether warning notices are correctly fixed and legible, and where necessary specify any limitations on the use of the crane o Witness any testing required as part of the thorough examination and evaluate the results o Report on the findings of the thorough examination Source: BS7121:2-2012 5.3.5 Assessment of Competence Employers should determine through a formally documented assessment process the competence of each individual person, both existing employees and new entrants, based on the attributes, competencies, knowledge and skills listed in 5.3.2 to 5.3.5. A shortfall in attainment level does not necessarily preclude ©LEEA Academy Overhead Travelling Cranes – Step Notes – Apr 2017 – v1.3 employment in this role but it is essential that such shortfalls are addressed before the person is allowed to carry out unsupervised thorough examinations of cranes. All Competent Persons should be assessed on appointment, again within their first 12 months, and at regular intervals (not exceeding 4 years) thereafter. Assessment should form part of any training. *Source: BS7121:2-2012 5.3.9 Training Records A comprehensive individual training record should be established for all personnel carrying out thorough examinations. This should be updated as training is undertaken and as a minimum should include: When the training, refresher training, assessment or re-assessment took place Where the training took place The scope of the training, including types and models of crane The duration of the training The outcome of the training Who delivered the training When refresher training is required Source: BS7121:2-2012 5.3.10 Continual Professional Development Continuing professional development is a joint responsibility between the Competent Person and their 164 employer. The employer should maintain a CPD record for each Competent Person. The record should include details of how CPD is being achieved and should include for example: Specific training towards enhancements/additions to competency Familiarization/re-familiarization, ongoing training and mentoring Any alterations and/or withdrawals of competency Enhancements to qualifications Membership of professional bodies/institutions Attendance at seminars and refresher training courses Visits to manufacturers and trade shows Source: BS7121:2-2012 5.3.11 Maintenance and Thorough Examination Selection of the Competent Person It is essential that the Competent Person undertaking the thorough examination of a crane has not been involved in the maintenance of the crane. This also applies to the inspection of cranes under MCA LOLER 2006:6 Regulation 12(1). ©LEEA Academy Overhead Travelling Cranes – Step Notes – Apr 2017 – v1.3 Preparation for the Thorough Examination The crane should be checked to determine whether it is clean enough not to conceal the structure or mechanisms to an extent that would prevent an effective examination. If necessary, the crane should be cleaned as required The crane should be positioned in a suitable area to enable the thorough examination to be undertaken safely Additional means of safe access should also be provided as required by the Competent Person, e.g. scaffolding, working platforms or mobile elevating work platforms These recommendations also apply to an inspection made under MCA LOLER 2006:6 Regulation 12(1). Note: Attention is drawn to the Work at Height Regulations 2005 (as amended). Access Employers and Competent Persons should ensure that procedures are in place to enable the Competent Person to access all relevant parts as and when required Some parts might be accessible by using permanent facilities such as access ladders to the gantry combined with gantry and cross-bridge walkways Such facilities do not always provide access to all parts, and the Competent Person might need to use personal protective equipment (PPE) to protect against the risk of a fall 165 Use of PPE requires suitable anchor points and a recovery plan in the event that a fall occurs Temporary access facilities, such as a mobile elevating work platform (MEWP) or scaffolding, might be required to reach some parts Such temporary facilities usually stand on the ground or floor of a building and require a suitable surface, space for access, space to operate in and time to deploy The Competent Persons who deploy and use such facilities should be trained for the purpose, and the equipment used should be in a serviceable condition Preparation for the Thorough Examination If the local lighting is not adequate for examination purposes it should be supplemented by portable lighting The identification and rated capacity marked on the crane should be checked against the records, for example the test certificate, declaration of conformity, the manufacturer’s instructions for use and the report of the last thorough examination The crane should be made safe by isolating and locking-off the power supply when necessary and reinstating it as appropriate The Competent Person carrying out the thorough examination should determine if there is any history of defects or malfunctions, and whether any repairs, alterations or additions have been ©LEEA Academy Overhead Travelling Cranes – Step Notes – Apr 2017 – v1.3 made. The last report of thorough examination and in-service inspection reports should be consulted Where it is not possible to ascertain the condition of hidden mechanism parts, for example ropes, chains, sheaves or terminations, dismantling prior to thorough examination should carried out as required by the Competent Person Notes: Method Statements and Work Instructions Generic risk assessments will normally suffice Unusual or potentially hazardous tasks may require specific risk assessment Always follow a ‘Safe system of work’ Toolbox talk 166 o All team members are fully briefed o Focussed o Discuss the ‘job specific’ method statement o Briefings should be recorded o Unusual features of the job to be highlighted Notes: ©LEEA Academy Overhead Travelling Cranes – Step Notes – Apr 2017 – v1.3 Working Above Ground Level Hierarchy of Control Measures 1. Working Platforms (crane walkways etc.) 2. Scaffolding 3. MEWPs 4. Controlled Zones 5. Safety Nets and Air bags 6. Work Positioning 7. Horizontal and Vertical Lifelines 8. Fall Arrest Equipment Rescue Plan A Rescue Plan must be developed whenever fall-arrest systems are in use and when personnel may not be able to perform a self-rescue should a fall occur. Before requesting a Rescue Kit (which is the last resort) you must first consider whether ladders, stepladders, MEWPs, controlled decent devices or other equipment can be used to perform a rescue. 167 If all else fails, then a Rescue Kit should be utilised. Other Things to Consider for a Rescue Plan You must never rely upon the emergency services as a primary rescue plan What obstructions may be in the way of reaching a suspended worker? How will the rescue be assured within 10 minutes of the fall to minimise the risk of further injury or suspension trauma? How will the safety of the rescuers be assured as well as the suspended worker? What communications will be used between the suspended worker and the rescue team? Notes: ©LEEA Academy Overhead Travelling Cranes – Step Notes – Apr 2017 – v1.3 Monitor and Review Continuously monitor activities in all three dimensions of your surroundings! Additional hazards may be presented o Traffic, pedestrians etc. o Changes in production activity o Additional hazards presented Record your findings and change the risk assessment as necessary This may result in the requirement for additional control measures High Ambient Temperatures Where Applicable: Special attention and planning are required for inspecting cranes in hot areas. Due to the adverse environment, these cranes may not receive the inspection time they deserve. The temperature in certain applications/environments (coupled with seasonal high temperatures) may mean that on occasion, the crane structure may be hot, and gloves are recommended for manoeuvring on the structure during an inspection. Your risk assessment may identify reduced exposure time for the personnel working on the crane(s). Summary 168 In this module, we have looked at the various safety considerations that are to be incorporated into our risk assessments, method statements and review procedures to ensure that all examiners involved in work on overhead travelling cranes are afforded the highest level of protection from injury or fatality. Examiners of overhead travelling cranes should always make themselves familiar with any national regulations of the country in which they are operating. Failure to do so may lead to prosecution, due to breaches of the law. Notes: ©LEEA Academy Overhead Travelling Cranes – Step Notes – Apr 2017 – v1.3 18. Testing as Part of the Thorough Examination General All cranes and supporting structures should be overload tested before first use o In some circumstances, it might be necessary to treat them as separate entities, for example where a structure supports more than one crane The extent and magnitude of the testing should be clearly stated in the thorough examination report/test report Cranes and supporting structures should be overload tested after major repairs or modifications Overload Testing of Cranes Thorough Examination and Functional Testing Before overload testing, the crane and the part of the supporting structure within the test area should be thoroughly examined to determine whether it is in a safe state and condition to be overload tested The crane should be functionally tested without a load applied to determine whether the controls, switches, contactors, relays and other devices operate correctly The operation and correct adjustment of the brakes and limit switches should be checked and tests carried out to determine whether primary safety and emergency systems are operating correctly 169 Tested at Rated Capacity After the functional tests, the crane should be tested with a load equivalent to the rated capacity At the start of the test, the crane should be positioned over a supporting stanchion or column of the gantry or beneath the connection point of a suspended track, as appropriate, with the crab or hoist positioned adjacent to the end carriage With the crane in this position, provision should be made for measuring the deflection of the crane main girders at the centre span The load should then be raised until each tooth on the gearbox system has been subjected to the load o Lower the load to approximately 100/200mm from the floor o Leave the load in this position for 10 minutes o Check that the brake is holding Lift the load again from the suspended position by a further 200 mm to check the hoists ability to re-hoist ©LEEA Academy Overhead Travelling Cranes – Step Notes – Apr 2017 – v1.3 o Lower the load again to 100/200mm above the ground Travel the crab (trolley) to centre span of the crane o Measure the deflection o Lower the load to the ground to relieve the structure and then raise load again to ensure the amount of deflection is constant The maximum deflection of the main bridge with the crab and load at the centre of the bridge should not exceed 1/750 of the span Deflection Note: Cranes manufactured to BS 466:1984 have a maximum permissible deflection of 1/750 of the span Cranes manufactured to BS 466:1960 have a maximum permissible deflection of 1/900 of the span For cranes manufactured to BS EN 15011:2011, sub clause 5.2.2.5 of that standard specifies, ‘the elastic deformations of the crane structure shall not have a detrimental influence on the function of the crane.’ 170 Testing as Part of the Thorough Examination Overload Test The load should then be increased by 25% to form an overload test load and the overload test load should be hoisted until each tooth of the train of gears has been subjected to the overload o Lower the load to 100/200 mm above the ground o Leave the load in this position for 10 minutes o Check that the brake is holding Lift the load again from the suspended position by a further 200 mm to check the hoists ability to re-hoist o Lower the load again to 100/200mm above the ground During the overload test the crane should remain stable and structurally sound and the brakes on each motion should function effectively. The traverse and travel braking systems should also function effectively with the overload applied During the overload test the crane should be operated at speeds appropriate to the safe control of the load, for example the lowest speed possible for the crane ©LEEA Academy Overhead Travelling Cranes – Step Notes – Apr 2017 – v1.3 Testing of Cranes with 2 or more Hoists For cranes with two or more hoists, separate tests in accordance with ‘rated capacity’ and ‘overload test’ should be carried out for each hoist Where the use of more than one hoist at a time is permitted, all tests including the measurement of deflection should be carried out with all these hoists loaded simultaneously Post Testing Thorough Examination On completion of the tests, a further thorough examination of the crane should be carried out by the Competent Person Any overload protection devices should be reset and their correct operation checked 171 Structural Stresses Due to Loading ©LEEA Academy Overhead Travelling Cranes – Step Notes – Apr 2017 – v1.3 Collateral Damage What damage may have been caused? Structural Problems 172 Load Testing Supporting Structures Assessment and Thorough Examination Cranes can be supported in a variety of different ways. This could include a free-standing structure, or a gantry or track supported by the structure of the building or an engineering structure. Prior to the application of the test loads, the Competent Person should carry out a thorough examination of the structure to determine whether it is in a safe condition to be load tested. An unloaded crane should then be travelled the full length of the supporting structure to check the alignment. Note: BS ISO 12488-1 contains detailed information about the alignment of crane supporting structures. ©LEEA Academy Overhead Travelling Cranes – Step Notes – Apr 2017 – v1.3 General Testing should be carried out using the combination of loadings, cranes and crane positions that imposes the maximum loadings on the structure under test. This includes cranes in an adjacent bay. Test at Rated Capacity - Deflections For structures built in accordance with BS 449-2, the maximum deflection should not exceed 1/360 of the span. For structures built in accordance with BS 5950-1 or BS EN 1993-6, the maximum deflection should not exceed 1/600 of the span. BUT: Where do we place the crane on the gantry to measure deflection effectively? Maximum Bending Stresses and Shear Load of Gantry Girders For testing purposes, if the end carriage wheel centres are equal to, or more than half of the gantry girder span (L/2), then the maximum stress will occur with one wheel in the centre line of the girder. The maximum deflection will occur at the centre of the girder: 173 If the end carriage centres are less than half of the gantry girder span (L/2), then the maximum stress will occur when the end carriage centreline is offset from the girder centre line by measurement C/4: Maximum stress will occur at X and maximum deflection in the girder will occur at girder centreline L/2 Notes: ©LEEA Academy Overhead Travelling Cranes – Step Notes – Apr 2017 – v1.3 Testing Overload Test The overload test load on each crane should be that determined previously in this unit. Each crane involved should then lift the overload test load 100 mm to 200 mm above the ground. The load lifted by each crane should be traversed to the end of the crane bridge nearest the side of the structure being tested. The cranes should be travelled the full length of the structure in such relative positions as to impose the maximum combined loading. The procedure should be repeated for the other side of the structure. Post-test thorough examination of the supporting structure. On completion of the test, a further thorough examination of the supporting structure should be carried out by the Competent Person. Notes: 174 ©LEEA Academy Overhead Travelling Cranes – Step Notes – Apr 2017 – v1.3 19. The Thorough Examination Thorough Examination of Overhead Travelling Cranes and Supporting Structures LOLER 1998 Regulation 9 requires cranes and supporting structures to be thoroughly examined in the following circumstances: 1. Before being put into use for the first time, unless the crane is new and the owner has an EC Declaration of Conformity dated not more than 12 months prior to the crane being used for the first time 2. Where safety depends on the installation conditions: I. After installation and before being put into service for the first time II. After assembly and before being put into service at a new site or in a new location (see note 1) 3. Periodically whilst in service, at maximum intervals of 6 months for cranes that lift people and 12 months for cranes that lift goods only (see note 2) 4. After exceptional circumstances have occurred Note 1: Thorough examination does not apply to a portable gantry crane which is moved from one location to another to perform a lifting operation, is not fixed in position, and is operating within the scope of the current report of thorough examination. Note 2: These maximum intervals may be reduced to take into account environmental factors or the 175 general age and condition of the crane etc. Selection of the Competent Person The Competent Person carrying out the thorough examination must not have had any involvement with the maintenance of the crane. (BS7121:2-7 2012) Notes: ©LEEA Academy Overhead Travelling Cranes – Step Notes – Apr 2017 – v1.3 Scope of Thorough Examination Before Putting an OTC into use for the First Time The scope of the thorough examination should be put together by the Competent Person. During this process, the Competent Person should give due consideration to the likelihood of anything failing and the associated risks involved from such a failure The Competent Person should consider the age of the crane and any deterioration that may have taken place since it was manufactured. This could lead to increased risk in operation Scope of Thorough Examination Following Installation The scope of the thorough examination should be put together by the Competent Person. LOLER 176 requires that this scope ensures that the crane has been installed correctly and is safe to use The crane manufacturer’s instructions should have been followed during the installation o The crane should be checked and tested in accordance with the manufacturer’s instructions The Competent Person should ensure that the scope of the thorough examination is in proportion to the complexity of the crane and its installation o Previous thorough examination reports should be consulted and taken into consideration where applicable Scope of Periodic Thorough Examination The Competent Person carrying out a periodic thorough examination should work to a defined scope of thorough examination that has been drawn up specifically for the crane they are required to examine The scope should be made in advance of the examination o All parts should be identified and listed o Any required supplementary tests and reports should be detailed I. Requirements for witnessing of tests should be detailed o Details of NDT tests should be provided Note: The Competent Person carrying out the thorough examination may add to the defined scope but is not permitted to reduce it! ©LEEA Academy Overhead Travelling Cranes – Step Notes – Apr 2017 – v1.3 It is essential that the defined scope of thorough examination includes any dedicated ancillary equipment. Particular attention should be paid to wire ropes! The defined scope of thorough examination should, as a minimum, include operation of the crane through all the motions: Listen for any sounds that might indicate defects and observing any other malfunctions All components should be assessed against relevant criteria (original manufacturer’s instructions and guidelines and standards offer guidance here), taking into account the path of the load through the crane’s structure and mechanisms It is essential that the scope is risk based and takes into account the consequences of failure of the 177 crane o The examination should be undertaken in a systematic manner to ensure that all components and structures, including the supporting structures, are examined Note: Parts of the supporting structure which are solely for the support of the crane should be included in the scope of thorough examination. Parts of the supporting structure which are not solely for the support of the crane gantry or track are not included in the scope of thorough examination. Components to be Included in the Thorough Examination Note: The following list of components is not exhaustive. The scope of the thorough examination should identify all components on any specific crane. End carriage structures Long travel drive, wheels, axles, bearings and brakes Note: The following list of components is not exhaustive. The scope of the thorough examination should identify all components on any specific crane. ©LEEA Academy Overhead Travelling Cranes – Step Notes – Apr 2017 – v1.3 Bridge girders Crab structure Cross travel drive, wheels, axles, bearings and brakes Cross travel rails 178 Hoist mechanism including motor, brake, couplings, gearbox, drum and bearings Wire rope(s), their terminations and anchorages, guides, sheaves/pins, bearings, bottom block and hook(s) ©LEEA Academy Overhead Travelling Cranes – Step Notes – Apr 2017 – v1.3 Electrical control panel and wiring Operator cab and seating Operator controls, whether cab, pendant or cable-less Limit switches 179 Platforms and access ladders Supporting structures Notes: ©LEEA Academy Overhead Travelling Cranes – Step Notes – Apr 2017 – v1.3 Gantry beams, rails and fixings End stops and buffers Down-shop conductor system Assessment Criteria Alignment – within manufacturer’s tolerance 180 Corrosion – affecting strength or functionality Cracks – affecting strength or functionality Damage – affecting strength or functionality ©LEEA Academy Overhead Travelling Cranes – Step Notes – Apr 2017 – v1.3 Distortion – affecting strength or functionality Functionality – as intended by manufacturer Leaks – affecting strength, functionality and slips Lubrication – adequacy 181 Markings – presence, accuracy and condition Mode of operation – as intended by manufacturer Rope fit – as specified by manufacturer Rope reeving – as specified by manufacturer ©LEEA Academy Overhead Travelling Cranes – Step Notes – Apr 2017 – v1.3 Rope specification – as specified by manufacturer Rope condition Obstructions Security – attachment of components and sub-structures, fasteners, welds, etc. 182 Seizure – full or partial seizure of rotating components Tidiness – general housekeeping Wear – affecting strength or functionality ©LEEA Academy Overhead Travelling Cranes – Step Notes – Apr 2017 – v1.3 Periodic Thorough Examination Interval The statutory maximum intervals of 6 months and 12 months may be reduced to take into account environmental factors or the general age and condition of the crane, etc. o The decision to reduce the interval between thorough examinations may be made by the Competent Person, the crane owner or the crane user Reasons for reduction of the interval between thorough examinations include the following: o If the crane frequently works above or near people o If the crane might be used for lifting of persons in exceptional circumstances, including rescue, even if it is not initially planned o To take into account the intensity of use of the crane and the environment in which it is used o Following a review by the Competent Person of the in-service lift plan (risk assessment, method statement and schedule of lifts) to ascertain the likely load spectrum and frequency of use of the crane Thorough Examination After Exceptional Circumstances 183 Examples of ‘exceptional circumstances’ would include: Use in very arduous conditions Failure of a structural component Collision Overload Subjected to extreme weather conditions in excess of design specifications It is a requirement of LOLER that if an overhead crane is subject to and exceptional circumstance, it is to be removed from service and a thorough examination is to be carried out. The Competent Person will then decided if the crane can be returned to service. The scope of the thorough examination should be proportional to the nature of the exceptional circumstances and the extent of any repairs, and should take into account the reports of previous thorough examinations, where applicable. Notes: ©LEEA Academy Overhead Travelling Cranes – Step Notes – Apr 2017 – v1.3 Scope of Periodic Thorough Examination The Competent Person who prepared the scope of thorough examination should review it periodically Consider any changes of use – increased productivity, heavier loading state, etc. Particulars from previous thorough examination reports may indicate particular areas for closer inspection Results of supplementary testing, maintenance and NDT activity A copy of the thorough examination scope should be available in the crane maintenance/history file Notes: 184 ©LEEA Academy Overhead Travelling Cranes – Step Notes – Apr 2017 – v1.3 20. Gantry Alignment Crane gantries will generally be constructed as ‘top running’ or ‘under-slung’. Top running gantries are supported in various ways. The latticed stanchion shown below tends to provide a lighter and more rigid structure since the transverse loading at the track level are all virtually transmitted through a very stiff column to the foundations. The method of gantry support shown below, although cheaper to produce, could have problems of fatigue with the cantilever brackets if the crane is in constant use. 185 The support steelwork shown in the illustration below provides direct support for gantry girders, additional stiffness and no tie bars are required. ©LEEA Academy Overhead Travelling Cranes – Step Notes – Apr 2017 – v1.3 After a number of years, gantry installations can suffer from what is known as ‘settlement’ which can affect the track levels and span. This is caused by the settling of the building foundations. Serious misalignment of a crane track will cause the crane to bind and bias to one side of the track rather than float. The immediate effect is to cause rapid wear on the crane runner flanges reducing their working life, often from years to months. Misalignment will often be found to occur only in certain areas when the crane lifts continually heavy loads, for example, a loading bay when the loads are all concentrated before they are dispersed to various parts of the building. Free Standing Crane Gantries If a building has not been designed to support a crane gantry then the gantry and stanchion may be totally free standing so that no load is transmitted to the building structure, (See Fig. 4 below). The illustration below shows three methods of making gantry columns. Types A and B are braced and therefore are very stiff. Type C, which is usually an edge on universal beam or column, are normally for lightly loaded light duty cranes. The Tester and Examiner will find that with rapid reversals of the crab unit type C will tend to resonate. With type C columns, down-shop surge bracings will be required. 186 Gantry Girders Generally manufactured from universal beams the girder will sit on top of the column cap with a packing allowance. The girder web should be laterally supported to provide a rigid connection at the cap. If two beams are joined at the cap they must be properly spliced with splice plates either side. Note that the beam section used for the column is extended past the capping plate to support lateral bracing. ©LEEA Academy Overhead Travelling Cranes – Step Notes – Apr 2017 – v1.3 Bridge Rails Depending on the duty, the bridge rail will have a profile similar to one of those shown below, but more often than not for light duties this will be square bar. These rails are normally fixed by intermittent welding and if not welded with the rail securely clamped to the beam weld, cracking will occur in service. 187 It is normal to offset the rail joint from the girder splice either bolting the overlap or welding on site. A 45° scarf joint is preferred thus avoiding point load contact at the join: ©LEEA Academy Overhead Travelling Cranes – Step Notes – Apr 2017 – v1.3 Gantry Rail Clips Gantry Foundations Foundation design is the responsibility of the Civil Engineer. He would be provided with foundation bolts 188 and a template to set their position. He will be informed what loadings his foundation will be required to take. The steel erector will then erect on the prepared foundations: With set in holding down bolts, these are cast into pockets which allow them to float. Once the erector has set out his stanchions, lining and levelling the caps, the stanchion bases are grouted. When the grouting is set, loose bolts can be tightened up and the erection completed. The crane and gantry will be tested whilst the foundation bolts are exposed so that they may be checked after testing. Grouted Anchors Some foundations anchors are provided by the civil engineers set into cones, allowing an amount of movement at the top of the anchors in order that they align with the column fixing holes. Once the column in place, a non-shrink grout is poured into the foundation to set the anchors in place. ©LEEA Academy Overhead Travelling Cranes – Step Notes – Apr 2017 – v1.3 Gantry Alignment When considering alignment of the crane supporting structure (gantry) the Competent Person should refer to the manufacturer’s specifications for crane running tolerances. In the absence of such information, reference can be sought from BS466 and ISO12488, depending on the standard to which the structure was designed. For in-service overhead cranes, it is likely that over a period of time the gantry will move; the original tolerances will then be exceeded. This can be caused by settlement of the structure or general vibrations and stresses resultant from the crane movements. The types of gantry alignment issues that are commonly found are: Level differences between the gantry rail heights Span differences between the gantry rails (parallel running) Line deviation of individual gantry rails Inclination of tracks in the vertical position Notes: 189 Gantry Levels Out of Tolerance ©LEEA Academy Overhead Travelling Cranes – Step Notes – Apr 2017 – v1.3 Gantry Rail Line Problem Possible Span and/or Line Problem 190 Notes: ©LEEA Academy Overhead Travelling Cranes – Step Notes – Apr 2017 – v1.3 Gantry Tolerances BS 466 and ISO 12488-1 specify the dimensional and geometrical tolerances of tracks for top running and under-slung cranes. BS 466 lists standard tolerances for all cranes, whereas ISO12488-1 has varied tolerances depending on the crane classification. In the absence of manufacturers’ specifications, the classification of a crane, as stated in ISO 12488-1 can be calculated as follows: The classification of the long travel drive mechanism (from ISO 4301-1) will provide the amount of service hours (S) L (Km travelled in crane life) = service hours (S) multiplied by the travel speed x 60 Example: ISO 12488-1 Tolerances - M5 Duty Crane Service hours (6,300 hours) x 32 metres/min x 60 = 12096 Km, therefore as per the table below, it would be in tolerance Class 2 and have a span tolerance of +/- 5mm. ISO 12488-1 Tolerances 191 BS 466 Tolerances ©LEEA Academy Overhead Travelling Cranes – Step Notes – Apr 2017 – v1.3 BS 466 and ISO 12488 Tolerances BS 466 Tolerances The tolerance on span should be as follows: ∆S ≤ 3mm where S < 15m ∆S ≤ 3mm + 0.25 (S 15)mm where S > 15m 192 ∆S Max = 15mm Misalignment of track running surfaces in the vertical plane Δ H ≤ 0.001S Δ H Max = 10mm Tolerances on track width under-slung only Δ W = 0.025W Track Straightness For the total length of track, the maximum lateral deviation from the straight line mean datum should not exceed 10mm. Local lateral deviation at any point of the track should not be greater than L/2000, measured over a length L of not less than 2m on a line parallel to the straight line mean datum. ©LEEA Academy Overhead Travelling Cranes – Step Notes – Apr 2017 – v1.3 Permissible Deviation in the Vertical Plane For the total length of the track, the maximum vertical deviation from the theoretical datum line should not exceed 10mm. The theoretical datum line may be the true horizontal line or a theoretical camber line. Local vertical deviation at any point of the track should not be greater than L/2000, measured over a length L of not less than 2m on a line parallel to theoretical datum. Running Surface Permissible Transverse Inclination from the Horizontal Datum Position 193 Notes: ©LEEA Academy Overhead Travelling Cranes – Step Notes – Apr 2017 – v1.3 Measurement of Crane Tracks When measuring crane tracks, calibrated steel measuring tapes should be used. It is important that the readings obtained are corrected to allow for sag in the tape and for temperature variation. All track measurements for a particular crane should be made with the same measuring tape and the same applied tension force. Gantry and Crane Surveys We have previously noted that the major cause of wear on crane wheels and tracks is misalignment. This could be misalignment of the track or misalignment of the crane. Check crane against end stops until buffers are touching, run crane back along track and come back to end stops. Should buffers not both be touching then the crane or buffers are out of line, but in any case this would suggest movement of the bridge girder connections. 194 Gantry Bridge Survey A crane bridge can be checked for serious misalignment whilst on the track, it is not easy and requires accurate measurements. The following checks should be made to establish any serious misalignment: 1. Check end carriages for parallelism 2. Check crane wheels for diameter and flange wear 3. Check crane wheels alignment in end carriages 4. Check crane wheel diagonals, i.e. from centre line of tread plumb down to rail, if not plumb down from axles 5. Check for issues with long travel drive and/or braking mechanisms If the crane appears reasonable the gantry should be checked. ©LEEA Academy Overhead Travelling Cranes – Step Notes – Apr 2017 – v1.3 Notes: Line and Level Surveys The Competent Person may be able to look along a crane track and detect serious misalignment. A line and level survey would then be required to decide what remedial action will be necessary. Line Check 1. Working from a datum point, e.g. a string line stretched the length of the gantry, the horizontal variations of the track would be measured and tabulated using numbered stanchions for reference 195 2. Using a steel tape and tension gauge, the span of the tracks could be measured at the numbered stanchion positions 3. The design office would lay those dimensions out as a drawing using an exaggerated scale for the track variation Level Check Again working from a datum level, using either a dumpy level or some other means, deviations from the datum level would be noted at the stanchion positions for both tracks. ©LEEA Academy Overhead Travelling Cranes – Step Notes – Apr 2017 – v1.3 Line and Level Drawings This drawing would show deviation in lines and levels and allow a decision to be made as to how best remedial action could be taken. By adjusting the datum lines it may be possible to reduce the amount of remedial work required. Great care must be taken to ensure end clearances are maintained between crane and steelwork. Notes: 196 Levelling Accurate levelling is far more difficult to achieve since we need to measure from an imaginary line. The traditional method is the dumpy or automatic optical level used in conjunction with a staff. ©LEEA Academy Overhead Travelling Cranes – Step Notes – Apr 2017 – v1.3 Line and Levelling Positioning a dumpy (optical level) for sighting gantry rails will often need improvisation. Engineers tend to make up their own attachments for clamping to gantry rails etc. The level is set up using a built-in bubble, similar to a spirit level except the glass is spherical, with a circular reticule thus providing a 360° level. The optical level, once set up, provides our datum from which variations can be calculated as previously explained. Laser Levelling A more recent innovation is the laser leveller. Power operated, the laser leveller will automatically plumb itself. 197 The laser beam is then rotated and becomes a continuous horizontal reference until switched off. Having set the laser the engineer can walk to where he wishes to measure and take a reading off the staff which is power operated and automatically seeks out the laser beam. ©LEEA Academy Overhead Travelling Cranes – Step Notes – Apr 2017 – v1.3 Training Operative training for all the equipment covered in these step notes should always take the manufacturer’s information and instructions for use into account. 198 We would be grateful for your feedback regarding these Step Notes, after completing this training course. Please make your comments known to us – you can use the note box below to list anything you would like to bring to our attention. We value your views and will use your comments to help our continual improvement of our learning and development materials. Thank you in advance for your participation. Notes: ©LEEA Academy Overhead Travelling Cranes – Step Notes – Apr 2017 – v1.3 Andrew Wright LEEA Learning and Development Manager Step Notes - feedback to LEEA: 199 ©LEEA Academy Overhead Travelling Cranes – Step Notes – Apr 2017 – v1.3