LEEA Academy Overhead Travelling Cranes PDF
Document Details
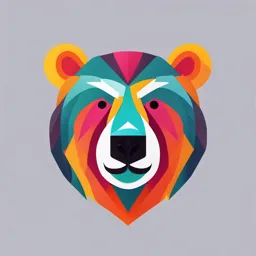
Uploaded by PromisingJadeite8923
2017
LEEA Academy
Tags
Summary
This document is a set of step notes for an advanced training course on overhead travelling cranes, taught by LEEA Academy. The document discusses important aspects of safety and compliance with regulations relating to the use of cranes. Topics covered include legislation, standards for overhead cranes, and lifting media.
Full Transcript
Developing Professionals for the Lifting Equipment Industry ©LEEA Academy Overhead Travelling Cranes – Step Notes – Mar 2017 – v1.3 Overhead Travelling Cranes Advanced Programme 2 Training Course Step...
Developing Professionals for the Lifting Equipment Industry ©LEEA Academy Overhead Travelling Cranes – Step Notes – Mar 2017 – v1.3 Overhead Travelling Cranes Advanced Programme 2 Training Course Step Notes ©LEEA Academy Overhead Travelling Cranes – Step Notes – Apr 2017 – v1.3 LEEA Learning and Development Agreement In the interests of all parties and to ensure the successful achievement of the LEEA Overhead Travelling Cranes Advanced Programme, the following arrangements are to be confirmed: Student: I agree to: Follow the instructions of my LEEA training facilitator at all times Follow all rules and procedures regarding health and safety matters whilst on site Respect the tidiness and cleanliness of training areas and rest area facilities Notify my LEEA training facilitator immediately if I have any concerns Inform my LEEA training facilitator of any learning difficulties at the soonest opportunity (this may be done privately between you and your LEEA training facilitator) Keep to agreed session times and return from rest breaks and lunchtime periods in a timely fashion Keep my mobile phone on ‘silent’ for the duration of all training sessions and to leave the class if I have to make or receive an urgent call, for the benefit of my fellow students Provide feedback to the LEEA facilitator regarding the training I have received Respect the opinions of my fellow students and to actively engage in group discussion Strictly adhere to the rules regarding LEEA Assessments Signed __________________________________________________________________ 3 Date __________________________________________________________________ LEEA Training Facilitator I agree to: Safeguard the health, safety and welfare of my students throughout the training programme Provide my students with quality training, maintaining the highest of professional standards throughout Maintain confidentiality for all students at all times Provide regular feedback to students on their progress, identifying areas which may need additional study Keep appropriate records of any assessments conducted Ensure that all students are able to discuss any issues or concerns which may arise during the training course Signed __________________________________________________________________ Date __________________________________________________________________ ©LEEA Academy Overhead Travelling Cranes – Step Notes – Apr 2017 – v1.3 Disclaimer These Step Notes are a useful and authoritative source of information for the LEEA OTC Advanced Programme student. Whilst every effort has been made to achieve the highest degree of accuracy in the generation of the data and information supplied, ultimate responsibility remains with the student and their employer to ensure that current legal requirements are followed. First Edition.........................Revised December 2016 © LEEA 2016. All rights reserved. No part of this publication may be reproduced, stored in a retrieval system or transmitted in any form or by any means, without the prior written permission of the Lifting Equipment Engineers Association. Contents CONTENTS 4 11. POWER FEED SYSTEMS 107 1. LEGISLATION 5 12. MOTION LIMIT SWITCHES 122 4 2. STANDARDS 27 13. OVERLOAD DEVICES 127 3. LIFTING MEDIA – LOAD CHAIN 30 14. BRAKING SYSTEMS 135 4. LIFTING MEDIA – WIRE ROPE 37 15. ELECTRIC MOTORS AND VFDS 144 5. MATERIALS 63 16. DUTY CLASSIFICATION 155 6. CRANE CONSTRUCTION 68 17. SAFETY ESSENTIALS – WORKING ON OTCS 7. CRANE CONFIGURATION 70 160 8. END CARRIAGES 74 18. TESTING AS PART OF THE THOROUGH EXAMINATION 169 9. HOIST CONSTRUCTION 80 19. THE THOROUGH EXAMINATION 175 10. ROPE DRUMS AND PULLEYS 104 20. GANTRY ALIGNMENT 185 Digital Navigation If you are viewing this document electronically, you can navigate using the Contents table above. Click the heading to jump to that module. To return to the Contents, click the at top of each page ©LEEA Academy Overhead Travelling Cranes – Step Notes – Apr 2017 – v1.3 1. Legislation Moral, Legal and Financial Reasons for Health and Safety Legislation Employers have a moral responsibility to ensure appropriate working conditions are provided This is known as a common law duty of care Unsafe working conditions are likely to have an impact on production Loss of output leading to lowering of morale and motivation Loss of sales turnover and profitability Society and customer expectations of a company’s approach to managing safety - health and safety culture Negative public relations would have a damaging effect on any business Financial cost from loss of output: Fines Damages Legal costs Insurance Etc. The Legislative Framework Health and Safety at Work etc. Act 1974 (UK) 5 The act is general in nature There is no reference to specific articles or substances The act applies to all sectors Specific duties of care for: Manufacturers/suppliers of articles or substances Employers Employees The health and safety at work act (HSWA) is an enabling act for specific regulations Status in UK: legal requirement. International: adopted as best practice, and requested by LEEA member companies. Notes: The Main Purposes of the HSWA ©LEEA Academy Overhead Travelling Cranes – Step Notes – Apr 2017 – v1.3 The Health and Safety at Work Act covers nearly all occupations. It is designed to protect people at work including staff, visitors, contractors and members of the public. The HSWA supersedes nearly all of the previous health and safety laws in the UK. The main purposes of the Act are set out in section 1 as follows: To secure the health, safety and welfare of persons at work To protect other people from hazards arising from work To control the keeping and use of dangerous substances and materials, including explosives and highly flammable materials To control the emission of noxious substances from certain premises It sets out a framework of general duties, primarily on employers, but also on employees and the controllers of premises, and on designers, manufacturers, importers and suppliers in relation to articles and substances used at work. Regulations from the HSWA Regulations are one form of delegated legislation made possible by section 15 of HSWA which gives powers to the secretary of state (UK) to make regulations for matters concerned with health and safety at work. Regulations are not acts of Parliament but do have the support of the law and therefore must be complied with. 6 Regulations are increasingly drafted by reference to European Directives (these will be discussed at a later stage in this module). There are many sets of regulations applying to health and safety. Some apply to all places of work and others are specific to particular industries, operations, substances, materials or premises. Here are a couple examples of such regulations: The Manual Handling Operations Regulations 1992 The Control of Substances Hazardous to Health Regulations 2002 Health and Safety at Work Act Section 2 Duties of the Employer “Duty to ensure so far as is reasonably practicable, the health, safety and welfare at work of all his/her employees” Safe plant and systems of work Safe use, handling, storage and transportation of articles and substances Information, instruction, training and adequate supervision Safe place of work and a safe means of access and egress ©LEEA Academy Overhead Travelling Cranes – Step Notes – Apr 2017 – v1.3 Safe working environment and adequate welfare facilities Health and Safety at Work Act Section 6 Duties of Designers, Manufacturers, Importers and Suppliers To ensure, so far as is reasonably practicable, that articles they design, construct, make, import, supply etc. are safe and without risk to health at all times e.g. when it is being set up, cleaned, used or maintained by someone at work To carry out or arrange such testing and examination necessary to perform the duties above To ensure that those supplying the item have adequate information about its designed and tested use. This includes essential conditions for dismantling and disposal Take steps to ensure, so far as is reasonably practicable, that those supplied are given updated information where it becomes known that the item gives rise to serious risk to health and safety Health and Safety at Work Act Section 7 Duties of the Employees States that employees must not endanger themselves, or others, by their acts or omissions Also, they must co-operate with their employers; as long as this does not lead to an increased risk to health and safety, or is an illegal act; so that employers can comply with their statutory duties 7 This makes responsibility for safety a joint employer/employee effort Management of Health and Safety at Work Regulations 1992 (Revised 1999) In addition to section 2 (2) c of the HSWA, the Management of Health and Safety at Work Regulations 1999 (MHSWR) require employers to ensure the effective planning, organisation, control, monitoring and review of preventive and protective measures. All these arrangements must be recorded and made known to employees. This is usually accomplished by the design of a company health and safety policy. MHSWR underlines the requirements for employers to provide instruction and training Employers must ensure that their personnel are properly trained to use any equipment necessary in the course of their work, but the regulations also place an obligation on employees to undergo such training and follow the instructions given by their employer Operatives are required to only use equipment for which they are trained and to use it in the manner and for the purpose for which they have been trained ©LEEA Academy Overhead Travelling Cranes – Step Notes – Apr 2017 – v1.3 LEEA Definition of a Competent Person The term ‘Competent Person’ has long been used in legislation. Current legislation uses it for a variety of duties to describe a person with the necessary knowledge, experience, training, skill and ability to perform the specific duty to which the requirement refers. There can therefore be several ‘Competent Persons’, each with their own duties and responsibilities, i.e. competent for the purpose. The term has never been fully defined in law, but for the purpose of thoroughly examining lifting equipment, the LEEA definition of a Competent Person is a person having such practical and theoretical knowledge and experience of the equipment which is to be thoroughly examined that will enable him/her to detect defects or weaknesses which it is the purpose of the examination to discover and assess their importance to the safety of the equipment. The Competent Person should have the maturity to seek such specialist advice and assistance as may be required to enable him/her to make necessary judgements and be a sound judge of the extent to which he/she can accept the supporting opinions of other specialists. He/she must be able to certify with confidence whether it is free from patent defect and suitable in every way for the duty for which the equipment is required. It is the view of LEEA that competency can be a corporate responsibility. Primary Elements of Competency Information Instruction Training 8 Supervision Note: LEEA Foundation Course and Advanced Programme certificates are not evidence, declaration or proof of competency. Notes: What are the Required Elements of Competency? ©LEEA Academy Overhead Travelling Cranes – Step Notes – Apr 2017 – v1.3 Risk Assessment What is, “Risk Assessment”? 9 Put simply, it is a careful examination of what, in your work, could cause harm to people, so that you can weigh up whether you have taken enough precautions or should do more to prevent harm. What are the 3 main reasons to assess and manage risk? Human Harm - Injury and illness. Legal Effects - Duty of care and consequences of unsuitable or insufficient risk management. Economic Effects - Substantial financial costs are related to accidents at work. Notes: ©LEEA Academy Overhead Travelling Cranes – Step Notes – Apr 2017 – v1.3 Definitions Hazard A hazard is something (object or situation) that has the potential to cause harm. Danger A liability or exposure to harm; something that causes peril. Likelihood How likely is it that someone could be harmed by the hazard? Severity If the potential for harm was to occur, how severe would the accident be. Risk (a Combination of Likelihood and Severity) Risk is the likelihood that the harm from the hazard is realised. Net Result (Risk) = Likelihood x Severity i.e. How likely x How severe the consequence Notes: 10 ©LEEA Academy Overhead Travelling Cranes – Step Notes – Apr 2017 – v1.3 5 Steps to Risk Assessment Identify the hazards Decide who might be harmed and how Evaluate the risks and decide on control measures Record your findings and implement them Review your assessment and update if necessary Control Measures: Hierarchy of control measures: (ERIC-PD) Eliminate Reduce Isolate Control PPE 11 Discipline -------------- Monitor and Review Ensure control measure compliance (discipline) Be vigilant - note changes: Additional hazards presented? E.g. traffic, pedestrians etc., changes in production activity Record your findings and change the risk assessment as necessary. This may result in the requirement for additional control measures. Notes: ©LEEA Academy Overhead Travelling Cranes – Step Notes – Apr 2017 – v1.3 Are You Following a ‘Safe System of Work’? You have identified the hazards You have decided who may be harmed You have evaluated the risks and decided control measures You have recorded your findings You will review and monitor the situation If you have completed the above checklist, you are now following a “Safe System of Work” The European Machinery Directive A European directive is a directive to the member states of the European community, which has been adopted by the council of ministers, to introduce legislation with common requirements throughout the community. The directives are used to remove barriers to trade and introduce common safety requirements. The Machinery Directive is largely based on risk assessment and use of European standards for critical features such as guards and emergency stops. Machinery directive provides the harmonisation of the essential health and safety requirements (EHSRs) for machinery. It applies only to products that are intended to be placed on or put into service in the market for the first time. What is a ‘Machine’? 12 "An assembly, fitted with or intended to be fitted with a drive system other than directly applied human or animal effort, consisting of linked parts or components, at least one of which moves, and which are joined together for a specific application". Note: As an example, a manual slew jib without hoist that could be fitted inside an offshore service container would not be within the scope of the Directive. The example below shows the hoist fitted to the slew jib so would be within the scope of the directive. Notes: ©LEEA Academy Overhead Travelling Cranes – Step Notes – Apr 2017 – v1.3 Supply of Machinery (Safety) Regulations 2008 – SM(S)R The Machinery Directive is implemented in the United Kingdom under the Supply of Machinery (Safety) Regulations. The Supply of Machinery (Safety) Regulations 2008, SI No 1597 implement the Machinery Directive and contain Essential Safety Requirements which the machinery, including lifting machines and lifting accessories must meet. Manufacturers, importers (into the European Union) and suppliers placing such equipment on the market for service in the community have a duty to: Design, build and supply equipment that is safe and meets the essential safety requirements To carry out such tests as may be necessary to ensure the requirements of above are met To maintain records of all calculations, tests and other relevant information that go to make up a Technical File which may be called upon by the enforcing authorities and which must demonstrate that the Essential Safety Requirements have been met Issue with each item of equipment information on the installation, maintenance, care and safe use o Issue a Declaration of Conformity and affix the CE mark, or issue a Declaration of Incorporation depending on its nature and intended use. In this context, if you manufacture or import (from outside the European Union) an item for your own use, you assume the full responsibilities of the manufacturer and must therefore meet all of the requirements of the regulations To support the machinery directive, the joint European Standards Organisation, CEN/CENELEC, has been producing Harmonised European Standards. 13 Most of these standards have been published but there are still some left in the pipeline. As and when they are published, they will supersede any existing British Standards or other European National Standards covering the same products. These Harmonised Standards have a special status in that products made to the standard are deemed to meet the Essential Health and Safety Requirements of the Relevant Directives, and therefore the UK Regulations, in so far as the standard addresses such essential requirements. They therefore provide a relatively easy way for manufacturers to know that their products meet the legal requirements and equally a convenient way for purchasers to specify their needs. Following the publication of the new Machinery Directive 2006/42/EC in 2006, all the relevant Harmonised Standards have been amended to make reference to it. The Technical File The Essential Health and Safety Requirements that apply to the lifting equipment: A description of the methods used to eliminate these hazards or reduce risks The standards used in the design; information from the user Design information (calculations, drawings, procedures, etc.) Material traceability; tests reports and instructions for use ©LEEA Academy Overhead Travelling Cranes – Step Notes – Apr 2017 – v1.3 Aligned to the requirements of the Machinery Directive, the Supply of Machinery (Safety) Regulations state that lifting equipment must be designed and built to sustain a static overload of: Manually operated machines: 1.5 x WLL Other machines: 1.25 x WLL Lifting accessories: 1.5 x WLL Machinery must be capable of sustaining a dynamic overload of: - 1.1 x WLL Previous standards and directives have used different values therefore it is important to always consult manufacturers documentation for specific requirements. Lifting machines must also be supplied with instructions for:- Care and safe use Installation, commissioning and testing Maintenance and adjustments Limitations of use and possible misuse Noise and vibration emissions 14 Training PUWER and LOLER Regulations Provision and Use of Work Equipment Regulations 1998 (PUWER) Applies to all work equipment Lifting Operations and Lifting Equipment Regulations 1998 (LOLER) Applies to lifting equipment in addition to PUWER Both PUWER and LOLER apply to all sectors of industry. Status of PUWER and LOLER United Kingdom: legal requirement International: good practice demanded by customers and local authorities, integral to the LEEA code of practice Notes: ©LEEA Academy Overhead Travelling Cranes – Step Notes – Apr 2017 – v1.3 The Essentials of PUWER PUWER places duties on the employer to ensure that: It is the duty of the employer to ensure that work equipment coming into his undertaking meets with any EHSRs and in the case of lifting equipment this would be of directive 2006/42/EC Work equipment is suitable for the purpose for which it is to be used The working conditions and risk to health and safety of personnel in which the work equipment is used is to be considered Equipment is suitably maintained and a log kept up to date Equipment is inspected on a regular basis (refer to LOLER) All inspection and maintenance records are kept and recorded All persons using work equipment have sufficient information pertaining to its use, e.g. operating manuals and guides to safe use PUWER requires employer to address risks or hazards of equipment from all dates of manufacture and supply. Equipment first provided for use after 31st December 1992 must comply with any ‘essential requirements’ 15 Equipment may still present a hazard or risk if: Application different from that originally envisaged Safety depends upon the way it is installed Technical mismatch between the supply side and user side legislation Employers can ensure compliance by checking: CE marking EC declaration of conformity Note: Offshore container standards slightly differ and require a Certificate of Conformity PUWER requires that, when providing equipment for use at work the purchaser obtains equipment complying with the relevant European Directives. e.g. In the case of offshore containers requesting the Certificate of Conformity which shows compliance with BS EN 12079 will ensure that the offshore containers meet this requirement. Notes: ©LEEA Academy Overhead Travelling Cranes – Step Notes – Apr 2017 – v1.3 Provision and Use of Work Equipment Regulations (PUWER) Regulation 4 Suitability of Work Equipment Regulation 5 Maintenance Regulation 6 Inspection Regulation 7 Specific Risks Regulation 8 Information and Instructions Regulation 9 Training Summary of the Key Requirements of PUWER PUWER requires employer to address risks or hazards of equipment from all dates of manufacture and supply. Equipment first provided for use after 31st December 1992 must comply with any ‘essential requirements’. Equipment may still present a hazard or risk if: Application different from that originally envisaged Safety depends upon the way it is installed Technical mismatch between the supply side and user side legislation 16 How does an employer check that equipment he has purchased complies with the requirements of PUWER? Locate the CE marking Obtain the EC declaration of conformity from the supplier Notes: ©LEEA Academy Overhead Travelling Cranes – Step Notes – Apr 2017 – v1.3 Lifting Operations and Lifting Equipment (LOLER) Regulation 4 Strength and Stability Regulation 5 Lifting Equipment for Lifting Persons Regulation 6 Positioning and Installation Regulation 7 Marking of Lifting Equipment Regulation 8 Organisation of Lifting Operations Regulation 9 Thorough Examination and Inspection Regulation 10 Reports and Defects Regulation 11 Keeping of Information ----------------- Regulation 4 Strength and Stability Requires the employer to ensure that the load they are planning to lift does not exceed the limits for strength and stability of the lifting equipment. Regulation 5 Lifting Equipment for Lifting Persons 17 Details the additional safeguards that must be considered when using lifting equipment to lift people. Regulation 6 Positioning and Installation Details the considerations on where lifting equipment, both fixed and mobile equipment, should be sited. Regulation 7 Marking of Lifting Equipment Requires all lifting equipment to be marked with its SWL and information that gives the items characteristics, e.g. grade, angle of use etc. Regulation 8 Organisation of Lifting Operations Clarifies that each lifting operation needs to be planned, supervised and carried out safely. Notes: ©LEEA Academy Overhead Travelling Cranes – Step Notes – Apr 2017 – v1.3 Regulation 9 Thorough Examination and Inspection Before lifting equipment is put into service for the first time it is thoroughly examined for any defect unless the lifting equipment: Is less than 12 months old Owner holds the original DOC Equipment that has not been used before will require thorough examination when entering service if the DOC is older than 12 months. Equipment can be damaged during long periods within the supply chain Maximum fixed periods for thorough examinations and inspection of lifting equipment as stated in regulation 9 of LOLER are: - Lifting Accessories 6 months Lifting Equipment 12 months People Carrying Equipment 6 months Or in accordance with a written scheme of examination. Or each time that exceptional circumstances which are liable to jeopardise the safety of the lifting equipment have occurred. The information to be contained in the report of thorough examination is given in schedule 1 of LOLER. 18 Minimum Requirements for a Report of Thorough Examination – Schedule 1 of LOLER The name and address of the employer for whom the thorough examination was made The address of the premises at which the thorough examination was made Particulars sufficient to identify the equipment including where known its date of manufacture The date of the last thorough examination The safe working load of the lifting equipment or (where its safe working load depends on the configuration of the lifting equipment) its safe working load for the last configuration in which it was thoroughly examined In relation to the first thorough examination of lifting equipment after installation or after assembly at a new site or in a new location: o That it is such thorough examination; o (If such be the case) that it has been installed correctly and would be safe to operate In relation to a thorough examination of lifting equipment other than a thorough examination to which paragraph 6 relates – ©LEEA Academy Overhead Travelling Cranes – Step Notes – Apr 2017 – v1.3 Whether it is a thorough examination: o Within an interval of 6 months under regulation 9(3)(a)(i) o Within an interval of 12 months under regulation 9(3)(a)(ii) o In accordance with an examination scheme under regulation 9(3)(a)(iii) o After the occurrence of exceptional circumstances under regulation 9(3)(a)(iv) (If such be the case) that the lifting equipment would be safe to operate In relation to every thorough examination of lifting equipment: o identification of any part found to have a defect which is or could become a danger to persons, and a description of the defect o particulars of any repair, renewal or alteration required to remedy a defect found to be a danger to persons In the case of a defect which is not yet but could become a danger to persons - o The time by which it could become such a danger o Particulars of any repair, renewal or alteration required to remedy it The latest date by which the next thorough examination must be carried out Where the thorough examination included testing, particulars of any test The date of the thorough examination The name, address and qualifications of the person making the report; that he/she is self-employed or, if employed, the name and address of his employer 19 The name and address of a person signing or authenticating the report on behalf of its author The date of the report Model report of thorough examinations are available for LEEA members on the LEEA website. Written Schemes of Examination The Lifting Operations and Lifting Equipment Regulations 1998 permits a scheme of examination, drawn up by a competent person, as an alternative to the fixed maximum periods. The benefit of an examination scheme is that, by focusing on the most safety critical areas, the examinations can be carried out the most cost effective way. This may provide a means of reducing examination costs, however, it may also provide a means of enhancing safety without increasing costs. Notes: ©LEEA Academy Overhead Travelling Cranes – Step Notes – Apr 2017 – v1.3 Information for Written Schemes of Examination The written scheme of examination should contain at least the following information: The name and address of the owner of the lifting equipment The name and contact details of the person responsible for the equipment. If responsibility is divided, e.g. between maintenance and operations, there may be more than one name, however it should be clear who should be notified in the event of a dangerous or potentially dangerous defect and to whom reports should be sent The name, qualifications and address of the person drawing up the scheme. If the competent person is not working on their own account, the name of their employing organisation and their position in that organisation should be given The identity of the equipment, i.e. a description including the make, model and unique identity number The location of the equipment if it is a fixed installation or the location where it is based for portable and mobile equipment Details of any information or references used in drawing up the scheme. For example the manufacturer’s manual, expected component life, or specific information on the design life of the crane structure and mechanisms as detailed in clause 7 of ISO 12482-1 The basis for the scheme. For example, is it based on hours of service, duty monitoring, examining 20 certain parts or components at different intervals to other parts? Details of any data logging system fitted, including a list of the parameters monitored and the means of data retrieval, monitoring and storage What determines when the thorough examination shall take place and who is responsible for monitoring that and instigating the examination? Identification of the safety critical parts requiring thorough examination A risk assessment should take account of: o The condition of the equipment o The environment in which it is to be used o The number and nature of lifting operations and the loads lifted o The details of any assumptions about usage, expected component life Etc. The frequency of thorough examination of those parts identified as safety critical taking into account the degree of risk associated with each part. This may include time or loading or duty cycle limits and vary for different parts of the equipment. Where the scheme is based on such criteria, we recommend that a maximum period between thorough examinations is always specified as equipment can deteriorate whether used or not ©LEEA Academy Overhead Travelling Cranes – Step Notes – Apr 2017 – v1.3 The method of examination of those safety critical parts, which may include the degree of dismantling required and the techniques employed e.g. visual examination, measurement, NDT, operational test, load test The rejection criteria or a reference to where this information may be found An indication of the resources required to prepare the equipment and carry out the thorough examination. This may include qualified personnel, workshop facilities, specialist NDT and metallurgical facilities Any changes to equipment condition, operational or environmental parameters that will require a review of the scheme by the competent person. These may include damage to the equipment, change of use from general duty to heavy duty or moving from an inland location to a marine environment A requirement for the person responsible for the equipment to monitor its circumstances of use and inform the competent person who drafted the scheme of any changes The date of drawing up the scheme and the date at which any routine review is required Further information on written schemes of examination can be found in the LEEA COPSULE Edition 8 Appendix 1.8. Lifting Operations and Lifting Equipment Regulations (LOLER) Regulation 10 Reports and Defects 21 A person making a thorough examination for an employer under regulation 9 shall: Notify the employer forthwith of any defect in the lifting equipment which in his opinion is or could become a danger to persons As soon as is practicable make a report of the thorough examination in writing authenticated by him/her or on his/her behalf by signature or equally secure means and containing the information specified in schedule 1 to the employer; and where there is in his opinion a defect in the lifting equipment involving an existing or imminent risk of serious personal injury, send a copy of the report as soon as is practicable to the relevant enforcing authority Where there is in his opinion a defect in the lifting equipment involving an existing or imminent risk of serious personal injury, the Competent Person will send a copy of the report as soon as is possible to the relevant enforcing authority. In this case, an employer who has been notified of an imminent risk shall ensure that the lifting equipment is not used before the defect is rectified. Notes: ©LEEA Academy Overhead Travelling Cranes – Step Notes – Apr 2017 – v1.3 Regulation 11 Keeping of Information An employer obtaining lifting equipment shall: Keep the EC Declaration of Conformity for so long as they operate the lifting equipment Ensure that the information contained in every report is kept available for inspection In the case of a thorough examination for lifting equipment: Until he ceases to use the lifting equipment In the case of a thorough examination for lifting accessories: For two years after the report is made LOLER and the Tester/Examiner LOLER refers to ‘Thorough Examination and Inspection’ of which a test may be part. A report of thorough examination to include details of any tests carried out. The duties of the Competent Person include ensuring that: Lifting equipment has been thoroughly examined before it enters service Second-hand, hired or borrowed equipment has a current examination report before it is used 22 And, where safety of equipment depends upon installation: That it has a thorough examination after it has been installed That it has a thorough Examination after it has been assembled Manual Handling Operations Regulations 1992 Refers directly to lifting operations and adds to the employers duties in section 2 of the HSWA Requires an assessment to be made of any operation where loads are handled manually, or where manual effort is necessary, with a view to reducing the number of injuries that result from such operations: o Task o Individual o Load o Environment Requires the introduction of lifting appliances where the risks are high or if the operation can be made safer by their introduction ©LEEA Academy Overhead Travelling Cranes – Step Notes – Apr 2017 – v1.3 Working at Height The danger of people and materials falling affects not only those working at height, but also sometimes to a greater degree, those underneath. Working at height is one of the biggest causes of fatalities and major injuries. Commonly, accidents are caused from falls from ladders and through fragile surfaces. Work at height means work in any place where, if there were no precautions in place, a person could fall a distance that could cause personal injury (for example a fall through a fragile roof). Employers and those in control of work at height must first assess the risks. Before working at height you must follow these simple steps: Avoid work at height where it is reasonably practicable to do so Where work at height cannot be easily avoided, prevent falls using either an existing place of work that is already safe or the right type of equipment Minimise the distance and consequences of a fall, by using the right type of equipment where the risk cannot be eliminated Working at Height Regulations (UK) The work at height regulations 2005 have an influence on lifting practice. They emphasise the need to avoid working at height if possible but, where it is necessary, they require the most suitable means of reducing and controlling the risk. 23 Consequently, this has affected the choice of equipment for some lifting operations. ©LEEA Academy Overhead Travelling Cranes – Step Notes – Apr 2017 – v1.3 Dos and Do Nots of Working at Height Do: As much work as possible from the ground Ensure workers can get safely to and from where they work at height Ensure equipment is suitable, stable and strong enough for the job, maintained and checked regularly Take precautions when working on or near fragile surfaces Provide protection from falling objects Consider emergency evacuation and rescue procedures Do not: Overload ladders; consider the equipment or materials workers are carrying before working at height. Check the pictogram or label on the ladder for information Overreach on ladders or stepladders Rest a ladder against weak upper surfaces, e.g. glazing or plastic gutters Use ladders or stepladders for strenuous or heavy tasks, only use them for light work of short duration (a maximum of 30 minutes at a time) Let anyone who is not competent (who doesn’t have the skills, knowledge and experience to do the job) to work at height Working at Height – A Brief Guide Please read the HSE document: “Working at Height – A Brief Guide”, available at www.hse.gov.uk 24 Electricity at Work Regulations The Electricity at Work Regulations apply to almost all places of work. The Regulations were enacted to impose duties to limit the risks involved with using electricity at work. The following people are subject to the Regulations: Employers and the Self-Employed Employees The duties under the Regulations are not just in relation to employers but also place a duty on employees in the following circumstances: To co-operate with his employer so far as is necessary to enable any duty placed on that employer by the provisions of these Regulations to be complied with To comply with the provisions of these Regulations in so far as they relate to matters which are within his control Many employees in the electrical trades and professions for example have responsibilities which are part of the duties of their employment of safety in relation to the installation of electrical equipment and systems The definition of electrical equipment provided by the regulations includes anything used, intended to be used or installed for use, to generate, provide, transmit, transform, rectify, convert, conduct, distribute, control, store, measure or use electrical energy. ©LEEA Academy Overhead Travelling Cranes – Step Notes – Apr 2017 – v1.3 For further information, please read the HSE documents: “The Electricity at Work Regulations 1989 – Guidance on Regulations” and “Electricity at Work – Safe Working Practices”. These can be found at www.hse.gov.uk. The Electromagnetic Compatibility Directive In order to facilitate a single European market for goods some 20 years ago the European Union began what is described as the 'New Approach'. A number of Directives were adopted with the aim of setting objectives for the harmonisation of technical rules, primarily but not exclusively, affecting the health and safety of new products by design and construction. The principal aim of the 'New Approach' was to remove barriers to trade by requiring all products to meet common minimum health and safety objectives, which would be supported by agreed standards at the product level. The Electromagnetic Compatibility Directive 2004/108/EC (EMC) will apply to equipment with an electrical aspect, primarily to prevent interference with other electrical equipment and its own immunity from such disturbance. The Electromagnetic Compatibility Regulations The EMC Directive is implemented in the UK by the Electromagnetic Compatibility Regulations which apply to electrical and electronic equipment liable to cause or be affected by electromagnetic disturbance. 25 The aim of the regulations is to ensure that electromagnetic disturbance generated by electrical or electronic equipment doesn’t reach levels which would prevent radio, telecommunications and other equipment from working properly. They also exist to ensure that such equipment itself has adequate immunity from electromagnetic disturbance. The rules don’t deal with safety-related matters. Whilst this is not a matter for the tester and examiner of lifting equipment, we should note that when the manufacturer affixes the CE mark to an item it implies that all the necessary directives have been complied with. The EC Declaration of Conformity for electrically operated lifting equipment should therefore refer to both the Machinery Directive and the Electromagnetic Compatibility Directive. Notes: ©LEEA Academy Overhead Travelling Cranes – Step Notes – Apr 2017 – v1.3 Revoked, Repealed and Amended Legislation Prior to 5 December 1998, the Factories Act 1961 was the main legislation concerned with the use of lifting equipment and it was augmented several sets of industry specific regulations. The Provision and Use of Work Equipment Regulations 1998 and the Lifting Operations and Lifting Equipment Regulations 1998 together repeal, revoke or amend and replace the requirements for lifting equipment given in the following: The Factories Act 1961 The Construction (Lifting Operations) Regulations 1961 The Shipbuilding and Ship-repairing Regulations 1960 The Docks Regulations 1988 The Mines and Quarries Act 1954 The Offshore Installations (Operational Safety, Health and Welfare) Regulations 1976 The Lifting Plant and Equipment (Records of Test and Examination etc.) Regulations 1992 LEEA COPSULE – Methods of Operation Whilst the LEEA COPSULE does not include operation of powered equipment, users should be reminded of the need for power systems to be installed, maintained and examined in accordance with the relevant regulations, e.g. The Electricity at Work Regulations, The Pressure Systems Safety Regulations etc., and their need to meet any obligations these regulations impose. Power operated equipment has the advantages of quicker operation than with manually operated equipment, often operatives can be remote from the load and heavier loads can be handled conveniently 26 without operative fatigue. In summary, where no power source is available, light loads are to be lifted, infrequent operation is called for or precision placement of the load is required, manual operation may be considered. Where heavy loads are to be lifted, frequent operation is called for or a more rapid operation is necessary power operation should be considered. Summary In this module, we have looked at the various laws that are applicable to lifting equipment and it’s examination in the United Kingdom. Examiners of lifting equipment should always make themselves familiar with the national regulations of the country in which they are operating. Failure to do so may lead to prosecution, due to breaches of the law. Notes: ©LEEA Academy Overhead Travelling Cranes – Step Notes – Apr 2017 – v1.3 2. Standards Standards for Overhead Travelling Cranes 27 There are many different standards that are directly related to overhead travelling cranes. In order to provide a simple reference guide, we have divided these standards into 5 categories: 1. Design 2. Classification 3. Gantries 4. Thorough Examination 5. Other Relevant Standards These categories, and the standards pertaining to each will be shown as you work through this module. It is advisable that the Competent Person has access to relevant standards in the course of their work in the thorough examination of overhead travelling cranes. Notes: ©LEEA Academy Overhead Travelling Cranes – Step Notes – Apr 2017 – v1.3 Types of Standards Manufacturing standards detail dimensions, materials and safe working loads, e.g. BS EN 14492 (Winches and Hoists). Performance standards offer a range of criteria that the final product must meet, e.g. BS EN 13001 – Cranes (General Design). ISO (or International Standards) generally take the form of performance standards, which are agreed internationally by a majority vote. Their use is optional but they are often used as the basis for writing National Standards. Where the UK accepts these as written, they are published in this country as British Standards. A new practice has been adopted in recent years of using the ISO number and adding the prefix BS, for example ISO 2330 - Fork lift trucks - Fork arms - Technical characteristics and testing is published as BS ISO 2330. ISO 9927-1 (Cranes – Inspection – General) is an example of an International Standard that sets out the minimum criteria for the inspection of overhead cranes. In the UK, BS 7121-2-7: 2012 is the standard that should be followed for the thorough examination of Overhead Travelling Cranes. Standards Relating to Overhead Travelling Cranes OTC Design BS EN 13001: Design of Cranes – General Design 28 BS 466 (withdrawn, but to be used for cranes designed to this standard): Design of Cranes BS 2573-1: Rules for the Design of Cranes BS EN 15011: Cranes – Bridge and Gantry Cranes OTC Classification BS ISO 12482: Cranes – Monitoring for Crane Design Working Period (Duty Holder/Owner) ISO 4301-1: Cranes and Lifting Appliances – Classification Gantries BS EN 1993-6: Design of Structures – Supporting Structures (Deflections) BS EN 1991-3: Gantries – Actions on Structures Induced by Cranes DIN 536-199: Rail Sections BS EN 13674-1: Rail Sections ISO12488-1: Cranes – Tolerances for Wheels and Travel/Traverse Tracks – General ©LEEA Academy Overhead Travelling Cranes – Step Notes – Apr 2017 – v1.3 Thorough Examination *BS 7121-2-7: 2012: OTC – Inspection, Maintenance and Thorough Examination ISO 9927: Cranes – Inspection – General BS ISO 4309: Wire Ropes – Discard Criteria *This training course has been primarily constructed in relation to the standard BS 7121-2-7:2012 for the inspection, maintenance and thorough examination of Overhead Travelling Cranes. Other Relevant Standards BS EN 13411: Terminations for Steel Wire Ropes BS EN 12385: Steel Wire Ropes BS EN 14492-2: Cranes – Power Driven Winches and Hoists BS EN ISO 9606-1: Approval Testing of Welders for Fusion Welding – Steel BS 4: 2005: Rolled Steel profiles 29 Notes: ©LEEA Academy Overhead Travelling Cranes – Step Notes – Apr 2017 – v1.3 3. Lifting Media – Load Chain Fine Tolerance – Short Link Chain BS EN 818 – 7, covering: Short link chain for lifting purposes — Safety — Part 7: Fine tolerance hoist chain Grades: (Types T, DAT and DT), 4mm to 22mm diameter BS EN 818-7 is applicable to electrically welded round steel short link hoist chains conforming to EN 818-1 ISO 3077 - Short-link chain for lifting purposes, - Grade T, (types T, DAT and DT), fine – tolerance hoist chain 30 Chain Finishes Fine tolerance chain can be recognised primarily by the Grade mark. Type DAT and type DT hoist chains possess a surface hardness greater than core hardness and are used for power driven chain hoists to offer greater resistance to wear Type DT hoist chain differs from DAT hoist chain in having higher surface hardness and/or greater case depth to optimise wear resistance Fine Tolerance – Short Link Chain The chain is made to precise dimensions in order that it engages freely, and without jamming into pocketed load wheels ©LEEA Academy Overhead Travelling Cranes – Step Notes – Apr 2017 – v1.3 The application of a tensile force at the final stages of manufacture (pulled to precise pitch) has the effect of work hardening the chain Fine tolerance chain is less ductile than chain used for general sling manufacture (medium tolerance) Fine Tolerance chain has better wear characteristics Load chains must: Be strong Be reasonably resistant to corrosion Have good resistance to wear These properties are partially achieved by material selection. Further improved by case hardening and/or plated with corrosion resistant finishes at the time of manufacture. Fine Tolerance Chain Guidance on the applications for which the different types of Grade T hoist chain shall be used is as follows: Type T manually operated hoists, or power operated hoists with slow speeds, where the working environment does not involve abrasive conditions 31 Type DAT power driven hoists where chain speeds are high in combination with high working capacity and where wear resistance is required to give longer chain life Type DT power driven hoists used in abrasive conditions Note: Case hardened chains are not suitable in portable manually operated hoists. Notes: ©LEEA Academy Overhead Travelling Cranes – Step Notes – Apr 2017 – v1.3 WLL Comparison of Chain Grades Fine Tolerance Chain Dimensional incompatibility between the hoist chain and mating parts of the hoist (chain wheel, chain guide and loading device) may lead to premature failure of the chain. 32 BS EN 818-7 contains dimensional requirements for correct assembly and fit. Notes: ©LEEA Academy Overhead Travelling Cranes – Step Notes – Apr 2017 – v1.3 Key Points Correct alignment with the load wheel o Use of suitable chain guide o Hoist not to be used if direct entry to load wheel is prevented, or: o Where the chain is twisted Chain must be under tension to engage the load wheel correctly o A few links of load chain will be sufficient Chain should not be corroded or covered in dirt or debris Chain stripper fitted to ensure disengagement of slack load chain from the load wheel Adequate and appropriate lubrication o Lubricants should be able to withstand high bearing pressures o Colloidal graphite used in adverse working conditions such as foundries, or: o Where lubricant may contaminate (e.g., food or pharmaceutical industries) o Must be acid free Chain collector box or bag usually fitted o Adequate size and alignment o Provide a means of drainage o Slack chain should never pile too high in the bag/box – this will remove the tension from the slack end of the load chain 33 o Could result in a twisted link entering the load wheel and cause disastrous consequences Load chain must always hang in a straight line o No twists o Load hooks fitted with a swivel to prevent live side of chain from twisting Load chains are never to be back hooked or choked o Separate sling attachments Frequent Inspection In addition to the requirements for statutory periodic examinations, hoist manufacturers will issue instructions for user inspections. The type and frequency of inspections depends basically on the working conditions of the hoist. General classifications are given for these inspections as ‘frequent' and ‘periodic'. Frequent inspections are visual inspections carried out by the operator or other designated person, with or without a record being made, to determine if damage or deterioration has occurred in service. The following inspection intervals are recommended when carrying out frequent inspections and are in addition to a daily pre-use check which should be made by the operator: Light service - every month Moderate service - every 2 weeks Heavy service - every week ©LEEA Academy Overhead Travelling Cranes – Step Notes – Apr 2017 – v1.3 Very heavy service - every day Periodic Inspection Periodic inspections are more thorough inspections by appointed persons making records of the external conditions to provide a basis for a continuing evaluation. The following periodic inspection intervals are recommended: Light service - yearly Moderate service - six monthly Heavy service - quarterly Very heavy service - every six weeks If at any of these user inspections external conditions indicate it necessary, the machine should be referred to a Competent Person for thorough examination. Thorough Examination Thorough examinations are made by a Competent Person, i.e. the tester and examiner. They are usually associated with statutory requirements calling for records to be made and certificates or reports issued which permit the hoist to enter or remain in service. This is far more thorough than the user inspection and will usually include disassembly of parts to permit detailed examination. Each of the regulations lays down a maximum time period between such examinations. 34 When carrying out thorough examinations the chain should be examined throughout its length to detect any evidence of wear, distortion or external damage. The block should then be operated under ‘no load' and ‘load' conditions in both directions to check for the smooth functioning of the chain and wheels. If the chain jumps, binds or is noisy after cleaning and lubrication then a more detailed examination must take place. Competent Person – Thorough Examination Preparation for examination o Chains should be cleaned (no strong alkalis or acids – hydrogen embrittlement) Visually examine chain throughout entire length, link by link Operate hoist under no-load and loaded conditions o Check for directional smoothness o Look for chain jumping in the pocket wheel o Listen for binding and noisy operation o If minor faults are not corrected by cleaning and lubrication, a detailed examination is necessary Link by link examination in adequate light. Check for NCCG (nicks, cuts, cracks or gouges), wear, elongation and other damage including build-up of debris ©LEEA Academy Overhead Travelling Cranes – Step Notes – Apr 2017 – v1.3 o Wear and elongation to be measured in accordance with ‘original equipment manufacturer’ (OEM) instructions Notes: Stretch and Elongation A common misunderstanding is that stretch in a load chain is the same as elongation. This is incorrect. Stretch in a load chain is not permitted as this is actually the chain having exceeded its elastic limit and now will have permanent set (it is now in the plastic deformation stage) and this should be withdrawn from service. Elongation is wear that has occurred due to articulation of the interlinking chain links at the intrados of the connection point. Manufacturers may have different instructions for measurement and the acceptance/rejection criteria may vary Where there are no OEM instructions: 35 o 2% increase in length (due to wear) over a minimum length of 5 links should be used as a rejection value Note: This is less than 5% which is used for chain slings This is because the load chain in a machine has to mate with the load wheel and therefore elongation would cause a poor fit and dangerous consequences Some hoist manufacturers issue a gauge for checking of elongation. The example below is taken from a manufacturers maintenance manual and is typical for most brands of hoists: ©LEEA Academy Overhead Travelling Cranes – Step Notes – Apr 2017 – v1.3 Chain Elongation due to Wear Rejection Criteria Load chains should be rejected if any of the following conditions are observed: Cracks Nicks or gouges Visible distortion Severe corrosion Deposits which cannot be removed Increase in length which exceeds the OEM recommendations or 2% over 5 links 36 Wear In the case of wear, rapid wear can lead to sudden failure of the chain. This is shown as a rough appearance of the mating surfaces. Such chains should be replaced even if they are within the OEM wear limits. Chain Replacement Calibrated chain for powered lifting hoists varies in dimensions, particularly pitch, for different manufacturers. For this reason it is important that only chain specified by the hoist manufacturer should be used for replacement. Each manufacturer provides details on the best methods of chain replacement for their particular units and it is recommended that these be closely followed. When replacing worn chain with new chain it is advisable to also replace the pocketed wheel(s) as the pockets will have worn with the chain. Manufacturer’s Criteria The certificate of test and examination shall give at least the following information: The name and address of the manufacturer or his authorised representative, including date of issue of the certificate and authentication Number and parts of BS EN 818 Quantity and description of the chain of which the test sample is representative ©LEEA Academy Overhead Travelling Cranes – Step Notes – Apr 2017 – v1.3 Identification of the chain of which the test sample is representative Nominal size of chain in millimetres Manufacturing proof force in kilonewtons Breaking force, in kilonewtons (confirmation of whether this was met or exceeded) Total ultimate elongation at fracture, as a percentage (i.e. confirmation that the specified minimum total ultimate elongation has been met or exceeded) Notes: 4. Lifting Media – Wire Rope Wire Rope and Wire Rope Examination 37 Wire Ropes for Lifting Appliances Wire ropes are generally regarded as an expendable component. The load rope requires replacement when inspection shows that its condition has deteriorated and further use would not be suitable for safety reasons. By following well-established principles, such as those detailed in various standards, LEEA COPSULE, and any additional specific instructions provided by the ‘original equipment manufacturer’ (OEM) of the crane or hoist and/or by the manufacturer of the rope, this criteria should never be exceeded. When correctly applied, the discard criteria given in full in BS ISO 4309 are aimed at retaining an adequate safety margin. Failure to recognize them can be extremely harmful, dangerous and damaging. ©LEEA Academy Overhead Travelling Cranes – Step Notes – Apr 2017 – v1.3 How Wire Rope is Made Elements of a Wire Rope 38 Definitions Outer wires: all wires positioned in the outer layer of a spiral rope or in the outer layer of wires in the outer strands of a stranded rope. Inner wires: all wires of intermediate layers positioned between the centre wire and outer layer of wires in a spiral rope or all other wires except centre, filler and outer wires in a stranded rope. Filler wires: wires used in filler construction to fill up the gaps in between the layers. Centre wires: wires positioned at the centre of a spiral rope or the centres of strands of a stranded rope. ©LEEA Academy Overhead Travelling Cranes – Step Notes – Apr 2017 – v1.3 Strand Construction A single wire, known as a king wire (centre wire), is taken and then the remainder of the required number of wires are twisted around this to form a strand. Wire sizes and the manner in which they are laid up can be adjusted to give varying performance characteristics to the rope for different service duties. 6 x 19 means that there are 6 strands each of 19 wires and 6 x 36 means that there are 6 strands each of 36 wires. Both of these are equal lay ropes. 39 The three basic methods of laying up a strand:- ©LEEA Academy Overhead Travelling Cranes – Step Notes – Apr 2017 – v1.3 Notes: Seale Construction This is a parallel lay strand with the same number of wires in both layers. 40 In the example shown below, the construction consists of 1 x centre wire, 9 x inner wires and 9 x outer wires: Filler Construction A parallel lay strand having an outer layer containing twice the number of wires than the inner layers with filler wires in the valleys between the layers. In the example shown below, the construction consists of 1 x centre wire, 6 x inner wires, 6 x filler wires and 12 x outer wires: Warrington Construction A parallel lay strand having an outer layer containing alternately large and small wires. In the example shown below, the construction consists of 1 x centre wire, 7 x inner wires and 14 (7 large and 7 small) x outer wires: You may have noted that previous images of Warrington construction rope in this module show a 1/6/12 (6 large and 6 small outer wires) however, as long as the geometry of the outer wires remains the same, there may be alternative numbers of wires in a particular rope construction. ©LEEA Academy Overhead Travelling Cranes – Step Notes – Apr 2017 – v1.3 Warrington Seale (Combined) Construction A parallel lay strand having three or more layers laid in one operation and formed from a combination of the previous strand types. In the example shown below, the Warrington Seale construction consists of 1 x centre wire, 6 x inner wires, 12 warrington wires and 12 x outer wires: Notes: 41 Types of Wire Rope Core Fibre core (FC) This type of core is made from either natural fibres or synthetic fibres. ©LEEA Academy Overhead Travelling Cranes – Step Notes – Apr 2017 – v1.3 Wire Stranded Core (WSC) Grades of Wire Rope Wire Tensile Strength/Grade The grade of the wire rope based upon the tensile strength of the wires in N/mm². 42 Note: Rope Grade 2160 is not covered by European Standards. Stranding The stranding operation takes place when all the wires are brought together at the forming point. Note that the wires during this and the closing operation are spun in to the correct helical shape, this process is called preforming. This reduces the internal stresses in the strands and the rope meaning that if the wires and strands are cut they do not spring out of the rope formation. ©LEEA Academy Overhead Travelling Cranes – Step Notes – Apr 2017 – v1.3 Pre-Forming During this operation, the strands are now brought together at the forming point around the specified core to make the rope. 43 The individual wires in the strand are bent into the correct helix before being wound into position. The strands are then wound into the correct helix, generally the opposite direction. Results in a relatively inert (dead) rope Resistant to kinking Easy to handle so when such a rope is cut: o Wires will stay in position o Broken wires do not stick out o Less dangerous to the user Rope is more flexible ©LEEA Academy Overhead Travelling Cranes – Step Notes – Apr 2017 – v1.3 Rope Lay Rope lay refers to the way in which the wires are laid when forming the strands and the way in which the strands are laid when forming the rope. There are 2 types of lay, ordinary (regular) lay and Lang’s lay: Ordinary lay: the wires that make up the strand and the strands that make up the rope are laid in opposite directions. When formed, this gives the impression that the wires are running the length of the wire rope. Lang’s lay: the wires that make up the strand are laid in the same direction as the strands in the rope. When formed the wires quite clearly run across the diameter of the rope. Due to the tendency of the rope to unwind, Lang’s lay ropes are not suitable for wire rope slings. Ordinary Lay Wires in the strands are laid in the opposite direction of lay to the strands in the rope. 44 The lower-case letter indicates the direction of the wires and the capital letter, the direction of the strands. Note: Ordinary Lay ropes will be letter designated with different letters. Lang’s lay Wires in the strands are laid in the same direction of lay as the strands in the rope. Not suitable for the manufacture of wire rope sling legs. Note: Lang’s Lay ropes will be letter designated with the same letters. ©LEEA Academy Overhead Travelling Cranes – Step Notes – Apr 2017 – v1.3 Lang’s Lay The advantage of Lang’s lay is that this construction offers a much better wearing surface than ordinary lay Lang’s lay rope is more flexible than one of ordinary lay Its disadvantage is that it can only be used in applications where both ends of the rope are secured, such as a lift or multi-fall hoist. If suspended under load with one end free to turn, such as on a single fall powered hoist rope, it will un-lay itself Both ordinary lay and Lang’s lay ropes are usually supplied right-hand lay, but left-hand lay is available for special applications Low-Rotating Rope Although the six strand rope is the most common, there are many exceptions, and the exception is most likely to be the low-rotating type usually used on cranes or on larger capacity hoists. All six strand ropes tend to untwist when load is applied to them: An undesirable characteristic especially on long multi-fall hoist blocks where it can cause the bottom block to twist It may be overcome by using what is known as a multi-strand rope, which has low-rotating qualities by having two or three layers of 7 wire 1-6 strand laid in opposite directions 45 Notes: ©LEEA Academy Overhead Travelling Cranes – Step Notes – Apr 2017 – v1.3 Effect of Rope Rotation Low-Rotating Rope The most common type is the 17 x 7 (1-6), which has an outer layer of 11 strands laid over an inner layer of 6 strands, which in turn is laid over a core strand. The construction is 11 strands/6 strands/1 strand all 7 wire 1-6. 46 The layers of strands are laid in opposing directions to prevent the rope from spinning under load. A more flexible version is the 34 x 7 (1-6), which is simply a 17 x 7 with an additional layer of seventeen strands laid around it. The construction is 17 strands/11 strands/6 strands/1 strand all 7 wire 1-6. The layers of strands are laid in opposing directions to prevent the rope from spinning under load. ©LEEA Academy Overhead Travelling Cranes – Step Notes – Apr 2017 – v1.3 Rotation-Resistant Rope (Illustration is 35LS – Low-Rotating Rope) Compacted Rope (K Designation) 47 Benefits of Compacted Rope Increased steel area: Increase in strength Crush resistance Diameter stability Reduced stretch Smooth surface: Increased fatigue life Lower contact pressures Accurate diameter: Improved spooling Twin rope systems ©LEEA Academy Overhead Travelling Cranes – Step Notes – Apr 2017 – v1.3 Rope Finish BS EN 12385 uses the symbol ‘U’ to denote uncoated or bright finish. For zinc finishes the symbol will depend on the class of the coated finish, e.g. Class A zinc finish is designated ‘A’ Class B Zinc is designated ‘B’ Rope Details and Designation 48 Wire Rope Examination Safe operation of manual lifting machines incorporating wire rope as the lifting medium depends, to a large extent, upon the level of detailed examination that is applied by the Competent Person during the thorough examination, not withstanding that daily operator checks by the user also have a significant bearing on safety of the machine in use. The Competent Person should firstly refer to instructions provided by the original equipment manufacturer. Local or application specific regulations should always be followed. ©LEEA Academy Overhead Travelling Cranes – Step Notes – Apr 2017 – v1.3 Rope should always be clean; if this is not possible, consider electromagnetic wire rope inspection method, where appropriate. In the absence of original equipment manufacturer’s criteria, BS ISO 4309 (to which BS EN 13157 refers) criteria may be used to determine the serviceability of the load rope fitted to a powered appliance. BS EN 13411 series of standards should be referred to for terminations in steel wire ropes. BS ISO 4309:2010 – Modes of Deterioration and Assessment Methods 49 BS ISO 4309 – Wire Rope Discard Discard Criteria (General) The safe use of wire rope is qualified by the following criteria: The nature and number of broken wires Broken wires at the termination Localised grouping of wire breaks The rate of increase of wire breaks The fracture of strands Reduction of rope diameter, including that resulting from core deterioration Decreased elasticity External and internal wear External and internal corrosion Deformation Damage due to heat or electric arcing Rate of increase of permanent elongation ©LEEA Academy Overhead Travelling Cranes – Step Notes – Apr 2017 – v1.3 Wire Rope Examination The examination of wire ropes should be systematic and follow a logical order so that no part of the rope, or the accessories and attachments to which it connects are missed. In manual machines, particular attention is to be taken at the following locations: Rope drum anchorage Rope within the area of a termination point Sections of rope travelling through sheaves Sections of rope travelling through the hook block Sections of rope that spool onto the rope drum, especially in areas where the rope crosses over itself in multi-layer drums Any section of the rope that can be damaged by abrasion in contact with an external fixture such as a hatch opening Any part of the rope that is exposed to heat Broken Wires It is usually the number of broken wires developing in a wire rope, which causes its removal from service. It is essential that the entire length of a wire rope be inspected frequently for broken wire(s), excessive wear, and lack of lubrication, with particular attention being paid to those areas adjacent to terminal fittings and where an accelerated rate of wear or corrosion is to be expected, e.g. where a rope passes around sheaves or pulleys, or is particularly exposed to the elements. All examinations shall take into account these individual factors, recognising the particular criteria. 50 BS ISO 4309 details the discard criteria for the allowable amount of broken wires, depending upon the rope category number of the rope (RCN) Example of BS ISO 4309 Rope Category Number Before determining the discard criteria for load ropes under BS ISO 4309, it is necessary to identify the RCN of the rope. By way of example, we are going to look at an RCN 02: ©LEEA Academy Overhead Travelling Cranes – Step Notes – Apr 2017 – v1.3 Viewing the example from BS ISO 4309 above, we can see that an ordinary-lay rope, categorised as an RCN 02 (single-layer or parallel-closed rope) may have a maximum of 6 broken wires over a length of 6 x its diameter, or 12 broken wires over a length of 30 x its diameter, in a machine such as a hand operated winch, utilising a multi-layer drum. What if you do not know the RCN number? If the RCN number of the load rope cannot be found in annex G of BS ISO 4309, the following method should be used for calculating the number of allowable broken wires: Determine the total number of load-bearing wires in the rope; Simply add together all of the wires in the outer layer of strands except for any filler wires and read off the 51 discard values for broken wires over a length of 6d and 30d for the appropriate conditions, in the tables provided. Notes: ©LEEA Academy Overhead Travelling Cranes – Step Notes – Apr 2017 – v1.3 Deterioration In the case of 6 and 8-strand ropes, broken wires usually occur at the external surface. In the case of rotation-resistant ropes, there is a probability that the majority of broken wires will occur internally and are “non-visible” fractures. Note: Students are reminded that access to relevant standards, such as BS ISO 4309, is necessary in order to carry out thorough examinations correctly. Wire Rope Examination The Competent Person can find it prudent to initiate or recommend more frequent periodic inspections than those required by legislation. This decision can be influenced by the type and frequency of operation. Also, depending on the condition of the rope at any time and/or whether there is any change in 52 circumstances, such as an incident or change in operating conditions, the Competent Person can deem it necessary to reduce or recommend the reduction of the interval between periodic inspections. Examples of Rate of Increase for Broken Wires in 2 Different Ropes Generally, ropes develop broken wires at a greater rate later on in the life of a rope than in the early stages. Have a look at the following graph which shows two examples of this. Key: X = time, in cycles Y = number of randomly distributed broken wires per unit length ©LEEA Academy Overhead Travelling Cranes – Step Notes – Apr 2017 – v1.3