Waterproofing PDF
Document Details
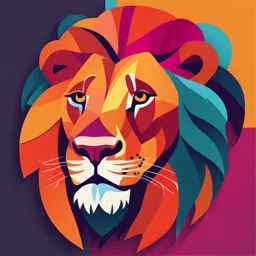
Uploaded by SoftBlackberryBush
SIWIN
Tags
Related
- ARQ. Test Tema 12. Salubridad. RF 13.09.19 PREGUNTAS PDF
- Bitumenhaltige Stoffe PDF
- Module 5: Pre-Cast and Prefabricated Construction Planning, Analysis, and Design PDF
- Arif Waterproofing & Construction Application for Bitumag's Country Agent Certificate PDF
- MAPEI Solutions for Your Work PDF
- Lesson 4- Need for Materials with Various Qualities PDF
Summary
This is a presentation on waterproofing, covering its introduction, types of systems, materials, benefits, and testing methods. The presentation details the importance of waterproofing in construction and maintenance, in addition to covering the safety precautions associated with it.
Full Transcript
Introduction To Waterproofing What is waterproofing? Why waterproofing is done? Where to apply waterproofing? Design approach for fool proof waterproofing system 2 What Is Waterproofing And Why It Is Done? According to world wide survey, cost of wate...
Introduction To Waterproofing What is waterproofing? Why waterproofing is done? Where to apply waterproofing? Design approach for fool proof waterproofing system 2 What Is Waterproofing And Why It Is Done? According to world wide survey, cost of waterproofing to a structure is only 3-5% of total building construction cost. 3 What Is Waterproofing And Why It Is Done? But avoiding that will results in 90% cost after causing damages to the structure!!!!! 4 What Is Waterproofing And Why It Is Done? Most people will have a doubt… Why it is required if I have done concreting? 5 What Is Waterproofing And Why It Is Done? Even concrete with high density and well compacted concrete is porous in nature Not Water tight or Gas tight 6 What Is Waterproofing And Why It Is Done? According to ASTM D 1079: Waterproofing is the treatment of a surface to prevent the passage of liquid in presence of hydrostatic pressure. 7 What Is Waterproofing And Why It Is Done? Waterproofing is the process of making an object or structure waterproof or water-resistant so that it remains relatively unaffected by water or resisting the ingress of water under specified conditions Waterproofing is prevention of water and vapour ingress. It’s helpful in filling structural cracks and overall protection of structure 8 Golden Rules In Waterproofing ✔ Waterproofing is 3-5% of the construction cost still most sensitive. Cost cutting on waterproofing always end up in spending five to ten times for rectification ✔ Do it first time right. ✔ All waterproofing products are good. Selection of the right product and the right applicator ensures performance & durability of waterproofing system 9 Golden Rules In Waterproofing ✔ Waterproofing is always an ‘Applicator’s Job’ and success of waterproofing purely depends on the applicator. ✔ Reliability and competency of applicator is of extreme importance, which depends on: ⯍ Skilled workmen for installation ⯍ Machinery strength ⯍ Experience of jobs 10 Areas For Waterproofing You are familiar with roof waterproofing or damp proofing.. But it is as vital to waterproof all components of a building 11 Areas For Waterproofing Basements and retaining walls Kitchen, bathroom and balcony Podium/landscape Roof/terrace garden Swimming pool Water tank etc. 12 Need for Waterproofing 1. Concrete is porous in nature. 2. Issues of concreting 3. Cracks in concrete due to various factors. 4. Type of construction Eg: Precast. 5. Corrosion due to water ingress affecting the life of the building. Importance of Waterproofing Risk of Damaging Your Property: ○ The infiltration of water into the structure will cause corrosion of the rebar, resulting in the formation of fissures in the concrete. ○ This might lead to structural failure later in the building's life. Importance of Waterproofing Health Risks: ○ In a building trapped moisture has the potential to become a breeding ground for fungi, moulds and other bacteria. ○ The growth of such microorganisms can pose health hazards to people residing or working in the building. Importance of Waterproofing Water Leakage Problems: ○ Furniture, food, and other items might be ruined if water leaks during monsoon season into the structure. ○ In laboratories and technical workshops, moisture can cause equipment failures or damage. Importance of Waterproofing Water Leakage Problems: ○ In a damp environment, stored grains germinate ○ The constant dripping sound can also be annoying to the people living under the roof. Importance of Waterproofing Fire Hazards: ○ Presence of moisture in the building can be responsible for short circuits from electrical installations. ○ These short circuits are one of the primary reasons behind fire accidents in the building. Importance of Waterproofing Damage to aesthetics: ○ Dampness and seepage cause discoloration, plaster shedding, and efflorescence, which leave unpleasant traces on the wall. Benefits of Waterproofing Water Damage Prevention: Protecting your buildings using barriers prevents leaky roofs, dripping walls, and unsealed windows. Value Retention: Protecting your building from water damage and corroding protects your building from diminished value. Benefits of Waterproofing Concrete Longevity: By coating materials such as steel, you decrease the damage that concrete and other materials around its face. Saves Money: By preventing costly water damage, ruined equipment, ruined inventory, or dangerous, wet working conditions, the building owner is bound to benefit from not being exposed to these costly incidents. Code of Practice/Standards of Waterproofing Mostly waterproofing materials are applied based on the companies recommendations. Some commonly used code of practice & standards are: ASTM C1127 - Standard Guide for Use of High Solids Content, Cold Liquid-Applied Elastomeric Waterproofing Membrane with an Integral Wearing Surface ASTM D779 - Standard Test Method for Determining the Water Vapour Resistance of Sheet Materials in Contact with Liquid Water by the Dry Indicator Method ASTM D2099 - Standard Test Method for Dynamic Water Resistance of Shoe Upper Leather by the Maeser Water Penetration Tester Code of Practice/Standards of Waterproofing ASTM D7281 - Standard Test Method for Determining Water Migration Resistance Through Roof Membranes ASTM D3393 - Standard Specification for Coated Fabrics Waterproofness D6135 - Standard Practice for Application of Self-Adhering Modified Bituminous Waterproofing IEC 60529 - Degrees of protection provided by enclosures (IP Code) BS.8102:2009 - "Protection of Below Ground Structures against Water from the Ground" (British Standards Institution) AS 3740 2021 - Waterproofing of Domestic wet areas (Australian Standard) Code of Practice/Standards of Waterproofing IS:3414-Code of Practice for Design & Installation of Joints in Buildings IS:1838 (Pt.I and Pt.II) - Specification for Preformed Fillers for Expansion Joint in Concrete Pavement and Structures IS:1834 - Specification for Hot Applied Sealing Compounds for Joints in Concrete IS:3067- Code of Practice for General Design Details & Preparatory Works for Damp Proofing and Water Proofing of Buildings IS 9918 (1981): Code of practice for in-situ waterproofing and damp-proofing treatments with glass fibre tissue reinforced bitumen IS 1346 (1991): Code of Practice for Waterproofing of Roofs with Bitumen Felts Code of Practice/Standards of Waterproofing There are more standards and effective test methods to ensure that the waterproofing product being used would last for the specified lifetime and purpose For elastomeric coatings following properties assume utmost importance, 1. Tensile Strength, Elongation and recovery after extension. (ASTM D 638) 2. Crack Bridging ability (ASTM C 1305) 3. Tear Strength (ASTM D 624) 4. Adhesion in wet and dry conditions (ASTM D 7234, 719 and 794) 5. Water Vapour Permeability (ASTM E 96) 6. UV Resistance (ASTM D 4587, 5894, 6695) History of Waterproofing Fight against the elements has been a constant battle for homeowners since the dawn of civilization. The history of waterproofing stretches as far back as 13,000 years, and is considered the third oldest trade behind carpentry and masonry. Yet, professional waterproofing contractors are still seeking to innovate. When humans felt the need and desire to protect their shelters from the elements, such as storms, rains, winds, trying that way to enhance their ability to survive from Nature elements. History of Waterproofing The Agricultural Revolution Techniques protecting agriculture surplus is invented, as the excess grain from the harvests needed to be stored and protected from moisture During this period, Straw and clay were some of the first materials used for waterproofing. Ceramics were developed and they were coated with bitumen to make them waterproof and suitable for the drainage and transport of liquids, History of Waterproofing The Neolithic Period They used a bitumen emulsion with peat bogs to seal the primate boats that allowed exploration, fishing, and trading with the rise of water transportation Therefore the boats became waterproofed allowing the civilization to use the watercourses more efficiently then before. History of Waterproofing Ancient Egypt In Ancient Egypt (around 3600 BC), the Egyptians built The Great Pyramid of Giza using bitumen emulsion that was applied in coats with dry reed fibre applied in cross layers on the limestone foundation blocks. By using bitumen mixed with resins they manage to keep both the mummies and the sarcophagi in excellent preservation. History of Waterproofing Roman Era The Romans also used waterproofing techniques in their housing constructions and public buildings such as Thermal Baths, Theaters, and Amphitheaters, Aqueducts and Temples. They used robust walls in order to guarantee their waterproofing, which made them endure until the present day in very good condition. History of Waterproofing Medieval Times In the XIII Century, the use of lime as a waterproofing element was resumed to waterproof some edification and also castles, fortifications or small towns that were not geographically protected, which during its construction were regularly coated with lead or thick bitumen glued to ensure its waterproof. Waterproofing Systems Positive Side Waterproofing Waterproofing systems that are applied on the same side as the applied flow of water are known as positive side waterproofing systems. It provides protection to RCC structures against chemical attacks. Waterproofing Systems Positive Side Waterproofing It arrests lateral migration of water in RCC. Hence, the source of leakage can be known. Positive waterproofing is preferable over negative waterproofing when it comes to safeguard structure integrity. Waterproofing Systems Negative Side Waterproofing Waterproofing systems that are applied on the opposite side as the applied flow of water are known as negative side waterproofing systems. Waterproofing Systems Negative Side Waterproofing Because the positive side was difficult to access and the backfill or protective layers required to be removed, these systems were adopted in repair procedures. Because of their ease of use, these systems are favoured over the positive side. Design Aspects - Waterproofing Systems Ideally, a waterproofing should be Strong Flexible Tear-resistant and Elastic so that it can stretch to cover cracks and also move with the building. If the membrane is to be exposed to the sun, then it should be UV stable. The membrane should be flexible enough to take any shape it is laid over, and be capable of turning up and over walls and other construction features. Design Aspects - Waterproofing Systems Depending on the surface condition, following waterproofing systems can be adopted: I. Completely dry surface: Solvent based coatings, epoxies, polyurethanes etc. II. Little damped surface: Cement based systems, water based acrylics and bituminous emulsions, waterproofing mineral slurries etc. Design Aspects - Waterproofing Systems Repair quality is affected by a number of factors mentioned below: ➔ Adhesion of new system applied over existing substrate ➔ Properties of the new system compared to the old system ➔ Durability ➔ Curing of restored area ➔ Tolerance to shrinkage Selection Criteria - Waterproofing Systems Following are the factors that influence selection of waterproofing product: Presence of ground water table. Inclination of terrace. Accessibility during treatment and under service conditions. Aesthetics requirement. Selection Criteria - Waterproofing Systems Following are the factors that influence selection of waterproofing product: Atmospheric conditions such as temperature, humidity etc. Whether the substrate is designed to carry load. Type of surface. Material Properties Product must be impermeable enough to make the structure waterproof. Better flexibility and elasticity to counter thermal stresses and other stresses. High bonding and adhesive properties to ensure product sticks with surface. Material Properties Breathing properties to maintain diffusion of water vapour. Abrasion resistant if used as a topcoat. Ease of application and free from solvents to an extent. Economical Good resistance to algae, fungus and other microbial attacks. Waterproofing Systems Points to keep in mind: Identifying potential sources of leakage Designing waterproofing systems to tackle these potential locations. Each part of the system to be compatible with other systems or construction processes Membrane should be UV Stable Waterproofing Systems Ideally, a waterproofing should be strong, flexible, tear-resistant and elastic so that it can stretch to cover cracks and also move with the building. The membrane should be flexible enough to take any shape it is laid over Capable of turning up and over walls Waterproofing Systems The following waterproofing products are commonly used in construction: Cementitious Waterproofing Liquid Waterproofing Membrane Bituminous Membrane and Coatings Polyurethane Liquid Membrane Waterproofing Systems Cementitious waterproofing system Often used in the internal wet areas such as toilets. Usually a rigid or semi-flexible type waterproofing, but since it is used in internal areas such as toilets, it is not exposed to sunlight and weathering. Thus cementitious waterproofing does not go through a contract and expansion process. Waterproofing Systems Cementitious waterproofing system Used in Water Treatment Plants Sewage Treatment Plants Bridges Tunnels and Dams Railway & Subway Systems Marine Cargo Ports & Docks River Locks/Channels & Concrete Dykes Parking Structures & Lots Tunnels etc Waterproofing Systems Liquid waterproofing membrane system Liquid membrane is a thin coating which consists of usually a primer coat and two coats of top coats which are applied by spray, roller, or trowel. It offers more flexibility than the cementitious types of waterproofing Durability depends on the polymer used for the making Waterproofing Systems Liquid waterproofing membrane system Benefits: Cost-effectiveness High performance (elongation) Encapsulation Safety Easy Application Waterproofing Systems Bituminous coating Bituminous coating is also called asphalt coating. The most common applications include areas that are beneath screed wet. It is an excellent especially on surfaces such as concrete foundations. Used to form a flexible and vapour proof protective coating, depending on the formulation and grade of polymerisation. Waterproofing Systems Bituminous coating It have the following properties: Good adhesive properties Corrosion resistance Strong, waterproof, durable and economical Resists harsh chemicals and UV light Waterproofing Systems Bituminous membrane waterproofing Popular method used for low-sloped roofs It have torch on membrane and self-adhesive membrane. 1. Self-adhesive compounds comprise asphalt, polymers and filler; additionally, certain resins and oils may be added to improve adhesion characteristics. Has low shelf life as bonding properties of the membrane reduces with time. Waterproofing Systems Bituminous membrane waterproofing 2. Torch on membranes have exposed and covered types. Exposed membrane often has mineral granular aggregate to withstand the wear and tear of the weathering and the other types of membrane Contractor need to apply one protective screed to prevent the puncture of the membrane. Waterproofing Systems Bituminous membrane waterproofing: Features High puncture and fatigue resistance. Good heat resistance. Good dimensional stability under tension. High tensile and tear strengths. High chemical resistance. Waterproofing Systems Bituminous membrane waterproofing: Features Excellent resistance to positive water and vapour pressure. Can accommodate structural movements because of excellent flexibility. Available in rolls in different thickness Waterproofing Systems Polyurethane liquid membrane waterproofing Used for the flat roof area and exposed to weathering. This waterproofing method is expensive. It can offer higher flexibility. Waterproofing Systems Polyurethane liquid membrane waterproofing Polyurethane is very sensitive to moisture content present. Therefore before application, one has to be very careful evaluating, otherwise peeling or de-bonding of membranes may happen after some time. Waterproofing Systems Polyurethane liquid membrane waterproofing Used in the following type of structures: Roofs, Balconies & Terraces Wet Areas Water Tanks / Ponds Pedestrian Decks Parking Decks / Bridges Detail & Decorative Waterproofing Polyurethane Foamed Roofs Waterproofing Materials Waterproofing membranes are made from several one or more layer materials such as Rubber and Elastomer Polyethylene and Polypropylene Bitumen Polyvinyl chloride (PVC) Polyurethanes Silicate Bentonite clay Waterproofing Materials Waterproofing membranes are made from several one or more layer materials such as Ethylene propylene diene monomer rubber (EPDM) Fabrics Fiberglass Resin coatings, Plastic sheeting, Polymer liners, mastics and metal sheet etc. Waterproofing Materials - Properties Most Important Property - Water Absorption Rate - Below 4% Thickness of the Material - Uniform - making the application even and easy Smooth, liquid-only appearance provides a monolithic application with no seams and therefore no weaknesses for cracks to form Waterproofing Materials - Properties Thus waterproofing material should have Water-tightness Flexibility Crack-bridging ability Bonding strength Breathability Insulation characteristics Waterproofing Materials - Properties Resistance to ○ UV radiations ○ Microbial attacks ○ Fungus growth ○ Mechanical stresses Cost effectiveness etc However, it is quite difficult to have all the above properties in one material and therefore a judicious combination of materials has to be used to suit individual requirements Waterproofing Systems - Other Classifications Waterproofing can be classified based on following parameters: 1. By areas of application 3. By water ingress medium a. Substructure a. Integral b. Superstructure b. Barrier 2. Type of material a. Preformed membrane b. Liquid/Slurry applied systems c. Injection systems d. Impregnation/sealers e. Integral additives Waterproofing Systems - Other Classifications Most waterproofing materials can be generally classified as 1. Preformed membranes Available usually in roll forms such as modified bitumen, PVC, TPO, ECB and other thermoplastic materials as well as EPDM, Butyl Rubber etc 1. Liquid Applied Also known as specialised coatings such as acrylics, epoxies, polyurethanes and polyisoprenes. Either water-based or solvent-based, single or two-component. Waterproofing Systems - Other Classifications Most waterproofing materials can be generally classified as 3. Power based systems Powder-Based systems such as concrete additives and admixtures, reactive pore- filling chemicals. It is very strong integral waterproofing for both concrete and plaster. Waterproofing Systems Comparison between Preformed membranes and Liquid Applied Preformed Membranes Liquid Applied Membrane quality consistent Quality depend on storage Thickness is standardised regardless of Thickness depend on roof surface profile surface profile. More tolerant to contamination on Requires clean and dry substrate before substrate application Considered water tight once laid Requires multiple coats to dry Joints can be potential weakness Generally considered as seamless Higher skill level in application Easy application - rollers, brush or spray Do’s & Don’ts Don't store/keep sharp objects near waterproofing membrane Avoid mixing foreign material like water to the LAMs or Cementitious waterproofing products to get better workability. Do’s & Don’ts Do ensure to properly cure the waterproofing system. Make use of cover blocks to place rebars over membranes. Do’s & Don’ts Mix the components of waterproofing products accurately as mentioned by the manufacturer. Surface must be prepared before application of a waterproofing product. Do’s & Don’ts Application of waterproofing products, especially Polyurea/Polyurethanes, must be carried out in suitable conditions. Proper pressure and temperature of spray guns must be maintained before application of Polyurea/Polyurethane. Testing Of Waterproofing Products As a porous material, concrete can allow water to migrate through, corroding steel reinforcement, bringing in harmful chemicals and creating general livability issues. This is why most construction industry professionals use some sort of waterproofing product to protect their concrete structures. Testing Of Waterproofing Products So how do you know if your waterproofing product actually works? There are two methods commonly used to determine if concrete is waterproof: absorption and permeability testing. These tests take into account how integral systems actually work. Testing Of Waterproofing Products Absorption test: Useful for concrete under non-hydrostatic conditions, such as above ground concrete that primarily needs protection from rain. They are applicable to hydrophobic products, which are designed to repel water from the concrete surface. Testing Of Waterproofing Products Permeability tests: Products that are required to resist water under pressure must be evaluated using this testing method. The most effective way to test an integral system’s ability to resist water penetration is through a permeability test. They determine how deeply the water has penetrated and whether crystal growth has started to occur. Testing Of Waterproofing Products Remember that these test methods are comparative. No matter which method you use, be sure to test the waterproofing agent against an identical plain concrete sample, using the same proportions of cement, aggregates and water. Testing Of Waterproofing Products Historically, Methods for testing of horizontal membranes Spray testing Flood testing Capacitance (impedance) testing Nuclear metering, and Infrared (IR) thermal imaging. Testing Of Waterproofing Products Within the last two decades, two new methods of testing have revolutionised the leak detection and integrity testing industry. 'Low Voltage Electrical Conductance Testing' and 'High Voltage Spark Testing'. Testing Of Waterproofing Products In general it can be classified as Integrity Testing: 1. Low Voltage Testing 2. High Voltage Testing 3. Flood Testing 4. Spray Testing Testing Of Waterproofing Products In general it can be classified as Moisture Detection: 1. Capacitance Testing 2. Infrared Thermography 3. Nuclear Meter Quality In Waterproofing Waterproof engineering in our country has developed by leaps and bounds, which is manifested by the rapid development of varieties in waterproof material industry, the vigorous research and development of new products, the introduction and use of advanced technology and equipment from developed countries, Increased level of production rate Quality In Waterproofing Key points for Quality Control 1. Roof waterproofing Design, selection of waterproof materials, roof structural details and other factors Design of the drainage system is unreasonable and the position of the drainage outlet is not correct. The slope of the drainage can’t meet the use of needs, which makes the drainage system can't timely and effectively discharge the rainwater Quality In Waterproofing Key points for Quality Control 2. Basement waterproofing The construction joint is the important reason which causes the building basement waterproof seepage. Therefore, reduce the artificial construction joint and adopt the construction joint treatment technology Quality In Waterproofing Key points for Quality Control 2. Basement waterproofing Deformation joints include expansion joints and settlement joints. Therefore, the treatment measures of deformation joints can be treated by filling joints and sealing construction measures. Quality In Waterproofing Key points for Quality Control 3. Waterproof works in toilets, baths and kitchens Pay attention to the thickness of the waterproof coating and painting time, because it is an important condition to ensure the quality of the project, so the thickness of the coating can’t be adjusted at will. If waterproof membrane is used, it should be relatively light and thin and has a good adhesion with the base materials, and to prevent the occurrence of hollowing. Safety Measures - Safety Concerns Primary safety concerns that go along with waterproofing Flammable materials: Many waterproofing products are solvent-based. Keep fire, smoking materials, welding operations, cutting torches, and other sources of ignition well away from the area. Safety Measures - Safety Concerns Respiration hazards: Use the manufacturer-recommended respirator, especially with solvent- based materials. In a close area, you might need an air- fed respirator. Don't be complacent about this. Safety Measures - Safety Concerns Respiration hazards: Solvent vapours are deadly, and a large surface area of newly applied material can put out a lot of vapour. The vapours are usually heavier than air, so they tend to build up in a sunken area like a foundation excavation. Safety Measures - Safety Concerns Skin injuries: Waterproofing materials can contain all sorts of chemicals that can harm your skin. As needed, wear protective clothing and gloves. When cleaning tools in solvent, wear chemical-resistant gloves. Safety Measures - Safety Concerns Injection hazards: Take precautions when working with or around spray equipment. A high-pressure airless sprayer can inject toxic chemicals directly into your bloodstream. Eye injuries: Wear protective glasses or goggles as needed, especially when working with liquids. Safety Measures - Personal Protective Equipments Safety Helmet Safety Shoes Rubber Hand Gloves Safety Belt Face Shield Self Breathing Apparatus Reflective Jacket Safety Measures - First Aid Measures Eyes: Irrigate immediately with copious quantities of water for several minutes. Obtain medical attention if irritation persists. Skin: Wash thoroughly with soap and water or suitable skin cleanser as soon as possible. Safety Measures - First Aid Measures Inhalation: Remove from exposure - unlikely to occur. Give artificial respiration. Seek medical advice. Ingestion: Do NOT induce vomiting. Wash out your mouth with water. Obtain medical attention. Now it’s Time for Q&A 94 Office 188/32/1, 2nd Floor, Bashyam Circle, 13th Cross Road, Sadashivnagar, Bengaluru, Karnataka -560080 Registered Office No 10 Ferns Paradise, Doddanekkundi, Bengaluru, Karnataka 560037 8861434168 www.siwinonline.com [email protected]