Documentation & Records PDF
Document Details
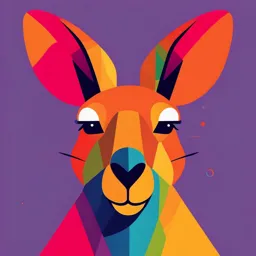
Uploaded by CharismaticHydrogen
Al-Zaytoonah University of Jordan
Tags
Summary
This document provides guidelines on pharmaceutical manufacturing documentation (PMD). It explains the importance of PMD, its objectives, steps for development, different types of documents, and procedures for handling and managing them.
Full Transcript
Documentation & Records Introduction Pharmaceutical Manufacturing Documentation (PMD) is a really complex subject. It may be very difficult to make a consolidated list of documents, which will meet the requirements of all the companies. For this you have to evaluate the need...
Documentation & Records Introduction Pharmaceutical Manufacturing Documentation (PMD) is a really complex subject. It may be very difficult to make a consolidated list of documents, which will meet the requirements of all the companies. For this you have to evaluate the needs of each company. Hence, one cannot think of a readymade solution for PMD for every one all alike, but it has to be tailor made. One needs to carefully study the organizational factors before designing the PMD for a specific organization. Introduction For this purpose following organizational factors need to be considered: Manufacturing activities undertaken or planned by the organization i.e. which formulations are being produced or likely to be produced like Injections, Tablets, Capsules, Liquids, Ointments etc. Which country's requirements of documentation the company needs to fulfill e.g. Jordan, WHO, UK, USA, Australia, Canada or any other? Level of computerization in the organization available for use of documentation. Any other consideration. Steps in TMD Program The total PMD program if tackled systematically then this complex task can become simple and manageable. The following way is proposed to tackle the total PMD program in the organization. Step 1: Identify at least two fairly knowledgeable persons, one each from production and QC/ QA who are familiar with organization product profiles and QC/ QA requirements etc. Step 2: List out the manufacturing formulation departments, existing or planned. Step 3: List out the QC/ QA activities, sections wise. Step 4: List out countries to which the products are likely to be sold/ distributed and collect the specific PMD requirements if any, of each of the countries. Steps in TMD Program Step 5: Categorize the sets of documents needed to meet the requirements as listed in step 4 e.g. the categorization should be on the following lines: First: (a) Documents required for personnel training. (b) Documents for QC. (c) Documents for Building/ Factory. (d) Documents for Equipment. (e) Documents for Materials/ Stores. (f) Documents for Engineering. (g) Documents for Distribution. (h) Documents for Market complaints etc. Steps in TMD Program Second: Documents in each of the categories then can be split into the following types: (a) SOP's. (b) Lists. (c) Charts/ formats. (d) Specifications. (e) Test Methods. (f) Reports. (g) One time and recurring documents like MPCR and BPCR etc. Steps in TMD Program Step 6: Design the documents - Considering the following points e.g. Contents. Formatting. Size and quality of papers etc. Step 7: Explain the document to concerned people. Train them in using the same. Step 8: Trial run the documents, study the difficulties, modify and re- design if required. Step 9: Implement the document. Step 10: Review by receiving feedback from the user at regular intervals. Guidelines for Designing and Implementing PMD Program Following are few guidelines presented for those who deal with PMD designing, and implementing in any organization. 1 Definition of document: Document is any written statement or proof. 2 Objectives of documentation: 2.1 Define the manufacturers system of information and control. 2.2 To minimize the risk of misinterpretation and errors inherent in oral or casual written communication. 2.3 To provide unambiguous procedures to be followed. 2.4 To provide confirmation of performance of a task. 2.5 To allow calculations to be checked. 2.6 And finally to allow tracing of the batch history of any product. Guidelines for Designing and Implementing PMD Program 3 Importance of documentation: 3.1 Good documentation is an essential part of the quality assurance system and as such should be related to all aspects of cGMP. 3.2 It defines the specification for all materials and methods of manufacture and control. 3.3 It ensures that all personnel concerned with manufacture know, what to do? how to do? when to do? and why to do? etc. 3.4 It ensures that authorized persons have all the information necessary to decide, whether or not to release a batch of a drug for sale or distribution. 3.5 It provides an audit trail that will permit investigations of the history of any suspected defective batch. Guidelines for Designing and Implementing PMD Program 4 Preparation, issue and use of documents: 4.1 Each document should indicate or include: The user's company or trading name. Purpose and title of document. Document identity number which uniquely identifies the document and indicate revision if any. Date of authorization. Date of expiry or review (in case of SOP's etc.). Signature of authorizing persons and where different, the signature of the person who prepared the document. The distribution list, where copies are distributed. Page numbers (and number of total pages). The way in which the document is to be used, and by whom, should be clearly apparent from the document itself. The reason for revision should be documented. Reference used for preparation of the document if any. Guidelines for Designing and Implementing PMD Program 4.2 Issued documents should not be hand written. In the case of batch documents each must be initialed to indicate a verified issue. 4.3 Any correction made in a document should be initialed or signed and dated and the correction should permit the reading of the original information. Where appropriate, the reason for the correction should be recorded. Guidelines for Designing and Implementing PMD Program 4.4 Documents which require the entry of the date or additional information should: Provide sufficient space for the entry. Clearly indicate what is to be entered. Where any issued document required the entry of data or additional information, entries should be hand written clearly and legibly in permanent ink. If a handwritten entry is corrected, the correction should permit reading of the original entry and should be initialed by the person making it. Guidelines for Designing and Implementing PMD Program 4.5 Where documents bear instructions they should be written in the imperative, i.e. as a direct command as numbered steps. They should be clear, precise, unambiguous and in plain language that the user can understand. 4.6 Documents should be kept up to date. Any amendments should be formally authorized before the document is used. In the case of permanent amendments, the amended document should be replaced at the earliest opportunity by a newly prepared document and superseded document so marked and filed. Guidelines for Designing and Implementing PMD Program 5 Product traceability: 5.1 A system should be in operation where, by the complete and up to- date histories of all batches of products from the starting material to the completed forms are progressively recorded. The system should be adequate to determine the utilization and disposition (including destruction) of all starting materials and products. 5.2 Sales and distribution records should be readily available, complete and easy to follow as to expedite the recall of goods wherever necessary. Guidelines for Designing and Implementing PMD Program 6 Storage and retention of documents and records: 6.1 Except where legislation require longer retention periods, the complete records pertaining to each batch, including original data such as laboratory note books, should be retained for at lest one year after the expiry date of the batch. 6.2 Paper or film records should be stored to a restricted access area. Records should be protected from tempering or loss. 6.3 Records may be retained by computer storing system. 6.4 Records may be retained on microfilms or microfiche. Guidelines for Designing and Implementing PMD Program 7 Retrieval of document: All documents should be stored in the department in such a fashion that their retrieval is easy. For this purpose following system may be adopted: 7.1 A total list (may be alphabetical) of documents should be made. This list should show: The name of the document. Location of availability. Person to be contacted for retrieval. 7.2 Any document on demand should be made available to the demanding authority in reasonable period of time. 7.3 Completed BPCR must always be kept under lock and key under the control of QA. 7.4 Retrieval of any MPCR and other important documents should be possible only on proper authorization of QA. Guidelines for Designing and Implementing PMD Program 8 Disposal of document: 8.1 The expired documents must be destroyed by QA with proper record and authorization by a suitable method e.g. shredding, burning etc. Specifications Specifications may be defined as a set of parameters expected to be met by a particular material, peace of equipment or any such object. In case of pharmaceutical products, we need specification for: (i) Active and inactive starting materials. (ii) Primary, printed and other packaging materials. (iii) Intermediate and bulk products and (iv) Finished pharmaceutical products. Now let us see the basic minimum requirements of each of the above categories of specification. Specifications Every specification is a company's unique document and it must have certain common contents and thereafter each type of document should have some specific contents. Let us first see the common contents in any type of document. They are as follows: (i) Name of the company and its address or location. (ii) Title of the document viz. "Specification". (iii) Unique Identification number of the specification. (iv) Date of issue and implementation (or effective date), and proposed date of review. (v) Names and signature of persons preparing, checking and authorizing the specification; in addition to date of preparation, checking and authorization, (vi) Pharmacopoeial or other references to the preparation of the specification. (vii) Circulation list of the specification. Specifications Now, let us see the specific contents of each type of specifications: (1) Specification for Active and Inactive Starting Materials These documents should contain the following things, in addition to the above mentioned common contents: (i) Name of the material. (ii) Code number reference. (iii) Pharmacopoeial reference to the specific monograph if applicable. (iv) Qualitative and quantitative requirements, physical and chemical characterization, microbiological standards and assay etc. acceptance limits, covering tests and limits for identity, purity. (v) Details of or ref to the test method to be used to assess compliance with the specification. (vi) Names of approved suppliers and original manufacturer. (vii) Direction for sampling and testing or reference to the procedures. (viii) Storage conditions and safety precautions if any. (ix) The maximum period of storage before re-examination. Specifications Specifications (2) Specification for Packaging Materials: This document should have the following things in addition to the common contents mentioned above. (i) Name of the material. (ii) Code number reference. (iii) A description of the nature, dimensions, and materials of construction of the components with quality standards, control limits, drawing and details of the test, as applicable. (iv) Details of or reference to the test methods to be used to assess compliance with the specification. (v) List of approved supplies/manufacturers. (vi) Sampling instructions. (vii) Storage conditions. (viii) Frequency of re-examination of stored components. (ix) A file of reference specimens of current printed packaging materials should be maintained. Specifications Specifications (3) Specifications for Intermediate and Bulk Product This document should have the following things in addition to the common contents mentioned above: Specifications for intermediate and bulk products should be available if these are purchased or dispatched or if data obtained from intermediate products are used in the evaluation of the finished product. These specifications should be similar to starting material or finished products as applicable. Specifications Specifications (4) Specifications for Finished Products: This document should have the following things, in addition to the common contents, mentioned above. (i) Name of the product. (ii) Code number reference. (iii) Names of the active ingredients. (iv) The formula or reference to the formula. (v) A description of dosage forms and package details. (vi) Direction for sampling and testing or reference to procedures. (vii) The qualitative and quantitative requirements with acceptance limits. (viii) The storage conditions and precautions, where applicable and (ix) Shelf life. Specifications Master Production and Control Record (MPCR) The above term is borrowed from CFR 211.186. This document is also known in various other regulatory literature as: Master Formula Record (India). Master Formulae and Packaging instructions (WHO). Manufacturing Formula and Processing Instructions (Australia). Master manufacturing instructions and Master Packaging instructions (South Africa). Master Production and Control Record (MPCR) This is a one-time document that should be prepared for each product. The purpose of this document is to assure uniformity from batch to batch. It should be dated and signed (Full, hand written signatures) by one person and independently checked, dated and signed by a second person. There should be a detailed SOP for preparation of MPCR. Master Production and Control Record (MPCR) A summary of the content of this document covering all the above guidelines is given below: The document should contain the following things: (1) The name and strength of the product and description of the dosage form e.g. Calpol 500 mg Tablets. (2) The name and weight or measure of each active ingredient per dosage unit or per unit of weight or measure of the drug product, and a statement of the total weight or measure of any dosage unit. e.g. Each tablet contains 500 mg of Paracetamol. or Each 5 ml contains -------- mg of (Active ingredient). or Each 1 gm contains -------- mg of (Active ingredient). In addition to above, it should also be stated that, what is the total weight of the tablet, capsule etc. (3) A complete list of special quality characteristics like, particle size, bulk density, color, crystalline or amorphous etc. Master Production and Control Record (MPCR) (4) An accurate statement of the weight or measure of each components, using the same weight system for each component. Reasonable variations may be permitted, in the amount of components necessary for the preparation, e.g. quantities of excipients like starch, talcum, magnesium stearate etc. (5) A statement of theoretical yield, including the maximum and minimum percentage of theoretical yield beyond which investigation is required. For this purpose different critical stages of operation are required to be defined. e.g. granulation, compression, coating in tablets and similarly for other formulations. Based on the practical experience, state of process technology used the limits of yields at the predefined critical stages are to be decided, so that any deviation from such limits will point to the deviations in the process and need to be investigated and corrective action taken. Master Production and Control Record (MPCR) (6) A description of the drug product containers, closures and packaging materials, including a specimen or copy of each label and all other labelling signed and dated by the person or persons responsible for approval of such labelling. (7) Complete manufacturing and control instructions, sampling and testing procedures, specifications, special notations, and precautions to be followed. For ease of preparation of the document and avoiding multiplication of work, reference to the SOPs common to sampling and testing may be made, specifications also can be referred in the same fashions. However special notation to a specific product and batch size may definitely be included in this document. Master Production and Control Record (MPCR) (8) A statement of processing location and principal equipment to be used. (9) The methods or reference to methods (Reference SOPs etc.) to be used for handling with the critical equipment including cleaning, assembling, calibrating and sterilizing. (10) The requirements for storage conditions of the products, including the container, labelling and special storage conditions where applicable. (11) Details of in process controls with instructions for sampling and acceptance. Batch Production and Control Record (BPCR) Similar to MPCR this term is also borrowed from USFDA CFR 211.188. This document is also known is various other regulatory literature as: Batch Processing and Batch Packaging Record (WHO, MHRA- UK, Australia) BPCR is a recurring document. This gives complete history of the batch produced. BPCR is primarily a replica of the MPCR, additionally it gives the actual process record of the batch produced and helps in maintaining the complete production and control history of the batch. Batch Production and Control Record (BPCR) The summary of the contents of this document is given below: (i) Dates and times of all the activities, which are carried out regarding production and control of the batch. (ii) Identification of individual major equipment and lines used. Identification of specific rooms/ locations preferably with unique identification numbers should also be included. (iii) Specific identification of each batch of components or in-process materials used. (iv) Weights and measures of components used in the course of processing. (v) In- process and laboratory control results. Batch Production and Control Record (BPCR) (vi) A statement of the actual yield and a statement of the percentage of theoretical yield at appropriate phase of processing. For this purpose the appropriate stages in the manufacturing are required to be identified. e.g. granulation, compression, coating, filling etc. Pre- defined theoretical yield, when compared with actual yields, gives a correct picture, whether the process is going on as desired or has gone wrong somewhere. (vii) Inspection of packaging and labelling area before and after use. (Line clearance records should be incorporated). (viii) Complete labelling control record, including specimens or copies of all labeling used. 'Labelling' here means all the printed packaging materials. Record of this proves that all correct printed packaging materials are used and they were correctly overprinted, wherever required. Batch Production and Control Record (BPCR) (ix) Description of drug product containers and closures; this should include primary, secondary and printed packaging materials. (x) Any sampling performed, during the production and /packaging activities. (xi) Identification of persons performing and directly supervising or checking each significant step in the operation. (xii) Any investigation made regarding any unexplained discrepancies including yield variations etc. or other deviations if any should be recorded and authorized. (xiii) Results of examinations made (as per CFR 211.134). Important SOPs and Records The regulatory guidelines enlist certain important/ critical SOPs and documents, which should be maintained. The list of such SOP and documents is given below for ready reference: SOP for receipt, sampling, storage, and dispensing of materials like, R.M./P.M. SOP for all instruments and equipment. Covering, operation, maintenance and cleaning of the same. Calibration SOPs should be incorporated where necessary. SOP on batch numbering. Standard Test Procedures for testing materials and products at different stages of manufacturing. Important SOPs and Records Records of analysis carried out. SOP and Records for equipment assembly and validation. SOP and Records for facility cleaning, sanitation and maintenance. SOP and Records for personnel matters related to qualification, training, clothing and hygiene. SOP and Records related to environmental monitoring SOP and Records related to Pest Control. SOP and Records related to handling of product complaints. SOP and Records related to product recalls and returns. SOP and Records related to finished product distribution. Log books for recording the use, validation, calibration, repairs and maintenance, cleaning and operation of the major equipment. SOP and Records for Retention and disposal of records. Important SOPs and Records Change Control Change control may be defined as a system of procedures through which changes are reviewed, justified, documented, approved and implemented in conformances with regulatory and corporate requirements. Change control hence prevents changes that could adversely affect product quality or conflict with registration or regulatory requirements/commitments. Change control systems today are expected to be designed in a way also to anticipate change within the quality organization based on some indicators such as: (i) An inordinate number of rejects means the process has shifted and the cause must be found. (ii) Product complaints are another indication that need changes to be implemented with appropriate review and approval. Change Control While considering the management of change control, one should also try to understand the difference between planned and unplanned changes. Unplanned changes are actually deviations and should be considered as deviations, and should be addressed appropriately using "deviation control procedures". Planned changes are in fact, the real changes that the change control system should be designed to anticipate, and effectively resolve. The quality management unit plays a big and major role in the management of change control procedure. The quality management unit reviews the proposed changes for adequacy and appropriate rationale to determine requirements needed to implement the change. The unit should provide final approval for the change. Change Control Although the quality unit manages change control, the other organisation units within the company coordinate change control. Any well-managed quality system requires a documentation counterpart. For change control, just as with other document driven quality system like deviation investigations, a well designed form should allow unique identification of changes for track and monitoring purposes, and ideally be easily accessed by groups when needed. The changes control form should allow designated fields for the description of the change, justification for the proposed change, classification of the change, and approval of the change. For effective implementation of the change control system, all the concerned people should be trained in its implementation. Site Master File Site Master File (SMF) is a document, which gives a complete and factual information regarding a site of pharmaceutical manufacturing plant. This document should generally be not very massive, like running into more than 100 pages, at the same time it should not be very brief. Even though the formats for such a document varies from country to country; the generally accepted format contains following topics: Site Master File 1.0 General Information: 1.1 Brief information about the organisation. 1.2 Name and address of the site. 1.3 Description of the site. 1.4 Pharmaceutical manufacturing activities. 1.5 Other manufacturing activities. 1.6 Types of products manufactured at the site. 1.7 Employees details. 1.8 External technical assistance. 1.9 Quality Management System. Site Master File 2.0 Personnel: 2.1 Organisation chart. 2.2 Qualification, experience, and responsibilities of key personnel. 2.3 Training. 2.4 Health requirements for personnel engaged in manufacturing. 2.5 Clothing. Site Master File 3.0 Premises and Equipment: 3.1 Description of manufacturing area. 3.2 Nature of construction and finish. 3.3 Brief description of ventilation system (HVAC system). 3.4 Special areas. 3.5 Water system. 3.6 Maintenance of premises. 3.7 Major production and laboratory equipment. 3.8 Maintenance of equipment. 3.9 Calibration system. 3.10 Sanitation. Site Master File 4.0 Documentation: 4.1 Preparation, Revision and Distribution of documents. 4.2 Other documents related to product quality. 4.3 Additional documents. 5.0 Production: 5.1 Brief description of production operations. 5.2 Handling of materials. 5.3 Handling of rejected materials and products. 5.4 Brief description of general policy for process validations. 6.0 Quality Control: 6.1 Quality Management System. Site Master File 7.0 Contract Manufacture and Analysis and other services: 7.1 Contract Manufacture. 7.2 Contract analysis. 7.3 Contract services. 8.0 Post Operational Activities: 8.1 Product distribution. 8.2 Handling of product complaints. 8.3 Product recall. 9.0 Self inspection 9.1 Self inspection program. 10.0 Export of Drugs: 10.1 Products exported to different countries. 10.2 Complaints and product recalls if any.