GMP Lecture 1 PDF
Document Details
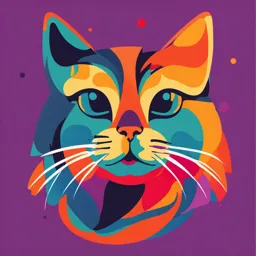
Uploaded by EducatedDalmatianJasper
Tags
Summary
This document provides a lecture on the principles of Good Manufacturing Practices (GMP). It covers 10 key principles related to GMP, including procedures, documentation, and quality assurance in manufacturing.
Full Transcript
LECTURE 1 INTRODUCTION Principles of GMP Good Manufacturing Practices (GMP) are a set of principles that systematically minimize risks associated primarily with pharmaceutical and medical device production in order to ensure the purity, safety, and efficacy of the products. Theregulations...
LECTURE 1 INTRODUCTION Principles of GMP Good Manufacturing Practices (GMP) are a set of principles that systematically minimize risks associated primarily with pharmaceutical and medical device production in order to ensure the purity, safety, and efficacy of the products. Theregulations that govern GMP require a quality approach to the manufacture of these products, such that errors, mix-ups, and contamination are minimized. Theultimate goal of GMP is to protect consumers from potentially dangerous or ineffective products. 10 Principle of Good Manufacturing Practices Good manufacturing practices is part of quality assurance which are particularly set of guidelines including basic control measure and procedures to be followed to meet standard specification of product which are safe to consume by human. These regulations address a variety of areas, including cleanliness, personnel qualifications and record-keeping, all in an attempt to ensure safety in the manufacture and care of FDA- regulated products by minimizing the chance of contamination or human error. To follow good manufacturing practices there are 10 basic principles which need to be addressed. PRINCIPLE 1: Step by step written procedures Alloperating procedures and work instructions should be written down and made available to employees for better understanding of the facility working procedures. Standard operating procedures are established methods that are to be followed routinely for the performance of the designated operations. PRINCIPLE 2: Follow procedures Inthe drug and food industry it is critical that good procedures are in place to ensure a controlled and consistent performance. Written procedures are to be concise and logical so that it is easy to follow and understand. While following SOP or written procedure it is important to mark that no shortcuts should to be taken as they lead to deviation from the procedure which may lead to hazards. PRINCIPLE 3 Document work Prompt and accurate documentation of work provides official information or serves as a record helping in compliance and traceability. Incase of error, these records can serve as the basis of investigation. E.g. Equipment user manual, GMP Manual PRINCIPLE 4 Validate work Establishingdocumentary evidence that the procedure, process or activity and production maintains the desired level of compliance at all stages. Maintaining and validating of consistent performance is very important and following written procedures is necessary. PRINCIPLE 5 Integrate productivity, quality & safety into facilities & equipment During construction of company facility and equipment it is important to integrate productivity, quality & employee safety. Designing and assigning location of equipment should suit its intended use. Product quality is impacted by factors like air, water, lightning and ventilation temperature. PRINCIPLE 6 Maintain facilities & equipment Propermaintenance schedule prevent equipment breakdown, reduces risk of product contamination and maintain the validated state of the facility or equipment. PRINCIPLE 7 Define, develop & demonstrate job competency Eachemployee should be provided with training whose activities could affect product quality. Training should be inclusive of basic training on theory & practice of GMP. Employees should demonstrate job competence by producing quality products in a safe & efficient manner. PRINCIPLE 8 Make cleanliness a daily habit This principle outlines the importance of ensuring a product to be protected from contamination by practicing good hygiene. This can be achieved by incorporating cleanliness in the workplace. All cleaning and sanitization procedure should be followed. Contamination may be physical, chemical or microbiological in nature. PRINCIPLE 9 Build quality into the product Every step in the products life cycle requires effective controls to ensure the quality of the product which can be achieved by controlling components, controlling the manufacturing process, packaging & labeling controls and distribution controls. Allcomponents of the product should be identified and stored in quarantine area for sampling & testing. For Controlling manufacturing process all product should have master record outlining specification with individual batch/history record. To enable traceability assigning batch no. to all products inspecting packaging & labeling before processing. PRINCIPLE 10 Conduct compliance & performance audits Only way to determine how well GMP is being implemented is to conduct planned and periodic audits. Audits must be conducted to assess whether the facility is following GMP. Audits can be internally held to ensure GMP compliance by in house audits or external audits can be conducted by external bodies.