Wax Patterns PDF
Document Details
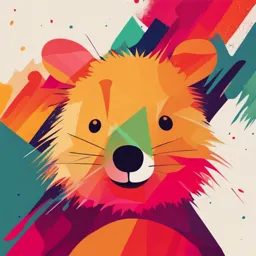
Uploaded by WiseAlgorithm
Batterjee Medical College
Dr. Wayel Mohammed Huraib
Tags
Related
- DEN203 Prosthetic Dentistry II - Record Base and Wax Rim Fabrication PDF
- DEN203 Prosthetic Dentistry II Lecture Notes PDF
- Prostodontics III: Materials Used in Edentulous Patients - Lecture 7 PDF
- Non-Metallic Denture Base Processing PDF
- Impressions in Fixed Prosthodontics Lecture 1 PDF
- Color and Optical Effects in Restorative and Prosthetic Dentistry PDF
Summary
This document provides a comprehensive overview of wax patterns in dentistry. It details the lost-wax process, emphasizing the crucial role of wax patterns in creating accurate cast restorations.
Full Transcript
Wax Patterns Wax patterns are crucial in fabricating fixed prostheses. They form the basis for the lost-wax process, a technique used to create accurate cast restorations. Dr. Wayel Mohammed Huraib Fixed Prosthodontics I Prosthodontics Division Dentistry Program The Lost-Wax Proces...
Wax Patterns Wax patterns are crucial in fabricating fixed prostheses. They form the basis for the lost-wax process, a technique used to create accurate cast restorations. Dr. Wayel Mohammed Huraib Fixed Prosthodontics I Prosthodontics Division Dentistry Program The Lost-Wax Process Impression 1 An accurate impression of the prepared tooth is obtained. 2 Casting A cast is made from the impression. Wax Pattern 3 A wax pattern resembling the final restoration is shaped on the cast. 4 Investing A mold is made around the wax pattern using refractory investment material. Completing the Lost-Wax Process 1 Wax Elimination The wax is vaporized in an electric furnace. 2 Casting The hollow mold is filled with molten casting alloy. 3 Retrieval The metal casting is retrieved and excess metal is removed. 4 Finishing After polishing, the cast restoration is ready for clinical evaluation. Dimensional Accuracy in Casting 1 Metal Shrinkage As the solidifying metal cools, it shrinks. 2 Mold Expansion Precisely controlled expansion of the mold balances the metal shrinkage. 3 Wax Advantages Wax is used for patterns due to its ease of manipulation and shaping. Historical Context of Lost-Wax Technique 1 Ancient Origins First bronze castings reportedly made in the third millennium B.C.E. 2 Ancient Artifacts Chinese bronzes, Egyptian deities, and Greek statues were created using this method. 3 Early Use Possibly used in Sumer as early as the Second Early Dynastic Period. Importance of Wax Handling in Dentistry Precision Every defect in the wax will appear in the casting. Correction Most defects are easily corrected in wax, but not in metal castings. Evaluation Careful evaluation of the pattern under magnification is crucial. Correcting Defects in Wax Patterns 1 Undercuts 2 Blocking Out 3 Materials Small undercuts on the die can Defects can be blocked out on Zinc phosphate cement or prevent pattern removal. the working die if not near commercial resin products can margins. be used for blocking out. Luting Agent Space Purpose Ideal Dimension Margin Adaptation Space between casting and tooth 40 to 80 μm total for complete 1 mm band of close adaptation at surface allows for luting agent and crown. margin prevents luting agent complete seating. disintegration. Consequences of Improper Luting Agent Space Too Narrow Casting doesn't seat properly due to hydraulic pressure from luting agent. Too Wide Casting is loose, resistance form reduced, position difficult to maintain. Longevity Wide space increases risk of crown loosening and reduces longevity. Factors Affecting Luting Agent Space 1 Impression Material Choice affects thermal and polymerization shrinkage. 2 Die Material Solid cast with individual stone dies affects space. 3 Wax Pattern Internal layer of soft wax can increase space. 4 Investment Expansion of investment mold affects space. Increasing Luting Agent Space Impression Shrinkage Increased thermal and polymerization shrinkage of impression material. Die System Use of solid cast with individual stone dies. Wax Layer Use of internal layer of soft wax in pattern. Die Spacers Application of die spacers. More Factors Increasing Luting Agent Space Investment Expansion Increased expansion of the investment mold. Metal Removal Removal of metal from fitting surface by various methods. Pattern Manipulation Stretching of pattern during manipulation. Reducing Luting Agent Space 1 Impression Material Reduced thermal and polymerization shrinkage of impression material. 2 Die Material Use of resin or electroplated dies. 3 Alloy Selection Use of alloys with a higher melting range. 4 Investment Reduced expansion of the investment. Identifying Casting Fit Problems On Die Evaluation On Tooth Evaluation Issues may be due to wax distortion, flash, improper Consistent seating problems. investment expansion, or casting nodules. Die Spacer 1 Purpose Increases cement space between axial walls and restoration. 2 Application Painted on die, maintaining constant thickness. 3 Margin Area 1 mm band near preparation margin left unpainted for adaptation. 4 Maintenance Thinner provided to replace evaporated solvent. Wax Cut-Back for Ceramic Veneers Process Final contour of wax pattern is cut back evenly. Thickness Usually about 1 mm is removed. Purpose Provides room for porcelain fused onto cast metal substructure. Waxing Connectors 1 Timing 2 Importance Created just before finalizing margins. Size, position, and configuration must be precisely controlled. 3 Mechanical Aspect 4 Biologic Aspect Should be as large as possible for optimal strength. Must not impinge on gingival tissues. Connector Design Considerations Position Embrasure Form Cervical Aspect At least 1 mm above crest of Must enable optimal plaque control. Shaped to a smooth archlike interproximal soft tissue. configuration. Esthetic Considerations for Connectors Placement Hidden behind esthetic ceramic veneer in anterior prostheses. Position Often placed slightly lingually for anterior prostheses. Waxing Procedure Summary 1 Sequential Order Following a sequential order helps achieve excellent results. 2 Experience With experience, steps can be combined and modified. 3 Natural Form Copying natural teeth shape is advised over redesigning from memory. Importance of Precision in Wax Patterns Accuracy Wax patterns must be highly accurate for successful restorations. Detail Reproduction Every detail in the wax is reproduced in the final casting. Quality Control Careful inspection of wax patterns is crucial. Wax Pattern Materials Types Properties Handling Various waxes are used, including Waxes should have low shrinkage Proper temperature control is inlay wax and casting wax. and good carving properties. essential when working with wax. Wax Pattern Techniques 1 Dipping Die is dipped in molten wax to create initial layer. 2 Brushing Wax is applied with a brush for precise control. 3 Flowing Molten wax is flowed onto the die with instruments. 4 Carving Final shaping is done with carving instruments. Wax Pattern Evaluation 1 Visual Inspection 2 Magnification Check for smooth surfaces and proper contours. Use magnifying tools to detect small defects. 3 Margin Check 4 Occlusal Check Ensure proper adaptation at preparation margins. Verify correct occlusal relationships and contacts. Common Wax Pattern Errors Voids Air bubbles or gaps in the wax pattern. Distortion Warping or bending of the wax pattern. Incomplete Margins Inadequate wax at preparation margins. Overcontouring Excessive buildup of wax in certain areas. Wax Pattern Finishing Smoothing Use fine instruments to smooth surfaces. Polishing Gently polish with soft materials to achieve high shine. Final Check Perform final inspection before investing. Investing the Wax Pattern 1 Preparation Clean and degrease the wax pattern. 2 Spruing Attach sprue former to the pattern. 3 Mixing Investment Prepare investment material according to manufacturer's instructions. 4 Pouring Carefully pour investment around the wax pattern. Burnout Process 1 Temperature Control Gradually increase temperature to eliminate wax. 2 Time Follow recommended burnout times for complete wax elimination. 3 Mold Preparation Ensure mold is properly prepared for casting. Casting Process 1 Metal Preparation Melt casting alloy according to manufacturer's instructions. 2 Casting Pour or inject molten metal into the prepared mold. 3 Cooling Allow casting to cool according to recommended protocol. 4 Divesting Carefully remove investment to retrieve the casting. Final Steps in Prosthesis Fabrication Finishing Remove sprues and polish the casting. Fit Check Verify fit on the working model. Quality Control Perform final inspection before clinical try-in. Documentation Record all steps and materials used for future reference. Steps By Step Blocking out undercuts on a die. Photopolymerizing resin being applied. Resin light-cured. Steps By Step Marking the preparation margin. Note that the side of the colored pencil tip is used to keep line width to a minimum. Steps By Step Starting the waxing procedure. Lubricating the die. Adapting plastic pins Steps By Step Forming the initial copings. Use a large instrument to keep the wax sufficiently hot. Ensure that previous applications are remelted as additional wax is added. Build up adequate bulk for rigidity. Steps By Step Forming the initial copings. Trim the wax very carefully to the margin. Steps By Step Wax pattern removal. sheet of washed rubber dam increases friction and aids removal. Steps By Step Evaluation. Well adapted pattern. Poor adaptation. Folds and creases (arrows) indicate that the wax was not hot enough when applied.