Electrical Installations Book 2 PDF - Chapter 4: Working on Site
Document Details
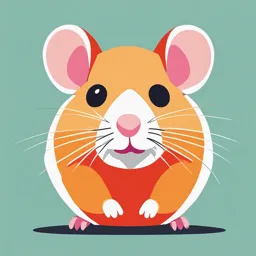
Uploaded by lectrical
Tags
Summary
Chapter 4 of the textbook focuses on planning and overseeing electrical installation work on a site. It covers the essential aspects to consider, including site organisation, safety, and customer/client service principles and site induction training. Moreover, the chapter details the planning of worksite, site services, and site restoration procedures.
Full Transcript
CHAPTER 4 WORKING ON SITE INTRODUCTION Organising and overseeing the workplace environment is a skill expected of most qualified electricians. Many electricians are expected to be able to plan electrical installation work, from the initial c...
CHAPTER 4 WORKING ON SITE INTRODUCTION Organising and overseeing the workplace environment is a skill expected of most qualified electricians. Many electricians are expected to be able to plan electrical installation work, from the initial contact with the client, through supervising others during the construction stage, to final handover to the client. For large contracts, these tasks might involve more than one person. For the majority of electrical installation work in the UK, however, one person will carry them out. The key to success within the electrotechnical industry is the ability to plan and supervise effectively. Careful planning will minimise any surprises during the work and lead to timely completion with little or no additional cost. Effective supervision will lead to reduced wastage of time and materials. Each will lead to good customer relationships, improved company image and, very importantly, a motivated and contented workforce. Above all else, good planning promotes safety. HOW THIS CHAPTER IS ORGANISED T Level mapping grids This unit covers the understanding needed to plan a worksite. Because of the way are available on the some units within 5357 and 5393 are written, some of the knowledge that belongs Hodder Education to the design unit sits here as it is much more related to planning work activities website. These map the than electrical design. As 2365 does not have a specific unit relating to planning book to the occupational the worksite, much of the understanding covered here is within the 2365-305 unit. specialisms: 8710-353 (Electrical Engineering) There is a lot of crossover of information between Chapters 3, 4 and 5 in this book. and 8710-352 The intention is to link as much learning that is unrelated to design calculations as (Electrical and Electronic possible. This will leave you prepared to focus on the design procedures in Chapter 5. Equipment). Table 4.1 shows the topics covered in this chapter. Table 4.1 Chapter 4 assessment criteria coverage 8202 Unit 301: 2365 Planning and Unit 305: Overseeing Electrical Electrical Work Topic 5357 Systems Design Activities 5393 Information: Unit 105/005: Understand 1.2 2.3 Unit 105/005: Understand Information from others How to Plan and Oversee How to Plan and Oversee Information from Electrical Work Activities Electrical Work Activities employer organisation 2.3; 2.4 2.3; 2.4 Contracts 3.4; 3.5; 3.6 Customer service principles 4.1; 4.2; 4.3 ➜ 226 9781398361607.indb 226 27/07/22 9:42 PM Chapter 4 Working on site Table 4.1 Chapter 4 assessment criteria coverage (continued) 8202 Unit 301: 2365 Planning and Unit 305: Overseeing Electrical Electrical Work Topic 5357 Systems Design Activities 5393 Planning the worksite: Unit 104/004: Understand 1.1; 1.3; 1.4; 1.5; 1.3; 1.4 Unit 104/004: Understand The work environment Design and Installation 1.6; 1.7 2.1; 2.2; 2.4 Design and Installation Site services Practices and Procedures Practices and Procedures 3.1; 3.2; 3.3; 3.4 Site meetings 1.2; 1.3; 1.4; 1.5; 1.6 1.2; 4.3 Site induction training Unit 105/005 Unit 105/005: Understand Pre-existing damage 1.4 How to Plan and Oversee Managing a safe site Electrical Work Activities Managing an efficient 2.1; 2.2; 2.5; 2.6; 2.7; 2.8; 2.9 site 1.3; 1.4 3.1; 3.2; 3.3 2.1; 2.2; 2.5; 2.6; 2.7; 2.8; 2.9 3.1; 3.2; 3.3; 3.4; 3.5; 3.6; 3.7 Site restoration: 1.7 Unit 104/004 Repair and restoration 3.6; 3.7 INFORMATION INDUSTRY TIP When planning, installing, commissioning and handing over electrical systems, a vast range of technical information is used. This information may include: Note: 5357/8202 Unit 004 topic 1.1 was covered in statutory regulations Book 1, Chapter 3. non-statutory regulations codes of practice manufacturers’ data and information wholesalers’/suppliers’ data and information client and installation specifications information from employer organisation contract information, such as drawings, charts and graphs handover information. We have covered statutory and non-statutory regulations and codes of practice in Book 1, Chapter 1. Information from others Manufacturers are responsible for providing a vast range of technical information, including: product specifications installation instructions user information safety certification. 227 9781398361607.indb 227 27/07/22 9:42 PM The City & Guilds Textbook: Electrical Installations Book 2 Product specifications It is essential that equipment is fit for purpose. Before any equipment is purchased, the buyer must check the product specification. Many manufacturers will provide this information free of charge, either in the form of a printed catalogue or data sheet, or electronically as a web page or downloadable file. In rare situations, manufacturers will only provide this information following the INDUSTRY TIP buyer making contact with a member of their sales team. Visit the manufacturer’s Product information will normally contain essential technical information. website for product Depending on the product, this may include the following. information and Dimensions – essential when considering the location of equipment. specifications. Manufacturers’ Weight – essential when considering possible fixing methods or support. websites have a large amount Loading – essential for determining circuit requirements, such as cable cross- of product information but sectional area, protective devices, maximum demands and power factor. you may need to register to Material – what the product is made of and whether the material will react access this. with adjacent materials. Connection methods – many items or products may require specialist methods of connecting cables and terminating the conductors. This, in turn, affects the selection of cable used to supply the equipment and determines any specialist tools required. Output/performance – helps you determine whether the product will perform as required and actually do what is intended. This information may be in the form of a description or, in the case of lighting, photometric data. Finish – helps you determine whether the colour or material finish is suitable aesthetically and suitable for its intended location. Associated equipment – helps you determine whether you need to purchase any further products in order for the product to perform correctly and safely. Suitability for the environment – helps you determine whether the product has a suitable international protection (IP) code rating or protection for the intended environment. Temperature – helps you determine whether the product will pose a fire risk due to high operating temperatures, and whether the product is affected by the location’s ambient temperature. All of the above information must be carefully scrutinised before any product is purchased, as an incorrect product could be costly to replace or modify. Installation instructions All but the simplest products will have installation instructions. These are normally packed with the product but may be available from the manufacturer before the product is purchased. The installation instructions will normally provide key detail, such as suitable methods of fixing and how to connect the product. A very important factor to note is that the manufacturer’s instructions will normally supersede the requirements of BS 7671. An example of this could be that a manufacturer stipulates that a particular product should be protected by a 30 mA residual current device (RCD), yet BS 7671 may not require the particular product or circuit to be protected by an RCD. In this situation, the manufacturer’s instructions should be followed over and above the requirements of BS 7671: 228 9781398361607.indb 228 27/07/22 9:42 PM Chapter 4 Working on site ‘134.1.1 Good workmanship by one or more skilled or instructed persons and proper materials shall be used in the erection of the electrical installation. The installation of electrical equipment shall take account of manufacturers’ instructions.’ (BS 7671: 2018 (2022) Regulation 134.1.1, IET) Installation instructions should ideally be researched and understood during the planning stage of any electrical installation in order to determine whether any INDUSTRY TIP further equipment is required. Installation instructions should ideally be kept by User information the installer and passed It is essential that installers of equipment pass on any user information on to the client, within any provided by a manufacturer, to the client. This will also form a critical part of operation and maintenance an operation and maintenance manual. What may seem a simple-to-use item manual for that installation, to the installer may prove complicated to the end user. An example of this is a as they may contain time switch. The installer may demonstrate the operation of the time switch to essential commissioning and a client or user, but the user may quickly forget the verbal instructions. maintenance information required later. User instructions or information will also contain information on any necessary spares or maintenance requirements for a particular product. IMPROVE YOUR ENGLISH Remember, customers are unlikely to have the technical vocabulary you have, so be sure to communicate in layman’s terms (plain English), and provide written user information. Safety certification HEALTH AND SAFETY Any electrical product must carry a mark, label, or have associated certification If you have any concerns supplied with it. This is to show that the product has been appropriately regarding electrical manufactured and tested to the product’s minimum safety standards. Caution products and equipment must be exercised if you are asked to install a product that has no visible safety and want to find out certification, if you are not sure of the product’s origin. more information, visit the Electrical Safety First Wholesalers’/suppliers’ data and information website. Many suppliers or wholesalers will pass on a manufacturer’s data, but many also produce their own paper-based and online catalogues. An electrical wholesaler will normally be able to provide verbal technical information about particular INDUSTRY TIP products. They will also have knowledge about any additional products that A big advantage of using may be needed when installing any specific item of equipment. wholesaler’s information is the ability to compare Client and installation specification products from a range of Job specifications are compiled in a variety of ways depending on the size, manufacturers. There is, complexity and contractual arrangement of a job. Generally, the specification for however, the disadvantage a project includes the following sections. that the full specification for a product may not be Preliminary information published. This first section includes details of: the client the contract administrator 229 9781398361607.indb 229 27/07/22 9:42 PM The City & Guilds Textbook: Electrical Installations Book 2 the form of contract governing the project (e.g. JCT Minor Works) further details, such as the anticipated overall contract period. In order to give some indication of all the different trades involved, a construction INDUSTRY TIP programme may also be referred to in the preliminaries. In large multi-trade projects, the preliminaries also include the cost of site set-up and maintenance of JCT Minor Works is an items, such as welfare and storage cabins, given as a cost per day or per week. example of the form of contract governing the Scope of works project. You can find The preliminaries are normally followed by a scope of works. This section examples of these on the determines the extent of the specification (i.e. the extent of what the contractor internet but it is important to has to quote a price for). If the contract is agreed, the scope of works will become ensure you are looking at UK versions. the extent of work to be carried out. For example, a simplified scope of works may be: ‘The scope of works for this project is to install electrical systems within a new two-storey extension to an existing four-bedroom house. The works will include all wiring and containment systems for power, lighting and distribution. The works will not include the intruder alarm or fire- detection systems.’ Although this scope of works immediately eliminates the intruder alarm and fire-detection systems, there will be interfaces between systems that need to be defined. These are generally included in the particular specification and drawings that follow this section. Specification of works This section describes the particular works to be carried out. It gives as much detail as possible of what the designer and client require for that particular package of works. It may consist of simple descriptions or technical requirements laid down for the contractor (tenderer) to price and eventually work to. This could include details of every circuit required or details of the equipment that needs a supply, therefore leaving the design to the company tendering. Materials and workmanship Also known as the standard specification, this section is usually the same for all projects. It comprises a list of requirements in terms of workmanship and the selection of material grades and quality, along with any applicable British Standards or industry codes of practice. Schedules This section includes drawing issue sheets that indicate which drawings have been issued as part of the tender/contract. It also contains other schedules, such as equipment schedules, containing manufacturer selections, performance requirements, sizes and weights, and distribution board schedules. Schedule of costs This is usually the final document in the specification. The contractor (tenderer) has to complete it, specifying the cost of sections of work. Daywork rates also have to be specified in case unmeasured or urgent works need to be carried out that are not already contracted and cannot reasonably be priced or measured because of time pressures. 230 9781398361607.indb 230 27/07/22 9:42 PM Chapter 4 Working on site Information from employer organisation During the planning and construction of an electrical installation, much information will be supplied to the site from your employer. This will include the client information and specification as detailed above, drawings as detailed below, and information relating to the administration of the organisation. Information from the employer organisation includes: copies of purchase orders so deliveries can be checked to ensure they are correct in quantity and type KEY TERM generic risk assessments and method statements. Many tasks that are Purchase orders: Official carried out on site are repetitive and common to all construction sites. orders that usually have The employing organisation will have devised generic risk assessments an order number which links the purchased and method statements which should require minimal revisions to suit the equipment to a specific particular construction site. This saves a lot of time for the supervisor on the contract. Purchase site, meaning that risk assessments and method statements only need to be orders have a detailed completed from scratch for tasks that are unique to that site list of materials that are further health and safety information, such as Control of Substances required, to eliminate Hazardous to Health (COSHH) data sheets the risk of incorrect equipment being regular updates and reports relating to labour, such as sickness or labour being purchased. diverted to other jobs. Contract information Numerous sets of drawings are produced to communicate information about individual systems or collections of systems within a project. They include: plans/layout drawings schematic (block) diagrams wiring diagrams circuit diagrams. Other types of information, in the form of graphs and charts, which assist in the planning and construction of an electrical installation will be covered later in this chapter. Drawings usually use British Standard symbols. However, in order to represent the wide variety of materials and equipment available, non-standard symbols may also be used. A legend or key explains them. Plans or layout drawings are used to locate individual systems within the overall project and give an indication of the scale of the project. In addition, there may be drawings to show specific fixing, assembly and/or completion LEGEND details. This is often the case where complex construction, lifting or use of a crane is required. These details may be provided in DISTRIBUTION BOARD elevation, plan or both (covered in Book 1, Chapter 3). They will then become part of the contractor’s method statement when the FUSED CONNECTION UNIT WITH INDICATOR project goes into the construction phase. TWO-WAY SWITCH MULTI-GANG SWITCH Schematic (block) diagrams M CORD-OPERATED SWITCH Schematic (block) diagrams can serve many purposes, but are 13 A SOCKET OUTLET (2 DENOTES 2-GANG) 2 primarily provided to show the overall functionality of a system, including interfaces and operational requirements. Figure 4.1 Part of a drawing legend 231 9781398361607.indb 231 27/07/22 9:42 PM The City & Guilds Textbook: Electrical Installations Book 2 Figure 4.2 Layout drawing 232 9781398361607.indb 232 27/07/22 9:42 PM Chapter 4 Working on site Figure 4.3 Basic schematic drawing Wiring diagrams Wiring diagrams are generally provided to show in detail how a system or collection of systems is put together. They show locations, routing, the length of run and types of systems cabling. These types of diagrams are sometimes mistakenly referred to when it is actually a circuit diagram that is required. 6 A lighting 1.5 mm2 6242Y kWh 25 mm2 tails 16 mm2 earthing 6243Y conductor 32 A cooker 6 mm2 6242Y 10 mm2 main protective bonding 20 A radial 32 A ring final 2.5 mm2 6242Y 2.5 mm2 6242Y 20 A radial 2.5 mm2 6242Y Branch Spur Figure 4.4 Typical wiring drawing 233 9781398361607.indb 233 27/07/22 9:42 PM The City & Guilds Textbook: Electrical Installations Book 2 Circuit diagrams Circuit diagrams contain information on how circuits and systems operate. They can be provided as detailed layouts, although some information, such as length of run, may be omitted for clarity. In most instances, circuit diagrams are used for diagnostic purposes so that designers, installers and maintainers understand how their actions may influence a particular component or arrangement. At different stages of work, the information on the drawings and diagrams is given in different levels of detail. The information becomes more detailed and accurate as the project develops. 1 2 3 ACTIVITY Figure 4.5 is a circuit CB diagram for a motor and Thermal over load relay its starter. Can you tell what type it is and how it Delta Star works? contactor contactor KM2 KM1 1 3 5 1 3 5 1 3 5 2 4 6 2 4 6 2 4 6 Main contactor KM3 U1 V1 W1 W2 V2 U2 3 Phase motor Figure 4.5 Typical circuit diagram Levels of drawing There are five main levels of drawing: sketch drawings/information design/tender drawings contract drawings working/construction drawings as fitted/installed drawings. Sketch drawings Sketch drawings are often hand-drawn sketches to help the designer demonstrate ideas and interpretations. They are usually drawn in the early stages of a project, when the scheme and designs are still fluid. They are therefore subject to change as every stakeholder is inputting to and potentially changing the scheme. 234 9781398361607.indb 234 27/07/22 9:42 PM Chapter 4 Working on site Sketch drawings are also often used at later stages of a project. Once the contractors have produced their working drawings, the designer may issue new sketch drawings for particular design details. These drawings become a KEY TERM contractual variation for that portion of the works and are recorded as a variation Residual hazards: by the contract administrator. Residual hazards are unavoidable hazards Design/tender drawings that will exist once the contract is complete These are produced by a designer to convey the main design intent of the and should be identified works. Although they are generally intended to be read in conjunction with for the client to take the specification and other written documents, it is often easier to show the reasonable precautions, geographical scope of works by hatching out areas not covered on a drawing. such as working at height, working with Design drawings are usually exchanged between designers initially to ensure electricity, etc. Although coordination and then to communicate items for consideration under the these tasks would not Construction (Design and Management) Regulations (CDM), to other designers normally be undertaken and stakeholders, including the client. by the client themselves, unless they had on-site At the design stage of a project, the designer has a duty to eradicate hazards maintenance teams, they (whether notifiable under the CDM Regulations or not) where possible. A number are identified in operation of hazards may be unavoidable and these need to be pointed out to contractors. and maintenance Residual hazards should be identified on the drawings or schedules. The Health manuals, so that others are aware of the risks and Safety Executive (HSE) prefers residual hazards or hazard-reduction strategies before work starts. to be indicated on drawings. The design drawings are then put together with any stakeholder comments and issued with the specifications and schedules as tender drawings. Details of the INDUSTRY TIP residual hazards and hazard-reduction strategies on the drawings help contractors (tenderers) to understand any potential difficulties or additional requirements During the tender procedure, for completing the task safely. Allowances can then be incorporated into the the contractor will put preconstruction health and safety plan so that construction is carried out in a safe together costs based on the manner. material required. In order to gauge the amount of material Area DB Drawing 2 efficiently, contractors will reference number normally use a take-off Ground DB-2 A-2011-3-R1 12 3 18 1 6 2 3 sheet (for example, see floor Figure 4.6). The symbols First DB-3 A-2011-4-R1 6 4 15 1 12 2 0 used on the tender drawings floor are transferred to a take-off Figure 4.6 Sample take-off sheet sheet and counted, giving the total for each piece of After the tender is awarded, the tender drawings usually form part of the contract equipment required. We will on which the scope and detail of work has been priced. The tender drawings are cover take-off sheets in more usually re-issued, containing any contractual variations made during the tender detail later in this chapter. period. They are then referred to as contract drawings. On many smaller projects the general contractor usually refers to contract drawings as construction drawings (i.e. drawings of what the contractor tendered for and will install). However, in building services engineering, contractually there is a considerable difference between a design drawing or a briefly amended contract drawing and a construction/working drawing. 235 9781398361607.indb 235 27/07/22 9:42 PM The City & Guilds Textbook: Electrical Installations Book 2 Construction/working drawings These are usually produced by the building services subcontractor. They are usually drawn at a very large scale and contain additional information not given on the previous drawings; for example, information on fixings, expansion measures, etc. This level of detail ensures installation exactly to the drawing. However, it is important that these drawings also reflect the overall design intent. Installed/fitted drawings Specialist shop drawings are a variant of construction drawings. They are normally produced so that manufacturers, suppliers and/or consultants can agree before manufacture takes place. In building services, installed/fitted drawings are normally produced by the subcontractor/installer. However, in structural engineering and certain architectural arrangements, they are provided by the structural engineer and architect respectively. This difference can cause problems and confusion. Installed/fitted drawings should represent what has been installed, but also contain information on any residual hazards and risk-reduction strategies employed and instructions on how to clean, maintain or deconstruct the works if necessary. The drawings become part of a wider set of operation and maintenance manuals. On completion of work which only involves electrical work, a specific Operation and Maintenance (O&M) manual should be provided for the electrical installation. This would include, depending on the extent of the work, key information such as: certification and test results circuit charts as-installed drawings what to do in the event of an emergency list of spare parts (lamps, fuses, types and ratings, etc.) instructions on use (timeclocks or other equipment) regular maintenance instructions (RCD test buttons, cleaning, etc.). O&M manuals should also be updated or referred to when maintenance tasks are undertaken by electricians or additions made to the installation. If maintained correctly, O&M manuals can save the client money. As a simple example, imagine that lamps need changing in one or two high bay light fittings. Getting to the lamps requires hiring special access equipment and once the fitting is accessed, it is discovered that the lamp type needed is not in stock and it will be three days until it is available. If the O&M manual is referred to first, the lamp type can be looked up and ordered before the specialist access equipment is hired, meaning the access equipment is only needed once. Maintained O&M manuals can also greatly assist in fault finding or spotting faults before they happen by referencing historical test results and seeing patterns of damage or failure. 236 9781398361607.indb 236 27/07/22 9:42 PM Chapter 4 Working on site Contracts There are legal implications that you need to bear in mind when submitting a KEY TERM tender for work. Tender: An offer to carry out work for a certain Contract law amount of money, in English contract law regulates contracts in England and Wales. A contract accordance with a particular contract. generally forms when the contractor makes an offer and another person accepts it. Once a contract is made, it is enforceable in court. If problems are to be avoided, the offer must be made clearly, in sufficient detail, including its terms and conditions. Obviously, it is preferable if the offer is made and accepted in writing. Small works Small works such as house rewires, or minor works such as additions or alterations, will usually be carried out under the contractor’s own terms and conditions rather than the templates used for larger contracts. The cost of the work is usually presented to the client in one of two ways: as a quotation. This is a fixed cost of the work. This is normally given where there are no hidden problems or issues that can create hidden additional costs. Where a quotation is given, the person providing the work must be confident that they have clearly understood the client’s requirements and have undertaken a site survey. as an estimate. This is a method of providing a close as possible cost of works but with the understanding that there could be some factors that affect the cost. It is always a good idea to prepare the client for what the additional costs could be and for what reason. Nobody likes, and may be unwilling to pay for, a hugely inflated estimate. When working out the cost of labour for small works, the cost must include overheads. KEY TERM Overheads include items such as: Overheads are added business insurances such as public liability and tool/equipment theft to the labour costs as office rent and costs of running the office, such as heating and lighting, a percentage. Annual overheads should be telephones/internet etc. calculated and divided National Insurance contributions into the expected hours holiday pay worked annually to general (i.e. not specific to the job) tools, plant and machinery spread the cost of them transportation/vehicle costs such as MOT, servicing, insurance, tax over all works. salary/cost for support staff/services such as accountants, office staff, lawyers. 237 9781398361607.indb 237 27/07/22 9:42 PM The City & Guilds Textbook: Electrical Installations Book 2 IMPROVE YOUR MATHS A small organisation employs two electricians who are each paid £16 per hour. It is anticipated that annual overhead costs are expected to be £17 600.00 and the labour force work an average of 35 hours a week with 5 weeks holiday a year. What would be their expected cost per hour to the client if 40% profit is added? Annual hours worked: 35 hours × 2 persons × (52 weeks − 5 weeks holiday) = 3290 chargable hours Overheads per hour: £17 600 = £5.35 additional cost per hour 3290 So, cost of labour with overheads: £16 + £5.35 = £21.35 Hourly rate with profit: £21.35 + 40% = £29.89 per hour So the charge out rate per hour would be £29.89. Procurement methods There are several methods the client can use to establish the right contractor for a project, some of which are explained below. The following factors need to be considered when deciding on the most suitable procurement method: budgets time to the start of the contract contract duration quality project limitations. The client may already know which contractor they would like to use for their project, based on recommendations from others or having previously appointed them on another project. However, decisions must be made with value for money in mind. Is the price given by the preferred contractor competitive? The only way to know is by having other tenders to compare it with. Open tendering Where the client invites an offer for the contract from any organisation, this is referred to as open tendering. The advantage of this is that the process is fair as it isn’t limited to preferred contractors. However, the client may have to choose a contractor whom they are not familiar with or who is less experienced. The client may have no alternative but to appoint a contractor based on their quotation and references from previous clients. Two-stage tender If the client would like to secure the services of a contractor early, without having all the relevant design information in place, they use a two-stage tender process. This would involve a contractor and client agreeing a cost based on the information provided so work can begin. At the second stage, when all 238 9781398361607.indb 238 27/07/22 9:42 PM Chapter 4 Working on site information is available, the contractor is able to negotiate a fixed price for completion of the work. Preferred supplier (selective) Clients with previous experience working on similar projects may have developed good working relationships with one or more contractors. Some of these contractors may be included on the client’s list of preferred suppliers. From this list, the client may select several contractors and invite them to tender. Negotiated tendering Where a client has invited just one contractor to price for a project, this is referred to as negotiated tendering. Before building contracts are signed, the client usually negotiates the best price for the work. This may not be the best method for a client that needs to prove value for money as they have no other costs with which to compare. Tender procedure for larger works When a company receives an invitation to tender for a particular contract, the normal process to follow would be: record all documentation gather information to form the estimate determine prime costs determine provisional sum make final tender. Record all documentation All documents received in the invitation will be recorded and checked against the list of documents supplied, which should also be included. This ensures that all relevant documents are present and the most up-to-date versions of drawings are used. If, by mistake, an older version of drawings is used, this will reflect in the overall cost submitted. KEY TERM Gather information to form the estimate All documents and drawings will be carefully scrutinised and lists of materials will Take-off sheet: A list be written. These may be regular materials, such as switches and socket outlets, detailing the number and scope of items needed that are listed on a take-off sheet. per area of installation. Area DB Drawing 2 reference number Ground DB-2 A-2011-3-R1 12 3 18 1 6 2 3 floor First DB-3 A-2011-4-R1 6 4 15 1 12 2 0 floor Figure 4.7 Sample take-off sheet The sample take-off sheet shows the number of particular items needed for a particular area of the installation. The symbols would be used from the drawing, to minimise any confusion, and the specification would be checked for any specific manufacturer or finish required. At the bottom of the sheet, 239 9781398361607.indb 239 27/07/22 9:42 PM The City & Guilds Textbook: Electrical Installations Book 2 totals would indicate the quantity of each product required. The advantage of KEY TERMS showing the quantity of items per area is that, should a contract be won, this Bill of quantities: A information can be used to order materials at suitable installation stages. pre-prepared list of materials usually created Other major items of specialist equipment, such as large motors and generators, by a quantity surveyor; will be put out for quotation to major suppliers or manufacturers. replaces the take-off sheet. In some situations the client may provide a bill of quantities. This would be a Schedule of rates: A ready-made list of specific materials and would normally be made by a quantity document that lists a surveyor. This would replace the take-off sheet. Once the material costs, including labour/time cost for any specialist plant, have been obtained, the cost estimate can be calculated. This installing and connecting will involve total material costs and estimated labour costs against each specific an individual item of area. In some instances, a schedule of rates may be used to assist in this process. equipment. Examples may be £2.50 to fix a Prime cost ceiling rose securely to a plaster ceiling and £1.50 Prime cost is an allowance for the supply of a particular item of equipment to connect the cable to where the equipment has been specified by the client. For example, if the client it. Running the cable to specifically requires a particular type of decorative chandelier to be installed, the the ceiling rose could prime cost would be for the contractor to purchase the chandelier. This would not be charged at a rate of include the cost of installation. In some circumstances, prime cost may be a cost £2.00 per metre. for supplying a service by a nominated subcontractor specified by the client. An example of this would be the prime cost for a specialist subcontractor to create and install a particular piece of decorative artwork, such as a statue or feature INDUSTRY TIP within a building. It is always wise, if possible, to visit the site at this point, Provisional sum to see whether there are This is a sum of money that will cover the work required to install a particular any issues that may affect item of equipment, when the actual cost is yet unknown. An example could be the installation process. For the installation of a decorative chandelier where the detail of its full size or weight example, issues such as is not yet known. In this case a provisional sum would be given to the client, space constraints, giving which can be renegotiated later in the contract. rise to delivery and storage problems, would require Final tender a lot of labour time spent Once all the costs of labour and materials, including prime costs and provisional moving materials around from sums, are determined, the company overheads will then be added to make storage to site. the final tender. Overheads include the hidden costs of a business, such as the costs of: van insurances office staff holiday pay National Insurance contributions. Overheads include many factors, but the list above gives some examples of what should be allowed for. Finally, the tender is completed by a senior manager, using the benefit of their own experience to account for further costs, such as profit and other considerations that may arise. This involves a very careful balancing act to ensure that the company benefits from the work while keeping the overall cost competitive. 240 9781398361607.indb 240 27/07/22 9:42 PM Chapter 4 Working on site Alterations to a tender INDUSTRY TIP If a tender is successful, a contract will be agreed and signed, based on the work contained in the tender and the agreed price. Rarely will an installation follow the Architects may also request tender exactly, as the various factors affecting the overall installation are likely to a change to original plans, by change during the work. Examples of this could be socket outlets needing to be issuing an AI, which stands re-sited, as a radiator needs to be fitted in a particular location and this not having for architect’s instruction. been anticipated. Where these instances occur, the installer must obtain a variation order. At this stage, an additional sum for the alterations may be agreed or the work could KEY TERM be undertaken on a rate per day. Day work sheets will be used to record the Variation order: A additional work and, at various points in the contract, the costs of these additional declared change to the jobs will be agreed. Some major contracts require the day rates to be agreed prior original contract. to work starting. Contract progress INDUSTRY TIP The progress of a contract is set and monitored using a variety of tools, such as Companies that have been critical path networks and bar charts. These are covered in detail starting on accredited ISO 9000 have page 257. demonstrated that they: perform effectively, using Should a contract fall behind expected progress, due to factors under the control of the electrical subcontractor, it is likely that penalty clauses would take effect. management systems meet regulatory These clauses are imposed as part of a contract agreement to ensure timely requirements completion. If completion is delayed, the client may need compensating due to work to ensure they meet loss of facilities. These penalties are set, normally at a single day rate, at the point their clients’ needs. where contracts are agreed. The longer the delay in completion, the larger the penalty imposed. For this reason, use of tools, such as critical path networks, can assist in avoiding delays. KEY TERM ISO 9000: A quality Customer service principles standard for management Good customer service is about exceeding the customers’ expectations and systems to ensure that providing a service that will make them want to recommend your organisation to organisations meet the others, as well of course use you again. needs of their clients while meeting all There are several points for employers and employees to consider that lead to an regulations. organisation providing good customer service. These include the following. Being helpful even if a request is beyond your abilities. Saying ‘that isn’t my job’ to a request is not helpful. Better responses are ‘I can find out for you’ or ‘Have you spoken to this person about that?’. Asking for feedback and acting on it. Everyone likes to receive good feedback, but negative feedback is useful too. It gives you something to aim for to make your service better. Accept negative feedback and act on it! Knowing your products and work. It helps to know your subject, so you are always in a position to offer the client the right product or service. 241 9781398361607.indb 241 27/07/22 9:42 PM The City & Guilds Textbook: Electrical Installations Book 2 Giving a great first impression. This applies to all persons at each stage of the work as each person that is new to the client is helping them to form an impression of your organisation. Planning and informing. Nobody likes inconvenience and unpleasant surprises. Planning work properly means you know what is coming up and you can give the client plenty of notice regarding occurrences such as power shutdowns or times where there will be limited access to particular areas, etc. Being proactive, not reactive. Get to know your client and act on situations before they arise as a problem. If you only react to something when the client has complained about it, it may be too late. PLANNING THE WORK ON SITE In the previous section we looked at preparations prior to starting work and the information needed to price or tender the work. When on site, a large amount of planning is required to keep the site efficient and safe. The work environment With the site management team taking care of the working environment, it is INDUSTRY TIP normally left to either the subcontractor or their nominated team leader to make the necessary preparations for the work activities that they will perform during The preparation work is the project. essential to performing the task correctly, cost effectively When an installation tender is submitted, it is based on getting it right first time and, of course, safely. It is and therefore making a profit. Every error, change or omission, no matter how worth noting the five ‘P’s: small, has an impact on the final profit. Correct planning and preparation are Proper intended to ensure that the work is performed quickly and correctly first time, Planning every time. Prevents Poor Performance. VALUES AND BEHAVIOURS ‘Fail to plan, plan to fail.’ This is very true in electrical installation work. Site services Before work begins on a construction site, the site needs to be ready for a variety of activities and persons, including: service provision ventilation provision waste disposal procedures storage facilities health, safety and welfare requirements access and egress. 242 9781398361607.indb 242 27/07/22 9:42 PM Chapter 4 Working on site Service provision Services are required for a construction site to function, including: electricity supplies wholesome water and other water sources waste-water systems fuel sources. Electricity supplies Nearly all construction sites will require an electricity supply for power tools and lighting, as well as for administration and welfare blocks. Where the site is a refurbishment project, the existing electricity supply may be used but careful consideration must be given to the requirements in Section 704 of BS 7671 (Construction and demolition site installations). As most major construction sites which use the existing electricity supply cannot guarantee the reliable connection of the main protective bonding conductor during refurbishment work, the site supply may be converted to a TT earthing arrangement during the site work. This means that the earthing for the construction site will rely on an earth electrode. An assessment must also be made as to whether the existing supply is suitably rated for the intended load during construction (see the considerations for load, below). If the construction site is new or remote, then a new supply must be requested, or a generator obtained. In both cases, an assessment of the demand needs to be made. This is INDUSTRY TIP difficult as the total load will change regularly. A good way to gauge the overall load is to assess the overall kVA (kilo volt-amperes), taking into consideration: Any application to the DNO needs to be made well in the quantity and rating of site transformers used to provide 110 V supplies advance of work commencing, charging points for battery-operated equipment as arranging and installing a total temporary lighting loads new electricity supply can be large plant and machinery, such as cranes, welders, bench saws, etc. a very lengthy process. If the site is considerable in size, a three-phase supply may be required. If a new supply is required, an application needs to be made to the local distribution network operator (DNO). INDUSTRY TIP Wholesome water and other water sources All generators have a rated Water is essential on site. Wholesome water is drinking water and is necessary for output measured in kVA the welfare of those on site. Other reasons for requiring a water source are: not kW. Generators can be seriously overloaded if this is mixing cement or other materials not considered. washing or showering cleaning equipment, roads or structures dealing with hazards, dust or chemicals. KEY TERM In remote locations, water bowsers could be used to provide a water supply Water bowser: A transportable water tank if mains water is not available. Water should not be drawn from rivers or lakes or tanker. unless specific permission is granted from the Environment Agency. 243 9781398361607.indb 243 27/07/22 9:42 PM The City & Guilds Textbook: Electrical Installations Book 2 Waste-water systems KEY TERMS Waste water needs to be considered along with water supplies as mentioned Soakaway: A system above. Waste-water systems need to be looked at in two ways. Firstly, any surface where surface water or water from rainfall needs to be diverted into local watercourses or soakaways. water from guttering is Secondly, blackwater needs to be discharged into either main sewers or septic channelled into an area tanks. of ground that has been suitably prepared to allow the water to disperse in the ground without VALUES AND BEHAVIOURS causing flood or damp Water efficiency should also be considered on any project. Visit the issues. Environment Agency’s website for more information on sustainability and Blackwater: Water that is energy reduction, at: www.gov.uk/government/organisations/environment- contaminated to the point agency of no use and must be treated at a waste-water treatment facility. Sewage is classed as blackwater. Fuel sources Larger construction sites will need to consider storage of fuels, such as diesel, for plant, vehicles and generators. Ventilation provision Ventilation needs to be considered in situations such as confined locations, tunnels, underground works or, more generally, in large buildings. Ventilation should also be considered for specific tasks which involve a large amount of dust, where the area is to be sealed off. Ventilation may also be required for particular items of equipment that are vulnerable to dust contamination. The most common method of ventilating areas is by a forced clean air system, where clean air is forced by fans through ducting into the area and, in many cases, extraction fans then remove stale air from the location. Other locations and equipment may adopt a system where air is forced into an area or enclosure, creating a high pressure. This high pressure minimises contamination by keeping out dust and contamination from lower pressure areas. Waste disposal procedures Careful consideration needs to be given to areas set aside for waste storage and collection. As waste is normally collected by large vehicles, easy access is one of the most important factors that affects the location of waste storage. Methods of separating waste for recycling, or hazardous waste, are covered in detail in Book 1, Chapter 1, pages 12–13. Construction sites for high-rise buildings require methods of moving waste from upper floor levels to waste collection points at ground level. This is normally done by rubbish chutes, which are flexible ducts that allow waste to fall safely, directly into a collection point. 244 9781398361607.indb 244 27/07/22 9:42 PM Chapter 4 Working on site Storage facilities Good storage facilities must be provided for plant, machinery and materials in order to minimise: theft damage congestion. A secure lockable area, such as a storage container, is a good method of reducing theft from sites as well as reducing the likelihood of damage from weather or general site activities. If a good secure area is not set aside for storage, materials left around a site can become a hazard by potentially blocking escape routes or becoming obstacles to others trying to carry out their tasks. As well as being a safety hazard, poor storage also becomes inefficient as it is more likely that materials will become damaged or lost, or time will be wasted moving the materials out of the way. When locating storage facilities, consideration should be given to: ease of delivery of the storage container ease of delivery of the equipment to be stored minimising distances from storage to point of use keeping emergency routes clear keeping traffic areas clear, e.g. lorry turning circles avoiding any location that is likely to be built on as part of the project or where services are to be laid not blocking services or systems, e.g. avoiding placing a container next to a wall with a flue or vent not blocking daylight from windows presence of overhead cables security. Health, safety and welfare requirements All construction sites, regardless of their size, must provide basic amenities, such as: toilet facilities washing facilities (hot and cold water) first-aid facilities changing rooms or lockers. On larger construction sites, rest areas which provide shelter from the weather should also be provided. Showers must be provided on sites where tasks involve INDUSTRY TIP working with chemicals or hazardous materials. When considering welfare For more information on facilities, the Health and Safety Executive (HSE) has produced an order of required welfare facilities, preference for the provision of welfare facilities, dependent on the nature of the research the HSE website. construction. 245 9781398361607.indb 245 27/07/22 9:42 PM The City & Guilds Textbook: Electrical Installations Book 2 Planning for materials and equipment The most significant cost of any installation work is that of the labour required; however, a close second is that of the materials to be used. When confronted with a new project, it is essential to understand what materials will be required to complete the work. To help understand this, the installation team needs a number of documents. The technical specification The technical specification is the most important document as it has been KEY TERM used as the basis of the agreed contract that is being followed. However, it is Technical specification: A important to ensure that all variations and departures are also documented and technical document have been included. The technical specification will indicate any client’s preferred giving concise details of manufacturers for certain components, or even desired finishes that need to be the client’s wishes and complied with. expectations. The technical specification will also detail what other standards are to be complied with, as well as extra options required. For example, the client may require a minimum of 25% extra capacity on every distribution board. This would have an impact on the equipment ordered. For example, if a distribution board was specified as providing a supply to ten circuits, then typically a 16-way distribution board would be required to meet the client’s request. Other key information that is normally contained within the technical specification is the detail of the building construction. The technical specification will detail the construction of the wall, along with the details of the floor, wall and ceilings finishes. This information is essential when planning an electrical INDUSTRY TIP installation, as it helps to identify where and how the wiring can be installed. If an installation team were not aware that the floor through which they were Appendix 5 of BS 7671 is dedicated to external expecting to run cables was actually a concrete slab, then this would create a lot influences that may need of problems on site and result in a significant delay if not discovered quickly. to be accounted for when It is also important to consider other factors, such as the purpose of the building, detailing an installation. who will be using it and other environmental factors. These may be detailed within the technical specification but, if not, then the design team need to establish these external influences. Materials list Trying to keep track of all the materials required, just by marking up drawings, can become very complicated, especially on larger projects. Therefore, it is common practice to use a series of documents generically called the materials list. Materials lists will contain different information, depending on company procedures and requirements; however, there are always some common aspects and these include: the index number – a simple numerical identifier that makes it easier to track items on the materials list the description – a brief description of the item to enable it to be identified 246 9781398361607.indb 246 27/07/22 9:42 PM Chapter 4 Working on site the unit of measure – used to clarify what the quantities are measured in, e.g. litres, metres or individual items KEY TERMS the quantity – how many of the items are required. Electrical buyer: The person who places the Other information that may appear on a materials list includes: purchase orders with cost – how much each item costs suppliers for electrical equipment. They are supplier – who is the current supplier or who stocks the item often required to source catalogue code – where a specific item must be used, this is the supplier’s and negotiate deals catalogue number. to secure the best price and delivery for Materials lists can be arranged in two different formats, depending on who is to a wide selection of use the information: electrical accessories Total counts of materials for buyers and components. Big discounts can be given Staged counts for the installation team. by the supplier if the Electrical buyers may want to know the total counts of materials so that they electrical buyer can place can exploit a higher level of buying power. For example, if an electrical buyer large orders. needs to order several thousand components from the same supplier, then they Short shipments: Occur will be able to request a bigger discount. when the supplier delivers an incomplete order. An installation team will require the materials list to be broken down, to show There are normally items what they will need in each part of the installation. This enables them to on the original order still undertake stock control and make sure that the correct quantities of materials to be delivered, or the quantity is short and the are in place at the right time, reducing waste and other losses, such as delays, and balance is yet to come. avoiding short shipments. Just in time: A site term Working from materials lists can enable bulk purchasing power to be used to gain used to describe an a lower cost. It can also be used to set delivery schedules with the suppliers, using approach to stock/goods just in time systems. This means that there is less requirement for storage of control; a large-quantity order is placed with a materials on site and less chance of materials being lost, damaged or even stolen. supplier, with agreement on a staged delivery. Tools and equipment This means that the total With the design completed, risk assessments performed, with method statements order is placed at the produced and all materials identified and ordered, the final stage of the start, to take advantage of quantity discounts, but preconstruction preparation is about ensuring that the correct tools are available, the supplier stores the safe and in good working condition. In reviewing the site drawings, it will also have materials and only delivers become apparent what access, equipment and working platforms will be required the required quantity to perform the installation work safely. at the agreed times throughout the project. The Provision and Use of Work Equipment Regulations (PUWER) states under Regulation 4 that: ‘(1) Every employer shall ensure that work equipment is so constructed or INDUSTRY TIP adapted as to be suitable for the purpose for which it is used or provided. (2) In selecting work equipment, every employer shall have regard to the A guide to the Provision working conditions and to the risks to the health and safety of persons and Use of Work Equipment which exist in the premises or undertaking in which that work equipment Regulations (PUWER) can be accessed via the HSE is to be used and any additional risk posed by the use of that work website. equipment.’ 247 9781398361607.indb 247 27/07/22 9:42 PM The City & Guilds Textbook: Electrical Installations Book 2 All tools must be checked at this point, to make sure that they are safe to be used. HEALTH