Fluid-Flow Theory PDF
Document Details
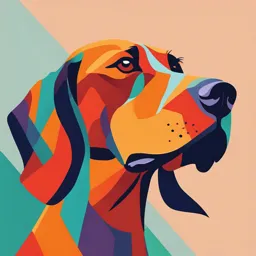
Uploaded by ImpressedLavender516
Tags
Summary
This document provides a comprehensive overview of fluid-flow theory, covering both fluid statics and fluid dynamics. It explores various properties of fluids, including pressure, density, and viscosity, using examples and equations to clarify the concepts.
Full Transcript
CHAPTER 3 FLUID-FLOW THEORY Many raw materials for foods and many finished foods are in the form of fluids. These fluids have to be transported and processed in the factory. Food technologists must be familiar with the principles that govern the flow of fluids,...
CHAPTER 3 FLUID-FLOW THEORY Many raw materials for foods and many finished foods are in the form of fluids. These fluids have to be transported and processed in the factory. Food technologists must be familiar with the principles that govern the flow of fluids, and with the machinery and equipment that is used to handle fluids. In addition, there is an increasing tendency to handle powdered and granular materials in a form in which they behave as fluids. Fluidization, as this is called, has been developed because of the relative simplicity of fluid handling compared with the handling of solids. The engineering concept of a fluid is a wider one than that in general use, and it covers gases as well as liquids and fluidized solids. This is because liquids and gases obey many of the same laws so that it is convenient to group them together under the general heading of fluids. The study of fluids can be divided into the study of fluids at rest - fluid statics, and the study of fluids in motion - fluid dynamics. For some purposes, further subdivision into compressible fluids such as gases, and incompressible fluids such as liquids, is necessary. Fluids in the food industry vary considerably in their properties. They include such materials as: Thin liquids - milk, water, fruit juices, Thick liquids - syrups, honey, oil, jam, Gases - air, nitrogen, carbon dioxide, Fluidized solids - grains, flour, peas. FLUID STATICS A very important property of a fluid at rest is the pressure exerted by that fluid on its surroundings. Pressure is defined as force exerted on an area. Under the influence of gravity, a mass of any material exerts a force on whatever supports it. The magnitude of this force is equal to the mass of the material multiplied by the acceleration due to gravity. The mass of a fluid can be calculated by multiplying its volume by its density, which is defined as its mass per unit volume. Thus the equation can be written: F = mg = Vg where F is the force exerted, m is the mass, g the acceleration due to gravity, V the volume and (the Greek letter rho) the density. The units of force are Newtons, or kg m s-2, and of pressure Pascals, one Pascal being one Newton m-2 and so one Pascal is also one kg m-1 s-2. For a mass to remain in equilibrium, the force it exerts due to gravity must be resisted by some supporting medium. For a weight resting on a table, the table provides the supporting reaction; for a multi-storey building, the upper floors must be supported by the lower ones so that as you descend the building the burden on the floors increases until the foundations support the whole building. In a fluid, the same situation applies. Lower levels of the fluid must provide the support for the fluid that lies above them. The fluid at any point must support the fluid above. Also, since fluids at rest are not able to sustain shearing forces, which are forces tending to move adjacent layers in the fluid relative to one another, it can be shown that the forces at any point in a fluid at rest are equal in all directions. The force per unit area in a fluid is called the fluid pressure. It is exerted equally in all directions. Consider a horizontal plane in a fluid at a depth Z below the surface, as illustrated in Fig. 3.1. Figure 3.1 Pressure in a fluid If the density of the fluid is , then the volume of fluid lying above an area A on the plane is ZA and the weight of this volume of fluid, which creates a force exerted by it on the area A which supports it, is ZAg. But the total force on the area A must also include any additional force on the surface of the liquid. If the force on the surface is Ps per unit area, F = APs + ZAg (3.1) where F is the total force exerted on the area A and Ps is the pressure above the surface of the fluid (e.g. it might be atmospheric pressure). Further, since total pressure P is the total force per unit area: P = F/A =Ps + Zg (3.2) In general, we are interested in pressures above or below atmospheric. If referred to zero pressure as datum, the pressure of the atmosphere must be taken into account. Otherwise the atmospheric pressure represents a datum or reference level from which pressures are measured. In these circumstances we can write P = Zg (3.3) This may be considered as the fundamental equation of fluid pressure. It states that the product of the density of the fluid, acceleration due to gravity and the depth gives the pressure at any depth in a fluid. EXAMPLE 3.1. Total pressure in a tank of peanut oil Calculate the greatest pressure in a spherical tank, of 2m diameter, filled with peanut oil of specific gravity 0.92, if the pressure measured at the highest point in the tank is 70 kPa. Density of water = 1000kgm-3 Density of oil = 0.92 x l000kgm-3 = 920kgm-3 Z = greatest depth =2m -2 and g = 9.81ms Now P = Zg = 2 x 920 x 9.81 kgm-1s-2 = 18,050Pa = 18.1kPa. To this must be added the pressure at the surface of 70kPa. Total pressure = 70 + 18.1 = 88.1 kPa. Note in Example 3.1, the pressure depends upon the pressure at the top of the tank added to the pressure due to the depth of the liquid; the fact that the tank is spherical (or any other shape) makes no difference to the pressure at the bottom of the tank. In the previous paragraph, we established that the pressure at a point in a liquid of a given density is solely dependent on the density of the liquid and on the height of the liquid above the point, plus any pressure which may exist at the surface of the liquid. When the depths of the fluid are substantial, fluid pressures can be considerable. For example, the pressure on a plate 1 m 2 lying at a depth of 30 m will be the weight of 1 m3 of water multiplied by the depth of 30 m and this will amount to 30 x 1000 x 9.81 = 294.3 kPa. As 1 tonne exerts a force on 1m 2 of 1000 x 9.81 = 9810Pa = 9.81 kPa the pressure on the plate is equal to that of a weight of 294.3 / 9.81 = 30 tonnes of water. Pressures are sometimes quoted as absolute pressures and this means the total pressure including atmospheric pressure. More usually, pressures are given as gauge pressures, which implies the pressure above atmospheric pressure as datum. For example, if the absolute pressure is given as 350 kPa, the gauge pressure is (350 - 100) = 250 kPa assuming that the atmospheric pressure is 100 kPa. These pressure conversions are illustrated in Fig. 3.2. Figure 3.2 Pressure conversions Standard atmospheric pressure is actually 101.3kPa but for our practical purposes l00kPa is sufficiently close and most convenient to use. Any necessary adjustment can easily be made. Another commonly used method of expressing pressures is in terms of "head" of a particular fluid. From eqn. (3.3) it can be seen that there is a definite relationship between pressure and depth in a fluid of given density. Thus pressures can be expressed in terms of depths, or heads as they are usually called, of a given fluid. The two fluids most commonly used, when expressing pressures in this way, are water and mercury. The main reason for this method of expressing pressures is that the pressures themselves are often measured by observing the height of the column of liquid that the pressure can support. It is straightforward to convert pressures expressed in terms of liquid heads to equivalent values in kPa by the use of eqn. (3.3.). EXAMPLE 3.2. Head of Water Calculate the head of water equivalent to standard atmospheric pressure of 100 kPa. Density of water = 1000 kg m-3 g = 9.81ms-2 and pressure = 100 kPa = 100 x 103Pa = 100 x 103 kgm-1s-2 but from eqn. (3.3) Z = P/g = (100 x 103)/ (1000 x 9.81) = l0.5m EXAMPLE 3.3. Head of mercury Calculate the head of mercury equivalent to a pressure of two atmospheres. Density of mercury = 13,600kgm-3 Z = (2 x 100 x 103)/ (13,600 x 9.81) = 1.5m FLUID DYNAMICS In most processes fluids have to be moved so that the study of fluids in motion is important. Problems on the flow of fluids are solved by applying the principles of conservation of mass and energy. In any system, or in any part of any system, it must always be possible to write a mass balance and an energy balance. The motion of fluids can be described by writing appropriate mass and energy balances and these are the bases for the design of fluid handling equipment. Mass Balance Consider part of a flow system, such for example as that shown in Fig. 3.3. This consists of a continuous pipe that changes its diameter, passing into and out of a unit of processing plant, which is represented by a tank. The processing equipment might be, for example, a pasteurizing heat exchanger. Also in the system is a pump to provide the energy to move the fluid. Figure 3.3. Mass and energy balance in fluid flow. (note: units for Ec and Ef are Jkg-1 ) In the flow system of Fig. 3.3 we can apply the law of conservation of mass to obtain a mass balance. Once the system is working steadily, and if there is no accumulation of fluid in any part the system, the quantity of fluid that goes in at section 1 must come out at section 2. If the area of the pipe at section 1 is A1, the velocity at this section, v1 and the fluid density 1, and if the corresponding values at section 2 are A2, V2, 2 the mass balance can be expressed as 1A1v1 = 2A2v2 (3.4) If the fluid is incompressible 1 = 2 so in this case A1v1 = A2v2 (3.5) Equation (3.5) is known as the continuity equation for liquids and is frequently used in solving flow problems. It can also be used in many cases of gas flow in which the change in pressure is very small compared with the system pressure, such as in many air-ducting systems, without any serious error. EXAMPLE 3.4. Velocities of flow Whole milk is flowing into a centrifuge through a full 5cm diameter pipe at a velocity of 0.22 ms-1, and in the centrifuge it is separated into cream of specific gravity 1.01 and skim milk of specific gravity 1.04. Calculate the velocities of flow of milk and of the cream if they are discharged through 2cm diameter pipes. The specific gravity of whole milk is 1.035. From eqn. (3.4) 1A1v1 = 2A2v2 + 3A3v3 where suffixes 1, 2, 3 denote respectively raw milk, skim milk and cream. Also, since volumes will be conserved, the total leaving volumes will equal the total entering volume and so A1v1 = A2v2 + A3v3 and from this equation v2 = (A1v1 - A3v3)/A2 (a) This expression can be substituted for v2 in the mass balance equation to give: 1A1v1 = 2A2(A1v1 – A3v3)/A2 + 3A3v3 1A1v1 = 2A1v1 - 2A3v3 + 3A3v3. So A1v1(1 - 2) = A3v3(3 - 2) (b) From the known facts of the problem we have: A1 = (/4) x (0.05)2 = 1.96 x 10-3m2 A2 = A3 = (/4) x (0.02)2 = 3.14 x 10-4m2 v1 = 0.22ms-1 1 = 1.035 x w , 2 = 1.04 x w , 3 = 1.01x w where w is the density of water. Substituting these values in eqn. (b) above we obtain: -1.96 x 10–3 x 0.22 (0.005) = -3.14 x 10-4x v3 x (0.03) so v3 = 0.23ms-1 Also from eqn. (a) we then have, substituting 0.23ms -1 for v3, v2 = [(1.96 x 10-3 x 0.22) - (3.14 x 10 –4 x 0.23)] / 3.14 x 10-4 = 1.1ms-1 Energy Balance In addition to the mass balance, the other important quantity we must consider in the analysis of fluid flow, is the energy balance. Referring again to Fig. 3.3, we shall consider the changes in the total energy of unit mass of fluid, one kilogram, between section 1 and section 2. Firstly, there are the changes in the intrinsic energy of the fluid itself which include changes in: (1) Potential energy. (2) Kinetic energy. (3) Pressure energy. Secondly, there may be energy interchange with the surroundings including: (4) Energy lost to the surroundings due to friction. (5) Mechanical energy added by pumps. (6) Heat energy in heating or cooling the fluid. In the analysis of the energy balance, it must be remembered that energies are normally measured from a datum or reference level. Datum levels may be selected arbitrarily, but in most cases the choice of a convenient datum can be made readily with regard to the circumstances. Potential energy Fluid maintained above the datum level can perform work in returning to the datum level. The quantity of work it can perform is calculated from the product of the distance moved and the force resisting movement; in this case the force of gravity. This quantity of work is called the potential energy of the fluid. Thus the potential energy of 1 kg of fluid at a height of Z(m) above its datum is given by Ep, where: Ep =Zg (J) Kinetic energy Fluid that is in motion can perform work in coming to rest. This is equal to the work required to bring a body from rest up to the same velocity, which can be calculated from the basic equation v2 = 2as, therefore s = v2/2a, where v (ms–1) is the final velocity of the body, a (ms-2) is the acceleration and s (m) is the distance the body has moved. Also work done = W = F x s, and from Newton's Second Law, for m kg of fluid F = ma and so Ek = W = mas = mav2/2a = mv2/2 The energy of motion, or kinetic energy, for 1 kg of fluid is therefore given by Ek where Ek = v2/2 (J) Pressure energy Fluids exert a pressure on their surroundings. If the volume of a fluid is decreased, the pressure exerts a force that must be overcome and so work must be done in compressing the fluid. Conversely, fluids under pressure can do work as the pressure is released. If the fluid is considered as being in a cylinder of cross-sectional area A(m2) and a piston is moved a distance L (m) by the fluid against the pressure P (Pa) the work done is PAL joules. The quantity of the fluid performing this work is AL (kg). Therefore the pressure energy that can be obtained from 1 kg of fluid (that is the work that can be done by this kg of fluid) is given by Er where Er = PAL / AL = P/ (J) Friction loss When a fluid moves through a pipe or through fittings, it encounters frictional resistance and energy can only come from energy contained in the fluid and so frictional losses provide a drain on the energy resources of the fluid. The actual magnitude of the losses depends upon the nature of the flow and of the system through which the flow takes place. In the system of Fig. 3.3, let the energy lost by 1 kg fluid between section 1 and section 2, due to friction, be equal to Ef (J). Mechanical energy If there is a machine putting energy into the fluid stream, such as a pump as in the system of Fig. 3.3, the mechanical energy added by the pump per kg of fluid must be taken into account. Let the pump energy added to 1 kg fluid be Ec (J). In some cases a machine may extract energy from the fluid, such as in the case of a water turbine. Other effects Heat might be added or subtracted in heating or cooling processes, in which case the mechanical equivalent of this heat would require to be included in the balance. Compressibility terms might also occur, particularly with gases, but when dealing with low pressures only they can usually be ignored. For the present let us assume that the only energy terms to be considered are Ep, Ek, Er, Ef, Ec. Bernouilli's Equation We are now in a position to write the energy balance for the fluid between section 1 and section 2 of Fig. 3.3. The total energy of one kg of fluid entering at section 1 is equal to the total energy of one kg of fluid leaving at section 2, less the energy added by the pump, plus friction energy lost in travelling between the two sections. Using the subscripts 1 and 2 to denote conditions at section 1 or section 2, respectively, we can write Ep1 + Ek1 + Er1 = Ep2 + Ek2 + Er2 + Ef -Ec. (3.6.) Therefore Z1g + v12/2 + P1/1 = Z2g + v22/2 + P2 /2 + Ef – Ec. (3.7) In the special case where no mechanical energy is added and for a frictionless fluid, Ec = Ef = 0, and we have Z1 g + v12/2 + P1 /1 = Z2 g + v22 /2 + P2 /2 (3.8) and since this is true for any sections of the pipe the equation can also be written Zg + v2/2 + P/ = k (3.9) where k is a constant. Equation (3.9) is known as Bernouilli's equation. First discovered by the Swiss mathematician Bernouilli in 1738, it is one of the foundations of fluid mechanics. It is a mathematical expression, for fluid flow, of the principle of conservation of energy and it covers many situations of practical importance. Application of the equations of continuity, eqn. (3.4) or eqn. (3.5), which represent the mass balance, and eqn. (3.7) or eqn. (3.9), which represent the energy balance, are the basis for the solution of many flow problems for fluids. In fact much of the remainder of this chapter will be concerned with applying one or another aspect of these equations. The Bernouilli equation is of sufficient importance to deserve some further discussion. In the form in which it has been written in eqn. (3.9) it will be noticed that the various quantities are in terms of energies per unit mass of the fluid flowing. If the density of the fluid flowing multiplies both sides of the equation, then we have pressure terms and the equation becomes: Zg + v2/2 + P = k' (3.10) and the respective terms are known as the potential head pressure, the velocity pressure and the static pressure. On the other hand, if the equation is divided by the acceleration due to gravity, g, then we have an expression in terms of the head of the fluid flowing and the equation becomes: Z + v2/2g + P/g = k'' (3.11) and the respective terms are known as the potential head, the velocity head and the pressure head. The most convenient form for the equation is chosen for each particular case, but it is important to be consistent having made a choice. If there is a constriction in a pipe and the static pressures are measured upstream or downstream of the constriction and in the constriction itself, then the Bernouilli equation can be used to calculate the rate of flow of the fluid in the pipe. This assumes that the flow areas of the pipe and in the constriction are known. Consider the case in which a fluid is flowing through a horizontal pipe of cross-sectional area A1 and then it passes to a section of the pipe in which the area is reduced to A2. From the continuity equation [eqn. (3.5)] assuming that the fluid is incompressible: A1v1 = A2v2 and so v2 = v1A1 /A2 Since the pipe is horizontal Z1 = Z2 Substituting in eqn. (3.8) v1 2 /2 + P1 /1 = v1 2 A12 /(2 A22) + P2 /2 and since 1 = 2 as it is the same fluid throughout and it is incompressible, P1 - P2 = 1 v1 2[(A12 /A22) –1]/2 (3.12) From eqn. (3.12), knowing P1, P2, A1, A2, 1, the unknown velocity in the pipe, v1, can be calculated. Another application of the Bernouilli equation is to calculate the rate of flow from a nozzle with a known pressure differential. Consider a nozzle placed in the side of a tank in which the surface of the fluid in the tank is Z ft above the centre line of the nozzle as illustrated in Fig. 3.4. Figure 3.4. Flow from a nozzle. Take the datum as the centre of the nozzle. The velocity of the fluid entering the nozzle is approximately zero, as the tank is large compared with the nozzle. The pressure of the fluid entering the nozzle is P1 and the density of the fluid 1. The velocity of the fluid flowing from the nozzle is v2 and the pressure at the nozzle exit is 0 as the nozzle is discharging into air at the datum pressure. There is no change in potential energy as the fluid enters and leaves the nozzle at the same level. Writing the Bernouilli equation for fluid passing through the nozzle: 0 + 0 + P1 /1 = 0 + v22/2 + 0 v22 = 2 P1 /1 _______ v2 = (2P1 /1 ) but from Equation 3.3 P1 / 1 = gZ (where Z is the head of fluid above the nozzle) ____ therefore v2 = (2 gZ) (3.13) EXAMPLE 3.5. Pressure in a pipe Water flows at the rate of 0.4m3 min-1 in a 7.5cm diameter pipe at a pressure of 70 kPa. If the pipe reduces to 5cm diameter calculate the new pressure in the pipe. Density of water is l000kgm -3. Flow rate of water = 0.4 m3 min -1 = 0.4/60 m3 s-1. Area of 7.5cm diameter pipe = (/4)D2 = (/4)(0.075)2 = 4.42 x 10-3m2. So velocity of flow in 7.5cm diameter pipe, v1 = (0.4/60)/(4.42 x 10-3) = 1.51 ms-1 Area of 5-cm diameter pipe = (/4)(0.05)2 = 1.96 x 10-3 m2 and so velocity of flow in 5cm diameter pipe, v2 = (0.4/60)/(1.96 x 10-3) = 3.4 m s-1 Now Z1g + v12/2 + P1 /1 = Z2g + v22 /2 + P2/2 and so 0 + (1.51)2/2 + 70 x 103/1000 = 0 + (3.4)2/2 + P2/1000 0 + 1.1 + 70 = 0 + 5.8 + P2/1000 P2 /1000 = (71.1 - 5.8) = 65.3 P2 = 65.3kPa EXAMPLE 3.6. Flow rate of olive oil Olive oil of specific gravity 0.92 is flowing in a pipe of 2cm diameter. Calculate the flow rate of the olive oil, if an orifice constriction is placed in the pipe so that the diameter of the pipe in the constriction is reduced to 1.2cm, and if the measured pressure difference between the clear pipe and the most constricted part of the pipe is 8cm of water. Diameter of pipe, in clear section, equals 2cm and at constriction equals 1.2cm. A1/A2 = (D1/D2) 2 = (2/1.2) 2 Differential head = 8 cm water. Differential pressure = Zg = 0.08 x 1000 x 9.81 = 785 Pa. substituting in eqn. (3.12) P1 - P2 = 1 v1 2[(A12 /A22 ) –1]/2 785 = 0.92 x 1000 x v2 [(2/1.2)4 - 1 ] /2 v2 = 785/3091 v = 0.5ms-1 EXAMPLE 3.7. Mass flow rate from a tank The level of water in a storage tank is 4.7m above the exit pipe. The tank is at atmospheric pressure and the exit pipe discharges into the air. If the diameter of the exit pipe is 1.2cm what is the mass rate of flow through this pipe? From eqn. (3.13) v = (2gZ) = (2 x 9.81 x 4.7) = 9.6ms-1 Now area of pipe A = (/4)D2 = (/4) x (0.012)2 = 1.13 x 10-4m2 Volumetric flow rate, Av = 1.13 x 10-4m2 x 9.6ms-1 = 1.13 x 10-4 x 9.6m3s-1 = 1.08 x 10-3 m3s-1 Mass flow rate, Av = 1000 kgm-3 x 1.08 x 10-3m3s-1 = 1.08kgs-1 EXAMPLE 3.8. Pump horsepower Water is raised from a reservoir up 35m to a storage tank through a 7.5cm diameter pipe. If it is required to raise 1.6 cubic metres of water per minute, calculate the horsepower input to a pump assuming that the pump is 100% efficient and that there is no friction loss in the pipe. 1 Horsepower = 0.746 kW. Volume of flow V = 1.6m3min-1 = 1.6/60m3s-1 = 2.7 x 10-2m3s-1 Area of pipe, A = (/4) x (0.075)2 = 4.42 x 10-3m2 Velocity in pipe v = 2.7 x 10-2/(4.42 x 10-3) = 6ms-1 And the mechanical energy = potential energy + kinetic energy Ec = Zg + v2/2 = 35 x 9.81 + 62/2 = 343.4 + 18 = 361.4Jkg-1 Therefore total power required = Ec x mass rate of flow = EcV = 361.4 x 2.7 x 10-2 x 1000Js-1 = 9758 Js-1 and, since l h.p. = 0.746kW = 7.46 x 102Js -1, required power = 13 h.p. VISCOSITY Viscosity is that property of a fluid that gives rise to forces that resist the relative movement of adjacent layers in the fluid. Viscous forces are of the same character as shear forces in solids and they arise from forces that exist between the molecules. If two parallel plane elements in a fluid are moving relative to one another, it is found that a steady force must be applied to maintain a constant relative speed. This force is called the viscous drag because it arises from the action of viscous forces. Consider the system shown in Fig. 3.5. Figure 3.5. Viscous forces in a fluid. If the plane elements are at a distance Z apart, and if their relative velocity is v, then the force F required to maintain the motion has been found, experimentally, to be proportional to v and inversely proportional to Z for many fluids. The coefficient of proportionality is called the viscosity of the fluid, and it is denoted by the symbol µ (mu). From the definition of viscosity we can write F/A = µv/Z (3.14) where F is the force applied, A is the area over which force is applied, Z is the distance between planes, v is the velocity of the planes relative to one another, and µ is the viscosity. By rearranging the eqn. (3.14), the dimensions of viscosity can be found. [µ] = FZ = [F][L][t] = [F][t] = [M][L] x [t] Av [L2][L] [L]2 [t2] [L]2 = [M][L]-1[t]-1 There is some ambivalence about the writing and the naming of the unit of viscosity; there is no doubt about the unit itself which is the Nsm-2, which is also the Pascal second, Pa s, and it can be converted to mass units using the basic mass/force equation. The older units, the poise and its sub-unit the centipoise(cP) seem to be obsolete, although the conversion is simple with 10 poises or 1000 centipoises being equal to 1 Nsm-2. The new unit is rather large for many liquids, the viscosity of water at room temperature being around 1 x 10-3 Nsm-2, and for comparison, at the same temperature, the approximate viscosities of other liquids are acetone, 0.3 x 10-3 Nsm-2; a tomato pulp, 3 x 10-3; olive oil, 100 x 10-3; and molasses 7000Nsm-2. Viscosity is very dependent on temperature decreasing sharply as the temperature rises. For example, the viscosity of golden syrup is about 100Nsm-2 at 16oC, 40 at 22oC and 20 at 25oC. Care should be taken not to confuse viscosity µ as defined in eqn. (3.14) which strictly is called the dynamic or absolute viscosity, with µ/ which is called the kinematic viscosity and given another symbol. In technical literature, viscosities are often given in terms of units that are derived from the equipment used to measure the viscosities experimentally. The fluid is passed through some form of capillary tube or constriction and the time for a given quantity to pass through is taken and can be related to the viscosity of the fluid. Tables are available to convert these arbitrary units, such as "Saybolt Seconds" or "Redwood Seconds", to poises. The viscous properties of many of the fluids and plastic materials that must be handled in food- processing operations are more complex than can be expressed in terms of one simple number such as a coefficient of viscosity. Newtonian and Non-Newtonian Fluids From the fundamental definition of viscosity in eqn. (3.14) we can write: F/A = µv /Z = µ (dv/dz) = where (tau) is called the shear stress in the fluid. This is an equation originally proposed by Newton and which is obeyed by fluids such as water. However, for many of the actual fluids encountered in the food industry, measurements show deviations from this simple relationship, and lead towards a more general equation: = k(dv/dz )n (3.15) which can be called the power-law equation, and where k is a constant of proportionality. Where n = 1, the fluids are called Newtonian because they conform to Newton's equation (3.14) and k = µ; and all other fluids may therefore be called non-Newtonian. Non-Newtonian fluids are varied and are studied under the heading of rheology, which is a substantial subject in itself and the subject of many books. Broadly, the non-Newtonian fluids can be divided into: (1) Those in which n < 1. As shown in Fig. 3.6 these produce a concave downward curve and for them the viscosity is apparently high under low shear forces decreasing as the shear force increases. Such fluids are called pseudoplastic, an example being tomato puree. In more extreme cases where the shear forces are low there may be no flow at all until a yield stress is reached after which flow occurs, and these fluids are called thixotropic. (2) Those in which n >1. With a low apparent viscosity under low shear stresses, they become more viscous as the shear rate rises. This is called dilatancy and examples are gritty slurries such as crystallized sugar solutions. Again there is a more extreme condition with a zero apparent viscosity under low shear and such materials are called rheopectic. Bingham fluids have to exceed a particular stress level before they start to move Figure 3.6. Shear stress/shear rate relationships in liquids. In many instances in practice non-Newtonian characteristics are important, and they become obvious when materials that it is thought ought to pump quite easily just do not. They get stuck in the pipes, or overload the pumps, or need specially designed fittings before they can be moved. Sometimes it is sufficient just to be aware of the general classes of behaviour of such materials. In other cases it may be necessary to determine experimentally the rheological properties of the material so that equipment and processes can be adequately designed. For further details see, for example, Charm (1971), Steffe (2000). STREAMLINE AND TURBULENT FLOW When a liquid flowing in a pipe is observed carefully, it will be seen that the pattern of flow becomes more disturbed as the velocity of flow increases. Perhaps this phenomenon is more commonly seen in a river or stream. When the flow is slow the pattern is smooth, but when the flow is more rapid, eddies develop and swirl in all directions and at all angles to the general line of flow. At the low velocities, flow is calm. In a series of experiments, Reynolds showed this by injecting a thin stream of dye into the fluid and finding that it ran in a smooth stream in the direction of the flow. As the velocity of flow increased, he found that the smooth line of dye was broken up until finally, at high velocities, the dye was rapidly mixed into the disturbed flow of the surrounding fluid. From analysis, which was based on these observations, Reynolds concluded that this instability of flow could be predicted in terms of the relative magnitudes of the velocity and the viscous forces that act on the fluid. In fact the instability which leads to disturbed, or what is called "turbulent" flow, is governed by the ratio of the kinetic and the viscous forces in the fluid stream. The kinetic (inertial) forces tend to maintain the flow in its general direction, but as they increase so does instability, whereas the viscous forces tend to retard this motion and to preserve order and reduce eddies. The inertial force is proportional to the velocity pressure of the fluid v2 and the viscous drag is proportional to µv/D where D is the diameter of the pipe. The ratio of these forces is: v2D/µv = Dv/µ This ratio is very important in the study of fluid flow. As it is a ratio, it is dimensionless and so it is numerically independent of the units of measurement so long as these are consistent. It is called the Reynolds number and is denoted by the symbol (Re). From a host of experimental measurements on fluid flow in pipes, it has been found that the flow remains calm or "streamline" for values of the Reynolds number up to about 2100. For values above 4000 the flow has been found to be turbulent. Between approximately 2100 and 4000 the flow pattern is unstable; any slight disturbance tends to upset the pattern but if there is no disturbance, streamline flow can be maintained in this region. To summarise for flow in pipes: For (Re) < 2100 streamline flow, For 2100 < (Re) 4000 turbulent flow. EXAMPLE 3.9. Flow of milk in a pipe Milk is flowing at 0.12 m3min-1 in a 2.5-cm diameter pipe. If the temperature of the milk is 21oC, is the flow turbulent or streamline? Viscosity of milk at 21oC = 2.1 cP = 2.10 x 10-3 N s m-2 Density of milk at 21oC = 1029 kgm-3 Diameter of pipe = 0.025 m Cross-sectional area of pipe = (/4)D2 = /4 x (0.025)2 = 4.9 x 10-4m2 Rate of flow = 0.12m3min-1 = (0.12/60) m3s-1 = 2 x 10-3 m3s-1 So velocity of flow =(2 x 10-3)/(4.9 x 10-4) = 4.1 ms-1 and so (Re) = (Dv/µ) = 0.025 x 4.1 x 1029/(2.1 x 10-3) = 50,230 and this is greater than 4000 so that the flow is turbulent. As (Re) is a dimensionless ratio, its numerical value will be the same whatever consistent units are used. However, it is important that consistent units be used throughout, for example the SI system of units as are used in this book. If for example, cm were used instead of m just in the diameter (or length) term only, then the value of (Re) so calculated would be greater by a factor of 10. This would make nonsense of any deductions from a particular numerical value of (Re). On the other hand, if all of the length terms in (Re) and this includes not only D but also v (ms-1), (kgm-3) and µ(Nsm-2) are in cm then the correct value of (Re) will be obtained. It is convenient, but not necessary to have one system of units such as SI. It is necessary, however, to be consistent throughout. ENERGY LOSSES IN FLOW Energy losses can occur through friction in pipes, bends and fittings, and in equipment. Friction in Pipes In Bernouilli's equation the symbol Ef was used to denote the energy loss due to friction in the pipe. This loss of energy due to friction was shown, both theoretically and experimentally, to be related to the Reynolds number for the flow. It has also been found to be proportional to the velocity pressure of the fluid and to a factor related to the smoothness of the surface over which the fluid is flowing. If we define the wall friction in terms of velocity pressure of the fluid flowing, we can write: F/A =fv2/2 (3.16) where F is the friction force, A is the area over which the friction force acts, is the density of the fluid, v is the velocity of the fluid, and f is a coefficient called the friction factor. Consider an energy balance over a differential length, dL, of a straight horizontal pipe of diameter D, as in Fig. 3.7. Figure 3.7. Energy balance over a length of pipe. Consider the equilibrium of the element of fluid in the length dL. The total force required to overcome friction drag must be supplied by a pressure force giving rise to a pressure drop dP along the length dL. The pressure drop force is: dP x Area of pipe = dP x D2 /4 The friction force is: (force/unit area) x wall area of pipe = F/A x D x dL so from eqn. (3.16), = (fv2/2) x D x dL Therefore equating pressure drop force and friction force (D2/4) dP = (fv2/2) x D x dL, therefore dP = 4(fv2/2) x dL/D Integrating between L1 and L2, in which interval P goes from P1 to P2 we have: dP = 4(fv2/2) x dL/D P1 - P2 = (4fv2/2)(L1 - L2)/D i.e. ΔPf = (4fv2/2) x (L/D) (3.17) or Ef = ΔPf / = (2fv2)(L/D) where L = L1 - L2 = length of pipe in which the pressure drop, ΔPf = P1 – P2 is the frictional pressure drop, and Ef is the frictional loss of energy. Equation (3.17) is an important equation; it is known as the Fanning equation, or sometimes the D'Arcy or the Fanning-D'Arcy equation. It is used to calculate the pressure drop that occurs when liquids flow in pipes. The factor f in eqn.(3.17) depends upon the Reynolds number for the flow, and upon the roughness of the pipe. In Fig. 3.8 experimental results are plotted, showing the relationship of these factors. If the Reynolds number and the roughness factor are known, then f can be read off from the graph. Figure 3.8 Friction factors in pipe flow (after Moody 1944) It has not been found possible to find a simple expression that gives analytical equations for the curve of Fig. 3.8, although the curve can be approximated by straight lines covering portions of the range. Equations can be written for these lines. Some writers use values for f which differ from that defined in eqn. (3.16) by numerical factors of 2 or 4. The same symbol, f, is used so that when reading off values for f, its definition in the particular context should always be checked. For example, a new f = 4 f removes one numerical factor from eqn. (3.17). Inspection of Fig. 3.8 shows that for low values of (Re), there appears to be a simple relationship between f and (Re) independent of the roughness of the pipe. This is perhaps not surprising, as in streamline flow there is assumed to be a stationary boundary layer at the wall and if this is stationary there would be no liquid movement over any roughness that might appear at the wall. Actually, the friction factor f in streamline flow can be predicted theoretically from the Hagen- Poiseuille equation, which gives: f = 16/(Re) (3.18) and this applies in the region 0 < (Re) 4000 flow is turbulent. Between 2100 and 4000 the flow is transitional. 6. Friction energy loss in pipes is expressed by the equation: Ef = (4fv2/2) x (L/D) and pressure drop in pipes: ΔP = (4fv2/2) x (L/D) PROBLEMS 1. In an evaporator, the internal pressure is read by means of a U-tube containing a liquid hydrocarbon of specific gravity 0.74. If on such a manometer the pressure is found to be below atmospheric by 83cm, calculate (a) the vacuum in the evaporator and (b) estimate the boiling temperature of water in the evaporator by using the steam tables in Appendix 8. ((a) 6.025kPa, absolute pressure 95kPa (b) 98.1oC) 2. Estimate the power required to pump milk at 20oC at 2.7 ms-1 through a 4cm diameter steel tube that is 130m long, including the kinetic energy and friction energy. (297.05 Js-1 = 0.40hp) 3. A 22% sodium chloride solution is to be pumped up from a feed tank into a header tank at the top of a building. If the feed tank is 40m lower than the header and the pipe is 1.5cm in diameter, find (a) the velocity head of the solution flowing in the pipe, and (b) the power required to pump the solution at a rate of 8.1 cubic metres per hour. Assume that the solution is at10oC, pipeline losses can be ignored, the pump is 68 % efficient, and that the density of the sodium chloride solution is 1160kgm-3. ((a) 8.2m (b) 2.42hp) 4. It is desired to design a cooler in which the tubes are 4cm diameter, to cool 10,000kg of milk per hour from 20oC to 3oC. Calculate how many tubes would be needed in parallel to give a Reynolds number of 4000. (11 tubes) 5. Soyabean oil is to be pumped from a storage tank to a processing vessel. The distance is 148m and included in the pipeline are six right-angle bends, two gate valves and one globe valve. If the processing vessel is 3m lower than the storage tank, estimate the power required to pump the oil at 20oC, at the rate of 20 tonnes per hour through the 5cm diameter pipe assuming the pump is 70% efficient. (41hp) 6. In the design of an air dryer to operate at 80oC, the fan is required to deliver 100 cubic metres per minute in a ring duct of constant rectangular cross-section 0.6m by 1.4m. The fan characteristic is such that this delivery will be achieved so long as the pressure drop round the circuit is not greater than 2cm of water. Determine whether the fan will be suitable if the circuit consists essentially of four right-angle bends of long radius, a pressure drop equivalent to four velocity heads in the bed of material and one equivalent to 1.2 velocity heads in the coil heater. Assume density of air is 1.00kgm -3. (Zwater = 0.124 cm, < 2cm of water)