Manufacturing Unit 1 PDF
Document Details
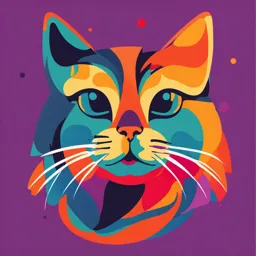
Uploaded by AmbitiousDiscernment3311
Tags
Summary
This document provides a general overview of various manufacturing processes, including primary shaping, deforming, machining, joining, and surface finishing. It also describes material properties like strength, elasticity, and plasticity.
Full Transcript
**[Manufacturing]** Technologically, manufacturing is the application of physical and chemical processes to alter the geometry, properties, and/or appearance of a given starting material to make parts or products. The word manufacture is derived from two Latin words, manus (hand) and factus (make)...
**[Manufacturing]** Technologically, manufacturing is the application of physical and chemical processes to alter the geometry, properties, and/or appearance of a given starting material to make parts or products. The word manufacture is derived from two Latin words, manus (hand) and factus (make); the combination means made by hand. The English word manufacture is several Centuries old, and ''made by hand'' accurately described the manual methods. **[Classification Of Manufacturing Process]** Classification of manufacturring processes 1. Primary Shaping Processes ---------------------------- Primary shaping or forming is manufacturing of solid body from a molten or gaseous state or from an amorphous material. Amorphous materials are gases, liquid, powders, fibers, chips. A primary shaping or forming tool contains a hollow space which, with the allowance for contraction usually corresponds to the form of the product. Some of the important priming shaping processes are: 1. 2. 3. **2. Deforming Process** Deforming processes is manufacturing process which makes use of suitable stresses like compression, tension, shear or combined stresses to cause plastic deformation of the materials to produce required shapes without changing its mass or material composition. In forming, no material is removed; they are deformed and displaced. Some of the forming processes are: 1. 2. 3. 4. 5. 6. 7. 8. 3. Machining/Removing Processes ------------------------------- The principle used in all machining process to generate the surface required by providing suitable relative motion between the workpiece and the tool. In these processes material is removed from the unwanted regions of the input materials. In this, the work material is subjected to a lower stress as compared to forming processes. Some of the machining processes are: 1. 2. 3. 4. 5. 6. 7. 8. **4. Joining Processes** In this process two or more pieces of metal parts are united together to make sub-assembly or final product. The joining process can be carried out by fusing pressing, rubbing, riveting or any other means of assembling. Some of the important joining processes are: 1. 2. 3. 4. 5. 6. **5. Surface Finishing Processes** These processes are utilized to provide intended surface finish on the metal surface of a job. By Imparting a surface finishing process, dimension of the part is not changed functionally; either a very negligible amount of metal is removed from or certain material is added to the surface of the job. Surface cleaning process is also accepted as a surface finishing process, Some of the surface finishing processes are: 1. 2. 3. 4. 5. 6. 7. 8. 9. 10. 11. 6. Material Properties Modification Process ------------------------------------------- In this type of manufacturing process, material properties of a workpiece is changed in order to achieve desirable characteristics without changing the shape. Many structural metals undergo some special treatment to modify their properties so that they will perform better for their intended use. Some of the properties are: 1. 2. 3. **Mechanical properties** **Mechanical properties** are useful for helping to specify and identify metals. 1. **Strength** 2. **Elasticity** 3. **Plasticity** 4. **Hardness** 5. **Toughness** 6. **Brittleness** 7. **Stiffness** 8. **Ductility** 9. **Malleability** 10. 11. 12. 13. 1. **STRENGTH :** It is the capacity to withstand destruction under the action of external loads. Stronger the material, greater the load it can withstand. Strength in another way determines the ability of a material to withstand stress without failure. **2. ELASTICITY:** It is the property of a material for which deformation caused by applied load & disappears upon removal of load. It is the power of a material of returning to its original position after deformation when the load was removed. Elasticity is the tensile property of a material. **3. STIFFNESS:** The ratio between the resistances of a material to elastic deformation or deflection of that material is called stiffness. A material which caused slight deformation under load has a high degree of stiffness. If a material follows hooke's law i.e. the material has a linear stress-strain relation, its stiffness is measured by young\'s modulus (E). The higher the value of young's modulus, the material is stiffer. **4. PLASTICITY:** It is the ability to undergo some degree of permanent deformation without failure. Plastic deformation will takes place only after the elastic range has been exceeded. It is important in forming, shaping, extruding and many other hot-cold metal working processes. Materials such as clay, lead etc. are plastic at room temperature and steel is plastic when at bright red. Generally plasticity increases with increasing temperature. **5. DUCTILITY:** It is the property of a material which enables it to draw out into thin wire. Mild steel is a ductile material. The percentage elongation and reduction in area in tension is often used as empirical measures of ductility. **6. MALLEABILITY**: It is the ability to flatten a metal into thin sheets without cracking by hot or cold working. Aluminium, Copper, Lead etc. are malleable material. **7. RESISTANCE**: It is the capacity of a material to absorb energy elastically. On removal of load the energy stored is given off, exactly as in when the load is removed. The maximum energy which can be stored in a body up to elastic limit is called proof resistance. **8. TOUGHNESS**: It is measure of the amount of energy of a material that can be absorbed before actual fracture or failure takes place i.e. if a load suddenly applied to a piece of mild steel, it will absorb much more energy before failure occurs. Thus mild steel is said to be much tougher than a glass. It can also be defined as it is the ability of a material to withstand both plastic and elastic deformation and it is a desirable quantity for structural and machine parts e.g. Manganese Steel, Wrought Iron, Mild Steel etc. **9. HARDNESS:** It is the fundamental property which is closely related to strength. It is usually defined in terms of ability of a material to resist scratching, abrasion, cutting, penetration. Hardness of a metal does not directly relate to hardenability of the metal. The methods are now in use for determining the hardness of material -- Brinell, Rockwell and Vickers. **10**. **BRITTLENESS**: It is the property of a material of breaking without much permanent distortion. There are many materials which break or fail before much deformation takes place such as glass, cast iron etc. **11. CREEP:** The slow and progressive deformation of a material with time constant stress is called creep. The simplest type of creep is viscous flow. It is most generally defined as time dependent strain occurring under stress. A metal generally shows creep at high temperature whereas plastic, rubber and similar materials are very temperature sensitive to creep. **12. MACHINEABILITY**: It is simply started that the ease with which a metal can be removed in various machining operations. Good machinability implies satisfactory result in machining. The machinability is indicated by percentage which is termed as machinability index. The machinability index of carbon, steels are from 40% to 60% and that of cast iron from 50% to 80%. **13. FATIGUE**: It is the property of a material which determines its behavior when subjected to cyclic load applications within the elastic range of material. Under these conditions, failure may occur to give services indefinitely. In many instances a component is designed to give a certain length of service under a specific cycle of loading. ### **Impact Strength** The **impact strength is the ability** of a metal to resist suddenly applied loads. **METAL CASTING** "Metal Casting is one of the oldest materials shaping methods known. Casting means pouring molten metal into a mold with a cavity of the shape to be made, and allowing it to solidify. When solidified, the desired metal object is taken out from the mold either by breaking the mold or taking the moldapart. The solidified object is called the casting." (Or) "Casting is a process in which molten metal flows by gravity or other force into a mold where it solidifies in the shape of the mold cavity." **Advantages of casting process:** Molten material can flow into very small sections so that intricate shapes can be made by this process. As a result, many other operations, such as machining, forging, and welding, can be minimized. Possible to cast both ferrous and non ferrous materials Tools are very simple and expensive Useful for small lot production Weight reduction in design No directional property There are certain parts (like turbine blades) made from metals and alloys that can only be processed this way. Turbine blades: Fully casting + last machining. Size and weight of the product is not a limitation for the casting process. **Advantages** **(A) Design advantages** (*i*) **Size :** There is no restriction on size. Items from a few grams to many tons can be produced by casting. In fact, casting is the only process for producing massive objects in one single piece. Eg. watch cases (few grams), rolling mill housing (around 50 tons). (*ii*) **Complexity :** The most complex curved surfaces and complicated shapes which are difficult or rather impossible to manufacture by other processes, can usually be cast. (*iii*) **Weight saving :** Large saving in weight is achieved as the metal can be placed exactly where it is required. (*iv*) **production of prototypes :** The casting process is ideal for making models and prototypes required for creation of new designs. (*v*) **Wide range of properties :** Special properties like corrosion resistance, heat resistance, damping capacity, high strength, electrical and thermal conductivity etc. are possible by alloying the base metal and proper heat treatment. (v*i*) **Fibrous structure :** In cast metals, the inclusions are more or less randomly distributed during the solidification process. Thus the cast alloys usually do not exhibit any fibering or directionality of properties. (v*ii*) **Grain size :** Most non-ferrous alloys retain the grain size attained during freezing. Subsequent heat treatment can improve the grain size. (v*iii*) **Density :** The density of cast alloy is usually identical to that of the wrought alloys of the same chemical composition and heat treatment, when both are fully sound. (*ix*) **Low cost** (*x*) **Dimensional accuracy :** Tolerance as close as 01. mm can be achieved depending on the cast metal, the casting process and the shape and size of the casting. The surface finish can also be controlled and may vary from 5 to 50. (*xi*) **Versatility in production :** Suitable for small quantity job shop production as welll as large volume mass production by employing at automatic machines **Disadvantages** (*i*) High energy consuming process. (*ii*) Labour intensive as compared to other processes. (*iii*) Needs large space and handling systems. (*iv*) Time requirement for producing castings is quite long. (*v*) Unfavorable working condition due to heat, dust fumes, heaps of scraps and slag etc.at different stages. Also there is high environmental pollution. **Applications of Casting (Metal : Ferrous and Non ferrous)** Cylinder blocks Cylinder liners M/C Tool beds Pistons Piston rings Mill rolls Wheels Housing Water supply pipes Bells Jet engine blades Turbine blades Sand Casting ------------ The term "Sand Casting" can be used to describe the final product and the process to make it. It is a metal casting process done at a place called a "Foundry". It has stayed as one of the oldest processes. Sand is used as the mould material in this metal casting technique. Sand casting is a widely used metal casting process that involves creating a mold from a mixture of sand and a binding agent, such as clay. This technique is employed to produce complex metal parts of various sizes and shapes. Sand casting is a widely used metal casting process. A mold is created by compacting sand around a pattern of the desired object. Molten metal is then poured into the mold, allowing it to solidify. After cooling, the sand is removed, revealing the cast metal object. It\'s versatile, cost-effective, and suitable for various shapes. Important sand casting terms 1\. **Flask:** A metal or wood frame, without fixed top or bottom, in which the mold is formed. Depending upon the position of the flask in the molding structure, it is referred to by various names such as drag -- lower molding flask, cope -- upper molding flask, cheek -- intermediate molding flask used in three piece molding. 2\. **Pattern:** It is the replica of the final object to be made. The mold cavity is made with the help of pattern. 3\. **Parting line:** This is the dividing line between the two molding flasks that makes up the mold. 4\. **Molding sand:** Sand, which binds strongly without losing its permeability to air or gases. It is a mixture of silica sand, clay, and moisture in appropriate proportions. 5\. **Facing sand:** The small amount of carbonaceous material sprinkled on the inner surface of the mold cavity to give a better surface finish to the castings. 6\. **Core:** A separate part of the mold, made of sand and generally baked, which is used to create openings and various shaped cavities in the castings. 7\. **Pouring basin:** A small funnel shaped cavity at the top of the mold into which the molten metal is poured. 8\. **Sprue:** The passage through which the molten metal, from the pouring basin, reaches the mold cavity. In many cases it controls the flow of metal into the mold. 9\. **Runner:** The channel through which the molten metal is carried from the sprue to the gate. 10\. **Gate:** A channel through which the molten metal enters the mold cavity. 11\. **Chaplets:** Chaplets are used to support the cores inside the mold cavity to take care of its own weight and overcome the metallostatic force. 12\. **Riser**: A column of molten metal placed in the mold to feed the castings as it shrinks and solidifies. Also known as "feed head". 13\. **Vent:** Small opening in the mold to facilitate escape of air and gases. Steps involved in casting: The following are the basic steps involved in casting process: Pattern Making Mold making Melting Pouring Solidification Fettling, Cleaning & Finishing Inspection The following diagram shows the flow of steps in casting: **Step 1 - Pattern Making**: The procedure involves the usage of a reusable pattern that has the same dimensions as the desired finished product. To account for thermal expansion or contraction, a pattern is always made larger than the finished product. The pattern is provided with allowances like shrinkage, draft, machining, and rapping allowance before adding sand. **Step 2 -- Mold making:** The second step in the sand casting process is to create the mold for the casting. A sand mold is formed by packing sand into each half of the mold i.e cope and drag. The sand is packed around the pattern, which is a replica of the external shape of the casting. When the pattern is removed, the cavity that will form the casting remains. The mold-making time includes positioning the pattern, packing the sand, and removing the pattern. **Step 3- Melting:** Melting is the preparation of the molten metal according to their Chemical Composition for casting, and its conversion from a solid to a liquid state in a furnace. The molten metal is maintained at a set temperature in a furnace, After the mold has been clamped then molten metal transferred in a ladle to the molding area of the foundry where it is poured into the molds. **Step 4- Pouring**:\ The metal which needs to be formed to the desired shape is melted and poured into the sprue (a funnel-like structure). This is made to flow to the cavity and allowed to cool. The sand around it holds the temperature without reacting to it. **Step 5- Solidification**: The molten metal that is poured into the mold will begin to cool and solidify once it enters the cavity. When the entire cavity is filled and the molten metal solidifies, the final shape of the casting is formed. The mold can not be opened until the cooling time has elapsed. The desired cooling time can be estimated based upon the wall thickness of the casting and the temperature of the metal. **Step 6-** Fettling, Cleaning and Finishing After the casting has cooled, the gating system is removed, often using bandsaws, abrasive cut-off wheels or electrical cut-off devices. A 'parting line flash' is typically formed on the casting and must be removed by grinding or with chipping hammers. Castings may also need to be cleaned and finished by some cleaning and finishing process. **PATTERN** A pattern is a model or the replica of the object (to be casted). It is embedded in molding sand and suitable ramming of molding sand around the pattern is made. The pattern is then withdrawn for generating cavity (known as mold) in molding sand. Thus it is a mould forming tool. It may be defined as a model or form around which sand is packed to give rise to a cavity known as mold cavity in which when molten metal is poured, the result is the cast object. When this mould/cavity is filled with molten metal, molten metal solidifies and produces a casting (product). So the pattern is the replica of the casting. **OBJECTIVES OF A PATTERN** 1\. Pattern prepares a mould cavity for the purpose of making a casting. 2\. Pattern possesses core prints which produces seats in form of extra recess for core placement in the mould. 3\. It establishes the parting line and parting surfaces in the mould. 4\. Runner, gates and riser may form a part of the pattern. 5\. Properly constructed patterns minimize overall cost of the casting. 6\. Pattern may help in establishing locating pins on the mould and therefore on the casting with a purpose to check the casting dimensions. 7\. Properly made pattern having finished and smooth surface reduce casting defects. **Difference between Pattern and Casting** Main difference between pattern and casting is their dimensions *i.e.,* a pattern is slightly larger in size than the casting because it carries shrinkage allowance (1 -- 2 mm per 100 mm), draft allowance (1° and 3°) for tenal and internal surfaces and machining allowance. Pattern carries core prints. Pattern can be in two or three pieces but casting is a single piece object. Material required for both are different. **COMMON PATTERN MATERIALS** The common materials used for making patterns are wood, metal, plastic, plaster, wax or mercury. The some important pattern materials are discussed as under. **1. Wood** Wood is the most popular and commonly used material for pattern making. It is cheap, easily available in abundance, repairable and easily fabricated in various forms using resin and glues. It is very light and can produce highly smooth surface. But, in spite of its above qualities, it is susceptible to shrinkage and warpage and its life is short because of the reasons that it is highly affected by moisture of the molding sand. After some use it warps and wears out quickly as it is having less resistance to sand abrasion. It cannot withstand rough handily and is weak in comparison to metal. In the light of above qualities, wooden patterns are preferred only when the numbers of castings to be produced are less. The main varieties of woods used in pattern-making are shisham, kail, deodar, teak and mahogany. **Advantages of wooden patterns** 1 Wood can be easily worked. 2 It is light in weight. 3 It is easily available. 4 It is very cheap. 5 It is easy to join. 6 It is easy to obtain good surface finish. 7 Wooden laminated patterns are strong. 8 It can be easily repaired. **Disadvantages** 1 It is susceptible to moisture. 2 It tends to warp. 3 It wears out quickly due to sand abrasion. 4 It is weaker than metallic patterns. **2. Metal** Metallic patterns are preferred when the number of castings required is large enough to justify their use. These patterns are not much affected by moisture as wooden pattern. The wear and tear of this pattern is very less and hence posses longer life. Moreover, metal is easier to shape the pattern with good precision, surface finish and intricacy in shapes. It can withstand against corrosion and handling for longer period. It possesses excellent strength to weight ratio. The main disadvantages of metallic patterns are higher cost, higher weight and tendency of rusting. It is preferred for production of castings in large quantities with same pattern. The metals commonly used for pattern making are cast iron, brass and bronzes and aluminum alloys. **3. Plastic** Plastics are getting more popularity now a days because the patterns made of these materials are lighter, stronger, moisture and wear resistant, non sticky to molding sand, durable and they are not affected by the moisture of the molding sand. Moreover they impart very smooth surface finish on the pattern surface. These materials are somewhat fragile, less resistant to sudden loading and their section may need metal reinforcement. The plastics used for this purpose are thermosetting resins. Phenolic resin plastics are commonly used. These are originally in liquid form and get solidified when heated to a specified temperature. To prepare a plastic pattern, a mould in two halves is prepared in plaster of paris with the help of a wooden pattern known as a master pattern. The phenolic resin is poured into the mould and the mould is subjected to heat. The resin solidifies giving the plastic pattern. Recently a new material has stepped into the field of plastic which is known as foam plastic. Foam plastic is now being produced in several forms and the most common is the expandable polystyrene plastic category. It is made from benzene and ethyl benzene. **4. Plaster** This material belongs to gypsum family which can be easily cast and worked with wooden tools and preferable for producing highly intricate casting. The main advantages of plaster are that it has high compressive strength and is of high expansion setting type which compensate for the shrinkage allowance of the casting metal. Plaster of paris pattern can be prepared either by directly pouring the slurry of plaster and water in moulds prepared earlier from a master pattern or by sweeping it into desired shape or form by the sweep and strickle method. It is also preferred for production of small size intricate castings and making core boxes. **5. Wax** Patterns made from wax are excellent for investment casting process. The materials used are blends of several types of waxes, and other additives which act as polymerizing agents, stabilizers, etc. The commonly used waxes are paraffin wax, shellac wax, bees-wax, cerasin wax, and micro-crystalline wax. The properties desired in a good wax pattern include low ash content up to 0.05 per cent, resistant to the primary coat material used for investment, high tensile strength and hardness, and substantial weld strength. Wax patterns are prepared by pouring heated wax into split moulds or a pair of dies. The dies after having been cooled down are parted off. Now the wax pattern is taken out and used for molding. Such patterns need not to be drawn out solid from the mould. After the mould is ready, the wax is poured out by heating the mould and keeping it upside down. Such patterns are generally used in the process of investment casting where accuracy is linked with intricacy of the cast object. **TYPES OF PATTERN** The types of the pattern and the description of each are given as under. 1\. One piece or solid pattern 2\. Two piece or split pattern 3\. Cope and drag pattern 4\. Three-piece or multi- piece pattern 5\. Loose piece pattern 6\. Match plate pattern 7\. Follow board pattern 8\. Gated pattern 9\. Sweep pattern 10\. Skeleton pattern 11\. Segmental or part pattern **Single-piece or solid pattern** Solid pattern is made of single piece without joints, partings lines or loose pieces. It is the simplest form of the pattern. Typical single piece pattern is shown in **Fig.** **Two-piece or split pattern** When solid pattern is difficult for withdrawal from the mold cavity, then solid pattern is splited in two parts. Split pattern is made in two pieces which are joined at the parting line by means of dowel pins. The splitting at the parting line is done to facilitate the withdrawal of the pattern. A typical example is shown in **Fig.** **Cope and drag pattern** In this case, cope and drag part of the mould are prepared separately. This is done when the complete mould is too heavy to be handled by one operator. The pattern is made up of two halves, which are mounted on different plates. A typical example of match plate pattern is shown in **Fig.** **Three-piece or multi-piece pattern** Some patterns are of complicated kind in shape and hence cannot be made in one or two pieces because of difficulty in withdrawing the pattern. Therefore these patterns are made in either three pieces or in multi- pieces. Multi molding flasks are needed to make mold from these patterns. The pattern can also be seen from the **Fig.** **Loose-piece pattern** A single piece are made to have loose piece in easy to allow withdrawal from the mold the molding process are completed, after the main pattern is withdrawn leaving from that piece in the sand. After the withdrawal of piece from mold, it cavity separately formed by the pattern. It loose piece pattern is highly skilled job and expensive. The pattern can also be seen from the **Fig.** **Match plate pattern** The match plate pattern type is having two parts, one for one side and another one for another side of pattern. It is called match plate pattern. The sand casting pattern making in two pieces. It also having gates and runner attached with pattern. The molding process completed after that match plate removed together, the gating is obtained for joining the cope and drag. It pattern is mainly used for casting of metal, usually aluminum are machined in this method with light weight and machinability. It should be possible for mass production of small casting with high dimensional accuracy. They are also used for machine molding. The cost will be high of molding but it is easily compensated by high rate of production and more accuracy. The pattern can also be seen from the **Fig.** **Follow board type pattern** In casting process some portions are structurally weak. It is not supported properly and may be break under the force of ramming. In this stage the special pattern to allow the mold may be such as wooden material. The pattern can also be seen from the **Fig.** **Gated Pattern** In the mass production of casings, multi cavity moulds are used. Such moulds are formed by joining a number of patterns and gates and providing a common runner for the molten metal, as shown in **Fig.** These patterns are made of metals, and metallic pieces to form gates and runners are attached to the pattern. **Sweep Pattern** Sweep patterns are used for forming large circular moulds of symmetric kind by revolving a sweep attached to a spindle as shown in **Fig.** Actually a sweep is a template of wood or metal and is attached to the spindle at one edge and the other edge has a contour depending upon the desired shape of the mould. The pivot end is attached to a stake of metal in the center of the mould. **Skeleton Pattern** When only a small number of large and heavy castings are to be made, it is not economical to make a solid pattern. In such cases, however, a skeleton pattern may be used. This is a ribbed construction of wood which forms an outline of the pattern to be made. This frame work is filled with loam sand and rammed. The surplus sand is removed by strickle board. For round shapes, the pattern is made in two halves which are joined with glue or by means of screws etc. A typical skeleton pattern is shown in **Fig.**  **Segmental pattern** The segmental pattern is used to prepare the mold of larger circular casting to avoid the use of solid pattern of exact size. It is similar to sweep pattern, but the difference from Sweep pattern, the sweep pattern is give a continuous revolve motion to generate the part, the segmental pattern itself and mold is prepared. In this segmental pattern construction should be save the material for pattern make and easy carried. The segmental pattern is mounted on the central pivot and mold in one position for after prepare of mold the segment is moved for next position. That is repeat together the complete mold is done. A typical segmental pattern is shown in **Fig.** Pattern Allowances: Pattern may be made from wood or metal and its color may not be same as that of the casting. The material of the pattern is not necessarily same as that of the casting. Usually, the pattern is always made larger than the desired size of the casting on account of allowance which should be allowed for machining, shrinkage, distortion and rapping etc. The size of a pattern is never kept the same as that of the desired casting because of the fact that during cooling the casting is subjected to various effects and hence to compensate for these effects, corresponding allowances are given in the pattern. These various allowances given to pattern can be enumerated as, allowance for shrinkage, allowance for machining, allowance for draft, allowance for rapping or shake, allowance for distortion and allowance for mould wall movement. The various allowances in pattern are \(i) Shrinkage/Contraction \(ii) Machining/Finish \(iii) Draft / Taper \(iv) Distortion / Camper \(v) Shake / Rapping **Shrinkage Allowance** In practice it is found that all common cast metals shrink a significant amount when they are cooled from the molten state. The total contraction in volume is divided into the following parts: 1\. Liquid contraction, i.e. the contraction during the period in which the temperature of the liquid metal or alloy falls from the pouring temperature to the liquidus temperature. 2\. Contraction on cooling from the liquidus to the solidus temperature, i.e. solidifying contraction. 3\. Contraction that results there after until the temperature reaches the room temperature. This is known as solid contraction. The first two of the above are taken care of by proper gating and risering. Only the last one, i.e. the solid contraction is taken care by the pattern makers by giving a positive shrinkage allowance. This contraction allowance is different for different metals. The contraction allowances for different metals and alloys such as Cast Iron 10 mm/mt.. Brass 16 mm/mt., Aluminium Alloys. 15 mm/mt., Steel 21 mm/mt., Lead 24 mm/mt. **Machining Allowance** It is a positive allowance given to compensate for the amount of material that is lost in machining or finishing the casting. If this allowance is not given, the casting will become undersize after machining. The amount of this allowance depends on the size of casting, methods of machining and the degree of finish. In general, however, the value varies from 3 mm. to 18 mm. **Draft or Taper Allowance** Taper allowance is also a positive allowance and is given on all the vertical surfaces of pattern so that its withdrawal becomes easier. The normal amount of taper on the external surfaces varies from 10 mm to 20 mm/mt. On interior holes and recesses which are smaller in size, the taper should be around 60 mm/mt. These values are greatly affected by the size of the pattern and the molding method. In machine molding its, value varies from 10 mm to 50 mm/mt.  **Rapping or Shake Allowance** Before withdrawing the pattern it is rapped and thereby the size of the mould cavity increases. Actually by rapping, the external sections move outwards increasing the size and internal sections move inwards decreasing the size. This movement may be insignificant in the case of small and medium size castings, but it is significant in the case of large castings. This allowance is kept negative and hence the pattern is made slightly smaller in dimensions 0.5-1.0 mm. **Distortion Allowance** This allowance is applied to the castings which have the tendency to distort during cooling due to thermal stresses developed. For example a casting in the form of U shape will contract at the closed end on cooling, while the open end will remain fixed in position. Therefore, to avoid the distortion, the legs of U pattern must converge slightly so that the sides will remain parallel after cooling. **Moulding Sand** Sand is the principle material used in casting for making moulds. The principle ingredients of moulding sands are: silica sand grains, clay, moisture and special additives. Moulding sand adds additives for improving some properties for making moulds: High fusion temperature and Good thermal stability. **The various types of moulding sand are** **1.** Green sand\ **2.** Dry sand\ **3.** Loam sand\ **4.** Parting sand\ **5.** Facing sand\ **6.** Backing sand\ **7.** System sand\ **8.** Core sand **1. Green Sand**\ **→** Green sand is a mixture of silica sand and clay. It constitutes 18% to 30% clay and 6% to 8 % water.\ **→**The water and clay present is responsible for furnishing bonds for the green sand.\ **→**It is slightly wet and has the ability to retain the shape and impression given to it under pressure.\ **→**It is easily available and has low cost.\ **→**The mould which is prepared in this sand is called green sand mould.\ **→**It is commonly used for producing ferrous and non-ferrous castings **2. Dry Sand**\ **→**After making the mould in green sand, when it is dried or baked is called dry sand.\ **→**It is suitable for making large castings.\ **→**The moulds which is prepared in dry sand is known as dry sand moulds.\ **→**If we talk about the physical composition of the dry sand, than it is same as that of the green sand except water. **3. Loam Sand**\ **→**It is a type of moulding sand in which 50 % of clay is present.\ **→**It is mixture of sand and clay and water is present in such a quantity, to make it a thin plastic paste.\ **→**In loam moulding patterns are not used.\ **→**It is used to produce large casting. **4. Parting Sand**\ **→**Parting sand is used to prevent the sticking of green sand to the pattern and also to allow the sand on the parting surface of the cope and drag to separate without clinging.\ **→**It serves the same purpose as of parting dust.\ **→**It is clean clay free silica sand. **5. Facing Sand**\ **→**The face of the mould is formed by facing sand.\ **→**Facing sand is used directly next to the surface of the pattern and it comes in direct contact with the molten metal, when the molten metal is poured into the mould.\ **→**It possesses high strength and refractoriness as it comes in contact with the molten metal.\ **→**It is made of clay and silica sand without addition of any used sand. **6. Backing Sand**\ **→**Backing sand or flour sand is used to back up facing sand.\ **→**Old and repeatedly used moulding sand is used for the backing purpose.\ **→**It is also sometimes called black sand because of the addition of coal dust and burning when it comes in contact with the molten metal. **7. System Sand**\ **→**In mechanical sand preparation and handling units, facing sand is not used. The sand which is used is cleaned and reactivated by adding of water, binder and special additives. And the sand we get through this is called system sand.\ **→**System sand is used to fill the whole flask in the mechanical foundries where machine moulding is employed.\ **→**The mould made with this sand has high strength, permeability and refractoriness. **8. Core Sand**\ **→**The sand which is used to make core is called core sand.\ **→**It is also called as oil sand.\ **→**It is a mixture of silica sand and core oil. Core oil is mixture of linseed oil, resin, light mineral oil and other binding materials.\ **→**For the sake of economy, pitch or flours and water may be used in making of large cores. **Properties of Moulding Sand** During Sand casting, we use sand for the preparation of mould. It is the moulding sand properties which improves the quality of the casting. If a sand of suitable property is chosen, than it greatly minimises the casting defects that may be produced during the mould preparation and casting. In this blog we will discuss all the properties of moulding sand that it must possesses for the preparation of excellent mould. A moulding sand should possess the following 6 properties 1. Porosity 2. Flowability 3. Collapsibility 4. Adhesiveness 5. Cohesiveness or strength 6. Refractoriness **1.Porosity or Permeability:**\ ***It is the ability of sand by which it allows the gases to pass through it easily.*** Some gases gets dissolved in molten metal and when this molten metal starts to solidify, these dissolved gases comes out of the molten metal and try to escape out of the moulding sand. If the sand is not enough porous than these gases will not be able to go out of the mould and gets trapped into the casting and produces holes and pores in metal casting. Also if the molten metal comes in contact with the moist sand, steam or water vapor is produced. This steam or vapors also results in the formation of holes in the casting if they do not able to escape out of the mould. So it is advised to use sufficiently porous moulding sand to eliminate the porosity defect in metal casting. **2. Flowability :**\ ***The ability of moulding sand to behave like a fluid when it is rammed is called flowability.*** Due to this property the sand can easily occupy the space in molding box and take up its shape.The sand should be of high flowability, so that it can be easily compacted for uniform density and to obtain a good impression of the pattern in the mould. The flowability of the sand can be increases as we increases the clay and water content in the sand. **3. Collapsibility :**\ ***The ability of the moulding sand to collapse after solidification of the molten metal is called collapsibility.*** After the solidification of molten metal, the sand should get collapse for free contraction of the metal. If free contraction of the metal will happen than if eliminates naturally the tearing or cracking of the contracting metal. **4. Adhesiveness :**\ ***The ability of the sand particles to get stick with another body is called adhesiveness.*** The sand should have sufficient adhesiveness so that it can easily get cling to the sides of the moulding boxes and does not fall out to the box when it is removed. **5. Cohesiveness or Strength**\ ***The ability of the sand particles to stick with each other is called cohesiveness.*** The strength of the sand depends upon how cohesive the sand particles are. The sand should have sufficient strength so that it can easily capable to retain its shape during conveying, turning or closing and pouring. If it is not of appropriate strength than it will not be able to hold its shape and the mould may damage during pouring of molten metal. Low strength sand leads to pouring casting defects in metals. To avoid pouring defects, the sand should be of sufficient strength to produce mold of desired shape and also retain this shaped even when the molten metal is poured in the moulding cavity. **The sand strength can be of two types:-** **(i) Green strength:** The strength of sand possessed by it in its green or moist state is called green strength. The mould with adequate green strength retains its shape and do not collapse even when the pattern is removed from the moulding box. **(ii) Dry strength:** The strength possessed by the sand in its dry or baked state is called dry strength. Enough dry strength allows the sand to withstand erosive forces due to molten metal and helps to retain its shape. **6. Refractoriness**\ ***The ability of the moulding sand to withstand the high temperature of the molten metal without fusing into it is called refractoriness.*** The moulding sand must have enough refractoriness property to produce excellent quality of casting free from defects. The sand with lack of refractoriness melts and gets fuse in the casting and spoils the quality of the cast metal. The refractoriness is the measure of sinter point of the sand not its melting point. **[CORE MAKING]** Core making basically is carried out in four stages namely:- I. Core Sand Preparation II. Core Making III. Core Baking IV. Core Finishing Each stage is explained as under. **[Core Sand Preparation]** Preparation of satisfactory and homogenous mixture of core sand is done by manually or machines. For getting better and uniform core sand properties using proper sand constituents and additives. Core sand is highly rich silica sand mixed with oil binders such as core oil which composed of linseed oil, resin, light mineral oil and other bind materials. The core sands are generally mixed with the help of any of the following mechanical means namely roller mills and core sand mixer using vertical revolving arm type and horizontal paddle type mechanisms. **[Core Making Process Using Core Making Machines]** The process of core making is basically mechanized using ***core blowing, core ramming and core drawing machines*** which are broadly discussed as under. **[Core blowing machines]** The basic principle of core blowing machine comprises of filling the core sand into the core box by using compressed air. The velocity of the compressed air is kept high to obtain a high velocity of core sand particles, thus ensuring their deposit in the remote corners the core box. On entering the core sand with high kinetic energy, the shaping and ramming of core is carried out simultaneously in the core box. **[Core ramming]** Cores can also be prepared by ramming core sands in the core boxes by machines based on the principles of squeezing, jolting and slinging. Out of these three machines, jolting and slinging are more common for core making. **[Core drawing]** The core drawing machine is preferred when the core boxes have deep draws. After ramming sand in it, the core box is placed on a core plate supported on the machine bed. A rapping action on the core box is produced by a vibrating vertical plate. This rapping action helps in drawing off the core from the core box. After rapping, the core box is pulled up thus leaving the core on the core plate. The drawn core is then baked further before its use in mold cavity to produce hollowness in the casting. **[Core baking]** - Once the cores are prepared, they will be baked in a baking ovens or furnaces. - The main purpose of baking is to drive away the moisture and harden the binder, thereby giving strength to the core. - The core drying equipments are usually of two kinds namely core ovens and dielectric bakers. - The core ovens are may be further of two type's namely continuous type oven and batch type oven. **[CORE FINISHING]** - The cores are finally finished after baking and before they are finally set in the mould. - The fins, bumps or other sand projections are removed from the surface of the cores by rubbing or filing. - The dimensional inspection of the cores is very necessary to achieve sound casting. - Cores are also coated with refractory or protective materials using brushing dipping and spraying means to improve their refractoriness and surface finish. - The coating on core prevents the molten metal from entering in to the core. - Bars, wires and arbors are generally used to reinforce core from inside as per size of core using core sand. **[GREEN SAND CORES]** - Green sand cores are not dried. - Green sand cores are made by green sand containing moist condition about 5% water and 15- 30 % clay. - It imparts very good permeability to core and thus avoids defects like shrinkage or voids in the casting. - They are poured in green condition and are generally preferred for simple, small and medium castings. - The process of making green sand core consumes less time. - Such cores possess less strength in comparison to dry sand cores and hence cannot be stored for longer period. **[DRY SAND CORES]** - Dry sand cores are produced by drying the green sand cores to about 110°C. - These cores possess high strength rigidity and also good thermal stability. - These cores can be stored for long period and are more stable than green sand core. - They are used for large castings. - They also produce good surface finish in comparison to green sand cores. - They can be handled more easily. - These types of cores require more floor space, more core material, high labor cost and extra operational equipment. #### #### GATING SYSTEM All the channels or passages through which the molten metal is delivered to mould cavity is termed as gating system. The main function of gating system is to lead molten metal from ladle to the casting cavity ensuring smooth, uniform and complete filling. A poorly designed gating system results in casting defects. A gating system controls mould filling process. **[Function of an Ideal Gating System]** The main functions of an ideal gating system are to \(a) distribute the molten metal with the least disturbance in order to reduce erosion of the mould material. \(b) facilitate complete filling of the mould cavity. \(c) fill the mould cavity with molten metal at the earliest possible time to avoid temperature gradient. \(d) develop such temperature gradient in molten metal and the mould which will lead to the directional solidification of the casting towards riser. \(e) prevent the formation of oxide and dross in the molten metal while flowing through it. \(f) prevent the entry of slag, sand and the other particles from the mould. ##### ##### **Elements of Gating System** - Pouring Cup - Sprue - Spruce Well - Cross-gate or Runner - Ingate or Gates **Pouring basin:** It is the conical hollow element or tapered hollow vertical portion of the gating system which helps to feed the molten metal initially through the path of gating system to mould cavity. It makes easier for the ladle operator to direct the flow of molten metal from crucible to pouring basin and sprue. It helps in maintaining the required rate of liquid metal flow. It reduces turbulence and vertexing at the sprue entrance. It also helps in separating dross, slag and foreign element etc. from molten metal before it enters the sprue. **Sprue:** It is a vertical passage made generally in the cope using tapered sprue pin. It is connected at bottom of pouring basin. It is tapered with its bigger end at to receive the molten metal the smaller end is connected to the runner. It helps to feed molten metal without turbulence to the runner which in turn reaches the mould cavity through gate. It sometimes possesses skim bob at its lower end. The main purpose of skim bob is to collect impurities from molten metal and it does not allow them to reach the mould cavity through runner and gate. **Sprue well:** It is designed to restrict the free fall of molten metal by directing it in a right angle towards the runner. It aids in reducing turbulence and air aspiration. Ideally it should be shaped cylindrically having diameter twice as that of sprue exit and depth twice of runner. **Gate:** It is a small passage or channel being cut by gate cutter which connect runner with the mould cavity and through which molten metal flows to fill the mould cavity. It feeds the liquid metal to the casting at the rate consistent with the rate of solidification. **Riser:** It is a passage in molding sand made in the cope portion of the mould. Molten metal rises in it after filling the mould cavity completely. The molten metal in the riser compensates the shrinkage during solidification of the casting thus avoiding the shrinkage defect in the casting. It also permits the escape of air and mould gases. It promotes directional solidification too and helps in bringing the soundness in the casting. **Types of Gates** Depending on the placing of gate, the various types of gates are **Top gate:-** The molten metal enters into the mould cavity from the top. These are only used for ferrous alloys. Suitable for simple casting shape. There may be chance of mould erosion. **Bottom gate:-** This type of gating system is used for very deep moulds. It takes higher time for filling of the mould cavity. **Parting gate:-** This is most widely used gate in sand casting. The metal enters into the mould at the parting plane. This is easiest and most economical. ##### ##### **Gating Ratio** Gating ratio refers to the relation between area of the sprue to total area of runner total area of ingates. Mathematically, it can be written as As: Ar: Ag. The gating system completely controls the molten metal flow. Gating systems can be classified as Pressurised system and Unpressurised system. Gating ratio depends on the nature of the molten metal. - Pressurized system is used for reactive metals like magnesium alloy etc. Unpressurised gating system is used for normal metals such as brass, steel, aluminium alloy, etc. - A Gating ratio such as 1:2:1 or 1:0.75:0.5 refers to pressured system; whereas the gating ratio such as 1:2:2 or 1:3:3, 1:1:3, refers to unpressurised gating system. - Pressurized system is referred to as "Gate control System", since ingates controls the flow of metal. - Unpressurised system is referred to as "Choke Control System", since the choke controls the flow of metal. - In the pressurized system high metal velocity occurs and results in turbulence. In the case of unpressurised system, turbulence is produced and streamline flow is induced. - Pressurized System Consumes less metal and yield is more. Unpressurised system consumes more metal and the yield will be slightly lowered. - In the case of pressurized system, the system will always be full of liquid metal. In the case of unpressurised system flow is not full. Depending on gating ratio, there are two types of gating systems are available. 1 Pressurized gating system 2 Un-pressurized gating system **Pressurized Gating System:** - The total cross sectional area decreases towards the mold cavity. - The gating ratio of a typical pressurized gating system is Sprue area: Runner area: Ingate area 1: 2: 1 or 1:0.75:0.5 - Back pressure is maintained by the restrictions in the metal flow. - Back pressure helps in reducing the aspiration as the sprue always runs full. - Because of the restrictions the metal flows at high velocity leading to more turbulence and chances of mold erosion. - Because of the turbulence this type of gating system is not used for light alloys but can be advantageously used for ferrous castings. **Un-Pressurized Gating System:** - The total cross sectional area increases towards the mold cavity. - The gating ration of a typical un-pressurized gating system is Sprue area: Runner area: Ingate area 1:2:2 or 1:3:3, 1:1:3 - Flow of liquid (volume) is different from all gates, aspiration in the gating system as the system never runs full - Less turbulence, Because of less turbulence this type of gating system is used for light alloys such as aluminum and magnesium alloys. **RISER:-** Most alloys shrink during solidification. As a result of this volumetric shrinkage, voids are formed which are known as hot spots. So a reservoir of molten metal is maintained from which the metal can flow steadily into the casting. These reservoirs are known as risers. Design considerations:- The metal in riser should solidify at the end and the riser volume should be sufficient for compensating the shrinkage in the casting. To solve this problem, the riser should have higher volume. Types of Riser:- \(a) **Top riser-** This type of riser is open to the atmosphere. It is very conventional & convenient to make. It looses heat to the atmosphere by radiation & convention. To reduce this, insulation is provided on top such as plaster of paris and asbestos sheets. \(b) **Blind riser :-** This type of riser is surrounded by the moulding sand and looses heat very slowly. \(c) **Internal riser:-** It is surrounded on all sides by casting such that heat from casting keeps the metal in the riser hot for a longer time. These are used for cylindrical shapes or hollow cylindrical portions casting. ##### **Cupola** A cupola furnace is generally used for melting and refining pig iron along with scrap for producing cast iron. **Description of Cupola** **[Shell]** -- It is vertical and cylindrical in shape -- Made of sheet thickness 6 -- 12 mm inside of which is lined with acid refractory bricks and clay consisting of silicon acid (SiSO~2~) and Alumina (Al~2~O~3~). -- Diameter of cupola varies from 1 -- 2 meters and height is 3 -- 5 times diameter. **[Foundation]** -- The shell is mounted on a brickwork foundation or cast iron columns. -- The bottom of the shell consists of a drop bottom door for cleaning purposes at the end of melting. **[Tuyers]** -- Air for combustion of fuel is delivered through the tuyers. -- These are provided at height of between 0.6 to 1.2 m above the working bottom. **[Wind Belt]** -- Air supplied by blower is delivered to the tuyers from wind belt/jacket. -- It is a jacket like structure which is a steel plate duct mounted on outside of shell. **[Blower]** A high pressure fan/ blower is used to supply air to the wind belt through a blast pipe. **[Slag Hole]** -- It is used for removing the slag. -- It is placed at a level at about 250 mm below the centre of the tuyers. **[Tapping Hole]** -- It is used for pouring out molten metal. -- It is located opposite and just below the slag hole. **[Charging Hole]** -- It is used for feeding charge to the furnace. -- Charge is a mixture of metal, coke and flux. -- Normally situated 3 to 6 meters above the tuyers. **[Chimney / Stack]** -- The shell normally continues for 4.5 m to 6 m above the charging hole to chimney. -- It starts from the charging zone upto top of cupola. -- Gases generated are carried out in this zone. **Zones of Cupola** The entire cupola can be divided into the following sections. **Crucible Zone** It is between top of the sand bed and bottom of the tuyers. **Combustion / Oxidizing Zone** -- It starts from top of the tuyer to 150 to 300 mm above it. -- Heat is generated in this zone due to the following reaction.  **Reducing Zone** -- It starts from the top of the combustion zone upto the top of coke bed. -- CO2 is reduced in these zone. **Melting Zone** -- It starts from top of the coke bed and ranges upto a height of 900 mm. -- Temperature is highest in this zone (1600°C). **Preheating / Charging Zone** -- It starts from top of the melting zone and ranges upto the charging door. -- Charging materials when fed gets preheated here. **Stack Zone** -- It starts from the charging zone upto top of cupola. -- Gases generated are carried out in this zone. **Operation of Cupola** i. Preparation of cupola. ii. Firing the cupola. iii. Soaking of iron. iv. Opening of air blast. v. Pouring the molten metal. vi. Closing the cupola. **Preparation of Cupola** -- Clean the slag and repair damaged lining using mixture of fire clay and silica sand. -- Bottom doors are raised up and bottom sand poured. -- The surface of the sand is sloped from all directions towards the tap hole and rammed. -- Slag hole is also formed to remove slag. **Firing the Cupola** -- Wood is ignited on sand bottom. -- Then coke is added to a level slightly above the tuyers. -- Air blast is turned on at a slower rate. -- After having red spots on the fuel bed, extra coke is poured upto required height. **Charging the Cupola** -- Cupola starts burning properly. -- Then alternate layers of pig iron, coke and flux (limestone) are fed from charging door till cupola is full. -- Flux does two functions (*i*) prevent oxidation (*ii*) remove impurities (Flux is normally 2 -- 3% of metal charge by weight) **Soaking of Iron** -- After charging these get slowly heated up. -- Air blast is kept closed for 45 minutes. -- This causes iron to soak. **Opening of Air Blast** -- Air blast is opened after near about 45 minutes. -- Tap hole is kept closed to gather sufficient amount of molten metal. -- The rate of charging should be equal to the rate of melting in order to keep the furnace full for continuous operation. **[Special casting process]** **Die-Casting Process** Die-casting is the process of making castings by using permanent moulds called die. This process is used for casting a low melting temperature material, e.g., aluminium and zinc alloys. The die used for die-castings is very much similar to mould. Designed to hold and accurately close two mould halves and keep them closed while liquid metal is forced into cavity. Die-casting is similar to permanent mould casting except that the metal is injected into the mould under high pressure of 10-210 MPa instead being fed by gravity. Pressure is maintained during solidification, then mould is opened and part is removed. Use of high pressure to force metal into die cavity is what distinguishes this from other permanent mould processes. This result in a more uniform structure, good surface finish and good dimensional accuracy. For many parts, post-machining can be totally eliminated, or very light machining may be required to bring dimensions to size. The process, when applied to a plastic casting, is called injection moulding. Die casting process can be classified into two types viz. 1\. Hot chamber die-casting process 2. Cold chamber die-casting process **Hot Chamber Die-Casting Process** The hot chamber die-casting process is shown in Figure. When the piston is in the extreme left position, molten material in the hot chamber around the cylinder fills the cylinder. As the piston moves forward, the die cavity is filled under pressure. The metal is solidified quickly and casting is removed from the die. This is very fast process with up to 1000 cycles/hour is possible. The process is suitable for low melting temperature materials, i.e. zinc, tin, lead, and magnesium. Final product **Cold chamber Die-Casting** The setup for cold chamber die-casting is shown in Figure. The process is very much similar to hot chamber die casting method. The molten material is fed into the cold cylinder chamber from where it is forced into the die cavity under pressure. Cold chamber die casting method is generally slower than hot chamber die casting method as pouring of molten metal is separate step. **Cold chamber die-casting differs from hot chamber die casting process in the following respects:** 1.Melting unit is not an integral part of the cold chamber die casting machine. Molten metal is brought and poured into the die-casting machine with the help of Ladles. 2.Molten metal poured into the chamber of cold chamber die casting machine is at lower temperature as compared to hot chamber die casting machine. 3.Pressure requirements in case of cold chamber die casting machine is higher than that of hot chamber die casting machine. **Note:** *Moulds for Die Casting. Mould usually made of tool steel, mould steel, etc. Tungsten and molybdenum (good refractory qualities) used to die cast steel and cast iron. Ejector pins required to remove part from die when it opens. Lubricants must be sprayed into cavities to prevent sticking* **Advantages of Die Casting Process:** 1\. Economical for large production quantities. 2\. Good accuracy and surface finish. 3\. Thin sections are possible, as the liquid metal is forced into the die with high external pressure. 4\. Rapid cooling provides small grain size and good strength to casting. **Disadvantages of Die Casting Process in general:** 1\. Generally limited to metals with low metal points 2\. Part geometry must allow removal from die **Centrifugal Casting Process** *A family of casting processes in which the mould is rotated at high speed so centrifugal force distributes molten metal to outer regions of die cavity.* When a body rotates about an axis a centrifugal force is created, this centrifugal force is used in getting the shape of the final casting. Typical centrifugal casting equipment is shown in Figure 8. In centrifugal casting, a permanent metal mould revolves at very high speeds in a horizontal, vertical or inclined position and the molten metal is poured. The poured molten metal is thrown on the walls of the mould cavity by centrifugal force. Centrifugal force is utilized to distribute liquid metal over the inner surfaces (walls) of the mould. The metal solidifies in the form of a hollow cylinder. Centrifugal castings can be made in almost any required length, thickness and diameter. The cylinder wall thickness is controlled by the amount of liquid metal poured. The centrifugal force of this process keeps the casting hollow, eliminating the need for cores. Using centrifugal casting process it is possible to produce castings of good quality, dimensional accuracy and external surface detail. **Typical examples of the products manufactured by** **this process include pipes, gun barrels, bushings, flywheel, pressure vessels.** **Types of centrifugal casting processes** There are three main types of centrifugal casting processes. (*i*) True centrifugal casting (*ii*) Semi centrifugal casting (*iii*) Centrifuging **True Centrifugal Casting** - This process is used for making castings of hollow cylindrical parts e.g. pipes, gun barrels and lamp posts, hollow bushes, etc which are axisymmetric with a concentric hole. - The molten metal is poured in a rotating mould. - The axis of rotation is usually horizontal but can be vertical for short workpieces. - The moulds are made of steel, iron, graphite and may be coated with a refractory lining to increase mould life. - Mould surfaces can be shaped so that pipes with various outer shapes, including square, polygonal, can be cast. - The inner surface of the casting remains cylindrical because the molten metal is uniformly distributed by centrifugal forces. - No core is required for making concentric hole because of the outward centrifugal force. - In true centrifugal casting the casting solidifies from outside towards the axis of rotation. So it provides / creates conditions which set up directional solidification to produce - castings free from shrinkage. - True centrifugal castings may be produced in metal or sand lined moulds. It largely depends on the quantity to be produced. - A water jacket is provided around the mould for cooling it. - The casting machine is mounted on wheels with the pouring laddle which has a long spout extending till the other end of the pipe to be made.  **Semi Centrifugal Casting** - It is also known as **profited centrifugal casting**. - Gear blanks, wheels are produced. - This process is used for jobs which are more complicated than those possible in true centrifugal casting but are axisymmetric in nature. - The central hole is not necessary but if present/required is to be produced by using a core (out of sand) - Moulds may be made of sand or metal. - The axis of rotation is always vertical. - Metal enters the mould through central pouring basin. - The rotating speed in this process is not as high as true centrifugal casting. - Directional solidification can be obtained by proper gating of casting and using proper chills. - For producing more than one castings at a time, a number of moulds are stacked together one over the other fed by a common central sprue. **Centrifuging / Pressure Casting** - Centrifuging method is used to obtain higher metal pressures - Bearing caps, small brackets during solidification, when casting shapes are not axisymmetrical. - This process is suitable for small jobs of any shape. - A number of small jobs are joined together by radial runners with central sprue on a revolving table. - The jobs are uniformly placed on the table around periphery so that their masses are properly balanced. - The casting is possible only in vertical direction. - The casting shape has no special limitations in this process and an almost unlimited variety of smaller shapes can be cast. - When castings in multiple layers one above the other are produced in one mould, the method is called **Stack moulding**. It is used for producing valve bodies, valve bonnets, plugs, yokes, pillow blocks and a wide variety of industrial castings.  **Advantages of Centrifugal Casting** - Obtain castings of better quality - Castings produced more economically. - Parts which are unsuitable to produce by other methods can be cast satisfactorily. - High rate of production can be achieved. - Cleaning and fitting costs are reduced considerably.This produces dense casting which obtains physical properties compared to that of forging. - In some metals this process improves tensile strength because of resultant increase in homogeneity and density. - There are no flow lines in centrifugal castings as obtained in case of conventional gear castings, low lines parallel to the lines of force and grain structure runs perpendicular to the gear tooth line of force. - Castings having thin sections or fine outside surface details can be easily produced. - Percentage of rejection is very low. - Directional solidification can be achieved easily - Easy to inspect, because defects if any will occur on the surface and not inside the castings. **Disadvantages** (*i*) These are limited upto/for certain shapes (axisymmetric) (*ii*) Equipment cost is high. So only for large scale production is profitable. (*iii*) Skilled workers are required for operation and maintenance. **Applications** (*i*) Bearings for electric motors and industrial machinery. (*ii*) Cast iron pipes, alloy steel pipes and tubings. (*iii*) Liners for I.C. engines. (*iv*) Rings, short or long pots and other annular components. **Shell Mold Casting** Shell mold casting or shell molding is a metal casting process in manufacturing industry in which the mold is a thin hardened shell of sand and thermosetting resin binder backed up by some other material. Shell molding was developed as a manufacturing process in Germany in the early 1940\'s. Shell mold casting is particularly suitable for steel castings less than 30 kg; however almost any metal that can be cast in sand can be cast with shell molding process. Also much larger parts have been manufactured with shell molding. Typical parts manufactured in industry using the shell mold casting process include cylinder heads, gears, bushings, connecting rods, camshafts and valve bodies. The Process The first step in the shell mold casting process is to manufacture the shell mold. The sand we use for the shell molding process is of a much smaller grain size than the typical greensand mold. This fine grained sand is mixed with a thermosetting resin binder. A special metal pattern is coated with a parting agent, (typically silicone), which will latter facilitate in the removal of the shell. The metal pattern is then heated to a temperature of 175 ^0^C-370 ^0^C.  The sand mixture is then poured or blown over the hot casting pattern. Due to the reaction of the thermosetting resin with the hot metal pattern a thin shell forms on the surface of the pattern. The desired thickness of the shell is dependent upon the strength requirements of the mold for the particular metal casting application. A typical industrial manufacturing mold for a shell molding casting process could be 7.5mm thick. The thickness of the mold can be controlled by the length of time the sand mixture is in contact with the metal casting pattern. The excess \"loose\" sand is then removed leaving the shell and pattern.  The shell and pattern are then placed in an oven for a short period of time, (minutes), which causes the shell to harden onto the casting pattern. Once the baking phase of the manufacturing process is complete the hardened shell is separated from the casting pattern by way of ejector pins built into the pattern. It is of note that this manufacturing technique used to create the mold in the shell molding process can also be employed to produced highly accurate fine grained mold cores for other metal casting processes. Two of these hardened shells, each representing half the mold for the casting are assembled together either by gluing or clamping. The manufacture of the shell mold is now complete and ready for the pouring of the metal casting. In many shell molding processes the shell mold is supported by sand or metal shot during the casting process. **Properties and Considerations of Manufacturing by Shell Mold Casting** The internal surface of the shell mold is very smooth and rigid. This allows for an easy flow of the liquid metal through the mold cavity during the pouring of the casting, giving castings very good surface finish. Shell Mold Casting enables the manufacture of complex parts with thin sections and smaller projections than green sand molds. Manufacturing with the shell mold casting process also imparts high dimensional accuracy. Tolerances of 0.25mm are possible. Further machining is usually unnecessary when casting by this process. Shell sand molds are less permeable than green sand molds and binder may produce a large volume of gas as it contacts the molten metal being poured for the casting. For these reasons shell molds should be well ventilated. The expense of shell mold casting is increased by the cost of the thermosetting resin binder, but decreased by the fact that only a small percentage of sand is used compared to other sand casting processes. Shell mold casting processes are easily automated The special metal patterns needed for shell mold casting are expensive, making it a less desirable process for short runs. However manufacturing by shell casting may be economical for large batch production **[Advantages of Shell Mold Casting]** Using resin sand to make a thin shell mold or shell core can reduce the amount of molding sand used, the casting parts will get a clear profile and accurate size. -- The process can be done without machining or only a small amount -- Economical for large-batch orders -- High dimensional accuracy -- Thin-walled, complex parts can be manufactured -- Smooth surface of the shell mold cavity -- Easy flow of molten metal during the pouring -- Good surface finish of castings -- Reduced tearing and cracking of casting -- Lower labor requirements **[Disadvantages of Shell Mold Casting]** A drawback of shell molding is the resin-coated sand used in the process is relatively expensive, and the template must be precisely machined, which raises the total cost. In addition, it will also produce a pungent smell when pouring, which to some extent limits the wide application of this method. - The raw materials are relatively expensive. - The process generates noxious fumes which must be removed. - The size and weight range of castings is limited. **[Applications ]** -Crankshaft fabrication -Steel casting parts, fittings -Moulded tubing fabrication -Hydraulic control housing fabrication -Automotive castings (cylinder head and ribbed cylinder fabrication). ### **Casting Defects** Casting defects can be categorized into 5 types **1. Gas Porosity:** Blowholes, open holes, pinholes\ **2. Shrinkage defects:** shrinkage cavity\ **3. Mold material defects:** Cut and washes, swell, drops, metal penetration, rat tail\ **4. Pouring metal defects:** Cold shut, misrun, slag inclusion\ **5. Metallurgical defects:** Hot tears, hot spot.  The various casting defects that appear in the casting process are #### #### **1. Shift or Mismatch** The defect caused due to misalignment of upper and lower part of the casting and misplacement of the core at parting line. **Cause:** \(i) Improper alignment of upper and lower part during mold preparation.\ (ii) Misalignment of flask (a flask is type of tool which is used to contain a mold in metal casting. it may be square, round, rectangular or of any convenient shape.) **Remedies** \(i) Proper alignment of the pattern or die part, molding boxes.\ (ii) Correct mountings of pattern on pattern plates.\ (iii) Check the alignment of flask. #### #### **2. Swell** It is the enlargement of the mold cavity because of the molten metal pressure, which results in localised or overall enlargement of the casting. **Causes** \(i) Defective or improper ramming of the mold. **Remedies** \(i) The sand should be rammed properly and evenly. #### #### **3. Blowholes:** When gases entrapped on the surface of the casting due to solidifying metal, a rounded or oval cavity is formed called as blowholes. These defects are always present in the cope part of the mold. **Causes** \(i) Excessive moisture in the sand.\ (ii) Low Permeability of the sand.\ (iii) Sand grains are too fine.\ (iv) Too hard rammed sand.\ (v) Insufficient venting is provided. **Remedies** \(i) The moisture content in the sand must be controlled and kept at desired level.\ (ii) High permeability sand should be used.\ (iii) Sand of appropriate grain size should be used.\ (iv) Sufficient ramming should be done.\ (v) Adequate venting facility should be provided. #### #### **4. Drop** Drop defect occurs when there is cracking on the upper surface of the sand and sand pieces fall into the molten metal. **Causes** \(i) Soft ramming and low strength of sand.\ (ii) Insufficient fluxing of molten metal. Fluxing means addition of a substance in molten metal to remove impurities. After fluxing the impurities from the molten metal can be easily removed.\ (iii) Insufficient reinforcement of sand projections in the cope. **Remedies** \(i) Sand of high strength should be used with proper ramming (neither too hard nor soft).\ (ii) There should be proper fluxing of molten metal, so the impurities present in molten metal is removed easily before pouring it into the mold.\ (iii) Sufficient reinforcement of the sand projections in the cope. #### #### **5. Metal Penetration** These casting defects appear as an uneven and rough surface of the casting. When the size of sand grains is larges, the molten fuses into the sand and solidifies giving us metal penetration defect. **Causes** \(i) It is caused due to low strength, large grain size, high permeability and soft ramming of sand. Because of this the molten metal penetrates in the molding sand and we get rough or uneven casting surface. **Remedies** \(ii) This defect can be eliminated by using high strength, small grain size, low permeability and soft ramming of sand. #### #### **6. Pinholes** They are very small holes of about 2 mm in size which appears on the surface of the casting. This defect happens because of the dissolution of the hydrogen gases in the molten metal. When the molten metal is poured in the mold cavity and as it starts to solidify, the solubility of the hydrogen gas decreases and it starts escaping out the molten metal leaves behind small number of holes called as pinholes. **Causes** \(i) Use of high moisture content sand.\ (ii) Absorption of hydrogen or carbon monoxide gas by molten metal.\ (iii) Pouring of steel from wet ladles or not sufficiently gasified. **Remedies** \(i) By reducing the moisture content of the molding sand.\ (ii) Good fluxing and melting practices should be used.\ (iii) Increasing permeability of the sand.\ (iv) By doing rapid rate of solidification. #### #### **7. Shrinkage Cavity** The formation of cavity in the casting due to volumetric contraction is called as shrinkage cavity. **Causes** \(i) Uneven or uncontrolled solidification of molten metal.\ (ii) Pouring temperature is too high. **Remedies** \(i) This defect can be removed by applying principle of directional solidification in mold design.\ (ii) Wise use of chills (a chill is an object which is used to promote solidification in a specific portion of a metal casting) and padding. #### #### **8. Cold Shut** It is a type of surface defects and a line on the surface can be seen. When the molten metal enters into the mold from two gates and when these two streams of molten metal meet at a junction with low temperatures than they do not fuse with each other and solidifies creating a cold shut (appear as line on the casting). It looks like a crack with round edge. **Causes** \(i) Poor gating system\ (ii) Low melting temperature\ (iii) Lack of fluidity **Remedies** \(i) Improved gating system.\ (ii) Proper pouring temperature. #### #### **9. Misrun** When the molten metal solidifies before completely filling the mold cavity and leaves a space in the mold called as misrun. **Causes** \(i) Low fluidity of the molten metal.\ (ii) Low temperature of the molten metal which decreases its fluidity.\ (iii) Too thin section and improper gating system. **Remedies** \(i) Increasing the pouring temperature of the molten metal increases the fluidity.\ (ii) Proper gating system\ (iii) Too thin section is avoided. #### **10. Slag Inclusion** This defect is caused when the molten metal containing slag particles is poured in the mold cavity and it gets solidifies. **Causes** \(i) The presence of slag in the molten metal **Remedies** \(i) Remove slag particles form the molten metal before pouring it into the mold cavity. #### #### **11. Hot Tears or Hot Cracks** when the metal is hot it is weak and the residual stress (tensile) in the material cause the casting fails as the molten metal cools down. The failure of casting in this case is looks like cracks and called as hot tears or hot cracking. **Causes** \(i) Improper mold design. **Remedies** \(i) Proper mold design can easily eliminate these types of casting defects.\ (ii) Elimination of residual stress from the material of the casting. #### #### **12. Hot Spot or Hard Spot:** Hot spot defects occur when an area on the casting cools more rapidly than the surrounding materials. Hot spot are areas on the casting which is harder than the surrounding area. It is also called as hard spot. **Causes** \(i) The rapid cooling an area of the casting than the surrounding materials causes this defect. **Remedies** \(i) This defect can be avoided by using proper cooling practice.\ (ii) By changing the chemical composition of the metal. #### #### **13. Sand Holes** It is the holes created on the external surface or inside the casting. It occurs when loose sand washes into the mold cavity and fuses into the interior of the casting or rapid pouring of the molten metal. **Causes:** \(i) Loose ramming of the sand.\ (ii) Rapid pouring of the molten metal into the mold results in wash away of sand from the mold and a hole is created.\ (iii) Improper cleaning of the mold cavity. **Remedies** \(i) Proper ramming of the sand.\ (ii) Molten metal should be poured carefully in the mold.\ (iii) Proper cleaning of the molten cavity eliminates sand holes. #### #### **14. Dirt** The embedding of particles of dust and sand in the casting surface, results in dirt defect. **Causes:** \(i) Cursing of mold due to improper handling and Sand wash (A sloping surface of sand that spread out by stream of molten metal).\ (ii) Presence of slag particles in the molten metal. **Remedies:** \(i) Proper handling of the mold to avoid crushing.\ (ii) Sufficient fluxing should be done to remove slag impurities from molten metal. #### #### **15. Warpage:** It is an accidental and unwanted deformation in the casting that happens during or after solidification. Due to this defect, the dimension of the final product changes. **Causes:** \(i) Due to different rates of solidification of different sections. This induces stresses in adjoining walls and result in warpage.\ (ii) Large and flat sections or intersecting section such as ribs are more prone to these casting defects. **Remedies** \(i) It can be prevented by producing large areas with wavy, corrugated construction, or add sufficient rib-like shape, to provide equal cooling rates in all areas.\ (ii) Proper casting designs can reduce these defects more efficiently. #### #### **16. Fins** A thin projection of metal, not considered as a part of casting is called as fins or fin. It is usually occurs at the parting of the mold or core section. **Causes**: \(i) Incorrect assembling of mold and cores.\ (ii) Insufficient weight of the mold or improper clamping of the flask may produce the fins. **Remedies** \(i) Correct assembly of the mold and cores.\ (ii) There should be sufficient weight on the top part of the mold so that the two parts fit together tightly.