Truck Company Operations (CFD Firefighter Manual) PDF
Document Details
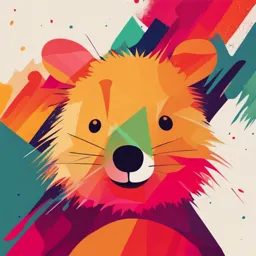
Uploaded by ProdigiousJasper737
Columbus Division of Fire
2025
Captain Sexton Towns
Tags
Summary
This manual provides a guide for CFD firefighters on truck company operations, covering various aspects like roles and responsibilities, standard operating procedures (SOPs), equipment, and maintenance. It aims to give firefighters the knowledge and practical information to excel in emergency responses. This is not a past paper.
Full Transcript
TRUCK COMPANY OPERATIONS A MANUAL FOR THE CFD FIREFIGHTER Adapted Version for the 2025 CSC Fire Promotional Exams Revised 08/30/21 Revised 08/30/21 TRUCK COMPANY OPERATIONS Riding on a CFD Ladder Company is a privilege. A privilege that every fire...
TRUCK COMPANY OPERATIONS A MANUAL FOR THE CFD FIREFIGHTER Adapted Version for the 2025 CSC Fire Promotional Exams Revised 08/30/21 Revised 08/30/21 TRUCK COMPANY OPERATIONS Riding on a CFD Ladder Company is a privilege. A privilege that every firefighter on CFD gained when they graduated the training academy. With that privilege comes a lot of responsibility. In this manual, you will learn your responsibilities when riding on a CFD Ladder Company. You will learn the roles and duties of each riding position on the ladder company. Part of being a Columbus Firefighter requires you to know and be able to effectively execute all riding positions on every truck. Granted, there may be more desirable positions on certain trucks, but the responsibility of the firefighter stays the same. The CFD Ladder Company is no different. Some may view being the tiller driver, or the inside firefighter, or even the officer as the best position, but they are all equally important. If one fails at successfully executing the tasks associated with each position, the crew fails. This manual will help teach you the tactics of each position to ensure success. To become what some senior firefighters refer to as a “Trucker” requires determination, hard work, training, and self-motivation. Not everyone assigned to a ladder is considered a “Trucker.” This title is only inferred when one possesses the drive and desire to become truly exceptional at their craft. It also takes experience on all types of emergency scenes. This experience will help the ladder company firefighter apply the appropriate skills at the appropriate time, thus ensuring success on the scene. The Columbus Division of Fire has been truly blessed to have amongst its members those that possess this drive and determination to not only excel at their craft, but to help others excel as well. This manual has taken the input passed down by generations of “Truckers”, who not only wanted to do their best, but also wanted to share that knowledge so others could carry on that legacy. This manual was created to help guide Columbus Firefighters as they progress through their apprenticeship training. However, this book is not limited to apprenticeship training. It has been designed as reference material for all members of the department. The information within this manual has been gathered from past experiences, manufacturer manuals, calculations, and previous training. The most important of these sources is the experiences shared by past and present members of the Columbus Fire Department. Their successes, and equally important, their failures, have been used to construct this manual so that you can better understand your role on a CFD Ladder Company. In the first section of the manual, you will find experiences shared by current and retired CFD members. These stories have been shared to allow you to learn from their experiences, good or bad, and to help you make your own decisions when the time comes. The fire service is an experience-based job; unfortunately, there is no substitute for experience. We should pay close attention to what others have learned as we strive to work hard and train day in and day out. Moving into the second section of the manual, you will find CFD standard operating procedures (SOPs). The SOPs pertain to the ladder company’s actions at fire scenes and other emergency scenes. You should take time to understand these SOPs, as they are a guideline to aid your initial Revised 08/30/21 actions as well as work with other companies during an emergency response. It is important to understand that SOPs should be followed if at all possible. However, it is also impossible to create an SOP for every situation you encounter on this job. Some decisions must be guided by experience and what the situation presents to you. The third section will cover the tools and equipment carried on CFD ladder companies. The equipment section is designed to help you become more familiar with CFD ladder company tool uses. The fourth section will cover care and maintenance for that equipment. CFD provides us with a great complement of resources and equipment. It is our responsibility to be proficient in their use and capabilities. The fifth section will provide you with information on the different makes and models of Ladder Trucks that CFD has in its fleet. It won’t teach you every single detail about each truck, because that would be nearly impossible. It will give you the information needed to be able to set-up and short-jack each type of ladder truck in the fleet, and some of the important things you should keep in mind when operating a certain type of ladder truck. The sixth section of this manual will inform you about the responsibilities of the different riding positions on the truck company. When riding on a ladder company, job functions are broken down by what position you are riding on the truck. The seventh and subsequent sections of this manual will discuss the multiple tasks that the truck company is/could be responsible for. These sections will make up a large portion of this manual. The final section of the manual will contain both hands-on skill sheets and teach-back topics. These skills are not just for apprentice firefighters, but for the veteran firefighter as well. You can never train too much for a job that can kill you. Don’t ever feel like you are inconveniencing someone else by becoming better at your job. There are plenty of skills that a firefighter riding a truck company should stay proficient at, and you won’t become proficient at them by sitting in the recliner. Train, learn, and share any knowledge that you feel someone else should know. Finally, we want you to understand that this manual is not set in stone. It can and will be changed as our department continues to learn new ideas and techniques. If there is something you do not understand, ask. The greatest thing about CFD is the amazing people that work for it. Our membership is our most valuable resource. Please pass on what you have learned, as this is the life blood of the fire service. Respectfully, Captain Sexton Towns Revised 08/30/21 TABLE OF CONTENTS EXPERIENCE Captain Lash Training Videos 2 437 N. Garfield Ave.—FF Sam Towns 4 4783 Bourke Road—Station 24 1 Unit 6 1803 E. Blake Ave.—BC Joe Leffe 10 SOPS 01-03-20 Rescue Factors 15 01-03-21 All Clear 17 01-03-25 Property Conservation 19 01-03-27 Ventilation Factors 21 01-03-28 Forcible Entry 24 01-04-01 Personal Protective Equipment 25 02-02-02 Staging Level 1 “A” Assignments 29 02-02-03 Fire Response Assignment 31 02-03-01 Residence Fires—Single/Double 36 02-03-04.04 High-Rise USE Group 38 02-03-04.07 High-Rise Ventilation 40 02-03-09 Carbon Monoxide 41 02-03-13 Gas Leak Response 44 02-03-17 Electrical Emergencies 45 EQUIPMENT Equipment Checks 51 STIHL MSA 220 C Chainsaw 57 STIHL MS 046, 460, and 461R Chainsaws 58 STIHL TS 400 and 700 Series Circular Saws 59 STIHL MS and TS 500i Fuel Injected Saws 60 Ground Ladders 61 Honda Generator EU1000i/2000i 63 Honda Generator EB 5000X/EM 6500SX 65 Adapters, Cords, and Lights 69 Positive Pressure RAMFANS 71 Smoke Ejectors 72 Columbus Rope Bag 73 Rabbit Tool and Hydra-Ram II 74 Revised 08/30/21 SMALL ENGINE MAINTENANCE Small Engine Maintenance Overview 76 Two-Stroke vs. Four-Stroke Engines 78 How to Properly Mix Two-Stroke Fuel 80 K-100 Fuel Additive 81 STIHL Chainsaws 82 STIHL Chainsaws—Changing a Chain 87 STIHL Circular Saws 91 STIHL Circular Saws—Changing a Blade 95 Honda Generators 98 Saw Operations—Reactive Forces 101 LADDER COMPANY APPARATUS Columbus Truck Reference Page 105 Platforms 106 Tillers 113 Short-Jacking 121 Emergency Power Unit (EPU) 130 Scene Lighting and Generators 135 FIREFIGHTER ASSIGNMENTS Firefighter Assignments Overview 148 Ladder Officer Responsibilities 150 Inside Firefighter Responsibilities 155 Ladder Driver Responsibilities 156 Tiller/Outside Vent Firefighter 166 SPOTTING THE TRUCK Spotting the Truck Overview 170 Basic Review and Terminology 172 General Run Type Considerations 174 Arrival Order 178 On Scene Operations 181 Defensive Operations 192 LADDERING THE STRUCTURE Laddering the Structure Overview 194 Before the Emergency 196 Setting the Truck Up for Success 198 On the Scene 200 Revised 08/30/21 FORCIBLE ENTRY Forcible Entry Overview 206 Conventional Forcible Entry 208 Initial Size-Up 209 Sizing Up an Individual Door 211 Forcible Entry Tools 215 Circular Saws 223 Methods of Forcible Entry 227 Residential Doors—Single Firefighter 236 Padlocks 238 Security Bars and Storm Doors 240 Garage Doors 243 Commercial Roll-Up Doors 245 Block Walls 248 Other Forcible Entry Considerations 250 Take Pride in Your Craft 257 SEARCH AND RESCUE Search and Rescue Overview 258 Search and Rescue Size-Up Factors 260 Residential Search and Rescue 262 VEIS 265 Victim Removal 269 Search Rope Deployment 278 VENTILATION FUNDAMENTALS Ventilation Fundamentals Overview 292 Ventilation Size-Up Factors 294 Types of Ventilation 297 Horizontal Ventilation 298 Natural Ventilation 299 Mechanical Ventilation 300 Positive Pressure Ventilation 301 Negative Pressure Ventilation 305 Hydraulic Ventilation 306 Vertical Ventilation 308 ROOF OPERATIONS Roof Operations Overview 310 Types of Roofs 312 Roof Pitches 317 Revised 08/30/21 Helpful Roof Tips 318 Residential Vertical Ventilation 321 Residential Louver—Roof Ladder 322 Residential Louver—Aerial Ladder 326 Commercial Flat Roof Ventilation 329 WATERWAY OPERATIONS Waterway Operations Overview 342 Offensive Operations 345 Defensive Operations 346 Flowing Water from a Tiller 347 Flowing Water from a Platform 353 Other Considerations 358 SALVAGE AND OVERHAUL Salvage and Overhaul Overview 360 Salvage Operations 362 Salvage Tools 363 Salvage Functions 367 Starting the Overhaul Process 368 Common Void Spaces 372 SERVICE CALLS AND UTILITIES Service Calls and Utilities Overview 376 Fire Service Runs 377 Natural Gas Emergencies and Response 379 Carbon Monoxide Alarms 384 Gas Monitoring and Detecting 388 Elevator Operations: An Advanced Understanding 392 Elevator Types 393 Basic Elevator Rescue Procedures 399 Securing Residential Water 406 Securing Commercial Water 410 Electrical Emergencies 417 Smoking Outlets and Breaker Panels 418 Wires Down and Pole Fires 421 Cutting Drip Loops 425 Remote Power Shut-Off Options 430 Revised 08/30/21 TEACH-BACKS AND HANDS-ON SKILLS TB-1: Emergency Power Unit (EPU) 435 TB-2: Outside Ladder Team Responsibilities 436 TB-3: Ventilation Fundamentals Review 437 HO-1: Replacing a Saw Chain/Blade 438 HO-2: Ventilation and Short-Jacking 439 HO-3: Ladder Care and Halyard Replacement 441 ACKNOWLEDGMENTS 442 Revised 08/30/21 EQUIPMENT OVERVIEW TRUCK OPERATIONS MANUAL SECTION TOPICS Honda Generator EB 5000X/EM Equipment Checks 6500 SX Stihl MSA 220 C Chainsaw Adapters, Cords, and Lights Stihl MS 046, 460, and 461R Positive Pressure RAMFANS Chainsaws Stihl TS400 and 700 Series Smoke Ejectors Circular Saws Stihl MS and TS 500i Fuel Columbus Rope Bag Injected Saws Ground Ladders Rabbit Tool and Hydra-Ram II Honda Generator EU1000i/2000i SECTION OBJECTIVES Understand the process for checking Understand the specifications and equipment during truck checks uses of the Honda Generator EU1000i/2000i Understand the specifications and Understand the specifications and uses of the Stihl MSA 220 C Chainsaw uses of the Honda Generator EB 5000X/EM 6500 SX Understand the specifications and Understand the specifications and uses of Stihl MS 046, 460, and 461R uses for various adapters, cords, and Chainsaws lights Understand the specifications and Understand the specifications and uses of Stihl TS400 and 700 Series uses of RAMFANS and smoke ejectors Circular Saws Understand the specifications and Understand the specifications of the uses of Stihl MS and TS 500i Fuel Columbus rope bag Injected Saws Understand how to maintain ground Understand the specifications and ladders uses for the rabbit tool and the Hydra- Ram II Revised 08/30/21 50 EQUIPMENT CHECKS OVERVIEW Everyone on CFD knows that after roll call, firefighters first place their PPE on the truck, then do equipment checks. This section covers some specific suggestions for checking the equipment on ladder trucks. Some of these suggestions may be new, and some suggestions will be things firefighters already do every shift. Checking the equipment on the truck is a very important part of every firefighter’s day, and it is something that must be taken seriously. Firefighter and civilian lives may depend on the readiness of these tools. Most CFD ladder companies carry the same complement of tools, with an additional tool here and there that crews have gotten on their own. It is the crew’s job to make sure those tools are functioning properly; when the time comes there must be no doubt that the tools are ready to get the job done. Each firefighter will develop their own method of checking the various apparatus and equipment in the Division. Newly assigned firefighters can seek the help of more senior assigned firefighters at their station to help familiarize them with the truck during their initial checks. Listening to the off-going crew’s pass on report can also be helpful when performing morning checks. These reports can help inform oncoming firefighters of any equipment that was used, is broken, or is currently missing. A thorough check of all equipment should always be done. However, if the off-going crew reports a busy shift with a significant incident (especially structure fires), firefighters should increase their attentiveness during the check. PPE AND SCBA During equipment checks in the morning, most companies start off by checking their own personal PPE and SCBA. All firefighters, including the ladder driver and Tiller/OSV firefighter, should be checking their PPE and SCBA. This equipment is designed to protect firefighters; every firefighter must take the time to make sure it is working correctly. Below is a short list of some of the actions firefighters should be taking in the morning when checking their gear: Put on the face piece and breathe air from the MMR Check the PASS device; let it cycle through all the alarms Check the purge valve, control module, and the Vibra-Alert Make sure the SCBA straps are placed appropriately for easy donning Make sure the SCBA cylinder is completely full at 5500 PSI Make sure each piece of gear is set-up as desired Portable radios should be checked to make sure the battery is full o Many firefighters set their portable radio to the fireground that they would respond on if the fire was across the street from the fire house. This removes any unnecessary steps when responding to a fire close to the station Revised 08/30/21 51 HAND TOOLS While working on ladder companies, a majority of incidents firefighters respond to will involve carrying some type of hand tools. Most CFD ladder companies have hand tools safely stored in the cab, allowing crews to come off the truck ready for work. Remember, the ladder crew’s number one concern is life safety; seconds count when possible victims are inside a structure fire. Which tools are carried in the cab depends on what each specific ladder company has decided on. If firefighters are TT’d in for the day and the tool they prefer to carry is not in the cab, they should ask the officer on the truck what he/she prefers for them to carry. During equipment checks, firefighters should be checking the truck to ensure the hand tools are in their proper storage location, are clean, and are in good working order. If a firefighter sees that an axe head is loose, get it exchanged at Tools and Equipment. If the adz on the Halligan needs to be sharpened or has burrs, firefighters should get out a file and hone it. If a piece of equipment is dirty from a fire the previous shift had the night before, clean it. The city does a great job of allowing the Division to buy nice equipment; all firefighters should do their part to ensure this equipment is maintained and ready at all times. The list below shows what should be checked on various pieces of equipment: Sledge hammer—Inspect the head and the handle. The striking surface should be wiped with a light oil to protect from rust. Handles should be checked for any chips or cracks Axe—Check the cutting surface for nicks or dings. Use a file and hone to sharpen the surface. Check the striking surface for any big chips or dings. Check for mushroomed metal; if any is found, use a file to clean up the striking surface. Handles should be checked for any chips or cracks Halligan—Pick should be tapered and sharp. The adz should be sharp with no damaged metal; use a file to remove any burrs. The forks should also be sharp Pike Poles—Make sure they are clean. The heads should be lightly oiled (photos below) Rope Bags—Make sure the length is labeled on the bag. Inspect the rope after each use Water Can—Ensure the can is pressurized to its proper range and feels like it has the appropriate amount of water in it Battery Lights—Ensure hand lights are stored properly and charging. Milwaukee lights should have a full charge Revised 08/30/21 52 COMPARTMENT CHECKS The majority of the equipment on the ladder truck is carried in one of the many compartments on the trucks. All this equipment should be checked daily. Each crew and firehouse will have a specific manner in which they check the truck. Some crews may have assigned compartments or equipment they are responsible for checking individually; others may work around the truck as a group. When checking a compartment, first look to ensure that all the equipment that is normally in the compartment is present. Firefighters who are checking the truck for the first time might need an equipment list or a firefighter who knows that truck to look over the truck with them. After ensuring all the correct equipment is within the compartment, make sure the equipment is clean and in good working order. Equipment that has a motor on it should be started and operated to see if it is working properly, along with topping off the fuel. Firefighters should ensure they are running gas powered equipment outside or with proper ventilation in place. Battery powered equipment should be checked for proper function and to ensure the batteries are fully charged. If a firefighter finds a tool they are unfamiliar with, they should ask the assigned crew to go over the tool with them to give them an understanding of its uses and to ensure they can operate it if needed. The scene of an emergency should not be the first time a firefighter has taken a tool off the truck. The next few pages will give some specific examples and considerations when checking various pieces of equipment on the ladder. This is certainly not an all-inclusive list, but it can be helpful for firefighters not normally assigned to a ladder company. More in-depth information can be found in each tool’s corresponding section of this manual. Revised 08/30/21 53 PPV Fans—Start them daily; make sure Salvage Kits—Make sure that the proper no trash or plastic is on the fan. tools are in the kit (Normally staplers, utility Firefighters should make sure they are knives, window plastic, and salvage plastic). familiar with how to adjust the angle on Make sure the staple guns are loaded the fans. correctly and not jammed. Portable Light—Check all lights to ensure Battery Powered Tools—Make sure all the bulbs are working and are not damaged. the battery packs are fully charged. Quartz lights can be checked in conjunction Any tool on the truck that is powered with cord reels and extension cords to make by a battery should be checked to sure those are working as well. Check to see ensure it is working properly. if the light will hold the position it is set to. Revised 08/30/21 54 Circular Saw—Make sure the blade is on correctly and the nuts are tight. Check the blade and replace it if needed. Start the saw and allow it to reach its operating temperature (about 5 minutes). Chain Saws—Make sure the chain is on correctly and that it has the correct tension. Make sure the chain does not have too many missing teeth. Start the saw and allow it to reach its operating Portable Generators—Start it and place a temperature (about 5 minutes). When left load on it by using it to power a fan or light running, a towel placed under the saw can with it. Make sure generators are started reduce vibrations and prevent damage to and stopped with no load. The auto throttle the saw over time. function (if equipped) should be left off until the generator engine has had time to warm up. The photo below shows the auto throttle in the off position. Box Fan—Start box fans daily. Firefighters should make sure they are familiar with how to use the fan hanger. Revised 08/30/21 55 Extra SCBA Bottles—Make sure they are at 5500 PSI. If it is at 5,000 PSI, do not be lazy; go top it off. Ground Ladders—Make sure the dogs and pawls are locked and that the ladders are oriented on the truck how your company wants them (Right or left shoulder carry). Check the halyard. If pike poles are attached to the ladders, make sure the straps on them are tight, and make sure Platform Ladder—Make sure there is a pike the pike pole is closer to the door. pole (8 ft. minimum) in the fly section and there is an axe in the bucket. Check to ensure the emergency stop switch (photo below) is disengaged. Make sure the nozzles and water curtain are closed. Aerial Ladder (Tiller)—Make sure there is a pike pole (8 ft. minimum) and an axe at the tip. Make sure the waterway is in rescue mode, and make sure the waterway intakes are closed on both sides. Revised 08/30/21 56 STIHL MSA 220 C CHAINSAW IDENTIFICATION AND GENERAL SPECIFICATIONS Newest saw in the Division, designed to replace the electric corded Stihl chainsaws 3 basic components—12” guide bar, chain, and battery pack Electric motor driven AP 300 S Battery o 1 solid red LED—battery is too hot/too cold o 4 flashing red LEDs—bad battery (faulty) o 3 solid red LEDs—chainsaw is too hot o 3 flashing red LEDs—chainsaw malfunction (electronics/motor) o Remove the battery when changing the chain or performing maintenance 7.1 oz. bar oil reservoir Weighs roughly 6.4 lbs. (without the battery) CHAIN SPECIFICATIONS Information stamped on the guide bar of the saw Carbide toothed chain 3/8” PICCO (Pitch: distance from one drive link to the next, divided by two) o The larger the pitch, the heavier/bigger the chain o Stamped on the raker with a “6”—Indicating 3/8” pitch.050” gauge (Width of the drive link) o Stamped on the drive link/tang with a “3”—Indicating.050” gauge 44 drive links; 22 cutting teeth (If 3 or more teeth are missing, replace the chain) WHEN TO USE Overhaul RIT scenarios Plywood on vacant structures Clearing trees/limbs for access Anywhere internal combustion saws will not run ADVANTAGES/DISADVANTAGES Speed and ease of use—quick to place into service Not subject to flooding like a traditional saw Ability to operate in a smoke-filled environment Does not have the same power compared to the Division’s larger internal combustion saws. Firefighters cannot expect this saw to operate at the same capacity as those. They are different saws, each with their own advantages and disadvantages Training Video 1: Saw Info Training Video 4: Bar Oil and Basic Care Training Video 2: Bar and Chain Training Video 5: Tips and Troubleshooting Training Video 3: Assembly and Chain Training Video 6: Safety Tips and Extra Info Revised 08/30/21 57 STIHL MS 046, 460, AND 461R CHAINSAWS IDENTIFICATION AND GENERAL SPECIFICATIONS 460/461—R refers to wraparound handle and larger starter grip 3 basic components—guide bar, chain, and powerhead Two-stroke engine Fuel mix ratio of 50:1 (2.6 fl oz. of oil to 1 gallon of gasoline) No more than 10% ethanol 20” guide bar 27 oz. fuel reservoir; 11 oz. bar oil reservoir Weighs roughly 15 lbs. (Powerhead only) CHAIN SPECIFICATIONS Information stamped on the guide bar of the saw Carbide toothed chain 3/8” PICCO (Pitch: Distance from one drive link to the next, divided by two) o The larger the pitch, the heavier/bigger the chain.050” gauge (Width of the drive link) 72 drive links 36 cutting teeth (If three or more are missing, replace the chain) Green drive link = low kick back chain; yellow drive link = more aggressive chain WHEN TO USE Roof ventilation Window cutdowns RIT scenarios Clearing large trees/limbs Cutting wooden garage doors Plywood on a vacant structure GENERAL CARE/MAINTENANCE GUIDELINES Fully choke the saw when disassembling for cleaning Turn the guide bar over after each use to promote even wear (Use a single cut file to file down burrs if necessary) When starting the saw for morning checks, allow the saw to run for 2 to 5 minutes to reach the proper operating temperature ADVANTAGES/DISADVANTAGES Versatile saw with large cutting depth (16”) Requires regular maintenance and care for proper operation (Carbureted) Internal combustion engine requires fresh, clean air to run (will not run in heavy smoke) Revised 08/30/21 58 STIHL TS400 AND 700 SERIES CIRCULAR SAW IDENTIFICATION AND GENERAL SPECIFICATIONS 3 basic components—arm, blade, and powerhead Two-stroke engine Fuel mix ratio of 50:1 (2.6 fl oz. of oil to 1 gallon of gasoline) No more than 10% Ethanol; minimum 89 octane Max spindle speed—5,350 RPM Weights range between 21 and 26 lbs. BLADE SPECIFICATIONS 12-inch blades have a max cutting depth of 3.9” 14-inch blades have a max cutting depth of 4.9” Composite blades come in two different types, metal or masonry o Inspect for chemical damage, deterioration, and fraying Dax blades—cuts metal up to 3/16” thick; multipurpose blade with carbide cutting teeth o Inspect for missing teeth, cracks, and fissures Diamond blade—cuts metal/concrete o Check for missing diamond bits, mushrooming on heads, and cracks or fissures GENERAL CARE/MAINTENANCE GUIDELINES Fully choke the saw when disassembling for cleaning Inspect the blade frequently after each use and change when needed When starting the saw for morning checks, allow the saw to run for 2 to 5 minutes to reach the proper operating temperature WHEN TO USE Roof ventilation Rebar and thicker metal RIT scenarios Masonry work Garage doors Vacant, boarded-up structures ADVANTAGES OF 700 The 700 is the most powerful circular saw the Division currently has Large blade ensures deeper cut depth for user DISADVANTAGES OF 700 Larger saw = more gyroscopic effect when cutting. Outboard operations are not recommended The weight and size of the saw makes it difficult to handle in odd positions, such as a firefighter cutting above their head Revised 08/30/21 59 STIHL MS AND TS 500i FUEL INJECTED SAWS OVERVIEW The Stihl MS 500i chainsaw and the Stihl TS 500i circular saw are fuel-injected saws that have been newly acquired by the Division Many of the basic components of the saws are the same as the non-fuel injected saws The main difference is the injection system and the electronics It is highly recommended that all firefighters read the associated manuals for each unit linked below. This sheet is only a basic introduction to the equipment MS 500i CHAINSAW INFORMATION Click here to view Stihl MS 20” bar, 72 drive links, 36 teeth 500i Chainsaw Manual Displacement—4.83 cu. in. Idle speed—3,000 RPM Max engine speed—13,700 RPM Fuel—50:1 mixed ratio Start-up procedures o Engage the chain brake o Remove the scabbard Click here to view Stihl MS 500i o Press the decompression valve Chainsaw Injection Video o Press the manual fuel pump bulb at least 8 times o Hold the saw firmly and pull the starter grip o Do not let the starter grip snap back or fully extend it o Once the saw is running, it is now ready TS 500i CIRCULAR SAW INFORMATION 14-inch blade—4.9” max cutting depth Displacement—4.41 cu. in. Idle speed—2,500 RPM Max engine speed—9,000 RPM Spindle Speed—5,350 RPM Fuel—50:1 mixed ratio Start-up procedures o Press the throttle trigger lockout and throttle trigger simultaneously o Move the stop switch to (I) o Release the throttle trigger, stop switch, and throttle trigger lockout in succession—this is the starting throttle position o Press the decompression valve o Press the manual fuel pump bulb 7-10 times o Hold the saw firmly and pull the starter grip o Do not let the starter grip snap back or fully extend it o Once the saw is running, blip the throttle. The saw is now ready Click here to view Stihl TS 500i Circular Saw Injection Video Click here to view Stihl TS 500i Circular Saw Manual Revised 08/30/21 60 GROUND LADDERS OVERVIEW CFD uses aluminum ground ladders, manufactured by Duo-Safety Ladder Corporation All extension ladders and roof ladders meet NFPA specifications For more information about ground ladders, see the Laddering the Structure section in this manual NFPA RATINGS AND STANDARDS Tools and Equipment performs annual service testing of extension and roof ladders in October every year to ensure they meet NFPA 1931 standards All extension ladders and roof ladders meet the following NFPA specifications: o Rungs load tested—1,000 lbs. o Rung spacing—14 inches o Weight rating—750 lbs with a 4:1 safety factor o Minimum width between ladder beams—16 inches Specialty ladders including the folding Attic Ladder, Fresno Ladder, and Little Giant Combination Ladder do not conform to NFPA 1931 or 1932 CARE AND MAINTENANCE The halyard should be inspected after each use. If the halyard is in good condition but adjustments are necessary, the halyard can be retied at the station. For a broken or damaged halyard, take it out of service and contact Tools and Equipment for replacement Using a mild detergent and soft bristle brush is sufficient for most cleaning. If needed, a generic lubricant such as WD-40 can be used in moderation on moving parts such as springs on hooks, attic ladders, etc. No ladder should require more than 75 lbs of force to raise. If it feels like more than this, the ladder should be immediately cleaned and waxed o Bar wax can be obtained from supply and applied liberally to the bed and fly section o Wax ladders every 6 months at a minimum; this can be adjusted based on usage rates HEAT SENSOR LABELS Visual warning labels are located on all aluminum ladders; four labels per ladder section These labels turn black if any heat greater than 300° F is present Once the aluminum ladder material (6061-T6 alloy) reaches 300° F, the ladder could lose at least 25% of its load capacity If a black sensor is found, take the ladder out of service and contact Tools and Equipment Revised 08/30/21 61 COMMON LADDER COMPLEMENTS Ladder complements will vary from one truck to another. The images below show an example of a common ladder complement that can be found throughout the Division Columbus Fire does not carry any ground ladder over 35’, which by NFPA standard would require “tormentor” or “bangor” poles for lateral stabilization Currently Tools and Equipment is ordering 2-section extension ladders. Previously, due to how ladders were stored on the SP model of Sutphen Platforms, 35’ extension ladders were ordered with 3-sections Ladder Size Weight Engines Ladders Fresno 30 lbs - 1 10’ Attic 16 lbs 1 1 14’ Roof 28 lbs 1 1 16’ Roof 39 lbs - 1 20’ Extension 60 lbs - 1 24’ Extension 72 lbs 1 2 28’ Extension 87 lbs - 1 35’ Extension 2 fly 122 lbs - 1 35’ Extension 3 fly 129 lbs - - Revised 08/30/21 62 HONDA GENERATOR EU1000i/2000i SPECIFICATIONS EU1000i Engine—Honda GX100 Displacement: 3.01 cu in. AC output: 120-volt, 1000-watt maximum, 900-watt rated Oil type and capacity: 10W-30 8oz Fuel tank capacity—.55 gallon Run time per tankful—approximately 3 hours under full load Dry weight—29 lbs SPECIFICATIONS EU2000i Engine—GX100T Displacement: 6.01 cu in. AC output: 120-volt, 2000-watt maximum, 1600-watt rated Oil type and capacity: 10W-30 13oz Fuel tank capacity—.95 gallon Run time per tankful—approximately 4 hours under full load Dry weight—45 lbs STORAGE AND FUELING To prevent fuel spillage, the generator should be stored upright in its normal operating position with the engine (on/off) switch and the fuel filler cap vent lever both turned off Use regular unleaded gasoline with an octane rating of 86 or higher, and no more than 10% ethanol or 5% methanol INDICATOR LIGHTS The Output Indicator Light (Green) is illuminated when the generator is operating normally. It indicates that the generator is producing electrical power at the receptacles If the generator is overloaded, or if there is a short circuit in a connected appliance, the Overload Indicator Light (Red) will go on. After about four seconds, current to the connected appliance will shut off, and the Output Indicator Light (Green) will turn off The Oil Alert system is designed to prevent engine damage caused by an insufficient amount of oil in the crankcase. Before the oil level can fall below the safe limit, the Oil Alert indicator light comes on and the Oil Alert system will automatically stop the engine These indicator lights have a slightly different layout on the EU2000 than on the EU1000. However, the lights operate the same and mean the same thing on both models Revised 08/30/21 63 ECO THROTTLE SWITCH When the Eco Throttle switch is on, engine speed is automatically lowered when loads are reduced, turned off, or disconnected. When appliances are turned on or reconnected, the engine returns to the proper speed to power the electrical load Turning the Eco Throttle on is recommended to minimize fuel consumption and reduce noise level when less than a full load is needed. Examples could include long-term events with low draw appliances, such as 500-watt quartz lights set up for a fire investigator to perform an investigation at a fire scene Engine should be run for a few minutes to warm up prior to turning on the Eco Throttle Having the Eco Throttle turned off means the generator will function like normal and idle at the designated setting when no load is attached. The Eco Throttle should be turned off for incidents such as working fires, where numerous appliances can be plugged in and the electrical load will frequently be changing CONNECTING A LOAD TO THE GENERATOR Verify the engine is running Ensure the Output Indicator Light is on Make sure the appliance is in good working order Make sure the electrical rating of the appliance does not exceed that of the generator. Never exceed the maximum power rating of the generator. Power levels between the rated amount of the generator and the maximum amount of the generator may be used for no more than 30 minutes Plug in the appliance Note: substantial overloading will switch off the AC circuit protector. Exceeding the time limit for maximum power operation or slightly overloading the generator may not switch the AC circuit protector off, but it will shorten the service life of the generator. If the AC circuit protector switches off automatically, check that the appliance is working properly and does not exceed the rated load capacity before resetting the AC circuit protector Revised 08/30/21 64 HONDA GENERATOR EB 5000X/EM 6500SX SPECIFICATIONS EB5000X Max power rating—5.0KVA for up to 30 minutes Continuous operation rating—4.5KVA Max output—7,000 watts for up to 10 seconds Weight—212.3 lbs Fuel Tank—6.21 gallons Run time at ½ Load—10.5 hours Run time at full load—7.1 hours SPECIFICATIONS EM 6500SX Max power rating—6,500 VA for up to 30 minutes Continuous operation rating—5,500 VA Max output—7,000 watts for up to 10 seconds Weight—227 lbs Fuel tank—6.6 Gallons Run time at ½ load—9.8 hours COMPONENTS Spark Plug Fuel Valve Lever Muffler Starter Grip Air Cleaner Manual Choke Lever Revised 08/30/21 65 CONTROLS AND FEATURES Engine Switch Controls the ignition of the generator. Some models may only have an On and Off function (left). Others may have a Start function that will not require a firefighter to use the starter grip (right). Starter Grip Operates the recoil starter to crank the engine. All generators will have pull start capability, including those with a turn start option in case that fails to work. Fuel Valve Lever This controls the fuel supply from the fuel tank to the carburetor; it should be kept in the off position when the generator is not running. Auto Choke Control This generator has an Engine Off Position On Position Control Module that will automatically control the motor’s throttle and choke when starting. The choke does not need to be operated when starting the motor. Use the choke only if the engine is hard to start using the normal starting procedures. Normal Start Position Hard Start Position Revised 08/30/21 66 Voltage Selector Switch (Photo on right) Changes the generator output to produce 120-volt only or 120/240-volt. If a 240-volt appliance is connected to the 4-prong receptacle, the switch must be in the 120v/240v position. The switch should also be in the 120v/240v position for back feeding the truck. If only a 120-volt appliance is connected to any of the 120-volt 3-prong receptacles, select the 120-volt only position. Select the voltage prior to starting the engine. AC Circuit Breaker (Photo on left) AC circuit will automatically switch OFF if there is a short circuit, significant overload at the receptacles, or if the ground fault circuit interrupter (GFCI) detects a ground fault current. The AC Circuit Breaker can be used to switch the generator AC electrical power ON and OFF. Use the GFCI test button to ensure the breaker is working properly. Auto Throttle System (Photo on right) With the switch in the ON position, engine speed is automatically reduced when ALL loads are turned OFF or disconnected. When appliances are turned ON or reconnected, the engine returns to the rated speed. In the OFF position, the Auto Throttle system does not operate. The Auto Throttle System will not respond to electrical loads of less than 1 ampere or intermittent loads such as a staple gun. Intelligent Auto Voltage System iAVR (Photo on the left) This is a built-in system that automatically regulates voltage. The iAVR can provide power in excess of the maximum rating for up to 10 seconds to start appliances that may require a higher initial startup current. Revised 08/30/21 67 AUTOMATIC ENGINE STOP FUNCTION The backup generators are equipped with several functions to protect the user and the generator itself. Below is a brief overview of some of these functions and how they operate. Oil Alert System During operation, the engine will automatically stop if there is not enough oil in the tank. If the generator is on a significant slope, the Alert System may also activate stopping the engine. The engine switch will remain in the ON position. Overspeed Detection Function Protects the engine from exceeding the engine load; the engine will stop if the speed becomes abnormal. Abnormal Voltage Detection Function Engine will automatically stop during generation when it detects abnormal voltage. STARTING PROCEDURES 1) Turn off the AC Circuit Breaker 2) Turn the Fuel Valve Lever to the on position 3) Make sure the Auto Throttle is in the off position 4) Turn the Engine Switch to the on position 5) If using a pull starter grip, lightly pull until resistance is felt, then give a brisk pull. Firefighters can also use the turn start function if equipped on that generator 6) Turn the AC Circuit Breaker on to send power to the AC circuits 7) Auto Throttle may be turned on after 2-3 minutes of operation STOPPING PROCEDURES If it is an emergency situation, just turn the Engine Switch to off. However, the recommended procedure that should be followed in most circumstances is shown below: 1) Turn off and disconnect all the appliances connected to the generator 2) Move the AC Circuit Breaker to the off position 3) Turn the Engine Switch to the off position 4) Turn the Fuel Valve Lever to the off position Revised 08/30/21 68 ADAPTERS, CORDS, AND LIGHTS OVERVIEW Firefighters will find various plug adapters as part of the equipment complement on ladder trucks. As mentioned elsewhere, ladder companies were previously outfitted with 15-amp plugs. Although this is becoming more of a rarity as front-line trucks are being transitioned to 20-amp plugs, situations may still arise where adapters for these older plugs are needed (Older trucks will remain backups for years to come). For example, an adapter with a 20-amp female receptacle and a 15-amp male plug may be needed when using an older ladder truck that still has 15-amp plugs This section will illustrate some of the different electrical equipment the Division uses, and show some of their common variations All new ladder trucks are being ordered with 20-amp twist lock Hubbell connections 20-AMP TWIST LOCK HUBBELL CONNECTIONS AND ADAPTERS One of the more commonly used adapters is a 20-amp Hubbell female to a 3-prong straight blade male. This adapter allows firefighters to connect a Ram Fan to residential receptacles, rather than having to run a cord reel from the truck. The Division also has newer adapters that allow firefighters to connect the 20-amp Ram Fan plug into a Honda 2000 generator When switching over to reserve apparatus, firefighters must check the junction boxes attached to the cord reels to ensure they are the correct type Various adapters and types of connections are illustrated below 15-amp male/20-amp male Hubbell 15-amp female Hubbell/20-amp female Ungrounded House 20-amp twist lock Hubbell Grounded House 15-amp twist lock Hubbell 20-amp Hubbell female to 110v grounded house 20-amp Hubbell female to 3-prong straight blade male Revised 08/30/21 69 CORD REELS 200’ cord reel (below right photo) with 4-outlet junction boxes, common on most trucks. These junction boxes can be either 20-amp or 15-amp junction boxes. Be sure to check! 200’ single outlet cord reel (below left photo). These are not on every truck CORD BAGS Common lengths include bags with 25’, 50’, or 100’ Lengths can vary depending on the truck and the storage bag being used Many have 20-amp twist lock Hubbell connections 500-WATT TELE-LIGHTS The below left photo shows some different set ups that may be found in the Division Lights can be strung together (below right photo) using the plug on the base of the unit BATTERY POWERED LIGHTS The 18-volt removable/rechargeable battery powered units have high and low modes Orange Streamlight lights are rechargeable using the in-truck mounts Not waterproof Waterproof Revised 08/30/21 70 POSITIVE PRESSURE RAMFANS ELECTRIC RAMFAN EV400 1.5 horsepower Power—has a dual current toggle switch with two settings: 15-amp or 20-amp. The 20-amp setting is for powering the fan from a GFCI 20- amp fire truck circuit; the 15-amp setting is for powering the fan from a 15-amp house circuit or a 2-kilowatt generator (Honda EU 2,000) 115 volts Air output with the 15-amp setting: 9,184 cfm Air output with the 20-amp setting: 11,381 cfm Dimensions—22.6” H, 17.4” W, 18.5” D Weight—68 lbs GAS RAMFAN GX200 2.1 horsepower Run time—1 hour and 40 minutes Impeller with 7 blades Noise—91 decibels Speed—3,450 rpm Air output—21,760 cfm Dimensions—21.5” H, 19.5” W, 20.5” D Weight—48 lbs Be aware that this fan produces CO BATTERY RAMFAN EX50Li.8 horsepower Battery system specifications—40-volt lithium- ion, 432 watt-hour, 12 ampere-hour Should be plugged in when not in use 115 volts Run time: o DC—90 minutes (4 battery packs) o DC—45 minutes (2 battery packs) o DC—23 minutes (1 battery pack) o AC—unlimited run time Air output: o AC power—9,635 cfm o DC power—10,120 cfm Dimensions—22” H, 21” W, 12” D Weight—55 lbs Revised 08/30/21 71 SMOKE EJECTORS SUPERVAC P164SE (OLD RED BOX FAN) 1/3 horsepower Power: 115/230-volt AC, 50/60 hertz Cold crank wattage—2,000 watts Normal run wattage—700 watts Speed—1,725 rpm Output—5,200 cfm Dimensions—19.25” H, 18.75” W, 13” D Weight—49 lbs RAMFAN EFC150X (NEW RED BOX FAN) 1.5 horsepower Power: 115/230-volt AC, 50/60 hertz Cold crank—80 amps Normal run—15 amps Speed—3,590 rpm Output—4,459 cfm Dimensions—19” H, 18” W, 16” D Weight—55 lbs SUPERVAC HF164E (YELLOW BOX FAN) 1.5 horsepower Power: 115/230-volt AC, 50/60 hertz Cold crank wattage—6,000 watts Normal run wattage—2,100 watts Speed—3,450 rpm Output—9,620 cfm Dimensions—19.25” H, 18.75” W, 13” D Weight—63 lbs CONSIDERATIONS For negative pressure ventilation, the tighter the seal that can be kept around the opening, the more effective the fan will be at drafting the internal contents of the structure out. All the above fans are intrinsically safe The yellow fan is designed as a confined space fan and can move a much larger amount of air. However, it is important to consider the watts required to do so. While a 2000-watt generator can run a fan for a short period of time, the on-board generator is a more suitable power source for the yellow box fan The door bar attachment tool, which is extendable from 26” to 60”, can be used to hang all types of fans at any height in a door or window Revised 08/30/21 72 COLUMBUS ROPE BAG OVERVIEW New rope bags were introduced to the Columbus Fire Department in 2019. The bags were designed by Columbus Firefighters for Columbus Fire. These bags were the direct result of many hours of training and hard work from many past and present CFD members. Below is a brief informational outline on the new Columbus Rope Bags Click here to view Target Solutions video on the CFD Rope Bag IDENTIFICATION AND SPECIFICATIONS Manufactured by Sterling Rope Co., Inc Classification: Escape Rope Search rope and personal escape rope Made of high strength, heat resistant nylon fiber Yellow Mainline Rope o 200’ long o 8 mm diameter o Reflective, lightweight, durable, and fire-resistive o Minimum breaking strength—3,484 pounds o One end of the rope attaches to the inside of the mainline bag using a figure eight on a bight with an overhand safety to a locking carabiner. The locking carabiner is hooked to a webbing loop sewn to the inside of the bag. This carabiner is the only locking carabiner in the system o The other end of the rope is attached to a square non-locking carabiner using a figure eight on a bight with an overhand safety. This end also has the company ID Tag o Yellow rope deploys out of only one end of the yellow mainline bag Red Tagline Bags o 4 total 30’ taglines—red rope o 8 mm diameter o Reflective, lightweight, durable, and fire-resistive o Minimum breaking strength—3,484 pounds o Each tagline bag has a bent neck non-locking carabiner that can be attached to the four D-ring attachment points on the mainline bag when stored, or they can be clipped to a firefighter when deployed Mainline and each tagline have non-locking carabiners for functionality Each bag has an ID Tag for easy accountability Revised 08/30/21 73 RABBIT TOOL AND HYDRA-RAM II HURST RABBIT TOOL SPECIFICATIONS 8,000 lbs of force Spreading distance—4” Weight—12 lbs Parts included: o Rabbit tool o 6’ hose o Manual pump o Pry bar o Mallet o Carrying bag with sling Tool should be checked under load To use the rabbit tool, turn the pump relief valve knob clockwise, then start pumping the handle up and down To relieve the pressure and retract the tool, turn the relief valve knob counterclockwise. The tool will retract automatically HYDRA-RAM II SPECIFICATIONS 10,000 lbs of force Spreading distance—6” Weight—13 lbs for the tool itself, 14 lbs with the bag Length—15” The Hydra-Ram is the first patented one-piece integrated hydraulic forcible entry tool without hoses or auxiliary pumps. Parts included: o Tips—made of stainless steel with a tensile strength of 220,000 lbs o Hydraulic piston o Pump handle—138 lbs of pressure needed to create 10,000 lbs of lifting force o Quarter turn spring-loaded valve The tool should be checked while under load. Use full pump strokes only; short pump strokes can damage the piston Three stage hydraulic system: o 0-400 lbs—piston will move ¾” per pump o 400-1,200 lbs—piston will move ¼” per pump o Above 1,200 lbs—piston will move 1/8” per pump To lubricate the Hydra-Ram, extend the piston fully, wipe clean with a rag, and apply 3-In-One Multipurpose Oil. Retract and extend the piston several times after lubricating to evenly distribute the oil Revised 08/30/21 74 PAGE LEFT BLANK FOR DOUBLE SIDED PRINTING Revised 08/30/21 75 SMALL ENGINE MAINTENANCE OVERVIEW TRUCK OPERATIONS MANUAL SECTION TOPICS Small Engine Maintenance Stihl Chainsaws—Changing a Overview Chain Two-Stroke vs. Four-Stroke Stihl Circular Saws Engines How to Properly Mix Two-Stroke Stihl Circular Saws—Changing a Fuel Blade K-100 Fuel Additive Honda Generators Stihl Chainsaws Saw Operations—Reactive Forces SECTION OBJECTIVES Understand the difference between Understand how to change a chain on two-stroke and four-stroke engines a Stihl chainsaw Understand how to properly mix two- Identify, inspect, and maintain the stroke fuel various parts of Stihl circular saws Understand the uses for K-100 fuel Understand how to change a blade on additive a Stihl circular saw Identify, inspect, and maintain the Define and understand the reactive various parts of a Stihl chainsaw forces present during saw operations Revised 08/30/21 76 SMALL ENGINE MAINTENANCE OVERVIEW This section of the manual is designed to help apprentice firefighters understand the difference between two-stroke and four-stroke engines, as well as their associated care and maintenance. It is important to note that this section is not a comprehensive guide for small engine maintenance. It is simply an introduction to basic firehouse-level care that can help keep equipment running smoothly and help the apprentice firefighter become familiar with the different components of the equipment in the Division. CONTENTS Two-Stroke vs. Four-Stroke Engines How to Properly Mix Two-Stroke Fuel K-100 Fuel Additive Stihl Chainsaws o Changing a Chain Stihl Circular Saws o Changing a Blade Honda Generators Saw Operations—Reactive Forces Revised 08/30/21 77 TWO-STROKE VS. FOUR-STROKE ENGINES OVERVIEW Most engines are classified as either two-stroke (two-cycle) or four-stroke (four-cycle). However, what does that actually mean? Does it mean more than simply adding oil to the fuel or not? Both types of engines are in CFD’s arsenal of equipment, and firefighters must be professional enough to know more than just which ones require oil in the fuel and which ones do not. WHAT IS THE DIFFERENCE? A "stroke" refers to how many stages (piston/crankshaft movements) an internal combustion engine needs to complete to finish a "power (working) stroke" Two-stroke (two-cycle) engines require firefighters to mix the oil with the gas in exact amounts; the oil acts as a lubricant for the crankcase. However, four-stroke engines take oil and gas separately and have dedicated reservoirs for each In a two-stroke engine, the piston fires with every 360° rotation In a four-stroke engine, the piston fires with every 720° rotation HOW DO 2-STROKE ENGINES WORK? A two-stroke engine combines the compression and exhaust steps on its upstroke while combining the intake and combustion on the downstroke. Because there are fewer moving parts in this engine, maintenance is easier and there is a high power-to-weight ratio. These engines produce torque at much higher rpms compared to their four-stroke (four-cycle) counterparts This diagram is from Chapter 4 of Powered Parachutes Flying Handbook figure 4-3 Revised 08/30/21 78 TWO-STROKE SUMMARY 1. Compression/Exhaust—as the piston travels up, a negative pressure is created in the crankcase. This draws the fuel/oil mixture into the crankcase for lubrication, and pushes the burnt fuel-oil mixture out of the combustion cylinder. The unburned fuel/oil mixture is then compressed into the combustion chamber in preparation for the power stroke 2. Intake/Combustion—after the spark plug ignites, the fuel/oil mixture burns, creating the power stroke forcing the piston down and creating positive pressure in the crankcase HOW DO FOUR-STROKE ENGINES WORK? Four-stroke engines have a separate reservoir for oil; there is no need to mix oil with the fuel. They have an internal oiling system to ensure proper lubrication. These engines are more fuel-efficient than two-stroke engines and provide more torque at a lower rpm. However, their weight-to-power ratio is much worse compared to a two-stroke engine FOUR-STROKE SUMMARY 1. Intake—a downward stroke draws in fuel 2. Compression—an upward stroke compresses the air/fuel mixture 3. Combustion (Power)—compressed air/fuel mixture is ignited, generating downward force of the piston/crankshaft 4. Exhaust—another upward stroke compresses and expels the burnt air/fuel mixture This diagram retrieved from PowerEquipmentDirect.com PROS AND CONS OF EACH ENGINE Two-Stroke Four-Stroke Pros Pros Simple Mechanics and Construction Fuel Efficient More Powerful Less Pollution, Cleaner Burning Not Positional More Low-End Torque Greater Longevity Cons Cons Less Fuel Efficiency Complicated Mechanics Limited Longevity Expensive Low End Torque Less Powerful Revised 08/30/21 79 HOW TO PROPERLY MIX TWO-STROKE FUEL OVERVIEW As discussed earlier, two-stroke/cycle engines do not have their own dedicated oiling systems (such as an oil reservoir, pump, etc.) to rely on for proper lubrication. Thus, firefighters must be proficient at properly mixing fuel to the proper ratio; this ensures the small two-cycle engines are protected and receive the correct lubrication needed to keep them performing efficiently. There is a slew of mix ratios for two-cycle small engines ranging from 25:1, 32:1, 40:1, and 50:1. The most common mix ratio is 50:1, and that is the mix ratio utilized within CFD for the Division’s saws. A 50:1 ratio means the following—50 parts of fuel is mixed with 1 part of oil. Therefore, firefighters are adding 50 times as much gas as they are adding oil. MIXING FUEL Within CFD, the Stihl High Performance two-cycle engine oil (orange bottle) is utilized. This is a conventional oil, unlike the Stihl Ultra High Performance two-cycle engine oil (silver bottle), which is a synthetic oil. The Ultra High Performance (silver bottle) is used in the Division occasionally, but it is not found in the same volume in which the orange bottles are found. These silver bottles are typically smaller and come in either the 2.6 fl. oz. size (which makes one gallon) or the 5.2 fl. oz. size (which makes two gallons) of mixed gas. A fool-proof way to determine the amount of oil needed is to take the 2.6 fl. oz. and multiply it by the number of gallons of gas that firefighters plan on mixing. A good habit is to ensure the gas container is empty prior to mixing. Add the oil in first; then fill the container with gas to ensure proper and complete mixing. Ideally, firefighters should be using premium high-octane fuel (Stihl recommends a minimum octane rating of 89 with no more than 10% ethanol; however, 90 or above is CFD’s preferred recommendation). EXAMPLE If making five gallons of mixed gas, use this formula: 2.6 fl. oz x 5 = 13 fl. oz. of oil in five gallons of gasoline to create a 50:1 mix ratio. Revised 08/30/21 80 K-100 FUEL ADDITIVE OVERVIEW K-100 is an all-in-one fuel treatment and stabilizer that should be added to both two-cycle mixed gas and straight gas in an effort to ensure the Division’s fleet of small engines are better maintained and cared for. K-100 USES Cleans injectors and carburetor jets Eliminates or reduces water in fuel Stabilizes fuel for up to two years Improves power and efficiency Lubricates the complete fuel system Reduces emissions TO PROPERLY USE Mix ½ ounce of K-100 per one gallon of gas. For longer term storage, utilize a mix ratio of one ounce of K-100 per one gallon of gas. Also reference Division Bulletin #15-015, which provides further information on K-100 and its uses/mix ratio. Revised 08/30/21 81 STIHL CHAINSAWS OVERVIEW This section is designed to build on the chainsaw pages in the Equipment section Breaking down and inspecting each individual part of the chainsaw will be covered in this section, in addition to some commonly accepted practices for station level maintenance The last part of this section will cover how to change the chain on most Stihl chainsaws Firefighters operating a chainsaw must always wear proper eye protection Click here to view a video on Chain Saw Components SPROCKET COVER Disengage the chain break and remove the screws and the cover. Use a rag to remove any dirt, debris, and sawdust from the unit. Wipe down the unit with Simple Green, then dry it. GUIDE BAR Release the tension screw and remove the guide bar and chain. Inspect the bar for any obvious signs of wear and tear. Any spurs can be filed down gently with a bastard file. The photo on the left shows an example of mushrooming. Any dirt and debris in between the guide bar can be carefully pulled away from the sprocket out the end of the bar using any flat head screwdriver. Wipe any dirt and debris with a rag. Simple Green can be used for any remaining stuck on grime, if necessary. Once the bar is clean, lightly cover the bar in WD40 and wipe the excess off. (Excess oil can attract dirt). After each use, flip the guide bar over to avoid uneven wear and tear, especially on the sprocket nose. Revised 08/30/21 82 CHAIN Inspect the chain for obvious signs of wear and tear. No more than 3 teeth in a row or 5 total can be missing. (72 links and 36 teeth total). If needed, replace the chain with a new one and keep the old chain for training. Inspect the chain to ensure all teeth are traveling in the same direction. These chains are cut from large spools at Tools and Equipment, and there have been instances where chains were put together incorrectly (photo on right). MAIN UNIT With the guide bar, sprocket cover, and chain still off, wipe down any additional dirt and debris from the main unit of the saw. Simple Green may be used for any tough grime. If using a water hose to spray off the saw, avoid getting the air filter wet. Inspect the oil inlet hole, oil outlet channel, and bar groove to ensure they are free of dirt and debris. If obstructions are found in the oil outlet channel, be sure to pull them out and away from the channel. Do not push or blow dirt back down into the unit. Use this time to check the oil quantity control setting on the bottom of the saw. (E = moderate oil delivery) CFD runs with the setting all the way open. Ensure both the fuel filler cap and the oil filler cap are free of dirt. Remove both and inspect the guides that lock in the caps for dirt. Wipe with a rag if needed. Do not forget to clean the bottom ground guard of the unit. Revised 08/30/21 83 AIR FILTER Before removing the carburetor box cover, make sure the saw is in the FULL choke position to ensure no dirt falls down into the carburetor. Once the box cover is removed, ensure the temperature slide is located in the correct position (Winter mode when 50° or below). Remove the air filter and knock the filter out by tapping it on the ground, or blow it clear with compressed air from the inside outward. (This should be sufficient 99% of the time). If not, filters may be cleaned using water and Dawn. This method is not preferred because the filter must be cleaned using low pressures and be given ample time to dry before being reinstalled. Visually inspect the carburetor for major dirt and debris and remove any debris, if necessary. Always pull debris out and away from the carburetor; never push it in. Revised 08/30/21 84 SPARK PLUG To change/check the spark plug, first remove the air baffle and unplug the spark plug boot. Next, use the tool to unscrew the spark plug. If needed, clean the spark plug using a wire brush or just replace the spark plug. Check the manufacturer spark plug gap measurement using a gap tool (.5mm). Finally, re-tighten the spark plug firmly with the tool and replace the boot and air baffle. FAN HOUSING Before removing the fan housing, slowly pull out the starter pull cord and visually inspect it for any obvious signs of damage. Use compressed air to blow dirt from the inside of the housing out. Wipe down the cover with a rag and Simple Green if needed. Avoid chemical direct contact with the pull cord. The red circle highlights the saw’s magneto. This is where the electrical charge is generated to fire the spark plug. As the flywheel spins, a magnet passes over the magneto; an electrical charge is then built up and sent to the spark plug. Revised 08/30/21 85 RETURN TO SERVICE Replace all components once each one has been properly cleaned, lubricated, and dried. Properly tension the chain as shown in the next section. The chain should be able to be slid along the bar by hand. With the saw on the ground, lift up on the chain only; when doing so the drive link tangs should not be fully exposed. Ensure the fuel and bar oil are filled. Once all components are back together, ALWAYS start it and go through a quick Monday check on the equipment to ensure it was put back together properly. Click here to view a video on Cleaning STIHL Chainsaws Revised 08/30/21 86 STIHL CHAINSAWS—CHANGING A CHAIN 1. Using a saw wrench, loosen the bar stud nuts and remove the chain sprocket cover 2. Next, turn the chain tensioning screw counterclockwise to loosen the chain 3. Disengage the chain brake 4. Remove the guide bar and chain from the drive sprocket. Inspect the oil inlet on the saw body and the oil passageway on the guide bar for cleanliness and possible obstructions 5. Discard the old chain or save it for training, depending on its condition 6. Inspect the guide bar for uneven wear, mushrooming, or other damage. If needed, file using a single cut mill bastard file. The photo on the left shows slight mushrooming on the guide bar. Revised 08/30/21 87 7. Prior to re-installation, flip the guide bar to promote even wear 8. Fit the new chain on the guide bar, starting at the nose or end of the guide bar 9. Fit the guide bar over the bar studs. The cutting edges on the chain on the top of the guide bar must point forward. (Rakers aka shark fins swimming away from you). The photo on the left highlights the direction of travel for the rakers 10. Engage the tensioner slide in the locating hole on the guide bar and place the chain over the drive sprocket at the same time. Firefighters might have to further loosen or take up slack with the chain tensioner to get the proper fit 11. Turn the tensioning screw clockwise, taking up slack with the chain saw chain and the drive tangs fully engaged in the guide bar Revised 08/30/21 88 12. Refit the sprocket cover and screw on the bar stud nuts finger-tight. Ensure that the bar does not drop or lower in position while this is being done 13. Utilizing the weight of the saw as a reference, pick up on the chain saw chain mid-length on the guide bar until the front body of the saw shows a slight sign of lift. With the saw body slightly lifted, the chain is properly tensioned if the bottom part of the drive tang is still engaged in the guide bar groove. The photos on the left show a loose chain vs. a correctly tightened chain 14. Confirm proper chain tension and repeat if necessary. Be sure to account for additional tensioning once the bar stud nuts are completely tightened 15. Fully secure the bar stud nuts 16. Check the chain tension again for proper tensioning following the tightening of the bar stud nuts. With the chain brake disengaged, ensure the chain travels freely and properly by pulling on the chain with a gloved hand. If unable to pull the chain by hand with the brake off, it is too tight. Remember that after running a new chain you may need to check the chain tension again because it will expand when heated Revised 08/30/21 89 17. Reengage the chain brake 18. Properly start the saw and ensure proper operation and oiling of the bar 19. At this time, allow the saw to warm up to operating temperature (roughly 2-5 minutes) 20. Top the saw off with 50:1 mixed fuel and with bar oil before placing the saw back in service Click here to view a video on Changing a STIHL Chainsaw Chain Revised 08/30/21 90 STIHL CIRCULAR SAWS OVERVIEW This section is designed to build on the circular saw pages in the Equipment section Breaking down and inspecting each part of the circular saws will be covered in this section, in addition to some commonly accepted practices for station level maintenance The last part of this section will cover how to change the blade on most Stihl circular saws Firefighters operating a circular saw must always wear proper eye protection Click here to view a video on STIHL Circular Saw Components BLADE Ensure that blades being replaced are the correct type, arbor size (20 mm), and spindle speed (5,350 RPM or higher). Inspect DAX blades for fissures, undercutting, and missing teeth. Inspect composite blades for frayed edges, chemical stains, and uneven wear. To remove the blade, insert the slide locking pin through the hole in the V-Belt guard. Use the wrench to remove the front thrust washer bolt and remove the washer. Note: ensure the locking pin is properly seated straight into the hole (bottom left photo), NOT on an angle (bottom right photo). Reinstall the blade by reversing these steps. Ensure that the blade does not wobble and that the washer sits flush against the blade. Revised 08/30/21 91 BELT Inspect the V-Belt for obvious wear and tear by removing the arm guard cover and visually inspecting the drive belt. MAIN UNIT Wipe down any dirt and debris from the main unit of the saw. Simple Green may be used for any tough grime. Avoid using a water hose to just spray off the body of the saw; an air hose would be preferred. Ensure the fuel filler cap is free from dirt. Remove and inspect the guides that lock in the cap for dirt; wipe with a rag if needed. Do not forget to clean the bottom ground guard of the unit. Revised 08/30/21 92 AIR FILTER Before removing the air filter cover, make sure the saw is in the FULL choke position to ensure no dirt falls into the carburetor. Unless cutting concrete or other masonry materials, the air filters will only need to be changed approximately once per year or as otherwise noted per the manufacturer. Once the cover is removed, wipe off any dirt and debris with a rag and Simple Green. Remove the auxiliary and primary air filters and knock the filters out by tapping them on the ground, or blow them clear with compressed air from the inside outward. (This should be sufficient 99% of the time). If not, filters may be cleaned using water and Dawn. This method is not preferred because the filters must be cleaned using low pressures and be given ample time to dry before being reinstalled. Both the auxiliary and primary air filters should be checked for damage. If damaged, both should be replaced together. Revised 08/30/21 93 PULL CORD Engage the decompression valve and slowly pull out the pull cord to visually inspect it for any dirt, debris, or fraying of the cord. SPARK PLUG To change/check the spark plug, remove the spark plug cover, unplug the spark plug boot, and use the tool to unscrew the spark plug. If needed, clean the spark plug using a wire brush or just replace the spark plug. Check the manufacturer spark plug gap measurement using a gap tool. Re-tighten the spark plug firmly and replace the boot and air baffle. RETURN TO SERVICE Reinstall the filters and the air filter cover. Ensure the saw is fueled using 50:1 gas/oil mixture. Check to make sure the blade is tightened before starting the saw. Once all components are back together, ALWAYS start the saw and go through a quick Monday check on the equipment to ensure it was put back together properly. Revised 08/30/21 94 STIHL CIRCULAR SAWS—CHANGING A BLADE 1. Slide the locking pin through the bore in the V-belt arm 2. Turn the circular saw blade by hand until the locking pin engages in the bore behind the guard 3. Confirm that the locking pin limits or restricts the rotational turn of the saw blade. Ensure the locking pin is properly seated straight into the bore, not on an angle like the photo on the right 4. Use a saw wrench to loosen and remove the arbor bolt Revised 08/30/21 95 5. Completely remove the front thrust washer from the spindle 6. Remove the circular saw blade and discard it, or save it for training use 7. Prior to installation, inspect the new circular saw blade to ensure it is the proper size for the saw (12” or 14” blade size). Make sure the blade is rated for at least 5,350 rpm, which is the max spindle speed of CFD Stihl circular saws. Make sure the type of blade is appropriate for the size of the saw (For instance, a TS500 should not run a DAX blade). Also, confirm whether the blade has a 20 mm arbor or a larger 25 mm arbor. The 25 mm arbor requires the use of a spacer placed over the spindle before installing the new blade 8. Fit the new circular saw blade onto the spindle (note the arrows indicating the direction of the rotation if applicable) Revised 08/30/21 96 9. Place the front thrust washer back onto the spindle. Ensure that the tangs of the front thrust washer engage the grooves located on the spindle 10. Screw in the arbor bolt and tighten it with the saw wrench 11. Remove the locking pin from the V-belt guard 12. Spin the circular saw blade by hand to confirm proper fit and to ensure the blade does not wobble 13. Start the saw and ensure proper operation 14. At this time, allow the saw to warm up to operating temperature (roughly 2-5 minutes) 15. Top off with 50:1 mixed fuel and place the saw back in service Click here to view a video on Changing STIHL Circular Saw Blades Revised 08/30/21 97 HONDA GENERATORS OVERVIEW This section is designed to build on the Honda Generator pages in the Equipment section Breaking down and inspecting each individual part of the Honda generators will be covered in this section, in addition to some commonly accepted practices for station level maintenance MAIN UNIT Using a rag and Simple Green, wipe down the unit to clean any dirt and debris present. Ensure the control panel is free of any damage. Check to ensure the Eco Throttle is turned off. Check for any damage to the appliance and the appliance cord, if applicable. FUEL Inspect the fuel filler cap and threads to ensure they are free of any dirt and debris. Store the unit upright in its normal operating position with the engine (on/off) switch and the fuel filler cap vent lever both turned off to prevent fuel spills. Ensure the unit is filled with gasoline of at least 86% octane and no more than 10% ethanol. Revised 08/30/21 98 AIR FILTER Remove the left side maintenance cover and locate the air cleaner cover. Remove the foam air filter and inspect it to see if it is dirty. If it is dirty, clean the filter using warm soapy water, rinse it, and allow it to dry fully. Once cleaned, take the dry air filter and dip it in clean engine oil. Squeeze the excess oil out (do not twist the filter) and place the filter back into place. The easiest way to do this at the station is to add some oil into a large zip lock bag, place the filter in the bag, and squeeze it out before reinstalling. Once the filter has been reinstalled, use a moist rag to wipe down the rubber air guide and any other debris inside the filter area. Reinstall and tighten the left side maintenance cover. Note: when the engine is started up, it will smoke when burning off any excess oil. OIL Remove the left side maintenance cover and locate the oil filler cap. Check the oil level; oil should reach the lip of the oil filler neck. If oil is below the limit, additional oil can be added directly into the oil filler neck (SAE 10W-30 oil preferred). When referring to oil, 30 references the viscosity at 100°. The W references the viscosity of oil at low temperatures. To change the oil, place a drip pan underneath the oil filler neck and drain the oil. Next, add the new oil as described above. A good practice is to place a piece of duct tape on the inside of the maintenance cover and document on it when the oil was changed and when it should be changed again. The manufacturer recommends changing the oil every 6 months or 100 hrs. Revised 08/30/21 99 SPARK PLUG To change/check the spark plug, remove the spark plug cover, unplug the spark plug boot, and use the tool to unscrew the spark plug. If needed, clean the spark plug using a wire brush or just replace the spark plug. Check the manufacturer spark plug gap measurement using a gap tool (.6-.7mm). Retighten the spark plug firmly and replace the boot and the air baffle. MUFFLER Remove the muffler protector and clean the inside of the housing cover using Simple Green and a rag. Additional muffler service to the spark arrester should typically be handled by Tools and Equipment. If needed, the muffler and spark arrester unit can be removed and cleaned with a wire brush. Removing the cover to clean should rarely need to be completed. Revised 08/30/21 100 SAW OPERATIONS—REACTIVE FORCES OVERVIEW This section outlines some of the common reaction forces encountered when operating a saw Watching the attached Target Solutions videos starring Retired Captain Greg Lash is highly recommended Click here to view Captain Lash’s video on Saw Reaction Forces Click here to view Captain Lash’s video on Cutting with Finesse SPRING POLE Definition—tree limb under tension which releases said tension after being cut. (CAUTION—this has the potential to seriously injure or kill the operator and those in close vicinity) o Can be encountered on auto accidents or downed trees o Can be countered by making relieving cuts along the length of the affected limb Felling o Requires experience o Dangerous operation which should be avoided unless absolutely necessary KICKBACK Most critical reactive force created by the chainsaw Occurs as a result of the top ¼ of the tip of the chain/bar (known as the kickback zone) hitting another log, knot, car, pipe, or other foreign object and rapidly pivoting the saw right back onto the operator Just by informing professional loggers in the 1980s about the dangers associated with kickback, injuries decreased by 50% Revised 08/30/21 101 KICKBACK CONT. Safeguards against kickback include the following: o Proper body positioning/stance ▪ Front arm straight (body mechanics will keep the saw from coming back onto the operator) ▪ Back leg out of the cut path of the saw o Hand positioning ▪ Thumb fully encircling the front handle ▪ Hand topside on the front handle in position to engage the chain brake if kickback occurs PULL IN Occurs when the chain grabs hold of the cutting material and pulls the operator toward the saw Has an amplified reactive force when the saw is not operated at full speed Can occur when the operator is stretching out from the end of an aerial or ground ladder and can result in the operator being pulled off the ladder PUSH BACK Another very quick reactive force Occurs when undercutting and the top of the bar stops or is pinched, forcing the saw to be shot back forcefully at the operator Can also occur when cutting normally Ideally, all cuts should be made using the following methods: o With the bar starting at a right angle to the cutting material o At full RPMs o The operator using feel and sound to know when the saw is performing inadequately, or when the chain is underperforming ▪ Chain is becoming dull when the thrown chip size is small and the cutting speed is redu