Transformer Lecture Notes 2018-19 PDF
Document Details
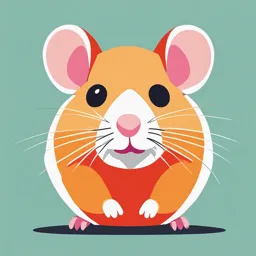
Uploaded by EnrapturedZirconium7880
Government Engineering College, Jamui, Bihar
2018
Prof. Amarendra Kumar
Tags
Summary
This document is lecture notes on Basic Electrical Engineering, Module 4: Transformers, from Aryabhatta Knowledge University, Patna for the 2018-19 academic year.
Full Transcript
GOVERNMENT ENGINEERING COLLEGE, JAMUI SUBJECT: BASIC ELECTRICAL ENGINEERING MODULE 4: TRANSFORMERS LECTURE NOTES As Per ARYABHATTA KNOWLEDGE UNIVERSITY, PATNA Effective from Academic year 2018-19 Based o...
GOVERNMENT ENGINEERING COLLEGE, JAMUI SUBJECT: BASIC ELECTRICAL ENGINEERING MODULE 4: TRANSFORMERS LECTURE NOTES As Per ARYABHATTA KNOWLEDGE UNIVERSITY, PATNA Effective from Academic year 2018-19 Based on AICTE model Curriculum 2018 4. Transformers 4.1 What is magnetic material and give difference between magnetic and non magnetic material. The magnetic material are define as material in which a state of magnetism can be induced. Magnetic materials, when magnetized create a magnetic field. Magnetic material Nonmagnetic material Magnetic materials are materials Non-magnetic materials are materials having a magnetic domain and are that are not attracted to an external attracted to an external magnetic field. magnetic field. The magnetic domains of magnetic The magnetic domains of non-magnetic materials are aligned either parallel or materials are arranged in a random anti parallel arrangements thus they can manner in such a way that the magnetic respond to a magnetic field when they are moments of these domains are cancelled under the influence of an external out. Thus, they do not respond to a magnetic field. magnetic field. Magnetic materials are used to make Magnetic materials are used to make permanent magnets are the parts of permanent magnets are the parts of operating systems where magnetic operating systems where magnetic properties are required. properties are required. 4.2 Explain the different types of magnetic material Classification of magnetic material as below: Paramagnetic material Diamagnetic material Ferromagnetic material Paramagnetic Diamagnetic Ferromagnetic Figure 4.1 Types of magnetic materials (1) Paramagnetic material If a bar of paramagnetic material is suspended in between the pole pieces of an electromagnet, it sets itself parallel to the lines of force. When a bar of paramagnetic material is placed in a magnetic filed the lines of force tend to accumulate in it. If a paramagnetic liquid is placed in a watch glass resting on the pole pieces of an electromagnet then it accumulates in the middle. It is because in the central region the field is the strongest. If the pole pieces are not close together the field is strongest near the poles and the liquid moves away from the Prof. Amarendra Kumar, EE Department Basic Electrical Engineering (100101/100201 2 4. Transformers center giving an almost opposite effect. If one end of a narrow u-tube containing a paramagnetic liquid is placed within the pole pieces of an electromagnet in such a manner that the level of the liquid is in the lie with the field, then on applying the field the level of the liquid rises. The rises in proportional to the susceptibility of the liquid. When a paramagnetic gas is allowed to ascend between the poles pieces of an electromagnet it spreads along the direction of the field. Example of paramagnetic material aluminum, manganese platinum, crown glass solution of salts of iron and oxygen (2) Diamagnetic material When a diamagnetic substance is placed in a magnetic field it sets itself at right angles to the direction of the lines of force. When a diamagnetic material is placed within a magnetic field the lines of force tend to go away from the material. When a diamagnetic substance is placed in a watch glass on the pole pieces of a magnet the liquid accumulates on the sides causing a depression at the center which is the strongest part of the field. When the distance between the pole pieces is larger, the effect is reversed. A diamagnetic liquid in a u-tube placed in a magnetic field shows as depression. When a diamagnetic gas is allowed to ascend between, the poles piece of an electromagnet it spreads across the field. Example of diamagnetic material bismuth, phosphorus ,antimony, copper, water, alcohol, ,hydrogen (3) Ferromagnetic material Ferromagnetic substance shows the properties of the paramagnetic substance to a much greater degree. The susceptibility has a positive value and the permeability is also very large. The intensity of magnetization I is proportional to the magnetizing field H for small value. Example of Ferromagnetic material Iron nickel, cobalt and their alloys Comparison of difference types of magnetic material Properties Paramagnetic Materials Diamagnetic Material Ferromagnetic Materials State They can be solid, liquid They can be solid, liquid They are solid. or gas. or gas. Effect of Magnet Weakly attracted by a Weakly repelled by a Strongly attracted by a magnet. magnet. magnet. Behavior under Tend to move from low Tend to move from high Tend to move from low to non-uniform field to high field region. to low region. high field region. Behavior under They do not preserve They do not preserve They preserve the magnetic external field the magnetic properties the magnetic properties properties after the external once the external field once the external field field is removed. Prof. Amarendra Kumar, EE Department Basic Electrical Engineering (100101/100201) 3 4. Transformers is removed. is removed. Effect of With the rise of No effect. Above curie point, it Temperature temperature, it becomes a paramagnetic. becomes a diamagnetic. Permeability Little greater than unity Little less than unity Very high Susceptibility Little greater than unity Little less than unity Very high and positive and positive and negative Examples Lithium, Tantalum, Copper, Silver, Gold Iron, Nickel, Cobalt Magnesium 4.3 B-H curve and magnetic hysteresis of magnetic material B-H Curve The curve plotted between flux density B and magnetizing force H of a material is called magnetizing or B-H curve. The shape of curve is non-linear. This indicates that relative permeability (µr = B / µ0H) of a material is not constant but it varies. B-H curves are very useful to analyze the magnetic circuit. If value of flux density and dimension of magnetic circuit is known than from B-H curve total ampere turn can be easily known. c b Ferromagnetic B material a o H Figure 4.2 B-H Curve Magnetic hysteresis The phenomenon of lagging behind of induction flux density (B) behind the magnetizing force (H) in magnetic material is called magnetic hysteresis. Hysteresis loop is a four quadrant B – H graph from where the hysteresis loss, coercive force and retentively of magnetic material are obtained. To understand hysteresis loop, we suppose to take a magnetic material to use as a core around which insulated wire is wound. The coils is connected to the supply (DC) through variable resistor to vary the current I. We know that current I is directly proportional to the value of magnetizing force (H). When supply current I = 0, so no existence of flux density (B) and magnetizing force (H). The corresponding point is o in the graph above. Prof. Amarendra Kumar, EE Department Basic Electrical Engineering (100101/100201 4 4. Transformers Magnetic core Magnetic Flux I V Figure 4.3 Circuit diagram form Magnetic hysteresis B +Bm a b Br -Hm c o f +Hm -H H Hc Br - Residual magnetism e Hc - Coercivity d -Bm -B Figure 4.4 magnetic hysteresis loop When current is increased from zero value to a certain value, magnetizing force and flux density both are set up and increased following the path o to a. For a certain value of current, flux density becomes maximum (Bm). The point indicates the magnetic saturation or maximum flux density of this core material. All element of core material get aligned perfectly. When the value of current is decreased from its value of magnetic flux saturation, H is decreased along with decrement of B not following the previous path rather following the curve a to b. The point b indicates H = 0 for I = 0 with a certain value of B. This lagging of B behind H is called hysteresis. The point b explains that after removing of magnetizing force (H), magnetism property with little value remains in this magnetic material and it is known as residual magnetism (Br) or residual flux density. If the direction of the current I is reversed, the direction of H also gets reversed. The increment of H in reverses direction following path b – c decreases the value of residual magnetism that gets zero at point c with certain negative value of H. This negative value of H is called coercive force (Hc) Prof. Amarendra Kumar, EE Department Basic Electrical Engineering (100101/100201) 5 4. Transformers Now B gets reverses following path c to d. At point‘d’, again magnetic saturation takes place but in opposite direction with respect to previous case. At point‘d’, B and H get maximum values in reverse direction. If decrease the value of H in this direction, again B decreases following the path d. At point e, H gets zero valued but B is with finite value. The point e stands for residual magnetism (-Br) of the magnetic core material in opposite direction with respect to previous case. If the direction of H again reversed by reversing the current I, then residual magnetism or residual flux density (-Br) again decreases and gets zero at point ‘f’ following the path e to f. Again further increment of H, the value of B increases from zero to its maximum value or saturation level at point a following path f to a. Hard and soft material hysteresis loop are given below. Hard B Soft H Figure 4.5 Types of hysteresis loop 4.4 What is requirement of transformer? A transformer is defined as a static device converts the electric power from one electrical circuit to another electrical circuit without change of frequency. It can also up and down the voltage level. In our country usually electrical power is generated at 11kV. For economical reason a.c. power is transmitted at very high voltage (220kV or 400 kV) over long distance, therefore, a step up transformer is applied at the generating station. To feed different area, voltage is step down to different levels by transformer at various substations. Ultimately for utilization of electrical power, the voltage is step down to 400/230 V for safety reasons. Prof. Amarendra Kumar, EE Department Basic Electrical Engineering (100101/100201 6 4. Transformers 4.5 Explain construction and working of single phase transformer A transformer is defined as a static device converts the electric power from one electrical circuit to another electrical circuit without change of frequency. It can also up and down the voltage level. Construction Transformer core Magnetic Secondary core coil Primary Secondary Primary coil ` V2 V1 V2 or V1 Np Ns Transformer symbol Transformer construction Figure 4.6 Transformer Primary and secondary winding Core Core HV 2 2 LV Core type construction Magnetic Shell type construction line and flux Figure 4.7 Types of construction of 1-phase transformer For the simple construction of a transformer, you must need two coils having mutual inductance and a laminated steel core. The device will need some suitable container for the assembled core and windings, a medium with which the core and its windings from its container can be insulated. In order to insulate and to bring out the terminals of the winding from the tank, the bushings that are made from either porcelain or capacitor type must be used. In all transformers that are used commercially, the core is made out of transformer sheet steel laminations assembled to provide a continuous magnetic path with minimum of air-gap included. The steel should have high permeability and low hysteresis loss. For this to happen, the steel should be made of high silicon content and must also be heat treated. Prof. Amarendra Kumar, EE Department Basic Electrical Engineering (100101/100201) 7 4. Transformers By effectively laminating the core, the eddy-current losses can be reduced. The lamination can be done with the help of a light coat of core plate varnish or lay an oxide layer on the surface. The thickness of the lamination varies from 0.35mm to 0.5mm. The types of transformers differ in the manner in which the primary and secondary coils are provided around the laminated steel core. According to the design, transformers can be classified into two: (1) Core type of transformer (2) Shell type of transformer Oil conservator Bushings Terminal Core Breather Figure 4.8 Transformer inside view (1) Core type of transformer In core-type transformer, the windings are given to a considerable part of the core. The coils used for this transformer are form-wound and are of cylindrical type. Such type of transformer can be applicable for small sized and large sized transformers. In the small sized type, the core will be rectangular in shape and the coils used are cylindrical. Round or cylindrical coils are wound in such a way as to fit over a cruciform core section is shown in figure. In case of circular cylindrical coils, they have a fair advantage of having good mechanical strength. The cylindrical coils will have different layers and each layer will be insulated from the other with the help of materials like paper, cloth, mica board and so on. The general arrangement of the core-type transformer with respect to the core is shown in figure. Both low-voltage (LV) and high voltage (HV) windings are shown. The low voltage windings are placed nearer to the core as it is the easiest to insulate. The effective core area of the transformer can be reduced with the use of laminations and insulation. (2) Shell type of transformer: In shell-type transformers, the core surrounds a considerable portion of the windings. The comparison is shown in the figure below. Prof. Amarendra Kumar, EE Department Basic Electrical Engineering (100101/100201 8 4. Transformers The coils are form-wound but are multi-layer disc type usually wound in the form of pancakes. Paper is used to insulate the different layers of the multi-layer discs. The whole winding consists of discs stacked with insulation spaces between the coils. These insulation spaces form the horizontal cooling and insulating ducts. Such a transformer may have the shape of a simple rectangle or may also have a distributed form. A strong rigid mechanical bracing must be given to the cores and coils of the transformers. This will help in minimizing the movement of the device and also prevents the device from getting any insulation damage. A transformer with good bracing will not produce any humming noise during its working and will also reduce vibration. Working Transformer I1 I2 Secondary Primary V1 V2 winding winding N1 N2 Figure 4.9 Working of Transformer The main principle of operation of a transformer is mutual inductance between two circuits which is linked by a common magnetic flux. A basic transformer consists of two coils that are electrically separate and inductive, but are magnetically linked through a path of reluctance. The transformer has two windings, (1) Primary and (2) Secondary winding. Primary winding is connected with input supply side and the secondary winding is connected with output load side. The core laminations are joined in the form of strips in between the strips you can see that there are some narrow gaps right through the cross-section of the core. These joints are said to be ‘laminated’. Both the coils have high mutual inductance. A mutual electro-motive force is induced in the transformer from the alternating flux that is set up in the laminated core, due to the coil that is connected to a source of alternating voltage. Most of the alternating flux developed by this coil is linked with the other coil and thus produces the mutual induced electro-motive force. So the produced electro-motive force can be explained with the help of Faraday’s laws of Electromagnetic Induction as, d e N dt Prof. Amarendra Kumar, EE Department Basic Electrical Engineering (100101/100201) 9 4. Transformers If the secondary coil circuit is closed, a current flows in it and thus electrical energy is transferred magnetically from the first to the second coil. In short the transformer carries the operations as shown below: Transfer of electric power from one circuit to another. Transfer of electric power without any change in frequency. Transfer with the principle of electromagnetic induction. The two electrical circuits are linked by mutual induction. 4.6 Emf equation of single phase transformer When a AC voltage is applied to the primary winding of a transformer, alternating flux sets up in the iron core of the transformer. This alternating flux links with both primary and secondary winding. The function of flux is a sine function. The rate of change of flux with respect to time is derived mathematically. Let, Φm be the maximum value of flux in Wb f be the supply frequency in Hz N1 is the number of turns in the primary winding N2 is the number of turns in the secondary winding Φ is the flux per turn (in Weber) m 1/f m Figure 4.10 Waveform of flux As shown in the above figure that the flux changes from + to – in half a cycle of 1/2f second. By Faraday’s Law of electromagnetic induction, Let E1 is the emf induced in the primary winding d E N 1 dt Maximum valve of induced emf Prof. Amarendra Kumar, EE Department Basic Electrical Engineering (100101/100201 10 3. Transformers E1(max) N1m But 2 f E1(max) 2 fN1m RMS value is given by, E E1 1(max) 2 Putting the value of E1(max) in above equation we get, E1 2 fN1m E1 4.44 fN1m Similarly, we get, E2 4.44 fN2m 4.7 Explain construction and working of three phase transformer Construction Three-phase transformer is effectively three interconnected single phase transformers on a single laminated core and considerable savings in cost, size and weight can be achieved by combining the three windings onto a single magnetic circuit as shown. Primary and secondary winding 3 Phase,3-leg Core 3 Phase,5-leg Core Coil Coil Coil Coil Coil Coil Coil Coil Coil Coil Coil Coil A A B B C C A A B B C C Core type construction Shell type construction Magnetic line and flux Figure 4.11 Type of construction of 3-phase transformer A three-phase transformer generally has the three magnetic circuits that are interlaced to give a uniform distribution of the dielectric flux between the high and low voltage windings. The exception to this rule is a three-phase shell type transformer. In the shell type of construction, even though the three cores are together, they are non-interlaced. The three-limb core-type three-phase transformer is the most common method of three-phase transformer construction allowing the phases to be magnetically linked. Flux of each limb uses the other two limbs for its return path with the three magnetic flux’s in the core generated by the line voltages differing in time-phase by 120 degrees. Thus the flux in the core remains nearly sinusoidal, producing a sinusoidal secondary supply voltage. Prof. Amarendra Kumar, EE Department Basic Electrical Engineering (100101/100201) 11 3. Transformers The shell-type five-limb type three-phase transformer construction is heavier and more expensive to build than the core-type. Five-limb cores are generally used for very large power transformers as they can be made with reduced height. Shell-type transformers core materials, electrical windings, steel enclosure and cooling are much the same as for the larger single-phase types. Working Consider the below figure in which the primary of the transformer is connected in star fashion on the cores. For simplicity, only primary winding is shown in the figure which is connected across the three phase AC supply. The three cores are arranged at an angle of 120 degrees to each other. The empty leg of each core is combined in such that they form center leg as shown in figure. When the primary is excited with the three phase supply source, the currents IR, IY and IB are starts flowing through individual phase windings. These currents produce the magnetic fluxes ΦR, ΦY and ΦB in the respective cores. Since the center leg is common for all the cores, the sum of all three fluxes are carried by it. In three phase system, at any instant the vector sum of all the currents is zero. In turn, at the instant the sum of all the fluxes is same. Hence, the center leg doesn’t carry any flux at any instant. R B Y IR IY IB R Three phase Y supply B Figure 4.12 3-phase transformer So even if the center leg is removed it makes no difference in other conditions of the transformer. Likewise, in three phase system where any two conductors acts as return for the current in third conductor. Two legs act as a return path of the flux for the third leg if the center leg is removed in case of three phase transformer. Therefore, while designing the three phase transformer, this principle is used. These fluxes induce the secondary EMFs in respective phase such that they maintain their phase angle between them. Prof. Amarendra Kumar, EE Department Basic Electrical Engineering (100101/100201 12 3. Transformers These EMFs drives the currents in the secondary and hence to the load. Depends on the type of connection used and number of turns on each phase, the voltage induced will be varied for obtaining step-up or step-down of voltages. 4.8 Comparison between Single Three Phase and Bank of Three Single Phase Transformers for Three Phase System It is found that generation, transmission and distribution of electrical power are more economical in three phase system than single phase system. For three phase system three single phase transformers are required. Three phase transformation can be done in two ways, by using single three phase transformer or by using a bank of three single phase transformers. Both are having some advantages over other. Single 3 phase transformer costs around 15 % less than bank of three single phase transformers. Again former occupies less space than later. For very big transformer, it is impossible to transport large three phase transformer to the site and it is easier to transport three single phase transformers which is erected separately to form a three phase unit. Another advantage of using bank of three single phase transformers is that, if one unit of the bank becomes out of order, then the bank can be run as open delta. 4.9 Types of connection of three phase transformer A verity of connection of three phase transformer is possible on each side of both a single 3 phase transformer or a bank of three single phase transformers. Marking or Labeling the Different Terminals of Transformer Terminals of each phase of HV side should be labeled as capital letters, A, B, C and those of LV side should be labeled as small letters a, b, c. Terminal polarities are indicated by suffixes 1 and 2. Suffix 1’s indicating similar polarity ends and so do 2’s. (1) Star-Star Transformer A B C A B C A2 A1 B2 B1 C2 C1 A2 A1 B2 B1 C2 C1 a2 a1 b2 b1 c2 c1 a2 a1 b2 b1 c2 c1 a b c a b c Star -Star Three phase Transformer Delta-Delta Three phase Transformer Figure 4.13 3-phase transformer connections Star-star transformer is formed in a 3 phase transformer by connecting one terminal of each phase of individual side, together. Prof. Amarendra Kumar, EE Department Basic Electrical Engineering (100101/100201) 13 3. Transformers The common terminal is indicated by suffix 1 in the figure below. If terminal with suffix 1 in both primary and secondary are used as common terminal, voltages of primary and secondary are in same phase. That is why this connection is called zero degree connection or 0o - connection. If the terminals with suffix 1 are connected together in HV side as common point and the terminals with suffix 2 in LV side are connected together as common point, The voltages in primary and secondary will be in opposite phase. Hence, star-star transformer connection is called 180o-connection, of three phase transformer. (2) Delta-Delta Transformer In delta-delta transformer, 1 suffixed terminals of each phase primary winding will be connected with 2 suffixed terminal of next phase primary winding. If primary is HV side, then A1 will be connected to B2, B1 will be connected to C2 and C1 will be connected to A2. Similarly in LV side 1 suffixed terminals of each phase winding will be connected with 2 suffixed terminals of next phase winding. That means, a1 will be connected to b2, b1 will be connected to c2 and c1 will be connected to a2. If transformer leads are taken out from primary and secondary 2 suffixed terminals of the winding, then there will be no phase difference between similar line voltages in primary and secondary. This delta delta transformer connection is zero degree connection or 0o-connection. But in LV side of transformer, if, a2 is connected to b1, b2 is connected to c1 and c2 is connected to a1. The secondary leads of transformer are taken out from 2 suffixed terminals of LV windings, and then similar line voltages in primary and secondary will be in phase opposition. This connection is called 180o-connection, of three phase transformer. (3) Star-Delta Transformer Here in star-delta transformer, star connection in HV side is formed by connecting all the 1 suffixed terminals together as common point and transformer primary leads are taken out from 2 suffixed terminals of primary windings. The delta connection in LV side is formed by connecting 1 suffixed terminals of each phase LV winding with 2 suffixed terminal of next phase LV winding. More clearly, a1 is connected to b2, b1 is connected to c2 and c1 is connected to a2. The secondary (here it considered as LV) leads are taken out from 2 suffixed ends of the secondary windings of transformer. The transformer connection diagram is shown in the figure beside. It is seen from the figure that the sum of the voltages in delta side is zero. This is a must as otherwise closed delta would mean a short circuit. It is also observed from the phasor diagram that, phase to neutral voltage (equivalent star basis) on the delta side lags by − 30o to the phase to neutral voltage on the star side; this is also the phase relationship between the respective line to line voltages. This star delta transformer connection is therefore known as − 30o-connection. Star- delta + 30o-connection is also possible by connecting secondary terminals in following sequence. a2 is connected to b1, b2 is connected to c1 and c2 is connected to a1. Prof. Amarendra Kumar, EE Department Basic Electrical Engineering (100101/100201 14 3. Transformers The secondary leads of transformer are taken out from 2 suffixed terminals of LV windings, A B C A B C A2 A1 B2 B1 C2 C1 A2 A1 B2 B1 C2 C1 a2 a1 b2 b1 c2 c1 a2 a1 b2 b1 c2 c1 a b c a b c Star -Delta Three phase Transformer Delta-Star Three phase Transformer Figure 4.14 3-phase transformer connections (4) Delta-Star Transformer Delta-star transformer circuit diagram shown in above figure. Delta-star transformer connection of three phase transformer is similar to star – delta connection. If anyone interchanges HV side and LV side of star-delta transformer in diagram, it simply becomes delta – star connected 3 phase transformer. That means all small letters of star-delta connection should be replaced by capital letters and all small letters by capital in delta-star transformer connection 4.10 Voltage and current ratios of transformer Voltage and current relation of primary winding and secondary winding is given as below. E1 4.44 fN1m.....................(1) If η of transformer 100% E2 4.44 fN2m................ (2) Input power = Output power Taking ratio of eq(1) and eq(2) V1I1 cos1 V2 I2 cos2 At no Load practically , cos1 cos2 E1 N1 or E2 N2 V1I1 V2 I2 E2 N2 E1 N1 I1 V2 At Load I2 V1 V1 E1 and V2 E2 V N But, 2 2 K V1 N1 or V2 N2 V1 N1 V2 N 2 V1 N1 I1 N2 V1 Pr imary voltage I 2 N1 V2 Secondary voltage cos1 Power factor of primary side cos2 Power factor of Secondary side Prof. Amarendra Kumar, EE Department Basic Electrical Engineering (100101/100201) 15 3. Transformers 4.11 Explain Ideal Transformer An ideal transformer is an imaginary transformer which does not have any loss in it, means no core losses, copper losses and any other losses in transformer. Efficiency of this transformer is considered as 100%. Ideal transformer model is developed by considering a transformer which does not have any loss. That means the windings of the transformer are purely inductive and the core of transformer is loss free. there is zero leakage reactance of transformer. As we said, whenever we place a low reluctance core inside the windings, maximum amount of flux passes through this core, but still there is some flux which does not pass through the core but passes through the insulation used in the transformer. An ideal transformer have the following properties: Its primary and secondary winding have negligible resistance. The core has infinite permeability (µ) so that negligible mmf is required to establish the flux in the core. Its leakage flux and leakage inductances are zero. The entire flux is confined to the core and links both the windings. There are no losses due to resistances, hysteresis and eddy currents. Thus, the efficiency is 100 %. This flux does not take part in the transformation action of the transformer. This flux is called leakage flux of transformer. In an ideal transformer, this leakage flux is also considered nil. That means, 100% flux passes through the core and links with both the primary and secondary windings of transformer. V1 Primary Secondary winding winding I1 I2 Core V2 V1 Iμ E1=V2 N1 N2 E1 Figure 4.15 Ideal transformer and its vector diagram Although every winding is desired to be purely inductive but it has some resistance in it which causes voltage drop and loss in it. In such ideal transformer model, the windings are also considered ideal that means resistance of the winding is zero. Prof. Amarendra Kumar, EE Department Basic Electrical Engineering (100101/100201 16 3. Transformers Now if an alternating source voltage V1 is applied in the primary winding of that ideal transformer, there will be a counter self emf E1 induced in the primary winding which is purely 180 degree in phase opposition with supply voltage V1. For developing counter emf E1 across the primary winding, it draws current from the source to produce required magnetizing flux. As the primary winding is purely inductive, that current 90o lags from the supply voltage. This current is called magnetizing current of transformer Iμ. This alternating current Iμ produces an alternating magnetizing flux Φ which is proportional to that current and hence in phase with it. As this flux is also linked with secondary winding through the core of transformer, there will be another emf E2 induced in the secondary winding, this is mutually induced emf. As the secondary is placed on the same core where the primary winding is placed, the emf induced in the secondary winding of transformer, E2 is in the phase with primary emf E1 and in phase opposition with source voltage V1. 4.12 Explain Practical Transformer A practical transformer hasn’t 100% efficiency due to losses. Transformer ‘no load’ condition A transformer is on no load when its secondary winding is open circuited. So, the secondary current is zero. When AC supply is applied to primary winding, a small amount of current Io flows in the primary winding. The current Io is called the no load current of the transformer. It is made up with two components Iµ and Iw. The component Iµ is called the magnetizing component and it magnetizes the core and it is in phase with ϕm. It is also called reactive component or wattles component of no- load current. Another component is Iw, it is called active component or working component or wattful component and it is in phase with supply voltage. V1 I0 Transformer Iw Io Primary Secondary Open circuit 0 V1 winding winding I2 =0 I E1 E2 Figure 4.16 Practical transformers on no load and vector diagram Prof. Amarendra Kumar, EE Department Basic Electrical Engineering (100101/100201) 17 3. Transformers The no-load current is small of the order of 3 to 5% of the rated current of primary winding. Consider the transformer under no-load and take ϕm as a reference phasor. At no-load we have, m sin t e E sin t 1 1m 2 e E sin t 2 2m 2 Since E1 and E2 are induced emf by the same flux ϕ and they will be in phase with each other.E2 differs from the magnitude of E1, because E2 = E1. E2 and E1 are lag behind ϕ by 900. If the voltage drop in the primary winding are neglected E1 will be equal and opposite to the applied voltage V1. Iμ is in phase with ϕ and Iw is in phase with V1.The phasor sum of Iμ and Iw is I0. Φ0 is called the no-load power factor angle, so that the power factor on no load is cosΦ0. I w I0 cos0 I I0 sin 0 I0 I 2 w I 2 I cos0 Iw 0 Also, core loss V1I0 cos0 V1Iw Watt. Magnetizing volt-amperes V1 sin 0 V1IVAr Transformer on load When an electrical load is connected to the secondary winding of a transformer, a current flows in the secondary winding. This secondary current is due to the induced secondary voltage that is set up by the magnetic flux created in the core from the primary current. The secondary current, I2 which is determined by the characteristics of the load this secondary current creates a self-induced secondary magnetic field Φ2 in the transformer core which flows in the exact opposite direction to the main primary field, Φ1. These two magnetic fields oppose each other resulting in a combined magnetic field of less magnetic strength than the single field produced by the primary winding alone when the secondary circuit was open circuited. This combined magnetic field reduces the back EMF of the primary winding causing the primary current, I1 to increase slightly. The Primary current continues to increase until the cores magnetic field is back at its original strength and for a transformer to operate correctly. Prof. Amarendra Kumar, EE Department Basic Electrical Engineering (100101/100201 18 3. Transformers A balanced condition must always exist between the primary and secondary magnetic fields. This results in the power to be balanced and the same on both the primary and secondary sides. Load I1 Transformer I2 R Primary Secondary V1 winding winding L Figure 4.17 Practical transformer on load We can calculate the primary current, IP by the following methods: Horizontal Component Ix I0 sin 0 I'1 sin 2 Vertical Component IY I0 cos 0 I'1 cos 2 I1 (I X 2 I 2 Y IY p.f cos IX I ' cos I1 V1 1 2 I1= Actual primary I’1 I0 cos 0 Phase Current angle I0 Flux I0 sin 0 I '1 sin 2 2 I2 -V2 Figure 4.18 Vector diagram of Practical transformer on load and vector diagram We know that the turns ratio of a transformer states that the total induced voltage in each winding is proportional to the number of turns in that winding. The power output and power input of a transformer is equal to the volts times amperes, ( V x I ). Therefore Prof. Amarendra Kumar, EE Department Basic Electrical Engineering (100101/100201) 19 3. Transformers Transformer Ratio PPr imary PSecondary V1I1 V2 I2 VI I 2 1 1 V2 V I 1 2 V2 I1 But we know that voltage ratio turns ratio N1 V I So, n n 1 2 N2 V2 I1 Note that the current is inversely proportional to both the voltage and the number of turns. This means that with a transformer loading on the secondary winding, in order to maintain a balanced power level across the transformers windings. If the voltage is stepped up, the current must be stepped down and vice versa. In other words, “higher voltage — lower current” or “lower voltage — higher current”. The total current drawn from the supply by the primary winding is the vector sum of the no-load current I0 and the additional supply current I1. As a result of the secondary transformer loading and which lags behind the supply voltage by an angle of Φ. We can show this relationship as a phasor diagram. Transformer Equivalent Circuit Actual real life, transformer windings have impedances of both XL and R. These impedances need to be taken into account when drawing the phasor diagrams as these internal impedances cause voltage drops to occur within the transformers windings. The internal impedances are due to the resistance of the windings and an inductance called the leakage reactance resulting from the leakage flux. These internal impedances are given as: Primary Impedence Secondary Impedence R1 L1 R2 L2 V1 N1 N2 Load Figure 4.19 equivalent circuit of transformer So the primary and secondary windings of a transformer possess both resistance and reactance. Sometimes, it can be more convenient if all these impedances are on the same side of the transformer to make the calculations easier. Prof. Amarendra Kumar, EE Department Basic Electrical Engineering (100101/100201 20 3. Transformers It is possible to move the primary impedances to the secondary side or the secondary impedances to the primary side. The combined values of R and L impedances are called “Referred Impedances” or “Referred Values”. The object here is to group together the impedances within the transformer and have just one value of R and XL in our calculations as shown. 4.13 Difference between Ideal transformer and actual transformer The windings (both primary and secondary) of an ideal transformer are considered to have zero resistance, hence the transformer is lossless. There is no leakage flux in an ideal transformer. The permeability of the core material in ideal transformer is considered to be tending to infinity and hence the current needed to set up the flux in the transformer is negligible. There is zero hysteresis and eddy current losses in an ideal transformer. 4.14 Losses in Transformer Figure 4.20 Block diagram of types of losses As the electrical transformer is a static device, mechanical loss in transformer normally does not come into picture. We generally consider only electrical losses in transformer. Loss in any machine is broadly defined as difference between input power and output power. When input power is supplied to the primary of transformer, some portion of that power is used to compensate core losses in transformer i.e. Hysteresis loss in transformer and Eddy current loss in transformer core. some portion of the input power is lost as I2R loss and dissipated as heat in the primary and secondary windings, because these windings have some internal resistances in them. The first one is called core loss or iron loss in transformer and the later is known as ohmic loss or copper loss in transformer. Another loss occurs in transformer, known as Stray Loss, due to Stray fluxes link with the mechanical structure and winding conductors. Prof. Amarendra Kumar, EE Department Basic Electrical Engineering (100101/100201) 21 3. Transformers (1) Copper losses Transformer Copper Losses are mainly due to the electrical resistance of the primary and secondary windings. Most of the transformer coils are made from copper wire which has resistance in Ohms ( Ω ). This resistance opposes the magnetizing currents flowing through them. When a load is connected to the transformers secondary winding, large electrical currents flow in both the primary and the secondary windings, electrical energy and power ( or the I2R ) losses occur as heat. Generally copper losses vary with the load current, being almost zero at no-load, and at a maximum at full-load when current flow is at maximum. A transformers VA rating can be increased by better design and transformer construction to reduce these core and copper losses. Transformers with high voltage and current ratings require conductors of large cross- section to help minimize their copper losses. Increasing the rate of heat dissipation (better cooling) by forced air or oil, or by improving the transformers insulation so that it will withstand higher temperatures can also increase a transformers VA rating (2) Iron losses or core losses Hysteresis loss and eddy current loss both depend upon magnetic properties of the materials used to construct the core of transformer and its design. So these losses in transformer are fixed and do not depend upon the load current. So core losses in transformer which is alternatively known as iron loss in transformer can be considered as constant for all range of load. (3) Hysteresis loss The work was done by the magnetizing force against the internal friction of the molecules of the magnet, produces heat. This energy which is wasted in the form of heat due to hysteresis is called Hysteresis Loss. When in the magnetic material magnetization force is applied, the molecules of the magnetic material are aligned in one particular direction, and when this magnetic force is reversed in the opposite direction, the internal friction of the molecular magnets opposes the reversal of magnetism resulting in Magnetic Hysteresis. Therefore, cores are made of materials with narrow hysteresis loops so that little energy will be wasted in the form of heat. Hysteresis loss in transformer is denoted as, W K f B 1.6 watt h h m Where Kh Hysteresis cons tan t (4) Eddy current losses Whenever a conductor is moving in a magnetic field or conductor is placed in changing magnetic field, an emf is induced in conductor according to faraday’s laws Prof. Amarendra Kumar, EE Department Basic Electrical Engineering (100101/100201 22 3. Transformers electromagnetic induction. These emf set up corresponding induced currents. These currents circulate in large number of small concentric paths within the solid mass of the conductor and are known as eddy currents. As these eddy currents are not used for doing any useful works and flow within the body, these currents cause power loss. The power loss due to eddy currents is called eddy current loss. Eddy current loss in transformer is denoted as, W K f 2 K 2 B 2 watt h e f m Ke Eddy current constant. K f form constant. Solid core Laminated core B l Figure 4.21 Eddy current losses 4.15 Explain Transformer efficiency A transformer is a static device this means there are no friction or windage losses associated with other electrical machines. A transformer has losses called “copper losses” and “iron losses” but generally these are quite small. Copper losses, also known as I2R loss.. The actual watts of power lost can be determined (in each winding) by squaring the amperes and multiplying by the resistance in ohms of the winding (I2R). Iron losses, also known as hysteresis is the lagging of the magnetic molecules within the core, in response to the alternating magnetic flux. The intensity of power loss in a transformer determines its efficiency. The efficiency of a transformer is reflected in power (wattage) loss between the primary (input) and secondary (output) windings. The resulting efficiency of a transformer is equal to the ratio of the power output of the secondary winding, to the power input of the primary winding, and is therefore high. An ideal transformer is 100% efficient because it delivers all the energy it receives. Real transformers on the other hand are not 100% efficient and at full load, the efficiency of a transformer is between 94% to 96% which is quite good. For a transformer operating with a constant voltage and frequency with a very high capacity the efficiency may be as high as 98%. The efficiency, η of a transformer is given as: Prof. Amarendra Kumar, EE Department Basic Electrical Engineering (100101/100201) 23 3. Transformers Output power Efficiency 100 % Input power Input power Losses 100 % Input power Losses 1 100 % Input power 4.16 Explain voltage regulation The voltage regulation is the percentage of voltage difference between no load and full load voltages of a transformer with respect to its full load voltage. Say an electrical power transformer is open circuited, means load is not connected with secondary terminals. In this situation, the secondary terminal voltage of the transformer will be its secondary induced emf E2. Whenever full load is connected to the secondary terminals of the transformer, rated current I2 flows through the secondary circuit and voltage drop comes into picture. At this situation, primary winding will also draw equivalent full load current from source. The voltage drop in the secondary is I2Z2 where Z2 is the secondary impedance of transformer. Now if at this loading condition, any one measures the voltage between secondary terminals, he or she will get voltage V2 across load a terminal which is obviously less than no load secondary voltage E2 and this is because of I2Z2 voltage drop in the transformer. E V Voltage regulation (%) 2 2 100% V2 4.17 Explain Auto Transformer Auto transformer is kind of electrical transformer where primary and secondary shares same common single winding. So basically it’s a one winding transformer. A I1 I2 V1 C I1 - I2 V2 Load I2 B Figure 4.22 Circuit diagram of Auto transformer Prof. Amarendra Kumar, EE Department Basic Electrical Engineering (100101/100201 24 3. Transformers In Auto Transformer, one single winding is used as primary winding as well as secondary winding. But in two windings transformer two different windings are used for primary and secondary purpose. The winding AB of total turns N1 is considered as primary winding. This winding is tapped from point ′C′ and the portion BC is considered as secondary. Let's assume the number of turns in between points ′B′ and ′C′ is N2. If V1 voltage is applied across the winding i.e. in between ′A′ and ′C′. V1 So Voltage per turn in this winding is , N1 Hence, the voltage across the portion BC of the winding, will be, V1 ×N and from the above,this voltage is V 2 2 N1 V Hence, 1 ×N =V 2 2 N1 V2 N2 = = Constant = K V1 N1 Hence, the voltage across the portion BC of the winding, will be, as BC portion of the winding is considered as secondary, it can easily be understood that value of constant ′k′ is nothing but turns ratio or voltage ratio of that auto transformer. When load is connected between secondary terminals i.e. between ′B′ and ′C′, load current I2 starts flowing. The current in the secondary winding or common winding is the difference of I2 and I1. Application of Auto transformer Compensating voltage drops by boosting supply voltage in distribution systems. Auto transformers with a number of tapping are used for starting induction and synchronous motors. Auto transformer is used as variac in laboratory or where continuous variable over broad ranges are required. The auto transformer is used as balance coil to give a neutral in a 3-wire ac distribution system Prof. Amarendra Kumar, EE Department Basic Electrical Engineering (100101/100201) 25