Track Machine Manual 120-150 PDF
Document Details
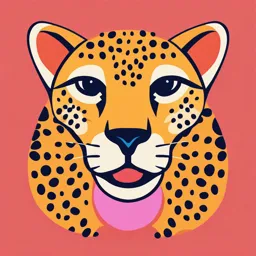
Uploaded by SolicitousOklahomaCity
null
Tags
Summary
This document provides a manual for track machines, with details covering ballast cleaning, handling, and regulating machines. The manual explains the different types of machines and their workings.
Full Transcript
CHAPTER 3 BALLAST CLEANING AND HANDLING MACHINES 301 General - Ballast cleaning and handling machines are used for handling of ballast during various maintenance and renewal operations. These machines are broadly categorized as:- (1) Ballast Cleaning Machines (BCM)...
CHAPTER 3 BALLAST CLEANING AND HANDLING MACHINES 301 General - Ballast cleaning and handling machines are used for handling of ballast during various maintenance and renewal operations. These machines are broadly categorized as:- (1) Ballast Cleaning Machines (BCM) – for screening of ballast. (2) Shoulder Ballast Cleaning Machines (SBCM) – for screening of shoulder ballast. (3) Ballast Regulating Machines (BRM) – for redistribution and profiling of ballast. The function of the Ballast Cleaning Machine is to carry out screening of full cross section of track ballast by excavating existing fouled ballast and then putting back clean ballast back in track, simultaneously disposing muck. This results in improvement of track resilience, drainage of track and elasticity of the ballast bed. Shoulder Ballast Cleaning Machines are used for cleaning of only shoulder ballast (beyond sleeper edge) by excavating and screening of ballast and removal of muck for improvement of drainage of track. Ballast Regulating Machines are meant for re-distribution of track Ballast and profiling of ballast along the track. 302 Ballast Cleaning Machines (BCM) - BCM loosens and excavates full section of fouled track ballast from crib, below sleepers and shoulders, collects it by continuous movement of endless cutter chain with fingers, depositing it to a set of vibrating screens, where muck is separated and thrown out by a waste conveyor and the screened/clean ballast is transferred back to the track through chute. The main functions of BCM are: (1) Screening of fouled ballast and disposal of muck away from track. (2) Restore clean ballast cushion, thereby improving the elasticity (resilience) of ballast bed. (3) Provide cross slope of formation. (4) Improve drainage of track. General layout and important units of Ballast Cleaning Machines are shown below: MAIN CONVEYOR WORKING DIRECTION BELT FRONT CABIN REAR CABIN SCREENING ACENDING/DECENDING WASTE CONVEYOR UNIT CHAIN GUIDE DISTRIBUTOR EXCAVATION CONV. BELT LIFTING AND UNIT SLEWING UNIT BALLAST CLEANING MACHINE Fig. 3.1 99 303 Important Assemblies of Ballast Cleaning Machines (1) Engine - The machine is powered by two independent air-cooled diesel engines. The front engine powers the hydraulic pumps for all conveyor belt drives, lifting movements and the hydraulic propulsion, both in working and travelling modes. The rear engine provides power for hydraulic pumps for the excavation chain drive and the screen drive and also powers the hydraulic propulsion for travelling. (2) Excavating unit - The excavating unit consists of endless scraper (cutter) chain consisting of scraper blades with carbide/steel fingers with tip attached to shovels with links and bolts. Endless chain is formed by connecting two parts of the chain – the cutter bar chain piece placed below the sleepers and main chain connected with the drive. Cutter bar assembly for guiding cutter chain is located between the bogies and moves under the track (sleepers) while working. Cutter chain is guided over the elbows and troughs fitted with wear plates to carry the ballast to the screening unit. The trough is connected to hydraulic cylinders for desired transverse and vertical positioning to set the cutter chain precisely at the desired excavation depth and adjust the slope of cut to provide desired formation drainage. The excavating unit is designed in such a way that the full ballast profile is handled in one working pass. However, the ballast towards the toe has to be pulled in manually beforehand towards the central portion over the sleepers and cribs. In the present model of machine, excavating chain has 82 scraper shovels and 82 intermediate links. The chain speed is variable with speeds varying from 1.8 to 4.0 meters per second. Scraper shovel is fixed with 2 or 5 scraping fingers depending on model of the BCM. (3) Screening unit - The screening unit in the present model of machine has screen area of around 21 m2 with screens of three square mesh sizes viz. 80 mm, 50 mm and 28 mm. These are vibrated by hydraulically driven rotating flyweights. Screening unit can be kept in horizontal plane on super-elevated curves by the operator-actuated controls. The top screen segregates oversized ballast and the bottom screen removes the muck. Middle screen helps to reduce the load on the bottom screen. (4) Conveyer system for distribution of ballast and disposal of muck - The clean ballast is directed through two chutes back to the track near both the rails, through distribution conveyors. These conveyers, which drop the ballast in the rear of the cutter chain, can be swung horizontally to distribute the ballast properly in the sleeper crib and area under the sleepers. Muck is collected on the waste conveyor belt underneath the screening unit, which carries it to another hydraulically adjustable belt controlled from the cabin. The waste is discharged outside the track by means of the waste conveyor, which can be moved horizontally and vertically and can throw the muck to a distance of up to 7.5 m away from the track. (5) Track lifting and slewing unit - A track lifting and slewing unit is located next to the cutter bar for adjusting the excavation depth and for avoiding the obstacles. 100 (6) Recording unit - Computerized recorder is provided on the newer version of BCM (RM80 92U), which records the following parameters: (a) Cross level before excavation of ballast. (b) Cross level after excavation of ballast. (c) Longitudinal level of left and right rails. (7) Brake system - Following brake system are provided on BCM: (a) Direct brake: This brake is applied directly on the machine while running itself. One hand operated brake valve is provided on each driving seat (3nos). (b) Indirect brake: This brake is used for application on machine and coupled camping coach/ wagon while running. One hand operated brake valve is provided on each cabin. (c) Emergency brake: This brake is used for application in case of emergency on machine and coupled camping coach/ wagon when connected through KE valve while running. It may be applied on machine only when KE valve is enabled. (d) Parking Brake: Hand operated brake systems are provided for stabling. (e) Safety Brake: This brake is applied automatically on the machine when air system pressure drops below 3.5 bar. 304 Types of Ballast Cleaning Machines - Three types of ballast cleaning machines are presently available on Indian Railways: (1) Plain Track Ballast Cleaning Machine (RM80) (Plasser India) - This machine is capable of deep screening of plain track only and is not capable of working on turnouts. Scraper blades of excavating chain are fitted with 5 scraping fingers. The important dimensions of the machine are shown in sketch at Annexure-3.1. (2) Points and Crossing Ballast Cleaning Machine (RM76) (Plasser India) - This is capable of deep screening of plain track as well as points and crossings without dismantling any component of points and crossings. For screening of points and crossings, which have longer sleepers, there is provision for extension of cutter bar by using 8 units of extension pieces, each 500 mm long; thereby providing for the maximum excavation width of 7.72m. Blades of cutting chain of this BCM are fixed with 2 scraping fingers. The important dimensions of machine are shown at Annexure 3.2. (3) Plain Track and Points & Crossings Ballast Cleaning Machine (RM80 92U) (Plasser India) This machine is similar to RM76 model except that it can handle heavier track structure with ease. The total excavation width of the cutter chain is 7.78 m, achieved by 7 extension pieces. Scraper blades are having 5 scraping fingers, in place of 2 in case of RM76. The important dimensions of machine are shown at Annexure 3.2. 101 305 Working Principle and Capability of Ballast Cleaning Machines - The excavating chain, having pentagon shape, cuts the ballast bed and carries the ballast and muck through the chain-guides to the screening unit. The vibrating screen with linear vibration effects separation of ballast from over/undersized ballast particles (muck). Underneath the vibrating screen, the muck falls on a main conveyor belt, which carries it to a slewable waste conveyor belt (which can be folded during travel), disposing the muck outside the track. Clean ballast is led to the distributor conveyor belts, from where it is distributed over the entire ballast profile. (1) Excavation width - The excavation should ideally cover full ballast width to screen the entire cross section of ballast for proper drainage as shown below: QCrit=150mm/h UNHINDERED DRAINAGE Fig. 3.2 Total width of excavation depends on size of cutter bar used. Two sizes of detachable cutter bar are 1900 mm and 2150 mm achieving cutting width of 4030 mm and 4280 mm respectively as shown below: 476 58 1900 531 (2150) 531 4030 (4280) Fig. 3.3 The desirable width of ballast bed at the formation level can be calculated by standard ballast profile for LWR. Since cutter bar cannot excavate full width of desirable ballast bed, pulling the ballast, a day or two prior to screening, from the toe towards the center, and heaping it on the sleepers and ballast crib area is 102 necessary. Other option is to separately screen this ballast either using shoulder ballast cleaning machine or manually. Normally, the width required at site for linking and opening cutting chain is approximately 5000 mm. However, the machine has a provision to fold the elbow and total width required can be reduced to less than 4500 mm, by proper planning and use of this arrangement. For deep screening at locations where the clear width available is 4500 mm like concrete and PSC Girder bridges and where linking/delinking of cutter bar over bridge or at other restricted locations may be required, cutter bar of 1900 mm should preferably be used to get more margin for such linking and delinking. FOULED SLEEPER END AREA QCrit = 1-10 mm/h Fig. 3.4 For deep screening of points and crossing, extension pieces of 500 mm each along with chain links are added to increase excavation width up to 7.78 m (Approx.), for deep screening of additional width of points and crossing. (2) Excavation depth - Depth of ballast cut by cutter bar is about 280 mm approximately. By keeping the top of cutter bar 20 mm below the sleeper’s bottom, minimum depth of excavation works out to be 300 mm approximately. The depth of excavation can be adjusted by lifting the track using the arrangement provided in the machine while screening. It is desirable that the depth of screening should be so adjusted that the formation is not cut. (3) Lifting and slewing of track - Lifting of track up to 100 mm and slewing up to ±300 mm in one pass can be achieved by machines presently available on Indian Indian Railways. (4) Disposal of muck - The retractable waste disposal conveyor belt can swing by 70° in both directions in machines presently available on Indian Railways. It extends to maximum 5 m from centre of track and is capable of disposing off the muck along the cess at a distance of about 7.5 m from the centre of track. (5) Screening capacity of BCM - The machine presently available on IR can handle excavated material up to 550 cum in an hour. If the ballast quantity in track is more, speed of longitudinal movement of machine has to be reduced to ensure proper screening. (6) Controlled ballast distribution - The screened ballast is brought back to track through distribution conveyor belt. The ballast falling through conveyor belt can be distributed by lateral swaying the distribution conveyor belt. There is a ballast guide plate over the screen to guide the ballast on one or the other side as shown below. 103 RIGHT RIGHT LEFT LEFT WORKING DIRECTION WORKING DIRECTION Fig. 3.5 The orientation of these guide plates can be adjusted to drop more ballast on one of the sides; like on outer side of curve. (7) Total excavation - BCM also has the facility to throw away entire ballast along with muck. It can be done by retracting the ballast guide plate completely, making the excavated material to fall directly onto the main conveyor belt as shown below. From main conveyor belt, it is disposed outside by waste conveyor belt. TURAS BALLAST GUIDE HOOD PLATE HYDAULIC ADJUSTABLE MAIN CONV.BELT BALLAST GUIDE PTATE Fig. 3.6 The change of mode from cleaning operation to total excavation is possible during working operation also. (8) Deep screening of Points and crossing - Deep screening of points and crossing can be done by BCM model RM76 and RM 80-92U by increasing the cutting width by attaching extension pieces, each 500 mm long. This extension is possible only on the right hand side (descending trough side) with respect to direction of working of machine as shown below. 104 DIRECTION OF WORK Fig. 3.7 Since, the direction of machine working cannot be changed frequently, the machine shall have to work on the main line or on turn out side depending on the direction of working as shown below: STARTING POSITION MORE FAVORABLE WORKING DIRECTION Fig. 3.8 It can be considered, to attach two extension pieces together to save time in the block, if feasible. Since entire length of ballast bed of points and crossing, in case of a crossover cannot be excavated/ screened by BCM, it is desirable to do the leftover sleepers in the same block manually, so as to have homogenous track resilience. Not doing this manual deep screening may cause deterioration of running. Distribution of screened ballast can be controlled by suitably aligning the ballast guide plate as shown in Fig 3.9 and Fig 3.10 (a) Working direction from switch to crossing WORKING DIRECTION BALLAST GUIDE PLATE 1/2 1/2 105 WORKING DIRECTION BALLAST GUIDE PLATE 1/4 3/4 BALL DISTR. CONV.BELT SLEWING REGION Fig. 3.9 (b) Working direction from crossing towards switch WORKING DIRECTION BALLAST GUIDE PLATE 1/4 3/4 BALL DISTR. CONV.BELT SLEWING REGION WORKING DIRECTION BALLAST GUIDE PLATE 1/2 1/2 Fig. 3.10 306 Works required before, during and after deployment of Ballast Cleaning Machines - Normally a tamping machine and a DTS should work along with Ballast Cleaning Machine in the same block. It is preferable to deploy more than one BCM along with at-least one tamping machine and a DTS to effectively manage the length of track under speed restriction. The appropriate working scheme for deployment of more than one BCMs, should be decided beforehand and made known to all concerned to plan and undertake all activities before, during and after working accordingly". (1) Introduction of Ballast Cleaning Machines for plain track and turnouts - Before undertaking screening of track ballast, advance planning and fulfilment of pre- 106 requisites are necessary to ensure work of good quality. A detailed project report shall be prepared duly incorporating location specific needs covering the following aspects: (a) A field survey should be carried out to: (i) Determine existing profile of track, formation and availability of clean and caked ballast cushion, to assess ballast recoupment requirements. (ii) Take census of hogged and battered joints, if any, which may require end cropping or reconditioning etc. (iii) Take census of broken and damaged sleepers. (iv) Make assessment of cess repairs required. (v) Plan for improvement of track drainage. (b) The proposed longitudinal profile should be finalized as per the relevant provisions in the Indian Railways Permanent Way Manual and Schedule of Dimensions. (c) Longitudinal section, showing formation level, existing and proposed rail levels should be plotted on a graph sheet either manually or using suitable software. (d) If the total (clean and caked) ballast cushion is less than 250 mm, cutter bar may cut the formation and form a channel under the track. Therefore, cutting of formation is to be avoided. If the cushion is less, the track can be temporarily or permanently lifted up to 100 mm by BCM itself during working to avoid cutting of formation. Lifting would have to be examined and carried out in consultation with electrical department as per the OHE clearance as also the other clearances available. Total ballast requirement should be calculated taking into consideration proposed lifting. The beginning and the end of transition as well as circular curves should be marked preferably by permanent reference pillars. These pillars should also be installed at every 30 m along the track and documented for future reference for alignment as well as levels. OHE masts can also be used for reference markings and documented with intermediate pillars. (e) Foot to foot survey of the section shall be conducted to see the condition of track components, and availability of land for disposal of muck. (f) Efforts should be made to identify locations having obstructions in the track, visible as well as hidden, (in a width of 4500 mm) by using the information in section register (for boulder/rubble dumped for restoration of breaches), detection of cables, rail pieces, signal, OHE and other foundations, so that action for clearing of obstructions can be planned to ensure obstruction free working and good output of BCM. Pucca drain walls etc., if infringing, should be dismantled, if the track cannot be slewed temporarily. 107 (g) Necessary action should be taken for permanent or temporary removal of obstructions beforehand. If it is not feasible to remove certain obstructions, work in those locations will have to be done manually along with the machine work. (h) All broken and damaged sleepers should be replaced. (i) Necessary attention to hogged/battered joints is given, as required, by end cropping or reconditioning etc. (j) Approaches to bridges, which cannot be screened by the machine, should be screened manually in advance or along with the machine working. (k) Number of BCM and other machines to be deployed to work together, stabling location of machines, station from which it will move to the work-site, station to which it will clear after the work, duration of blocks, lighting arrangements if working at night etc., have to be planned in sufficient details and informed to all concerned. (l) Co-ordination with other departments (i) Operating department: for planning and arrangement of line blocks and other details as above to ensure optimum utilization of tamping machines. (ii) Electrical department: for availability of OHE staff, as required. (iii) S&T department: for availability of signal staff for disconnection, reconnection etc. as required, particularly for the work of protection to cables, removal and refixing of axle counters and screening of points and crossing. (2) Preparatory works (a) Adequate arrangements for regular supply and training out of ballast shall be ensured commensurate with BCM progress. (b) The pockets of the ballast beyond the reach of cutter chain shall be pulled in its cutting width before commencement of deep screening. (c) In electrified section, distance of foundation of mast from track centre will have to be accurately measured to ensure free movement of cutting chain. (d) Any signal rodding, cable or OHE connectors, which is likely interrupt the work, should be temporarily removed. (e) Level crossings should be opened in advance so as to enable machine to work, and any infringement in cutting zone on road of LC shall be identified & removed prior to block. Sleepers should be arranged for replacement of unserviceable sleepers at level crossing. (f) Sleepers should have all the fittings intact so that no sleeper becomes loose and come in the way of cutter chain while the ballast is being excavated. 108 (g) Gas cutting equipment and concrete breaker should be available at site to cut any obstruction like rail pieces, pipes, buried foundations etc., which might get entangled with and obstruct the cutting chain. (h) Spoil disposal units (i.e. special type of wagons), should be arranged for attachment with the machine while working in station yards having multiple lines, cuttings, tunnels where dumping of the spoil along the cess is not feasible. If waste is to be disposed off across any adjacent track, the adjacent track shall also be blocked for traffic. (i) A trench of 30 cm depth and around one meter width should be made for lowering cutter bar by removing one sleeper or re-spacing the sleepers for insertion of cutter bar in track. (j) While working in LWR territory, Provision of Manual of Instructions on Long Welded Rails should also be followed. Temporary de-stressing at higher/lower temperature may be done to avoid building-up of excessive stress, as the lateral ballast resistance of track reduces substantially after the screening. (k) Arrangement and placement of engineering speed Indicators should be done as per IRPWM provisions prior to start of work and also as the work progresses. (3) Operations during traffic block (a) It should be ensured that S&T and electrical staff are available as necessary. (b) Protection of worksite and safety of staff working in the vicinity of machine shall be ensured. Hooter shall be available at site in addition to that provided on the machines to forewarn staff about approaching train on adjacent lines. (c) When the machine reaches site, the cutter bar unit shall be lowered in the trench, and both ends of cutter bar connected to guides through links. If the cutter bar is already at site (left outside the track after previous block), it may be inserted before the machine reaches the site after taking all necessary precautions. (d) When the machine starts working, one person should move with the machine on either side, to watch for any obstruction to cutter chain, so as to arrange for stoppage of the machine immediately. (e) If the machine stops moving during work, it should be ensured that gates for clean ballast below screen are instantly closed to avoid heaping up of excess ballast at one location. (f) BCM working requires manpower for activities like insertion and removal of cutter bar, filling up of ballast behind BCM etc. Sufficient manpower shall be deployed so that the progress of BCM is not affected on this account. In case of non-deployment of tamper behind the BCM, e.g. deep screening of points and crossing etc., additional manpower shall be deployed for manual packing of track for train running after the block. In exceptional cases of delay in 109 arranging the tamper, manual packing may be required to raise the speed to 40-45 kmph. (g) Screening should be stopped well before expiry of traffic block to permit proper winding up of BCM, tamping, consolidation by DTS, if deployed and movement of machines to the station. Before clearing the block it should be ensured that the cutter bar is removed, sleepers re-spaced correctly, ballast filled and packing done in the cutter bar location. (h) Ramp shall not be located in location like LC, girder bridge approach or transition of curve. Ramp should be kept away from such locations by minimum two rail lengths, (i) In case of malfunctioning of tamping machine, BCM working shall be stopped and track, which has not been tamped, shall be attended manually before opening for traffic with speed restriction as per provisions of IRPWM. (j) Proper profiling of ballast in cribs and in shoulders should be done either by BRM or by deploying adequate labour during and after machine working. (k) Utmost caution should be observed while controlling movement of waste conveyor to avoid hitting against electrical mast/signal post. Safety switch provided to sense the mast should, therefore, be kept 'ON' (in working condition). (l) All the staff working with the machine must wear safety helmets, proper shoes and masks to avoid inhaling dust. (m) In case muck disposal units are not available or cannot be used in case of multiple lines, muck should be discharged to fall on a polythene sheet placed between the lines in advance, to cover the expected length of screening. The muck shall then be filled in the gunny bags and carried away by suitable means. (n) Machine shall be driven by front side drive cabin. Reverse driving shall not be allowed for more than 4 m. (4) Operations after deployment of machine (a) At the end of work, about five sleeper spaces are left without ballast. The cutter bar shall be removed from track and these sleepers filled manually with clean ballast. (b) One round of tamping with work site tamper should be carried out immediately after deep screening in the same block with stabilization by DTS to make track fit for resumption of traffic at a speed of 40 kmph. In absence of DTS for stabilization, the relaxation of speed restriction should be made in accordance with the provisions contained in IRPWM. For Points and Crossing, UNIMAT should be used for tamping. (c) The vertical and lateral clearances for OHE, signal post, and any other structures should be checked and adjusted before clearing the BCM block. 110 (d) Ballast recoupment activity should be synchronized with deep screening activity so as to enable raising speed to normal after necessary packing. This is important to reduce the length of track under temporary speed restriction. (e) One watchman should be posted at the location where cutter bar and chain are left on cess, wherever considered necessary. (f) Arrangement and placement of Engineering Indicators should be done as per IRPWM provisions prior to start of work and also as the work progresses. (g) Group working of BCMs and allied machines, with training out of ballast in the same block will have to be considered as per field requirements to increase the effective utilization of block. 307 Shoulder Ballast Cleaning Machine (SBCM) - The machine is used for cleaning of shoulder ballast to improve the drainage of track. The working principal of SBCM is similar to BCM (RM-80). The machine is provided with two excavating cutter chains, one on either side moving in a vertical plane. Each chain excavates and picks up the shoulder ballast and directs it to a set of vibrating screens of sizes similar to that in BCM. Excavated muck is screened and clean ballast is deposited on shoulders of the ballast profile. The main functions of SBCM are to remove the muck from the shoulder ballast and improve the track drainage. General layout and important units of Shoulder Ballast Cleaning Machines (FRM-85) are shown below: WORKING DIRECTION EXCAVATION MAIN CONVEYOR WASTE CONVEYOR MAIN CONVEYOR CONVEYOR BELT BELT BELT BELT SCREEN BROOM RUNNING PLOUGH DRIVING AXLES EXCAVATION DRIVING AXLES DISTRIBUTOR CHAIN & TROUGH AXLES CONVEYOR BELT Fig. 3.11 308 Important Assemblies of Shoulder Ballast Cleaning Machines (1) Engine - The machine is powered by one water cooled engine. It powers the hydraulic pumps for excavation chain drive, screen drive; all conveyor belt drives, lifting movements and the hydraulic propulsion both in working and travelling modes. (2) Excavating Unit - The machine is provided with two excavating cutter chains, one on either side rotating in a vertical plane, while working. Each chain excavates and picks up the shoulder ballast and directs it to a set of vibrating screens. Each excavating chain has 43 scraper plates with two caps and 43 intermediate links. 111 (3) Screening Unit - SBCM has screening units similar to that of BCM and are of same screen sizes i.e. 80 mm, 50 mm and 28 mm. (4) Conveyer system for distribution of ballast and disposal of muck - The ballast from excavating unit is carried to vibrating screen through excavating conveyor belt system. The screened ballast is distributed on shoulder by distribution conveyor belt system. The muck is disposed by the side of track via main conveyor belt through the waste conveyor belt system. (5) Ballast profiling plough - One center plough is provided to profile and distribute the screened ballast. (6) Broom - These are provided at the rear end and are used for cleaning sleeper and fittings and for collecting and distributing ballast. (7) Brake System - Following brake system are provided on SBCM: (a) Direct brake - This brake is applied directly on the machine while running itself. One hand operated brake valve is provided on each driving seat (2nos). (b) Indirect Brake - This brake is used for application on machine and coupled camping coach/ wagon while running. One hand operated brake valve is provided on each cabin. (c) Emergency Brake - This brake is used for application in case of emergency on machine and coupled camping coach/ wagon when connected through KE valve while running. It may be applied on machine only when KE valve is enabled. (d) Parking Brake - Hand operated brake systems are provided for stabling. (e) Safety Brake - This brake is applied automatically on the machine when air system pressure drops below 3.5 bar. 309 Types of Shoulder Ballast Cleaning Machines - Presently, two types of Shoulder Ballast Cleaning Machines are available on Indian Railways. (1) Shoulder Ballast Cleaning Machine - FRM 80 (Plasser India). (2) Shoulder Ballast Cleaning Machine - FRM 85F (Plasser India). Both the machines are similar except that the muck in FRM 80 is thrown on the backside while that in FRM 85 is thrown in the front. The important dimensions of machine are shown at Annexure 3.3 and 3.4 310 Capacity of Shoulder Ballast Cleaning Machines (1) Width of excavation - Normal width of excavation on either side is 1,530 mm. The minimum distance to the end of the plough from center of track is 1,790 mm extending to 3,320 mm. Thus, the excavating unit can be extended on either side to cover width up to 4150 mm from center of track. 112 880 1435 1930 1790 2530 3320 415 2620 865 665 4150 1245 1700 1700 Fig. 3.12 (2) Depth of excavation - The depth of excavation should be regulated so as to maintain uniform continuous cross slope of the top of the formation. (3) Muck disposal system - The muck is disposed by the side of track, via main conveyor belt through the waste conveyor belt system, up to maximum distance of 7.5 m from center of track. (4) Ballast distribution system - The screened ballast is distributed on shoulder with the help of swiveling distribution conveyor system. (5) Screening capacity - The screening capacity is 500 cum per hour. (6) Total excavation - The ballast from excavating conveyor belt system can be dropped directly to main conveyor belt thus bypassing screen and can be disposed via waste conveyor belt. 311 Works required before, during and after deployment of Shoulder Ballast Cleaning Machines - The preparations for this machine are almost same as those of plain track ballast cleaning machines. In addition, following aspects should be given attention: (1) Operations prior to deployment of machine - Any obstruction existing in the shoulder area should be removed. (2) Operations during block - After taking the machine to the site, the operator shall set the excavating units such that they do not touch the sleeper. The depth of excavating units is set hydraulically, taking into consideration the required cross slope. Thereafter, the conveyor belt is unlocked and turned to the desired direction. Similarly plowing, grading units, conveyor belts and vibrating units are set as per the manual of the machine. It takes about five minutes for setting up the machine from drive mode to working mode. Other aspects to be watched are given below: (a) In case of single lines, full depth of the haunches should be excavated to ensure good drainage. (b) In case of double lines or multiple line sections, full depth of the haunches should be excavated on cess side. Between the tracks, the depth of haunch excavation should be just sufficient to provide continuity to drainage line of the cribs. 113 312 Ballast Regulating Machine (BRM) - These machines are used for ballast transfer, spreading and profiling operations. The machine can move ballast towards center of track or away from center of track, transfer ballast across the track and transfer ballast from a surplus zone to deficient zone. The main features of BRM are: (1) Regulation of ballast to achieve proper profile. (2) Transfer of ballast from centre to outwards either on both sides or on one side only. (3) Transfer of ballast from one side to the other or to the centre or from both sides to the centre. (4) Sweeping the sleepers and cribs and picking up of surplus ballast in to hopper, if available and transporting it to another location. (5) Sweeping the fasteners after ballast regulation using brooms. This machine operates in both directions. General layout and important units of Ballast Regulating Machines (BRM Kershaw) are shown below: SIDE PLOUGH FRONT CENTER BROOM PLOUGH SWEEPER Fig. 3.13 313 Important assemblies of Ballast Regulating Machines (1) Shoulder plough – These are attached to the sides of the machine and are hydraulically operated and controlled from the cab. These are designed to work on shoulder ballast and shift ballast from outside to inside and from inside to outside. The machine can be equipped with standard fixed width ballast wings or optional variable width ballast wings for better profile shaping. (2) Front plough –It is placed in between rails in front portion of the machine and is used for handling ballast in between rails. The plough can be positioned from the operator’s cab to plough out, plough in or to transfer ballast to either side of the track with the machine travelling either forward or backward. (3) Centre plough - It is provided in the middle of the machine i.e. between bogies/wheels and is hydraulically operated and controlled from the cab. Like front 114 plough, it is placed in between rails and is used for handling ballast in between rails. Normally, a machine is provided either with front plough or with centre plough, but not both of them. (4) Broom (Sweeper conveyor system) - It is mounted in the rear or in the middle between the bogies of the ballast regulator. It is used for track dressing operations, to remove ballast from top of sleepers, to fill under-ballasted cribs and to place extra ballast on the shoulders for final regulation and dressing. The sweeper unit consists of rotating drum fitted with flexible tubular rubber pieces of designated length and mounted inside steel plate housing. While rotating it throws surplus ballast via a guiding duct on to two lateral conveyors. In machines provided with hopper, these take ballast to a steep conveyor belt, which takes it to a hopper for collection. Broom is rotated by hydraulic motor. (5) Hopper - Hoppers have capacity varying from 5-12 m3 depending on the model and collect excess ballast through broom sweeper conveyor system and then places it on shoulder through chutes, where required. (6) Rail fastening sweepers - These are provided to remove ballast from over the fastenings. (7) Welded-on-tunnels for covering rail and fastenings - These are sturdy inverted steel troughs provided to cover the rail and fastenings area to avoid flooding of rail area with ballast at different stages of working. (8) Brake System - Following brake system are provided on BRM Machine (PBR-400R):- (a) Direct brake - This brake is applied directly on both bogies/axles on this machine while running by one hand operated brake valve. (b) Indirect brake - This brake is used for application by one hand operated brake valve on machine and coupled camping coach/ wagon when connected through KE while running. It may be applied on machine only when KE valve is enabled. (c) Emergency brake - This brake is used for application in case of emergency on machine and coupled camping coach/ wagon when connected through KE valve while running. It may be applied on machine only when KE valve is enabled. (d) Parking brake - Hand operated mechanical brake systems are provided on one axle for stabling except Kershaw machine. On Kershaw machine dual acting brake cylinders are provided for parking as well as braking. 314 Types of BRM - Ballast Regulating Machines working on Indian Railways are classified into two categories as below : (1) Without hopper - These machines are provided with shoulder plough, front/center plough, brooms, and conveyor belts. These are four-wheeler vehicles. Different models of BRM’s working on Indian Railways are: (a) BRM Model 66-2/56-3 and 66-4 (Kershaw). (b) PBR 400R (Plasser India). (c) BRM Model SPZ-210 K (Gemac Engg ). 115 BRM Model SPZ-210 K (Gemac Engg) has centre plough while other two models have front plough. The important dimensions of machines are shown at Annexure 3.5, 3.6 and 3.7. (2) With hopper - These machines have a system of collecting excess ballast from over sleeper to the hopper via broom and conveyor belt arrangement. The collected ballast is unloaded at the shoulder wherever required through a chute opening. (a) USP 2000 SWS (Plasser India). (b) RPB-01(Metex, Russia). These are bogie type 8-wheeler vehicles. They are provided with center plough along with brooms provided in the middle i.e. between bogies. The important dimensions of machines are shown at Annexure 3.8 and 3.9. 315 Working principle and capacity of Ballast Regulating Machines - The transfer of ballast from one side to other is done by properly positioning the shoulder plough and front/center plough. The shoulder plough can transfer ballast from outside to inside and from inside to outside as shown below : SHOULDER PLOUGH SHOULDER PLOUGH SHOULDER PLOUGH Fig. 3.14 It can also carry ballast by enclosing ballast in boxed enclosure using shoulder plough SHOULDER SHOULDER PLOUGH PLOUGH Fig. 3.15 116 The front plough of BRM, Kershaw make guides ballast flow as shown below: FLOW BALLAST IN FLOW TRAVEL MACHINE TRAVEL MACHINE FRONT PLOUGH FLOW BALLAST OUT FLOW FLOW BALLAST OUT FLOW TRAVEL MACHINE TRAVEL MACHINE FRONT PLOUGH FRONT PLOUGH FLOW BALLAST IN FLOW Fig. 3.16 FRONT PLOUGH Fig.3.17 117 The front plough of Plasser machine guides the ballast flow as shown below: FRONT FRONT PLOUGH PLOUGH FRONT PLOUGH FRONT FRONT PLOUGH FRONT PLOUGH PLOUGH Fig.3.18 The center plough has two or four blades and it does shifting of ballast as shown below: CENTER CENTER PLOUGH PLOUGH CENTER CENTER PLOUGH PLOUGH Fig. 3.19 118 Shoulder plough combined with front plough can be used to regulate the ballast flow from shoulder to center or other side and also from center to shoulder as shown below: SHOULDER PLOUGH FRONT FRONT PLOUGH PLOUGH SHOULDER PLOUGH Fig. 3.20 Similarly, shoulder plough can be combined with center ploughs for transferring ballast. Behind the regulation activity, the brooms pick up the ballast from over sleepers and it is either collected through conveyor belt to hopper or distributed directly through horizontal conveyor to sides. The sweeper cleans the fittings of ballast. In machines with front plough, for dressing of the ballast left by shoulder plough on sleepers, one reverse pass shall be required. Thus two or more passes are required for complete profiling of ballast by BRM. In machines provided with center plough, only one pass should normally be required for complete profiling. (1) The Regulation Width - Shoulder plough has a reach of up to 3.5 meter approximately from centerline of track in all machines and thus can handle ballast well beyond full ballast section of standard Indian railway track. (2) Ballast Handling Capacity It can handle around 2000 m3 ballast in an hour. 316 Works required before and during deployment of Ballast Regulating Machines (1) Operations prior to deployment of machine (a) The locations of excess and deficiency of ballast should be identified. In case of overall deficiency of ballast, training out of adequate ballast at locations of deficiency, which can-not be balanced by excess ballast in adjacent stretches should be carried out. (b) Any obstruction existing in the shoulder area, which may infringe plough (blades) of BRM, should be removed in advance. (2) Operations during Block (a) Adequate protection as per G & SR shall be ensured for the machine working under line block. (b) Profiling of ballast and its shifting should be done on the basis of an advance survey of excess and deficiency of ballast. 119 (c) In case of double lines or multiple line sections, proper protection should be taken while using shoulder plough so as not to infringe adjacent line. In case it is likely to infringe with the adjacent line, line block for that line, for the period of infringement shall also be taken. (d) Adequate precautions should be taken in using shoulder plough near OHE mast, Signal post or any fixed structure alongside the track to avoid any damage to these installations. (e) While working on Points and Crossings, care should be taken, not to hit the S&T installations in switch portion by any of the BRM plough. (f) Normally more than one pass might be required to achieve the target ballast profile. (g) Before clearance of the block it shall be ensured that the ballast is not heaped in such a way that it is/may infringe the unrestricted movement of trains. 120 Annexure3.1 Important features/dimensions of Ballast Cleaning Machine (RM-80) BALLAST CLEANING MACHINE DIRECTION OF WORK MAIN CONVEYOR BELT FRONT CABIN REAR CABIN SCREENING UNIT ACENDING/DECENDING WASTE CONVEYOR CHAIN GUIDE G E F D DISTRIBUTION CON. BELT EXCAVATION UNIT C B LIFTING AND SLEWING UNIT A D E F G WHEEL DIA AXLE MODEL A B C DRIVEN IDLE LOAD WIDTH RM-80 30600 29360 22200 1830 880 1785 4015 900 700 18.5t 3140 ALL DIMENSIONS ARE IN mm. 121 Annexure 3.2 Important features/dimensions of Ballast Cleaning Machine (RM-76 & RM-80-92U) BALLAST CLEANING MACHINE DIRECTION OF WORK G F B D D B C E H A MODEL A B C D E F G H WHEEL DIA. AXLE LOAD WIDTH RM-76UHR 24730 620 2710 1830 19500 4015 2520 900 19.0t 3150 RM-80-92U 29540 620 3670 1830 22200 4015 3670 900 19.8t 3140 ALL DIMENSIONS ARE IN mm. 122 Annexure3.3 Important features/dimensions of Shoulder Ballast Cleaning Machine (FRM-80) SHOULDER BALLAST CLEANING MACHINE (FRM-80) DIRECTION OF WORK EXCAVATING CONVEYOR BELT MUCK CONVEYOR BELT MAIN CONVEYOR BELT EXCAVATING CHAIN SCREEN H RUNNING AXLE DRIVING AXLES DRIVING AXLES PLOUGH E DISTRIBUTION CONVEYOR BELT G C D F B A WHEEL MAX AXLE MAX NAME OF MACHINE A B C D E F G H DIA LOAD WIDTH FRM-80 39470 38200 16000 15000 1810 635 3600 4260 900 20.0t 3090 ALL DIMENSIONS ARE IN mm. 123 Annexure3.4 Important features/dimensions of Shoulder Ballast Cleaning Machine (FRM-85 F) SHOULDER BALLAST CLEANING MACHINE (FRM-85) DIRECTION OF WORK MAIN CONVEYOR WASTE CONVEYOR MAIN CONVEYOR BELT BELT BELT EXCAVATION SCREEN CONVEYOR BELT H RUNNING AXLE DRIVING AXLES EXCAVATION CHAIN DRIVING AXLES PLOUGH E AND TROUGH DISTRIBUTION CONVEYOR BELT G C D F B A WHEEL MAX AXLE MAX NAME OF MACHINE A B C D E F G H DIA LOAD WIDTH FRM-85F 39440 38200 16000 15000 1830 620 3600 4085 900 20.4t 3090 ALL DIMENSIONS ARE IN mm. 124 Annexure 3.5 Important features/dimensions of Ballast Regulating Machine (Model - 56-3 & 66-4) BALLAST REGULATOR SIDE PLOUGH FRONT CENTER F BROOM PLOUGH D E B C A SWEEPER MODEL MODEL-56-3 MODEL-66-4 ALL DIMENSIONS ARE IN mm. 125 Annexure 3.6 Important features/dimensions of Ballast Regulating Machine (Model BRM PBR 400R) BALLAST REGULATING MACHINE DIRECTION OF WORK SIDE PLOUGH BROOM FRONT CENTER PLOUGH J PLATE COVER I H D G E C B F E A MODEL A B C D E F G H I J WHEEL DIA MAX AXLE LOAD MAX WIDTH BRM PBR 400R 11020 4500 2700 2605 635 2550 2275 1105 3220 3500 730 10.0t 3184 ALL DIMENSIONS ARE IN mm. 126 Annexure 3.7 Important features/dimensions of Ballast Regulating Machine (GEMAC). BALLAST REGULATOR (GEMAC) CABIN FRONT CENTER PLOUGH F E B C D C B A REAR CENTER PLOUGH SIDE CONVEYOR SIDE PLOUGH MID CENTRE PLOUGH MODEL A B C D E F WHEEL AXLE WIDTH DIA LOAD BRM GEMAC 14780 640 3000 7500 1105 3820 915 18.8t 3080 ALL DIMENSIONS ARE IN mm 127 Annexure 3.8 Important features/dimensions of Ballast Regulating Machine (BRM 2000 SWS) BALLAST REGULATING MACHINE BROOM CONVEYOR BELT HOPPER G F SIDE PLOUGH MID CENTER E D PLOUGH E C B C D A NAME OF MACHINE A B C D E F G WHEEL DIA AXLE LOAD WIDTH BRM 2000 SWS 19140 11500 3200 1830 620 1105 4110 850 20.0t 3180 ALL DIMENSIONS ARE IN mm. 128 Annexure 3.9 Important features/dimensions of Ballast Regulating Machine (BRM METEX) BRM METEX HOPPER CONVEYOR BELT F E D B C CENTER PLOUGH BROOM SHOULDER PLOUGH A MODEL A B C D E F WHEEL DIA AXLE LOAD WIDTH BRM METEX RPB-01 22300 650 2000 13800 1105 4070 957 20.32t 3090 ALL DIMENSIONS ARE IN mm. 129